PREMIER GEAR


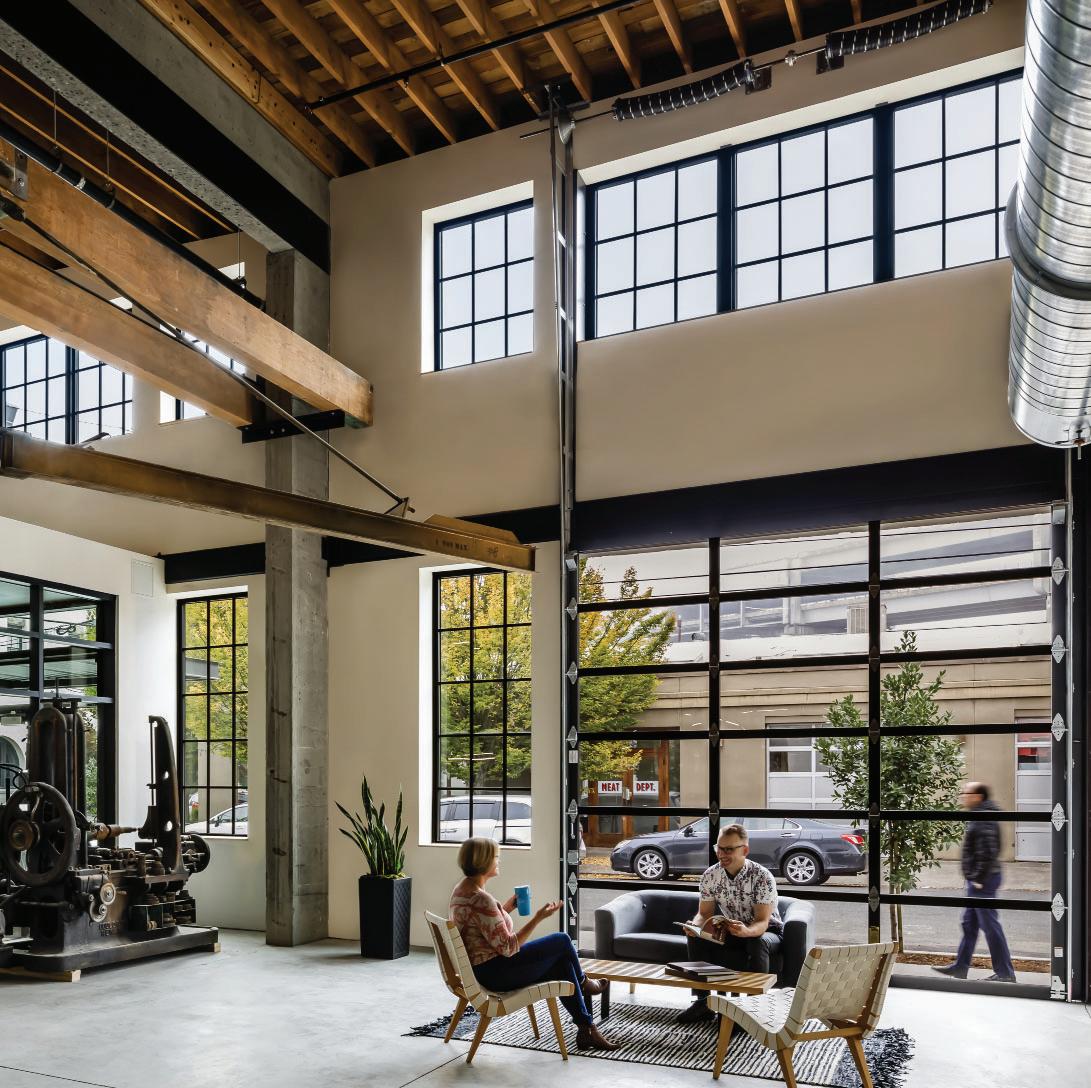
Premier Gear & Machine Works Building
After the property was successfully rezoned from Industrial to Commercial Mixed-Use, the building was in need of a complete interior and exterior renovation to be repositioned for multi-tenant leasing. Having worked with SDP on a number of development projects, LRS was asked to design Premier Gear for commercial office use, maximizing rentable area while maintaining the flexibility to include options for retail or restaurant. The project needed to include competitive features and amenities, allow for large event/gathering spaces, maintain connectivity between levels, and celebrate the historical character of the building.
The Premier Gear & Machine Works Building was purchased by Sturgeon Development Partners in 2017. Headquartered in Portland, SDP holds a robust local portfolio with numerous ground-up construction projects. Premier Gear is one of their first ventures into adaptive reuse.
CASE STUDY:
Three-dimensional thinking was key to balancing priorities of maximizing rental space yet maintaining openness and connectivity, as well as providing flexibility necessary for customizable tenant configurations and future adaptations.
PLANNING FOR THE FUTURE
FOCUS ON VOLUME
Key considerations and goals for Premier Gear were set to encompass the client’s priorities and position the building competitively in the market.
The original timber structure defined much of the character of the building and design of new structure focused on providing visual and material continuity.
APPROACH01
ILLUMINATING WITHIN Daylighting strategies, including expansive glazing, needed to be carefully considered to bring light to the depths of the full-block building and provide views and connection to the outdoors.
Incorporating a full seismic upgrade, core-shell change of use requirements, and carefully distributed egress routes supports flexible building usage and streamlined future development.
UNIQUE EXPERIENCE
Design intent focused on the experience of the occupants, especially visual layering and connectivity. Desirable community features, including generous atriums, were planned to maximize impact for both tenants and visitors.
TIMBER STRUCTURE

DISCOVER02
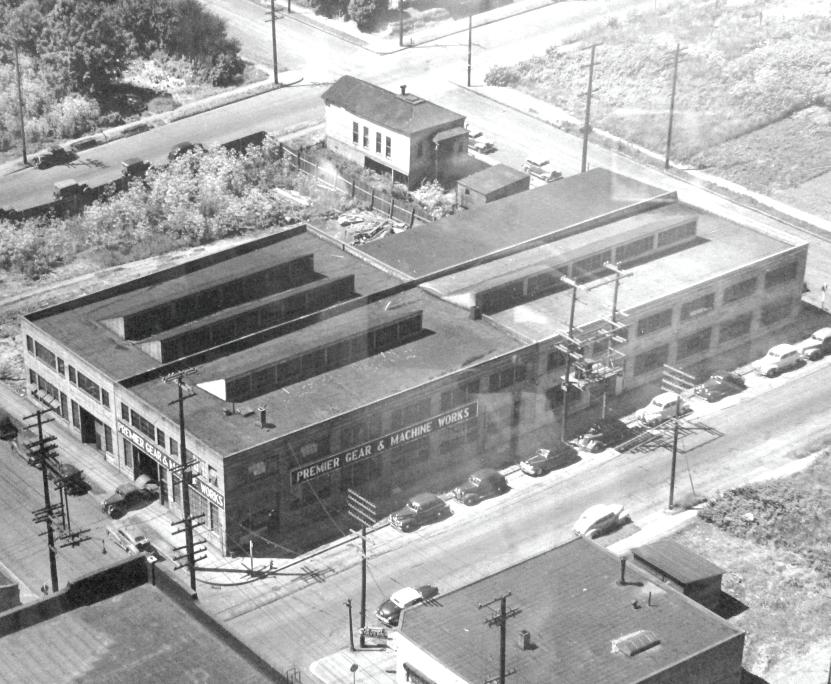
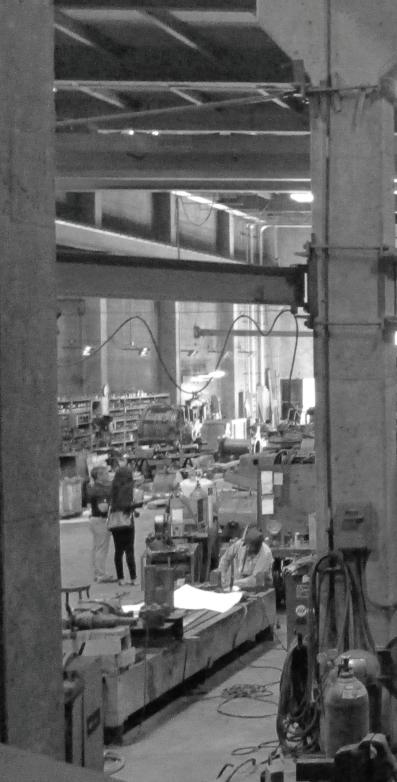
Premier Gear & Machine Works was founded in 1923 as a specialty shop for gears. This property was developed in phases from 1926 to 1970 as their office and industrial machine shop expanded. The building, originally occupying only 1/8 of the site, eventually grew to fill the entire city
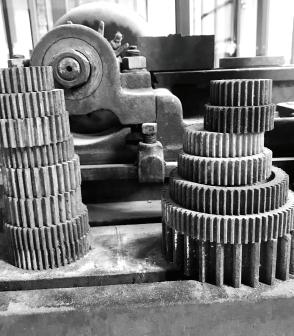
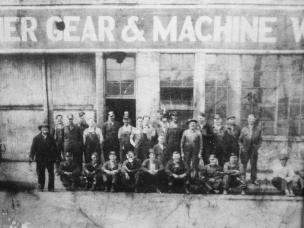
Premierblock.
Gear continued to operate their business here until they sold the facility to Sturgeon Development in 2017.
History

1923
ENTRY LOCATION


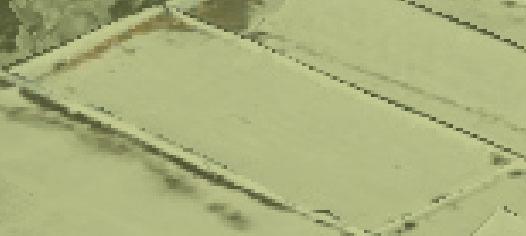
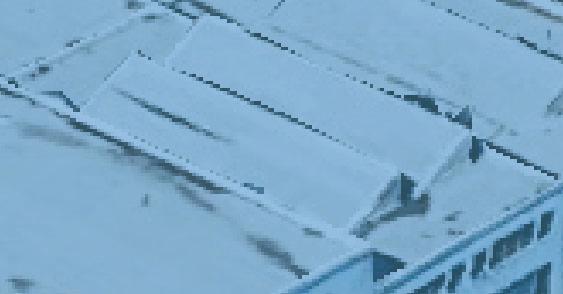
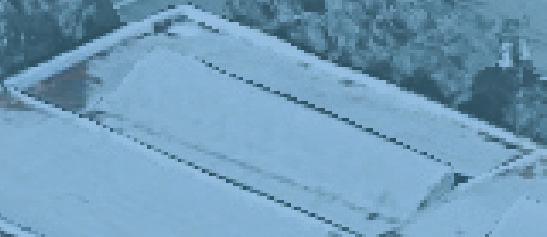
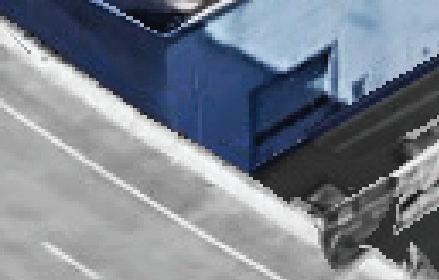
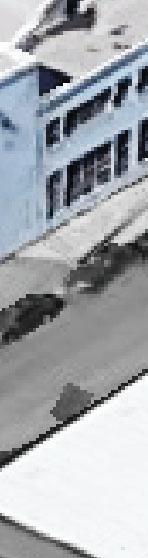
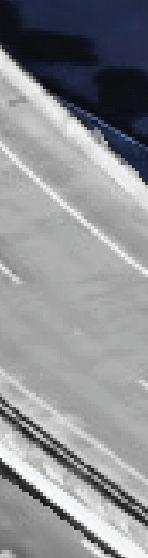
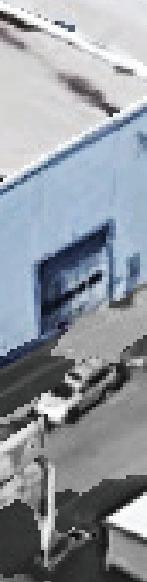
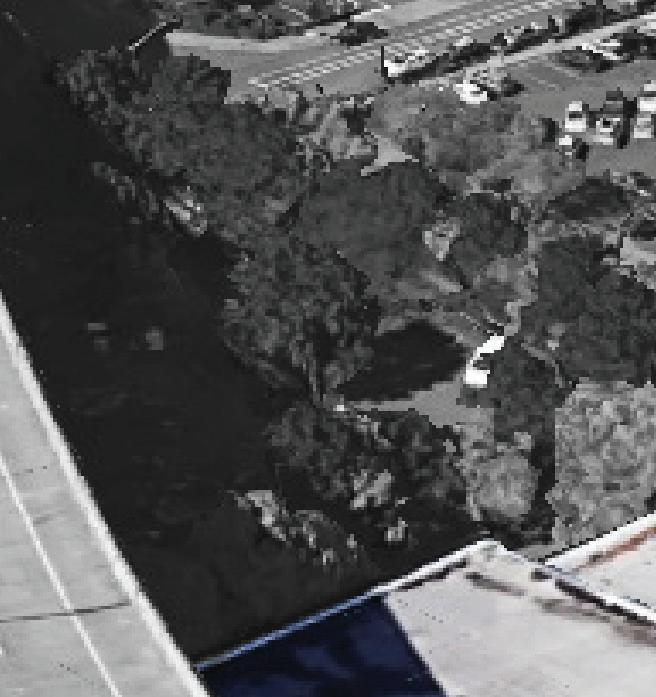
The NE corner of the building is the only area of the ground floor that is at grade and Thurman provides the viable commercial frontage for retail or restaurants.

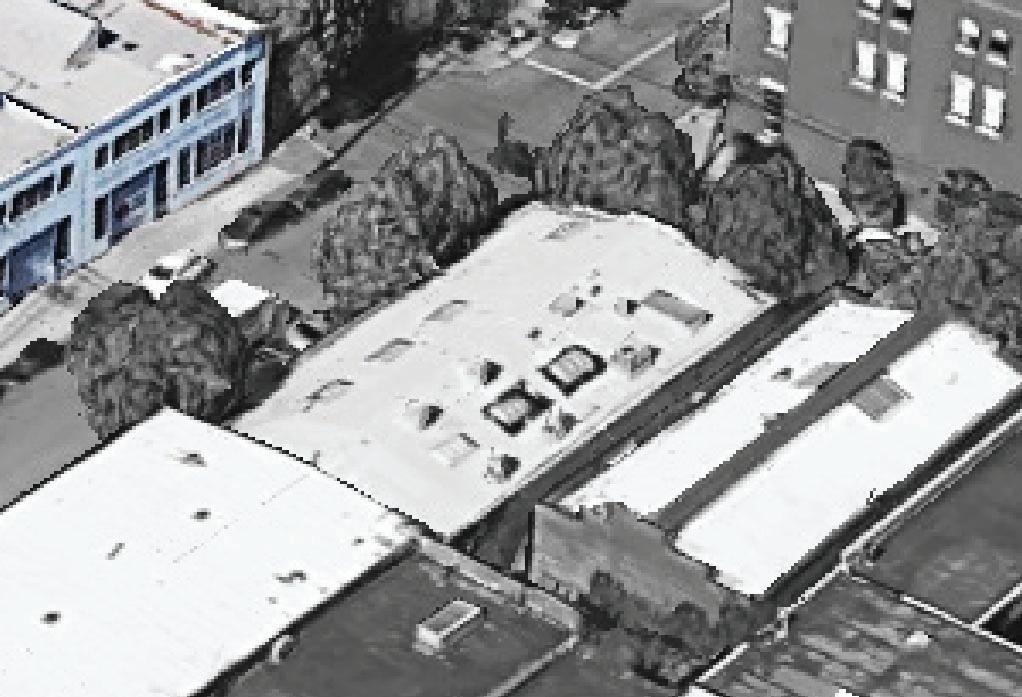
1970


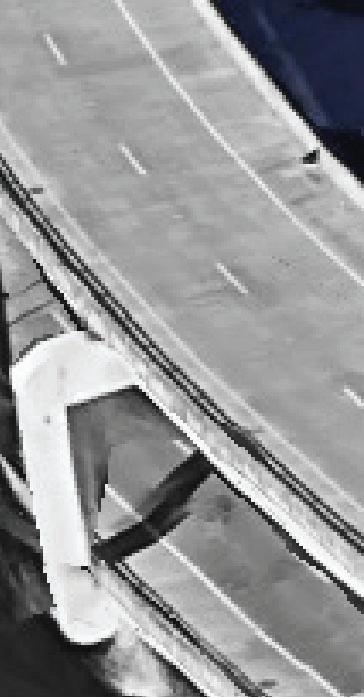
The south building was constructed with tilt-up concrete wall panels (with minimal openings) and a timber decking roof structure. The exterior loading area of the north building was also enclosed at this time.
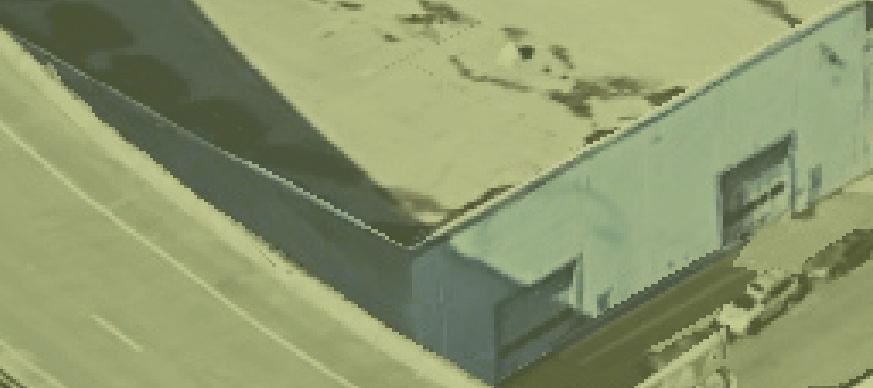

The building was expanded to the south and west by replicating the original design and construction.
1924-1930
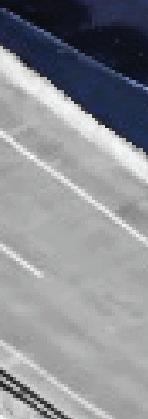
The original building was completed. Constructed of site-cast, board-formed concrete with heavy timber roof framing and interior wood columns.
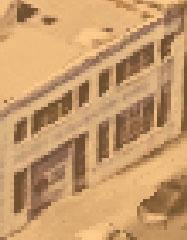

BUILDING USE Industrial EXISTING SIZE
LEVELS 1 plus Mezzanine
ADDRESS
1700 NW Thurman Street Portland, OR 97209
COMPLETED 1923, 1924-1930, 1970
Approx 39,000 SF
Site Assessment
Occupying a full NW Portland city block, the Premier Gear building is actually an amalgamation of structures compiled over almost 50 years. Each addition and remodel introduced new construction methods and materials. Accurately assessing the building was particularly challenging as there were very limited existing architectural drawings and Premier Gear continued to operate in the building throughout the design process. It was known that some level of seismic upgrade would be required. Also, due to long-term industrial use, the majority of the building floor slabs were deteriorated and required remediation. As is typical in adaptive reuse projects, flexibility in approach would be needed. It was clear that the building had solid bones and a vast interior space opportune for adaptation to amazing creative office spaces.
DESIGN03


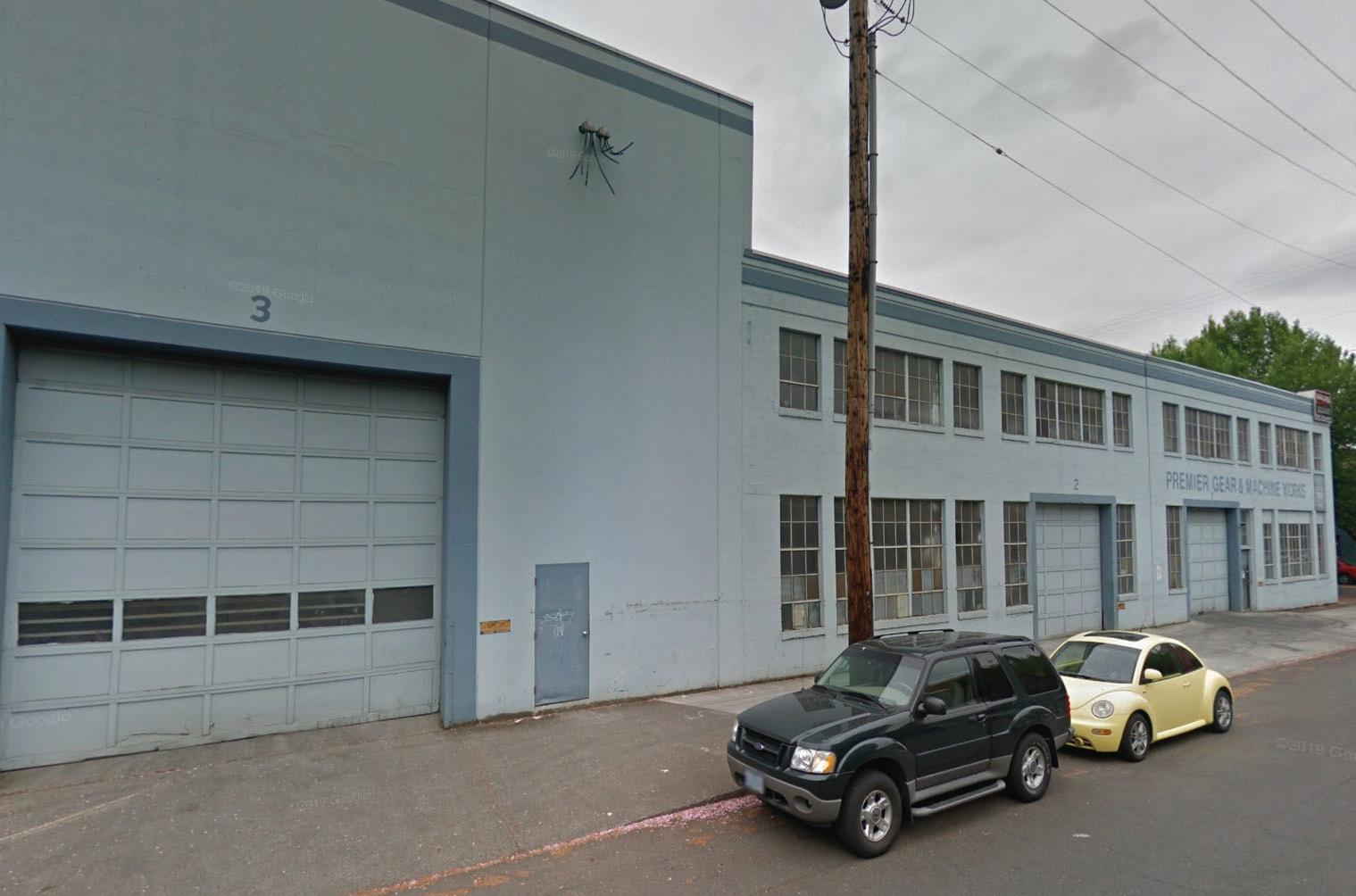
The LRS design team created new window openings for the south building that continue the pattern and elevational alignment of the north building to unify the overall facade along the street frontages. A new third tier of windows were added at the south building to celebrate the greater height and maximize daylight into the interior. Existing vehicle openings were repurposed with glazed overhead doors to create exterior connections. In order to provide desired outdoor amenity space, designers carved out a major area of the east facade to create an exterior patio on the second floor, recessed within the building footprint.
Facade/Elevations

The Premier Gear building’s phased, organic growth resulted in two structure heights with very different facade rhythms and patterns. The north part of the building was highly-punctured whereas the southern portion was a black-box with few utilitarian openings. Creating an aesthetic cohesion between structures built 50 years apart would require creative solutions.
SOLUTIONS
CHALLENGES
The building face is on the property line on all frontages so options are limited for vehicular access, openings and recesses for doorways, aligning floor elevations with exterior grade, and getting light into deeper interior spaces.
DESIGN STUDIES
In exploring options for new windows and an exterior patio, designers considered composition, scale, voids versus positive space, shadows and daylighting. The human experience was considered in every possibility, both from the perspective of the occupants inside and those viewing the building from the street.
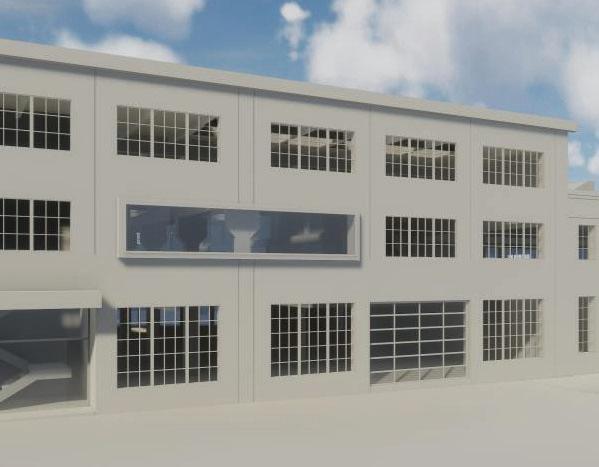
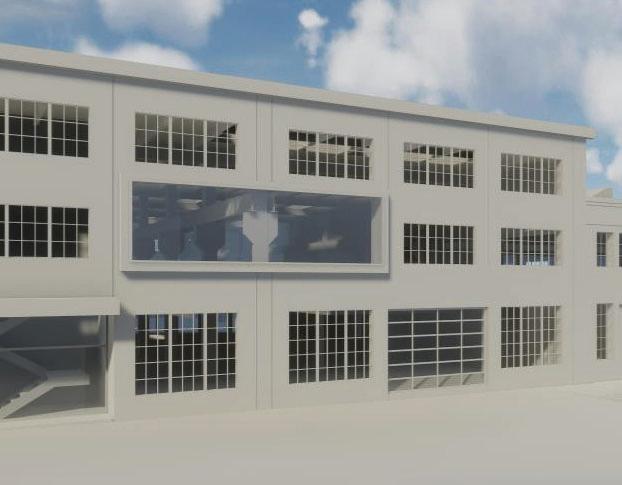
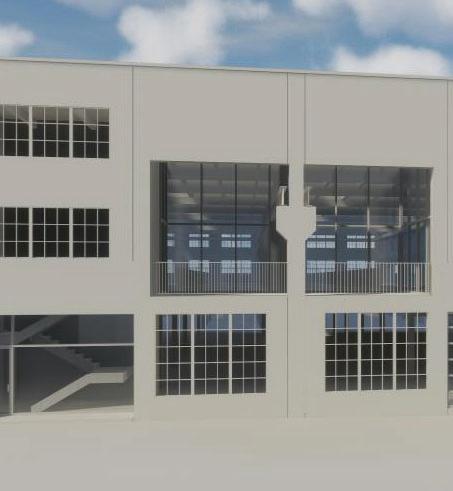
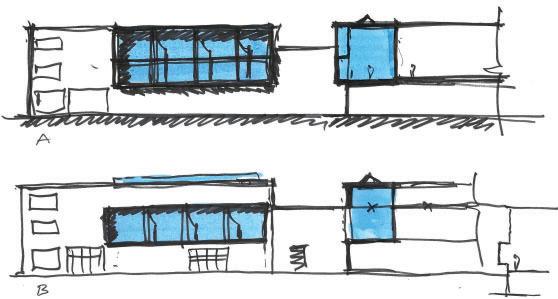
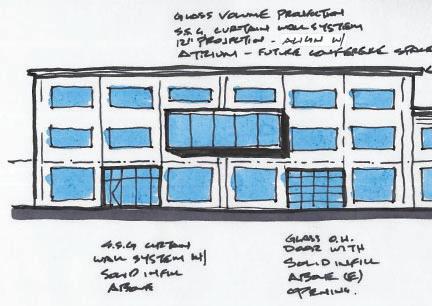
RENDERED OPTIONS
Rendered images illustrated the progression of the discussion exploring competing priorities for rentable square footage, interior connectivity and access, and exterior visual impact and presence.
The final design for the patio features a high opening to align with existing windows and bring in maximum daylight. The design preserves a unique existing central column and steel crane rail providing visual impact from the street and continuity between the interior and exterior space.
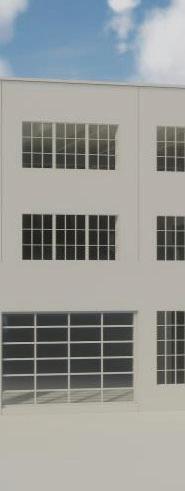
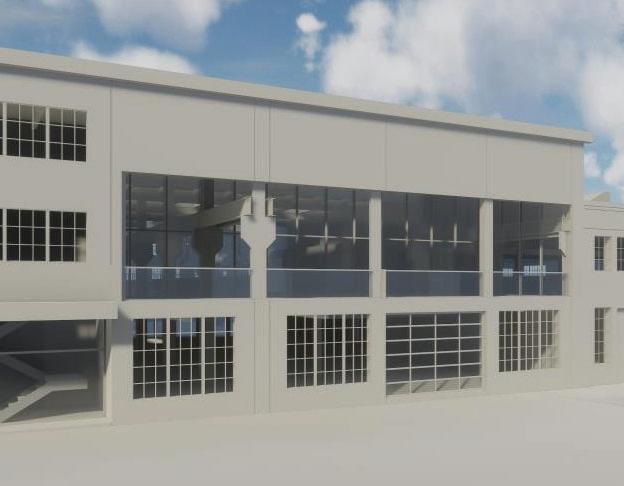
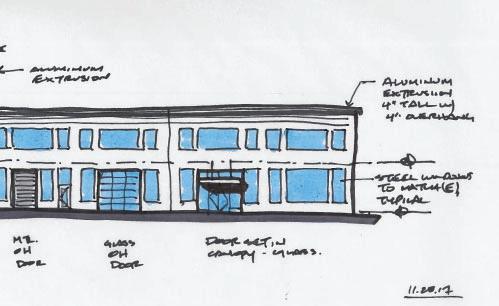
PATIO FINAL DESIGN
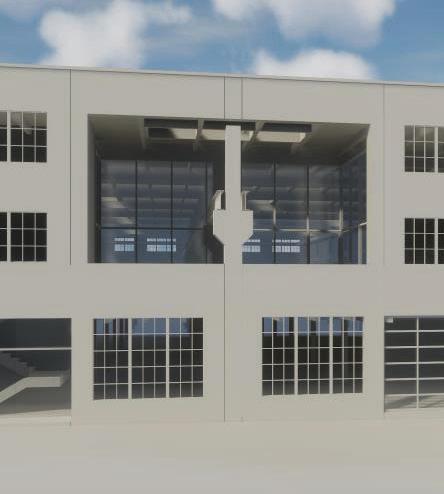
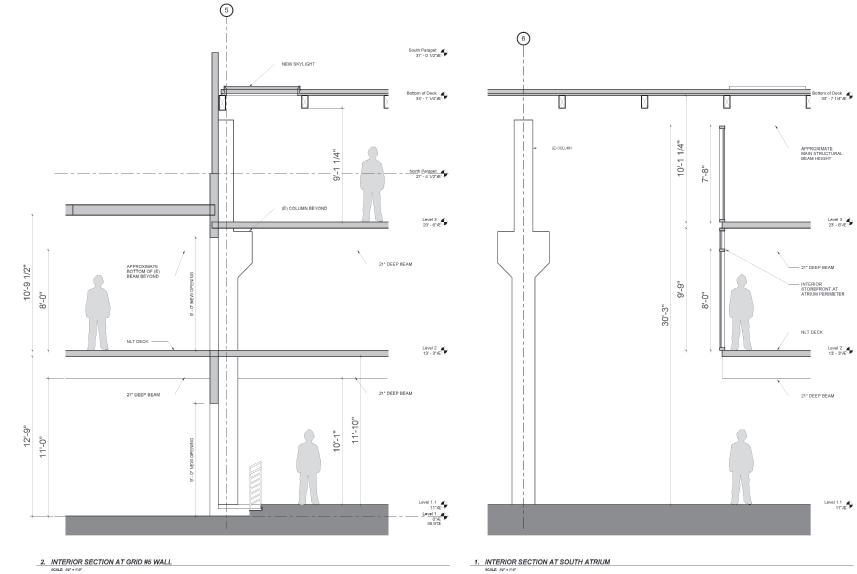
CHALLENGES
To maximize the available project square footage, designers knew they needed to create a second level for the entire building, and also studied the possibility of a third level for the southern portion. The existing mezzanine was not salvageable but even with a clean slate, there were no clear ideal floor heights due to the differing volumes and structural modules. Areas of the building were constructed using dramatically different historical framing methods, and the north portion was especially difficult due to the massive timber beams resting about 21 feet above the existing slab.
Although a partial third level was tempting, the lower ceilings didn’t uphold the vision for the project so the team agreed to prioritize the quality of the space over the square footage. It was also agreed that better connectivity would be achieved by setting the second floor at a consistent elevation through the entire building. This approach, along with the removal of large portions of the concrete dividing wall, increased the “perceived space” by providing continuous flow, improved circulation, and an open visual expanse. It also served to make the space more attractive to tenants wanting to occupy the entire level.
SOLUTIONS
Considerations for flexibility of the space were further hampered by a first floor that changed elevations and a solid concrete wall dividing the building.
Interior Architecture
1ST LEVEL
The entry level maintained the existing split elevation, providing a connective ramp at the central amenity zone. A large, full-height lobby provides an impactful entry; restrooms, shower, bike room, and storage and trash areas are centralized for easy access and demising flexibility.
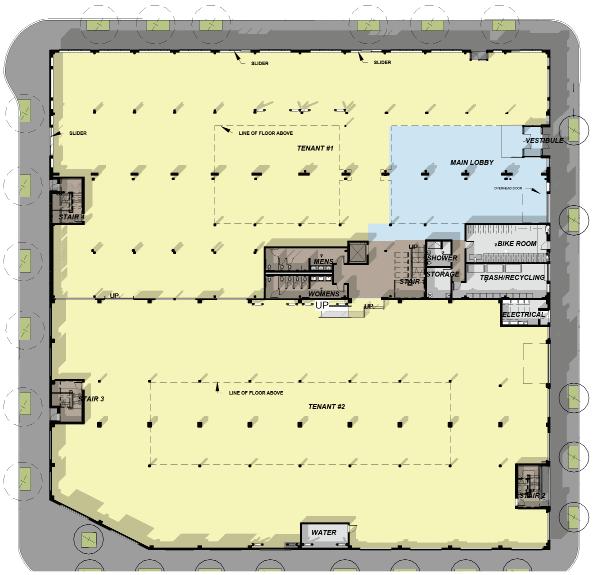
2ND LEVEL
For flexibility in tenant configurations, the concrete wall between the north and south portions of the space is punctured to the maximum extent possible and egress is provided via four distributed stairways. This level also features large skylights that bring daylight into the deepest interior areas of the building and an outdoor patio amenity space.
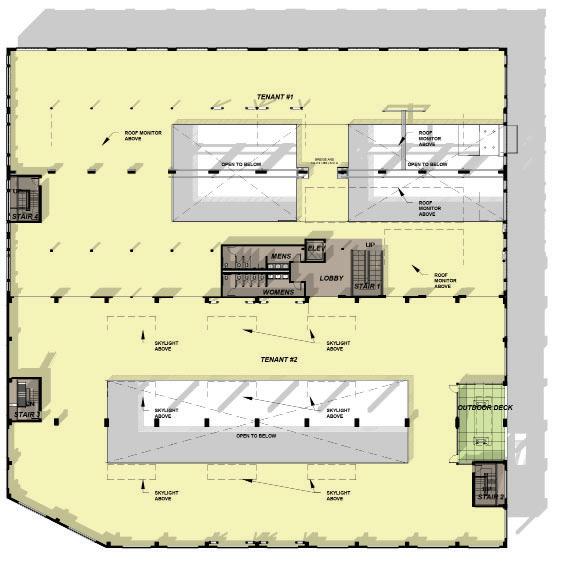
STRUCTURE & SYSTEMS
ENTRY
Removed concrete “beam” heads allow visibility from one side of the atrium to the other. This, and creative planning, also enabled HVAC and sprinkler runs to cover the building in discrete locations. Reinforcing of concrete openings was required due to lack of existing rebar.
A spacious atrium space creates a welcoming entry. Designers imagined a flexible space that would be ideal for events and could provide extra amenities such as a coffee bar, meeting areas and co-working space.

Large openings in the second level create double-height atriums that provide connectivity and activation between levels, and bring needed daylight to the lower interior.
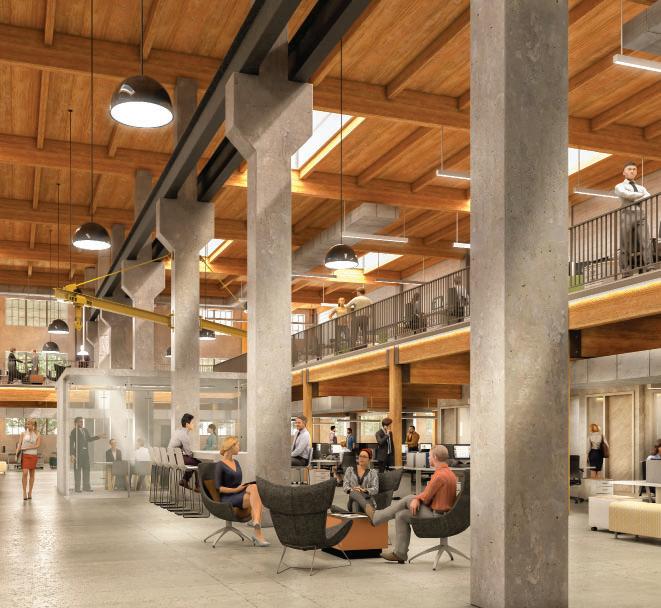
ATRIUMS
Exposed structure and salvaged machinery provide the vintage industrial vibe highly desirable in this district
PRESERVATION
This outdoor space, carved out of the building, provides a highly desired amenity space, connects the interior to the outdoors, and provides a bit of nature in the city, as well as coveted views toward the Willamette River and iconic Fremont Bridge.
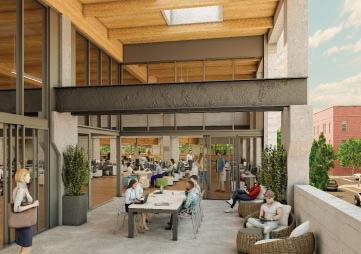
EXTERIOR PATIO
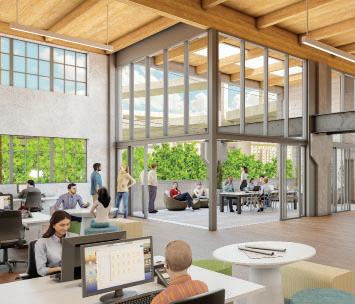
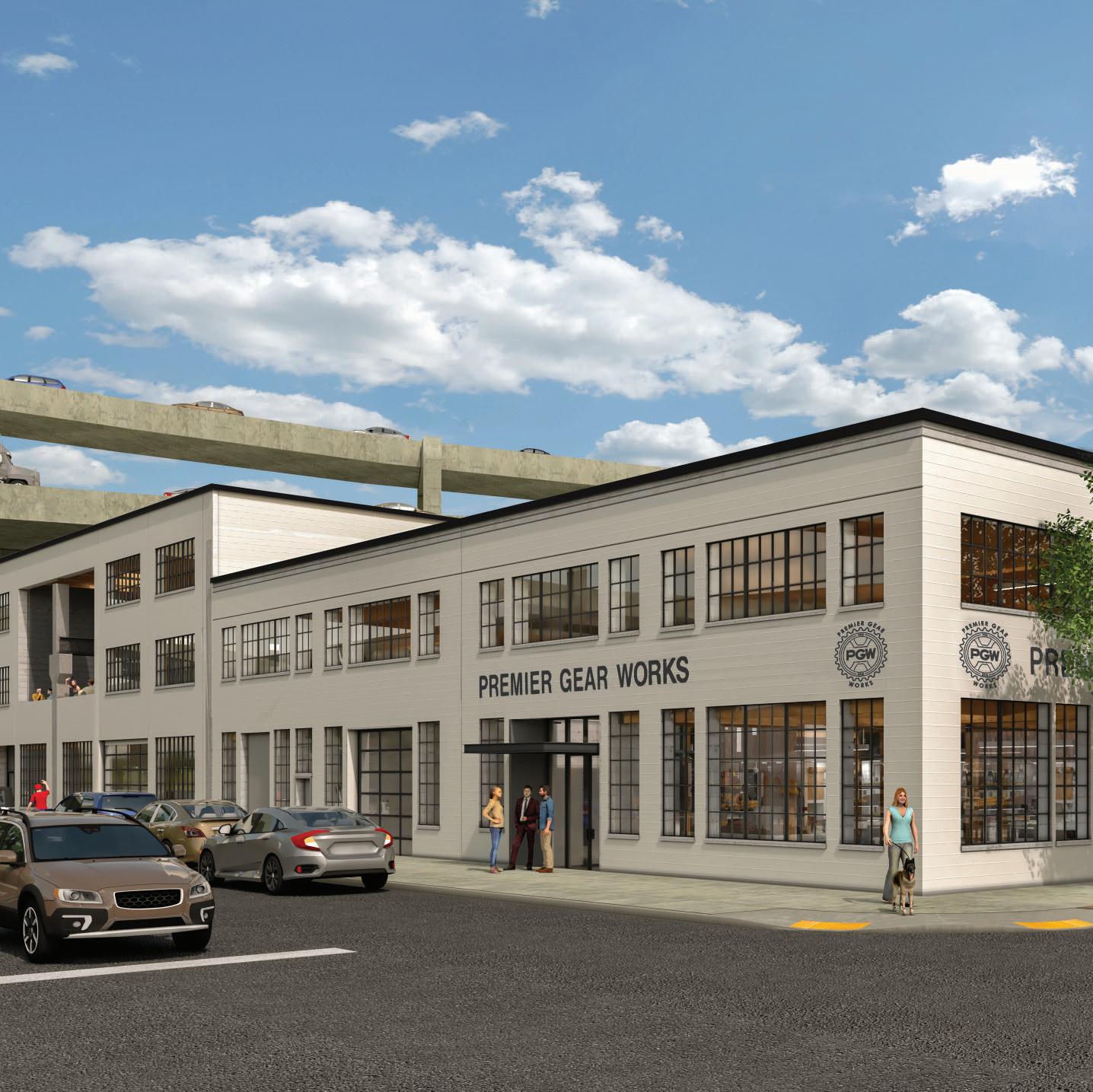
Imagining the future occupants of the Premier Gear building, the LRS team sought to provide them with a space that would inspire thoughts of “What a beautiful, truly Portland space”, and “Such a transformation, it’s amazing this was once a machine shop.”
Design Vision
The design of the exterior successfully marries the disparate structures to create a unified, balanced street view Composition and detailing honor the buildings roots and context.
Inside the building, the history and character of the original structures and industrial roots are exposed and celebrated. New interior elements are kept simple, clean, and contemporary; the monochromatic hues create a backdrop to accent exposed timber and safety-yellow salvaged machinery.

DELIVER04 Construction Administration
The Premier Gear building revealed it’s share of surprises during demolition and construction. Floor slabs showed extensive deterioration, significant uneven patches, and many areas were completely saturated through with oil. Removal of walls disclosed that columns were mis-located, missing, or did not extend full-height to structure. Concrete walls lacked rebar necessary for structural integrity. Walls that were intended to be removed divulged hidden structure supporting major roof areas. Cast concrete window sills crumbled from years of water infiltration.
SOLUTIONS
Each new discovery required the project team to collaboratively determine a method for proceeding. Studying the conditions onsite, together with the contractor and owner, anticipated details were revised and new ones created to maintain (or improve) the design.
1715 NW 17th Avenue Portland,
PROJECT TYPE Adaptive CommercialReuse,Of fice SIZE 68,646 SF LEVELS 2 COMPLETION September, 2020
ADDRESS OR 97209
Plans were adjusted and new structural elements were integrated. For the entire first floor, a topping slab was coordinated with an added hydro-carbon resistant vapor barrier. Steel channels were used to provide structure for concrete openings, and window sills were removed and replaced with custom concrete sills to match the originals.
CHALLENGES

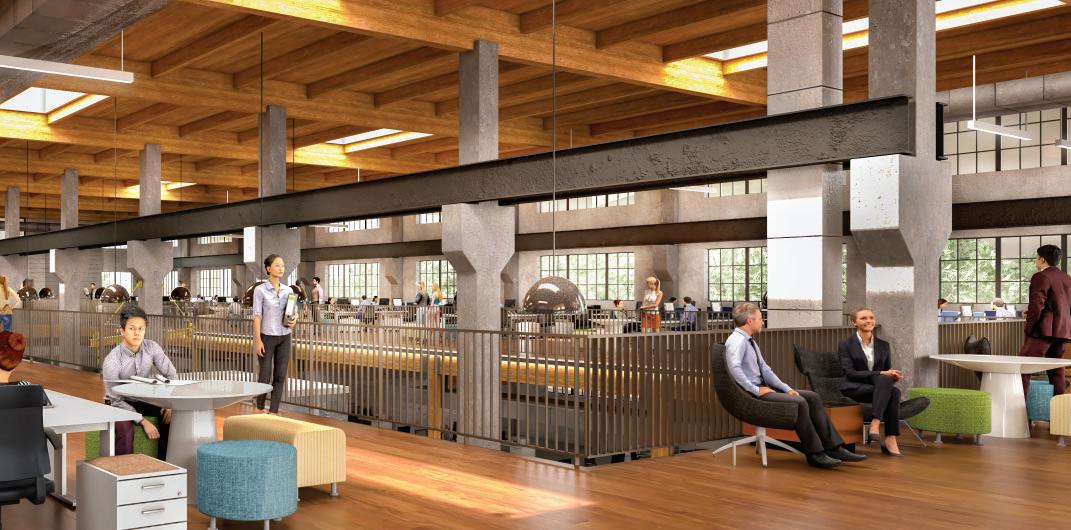
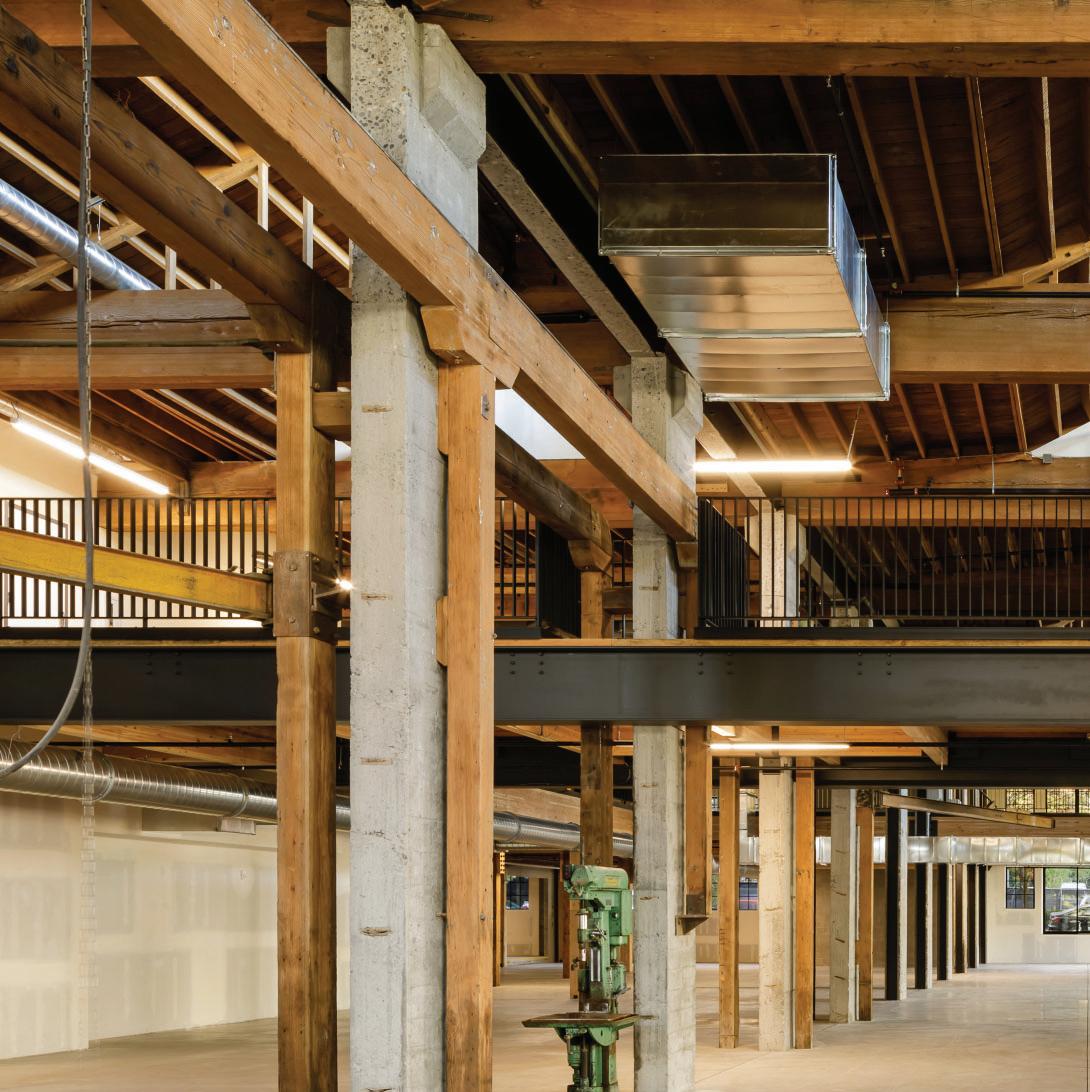
The beauty of adaptive reuse projects arises from onsite challenges that generate unexpected and innovative design. In this project, a bridge was created at the second level spanning the atrium in the north section. Framed from salvaged steel crane rails, the bridge features a void at it’s midspan for a preserved crane rail column to slip through to it’s first floor supports.
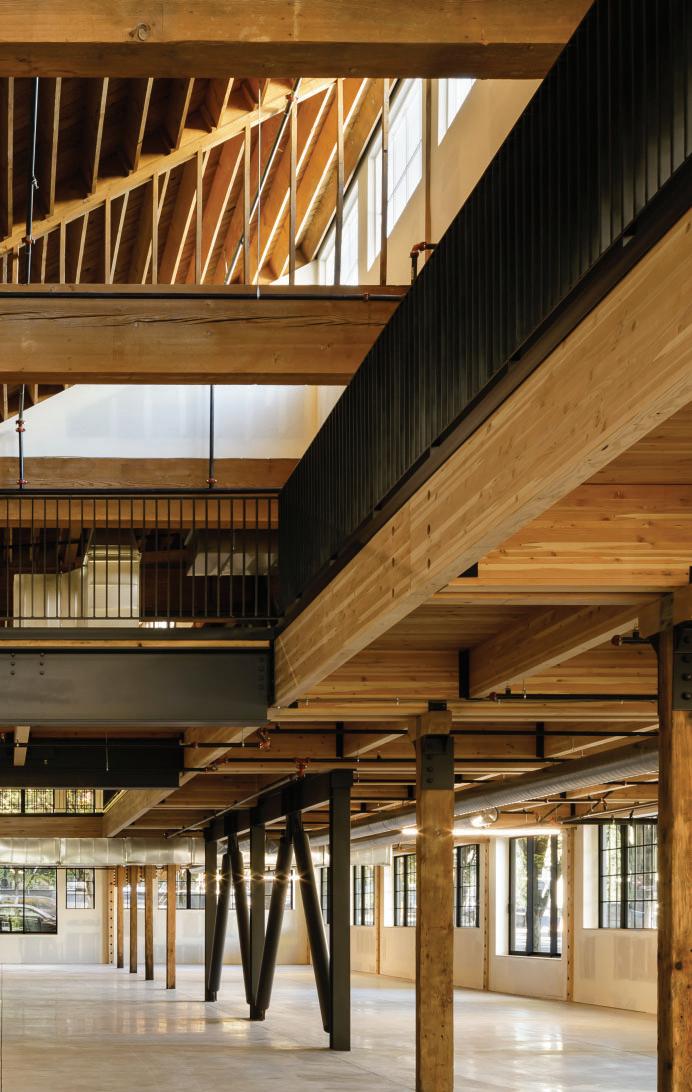
SUCCESSES
In the south portion of the building the preserved crane rails are unique accents that can be seen from the street, running from the terrace into the building and beyond. Vintage gears, left on site by the owner, were used to infill a challenging railing termination creating an original industrial art installation.
–VANESSA STURGEON, FOUNDER OF STURGEON DEVELOPMENT PARTNERS
“The Premier Gear project was especially exciting in that it was challenging to marry the old with the new in a way that was authentic, functional and beautiful. We are so proud of this project!”

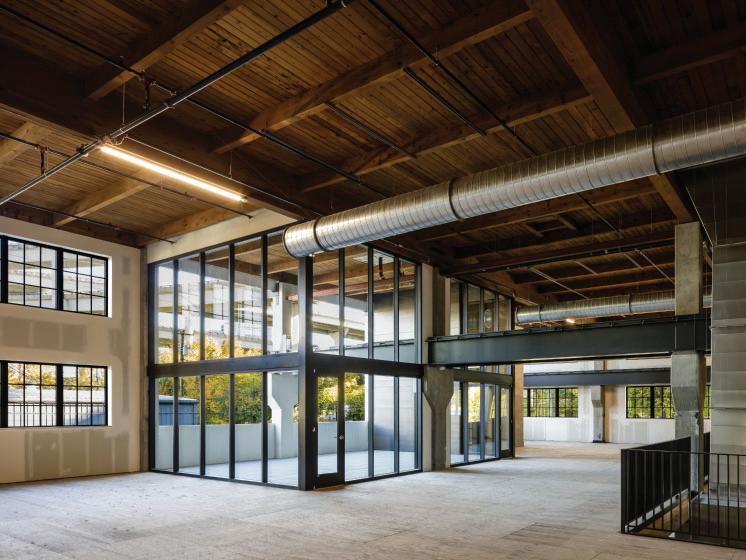


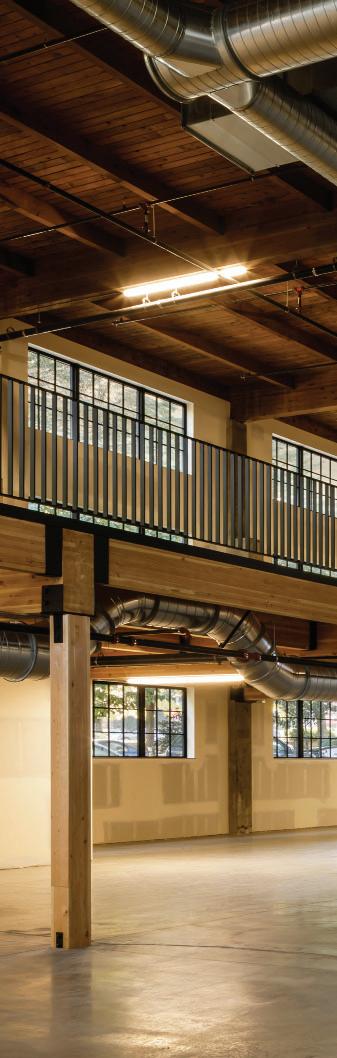

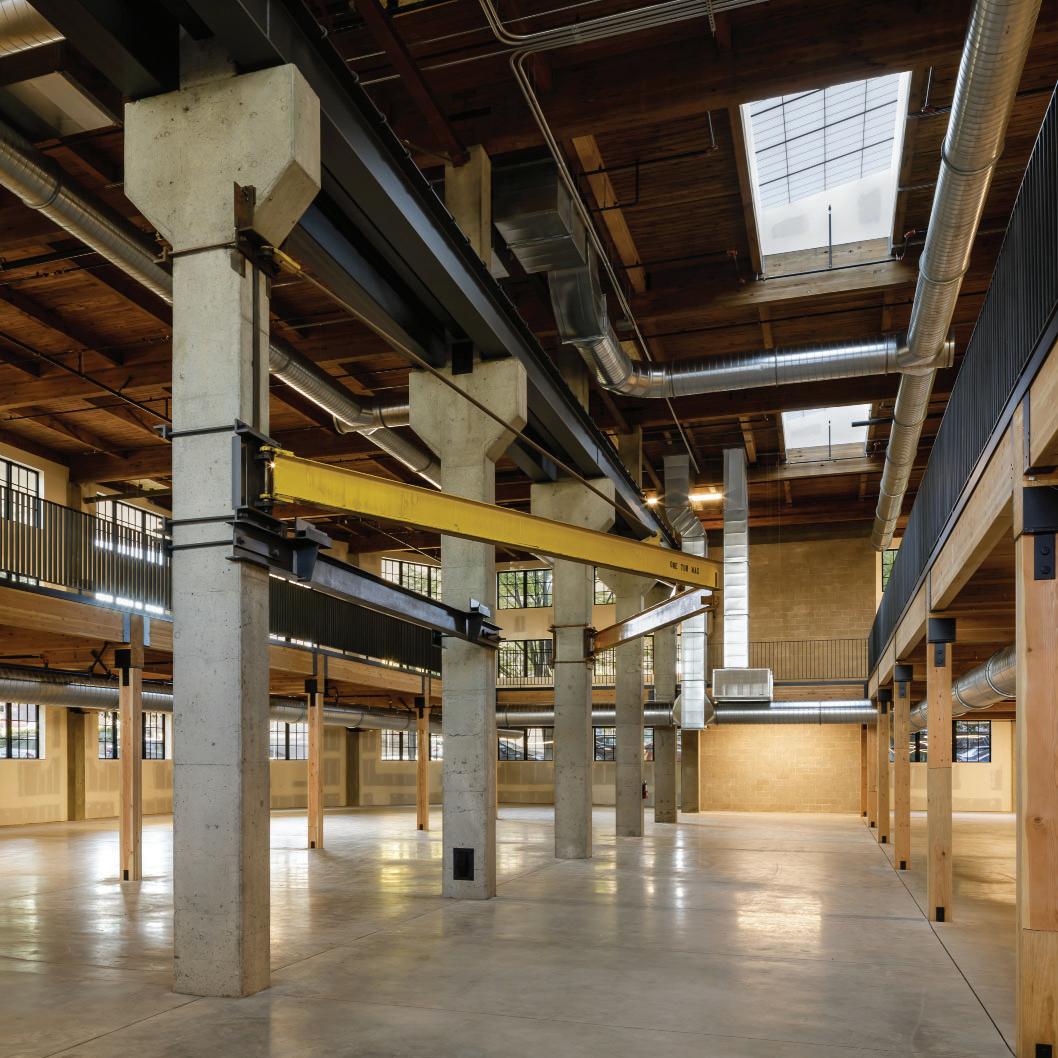
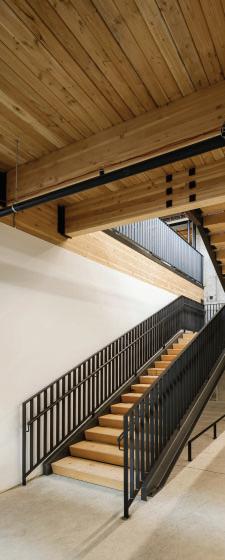
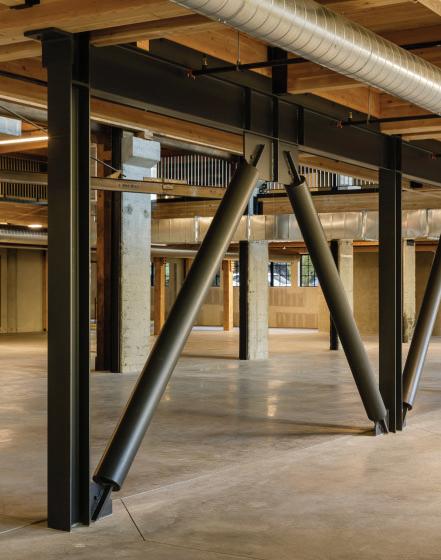
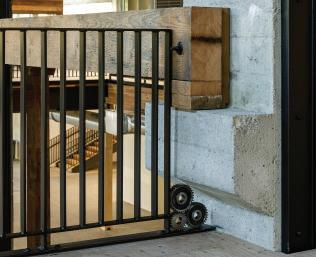
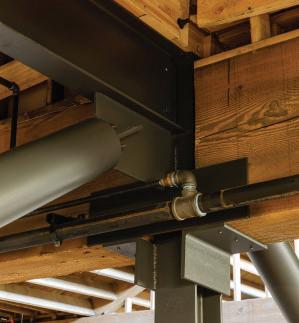
“The Premier Gear project was a fantastic opportunity to focus on space, experience, simplicity and quality. We wanted users to be able to connect to the outdoors at all times while maintaining a sense of the history of the place, relative to feel, scale, and materials.”
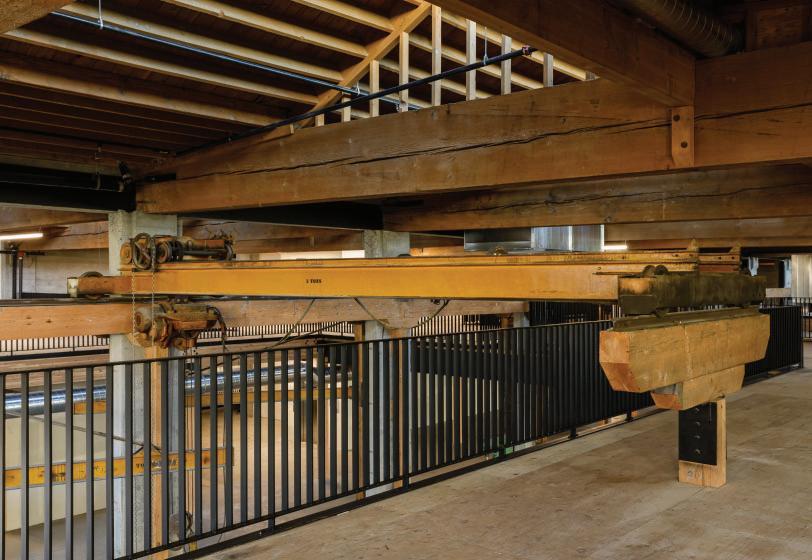
–JULIO ROCHA, SENIOR ASSOCIATE AND LEAD DESIGNER, LRS ARCHITECTS
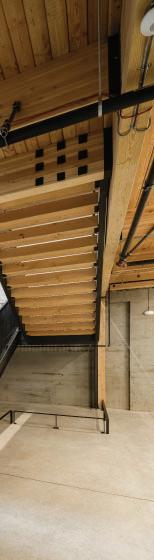
Driven by a passion for good design and supported by endless curiosity, LRS is a forward-thinking architecture and interiors firm offering creative solutions and transformative spaces. Our diverse portfolio of work highlights our commitment to shaping the human experience through the physical environment.
A single principle encompasses all we do: design with integrity. We are your honest project partners. We design sustainably, planning vibrant communities and building structures to stand the test of time. Wellbeing is our top priority because great design goes beyond aesthetics. Our balanced, holistic approach fuses function and beauty to create meaningful places for people.
ABOUT US

1777 SW CHANDLER AVENUE • SUITE 270 BEND, OREGON 97702 • 541.668.9550 720 NW DAVIS STREET • SUITE 300 PORTLAND, OREGON 97209 • WWW.LRSARCHITECTS.COM503.221.1121
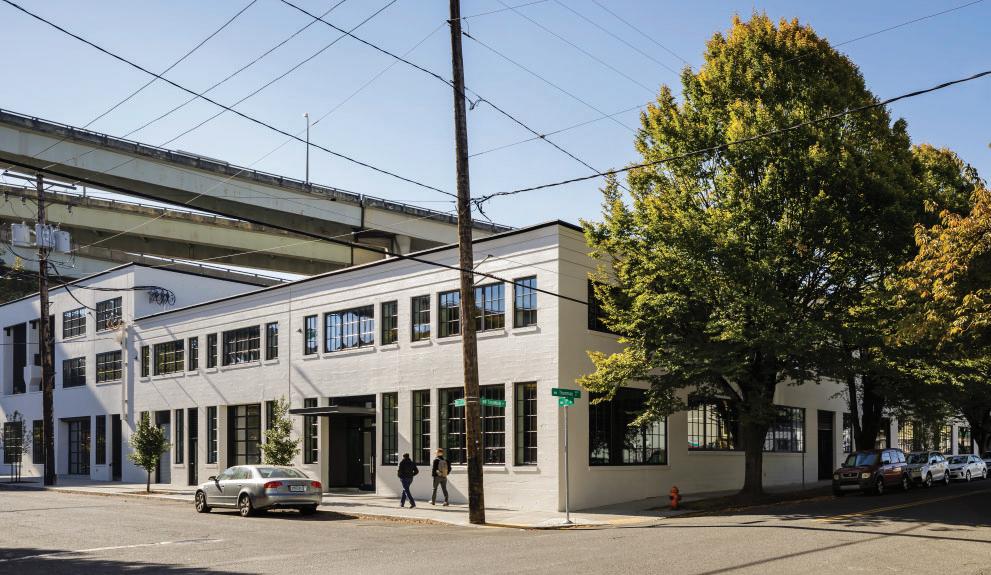