MANUFACTURING PRODUCTION
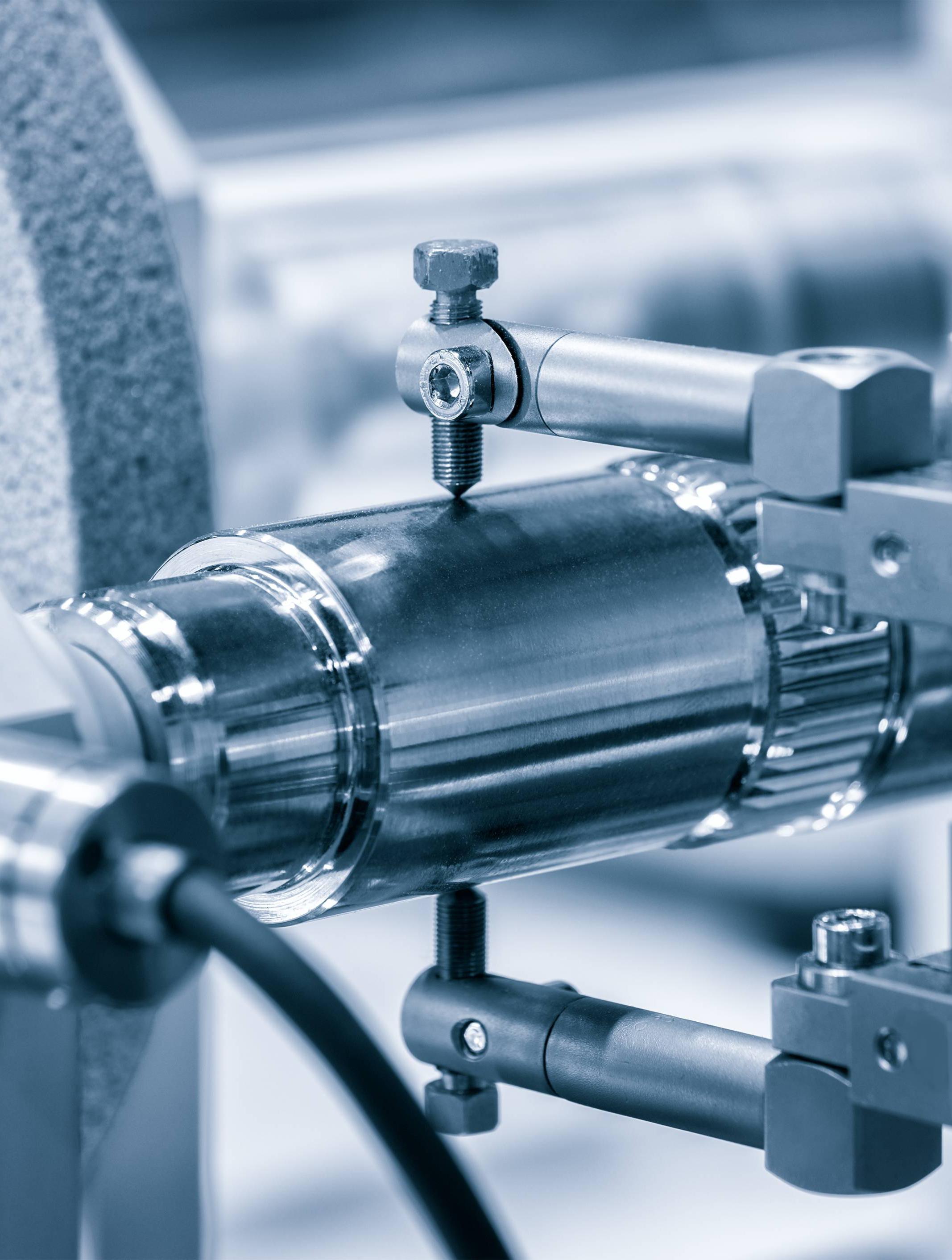
INTERVIEW
WOMEN IN ENGINEERING: Q&A WITH BARBARA HATHAWAY
DRIVES & CONTROLS
KEEPING INDUSTRIAL CONTROL WITH ASICS
ENGINEERING



















































































































































































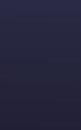
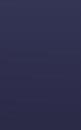
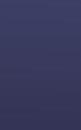



























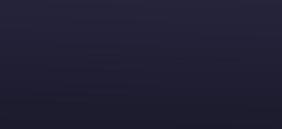
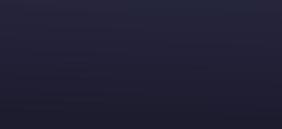










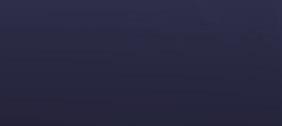

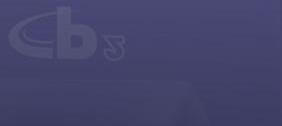

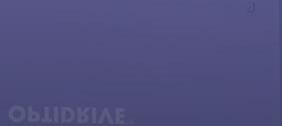













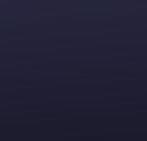
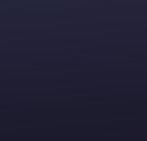
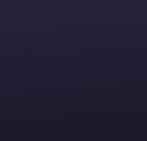
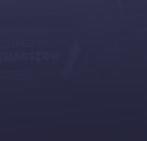
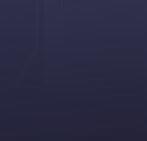
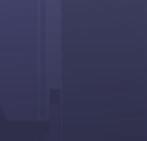
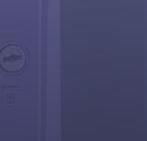
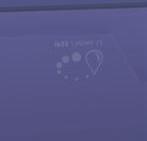
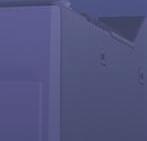









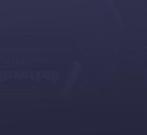
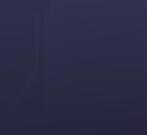

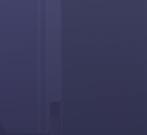
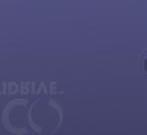
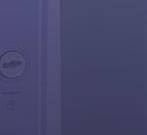
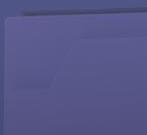
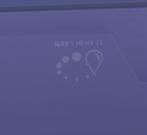
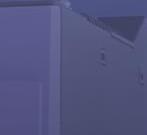










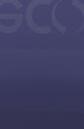
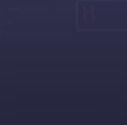
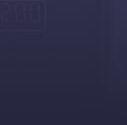
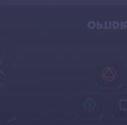
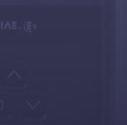
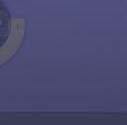
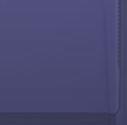
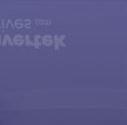
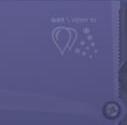













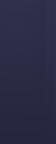
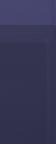
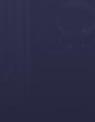


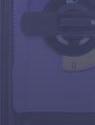
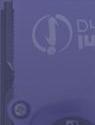









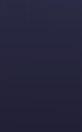
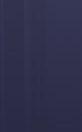
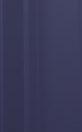










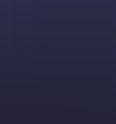
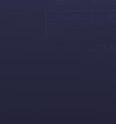
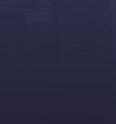
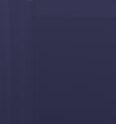
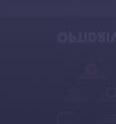
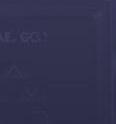
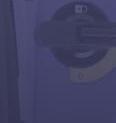
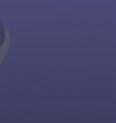
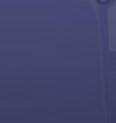
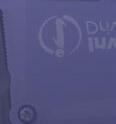
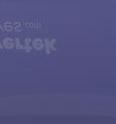
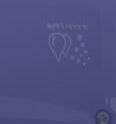
















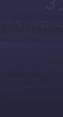
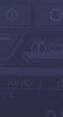
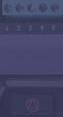
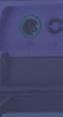



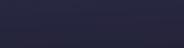

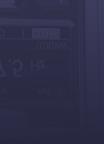
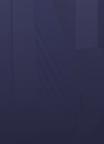
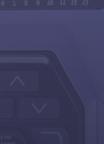
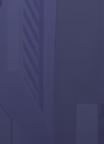
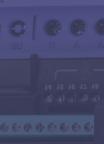
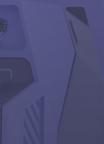












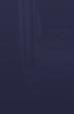
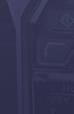
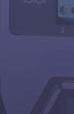
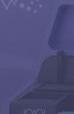





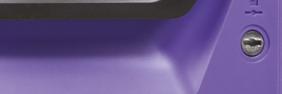
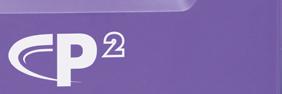

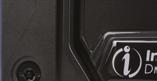
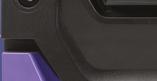

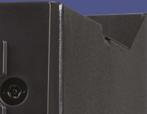
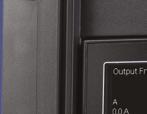



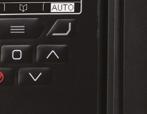


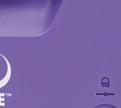
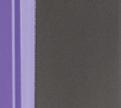
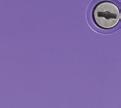
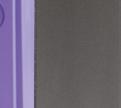
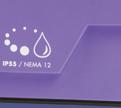
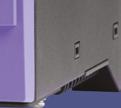





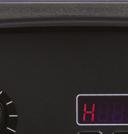
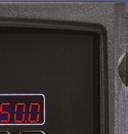
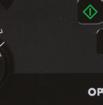
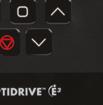





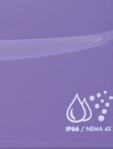





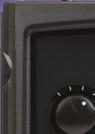

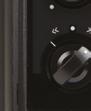








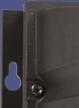


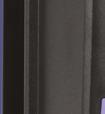

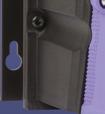



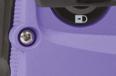
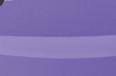
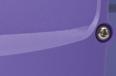

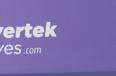






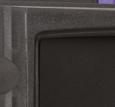
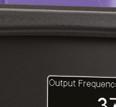
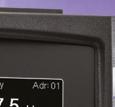
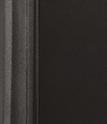
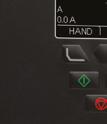

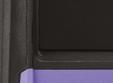
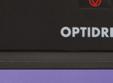
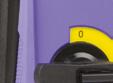
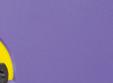





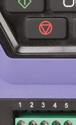
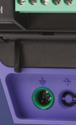




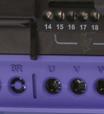






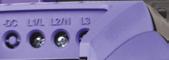
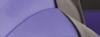
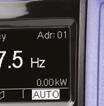
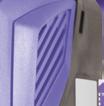
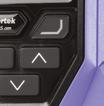
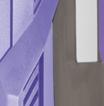











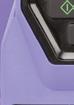
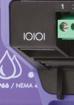

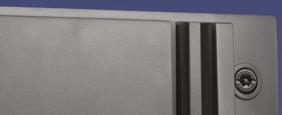
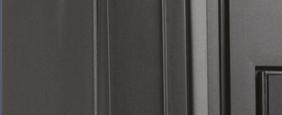
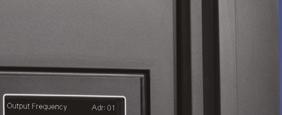
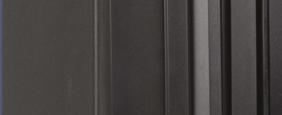

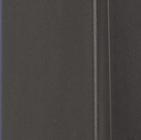
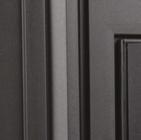

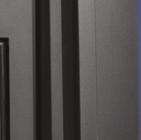

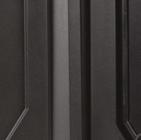

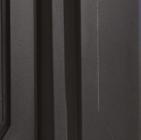
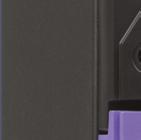
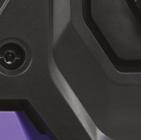
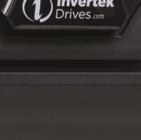
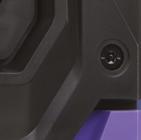
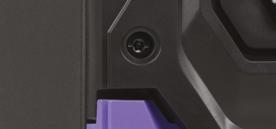
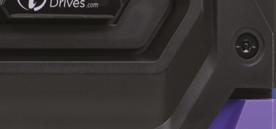



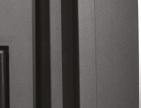
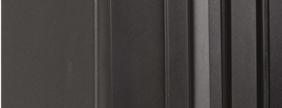
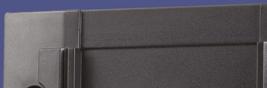
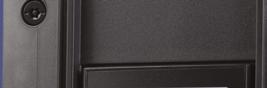
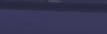
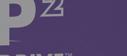
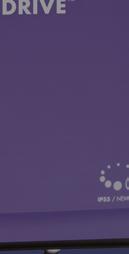




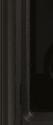
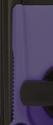


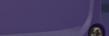
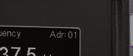
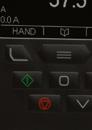

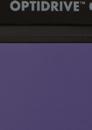





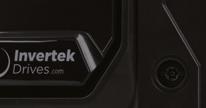





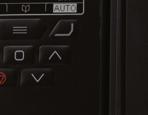
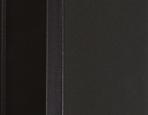


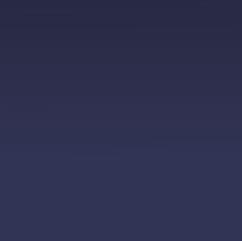


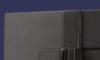

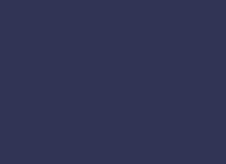




INTERVIEW
WOMEN IN ENGINEERING: Q&A WITH BARBARA HATHAWAY
KEEPING INDUSTRIAL CONTROL WITH ASICS
Altus Group, the leading distributor of capital equipment for electronics assembly in the UK and Ireland, recently partnered with SKALARKI electronics Ltd, specialists in flight simulator design and manufacturing, to further enhance its production capabilities. The collaboration aims to elevate SKALARKI’ S manufacturing capabilities by providing state-ofthe-art equipment from Essemtec.
Recognising the market need for flight simulators, Skalarki’s operations expanded over the years, and last year the company moved to its own stateof-the-art 900m² facility, providing a
solid foundation for its ongoing growth.
In order to develop their production processes and meet the advanced requirements SKALARKI consulted with Altus Group to add to their assembly technology.
The company invested in equipment from Essemtec, an industry leader in SMT pick-and-place equipment and intelligent production storage and logistic systems.
Joe Booth, CEO of Altus Group, said: “SKALARKI’ S commitment to delivering top-quality flight simulators and their drive to continuously improve production aligns perfectly with our mission to provide cutting-edge
solutions to our customers. When we assessed SKALARKI’ S requirements, it became evident that Essemtec’s innovative equipment was the obvious choice.
“The Essemtec Fox SMT Pick and Place unit, with its remarkable versatility and compact size, along with The Lizard Convection Reflow Oven, offer SKALARKI the perfect combination of flexibility, efficiency, and precision.
“We are confident that these state-of-the-art machines will enhance SKALARKI’ S manufacturing capabilities, enabling them to deliver quality products quickly and efficiently.”
Marcin Kapera, SKALARKI Company Director, added: “Manual assembly has its limitations. As we expand to a commercial market, our products face advanced requirements and must meet higher expectations.
“Implementing automated assembly processes will allow us to meet quality standards quickly and efficiently.”
SKALARKI plans to maximise its investment in Essemtec equipment over the next 18 months, utilising the machines to ensure a seamless transition into full-scale production.
Altus Group looks forward to seeing the impact of the Essemtec machinery on SKALARKI’ S production of PCBAs.
To find out more visit www.altusgroup.co.uk
Some two years after introducing LiBiao robotic parcel sortation technology at its sorting centre in Athens, Hellenic Post (ELTA), the state-owned provider of postal services in Greece, has introduced additional robots, chutes and induction stations at the site.
The investment means throughput capacity at the Athens facility has been significantly increased and allows ELTA to provide next-day delivery services
to several additional destinations throughout Greece.
In all a total of 120 LiBiao autonomous mobile robots (AMR) are now deployed at the sorting centre in Athens. They scan each parcel’s barcode, weigh the package and, directed by sensors, empty it into the appropriate mail sack sited around the platform on which the robots travel.
Initially introduced as part of ELTA’s digital restructuring programme which was established to tackle the growing number of parcels generated by the growth of online shopping, the AMRbased sortation solution has enabled ELTA to improve the efficiency of its workforce by assigning personnel to more productive tasks.
Before the LiBiao sorting system went live, ELTA had undertaken parcel sorting manually – which was obviously extremely time consuming and labour
intensive. It was also prone to errors which caused parcels to be delayed. Late deliveries were not only frustrating for ELTA’s customers and courier partners but also extremely costly for the company.
Since the parcel sorting function has been handed over to the LiBiao robots the process is three times faster, ensuring next-day delivery, while errors have been virtually eliminated.
With the additional robots, ELTA can now handle close to 125,000 parcels weighing up to 10 kg every day and, because each robot only needs to be recharged for five minutes every four hours, on-site power consumption and energy costs are minimised.
Based on the performance of the first phase of the installation ELTA expect this latest investment to pay for itself within two years.
Website: www.libiaorobot.com
Helping ease global supply chain disruption has seen Nemco extend its working relationship with one of the world’s leading designers and manufacturers of customised safety equipment.
The Stevenage-based contract electronics specialist is celebrating 10 years of supplying Fortress with assembled PCBs for a growing range of products that keep hundreds of thousands of people safe every day.
What started as prototype support and a few thousand assembled PCBs has now grown to volumes in excess of 90,000 per year and covering more than 50 different board variations across various solutions, including mGard trapped key, proNet, amgard ethernet enabled interlock, Atom and tGard configurable interlocks.
The business will be worth £2m per year for Nemco, which is on course to hit its bestever sales year.
Rhodes Interform, the UK manufacturer of hot and cold forming equipment for metals and composites, has secured a new contract with Cascade (UK) Limited to produce a bespoke twin press facility for forging forklift truck forks. Cascade UK is part of Cascade Corporation, a leading manufacturer of material handling products.
Rhodes Interform will manufacture a complete robotic handling line including a horizontal hot forge upset press, a horizontal bending press and integrated conveying system. The facility will use the latest robotics technology to provide a fully automated solution, replacing an existing manually operated line.
The bespoke project involves Rhodes Interform engineers designing a manufacturing cell to fit within a relatively confined floorspace in Cascade’s factory yet still retaining the ability to manipulate and position the product between the two presses. The new fork line will be fully programmable with memory recall to forge Cascade’s small to medium product range, resulting in maximum throughput with minimum inventory.
Peter Anderton, Technical Director for Rhodes Interform, said “We are delighted to be able to supply Cascade with a fully automated process for forging forklift truck arms. The solution we have designed offers accuracy, repeatability and programmable flexibility, with the added feature of process memory re-call. Manufacturing automated solutions is a major part of our business, generating major time and laboursaving benefits for our blue-chip customer base.”
Rhodes Interform will manufacture and install the automated line at Cascade’s factory in Openshaw, Manchester.
Jed Shaw from Cascade, said: “We are making a major investment in our plant to upgrade from a manual to a fully automated process. We chose to work with Rhodes Interform as the company has the skills and experience to be able to provide a bespoke solution, full turnkey package, technical support and installation capability. This will represent a large step forward in futher facilitating a class leading product.”
For further information, call 01924 371161 or visit the website www.grouprhodes.co.uk.
There has been a lot of talk about disruption in the electronics supply chain and this is something Nemco has helped Fortress overcome through flexibility of supply, just-in-time production and providing alternative components to negate shortages across the sector. This has ensured that many Fortress products can be supplied to customers in just two weeks, thanks to forward scheduling and advancing ordering.
Nemco, which was formed in 1985 by Dave Pearce and currently employs 130 people at its 60,000 sq ft Wedgwood Way facility, has identified significant opportunities in the automotive, aerospace, renewable energy and EV sectors and is planning to make significant inroads in the years ahead.
The company has made several strategic appointments in recent months and also joined the Manufacturing Assembly Network (MAN), a collective of seven subcontract manufacturers and an engineering design agency. This will see it tap into best practice, learning and development opportunities and, importantly, access to new opportunities that will arise from being part of the group.
For further information: nemco.co.uk or fortress-safety.com
What does your average day look like?
The day normally starts with a team meeting which can be scheduled across the morning - we discuss priorities and anything important that’s been scheduled for that day. This can include preventive maintenance and development of test equipment and fixtures on the production lines.
From there, I move into new product development meetings with other departments across the business, including Product Marketing and Software Development and Firmware Test and Validation teams, part of Tunstall Technology Group. This can also be part of wider project planning, where business strategies are discussed.
I make sure I prioritise early afternoons to engage with my team on all the test and development work being undertaken. This is probably my favourite part of the day - for me, it’s the hands-on, technical work I really enjoy! Finally, in the late afternoon I go through and review all the production statistics - yields, throughputs, KPIs and OEEs so I’m ready to take on the next day.
What are your main roles and responsibilities?
I am responsible for the design, development, implementation and the maintenance of all factory processes that are required for manufacturing products here at Tunstall in-line with the latest BSI ISO quality standards.
We generate digital solutions that enable providers to deliver integrated, efficient and personcentred care in the community, that empowers people to live more independently and with an improved quality of life.
This is a huge responsibility as a pioneering business in the technology sector for the health, housing and social care markets, quality standards are of the utmost importance. Myself and my team develop test
equipment, fixtures and assembly lines in-house which incorporate state-of-the art technologies used throughout the industry.
How long have you been in the industry?
I have worked at Tunstall Healthcare for over a decade now, starting out as a Senior RF Engineer back in 2012 and working my way up. Prior to that I was a post-Doctoral Research Associate at the University of Leeds. I’m also a proud and active member of the Institute of Electrical and Electronic Engineers (IEEE).
What do you like most about your role?
I love the hands-on part of my role and feel very lucky to have the opportunity to get involved and stuck in with my team developing new innovative test systems that improve production yield and throughput.
As technology advances and solutions become increasingly digital and cloud-based, we are developing new products that can predict and even prevent emergency events, using data-driven insights. Our focus is on creating a more connected world that fulfils the potential of technology to offer intelligent care and support, and give people greater choice and control about how they live their lives.
Currently we’re building our next generation of platforms with data at the centre, using technologies such as machine learning and AI to enable quicker and data-driven decision-making to determine whether someone’s health could be about to deteriorate and action accordingly.
My line manager is also my mentor, and thanks to her support and guidance I lead the team to develop and incorporate state-of-the-art technologies into our production processes, continuing the legacy of Tunstall as an innovator and industry leader in health and care technology provision.
Engineering Manager at Tunstall Healthcare
Myself and my team develop test equipment, fixtures and assembly lines in-house which incorporate state-of-the art technologies used throughout the industry.
- Kashif Saeed
A manufacturing partner who helps over 5000 UK businesses save money on part production.
¥ Upload your design file for an instant quote (.stl, .step, .igs, .obj).
¥ Parts to your door in 3 working days on our express service
¥ Easy application trade account - 30 days interest free
¥ Specialists in low volume batch production and one off prototypes
¥ Discounts available for batch production
FREE SAMPLE PACK scan the QR code and fill in your details
At Close Brothers Asset Finance we regularly survey business owners in the sectors we fund, including Manufacturing. Taken from our latest survey, in this piece we focus on attitudes to ‘funding’, finding out, for example, if firms are planning on seeking funding, and if they’re confident about getting access to the loans they need to grow their business.
A key finding is that only half of Manufacturing firms are aware of Asset Finance, meaning a large number still haven’t taken advantage of the many benefits to be gained from leveraging value from their existing assets.
A third of Manufacturing business owners say getting access to funding is a ‘major challenge’ and more difficult now than it was a year ago. A further 56% tell us it’s a ‘moderate challenge’ and as difficult now to access finance as it was a year ago. Only 5% say it’s become easier.
Exactly 40% admit to having been declined access to finance by a bank in the last six months, but despite the additional challenges, 77% of Manufacturing firms are planning on seeking funding for investment in 2023, although 63% have delayed their investment decisions because of market uncertainty.
Funding options ranked in order of popularity: 1.
Unfortunately, 47% of Manufacturing respondents to our survey stated they had missed a business opportunity in the last 12 months because of a lack of available finance.
The increases in the cost of doing business, compounded by significant energy price rises, has had a major impact on businesses in all sectors, including Manufacturing, leading to 47% of firms in the industry needing to take out finance just to cover higher energy costs.
Nearly seven in 10 (67%) business owners disclosed that their energy bills had risen, with a further 59% stating it had impacted their profitability. As a consequence, 91% have implemented various energysaving measures, including (in order):
1. Switching off lights
2. Lowering the thermostat
3. Turning off air conditioning
4. Insulation
5. Switching providers
Interestingly, well over half of firms polled said they’d consider moving to a four-day week to save on energy costs, which is well below the UK average of 57%.
For more information, please visit: closeasset.co.uk/manufacturing
A third of Manufacturing business owners say getting access to funding is a ‘major challenge’ and more difficult now than it was a year ago.
Nearly seven in 10 (67%) business owners disclosed that their energy bills had risen, with a further 59% stating it had impacted their profitability.
With specialist industry knowledge and tailor-made support, we offer a range of finance options which can:
• Unlock the value of your existing assets
• Let you invest in new equipment
• Create positive cash flow for your business
Contact us today, we’re here to help
closeassetfinance.co.uk/mpe
Products and services are subject to eligibility, status, terms and conditions and availability.
All lending is subject to status and our lending criteria. The right to decline any application is reserved.
Water is at the front line of environmental crises and has been for over a decade. Driven by climate change, growing populations, increasing economic activity and poor water governance in both public and private sectors, water scarcities are causing regional emergencies around the globe, with implications for industrial companies across all sectors. Joe Higgins explores how companies like Envirogen can help businesses develop effective solutions.
Global shortfalls in the water supply are predicted if current consumption and production patterns do not change. According to a study by the Organization for Economic and Cooperative Development (OECD), worldwide water demand is expected to increase by 55%*, with demand for water in manufacturing expected to increase four-fold by 2050.
Most industrial processes utilise water as a component of the final product, part of the production process, or even indirectly, through energy use. Substantial volumes of water are consumed by industry.
Companies in sectors such as food and beverage, energy, chemicals, pharmaceuticals, and mining account for 70%** of the world’s water use. They have the opportunity and may be required by legislation, to play a critical role in the transformation to a watersecure world by conserving water and maintaining low energy and waste operations.
LEFT AND ABOVE: The Elan Valley (Mid-Wales) reservoir has its banks on show following Summer 2022 droughts.
Its primary purpose is to supply Birmingham, UK, with water, as well as Herefordshire via the river Wye.
Building water-resilient business models is one of the most pressing challenges for those interested in developing a safer, more circular, and sustainable industrial economy. Finding commercially efficient ways to lessen the impact of water withdrawals via water recovery, recycle and reuse becomes more critical than ever. It can happen and is happening.
Saving water simply makes good financial, environmental, and social sense
Water security and resilience is emerging as a core strategic consideration among many manufacturers. In the wake of extreme droughts, some of them very longrunning, and exposure to water stress, more and more manufacturing companies are recycling wastewater whenever reuse can be implemented as a feasible, cost-effective option.
Manufacturers are taking control of their water management with on-site “behind the fence” solutions, resulting in increased investment in water reuse to maximise the use of water in the plant. Operational efficiency and sustainability can be expected to increase, along with improved production capacity, due to the increase in available potable water.
Limiting dependency on outside water allows manufacturers to leverage reuse to reduce water supply costs, moving them closer to zero liquid discharge systems, with the added benefit of reduced discharge costs. Businesses can also demonstrate corporate social responsibility (CSR) commitments via water stewardship which, for consumer-facing brands, are of direct economic value to companies. We have instigated numerous re-use / recycle projects where there is a significant return on investment, generally within 2 years, thereby not only reducing water footprint and improving system resilience but also supporting operational efficiency through cost reduction.
Those companies that are perceived to have better environmental practices may see improved brand value, a subsequent expansion in sales, and, where they are listed, an improvement in share price. On this subject, the investment landscape has been broadened and deepened through the addition of environmental, social, and
- Joe Higginsgovernance (ESG) opportunities, for example, in ESG investment trusts and funds and individual ESG stocks.
Numerous methods can be considered, depending on the quality and volume of the water to be recycled, as well as reuse applications. Industries can recapture and process wastewater that would otherwise be lost to trade effluent whilst in many cases incurring discharge costs, and recycled water can be used for a variety of applications. Included among the applications are washing, rinsing, plating, spraying, coating, cooling, boiler water makeup, cooling tower make-up and fire suppression systems. In some cases, their effectiveness will be impacted by space constraints and budgetary considerations.
The degree of treatment required varies according to the specific reuse application and associated water quality requirements. Water reuse generally takes place by combining several processes or technologies - depending on the case - such as biological or physicochemical treatment, solids separation, gravity and/or membrane filtration, evaporation, disinfection, membrane or ion exchange demineralisation, and advanced oxidation. We provide value engineered solutions implementing all of these technologies.
Finding a treatment solution that’s right for a company’s specific needs begins with answers such as these to the following questions:
“What volume of water is sent to drain and what quality is it?”
Reaching a sustainable, cost-effective solution is paramount, and companies will need sufficient data to make informed decisions. Typically, this will mean measuring peak flow rates, volume, quality and cost of water sent to drain, as well as benchmarking against international high performers. A thorough analysis, including return on investment (ROI) and payback calculations, can help determine what type of water reuse system is needed in a facility and which recycling measures will pay off both from sustainability and cost perspectives - and in line with water treatment obligations.
“For what applications can we reasonably use reclaimed water and where are these located onsite?”
It’s important to look at the manufacturing system in its entirety. A complete process flow diagram of a plant serves as a great overview of the process in determining which streams can be reused and where. Water reuse applications include, but are not limited to - washing, rinsing, plating, spraying, coating, cooling, boiler water make-up, cooling tower make-up and fire suppression systems.
It is recommended to start with highvolume reuse applications that have lower water quality requirements, therefore requiring less treatment. By following this approach, the facility will achieve the greatest return on investment, as higher levels of treatment increase cost. In many instances, it’s more straightforward to capture and recycle wastewater at the source (i.e., directly after a manufacturing process and before it reaches an effluent treatment system).
“What level of water quality must be achieved?” or “How to close the gap?”
Finally, determine the treatment levels required for the selected applications by measuring current wastewater quality to establish a baseline and then compare that to the quality level required for the selected applications. This gap in water quality will determine the treatment intensity.
Most industrial processes utilise water as a component of the final product, part of the production process, or even indirectly, through energy use. Substantial volumes of water are consumed by industry.
ABOVE: Visual representation of OECD Environmental Outlook to 2050 (from 2000 baseline).
In theory, it’s possible to recover most wastewater. However, some will require more complex process equipment than others, and in a lot of circumstances, a pilot project and trial will determine the best solution.
The most challenging water treatment problems can be addressed and solved by skilled, experienced engineers with access to the innovative processes and technologies needed to build water reuse systems tailored to meet specific objectives, complying with each application’s required specifications. Partnering with an experienced provider like Envirogen to consult on the process can help
manufacturers position themselves as leaders in the industry, bringing a positive brand image and growth to those companies that embrace the challenges ahead. Being an environmentally conscious company goes hand-in-hand with profitability.
With corporate and social responsibility, good governance, consumer pressure and related financial performance in mind, I suggest manufacturers lagging in these areas might want to turn their attention, or more of their attention, to these opportunities. Industry has a key role to play in reducing problems associated with chronic water shortages; some caused at least in part by players in the sector.
To reflect the headline of this article - water recycling and reuse can help industry meet water usage goals and much more, all through building a water-resilient business model appropriate to each sector.
Website: envirogengroup.com
*OECD Environmental Outlook to 2050: “The Consequences of Inaction - Key Facts and Figures”.
** Source: CDP Global Water Report 2020.
Reaching a sustainable, cost-effective solution is paramount, and companies will need sufficient data to make informed decisions.
- Joe Higgins
Pentagon delivers a full turnkey solution for plastic injection moulding from one site of UK Manufacture.
With over 50 years’ experience you can be confident that your Bespoke Moulding project is in the hands of the experts for both mould tooling and repeat production.
Meet us at this years’ Interplas UK –26- 28 September at the NEC, Birmingham.
www.pentagonplastics.co.uk |
websales@pentagonplastics.co.uk
Tel: +44 (0) 1403 264 397 |
Totalkare’s ergonomic positioners are single or double column devices that enable the lifting and rotation of a product during welding and assembly operations.
With overall capacity from 2,000 - 90,000kg to suit, they are both compact and flexible.
The UK’s biggest independent STEM event crowned four major winners last week in a competition that attracted more than 80 pupils keen to get an insight into engineering.
Bishop Vesey’s Grammar School, Great Wyrley Academy, John Taylor High School, and Lawrence Sheriff High School took the prizes at the Design & Make Challenge 2023, the largest one ever held by the Manufacturing Assembly Network (MAN).
The Year 10, Year 11 and Year 12 students split up into teams of four to design, test and build an aircraft.
Using just a box of simple materials and a selection of hand tools, they had to work together to create a machine that could be launched from a pair of purposebuilt air cannons.
Held with WMG at the University of Warwick, the challenge pitted sixteen schools against each other to see whose design could go the furthest, with Great Wyrley Academy’s model surpassing
Students from Fallibroome Academy in Cheshire, have won the Institution of Engineering and Technology’s (IET) national IET Faraday® engineering challenge, securing £1,000 for their school.
the organisers’ expectations by travelling 16 metres to the wall at the end of the test area, earning them the ‘efficiency’ title.
John Taylor and Lawrence Sheriff won the ‘manufacturing’ and ‘innovation’ titles for ease of manufacture and the uniqueness of their designs respectively, with Bishop Vesey’s securing the ‘communications’ prize for the way they told the story of the day.
The latter was a real coup after the ambitious pupils managed to secure a mock TV interview with Sky Business Correspondent Paul Kelso as part of their winning entry.
Great Wyrley, John Taylor and Lawrence Sheriff each received a 3D Printer as part of their prize package, which was sponsored by 3DPrint UK. These will be taken back to each of the schools and used to develop additive manufacturing skills.
More details on MAN can be found at www.man-group. co.uk or follow MAN Group on LinkedIn.
The top five school teams from the season league table attended the IET Faraday® National Final on Thursday 29 June 2023 at the Digital Aviation Research and Technology Centre (DARTeC) at Cranfield University. The teams were Sandringham School from Hertfordshire, Fallibroome Academy from Cheshire, Thomas Alleyne Academy from Hertfordshire, The Gilberd School from Essex and The Corbet School from Shropshire.
This year’s challenge was in association with UKRI’s Future Flight Challenge and tasked teams to design a prototype that could support UKRI’s Future Flight Challenge with regards to accessibility and ease of use, safety and impact on the environment.
The winning team designed a prototype receiver box with pressure pad for drone deliveries at hospitals. On winning, the team said: “This has been an amazing day. We’ve done so much, and we got to fly a drone!”
A total of 176 events took place across the UK to host the 2022-2023 IET Faraday® Challenge Days. Up to six teams of local school students competed at each event to find the best solution to the engineeringrelated challenge. The final was judged by Michelle Richmond, Director of Membership and Professional Development at the IET, Ama Frimpong, IET Young Woman Engineer of the Year 2022, Vicki Murdie, Innovation Lead at UKRI’s Future Flight Challenge, Amy Camp, Innovation Lead at UKRI’s Future Flight Challenge, and Adrian Cole, Programme Manager at DARTeC.
The events aim to encourage more young people to study and consider exciting and rewarding careers in science, technology, engineering and maths (STEM) by using creativity, innovation and problem-solving skills.
The IET Faraday® Challenge Days are part of a wider Education programme, made up of a whole host of teaching resources and activities to inspire and attract the engineers of tomorrow.
For more information on the IET and its initiatives to promote STEM subjects and careers in the classroom, visit the IET’s dedicated Education website
The ideal solution for cooling production and warehouse facilities, energy efficient evaporative cooling can be used to blanket cool large spaces or spot cool problem areas or mezzanine floors. Air supply temperatures off the coolers do not exceed 25C, without the need to utilise any refrigerant technology.
Utilised in 100s of facilities across the UK, EcoCooling are the go-to provider for evaporative cooling for industrial applications. Our installation network provides free site visits and quotes for supply and install of equipment. All spares and coolers are held in our Suffolk warehouse, ensuring rapid delivery and maintenance options.
Your all-in-one solution
Benefit from the comprehensive DC 24 V circuit protection solution for mechanical and plant engineering. The REX system combines power supply, communication, circuit protection and power distribution in one system.
Website: www.ecocooling.co.uk
Email: sales@ecocooling.co.uk
Phone +44 (0)1284 810586
BFPA FOUNDATION LEVEL –HYDRAULICS
The aim of the Foundation Level in Hydraulics is to provide candidates with the understanding of where Fluid Power –Hydraulics is used in modern society and its importance in the provision of power and motion control
Examples of topics covered include:
Fundamental principles of all hydraulic systems
Hydraulic symbols, pumps, fluid oil reservoirs, actuators
Pressure, flow and direction control, contamination control, hose technology maintenance procedures
E-T-A Circuit Breakers Ltd. +44 (0) 1296 420336 info@e-t-a.co.uk www.e-t-a.co.uk
YOUR BENEFITS:
• Increased machines availability: Clear error detection, high transparency and remote diagnosis
• Flexibility: Easy assembly, modularity and convenient adjustment
• Time saving: Innovative and flexible connection technology
• Cost efficiency: No further accessories necessary
The BFPA have for many years been passionate about raising standards within the fluid power market and industr y as a whole, beginning with our Foundation Level programme
BFPA FOUNDATION LEVEL –PNEUMATICS
It is acknowledged that in today’s world it is rare for pneumatics to be applied as a single technology and invariably electrical /electronic controls are included as well We therefore recommend that a basic introduction to electronics is considered alongside this foundation level pneumatics programme
Examples of topics covered include:
Basic fundamental principles for pneumatic systems
Pneumatic symbols, compressors, airline components, actuators, tube & pipework
Pressure, flow and direction control
Electrical principles, techniques and symbol
Maintenance procedures
For more infor mation about any of our cour ses or to check availabilit y please visit: www.bfpa.co.uk/training
Please call 01608 647900 or email enquiries@bfpa.co.uk
BFPA FOUNDATION LEVEL –ELECTRONIC
Engineers need to be equipped with at least the basics of electronic and control technology in order to embrace their ever-increasing role as part of Integrated Fluid Power Systems
Examples of topics covered include:
Basic principles equating to fluid power analogies where possible
Electronic components and their applications
An introduction to control systems
Power supply methods
Magnetism and electro-magnetism
Electrical symbols, test and measurement motors and motor control
Cables and termination methods
Maintenance procedures
Proactive Energy Saving Technology
Gas Fired or Full Electric Option
Automatically modulating airflow with 100% in Performance mode & 50% in Economy mode.
“HighLight” high performance LED lighting system
Hi-visibility Mode indicator countdown timer
‘ProActive’ Touchscreen control
Stop/Start energy saving technology
Energy consumption as low as 1KW*
Energy Savings Of Up To 65%*
AquaDry blowers
Invertor control
Rear Extract, Pit extraction or Raised Floor airflow options
Conveyorised line options
Space Saving Design
Energy cost per job recording
Robotised paint application options
Turnkey installation available
A young apprentice that is helping motorsport teams achieve their best possible performance has been named as the Outstanding Apprentice of the Year for the West Midlands.
Precision Technologies International’s Joshua Peace beat off the challenge of more than 100 peers to secure the prestigious honour in front of 300 people at the In-Comm Training Awards in Birmingham on Friday. Judges praised the Tamworth engineer’s all-round stunning performance and a clear desire and drive to inspire others to follow a career in industry.
The high-profile ceremony, which was backed by main sponsor the Engineering Technology Group (ETG), saw ‘girl power’ come to the fore again, with Katie Mayo (PcP Gratings) and Kirsty Locking (Cross & Morse) sharing the Most Improved Learner of the Year title.
In addition to the young apprentices, companies were also in the spotlight for the way they back the next generation of talent and how they continue to invest in their workforces.
Assa Abloy and Brandauer won the Large Company and SME Awards respectively, with the latter impressing the judging panel with the way it has jointly invested £1m into a new Precision Tooling Academy to reverse the toolmaking skills drain.
This was the twelfth year the In-Comm Training Awards have been held and gave over 55 finalists the opportunity to celebrate their achievements in front of their peers, mentors, and employers.
Following a successful first decade, the popular Tomorrow’s Engineers Week will return this November – taking place from 6 to 10 November 2023.
Now entering its 11th year, the annual celebration is an opportunity to inspire young people with modern engineering and technology and showcase the benefits of a career in this sector.
Tomorrow’s Engineers Week sees schools, employers, professional engineering institutions and individuals working in engineering and technology come together to bring engineering careers to life for young people.
Over the past 10 years, Tomorrow’s Engineers Week has seen hundreds of thousands of young people take part in interactive activities showcasing engineering careers. This includes almost half a million views of inspiring films about engineers on a mission to make the world a better place, hundreds of millions of social media content views and widespread media coverage.
Full details regarding Tomorrow’s Engineers Week 2023 will be released in the autumn.
To find out more and stay up to date visit www.teweek.org.uk or for any further queries email hello@teweek.org.uk
For more information call 0121 601 6691 scan code for the training guide or email: training@bpma.org.uk
Gas and liquid diaphragm pumps have been essential in diverse industries for many years. Their reliability, robustness and versatility make them ideal for use in a wide range of applications, including medical, inkjet, analytical instruments as well as food and beverage. However, despite their widespread use, diaphragm pumps are not without their limitations and challenges. By exploring these advantages and disadvantages in detail, we can examine the pros and cons of this type of pump, to enable you to make an informed decision when selecting the right pump.
As a type of positive displacement pump, diaphragm pumps use a flexible diaphragm, usually made from elastomers or thermoplastic, to move fluids or gases through a system. The diaphragm also acts as a seal between the media being pumped and the drive of the pump as well as the environment, making them ideal for handling abrasive, corrosive, or viscous liquids that would damage other types of pumps.
Diaphragm pumps are a popular pump type that offer several advantages over other pumps, including gastight operation, low maintenance requirements, and the ability to handle abrasive or viscous fluids. We will explore some key advantages of diaphragm pumps in more detail, discussing their benefits for specific applications and industries.
• High gas-tightness: Using a diaphragm provides a high level of gas-tight operation. To reduce the risk of leakage further, diaphragm pumps can be equipped with a back-up diaphragm. If the primary diaphragm becomes damaged, the additional diaphragm’s closed surface safeguards against
potentially hazardous gas leaks.
• Low maintenance construction: Diaphragm pumps are designed for long-lasting durability and therefore have a low maintenance requirement. They have the potential to be maintenance-free and contain few moving parts, reducing the risk of wear and tear.
• Oil-free operation: As all pump parts in contact with the media are strictly separated from the drive, oil cannot pollute the media. This makes diaphragm pumps ideal for all applications that require the utmost cleanliness.
• Customizable: KNF diaphragm pumps rely on a modular design. This allows for fast and economic customization of the pump while relying on tested and proven parts. This way, customers can receive a pump solution that truly and precisely fits their project requirements. KNF is able to offer customization from batch size one.
• Chemical resistance: Only very few parts of the diaphragm pump come in contact with the media, and all of them can be chosen from a wide range of different materials to ensure compatibility.
• Compact design: Their robust, compact design makes diaphragm pumps ideal for use in tight spaces or where floor space is limited. They are also lightweight, portable and can be mounted in any direction, providing additional flexibility.
• Dry-run safe: Diaphragm pumps used to transfer liquids are dry-run safe and can continue operating for long periods without damaging any components.
• Self-priming functions: The pump’s design allows it to generate pressure and self-prime without any start-up procedure or manual priming.
• Advanced motor types: Diaphragm pumps can be equipped with advanced brushless DC (BLDC) motors for greater controllability. They can also be digitally customized for specific application requirements.
While diaphragm pumps offer many advantages, they also have some disadvantages that should be known when considering their use. We will examine these disadvantages, discussing their limitations and potential challenges in different industrial applications. This should enable an informed decision about whether a diaphragm pump is the right choice for a specific application.
• Flow rate restriction: Diaphragm pumps are generally better suited for low to medium flow rates and may not be the best choice for high-volume pumping applications
Diaphragm pumps have advantages and disadvantages that must be considered when selecting the right pump technology for an application.
such as operating international gas pipelines or public drinking water networks.
• Lacking in high pressure: While diaphragm pumps can generate moderate pressure, they are not designed for high-pressure applications such as liquifying gasses or waterjet cutting.
• Pulsation: As all positive displacement pumps, diaphragm pumps generate pulsation.
Excessive pulsation can cause vibrations, noise and might lead to system damage. To counter this challenge, KNF has developed the KNF Smooth Flow Technology, which minimizes pulsation of liquid pumps. Also, gas pumps can be designed with multiple pump heads and pulsation dampeners can be used for both gases and liquids to minimize pulsation.
• No high-viscosity liquids: While excellent at pumping gases and most liquids, diaphragm pumps will struggle to pump fluids that are very highly viscous or particulate-laden. This can be sewage sludge, honey or resins. In these cases, specialist viscous fluid pumps will be more suited to deliver the required flow rate and efficiency.
• Extreme temperature handling: By relying on the flexibility of their diaphragms to generate a pumping action, extreme temperatures can cause the diaphragms to become brittle, crack or deform. KNF diaphragm pumps are suitable for media temperatures of up to 240° Celsius, but alternative pump types should be considered if higher media temperatures are required.
Diaphragm pumps can be an effective and reliable choice for many applications. However, it is essential to evaluate the specific requirements of a given application to determine whether a diaphragm pump is the best choice or whether a different type of pump may be more suitable.
As manufacturers of high-quality diaphragm pumps for OEM use, process applications and lab, our technical experts have in-depth knowledge and experience to help our customers understand them better. If you have questions regarding gas or liquid diaphragm pumps or finding a pump that will suit your application requirements, contact our KNF experts to get detailed answers based on your specifications.
Website: knf.com/en/uk
As a type of positive displacement pump, diaphragm pumps use a flexible diaphragm, usually made from elastomers or thermoplastic, to move fluids or gases through a system.
The upgrade of chemical dosing equipment at a wastewater treatment plant in Germany is delivering high performance sludge dewatering through more reliable polymer dosing.
Safe and reliable chemical dosing helps wastewater treatment plant (WwTP) operators meet the required environmental standards at the facilities they manage every day of the year.
A WwTP in Heide, a small town in Schleswig-Holstein, Germany, has upgraded the polymer dosing pumps in its sludge conditioning process with specialist peristaltic pumps to reduce the maintenance interventions and polymer leaks it experienced previously with screw pumps.
In Germany, strict regulations for harmful chemicals, pharmaceutical residues, and microplastics mean the opportunities for reusing wastewater sludge as agricultural fertiliser are increasingly limited and sending it to a landfill is usually not permitted. This means thermal recycling is becoming more accepted as an effective route to sludge disposal, but the required dewatering and polymer dosing during the sludge conditioning process can add significant costs.
Identifying cost-efficiencies in the dewatering process can mean significant savings for wastewater treatment plant operations and a significant reduction in the amount of sludge produced. In the case of Heide WwTP, deploying a Qdos chemical metering pump from WatsonMarlow Fluid Technology Solutions (WMFTS) to replace a screw pump has made a big difference.
The WwTP installed a Qdos 60 PU peristaltic pump, which is specially designed to dose hard-to-process polymers, and other hydrocarbons, with high accuracy.
In most cases, polymers are used as a flocculant in the sludge dewatering process, binding together micro or nano sized particulates to form larger ‘flakes’. This improves the effectiveness of the solid-liquid separation system later in the sludge conditioning process. Selecting the correct polymer and ensuring it is used efficiently achieves the best possible sludge dewatering outcomes.
Qdos 60 PU peristaltic pumps easily achieve this high standard of polymer dosing and are crucial to this process. The low-maintenance pumps are easy, safe, and quick to service, offering substantial benefits in terms of timesaving and onsite health and safety, producing a streamlined and reliable process.
Sludge conditioning happens daily at Heide WwTP, which has the capacity to serve a population of 40,000.
“We’ve modernised our sludge conditioning process considerably in recent years,” said Peter Dohrn, wastewater treatment & technical department manager at Abwasserzweckverband Region Heide (AZV Heide).
“The sludge is thickened by adding an oil-based polymer flocculating agent and then fed through a screw press, which removes the water. This thickened sludge is then transported into the digestion tank, where it stays for up to 25 days before being dewatered again. After this, it is transported to the storage site before being collected for use in agriculture.”
Sludge is processed at a rate of 7m3/ hour, and conditioning reduces the volume by 80%, increasing the dry residue from 0.71% at the beginning of the process to 4.83% at the end. Each polymer dose takes around five minutes and occurs six times a day.
The process needs a pump which can deliver this repeatability and is robust against the polymer’s viscosity and resistance to pumping. Therefore, dosing pump reliability is critical to ensuring the sludge is thickened in a cost-effective and time efficient way.
We’ve modernised our sludge conditioning process considerably in recent years.BELOW: The new Qdos 60 PU has a pumphead with a polyurethane tube. The dosing process is regulated by an external control system.
Previously, progressive cavity pumps were used to dose polymers at Heide WwTP, but they were difficult to operate and required frequent servicing. Since progressive cavity pumps cannot run dry, suction from the intermediate bulk container (IBC) had to take place via the outlet fitting on the bottom of the IBC. This made changing the IBC timeconsuming and often caused minor leaks. The most serious problem though was the lack of leak detection during operation.
This meant that if a tube failed, the entire polymer contents in the container could leak out leading to a loss of expensive polymer and additional maintenance as “a slippery mess on the floor would require intensive cleaning,” said Dohrn.
Additionally, the amount of time and effort involved in servicing the screw pumps, due to the different parts coming into contact with the polymer, was a growing problem.
“Every servicing run involved several hours of work [with the screw pumps],” Dohrn explained. “Also, the extremely heavy progressive cavity pump was hard to move around, and its working principle meant it couldn’t achieve the dosing accuracy of other pumps due to its design.”
The Qdos 60 PU peristaltic pump provided an effective solution, with no need for diaphragms, valves, or seals that could be clogged by the polymer.
Operators at Heide wastewater treatment plant are also impressed with the durability of the new Qdos 60 PU.
It also has a highly innovative design principle as the only part on the pump that ever requires replacement is the patented ReNu 60 PU pumphead. It is simply removed as a single unit and a new one clicked into place. As the pumphead is fully sealed, there is no risk of the polymer leaking or the operator coming into contact with chemicals during replacement.
Leak detection
The pumphead has an integrated leak detector which automatically stops the pump and displays an error message if the tube ruptures. This also eliminates the risk of contamination caused by leaking polymer.
“In comparison to our previous pump, the Qdos has a much higher level of safe chemical handling and operational safety,” said Dohrn.
The intermittent dosing process is regulated from an external control system and has an accuracy of ±1 per cent.
“Thanks to its highly effective suction capability, the self-priming Qdos pump can extract polymer from the IBC from above by means of a suction tube,” reported Dohrn.
“The pump handles the suction height of just under a metre with ease. The pump can also empty the polymer almost completely, reducing the risk of leakage during changeover.”
“The first pumphead ran smoothly for a year before we had to replace it, purely as a preventive measure, and the second one has been working without any trouble,” said Dohrn.
“The Qdos 60 PU pumphead has been specially developed to dispense the hard-to-handle polymers involved in sludge dewatering and has recently been added to the Qdos series,” explained Adeel Hassan, product manager at the Watson-Marlow Fluid Technology Solutions.
“As the model has a pump tube made of polyurethane, it is ideally suited to dosing liquid acrylamide-based polymers or aliphatic crude-oil-based hydrocarbons.
“These versatile pumps can be used for dosing liquids at up to 120 l/hr and up to 7 bars in various applications, across a range of sectors.
“They are available in different sizes and control options, depending on requirements.”
SIGMA Group, one of Europe’s leading industrial pump manufacturers, has specified Thordon Bearings’ grease-free bearings for installation to the specialized pumping sets destined for flood defence and irrigation projects across Egypt.
In total, Thordon is supplying 64 of its water-lubricated Composite bearings for use in 49 SIGMA BQBV vertical diagonal pumps specified for projects along the Nile River and the Sinai Peninsula.
SIGMA has already delivered nine 800-BQBV pumps for projects in North Sinai, while twelve 1400-BQBV pumps are scheduled for installation at the El-Hammam agricultural wastewater treatment facility later this month. Twenty-eight 1500-BQBV pumps are also being built for the mammoth Mostakbal Misr project (a project for agricultural production in the Western Desert) with deliveries taking place from June 2023 through to April 2024.
“Pumps installed on the river Nile operate in very abrasive water. As a result of these harsh operating conditions, the bronze bearings these pumps are typically fitted with last only 1 to 2 years.
“SIGMA wanted a much more robust, abrasion-resistant solution,” said Josef Hozák, Managing Director, Eribos, Thordon’s authorized distributor in Czech Republic (Czechia).
“The new contract follows the success of bearing installations to SIGMA pumps dating back fifteen years,” said Malcolm Barratt, Thordon Bearings’ Regional Manager –Southern Europe & Middle East.
“Based on the large amount of sand in the pumped liquid and the success of Thordon’s bearings in muddy and abrasive environments, as well as the strong relationship Thordon’s distributor Eribos has with SIGMA, the pump manufacturer chose Thordon’s Composite material for its pumps.”
With a much lower friction coefficient than rubber, Thordon’s Composite bearing material has been specially developed for use in very abrasive aquatic environments. It is also much easier to install and maintain than any alternative bearing solution in the market.
“It is by far the best bearing solution for pumps operating in harsh environments,” Barratt said.
“Based on current wear rates, a 10-year wear life is projected before a replacement is required. By using Composite in its pumps, SIGMA customers benefit greatly from reduced maintenance and plant downtime, resulting in significant savings to operational expenditure.”
SIGMA is currently working on its second major pump project in Egypt – the El Hamam project. All twelve SIGMA 1400-BQBV vertical pumps, each of which is fitted with two Thordon Composite bearings, will pump 6 million m2 (64.5 million ft2) of agricultural water from the north of the Nile to irrigate a 2100km2 (810.8mi2) area 120km (74.6mi) to the west, in the Western Desert.
The company is also starting work on the Mostakbal Misr project, which will see 28 SIGMA 1500-BQBV vertical pumps used to irrigate 500,000 acres around Egypt’s northwestern coast region.
SIGMA’s early adoption of Thordon’s bearings in the Egyptian pump market has led to widespread adoption in industrial and hydro pumps across the region and beyond.
“The bearing supply agreements we have recently signed with major pump manufacturers in Europe and Asia are a direct result of the robust performance of Thordon’s water-lubricated bearings in pumps operating across Egypt,” said Barratt.
For further information visit: www.thordonbearings.com
Saving energy and space at the same time, that doesn’t have to be a contradiction. Quite the opposite. At ALMiG, we have been proving for many years that the concept of a vertical arrangement of motor and compressor unit is the key to success - to efficiency. Energysaving speed control through an oil-cooled permanent magnet motor, a highly efficient compressor stage combined with the most intelligent control technology and the lowest noise level are our answer to the increasingly demanding requirements of the future.
o Extremely energy-efficient due to direct drive and speed control
o Smallest footprint due to vertical arrangement of the motor-compressor unit
o Easy accessibility and maintenance
o Motor efficiency corresponds to IE4 or better
o Heat recovery optionally available incl. utilisation of waste heat from the motor!
o Air Control P as standard compressor control
The Air Power Group consists of Air Power Products, (Compressed Air Specialist) Procut Engineering (CNC Precision Engineering) and APP Site Services (Site Supplies and Tool Hire).
The group benefits from a full-service department with a wealth of compressed air and hydraulic tool knowledge. We provide an excellent service, not only with the range of products but with the level of care each order is given and the speed with which we can deliver.
We have a range of construction tools available for sale and hire which include Rebar Cutters, Rebar Benders, Hydraulic Splitters and Pneumatic Picks.
With offsite construction and the prefabricated building systems market booming, a new ‘Prefabricated Solutions’ service from Elta Fans is now available for a wide range of its fans. The solution is set to help cut installation costs and speed up building projects with greater efficiency and compliance while enhancing site safety.
Elta Fans’ Prefabricated Solutions service is ideal for specifiers and contractors working on commercial building projects of any scale.
Fans and ancillaries, such as acoustic equipment, mounts, panels, flexible connections, fan controls and more, can all be assembled offsite and delivered as a compliant assembly. These are then ready for crane lifting, resulting in quick, efficient installation. The ventilation and air movement manufacturer is one of the first in its sector to offer this kind of solution across multiple fan types and ranges.
Main base of operation is near Sheffield with a sales team based in Kent servicing the South of England and London. Specialists in compressed air since 1989, call us today on 01909 519 519 or visit AirPowerGroup.co.uk to find out more.
L O W C O S T
The Belaria® fit heat pump can be used as a standalone unit, in cascades or in hybrid systems. Attractive price/ performance ratios can be achieved in hybrid configuration alongside a gas condensing boiler such as the UltraGas® 2.
from 53-1357 kW
Wanner International will announce at CHEMUK that Laxmi Organic Industries, a market leader in the manufacturing of speciality chemicals, has successfully completed a development trial with three Wanner Hydra-Cell flow chemistry pumps to manufacture intermediaries for a number of active pharmaceutical ingredients (API).
The pilot plant will now be upscaled to full production at the company’s Mahad operation in India. Delivering an extremely low pulse flow, the HydraCell pumps will be dosing solvents at a rate of 80-100 litres per hour into the continuous flow reactors at a discharge pressure of 15 bar.
This is important in maximising the efficiency of the process, as it ensures that the concentrations of the various reactants are maintained at an optimum level for consistent manufacture.
The Hydra-Cells have a number of advantages, such as being leak-free, which is especially important when handling highly hazardous chemicals.
The Hydra-Cell pumps also benefit from an advanced mechanical and hydraulic design, with little ancillary equipment required, and high accuracy over a wide flow range.
Wanner’s commitment to research and development, and its strong protection of this IP, has enabled it to evolve its capability and make it ideal for this application. This has wider implications for the whole pharmaceutical industry.
As the pharmaceutical and biopharmaceutical industries move from batch to continuous production processing gathers momentum, the Hydra-Cell’s unique technology offers the industry a trusted mechanism for cost-efficiency, consistency and scalability.
The technology team of Laxmi Organic Industries believes,
“Manufacturing excellence runs through the DNA of Laxmi and we are constantly looking at ways to improve effectiveness of our production facilities.
“The Wanner pumps have been very successful in delivering what is needed – in a safe environment, day-in, day-out. As manufacturing chemicals for life sciences demands large scale operations, we are now moving this line into full production.”
Critical for Flow Chemistry and HPLC applications, the Hydra-Cell pumps exceed API 675 performance standards and boasts extremely low pulse flow. This eliminates the need for pulsation dampeners, eliminates pipe strain due to pulsation, delivering an accurate and smooth flow for flow chemistry dosing applications over a large adjustable range of flow rates.
Paul Davis, Wanner International’s Managing Director commented: “The production of modern drugs is a highly complex process, and we want to help customers with their challenges with a process pump that is safe, accurate and reliable in handling difficult and different liquids. We are all faced with changes driven from the need for sustainability and conserving the environment, which forces technology change in equipment design and different use of materials and processes.
“It is a fantastic achievement that Laxmi Organic Industries is improving these processes so quickly, and we are pleased that our pumps have been able to play their part in maximising production output and efficiency.”
Wanner designs and manufactures Hydra-Cell seal-less and packingfree, flow-chemistry, HPLC, transfer, injection, and dosing pumps, helping customers around the world improve their processes by running safe, reliable, and efficient pumping processes whilst lowering energy consumption, servicing and maintenance costs – lowering the total cost of ownership for a more sustainable future.
For more information, please visit Hydra-Cell.co.uk/ FlowChemistry or https://www.laxmi.com
The pilot plant will now be upscaled to full production at the company’s Mahad operation in India.
Gearing up to take the lead on business development in the South of England is PCL’s new Area Sales Manager Michelle Foord.
With a background in manufacturing, Michelle has a proven track record of building customer relationships within the railway and automotive industries.
Her appointment came just in time for her to join PCL’s expert team at Automechanika 2023, where she took the opportunity to meet as many industry contacts as possible.
Michelle has since spent a week familiarising herself with PCL’s marketleading portfolio and operations at its state-of-the-art production facility in Sheffield, where she got hands-on helping to build some couplings.
She said: “It’s been fantastic to spend time on the shop floor getting into the detail of the products; how they’re put together and the time, effort and skill involved in the process.
“The production facility is incredibly impressive and immensely clean – I
couldn’t believe it’s a working factory from how clean it actually is. The whole operation runs so smoothly - the picking, fulfilling of the shelves, the traffic light systems - all the departments work seamlessly together.”
The next step, Michelle said, is getting out on the road: “In the shortterm my focus is meeting my customers and understanding their business needs. My long-term focus is growth and identifying further potential in the South.
“I’m really looking forward to meeting existing customers and looking at where the gaps are to build new business and get a plan in place.”
Michelle also enthused about the customary warm welcome at PCL: “Everybody is delightful. You don’t realise how big the company is at first because it feels like a family. It’s not like the usual commercial company where you’re just a number. Here you’re made to feel like a person.”
PCL’s Managing Director Lee Wright said: “Michelle is an excellent communicator with a pro-active, customer-first approach.
“Her dedication to supporting individual business needs, combined with her expertise in identifying market opportunities, makes her the ideal candidate to strengthen operations in the South and facilitate growth for our customers as well as PCL.
“I’m really pleased to see Michelle settle so well into the fold. I am confident customers will feel in safe hands as she works with them to help their businesses flourish.”
Mitsui Seiki announces that Mr. Daniel Cleary has been chosen as the next President of Mitsui Seiki USA, Inc.
“It is my sincere privilege to be the new President of Mitsui Seiki USA,” said Mr. Cleary.
“I am incredibly proud to lead this organization and equally excited to have the opportunity to work with such a talented and enthusiastic group of people.”
Mr. Cleary’s passion for innovation, process improvement and superior customer service are a great complement to Mitsui Seiki’s forward thinking and inventive culture. He plans to focus his attention on the company’s investment in people, technology and infrastructure in order to position Mitsui Seiki as an industry leader and the preferred machine tool
supplier for many years to come.
“I was a customer of Mitsui Seiki first, so I know our talented team of engineers, technicians, sales professionals, and service staff are among the best in our industry. At that time, no one else could build a machine that could do what we needed,” said Mr. Cleary. “As the requirements for industry 4.0 and 5.0 continue to evolve, our customers will need to continue to find new and creative ways to improve quality and sustainability while making capacity, cost and production optimization a priority. Mitsui Seiki will be there to help.”
Mr. Cleary comes to Mitsui Seiki from The Bromford Group (Hartford, CT) where he served as the Vice President of Group Strategy.
Website: www.mitsuiseiki.com
I’m really looking forward to meeting existing customers and looking at where the gaps are to build new business and get a plan in place.
Oxford Flow, the flow control equipment specialist, is delighted to announce the appointment of Adam Eckersley as Chief Technology Officer, to help drive the company’s ambitions to lead the transition of the valve industry to innovative technology and reduced emissions.
Adam joins Oxford Flow from Severn where he was Director of Engineering. He brings two decades of experience in the oil and gas, power, and process industries, and has significant experience in valve product development.
Tasked with producing a market leading engineering and innovation programme for Oxford Flow, one of Eckersley’s primary focuses will be zero emission solutions and hydrogen ready products, as the firm continues to lead the way in technology for the energy transition, such as its ES stemless actuated valve, and its IM series regulators.
Neil Poxon, CEO at Oxford Flow, comments: “We’re delighted to welcome Adam into the Oxford Flow team at such an important period of growth. He brings a strong engineering track record working across sectors such as oil and gas, power, LNG, gas storage, petrochemical and air separation. Having also worked in Europe, Middle East, North Africa, and South America, where we are seeing significant expansion, Adam will be vital to building on our existing innovative approach to developing solutions specifically designed to address customer needs and market challenges.”
As CTO, Eckersley’s role will also involve the review and development of the company’s technology strategy, to expand the offering of control valves and regulators amongst other flow control equipment.
Eckersley added: “Oxford Flow is going from strength to strength, especially with the success of its zero emission, low maintenance technology. The ES stemless actuated valves are game changing, and I feel they will transform not only the valve industry but the energy sector as a whole. I am very excited to be joining as innovation is a real driver for me and Oxford Flow is a world leader with its hydrogen-ready and emission abating products.”
More than two thirds of engineers within the UK’s manufacturing sector report that business has returned to or even surpassed pre-pandemic levels, in a report published by Essentra Components in early 2023. As manufacturers strive to meet production demands, more and more businesses are using automation technologies, driven by industrial control systems. Here, Richard Mount, Director of Sales at ASIC design and supply company Swindon Silicon Systems explains the crucial role of ASICs in improved industrial control systems.
An industrial control system is used to operate and automate industrial processes. The control system encompasses a variety of equipment and technologies, including the sensing element, data processing, communications, and actuation devices.
The control system works by first monitoring process variables, such as temperature, pressure, or position. This data is then processed, and decisions made dependent upon the result. The resultant is then used to determine what actions need to be taken.
-Traditionally, this cycle of monitoring and adjusting would often be done manually, with workers taking frequent readings of various monitors around the plant. But the adoption of industrial control systems allows these processes to become automated, operating in closed-feedback loops. By removing the need for manual monitoring, the risk of human error is reduced, and more readings can be taken within a given period.
One example of an industrial control system is that used for position sensing. Encoders are used to
determine exact positioning of moving objects. This can be done by either directly providing an absolute position value, or by using the direction and velocity of movement to derive position. For sensitive applications where precise positioning is paramount, optical encoders can be used to obtain positional information to an accuracy of up to one nanometre.
Both linear and rotary optical encoders may be used depending on the nature of the movement. In a linear encoder, the sensor or transducer is paired with a marked position scale. The sensor counts the lines on the scale to determine position and converts this into a digital signal.
Rotary encoders work in a similar way, but instead detect the angular or rotational movement of a shaft. An LED shines through an etched rotating disk onto a mask, creating patterns unique to each arc revolution. These unique light patterns illuminate the sensors beneath, which then use these unique patterns to determine rotational movement.
The sensing element within optical encoders is the photodetector or photodiode, which converts photons of light into an electrical signal. Before this information can be processed by the main logic controller, the analogue signal must first be amplified, conditioned, and converted into a digital signal. This digitisation, which can be performed by standard ICs, transforms the signal into something that can be understood by digital equipment. The conversion and conditioning processes are crucial in allowing data transmission and interpretation by the central control.
ICs also facilitate the communication between these individual devices, allowing for the creation of “joinedup” manufacturing systems. Each IC will often work alongside many other sensor interfaces and communication ports. To streamline the process, some processing may be done locally
Industrial specific protocols such as I/O–Link, either wired or wireless, are now widely used and BLE is also making an appearance.
Richard Mount
at the sensor before reporting the data back to the main console.
Data transmission is possible through both wired and wireless communication protocols, with the most common protocols being the Serial Peripheral Interface (SPI), and the Inter-Integrated Circuit (I2C). These two interfaces facilitate short-distance communication between peripheral devices and microcontrollers and are a key link in ensuring all devices and equipment are synchronized with one another. Industrial specific protocols such as I/O–Link, either wired or wireless, are now widely used and BLE is also making an appearance.
Off-the-shelf, standard ICs may be suitable for performing the necessary signal conversion, amplification, and communication required. But for manufacturers who are seeking a more sophisticated industrial control system, choosing a custom IC, or Application Specific IC (ASIC) can provide the technical and commercial competitive edge.
ASICs are designed with their specific application in mind, where optimised
performance and environmental objectives are achieved through a customised solution. This approach leads to a chip optimised for its use, whether it’s within a pressure sensor or facilitating accurate positioning in a drive system.
When it comes to industrial applications, this optimisation can make a huge difference when considered across the entire
manufacturing plant, by improving performance where it is required and maximising production.
This improved performance can also help improve and maintain product quality, as well as reduce the amount of waste product as a result of manufacturing imperfections.
The smaller footprint and reduced power consumption offered by ASICs also expands the number of possible applications and areas for ASIC-based technology, leading to more efficient processes overall.
And unlike standard ICs, ASICs come with non-obsolescence strategies. With industrial equipment expected to work for many years, it’s key to ensure availability of ICs. Standard ICs may not have guaranteed supply for the entirety of the control system’s lifetime, which can cause issues later down the line when performing maintenance or repair work.
At Swindon, ASICs are designed with non-obsolescence in mind. By considering product lifetime right from design, the ASIC designer can choose appropriate production methods, guaranteeing a supply for the lifetime of the product.
As manufacturers seek to produce more, and in less time, industrial control systems are key in making the most of automation technology and maximising process efficiency. By looking deeper into the industrial control system and optimising right from chip level, production and efficiency can be taken to new heights.
Interface Force was recently approached by an Aircraft manufacturer who wanted to ensure the correct torque and clamping force were being applied to fasteners during assembly.
An aeroplane manufacturer needs a solution where they can control the torque when fastening screws on their aeroplane models. They do not want to create any damage to materials or apply too much torque when plane components are being fastened together.
Interface’s Model T15 Hex Drive Rotary Torque Transducer can be attached to the fastening workbench, measuring and recording torque, rotational speed and angle of the screwdriver. The LWCF Clamping Force Load Cell is installed, measuring the forces applied on the screw being fastened.
Interface’s Model T15 Hex Drive Rotary Torque Transducer can be attached to the fastening workbench, measuring and recording torque, rotational speed and angle of the screwdriver.
Results are sent to the SI-USB4 4-channel USB Interface Module, which is connected to the customer’s PC or laptop where data is logged, graphed and displayed.
The aeroplane manufacturer was able to calibrate their screwdriver by measuring its torque, rotational speed, and angle when attaching components to their aeroplane. They were also able to measure the forces being applied to the screw, to ensure it was not applying too much torque to the components.
• T15 Hex Drive Rotary Torque Transducer
• LWCF Clamping Force Load Cell
• SI-USB4 4-channel USB Interface Module
• Customer PC or Laptop
1. The T15 Hex Drive Rotary Torque Transducer is attached to the screwdriver fastening bench.
2. The LWCF Clamping Force Load Cell is placed beneath the bolt head.
3. The T15 Hex Drive Rotary Torque Transducer measures the screwdriver’s torque, rotational speed and angle, for the customer to determine the right amount of torque needed to be applied to the screw to prevent any damage to the materials being fastened together.
4. The LWCF Clamping Force Load Cell measures the forces applied to the screw, so the customer can determine the maximum torque it can take.
5. The measurements and results are sent to the SI-USB4 4-Channel USB Interface Module, where the customer can record the results when connected to their PC or laptop.
For more information about the force and torque sensors mentioned in this application note or how Interface Force Measurements could help with your force, torque or pressure measurement challenges please email us at info@interface.uk.com or visit our website www.interfaceforce.co.uk
• Rugged and compact
• Easy to use
• Dust, splash or waterproof
• Data downloaded to PC
• Cost-effective
Accompanying probes are available for monitoring extremes of temperature, and for awkward to reach areas such as pipework.
For sites requiring remote data access, Tinytag Radio and LAN loggers gather data automatically for viewing on a PC, across a LAN, or remotely across the inter net.
outside the pipe, there is absolutely no risk of contamination or leakage.
Transducers are simply clamped to the pipe’s outer surface, meaning there is no contact with the medium flowing, and they are completely independent of the pressurisation levels within the pipe. The entrained particles do not affect measurement accuracy, and the system can be installed without any interruption to production.
Non-invasive flow measurement solution
by clogging the impulse lines for recording the differential pressure, causing measurement failure. Therefore, the process engineers needed a more accurate and reliable measurement solution.
Non-invasive ultrasonic flowmeter technology is helping plant operators to optimise processes, without the risk of leaks in highpressure piping systems.
Ethylene and propylene are plentiful gaseous feedstocks for the most common base polymers. Gases are highly compressed and heated during the polymerisation process - pressures can peak at around 3000 bar. This is where inline metering is prone to heavy wear and tear, often causing high pressure drops, which in turn leads to excessive operational cost and time consuming maintenance.
Using sound waves to measure the flow of media within the pipe, ultrasonic flowmeters work by alternately transmitting and receiving pulses of ultrasound waves between two transducers. This allows the flowmeter to accurately and reliably determine the flow rate. And because measurement is carried out safely from
At a high-pressure polymerisation and oxidation plant for the manufacture of specialty ethylenebased products, FLEXIM was tasked with flow measurement of ethylene gas, along with ethylene-copolymer gas mixtures under high pressure.
A steam cracker is located within the plant, and longer-chain hydrocarbons from the distillation of crude oil are thermally cracked in the presence of steam. This produces, among other things, ethylene and propylene. Polyethylene and ethylenevinyl acetate copolymers from ethylene (ethene, C2H4) are produced with precisely specified product properties for a wide variety of applications. The high pressures required of over 1500 bar are typical of the polymerisation processes in ethylene chemistry.
Orifice plates installed to measure quantities were subject to a great amount of wear and tear due to wax particles carried along in the gas flow, and they demanded a high level of maintenance. These wax deposits reduced measuring accuracy
A key advantage of non-invasive clamp-on flowmeters is that they can be thoroughly tested for suitability prior to permanent installation, without any process disruption. Following a successful demonstration measurement, the operator made the decision to replace the highmaintenance orifice plates with fixed FLEXIM ultrasonic flowmeters. Because the gas flow is routed through two lines of identical pipe geometry (DN32, wall thickness 23.5 mm) behind the intermediate-pressure compressor, the two-channel version of the transmitter was chosen, meaning flow could be measured on both lines simultaneously with a single flow instrument. Two lines on the pressure side of the high-pressure compressor have now also been identically instrumented.
Thanks to the extraordinary dynamics of clamp-on ultrasonic flow measurement technology, it’s now possible to record the start-up and shut-down phases of the ethylene cracker system. And as well as optimising process control, the flow measurements enable predictive maintenance capability through the delivery of crucial information on compressor performance - effectively reducing downtimes.
Clamp-on ultrasonic flow measurement of ethylene under high pressure
The new 0330 Optical Sensor from sensing and instrumentation specialist BAUMER is the latest addition to their ever-expanding photoelectric range of sensors combining smart design features with high performance reserve capacities. Reliable and
economical object detection has become a crucial requirement in today’s increasingly automated systems across a wide range of industry sectors, so the introduction of these sensors is well timed. Typical applications across a wide range of industry sectors include; intralogistics, electronics manufacturing, textile machines and packaging applications.
Whilst standard compact light barriers and photoelectric proximity sensors are widely available, the ultracompact 0330 sensor provides enhanced performance reserve capacity with features such as 3D MCAD data and integrated beam path, as a starting point. This additional data helps system designers and engineers to minimise time spent in selecting the right sensor and provides easy visual prechecks with the help of a 3D preview. Also, as the 3D models integrate the
beam path this helps to minimise the time spent on installation, thus saving time and money.
Thanks to qTarget (the smart Baumer standard), the beam paths in the 3D MCAD model comply with the application reality which ensures time savings from design stage to installations. This eliminates the need for further alignment, so the sensor is virtually ready for immediate use. The sensor is also available with a linear beam option although this also delivers outstanding performance, for example reliable detection of dark, irregular or perforated objects. In these situations, diffuse sensors with background suppression are characterised by their extended detection range of up to 385mm, with the linear beam incorporating Pin Point LED combined with extremely high immunity to ambient light, which Baumer claims is unrivalled in this price category.
Furthermore, other benefits include; a robust metal connector, LED display which is visible throughout 360º along with easy instructions via the proven Baumer qTeach feature. The sensor only requires a touch with a ferromagnetic object to ensure easy, reproducible and tamper-proof sensor teaching.
The VariMill range of end mills has been the standout performer in the industry for several years with WIDIA continually evolving the industry’s most dynamic range of end mills for high-performance machining. Now, the VariMill series has been improved once again with the arrival of the new VariMill Chip Splitter range that is available from Industrial Tooling Corporation (ITC).
Designed for dynamic milling, ramping, helical interpolating and side milling at high speeds and feed rates, the new VariMill Chip Splitter series from ITC delivers exceptional chip control that allows the tool to run with a longer axial depth of cut while productively diving into deep pockets in steel, stainless steel and
high-temperature alloys. Suitable for cutting materials ISO groups P, M, K, S and H, the new series is a genuine high-performance tool that delivers exceptional material removal rates.
Presented as a 5-flute solid carbide end mill that is available in WIDIA’s WP15PE and WS15PE carbide grades, the new VariMill Chip Splitter has features incorporated that improve chip evacuation by breaking the chips into the smallest possible segments. This simplifies swarf removal from the work area and it significantly improves cutting speeds and feeds when processing small pockets up to 5XD or when machining at full depth of cut.
The 5-flute end mills are available with a straight or Weldon shank in 3XD or 5XD variants. The straight shank 3XD end mills are available in 10, 12 and 16mm diameters with the Weldon shank designation also offering a 20mm diameter variant. The 3XD tools have a flute length from 32 to 60mm with an overall length of 80 to 125mm. Similarly, the 5XD plain shank variant is available from 10 to 20mm diameter with the Weldon shank also offering an 8mm diameter variant. The exceptionally robust geometry with a thick core and ultra-tough micro-grain carbide substrate as well as a 0.3mm corner radius – all combine to deliver astounding tool life and longevity.
With the Xtra·tec® XT M5137, Walter introduces a shoulder milling cutter that brings with it incredible benefits for machining ISO materials P and K. Firstly, users benefit from double-sided indexable inserts with six usable cutting edges. This provides an attractive price-to-cutting edge ratio. Secondly, the milling cutter has an approach angle of 90 degrees and is capable of ramping, circular interpolation milling and pocket milling.
This combination is something the market has not seen before now. Following on from the successful launch, Walter is now expanding its M5137 range to include the new G27 indexable insert geometry for universal use.
Whilst the G57 geometry that was previously available, primarily excelled in average to good
conditions with low cutting forces and average feeds such as premachined workpieces, the sintered G27 now completes the Walter range. The geometry can be used for challenging jobs as well as unstable clamping arrangements, interrupted cuts or forged skin.
Both geometries are suitable for face milling, shoulder milling and pocket milling, as well as circular interpolation and ramping in steel and cast iron workpieces, and in stainless and difficult-to-cut materials. The Walter range now includes the cutter body with bore adaption and Weldon shank. It is also available in new inch-diameters from 1 to 4”. The high process reliability and cost-efficiency achieved through low cutting tool material costs and the wear-resistant Tiger·tec® grades make the milling cutter a particularly good choice for users producing mid-range quantities.
Altus Group, a leading supplier of capital equipment for the electronics industry in the UK and Ireland, is excited to announce the latest addition to its portfolio, the innovative AQUBE® MV 3 One multitool developed by Kolb Cleaning Technology. The system is specifically designed to provide lower volume productions with multiple cleaning processes, providing a cost-effective alternative to purchasing several machines for each process in PCBA production.
This fully automatic system offers process-safe fine cleaning for screens, stencils, PumpPrints, and other flat products. Moreover, with an optional function package, it is also suitable for PCB assembly cleaning too. The AQUBE® MV 3 One quickly and thoroughly eliminates contaminants such as SMD paste, SMD adhesive, conductive materials, flux, oil, grease, or dust. Its efficient configuration with two tanks and two independent circuits, along with ClosedLoop water treatment, ensures short throughput times, making it the economically perfect choice for smaller quantities of different cleaning materials.
One of the standout features of the AQUBE® MV 3 One is its intelligent connectivity, which
allows seamless integration into Industry 4.0 environments. This feature enables networking for traceability, remote control, remote maintenance support, bidirectional machine-to-machine communication, machine-toproduct communication, and integration into comprehensive monitoring systems. With its retractable touch screen and integrated industrial PC, the system offers state-of-the-art connectivity for advanced operations.
The Kolb AQUBE® MV 3 One also offers a range of other key features that enhance its performance and versatility. Its two-tank system with two separate circuits ensures efficient cleaning processes, while the fully automated 4 Step process (cleaning, MediumWipe®, rinsing, and CWA® high-performance compressor drying) guarantees optimal results. The system’s vertical rotor system, equipped with ASYNCHRO® spray rotors, ensures thorough wetting without any blind spots. Additionally, the integrated condensate recovery in the process chamber further enhances efficiency.
Designed for optimal productivity, the AQUBE® MV 3 One boasts short cycle times offering the flexibility to use a cleaning/rinsing medium instead of water allowing for water-free operations. It also incorporates an EDGELESS design and VARIccess® maintenance access, providing the highest capacity and easiest maintenance on the smallest footprint. Its robust construction enables it to withstand high temperature cleaning up to 80 °C, expanding its applications to a wider range of industries.
For more information about the Kolb AQUBE® MV 3 One and Altus Group’s comprehensive range of capital equipment for the electronics industry, please visit www.altusgroup.co.uk
Following on from the successful launch, Walter is now expanding its M5137 range to include the new G27 indexable insert geometry for universal use.
Solar PV Panels now at ESSE Engineering, Barnoldswick.
ESSE Engineering is pleased to announce the completion of the installation of Solar PV modules at the ESSE factory and showroom situated at Ouzledale, Long Ing, Barnoldswick. The installation of twelve hundred panels can produce 250 kW of electricity adding up to over 2 million kW within its lifetime.
A short video displaying the install can be viewed on the ESSE Cookers and Stoves YouTube channel. (https://www.youtube.com/ watch?v=QneOjCcNQLU) Meeting MEES requirements, introduced by the government to improve energy efficiency and meet the UKs targets for decarbonisation, the solar PV system will allow ESSE to reduce its carbon footprint by producing clean energy and become less reliant on fossil fuel supply.
The solar panel installation will be used in the production of ESSE’s electric range cookers and
wood burning stoves which are sold globally.
ESSEs reputation for producing high-quality, energy-efficient stoves and range cookers comes with a responsibility to keep up with the rapidly changing world. A devotion to being as good as can be, means developing some of the cleanest, most efficient and innovative heating and cooking appliances available today.
The approach to sustainable manufacturing is also evidenced by the use of the latest machinery to improve both manufacturing efficiency and the integrity and finish of the product.
“We’ve been growing significantly since the pandemic,” states production director, Peter Ashby. “This prompted investment in additional machinery powered by a sustainable energy solution. It will help to provide more capacity and is key to ensuring that production processes remain efficient without compromising on quality.”
Draw-wire displacement sensors from Micro-Epsilon are used successfully in many different industries, one of the most important being mobile machinery, where the sensors need to be compact, provide large measuring ranges (typically 6 m to 8 m) and offer an attractive price/performance ratio.
A common application for drawwire sensors in mobile machinery is the measurement of boom and support positions. Telescopic loaders, for example, often require a measuring range of 8 m. In addition to analogue outputs, the demand for digital interfaces is also increasing, particularly for CANopen.
To better serve these applications, Micro-Epsilon has expanded its wireSENSOR WPS-MK88 and
Wanner has published findings of research showing that a Hydra-Cell seal-less, multi-diaphragm pump reduced the shear degradation in a polymer solution by over 90% compared to a plunger pump. The independent testing was conducted by a professor specialising in enhanced oil-
wireSENSOR WPS-K100 series of drawwire sensors with larger measuring ranges and CANopen interface.
The wireSENSOR K100 series of draw-wire displacement sensors measure distance and position precisely, combining high performance for outdoor use with an excellent price/performance ratio. The series now offers a larger measuring range of up to 8 m, as well as a CANopen interface for all measuring ranges up to 8 m, making the sensors ideal for off-highway vehicles, mobile machinery, mobile cranes and lifting technology. The compact K100 series is protected by a glass fibre-reinforced plastic housing, as well as separate drum and spring spaces, making the sensors extremely robust (IP69K) against external influences.
The MK88 series of draw-wire sensors has also been expanded with a larger measuring range of up to 6 m, as well as a CANopen interface for all measuring ranges up to 6 m. The MK88 is specially designed for mobile applications in series such as mobile cranes and mobile working platforms. The combination
of compact size, robustness and price makes the sensors unique, offering new potential in design and cost optimisation.
Ever-expanding portfolio
Draw-wire displacement sensors from Micro-Epsilon are extremely robust and flexible. They measure positions and distances between 50 mm and 50 m. Robust housings protect against external influences. Due to their compact design, the sensors can also be integrated in narrow installation spaces. Measurements are performed in a simple way, quickly and with a long sensor service life. Output of measurement
values is either analogue or digital, depending on the sensor model. For customer applications, various adaptations can also be implemented at any time. For example, the measuring wire can be guided over deflection pulleys to achieve an ideal measuring situation. Micro-Epsilon’s portfolio of draw-wire displacement sensors includes more than 120 models in different designs and measuring ranges.
For more information on draw-wire displacement sensors, please call the Micro-Epsilon sales department on +44 (0)151 355 6070 or email info@micro-epsilon.co.uk
recovery and transport in porous media at the University of Wyoming. The testing investigated how to minimise shear effects during polymer flooding.
Surface facility pumps often cause large amounts of shear degradation in polymer slugs, which can lead to dramatic reduction in production.
Overall, the Wanner Hydra-Cell T100K API 674 pump demonstrated a marked reduction in polymer solution viscosity degradation, achieved by its low shear pumping action; significant savings can therefore be realised through lower polymer utilisation and higher cumulative EOR production.
Many of Wanner’s pumps have been reliably operating in the field for a quarter of a century plus; with the Hydra-Cell low-shear pump technology, these operators have extended their financial recovery of wells on polymer injection and seen an increased rate of return.
The Hydra-Cell true positive displacement pumping action and minimal internal losses achieve high efficiencies from pump shaft to hydraulic power; this, combined with the wide range of flow rate controllability, ensures optimum energy usage, freeing resources that can be invested into further improving efficiency and sustainability. Also, the pumps’ components can be constructed from a variety of materials, including stainless steel, Hastelloy, PTFE and polypropylene, which coupled with the flexible design makes repurposing easy.
Paul Davis, Wanner International’s Managing Director, commented: “Our priority is to help energy organisations run safe and cost-effective pumping processes; this research shows with our low shear pumping action technology, significant savings can be made in EOR polymer injection. This has a huge impact on the efficiency and profitability of oil fields around the world, which is
especially significant given the energy crisis the world is facing.”
Wanner designs and manufactures API 674 and API 675 process, transfer, injection and metering pumps for the energy industry; helping customers around the world improve their processes and reduce energy consumption and maintenance costs.
Download the whitepaper
“Minimising Shear Effects in EOR Polymer Solutions”: https://www. hydra-cell.co.uk/Polymer-Injection
Draw-wire displacement sensors from Micro-Epsilon are extremely robust and flexible.
CGTech, developer of the marketleading CNC machine simulation software VERICUT, is launching the new VERICUT Version 9.4 just in time for EMO 2023 in Hanover (Hall 9/Stand B24). Under the motto “Get connected”, CGTech offers outstanding features & functions with the current version, which offer immediate added value in the day-to-day business of metalcutting production.
Number 1 priority: Usability
“Whether it’s milling, turning, mill-turning or any other type of CNC machining, VERICUT is the industry standard for CNC machine simulation, NC program optimisation and verification,” said Daniel Magnusson, CGTech Vice President of Commercial Business. The fact that CGTech’s solutions are deeply rooted in the history of the Aerospace industry and are used today in all industries, from Oil and Gas and Medical Technology to Tool and Mould making and Formula 1, goes back to a core focus: to offer the highest level of usability to all users, in all industries across the globe.
The new CNC Machine Monitoring module focuses on increasing connectivity across the manufacturing workflow, enabling organisations to do more with the resources they already have. Via VERICUT, the real events on
the shop floor can be streamed live in real time to monitor what the machines in the workshop are actually doing. In this way, it is possible to check which NC program or subprogram is currently running, how the movements of the machine axes and spindle activity are currently present, or which tool is loaded.
With the new CNC Precheck - a standalone app - machine operators can ensure that key points of the machine setup correspond to the data checked in VERICUT, without tying up a VERICUT license. Any differences, which may lead to problems, can then be investigates and corrected before any actual machining takes place. A typical application is checking whether the parameters of the real machine match the parameters of the virtual VERICUT machine.
The new improved VERICUT Reviewer is very practical as everyone in the company, including Machinists, Engineers, Quality Assurance, can check NC programs before they run on the real CNC machine, and without tying up a VERICUT license. All that is required is the free downloadable Reviewer app.
All VERICUT users, even those without the Force module, can benefit from the enhancements to optimisation in VERICUT 9.4. Streamlined setup
and the settings provided by VERICUT Tool Data gives users an opportunity to quickly optimise their NC programs, without having to search for starting values when it comes to materials and cutting tool parameters. Users can also import cutting data with cutting tool assemblies, such as those from tool vendor sites and repositories like MachiningCloud, TDM, ZOLLER and more.
Finally, VERICUT 9.4 offers improved support of Multi-ToolStations (MTS), a new ToolsUnited interface (access to tool and cutting data from over 40 tool manufacturers) and improved tool data (extension to include HSS and ceramic milling cutters as well as knurled milling cutters).
With labour hard to find and performance at peak under scrutiny, businesses may be tempted to opt for a complete, turnkey warehouse automation project to solve all their problems in one move. But might a stepped approach make more sense? Dan Migliozzi, Head of Sales at independent systems integrator, Invar Group, considers the options.
There can be little doubt that automation is the future for all but the smallest of warehouse operations. New affordable technologies are now within reach of most small to medium sized businesses (SMEs) and these technologies, often involving robotics and AI, are transforming performance across intralogistics processes.
Driven by poor labour availability and increasing customer demands, many businesses will be thinking about a comprehensive review of their operations, and may be tempted to go for a full turnkey approach –introducing a whole raft of systems at the same time. However, whilst this may be appropriate for some companies, others may be exposing themselves to unnecessary levels of risk, and a more considered approach could yield greater gains.
For a major corporation with the luxury of multiple warehouses or distribution centres, and facing challenges or changes to their current operational model, it may be practical, even desirable, to take facilities off-line one by one and rebuild them. For smaller businesses though, this could be a highly risky strategy and may be unviable – a considered, step-by-step approach to the end goal of significant automation may be preferable, both financially and operationally.
Financially, moving towards automation in planned stages limits the need for often significant upfront capital expenditure, a particular concern for start-ups and other
companies in a phase of rapid growth when other demands on working capital can be considerable. A stepped approach that quickly takes advantage of ‘low hanging fruit’ can achieve an early Return on Investment and bring many other benefits – potentially helping to fund subsequent phases of automation.
But even if capital funding isn’t an issue, the risks of an ‘all-in’ approach are significant. Some degree of disruption is inevitable during installation, and even with the most careful planning, highest quality equipment and dedicated vendors and integrators, it’s rare for everything to work straight out of the box. The risk of a major delay or disruption could have a far-reaching impact on the business and may lead to lost sales and reputational damage.
A further consideration is, with a complete turnkey approach it’s usually not possible to revert to the old ways of working while the fixes are actioned. There is no redundancy in this situation.
So rather than playing with the entire operation in a giant sandbox, better by far to identify and address the most urgent or compelling challenges and opportunities as they arise. That way, processes can be better defined and understood, employees at all levels trained and other necessary capabilities – maintenance, for example – built up at a manageable pace.
‘Step-by-step’, however, does not mean ‘piecemeal’. The planning for a stepped migration to more automated operations is just the same as it would be for a turnkey project – indeed the ultimate goals will be just the same – it’s merely a question of how to get there.
Firstly, and obviously, the company needs to know its objectives and requirements. Is automation needed because the business is in, or is anticipating, a period of rapid growth? Growth is good, but for many companies, perhaps in a mature or niche market, higher volumes and throughputs may not be the issue –greater efficiencies, lower costs and perhaps particularly better use of scarce labour may be the imperatives.
The company needs to map and understand its processes from cradle to grave, including processes which are unlikely to be directly addressed
Planning a stepped approach to warehouse automation cannot be just a top down, or a bottom up, process.
- Dan Migliozzi
by automation. Where are the biggest wins, the greatest challenges, the most acute pain points? Address these first – paradoxically, trying to optimise a process that you know to be already very good often carries a larger downside risk.
But the automation plan can’t just address short term issues. The business may need to consider the extent to which the automation is scaleable – can a robotic installation, for example, be scaled up for future growth just by leasing more units, or will there be a point at which the racking and other physical attributes of the warehouse require major change? And if so, should that be done now, even though it may not be needed for some years?
The plan also needs to consider the pace of technological change. Evolution in fields such as robotics is lightning-fast. There is no shame in buying last year’s model if it does the job, but there are risks that equipment
and systems may become ‘obsolete’, or worse, unsupported, much quicker than expected. This means that some of the steps in the automation road map may need to cover replacing or upgrading earlier and relatively recent investment steps. Robust continuity planning, in partnership with reputable vendors and integrators, is key.
Planning a stepped approach to warehouse automation cannot be just a top down, or a bottom up, process. It really does require the involvement of every stakeholder in the business. Clearly it needs high level strategic direction to ensure that the plan is aligned with the company’s goals, its financial capacity, and its appetite for risk. Operational input – will the proposals actually meet the requirements of, for example, seasonal peaks. Engineering – does the business have, or can it expect to establish, an adequate maintenance capability or will this have to be outsourced. HR may have views on how staff can be trained, and whether new staff with new skills need to be hired.
And then there is installation. Even quite modest steps in automation are likely to involve systems and equipment from multiple manufacturers and vendors and will require some level of integration, both with each other and with existing equipment and systems. ‘Plug and play’ is a much-vaunted term, but it’s hard to find evidence that it really exists in the modern warehouse!
Therefore, it’s important to find a reliable, independent integrator that has the necessary technical capability and in-house software skills to deliver a project successfully over several planned stages – an integrator that supports you every step of the journey.
Ovarro’s new technology leader for leakage solutions, Barbara Hathaway, discusses her career and gives words of advice for aspiring engineers
What led you to engineering?
My father was a physics teacher, who encouraged me and my two older brothers to consider how things worked. We learnt to value knowledge and understandingand it was fun! Both my brothers became engineers – one a civil engineer and the other in mining. There was never any suggestion that engineering was not for girls, so I decided to follow them into the arena and study electronic engineering.
What is the best thing about being an engineer?
Engineers create solutions. Give an engineer a problem and they will help you solve it.
My father was a physics teacher, who encouraged me and my two older brothers to consider how things worked. We learnt to value knowledge and understandingand it was fun!
- Barbara Hathaway
I love developing an important solution for a customer and seeing the satisfaction my team gets from delivering a successful project. Engineers really do make a difference and given that we are in the midst of an unprecedented global water crisis, their problem-solving skills are urgently required.
I graduated with a degree in electrical & electronic engineering from Portsmouth University in the 1990s. I joined Primayer – a pioneering leakage technology company which was acquired by Ovarro in 2019 - 27 years ago, as a software engineer. After working as customer services manager and technical services director, I became vice president of engineering in 2020. Now, in the newly-created role of technology leader for leakage solutions, I will be leading and developing Ovarro’s technology strategy and roadmap for leakage reduction products.
It is an exciting time to be working in leakage reduction - globally, more and more utilities are adopting datapowered tools, which are transforming network management, positively impacting leakage targets and environmental performance. Products that apply artificial intelligence and machine learning, as well as cloud-based, as-a-service models, are recent additions to the Ovarro portfolio.
Looking back, I found the transfer from engineering into business leadership challenging, in a good way. I have always been a problem-solver, but I now have to be careful not to dive too far into the detail, allowing my teams to do the more technical work.
Women remain underrepresented in engineering. Are there enough opportunities?
Historically, what I’ve seen is a lack of female engineers to fill the opportunities that arise .Figures from 2021 indicate that in the UK, only 16.5% of engineers are female, but I feel the landscape is changing. Girls are excelling at STEM subjects in school. There are support and mentoring networks in place to encourage girls to study what they want.
Once in the workplace, options for more flexible working and better parental leave have made a big difference, particularly in the last three years, which can only help and encourage women to join and stay within the sector. However, there remains an implicit gender bias in wider society which puts up barriers for many. Until this is tackled, we will not have true equality.
Have you encountered any gender bias in your career?
I am lucky to say I have not found being female has had an adverse effect on my career. Colleagues have always treated me as an equal. On occasions, when I’ve attended client meetings with male colleagues, people have initially assumed the man occupies the more senior role. This kind of implicit bias still exists and is one of the key things we need to educate about.
I feel the Bechdel test – which is an informal way to evaluate bias against women in films and other mediashould be referred to more often. Until men and women are viewed in the same light then ‘female engineers’ will always exist. I wish for a world where I was simply referred to as an ‘engineer’.
Do you see more women in engineering now than when you started your career?
When I joined an engineering course at university, I was one of four women
out of 100 students. Looking internally at Ovarro today, around 12% of our technical staff are female. It is a statistic I would like to improve.
We have an excellent female engineer in our Netherlands office, who is leading the development of our Stream Webscada software and we have other female engineers working at all levels within our SCADA and RTU teams. I see more women in technical and engineering roles now and feel proud to see how far we have come since I started my career - but this is still a work in progress.
I am very conscious that I am seen as a role model for younger engineers, so am always ready and available to offer a helping hand.
How would you encourage young women and girls to take up engineering?
Go for it! Engineering is an incredibly satisfying career choice. Find yourself allies early in your career who will encourage your ambitions. Do not be limited by the words and attitudes of others.
At Ovarro, we’re always on the look-out for new talent. Engineering constantly moves on and we need new ideas to be able to continue to innovate. Water is a critical sector to be part of – it is central to all our lives – and reducing leakage will put you at the very heart of global efforts to preserve supplies for future generations.
It is an exciting time to be working in leakage reduction - globally, more and more utilities are adopting datapowered tools, which are transforming network management, positively impacting leakage targets and environmental performance.
- Barbara Hathaway
I see more women in technical and engineering roles now and feel proud to see how far we have come since I started my career - but this is still a work in progress.
- Barbara Hathaway
When it comes to material, surface and solid wood processing, choosing the right drive solution for the woodworking machine is critical. As different as the requirements for the drive controllers are, one topic is always important: ensuring the highest possible level of safety, says Mark Checkley, Managing Director of KEB UK.
Functional safety is intended to keep the risks posed by technical equipment to people and the environment as low as possible.
Processing machines or machine tools, for example, can endanger machine operators through tools that rotate at high speed. To prevent this from occurring in the first place, we provide drive solutions with integral safety functions with or without an encoder. To avoid dangerous operating conditions, these safety functions monitor the speeds, directions of rotation or axis positions. As safety functions are already integrated in our drive controllers and interact optimally with our safety controllers, users can implement functional safety costeffectively.
In our ‘PRO’ version, the COMBIVERT F6 drive controllers and COMBIVERT S6 servo drives have Safe Door-Lock Control (SDLC) with Performance Level d (PL d). We developed this function and it can be used to lock the door or bonnet of the machine. With SDLC, the door can only be opened when the motor is at a safe standstill, in order to enable tool changes, for example, or the machine to be cleaned. In addition, we offer further speed- and position-dependent safety functions such as Safe Speed Monitoring (SSM) or Safely Limited
Speed (SLS), also in combination with Safe Direction (SDI), whereby the drive safely monitors the speed. If the set speed limit is exceeded, an error reaction takes place and tools are ultimately protected from overspeed by SLS. Of course, we also rely on safe communication – as an established solution with Safety-over-EtherCAT or PROFIsafe, which is integrated in the ‘APPLICATION’ version of our drives.
In woodworking machines, fires can start faster than you might think. Even leakage currents of 300 mA can trigger a fire in the worst case scenario. That is why 300 mA residual current circuit breakers are required in the machines. With this in mind, we developed the COMBILINE E6 filter series – which is implemented in the latest generation of our inverters –which feeds the leakage currents in the inverter-cable-motor-network back into its own system. The filters are available as sub-, auxiliary- or collector filters and contribute to reducing leakage currents to a minimum and to lowering the risk of fire.
For more information, please visit www.keb.co.uk
In woodworking machines, fires can start faster than you might think. Even leakage currents of 300 mA can trigger a fire in the worst case scenario.
- Mark Checkley