
31 minute read
DOSSIER ‘Circulair denken vergt een integrale benadering.’ P20Taart voor Europese vakorganisatie CETOP
CIRCULAIR DENKEN VERGT EEN INTEGRALE BENADERING
Recycleren, de ecologische voetafdruk, circulariteit, cradle-to-cradle, ... het zijn termen die de afgelopen jaren een sterke opmars kenden. Recycleren is één zaak, maar om een echt circulaire economie te creëren moeten àlle puzzelstukjes in elkaar passen, vanaf de ontwikkeling van een product tot het creëren van afzetmarkten. Technologie is daarbij de facilitator.
Advertisement
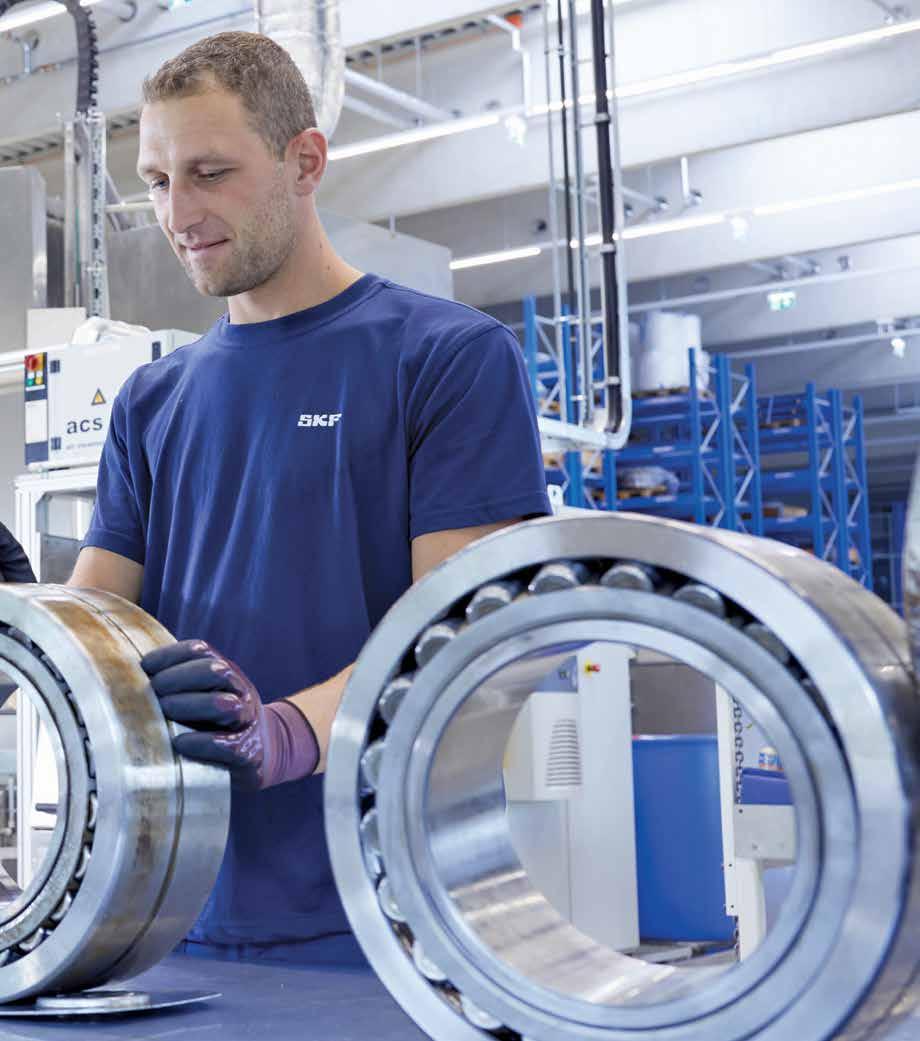
SKF heeft een programma om de levensduur van lagers te verlengen via remanufacturing.
Wie als leek aan circulariteit denkt, denkt vooral aan het hergebruiken van afval. Maar om van een echt circulaire benadering te spreken, moeten we meerdere paden bewandelen. De stromen vertragen (= producten blijven langer in de waardeketting) of de stromen versmallen (= er komt minder product in omloop) zijn zeker even belangrijk.
Om van een echt circulair model te spreken, is een optimale combinatie van drie aspecten vereist, en dat legt meteen de vinger op de wonde: als bedrijf écht circulair willen zijn is één zaak, het effectief ook kunnen hangt vaak af van externe factoren zoals het design van externe producten en systemen, een duidelijke wetgeving en vooral businessmodellen die aangepast zijn aan deze circulaire insteek. Per slot van rekening willen bedrijven de eigen concurrentiepositie niet ondermijnen door circulair te gaan werken.
In wat volgt lichten we eerst de ‘heilige drievuldigheid’ ‘Vertragen – Ontwerpen – Sluiten’ toe, gestoffeerd met enkele markante voorbeelden over hoe technologie daar bij helpt.
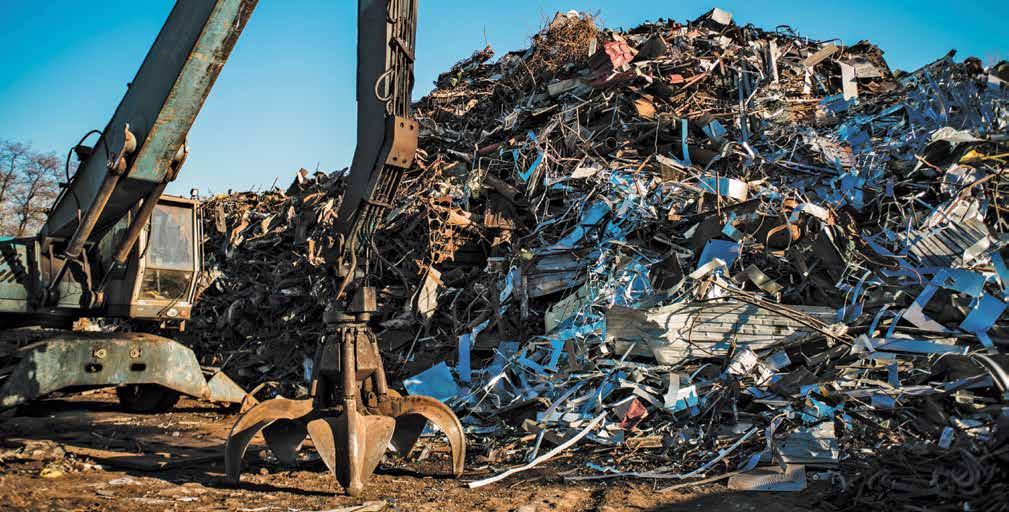
1 VERTRAGEN VAN DE CIRKEL: IN ELKE GELEDING VAN EEN BEDRIJF
Een product dat langer meegaat, vermijdt vroegtijdige vervanging. Dat bespaart niet alleen op grondstof die niet gebruikt moet worden, maar ook op de benodigde energie voor het proces en de bijhorende kosten. Een product langer laten meegaan kan op diverse manieren. Er wordt in dat opzicht wel eens gesproken over de 9 R’en:
Refuse (Heroverweeg doel en middel – is er geen andere manier van werken mogelijk?); Rethink (Kan ik weinig gebruikt gereedschap niet beter huren of delen?) Reduce (Is een betere efficiëntie mogelijk?); Repair (Is maintenance of herstelling toepasbaar op een defect component?); Reuse (Is een tweede markt mogelijk voor een afgedankt product?); Refurbish (Opknappen voor herverkoop); Repurpose (Is een compleet nieuw doel mogelijk voor (een deel van) een product?); Remanufacture (Hergebruik of regeneratie product mogelijk in dezelfde functie?); Recycle (Terugwinning van de grondstoffen in al dan niet vergelijkbare toepassingen). We zien dat ook fabrikanten stilaan deze nieuwe wegen inslaan. Zo beschikt SKF al enkele jaren over een remanufacturing programma voor bepaalde types lagers. Gemiddeld gaan die componenten 3 jaar mee maar via remanufacturing - klanten sturen ze terug, SKF maakt ze gebruiksklaar - kan die termijn verlengd worden tot 9 jaar. Bovendien: als lagers na die tijd dan toch gerecycleerd moeten worden, worden ze voortaan herwerkt in nieuwe toepassingen met hoogwaardig staal. Voorheen werden afgedankte lagers verwerkt in toepassingen met lagere kwaliteitseisen. De winst die behaald kan worden is groot: naast het minder verbruik van staal, vraagt remanufacturing veel minder energie dan de productie van een nieuw lager.
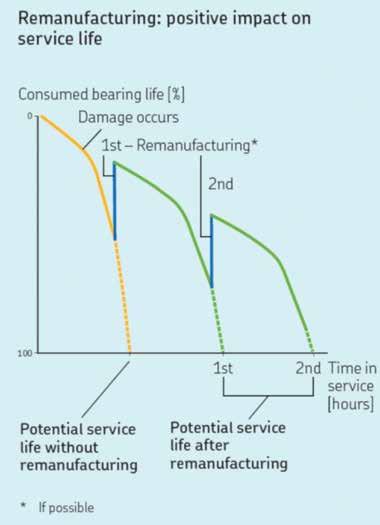
De levensduurverlenging leidt tot minder grondstof- en energieverbruik.
2 VERSMALLEN: ONTWERPEN
Bedrijf X produceert iets, klant Y koopt het. Die simpele benadering is vandaag niet meer houdbaar, noch wenselijk. Wie produceert wil dat zo efficiënt mogelijk doen om de winst te maximaliseren. Factoren als een eenvoudige recyclage na de levensduur kwamen daarbij weinig aan bod, want die kosten zijn veelal voor de klant (of voor de gemeenschap). Dit komt ook tot uiting in het productontwerp, waarbij meestal niet stilgestaan wordt bij de laatste levensfase. Gelukkig is dat vandaag steeds minder het geval.
Een duurzaam productiesysteem houdt rekening met alle fasen van de levenscyclus van een product, met inbegrip van de aankoop van materialen, de productie, het gebruik van het product en ten slotte het beheer van het einde van de levensduur van het product (recycling, verwerking, ...). Dat houdt ook in dat alles in het werk moet gesteld worden om het energieverbruik drastisch te verminderen. Ecodesign integreert ecologische criteria vanaf de ontwerpfase van een product of dienst via een globale en meervoudige aanpak.
Een goed voorbeeld van het potentieel van ecodesign is de ‘Clever Little Bag’ van schoenenfabrikant Puma (zie foto). Zij ontwierpen een schoenenverpakking met een herbruikbare draagzak uit polymeer en een doos uit licht karton. De resultaten waren impressionant. Tijdens het productieproces werd 60% minder water en energie verbruikt en werd 65% minder karton ingezet. Op jaarbasis werd 8.500 ton papier minder verbruikt. Het lichtere gewicht en compacte vorm zorgden ook voor een aanzienlijke reductie van de transportnood, waarbij omgerekend 500.000 liter diesel op een jaar uitgespaard werd.
De ‘Clever little bag’ van Puma is een prima voorbeeld van ecologisch design.
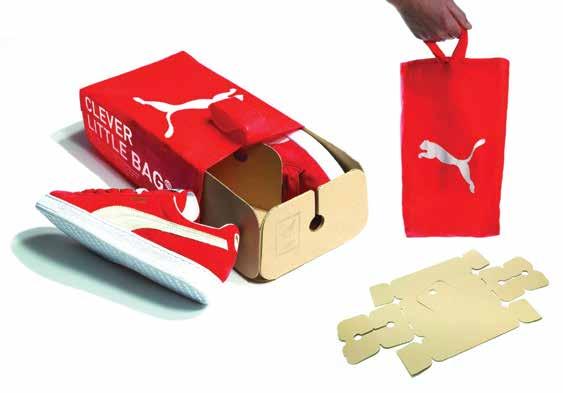
PIJLERS VAN ECODESIGN
Onderstaande leidraad met bijhorende vragen helpt om de diverse thema’s waarbij ecodesign een verbetering kan creëren te analyseren. We kunnen ze onderbrengen in 6 hoofdthema’s:
A. Optimalisatie van de productprestaties en het gekozen bedrijfsmodel
• Hoe optimaliseert u de gebruiksprestaties van een product op basis van de behoeften van de gebruiker?
B. Strategische selectie van grondstoffen
• Welke materialen met een lage milieu-impact zijn het meest geschikt voor het product in functionele en economische termen? • Welke materialen kunnen worden vervangen en wat zijn de geldige alternatieven? • Welke schadelijke/toxische stoffen moeten worden vermeden? • Hoeveel energie is er nodig om de geselecteerde materialen te verwerken?
C. Materiaalefficiëntie: intelligent gebruik van materialen
• Hoe kunnen we producten slimmer bouwen, met minder materiaal en met minder verschillende soorten materialen?
D. Optimalisatie van de logistieke ketting (opslag, transport, levering, herstel aan het einde van de levensduur)
• Welke interventies zijn mogelijk op het niveau van productontwerp en verpakking om de logistiek (voor en na de productie) beter te organiseren?
E. Optimalisatie van de levensduur van het product
• Hoe kan men de levensduur van een stuk optimaliseren en verlengen? • Wat zijn de belangrijkste redenen voor het einde van het gebruik? • Hoe kan reparatie of hergebruik worden gestimuleerd om de gebruiksfase zo lang mogelijk te verlengen?
F. Optimalisatie van het einde van de levensduur (door suggesties voor demontage)
• Een richtinggevende demontage verlengt de levensduur en optimaliseert de “end-of-life” fase van het product door bij te dragen aan de activiteiten van reserveonderdelen, terugname, identificatie van onderdelen, demontage en recycling.

Een zonnepaneel laat zich in principe makkelijk recycleren. Onder meer aluminium uit panelen zal snel een weg terugvinden richting nieuwe toepassingen.
3 SLUITEN VAN DE KETTING: ZONNEPANELEN ALS VOORBEELD
Het wordt vaak over het hoofd gezien, maar het is niet omdat iets kàn gerecycleerd worden, dat het ook gedaan wordt. Het beste voorbeeld vormt de zonnepanelensector, waar de panelen in principe bijna volledig gerecycleerd kunnen worden. ‘In principe’, want in de praktijk gebeurt dat nog niet. Als groene sector bij uitstek wou men natuurlijk het goede voorbeeld geven. Daarom werd al in 2007 PV Cycle opgericht, een organisatie die de verwerking van afgedankte zonnepanelen in milieuvriendelijke banen moet leiden. Om het geheel te financieren betalen kopers een kleine bijdrage per zonnepaneel bij de aankoop. In ruil kunnen zij hun panelen na hun levensduur inleveren bij het containerpark (particulieren) of via een ophaalcircuit (professionelen). In deze sector wordt de komende jaren een enorme volumetoename verwacht door de fikse groei in het aantal nieuwe installaties het afgelopen decennium. Deze panelen zullen nu geleidelijk in het afvalcircuit terechtkomen. Wat gebeurt daar vandaag mee?
PV Cycle: ‘Bijna 95% van het gewicht van de aangevoerde standaard silicium zonnepanelen kan vandaag in principe gerecycleerd worden. In België draait dat cijfer rond de 85%. Dat is een zeer mooi resultaat, te wijten aan de aard van de producten en bestanddelen van een zonnepaneel: fracties als aluminium, glas, plastiek, koper, zilver en silicium laten zich relatief makkelijk recycleren en bovendien is er ook een markt voor het gerecycleerde product. Dat wordt wel eens vergeten: er moet ook een afzetmarkt zijn voor de gerecycleerde stoffen én ze moeten betaalbaar blijven. Een voorbeeld is de backsheet. Die bestaat veelal uit EVA (ethyl vinyl acetaat) of tedlar. Die stof is wel degelijk recycleerbaar en zou in principe als bestanddeel in verfstoffen kunnen dienen, maar daarvoor zou het eerst gezuiverd moeten worden. Maar omdat daar enorme hoeveelheden water voor nodig zijn, is het milieuvriendelijker om die stof te verbranden en de vrijgekomen lucht achteraf te filteren. Daarom moeten we ons ook niet blindstaren op percentages, we moeten altijd het complete plaatje bekijken. Stel bijvoorbeeld dat we in plaats van 85% in België, 95% zouden kunnen bereiken in een ander recyclagebedrijf in pakweg Polen, dan moeten we ook het extra transport meenemen in de berekening van de totale milieubelasting.’
‘Het is met andere woorden een voortdurende afweging en berekening van de te nemen weg en we zijn ons zeker bewust van de hiaten. Wat hierboven staat geldt bijvoorbeeld voor de standaard silicium zonnepanelen die we overal op onze daken zien. BIPV (building integrated photo voltaics) en de flexibele panelen vallen daarentegen niet onder ons ophaalsysteem, maar onder het gewone stelsel van bouwafval. Die zaken vallen moeilijker te recycleren, de flexibele panelen bevatten bijvoorbeeld niks anders dan plastic en zonnecellen. De enige oplossing daarvoor is vaak ze te verbranden en de warmte te gebruiken als energiebron voor elektriciteitsproductie. Voor andere types panelen zoals CdTe (Cadmium Telleride) moeten we samenwerken met een gespecialiseerde Duitse afvalverwerker, omdat in België er geen oplossing voor is. Gelukkig maken die types slechts een zeer miniem deel van de markt uit.’’
HOE RECYCLEER IK EEN WAGEN?
Het belang van een afzetmarkt en een integrale benadering kunnen we niet beter illustreren dan aan de hand van een wagen. Als we even oplijsten welke materialen er allemaal gebruikt worden bij een standaard personenwagen, dan blijkt meteen de enorme opgave die een circulaire benadering vraagt.
Als we de vloeistoffen alleen al bekijken, dan zien we de brandstof, diverse smeerolies, aircovloeistof, ruitenwisservloeistof, remvloeistof,... . Bij de metalen vinden we onder andere aluminium, staal, koper, zink, lood en zelfs goud. Kunststoffen zijn aan een opmars bezig en vinden we onder meer in en rond het dashboard, bij de ruitenwissers, in diverse motor- en airco-onderdelen. Het gaat daarbij om zeer diverse stoffen: PVC, PE,PP, ABS en in de vorm van thermoharders, thermoplasten en elastomeren.
Ook rubber vinden we veelvuldig terug. Niet alleen in de banden, maar ook in onder meer de afdichtingen, matten, beschermingsflappen en ruitenwissers. Verder vermelden we nog onder meer printplaten, textiel, elektronische componenten, gassen, schuimrubber, glas en batterijen. Door deze diversiteit is het niet verwonderlijk dat het recycleren van een wagen om een zeer uitgebreid ecosysteem vraagt, met gespecialiseerde nichebedrijven in zowel de verwerkings- als afzetsector.
Minimaal 95% gerecycleerd
Het recyclageproces bestaat uit een getrapt proces om de diverse stoffen stap voor stap te scheiden. Febelauto - de federatie die het recyclageproces in ons land regelt - geeft ons de introductie: ‘Het einddoel voor de verwerking van afgedankte voertuigen is een hergebruiks- en nuttig toepassingpercentage van 95%. De eerste stap bestaat uit het zorgvuldig verwijderen van alle vloeistoffen en onderdelen die schadelijk kunnen zijn voor het recyclageproces, de zogenaamde depollutie. Dat gaat niet alleen om chemische stoffen en banden, ook airbags worden bijvoorbeeld verwijderd omdat zij kunnen ontploffen in de schredder. In deze stap worden verder ook de elektrische kabels eruit gehaald om apart te verwerken. Zij worden fijn vermaald tot kleine korrels die toelaten om de metalen en het mantelmateriaal - meestal is dat PVC - te scheiden.
Voorts worden alle herbruikbare wisselstukken zoals spiegels en glas gedemonteerd. Deze onderdelen komen weer op de markt als tweedehandsonderdelen. In de derde stap komen de ‘grote kanonnen’ in actie, want wat overblijft van de wagen moet worden gecompacteerd en geschredderd. Als laatste stap wordt het resulterende product dan op diverse manieren gesorteerd en verwerkt.’
In de autorecyclage vormt een getrapt proces de basis voor een nuttige recyclage tot 95% en meer.
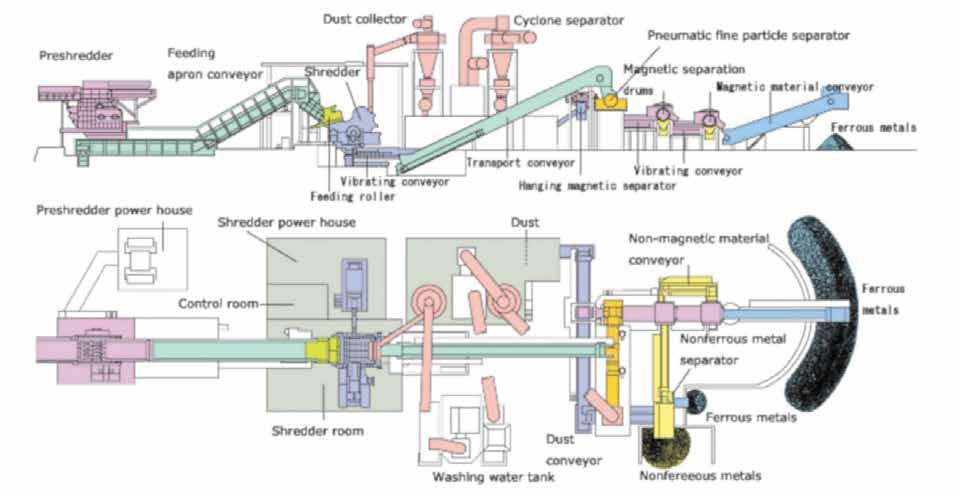
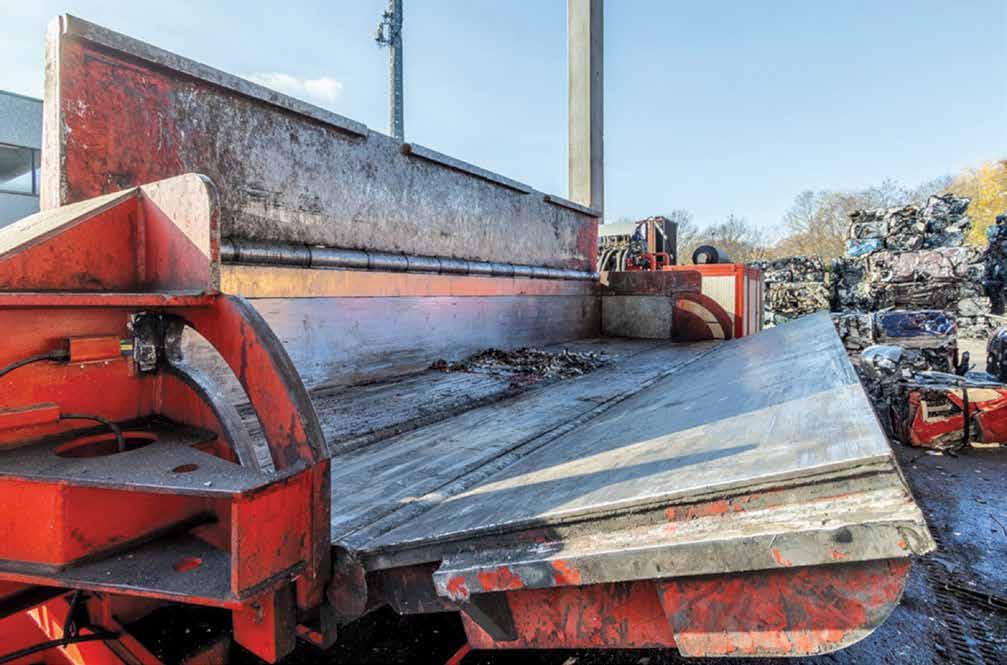
Er kunnen diverse paden bewandeld worden om materialen van elkaar te scheiden. Na de depollutie volgt meestal het compacteren en shredderen.
Hoe dat praktisch in zijn werk gaat, horen we bij Ad Rem, een bedrijf dat in 2008 onder de vleugels van autorecyclagebedrijf Galloo en Valtech opereert. Ad Rem is gespecialiseerd in machines die in het recyclageproces van wagens ingezet worden. Jelle Saint Germain is sales ingenieur van het bedrijf en licht toe: ‘Galloo deed tot 2008 beroep op een extern bedrijf voor de ontwikkeling van haar machines, maar dat bedrijf hield ermee op. Galloo wilde in eerste instantie de opgedane kennis en patenten in eigen huis houden, om de technologie later ook internationaal te commercialiseren. Daarom werd in een joint venture van Valtech en Galloo het nieuwe bedrijf Ad Rem opgericht. Vandaag zijn we overal ter wereld actief, recente projecten van onze hand vind je onder meer in Zweden, Verenigd Koninkrijk en Japan. Er zijn diverse manieren om fracties van elkaar te scheiden, maar onze kerntechnologie is de zogenaamde flotatietechniek, waarmee we plastiek en metalen op een performante manier kunnen scheiden. Maar voor ik dat werkingsprincipe toelicht, loont het de moeite om enkele processtappen en fractietypes even toe te lichten want dat heeft een invloed op het verdere proces.’
Met alle Ad Rem technologie worden 3 types fracties verwerkt: • WEEE (Waste of electric & electronic equipment), dit is onder meer alles wat consumenten binnenbrengen bij het containerpark: stofzuigers, elektronica, IT-toestellen, noem maar op. • IBA (Incinerated Bottom Ash) is wat overschiet van de verbrandingsprocessen in de verbrandingsovens voor huishoudelijk afval. In dat asresidu bevinden zich nog waardevolle metalen, die er via de Eddy Current- en flotatiemethodes (zie verder) uitgefilterd worden. • ASR (Automotive Schredder Residu) is tot slot het materiaal dat uit de schredders in de autorecyclage komt, een mengeling van diverse metalen, plastieken, autozetels,... .
Bij een bedrijf als Galloo worden deze drie hoofdtypes verwerkt. Deze fracties hebben verder nog diverse onderverdelingen, vaak gaat het ook over mengelingen van pakweg ASR met industrieel en/of bouwafval.
Compacteren en richting shredderinstallatie
In deze stap wordt het voertuig in stukken geknipt of samengedrukt met een balenpers (foto) De bedoeling is eenvoudig: het wrak zo compact mogelijk maken om het transport naar de shredderinstallatie te vergemakkelijken. De specifieke uitvoering kan wat variëren, maar over het algemeen beschikt een balenpers over een grote trechter of container waarin de auto geplaatst wordt. Vervolgens wordt via één of twee (meestal hydraulisch aangedreven) bewegende Hardox persplaten het voertuig van boven naar beneden samengedrukt, dat gebeurt afhankelijk van de fabrikant met een drukkracht van enkele honderden ton. Daarna comprimeren horizontaal inschuifbare hydraulische

De voorbehandelingsinstallatie maakt de fracties klaar voor verdere verwerking in de flotatie.
armen het voertuig in de langsrichting. Het eindresultaat is een rechthoekige baal die verwerkt kan worden in de schredder. Een performante compacteerinstallatie of baler kan makkelijk 40 wagens en meer verwerken per werkuur. De geproduceerde schrootblokken hebben een gemiddelde dichtheid tussen 400 à 500 kg/m³, al kan dat oplopen tot 1.500 kg/m³.
Vermalen in de schredder
Om het wrak te kunnen recycleren, wordt het vervolgens vermalen in een shredder. De bedoeling is om de diverse materialen zoveel als mogelijk los te maken. De rotoren van deze machine bevinden zich in een trechter en zijn uitgerust is met een dubbele reeks hamers uit mangaan of een legering met vergelijkbare sterkte, die zich naast elkaar bewegen en het wrak tegen het aambeeld duwen. Zo wordt het autowrak in enkele tientallen seconden versnipperd in kleinere fracties. Het eindresultaat van de recyclage is in belangrijke mate afhankelijk van de kwaliteit van dit schredderproces.
Sorteren in afvalfracties
‘Na de schredder volgt een fijne zogenaamde voorbehandeling, waarbij de afvalfracties kleiner dan 4 mm er uitgefilterd worden, als dat niet gebeurt dreigen zij de pompen te verstoppen’, weet ingenieur Jelle Saint Germain. ‘Te licht materiaal wordt er in deze stap eveneens uitgehaald via afzuiging, want dat materiaal zuigt het medium uit de flotatieprocessen te veel op. Een voorbeeld hiervan is het schuimrubber uit de zetels. Bovendien zijn deze schuimrubbers niet recycleerbaar, ze moeten na afloop toch verbrand worden. De kost van verbranding wordt verrekend per kilogram, je zou in dit geval met andere woorden vooral betalen voor het verbranden van het opgenomen water.‘
‘Metalen zijn zo goed als 100% recycleerbaar via dit proces. Bij ASR-plastics is dat niet het geval door de kleine verschillen in dichtheid, terwijl groepen als thermoharders zich moeilijker laten verwerken. De verdeling bij de plastics is 1/3de dat gerecycleerd kan worden, 1/3de waarvan we het chloorgehalte zodanig naar beneden kunnen halen zodat het verbrand kan worden voor energietoepassingen en het resterende derde moet gestort worden. Bij WEEE-materiaal kan 50% gerecycleerd worden. Let wel dat deze cijfers louter over dit proces gaan. Als we een wagen in zijn totaliteit bekijken, dan scoort een bedrijf als Galloo daar rond de 98,5% nuttig materiaal. Daarmee halen ze vlot de norm van 95% die door Febelauto opgelegd wordt. Bovendien is minder dan 10% daarvan thermisch gevaloriseerd, dus voor verbranding bedoeld.’
Flotatietechniek: filteren door gewicht
Jelle Saint Germain: ‘De basis van onze techniek vormt flotatie, waarbij fracties in functie van hun soortgelijk gewicht gefilterd worden door ze letterlijk boven te laten drijven. We werken
Een deel van de plastic scheidingsinstallatie die Ad Rem plaatste in Japan.
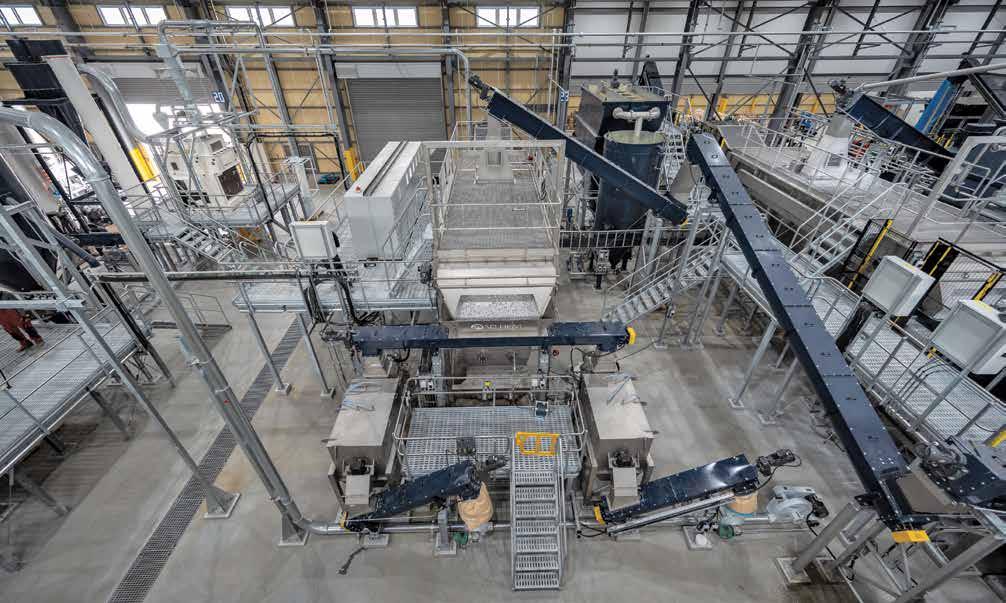
met 2 verschillende flotatieprocessen, een lijn voor het plastiek en een voor de metalen. De metalen fracties wordt eerst in een grote trommel gebracht waarin zich een medium bevindt, een mengeling van ferrosilicium met water. Op zich is dat een zeer onstabiele suspensie: mocht de vloeistof stilstaan, dan zou het ferrosilicium meteen naar de bodem van de tank zinken en wordt het systeem onbruikbaar.’
‘Door te werken met een bewegende trommel waarin de vloeistof voortdurend wordt ingepompt, verhinderen we dat. Je kan flotatieprocessen in principe ook uitvoeren met zout in plaats van ferrosilicium, maar zout lost in tegenstelling tot deze laatste wel op. Bovendien is zout corrosief, met alle gevolgen van dien voor je processen.’
‘Bij metalen werken we bijvoorbeeld met een densiteit van 3 kg/l. Metalen als aluminium zitten op ongeveer 2,7 kg/l en zullen dus drijven en er uitgeschroefd worden. Eventuele plastics worden naar de plasticflotatie gebracht. Zwaardere metalen als RVS, zink, koper, brons en lood zitten allemaal rond 7 a 8 kg en zinken meteen naar de bodem.’
‘Bij de plastics werken we noodgedwongen op een iets andere manier. Het verschil in densiteit tussen diverse plasticsoorten is veel kleiner dan deze tussen metalen onderling, waardoor we niet met een bewegend medium kunnen werken. Stel dat we instellen op densiteit 1,09 dan zouden de stukken met 1,10 in theorie moeten zakken, terwijl die van 1,08 zouden moeten bovendrijven. Door de turbulentie in een bewegend medium wordt dat proces echter grondig verstoord. Daarom werken we met een ander mengsel - water en calciumcarbonaat - in een statische tank.’ ‘Deze suspensie is immers stabieler en moet niet in beweging gehouden worden’, weet Jelle Saint Germain. ‘De werking is uiteraard ook wat afhankelijk van de noden van de applicatie. Zo leverden we onlangs een installatie op voor een klant in Engeland. Het geschredde materiaal wordt er eerst afgezeefd, vervolgens brengt een wasschroef ze naar de separator. We scheiden vervolgens eerst op een medium met densiteit 1,09 om de recycleerbare en niet-recycleerbare materialen te separeren. De ‘zinkers’ vormen de niet-recycleerbare plastics, zij worden uitgeschroefd en gespoeld en vormen één output. In de tweede fase worden de drijvers via een rol naar de uitgang geduwd. Het medium wordt daar eerste afgezeefd, vervolgens worden de plastics gespoeld en belanden ze in een tweede separator op basis van water. Hier zullen de polyolefinen (PE en PP) bovendrijven, terwijl de polystyrenen (PS en ABS) zinken. Zo krijgen we enerzijds het eindproduct PE/PP en het andere product wordt extern nog gescheiden om het PS en ABS te separeren. Na afloop wordt het water onder meer gefilterd via een lamelladecanter en beltfilters. Voor ons was dit Engelse project relatief eenvoudig, maar we hebben in Japan net een project afgewerkt waarvoor we meer dan 100 zeecontainers verscheepten. Een project in de recyclagesector is meestal maatwerk.’
‘Het type residu is belangrijk om de processtappen te bepalen. WEEE bevat bijvoorbeeld hoogwaardiger plastiek dan ASR. De meeste fracties WEEE bevatten ook heel weinig metalen, en worden rechtstreeks naar de plastiekflotatie gebracht. ASR bevat ook meer extra materiaal zoals rubber en textiel van de autozetels. In dat geval zijn er wat bijkomende stappen nodig om die zaken eruit te filteren, die je bij WEEE veelal niet moet uitvoeren.’
‘Het eindresultaat van de plastiekflotatie is een zogenaamde flake die zo puur en hoogwaardig is, dat hij terug verkocht wordt aan autofabrikanten voor nieuwe onderdelen. De cirkel wordt dus echt gesloten, met een hergebruik in een vergelijkbare toepassing. Al ligt daar nog veel potentieel, want mocht men in het begin meer opteren voor materialen zoals PP, PS, PE en ABS dan zouden we nog meer kunnen recycleren.’
‘In de toekomst zal de komst van de elektrische voertuigen op zich niet zoveel veranderingen teweegbrengen. Bij de depollutie wordt de batterij eruitgehaald en verder blijft het proces hetzelfde. Wel wordt het boeiend om de evolutie van de afzetmarkten te bekijken. Eén van de grootste focussen ligt vandaag op aluminium, omdat daar veel vraag naar is. Vandaag wordt veel van dat gerecupereerde aluminium hergebruikt in de motorblokken voor verbrandingsmotoren. Maar wat zal er gebeuren als die afzetmarkt sterk krimpt en de bijhorende vraag naar aluminium daalt?’
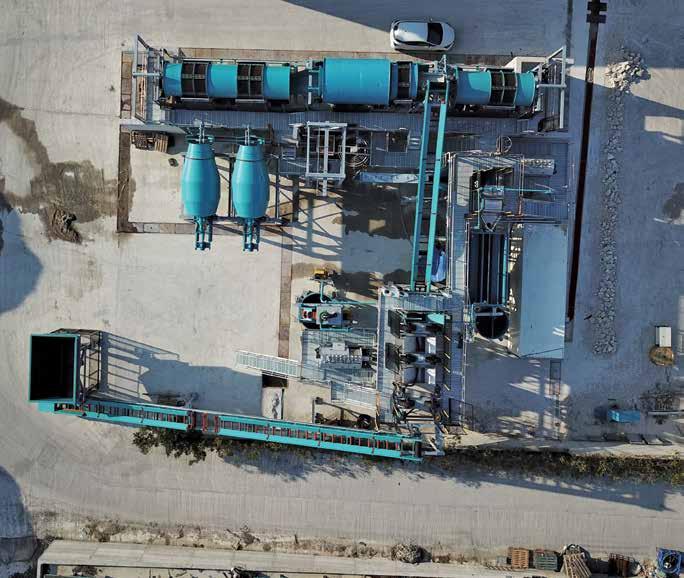
Een ‘dense medium separation’ systeem voor het scheiden van metalen.
EDDY CURRENT (= WERVELSTROOM) METHODE VOOR SCHEIDING PLASTIEK EN METALEN
Er zijn wel meerdere manieren om plastiek en metalen te scheiden, dit zijn meestal geen concurrende maar aanvullende systemen. Zo is de ‘Eddy Current’- methode eveneens populair. In dit systeem scheiden en sorteren achtereenvolgens een boven- en overbandmagneet, een magnetische koprolmagneet en/of een trommelmagneet het ijzer in de eerste fase. De Eddy Current scheider zal vervolgens de waardevolle non-ferro metalen zoals aluminium, koper en zink eruit halen.
Bij de eerste stap met de overbandmagneet wordt op een eenvoudige wijze - een magneet boven de transpotband - het ijzerhoudend materiaal uit het aangevoerde afval verwijderd. Er kan geopteerd worden voor 2 hoofdtypes: een permanent- of elektromagneet. Die laatste zijn iets duurder en ingewikkelder, maar hebben het voordeel dat ze makkelijk uit te schakelen zijn voor onderhoud. Over het algemeen is een elektro-uitvoering meer geschikt voor het verwijderen van grote fracties, maar in de keuze spelen meerdere factoren een rol, zoals type puin, bandbreedte, opstellingshoogte en gewenste instellingsmogelijkheden.
Bij de tweede stap wordt gebruik gemaakt van een trommelmagneet en/of een koprolmagneet. De werking van beide is wat vergelijkbaar. Een trommelmagneet wordt op het einde van een transportband geplaatst en zal de ijzerhoudende stukken eruit halen voor de fractie gestort wordt. Een koprolmagneet wordt als aandrijfrol in de kop van een transportband gebouwd. De fracties worden via de band aangevoerd en zodra de ijzerhoudende deeltjes in het magnetisch veld komen, worden ze door de magneet aangetrokken en rond de koprolmagneet meegebogen en uit het circuit gehaald. Het restmateriaal vervolgt gewoon zijn weg. Hierdoor krijgen we op een eenvoudige manier een zeer goede scheiding tussen ijzerhoudend en nietijzerhoudend materiaal.
Tot slot volgt dan de eigenlijke Eddy Current-zuivering, die zoals de naam het weggeeft gebruik maakt van het fenomeen wervelstroom. Het materiaal wordt over de gehele breedte van de transportband door de Eddy Current installatie gevoed. In de kopse zijde van de band is een pooltrommel ingebouwd.
Deze pooltrommel bestaat uit een combinatie van meerdere noord-zuid magneten. Deze pooltrommel draait aan hoge snelheid en induceert wervelstromen in de geleidende deeltjes die er voorbij komen. Dit effect zorgt voor een afstotende kracht van geleidende non-ferro metalen waardoor deze zich automatisch richting een separate materiaalstroom begeven en de scheiding een feit wordt.

Een plastic scheidingsinstallatie van Ad Rem in de UK
INDUCTIE IN COMBINATIE MET SENSOREN
R&D draait ook in de recyclagesector op volle toeren. Zo zien we dat de combinatie van meerdere technieken vaak leidt tot een prima resultaat.
Om ook bij de kleinste korrelgroottes metaal uit een mix van restmaterialen te halen, kan bijvoorbeeld gebruik gemaakt worden van inductiesortering in combinatie met de eerdere vermelde methodes zoals magnetische sortering en de Eddy Current methode.
Materialen uit composiet zoals printplaten kunnen zo omgeturnd worden in een bron van herbruikbare metaalconcentraten zoals zurik (een combinatie van RVS met aluminium, koper, lood, magnesium of nikkel) of enkel RVS. Bij deze inductiesorteersystemen passeert de transportband door een inductieve lus, waar een elektromagnetisch veld gecreëerd wordt. Telkens er een geleidend voorwerp door dat gebied passeert, heeft dit een invloed op het magnetisch veld.
Door die verandering op te nemen via een inductiesensor, kan exact - tot op 1 mm nauwkeurig volgens de producenten - de locatie bepaald worden van een stuk, een gerichte persluchtstoot doet de rest. Afhankelijk van de eisen van de toepassing zijn er sensoren beschikbaar met een grove of fijne resolutie door aanpassing van de spoeldiameter. Dit soort technologie komt tegemoet aan de toenemende vraag naar scheidingssystemen voor metalen in partikelgroottes tot minder dan 10 mm. Shredderfracties in deze korrelgroottes bevatten meestal grote hoeveelheden fijne koperdraden die moeilijker te scheiden zijn met de Eddy Current methode.
www.skf.com www.pvcycle.org www.adremcyclingmachines.com www.galloo.com www.valtechgroup.eu www.steinertglobal.com www.lybover.be www.redwave.com
IGUS BEVORDERT DE CIRCULAIRE ECONOMIE MET 'S WERELDS EERSTE KABELRUPS VOLLEDIG UIT GERECYCLED MATERIAAL
Cradle-to-cradle: dit is het principe van de circulaire economie, die uitgaat van de natuur. Het doel: consumptiegoederen terugbrengen in de biologische of technische kringloop om zo waardevolle hulpbronnen en grondstoffen te behouden. De motion plastics specialist igus streeft dit doel ook na en heeft nu 's werelds eerste kabelrups van gerecycled materiaal ontwikkeld op basis van haar eigen "chainge" kabelrups recyclingprogramma.
Van extreme weersomstandigheden en natuurrampen tot vervuiling van de zee: de klimaatcrisis wordt steeds erger en steeds meer mensen worden zich ervan bewust. ‘Zelfs de aankoopbeslissingen van onze klanten worden steeds meer bepaald door ecologische overwegingen. Daarom hebben we veel energie gestoken in productontwikkeling om efficiënter met hulpbronnen te kunnen produceren - zonder aan productkwaliteit in te boeten’, legt Jörg Ottersbach, hoofd van de igus kabelrupsen Business Unit uit.
Het resultaat: de E2.1.CG cradle-kabelrups - een complete reeks kabelrupsen gemaakt van het nieuwe igumid CG materiaal. Talrijke tests in ons eigen testlaboratorium tonen aan dat de nieuwe kabelrups bijna dezelfde technische eigenschappen en belastingsgrenzen heeft als een kabelrups gemaakt van het standaard igumid G materiaal. Een ander voordeel is dat de cradel-kabelrups beschikbaar is tegen dezelfde prijs als kabelrupsen gemaakt van het standaard materiaal. Het nieuwe gamma is uit voorraad leverbaar in vijf series en 28 kabelrupstypes.
Van afgedankte kabelrups tot gerecycled materiaal
De cradle-to-cradle-kabelrups maakt onder meer gebruik van gerecycled materiaal uit het "chainge"-recyclingprogramma. In het kader van dit programma zamelt igus sinds 2019 gebruikte kabelrupsen van klanten in, zodat ze niet eindigen
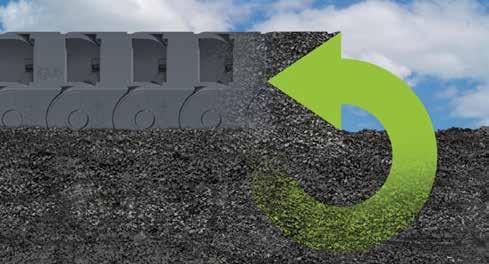
Meer duurzaamheid met constante kwaliteit: de nieuwe cradle-kabelrups van gerecycled materiaal spaart hulpbronnen en stuwt de circulaire economie vooruit.
als industrieel afval. Deze service wordt aangeboden voor zowel igus kabelrupsen als kabelrupsen van andere fabrikanten. Tot dusver is in 13 landen meer dan 32 ton materiaal ingezameld. Voor 2022 heeft igus zichzelf het doel gesteld om dit totaal te verhogen tot 500 ton. Afvalmateriaal wordt per soort gesorteerd, gereinigd en verwerkt tot nieuwe kwaliteit. Dit is mogelijk met behulp van een chemische analyse en formule-tuning - een proces waarbij het materiaal wordt geoptimaliseerd voor de gewenste eigenschappen en daardoor een constante productkwaliteit mogelijk maakt. Het post-consumer materiaal igumid CG wordt vervolgens gebruikt om de gerecyclede kabelrups te produceren, zonder verlies van kwaliteit wat betreft slijtagegedrag, stabiliteit of buigmoeheid.
Duurzame grondstofcyclus – met 28% minder CO2
Met het nieuwe kabelrups productassortiment van gerecycled materiaal levert igus een verdere bijdrage aan het behoud van hulpbronnen en het bevorderen van de circulaire economie. Volgens de milieuproductverklaring vermindert deze duurzame grondstofcyclus ook de CO2-uitstoot met 28%.
Is er een fabrikant die mij een garantie op robotkabels geeft?
Ethernet CAT5e-Kabel 15

miljoen cycli getest Test 4888
Bezoek ons: igus.be/news Nieuwe buskabel met dubbele torsiehoek (± 360 °/m) en gegarandeerde levensduur
● 49 robotkabels uit voorraad leverbaar ● Met 3.800 m2 het grootste testlab in de industrie ● Aansluitklaar geconfectioneerd of per meter ● Al vanaf 1 meter zonder snijkosten ● Levensduur online berekenbaar ● Met 36 maanden garantie motion plastics® Tel. 03-330 13 60 info@igus.be
.be/chainflex
Jörg Ottersbach zegt hierover: ‘De nadruk moet niet alleen liggen op het eerste gebruik van producten, maar ook op het hergebruik van grondstoffen. Wij zien veel 'cradle-to-cradle'potentieel en streven ernaar zoveel mogelijk grondstoffen en afgedankte producten opnieuw te verwerken, zodat kostbare grondstoffen geen afval worden, maar zo lang mogelijk op een verstandige manier worden gebruikt.’
www.igus.be
DE FIETS DIE NIET ROEST
‘Van plastic uit de oceaan naar motion plastics’, is het doel dat wordt nagestreefd met het igus:bike project - het concept van een fiets die voor meer dan 90 procent uit kunststof bestaat. Het hoogtepunt van het project is dat de fiets in theorie kan worden gemaakt van gerecycled kunststofafval, zoals afgedankte visnetten. Zo kan het plastic uit de zee van gisteren de mobiliteit van morgen creëren. Voor de gezamenlijke ontwikkeling van een eerste fietsmodel heeft igus geïnvesteerd in de Nederlandse start-up mtrl.
Het pleidooi voor een schone toekomst is een zorg die ook de in Keulen gevestigde onderneming igus deelt. Het bedrijf streeft ernaar om de levenscyclus van producten te verlengen en zo waardevolle hulpbronnen te sparen, bijvoorbeeld door het recyclen van niet meer gebruikte kabelrupsen. Uit deze motivatie is onder andere het igus:bike project ontstaan: het concept van een smeer- en onderhoudsvrije, volledig uit kunststof vervaardigde fiets, die ook van gerecycled kunststofafval kan worden gemaakt. igus presenteert nu het eerste model en het duurzame concept achter het project.
De igus motion plastics worden al tientallen jaren met succes gebruikt in de mobiliteitssector - of het nu gaat om de automotive-, scheepvaart-, vliegtuig- of fietsindustrie. Met het igus:bike project streeft igus naar een oplossing voor de moderne mobiliteit en de milieuvervuiling door plastic afval. Het concept: een volledig kunststof fiets die volledig smeer-, roest- en onderhoudsvrij is en dus in alle weersomstandigheden buiten kan staan en bedoeld is om generaties lang aan mensen vervoer te bieden. Als de fiets op een bepaald moment het einde van zijn levensduur bereikt of als een nieuwe framemaat nodig is, kan het plastic worden gegranuleerd en kan er een nieuwe fiets van worden gemaakt. Het eerste model werd samen met de Nederlandse start-up mtrl ontwikkeld, die al een aantal jaren fietsen met kunststof frames en wielen maakt.
Duurzaamheid - het productieproces telt ook mee
De start-up mtrl kiest ook voor een duurzame aanpak van het productieproces, aangezien de kunststof op de locatie kan worden gerecycled en met weinig energie opnieuw kan worden gevormd. Om dit te bereiken, vertrouwt mtrl in zijn eigen laboratorium in Nijkerk volledig op hernieuwbare energiebronnen, bijvoorbeeld via zonnecellen op het dak, om de CO2-footprint zo laag mogelijk te houden.
Voor de productie gebruikt mtrl speciaal gebouwde machines met smeermiddelvrije en duurzame iguscomponenten. De kunststof wordt gevormd door rotomoulding of roterend gieten met lage druk en hoge temperatuur, waarbij warmte en tweeassige rotatie worden gecombineerd. De fiets is gemaakt van zachte kunststoffen, zoals bijvoorbeeld polyethyleen (PE). Het is de bedoeling om in de toekomst overal ter wereld lokale productielocaties te bouwen in de buurt van vuilnisbelten en op die manier een duurzame en transparante toeleveringsketen tot stand te brengen. De firma mtrl zal de productie van de mtrl.bike tegen het einde van dit jaar starten. De marktintroductie in Duitsland is gepland voor begin 2023.
Maar er zit nog meer achter het igus:bike concept: met de lancering staan de deuren open voor verdere partnerschappen. ‘Met het igus:bike platform willen we de knowhow over kunststoffen in de wereldwijde fietsindustrie bevorderen’, legt Alexander Welcker, Bicycle Industry Manager bij igus, uit. ‘Dit stelt ons in staat om het concept te implementeren en verder te ontwikkelen met vele andere fiets- en onderdelenfabrikanten. Onze visie is om van plastic een waardevolle en duurzame grondstof te maken en de circulaire economie internationaal te promoten. De omgang met kunststof kan dan ook op veel andere gebieden positief veranderen.’
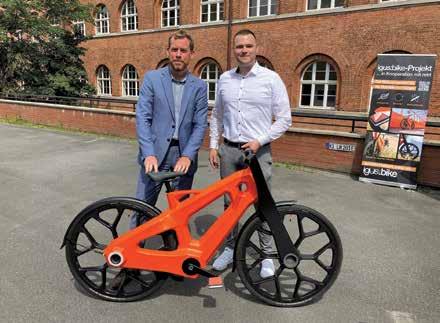
Bij de start van de Olympische herdenkingsrally presenteerden de burgemeester van Kiel Dr. Ulf Kämpfer (links) en Alexander Welcker, Bicycle Industry Manager bij igus (rechts), samen het eerste model van een fiets die voor meer dan 90 procent uit kunststof bestaat.
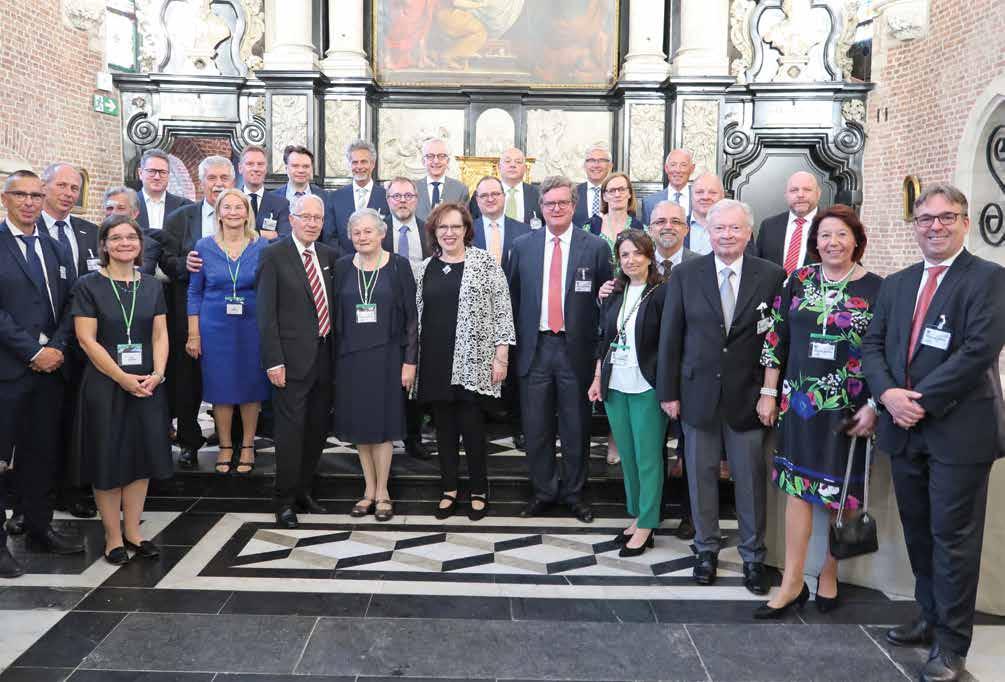
De CETOP-leden verzamelden in Antwerpen voor het 60-jarige bestaan.
TAART VOOR EUROPESE BEROEPSFEDERATIE CETOP
De Europese federatie CETOP vierde in Antwerpen het zestigjarige bestaan van de organisatie. De bestuursleden van de diverse nationale beroepsverenigingen die deel uitmaken van CETOP verzamelden voor een diner, inclusief grote verjaardagstaart, in het nieuwe vijfsterren Antwerp Botanic Sanctuary Hotel.
De oprichting van CETOP kwam er onder impuls van Franse, Duitse en Britse brancheverenigingen die in 1959 de eerste zaadjes van een overkoepelende organisatie plantten. Dat zou drie jaar later in het Zweedse Stockholm uitmonden in de oprichting van het ‘Comité Européen des Transmissions Oléohydrauliques et Pneumatiques’, kortweg CETOP.
Eén van de allereerste taken die CETOP in de beginjaren op zich nam was de standaardisering van componenten, dat deed ze onder meer voor kleppen en ventielen, waarvan sommigen tot op vandaag nog steeds aangeduid worden als CETOP kleppen of -ventielen. De organisatie was opgericht om de belangen van haar leden te verdedigen, en deed dat met verve. Geleidelijk werden ook andere belangrijke pijlers toegevoegd aan de dienstverlening, met opleiding, marktonderzoek en impact op de wetgeving en normeringen als voornaamste activiteiten.
CETOP waakt op Europees niveau over de belangen van iedereen die actief is in de ‘fluid power’, met name hydraulica en pneumatica. In ons land maakt InduMotion – de uitgever van Automation Magazine – deel uit van moederfederatie CETOP. De Belgische beroepsorganisatie was dit jaar in Antwerpen gastheer voor het congres. De Europese vakorganisatie groeide inmiddels uit tot de overkoepelende entiteit van 19 nationale federaties, goed voor een vertegenwoordiging van meer dan 1.000 bedrijven die actief zijn in fluid power, met in totaal 70.000 werknemers en een omzet van ongeveer 13 miljard euro.
Tijdens het congres verkozen de CETOP-leden de Nederlander Arjan Coppens als nieuwe voorzitter voor de periode van 20222025. Arjan Coppens is actief bij FEDA Nederland en Managing Director bij Bosch Rexroth Nederland. Hij volgt nu Stefan König op, die CETOP leidde sedert 2016. Naast Coppens werden ook vier nieuwe bestuursleden gekozen: Vice-President Economics Carlo Vergano (ASSOFLUID-Italië), Vice-President Education Nik Watson (BFPA-Verenigd Koninkrijk), Vice-President Marketing


Drie leden van het nieuwe CETOP-bestuur (foto vlnr): Carlo Vergano, voorzitter Arjan Coppens en Christian H. Kienzle. Bestuursleden Nik Watson en Eric Vives konden wegens professionele activiteiten niet in Antwerpen zijn. Een grote verjaardagstaart mocht op het feest niet ontbreken.
Econoom Etienne de Callataÿ gaf als gastspreker een uiteenzetting over macro-economische tendensen.
& Communication Christian H. Kienzle (VDMA-Duitsland) en Vice-President Technics Eric Vives (ARTEMA-Frankrijk). Zetelen eveneens in de raad van bestuur: de vorige Voorzitter Stefan König (VDMA-Duitsland) en Ere-Voorzitter Amadio Bolzani (ASSOFLUID-Italië). De Zweed Sten-Ove Claesson die 9 jaar als ‘Mister Education’ fungeerde als Vice-President, werd gehuldigd voor zijn inzet voor CETOP. Econoom Etienne de Callataÿ gaf voor de genodigden een analyse over de gevolgen van een mogelijke stagflatie en schetste enkele economische korte termijn vooruitzichten. De organisatie besprak vervolgens de omzetcijfers in de fluid power sector. Dirk Decker (VDMA) hield als Secretaris-Generaal van EUROTRANS een toespraak en feliciteerde het jarige CETOP.
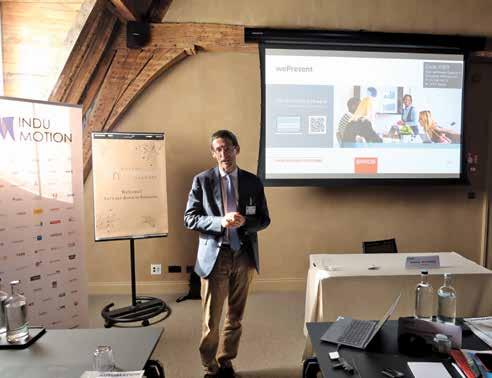

Het tweedaagse congres vond plaats in het historische Botanic Sanctuary Hotel in Antwerpen.
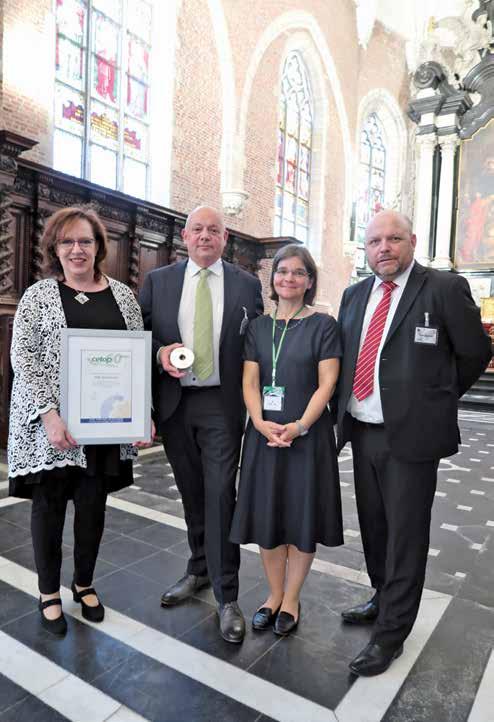
‘In 1969, creëerde de Europese aandrijftechnologie industrie een netwerk genaamd EUROTRANS en er was vanaf het begin een vriendschapsband met CETOP. Beide industrieën hebben immers een vergelijkbare klantenstructuur en vergelijkbare uitdagingen. Het motto van dit informele netwerk was: ‘laten we profiteren van de kansen die Europa biedt.’ CETOP is ontstaan uit het besef om samen een stem en identiteit te creëren voor de Europese Fluid Power-industrie. Destijds enigszins gedreven in concurrentie met de VS – vandaag zijn er de uitdagingen door Azië en de snelle wereldwijde technologische veranderingen. Onze netwerken doen dit samen altijd in een eerlijke dialoog, met als opzet de branche in het juiste licht te zetten en gemeenschappelijke doelen te definiëren. Bijvoorbeeld: de werving van jonge talenten, de mogelijkheden van digitalisering, de noodzaak van duurzaamheid, de stabiliteit van waardeketens en energie, de uitwisseling van statistieken en marktgegevens, de bevordering van onze Europese identiteit, … Om al die veranderingen succesvol te managen zijn er informele netwerken nodig en EUROTRANS hoopt nog lang een partner van CETOP te zijn’, aldus Dirk Decker.
www.cetop.org www.indumotion.be
Vlnr: Sylvia Grohmann-Mundschenk (VDMA Fluid Power), Voorzitter Arjan Coppens, Stefanie Inoue (CETOP) en Dirk Decker (EUROTRANS).