MANUFACTURING PRODUCTION
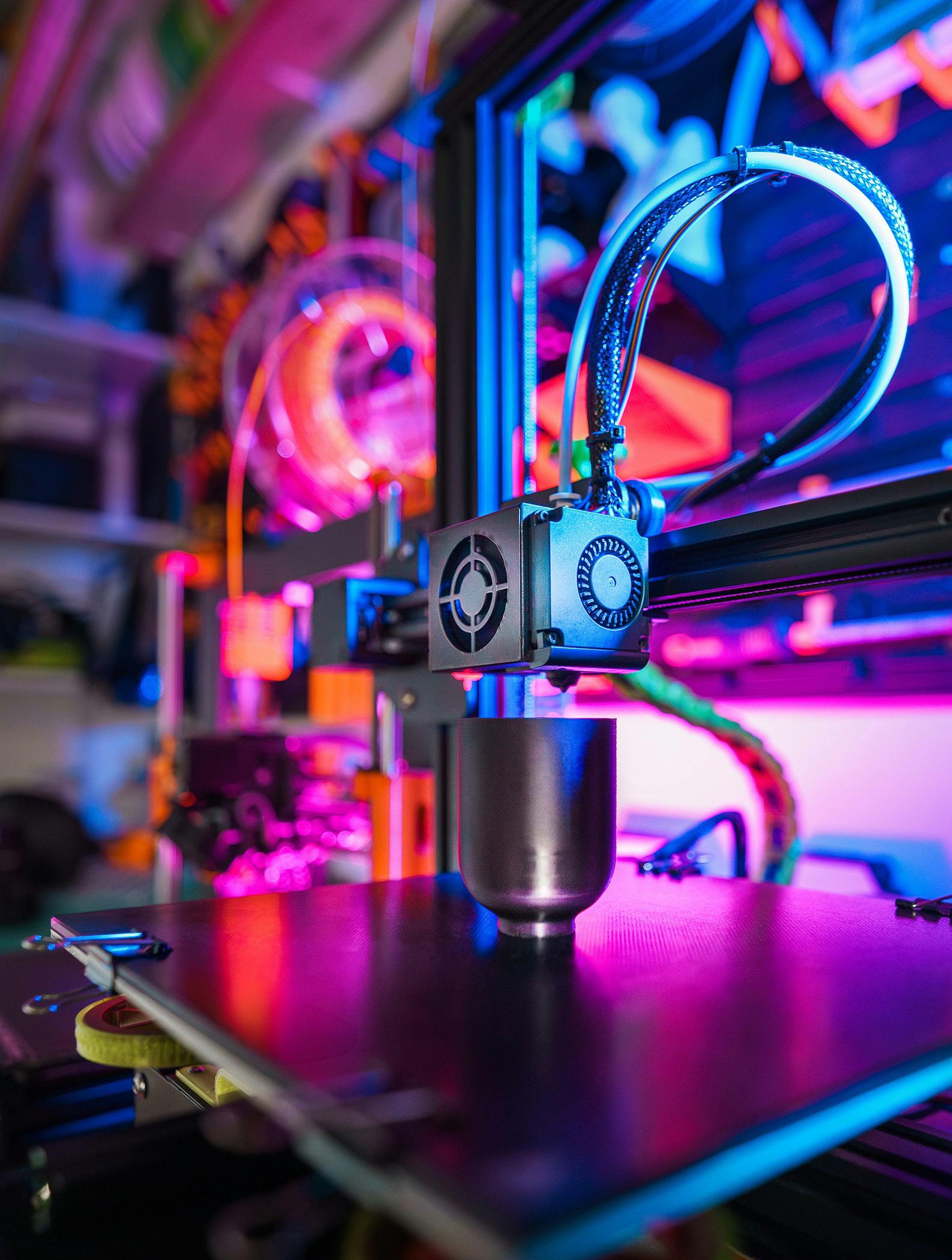
SUSTAINABILITY
THE CRUCIAL ROLE OF DATA ANALYTICS IN ACHIEVING NET ZERO
12 MANUFACTURING WAREHOUSE TIPS
SUSTAINABILITY
THE CRUCIAL ROLE OF DATA ANALYTICS IN ACHIEVING NET ZERO
12 MANUFACTURING WAREHOUSE TIPS
At OPC Assessment, we’re more than test publishers – we’re experts in selecting and developing top talent. With over 25 years’ supporting the rail industry and beyond, we specialise in creating psychometric tools that enable our global clients to recruit and develop exceptional employees.
We believe that in safety-critical roles, specific personal competencies are non-negotiable and that there are nine essential attributes for success. From understanding rules to cultivating resilience and conscientiousness, we can help measure these vital competencies to ensure your team is equipped for safety excellence
Tailored to support the development of existing employees and prospective recruits, our innovative assessment tools cater for a variety of roles. Testing via our user-friendly online platform, Candela, provides clear, instant results.
Some of our top-rated tools include:
The Safe Concentration and Attention Test (SCAAT): One of the world’s leading psychometric tests for assessing concentration.
The Verbal Comprehension for Safety Test (VCST): Evaluating a candidate’s ability to navigate and apply rules effectively.
The Safe Personality Questionnaire (SAFEPQ): Assesses four key personality characteristics linked to safety performance.
In this edition we hear from Adam Goves, sector lead for manufacturing and infrastructure at global climate tech company, IES. Adam raises the question ‘What should manufacturers prioritise in 2024 to accelerate progress to net zero?’ It is encouraging to see that 92% of
see net zero as a priority, greatly encouraged by the Government’s grants to help manufacturers make changes, it seems we are moving steadily in the right direction.
We hope you enjoy this issue and as always, if you have any news that you would like to feature, please email details to
North West adoption programme backs 300th business to digitalise on fifth anniversary
Donna Edwards, programme director, issues rallying call for more manufacturers to seek funded support
SME manufacturers have invested £22m in technology, backed by Made Smarter’s trailblazing adoption programme in the North West.
300 businesses have now secured £6.5m matched funding from the government-funded, industry-backed initiative, adopting technologies as diverse as sensors, robotics, 3D printing and artificial intelligence (AI).
These 350 technology projects, supported by £16m private sector investment over the last five years, are forecasting the creation of almost 1,600 new jobs and over 2,850 upskilled roles, and are set to add £242m to the economy over the next three years.
Among the latest wave of businesses starting their journey with Made Smarter to benefit their bottom line and the environment are food and drink manufacturers: Harbourside Products, Northern Pasta Company, Brightside Brewing Company, Just Bee Honey, Studio Bakery and Chandley Ovens.
Lifestyle product manufacturers adopting industrial technologies include: Weaver Dane, Saxon Furniture, Crozier Design, Neal Jones Furniture, Contour Campervan Furniture, Evertaut, Mactapes, English Trading Company, and Alphin Pans.
Organisational changes are commonplace, from changes in management structure and departmental responsibilities through to implementing a new organisation-wide IT platform. However, latest research from O.C. Tanner reveals that just 65 per cent of manufacturing leaders take their employees into account when deciding to enact business-wide changes. And only 59 per cent seek employee opinions as changes are rolled-out. These are the findings from O.C. Tanner’s 2024 Global
Culture Report which gathered data and insights from more than 42,000 employees, leaders, HR practitioners, and executives from 27 countries worldwide including 3,583 from the manufacturing industry.
“Organisational changes can have far-reaching impacts on the workforce” says Robert Ordever, European MD of O.C. Tanner. “Regardless of whether these changes are strategic, structural, technological or peoplecentric, by not considering employees and seeking their feedback before
rolling-out change, this is a recipe for disaster, potentially leading to widespread frustration, cynicism and disengagement!“
The Report suggests that traditional change management practices, which tend to be linear, top-down, and process-oriented, are no longer fit for our evolving work environments. They also fail to involve employees in the planning, thereby underestimating and under-prioritising the organisation’s people.
With this in mind, it’s no surprise that almost a third of manufacturing employees (30 per cent) believe that the organisational changes they have experienced were either poorly managed, or they were left feeling indifferent to how the changes were enacted.
Ordever says, “It’s crucial that an organisation’s people are the centre of change strategies. This approach will not only remove friction from change management processes, but will increase employee wellbeing and strengthen workplace culture.”
The Report recommends that effective change management must first start with nurturing a culture where employees have high trust and feel
With the Government committing to continue the North West adoption programme as part of a UK roll out, manufacturers are being urged to connect with Made Smarter to access the funded support on offer. This includes digital transformation workshops to create a digital roadmap, impartial and expert technology advice, leadership and skills training, as well as grant funding for digital internships and technology projects.
For more information, visit www.madesmarter.uk
appreciated and valued. Decentralising the change management process so managers at all levels can be involved is also important, together with ensuring regular, transparent communications and that all employees have a voice.
When employees have a voice in organisational changes, they are eight times’ more likely to have feelings of trust, are five times’ more likely to have a sense of community and thriving at work is three times’ more likely.
Ordever adds, “The truth is that no organisational change is going to be effective or lasting without the buy-in of employees. And the sooner leaders recognise this and ensure the organisation’s people are always considered, the more successful any changes will be.”
In the dynamic realm of the world’s second largest aerospace economy, where challenge often accompanies opportunity, the UK aerospace industry is enjoying a resurgence after weathering the storm of the COVID-19 pandemic. Against this backdrop, Simon Weston, the Managing Director of ASG Group in Stockport, is leading the charge, advocating for a bullish approach and strategic investment to position UK aerospace and defence suppliers for future success.
The aerospace sector has historically been a cornerstone of the UK’s industrial prowess, contributing significantly to the nation’s economic growth and technological innovation. However, the pandemic-induced lull tested the resilience of the industry, exposing vulnerabilities in global supply chains and intensifying competition for skilled talent.
Simon Weston, a seasoned leader with a track record of steering ASG Group through these turbulent recent years, recognises the imperative for businesses to adopt a proactive stance.
In a recent conversation, Weston emphasised the need for UK aerospace and defence suppliers to embrace a spirit of boldness and continue investing to stay ahead of the curve.
The pandemic-induced disruptions unearthed vulnerabilities in global supply chains, prompting a reevaluation of traditional sourcing strategies. Weston suggests that diversification and strengthening of local supply chains are pivotal to mitigating risks associated with geopolitical uncertainties and sudden disruptions. The ASG Group has been at the forefront of such initiatives, forging strategic partnerships and investing in cutting-edge technologies to enhance the resilience of its supply network through continued plant investment and acquisition.
However, the challenges extend beyond the supply chain. Access to skilled talent has become an increasingly pressing concern, as the industry experiences a surge in demand for specialised skills. With a keen eye on talent acquisition and retention, Weston underscores the importance of fostering a culture of continuous learning and development between organisations.
In the midst of uncertainty, one thing is clear – Simon Weston and ASG Group are leading by example, urging their counterparts in the industry to be bullish, invest strategically, and navigate the skies with confidence as the aerospace sector takes flight once again.
For more information, visit; www.asg-group.co
As climate targets loom closer, decarbonisation is more urgent than ever – particularly in sectors like manufacturing, which accounts for one-fifth of global carbon emissions.
Encouragingly, 92% of manufacturers now see net zero as a priority and the sector is making progress. However, understanding how to overcome barriers to reducing emissions can be challenging for businesses looking to make a meaningful change. Here are some steps that manufacturers should prioritise this year to accelerate their progress.
Economic uncertainty and inflation pose barriers to net zero, but emerging funding schemes can support the implementation of decarbonisation strategies. These strategies can enable businesses to unlock benefits such as lower operating costs, risk mitigation, and better access to finance.
Major funding opportunities have been announced, including the UK Government’s £4.5bn package of grants and loans for British manufacturers to make changes and meet net zero.
The EU Commission’s Innovation Fund also allocated €1.4 billion to strengthen industrial manufacturing capacity and supply chain resilience. These grants can be combined with funding from other support programmes too, and the applications for the 2023 fund are open until 9 April 2024.
Additionally, manufacturers can benefit from the Industrial Energy Transformation Fund (IETF) - a £500 million fund to support investment or studies relevant to on-site infrastructures, enabling an energy efficiency or decarbonisation measure. The phase 3 application window is currently open, closing in April.
Technology will also be critical, and the manufacturing sector is increasingly utilising methods such as data analytics, cloud computing, and 3D modelling. However, these tools are more
commonly used to help decarbonise factory processes and supply chains, without accounting for factory buildings themselves, which contribute significantly to overall emissions.
A more holistic approach which leverages data from production processes, the building shell, services, and systems is required, providing an overall view of the energy balance in a factory. Digital twins - virtual replicas of buildings that gather data and use physics-based simulations to respond like their real-world counterparts - are an effective way to access this intel and use it to assess different scenarios to optimise operational efficiency and reduce emissions.
Digital tools can also support decarbonisation feasibility and monitoring and verification studies that are often required as part of funding proposals. This can help manufacturers stand out with data-backed funding applications. Similarly, as ESG reporting becomes an increasing requirement, digital tools can provide the insight needed to keep track of progress towards targets and comply with legislation.
Finally, collaboration will be paramount in making industry-wide progress towards net zero. According to research, manufacturers forming external partnerships and joint ventures to meet emissions goals are making more significant strides towards their goals. Sustainability consultants should work together, sharing data and insights to uncover hidden energy, carbon, and cost savings that might otherwise have gone undetected.
With 2024 underway, and sustainability remaining high on the agenda, manufacturers should research funding schemes, utilise tech, and foster collaboration to ensure their businesses are firmly on the path to net zero.
THE DHS-150 DOOR HANDLE SYSTEM IS ESPECIALLY SUITED TO HEAVY SWING DOORS
With the new practical DHS-150 door handle system, the slimline AZM150 solenoid interlock from Schmersal is now even easier to use. The ergonomic DHS-150 avoids the need for a separate door handle and is suitable for machine enclosures or fencing and all standard aluminium profiles with a width of 40 mm. The robust door bolt is particularly useful on heavy swing doors and for use in harsh environments.
One benefit of the new accessory is that the actuator is pre-positioned by the bolt in the DHS system, thus ensuring optimal insertion into the device. This gives the system stability against lateral forces. In addition, the DHS-150 door handle system is also equipped with an integrated locking device (LOTO). This locking tag function protects operating staff from mistakenly being locked inside larger, walk-in systems and machines while performing servicing and repair work.
The AZM150 has an interlocking force of 1500 Newtons and can be combined with three different actuators for different attachment situations. A positive of the interlock is the rotating actuator head which can be locked with ease by simple placement on the cover, rather than being bolted into place. The solenoid interlock is electromechanical in design and can be combined with a high safety standard: a low coding level as standard, or optionally with a high coding level in accordance with ISO 14119.
www.schmersal.co.uk
uksupport@schmersal.com
Manufacturers who need high positional accuracy for their machinery rely on the accuracy of metrology technology. Here, Ross Turnbull, Director of Business Development and Product Engineering at ASIC design and supply company Swindon Silicon Systems, explains how custom Application Specific ICs (ASICs) offer enhanced precision for even the most demanding measurement applications.
Metrology instruments are a crucial element of the manufacturing plant. Whether for calibrating production machinery or for post-production verification, metrology equipment goes a long way in ensuring a highquality finished product that meets specification.
Coordinate measuring machines (CMMs) are an example of a metrology instrument, able to provide measurements in all three dimensions. In post-production quality processes,
Control of the probe angle is also possible, allowing the machinery to measure surfaces that would be otherwise unreachable.
CMMs are used to measure the geometry of physical objects for any manufacturing flaws or errors. This is achieved with a scanning probe by measuring discrete points or lines across
the object. Control of the probe angle is also possible, allowing the machinery to measure surfaces that would be otherwise unreachable.
Converting the motion of the scanning probe into useful positional information is possible with the use of encoders. Encoders combine a scale, similar to the markings on a conventional ruler, with a readhead describing motion relative to the values on the scale.
The encoder typically converts a physical stimulus into an analogue signal. For this signal to be understood and interpreted by digital devices, including the metrology software, this signal must first be digitised.
It’s possible to use a variety of offthe-shelf integrated circuits (ICs) to perform the necessary tasks of signal amplification and conversion. However, for an optimised solution, the roles of these individual ICs can be condensed into a single chip: an ASIC.
An ASIC is a chip that has been designed exactly for customer requirements.
A complete custom design approach results in a high-performance IC with capabilities beyond those offered by standard off-the-shelf devices.
By taking a careful approach to design, it’s possible for an ASIC to encompass all the features of several standard ICs in one package. Consolidating functionality into a single package typically allows for a reduction in PCB size. A more compact size allows for a smaller and lighter encoder that can be easily designed into CMM equipment.
ASIC design also facilitates greater performance where it matters. In a position sensor, this might be a nonlinearity specification for improved sensor calibration and accuracy. This is where working with an experienced ASIC designer can be hugely advantageous; the entire signal path can be optimised for a chip that offers both the technical and commercial advantage to the customer.
In metrology, even a minute fraction of a millimetre could be the difference between product success and failure. As a result, it’s vital that metrology equipment and the sensors within are class-leading. With the help of ASICs, accuracy of these devices can be enhanced for improved product quality and efficiency.
Totalkare’s ergonomic positioners are single or double column devices that enable the lifting and rotation of a product during welding and assembly operations.
With overall capacity from 2,000 - 90,000kg to suit, they are both compact and flexible.
NMi Group, a global leader in mission-critical Testing, Inspection, Certification, and Calibration (TICC) services, proudly announces the transformative acquisition of TrustCB in the Cyber Security domain. This strategic move solidifies NMi Group as the premier provider of certification services for the evolving landscape of digitally integrated and smart devices.
Now part of NMi Group, TrustCB is the exclusive commercial Certification Body for the globally recognized Common Criteria cybersecurity standard, working with globally leading clients and capable of
certifying up to the highest levels (EAL7). This strategic alignment reinforces NMi Group’s commitment to a comprehensive approach, integrating legal metrology and Common Criteria standards to ensure the overall reliability and integrity of smart industrial devices.
A key emphasis of the acquisition is TrustCB’s expertise in translating Common Criteria standards via SESIP to the Internet of Things domain. This strategic move further fortifies NMi Group’s dedication to “Measure Tomorrow” by synergizing precision in measurements with increasingly requested robust cybersecurity standards.
In legal metrology and Common Criteria, coexistence is imperative to guarantee a holistic approach to the functionality, accuracy, and security of devices such as smart meters, smart grids, and other smart industrial devices.
Manufacturers and operators navigating these digital landscapes must adhere to both legal and cybersecurity regulations, ensuring compliance with standards for accuracy and security.
This acquisition marks a pivotal milestone in NMi Group’s Build and Buy strategy, solidifying its position as an industry leader in legal and applied metrology services for smart industrial devices.
Energies PH, Inc, through its affiliate San Bernardino Ocean Power Corporation, has contracted with Inyanga Marine Energy Group to build Southeast Asia’s first ever tidal power generation plant.
The site will be at the remote Capul Island of Northern Samar in the Philippines, along the San Bernardino Strait, a passage well-known for the strength of its marine currents.
The contract for Engineering, Procurement, and Construction has been awarded to Inyanga Marine Energy Group.
The 1MW project, which is expected to deploy in late 2025, will use Inyanga’s innovative HydroWing tidal stream technology.
The HydroWing tidal stream turbines will be connected to the electrical network of Capul, an off-grid island currently relying on a 750 kW diesel power plant. The first stage of the project consists of a 1MW tidal power plant, to be connected into a microgrid network coupled with Solar PV and energy storage, delivering a reliable, sustainable, and cost-competitive alternative to fossil-based power generation.
Other tidal power generation sites planned for subsequent deployment by San Bernardino Ocean Power Corporation are in San Antonio Island, also in Northern Samar, and the Calintaan Island in Matnog, Sorsogon.
The new season of the ABB FIA Formula E World Championship begins in January 2024, and next time you watch the cars from the TAG Heuer Porsche Formula E Team, you might not realise they feature a secret ingredient: LOCTITE.
Henkel Adhesive Technologies, through its LOCTITE brand, has formed a close partnership with the TAG Heuer Porsche Formula E Team. The collaboration began in 2021, when Henkel Application Engineer Martin Christall met the team to identify possible points of use where Loctite could further improve the performance and reliability of the team’s electric race car.
The biggest challenge was that, in Formula E, the chassis,
battery, aerodynamics, and front suspension are provided centrally and are the same for all teams. This means there is only a certain amount of leeway when it comes to incorporating a team’s technologies and components, for example in the engine, transmission, rear suspension, and control systems.
Today, the teams work closely together to get even more out of the cars of the future – and TAG Heuer Porsche Formula E Team is improving season on season, with its best-ever placing of 4th in the 2023 season.
Their shared goal is to develop even better ways of using LOCTITE products, while also testing new products that enhance the car’s performance and speed – and, of course, its sustainability.
Already, different Loctite solutions are used to ensure mechanical reliability for a host of key applications, which extend from suspension bearings, gearbox housing parts, and powertrain bolts to steering wheel components.
You can see TAG Heuer Porsche Formula E Team in action throughout 2024.
Warehouses across Europe and beyond are embracing high performance robotic based goods-to-person (GTP) automation systems. Particularly as some contemporary systems are able to handle very high throughput volumes with industry leading productivity, whilst increasing storage density and utilising the full height of many buildings without needing mezzanines. They are very flexible, easy to expand, and robots can be moved from site to site to maximise their usage.
However, experience suggests that the UK’s third-party logistics companies (3PLs) haven’t yet fully embraced owning and investing in more sophisticated high performance automation. To maximise the potential of robotics, there are a number of obstacles 3PLs need to overcome which I have discussed below.
Open-book contracts
Open-book contracts have served both 3PLs and their customers well over the last few decades. During this period of low inflation, incremental productivity improvements were adequate for both sides, and they required relatively low investment.
However, with an open-book contract, the 3PL usually makes most of their revenues by adding a small management charge percentage on top of all the costs they incur running the operation, before passing the bill to their customer.
One of the biggest costs of a manual fulfilment operation is the labour force. If automation is deployed in a warehouse that reduces the labour requirement by 80%, the revenue and profit generated by the unfortunate
There are a myriad of contract permutations and hybrid structures when it comes to 3PL contracts in the UK.
3PL drops by a similar amount. No one would blame them for finding this a difficult initiative to encourage, let alone expecting them to make a multi-million-pound investment in the automation required to achieve it!
Two of the reasons often given for the popularity of open-book contracts in 3PL fulfilment are the reduction of risk for the 3PL, which allows them to operate on very low margins, and the
comfort the customer feels because they can see the 3PL is not making excess profits from their contract. This does not necessarily mean that they are receiving the best value, however. The customer is only getting the highest value if their 3PL’s operating costs are also as low as they can be, and without the use of effective automation, this is very unlikely to be the case in today’s environment.
Customer owned vs 3PL owned warehouses
There are a myriad of contract permutations and hybrid structures when it comes to 3PL contracts in the UK. One of the most fundamental variables is the ownership of the building where the fulfilment operation will be. If it is owned by the customer, the 3PL will only be able to offer lowimpact, easily relocatable automation as part of the contract.
This will make little improvement to productivity and may reduce the storage density compared to a manual operation. In a customer owned warehouse, the best way to achieve 80% labour reduction is for the customer to own the automation and the 3PL to operate it. If the 3PL owns the warehouse, then it can make the investment with low risk, assuming the selected automation has the flexibility to be used for a variety of clients.
For manufacturing and production plants to achieve success, grow sustainably, and meet customer requirements, operators must maintain accurate inventory control, avoid bottlenecks, and deliver goods with speed and precision. It is critical to incorporate modern trends, test new technologies, and implement best practices.
Gathering information from our years of experience, we compiled 12 best practice tips for manufacturers to improve warehouse processes in the production environment. To read these in full click here.
#1 Organise your SKUs: Raw materials, components, assembly kits, tools, semi-finished goods, goods ready for shipment – they are all used throughout your warehouse. Can you always find them in the right location without long search or walking times? Create a list and write down what is needed where.
#2 Save valuable floor space: Don’t waste valuable floor space. Once it is clear which goods you need in which production steps and warehouse areas, review the space required for storing them. You don’t want to waste valuable space by keeping raw materials or semifinished goods in aisles.
#3 Implement efficient & ergonomic storage for heavy parts & pallets: Storing heavy and bulky parts or goods on pallets does not have to require additional labour. Think about implementing automated storage solutions for those parts and tools.
#4 Eliminate bottlenecks: Tools, spare parts, production components, and raw materials are essential to keep production processes running smoothly. Combine your storage system with an interface to a tool management software to always have inventory information easily accessible.
#5 Speed up manufacturing with automated kitting: This will help you to save valuable labour time and reduces search times – increasing overall productivity and efficiency. Using an automated storage and retrieval solution to store assembly kits creates a highdensity and space-saving solution.
#6 Integrate a buffer storage for semi-finished goods & assembly kits: Improve production planning and supply by providing space-saving buffer storage for semi-finished goods or assembly kits. Certain production steps need buffer systems when they include a wait or hold step (e.g., waiting for paint to dry) or their material handling process requires reserve inventory to absorb expected variations in demand.
#7 Ensure secure storage for all parts: When thinking about which storage system is the right one for your warehouse, you should also think about
security. It is not only about having all components or tools in the right place, but also about protecting those in their storage location. Automated storage systems allow restricted access to specific stored goods as needed.
#8 Pick parts fast & accurately: Are long walking and search times or inaccurate and slow picking some of your challenges? If yes, you should review your processes. Implementing the right picking strategies along with pick-to-light technology will significantly increase performance.
#9 Integrate a WMS for fast & reliable material flow: Control your material flow with an intelligent warehouse management system (WMS). Implement a WMS that confirms when incoming goods arrive in the receiving area, sends them for quality control, and stores them in the right storage location.
#10 Investigate the implementation of robotics & conveyor systems: It is also time to think about including robotics, Automated guided vehicles (AGVs) and conveyor technology to further support, facilitate, and accelerate material flow and picking processes to automatically deliver goods just-in-time for production or shipping.
#11 Consolidate orders in the shipping area: Review your shipping area. Do you have smooth operations in place? Do you need to consolidate many parts before shipping? Automated solutions enable a space-saving, organised storage area for parts ready for packing or shipment to wait until an order is complete and it’s time to dispatch.
#12 Create an ergonomic work environment: Equally as important as smooth processes and organised storage locations are ergonomic working conditions. Unergonomic workplaces require operators to climb stairs, reach shelves, or lift heavy parts. This often results in injuries and employee dissatisfaction. By using automated storage solutions, you will simplify daily workloads to accelerate more efficient processes.
Keeping an eye on the wellbeing of your equipment and machines can greatly improve your sustainability efforts.
For example, having preventative maintenance schedules in place can lead to up to 20% savings in raw material usage, as well as a 30% decrease in greenhouse gas emissions.
So, if you’re actively trying to become more eco-conscious in your operations, what value can preventative maintenance bring to the table?
Welding Alloys, a leading expert in cladding and hardfacing applications, looks at the importance of minimising equipment downtime to ensure energy is used as efficiently as possible.
Whether it is machining equipment, cement plant components or components in the recycling industry, most industries are generally exposed to challenging wear environments.
Many parts and components of machinery experience continuous friction, heat, and stress during operation and will gradually wear out over time. As part of an effective preventative maintenance strategy, these require inspection, maintenance, and repair to
Performing constant maintenance checks on your tools and equipment will allow your assets to always operate at the height of their efficiency.
delay or avoid costly replacement. to keep the machinery running efficiently. Welding Alloys, a leading expert in cladding and hardfacing applications, highlights the importance of minimising equipment downtime by repairing components using latest technologies to ensure energy is used as efficiently as possible.
One of the most beneficial advantages of keeping your machinery in order is that it can improve your energy efficiency.
Pieter du Plessis, Group Product Engineer at Welding Alloys, explained: “Performing constant maintenance
checks on your tools and equipment will allow your assets to always operate at the height of their efficiency.
“Well-maintained machinery tends to consume less energy as everything is ticking as it should. In turn, this will significantly lower your carbon emissions and leave you with a more affordable bill at the end of the month. When comparing the energy requirements of replacement versus the maintenance and repair of components, it is always more beneficial to adhere to preventative maintenance when aiming to improve sustainability goals.
“It’s also worth noting that preventative maintenance to reduce downtime can actively help with resource conservation. Any inefficiencies and hiccups in your processes can waste lots of precious energy, as your assets will need to work twice as hard to overcome the fault and keep operating as usual.
“So, regular maintenance tasks can nip any potential problems in the bud and promote a more sustainable use of your resources.”
Looking after the wellbeing of your tools will no doubt increase their life expectancy.
In fact, from regular inspections to cleaning and timely repairs, preventative maintenance measures allow you to identify issues before they escalate into bigger, more troublesome problems.
This means that you can monitor your equipment’s health and tackle any hazards on the spot, which will then favour optimal longevity and reduce the need for frequent, pricey purchases.
In this respect, extending the lifespan of your machinery will cut your wastage levels, too. For example, regularly replacing worn-out welding torches with brand-new assets can generate significant waste, putting a dent in your sustainability efforts.
Educating people about the impact of downtime on the environment
might encourage them to review the performance of their own tools, too.
Fostering a culture of sustainability within the business is a crucial step to make preventative maintenance a priority task on everyone’s agenda. This will empower workers to contribute to the company’s eco-friendly goals, as they will feel the responsibility to promote sustainable behaviours in their operations.
If you’re in a senior position, provide your co-workers with training sessions on maintenance and environmental best practices. With all the right resources and knowledge, they are more likely to embrace an eco-conscious mindset and play an active role in preventing energyconsuming downtime.
Preventative maintenance programmes can minimise emissions and aid your carbon footprint.
Underperforming machineries tend to emit higher levels of pollutants, affecting the wellbeing of your surroundings. This is particularly relevant in the welding
industry, as ill-kept assets can generate fumes and particulate matter.
Conversely, well-maintained equipment is more likely to operate in a clean, effective fashion. By monitoring your machinery’s health and performance, you can avoid leaks, spills, and other malfunctions that could harm the environment.
What’s more, preventative maintenance can help minimise water consumption, too. Every day, just under three billion litres of water, equivalent to 1,180 Olympic swimming pools, are lost due to leaks.
However, by monitoring your tools on a regular basis, you can identify and rectify any problems causing water leaks and ensure they’re adequately conserved to drive your operations forward.
From improving your business’s energy efficiency to extending your equipment’s longevity, there are many ways in which preventative maintenance can support your sustainability efforts.
By checking the health of your assets consistently, rather than when the
any potential problems in the bud and promote a more sustainable use of
damage is done, you can minimise downtime, save money on expensive repairs, and make a difference in the wellbeing of your surroundings. www.welding-alloys.com
Let’s talk sustainable waste management. Ok, it’s not the sexiest topic, but at Waste Mission, we believe there’s never been a more important time to get serious about waste.
Did you know? The latest government data shows the UK generated an estimated 40.4 million tonnes of commercial and industrial (C&I) waste in 2020, of which 33.8 million tonnes (84%) was generated in England. The latest estimates for England only indicate that C&I waste generation was around 33.9 million tonnes in 2021.
Sadly, the amount of commercial and industrial waste generated by businesses is having a massive impact on the environment. Most of this waste ends up in landfills, generating greenhouse gas emissions 25 times more effective at trapping heat than carbon dioxide.
This is terrible news for our planet. And consumers are not ignoring the facts.
Deloitte’s 2023 Sustainable Consumer survey revealed that 30% of consumers had stopped buying products due to ethical or sustainability-related concerns. And almost 50% see circularity (explained in more detail later) as essential for buying a product.
If those aren’t reasons enough to reconsider waste management within your business, then how about this statistic: Every year, UK businesses can spend between 4–10% of their average annual turnover on waste disposal. That’s a significant chunk of profit.
Your waste challenge may seem complex, but let’s explore sustainable waste management and how we can help turn your waste into savings.
For actionable strategies check out our recent waste management blog.
Instead of collecting, transporting and disposing of waste, sustainable waste management looks for solutions that won’t harm the environment or human health and instead focus on reducing natural resource consumption.
Sustainable waste management revolves around a hierarchy:
• Reduce the initial amount of waste generated
• Reuse where possible
• Recycle what can’t be reused
• Sell what we can
• Only then, dispose of what’s left
“We already work with a range of major electricity network operators, offering them unique services for their transformer and switchgear recycling, ensuring that nasty elements like PCBs and F Gases are safely recycled. Additionally, we are developing some unique technologies in the WEEE waste sector, allowing us to extract precious metals from WEEE waste.”
Nicola Guest, Waste Mission’s Group Marketing ManagerFrom helping to reduce carbon emissions to improving air and water quality to commoditising waste streams that may be currently running at a financial loss – sustainable waste management has incredible environmental, economic and social benefits.
This type of model, where everything is reused, repaired or recycled, can also be understood as the circular economy.
With natural resources depleting and CO2 emissions rising, now is the time to embrace the circular economy.
Circular practices promote restoration and circularity rather than products reaching their end-of-life (linear economy). The result is less waste and a closed loop in the industrial ecosystem.
While some manufacturers are making positive steps forward, a 2023 report by Qflow revealed that although the construction industry generates 62% of the UK’s waste, only 2% is reused. This report highlights an incredible opportunity for increasing the adoption of circular practices within this sector alone.
It can be challenging transitioning to a circular economy. Yet, it’s important to remember that circular economy strategies can turn waste into savings. They stimulate local economies by converting waste into raw materials for production and generating sustainable employment growth.
At Waste Mission, we can educate, inspire, and facilitate waste reduction for your business by collaborating with you and your supply chain to innovate
and identify “waste” materials for conversion into valuable recyclable commodities.
Discover more benefits of the circular economy in our recent blog.
From groaning landfill sites to ecosavvy consumers and wasted profit, there are multiple reasons to embrace a sustainable waste management strategy and reduce the amount of waste your company produces.
Plus, let’s not forget how there are growing concerns around securing supply chains in an ever more volatile world. But, the great news is that sustainable waste management practices can help manufacturers ride the fluctuation in raw material prices.
We firmly believe that to achieve a more innovative and sustainable future, manufacturers in the UK need to
prioritise long-term sustainable waste management goals.
And that’s where our team at Waste Mission can help.
Waste Mission transforms complex waste into simple solutions.
At Waste Mission, we are driven by our unwavering commitment to doing what’s right – for our clients, staff, and the planet. No matter the complexity of the task, we want to simplify waste solutions for UK industries and manufacturers. We aim to educate, encourage and uncomplicate waste management by offering a bespoke, tailored service, all from a single point of contact.
Our responsive team of experts becomes an extension of your business, taking care of waste so
you can stay focused on your core operations. We promise to:
1. Guide you to reduce waste and increase your profitability
2. Help turn your waste into solutions, reducing reliance on new materials
3. Navigate complex regulations for you, ensuring you meet environmental and legal requirements
4. Provide a waste portal so you can easily access data on your waste production, recycling levels, and carbon footprint.
“What separates Waste Mission from their competition is the level of professionalism and transparency they bring to the industry. They continue to question the status quo and propose initiatives to drive our business forward.”
LG FlexitallicIf you care about your environmental impact and are looking for a reliable partner to help navigate the complexities of your waste management, then we’d love to talk.
Contact Waste Mission:
To book a waste review or learn more, visit our website wastemission.com, call us at 01438 745307 or email control@wastemission.com or visit us at stand 6-545 at MACH.
Using dimensions from the customer, Sulzer redesigned the pump with a new drop-in assembly.
Condensate pumps retrofitted by Sulzer offer fourfold improvement in MTBF
Operators of offshore platforms are very focused on the reliability of their equipment. Working in such a remote location means that major repairs, if not carefully planned, can result in extended downtime and loss of production. For one platform in Malaysia, a change in output was shortly followed by an increased rate of seal failures on the condensate pumps –an issue that was effectively resolved with a Sulzer retrofit, through their OEM-X line service.
Pumps for any application are designed to take fluid at a certain pressure and deliver it at an increased pressure and at a specific flow rate. If these figures are kept relatively constant, the pump should continue to provide reliable service for many years. However, moving too far away from the original specifications, for example lowering the flow rate, can drastically reduce efficiency as well as reliability.
In offshore applications, pumps are used for many tasks and their reliability is essential for continued productivity. Therefore, regular maintenance and inspections are carried out to ensure future performance. Ideally, pumps in this environment should be able to operate for around three years without a maintenance intervention and if the mean time between failures (MTBF) starts to drop, a solution needs to be found quickly.
So, when an offshore platform in Malaysia started to experience problems with its condensate pumps, which were suffering from seal leaks and excessive vibration, it was important to promptly find the cause and resolve the problem. All three condensate pumps, which operate as two duty, one standby, had performed well since installation. However, more recently, output from the platform had dropped
As a result of these savings, the return on investment for this project will be just two years.
and the condensate flow rate had been reduced from 93 m3/hr to 46 m3/hr; following this parameter change, the MTBF dropped to around 12 months.
At this point, the platform operator contacted the original equipment manufacturer (OEM) to find a solution. However, the only suggestion was to install new pumps designed for the current application data; this solution was outside the required scope both in terms of investment and time for delivery. This led to Sulzer being approached for an alternative solution that would help the customer ensure production continuity on its platform with minimal lead-time and without substantial capital outlay.
The original concern from the platform’s operator was that the mechanical seals were failing, and this was causing unexpected downtime. Further investigation found that the seal leaks were caused by excessive vibration, a result of the pump operating far away from its best efficiency point.
Sulzer’s expertise as a pump manufacturer and a OEM-agnostic provider of retrofit solutions enables it to offer reconfigured components that will fit in the original casing and deliver the new specifications for the task. All of which were delivered through its OEM-X line service, the universal repair service from Sulzer. In cases such as this, where a BB5 style pump needs to be updated, the usual approach is to design and manufacture a new cartridge, laser scanning the legacy pump to ensure precision dimensions. All the other components are usually retained to keep the project as cost-effective as possible.
However, due to restrictions imposed at the time as a result of the global pandemic, it was not possible for Sulzer’s technicians to be on-site and execute the pump scanning. On the other hand, due to the frequency of seal failures, the operator also preferred for the pump to remain on the platform. Therefore, using the external dimensions
of the pump provided by the operator, Sulzer’s manufacturing plant in India produced a highly accurate new pump assembly that was a drop-in fit for the legacy equipment.
The design retained the original mechanical seal system, which performed very well during the testing phase. The pump went through rigorous tests at Sulzer’s service center before being shipped to the platform for installation. Thanks to the precision manufacturing capabilities, the pump was quickly in place without any changes to the surrounding infrastructure. Having been successfully commissioned, the pump has been operating reliably since.
Radhika Bajpai, Retrofit Specialist for Sulzer, comments: “The redesigned pump has a power requirement of 216 kW, compared to the original 370 kW, enabling the original electric motor
to be retained and operate well within its capacity. Of greater significance to the platform operator, the mean time between repairs for the new pump is calculated to improve to 48 months, which will reduce maintenance costs dramatically.”
As a result of these savings, the return on investment for this project will be just two years. Following the success of this project, the operator wants all three pumps to be identical to minimize the spare parts inventory and make the most efficient use of resources. Therefore, the same retrofit will be carried out for the remaining two pumps in the near future.
API 610 standards recommend pumps that are in continuous operation should be designed to operate without any maintenance interventions for a minimum of 36 months. Sulzer’s aim is to far exceed this standard and offer its customers a greater peace of mind for their pump operations.
A lower condensate flow rate had resulted in the pump to operating outside best efficiency point, causing vibration and seal failures.
With a recent report further underlining skills shortage issues faced by the UK manufacturing sector, a prominent utilities equipment supplier is calling upon industry professionals to reevaluate their current approaches to temperature control.
According to findings from the Q4 Manufacturing Outlook published by Make UK and advisory firm BDO, UK manufacturers have seen their outputs surge three times fast than orders. Yet despite rising business confidence, the report’s stakeholders have highlighted that its employment data indicates skills shortages are now structural and systemic within the sector.
Taking this into account, Ruth Martin, Manufacturing Sector Manager for Aggreko UK and Ireland, is advocating for a shift in the industry’s approach to procuring power and temperature control to best navigate this critical issue. Specifically, Ruth is encouraging the sector to explore leveraging third-party expertise to address key challenges, including those around temperature control, to circumvent skills shortage concerns.
Engaging third-party suppliers on a continuous basis can help address these knowledge gaps and allow manufacturers to capitalise on growing sector confidence.
- Ruth Martin
“In the manufacturing environment, being able to source and operate temperature control equipment is vital to product yields and outputs,” she explains. “Yet ensuring operational processes are carried out as effectively as possible requires personnel with specialist skillsets.
“As this latest BDO-Make UK report makes clear, this is easier said than done, and will require long-term governmental intervention if skills shortage issues are to be remedied. However, industry does not stand still, and solutions must be found for the here and now.
“Engaging third-party suppliers on a continuous basis can help
address these knowledge gaps and allow manufacturers to capitalise on growing sector confidence.”
With the UK manufacturing sector demand remaining in flux and weather patterns becoming increasingly volatile, Ruth is also highlighting the potential role of equipment hire strategies in addressing these challenges. Specifically, she is underlining the added dynamism and adaptability made possible by securing chilling and heating equipment on a modular, temporary basis as demand rises and falls.
“Manufacturing is a fast-moving sector and many variables simply cannot be predicted beyond the short term,” Ruth concludes.
“Given the pressures the industry is facing, from varying sector confidence to increasingly extreme weather, it is logical to add greater flexibility to ensure efficient equipment performance while minimising the risk of under- or overspecification.
“Consequently, it is recommended that manufacturers engage with temperature control solution suppliers to best safeguard future operations.
“Given the skills shortages affecting the industry, establishing ongoing partnerships and using the expertise of these organisations may also provide businesses with resilience as 2024 progresses.”
To find out more about Aggreko’s solutions for the manufacturing sector, click here.
The industry’s leading showcase for robotics and automation solutions for manufacturing and supply chain operations has expanded its programme, resulting in an exhibition packed with more shows, innovation, insights and inspiration than ever before.
Robotics & Automation 2024 offers unprecedented opportunity for those looking to stay one step ahead in a competitive global market place. Now in its 8th year, the show thrives on its reputation as the go-to connective for industry leaders and innovators to propel businesses to more productive, cost-effective levels. The event showcases all the latest solutions in automated assembly, machine vision, conveyors & handling, robotic systems, machine safety, and much more!
The journey continues with 2024’s event, which adds a Sustainable Supply Chain exhibition to the two-day multiexperience show that also features the IntraLogisteX exhibition which offers an ‘Intralogistics’ space showcasing the smartest moves in warehousing and logistics.
There is no question that 2024 will be our biggest and best show to date.
Stephen Brooks, Robotic & Automation’s managing director, said: “There is no question that 2024 will be our biggest and best show to date. The Sustainable Supply Chain Exhibition is a particularly exciting addition to the programme. It’s our response to the industry call for a show that offers tangible, results-driven solutions that businesses can enact immediately. It’s an opportunity not to be missed for companies looking to engage with experts and get the inside track on sustainably-based supply chain solutions and trends.”
Featuring more than 350 exhibitors, 60 conference sessions and an expected 8,000-plus attendees from across the industry, Robotics & Automation is expertly-curated to maximise business profit through the optimisation of supply chain & manufacturing management. Ocado Intelligent Automation, Körber
Supply Chain Automation, Siemens, Autostore, Exotec, Hai Robotics, Locus Robotics, Movu Robotics, SSI SCHAEFER, and SEE are among the global brands exhibiting at this year’s event, with more leading names in the robotics and automation sector due to confirm their attendance in the coming weeks.
The newly-created Sustainable Supply Chain Exhibition is aimed at compliancefocused supply chain professionals, as well as companies committed to achieving ‘above and beyond’ environmental outcomes. It includes an array of exciting, enterprising spaces including a Start-Up Hub that offers small and medium-sized businesses an exclusive opportunity to promote revolutionary services and solutions that will help businesses to achieve sustainability goals.
The brand-new exhibition focuses on pivotal sectors such as packaging, last-mile logistics, cold-chain logistics, software and more – all crucial components of the supply chain operation. As well as developments in sustainable delivery and materials, the Start-up Hub will shine a light on new systems to improve traceability.
A Sustainability Theatre will also form part of the Sustainable Supply Chain Exhibition Space, providing a platform for industry thought leaders and influencers to share their aspirations for the sector’s future sustainability.
MOVE YOUR BUSINESS FORWARD WITH ROBOTICS AND AUTOMATION
DISCOVER THE LATEST IN:
CONVEYORS
MACHINE VISION
MACHINE SAFETY
ROBOTICS
SENSORS
350+ EXHIBITORS
8000+ VISITORS 60+ EXPERT SPEAKERS
MACHINE VISION
AUTOMATED ASSEMBLY
RFID
MOTION CONTROL AND MUCH MORE
REGISTER FOR FREE
THESE EXHIBITORS HAVE ALREADY SIGNED UP:
When considering automation it’s easy to overlook how the raw materials arrives at the process and how the product leaves, how packaging arrives and how waste leaves.
Often this is your biggest opportunity!
On top of reduced labour costs you have inventory record accuracy, traceability, product damage, infrastructure damage and safety to consider.
And in labours costs wages are only part of the story, there’s social costs, training, hiring and firing and supervision and motivating!
Automated Guided Vehicles are a mature technology that really works but they sit in a system and you need established experience to make a system really deliver.
AGVE have been making AGVs and delivering AGV systems for 40 years and for your sort of industry. We are the go to company to look at your process and process equipment and define how the mechanical and system interfaces should be designed to produce the optimum solution and the biggest savings.
We have joined the Robotics and Automation show to help process operators really explore their options across a wide range AGV systems deploying fork, conveyor, lift AGVs in tight spaces or over short or long distances.
Come and talk this through at stand 944 at Robotics and Automation. For
For nearly 50 years’ we at Litre Meter have been designing and manufacturing bespoke flow measurement solutions.
Designed to handle the highest of pressures and lowest of flows, our VFF and Pelton Wheel flow meters are engineered to withstand a range of applications and viscosities. Originally designed for the Oil & Gas sector, our flow meters are versatile for a range of industries including Subsea, Hydraulics, Water & Renewables.
We tailor each project to align with our customers’ needs and requirements. Our Design & Engineering team work alongside you, from project kick-off to installation and aftercare solutions.
Applying our specialist flow measurement knowledge and using the latest design software. We will design, engineer, and manufacture your ideal flow measurement solution.
Speak to our inhouse specialists on your flow measurement requirements today.
Quality Bearings Online has won the Feefo Platinum Trusted Service Award for 2024, an independent seal of excellence which recognises businesses that consistently deliver a world-class customer experience.
Backed by over 75 years of industry experience, Quality Bearings Online (founded in 2012) is a multi-award-winning ecommerce business known for supplying precision bearings, engineering spares, and technologically advanced lubricants. Operating on a global scale, the company supplies industry-leading products to clients in over 110 countries and a range of industry segments, including: industrial supplies, manufacturing, aerospace, defence, oil and gas, and precision engineering. Quality Bearings Online only supplies products of the highest calibre and works closely with world-leading brands such as SKF, Kluber, Shell, NSK, Timken, IKO, FAG, RHP and many more.
Quality is at the forefront of everything Quality Bearings Online does, from the products it supplies to the services provided.
Denny Maude, CEO at Quality Bearings Online, comments: “We’re so thrilled to receive a Platinum Trusted Service Award from Feefo. Keeping our customers happy is our main priority. So, the fact that this award is based on feedback from genuine customers gives us confidence we are providing an exceptional level of service.
The award also reflects how hard our staff work to listen to our customers and keep them happy, so a huge shoutout goes to the QBOL team. As we enter 2024, we’ll continue to listen to and deliver what our customers want.”
Feefo established the Trusted Service Awards to recognise brands that use the platform to collect verified reviews and receive exceptional customer feedback. The award stands apart from others of its kind by analysing feedback from real customers to offer a true reflection of a business’s dedication to providing outstanding customer service.
To achieve a Feefo Platinum Trusted Service Award, businesses must achieve the Gold standard for three consecutive years and collect over 50 reviews with a Feefo service rating of 4.5 and 4.9 between 1st January 2023 and 31st December 2023.
In 2023, 89% of Quality Bearings Online’s customers gave them a 5-star service rating and recommended their products and services to others.
Congratulating Quality Bearings Online on winning this year’s award, Tony Wheble, CEO at Feefo, said: “The Trusted Service Awards have always been about recognising companies that go way beyond the norm in customer service and in turn receive great feedback from delighted customers.
“A particular congratulations to Quality Bearings Online for winning a Platinum Trusted Service Award by providing great customer service consistently over a number of years. I look forward to seeing them continue to achieve next year and beyond.”
or contact
ready to assist you.
RelyOn Nutec UK (RelyOn), leaders in specialist safety training, competence and related services for safety critical industries, announces Colin Leyden as Managing Director, to drive regional and business growth as the company cements its presence in key energy and maritime hubs across the UK.
Colin, who joined the RelyOn Nutec Group in 2013, will maintain his current responsibilities as Vice President of Partnerships and New Markets for the Group as he takes the helm in this new appointment as managing director of the UK business.
Bringing more than 25 years’ industry experience to the role, Colin offers significant expertise in scaling businesses across the energy and engineering sectors globally.
In his new role, Colin will focus on supercharging RelyOn Nutec UK’s regional training hubs in Aberdeen, Teesside and Liverpool. Poised for investment in staff, facilities and equipment across these centres in 2024, RelyOn celebrated recent expansion in Liverpool, as well as a roll out of various technical training capabilities across all centres in the UK.
Quality and engineering recruitment specialist, G&P Recruitment Services, has appointed David Woakes to lead the business in the newly created role of head of talent acquisition and recruitment.
Woakes brings a wealth of experience to the role, having previously held senior positions across several recruitment, engineering and technology businesses.
Commenting on his new role, Woakes said, “G&P has some incredibly exciting and ambitious plans for its resourcing business so it’s a fantastic time to be joining the team. Engineering and manufacturing companies across a whole range of industry sectors are going through a skills and resourcing transformation themselves at the moment, so our own experience, coupled with our value-add proposition is a really compelling offer, and one which I look forward to introducing to even more potential customers and candidates.”
G&P Recruitment Services works with engineering and manufacturing
businesses to provide them with either temporary, contract or permanent staff. Candidates skills are closely matched to the unique requirements of customers, ensuring quality standards are upheld, or even improved.
The company has particular experience in the automotive industry and has already placed more than 200 qualified electric vehicle technicians, an area where a major skills shortage currently exists. Beyond automotive
and future mobility, G&P also works closely with companies in the aerospace, household goods, offhighway and advanced manufacturing sectors.
Woakes himself has also been involved in similarly exciting resourcing projects having previously worked with a marine company to recruit 200 skilled engineers on a renewable technology project. He’s also been closely involved in helping skilled engineers pivot into other sectors by transferring their highly valuable software related skills.
As a firm believer in life-long learning and development, Woakes has recently become a qualified statement of work practitioner. This professional qualification confirms his ability to create and deploy resource plans properly for companies, ensuring they get the best returns from their team.
For more information about the talent and resourcing services available for engineering and manufacturing business from G&P, visit www.gpqm.com.
We’ve been pioneering digital training solutions for some time now, and we’re already looking to what the energy sector wants next to service its ever-growing and diversifying sources.
Additionally, the continued development and growth of digital learning products for the energy sector throughout 2023 has prepared RelyOn for growth in the months to come.
Colin Leyden said: “The UK is home to some incredible energy talent and as our sectors diversify, nurturing and developing this will be more important than ever.
“Homing in on regional hubs where existing skills lie and potentially untapped expertise is waiting in the wings, we are primed and ready to develop the energy workforce of tomorrow.”
Colin is joined by several other senior appointments as the UK arm of the business realigns itself for the road ahead. Lee Fenton has a new role of Operations Director and Catherine Liebnitz moves into the newly created role of Centre Director - Aberdeen, while Paul Alexander has been promoted to Sales and Marketing Director. Nicola Yates, who joined the business in December 2023, also joins the wider team as Head of Energy Transition. Together, these additions reinforce a highly capable and expert senior team, positioned to continue RelyOn’s growth trajectory across the UK in 2024.
Colin added: “By refreshing our leadership team, we’re not only demonstrating our readiness to continue to serve our customers’ existing needs, but also preparing to meet their future needs.
“We’ve been pioneering digital training solutions for some time now, and we’re already looking to what the energy sector wants next to service its evergrowing and diversifying sources.
“I’m incredibly excited to implement our expansion strategy with this team at the helm to ensure the continued success of the UK’s energy industry.”
Leading law firm for businesses Muckle LLP has appointed Ross Galbraith to its growing construction team.
Darlington-born Ross, who has nearly 10 years’ experience specialising in non-contentious and engineering law, joins Muckle as a partner.
Muckle’s construction team is ranked by both Legal 500 UK and Chambers & Partners and is best known for delivering major projects for clients across the UK and the Channel Islands.
Ross brings a wealth of specialist knowledge, having acted for a range of developers, funds, contractors and sub-contractors.
Before joining Muckle, Ross worked at a leading international law firm and, more recently, as a Legal Director at a boutique construction law firm in Leeds. In this role, Ross advised on all aspects of noncontentious construction law.
Ross said: “I’m extremely excited to be back in my home town, working for a well-established
firm like Muckle. What drew me to Muckle was its size, location and the opportunity to contribute to the team’s growth and success”.
“I have acted for various large developers including residential, commercial, and mixed-use developments. I’m looking forward to getting stuck into more complex matters and working alongside an ambitious team.”
Adam Aston, Partner and Head of Construction, said: “It’s great to be welcoming Ross to our team and he brings with him a wealth of construction expertise. As we strive to expand our offering and maintain excellent levels of services, Ross’s experience and positive approach add a valuable dimension to our capabilities”.
“This is a really exciting time for the team as we look to cement our reputation in Newcastle and seek to grow our presence across Tees Valley. Ross’ experience really fits our aspirations for growth in the region and I am really looking forward to working together.”
Nine in 10 of the UK’s SMEs believe apprenticeships are at least partly the solution to the UK’s skills gap crisis, with a further 68% of the view apprenticeships are a ‘valuable alternative to university’. Nearly half (47%) feel not enough is being done to encourage young people to consider apprenticeships.
The findings in this release are taken from the latest independent research commissioned by Close Brothers Asset Finance and Leasing, which highlights the positive impact apprenticeships make to individuals, businesses and the wider economy.
According to Government figures, 1.72 million employees in the UK workforce were judged by employers to have a skills gap (i.e. considered by the employer to be lacking full proficiency), an increase of 45,000 when compared to 2017. Overall, 15% of employers reported skills gaps, up from 13% in 2017.
A third of responding firms report having an apprenticeship scheme of their own, with many (58%) stating that if financial assistance was available from either the government or the private sector to help contribute towards wages and / or training, they would put someone from their company forward to participate in an apprenticeship scheme.
We’re proud of our relationship with Close Brothers and acknowledge their constant support in delivering apprenticeships throughout the years, helping apprentices kick-start their careers.
- Nikki Jones, director of the University of Sheffield AMRC Training Centre
The National Apprenticeship Service states 96% of employers with apprentices have experienced at least one benefit from taking on apprentices, and most can count at least eight benefits. In addition, 74% of employers say that apprentices improved products or service quality, and 78% say that they improved productivity while 73% say that staff morale is improved by having apprentices.
Steve Gee, CEO of Close Brothers’ Asset Finance’s Industrial Equipment Division, said: “As a funder of a number of sectors that rely on apprentices, we’ve long seen the need – and value - of apprenticeship schemes, which encourage new talent into industries that really need them.
“As part of our commitment to the SME community, we’ve been funding an apprenticeship scheme since 2015, in partnership with the University of Sheffield’s Advanced Manufacturing
Research Centre (AMRC). Under the scheme, we contribute strongly towards the wages of the apprentices in both the first and second, with all training costs also covered.
“The reality is, it’s not cheap for an SME to invest in apprentices – and it’s important small business owners see it as an investment and not a cost. Handled correctly, apprenticeships can help an SME flourish and at the same time develop the individual apprentice.
“I believe we all have a duty to look at where, as ‘UK PLC’, we need to concentrate our efforts and money. I would strongly encourage firms to support apprentices – we know firsthand what a hugely positive impact they can have.”
Nikki Jones, director of the University of Sheffield AMRC Training Centre said: “At the AMRC Training Centre, we’re transforming lives through apprenticeships. We combine classroom learning and shop floor industrial experience to equip new, young talent with all the skills they need to become the advanced engineers of tomorrow.
“It is crucial to invest in apprenticeships and support employers to take on apprentices to help close the huge skills gap in the industry currently. We’re proud of our relationship with Close Brothers and acknowledge their constant support in delivering apprenticeships throughout the years, helping apprentices kick-start their careers.”
Cambridge Vacuum Engineering (CVE) – a specialist in power beam welding technologies – has been shortlisted for a prestigious International Energy Award for its ground-breaking RapidWeld project. RapidWeld saw CVE work alongside industry partners to fast track the production of an offshore wind turbine monopile foundation destined for the Dogger Bank Wind Farm. During the project, CVE and the RapidWeld team demonstrated that critical pieces of energy infrastructure can be produced up to 25 times quicker if the correct electron beam welding technologies are deployed.
Organised by the Energy Institute, the annual International Energy Awards celebrate game-changing and disruptive technologies that are supporting the transition to net zero and / or extending universal access to energy. CVE has been shortlisted in the ‘International Energy Technology Award’ category, alongside five other businesses including Octopus Energy and UK Power Networks.
The RapidWeld project was funded by Innovate UK and led by a consortium including CVE, SSE Renewables, DNV, Sif Netherlands B.V., Agile NDT and The Welding Institute (TWI).
Harnessing CVE’s innovative Ebflow technology, the consortium delivered the first-ever electron beam welded section to be incorporated into an offshore wind turbine monopile foundation (transition piece). Ebflow uses a local vacuum system that creates and maintains a vacuum around only the seam that is being welded. Significantly quicker, cheaper and cleaner than conventional welding techniques, this innovative method can be used on the largest structures. During RapidWeld, CVE demonstrated that it is possible to weld monopiles far quicker than current methods. It also proved that Ebflow uses 90% less energy, costs 88% less, and produces 97% less CO2 emissions.
Now in its 25th anniversary year, the International Energy Awards attract entries from businesses across the world that are championing more sustainable ways of working. Winners are decided by an elite judging panel including some of the biggest names in the energy sector such as Dame Angela Strank DBE FRS FREng FIChemE HonFEI. Winners of the International Energy Awards will be announced at the International Energy Week Dinner on 29th February 2024 at The Grosvenor House, London.
The Energy Institute is the chartered membership body for professionals working globally across the energy
Parsionate, a data and analytics consultancy recognized by Gartner for its MDM expertise, is excited to announce that it has received two prestigious Partner Awards from Informatica, a global leader in enterprise cloud data management solutions.
The “Global Emerging Channel Partner of the
sector. A registered charity, the Energy Institute provides the skills, knowledge and good practice needed to protect the environment during operations and to advance the global energy transition required by the climate emergency.
CVE is headquartered in Waterbeach and has regional offices in Beijing, China and Massachusetts, USA, as well as a global network of agents. For more information about CVE go to www.camvaceng.com
Year” as well as the “Regional Channel Partner of the Year” awards are a clear recognition of Parsionate’s leadership in customer engagement and service execution. These honors not only validate the company’s data leadership and commitment to innovation, but also underscore the effective partnership between Parsionate and Informatica.
Tobias Wrobel, Director Ecosystem Sales at Parsionate, enthused about the awards: “Especially this first-time global recognition shows that we are on the right path in our partnership with Informatica in both strategy and execution. The partnership with Informatica is of strategic importance to us and these awards are a testament to the commitment and hard work of our team.”
As a boutique consultancy focusing on strategy, consulting, implementation and supervision of customer solutions in the area of data & analytics, Parsionate has established itself as a trusted partner for Informatica.
The popular Big Bang Fairthe UK’s largest celebration of science, technology, engineering and maths (STEM) for young people - is set to return this summer.
The annual Fair, which is run by EngineeringUK, is designed to ignite a passion for STEM and showcase the exciting career possibilities in these sectors.
Taking place from Wednesday 19 to Friday 21 June 2024 at the NEC in Birmingham, The Fair will welcome students aged 10 to 13 from across the UK. From today, schools and home educators can register for free tickets to attend.
A diverse range of employers will come together at The 2024 Fair to bring engineering and tech careers to life – from the aerospace, rail and automotive industries to energy, healthcare and more. This gives young people the opportunity to meet STEM professionals, as well as join exciting live shows and inspiring career panels. There will also be plenty of hands-on activities to get stuck into, including testing their driving skills by putting powerful robots through a series of challenges, experiencing piloting a submarine, discovering how different materials are used in sports and space exploration and much more.
Given the UK’s acute skills shortage and ambitions to meet
net zero by 2050, we urgently need more young people to progress into engineering and technology. STEM engagement activities such as this are vital for developing their awareness and interest in these careers - helping the sector to secure a skilled and diverse future workforce.
Also taking place at The Fair, will be the awards ceremony for the popular Big Bang UK Young Scientists & Engineers Competition. Winners will be announced, including the crowning of the prestigious Big Bang UK Young Engineer, UK Young Scientist and UK Young Technologist of the Year, supported by Siemens.
The Competition, which is free to enter, is open to young people in the UK aged 11 to 18 in state funded education, who are home educated or who enter as part of a community group. There’s still time for young people to get involved – with The Competition open for entries until 27 March.
With tickets for The Big Bang Fair always booking up quickly – schools are advised to book their free tickets early, to avoid disappointment.
To find out more about exhibiting and sponsorship opportunities for The Big Bang Fair 2024 and The Big Bang Competition – email partnerships@engineeringuk. com
A leading manufacturer of industrial heat exchangers is warning engineers and those specifying heat exchanger installations not to underestimate the effects of material fouling on performance. Light fouling can impact the heat transfer process, reducing energy efficiency or preventing the heat exchanger operating within its designed parameters. In extreme cases, fouling can completely block heat exchangers, requiring significant intervention to remove or replace the affected equipment.
Watford-based HRS Heat Exchangers says that in many cases the effects of fouling can be reduced by specifying the correct type of heat exchanger in the first place.
Limescale build up in heat exchangers can be prevented by dosing the solution with suitable chemicals, such as acid salt, while chemical agents are required for cleaning or removing limescale deposits.
“Heat exchangers can be particularly susceptible to the effects of fouling when they handle difficult materials, such as sewage sludge or corrosive chemicals,” explains Matt Hale, International Sales & Marketing Director at HRS. “Fouling can generally be divided into one of four categories: chemical fouling, biological fouling, deposition (or sedimentation) fouling, and corrosion fouling. Prevention is always better than cure, but as each type of fouling is caused by a different combination of chemical and physical reactions, prevention requires different actions in each case.”
Chemical fouling can take many forms but is caused by the deposition of different chemicals found in the solution being treated. Limescale (usually a mixture of calcium and magnesium) is the most familiar chemical fouling agent, regularly building up in our kettles and pipework. Limescale build up in heat exchangers can be prevented by dosing the solution with suitable chemicals, such as acid salt, while chemical agents are required for cleaning or removing limescale deposits.
Struvite (magnesium ammonium phosphate) is a phosphate mineral which can be a problem in sewage and wastewater applications. Keeping water temperatures below 65°C will help prevent struvite formation, as will restricting the amount of phosphorus added to sludge digesters.
Another chemical which causes fouling is vivianite (ferrous phosphate), a particular problem where ferric chloride (pickle liquor) is added to sludge to control hydrogen sulphide (H2S) emissions. Prevention also relies on keeping operational temperatures below 65°C.
Various forms of biological fouling can occur in heat exchangers. Algal fouling is often encountered where untreated river water is used for cooling. Environmental regulations may prevent the use of chemical additives, so using high water velocities or scraped surface heat exchangers can prevent algal fouling.
In some wastewater treatment sites, final filtered effluent (FFE) taken after the filter press is used as a free cooling medium. However, due to the high level of biological material contained in FFE, it has a high fouling potential and fouling can quickly occur, depending on the exact nature of both the FFE and the heat exchanger design. UV treatment can reduce the biological load, but the
use of scraped surface heat exchangers is the most efficient way to prevent this type of fouling.
Deposition fouling occurs when particular materials present in a mixture or solution drop out and attach themselves to the heat exchanger surface. Fouling from sediment is the most common type of heat exchanger fouling seen. It can usually be prevented by good heat exchanger design. For example, making sure that the fluid has sufficient velocity and pressure; the use of corrugated tubes to prevent sedimentation; or specifying scrapedsurface heat exchangers to continually remove sediment to ensure efficient operation.
Burn-on fouling occurs when fluid temperature is too high, causing sediment (particularly organic materials) to become baked on to the heat exchanger surface, and can occur where a malfunction has occurred. Control of water temperature (keeping it below 80 °C) will also help prevent burn-on.
Corrosion fouling usually occurs in specific circumstances where either the material being treated, or the construction of the heat exchanger itself, is particularly susceptible to corrosion. For example, aluminium and copper can be highly reactive and frequently suffer from galvanic corrosion or the formation of oxides on the tube surface. Specifying a heat
Deposition fouling occurs when particular materials present in a mixture or solution drop out and attach themselves to the heat exchanger surface.
exchanger manufactured in a material which is resistant to such corrosion, yet maintains good thermal transfer properties, such as stainless steel, will overcome most of these issues.
“In all cases, good heat exchanger design can greatly reduce the incidence of fouling, or assist with regular cleaning,” comments Matt Hale. “Many factors, such as increasing turbulence through the use of corrugated tubes, using rotating or reciprocal scraper surface heat exchangers, choosing the right construction materials, designing integrated system failsafes, and facilitating servicing with easily removable tubes can all be employed to prevent, reduce or manage fouling so that heat exchangers work more efficiently for longer with minimal interference.”
For more information: hrs-heatexchangers.com
Titan
a leading design and manufacturer of innovative end user and OEM high-performance flow meters, used
a wide range of environments and applications.
• Compact, robust, reliable
• Excellent accuracy and repeatability
• Measure low to high flow ranges
• High chemical resistance
• OEM bespoke design capability
REQUEST
•
•
•
In the rapidly evolving field of Additive Manufacturing, the globally leading 3D printing service bureau CRP Technology unveils Windform SL, a groundbreaking material for Powder Bed Fusion/Selective Laser Sintering professional 3D printing. As the twelfth addition to the prestigious Windform TOP-LINE range (created by CRP Technology), Windform SL marks a significant leap forward in the AM industry.
Windform SL, a black polyamidebased composite reinforced with carbon fibers, is exceptionally light, as indicated by the “SL” designation, standing for “Super Light,” and boasts a density of 0.87 g/cc. This unique combination of characteristics, blending lightness and rigidity, positions Windform SL as a premium material.
The market debut of Windform SL, occurring just a few months after the introduction of CRP Technology’s second elastomeric material (Windform TPU) and the eleventh addition to the TOP-LINE range, reaffirms the company’s unwavering commitment to innovation in the realm of 3D printing.
Windform SL is particularly well-suited for producing functional
prototypes and components in the UAV/UAS sector, and applications demanding a balance of lightness, stiffness, and thermal resistance.
The HDT at 1.82 MPa of 182.5 °C, combined with high values of Specific Tensils Modulus, Specific Tensile Strength, and Impact Strength (Charpy and Izod), are among the key features of Windform SL. These characteristics indeed provide it with the ability to maintain structural stability under intense stress, even at elevated temperatures, ensuring reliable performance in demanding environments.
The post-process surface finish is equally noteworthy, with Ra values of 5.44 µm after the SLS process, 1.56 µm after manual finishing, and 0.83 µm after CNC processing, ensuring smooth and precise surfaces.
Windform SL is more than just a material; it is an advanced solution for the future of professional 3D printing. With broad applications in the UAV sector and beyond, Windform SL promises to revolutionize the production of sophisticated and efficient components across various fields, from aerospace to automotive, ensuring lightweight without the need to reduce thickness.
MCP998x family represents one of the largest automotive-grade remote temperature sensor portfolios available from a single vendor
Thermal management is a critical aspect of automotive design, yet compared to many other components, there is a noted lack of options when it comes to multichannel remote temperature sensors.
Speed Reducers New line builds upon success of original series with customer-sourced innovations
This high temperature tolerance makes them wellsuited for automotive applications where operating temperatures for electronics is a major factor.
To fill this gap, Microchip Technology has launched the MCP998x family of 10 automotive-qualified remote temperature sensors. The MCP998x family is one of the largest portfolios of automotive-grade multi-channel temperature sensors in the industry and is designed for 1°C accuracy at a wide operational temperature range. The device family includes five sensors with shutdown temperature setpoints that are designed not to be overwritten by software or maliciously disabled.
With up to five channels of monitoring and several alert and shutdown options for security, this product family can support systems that supervise more than one thermal element. The remote sensors also integrate resistance error correction and beta compensation, eliminating the need for additional
700 Series Worm Gear Speed Reducer. The SS700 Gen2 stainless steel speed reducer is an evolution of its first-generation series that has served the food and beverage industry for over 10 years.
The NSF-certified SS700 Gen2 is designed with innovative new features sourced directly from customers’ feedback on the widely popular firstgeneration series. An improved Domed Crown™ curved design eliminates virtually all pooling of liquids during washdowns. Its 316-grade stainless steel construction offers enhanced benefits in durability and hygiene over painted, coated and aluminum alloy speed reducers for food and beverage applications. The SS700 Gen2 has an IP69K-rated stainless steel enclosure, compliant with IEC 60529 and capable of withstanding washdown nozzle pressures up to 1450 psi at four inches without water ingress.
New field-installable, FSMA and OSHA-compliant shaft covers protect against potential food traps while eliminating safety risks associated with
configuration for improved accuracy. Monitoring temperatures at multiple locations with a single, integrated temperature sensor reduces board complexity and size and simplifies design for a lowered bill of material (BOM).
More accurate where it counts, designed for 2.5°C accuracy up to 125°C, the MCP998x device family can be used at the high end of the traditional temperature range where many competitors are challenged. This high temperature tolerance makes them wellsuited for automotive applications where operating temperatures for electronics is a major factor. The MCP998x sensors are designed to support vehicle functions including HID lamps, advanced driverassistance system (ADAS), automotive
rotating elements. An optional tapered bushing eliminates the need for troublesome keys and keyways on the output shaft, removing opportunities for food traps, pathogen formation and sharp edge safety hazards, while mitigating customer shaft damage costs from galling damage that can occur over time.
SS700 Gen2 Series speed reducers offer high energy efficiency along with the lowest operating temperatures available. The series features larger output shaft bore sizes that enable the selection of smaller speed reducers, especially in low-torque or low-duty applications, providing the opportunity to downsize product selection (offering savings in weight, envelope size and cost) and standardize conveyors throughout customers’ facilities.
The new SS700 Gen2 Series is backward compatible with the 700 Stainless Steel series, and newgeneration counterparts can act as drop-in replacements for firstgeneration models. The new series is manufactured at the company’s
servers, video processing, infotainment systems, engine control, telematics and body electronics such as seat control, lighting systems, mirror control and power windows. Visit the website to learn more about Microchip’s full portfolio of temperature sensors.
To enable easier design and development, the MCP998x family is supported by the new EV23P16A evaluation board.
For additional information and to purchase, contact a Microchip sales representative, authorized worldwide distributor or visit Microchip’s Purchasing and Client Services website, www.microchipdirect.com.
headquarters in Charlotte, North Carolina, and available with standard lead times of two days or less, as well as our industry-recognized Reducer Express™ Same Day service for urgent requirements.
For more information about the new Boston Gear SS700 Gen2 Series, visit www.bostongear.com/ss700gen2.
Anthony Lamoureux, CEO of Velocity Smart Technology, sheds light on the evolving landscape of smart locker and smart vending solutions in manufacturing and engineering.
In large manufacturing sites or engineering centres, effective asset management is crucial for maintaining smooth production line operations. The challenges in IT support, particularly in diverse asset management and production line interruptions, have prompted a much-needed surge in interest in digital solutions. Indeed, with only 24% of manufacturing companies having a digital transformation strategy - there is a huge opportunity for improvement.
In the intricate web of machinery tools and components within manufacturing plants, misplacing or inadequately tracking high-value assets can lead to significant financial losses and any interruptions in production line activities are equally as costly. This makes effective IT asset management a key component for ensuring continuous efficiency.
The challenges in IT support, particularly in diverse asset management and production line interruptions, have prompted a much-needed surge in interest in digital solutions.
Beyond this, additional issues are also seen in tackling ongoing supply chain risks through technological interventions i.e. utilising automation to overcome obstacles in new product development; implementing strategies to navigate workforce challenges; and incorporating additive manufacturing for sustainable practices. Add to this the constant struggle to ensure engineering tools are readily available and you begin to ponder ‘There must be a better way?’
A majority (72%) of respondents from our research into the manufacturing and engineering sectors have expressed their willingness to invest in digital workplace technology. This widespread appetite goes against the lack of a digital strategy mentioned earlier, and underscores the growing need for recognition of technology’s potential to elevate productivity and streamline processes for both employees and IT support staff.
Boosting production line efficiency can be achieved through the implementation of smart lockers and smart vending systems, which ensure the ready availability of critical tools and spare parts. The automated check-out and check-in processes play a pivotal role in minimising disruptions, fostering a streamlined workflow.
These intelligent systems provide proactive alerts for maintenance tasks, allowing for timely interventions to uphold optimal operational performance which, again, contributes significantly to the enhancement of production efficiency and the overall management of resources. This is the change which is needed in the manufacturing and engineering industry in 2024.
Elevating tool availability and efficiency can be achieved through streamlined tool management practices. By gaining insights into asset utilisation patterns, organisations can make informed decisions about tool allocation, ultimately reducing costs and enhancing overall efficiency.
An optimised tool management system not only ensures that the right tools are readily available when needed, but also contributes to a more cost-effective and efficient operational workflow, aligning with the goal of maximising resource utilisation.
The benefits derived from smart lockers and smart vending systems are notable,
and by managing these through centralised platforms, exemplified by integrating the world’s first ServiceNow Built On Now certified application, Asset Managers get peace of mind through having a streamlined approach to tracking and managing a diverse array of assets.
Integrating with ServiceNow enhances these advantages by ensuring a seamless operational experience, capable of accommodating various asset types and configurations.
This integration not only optimises asset management but also contributes to a more cohesive overall organisational workflow, illustrating the efficiency and versatility that smart lockers and smart vending systems bring to manufacturing and engineering providers.
Manufacturing and engineering providers are undergoing a transformative shift propelled in part by new investment in 2024, but also as a result of a necessity for effective asset management and the increasing demands for modern digital solutions.
Manufacturing and engineering industries across the world all face these challenges. Yes, some might be further down the path of their digital transformation journey, but there are still clear and tangible gains to be achieved
Regardless of where you are on your journey towards a more efficient, connected, and sustainable future, make sure it is marked by the strategic integration of digital solutions.
through the widespread adoption of smart technologies and innovative solutions. More centralised platforms, smart lockers and smart vending systems hold the key to overcoming operational hurdles.
So regardless of where you are on your journey towards a more efficient, connected, and sustainable future, make sure it is marked by the strategic integration of digital solutions.
By leveraging the power of technology, organisations not only equip themselves better to navigate the challenges of today but also position themselves at the forefront of innovation, future-proofing their competitive edge in an everevolving industry.
The first Lifting Equipment Technician apprentice will be undertaking their End Point Assessment at the LEEA workshops in Huntingdon on 15th March 2024.
The assessment will be conducted by the End Point Assessment organisation, LEIA (Lift & Escalator Industry Association) and will include a multiple-choice exam paper, professional discussion and practical assessment using a range of lifting equipment.
Andrew Wright, Head of Learning and Development at LEEA said: “We are delighted that the very first apprentice will soon be completing their End Point Assessment, followed by three further apprentices on 25th March, 22nd and 26th April and we wish them every success. The formation of the apprenticeship trailblazer group was facilitated by LEEA at LiftEx 2018 in Milton Keynes. An enormous amount of work, carried out by a number
of organisations, followed to get the Lifting Equipment Technician apprenticeship up and running.”
Wright added: “It is encouraging to see that training providers are reporting that new cohorts are planned for this year with several apprentices having signed up already. LEEA will provide support wherever we can.”
The Level 3 Lifting Equipment Technician Apprenticeship is only available to residents of England at companies registered in England. It opens up a wide choice of opportunities to work with lifting equipment in all kinds of applications and career paths. Apprenticeships generate a new breed of experts that can keep pace with the changing world of lifting around them and provide a great first step towards a career in the Lifting industry.
Visit the Institute for Apprenticeships for more information of the Lifting Technician Apprenticeship.
DuPont™ Tedlar® and the SPE (Society of Plastic Engineers) Foundation announced that two students have been awarded the DuPont™ Tedlar® Scholarship for academic study focused on plastics engineering. Each scholarship recipient received $2,500 to support their studies in STEM. The scholarships are part of a year-long partnership between DuPont™ Tedlar® and SPE to support the Foundation’s three-pronged approach to enrich and develop the future workforce for plastics industry.
The two scholarship recipients are Cameron Sawicki, a junior at Ferris State University majoring in Plastics and Polymer Engineering Technology and Michael Quinn, Jr., a senior at Penn State Behrend majoring in plastics engineering technology.
“Receiving this scholarship is a significant milestone in my academic journey,” said Michael Quinn, Jr. “I’m determined to give back to the community and make a positive impact, just as DuPont™ Tedlar® has done through this scholarship program.”
DuPont™ Tedlar® and the SPE Foundation partnered in 2023 to enable these scholarships, as well as developing a PlastiVan® curriculum to travel to schools for STEM educational days. Furthermore, Tedlar® sponsored the Girl Scouts of America event in Orlando, Florida, providing demonstration material and support. This collaboration has been extended through 2024, with Tedlar® helping to expand the PlastiVan® program as well as continued work with the Girl Scouts of America. Tedlar® and the SPE Foundation are focusing on classrooms and STEM education in Buffalo, NY, and Circleville, OH, two locations where Tedlar® is manufactured.
To
Apprenticeship Week (5 to 11 February), BGEN -
of the
largest engineering firms driving the energy transition - has pledged to expand its apprenticeship programme to 75 employees by the end of this year.
50 apprentices already work for the company, each receiving valuable vocational training and study to achieve industry-recognised qualifications. Apprenticeships range from Level 3 to Degree and are in a variety of disciplines - enabling recruits to forge careers as electricians, mechanical engineers and pipefitters, as well as quantity surveyors, and network and systems engineers.
The scheme is also being used to upskill a further ten existing BGEN employees - enabling BGEN to grow talent through the provision of learning
opportunities for career development.
To invest in its future and create a more diverse workforce, BGEN has already doubled its apprentice headcount over the last two years. 2024’s planned intake follows several recent new business wins and supports the firm’s ambitious targets for further growth.
The company hosted a National Apprenticeship Week event, to bring together its cohort.
Michelle Stott, HR Director at BGEN, said: “We’re widely recognised as being an employer of choice for both skilled tradespeople and office-based professionals, which is why many of our employees have been with us for over three decades, during which time we’ve supported their career development within the organisation.”
Danfoss Power Solutions, a leading global supplier of mobile and industrial hydraulics as well as electric powertrain systems, has partnered with Australian crane manufacturer Franna to improve the performance of its MAC 25 crane. With the PVG 48 proportional valve at the heart of the work and steering subsystems, Danfoss is delivering a reliable, precise, future-proof solution.
Franna, a Terex brand, is a leading manufacturer of pick and carry cranes with a rich heritage of design and engineering excellence. For more than 40 years, Franna has been a leader in the Australian market, and today its products are at work in more than 30 countries across the globe.
Franna’s MAC 25 mobile articulated crane features a maximum lifting capacity of 25 tonnes (27 tons) and a maximum boom length of 18.4 meters (60 feet). The crane offers maximum safety, excellent roadability, intuitive operation, and unmatched versatility. True to
• WISE-4250 redefines data acquisition efficiency.
• Cut wiring costs with the dualband 2.4/5 GHz Wi-Fi I/O
• Smart roaming for reliable connections
• Remote and diverse I/O management
Advantech has introduced the new WISE-4250 dual band based Industrial Wi-Fi I/O Module. The WISE-4250 features interchangeable I/O and sensors integrated with IoT data acquisition, processing and publishing. Data can be sent directly from Edge to Cloud with higher security and no loss functions. All Wi-Fi channels can be flexibly connected with a smart roaming function. Users can directly configure products with devices via a HTML5 based web page user interface. Products support RESTful API in JSON format for any IoT integration.
The WISE-4250 supports 2.4/5GHz dual band concurrently, enabling leverage of both frequencies at the same time, reducing wireless interference against device data transmission delay. Diverse I/O modules support a wide range of data
acquisition. WISE-4250 provides a number of embedded drivers which can easily plug-and-play with wireless modules. The data logger provides data resume functions ensuring zero data loss during on-line, off-line and power off situations. Users can easily find real data with RTC time stamps.
Secure Edge-to-Cloud AES encrypted security is built-in with 802.1x, up to WPA3 Personal and Enterprise, and effortlessly configurable via P2P (peer to peer) functions with mobile devices. Push data to SCADA, the cloud, or private servers while integrating IoT through RESTful web APIs or diverse protocols.
The WISE-4250 features and
industrial-Grade design suitable for use in harsh environments. The device will operate over wide temperature and humidity ranges and provides voltage endurance. Diverse mounting methods and fast roaming simplify implementation in a wide variety of applications.
The Advantech WISE-4250 is available now, contact your local sales team or visit the website www.advantech.com/en-eu for more information.
A video demonstration is available to view here https://www. advantech.com/en-eu/resources/ video/wise-4250-dual-band-wi-fiwireless-io-module
the company’s heritage, the crane’s design has been tested, proven, and continuously improved over the years.
In 2021, Franna began looking at other options for the MAC 25 crane’s main control valve. The company required a solution that was precise, reliable, and future proof to accommodate increasingly sophisticated electronic control systems. The Danfoss PVG 48 proportional valve, then in development, emerged as the superior solution.
PVG 48 is a pre-compensated proportional control valve for applications requiring flow rates of up to 180 liters per minute (47.6 gallons per minute). The latest member of the PVG load-sensing valve family, PVG 48 is ideal for machines such as wheel loaders, aerial lifts, and cranes in which precise flow and controllability are essential.
Danfoss launched the PVG 48 valve to the general market in June 2023 with Franna as a key pilot customer. On the MAC 25, the valve turns operator joystick inputs into quick, accurate boom movement.
The PVG 48 valve integrates easily with electric actuators, sensors, and digital controls, opening a range of possibilities. One of them is to automate certain machine functions so the crane assists – or even takes over from –the operator. Such a function can be advantageous in many situations, particularly when instant reaction is required to ensure safety.
With the change to PVG 48, Franna also switched to Danfoss counterbalance valves. Together with PVG 48, they ensure smooth and safe activation of the crane’s boom.
The Danfoss PVG 48 proportional valve is already at work in more than 100 of Franna’s MAC 25 cranes throughout Australia.
To learn more, read the full Franna MAC 25 success story.
Bespoke
from
Embedded designed to meet the rigorous demands of industrial environments
Impulse Embedded’s Senior Production Technician, Andy Shaw, recently built a VELA Rack PC that was designed to meet the rigorous demands of industrial environments.
Impulse Embedded’s workshop team builds such powerful bespoke computers to customer’s exacting specifications to create fully robust computers that can easily integrate into any pre-existing system.
The VELA, powered by Advantech, is Impulse’s flagship series for industrial computing. It is built, configured, tested and shipped from their facility in Newcastleunder-Lyme and is available in both rack and tower formats. Because they keep all the component parts in stock, the VELA series can ship anywhere within the UK with a quick turnaround.
In this recent order for an ongoing project with a fixed BOM,
Impulse Embedded integrated carefully chosen components to meet the customer’s demands for their application. The rack PC has an Intel Core i5-10500TE 2.3GHz processor, an Intel embedded CPU that guarantees availability for at least seven years from release date, which is vitally important for this customer to save on software redevelopment costs.
Impulse Embedded takes pride in delivering custom solutions that empower businesses across the UK to excel. Their collaboration with their valued customers and preferred technology partner, Advantech, enables them to constantly push technological boundaries and supply only the highest-quality devices.
For further information regarding Impulse Embedded’s VELA series, please get in touch with their knowledgeable team at 01782 337 800 or email sales@ impulse-embedded.co.uk.
With stricter reporting standards expected there is a risk manufacturer are not fully prepared, especially given disparities in approaches to reporting of Scope 1, 2 and 3 greenhouse gas (GHG) emissions. Product strategies are increasingly looking at quantifying positive impacts by calculating avoided, or Scope 4 emissions. Here, Paul Bansil, Director KBR Consulting International explores the challenges facing manufacturers in capturing GHG data.
Some of the largest UK manufacturers are required to report on their Scope 1 and 2 GHG emissions annually through the Government’s Streamlined Energy and Carbon Reporting framework (SECR). Reporting on Scope 3 emissions however remains largely voluntary.
Accurate GHG data remains a challenge, not least because of the abundance of approaches which often makes industry comparisons difficult. Furthermore, variances in standards, such as between the GHG Protocol and US GAAP, often necessitates external expertise to ensure accuracy. As a result, industry efforts have all too often adopted qualitative assumptions or rely on carbon offsetting
schemes; compromising the quality of the data reported and limiting its value for future operational decisions.
Whilst qualitative methods should not be entirely disregarded there is a clear need for a more verifiable data-led reporting approach based on engineering analytics. This will help increase transparency as regulations become stricter and offers significant CAPEX advantages as businesses identify emission reductions efficiencies in their processes.
Achieving this demands a concept engineering approach in terms of the type of data required and how it is analysed. This is something we understand and use to raise the bar for the reporting and analysis of GHG emissions and over five stages:
Descriptive analytics offers a historical perspective on emissions and enables
organisations to set a benchmark. With this in place it’s possible to develop a plan for reduced emissions.
Having a clear view on the wider scope of specific emission levels is also important. Diagnostic analytics can play a significant role in this - leveraging data sources and utilising graphical visualisations to provide clarity on trends and patterns.
Predictive analytics, enhanced by machine learning, can highlight possible future outcomes and can be used to show the environmental impact of any changes in production design and output.
Prescriptive analytics are useful for refining designs to minimise carbon footprint. By utilising simulations and providing suggestions, it paves the way for robust decarbonisation strategies.
As with all science, it’s essential to explore alternatives. Cognitive analytics allows manufacturers to explore ‘what if’ scenarios. Such exploratory thinking can foster better understanding towards lowcarbon energy solutions.
Being able to accurately analyse the different levels and sources of data, from descriptive through to cognitive, however, requires tools, software and a proven methodology to become universally accepted.
KBR has invested in the development of technologies to report and reduce GHG emissions as well as bespoke solutions to gather and analyse lifecycle data, enabling businesses to make better informed decisions on their glidepath to Net Zero.
To
• Manifolds, Needle, Check and DBB Valves to 22.5K psi
• Cryogenic
• Severe Service 650ºC, 10K psi
• Forged & Bolted Construction
• Instrumentation, Ball, Needle and DBB Valves for Hydrogen and Carbon Capture Applications
• Pipeline Ball Valves upto 18”
• 1” to 20” Bore Size
• High Temperature
• High Pressure
• Cryogenic
• API 10K Design
• 10K Ball Valves for Hydrogen Fuelling Stations
• Diver & ROV Operated Needle Valves
• Ball Valves Upto 15K
• Manual & Hydraulic Parallel Slide Gate Valves