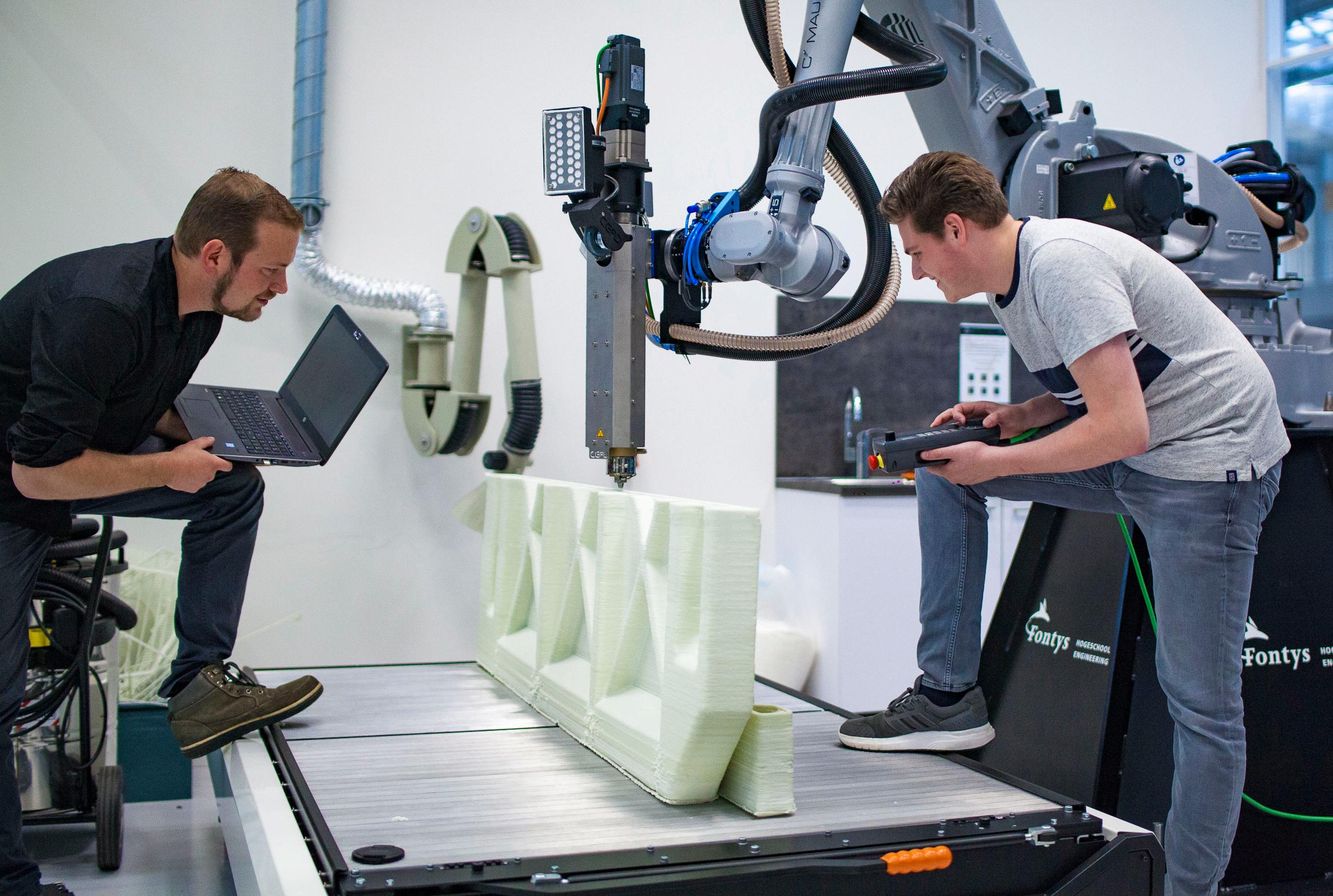
4 minute read
Fontys neemt CEAD AM Flexbot in gebruik
3D robot printen samen met de maakindustrie
Fontys Hogescholen heeft op de Brainport Industries Campus (BIC) een AM Flexbot robotprinter van CEAD in gebruik genomen, inclusief een f reeskop voor het nabewerken van grote werkstukken. Dit najaar wil Fontys samen met bedrijven de eerste onderzoeksprojecten starten.
Advertisement
Na de impuls voor het 3D metaalprinten, nu met een Renishaw RenAM 500S, bouwt het Objexlab van Fontys Hogescholen ook de positie in het 3D printen met kunststoffen en composieten verder uit. De AM Flexbot neemt hierin een prominente positie in. Werktuigbouwkunde wil binnen het onderzoek meer aandacht geven aan lichtgewicht constructies en kiest daarom voor de AM Flexbot van CEAD. “Met deze printer versterken we het AM-onderzoek en geven het onderzoek aan lichtgewicht constructies een stimulans. Als de belangstelling en de groei van het onderzoek aan lichtgewicht constructies doorzet in het komende jaar, zou het een eigen onderzoeksgebied kunnen worden”, zegt Joris Glaser, docent/onderzoeker bij Fontys Hogescholen.
Zelfde materiaal als spuitgieten
Met deze robotprinter kan het team onderdelen tot 1,8 meter hoogte printen. De tafel waarop de AM Flexbot print, meet 1,2 bij 2,0 meter. De stukken worden geprint met granulaat dat in de extruder van de 3D printer gesmolten wordt. “We printen nu met hetzelfde materiaal als veel spuitgietmachines doen”, zegt Joris Glaser. Als docent/onderzoeker coördineert hij de activiteiten rond de robotprinter bij Fontys. Omdat een deel van een belangrijk onderzoek zich richt op de materiaalkant, werkt de opleiding Werktuigbouwkunde er samen met Technische Natuurkunde, die zich met materiaalontwikkeling bezighoudt. “We kunnen zo nieuwe granulaten ontwikkelen en hun eigenschappen verbeteren.”

Joris Glaser (links) samen met Mike Braat bij de CEAD AM Flexbot in het Objexlab. Een van de proefstukken is een deel van een frame van 1,8 m lengte. De printtijd van het onderdeel bedraagt 8 uur. Het gevuld PP heeft een treksterkte van 91 Mpa.
Geprint frame
De voorbije maanden zijn Joris Glaser en Mike Braat, die onlangs is afgestudeerd op een onderzoek naar het produceren van hybride productiemallen met behulp van additive manufacturing, vooral bezig geweest met het leren 3D printen met de robotprinter en het onderzoeken van de materiaaleigenschappen. Het grootste stuk dat ze tot nog toe hebben geprint, is een 1,8 meter lang frame, met een hoogte van een meter en wanddiktes tot 6 millimeter. Dit is geprint in polypropyleen (PP) dat voor 30% gevuld is met glasvezels. Joris Glaser: “We hebben de afgelopen maanden gebruikt om ervaring op te doen. Het proces kunnen controleren is bij deze 3D printer van groot belang.” Het formaat van het werkstuk vergt extra aandacht om warping en andere ongewenste effecten te voorkomen. Om op dit vlak stappen te zetten, gaat het team de AM Flexbot dit najaar aansturen vanuit Siemens NX software met daarbinnen een eigen CEAD omgeving, de postprocessor voor de Comau robot, de slicer plugin en extra besturing en simulatie mogelijkheden. Joris Glaser: “Tot nog toe gebruiken we Cura van Ultimaker als slicer, maar daarmee zijn de mogelijkheden te beperkt. Cura is ontwikkeld voor een 3-assige machine, terwijl wij met de robot zes assen kunnen aansturen. Je hebt in Cura niet alle vrijheidsgraden tot je beschikking, dus geven we Cura de opdracht alleen de contouren van het onderdeel te printen, om zo een continupath te creëren.” Het Objexlab gaat komende tijd intensiever samenwerken met Siemens, dat eveneens een vestiging op de BIC heeft alsook met CEAD.
Anders denken
Een ander punt waarop het 3D printen met een robot lastiger is dan met een gewone FFF printer (FDM), is volgens Joris Glaser het regelen van de materiaaltoevoer als de robot versnelt of vertraagt, bijvoorbeeld bij een hoek in het model. De traagheid in de warmtehuishouding zorgt bij de relatief grote hoeveelheid geprint materiaal dat een grote afkoeltijd per laag vereist is. Omdat het volume geëxtrudeerd materiaal een veelvoud is van dat op een normale FFF printer (FDM) is het onderbreken en starten van de materiaal toevoer op een specifiek punt erg lastig. Dit vereist dan ook dat de robot print in een continu doorlopend pad. Ook kan degeneratie van het kunststof optreden wanneer deze te lang verhit wordt in de kop. Het grote formaat vergt een andere manier van denken.
Tot 12 kilogram per uur
De E25 printkop die op de robotarm is bevestigd, is goed voor tot 12 kg materiaal per uur, afhankelijk van de nozzles die variëren van 2 mm tot 12 mm diameter in doorlaat. Ook de krimp van het gevuld PP is een punt van aandacht. Joris Glaser verwacht dat met de aansturing vanuit Siemens de mogelijkheden groter worden. Het nabewerken met de freeskop is tot nog toe niet gedaan. “Als je het juiste materiaal met de juiste instellingen gebruikt, kun je redelijk gladde oppervlakken 3D printen. Je hoeft dan alleen na te bewerken waar bijvoorbeeld een insert komt of om andere redenen een glad oppervlak vereist is.”
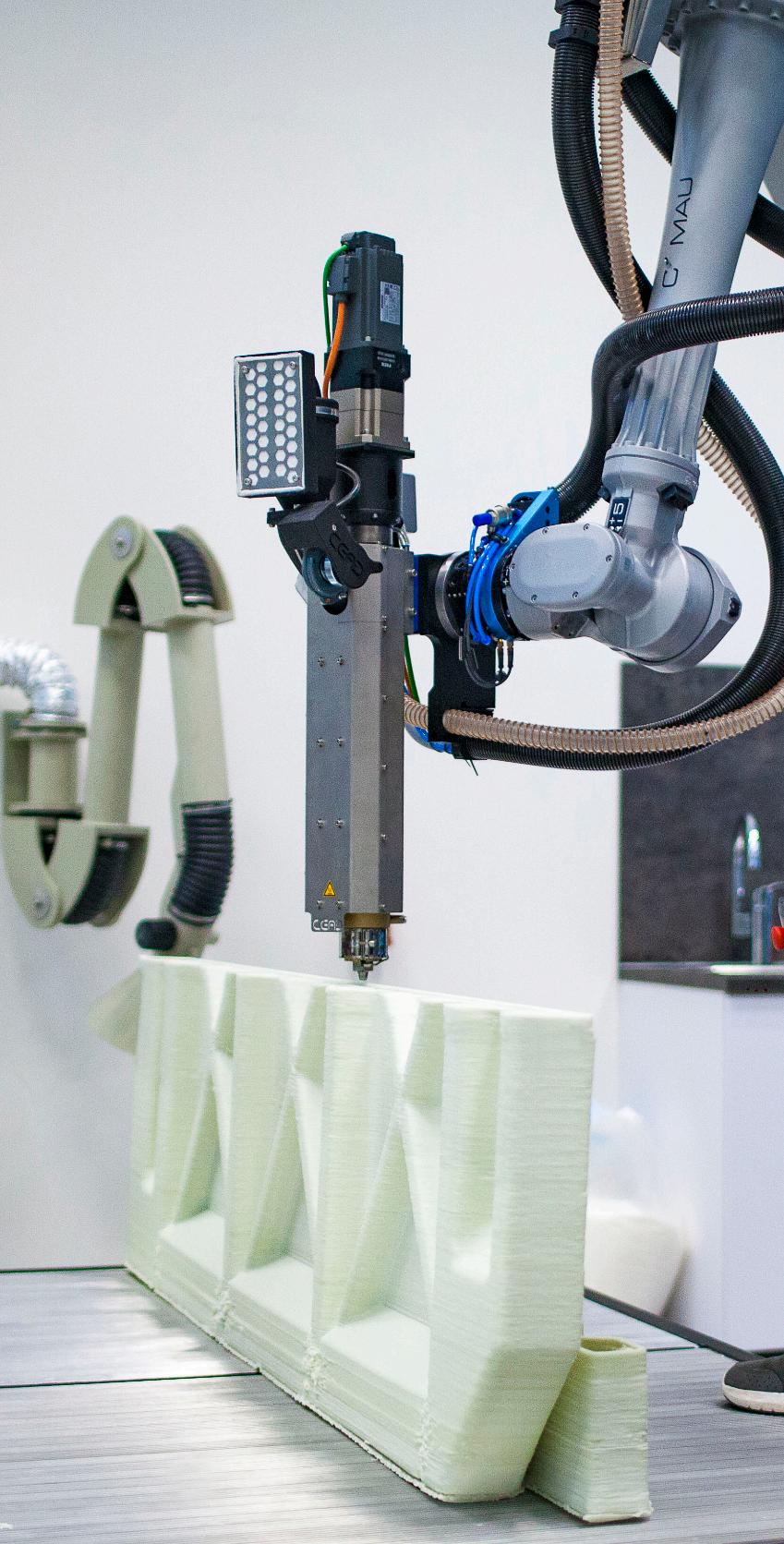
Projecten met bedrijfsleven
In de loop van het najaar wil Fontys Hogescholen projecten starten samen met het bedrijfsleven. De interesse is er al, merkt Joris Glaser. “Deze 3D printer biedt talloze mogelijkheden, niet alleen voor het bouwen van frames, maar ook in de woningbouw, het produceren van composietdelen en andere eindproducten.” Ook het 3D printen met recyclaat staat op het lijstje van de Eindhovense onderzoekers.
De AM Flexbot printer maakt de verwerking van composieten met korte vezels mogelijk. Parallel hieraan zal in samenwerking met het bedrijf Nexperia binnenkort een printer voor continue vezels worden geplaatst. Fontys verwacht in december, tijdens de 3D Delta Week, diverse resultaten te kunnen tonen van zowel composiet als metaal geprinte delen.