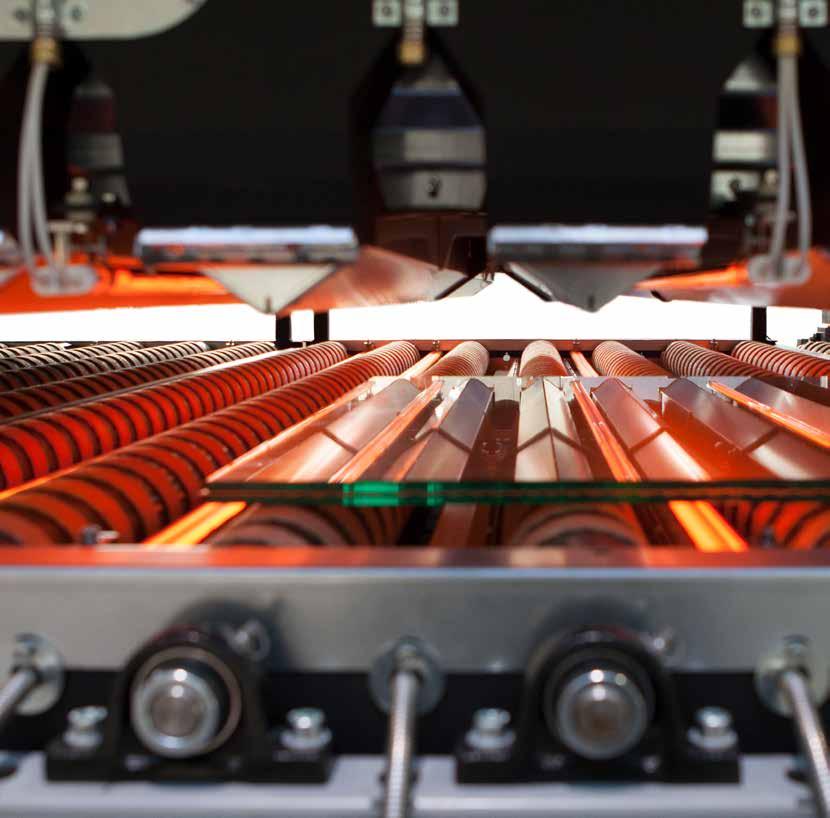
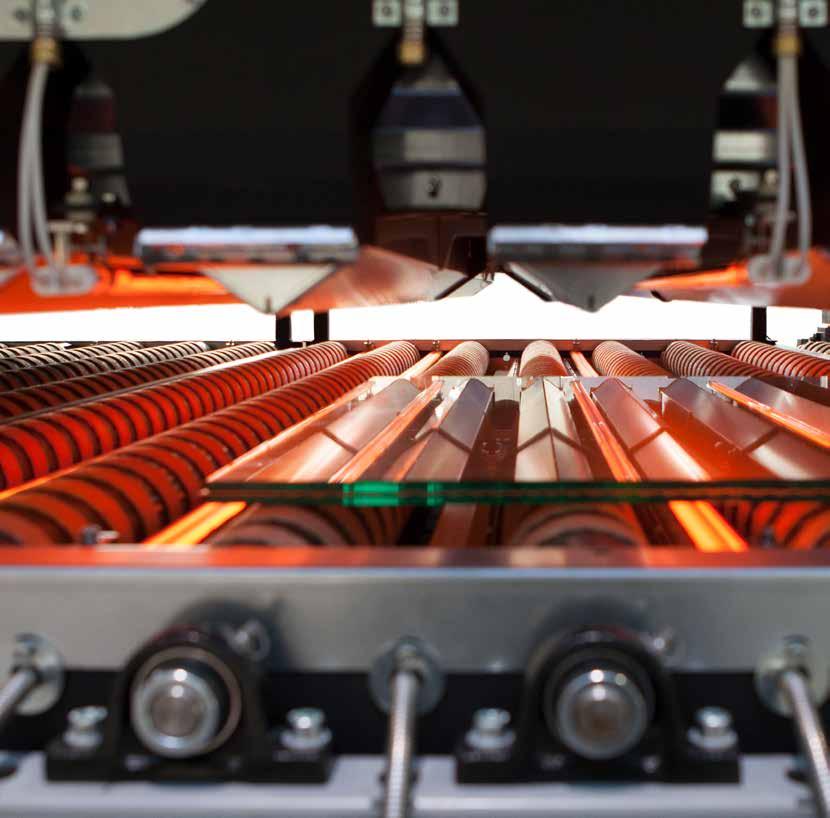
Machinery for Laminated Glass Production
Facts and figures:
1961 founding year
1 strong brand
1,300 employees
20 sites
300 million Euros turnover (2023)
95 % export rate
7 % of turnover for R&D
more than 330 patents
Reliable processes, good quality, solid profit: LiSEC solutions provide flat glass processors around the world with security and drive in a challenging environment.
For the last 60 years, we have been working hard to enable you to sustainably boost the efficiency, the system availability and the quality output of your flat glass production process. Thanks to forward-looking thinking, continuously striving to find the best solution and a great deal of personal commitment from our employees, we have grown from a one-man company to a technology leader.
Our advanced solutions generate a great cost-to-benefit ratio throughout the entire lifecycle of your machines and systems.
Customers around the world can benefit from this: be they experienced manufacturers or newcomers to the industry; from family businesses to industrial glass processors. Three main factors are essential for long-term success:
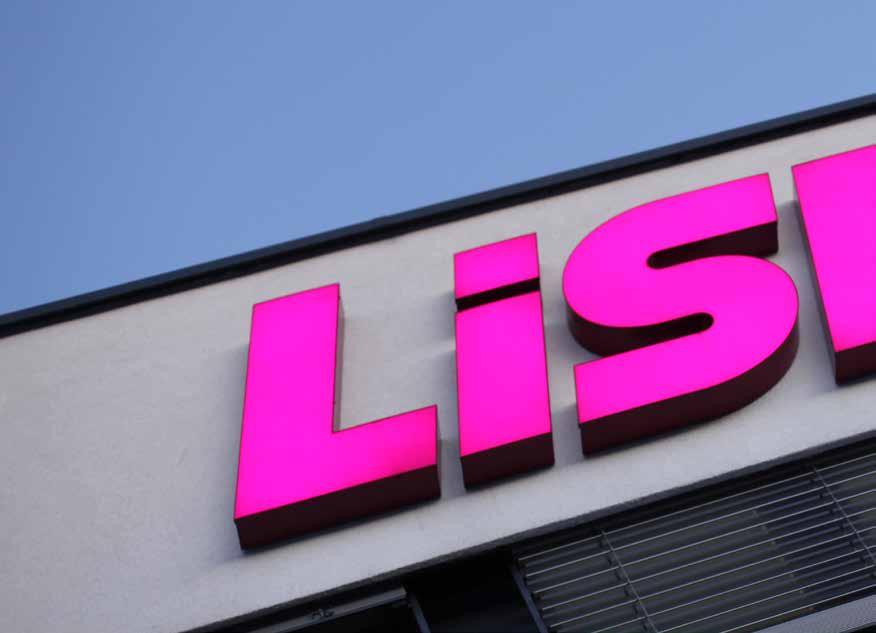
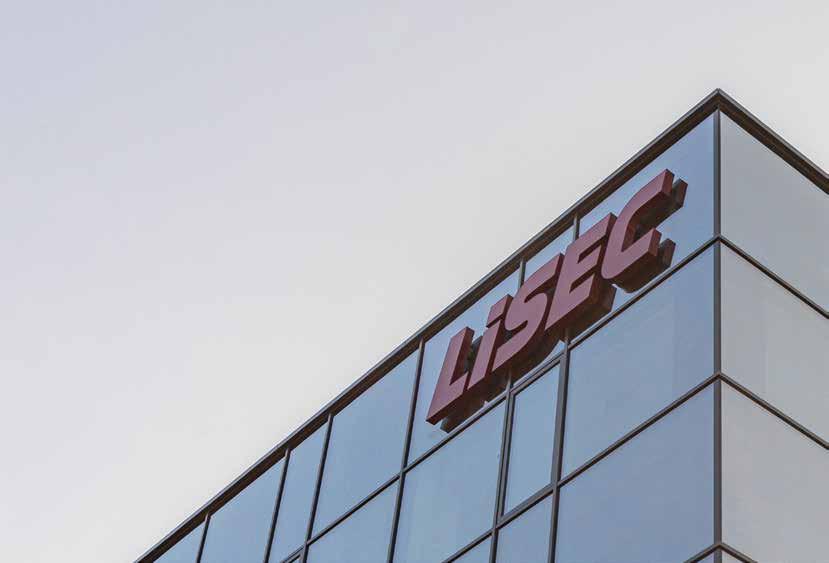
1. Turn Key Solutions
Everything from a single source including software. Customers benefit from the only company in the flat glass machine industry that can comprehensively plan and develop large projects - also thanks to the widest product range in the industry.
2. Excellent Service
Investment security and the highest availability and productivity enable the large, global LiSEC service network. A contact person familiar with the local language and customs is available close to you.
3. Performance through software integration
Integration of the production management software and the machinery control (digitalization/Industry 4.0) allows top operation and optimization of all integrated machines or whole glass factories.
The benefits:
Over 60 years of partnership, pioneering spirit and stability
Investment security due to the size of our company
Leading technology with a high resale value
Great cost-to-benefit ratio throughout the entire system lifecycle
To improve readability, this brochure refers to groups of people in a neutral form, whereby both male and female persons are always meant.
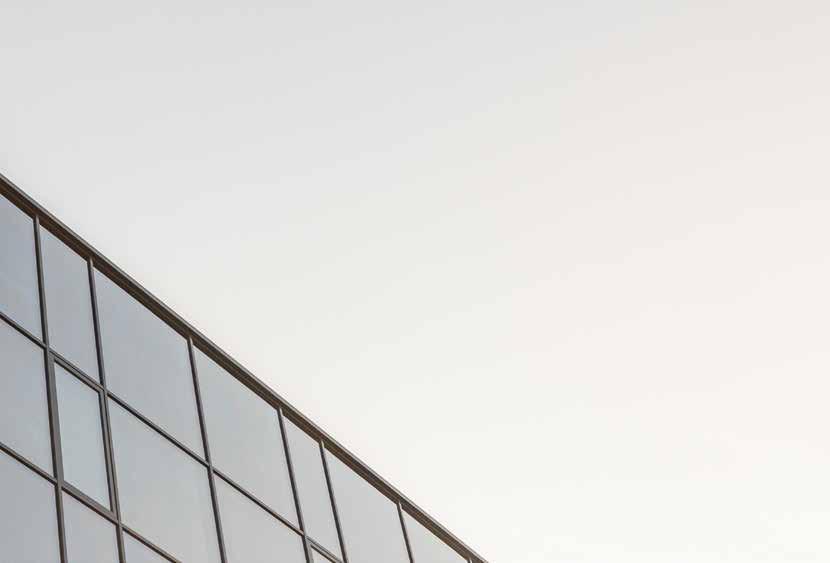
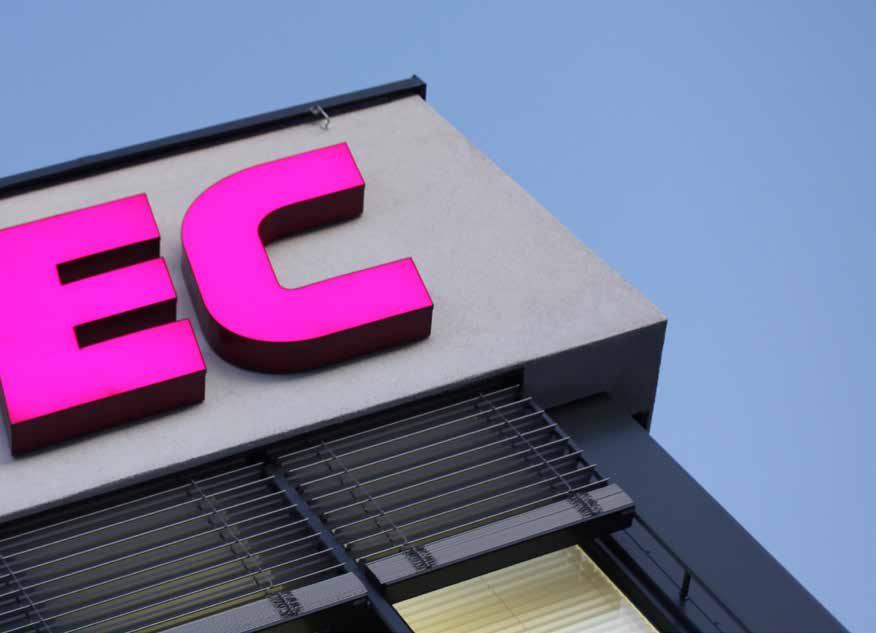
Machinery for Laminated Glass Production
LINES
PlusLam p. 10
One storey LiSEC Lamination Line with 3, 6, 9 or 12 foil-rolls magazines for production halls with a minimum height of 4900 mm
Overview PlusLam p. 11
MaxLam p. 14
Two storey LiSEC Lamination Line with 12, 18 or 24 foil-rolls magazines for production halls with a minimum height of 6700 mm
Overview MaxLam p. 15
Line Components
Conveyor Wheels (OCW) p. 16
Horizontal transport and storing station
Loading Tilting Table (LTT) p. 16
Loading station for a laminated glass line
Horizontal Washing Machine (HWM) p. 16
Horizontal glass washing and drying machine for flat glass
Positioning Table (PST) p. 16
Station for the precise positioning of glass sheets before the assembly of laminated glass sandwiches
Carry Over Lifter (COL) p. 16
Station for the transport and positioning of glass sheets on the assembly station
Assembling Table (AST) p. 16
Station for the assembly of laminated glass sandwiches
Foil Unwinder Feeding (FUF) p. 17
Bridge feeding system for feeding a foil magazine (FUW)
Foil Roller Cart (FRC) p. 17
Light cart for transporting foil rolls
Foil Unwinder (FUW) p. 17
Foil magazine with unwinding unit
Foil Cross Cut (FCC) p. 17
Station for the foil rough cut
Foil Laying Automat (FLA) p. 17
Unit for automatically placing a foil
Foil Shuttle Station (FSS) p. 17
Foil unloading station for special foils, standard foils and foil remnants
Foil Trim Cut (FTC) p. 17
Horizontal transport station for automatic trimming of the laminated sheets
Pre Nip Machine (PNM) p. 18
Pre-lamination furnace for heating and pressing “laminated glass sandwiches” for laminated glass production
Table of Contents
Conveyor Wheels (OCW) p. 22
Horizontal transport and storing station, as an inlet, outlet or buffer station in a laminated glass line
Unloading Tilting Table (UTT) p. 22
Tilting table for removal of laminated glass sandwiches
Foil Storage Rack (FSR) p. 22
Magazine for film rolls
Climate Clean Room - (CCR-A1) p. 22
Climate room for PlusLam
Climate Clean Room - (CCR-A2) p. 22
Climate room for MaxLam
Autoclave (ACL) p. 23
System for establishing the end lamination of glass and foil at the end of a laminated glass line
Mode
Speed Assembling Mode p. 24
One-By-One Mode p. 24
Basic Mode p. 24
PNM Exchange
Software
Information and ready messaging terminal at the production
Service Services
We offer you worldwide service and the fastest possible supply of spare parts.
The LiSEC Lamination Portfolio
The best of 2 technologies, more than 170 installed lamination linesDecades of experience
LiSEC Lamination Line is the intelligent and customer specific lamination line for PVB and SGP-foils. We distinguish in PlusLam and MaxLam.
PlusLam is a single storey production line with 3, 6, 9 or 12 foil-rolls magazines for production halls with a minimum height of 4900mm.
MaxLam is a double storey production line with 12, 18 or 24 foil-rolls magazines for production halls with a minimum height of 6700mm.
Both lines are available in three standardized configurations.
COMPACT is the most cost effective way for prelamination for a low volume of laminated glass.
COMFORT is a comfort and ergonomic high-speed and semi-automated lamination line for customers with a big mixture of products and many special shapes. The line is designed for a mid to high volume.
PREMIUM is a comfort, ergonomic, personal-saving high-speed and nearly fully automated lamination line appropriate for customers with a large production volume of lamination glass. Most of them rectangular. This concept sets the focus strongly on elements important for each organization, such as production cost reduction.
All lines are available with the PNM-B: 80 mm und optional 100 mm | PNM-B SN (single-nip): 60 mm and 80 mm on demand. PNM-B is as a single-nip and also as a double-nip press available. So whatever you choose, you always get the spindle-pressingtechnology for accurate and parallel pressing as well as three heating-systems: Convection | Radiation or Convection + Radiation.
Due the special designed IR-Heaters, the quick upheating for switching off and on as we need, also the Ecoheaters to segment the width into two heating segments, the automatic speed-adjustment instead of opening the flaps to cool-down the oven helps to save energy. Speed Assembling, automatic foil-length-measurement, automatic foil-cross-cut, automatic foil-laying and automatic foil-trimming on all four sides of rectangular glass-sheets helps us to increase the degree of automation and also of the higher productivity.
Highlights
High Output through smart technology
Fast Pre-Nip lamination speed on very short furnace length due to combination of special radiation & convection system.
Energy efficient due to intelligent heating system
Advanced radiators heating up from approx. 25 °C to over 900 °C in less than 60 seconds. The heaters are only in use when glass is actually being processed in the pre-lamination machine. In addition the automatic glass width detection at the infeed controls the switch between half and full radiator width.
Precise adjustment of press force and gap due to servomotor-controlled press
Double-sided electrical control of the presses with servo spindles ensures perfectly parallel pressing with exact press force and enables easy, toolless fine adjustment of the presses.
High positioning accuracy
The positioning accuracy of the glass is +/-0.5 mm (half of the max. length)
The positioning accuracy of the glass is +/-1.0 mm (max. length)
Positive feasibility studies with 1 mm thin tempered glass
The gentle accurate press technology allows to laminate very thin glass.
Turn-key package solution
When additional equipment, such as autoclave and clean room, is purchased from LiSEC, we take care of the complete coordination to provide a turnkey production for composite and laminated safety glass.
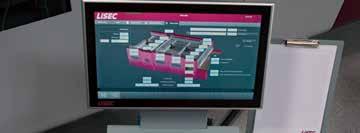
up to 55%* better energy efficiency
up to 10% higher degree of automation
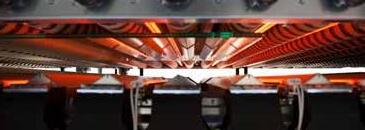
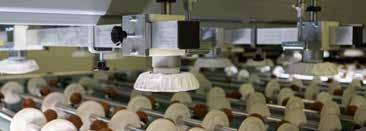
always proper pressing force
up to 50 pcs/h higher productivity
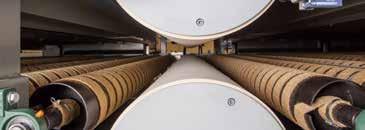
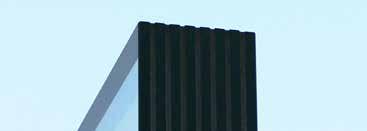
nearly zero offset on the reference side
ergonomical working
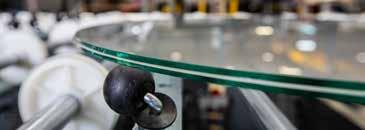

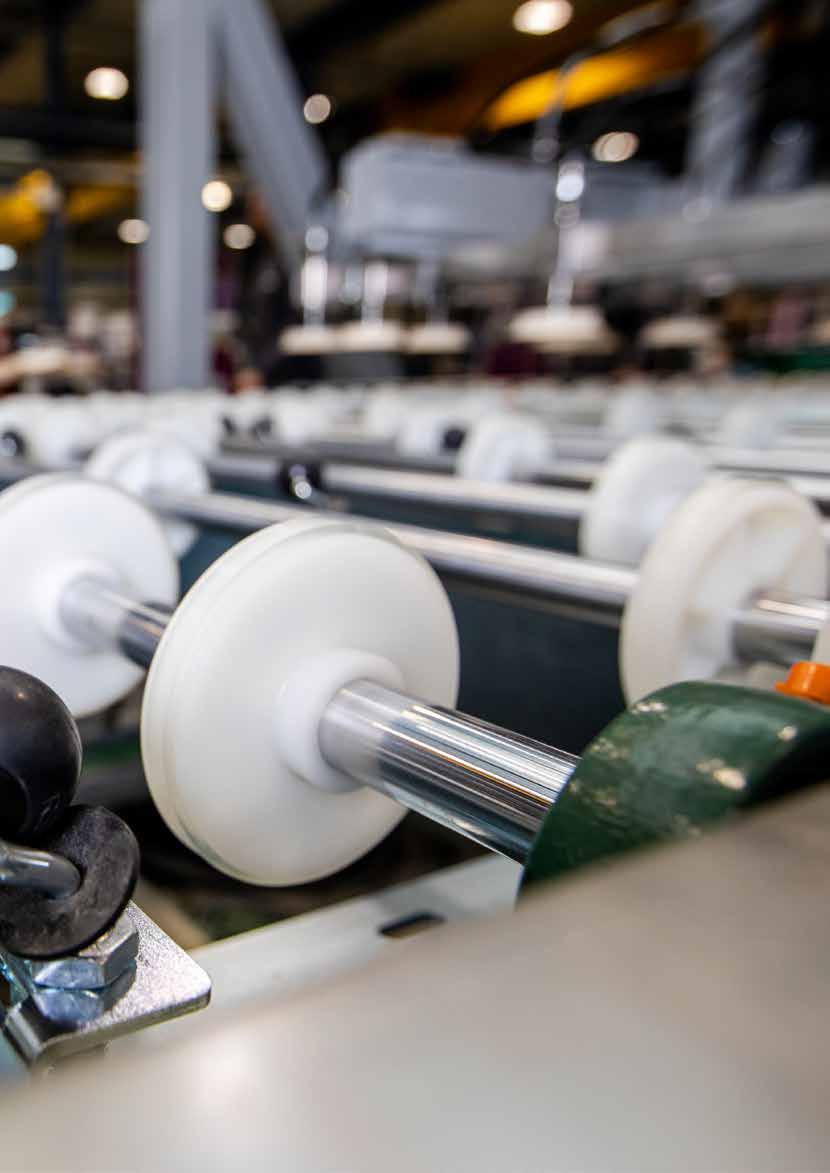
LINES
We created lamination lines, which fit your production requirements. The combination of the strength of LiSEC in different areas such as process, software and machine engineering, does lead to a highly stable lamination system.
In order to use the full efficiency of our lamination products, cross-line software solutions are available.
One
storey LiSEC Lamination Line with 3, 6, 9 or 12 foil-rolls magazines for production halls with a minimum height of 4,900 mm
Highlights
Cost-effective entry-level lamination line
Dimensions 2,000 x 4,000mm up to 3,300 x 12,000mm
Simple operation with Smart Press Technology
Single Nip or Double Nip Press possible
Foil unwinder for 3, 6, 9 or 12 rolls in one floor
Options
U-Form: U2040, U2650, U2860, U3360
S-Form (Straight): S2040, S2650, S2860, S3360, S3390, S33120
Economic single storage climatic room CCR-A1
*for the sizes 3390 und 33120 we only offer Double Nip Press
1 | OCW - Conveyor Wheels or LTT - Loading Tilting Table
2 | HWM - Horizontal Washing Machine
3 | PST - Positioning Table
4 | COL - Carry Over Lifter
5 | AST - Assembling Table
7 | FRC - Foil Roller Cart (not visible on the rendering)
8 | FUW - Foil Unwinder
9 | FCC - Foil Cross Cut
10 | FLA - Foil Laying Automat
11 | FSS - Foil Shuttle Station
12 | FTC - Foil Trim Cut
14 | PNM - Pre Nip Machine
15 | OCW - Conveyor Wheels or UTT - Unloading Tilting Table
16 | CCR-A1 - Climate Clean Room - 1 Floor
17 | ACL - Autoclave (not visible on the rendering)
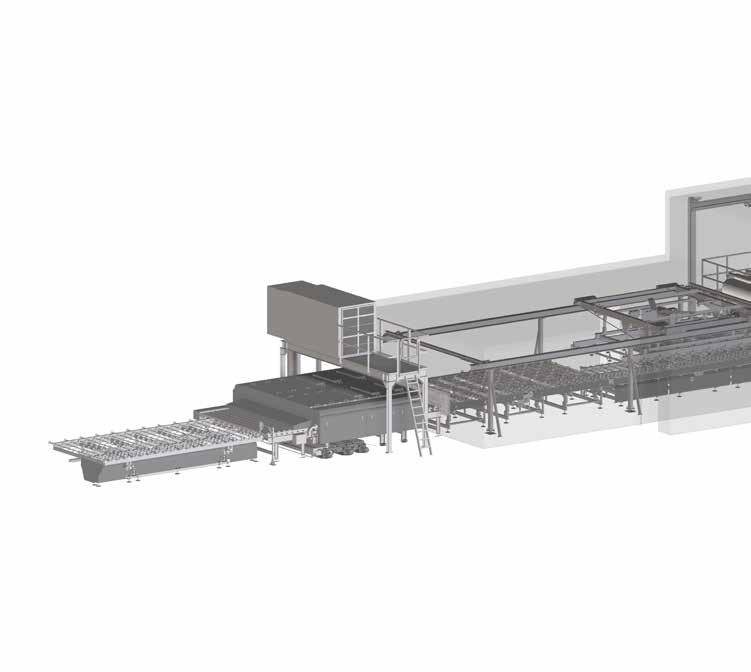
Overview PlusLam
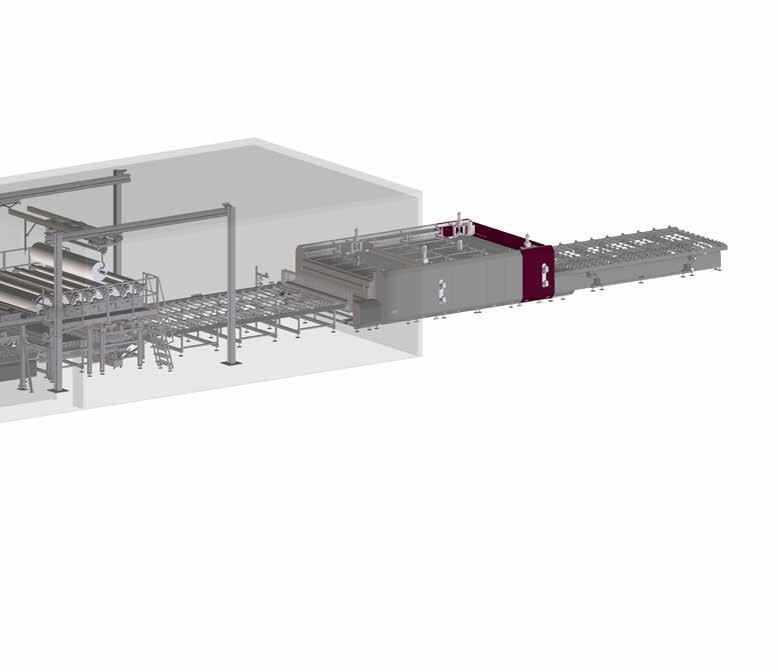
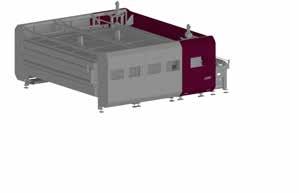
Overview PlusLam
Straight-Form
(LxW) [mm]
(LxW)
number of foil-rolls 3, 6, 9 or 12 rolls
Standard-Configuration
Design-Variant / Equipment-Variant
| COMFORT | PREMIUM max. glass thickness of the laminate: 100 mm
PNM-B: 80 mm und optional 100 mm PNM-B SN (single-nip): 60 mm and 80 mm on demand PNM-B20 PNM-B20SN PNM-B26 PNM-B26SN PNM-B28 PNM-B28SN
PNM-A33/5 PNM-A33
PNM-B33/5 PNM-B33 PNM-B33SN
U-Form
max. glass-size (LxW) [mm] 4,000 x 2,000 5,000 x 2,600
number of foil-rolls 3, 6, 9 or 12 rolls
Standard-Configuration 6 rolls
Design-Variant / Equipment-Variant
| COMFORT | PREMIUM
max. glass thickness of the laminate: 100 mm PNM-A20 PNM-A26 PNM-A28
max. glass thickness of the laminate: 60 mm (80 mm on demand)
PNM-B20 PNM-B20SN
PNM-B26 PNM-B26SN
PNM-B28 PNM-B28SN
PNM-A33/5 PNM-A33
PNM-B33/5 PNM-B33 PNM-B33SN
max.glass weight single sheet 500 kg 500 kg 500 kg 950 kg
max glass weight glass package 1,000 kg 1,000 kg 1,000 kg 2,000 kg
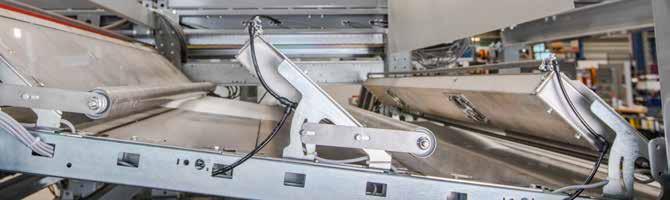
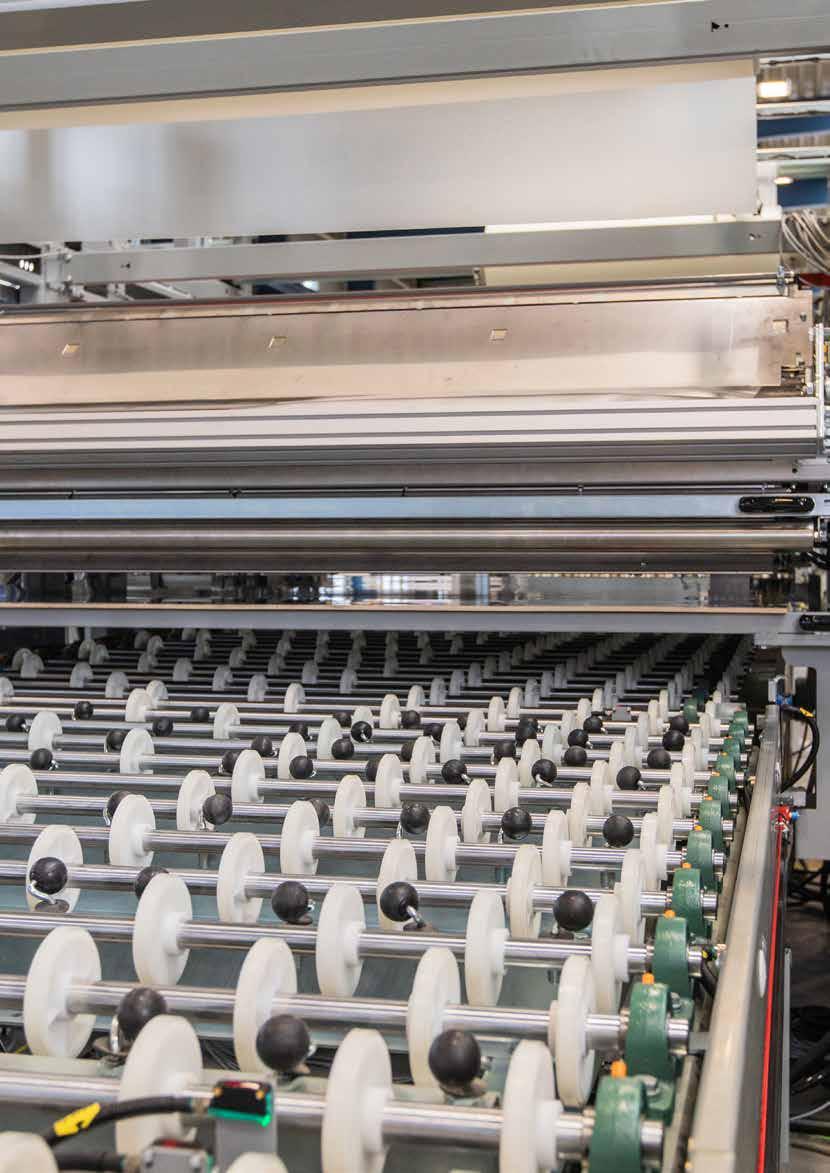
Two storey LiSEC Lamination Line with 12, 18 or 24 foil-rolls magazines for production halls with a minimum height of 6,700 mm
Highlights
Very flexbible by using the maximum numbers of foils
Foil unwinder for 12,18 or 24 rolls on second floor
Dimensions 2,000 x 4,000mm up to 3,300 x 12,000mm
Simple operation with Smart Press Technology
Straight-form
Single Nip or Double Nip Press possible
1 | OCW - Conveyor Wheels or LTT - Loading Tilting Table
2 | HWM - Horizontal Washing Machine
3 | PST - Positioning Table
4 | COL - Carry Over Lifter
5 | AST - Assembling Table
7 | FRC - Foil Roller Cart (not visible on the rendering)
8 | FUW - Foil Unwinder
9 | FCC - Foil Cross Cut
Options
Single or Double Nip Press possible (S2040, S2650, S2860, S3360)
Double Nip Press possible (S3390, S33120)
Double storage climatic room CCR-A2
10 | FLA - Foil Laying Automat
11 | FSS - Foil Shuttle Station
12 | FTC - Foil Trim Cut
14 | PNM - Pre Nip Machine
15 | OCW - Conveyor Wheels or UTT - Unloading Tilting Table
16 | FSR - Foil Storage Rack
18 | CCR-A2 - Climate Clean Room - 2 Floors
19 | ACL - Autoclave (not visible on the rendering)

Overview MaxLam
Straight-Form
glass-size (LxW) [mm]
Min. glass-size (LxW)
S2650
x
Number of foil-rolls 12, 18 or 24 rolls
Standard-configuration 12 rolls
Design-variant / Equipment-variant
Max. glass thickness of the laminate: 100 mm
PNM-B: 80 mm und optional 100 mm
PNM-B SN (single-nip): 60 mm and 80 mm on demand
weight single sheet
glass weight glass package
S3390 S33120
PNM-A33
PNM-B20 PNM-B20SN PNM-B26 PNM-B26SN PNM-B28 PNM-B28SN PNM-B33/5 PNM-B33 PNM-B33SN PNM-B33/5 PNM-B33
Total height 6,500 mm (Clean room interior height without ceiling thickness) Total width 7,100 mm 7,500 mm 9,000 mm
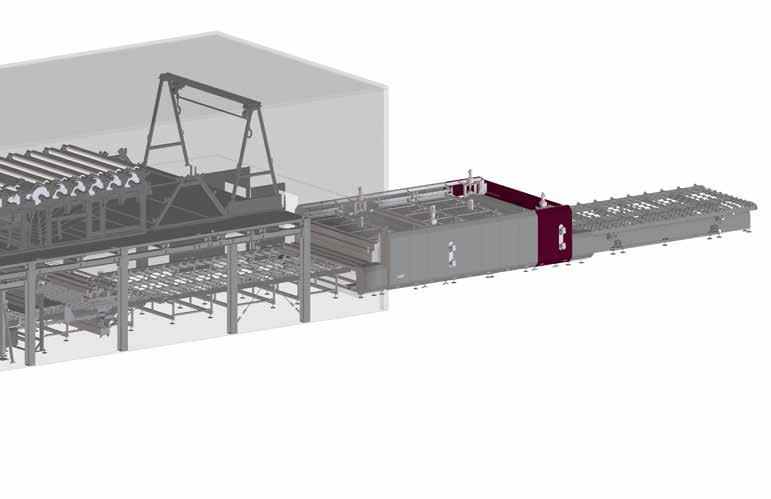
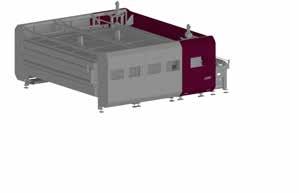
1 | OCW (Conveyor Wheels)
Horizontal transport and storing station

1 | LTT (Loading Tilting Table)
Loading station for a laminated glass line
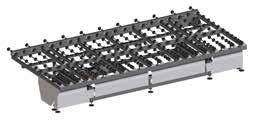
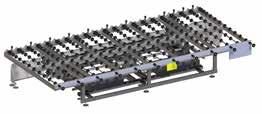
2 | HWM (Horizontal Washing Machine)
Horizontal glass washing and drying machine for flat glass
3 | PST (Positioning Table)
Station for the precise positioning of glass sheets before the assembly of laminated glass sandwiches
4 | COL (Carry Over Lifter)
Station for the transport and positioning of glass sheets on the assembly station
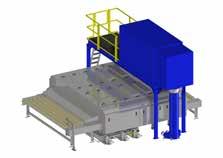
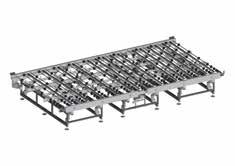

5 | AST (Assembling Table)
Station for the assembly of laminated glass sandwiches
AST-A40/20 (automatically adjustable in width)
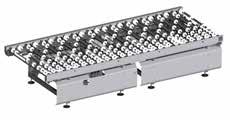
AST-B50/26 (manually adjustable in width)
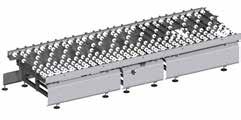
LTT-H (hydraulic up to 3360)
LTT-K (electric from 3360)
6 | FUF (Foil Unwinder Feeding)
Bridge feeding system for feeding a foil magazine (FUW)

7 | FRC (Foil Roller Cart)
Light cart for transporting foil rolls

8 | FUW (Foil Unwinder)
Foil magazine with unwinding unit
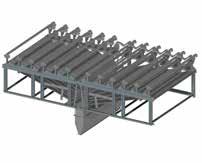
9 | FCC (Foil Cross Cut)
Station for the foil rough cut
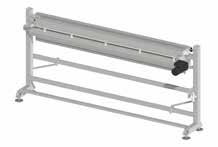
10 | FLA (Foil Laying Automat)
Unit for automatically placing a foil
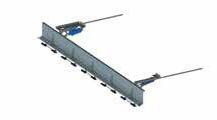
11 | FSS (Foil Shuttle Station)
Foil unloading station for special foils, standard foils and foil remnants
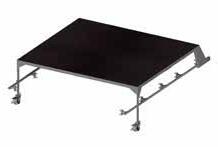
12 | FTC (Foil Trim Cut)
Horizontal transport station for automatic trimming of the laminated sheets
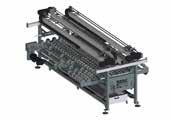
FUW-A
14 | PNM (Pre Nip Machine)
Pre-lamination furnace for heating and pressing “laminated glass sandwiches” for laminated glass production
The Pre-Nip machine (PNM) is the heart of every laminating line and is very decisive for the success or failure of the whole process.
The foil is heated and then pressed against the glass by rollers - the glass forms a strong bond with the foil. In the pre-lamination process, any remaining air is also removed from the glass package. After that follows the autoclave process, in which the molecules of the glass and the foil are made to swing under heat and chain together under pressure and clean surfaces.
One Pre-Nip machine: Three heating systems
CONVECTION
Convection is needed for thick glass elements.
RADIATION
Radiation is needed for thin glass elements, mostly double laminated glass (glass-foil-glass).
We don´t want to heat up the glass - we primary heat up the foil by IR-Heaters. This saves time, money and energy.
CONVECTION + RADIATION
A combination of convection and radiation is needed for coated glass.
Low-E, which is on the top of the glass-package reflects the IR-energy. So we can bring in the energy from the bottom and by the air around the product.
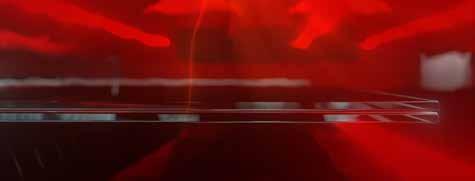
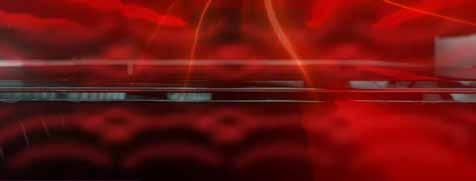
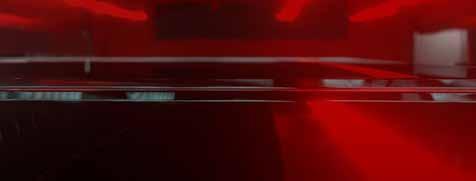
CONVECTION
RADIATION
CONVECTION & RADIATION
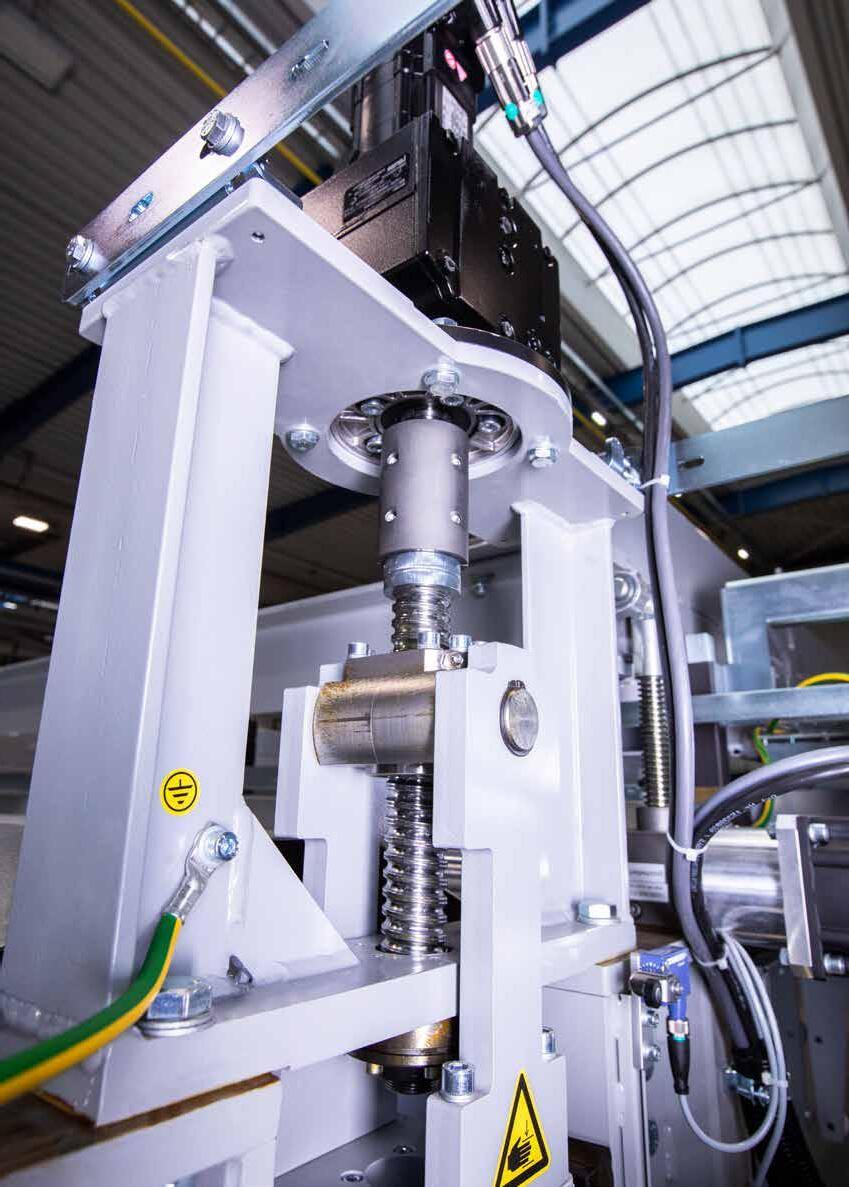
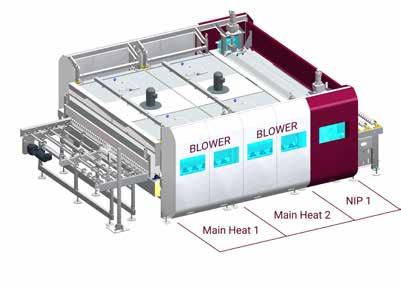
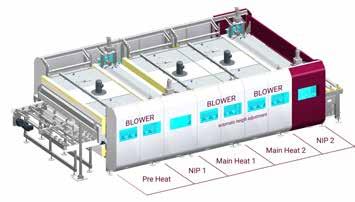
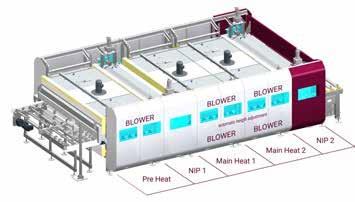
Single-NIP (PNM-B_SN)
Double-NIP
Double-NIP (PNM-B)
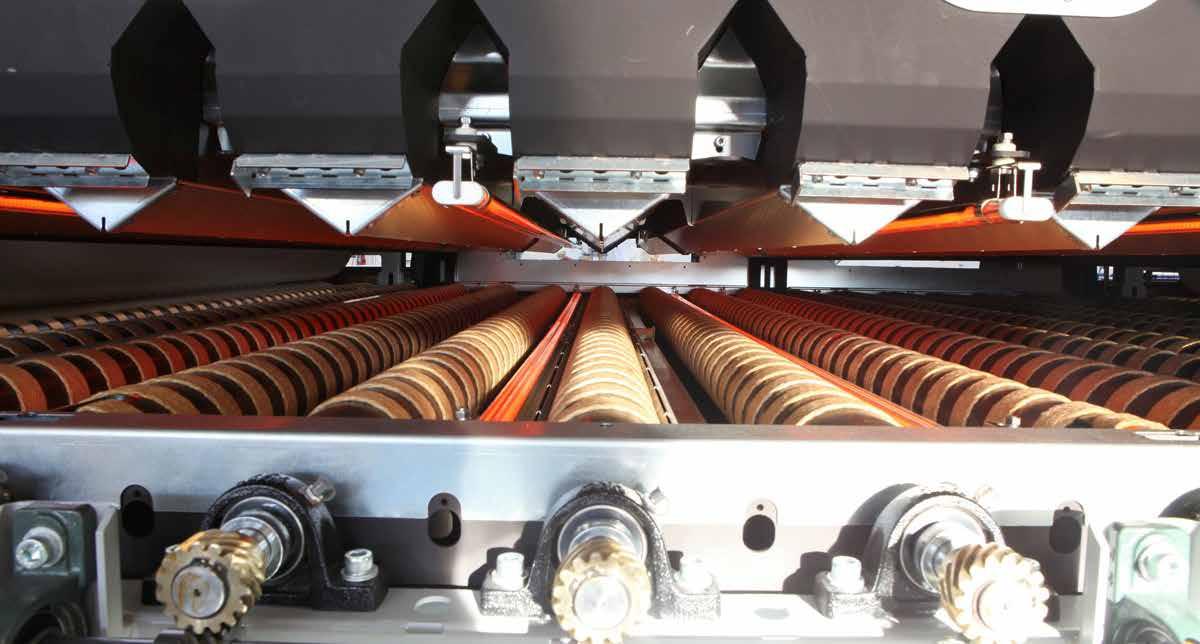
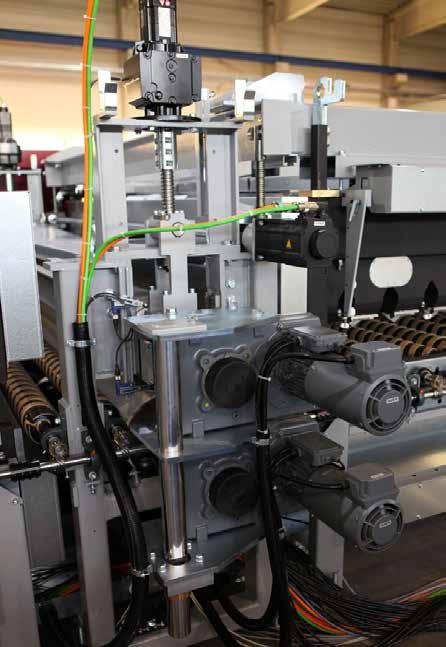
Pre Lamination – Heating Technology (PNM-A)
Pressing Technology (PNM-A / PNM-B)
Pre Lamination – Heating Technology (PNM-B)

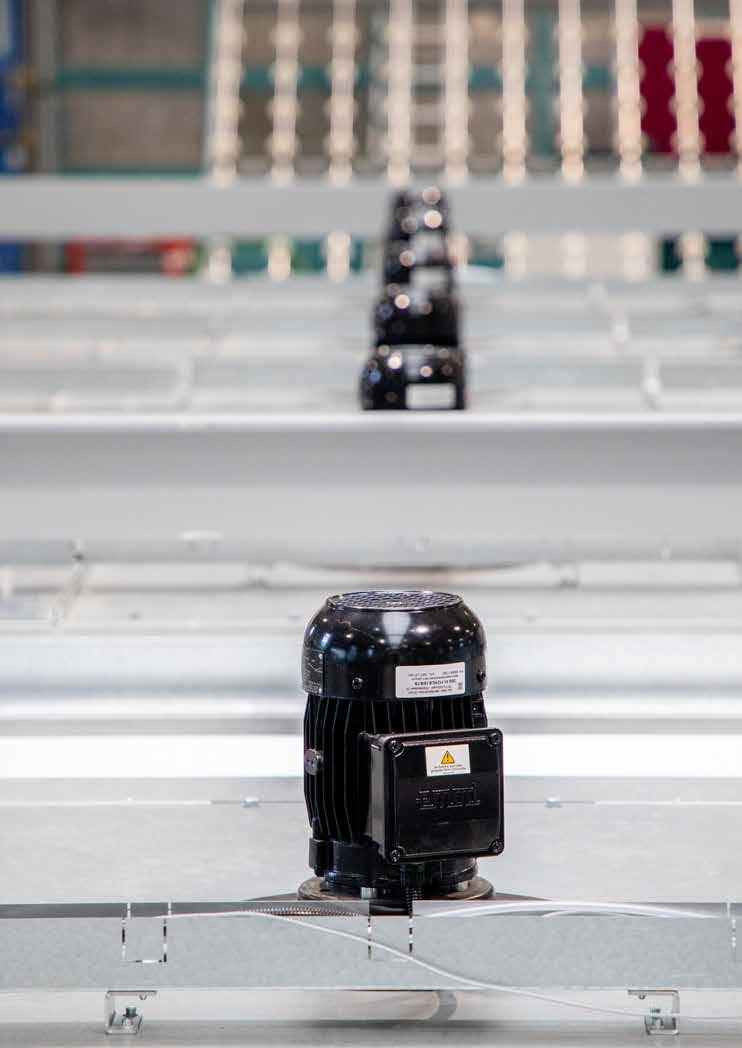
How does the PNM work?
The machine automatically records the width and shape of the glass before it enters the PNM. The correct pressing force is calculated. Less force is used for small widths than for large widths. If you have selected the Eco heating option, you can save energy and money. If the glass is < than the half of the max. width, the long IR heaters are switched off over the entire length and the short IR heaters are switched on.
Thanks to the unique servo spindle drive, we are always able to press in parallel and we can finely dose the pressing force. We press the glass pack on the glass surface and not on the glass edge to avoid misalignment or breakage. We are able to produce laminates up to 100 mm thickness.
After the pre-laminating press, the temperature on the glass surface is measured on the top and the bottom. If the glass is too „warm“, the machine speeds up automatically and if it‘s too „cold“, the transport-speed through the oven is slowed down. This safes energy and money for the best possible result. After all these things the pre-laminated glass is ready for the autoclave or vacuum bags.
USP‘s of the PNM:
Servo spindle drive
Eco Heaters
Parallel pressing
Finely dosed pressing force
Pressing the glass not on the front edge but pressing quite behind the edge on the surface
Specially developed IR heaters with the optimum wavelength
Up to 55 % better energy efficiency
Combination of radiation and convection
High productivity up to 50 pcs/hour
Start / Stop automatic
Production on the reference side
Recipes for the main unit build-up
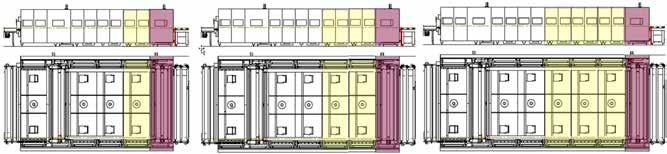
We can grow with our customer needs and speed up the PNM with additional main heating zones.
15 | OCW (Conveyor Wheels)
Horizontal transport and storing station, as an inlet, outlet or buffer station in a laminated glass line
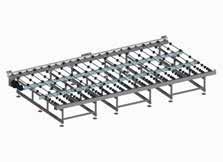
15 | UTT (Unloading Tilting Table)
Tilting table for removal of laminated glass sandwiches
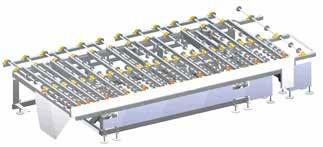
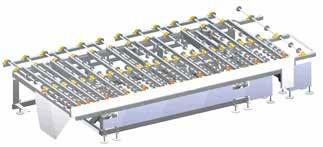
16 | FSR (Foil Storage Rack)
Magazine for foil rolls
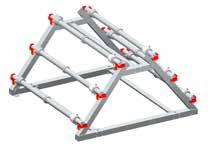
17 | CCR-A1 (Climate Clean Room - 1 Floor)
Climate room for PlusLam
18 | CCR-A2 (Climate Clean Room - 2 Floors)
Climate room for MaxLam
UTT-H (hydraulic up to 3360)
UTT-K (electric from 3360)
System for establishing the end lamination of glass and foil at the end of a laminated glass line
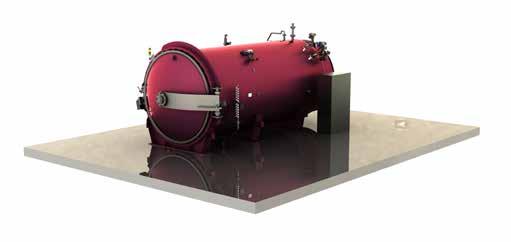

Speed Assembling Mode
This mode is suitable for large production volumes of elements and can be performed by just one person. The ability to rotate the foil 90° to obtain the desired glass width means that narrower foil rolls can be dispensed with, and waste is reduced.
The foil shuttle is extended. The applicator positions the glass at the front half of the assembly table
Automatic length measurement of the foil
Pre-cutting of the foil with an automatic foil rough cut „FCC“ according to the width
Turning of the foil on the shuttle
Manual laying of the foil by the staff
Manual or, in the case of rectangular sheets of glass, automatic trimming with the FTC on all four sides of the protruding foil
One-By-One Mode
This mode is especially suitable for the series production of small glass at high speed with only one person. In addition, there is less foil waste due to the waste optimisation.
The foil shuttle is extended
Automatic length measurement of the foil
Pre-cutting of the foil with an automatic foil rough cut „FCC“
Temporary storage of the cut and prepared foils on the Foil-Shuttle
Pairwise glass transport to the assembly table
Manual assembly of the glass-foil-glass package by the staff
Manual or, in the case of rectangular sheets of glass, automatic trimming with the FTC on all four sides of the protruding foil
Basic Mode
Width adjustment of the table manually or automatically
Assembly with a carryover lifter
Pre-cutting of the foil manual or automatic
Foil laying manual or automatic
Manual or, in the case of rectangular sheets of glass, automatic trimming with the FTC on all four sides of the protruding foil
PNM Exchange
Exchange of a Pre Nip Machine
Customer-needs:
Best possible product quality for all types of glass
Best economical solution (combination of energy saving and a minimum of remakes)
The shortest possible replacement during the operating holiday
Integration of the control-system
USP‘s of the Exchange:
CO2 reduction
Mechanical change within a few days
Moderate investment
Quick ROI
Maintaining the existing line
Integration of the control-system
Latest PNM-technology
Best possible product quality
Best economical solution

Before After
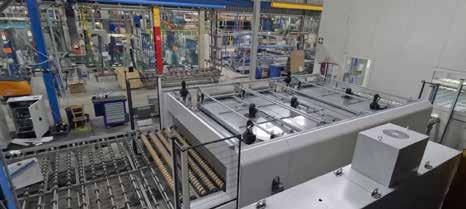
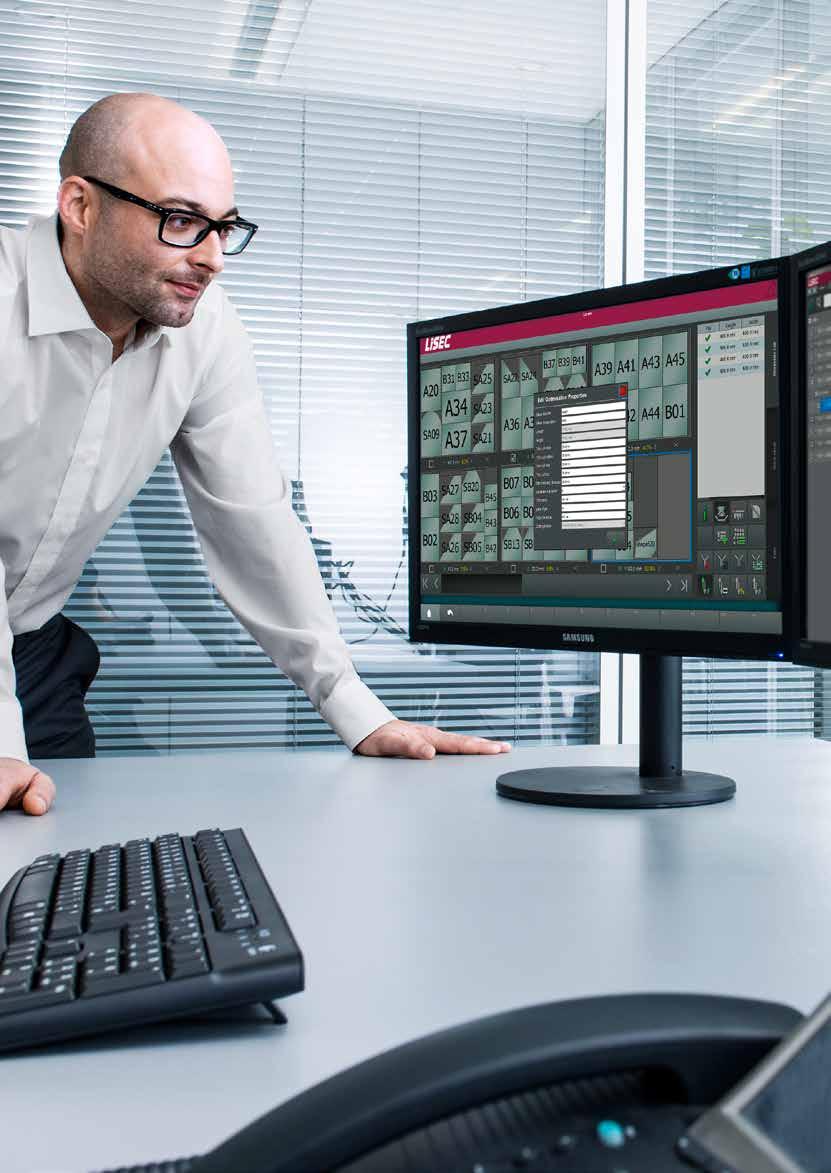

SOFTWARE
With our broad product portfolio we offer our customers a modular set-up, from single-user to complex group solutions with central administration and decentralized sales and production branches.
Our whole team supports the development and service of our products, with the goal of generating the greatest benefit for our customers.

Quality scanner for single sheets and insulating glass perfectscan
perfectscan makes it possible to check each single glass sheet and insulating glass unit for visual defects. This system allows you to prove the added value of your products, guarantee a higher product quality and significantly reduce customer complaints.
Highlights
Scalable in design and function depending on the area of application
Different technologies available to cover all requirements
Combined with line management, job data is assigned to scan results
Flexible application possibilities in all areas of your production
Can be retrofitted to existing lines
Quality and process improvement through defect analysis
Integration in OAD
Technical Data
Glass
Functions
Free definition of different quality zones
Qualities definable per customer
Reliable detection of coating defects
Checking of frame spacing and muntin installation
Dimensional check (target/ actual comparison) in combination with precise mechanics
Glass type recognition
Archiving of scan data - statistics and analysis
One contact person for system and scanner
bit Scanmodule (LIS – Linear Image Sensor)

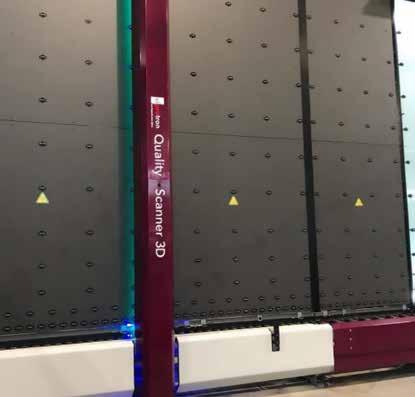

Individual setting options
Based on parameter and filter settings, perfectscan shows only relevant defects for quality assessment. The parameter settings and filter criteria can be adjusted by the operator at any time.
Flexible application in all areas of your production
Whether it is an insulating glass line, a tempering furnace or a laminated glass line, per fectscan can be used in any context and mounted within a very short time. The intelligent construction of the system allows you to ensure quality and efficiency quickly and easily in almost all areas of your production.

lis.analytics
Transparency in Production Based on Data
With the lis.analytics web application, it is easier to maintain an overview of a production facility consisting of a large number of machines and systems. How many units or what area was produced on all systems today? What was the product mix like today? Which alarms were triggered and how quickly were the problems resolved? These are the kinds of questions that we want and need to answer, for a day or for a single shift, for a single machine or an entire line. It's also vital to be in a position to compare the figures for a day or a shift so you can be sure that you are constantly improving. This is precisely where lis.analytics comes into its own – processing data from the machines so that targeted decisions can be made to improve production. This software currently offers two functional areas, Live Performance Monitoring and Productivity Analysis.
Live Performance Monitoring
With the help of Live Performance Monitoring, it is possible to visualize various data from production in real time – and this can be individually adapted.
Productivity Analysis
More in-depth analyses require not only data, but also key figures based on it, such as OEE (overall equipment effectiveness). With the OEE dashboard, LiSEC enables its customers to gain direct insight into where the greatest potential for improvement lies. The three components availability, performance and quality are considered individually.
Highlights
Customised dashboards for different purposes
Calculation of Overall Equipment Effectiveness (OEE) for machines and lines
Shift plan for comparing different shifts and calendar days
Analysis of the reasons for downtimes and alarms
Functions
Creation and management of customised dashboards for the real-time analysis of output, productivity, product mix, alarms, etc.
OEE dashboard with automatic categorisation of downtimes based on alarms
Calculation of key figures for machines and lines, shifts and calendar days
Detailed traceability of machine statuses
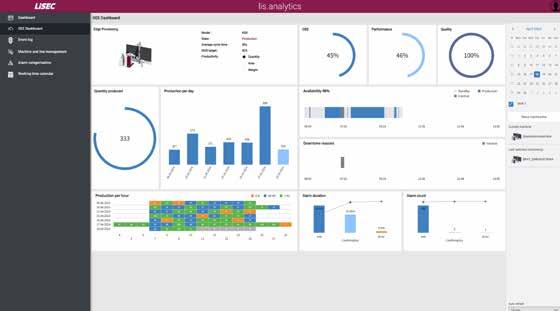
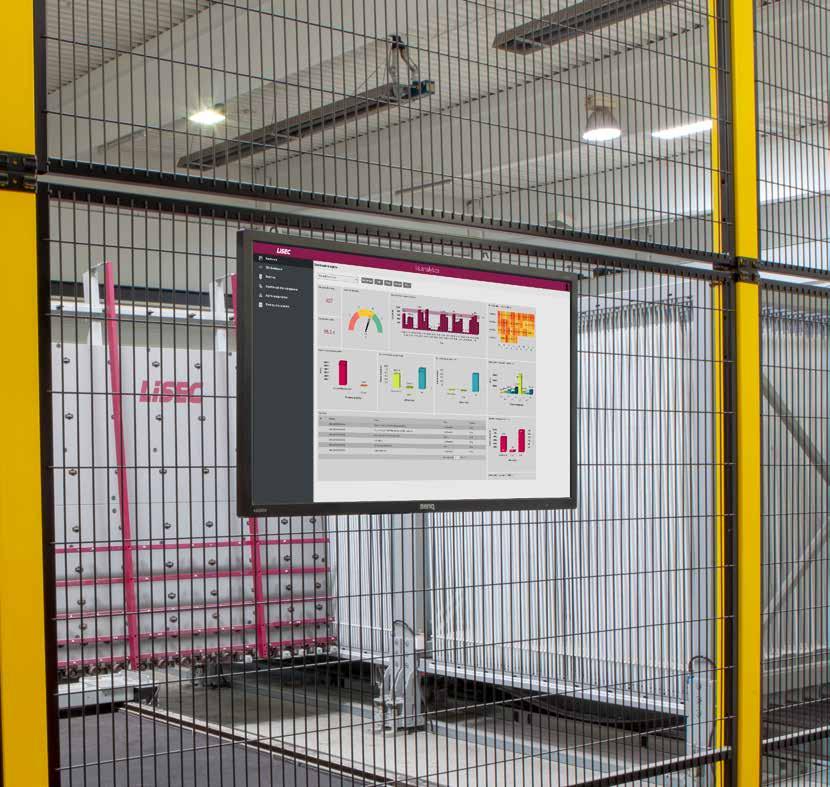
Visualisation of key output figures per machine
Based on the configurable shift plan, the respective output can be compared over several days and even on an hourly basis in order to derive appropriate measures.
Calculation of OEE for machines and lines
By combining several machines into lines, the OEE figure can be calculated not only for individual machines but also for entire lines.
Analysing the causes of problems (alarms, product mix, availability, ...)
If the output does not meet expectations, the causes can be found by analysing alarms that have occurred, the product mix or the reasons behind individual stoppages in more detail.

Information and ready messaging terminal at the production ident
The main function of ident is to inform the user within the production about relevant details resp. to register remakes and ready messages and transfer the information to the ERP system. The program also supplies work step specific information (e.g. shape position) and generates control codes for machines from third-party suppliers.
LiSEC.prdCtrl - mobile app for industrial scanners and smartphones in the production. This app offers useful functions that support the daily work on the shop floor. By simply scanning barcodes, ready and breakage messages can be triggered. The management of transport racks is also significantly simplified.
Extensions & Additional Products:

Highlights
Paperless production list
Ready messages to release capacities and actualization of the status e.g. for an order
Remake messages for fast post-produciton
Detail display for shapes and processings for error prevention
Higher flexibility through real time adaptation at production planning
Mobile app for production tracking and management of racks

Functions
Display of production drawings
Entry of rack number and stock location
Entry of remakes
Online connection to processing machines
Synchronising to other ident
Material management
Label printout (switching production / customer label)
Status display
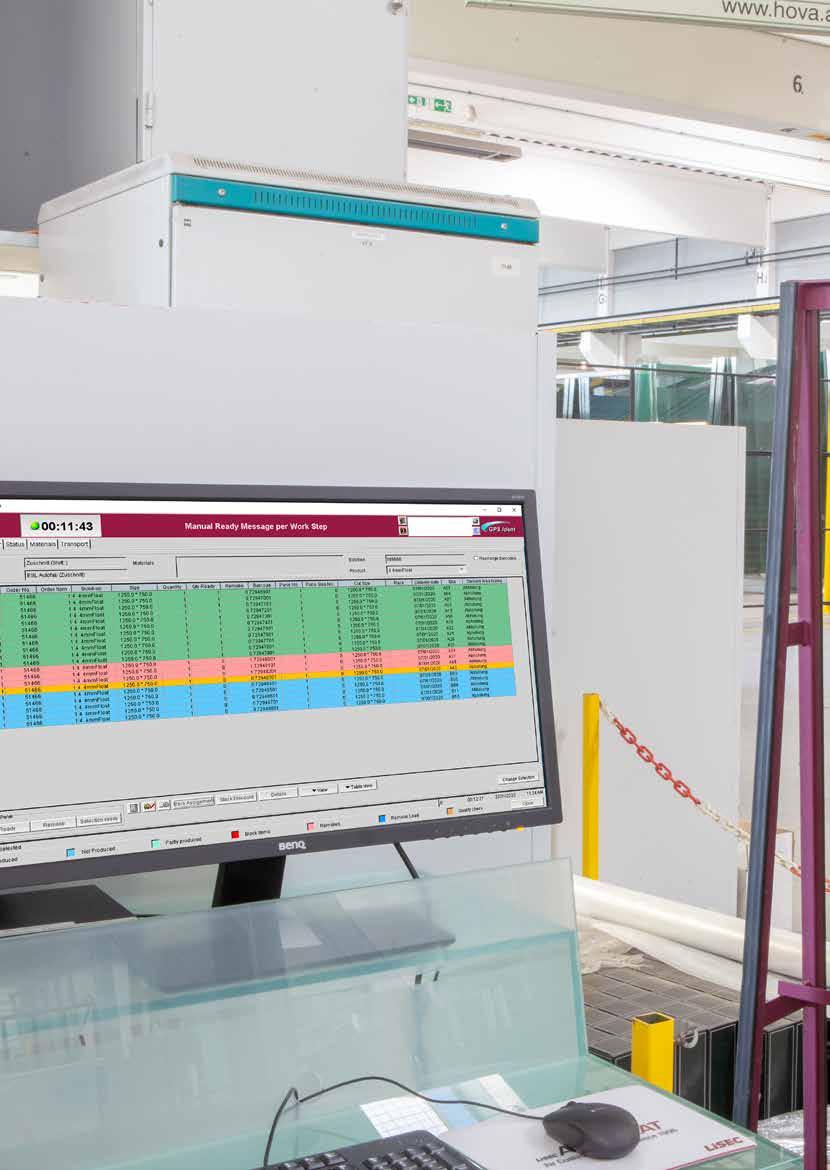
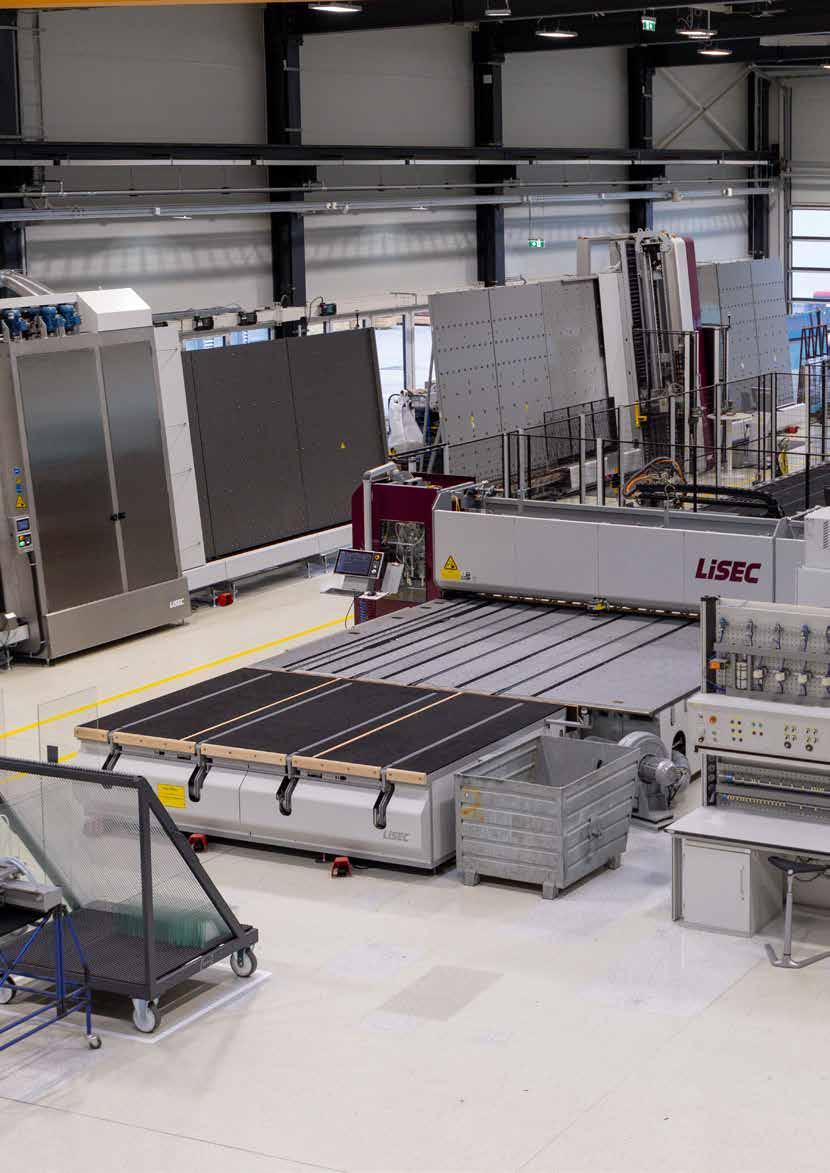

SERVICE
Machines and systems for flat glass processing are in use for many years, sometimes even for decades. Ongoing maintenance and optimisation are essential to keep performance, efficiency and availability at a consistently high level and to ensure high-quality glass products.
Services
We offer you worldwide service and the fastest possible supply of spare parts
From machine installations to modernization of existing systems, we offer a wide range of services, and stay on your side as a competent and reliable partner throughout the entire life cycle of your systems. Whether you need a customized training program, detailed machine inspections, online support, spare parts or upgrades – the LiSEC service team will take care of it for you.
Facts & figures
More 140 service engineers worldwide
Global network with local partners all over the world
Spare part deliveries worldwide within shortest time
Super-fast problem solving via remote service
Compentent technical consulting
Service Products
Machinery & Software Support
Service / Maintenance
Training
LONGLiFE
Spare parts
Installation
Repairs
Machinery & Software Support
SUN 22:00 – FRI 21:00 (CET) | Phone: +43-7477 405-5700
Machine support: tbe.service@lisec.com | E-Mail software support: support@lisec.com
Emergency contact for urgent issues outside our working hours: SAT 6:00 – 22:00 (CET) | SUN 6:00 – 22:00 (CET) | Phone: +43-7477 405-5700
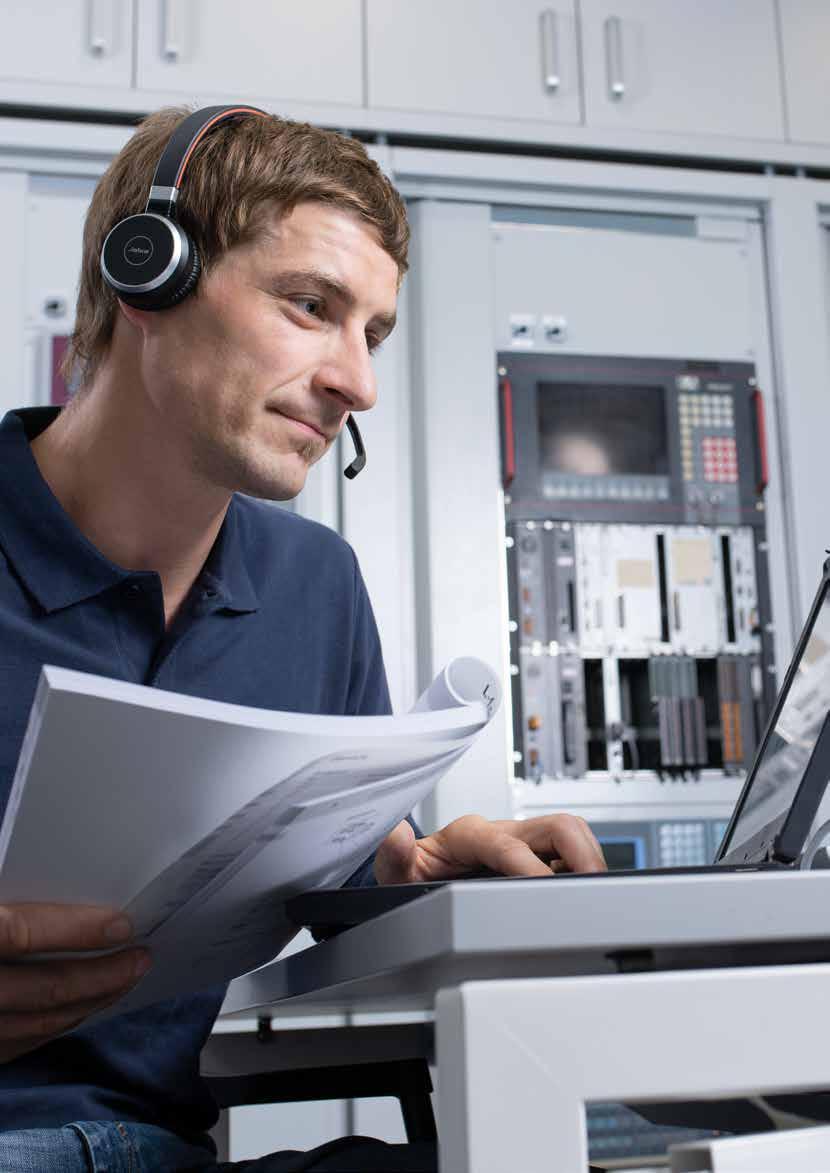
Training
Quality is our passion. Our goal is to qualify your employees to get the most out of your LiSEC equipment in your factory. Our team of experts looks forward to welcoming you to our top-equipped training center in Austria. Here you will have time to familiarize yourself with the operation and maintenance of LiSEC equipment, without the stress of production. Our experienced trainer team will support you with competence, advice and support. We train self-confident operators who work independently and quality-consciously and handle crisis situations with confidence. The knowledge acquired in the training in handling your LiSEC systems increases your productivity and product quality.
The advantages of a training programme
www.lisec.com/de/service/schulungen/
Full production output is more quickly achieved
Higher machine availability
Increased product quality
Increased skills of the operating personnel
Increased technological expertise of your employees
Increased employee motivation
Tel.: +43-7477 405-0
E-Mail: training.coordination@lisec.com
Good planning is key
The LiSEC training program includes many different machine and software training courses. Details of the training content can be found on our website at: www.lisec.com/service/training/
Service/Training
We offer personalized trainings for operators or maintenance personnel on request.

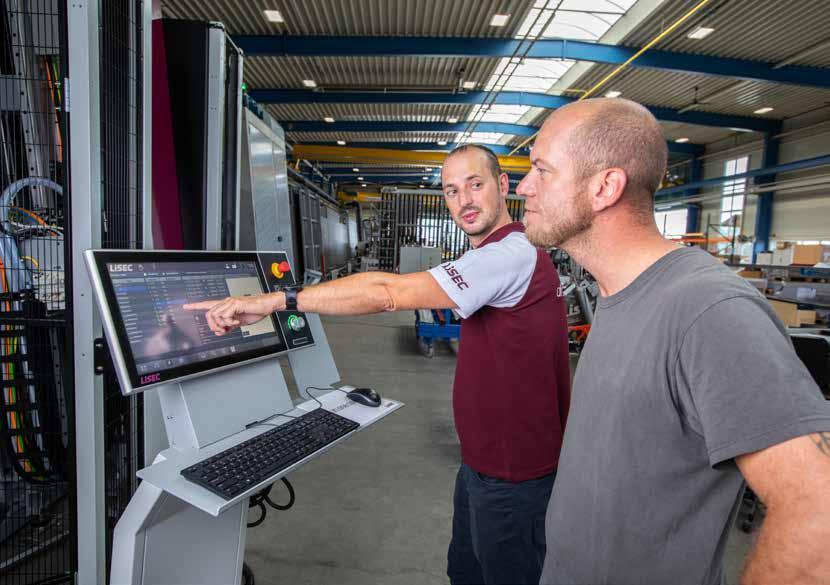