MEASUREMENTS
MEASURING COLOUR IN INDUSTRIAL PROCESSES
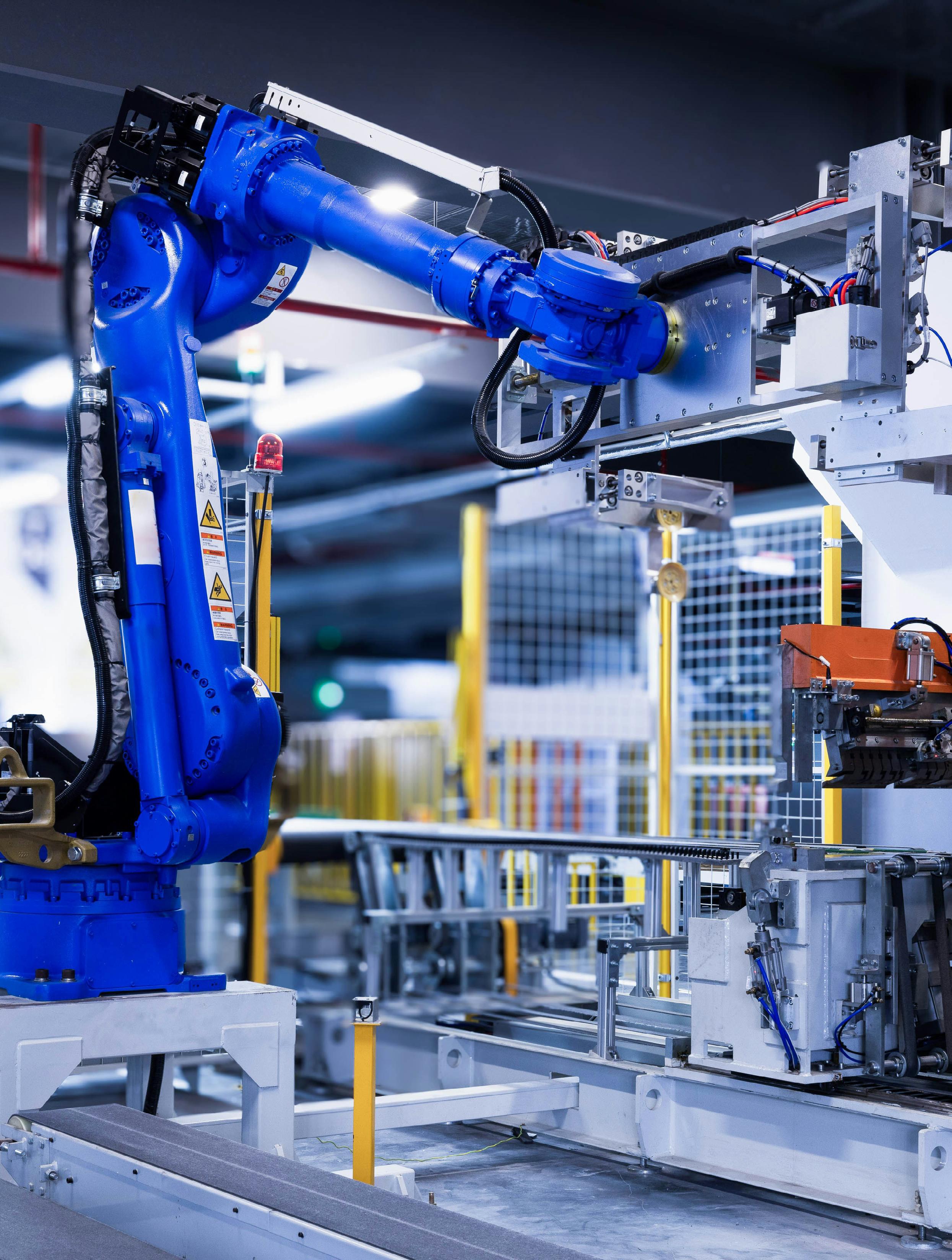
TRAINING & EDUCATION
£14M BOOST FOR NEXT GENERATION MANUFACTURING
MANUFACTURING PRODUCTION
ENGINEERING
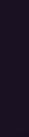


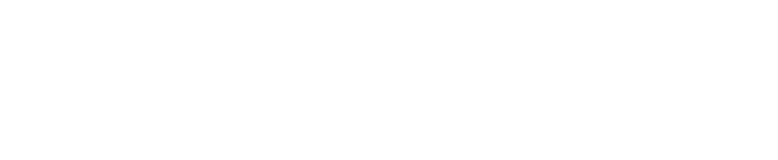
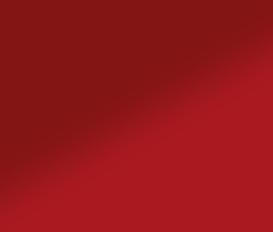
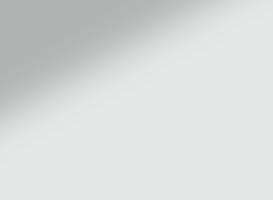



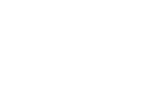

MEASUREMENTS
MEASURING COLOUR IN INDUSTRIAL PROCESSES
TRAINING & EDUCATION
£14M BOOST FOR NEXT GENERATION MANUFACTURING
MANUFACTURING PRODUCTION
ENGINEERING
forge transparent partnerships as we simplify the complexities of marketing for all our customers. Since 2005, our mantra has been: success will look after itself.”
We look after your marketing from start to finish!
Editor
Paul Attwood editor@mpemagazine.co.uk
Senior Editorial Assistant
Anna Startin editorial@mpemagazine.co.uk
Features Editor
Harry Peters editorial@mpemagazine.co.uk
Production/Design
Laura Whitehead laura@lapthornmedia.co.uk
Sales Manager
Charlotte Chapman charlotte@mpemagazine.co.uk
Accounts
Richard Lapthorn accounts@mpemagazine.co.uk
Circulation Manager
Leo Phillips subs@mpemagazine.co.uk
Publishing Director
Maria Lapthorn maria@lapthornmedia.co.uk
Lapthorn Media Ltd
5-7 Ozengell Place, Eurokent Business Park, Ramsgate, Kent, CT12 6PB
Tel: 01843 808 102 06 12 23 29 44
Interview with Donna Green, an engineering professional turned FE teacher £14M boost for next generation manufacturing
New ESG team will drive Toyota’s sustainability plans
Bruno Teuber explains how manufacturers can adapt to the digital selling landscape Sealy UK expands leadership team as it plans for continued growth
Welcome to the latest issue of Manufacturing & Production Engineering Magazine.
In this edition we have a case study by Auto-Trail V.R. and AXYZ, about how Auto-Trail have implemented AXYZ’s advanced CNC routing technology into the processes for their motorhome and campervan production, which has resulted in improved efficiency and product quality.
We conduct an interview with Donna Green, an engineering professional who took her experience and knowledge into the classroom to become a teacher in further education. We also hear from David Malan, Sales Director in UK & Ireland for DocuWare, who tells us about the advantages of digitalisation in manufacturing, from productivity and profitability to sustainability and security.
We hope you enjoy this issue and as always, if you have any news that you would like to feature, please email details to editorial@mpemagazine.co.uk.
Precision craftsmanship has paved the way for the two halves of the expansive Fan Plaza at Everton Stadium to come together.
So far, work on the 30,000m sq plaza has been undertaken in two sections, with the busy vehicle access road slicing through the middle.
Now, following the relocation of all deliveries to the north end of the stadium, the specialist Laing O’Rourke stone contactors are fully-focused on combining the two paved sections to inch-perfect precision.
A further level of complication sees the heritage assets being reinstalled as the plaza grows.
That means many more of the historic railway lines, dating back to the dock’s heyday as a distribution point for goods
heading into and out of Liverpool, being integrated into the final design.
Skilled craftsmen from Vetter, who are part of the Laing O’Rourke group of companies, have worked diligently through all that the weather could throw at them during the 52-week programme to create the fan plaza.
And Ruddy is full of praise for the workforce in keeping the landscaping scheme firmly on track for completion in late summer.
The AJ Bell Great Birmingham Run, this year held on May 5th, is the Midlands’ biggest running event, challenging participants to run either a half marathon or a 10K around the Birmingham city centre.
Over 14,000 people are believed to have participated, with many businesses and individuals raising money to support local charities and causes of importance.
Starting and finishing in the heart of the city, the event provided participants and spectators with an extraordinary atmosphere, with top en-route entertainment, an event village offering plenty of activities as well as a post-race party zone.
This year, Birmingham-based engineering firm adi Group took part with a team of 17 people, raising an incredible £2,600 in support of Birmingham Children’s Hospital Charity.
Supporting over 100,000 sick children from across the UK, the charity strives to raise vital funds to make a real difference to all who use the hospital’s services, spaces, treatment and equipment, offering the best experience possible.
As adi Group’s selected charity of the year for the second year, the firm has pledged to offer its support in a variety of ways. As a result, its employees regularly get involved in its large annual calendar of events, including a range of volunteering and fundraising opportunities.
The team has so far supported the hospital with electrical remedial works, site clean-up, planting trees, purchasing and delivering Christmas presents to children in care, as well as purchasing a sensory pod the hospital had on hire, an essential piece of equipment for the children visiting the hospital.
A stark gender gap in young people’s interest in engineering and science and a sharp decline in practical science have been identified through a new survey by the Royal Society in partnership with EngineeringUK, with support from Wellcome.
The third Science Education Tracker included specific questions about engineering for the first time in this 2023 survey. The tracker looked at the responses of 7,000 young people around their attitudes to and experience of science education and careers.
For those not interested in a STEM (science, technology, engineering and maths) career, girls are more likely than boys to say this is because they don’t enjoy the subjects (57% vs 41%)
and that they don’t feel they are good at them (38% vs 20%).
Across all age groups, boys report much higher knowledge of engineering careers than girls and are more likely to say engineering is something for them. Only 12% of girls say being an engineer fits well with who they are compared to 38% of boys. And just 16% of girls think a career in engineering is suitable for someone like them, this is up at 44% of boys.
Doing practical science is the key motivator to learning science (52% of year 7 to 9 students), with girls statistically more likely to say this. Yet, opportunities for hands-on practicals are in decline in school, with only 26% of GCSE students doing practical work at least once a fortnight.
Only 12% of girls say being an engineer fits well with who they are compared to 38% of boys.
70% of students across secondary schools say they want to do more and the appetite for more practical work is higher among students who are generally less engaged with science. This includes students who say they aren’t interested in science or who see science as ‘not for me’. 32% of young people in years 7 to 13 are in the ‘not for me’ group and this group is more likely to include girls. Indeed, 36% of girls say science is not for them.
The Science Education Tracker report and further information is available at www.engineeringuk. com/set.
Manufacturing & Production Engineering Magazine speaks with an engineering professional turned FE teacher, Donna Green.
Firstly, could you tell us more about the start of your engineering career and your experience within the engineering sector?
I always wanted to be an engineer but was always told that it was ‘boy’s job’, so I built a career in administration instead. However, when I was in my mid-30s I decided to pivot my career and re-train as a computer-aided designer at an electrical engineering company. I really enjoyed the subject and after receiving my qualification, I started to think about how I could share these skills with others.
What inspired you to transition into the Further Education sector?
After 8 years working and studying for my higher diploma, the Head of the Engineering Department at the College asked me if I had ever thought about further education (FE) teaching. I jumped at the chance.
Seeing the passion of the teachers at college when I was a student, the appeal of each day being different, the open-minded approach of staff and the environment that I was learning in that made me want to join and be a part of it.
Teaching is a vocation, but if you do take it on and the shoe fits, it’s a lovely shoe to wear. If you have a passion for your sector and real-world industry skills, you already have what it takes to
be a further education teacher, your skills are so much more valuable than you realise!
Have you experienced any barriers entering the industry?
I haven’t experienced any barriers entering the industry as companies are usually open to the best candidate for the role. However, stereotypes do still exist, for example sometimes I find people assume I’m working in an admin-based role at my company rather than as a lead engineer. But this is why role models, particularly in
further education, are so important to help break down these stereotypes and convince more women and girls that this is an industry for them too.
Can you talk about the valuable training opportunities you each offer to students?
I believe that teaching the practical skills of engineering in a creative manner allows for students to think outside the box to solve problems. Lessons don’t just take place in the classroom. Instead, teaching in FE is varied and can take place
in workshops, on-site or anywhere that allows learners to get hands-on experience in their field.
In your opinion how does Further Education engineering opportunities benefit students?
Further education (FE) is any formal learning for those aged 16+ that is not a degree and within Engineering and Manufacturing covers a wide range of subject areas from Mechanical or Civil Engineering to Electronics or Welding.
Learners in FE are diverse and can range from those who have just finished their GCSEs to adults of all ages looking for a career change or to follow a passion. But they are all connected by the curiosity of learning how things work. You can feel their excitement in the room when we are looking into some real-life industry cases. It really helps bring the theory to life and gives learners the opportunity to gain hands on experience in situations they’re likely to come across in industry. This is why it is so vital to have more industry professionals deliver FE courses.
What is your proudest achievement within the industry?
I’m always proud to see what my former learners go on to achieve, for example, one former learner has become the youngest female ever to receive a code welder certification on the Isle of Wight. This is just one of the examples of how much women have to offer to the industry! Despite all stereotypes, women prove to be great engineers every day.
Slowly and steadily the message is getting out there and we are seeing increasing numbers of female students, which is brilliant.
I’m so grateful for this excellent opportunity to be a further education teacher who can help other women make their first steps in the engineering industry. Teaching in FE is a great a way for me to stay connected to my industry whilst inspiring the next generation of engineers and passing on my trade.
Engineering offers a multitude of routes so don’t be afraid to set your own path. Even if you’re unsure about your specific interests, give different areas a try.
- Donna Green
What would your advice be to young women wanting to enter the industry?
Engineering offers a multitude of routes so don’t be afraid to set your own path. Even if you’re unsure about your specific interests, give different areas a try. The skills you acquire along the way will open doors you may not even expect.
To find out more about how you could share your existing industry skills by teaching further education and the next steps to take, visit gov.uk/ teach-in-further-education
Stargate Hydrogen, a pioneering force in green hydrogen solutions, announces the successful completion of its seed funding round, raising €42 million. This substantial investment, comprising both equity and grant instruments, is designated for the scaling of its patented electrolyser technology. Stargate Hydrogen’s technology is fundamentally different from other electrolysers in terms of both materials and the development approach used, allowing to bring down the cost of green hydrogen to 1 Euro per kilogram.
Instead of precious metals, Stargate is using ceramic-based catalyst material that significantly contributes to the reduction in levelized cost of hydrogen, without renouncing the reliability of alkaline technology.
Additionally, Stargate has developed its proprietary stack and system design, using a development approach that considers electrolyzer as a battery system, thereby adopting the learnings from the rapid developmental cycles of lithium-ion batteries over the past 15 years. The IP portfolio of Stargate covers all the levels of
the system, including materials, electrodes, stack and even control systems of the whole plant. The first installations of Stargate´s electrolyzer technology are already on the field, and offtake customers include Utilitas, one of the largest renewable energy developers in the Baltic Sea region.
In tandem with this financing achievement, Stargate Hydrogen is thrilled to announce the appointment of Mr. Taavi Madiberk, the Founder and CEO of Skeleton Technologies, the world’s leading manufacturer of graphene-based supercapacitors, as the company’s NonExecutive Chairman. With a deep understanding of disruptive innovation, Taavi Madiberk brings invaluable expertise and strategic vision to Stargate Hydrogen’s board.
As the global demand for clean, sustainable energy solutions continues to escalate, Stargate Hydrogen remains committed to decarbonize industry via enabling the switch from grey to green hydrogen. The infusion of €42 million in funding, coupled with the appointment of Mr. Madiberk as Non-Executive Chairman, positions Stargate Hydrogen at the forefront of the growing hydrogen economy.
Rachel Bridges has been appointed as Managing Director for global heat transfer, separation and fluid handling company, Alfa Laval, and is the first female to take the post.
Having spent 20 years at Cummins Incglobal power technology company – in both the marine and aftermarket businesses, Rachel brings a wealth of experience to Alfa Laval as it gets poised for further growth. She will now oversee business in a multitude of sectors including marine, energy, food and beverage, and water management.
Rachel is also passionate about driving Alfa Laval’s well-established sustainability and diversity, equity, and inclusion (DE&I) strategies forward in the UK. In her previous role, she was a leader focused on DE&I and active supporter of the Women’s Affinity groups which provided guidance and mentorship for girls and women across the world. She would also regularly support STEM focused activities helping each problem solving and creating thinking skills from a young age.
Rachel’s predecessor, Micael Hellborg remains within Alfa Laval as he takes on the role of Global Multibrands Manager in Sweden.
For mor information on Alfa Laval, visit: www.alfalaval.co.uk
The new AZM150 electromechanical interlock boasts a slimline design and a holding force of 1,500 N. The AZM150 can be combined with a range of different actuators to suit different mounting situations, including a straight or angled actuator for sliding guards and a flexible actuator for small hinged guards.
A plus point of the interlock is the 360 degree rotating actuator head which is locked by simply putting on the cover. The actuator head with its two insert slits allows for a range of mounting and approach options for highly versatile use. o
SCHMERSAL | Enigma Business Park
Malvern, Worcestershire, WR14 1GL
www.schmersal.co.uk
uksupport@schmersal.com
Lincoln-based manufacturing firm Micrometric is continuing to lead the way in laser manufacturing and multiprocess services.
The company, which was established over 40 years ago, produces fine parts and precision components for a range of customers in the UK and international markets. It specialises in a range of services including cutting, etching, drilling, and welding as well as tube cutting and precision component machining.
Commercial Director Chris Waters said: “Lasers are at the heart of everything we do, and we have the relevant capabilities and laser equipment to cut, assemble and weld complex manufacturing medical devices including small tubes, injection needles, and endoscopes and intricate parts required for surgical equipment.
“We have built up a reputation for our personal approach with customers as we want to fully understand our customers’ laser cutting requirements. We’re committed to providing exceptional, customised services that help our customers achieve their goals faster and with greater precision.”
Chris added: “Our laser machines are suited to cutting materials with a wide
range of thicknesses and can cut a range of materials including metal, plastics, and ceramics. We offer micro laser cutting capabilities that allow small parts to be cut to tight tolerances down to +/-0.02mm (material and thickness dependent) across a variety of materials including stainless steel, titanium, copper, brass, and ceramic.
“We are AS9100 qualified and can supply process sheets, certification, first article inspection reports or similar inspection regimes to clients, as required.
“We use several CO2 and state-of-theart fibre laser cutting systems which precisely cut materials with minimal heat and excellent edge quality to produce components quickly, efficiently, and cost-effectively.”
Since investing in this equipment, Micrometric’s skilled workforce has used the machines to cut, assemble and weld complex medical and aerospace components for companies which produce aerospace filters, automated injection needles, endoscopy components and MRI scanning equipment as well as producing finer, precise parts for other sectors.
Micrometric is equipped with a range of lasers and its experts can weld a wide range of parts to deliver high-quality solutions.
Chris added: “Laser welding offers the benefit of welding while minimising heat input which is critical when welding components with temperature-sensitive items inside them or minimising any distortion due to heat.
LEFT: Laser welding
BELOW: Laser cutting examples
ABOVE: Chris Waters is Commercial Director
“We can also weld autogenously or with wire feed. Depending on the metallurgy of the parts, it is possible to add different alloys as wire to adjust the weldability of the component. The wire feed can be fully automated within the welding machine. For some welds, such as titanium, an inert atmosphere is required, and an enclosed argon welding system is used.”
Micrometric offers a range of in-house and resourced services to complement its laser machining services and has dedicated equipment for laser drilling, cutting, etching and welding applications. Its extensive work of subcontracting means that it’s able to offer a single point of contact for manufacturing parts from the initial process through to completion, helping to reduce lead times and production costs.
Micrometric is a member of the Midlands Aerospace Alliance (MAA), The Manufacturers’ Organisation (MAKE UK), Association of Industrial Laser Users (AILU), and Motorsport Industry Association (MIA).
To find out more about Micrometric and its services, visit micrometric.co.uk or contact the sales office on 01522 509999.
The three projects will accelerate productivity and sustainability across local manufacturing and engineering specialists, with smaller businesses working alongside partners including Boeing, SSE Renewables, Howden, Thales and Babcock. The projects are supported with £5.4 million from the UK Government and up to £8.6 million from industry partners.
One project, ReMake Glasgow, will see a first-of-its-kind national ReMake
hub developed at NMIS’ flagship facility next to Glasgow Airport within the Advanced Manufacturing Innovation District Scotland. The hub will provide the skills and technologies needed to support ambitious manufacturers of all sizes to adopt circularity and extend the life of products and parts.
The second NMIS led project, Data Driven Design and Manufacturing Colab (D3M_Colab), will explore the potential of data science to solve real-world
manufacturing problems and boost productivity. It will upskill 300 local people with 100 hours of free training that includes a transformation project deployed within their workplace and ongoing support from NMIS experts and PhD students from the University of Strathclyde.
Meanwhile, the third initiative, named Stratellite, led by the NMIS Lightweight Manufacturing Centre (LMC) taps into Scotland’s growing satellite manufacturing sector and focuses on an innovative reconfigurable, modular, and scalable production system developed by the LMC.
The projects are funded by the Glasgow City Region Innovation Accelerator programme with additional contributions from project partners. Led by Innovate UK on behalf of UK Research and Innovation, the pilot Innovation Accelerator programme is investing £100 million in 26 transformative R&D projects to accelerate the growth of three highpotential innovation clusters – Glasgow City Region, Greater Manchester and West Midlands.
Together with Porsche AG, management and IT consultancy MHP is taking industrial and production sector training to a new level: in a showcase event, part of the production process at the Zuffenhausen plant was implemented as highly realistic 3D training in Apple Vision Pro. CAD data of a robot and a rotary table (welding) are realistically mapped in Apple Vision Pro in the “Shopfloor Training” showcase. With the capabilities provided by Apple Vision Pro, employees can now utilize an innovative training application that not only saves time, but also provides extremely effective training, thanks to the authentic representation of the production facility.
Training and simulation in the virtual world
Making procedures and exercises interactive and as realistic as possible is always crucial for the success of all training courses, whether you’re preparing shopfloor employees to maintain machines and systems or instructing them in complex production tasks.
Digitalization and spatial computing are a driving factor in ensuring training is successful and cost-efficient at the same time.
The long-term goal is to use Apple Vision Pro to educate and train employees for production. This solution also has the potential to revolutionize other areas, such as after sales in the automotive industry.
An Aston University researcher’s project has been selected as part of a package of support to help rebuild Ukraine’s energy system, phase out fossil fuels and support post-war recovery.
In November 2023 it was announced that senior lecturer in engineering and technology Dr Muhammed Imran and his collaborators were to receive almost £1 million from the UK government to develop and commercialise cascade heat pumps.
Using thermal energy, the new technology is designed to replace existing systems and be used for both cooling and heating homes.
In May 2024 the government officially announced it was investing £16 million to support the recovery and future sustainability of Ukraine’s energy system.
Dr Imran will be working with the Institute of Engineering Thermophysics of the National Academy of Sciences of Ukraine, Heat Pumps VDE LLC and other partners on making heat the new
technology easier to retrofit into existing domestic heating systems
The project aims to swap conventional boilers for heat pumps without the need for expensive modifications to existing distribution systems.
The team plan to do this by efficiently delivering significantly higher temperatures than existing technologies. A demonstration system will be installed in Ukraine as part of the project.
The government initiative involves collaborations between over 50 UK and Ukrainian organisations and will receive an additional £5 million from private sector money.
The various funded projects will carry out their work plans over the next two years and receive support from an accelerator programme for further investment and market entry.
Originally announced at the UKhosted Ukraine Recovery Conference in June 2023, the partnership has been designed by the two governments over the course of the last 12 months.
The first ERIKS apprenticeship programme started in 2023 and 13 engineering apprentices were taken on at ERIKS service centres across the UK. These apprentices get hands-on experience in the service centres while also studying for their Level 3 engineering fitter qualifications at SMB College in Leicester in regular one-week blocks.
Commenting on the first year’s intake Lori Broadhurst, Talent Development Partner at ERIKS said, “Our first-year programme is going well. We have had some notable successes with several of the apprentices taking on activities or going out to customer sites and completing their safety passportswhich is ahead of where we thought they would be at this point.
“It shows how quickly our more experienced team members’ knowledge in the service centres is being passed on.”
The apprentices are on the second of four rotations, focusing on the skills that manufacturers and engineering businesses in their region require, and they will complete all four by the end of August
Looking to the future, ERIKS is to expand the programme further in future years as it seeks to provide its customers with the specialist knowledge they require.
Are you passionate about engineering and keen to inspire others to pursue a career in your field? Are you seeking ways to boost your pension and enjoy more family time? If you’re eager to share your expertise with the next wave of workers, perhaps you should consider becoming an engineering instructor or lecturer?
Do I have what it takes to become a lecturer?
If you like working with young people, have great people and communication skills as well as industry experience, time management and organisational skills, you have what it takes to become an instructor! Any additional experience working with apprentices or training junior staff would be an advantage. Our team will help you move into education and support you throughout the process every step of the way.
A day in the life of an engineering educator involves teaching 16 to 19-year-old students in a classroom or workshop, sharing your theoretical and practical knowledge of working in the engineering industry, assessing the standard of their work, providing constructive feedback, and preparing them for a career in engineering.
Depending on your experience and preferences, you can become a lecturer and spend more time in the classroom, or an instructor and provide more practical knowledge in the workshop.
Here are just few out of many benefits of becoming an educator:
• More paid holidays – lecturers and instructors can get up to 52 days annual leave with bank holidays, as well Christmas shutdown time!
• Teachers’ pension scheme with an employer contribution of up to 28.6% – further education providers will pay the employer’s contribution to your pension.
• No shift work – all lecturers and instructors work Mon-Fri, maximum five times a week.
• Funded training and progression – provider will train you on the job, invest in you and offer ongoing professional development to support you through your career.
• Job satisfaction – you’ll gain satisfaction from sharing your industry knowledge and experience with your students and have a direct impact on shaping the next generation of engineers.
Why work with jjFOX?
We have a dedicated team of experienced recruiters specialising in the engineering sector who are ready to help you with the transition from trade to education. Our specialists have the insight knowledge of the market and organisations and will be happy to share them with you to help you secure your first exciting role. They also know the recruitment process insight out and will assist you in the interview preparation if needed.
Our consultants will act on your behalf and help you negotiate the salary. This means no awkward conversations between you and your future employer. And, most importantly, our service is free of charge for candidates. You won’t have to pay for our help.
What jobs are available?
We work closely with a variety of further education providers across the UK, who are always on a lookout for instructors, assessors and lecturers in the following sectors:
• Automation
• Automotive Engineering
• Electrical Engineering
• Electronics
• Fabrication/Welding
• Maintenance Engineering
• Manufacturing Engineering
• Mechanical Engineering
Do I need a DBS check?
Working with students under 18 requires a DBS check. You need to be enhanced DBS checked, which can be done through us; we have a specialist in-house vetting team that can help you with this and address any queries you may have.
How do I become a lecturer/ instructor?
Whether you are considering a parttime, contracted position or want to transition into a full-time teaching career, we have a variety of roles available for you. Your first step will be to get in touch, discuss your options and send us your CV.
If you don’t hold any teaching qualifications, don’t worry. Due to staff shortages, a lot of organisations will be happy to train you on the job and provide funding to your courses.
Interested and curious to find out more? Make your first move and get in touch with our team today!
Email us on contact@jjfox.com or, alternatively, visit our website www.jjfox.com/candidates2
MSc - 1 year full time
MSc - 1 year full time
MSc - 2 or 3 year part time
MSc - 2 or 3 year part time (Taught and Distance Learning)
PG Diploma • PG Certificate
Short Courses for CPD
PG Diploma • PG Certificate
Short Courses for CPD
Designed to create a generation of nuclear engineers and scientists with the skills to secure a sustainable and safe future for nuclear energy.
info.ntec@manchester.ac.uk
A jury made up of no less than 132 independent experts from all over the world recognised the unique ergonomic features of the latest version of Toyota’s BT Staxio li-ionpowered ride-on stacker truck - the SSI200D model – by naming it among the winners of a Gold Award at the final of this year’s prestigious iF Design Awards.
In a statement, a spokesperson for the iF Design Awards jury described the Toyota SS1200D as “a masterpiece of ergonomic design.”
The stacker, which is considerably smaller and more manoeuvrable than a traditional forklift, was also praised for its “subtle use of curved forms and colours that add richness and humanity to this most industrial of products.”
And Toyota collected a second Gold Award for its Urban Runner – a new delivery drone concept that is being developed by the design team at Toyota Material Handling Europe specifically for the logistics sector.
The Urban Runner is an easily deployable fully automated delivery vehicle. It is one of a series of products that reflect Toyota Material Handling’s vision of the future and, it is hoped, will eventually deliver more sustainable, productive and safer automated logistics operations.
iF Gold Awards are only presented to products considered to represent an example of outstanding design. Out of some 11,000 entries to this year’s iF Design Awards just 75 received a Gold.
The team at a Somerset air filter manufacturing company are celebrating after receiving an achievement award from the British Standards Institution (BSI) following up to 30 years of successful accreditation (April 2024).
Bridgwater-based Jasun Envirocare was recently recognised for its decades of environmental, management and health and safety awards by the BSI, which is one of the world’s largest certification bodies. BSI produces technical standards for a wide range of products and services. It audits and provides certification to companies worldwide that implement measurable management systems.
Jasun Envirocare is accredited by BSI to ISO 9001 Quality Management, ISO 14001
Environmental Management and ISO 45001 Occupational Health & Safety.
ISO 9001 helps firms monitor and continually improve the quality of their products and services.
This standard not only streamlines operations but also emphasises the importance of constantly adapting to meet customer needs, thereby fostering a culture of continuous development and excellence.
ISO 45001 is all about prioritising the health and happiness of a company’s workforce to create a more successful, resilient organisation.
This management system standard enables organisations to provide safe and healthy workplaces by reducing the risks of work-related injury, as well as by continually improving their occupational health and safety (OH&S) performance.
In the heart of the West Midlands, nestled amidst the industrial landscape, Midland Deburr & Finish stands as a testament to the spirit of entrepreneurship, innovation, and unwavering determination. As the company commemorates its 25th anniversary this month, Directors Chris and Sue Arrowsmith reflect on the remarkable journey that has shaped their lives and the landscape of metal finishing in the region.
The story of Midland Deburr & Finish begins in April 1999 when Chris Arrowsmith, armed with a wealth of experience from leading operational management roles in the manufacturing sector, embarked on a journey to redefine industry standards. Frustrated by the inflexibility of larger corporations and inspired by the potential for innovation within the sector, Chris took a leap of faith and incorporated the business, laying the groundwork for what
would become Midlands’ premier metal finishing specialist.
The early years were marked by challenges and triumphs alike, as Chris navigated the complexities of entrepreneurship and the ever-evolving manufacturing landscape. However, it wasn’t long before his efforts began to bear fruit. Midland Deburr & Finish quickly gained traction, earning a reputation for quality, reliability, and innovation.
Dura Composites is one of just 252 organisations nationally to be recognised with a prestigious King’s Award for Enterprise, announced on the 6th May.
The company has previously received Queen’s Awards for Enterprise for International Trade in 2017 and Innovation in 2020. Through a careful combination of design, technology, and manufacturing improvements, Dura Composites created a unique range of Glass Reinforced Polymer (GRP) walkway products known as the d2 Dura Grating range that have up to 33% less embodied carbon, whilst also being fully recyclable and lighter than anything else on the market, making installation safer, easier and more cost-efficient. d² Dura Grating has patents relating to its design and
is used extensively in UK infrastructure heavy-duty flooring projects such as constructing walkways, covering voids (e.g. trenches), and for service risers in high rise buildings.
As well as being lower in carbon and fully recyclable, the grating is easier to handle and achieves a better performance-to-weight ratio, the highest fire rating, best anti-slip properties and the most proven performance in the GRP grating industry.
The King’s Awards for Enterprise, previously known as The Queen’s Awards for Enterprise, were renamed last year to reflect His Majesty The King’s desire to continue the legacy of HM Queen Elizabeth II’s by recognising outstanding UK businesses. The Award programme, now in its 58th year, is the most
prestigious business award in the country, with successful businesses able to use the esteemed King’s Awards Emblem for the next five years. Alongside its investment into innovation, Dura Composites also prioritises sustainability within its everyday operations, such as its use of electric company cars and forklift trucks, recyclable packaging, use of wood waste as heating fuel and ecofriendly lighting systems.
Heating is a critical component in manufacturing, directly influencing product quality and operational efficiency. Secomak’s innovative Heat Pack system addresses these needs with precision and energy efficiency, making it a vital tool for industries requiring exact temperature control.
Marshall Slingsby Advanced Composites, a part of the Marshall group, faced significant challenges in their aerospace composite manufacturing process. These components must withstand fluctuating temperatures and pressures, necessitating precise and consistent surface heating. Given the components’ large size and complex shapes, uniform heating was essential but challenging to achieve.
Secomak tackled these challenges by deploying the 18kW Heat Pack, which includes a DD643 direct-drive fan, a HT648 18kW heater, and a master HMI controller capable of managing up to three Heat Packs. This setup was tailored to meet Marshall’s specific requirements. A Variable-Speed Drive (VSD) was added to the blower for precise airflow control, enhancing temperature regulation.
In this project, instead of the usual two temperature probes, up to 16 surface-mounted PT100 probes were used, allowing for detailed temperature monitoring. All heating and temperature
Secomak’s Heat Pack and blower technology are versatile and used across various industrial sectors, such as printing, pharmaceuticals, and food production.
data could be externally exported to calibrated data loggers. Some of the components being manufactured are worth millions, and therefore, precise heating and data logging of temperatures achieved are of vital importance. The advanced HMI controller provided a user-friendly interface for setting and operating the machine, with all temperatures and alarms recorded for review. Only trained operators could access critical settings, enhancing security and reliability. The system’s PID control within the PLC achieved a temperature accuracy of ±1%, ensuring the integrity of high-value components.
The new Heat Pack seamlessly replaced the existing systems that had reached the end of their life. Designed to match the existing configuration, the implementation was quick and smooth, allowing Marshall to start trials within minutes. Key benefits included a 50% reduction in initial heating time and a three-hour reduction in the overall curing process. This automation not only improved efficiency but also reduced
manual intervention, saving significant operational costs annually.
Customer feedback was highly positive. Specifically highlighted was the enhanced control, accuracy, and reliability, resulting in lower curing costs..
Secomak’s Heat Pack and blower technology are versatile and used across various industrial sectors, such as printing, pharmaceuticals, and food production. In printing, Secomak blowers efficiently dry inks on substrates, while in the pharmaceutical industry, they ensure precise drying of interior IBCs. The technology is also crucial in food production, where it dries internal pipes during cleaning cycles and pre-heats glass containers to prevent thermal shock during hot filling.
Looking ahead, Secomak is leading the way in industrial heating innovations. Recent advancements in aerodynamic impellors and blower testing facilities promise increased efficiency and control, aligning with the industry’s shift towards net zero and decarbonisation. With over 90 years of experience, Secomak continues to develop solutions that meet the evolving needs of its diverse customer base.
Discover the precision and efficiency of Secomak’s Heat Pack and see how it can transform your industrial heating processes. Visit our website or contact our team to learn more about this cutting-edge technology.
The Secomak Heat Pack is a complete and ready-to-install industrial hot air blower. With a rated heat output between O.SkW36kW, the system includes all you need for precisely controlled hot air.
In many industries, colour implies quality. It is therefore crucial to match the correct colour shade in the production process and to produce it homogeneously throughout numerous batches, says Glenn Wedgbrow, Business Development Manager at Micro-Epsilon UK.
In many industries, particularly consumer goods, colour implies quality. For any goods that arrive at the final customer, the exact colour shade affects the value and identity of the product and the brand. Colour not only leaves behind an impression of quality but can also be used as an indirect quantity to control the process. For example, colour sensors are used to monitor the presence of adhesive beading, to sort parts or to determine active ingredients. In most cases, colour sensors are the more costeffective solution as they provide more precision than conventional switching sensors.
In physical terms, colour is a reflected intensity spectrum in the visible wavelength range. This reflection spectrum depends on the object colour and the illumination. Illumination is defined by different light sources, e.g. light bulbs, daylight, fluorescent lamps or
cold white LEDs. A colour sensor detects the reflected spectrum and imitates the principle of the human eye. The ability of a colour sensor to determine or measure the colour presented to it is dependent on the detection technology used in the sensor.
Narrow-band colour filters divide the received light spectrum into the three colour coordinates: Red (R), Green (G) and Blue (B). The sensor evaluates the intensity of the respective colour coordinates and outputs them as an analogue signal. The three colour values are often combined into one displayed digital value and therefore have only little information value about the colour detected. Furthermore, an RGB sensor cannot separate colour information and brightness, i.e., changing the brightness also changes the displayed colour. Also, the RGB filters only cover a small portion of the spectrum and thus not all colours can be seen.
Three high-resolution colour filters divide the received light spectrum into the following three colour coordinates: X =
long-wave, Y = medium-wave and Z = short-wave. Similar to the cones in the human eye, these colour filters image the entire spectral sensitivity of the eye. Due to these broad-band colour filters, the wavelengths of the light spectrum are imaged in more detail and contain more information about the colour composition. Based on stored standard formulas, the values are converted into a standardised colour space (e.g. L*a*b*). Due to this standardisation to L*a*b*, changing the brightness (e.g. fluctuating distance between sensor head and target) has only little influence on the colour value. True Colour sensors, such as the Micro-Epsilon colorSENSOR CFO series, are designed for relative colour inspection and are ideal for recognising deviations from a reference colour.
Another functional principle is spectral technology and is applied by colour measuring systems such as the colorCONTROL ACS7000 from MicroEpsilon. With a grid, the received light is refracted into individual wavelengths and projected onto a CCD line. Each of the 256 measurement pixels of this line is assigned to a certain wavelength. Based on interpolation, an intensity value (0-100%) of the received colour wavelength is then output for each pixel. This allows for the computing unit to image and output the full spectral curve of the visible light. Based on its spectral curve, the colour obtained can be clearly identified. With the freely selectable standard observers and illuminants stored in the controller, the values and spectral curves received can be converted and output in the desired colour space. “White referencing” makes it possible to largely eliminate any ambient influences onto the measurement result.
Sensors operating according to the spectral technology are colour measuring sensors.
The Babcock Wanson Group, of which industrial process heating equipment and solutions specialist Babcock Wanson UK is a founding company, has joined the United Nations Global Compact, the largest international initiative for sustainable development and corporate social responsibility (CSR).
At the heart of Global Compact is 17 Sustainable Development Goals, which aim to respond to the most pressing social and environmental challenges of our time by 2030. By joining Global Compact, Babcock Wanson has committed to respecting these principles and contributing to their achievement. Cyril Fournier-Montgieux, Babcock Wanson Group CEO states: “This network will provide us with a framework for exchange and learning, as well as tools and resources to strengthen our CSR performance and report on our progress.”
For more information, please contact Babcock Wanson on 020 8953 7111 or info@babcock-wanson.com or go to www.babcock-wanson.com
Titan is a leading design and manufacturer of innovative end user and OEM high-performance flow meters, used within a wide range of environments and applications.
Compact, robust, reliable • Excellent accuracy and repeatability
• Measure low to high flow ranges
• High chemical resistance
• OEM bespoke design capability
ergonomic positioners are single or double column devices that enable the lifting and rotation of a product during welding and assembly operations.
With overall capacity from 2,000 - 90,000kg to suit, they are both compact and flexible.
Skechers - the US-owned manufacturer of leisure footwear and clothing - has halved the amount of space needed to store close to 100,000 tote boxes and improved pick speeds and picking accuracy at its multichannel fulfillment hub in Eastern China with the introduction of AirRob – a new automated, high density tote storage and picking solution from LiBiao Robotics.
AirRob travels horizontally and vertically on a lightweight frame that is fitted to the face of storage racking. Straightforward and cost effective to install, the frame infrastructure is compatible with all major racking brands, but the rack structure must be at least two metres high.
AirRob’s clever and compact design allows the aisles of the storage scheme to be reduced to just 0.85 metres wide. 0.85 metres is considerably less than
AirRob travels horizontally and vertically
the aisle width that is needed to accommodate even the slimmest very narrow aisle (VNA) lift truck and the building space that is saved by reducing aisles so significantly guarantees that the highest storage density is achieved.
In operation, AirRob travels to its designated location within the storage scheme and automatically picks a tote. With the required box on board it returns to ground level and passes the tote on to a transfer robot. In effect, the ground level robot performs the role of a mobile Pick & Drop station.
Skechers has a fleet of 450 ultra-reliable ‘Mini Yellow’ groundlevel robots that ferry totes between the storage system and the workstations. By using multiple ground-level robots the flow of totes is never interrupted.
As part of its ongoing commitment to sustainability Toyota Material Handling Europe has announced the creation of an Environmental, Social and Governance (ESG) committee.
The new team will help shape Toyota’s strategy and decision making as the company continues its progress towards becoming a highly sustainable organisation Directors from every business function within TMH Europe will make up the ESG team and together they will tackle a full range of sustainability issues, such as climate change, diversity and health & safety.
ESG is a set of standards measuring a business’s impact on society and the environment. The standards cover areas such as how transparent and accountable companies are in terms of their leadership, executive pay, audits, internal controls and shareholder rights.
According to the CBI, In the UK ESG is considered an increasingly important component for business growth, while research by McKinsey found that customers in a range of industries are more willing to buy brands that they perceive to be ethical.
The Fabrication Division at the Engineering Technology Group (ETG) is now proud to present the latest arrival to its product range – the Durma PB Bending Centre. Capable of performing bending operations on a wide range of sheet metals, the PB accurately positions the lower and upper bending dies to achieve incredibly flexible part profiles with unparalleled precision.
The impressive Durma PB Bending Centre offers maximum speed, flexibility and safety with a fully
Omron Electronic Components Europe has addressed the need for denser packed onboard relays with the introduction of higher temperature relays that provide Class-F coil insulation.
Extending the G5NB-1A4EL-HA from Class B to Class F, the G5NB-1A4-EL-HA-CF type provides 5A switching from -40℃ to 105℃ PCB in a fully sealed power relay. The new relays allow a higher density of parts by operating at higher temperatures than their predecessors.
Fully sealed, the G5NB-1A4-ELHA-CF type relays ensure a longer
automatic tool change that ensures minimum set-up time and maximum productivity.
With the PB Bending Centre, manufacturers can achieve excellent bending results and increase production efficiency with a choice of different models available to suit the desired angle or shape, during the sheet bending process. The Durma PB Bending Centre is perfect for the fully automatic bending of thick plate materials in the range of 0.5 to 4mm in simple and complex bending profiles.
lifetime in environments up to 85℃. Alternatively, they can deliver the same lifetime as existing G5NB-E relays in considerably harsher temperature environments.
VDE approval standards rate the Class F relay up to 50Kops at 105℃ and up to 100Kops at 85℃.
Applications range from HVAC and heat pumps, through domestic cooking equipment, washing machines and refrigerators, to industrial devices such as PLCs, I/O terminals and temperature controllers.
The new G5NB-EL-CF relays are available now from authorised distributors and stockists throughout the UK and Europe.
Reading-based PTC has today announced the eleventh version of its Creo® computer-aided design (CAD) software and the latest version of its Creo+™ SaaS CAD solution.
This launch enables engineers to deliver their best designs in less time and enjoy a wide range of enhancements for electrification, composites, model-based definition, simulation-driven design, and manufacturing.
“Creo 11 and Creo+ deliver enhancements that design engineers will use every day,” said Brian Thompson, General Manager of Creo at PTC.
“Improvements to our AIpowered generative design and integrated Ansys-based simulation gives customers the opportunity to employ simulation-driven design earlier in the development process to improve time to market, initial product quality, and manufacturing cost.
“PTC has continued to invest in Creo’s capabilities for model-based definition (MBD), design of electrical sub-systems, composite designs, and advanced manufacturing.”
Creo+ is fully upward compatible with on-premises versions of Creo and is built on the same core technology, so no data translation is needed.
Creo 11 includes all the capabilities of previous Creo versions. For additional information on Creo 11, please visit www.ptc.com/en/products/ creo/whats-new
Whether you are looking to move your existing Plastic Injection Moulding production or sourcing a supplier for a new product, Pentagon will support you at every stage of the process. Delivering a full turnkey solution from one site of UK Manufacture.
www.pentagonplastics.co.uk |
Auto-Trail V.R. Ltd is a distinguished British motorhome and campervan manufacturer, with a rich history dating back to 1982. Originating as a caravan repair business, Auto-Trail has evolved into a market leader, known for its customisable, highquality leisure vehicles. This case study examines how Auto-Trail V.R. Ltd has implemented AXYZ’s advanced CNC routing technology to transform its manufacturing process, resulting in increased efficiency, reduced waste and enhanced product quality.
Auto-Trail V.R. Ltd began as a caravan repair business but quickly evolved into a motorhome manufacturer, responding to growing customer demand for bespoke, luxury vehicles. Throughout the decades, from introducing the Cheyenne range in the 1990s to launching their first A-Class motorhome in 2006, Auto-Trail has been at the forefront of motorhome design and functionality.
Auto-Trail offers more than just motorhomes; they provide a gateway to exploration and discovery. Each vehicle is designed to integrate seamlessly into the lifestyle of adventurers, enabling them to create lasting memories. Auto-Trail stands out in the motorhome industry for its commitment to
personalisation, offering an extensive range of customisation options. This dedication ensures that each vehicle not only meets but exceeds customer expectations.
“In early 2024, facing the upcoming retirement of a skilled employee and the limitations of manual production methods (including hand-cutting from drawings and patterns) Auto-Trail decided to automate their manufacturing process” said Paul Spivey Design Engineer. This decision was also driven by the need to streamline operations and maintain control over material use, which manual methods could no longer efficiently support. Auto-Trail therefore decided to invest in AXYZ routers to automate its manufacturing processes. The adoption of CNC technology offered greater control over materials, improved design flexibility and enhanced production efficiency. After considering various options (including waterjet technology which proved to be logistically not viable) and the need for precise cuts, led them to explore other options, culminating in the selection
of AXYZ’s CNC knife cutter. “I looked at several different manufactures, but AXYZ gave us the flexibility we were looking for with the ability to have a multi change router head and suitability for the manufacturing environment” said Paul Spivey.
Auto-Trail chose the AXYZ INFINITE 4022 1C2Z ATC CNC Router. The INFINITE router is a highly configurable CNC machine that is suitable for oneoff, small batch production as well as high volume and high productivity applications, including woodworking, plastic fabrication, engineering plastic machining and so much more. For a wide range of routing operations, one can choose from high-speed spindles ranging from 5HP to 15HP. For knife cutting, choose from a tangential knife, which can be used for creasing and folding applications or an oscillating knife which can be used to process soft goods material.
The AXYZ machines revolutionised AutoTrail’s production processes, particularly
in handling insulation material for pressed panels. Instead of manual cutting, CNC routing enabled precise shaping, reduced component count per panel, improved fit and reduced waste, printing, paper and transport costs. Additionally, the machines facilitated the production of customised parts specific to vehicle models, enhancing overall efficiency and material utilisation.
The integration of AXYZ routers at Auto-Trail has also enhanced design and production. The CNC technology has enabled complex cuts, reducing the need for plywood patterns and the number of components per panel from ten to four. This has streamlined the assembly process significantly.
The improvement in fit of components, due to the precise cutting ability of the AXYZ machines has led to less rework and errors, resulting in a reduction in the labour intensity. The automation of cutting processes has descaled the skill requirements, allowing less skilled workers to manage operations efficiently, which is vital as the workforce ages.
The integration of AXYZ technology has not only optimised production but also maintained, if not enhanced, the quality of the final products. The precision of the AXYZ routers ensures each part meets strict quality standards, which is crucial for the overall reliability and performance of Auto-Trail’s motorhomes.
The adoption of AXYZ machines resulted in significant cost savings and quality improvements for Auto-Trail. By optimising material usage, reducing waste and enhancing panel construction, the company achieved measurable efficiencies in production. Furthermore, the precision and accuracy afforded by CNC routing translated into superior product quality, reinforcing Auto-Trail’s commitment to excellence and customer satisfaction and reinforcing Auto-Trail’s reputation for excellence.
The introduction of automation at Auto-Trail elicited positive responses from employees, who viewed it as an opportunity for professional growth and skill development. Rather than displacing workers, the integration of AXYZ machines empowered employees to adapt to new technologies and enhance their roles within the organisation. As automation freed up time previously
I looked at several different manufactures, but AXYZ gave us the flexibility we were looking for with the ability to have a multi change router head and suitability for the manufacturing environment.
- Paul Spivey, Design Engineer
spent on manual tasks, employees could redirect their efforts towards innovation, collaboration and continuous improvement.
While the current workforce size remains stable, the skill requirements have evolved. Auto-Trail has invested in training and development to ensure employees are well-equipped to operate the new technology efficiently.
The integration of AXYZ machines presented Auto-Trail with several challenges, including spatial constraints and process optimisation. However, through meticulous planning, iterative testing and collaborative problemsolving, the company successfully overcame these obstacles. Specialised equipment, such as customised cages for transporting parts and comprehensive adjustments to bills of materials (BOMs), cut lists and drawings ensured a seamless transition to automated production.
Auto-Trail ensures the smooth operation of AXYZ machines through regular maintenance by onsite engineers and a maintenance contract with AXYZ. Looking ahead, the company remains committed to further integrating automation into its processes, continually evaluating opportunities to optimise production and drive innovation.
Auto-Trail V.R. Ltd is continually assessing and integrating automation into their production processes. The company plans to expand the use of automated technologies to enhance other areas of production, aiming for greater efficiency and productivity.
The implementation of AXYZ machines went beyond mere automation; it ushered in a paradigm shift in how Auto-Trail approached its manufacturing processes. Beyond the initial task of replacing manual cutting of insulation material, the CNC routers enabled the company to reimagine its entire production workflow. By embracing CNC technology, Auto-Trail gained the flexibility to create custom-shaped parts, optimise component count and improve overall panel construction. The ability to interlink multiple pieces and integrate router cut-outs and wiring grooves directly into panels showcased the versatility and ingenuity of AXYZ machines.
The adoption of AXYZ CNC routers by Auto-Trail V.R. Ltd has significantly transformed their manufacturing landscape. By automating key production processes, Auto-Trail has enhanced operational efficiency, reduced costs and maintained highquality standards in their motorhomes. The successful integration of AXYZ technology showcases Auto-Trail’s commitment to innovation and customer satisfaction, setting a benchmark in the motorhome manufacturing industry.
For more information on Auto-Trail V.R. Ltd www.auto-trail.co.uk 01472 571 000
For more information on the AXYZ range of routers: www.axyz.com 01952 291600
Donal Bourke, Director at maintenance and asset management software specialist PEMAC, explains how Mobile Computerised Maintenance Management Systems (CMMS) are becoming a critical part of modern manufacturing.
At the heart of implementing mobile Computerised Maintenance Management Systems (CMMS) applications is the empowerment of maintenance teams with instant access to data, such as work orders, asset information, and inventory levels. This enables informed decision-making and rapid response to issues. Such real-time capability significantly reduces downtime and improves the reliability and longevity of critical assets.
Moreover, mobile CMMS applications facilitate a proactive maintenance strategy, shifting away from the reactive ‘fix it when it breaks’ approach to preventive and even predictive maintenance. Through features such as predictive maintenance alerts and scheduled inspections, maintenance teams can anticipate issues before they escalate, minimising unplanned downtime and extending the life of equipment. This strategic shift not only saves costs but also improves overall plant efficiency and productivity.
If your business is operating a seasonal shutdown Filtermist’s team of P601 and P602 qualified engineers are on hand throughout the summer to visit your site and provide support with essential maintenance and repairs of your Local Exhaust Ventilation extraction equipment.
Find out more by visiting www.filtermist.com/aftermarket-support or speak to one of our team +44 (0)1952 290500 sales@filtermist.com
Click
For decades, the UK manufacturing sector has operated under a familiar yet complex sales model, characterised by direct, interpersonal sales and legacy systems with manual operational processes. However, in a time where personalised and contextualised buying experiences prove essential, the B2B manufacturing industry needs to step up its game and do things differently.
Despite the global B2B eCommerce sector being over one and a half times the size of the B2C market, the UK market remains somewhat underdeveloped. Recent challenges, such as Brexit, high inflation, and supply chain disruptions, have forced the industry to slow its progress towards digitisation. While COVID-19 helped accelerate digital transformation initiatives by removing face-to-face sales from the equation, B2B manufacturers still have a long way to go in modernising the customer journey.
To survive in 2024, B2B manufacturers need to think differently and revamp their eCommerce sales approach.
To efficiently drive revenue and greater customer relationships, B2B manufacturers must keep up with modern customer demands — no matter how these are shaped or influenced. This means finding the agility and flexibility to sell efficiently and nurturing customer relationships on an ongoing basis.
Historically, eCommerce platforms haven’t been the primary driver of revenue for manufacturers, creating an industry-wide hesitation to invest. However, this resistance has created a bottleneck for B2B manufacturers as more millennials assume decisionmaking positions and the shift toward digital channels continues to boom.
Survival in 2024 relies on manufacturers realising the transformative potential of the digital commerce landscape and its power to unlock new avenues for revenue generation and market expansion. According to IDC’s ‘Global Manufacturing Survey’, 47% of manufacturers globally consider B2B digital commerce as a strategic initiative to drive the customer experience. Additionally, data from PwC indicates a growing willingness in manufacturing to adapt business models, with plans to go from zero online sales to 60% of all sales within a few years.
In doing so, there has been a surge in demand for solutions that improve supply chain efficiency and facilitate a seamless, engaging customer journey. However, some manufacturers have turned to supposedly easier solutions advertised by all-in-one monolithic platforms, which have been shown to increase technical debt and reduce innovation releases. This is where composable commerce emerges as a new and reliable solution that’s transforming the eCommerce narrative within the B2B sphere.
Composable commerce is a componentbased approach that allows companies
to select and integrate the best commerce features to suit their individual needs. Instead of working with restricted, out-of-the-box systems, businesses have the freedom to build an entirely bespoke shopping experience with the flexibility to seamlessly adapt to new market conditions.
With cloud-native, API-driven, composable architectures, businesses gain virtually infinite scalability to handle traffic growth, product catalogues, and new business models. This future-proofs operations by eliminating the need for costly upgrades and replacements as the market evolves.
Manufacturing company Orbia Building & Infrastructure (Wavin) is a key example of what’s possible with composable commerce. Following an established one-to-one sales process with long-term customers, the company transitioned to digital platforms as its primary sales channel. With this shift, the manufacturer was able to meet the growing demand of B2B merchants by opening various webshops, substantially growing its online presence and driving significant revenue growth as a result. Now, the company estimates that 60% of its global sales will be digital — all made possible with the agility and scalability of composable commerce.
In the tech-driven era, the rush to digitise B2B manufacturing operations is only getting more intense, with 52% of manufacturers setting their sights on transforming their eCommerce platforms, customer portals, and digital services to drive stronger sales in 2024.
To keep up the pace, it’s imperative for B2B businesses to consider moving away from rigid, monolithic solutions and adopting sophisticated tech stacks with the flexibility to meet adapting needs. Looking to the future, the B2B manufacturing industry must prioritise digital transformation to sustain growth and maintain a competitive edge in the market.
While your product technology is jetting
throttle into the Space Age, your planning tools tend to crawl around in the Stone Age. Here’s why AI will change that.By Jan Brittner, Business Development Manufacturing,
Manufacturers face many challenges today including supply chain disruptions, rising material costs, skilled labor shortages, and rising interest rates. It’s understandable why, according to a National Association of Manufacturers (NAM) survey, manufacturers’ optimism caused the Manufacturing Outlook Index to drop to 55, a reduction of 4.2 points since the first quarter of 2022. It also explains why manufacturers are adopting new strategies.
In Their Words
In its 2023 Manufacturing Trends, Alithya found that 43% of manufacturers plan to continue increasing their technology investments, driven by their focus on improving efficiency and productivity. Survey respondents
reported efficiency and productivity as their top priorities in an environment of rising input costs and tightening margins.
So how is it that well over 50 percent of all one-off and small-batch manufacturers are only too familiar with one or more of these problems?
1. They are planning unrealistically against unlimited capacities and based on dates from the past.
2. Their delivery dates are brewed from a mixture of standard delivery times, intuition, and “Excel-Magic”.
3. They suffer high manual planning efforts and dissatisfied customers despite all the trouble.
4. They are never sure whether they are really getting the most out of their production environments.
Well understandable, manufacturers seek solutions to better address these challenges and support their greater agility and resilience. Deloitte reported that 86% of manufacturers believe that digital solutions and transformation will be the main drivers of their future competitiveness. The 2023 Deloitte Manufacturing Outlook Survey indicated that 61% of respondents are partnering with specialized technology companies to deploy intelligent technologies such as advancing planning and scheduling systems (APS) that support their planning needs, while also enabling reliable delivery dates, needs-oriented procurement, optimized material flow, and the ability to detect, prevent and respond to unexpected developments.
APS systems incorporating leadingedge technologies such as Artificial
Intelligence (AI), machine learning, operations research, fuzzy logic, and proprietary algorithms. INFORM, a global leader in AI-powered optimization software, has developed FELIOS, an APS system that synchronizes all production processes and evaluates the resulting data to facilitate agile short- and long-term production planning. FELIOS is used by over 300 manufacturers optimizing over 23.5 million production work sequences daily.
An add-on to any conventional Enterprise Resource Planning (ERP) system, FELIOS compensates for an ERP’s planning weaknesses and enables interdepartmental planning transparency in production, purchasing, construction and sales. It ensures that all processes are implemented as planned and to meet delivery deadlines.
Manufacturers with multi-variant products, and those with single-item and small-batch production, need to focus on several factors in planning and managing their production. FELIOS tackles these complex production requirements. It helps ensure that all orders are executed on time, efficiently with short production cycles, minimal work-in-progress, and high quality. An intelligent production planning solution, INFORM’s FELIOS provides manufacturers with essential capabilities, including the ability to:
• Keep customers informed at any time with reliable delivery dates,
• Establish the optimal sequence of all production process,
• Ensure a backlog-free production process,
• Create the production plan without time-consuming team meetings,
• Integrate high-priority orders on short notice,
• Dissolve capital-binding stock buffers while preventing missing parts that would cause assembly standstills,
• Relieve foremen and machine operators from planning tasks, and
• Proactively plan the production as a whole system while considering all limiting conditions,
FELIOS delivers these critical capabilities, providing extensive transparency by linking all involved departments and merging all relevant data in one central planning system.
Through its automated real-time planning support, FELIOS schedules all production orders simultaneously. It plans realistically within the context of potential constraints (e.g., limited personnel, machines, and materials). When faced with unexpected changes, FELIOS automatically recalculates the production plan during the next optimization run.
Focusing on providing manufacturers with agility and resilience for longterm success, FELIOS takes a holistic approach to order processing by not only optimizing the scheduling of a single resource but the complete order network, arming manufacturers with agile planning capabilities and related intelligence that supports their simultaneous production based on market demands. Complete planning transparency is achieved along with high adherence to production schedules, low stocks, and short lead times.
FELIOS operates in three key steps:
1. FELIOS is connected to a manufacturers’ existing ERP system via an interface. It extracts all relevant planning process data (e.g., purchase orders, materials availability, machine capacities).
2. Based on the ERP data, FELIOS plans the production process for the next and subsequent days and weeks. Applying intelligent optimization processes, it calculates worklists, considers realistic machine capacities, and creates delivery deadlines for materials, machine parts and components.
Deloitte reported that 86% of manufacturers believe that digital solutions and transformation will be the main drivers of their future competitiveness.
- Jan Brittner
It distributes the capacities to meet predicted delivery deadlines for all customer orders.
3. FELIOS gives production foremen and workers a work plan for what must be completed on a given day. Time horizons can be selected individually so foremen can organize optimal setup times. When unexpected changes in relevant production parameters occur, or a worklist cannot be completed, FELIOS addresses them in its calculations for the next day.
FELIOS can be configured to a customer’s specific requirements with additional modules available to support other functions such as project and assembly planning, shift and personnel planning, and production and machine data acquisition.
For more information, visit: www.felios.com
LG Electronics (LG) is accelerating the growth of its advanced materials business with the launch of LG PuroTecTM, a cutting-edge antimicrobial glass powder. Designed to safeguard product hygiene and suitable for diverse applications, this innovative material leverages the company’s proprietary glass composition design technology and thorough understanding of real-life home appliance usage environments.
PuroTec, a portmanteau of the words Pure, Protect and Technology, possesses anti-fungal and antibacterial properties that prevent microorganism contamination and associated odors. LG’s glass powder can be incorporated into various materials, including plastics, paint and rubber. Additionally, the company’s antimicrobial glass powder provides chemical and thermal stability, as
well as durability and resistance to discoloration.
LG first began developing antimicrobial glass powder in 1996, and now holds an impressive 219
patents related to the production and application of glass powder. The company manufactures its antimicrobial glass powder at LG Smart Park in Changwon, South Korea, which has an annual production capacity of 4,500 tons. This year, the company is expanding sales of its antimicrobial glass powder to major markets in Asia, such as China, Vietnam and India, and is anticipating a year-on-year increase in sales of over 700 percent.
Moving forward, LG aims to significantly ramp up its advanced material business, utilizing international exhibitions to introduce PuroTec to potential global customers. PuroTec was recently honoured at Chinaplas, Asia’s largest plastic and rubber industry exhibition, held in Shanghai, China (April 23-26), where it was awarded ‘Innovation of the Year’s status.
As part of their ongoing mission to become a truly sustainable business, a national galvanizing company has successfully become completely Chromium Trioxide free.
After dedicating several years and significantly investing into the research, development and trials of alternative chemicals, Wedge Group Galvanizing Ltd is proud to have completely removed Chromium Trioxide from their processes –months ahead of the latest legislation set to govern this industry-wide.
Chromium Trioxide is traditionally used in the passivation process during galvanizing. It creates a protective surface on the galvanizing coating that keeps the surface bright and shiny for up to 12 weeks, and minimises wet storage stain on the coating for the immediate period after galvanizing.
But as of September 2024, the European Union’s REACH legislation is banning the use of Chromium Trioxide in most manufacturing processes (including galvanizing). Due to this, the leading UK supplier will cease manufacture of the chemical ahead of this upcoming deadline.
Wedge Group Galvanizing Ltd is the largest hot-dip galvanizing organisation in the UK with a history dating back over 150 years. With 14 plants strategically placed across the country, the firm offers a truly national galvanizing service.
For further information, please contact Wedge Group Galvanizing Ltd on 01902 601944 or visit www.wedge-galv. co.uk.
Brixworth Engineering, manufacturer of the globally renowned Benco engine stands, has produced its largest-ever side-mounting turnover stand. Supplied to the Croydon facility of leading power transmission specialist Voith Turbo, the Benco 1050 (an upgrade to Brixworth’s standard Benco 1000 engine stand) is helping this progressive plant to inspect and service a variety of engines and transmissions.
With a load capacity of 5000 kg (at 500 mm from the mounting spindle) and a turning capacity of 10,000 Nm, the Benco 1050 supplied to Voith Turbo facilitates the manipulation of complete engines for inspection, repair or modification.
Moreover, it is a mobile version featuring a motor drive to deliver rotational speed up to 4 rpm, although customers can opt for floor mounting and manual operation if preferable.
Control of the Benco 1050 at Voith Turbo is via a fixed
pushbutton station, with pendant control available as an option. As a further point of note, Brixworth designed and manufactured additional mounting arms to minimise deflection throughout the loading and rotation process.
Although a comprehensive range of standard models is available, Brixworth has considerable experience in the design and manufacture of bespoke engine stands to suit individual customer requirements. The company can undertake site surveys and provide engineers to evaluate any special demands, ensuring the supply of a safe, effective and cost-competitive solution.
The stands, more than 5000 of which have been produced for use in over 20 countries, can reduce man hours by up to 50% through the elimination of non-productive handling procedures. They fully comply with all current working practices and safety regulations, and come with an extensive guarantee for complete peace-ofmind.
At Close Brothers Asset Finance, we have a long history of commissioning independent research to ensure we understand what business owners’ priorities are. In this article, we take a closer look at Manufacturing companies’ views on four key metrics:
• Appetite for investment in their business in the coming 12 months
• Access to finance and whether firms have missed a business opportunity through lack of available finance
• Views about the UK’s economic outlook
• Thoughts on their likely performance in the coming 12 months
Q: Have you missed a business opportunity in the last 12 months, due to lack of available finance?
Confidence in the macroeconomic outlook among SMEs –including those in Manufacturing - has incrementally improved in 2024, with 50% confident the economy will grow in the coming 12 months, compared to 47.5% in September.
However, while this is a step in the right direction, it’s worth remembering that in November 2021, 75% of respondents were positive about the economy, which means we are still some way off previous highs.
Q: How would you best describe your business’s economic outlook for the coming 12 months?
Predictions about future business performance rose slightly, in line with the rest of the UK. What hasn’t changed is that most firms expect to continue treading water in 2024, with their prospects remaining unchanged.
Q: In general, how do you expect your business to perform over the next 12 months?
Manufacturing firms’ appetite to invest dipped significantly from a high of 81% in September 2023 to 69% in January 2024 as the UK economy continues to perform sluggishly and interest rates remain at their highest levels for some time.
Q: Does your business plan to seek funding for business investment in the next 12 months?
The number of companies that have missed business opportunities because of a lack of available funding continued to fall and this latest figure is in line with the more normalised levels achieved for this question, last seen in May 2022.
At 40% (Sept 2023: 47%), the Manufacturing sector’s responses are very much in line with that of the UK, as a whole.
Steve Gee, CEO of Close Brothers’ Industrial Equipment Division, said: “The recovery in confidence, albeit cautious, among the UK’s small and medium business owners continues, is clearly positive news. However, our research reinforces the feedback we’re getting from the stakeholders in our key sectors that the recovery in sentiment very much depends which industry they operate in. Our commitment to the SME community is that we will continue to work with firms through the cycle, providing expert advice and building long-term relationships, as we’ve always done.”
In the evolving landscape of the manufacturing industry, large global manufacturers have seen the advantages of technology and the successful ones have consistently driven the adoption of digital document management solutions. In the present climate, where manufacturers contend with growing competition, supply chain vulnerabilities, and shifting regulations, a pivotal transformation beckons and manufacturers must elevate their technological prowess.
Now, more than ever, the convergence of unprecedented challenges and
remarkable opportunities necessitates this shift. In order to stay profitable, manufacturers need to accelerate product journeys, conquer global markets, and streamline costs without compromising on quality and customer satisfaction. The good news is that they have a lot of tech tools to choose from and this article can help identify priorities and pick the best ECM for your business needs.
The path to sustainability, efficiency, and elevated outcomes necessitates the automation of both manufacturing and administrative processes. Manufacturers are tasked with
operating smarter, managing costs astutely, and delivering unparalleled results - these are all achievable through the power of digitalisation.
Time-to-value matters and digital tools have the potential to impact various facets of manufacturing positively and quickly, beginning with automation and flexibility in production. It extends further to encompass digitisation and automation in the back office and administrative functions, such as material procurement, financial operations, quality control processes, and human resource management. Manufacturers of all sizes can see almost instant ROI’s from digitalisation investments in these four areas:
1.
By digitising paper records, data flows securely and seamlessly across various departments, overcoming constraints of time and location. Automated workflows are activated following document reviews and approvals. Ultimately, when data can be retrieved, searched, and archived electronically, bottlenecks are eradicated, and processes are expedited. This results in a more efficient and content workforce, thereby enhancing the overall work setting and boosting employee satisfaction.
Manufacturing companies can control unauthorised access to sensitive documents and establish protocols safeguarding proprietary information. A good ECM solution supports adherence to regulatory mandates and effectively protects data from cyber threats through the use of encryption. A secure and compliant document archiving process stands as another significant benefit, especially in the medical, aerospace, and photonics sectors, where government regulations necessitate that manufacturers retain documentation about the parts they supply for the entire lifespan of the respective product or instrument. Overall, the adoption of a paperless, digitised document storage system translates to substantial reductions in time, cost, and stress.
To maintain a competitive edge, it is imperative to streamline time to market, even while an organisation upholds rigorous reporting, compliance, and security benchmarks. Achieving this demands the implementation of an effective document management solution.
Through this approach, all documents pertaining to production, logistics, or accounting procedures are digitised and centrally stored. Be it design blueprints, material requisitions, production records, sales orders, or invoices, staff can conveniently access these documents around the clock, whether situated in the office or working remotely from home. This instantaneous, secure access ensures relevant information is always immediately available, production risks are mitigated, and costs are managed.
Many modern organisations are now prioritising reducing their carbon footprint and embracing paperless operations as essential sustainability goals. By digitising operations and streamlining workflows, companies can make substantial reductions in paper consumption. Embracing a paperless strategy not only conserves precious resources, leading to long-term cost savings for businesses but also plays a role in the preservation of forests. This aligns with the larger mission for many organisations of safeguarding the planet’s essential and fragile ecosystems.
Swagelok Manchester, a leader in fluid systems solutions, embraced digitisation to boost productivity. The switch from paper-based processes to an electronic document management system streamlined workflows. A fourstep plan phased in department-centric implementation, improving order processing and inventory tracking. With top data security and time-saving benefits, 70% of daily invoices are now emailed.
1. Prioritise simple and frequently used business processes –Automated processes effectively decrease the time and effort required from employees, resulting in higher productivity. So, it’s essential to prioritise business-critical processes that align with objectives.
2. Improve paper-based processes instead of emulating them – Seize the chance to remove unnecessary steps during the process of digitisation. Reflect on the rationale behind previous procedures and assess whether those actions remain essential within this new context. Embrace enterprise content management (ECM) systems and encourage employees to digitise files, memos, and reports instead of relying on hard copies.
3. Take advantage of the cloud - By choosing the cloud, the responsibility for system upgrades and security patches shifts to the ECM provider, simplifying scalability without the need for additional inhouse IT resources. Cloud systems also cater to mobile device users, ensuring secure remote work settings and enhanced flexibility for teams.
4. Electronic signatures offer tighter security and easier compliance –choosing a provider who offers this can further protect your business. E-signatures hold legal validity, fulfil security prerequisites, and mitigate the potential for document alterations, unauthorised signatures, or missing signatures.
In the dynamic landscape of manufacturing, embracing digital transformation is pivotal to sustainable success.
- David Malan5. Streamline with automationWorkflow choices can substantially diminish the duration required for manual tasks. Automated workflows mean individuals can effortlessly transmit documents with a simple click, ensuring that everyone has instant visibility into their designated tasks.
In the dynamic landscape of manufacturing, embracing digital transformation is pivotal to sustainable success. As industry challenges intensify, manufacturers must invest in technology to streamline operations, conquer markets, and manage costs effectively. Manufacturers who successfully navigate this path of digitalisation will reshape their industry landscape, foster innovation and thrive for years to come.
DocuWare is built for the dynamic needs of manufacturers, in fact almost 20 per cent of our customers are from the manufacturing industry. Our ECM solution organises, archives, secures and processes critical business data: employee documents, client records, compliance and certification information, and much more.
Find out more and read how our Manchester-based customer used DocuWare to improve their business here.
With the continued rise of offsite construction, and the prefabricated building systems market booming, Elta is proud to offer its innovative ‘Prefabricated Solutions’ service, catering to a wide range of fan applications, including smoke fans. The solution is set to help cut installation costs and speed up building projects with greater efficiency and compliance while enhancing site safety.
Modern Methods of Construction and offsite initiatives are growing exponentially across the UK. To highlight this, last year, the Crown Commercial Services selected 29 firms to be part of the £10bn Offsite Construction Solutions framework, with public sector buildings across healthcare, education, justice and defence all expected to swing toward modular construction.
Elta’s Prefabricated Solutions service is ideal for specifiers and contractors working on commercial building projects of any scale. Fans and ancillaries, such as acoustic equipment, mounts, panels, flexible connections, fan controls and more, can all be assembled offsite and delivered as a compliant assembly. These are then ready for crane lifting, resulting in quick, efficient installation. The ventilation and air movement manufacturer is one of the first in its sector to offer this kind of solution across multiple fan types and ranges.
Colin Moss, Car Park and Spoke Control Manager at Elta, has pioneered the
Installing individual components onsite can be a cumbersome and time sensitive task
service and elaborates on the multiple benefits specifiers and contractors can gain by going down the prefabricated assembly route. He said: “Installing individual components on-site can be a cumbersome and time sensitive task. It requires ample storage and working space, leading to congestion on busy sites and increasing the potential for site safety issues. The collection and assembly of various parts can also be time-consuming, causing delays to projects.
“Not only this, but site time is costly, and labour costs can quickly add up when dealing with unnecessarily complex, site installations. With Prefabricated Solutions by Elta, these challenges are a thing of the past, and you can manage these expenses and have better quality control of the finished product.”
A key benefit of the new service from Elta is the provision of both acoustic and air flow performance data when engineering a solution. Using Elta’s selection software, the acoustic performance data can be supplied at the initial stages to help simplify the process for specifiers and contractors.
This means an engineered acoustic solution can be developed from the start, and there is no need to re-select or re-calculate separately were they sourcing these components from elsewhere.
Elta’s Prefabricated Solutions service means units are built to the highest standards within a controlled factory environment. The company, which has UK-manufacturing sites in Kingswinford, Fareham, and Colchester, is certified to ISO 9001, meaning even units built to bespoke specification will still be accredited and, importantly, all smoke fans are certified with the ancillaries and mounting base.
Luke Hammond, Applications Specialist at Elta, explains that prefabricated assembly of fans also unlocks a host of other benefits. These include a more streamlined design process, offering simpler compliance with both ‘The Golden Thread’ and environmental requirements while reducing disruption to the local community, and other related site activities.
“Gone are the days of waiting for single components to be delivered to the site, which can get lost or damaged while other elements of the project are in transit. With our Prefabricated Solutions service, all necessary components are packaged together, ensuring a hasslefree delivery,” said Luke.
“Preassembled units also mean other costly, disruptive activities on-site, such as crane lifting and road closures, can be minimised. Shipping materials like pallets, packaging and strapping is all reduced as well, and with better overall coordination, Prefabricated Solutions allows workforces to focus on boosting productivity in other areas.”
For more about Elta and its Prefabricated Solutions service, visit https://eltauk. com/prefabricated-solutions/
Recently published data in March 2022 summarises how the gender composition of the UK’s engineering workforce has changed over the last 11 years and confirms unsurprisingly, that engineering remains a very much male-dominated field. However, the trends are gradually shifting, confirming that while the percentage of women in engineering has increased, the increases are concentrated in certain roles. In 2010 just over 1 in 10 (10.5%) of those working in engineering roles
were women. Fast forward to 2021 and the percentage had risen to 16.5% (Source, ONS) with the rates of change (in terms of gender balance) focussed on the associate and technical professional levels, rather than managerial or director level.
A good example of how women are becoming increasingly involved in engineering is at precision bearing specialists CARTER MANUFACTURING, where in her position as Sales Director, Francesca Brundell-Romero is
proving to be an outstanding success. In a revealing interview with Francesca we learn about her journey, growing up amidst the world of bearings and her ascent through the ranks of this complex and fast-expanding industry sector. From very early exposures to bearing events and factory visits to pivotal roles in Carter’s US offices and now at Carter’s UK HQ in Oxfordshire, Francesca shares her insights and experiences. This is through the recent global challenges along with the evolving landscape of gender representation in a traditionally maledominated industry sector.
What was it like growing up with family in the Bearing Industry?
“From a young age I was experiencing bearing industry events and exhibitions, meeting many businesses who we still work with today. This allowed me to improve my customer engagement skills and I think people like to ‘buy’ from a familiar face”.
Attending Conferences helped sow-the-seeds
“In the early years I was too young to ‘officially’ attend conferences and events, but I did interact and meet people briefly. As I got older I started attending conferences and enjoying and exploiting the benefits of socialising with customers. For example, Bearing.Net is a good annual event to meet familiar faces in the industry and catch-up on the latest worldwide industry and environmental trends”.
“Visiting suppliers on an annual basis is critical to maintaining a fluid and consistent relationship with all our customers. This has enabled us to build long-lasting relationships helping to ensure that suppliers are more available and understanding when more complex inquiries occur. This also provides us with the opportunity to see first-hand the factory environments of our suppliers and to ensure manufacturing processes are of the highest quality”.
University placement at Carter Inc. Valuable Experience in External and Internal Sales, Bearing Assembly and Manufacturing
“Following on from studying International Business at Nottingham Trent University I worked at Carter Inc. in Michigan where I got the opportunity to assemble bearings and start by working in the workshop and seeing the ‘back-end’ of factory work from assembly to packaging and delivery. Basically, women doing the assembly work and the men operating the machinery. I then moved on to do more business development work where I was given projects on cold-calling potential customers for certain products and industry sectors which Carter Inc. were particularly interested in. I also had the
From a young age I was experiencing bearing industry events and exhibitions, meeting many businesses who we still work with today.
opportunity to do some regional sales where I travelled around Michigan, Chicago, Indiana and Texas for scheduled meetings and drop-ins.”
“I began working at Carter UK mainly focussing on the sales inbox and supporting Unasis, Carter’s sister company. The role progressed through to business development once the team expanded and led me to the position of Head of Sales, managing the sales team and supporting the account and business development managers. Throughout this time I was exposed to many external trips due to it being through the post-Covid period when everyone was keen to meet again. I visited Germany, Sweden and the USA to name a few locations where I was able to optimise business relationships, whilst the team managed the sales inbox back in the UK”.
“The company recently expanded by opening new offices in both USA and Spain whilst also increasing our headcount at our UK HQ. The combination of this has meant we’ve gone through an internal re-structure creating an opportunity for more roles and promoting my role up to Sales Director. This means my role is even more varied and has shifted into many different elements of the business where I oversee the Sales Team and delegate down to our Technical Manager who can filter through the requirements and expectations to the Sales Team. My main interest and focus still lies within sales and customer relationships, so I manage my time by reviewing and optimising
the Sales Team whilst also managing a select number of key accounts”.
We asked Francesca, Do you feel there were any barriers as a woman?
“There are fewer women employed in the bearing industry, compared to other manufacturing sectors, so initially it can be daunting. I didn’t have a technical upbringing so I’ve had to rely on the engineers to fill the gaps in my knowledge. I think it can be seen as a bit of an old boys club with an assumption that as a woman I don’t know what I’m talking about! But I don’t feel like I’ve ever not been taken seriously because of my gender”.
Do you see growth in women in the bearing industry?
“At the first BearingNet conference in the early 2000’s I can remember seeing roughly four to five women in total, since then the female representation has grown and grown, probably by as much as three to four times. Looking more locally Elif has recently joined us as the first female Engineer at Carter and I’ve definitely seen progression in the last few years”. To sum up her journey so far and her hopes for the future, Francesca comments, “I can definitely see a movement in the Bearing industry which includes and holds space for more women. It’s definitely inspiring to see this growth and change offering equal opportunities to both males and females and I look forward to seeing what the future holds”.
Let’s talk sustainable waste management. Ok, it’s not the sexiest topic, but at Waste Mission, we believe there’s never been a more important time to get serious about waste.
Did you know? The latest government data shows the UK generated an estimated 40.4 million tonnes of commercial and industrial (C&I) waste in 2020, of which 33.8 million tonnes (84%) was generated in England. The latest estimates for England only indicate that C&I waste generation was around 33.9 million tonnes in 2021.
Sadly, the amount of commercial and industrial waste generated by businesses is having a massive impact on the environment. Most of this waste ends up in landfills, generating greenhouse gas emissions 25 times more effective at trapping heat than carbon dioxide.
This is terrible news for our planet. And consumers are not ignoring the facts.
Deloitte’s 2023 Sustainable Consumer survey revealed that 30% of consumers had stopped buying products due to ethical or sustainability-related concerns. And almost 50% see circularity (explained in more detail later) as essential for buying a product.
If those aren’t reasons enough to reconsider waste management within your business, then how about this statistic: Every year, UK businesses can spend between 4–10% of their average annual turnover on waste disposal.
That’s a significant chunk of profit.
Your waste challenge may seem complex, but let’s explore sustainable waste management and how we can help turn your waste into savings.
For actionable strategies check out our recent waste management blog.
Instead of collecting, transporting and disposing of waste, sustainable waste management looks for solutions that won’t harm the environment or human health and instead focus on reducing natural resource consumption.
Sustainable waste management revolves around a hierarchy:
• Reduce the initial amount of waste generated
• Reuse where possible
• Recycle what can’t be reused
• Sell what we can
• Only then, dispose of what’s left
“We already work with a range of major electricity network operators, offering them unique services for their transformer and switchgear recycling, ensuring that nasty elements like PCBs and F Gases are safely recycled. Additionally, we are developing some unique technologies in the WEEE waste sector, allowing us to extract precious metals from WEEE waste.”
Nicola Guest, Waste Mission’s Group Marketing ManagerFrom helping to reduce carbon emissions to improving air and water quality to commoditising waste streams that may be currently running at a financial loss – sustainable waste management has incredible environmental, economic and social benefits.
This type of model, where everything is reused, repaired or recycled, can also be understood as the circular economy.
With natural resources depleting and CO2 emissions rising, now is the time to embrace the circular economy.
Circular practices promote restoration and circularity rather than products reaching their end-of-life (linear economy). The result is less waste and a closed loop in the industrial ecosystem.
While some manufacturers are making positive steps forward, a 2023 report by Qflow revealed that although the construction industry generates 62% of the UK’s waste, only 2% is reused. This report highlights an incredible opportunity for increasing the adoption of circular practices within this sector alone.
It can be challenging transitioning to a circular economy. Yet, it’s important to remember that circular economy strategies can turn waste into savings. They stimulate local economies by converting waste into raw materials for production and generating sustainable employment growth.
At Waste Mission, we can educate, inspire, and facilitate waste reduction for your business by collaborating with you and your supply chain to innovate
and identify “waste” materials for conversion into valuable recyclable commodities.
Discover more benefits of the circular economy in our recent blog.
From groaning landfill sites to ecosavvy consumers and wasted profit, there are multiple reasons to embrace a sustainable waste management strategy and reduce the amount of waste your company produces.
Plus, let’s not forget how there are growing concerns around securing supply chains in an ever more volatile world. But, the great news is that sustainable waste management practices can help manufacturers ride the fluctuation in raw material prices.
We firmly believe that to achieve a more innovative and sustainable future, manufacturers in the UK need to
prioritise long-term sustainable waste management goals.
And that’s where our team at Waste Mission can help.
Waste Mission transforms complex waste into simple solutions.
At Waste Mission, we are driven by our unwavering commitment to doing what’s right – for our clients, staff, and the planet. No matter the complexity of the task, we want to simplify waste solutions for UK industries and manufacturers. We aim to educate, encourage and uncomplicate waste management by offering a bespoke, tailored service, all from a single point of contact.
Our responsive team of experts becomes an extension of your business, taking care of waste so
you can stay focused on your core operations. We promise to:
1. Guide you to reduce waste and increase your profitability
2. Help turn your waste into solutions, reducing reliance on new materials
3. Navigate complex regulations for you, ensuring you meet environmental and legal requirements
4. Provide a waste portal so you can easily access data on your waste production, recycling levels, and carbon footprint.
“What separates Waste Mission from their competition is the level of professionalism and transparency they bring to the industry. They continue to question the status quo and propose initiatives to drive our business forward.”
LG Flexitallic
If you care about your environmental impact and are looking for a reliable partner to help navigate the complexities of your waste management, then we’d love to talk.
To book a waste review or learn more, visit our website wastemission.com, call us at 01438 745307 or email control@wastemission.com or visit us at stand 6-545 at MACH.
Talema Group, a leading manufacturer of toroidal transformers and related magnetic components, has appointed Vanessa Berry as Midwest Sales Manager to work on behalf of EG Magnetics Group and drive the company’s growth in the region.
The EG Magnetics Group, a business area within KAMIC Group, serves a global customer base and offers a comprehensive portfolio of power magnets. The unit includes five specialist businesses: Talema Group, AGW, Avon Magnetics, ETAL and SIGA Electronics, with over 1,100 employees, manufacturing in five countries and direct representation in the world’s most significant economies.
In her new role, Vanessa will be responsible for driving Talema’s Midwest sales activity and will lead a team looking to continue the growth of its customer base in the region, promoting its global portfolio of products.
With a background in pharmaceuticals and key account management, Vanessa has over 25 years of experience and joins Talema Group from Dexter Magnetics where she spent six years leading significant accounts. She recently completed a bachelor’s degree in management at Concordia University in Chicago and will draw upon these experiences in her new role.
Sealy UK expands leadership team as it plans for continued growth
Sealy UK, part of the market leading global network of Sealy International businesses and manufacturer of the famed Sealy Posturepedic mattress, has announced a new senior hire for the business, as sales continue
to build following three years of transformation under new ownership.
Neil Clark has been appointed as Sealy UK’s General Manager, having previously worked as Managing Director for UK & Ireland and Regional
Director for Northern Europe & South Africa at Franke; a globally renowned leader in kitchen sink-ware and taps.
During his impressive 19-year journey at Franke, Neil assumed several senior roles, including sales and marketing directorships, honing his expertise in strategic leadership.
In his new role, Clark will spearhead the company’s strategic growth initiatives, positioning Sealy within the premium sectors of the UK’s mattress market, with a continued focus on NPD.
Mark Tuley, Chief Commercial Officer at Sealy UK, commented: “We are thrilled to welcome Neil to the Sealy family. His proven leadership, coupled with a passion for high quality local manufacturing, perfectly aligns with our vision for the future.”
This new appointment underscores Sealy UK’s commitment to reinforcing its position as a leader in the industry, driving innovation, and delivering exceptional, world-class products and services to customers across the UK.
For more information about Sealy UK and its offerings, visit: www.sealy.co.uk/contact-us/
Saving Technology
enquiries@dalby.co.uk
Gas Fired or Full Electric Option
Automatically modulating airflow with 100% in Performance mode & 50% in Economy mode.
“HighLight” high performance LED lighting system
Hi-visibility Mode indicator countdown timer
‘ProActive’ Touchscreen control
Stop/Start energy saving technology
Energy consumption as low as 1KW*
Energy Savings Of Up To 65%*
AquaDry blowers
Invertor control
Rear Extract, Pit extraction or Raised Floor airflow options
Conveyorised line options
Space Saving Design
Energy cost per job recording
Robotised paint application options
Turnkey installation available