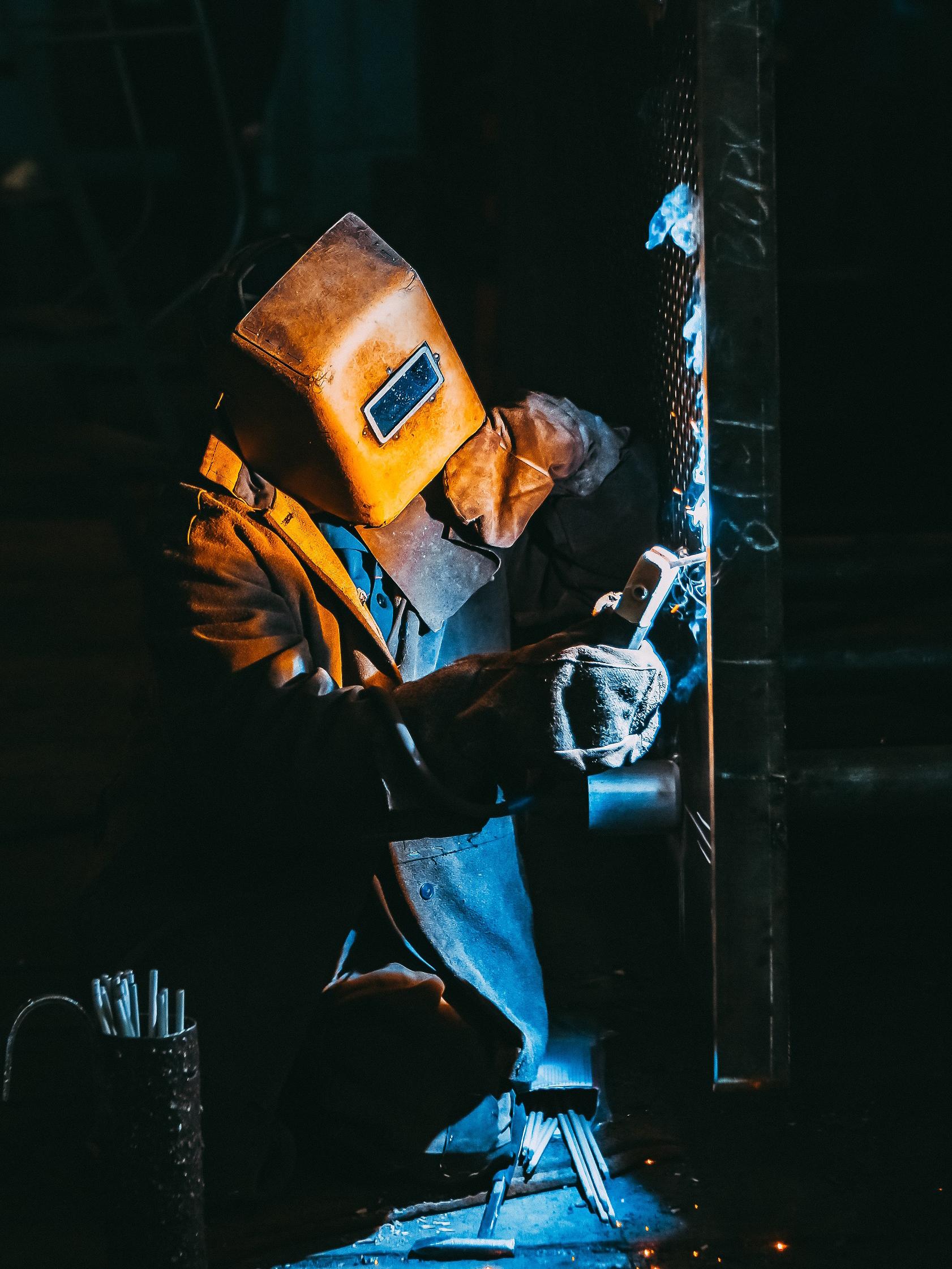
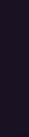
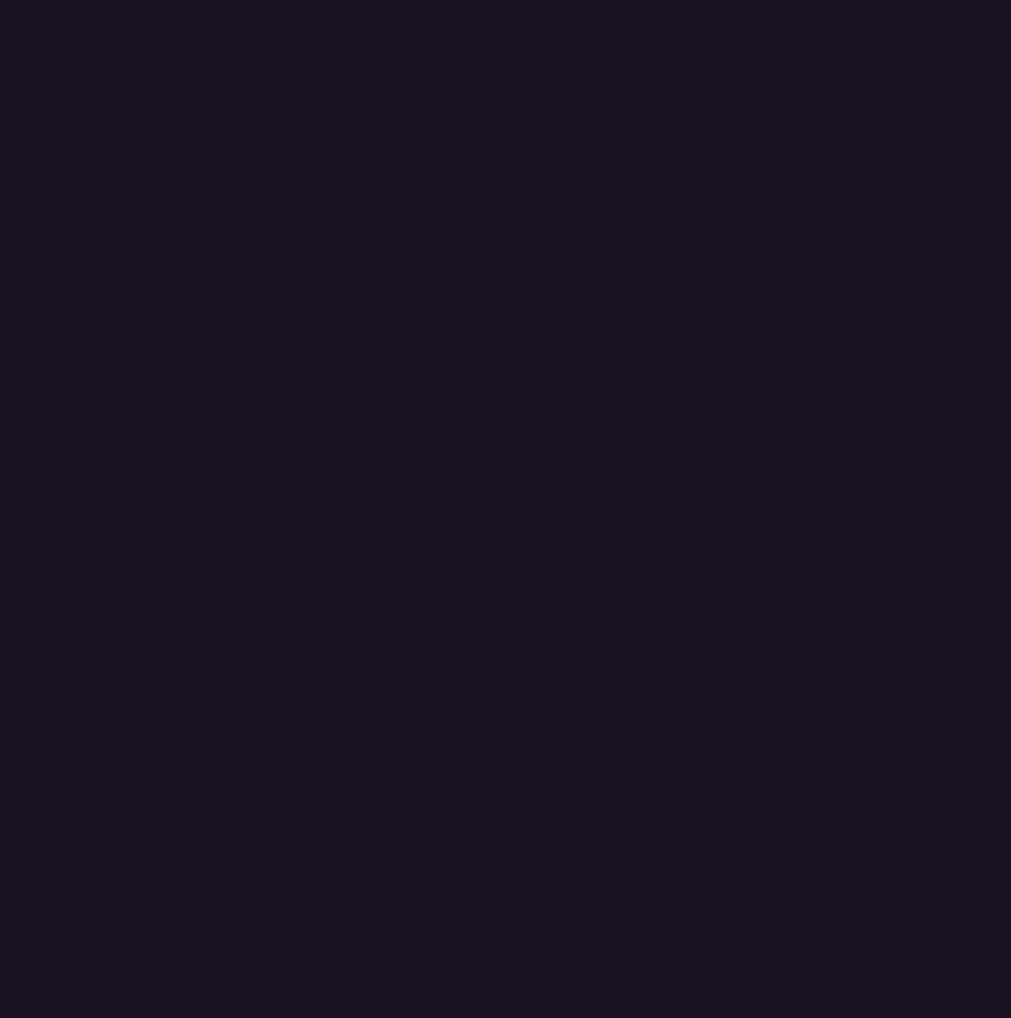







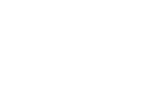

forge transparent partnerships as we simplify the complexities of marketing for all our customers. Since 2005, our mantra has been: success will look after itself.”
We look after your marketing from start to finish!
Editor
Paul Attwood editor@mpemagazine.co.uk
Senior Editorial Assistant
Sophie Weir editorial@mpemagazine.co.uk
Features Editor
Harry Peters editorial@mpemagazine.co.uk
Production/Design
Laura Whitehead laura@lapthornmedia.co.uk
Megan Carley megan@lapthornmedia.co.uk
Sales Manager
Charlotte Chapman charlotte@mpemagazine.co.uk
Accounts
Richard Lapthorn accounts@mpemagazine.co.uk
Circulation Manager
Leo Phillips
subs@mpemagazine.co.uk
Publishing Director
Maria Lapthorn maria@lapthornmedia.co.uk
Lapthorn Media Ltd
5-7 Ozengell Place, Eurokent Business Park, Ramsgate, Kent, CT12 6PB
Tel: 01843 808 102
Digital transformation enables more than cost-savings – it can re-engage the frontline
Removing The Biggest Barrier to Autonomous Vehicle Development
Health & Safety: Culture is the key to safer operations
Interview with Donna Edwards: Technology Adoption in Manufacturing From the workshop to the boardroom - a manufacturing success story
Welcome to the December issue of Manufacturing & Production Engineering Magazine.
In this issue we interview Donna Edwards, Director of Made Smarter’s Northwest Adoption Programme, who provides an insight into how manufacturers can overcome the challenges involved with adopting new technologies including Artificial intelligence, and its importance on the future of the UK manufacturing industry.
We also take a close look at the finalists for the prestigious Institution of Engineering and Technology’s Young Woman Engineer of the Year Awards 2024. Congratulations to the five ladies, whose contribution to the engineering sector has led to the nomination. The winner is announced at the Awards ceremony on 9th December.
We hope you enjoy this issue and like always, if you have any contributions you would like to feature, please email details to editorial@mpemagazine.co.uk.
The UK electrolyser technology sector has been given a boost with the announcement of three winners of the Net Zero Technology Centre’s (NZTC) 2024 Electrolyser funding competition.
Efficient electrolysers are key to cost-effective and large-scale green hydrogen production. Research from phase one of NZTC’s Energy Hubs project identified the need to accelerate the development of nextgeneration electrolyser technologies to meet future domestic and global hydrogen demand.
Taking action, NZTC is pushing forward the development of prototypes, with a goal to pilot. This initiative aims to scale the Scottish supply chain and establish an export market.
Thirty-six applications were received from around the globe with three UK electrolyser developers selected. Each will each receive a share of the £500,000 funding to accelerate the development of their technology.
‘iGSE’
The CEO of Aurrigo International plc, a leading international provider of smart airside solutions, has today urged aviation industry stakeholders to embrace innovation and drive the evolution of ground support equipment.
Professor David Keene emphasised the necessity for ground handlers to transition into a new paradigm he has coined as ‘iGSE’ - intelligent Ground Support Equipment.
His vision encompasses a suite of advanced, integrated technologies designed to enhance operational performance and streamline airside activities.
By adopting smart airside solutions, the industry can reduce turnaround times, improve reliability, and significantly lower its environmental footprint.
Aurrigo is committed to leading the charge in this transformation, investing in designing and developing innovative solutions that position the company - and its partners - at the forefront of the future of airside operations.
Customers choose to partner with the UK-based company to transform their baggage and cargo handling operations, improving safety, operational efficiencies and meeting sustainability targets, whilst navigating growing passenger volumes, rising costs and increasing labour shortages.
Efficient electrolysers are key to cost-effective and large-scale green hydrogen production.
The Energy Hubs project aims to develop energy infrastructure across Scotland to produce large-scale green hydrogen and alternative fuels by harnessing the country’s natural resources. The hydrogen produced in Energy Hubs will transform Scotland into a leading exporter of green hydrogen, with plans to export over 0.9 million tonnes to Europe every year via a dedicated hydrogen pipeline.
Electrolysers, which use electricity to split water into hydrogen and oxygen, are a critical technology for success.
The National Manufacturing Institute Scotland (NMIS) has welcomed its 100th member with international aerospace leader ATI Inc. (NYSE: ATI) joining the University of Strathclyde’s Advanced Forming Research Centre (AFRC) as a Tier One Member, marking the beginning of a collaboration in advanced engineering and materials science that will support sustainable air travel.
Based in Dallas, Texas, ATI is a major producer of materials to global aircraft engine manufacturers and has over one hundred years of experience in creating materials and component solutions such as titanium and nickel superalloys that can withstand extreme conditions, heat, pressure, and corrosion.
Access to the AFRC’s pioneering FutureForge facility is expected to support ATI with the development of the next generation of materials and process technologies, with the world-leading forging research facility providing an industrial-
scale iso-thermal testing platform. As airlines increasingly focus on sustainability, new metallic alloys that can endure higher temperatures than ever before will be key to allowing jet engines to operate at maximum efficiency and, ultimately, burn less fuel.
The AFRC, which is one of the founding centres of the High Value Manufacturing (HVM) Catapult, launched FutureForge earlier this year, connecting the $75 billion global forging sector with the industry-scale testbed and centre’s expertise, no matter where they are in the world.
FutureForge comprises a tri-modal 2,000-tonne press offering open die, closed die, and iso-thermal forging capabilities, instantaneous data analytics through a state-of-the-art control room, two furnaces - one powered by electricity and the other by gas - and a custom-built smart robotics manipulator arm. Companies such as ATI can use the platform to de-risk the development of new products, processes, and technologies.
By Sam Byrnes, Chief Product Officer at SafetyCulture, the global workplace
operations platform.
Most manufacturers have strictly practical reasons for embarking on digital transformation – they want to increase efficiencies, save costs, and improve productivity. Of course, these are vital for remaining competitive, but there’s another huge benefit to digital transformation which is often overlooked: better frontline morale.
Ironically, many manufacturing and engineering businesses which produce highly sophisticated products are still using paper-based processes that aren’t fit for purpose. For frontline workers, these clunky outdated processes are demotivating and frustrating, resulting in a host of workforce issues, from high churn rate to low employee engagement.
Even when businesses introduce software, if this isn’t done strategically it can compound the problem. In fact, in a recent SafetyCulture survey, we found that nearly two-thirds (61%) of workers aren’t fully happy with their workplace tools and IT systems. The chances are that your employees find your tools outdated, feel overwhelmed by the sheer number of them, or undertrained to use them.
But businesses that get digital transformation right benefit from workforce transformation too. One of today’s boldest trends is the move towards paperless, appbased operations. Forward-thinking businesses are investing in easy-touse, mobile-first workflows which are intuitive – if you can use a smartphone, then you can use your workplace IT.
But if your workers are frustrated and constantly questioning why certain processes exist, it’s worth listening.
It might seem obvious to give workers kit which is simple to use, but the knock-on impact can be very powerful.
Workers feel more empowered in their role, more confident in their skills and development, and more valued by their company – and in our experience, this is actually truer for older generations of workers who built their careers around paper-based processes.
Let’s look at an example from the more than 160-year-old Scottish family-owned business Donaldson Group. With 1,700 employees at 47 locations, the group provides the UK housebuilding industry with a wide range of products and services. But the business conducted 100 monthly internal audits with pen and paper –using around 30 sheets of paper for every three to four sites – a practice which Chief Risk Officer, Mark Murphy, needed to modernise. In 2020, after Mark digitised the company’s audits using SafetyCulture’s platform, he saved 30-40 minutes on each internal audit per employee, not to mention a forest’s worth of paper.
But Donaldson Group was also strategic in its use of internal advocacy. Mark’s approach was to
identify the business risk, then find a worker considered a leader by peers, though not necessarily someone in a management role. This workforce leader was trained in the platform and used it to conduct checks. As word of mouth spread and workers saw the benefit of digitisation, more colleagues adopted the platform in their workplace operations. Workers have responded
positively to having their feedback heard and gaining a tool that drives efficiency and is tailored to their needs. Ultimately, frontline morale is a complex phenomenon, and it can be difficult to measure, let alone impact. But if your workers are frustrated and constantly questioning why certain processes exist, it’s worth listening. And digital transformation could be the answer.
ergonomic positioners are single or double column devices that enable the lifting and rotation of a product during welding and assembly operations.
With overall capacity from 2,000 - 90,000kg to suit, they are both compact and flexible.
At this year’s Engineering & Manufacturing Awards, Spanwall was presented with the Digital Innovation Award for its Smart Manufacturing initiative.
The Digital Innovation Award was presented for Spanwall’s market-leading Smart Manufacturing initiative, which has applied digital technology to streamline processes and workflows. This has leveraged
The leading supplier of renewable heating technology was ranked at number 29 in Great Place to Work’s 2024 UK’s Best Workplaces for Construction, Engineering & Property as a result of its efforts to drive the sector forward while providing a sense of fulfilment, job satisfaction, and financial security for employees.
Listed in the UK Small Business category, 100 percent of employees said STIEBEL ELTRON treated them fairly regardless of race or gender, gave them the resources to do their job, created a safe environment, and provided facilities for a good working environment.
STIEBEL ELTRON UK has placed an onus on growing its offering to the UK’s renewable heating market as it looks to drive the adoption of heat
the power of digital twinning for rapid prototyping of its metal façade components before going into full production.
The new technology also allows the live tracking of every component part through each stage of design and manufacturing, delivering real-time reporting for improved efficiency and a completely new level of customer communication, transparency and traceability.
The digital system has integrated multi-disciplinary data to create a truly information-driven product workflow. This allows Spanwall to create and test new metal rainscreen cladding designs for its customers and specifiers more efficiently, whilst optimising manufacturing resources and significantly increasing overall capacity.
The new digital technology provides increased certainty of project delivery on time and on budget, and to consistently high-quality standards.
The next phase of Spanwall’s digital transformation will apply new technology to integrate quality control, preventative maintenance, health and safety, and estimating into digital workflows.
pumps across the country with the most innovative technologies and comprehensive training for installers.
Recently partnering with solar panel provider Solarwatt, they are implementing a holistic approach towards renewable technologies, maximising energy efficiency and cost savings.
The company has invested in an initial £350,000 investment into a new state-of-the-art training centre and programme in November 2022, expanding the facility at its headquarters in Bromborough, in September last year, increasing capacity for new heat pump installers.
As demand for the technology increases, the company has finetuned training courses to aid gas boiler installers looking to transition to a growing base of heat pump installers.
www.stiebel-eltron.co.uk/en/ home.html
The leading supplier of renewable heating technology was ranked at number 29 in Great Place to Work’s 2024 UK’s Best Workplaces for Construction, Engineering & Property as a result of its efforts to drive the sector forward while providing a sense of fulfilment, job satisfaction, and financial security for employees.
Listed in the UK Small Business category, 100 percent of employees said STIEBEL ELTRON treated them fairly regardless of race or gender, gave them the resources to do their job, created a safe environment, and provided facilities for a good working environment.
STIEBEL ELTRON UK has placed an onus on growing its offering to the UK’s renewable heating market as it looks to drive the adoption of heat pumps across the country with the most innovative technologies and comprehensive training for installers.
Recently partnering with solar panel provider Solarwatt, they are implementing a holistic approach towards renewable technologies, maximising energy efficiency and cost savings.
The company has invested in an initial £350,000 investment into a new state-of-the-art training centre and programme in November 2022, expanding the facility at its headquarters in Bromborough, in September last year, increasing capacity for new heat pump installers.
As demand for the technology increases, the company has finetuned training courses to aid gas boiler installers looking to transition to a growing base of heat pump installers.
The global edge computing market is expected to grow by more than 30 percent in the next five years, serving missioncritical applications in the aerospace, defense, military, industrial and medical sectors.
To meet this increasing demand for reliable, embedded solutions for mixed-criticality systems, Microchip Technology (Nasdaq: MCHP) has announced the PIC64HX family of microprocessors (MPUs).
Unlike traditional MPUs, the PIC64HX is purpose built to address the unique demands of intelligent
edge designs, supported with TSN Ethernet switching and AI capabilities.
The latest in Microchip’s 64-bit portfolio, the PIC64HX is a highperformance, multicore 64-bit RISC-V® MPU capable of advanced Artificial Intelligence and Machine Learning (AI/ML) processing and designed with integrated Time-Sensitive Networking (TSN) Ethernet connectivity and postquantum-enabled, defense-grade security.
PIC64HX MPUs are specifically designed to deliver comprehensive
Walter has completed its existing Perform line with the addition of new five and six-flute solid carbide milling cutters for the ME232 Perform series. In addition, Walter has also added two and four-flute ball-nose end mills to the ME432 Perform series.
The Perform line offers advantages to users that work with small and medium batch sizes whereby users are often not able to maximise the tool life of a high-volume tool. At the same time, manufacturers in the price-conscious segment also stand to benefit. The new, short three and
four-flute cutting tools for turning centres with stationary or driven tools offer huge potential as they are part of the standard set-up in this field.
Walter now offers the Perform line of milling cutters with diameters from 1 to 20mm, two to six cutting edges, and cutting edge lengths from 1XDc to 3XDc. The new Perform line of milling cutters incorporates a ‘highperformance geometry’, meaning that the number of teeth and the helical pitch are perfectly coordinated. This ensures excellent operational smoothness and an outstanding material removal capacity.
fault tolerance, resiliency, scalability and power efficiency.
The PIC64HX MPU allows system developers to deploy the cores in multiple ways to enable SMP, AMP or dual-core lockstep operations. WorldGuard hardware architecture support is provided to enable hardware-based isolation and partitioning.
The PIC64HX MPU is a powerful and versatile solution for intelligent edge applications, addressing key requirements for low latency, security, reliability and compliance with industry standards.
In addition to being excellent value for money, Perform line users can enjoy the same support services that are typical of Walter’s higherend tools. Alongside STEP files and data models for programming, these services also include calculating and providing cutting data with the Walter GPS ‘machining navigation system’.
When production halts unexpectedly, it disrupts the entire supply chain, leading to delays in product delivery and substantial costs. Frequent downtime can damage equipment, reducing its potential lifespan and increasing maintenance costs.
Thermal imaging is a powerful tool for preventative maintenance in manufacturing, involving infrared cameras to detect heat patterns and anomalies in equipment. Identifying areas of excessive heat allows
maintenance teams to address issues before they lead to costly unscheduled downtime.
Thermography provides data that can be used to track the condition of equipment over time, enabling more informed decision-making and better planning of maintenance activities. Overall, thermography is an essential component of a robust preventative maintenance strategy, ensuring operational continuity and safety.
Teledyne FLIR specialises in the
design and production of thermal imaging cameras and sensors, renowned for their innovative technology. FLIR’s products are used across various industries, including manufacturing, security, and environmental monitoring.
While training can be provided by organisations such as the Infrared Training Centre, or online via the FLIR Academy; FLIR offer multiple features to support both experienced and inexperienced thermographers to monitor their equipment.
There is increasing demand from engineers and specifiers working on complex motion control applications for cutting edge motors requiring high-torque, precise positioning and efficient operation, even in demanding environments.
To meet these demands, MOONS’ Industries continue to develop its range of Super Large Hollow Shaft Stepper Motors for diverse applications. These motors provide exceptional performance and flexibility across applications such as robotics, semi-conductor manufacturing, industrial automation and security systems, potentially revolutionising how machine builders and system
integrators approach their projects. They offer a unique combination of high torque output and large bore diameters, making them ideal for motion control applications requiring both power and versatility. The large bore diameters of MOONS’ hollow shaft stepper motors allow for the integration of linear transmission shafts, cables, air flow, liquids, or even beams directly through the motor’s centre.
When paired with a harmonic gearbox, these motors deliver output torque, resulting in a motor that can deliver at least twice the torque for the same frame size and aperture compared to solid shaft motors.
As with all MOONS’ products, these super large hollow shaft motors are backed by MOONS’ global support network and application expertise. MOONS’ engineers work closely with customers to develop tailored motion control packages that maximise performance and reliability whilst minimising the total cost of ownership.
By Brian Fitzgerald
The UK manufacturing industry supports over 2.6 million jobs and accounts for 49% of national exports. In 2023, the sector generated a notable output of £224 billion, climbing to 8th in the global manufacturing rankings. This commendable achievement is a testament to the industry’s resilience and its future potential.
However, to continue this progress within the UK, manufacturers need to overcome major industry challenges, from the skills gap to meeting regulatory challenges head on.
The skills demand
Augury’s State of Production Health report highlights a key issue for nearly 34% of manufacturers – the urgent need to upskill their workforce. This is largely due to the widespread use of outdated technology, which has created a significant skills gap as companies transition to Industry 4.0 and 5.0. As technological advancements reshape manufacturing, addressing this gap is crucial to staying competitive and innovative.
The report also shows that 31% of UK manufacturers say adopting new technologies is their biggest challenge. This not only slows organisational growth but also adds pressure to the workforce. Further complicating matters are issues such as an ageing workforce and immigration restrictions, making it harder to attract and retain young talent.
Manufacturing companies need to take recruitment seriously. By embracing technology, data, and analytics, manufacturing can attract talented and motivated graduates with a passion for cutting-edge experiences. It’s about rebranding the sector and demonstrating the key role of manufacturing in everyone’s lives.
Technology is your ally
As these challenges continue to grow, there is an urgent need for manufacturers to integrate technology into their operations.
It’s about rebranding the sector and demonstrating the key role of manufacturing in everyone’s lives.
Many manufactures have already started shifting their focus from Industry 4.0 to Industry 5.0, driven by AI, robotics, and human-machine collaboration. This evolution is more than digital transformation – it’s about enhancing production outcomes, bridging workforce gaps, and responding to global challenges.
AI can be used to enhance demand prediction and trend forecasting through advanced data analysis, machine learning, and predictive analytics. By analysing both historical and real-time data, AI identifies patterns and correlations, continuously improving its predictive accuracy.
The percentage of survey respondents citing increasing capacity as their top objective for leveraging AI more than doubled from 21% in 2023 to 44% in 2024. Clearly, integrating AI into supply chain optimisation and predictive maintenance ensures efficient and reliable production, helping manufacturers meet demand without unexpected delays.
These technologies will only enhance efficiency and productivity across the sector, positioning manufacturers to navigate future challenges more effectively.
As pressure mounts for manufacturers to meet ESG requirements, streamlining operations becomes a critical part of the solution. AI-driven machine health solutions play a pivotal role in helping companies achieve these sustainability goals by optimising equipment performance and production outputs while also minimising waste.
By leveraging real-time data to monitor and maintain equipment health, manufacturers can reduce energy waste, avoid unnecessary maintenance, and minimise machine breakdowns, which in turn leads to fewer disruptions and reduced resource consumption. For example, whenever manufacturers prevent a machine failure, they also prevent a host of downstream impacts, from safety risks to the maintenance team to supply chain snarls and missed customer shipments. And these impacts extend more broadly, reducing labour time, machine time, and inputs used in our operating machines like energy, water, and gas emissions.
Additionally, businesses can boost operational efficiency by improving machine reliability, extending equipment lifespan, and reducing the need for frequent repairs and replacements. This directly aligns with ESG goals by lowering the overall carbon footprint of manufacturing operations and ensuring more sustainable use of resources across the supply chain.
Striving for success
As manufacturers look toward the future — and specifically toward improving overall production health — those who have yet to embrace IoT connectivity and AI solutions need to do so immediately. Those who have already found success should expand those investments to better visualise and act on the data that connects machines, processes, and operations. This is foundational to the ability to meet production objectives while overcoming what they say are today’s key challenges, such as capacity constraints, supply chain issues, workforce concerns, and equipment reliability and efficiency.
Process improvement is like cycling. Everything runs more efficiently with the right partner.
Energy optimization is the key to sustainable production. As a strong partner for strategic energy management, we help you cope with rising energy costs and tighter environmental targets. We are at your side –uncovering the ways to save and be resourceful while maintaining safety, quality, reliability, and uptime.
rFpro has launched AV elevate™, a fully integrated simulation solution that accelerates the development of autonomous vehicles. It enables the tuning of sensors, the training of perception and control algorithms and testing of the full AV technology stack. It is the industry’s most advanced platform to provide both closed-loop perception testing and the creation of engineering-grade synthetic training data.
To create AV elevate, rFpro has integrated several new technologies to its existing platform including; LiDAR, radar and camera models, a new Simulation Manager to simply define the full vehicle sensor suite and create base test scenarios with thousands of iterations, and compatibility with High Performance Computing (HPC) in the cloud to conduct and scale the testing rapidly.
AV elevate integrates high-fidelity sensor models for all major AV sensor types and enables installation choices and configurations to be tuned and optimised. The platform’s synchronous architecture allows for hundreds of sensors to be tested, enabling sensor fusion testing to a level of accuracy not previously possible.
Included within the simulation solution is a comprehensive library of standard sensor models alongside digital twins of commercially available sensors. This allows development to progress before a physical sensor exists or enables OEMs to benchmark technologies against their competition.
Training perception and control systems with 100% accurate synthetic training data
Typically, AV developers manually annotate each frame of video, LiDAR point or radar return to identify objects in the scene to create training data. This approach generally takes 20
minutes per frame and has a 10% error rate. AV elevate automates this process using engineering-grade synthetic training data, meaning it is 100 times faster and 150 times more cost-effective than manual annotation and is completely error-free.
AV elevate’s Simulation Manager provides a user-friendly way to set up and execute test scenarios simply and automatically. This allows largescale simulations with multiple sensor systems to be created with ease. The Simulation Manager can automate
the environment.
For example, changes to the sensor types, positioning of sensors on the vehicle, traffic, pedestrians, time of day, weather conditions, street furniture and obstructions. It quickly enables the creation of focused variations of the base scenario to be generated, creating hundreds of edge case scenarios for testing. Users can create their own ever-increasing database of scenarios or connect to large external third-party databases.
AV elevate generates and subjects perception and control systems to a massive array of simulated driving scenarios to develop, train and test them. Due to AV elevate’s synchronous architecture, the time to complete tests is directly linked to the available computing power. As the platform is cloud and HPC compatible, it allows users to flexibly and rapidly scale testing as required without
significant investment in internal computing hardware.
At the core of AV elevate is rFpro’s industry-recognised physically modelled virtual environments and ray tracing rendering technology. Its library of more than 180 real-world digital twins provides a highly accurate and diverse virtual proving ground with every element in the scene physically
• Rugged and compact
• Easy to use
• Dust, splash or waterproof
• Data downloaded to PC
• Cost-effective
Accompanying probes are available for monitoring extremes of temperature, and for awkward to reach areas such as pipework.
For sites requiring remote data access, Tinytag Radio and LAN loggers gather data automatically for viewing on a PC, across a LAN, or remotely across the inter net.
modelled with realistic material characteristics and a road surface model accurate to 1mm.
Its ray tracing rendering technology replicates the nuances of how a vehicle’s sensor system perceives the world. The multi-path technique reliably simulates the huge number of light and electromagnetic sources and reflections that happen around a sensor. It generates the highest fidelity data for sensors and includes phenomena such as motion blur and rolling shutter effects.
Transformers are a crucial part of electricity distribution and transmission networks, performing the important conversion steps between the very high voltages at which power is transmitted over long distances to intermediate voltages in local networks.
Achieving this process with minimal losses is a high priority for electricity distribution and transmission network operators, who only earn revenues on the power that is actually supplied to their end users.
Being able to measure power losses accurately to make sure
products comply with specifications is an important part of the process. Each of Royal SMIT’s test bays incorporates a three-phase transformer power-loss measuring system consisting of high-voltage reference capacitors, zero-flux current transformers, and a threephase precision power analyzer supplied by Yokogawa Test and Measurement.
When Royal SMIT decided to build a new test facility, the challenge was to design a stable and reliable environment in which measurement uncertainty forms a negligible component of measured losses. Part of the solution, based on experience with Yokogawa precision power analyzers that have served Royal SMIT well in the past, was to use Yokogawa’s newer WT5000 model.
The WT5000 Transformer Version’s exceptional accuracy of just ±0.008% at a power factor of 1 restricts measurement error to a negligible fraction of total measured losses. It also achieves the highest possible accuracy at power factors as low as 0.001.
One of the features that contributes to the WT5000’s accuracy and long-term stability is a special aging treatment.
First the instrument is optimized by calibration at 53 Hz at power factors of 1, 0.5, 0.05, 0.01 and 0.001. Additional calibration at up to 100 kHz ensures the required performance when measuring distorted waveforms that can be encountered when measuring noload loss currents.
Other features include an intuitive user interface with the ability to define and use event triggers and custom computations. Measurements can be viewed in numeric, waveform, bar, vector or trend formats, while multiple interface options support GPIB, USB and Ethernet communications. Backwards compatibility with communication protocols used by earlier models allows users replacing legacy instruments to continue using existing test software.
The WT5000 Transformer Version has helped Royal SMIT reduce measurement error significantly, with 12-month accuracy improved from ±0.01% to ±0.008%. The linearity of the WT5000 Transformer Version is also superior. The newer product offers one effective input range covering values from 10% to 110%, as well as sampling 50 times faster than the WT3000 and providing resolution that is four times higher.
Calibration certificates from Yokogawa’s ISO 17025 accredited laboratory give Royal SMIT’s engineers the confidence that they can consistently produce traceable low power-factor measurements that comply with the specifications of the IEC 60076-8 and IEEE C57.12.00 standards. According to Steven Lauf, Senior Test Engineer at Royal SMIT, the WT5000 has operated completely trouble free, and the three measurement channels being operated in the test system hardly need to be adjusted at all, even though the instrument can be on for days at a time.
Titan is a leading design and manufacturer of innovative end user and OEM high-performance flow meters, used within a wide range of environments and applications.
• Compact, robust, reliable
• Excellent accuracy and repeatability
• Measure low to high flow ranges
• High chemical resistance
• OEM bespoke design capability
Carbon capture, utilisation and storage, or CCUS, is a field that has sparked a lot of public debate –and investments. Knowing exactly how much and what quality carbon has been captured is essential if CCUS is to become a viable addition to the toolset against climate change. Vaisala’s new MGP241 multigas probe offers always-on data at a third of the cost compared to measurement solutions most used in CCUS processes today.
Vaisala, a global leader in measurement technology, has launched a new measurement product, MGP241, that measures CO₂ and humidity and is specifically designed to bring transparency to CCUS projects. Both governments and private companies need CCUS to reduce and offset carbon emissions if they are to meet their reported decarbonisation targets. However, with current technology still not ready for widespread use, constant, and accurate measurement of captured carbon is vital to ensure its continued development.
The success of CCUS technology is especially critical for hard-to-abate industries like materials manufacturing, energy production, and the chemical industry. With high emissions and few other significant solutions beyond improving their energy efficiency, these industries experience increased pressures from regulators and the public to decarbonise their operations.
One especially crucial industry is the cement industry that alone emits 7% of global CO₂, helping the industry utilise captured carbon dioxide in concrete manufacturing. Through the carbonisation process, Carbonaide’s technology reduces the amount of cement needed in concrete production. While the reduction of cement needed is remarkable, 20–100%, the process also creates a permanent storage for the carbon captured from an emission source.
MPG241 measures carbon dioxide and humidity in point source and direct air carbon capture processes, and in different carbon utilization and storage projects.
Unlike traditional gas analysers, Vaisala’s MGP241 requires no expensive calibration gases, needs dramatically less maintenance, and promises a 10+ year lifespan in heavy-duty use. The compact size and in-situ design of the instrument has allowed for competitive pricing – around a third of the price of most common solutions in the market.
Magnetic switches are used for positioning and control in electric monorail systems and in lift construction, they are characterised by wide-ranging wear resistance and tolerance in the event of misalignment.
A connected control unit uses the signals to determine the position and section of the sensor box and controls the speed and holding positions of the drive motor. In addition, two angle sensors enable fine positioning.
Electric monorail conveyors are used to transport workpieces, tools and other purchased parts in almost every industry. The SSB-R magnet sensor box is used to define route sections for speed regulation for electric monorail conveyors in a manner that is cost efficient and maintenance free. It also allows park positions to be approached with careful accuracy.
SCHMERSAL | Enigma Business Park Malvern, Worcestershire, WR14 1GL
www.schmersal.co.uk
uksupport@schmersal.com
JSW Steel, India’s leading private sector steel company, carbon capture solutions provider Carbon Clean, and leading global resources company, BHP, are collaborating to accelerate deployment of carbon capture technology for steelmaking decarbonisation, following the signing of a joint study agreement between the parties.
Under this agreement, the parties will commence joint studies to explore the feasibility of Carbon Clean’s CycloneCC modular technology to capture up to 100,000 tonnes per year
of CO2 emissions – the largest scale CycloneCC deployment to date in steelmaking.
Carbon capture, utilisation, and storage (CCUS) technology is anticipated to be a critical abatement to support a near zero CO2 emissions intensity for this process route, as well as potentially for other hard-to-abate industrial sectors.
There are several challenges with the adoption of carbon capture technology in the steel industry, including capital expenditure and ongoing operating costs, as well as the integration of new equipment
Bridgnorth Aluminium has kickstarted a £2m investment drive in new technology at its 66acre Midlands site as part of a long-term growth plan targeting new markets.
The company, which employs more than 330 people, has seen sales increase by 33% in 2024 and is currently recruiting for another 10 roles.
The growth is good news for Bridgnorth Aluminium which was negatively impacted in 2023 by rising UK energy prices and the decision of a major customer to move production from Europe to China.
However, directors say the company’s decision to restructure and target new markets in EV
technology and packaging is already proving successful.
Gerhard Trilling, General Manager of Bridgnorth Aluminium, said the 2024 order book was strong.
Bridgnorth Aluminium primarily manufactures aluminium coils for use in lithographic printing plates, pharma and household foils for packaging, and battery foil stocks for electrification.
The new £1.6m investment is in molten metal filtration equipment which is deployed prior to the casting process and will support the company to increase its share of new and growing markets.
The company’s core business remains in lithographic printing for companies across the globe,
into an existing operations site with space limitations. The CycloneCC rotating packed bed (RPB) technology in combination with Carbon Clean’s proprietary APBS-CDRMax solvent aims to address these challenges through reducing total installed cost and the unit footprint by up to 50 percent, and equipment that is ten times smaller in size than conventional carbon capture technologies.
This project is an important step towards supporting the scaleup of carbon capture, including understanding the potential performance, costs, and carbon abatement outcomes.
It is anticipated that these joint studies will be completed during 2026. If the project is successful, JSW Steel intends to liquefy captured CO2 so that it can be sold locally.
Gerald Trilling
with 90% of its products exported outside of the UK. It has a dedicated Research & Development department and production capabilities spanning casting, hot/ cold rolling, heat treatment, slitting, levelling and degreasing.
With a rich history spanning over 90 years, Bridgnorth Aluminium is the only fully integrated UK operation producing flat rolled aluminium coils to global customers.
2024 ESG Report reveals continued progress ahead of 2025 ambitions.
Scottish Leather Group has published its 2024 ESG (Environmental, Social, and Governance) Report, detailing the company’s progress towards its key goal of zero impact leather manufacturing.
The producer of the world’s lowest carbon leather has made significant progress over the last 12 months. Its 21st ESG Report reveals Scottish Leather Group is now 90% on the way to achieving net zero greenhouse gas emissions for its Scope 1 & 2 impacts, with
89% of group waste now recycled or recovered through its own processes towards the 100% target set for 2025.
The group already offers industry-leading traceability and transparency in its raw material supply chain, with 100% traceability, ensuring zero deforestation and compliance with EU legislation which is due to be introduced next year. Around 98% of Scottish Leather Group’s hides come from the UK and Ireland.
Scottish Leather Group continues to have the industry’s lowest Life Cycle Assessment (LCA) impact, with an independently
verified carbon footprint of just 8kg CO2e/m2 on average.
Over the next year, it will continue to pursue innovative operations to achieve its sustainability targets, including the development of an onsite solar PV plant which will directly supply 25% of the operating electricity consumption.
By Robert Schuhmann, Sales Manager Domestic and Commercial Wastewater
Designing new airport terminals is a complex task and involves many engineering disciplines. While the flow of passengers and luggage are obvious areas for optimization, the planning and design of equipment for managing wastewater and rainwater are equally important, even if they are less noticeable. Sulzer has applied its expertise to the new terminal under construction in Frankfurt, Germany, to ensure all the wastewater remains out of sight.
Wastewater presents many challenges for the equipment that must collect and transport it to a treatment plant. These are compounded when the facilities are located in areas of high population density, such as airports, where the additional debris that enters the sewerage system poses a significant threat to the reliable operation of the pumping equipment.
In Frankfurt, a third airport terminal building and apron are under construction and the wastewater system
will have to deal with both wastewater and the rainfall, which must be pumped to the local treatment works. Such a large infrastructure project requires considerable planning and Sulzer was brought in from an early stage to support the design and construction of the system to handle this.
LEFT: The Sanimat tank was customer designed for this application
The new terminal will have a capacity up to 19 million passengers per year and Sulzer’s expertise has helped to develop an efficient and effective solution for collecting and transporting the water for treatment. In all, 10 pumping stations for rainwater and one for wastewater will be installed, ready for passengers in 2026.
Although, the drainage water from the apron shouldn’t cause any issues under normal circumstances, it is kept separate from the wastewater to avoid overloading the downstream station. If some of the water is contaminated by chemicals, such as jet fuel or fire suppressant foam, it can be diverted to the treatment works, rather than joining any stored rainwater.
The waste that enters the system in airports is surprisingly diverse, including cleaning rags, items of clothing and nappies – all of which pose a significant challenge to any pump. Should a pump become blocked, it needs to be removed from service and cleared. In the meantime, the remaining pumps must cover the pumping demand until the blocked pump is returned to service.
Experience from the pumping stations in Terminals 1 and 2 have highlighted concerns with debris in the wastewater flow that can cause pumps to stop working. Sulzer’s suggestion was to add a Muffin Monster inline grinder, which would ensure continuous pump reliability and an extended service life.
With prevention always better than cure, the installation of a grinder upstream of all the pumps can mitigate the downtime caused by debris in the system. Sulzer’s Muffin Monster has proven its worth in many installations, resolving even the most challenging environments and will
LEFT: The Muffin monster inline grinder ensures continuous pump reliability and extended service life.
planning phase, care was also taken to use the same pump types wherever possible.
- Robert Schuhmann
provide the same protection at Terminal 3.
The wastewater will be collected in a Sanimat tank that was custom-designed for this application. The inflow will initially pass through the Muffin Monster grinder to ensure that any wipes or other debris
LEFT: The XFP pumps were mounted horizontally on sliding carriages in order to simplify maintenance.
from the terminal will not interfere with the reliable operation of the pumps. The Sanimat tanks can be specified with tank dimensions to suit the application and ensure that they can be transported through any access or doorways for installation. Applying Sulzer’s design expertise to this project from the outset ensured that the location and capacity of the pumping stations could be optimized for efficiency and reliability.
For structural reasons, it was not possible to realize gravity drainage of the rainwater from the piers and the apron. For this reason, a total of 10 pumping stations of various designs were planned for rainwater and one for wastewater.
The planned and constructed sewerage network on the site of the new Terminal 3 was not designed to absorb the rainwater produced. Through careful planning and prioritization of the pumping stations, the rainwater is disposed of via the sewer network to avoid flooding of the apron.
During the planning phase, care was also taken to use the same pump types wherever possible. This makes it possible to interchange the pumps in the pumping stations in the event of an emergency. This mainly affected the two largest pumping stations, which are responsible for the disposal of approximately 662 l/s. Instead of two large pumps of type XFP501U-SK350, three pumps of type XFP351M-CH350 were planned and installed, making them identical to the pumps in another building.
By Mark Garrett, Europe and Africa EHS & Quality Director, Air Products
Our ethos is to encourage people to be proactive, and report near misses without fear or hesitation. And this has been a major factor in our progress towards zero accidents.
Maintaining a robust and effective health and safety programme in the manufacturing sector is a necessity, not an option. But keeping workers safe in a high stakes environment goes beyond compliance with industry regulations. A positive, empowering culture around health and safety not only keeps people safe but also helps boost productivity, strengthen business reputation and deliver better commercial results.
Although good for business, operationally, this is a complex task. At Air Products, safety is one of our core values and we’ve set ourselves the goal of becoming the world’s safest industrial gas supplier. However, with nearly 20,000 staff distributed across the world, addressing the diverse health and
safety practices and regulations across each of our operations has historically been challenging.
Our approach has been to embed a customised and standardised global environment health and safety management (EHS) system across all regions. Based on the Occupational Safety and Health Administration (OSHA) rulings from the US and centred around the three Es: evaluation, education and enforcement, it was rolled out in the 1990s and 2000s.
We found that while Europe and North America were relatively mature in terms of health and safety standards, regions such as Asia and Africa were a series of phases behind where we were as a company. The priority for us was to urgently bring all areas to the same baseline.
In our experience, the best way to achieve any large-scale positive change requires a two-pronged process. While the directive for higher safety standards came from the top corporate echelons, it’s been critical to get the buy in of our employees, from plant engineers and managers to technicians, contractors and fleet drivers.
Our health and safety results as they stand now are impressive. At the end of fiscal 2023, Air Products’ lost time injury (LTI) rate was 0.9, boasting a 63% reduction from 2014. This was in addition to 0.29 for recordable accidents, a 50% improvement in the same 10-year period.
There’s no time to rest on our laurels, however – every new plant has to be brought to the same standards and the challenges vary with the geography. For instance, in 2023, we went into a
partnership worth $1bn with the Uzbek state gas company to own and operate some of their gas manufacturing units. These assets came with more than 150 local employees many of whom had joined as young engineers when the plant first started. While there was no doubting their technical expertise, there was work to be done in strengthening their health and safety culture.
Implementing our standard safety measures alone was only half the job done. It was equally important to help the employees see how these measures would enhance their working practice and lower risk – and encourage them to help us in putting safety first.
In some cultures, it’s not acceptable to make a mistake and as a result people only report accidents. Our ethos is to encourage people to be proactive, and report near misses without fear or hesitation. And this has been a major
factor in our progress towards zero accidents.
Promoting this culture of shared responsibility for everyone’s safety ensures that when an issue or risk is found, it can be addressed immediately. At another recent acquisition, after we implemented the EHS management system and had the employees fully on board, we recorded zero LTIs within the first six months, and only one minor incident involving first aid in the whole two years since we acquired the company.
It’s far from easy but achieving zero accidents is possible. Once employees see for themselves that there are fewer mishaps and accidents when the proper protocol is followed, it motivates them even further to take ownership of the safety standards, and the positive cycle continues.
By Darrell Taylor, Strategic Marketing Director and Product Manager for FLIR Teledyne
The other day I performed a Google search for ‘How to detect an air leak’. Whether solving the problem in a commercial establishment or a domestic home environment, most search results pointed to one solution, soapy water!
Before we all ridicule the idea as belonging to a bygone era, take a vehicle with a slow puncture to a tyre fitting depot and the chances are they remove the wheel and spin it in water to determine the leak. It’s a simple time proven method for determining leaks from pressurised systems.
But of course, not all equipment can be placed in soapy water. What if a system is known to be losing pressure and yet the lines carrying the compressed air from the source are located 10 metres above the ground, and dismantling the system is out of the question? Thankfully there is a fast and effective solution to hand.
Each time air or indeed any gas, leaks from a pressured system there is an associated sound. If the leak is significant, it can be audible to the human ear and therefore easily identified and rectified accordingly.
However, most leaks in high pressure systems are extremely small and out of our hearing range.
Think about a pressured air system on a large factory delivering compressed air from a bank of compressors to various stages of production throughout the manufacturing process. The chances are there are hundreds if not thousands of connections in the form of joints, reducers, valves, elbows, condensers etc. Each of these has the potential to leak small amounts of air, reducing the pressure of the system.
One leak might make very little difference but multiply this by the number of potential leaking joints and efficiency can be significantly compromised. The compressor will seek to compensate for any pressure loss by simply working harder. However, compressors can be expensive to operate in terms of energy and therefore will increase an operator’s energy consumption; identifying these small leaks can make a real difference to a company’s energy bills.
Although the sound produced by a small leak is inaudible to the human ear, a high-performance acoustic imaging camera such as the FLIR Teledyne Si2 – LD will have absolutely no problem identifying the source.
For closer work the camera is more sensitive and detects minute
leaks of 0.0032 litres per minute at a distance of 2.5 metres. Coupled with this improvement, the thirdgeneration camera has improved microphones now capable of detecting sounds over an extremely wide frequency range, namely 2 –130 kHz.
The FLIR Si2-LD has built in software termed Industrial Gas Quantification. If the leaking gas is ammonia, hydrogen, helium, or carbon dioxide, very commonly used gases in a number of industries; the software is capable of quantifying the financial loss caused by the leak. By simply entering factors such as the cost per litre, the software identifies the amount each leak is causing over a given period of time. Such data is invaluable to financial analysts and senior management within an organisation.
It goes without saying that the financial considerations are only one aspect of leaking gas. The gases mentioned above all carry significant health hazards and can present a variety of dangers to personnel if allowed to leak for any period of time. Clearly the cost of such problems goes way beyond any financial considerations. We’ve come a long way since the ‘soap and water’ approach.
See how the latest technology from FLIR Teledyne can help your organisation.
Valves for Hydrogen, Carbon Capture, Topside, Subsea, and Pipeline Applications.
Instrument & DBB Valves
• Manifolds, Needle, Check and DBB Valves to 22.5K psi
• Cryogenic
• Severe Service 650ºC, 10K psi
• Forged & Bolted Construction
Hydrogen & Carbon Capture Valves
• Instrumentation, Ball, Needle and DBB Valves for Hydrogen and Carbon Capture Applications
• Pipeline Ball Valves upto 18”
Pipeline Valves
• 1” to 20” Bore Size
• High Temperature
• High Pressure
• Cryogenic
• API 10K Design
• 10K Ball Valves for Hydrogen Fuelling Stations
Subsea Valves
• Diver & ROV Operated Needle Valves
• Ball Valves Upto 15K
• Manual & Hydraulic Parallel Slide Gate Valves 3/8”, 1/2”, 3/4” and 1”
Donna Edwards, Director of Made Smarter’s Northwest Adoption Programme, discusses how the initiative supports manufacturers in overcoming challenges to adopt new technologies. Sharing insights on the impact of AI and IoT on productivity and sustainability, Donna emphasises the importance of digital transformation in future-proofing the UK manufacturing sector.
Made Smarter’s North West Adoption Programme is recognized for helping manufacturers overcome barriers to technology adoption. What is the most common challenge manufacturer’s face when adopting new technologies?
The key obstacles to digital transformation for manufacturers are a lack of time, knowledge, capital and a fear of failure.
The Made Smarter approach has been designed to overcome these with access to support that is quick, simple and high impact. We have created a set of short, focussed interventions to help time-poor SME leaders.
This includes help creating a digital strategy, skills and leadership advice/ programmes, as well as grants of up to £20,000 towards technology projects.
How do you see digital technologies, like AI and IoT, reshaping the future of manufacturing in the North West?
We’re on the cusp of a new era in manufacturing, where human expertise and AI capabilities work in harmony. Our goal is to ensure that SME manufacturers are at the forefront of this opportunity. However, for most the current focus is on data and systems integration, and getting that infrastructure in place to be able to deploy machine learning algorithms
in the future, to make decisions based on the data rather than assumptions.
Sensors and the Industrial Internet of Things (IIoT) technologies can be deployed to connect machines across a factory shop floor, or even multiple locations, generating vast amounts of useful industrial data in real time. Even legacy tools and machinery could be connected, and their data harnessed for insights.
Having created a digital thread, data analytics and AI can bring benefits such as identifying methods to simplify manufacturing processes, predictive maintenance or projection of market demand.
Could you share some success stories where manufacturers, with support from Made Smarter, have significantly improved efficiency or scaled their operations? What role did technology play in these transformations?
In the last five years we have funded 379 technology projects valued at £25.2M including £7.12M of grants and £18M of private sector investment.
JJ Smith & Co. (Woodworking Machinery) Ltd, an OEM based in Liverpool, adopted a Nordbo Mimic Robot with FT Tracker software to accelerate its development of automation solutions aimed at simplifying manufacturing processes to the woodworking sector.
The technology simplifies what can be a very complex and consuming process.
Tests on sanding applications reduce programming time from up to two weeks for more complex tasks, down to minutes, significantly cutting down the time it takes to develop solutions. This increases the capacity for product development, boosts overall productivity and enables JJ Smith to increase the complexity of its products for more niche markets, increasing sales further.
For smaller manufacturers hesitant about the investment in digital tools, what advice do you give them regarding the ROI of adopting smart manufacturing solutions?
It is okay to be hesitant. Change is difficult. But to stand still is to fall behind. Digital transformation is a necessity to remain competitive, relevant and future proof. One way to think about it is to consider it as a journey, with milestones and many different paths which lead to the same destination. However, even within a single company or industry, this journey can mean very different things. It will depend upon the starting point, the challenges and opportunities being addressed, the budget, the leadership, and the skills available.
The key to success is breaking down the digital journey into quick iterative steps and creating a roadmap of how to get there. Made Smarter’s digital transformation workshops are designed to identify the digital tools and technologies that can be implemented to maximise operational processes and enhance business growth.
It is also important to understand that technology is just a tool. Made Smarter takes a people-first approach to helping SME manufacturers develop manufacturing leaders who are able to foster a digital culture within their organisation which empowers employees to embrace change and encourages innovation, collaboration and learning.
With global disruptions and challenges in supply chains, what strategies are manufacturers in the North West adopting to stay resilient, and how is Made Smarter helping them to adapt?
Technology has enabled some companies to bring processes inhouse, securing control over their scheduling, increasing reliability and quality of the products, and having a
It is okay to be hesitant. Change is difficult. But to stand still is to fall behind.
positive impact on their foot carbon footprint.
A good example is Tibard, based in Dukinfield, a manufacturer of uniforms. Its investment in automation and data and systems integration helped the business navigate the recent supply chain challenges and pivot to diversify its product range.
Given your experience, what do you believe are the key factors that will determine the success or failure of the UK’s manufacturing sector over the next decade?
Decarbonisation is the industry’s biggest challenge - but also a significant opportunity.
To meet the UK’s net zero target by 2050, industrial emissions have to be reduced by at least 90%, the equivalent of removing every car from our roads immediately. To make things greener, we need to make things smarter. This is where digital technologies will be key to the netzero transition.
For the climate emergency, digitalisation offers manufacturers a huge opportunity to deliver operational efficiencies, decarbonise heat and power, optimise design and materials, and improve logistics and transport, benefitting their business, their bottom line and the environment. Then there is the reputational gain which helps secure customer loyalty, as well as attract new talent and investment.
Made Smarter is committed to help SME makers get there with vision, technology, leadership and collaboration.
How do you think the manufacturing industry can better collaborate with the public sector, academia, and tech providers to drive innovation and ensure sustainable growth?
The Made Smarter Adoption Programme is a key part of the Made Smarter movement, which is focussed on greater innovation in developing new technologies, faster implementation and adoption, and deeper understanding of the sector’s skills and leadership needs.
Made Smarter works closely with a wide-ranging network of industry, government and academia partners supporting SME manufacturers to pursue positive change. Over the last five years Made Smarter has created countless connections and a formidable ecosystem. To build on that, we need to continue to create spaces where SMEs, larger
companies and technology innovators can collaborate to solve our most pressing challenges. We must also keep up the good work of engaging SMEs in the adoption programme in the North West, North East, Yorkshire and Midlands, and as part of a national roll out. Over the next few years more companies across the UK will have access to that support to become a real national support service.
Sustainability is increasingly becoming a priority for manufacturers. How is the Made Smarter programme helping businesses in the North West adopt more sustainable practices alongside technological innovation?
The pressure and scrutiny on the sector to be more sustainable is ramping up and coming from all directions including employees, customers, the government, investors, regulators, and the communities in which manufacturers operate.
Made Smarter is supporting manufacturers to embrace new technologies to deliver operational efficiencies, decarbonise heat and power, optimise design and materials, and improve logistics and transport, benefitting their business, their bottom line and the environment.
Combining Miniaturization and High Performance to Drive Further Evolution in Electronic Devices.
Alps Alpine announces the launch of the world’s smallest* class surface-mount type TACT
Switch™, the “SKUB Series.” At just 2.4mm×1.4mm×0.55mm (W×D H), this switch achieves a smaller size than previous models, while maintaining the same tactile feel and durability.
The SKUB series has an actuating force of 1.6N and a switching travel of 0.11mm.
The initial contact resistance is 500mΩ. The IP68-protected component has a long service life of 500,000 switching cycles. It is designed for switching currents of 50mA at a maximum of 12VDC. Mass production began in September 2024.
To meet growing demand for miniaturisation and higher performance, electronic components on circuit boards are increasingly densely packed, making it essential to reduce the size of each component.
This switch supports further advancements in the electronic devices in which it is installed, expanding the possibilities of nextgeneration electronics.
Crane Garden Buildings, a UK leader in the manufacture and supply of premium garden buildings, has installed a state-of-the-art robotic spray paint line at its headquarters in Narford, Norfolk.
After planning this for a number of years, the multi-million pound conveyor line was publicly revealed for the first time at an onsite event to celebrate the familyrun company’s 50th anniversary. It is the largest investment the company has ever made.
Now fully operational, the investment is expected to be fundamental to the business’ plans to grow by 10% yearon-year over the forthcoming decade.
The new line is a power-andfree overhead conveyor that
moves the company’s buildings through the factory, removing approximately half a million manual lifts a year. Once on the conveyor, the building panels pass through the robotic paint line and then into a drying system, which ensures the paint is applied and dried under consistent ideal conditions.
As well as significantly improved health and safety for the company’s factory team, it will offer greater consistency and precision.
Crane Garden Buildings has also confirmed that no jobs will be impacted by the installation of the overhead conveyor. Instead, it will require a new skillset with its factory operatives moving from manual labour-centric roles to software management.
MORE THAN 20.000 MOTORS AVAILABLE FROM STOCK!
Motors up to 25 MW and 13.8 kV
• Low voltage slip-ring and squirrel cage motors up to 3,000 kW
• Medium voltage slip-ring and squirrel cage motors up to 15,000 kW
• Direct current motors up to 2,000 kW
• Frequency converter-proof drives
• In-house load test facility up to 13.800 V, 2.300 kVA, 120 Hz
Customized special designs
• Custom designs for special applications and operating conditions
• Optimized motor design for higher efficiency
• Mechanically and electrically interchangeable motors
• Commissioning worldwide
MENZEL Great Britain Ltd. | UK Branch Office
27 Hunt Drive | Melton Mowbray | Leicestershire LE13 1PB
Martin Rooney | Tel.: +44 1664 500 844 | Mobil: +44 7957 618046 martin.rooney@menzelgb.co.uk NEW ELECTRIC MOTOR PLANT FROM JANUARY 2024
MENZEL Elektromotoren GmbH
German Headquarters
Am Alten Walzwerk 2 | 16761 Hennigsdorf | Germany
menzel-motors.com info@menzel-motors.com
24,000 m 2
Rushlift, the national full-service provider of materials handling equipment (MHE), has opened a Centre of Excellence for training forklift truck maintenance engineers and drivers at its Northampton HQ.
As an Association of Industrial Truck Trainers (AITT) accredited training provider, Rushlift is now able to provide technical training courses and operator training for employees, apprentices, customers and businesses nationwide.
The new facilities include a spacious training room that can comfortably accommodate up to 16 trainees. A large screen TV is used to display presentations, with computer tablets available to access technical information. The practical workshop area is well appointed for technical training offering tooling, benches and diagnostic equipment for hands-on training. The area is also used for operator training, allowing trainees to practice driving
manoeuvres, such as stacking and de-stacking using the dedicated racking.
Investment in people is the focus of the initiative. Bringing training in-house, Rushlift’s Centre of Excellence delivers induction training to new engineers joining the company and ensures that the company’s 150 field service engineers and apprentices are fully up-to-date on new truck models, technical developments and bestpractice maintenance procedures.
Operator training is another key activity, where AITT accreditation allows Rushlift to further develop the in-house skills of employees and offer fully certified forklift driver training courses to businesses nationwide, undertaken either at Rushlift’s Centre of Excellence in Northampton or at customer premises across the UK.
A core element of the investment is the training team itself. Along with
Funded training courses are being offered to Chesterfield’s manufacturing and engineering sector to support recruitment and growth.
A new initiative - known as Manufacturing Futures - will teach mentoring skills to businesspeople from the sector to help firms engage with young talent. This programme will empower companies to offer more work experience opportunities, confidently take on apprentices and interns, and provide career advice to young people.
The concept emerged at a Manufacturing and Engineering Forum organised by Destination Chesterfield which identified recruitment challenges in the sector. Recent data indicates that 66% of businesses attempting to recruit in the past three months have struggled to find suitable candidates.
With manufacturing comprising 8% of Chesterfield’s workforce — nearly double the national average — it’s crucial to inspire and equip the next generation with the skills needed to drive local manufacturing forward.
Manufacturing Futures was launched alongside the tenth edition of Made In Chesterfield, an annual festival supported by The Chesterfield College Group offering tours of local manufacturing, engineering, and construction businesses to school pupils, showcasing the diverse career
Steve Briscall’s appointment to the role of National Training Manager in 2023, Sam Cook recently joined the team as Technical Training Manager bringing to the business 37 years of experience as a research and development technician, workshop supervisor, apprentice development officer and technical trainer. Both managers have extensive experience in training and engineering having worked for one of the industry’s largest FLT manufacturers.
opportunities available in the sector. The programme is funded through the UK Shared Prosperity Fund and is one of several skills programmes to receive funding which will help ensure local residents can advance their career and that the local economy can grow.
To get your business involved in Manufacturing Futures, go to https://www.chesterfield.ac.uk/ manufacturing-futures/ for more information.
Businesses can also stay up-todate with the latest opportunities to engage with young people by signing up to Destination Chesterfield’s skills and employability newsletter.
The government’s new plans to restrict levy funding of level 7 apprenticeships will widen the skills gap, hinder the economy and have a significant financial impact on manufacturing firms needing to develop future managers, business leaders or fill specialist roles.
The warning comes from the University Vocational Awards Council (UVAC) which has produced a new national report in partnership with Sheffield Hallam University to explore the critical purpose of training apprentices of all ages to deliver jobs of the future.
The report also explores the importance of older apprentices to employers in a shifting labour market and the impact higher and degree apprenticeships, such as those at level 7, have on firms from a growth, employee retention, skills and productivity perspective.
Findings from the National Foundation of Educational Research reveal that 90% of roles within firms across sectors such as manufacturing will require higherlevel skills by 2035, highlighting how the wider economy and more employers than ever will be dependent on degree apprenticeships at levels 6 and 7, rather than just those at lower levels.
The ‘Apprenticeships – a system built for adults’ report is now freely available to view online at www.uvac.ac.uk.
With the looming 2030 deadline for achieving a 45% reduction in global emissions, hard-to-abate industries are facing increasing pressure to decarbonise. However, more than 50% of industrial emitters lack the space required to deploy conventional carbon capture plants.
Carbon Clean, a leader in revolutionising carbon capture solutions, announced the launch of its breakthrough CycloneCC C1 series, marking the penultimate stage in the technology’s commercialisation. The CycloneCC C1 series is available in concentrations ranging from 3% to 20%, capturing up to 100,000 tonnes of CO2 per year. CycloneCC C1 uses first-of-a-kind (FOAK) technology to reduce the total installed cost of carbon capture by up to 50% compared to conventional solutions.
At the heart of CycloneCC C1
is the breakthrough combination of two process intensification technologies: rotating packed beds (RPBs) and Carbon Clean’s proprietary APBS-CDRMax solvent. The FOAK technology application of RPBs to a carbon capture plant is a gamechanger for the sector. Using RPBs to replace the columns used in conventional carbon capture solutions both reduces the size of the plant and accelerates the mass transfer process, increasing CO2 absorption.
Carbon Clean’s high-performing APBS-CDRMax solvent achieves substantial OpEx savings through outperforming the industry standard
Fieldcode GmbH, a leading cloud-based web application for managing field service operations, is thrilled to announce its collaboration with Green-AI Hub for an innovative AI pilot project aimed at optimizing ticket diagnostics in field service management.
This joint project leverages Large Language Models (LLMs)
to enhance decision-making in ticket analysis and reduce climatedamaging outcomes. The project focuses on implementing an LLMbased solution that uses historical ticket data and freely available technical documentation to analyse service tickets.
The system provides automatic recommendations, enabling companies to determine whether
solvent. APBS-CDRMax lowers energy demand by 10-25%, reduces corrosion by a factor of 20, decreases degradation by a factor of 10, and has a lifespan that is five times longer than conventional solvents.
First-mover customers of the CycloneCC C1 series will have the opportunity to influence the development of the fully commercialised product while experiencing the benefits of tangible decarbonisation results. Early adopters will also be priority customers for the fully commercialised product when it is rolled out at scale.
www.carbonclean.com
an issue can be resolved remotely or if a field service visit with specific spare parts is required. This approach is designed to improve remote problem resolution and increase the first-time fix rate, reducing unnecessary site visits and saving valuable resources.
The pilot project is already in progress, with more updates to follow as implementation advances.
Hart Door Systems, the original British manufacturer of the high-speed door concept, is confident of another successful year for its Speedor and Typhoon brands.
“Despite global uncertainties I believe our leading Speedor and Typhoon brands will continue to be in demand,” says Doug Hart, Hart’s chairman. “We have had many successes at home and abroad during 2024 not just through our Speedor range of high-speed doors but through our range of high quality Typhoon shutters too. Both these leading brands offer a choice of solutions for industry and commerce.“
The Speedor high speed door is a good example of an engineered door system for frequent use in high-traffic situations. This rapid roll door is robust, requires low maintenance and delivers exceptional wind resistance in exposed areas. Its high-speed opening and closing action improve efficiency, the energy-saving potential of this rapid roll door is high, controlling internal temperatures, escaping dirt, odours and noise.
Special features include; moisture-controlled electrics, mechanical components shielded from dust and dirt, and a unique guide system offering exceptional wind resistance up to class 5 as defined by DIN EN 12424.
There are several options with the Speedor brand namely ECO, Storm, Mini, Conveyor and Cleanroom which together strengthen Hart’s overall high-speed door offer.
Speedor Storm is Hart’s bestselling door, ideal for challenging applications where reliability is essential. Its increasing success is based on its improved, rugged, design predominately for external use up to 8m x 6m/6m x 8m) often in robust operating conditions with high wind loads.
Quality is Hart’s prime driver not just in high-speed doors but shutters such as the Typhoon range. The fundamentals are quality throughout manufacture to installation and service to comply with changing national and international safety standards.
www.hartdoors.com Hart sees 2025 as another year of opportunity
British design and manufacture, wide range of models covering high security, large doors with high wind resistance (3,000 to 5,000 pascals), fire and high speed automation with systems’ interface. One stop door shop for
Globally recognised Hart’s high speed doors and shutters deliver
By Ross Turnbull, Director of Business Development and Product Engineering at ASIC design and supply company Swindon
The industrial robotics sector continues to experience strong growth, with operational stock at approximately four million robots according to statistics from the International Federation of Robotics. Improvements in robotic grippers have helped accelerate industrial robot uptake, but is there room for further development?
Here, Ross Turnbull, Director of Business Development and Product Engineering at ASIC design and supply company Swindon Silicon Systems, explores.
Whether it’s moving large, heavy goods from point A to point B or assembling something small and fragile, industrial robots can be useful for a wide range of tasks. To give them the ability to hold and manipulate objects on their own, many robots will feature one or more grippers. But it isn’t as simple as directing the gripper to just open or close. These robots must be able to work with objects of all shapes and sizes and materials of different hardnesses — and adapt accordingly.
This can be a challenge. The gripper needs to be able to sense the object to pick it up quickly and accurately, holding it securely to prevent it from being dropped. But it cannot close too tightly, as this could impair the gripper jaws themselves or damage fragile products. It’s also important to consider the electronics assembly. Thin connector wires in small electronic components can be easily bent and damaged through poor handling. It’s these kinds of problems that gripper manufacturers are keen to avoid.
To prevent damage while ensuring proper operation, robotic grippers need to have at least one sensor. It’s imperative that these sensors have
both accuracy and precision to move, hold and assemble objects efficiently. So, how can we build sensors capable of this?
For the gripper to be able to move accurately, it needs to know its exact position to the same level of precision. This is where position sensors come into play.
There are a couple of different types available: inductive and optical. Inductive position sensors rely on electromagnetic induction for non-contact detection of metallic objects. Conductive targets cause disturbances in the magnetic field, which can then be detected by the sensing element. Optical position sensors, in contrast, make use of an LED and photodetector, with an optical scale to measure linear displacement at very high accuracy.
Force or torque sensors are another important sensor type. While humans can naturally feel forces — for example, when pushing two objects together — a robot lacks this sensation. Integration of a torque sensor can help give robots ‘feeling’. These typically make use of strain gauges, which convert pressure into a measurable electrical signal. Multiple gauges can be combined to determine not only the intensity but also the direction of the force. The result is a robot that can handle even fragile materials or precisely tighten a screw without going too far to cause damage to the product.
The last key type for discussion here is the proximity sensor. These are particularly helpful to check the angle of the jaw grippers for accurate movement, and can even provide part verification while the part is still inside the gripper.
Proximity sensors for this application are commonly inductive. Using the principles of electromagnetism and Eddy currents, the sensors can detect the metal of the jaws themselves or a metal target attached to the jaws.
Whether systems contain just one of these sensor types or a combination, they’ll still have something in common: at least one or more ICs. The aforementioned sensor types will typically produce an analogue signal output. For this signal to be interpreted by the rest of the robot or industrial control system, it must first be digitised.
The necessary processes of signal amplification, processing and digitisation may be performed by a standard off-the-shelf IC. But for manufacturers looking to set their sensor apart from the rest, there’s a better solution available.
This takes the shape of an Application Specific IC, or ASIC. This is a
For the gripper to be able to move accurately, it needs to know its exact position to the same level of precision. This is where position sensors come into play.
completely bespoke chip that has been designed uniquely to fit the specific demands of the application — in this case, a robotic gripper.
The result of bespoke design means the IC can be fully optimised for superior performance. An ASIC designer will work closely with the manufacturer to discuss the current sensor system and identify the best areas for improvement for maximum
benefit. For example, sensor-specific processing functions can be included to improve signal quality and minimise noise to ensure the accuracy of data and therefore movement of the robot. Industrial grippers working with extremely small components such as printed circuit board assemblies will benefit from the enhanced precision offered by an ASIC.
Speed can also be improved for reduced latency and real-time decision-making. This is particularly important for robots working in a collaborative environment with humans, who may need to make quick decisions to avoid collisions or other accidents when working in a nonpredictable environment.
Products are growing in complexity while shrinking in size, making their manufacture more and more challenging. But levelling up plant machinery can help. Custom ICs can help alleviate manufacturer concerns around precision and reliability of their industrial robots, providing the dexterity and capabilities required for modern manufacturing.
To
Gerard Bush, engineer at motion specialist INMOCO, discusses motion system specification for gantry-based applications.
Involving the management of a mechanism that moves along X, Y, and Z axes, a gantry can be used to navigate a tool or platform through three-dimensional space with a high degree of precision. Whether controlling a pipette on a liquid handling system, or a suction cup on a pick-and-place application, these machines rely on a gantry.
Operating to pre-programmed profiles, the gantry relies on a motion controller to coordinate three axes of travel. Each axis typically involves a motor with a sensor for position feedback, controlled locally by a drive.
Another important technique is acceleration feedforward.
Motor control technology selection is highly dependent on the torque and control precision required by the application. For larger machine applications, AC servo motors are frequently used, with rotary motion converted into linear motion with belts, pulleys, or lead screws.
For smaller machines, typically requiring up to around 500W, brushless DC (BLDC) motors are increasingly integrated to optimise control precision, and linear BLDC designs can also be used. This technology also enables high-speed operation, required, for example, to maximise throughput on a pickand-place application, rapidly accelerating and decelerating without losing position.
Also, for smaller scale applications, stepper motors are an alternative, ensuring repeatable accuracy by providing discrete ‘steps’ of motion. Traditional DC motors could also be integrated if cost is critical.
For applications where precision is vital, such as laser cutting or 3D printing machines, the control system must support smooth and accurate motion. Crucial to achieving this are the motion profiles of each axis, including the acceleration and deceleration ramps, commanded by the drives.
A typical requirement for gantry control is S-curve profiling, which adds stability as well as reducing mechanical stress. Shaped like the letter of its namesake, usually with seven individual segments of speed profile, the S-curve achieves smooth acceleration and deceleration.
The initial motion phase includes gradual acceleration to a set rate, where it then maintains a constant speed, before gradually decelerating. These controlled changes in speed reduces jerks, oscillations, and sudden stops, which enhances the smoothness of motion.
Another important technique is acceleration feedforward. Inertia can cause delays or position errors if left unmanaged, resulting in oscillations or overshoot, impacting accuracy and smoothness of motion. Acceleration feedforward mitigates these challenges by improving the system’s response.
To achieve this, the drive sends an additional command to the motor based on the expected acceleration, and this input enables the motor to achieve the desired acceleration from the outset. As a result, this technique reduces lag and ensures that the end effector reaches the target position accurately and smoothly.
Motion error detection is also important to ensure accuracy by identifying, in real time, unwanted deviations in the motion path or profile, and enabling corrective action. Vibration, for example, is a common challenge, which could cause motion path deviation sufficient to impact the precision. Combined with a feedback device that monitors deviation, a suitably intelligent drive can correct the error.
When specifying a gantry control system, wider considerations are also required, such as needs in reliability, addressing thermal management and the demands placed on the system. Fundamental considerations on design integration, such as power supply, form factor, and installation, are also important, particularly for machines that require embedded electronics.
As a result of the complexity faced when developing a 3D gantry system, it’s often useful to engage with a specialist, like INMOCO. Dedicated motion engineers can specify the most suitable system for the particular requirements, and partner with motion vendors like Performance Motion Devices that offers a range of motion control chips and boards, as well as digital drives and modules for embedded designs. Engaging early with a motion specialist not only saves time in development, but ultimately helps to optimise the performance of the application.
Pictured below: In machine automation, gantry control is required across a range of applications, from 3D printing to CNC machining
Lincoln-based manufacturing firm Micrometric is continuing to lead the way in laser manufacturing and multiprocess services.
The company, which was established over 40 years ago, produces fine parts and precision components for a range of customers in the UK and international markets. It specialises in a range of services including cutting, etching, drilling, and welding as well as tube cutting and precision component machining.
Commercial Director Chris Waters said: “Lasers are at the heart of everything we do, and we have the relevant capabilities and laser equipment to cut, assemble and weld complex manufacturing medical devices including small tubes, injection needles, and endoscopes and intricate parts required for surgical equipment.
“We have built up a reputation for our personal approach with customers as we want to fully understand our customers’ laser cutting requirements. We’re committed to providing exceptional, customised services that help our customers achieve their goals faster and with greater precision.”
Chris added: “Our laser machines are suited to cutting materials with a wide
range of thicknesses and can cut a range of materials including metal, plastics, and ceramics. We offer micro laser cutting capabilities that allow small parts to be cut to tight tolerances down to +/-0.02mm (material and thickness dependent) across a variety of materials including stainless steel, titanium, copper, brass, and ceramic.
“We are AS9100 qualified and can supply process sheets, certification, first article inspection reports or similar inspection regimes to clients, as required.
“We use several CO2 and state-of-theart fibre laser cutting systems which precisely cut materials with minimal heat and excellent edge quality to produce components quickly, efficiently, and cost-effectively.”
Since investing in this equipment, Micrometric’s skilled workforce has used the machines to cut, assemble and weld complex medical and aerospace components for companies which produce aerospace filters, automated injection needles, endoscopy components and MRI scanning equipment as well as producing finer, precise parts for other sectors.
Micrometric is equipped with a range of lasers and its experts can weld a wide range of parts to deliver high-quality solutions.
Chris added: “Laser welding offers the benefit of welding while minimising heat input which is critical when welding components with temperature-sensitive items inside them or minimising any distortion due to heat.
LEFT: Laser welding
BELOW: Laser cutting examples
ABOVE: Chris Waters is Commercial Director
“We can also weld autogenously or with wire feed. Depending on the metallurgy of the parts, it is possible to add different alloys as wire to adjust the weldability of the component. The wire feed can be fully automated within the welding machine. For some welds, such as titanium, an inert atmosphere is required, and an enclosed argon welding system is used.”
Micrometric offers a range of in-house and resourced services to complement its laser machining services and has dedicated equipment for laser drilling, cutting, etching and welding applications. Its extensive work of subcontracting means that it’s able to offer a single point of contact for manufacturing parts from the initial process through to completion, helping to reduce lead times and production costs.
Micrometric is a member of the Midlands Aerospace Alliance (MAA), The Manufacturers’ Organisation (MAKE UK), Association of Industrial Laser Users (AILU), and Motorsport Industry Association (MIA).
To find out more about Micrometric and its services, visit micrometric.co.uk or contact the sales office on 01522 509999.
A high-flyer at a precision manufacturing company Titan has been made a Company Director a decade on from starting out as a 22-year-old trainee on the shop floor.
Ryan Hanger has had a meteoric rise at Titan Manufacturing in Weymouth, Dorset, which specialises in sheet metal fabrication, CNC machining, laser cutting and surface finishing. He started out in March 2015, fresh
from completing his NVQ Level 3 apprenticeship in engineering services, as a trainee doing basic duties on the workshop floor, before progressing to laser operator two years later.
When the position opened up, he stepped up to become laser manager – taking on responsibility for running the workshop - a role in which he was able to implement process improvements which saw a 15% increase in production output. The past year, his career has been turbo charged; Ryan was made Business Manager in June, working on driving efficiency and costeffectiveness and implementing structural improvements within the company.
Just months later in October, he was promoted to company director taking the lead on running day-to-day operations, business development, building relationships strategic and generating new leads, as well as rolling outgrowth and improvement initiatives – such as a material resource planning system called Tricorn, which streamlines the production process from start to finish.
Ryan stated, “It has been an incredible journey at Titan. I’m not sure I imagined myself becoming a company director when I started out a decade ago, but with the support and opportunities I’ve been given here, I’ve grown into that responsibility. I have loved the process of continual learning and improvement, and that is something I will continue to do in my new role. I am keen to put all I’ve learned to good use, drawing on my own experiences to help others in the Titan team to grow and develop in their careers, through that, safeguarding the future of the company.”
Ryan is taking the helm during a period of intensive growth for Titan, which secured significant private investment last year. The company opened a second £1.8m purpose-built
production workshop this summer, bringing their total factory premises up to 30,000 sq ft.
“This is an incredibly exciting time for Titan, as we continue to push ahead with our plans to grow this business, with an ambition of doubling turnover within two years.
“Being born and bred in Weymouth, I am also passionate about being able to serve our local community. We have plans for a charity partnership in the pipeline, and I’m also looking to strengthen our connection with local education providers and develop our training pathways.
“As my story testifies, Titan is a company where you can carve out a fantastic career, and I want to give other people looking for opportunities all that they need to succeed.
“Attracting and retaining young people and equipping them with the right skills is vital, not only for the future of Titan, but for the future of the manufacturing sector as a whole.”
New logistics hub and CNC manufacturing facility to strengthen supply chain solutions.
Expromet Technologies Group is opening a new base within the Philippines Economic Zone Authority (PEZA).The new facility will offer customers extended sourcing solutions, inventory management, faster delivery times and local precision CNC machining capability.
Expromet is a fully integrated, leading-edge supplier of engineered solutions, providing UK-manufactured precision casting and machining solutions alongside extensive supply chain partnerships with worldwide manufacturers.
Global economic, political and social considerations now make it more important than ever to offer an increasingly wide range of sourcing options. Expromet Asia Inc. will initially
I have loved the process of continual learning and improvement, and that is something I will continue to do in my new role.
Ryan is married and a father of three. Outside of work he enjoys running and will be taking on some half marathons next year. Family time is very important to him, he adds: “My family is my reason for everything I do.”
Titan Manufacturing, founded in 2011, specialises in CNC precision engineering, sheet metal welding fabrication, laser profile cutting and surface finishing: a versatile range of services enabling them to offer a full-service package, including parts assembly services. The company’s new facility is equipped with a 4m flatbed fibre laser for precision cutting,
250 tonne hydraulic press brake sheet metal folding machine, glass bead blast finishing and paint spraying facilities.
Titan Manufacturing also invested £500,000 in four state-of-the-art CNC (Computer Numerical Control) machining centres and one driven tool CNC lathe from Hurco to help increase production capabilities and allow Titan to meet the growing demand for its quality services.
provide a new logistics and inventory call-off facility, giving worldwide customers:
• increased security of supply, minimising risk in the supply chain
• reduced lead times through warehousing and inventory management
• cost efficiencies and enhanced operational reliability.
Expromet plans to provide CNC machining in the Philippines, helping to optimise the efficiency of Expromet’s worldwide manufacturing supply chain. This will also provide
opportunities to eliminate tariffs and benefit from significantly lower costs, giving customers a competitive edge.
Turnkey solutions for demanding sectors
Expromet supplies precision engineered solutions for performance-critical applications to a wide range of industry sectors, including Aerospace, Automotive and Electronics.
“Expromet Asia will ultimately provide a turnkey solution for customers, including product development, sourcing and inventory management. It is a fantastic opportunity for customers to benefit further from strategic sourcing, optimising cost and lead times without impacting on quality,” says Jason Tyas of Expromet Asia.
To find out more please call on 0271 866200 or email Expromet Technologies Group: enquiry@expromet.com
Repolywise, a start-up founded by Oxford University researchers, is proud to announce the development of its revolutionary ‘Atomic Scissors’ technology, poised to tackle the growing global plastic waste crisis.
Repolywise’s Atomic Scissors technology involves a highly innovative hydrocracking process to break down waste plastics at the atomic level. In its current lab-scale capacity, the technology has demonstrated the efficient, selective, and high yielding degradation of assorted samples of polyolefins.
This initial capacity serves as proof-of-concept for the innovative catalyst developed at Oxford. Repolywise was founded to scale this technology, enabling it to handle larger quantities of plastic waste, from kilograms to tonnes, through a continuous flow process. This advancement moves us closer to a sustainable solution for plastic pollution.
How Atomic Scissors technology works
The Atomic Scissors process selectively converts plastic waste into propane in a one-step process. This propane is then sold to the petrochemical industry, where it is dehydrogenated or cracked into olefins before being used in the production of new polyolefins, such as polyethylene (PE) and polypropylene (PP). This approach not only helps reduce plastic waste but also supports the circular economy by creating valuable raw materials for new plastic products.
Repolywise’s technology is designed to process polyolefin plastics, including polyethylene and polypropylene, which account for approximately 50% of the 330 billion kilograms of plastics produced globally each year.
These types of plastics are particularly challenging to recycle using conventional methods, often leading to downcycling into
lower-quality materials. In contrast Repolywise’s Atomic Scissors offer a solution to recycle these materials back into high-quality polypropylene, ready for reuse in the production of new plastic products. Vitally this is a more efficient, higheryielding, lower energy required reaction than current hydrocracking techniques seen elsewhere.
Scaling for commercial use
While the Atomic Scissors technology is a breakthrough in chemical recycling of plastic, a challenge remains to scale the process. The current lab-scale is a 2 gramme batch process, and will be increased to 2 kilogrammes in the next phase of development. Following further funding, Repolywise plans to achieve a commercial-scale capacity of 2 tonnes in a semi-flow process,
marking a substantial step towards industrial application.
Fundamentally Repolywise’s technology operates under relatively mild conditions with a highly selective process, which contributes to reduced costs compared to other chemical recycling methods. This cost-effectiveness, combined with the technology’s ability to handle hard-to-recycle plastics, positions it as a game-changer in the global effort to reduce plastic waste.
Repolywise is committed to meeting the highest standards of environmental and operational compliance. The company is working towards obtaining ISCC certification, which will validate its mass balance approach and ensure the sustainability of its processes. With the support of £375,000 in grants from Innovate UK, Repolywise is conducting further research and development from the AgileLab at Oxford University Begbroke Science Park to enhance and scale up its Atomic Scissors technology. The company continues to leverage its academic roots and cutting-edge research undertaken at Oxford University to drive innovation in the field of plastic recycling.
Wilkinson Star, one of the UK’s largest wholesale welding equipment distributors are proud to be the exclusive partner for Max Photonics handheld laser welding equipment in the UK and Eire.
Targeted at sheet metal fabrication industries, this technology has now been adopted into a growing list of applications including nuclear, aerospace, pharmaceutical and catering to name but a few.
Max Photonics fibre laser technology is a great supplement to conventional welding methods in most fabrication workshops. The technology can offer many advantages over conventional welding methods as below:
• Fast welding speeds
• Minimal heat affected zone
• Minimal heat distortion
• High precision and neat welding seams
• Up to 4 times faster than TIG
• Low consumable usage
• High repeatability
• Minimal training required
• Uniform weld bead
• Ability to weld various metals as well as dissimilar materials
• Improves production efficiency
• Reduced post weld cleaning times
• Easy to use
• Low application costs
• Efficient energy usage
• High welding strength
• Excellent welding performance
To learn more about our range of available products please visit wilkinsonstar247.com or contact your local welding laser equipment distributor. Demonstrations are available at our training facility in Manchester. For further information please contact 0161 793 8127.
Five young women engineers have been announced as finalists for the Institution of Engineering and Technology’s (IET) Young Woman Engineer of the Year Awards 2024.
These prestigious engineering industry awards celebrate women working in modern engineering – and aim to help change the perception that engineering is predominantly a career for men by banishing outdated engineering stereotypes.
Alexia Williams
Alexia is a Through Life Technical Lead at Rolls-Royce Plc. Alexia improves assets throughout their life, utilising data and information collected to make informed decisions to extend the products operation life and reduce maintenance periods.
Alexia is the current Chair of the Institute for Apprenticeships and Technical Education Apprentice Panel, she is the Apprentice Representative in the UCAS Apprenticeship Stakeholder group, she is on the IMechE Bath and Bristol Young Members Panel, as well as being the Apprentice Representative on the IET Young Members Panel.
Over the last year she has contributed over 200 hours to promoting STEM to the younger generation through Air Shows, Careers Fairs, Conferences and in schools. She is passionate about encouraging more women to go into engineering especially via an apprenticeship.
Erin
Lowe
Erin is an Apprentice Electrical Engineer at Yamazaki Mazak UK, where she wires electrical components, looms cables, carries out earth testing and electrically adjusts the CV5-500 machining centre.
Over the last year, Erin has also delivered customer and public educational tours of the European Manufacturing plant, as well as attend numerous career and trade fairs, giving outreach presentations and providing regular support to the cadetship programme.
Marisa Kurimbokus
Marisa is a Chartered Engineer with a career spanning over a decade in product design and systems engineering within the automotive and power electronics industries, including Jaguar Land Rover, Triumph Motorcycles and Lyra Electronics. Most recently, Marisa was Head of Engineering and Product Development at Aeristech, where she led a multidisciplinary engineering design team to create high speed air compressors, primarily for hydrogen fuel cell applications.
She was listed in the Top 50 Women in Engineering: Inventors and Innovators in 2022 for her work in net-zero and green technology and she supports developing engineers through their careers, providing mentoring for university students through to engineers applying for Professional Registration.
Natalie Parker
Natalie is a Technical Specialist and Manager for Operational Technology Group at Sellafield. She provides technical and assurance support to front line engineering teams and wider projects. Natalie works to support and develop an offsite central location that allows engineers to share problems, innovate ideas and learn from experience.
As the co-lead of Sellafield’s Women in Technology group, Natalie has led on the development of a primary school workshop and rolled it out in a vast number of primary schools to introduce students to electrical circuits and programming through fun and interactive activities, showing them how STEM skills can be used in everyday life.
Salma Al Arefi
Salma is a Lecturer in Engineering Education at the University of Leeds, teaching and supporting the learning of future engineers. Her teaching expertise focuses on the field of renewable energy systems, and as well as delivering lectures and laboratory sessions, Salma also supervises student’s technical projects.
Outside of teaching, she enjoys conducting research on teaching methods with a focus on inclusive engineering pedagogy.
Registration is open
As well as highlighting engineering talent, the IET Young Woman Engineer of the Year Awards seek to find role models who can help address the UK science and engineering skills crisis by promoting engineering careers to more girls and women. Just 15.7 per cent of those working in engineering occupations are women (source: Engineering UK).
The winner will be announced at the IET’s Young Woman Engineer of the Year Awards ceremony on: Monday 9 December 2024.