
22 minute read
L’EAU DE MER, UNE SOURCE ALTERNATIVE ?
Près de 97% de l’eau sur terre se trouve dans la mer et les océans et le dessalement semble être une idée séduisante. Mais des obstacles majeurs s’opposent à cette solution.
La consommation d’énergie nécessaire au dessalement est un facteur qui entrave le déploiement de telles techniques à grande échelle, tandis que la problématique des flux résiduels doit être mieux abordée. Mais ne jetons pas le bébé avec l’eau du bain car la technologie évolue aussi dans ce domaine.
Le producteur Farys à Ostende a ainsi inauguré une installation qui transforme l’eau saumâtre – un mélange d’eau douce et d’eau de mer – en de l’eau potable. « L’eau devient rare et nous recherchons des manières de diversifier l’approvisionnement et de le rendre durable. De plus, la situation géographique est complexe en Flandre. La quasi-totalité de notre production d’eau potable se trouve dans l’est du pays, principalement au canal Albert. Le transport vers le reste de la Flandre est coûteux et jusqu’à récemment, nous n’avions pas d’alternative. Nous voulions trouver un moyen de contourner ce problème », dit-on.
La solution est un développement interne. Farys a combiné et affiné plusieurs techniques existantes. Wim Jacobs, directeur exécutif Production & Transport de Farys, nous explique cela.
L’innovation semble être la clé de la solution : « Nous avons construit une installation de traitement d’eau d’une capacité initiale de 500 m³ à l’heure que nous pourrons augmenter à 1000 m³ à l’heure à terme. Sur une base annuelle, cela représente une capacité de 8 millions de m³. Depuis Ostende, nous soutirons de l’eau dans le canal Bruges-Ostende que nous transformons en une eau potable dans l’heure qui suit. »
« Nous appliquons plusieurs filtrations en série et déployons plusieurs techniques. L’eau du canal passe d’abord par un tamis à racleur de 3 mm. Un double tamisage mécanique a ensuite lieu de respectivement 1 et 0,25 mm, suivi d’une filtration membranaire où la microfiltration retient les particules en suspension et les grandes bactéries. Une osmose inverse est ensuite réalisée pour éliminer les matières dissoutes, les virus et les bactéries résiduelles. À ce stade, nous disposons d’une eau déminéralisée qui n’est pas encore potable. »
« Après une filtration via un charbon actif, le processus de reminéralisation est lancé. Des granulés de chaux sont dissous dans l’eau pour ajouter les minéraux nécessaires. L’eau est amenée au bon pH. Le résultat final est une eau parfaitement potable. »
« En soi, ces techniques de filtration ne sont pas nouvelles mais nous avons réussi à optimiser cette chaîne ‘multi-barrières’ entre le pompage de l’eau dans le canal et la production d’eau potable. Nous en tirons de beaux avantages. Tout d’abord, le
Au-dessus:
Farys a développé un système innovant en combinant et en optimisant plusieurs techniques.
Droite: processus est rapide : après environ une heure, l’eau du canal est potable. Deuxièmement, la consommation d’énergie est limitée. C’est important pour la rentabilité de l’installation car grâce à ce développement, produire de l’eau potable sur place coûte moins cher qu’un transport sur une longue distance. »
Aperçu de l’installation d’osmose inverse.
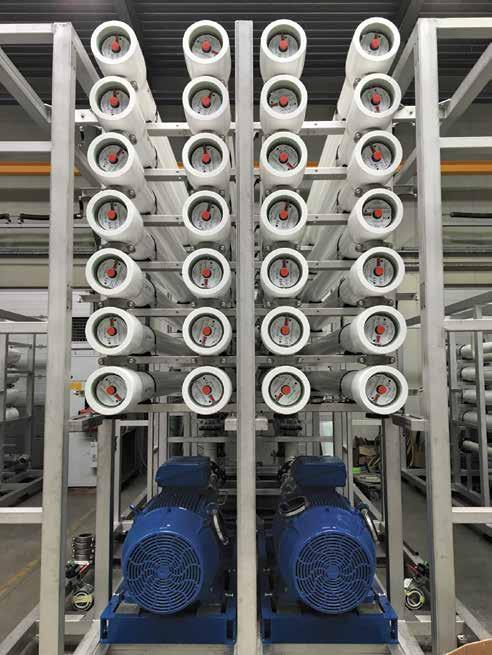
« Enfin, l’installation peut traiter diverses qualités d’eau, ce qui est un grand avantage par rapport à d’autres systèmes. En périodes de fortes précipitations, l’eau est douce, en période de sécheresse, l’eau est saumâtre et lors de calamités, l’eau du canal peut contenir des polluants. L’installation de traitement fournit la même qualité finale malgré les diverses qualités au départ. La seule conséquence est qu’il faut plus d’énergie pour alimenter le processus selon le degré de salinité et de concentration des matières dissoutes dans l’eau. »
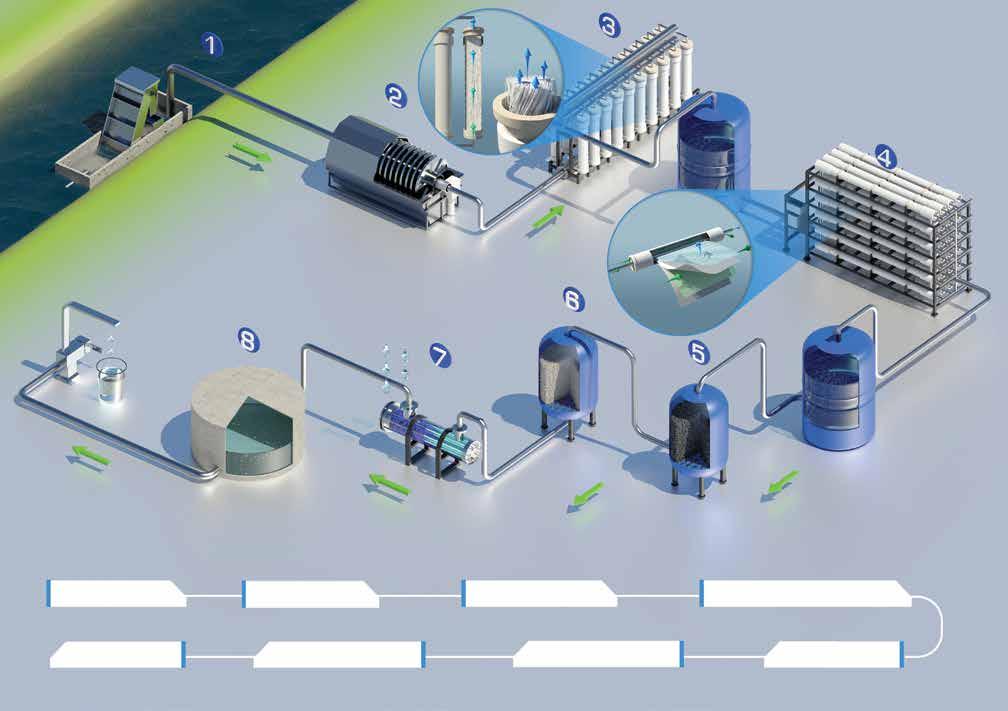
LE RÉSEAU D’EAU POTABLE DU FUTUR EST EN WALLONIE
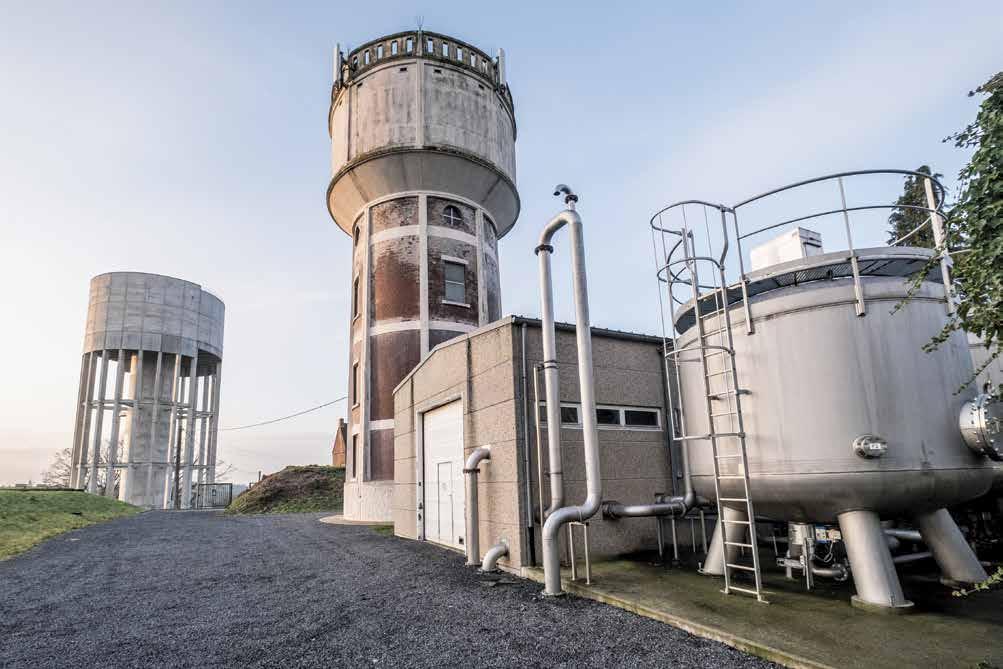
Dans le pays, la modernisation du réseau d’eau potable bat son plein. À la SWDE, on modernise le réseau pour en faire une installation exemplaire. Le projet doit être achevé en 2026 et il sera une référence pour les installations d’eau potable dans le monde entier. Les pays voisins sont vivement intéressés par la technologie déployée.
L’Ingénieur Industriel Bernard Daulne travaille depuis 1994 à la SWDE (Société wallonne des eaux). Il nous guide à travers les installations de l’organisation : « Les 1.340 collaborateurs de la SWDE sont responsables de 1,1 million de branchements d’eau qui desservent un peu moins de 2,5 millions d’utilisateurs. Nous couvrons aujourd’hui environ 67% du territoire wallon et nous desservons 207 des 262 communes. Nous disposons d’un propre laboratoire où des dizaines de test de qualité sont réalisés chaque jour afin de répondre à la norme de qualité ISO 17025. »
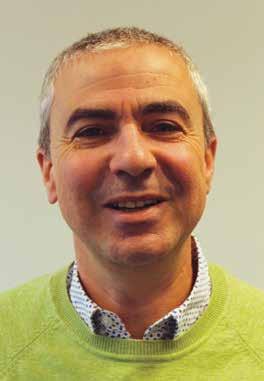
« Ces dernières années, la SWDE a repris des installations de plusieurs organisations et collectivités locales et nous gérons actuellement environ 1.000 installations. Ce chiffre est énorme et les défis sont nombreux car les emplacements sont souvent éloignés et les sites distants entre eux. Nous gérons par exemple des installations à Comines mais aussi à Arlon à 300 kilomètres de là. Par ailleurs, de nombreuses installations
Bernard Daulne:
« Grâce à ce projet, nous pouvons réagir plus rapidement dans des domaines comme les fuites d’eau et la sécurité. » étaient vétustes et il y avait des problèmes de maintenance. Ajoutons à cela le fait qu’il y avait peu de standardisation suite à la fragmentation historique des installations entre les communes et les organisations. Cela entraînait des problèmes, notamment au niveau de la communication des valeurs de mesure qui se faisait encore avec des systèmes comme l’ISDN (réseau numérique à intégration de services). Il n’était pas non plus possible de consulter les données en temps réel. Bref, il fallait absolument revoir tout cela. »
Lancement du projet Aveva jusqu’en 2027
« La solution est venue sous la forme d’un système de commande à distance. Nous sommes passés à un système unique et standardisé pour la commande des stations de pompage, les réservoirs et le traitement des eaux. Le système orienté objet Wonderware – connu aujourd’hui sous le nom Aveva - a été déployé. La mise à niveau fait partie d’un projet de dix ans qui s’étend de 2017 à 2027 et représente un investissement d’environ 100 millions. »
« Aujourd’hui, nos installations sont entièrement automatiques et surveillent elles-mêmes les débits, les pressions et les niveaux en permanence. Les systèmes locaux et autonomes analysent et résolvent les alarmes par l’activation ou la désactivation des pompes, l’ouverture des vannes, etc. Outre cette autonomie locale, nous avons prévu une couche supérieure pour piloter le système à distance ou reprendre la main si nécessaire. » « Un élément important de cette approche est la manière standardisée dont les données sont générées. C’est une grande amélioration car la rationalisation des données de mesure permet de mieux définir les paramètres. Il en résulte une disponibilité supérieure, une moindre consommation d’énergie et une meilleure estimation des niveaux. De plus, nous pouvons réagir de manière proactive avec des actions de maintenance préventives. »
Une automatisation standardisée
« Outre la standardisation de la communication, nous voulions simplifier la programmation des installations. Chaque installation a sa propre structure spécifique selon les besoins sur place mais il y a toujours une structure basique identique : le nombre de pompes centrifuges, les capteurs de niveau, les indicateurs de qualité, etc. Standardiser la programmation évite de devoir refaire à chaque fois le même travail. S’il faut activer à Malmédy une pompe au niveau X et faire la même chose à Mouscron mais au niveau Y, il n’est pas nécessaire d’écrire 2 programmes distincts. Les blocs logiciels sont configurés de telle sorte qu’il suffit d’adapter les variables à la situation sur place. Avec Esco Drives, nous avons conçu une bibliothèque qui rassemble les blocs de programmation. Plus besoin de réinventer l’eau chaude. Cette méthodologie présente de nombreux avantages : il y a moins d’erreurs de programmation et on gagne du temps. »

« Au lieu d’écrire des programmes pour chaque installation pendant des semaines, une heure suffit généralement. Calculez ce que cela représente pour une organisation qui gère 1.000 installations. Nous avons déjà présenté notre système aux Pays-Bas et d’autres régions sont vivement intéressées. »
La SWDE a fait appel à Esco Drives pour aider les collaborateurs à utiliser les installations de façon optimale. L’entreprise a fourni des écrans HMI Exor qui permettent d’accéder facilement au système. François Vin (Esco Drives): « A partir de ces écrans, les collaborateurs peuvent ajuster des paramètres de manière visuelle, consulter des données, entreprendre des actions, etc. La standardisation génère un fonctionnement plus fluide. Nous avons participé à la conception de la bibliothèque avec les éléments constitutifs. Il n’est plus nécessaire de réécrire chaque programme et la bibliothèque est ouverte à d’autres parties qui travaillent avec la SWDE. »
Fuites et enregistreurs de données
Chaque année, dans le pays et ailleurs, des millions de mètres cubes d’eau potable disparaissent dans la nature à cause de fuites. Concrètement, la Wallonie a perdu 66,7 millions de m³ d’eau potable en 2021 et la Flandre 57 millions m³. Ces chiffres semblent édifiants mais il est bon de les replacer dans leur contexte. Ils sont repris dans une comparaison via l’Indice de fuite dans les infrastructures (ILI), un indicateur international qui compare les pertes dues aux fuites d’eau dans plusieurs pays.
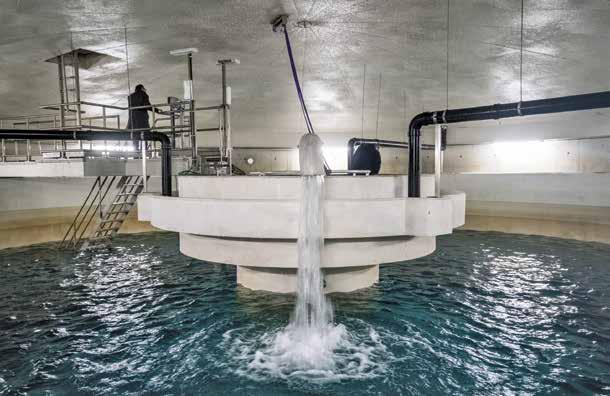
Par rapport à d’autres scores européens, la Belgique ne se porte pas trop mal. En 2021, la moyenne était de 1,1 et l’ILI montre des fluctuations importantes entre les compagnies des eaux (entre 0,34 et 1,50). L’objectif est de parvenir à un ILI moyen de 0,5 d’ici 2025. Les chiffres montrent une tendance à la baisse depuis quelques années et indiquent que les vagues de maintenance et de modernisation portent leurs fruits.
« Les fuites sont un sérieux défi à relever et nous avons également mis un projet spécifique en place », poursuit Bernard Daulne. « Via des enregistreurs de données, nous recevons quotidiennement de l’information sur les pertes, ce qui nous permet de détecter rapidement des problèmes potentiels et de prendre des mesures ciblées. Nous avons déjà pu économiser plusieurs millions de mètres cubes. »
« Dans le même temps, il faut détecter les nouveaux problèmes de manière proactive car l’une de nos missions est la préservation de nos resources. C’est important dans le cadre de la problématique du climat. Nous sommes pleinement engagés dans la récupération de l’eau, les solutions spécifiques pour l’agriculture, etc. »
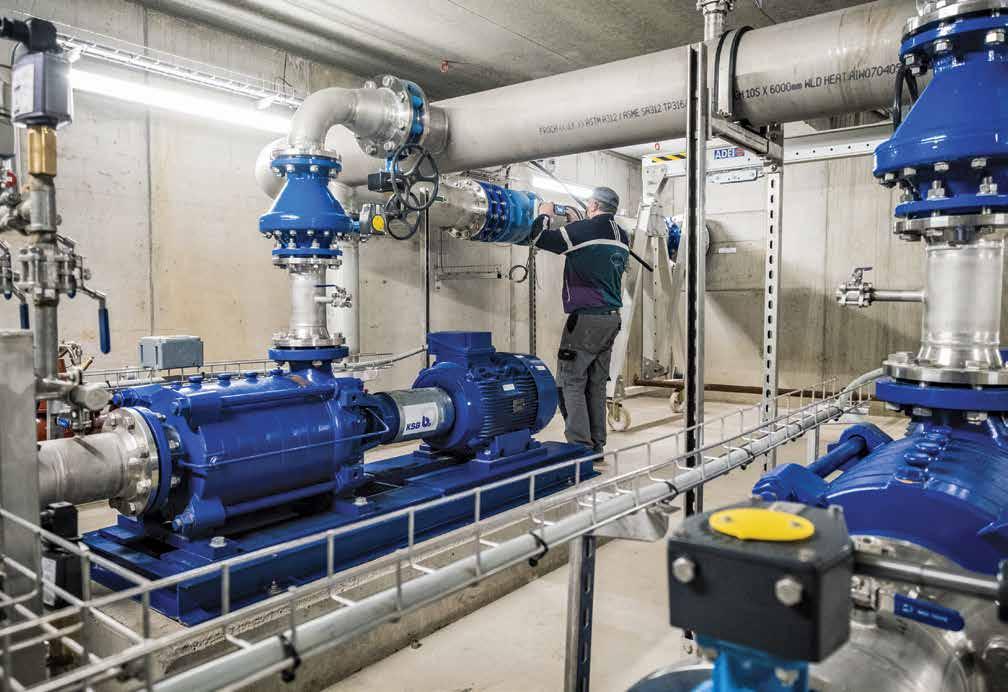
Esco Drives a aidé la SWDE à concevoir une bibliothèque avec des blocs d’automatisation qui rend la programmation nettement plus efficiente.
François Vin: « Les écrans HMI permettent d’adapter rapidement certains aspects de manière visuelle, de consulter des données, d’entreprendre des actions, … »
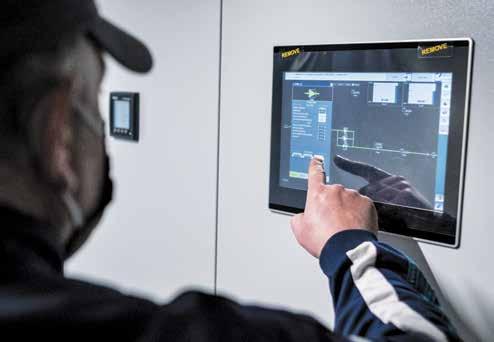
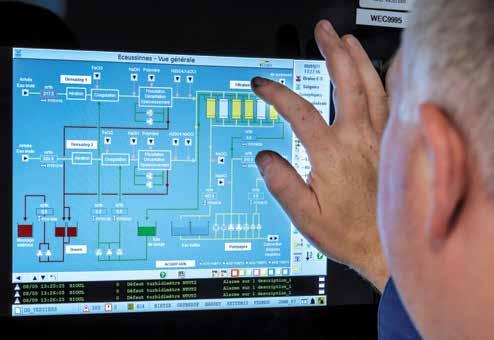
ET L’EAU INDUSTRIELLE ?
La production et l’épuration d’eau potable nécessitent plusieurs traitements dont la filtration, l’aération, la désinfection, la chloration et le dessalement. Les entreprises sont confrontées à un défi supplémentaire : quid si des processus exigent une autre qualité ou que l’eau de processus doit répondre à des normes de déversement strictes ?
L’entreprise Pantarein de Malines est active dans cette branche. Elle commercialise et loue des installations pour transformer les eaux usées en de l’eau potable ou de l’eau pouvant être déversée dans l’environnement. Les gradations sont nombreuses.
Le co-gérant Wim Mariën nous explique : « Chaque entreprise a une situation propre. Une brasserie, par exemple, possède souvent une pompe à eau souterraine. Elle transforme cette eau pour son processus de brassage avant de la rejeter en respectant la norme. L’eau utilisée qui est rejetée doit être conforme à la norme mais nous pouvons aussi la réutiliser dans des applications comme le nettoyage. Pour la brasserie, l’avantage est double : elle paie moins de redevances sur les rejets et elle peut mieux utiliser son quota maximum de pompage des eaux souterraines. »
« Les normes de rejet peuvent varier d’une région à l’autre, voire d’un cours d’eau à l’autre. De plus, la qualité de l’eau rejetée peut fortement varier. Une entreprise chimique a des besoins de traitement totalement différents qu’une entreprise de transformation de la viande. Et dans une même entreprise, la qualité peut fluctuer selon la production du moment. Voilà pourquoi le traitement des eaux usées est souvent une question de mesure et de techniques adaptées. Je vous donne un aperçu des principales méthodes. »
1 PRÉTRAITEMENT: ÉPURATION PARTIELLE AVEC UN SYSTÈME DAF (DISSOLVED AIR FLOTATION)
Une installation DAF assure un prétraitement physicochimique (coagulation et floculation) pour éliminer l’huile, les graisses, les particules en suspension et une partie des matières dissoutes (les métaux lourds par exemple) présentes dans l’eau usée. À l’étape de la coagulation, les particules colloïdales ou en suspension sont stabilisées par la neutralisation de leur charge via l’ajout d’un coagulant. On peut citer comme exemples de coagulants le FeCl3, le FeSO4, l’AlCl3, le Al2(SO4)3 et le coagulant organique. Typiquement, on ajoute 0,5 – 1,5 l de coagulant/m³ selon le degré de pollution de l’eau usée. Après l’ajout du coagulant (et la stabilisation du mélange en suspension), des flocs se forment. La coagulation est un processus rapide.
Les flocs formés sont submicroniques et ne peuvent augmenter de taille qu’en les agitant doucement pour permettre la floculation. Pour rendre ce processus plus efficient, on ajoute des floculants, c’est-à-dire des polymères à poids moléculaire élevé avec divers groupes fonctionnels. Typiquement, on ajoute 5 – 20 L floculant/m3 (0,2 % polymère) selon le degré de pollution de l’eau usée. Les particules chargées et/ou les flocs sont attirés par les groupes de charge du polymère, créant des flocs plus grands. La floculation est un processus lent.
2 Flottation
Après les étapes de coagulation et de floculation, l’eau usée est envoyée vers une unité de flottation avec de l’eau saturée en air (eau blanche). Cette eau blanche provient de l’effluent du DAF où de l’air comprimé est ajouté sous haute pression (> 5 bar). Des bulles d’air sont créées qui vont adhérer aux flocs dans l’eau usée et les ramener en surface. Un racleur en surface du DAF retire la boue et la dirige vers un bassin de boues.
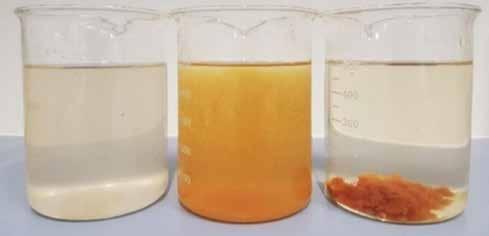
Wim Mariën: « Dans les brasseries, il y a peu de graisse dans l’eau et cette étape n’est en principe pas nécessaire mais c’est le cas dans les abattoirs ou les laiteries. Notre expertise nous permet de calculer précisément la structure d’un tel processus. »
3 Traitement A Robie Des Eaux Us Es
L’eau usée peut être traitée avec un système de boues activées, sauf s’il s’agit de gros volumes. Dans ce cas, il faut d’abord passer par une étape anaérobie où des bactéries déclenchent une fermentation. Le traitement aérobie pourra ensuite avoir lieu. Dans le système des boues activées, un ensemble diversifié de micro-organismes est capable, en fonction de la présence d’oxygène, de décomposer les composés organiques DCO (demande chimique en oxygène), en CO2 et en eau.
Chimiquement, cela se présente comme suit :
Compatibles avec SEW, Siemens, Bosch Rexroth, Lenze, Heidenhain, Beckhoff, B&R, Baumüller et plein d’autres ...
Cks2
Lock & start avec un seul système
Configurable par FlexFunction


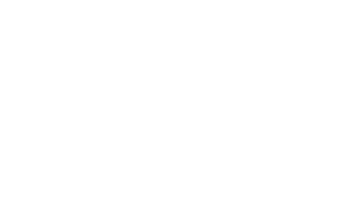
Possibilité de liaison série
Diagnostic complet avec IO-Link
Catégorie 4 / PL e / SIL3
Résistant aux fluides IP65 et IP67
Verrouillage, démarrage sécurisé, autorisation, etc.
Commandez rapidement vos câbles moteur prêt à être raccordés!
Envoi en 7 jours ouvrables.
Tél. 03-330 13 60 info@igus.be motion plastics®
4 SÉPARER L’EAU ET LES BOUES: LES TECHNOLOGIES CAS ET SBR (ET MBR)
Après l’épuration de l’eau usée par les boues activées dans le bioréacteur, il faut séparer l’eau épurée de la boue. Comme les boues ont une densité supérieure à l’eau, celles-ci vont décanter si aucune énergie de mélange ou d’aération n’a lieu dans le réacteur. On obtient alors une couche d’eau claire en surface qui peut être déversée. Ce principe est mis en œuvre de deux manières : via le CAS (procédé à boues activées conventionnel) ou le SBR (réacteur biologique séquentiel).
La technologie CAS
Le système CAS se compose de deux cuves, un bioréacteur et un clarificateur secondaire. Le mélange eau-boues s’écoule en continu du bioréacteur vers le clarificateur secondaire où, en l’absence d’énergie de mélange, les boues décantent et la couche d’eau claire supérieure est déversée (décantation dynamique). Les boues décantées sont repompées vers le bioréacteur à l’aide d’une pompe à circulation de boues.
Technologie SBR
Le système SBR (réacteur biologique séquentiel) combine la fonction de bioréacteur (épuration) et de clarificateur secondaire (décantation) dans une cuve. Pour pouvoir réunir ces fonctions dans une seule cuve, il faut les séparer dans le temps, ce qui entraîne une décantation statique. Dans un système SBR, plusieurs phases ont lieu :
• Alimentation : l’eau usée est pompée dans le réacteur tandis que les boues sont mélangées ou aérées. La charge en boues est élevée et la matière organique est adsorbée et partiellement dégradée par les boues.
• Aération : l’alimentation en boues activées est arrêtée. Le mélange et l’aération se poursuivent et les composants biologiques sont éliminés.
• Décantation : l’aération et le mélange sont arrêtés et la boue commence à décanter.
• Décharge : une pompe de décharge flottante évacue l’eau épurée du réacteur biologique.
La force de la technologie SBR réside dans le mode d’alimentation. L’alternance entre l’alimentation et l’aération permet d’obtenir une bonne structure des boues et de bonnes caractéristiques de décantation. Grâce à la bonne décantabilité, le cycle de décantation et de décharge est raccourci et la qualité de l’effluent est meilleure (moins de particules en suspension, de DCO, de N et de P).
Plus le temps d’alimentation est court par rapport au temps d’aération, plus les caractéristiques de décantation sont meilleures. C’est le principe de la régénération par accumulation.
La technologie SBR offre plusieurs avantages :
• une configuration simple par la combinaison de la fonction de bioréacteur et de clarificateur secondaire dans une cuve;
• une grande flexibilité par l’adaptation aisée des volumes traités et des temps de cycle SBR;
• une meilleure décantation des boues par le principe de régénération par accumulation et une décantation statique;
• le fonctionnement de l’installation est indépendant d’une charge hydraulique variable;
• un faible coût d’investissement et de maintenance du fait de la simplicité de l’installation.
Une alternative pour séparer l’eau de la boue : la technologie MBR
Contrairement aux systèmes conventionnels, la séparation eau-boues avec la technologie MBR n’est pas fondée sur une différence de densité. Le système MBR utilise une membrane d’ultrafiltration (UF) ou de microfiltration (MF) pour traiter l’eau du bioréacteur. Les avantages d’un système MBR par rapport à un système CAS ou SBR sont les suivants :
• Il est possible de faire fonctionner le bioréacteur lors de concentrations de boues plus élevées, ce qui permet de réduire le volume du réacteur (encombrement limité);
• La qualité de l’effluent d’un système MBR est meilleure que la qualité de l’effluent d’un système conventionnel compte tenu de l’absence de particules solides en suspension dans l’effluent;
• Il s’agit d’un prétraitement fiable lorsque la réutilisation de l’eau usée est une option (suite notamment à l’absence de particules en suspension).
5 CONCEPT GÉNÉRAL DE L’ULTRAFILTRATION DEAD-END
L’effluent du traitement biologique doit subir une étape de finition avant d’être traité dans une unité d’osmose inverse pour rendre l’eau potable. L’effluent contient encore trop de particules en suspension et pourrait colmater l’unité d’osmose inverse. Une unité UF dead-end élimine les derniers résidus de matières en suspension. La membrane UF les retient et laisse passer les ions et l’eau.
Le fonctionnement optimal de l’installation est contrôlé par une mesure de turbidité à l’alimentation de l’unité UF. En cas de concentrations élevées en particules en suspension (lors de la lixiviation des boues, par exemple), le fonctionnement peut être altéré. La mesure de turbidité permet de réagir rapidement et d’éviter des problèmes plus importants.
UF dead-end
Lors de la phase de filtration, l’eau traverse les membranes UF et les vannes V1 et V6 sont ouvertes. La pompe crée une différence de pression et pousse l’eau contre la membrane qui retient les matières en suspension. Pour éviter que les particules solides ne se fixent aux membranes, une pompe de circulation interne est activée (les vannes V4 et V5 sont ouvertes) et envoie de l’eau autour des modules à un faible débit. Comme les matières en suspension retenues ne sont pas évacuées en continu, la concentration augmente lentement dans la boucle de filtration. Un rinçage automatique des membranes est alors effectué à intervalles réguliers selon plusieurs étapes :
•Forward flush: La pompe de circulation interne est arrêtée et les vannes V4 et V5 sont fermées. La vanne de perméat V6 est fermée et la vanne V2 est ouverte tandis que la pompe d’alimentation reste active. Les matières en suspension accumulées sont détachées des modules à membrane et évacuées via la conduite de concentrat.
•Backwash: Lors de la dernière phase du rinçage vers l’avant, la vanne V7 est ouverte et la pompe de rinçage à contrecourant est activée. Les résidus des matières en suspension se détachent de la surface de la membrane et sont évacués via la conduite de concentrat.
•Démarrage de la filtration: A l’issue du rinçage à contrecourant, la pompe backwash est arrêtée, les vannes V7 et V2 sont fermées, la pompe de circulation interne est activée et les vannes V4, V5 et V6 sont ouvertes : le cycle de filtration classique peut reprendre.
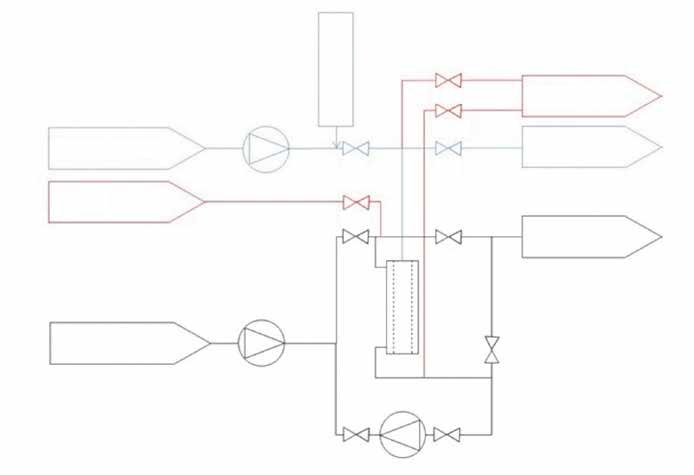
Après un certain nombre de cycles de rinçages à contrecourant, les membranes subissent un rinçage chimique standard qui consiste en un rinçage vers l’avant et un rinçage à contre-courant suivi d’un rinçage chimique. Après le rinçage à contre-courant, la pompe d’alimentation est désactivée, la vanne V1 est fermée et les modules à membranes sont remplis avec la pompe à contre-courant tandis que du NaOCl/NaOH ou H2SO4 est dosé (deux rinçages ont lieu successivement). Après le remplissage, les membranes trempent durant 10 minutes dans la solution puis les modules sont rincés.
Outre la réalisation d’un CEB (chemical enhanced backwash), il est possible d’effectuer un nettoyage chimique plus poussé à l’aide de l’unité CIP (Clean in place) centrale. Ici, une solution de nettoyage circule durant un certain temps parmi les modules de membranes. À l’inverse du CEB où la solution de rinçage est pompée du côté du perméat dans les modules de membranes, la solution de rinçage est introduite par le côté alimentation dans les modules, ce qui permet d’obtenir un meilleur effet sur la surface contaminée des membranes. La solution CIP peut à la fois circuler via le côté concentrat que perméat vers l’unité CIP. Comme un nettoyage CIP poussé n’est pas fréquent, aucune unité UF CIP n’est prévue mais l’unité CIP de l’installation d’osmose inverse est utilisée à cette fin.
Le perméat (liquide qui a été filtré, en passant à travers une membrane) produit est stocké dans la cuve d’alimentation de l’osmose inverse. Une partie du perméat est utilisé pour le nettoyage des membranes UF (rinçage à contre-courant et CEB) mais la plus grande partie peut être traitée ultérieurement dans l’unité d’osmose inverse. Il est conseillé de prévoir une cuve de 10 m³ afin que l’unité d’osmose inverse ne soit pas désactivée pendant le rinçage standard de l’unité UF. Lors d’un rinçage CIP plus poussé, une unité UF restera inactive plus longtemps et l’unité d’osmose inverse ne pourra pas fonctionner.
Pour contrôler le bon fonctionnement de l’unité UF, une mesure de turbidité du perméat est prévue. Si des matières en suspension sont détectées dans le perméat, la mesure de turbidité génère une alarme et des actions appropriées sont déclenchées. L’unité UF est également équipée de mesures de débit et de pression pour suivre le fonctionnement.
6 Osmose Inverse
L’osmose inverse (RO) est un processus de membranes à pression qui utilise des membranes denses. Tant les molécules organiques que les sels sont (partiellement) retenus, ce qui génère un perméat d’une pureté élevée. La technologie RO repose sur le fait que certaines matières sont retenues par les membranes. Comme elles ne sont pas décomposées, la concentration va augmenter et entraîner un flux concentré.
Ce flux de concentrat doit être évacué de l’unité de filtration et est généralement déversé. Plusieurs précautions permettent de garantir un bon fonctionnement de l’unité de filtration :
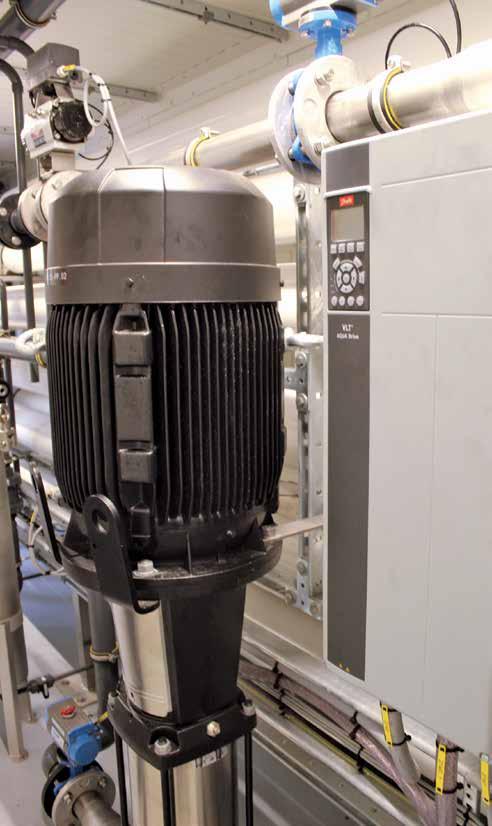
• Suite aux concentrations croissantes des matières retenues dans la boucle de circulation, certains sels peuvent précipiter. Pour éviter ces dépôts minéraux sur les membranes, un antiscalant est dosé dans l’alimentation. L’antiscalant est important pour aider les membranes utilisées dans le système RO à ne pas être exposées à la formation de tartre.
• A des intervalles réguliers, un CIP est lancé pour éliminer l’encrassement à la surface de la membrane. En fonction du type de pollution, un CIP acide (encrassement minéral) ou basique (encrassement organique) est appliqué;
• L’installation RO doit être équipée d’une configuration CIP à contre courant. On utilise une pompe CIP qui envoie la solution CIP dans le sens opposé à travers la filtration. Cette méthode de rinçage est appliquée car la plus grande partie de l’encrassement se situe dans la première partie des membranes. Si la solution CIP suit le même sens d’écoulement que le fonctionnement normal de l’unité, l’encrassement passera à travers tous les modules de la membrane avant d’être éliminé. Avec le sens inversé, l’encrassement est immédiatement éliminé des membranes.
Le fonctionnement optimal du RO est suivi par une mesure de conductivité de l’alimentation et du perméat. Une augmentation de la valeur du perméat (sans une augmentation dans l’alimentation) peut être causée par une moindre rétention des sels par les membranes, ce qui peut indiquer une dégradation du fonctionnement des membranes.
Une mesure continue et en ligne de la conductivité est dès lors un outil de surveillance facile et fiable. Le perméat est stocké dans un tampon d’où l’eau est pompée vers une cuve de stockage centrale ou l’application de réutilisation.
7 D Shydratation Des Boues Par Centrifugation
Les boues accumulées proviennent des diverses étapes du traitement de l’eau. Une masse de matière sèche trop élevée empêche la décantation de la boue dans un système SBR et freine les performances de la filtration par membranes d’un système MBR. Pour ces raisons, on essaie de maintenir dans chaque système une concentration constante en matière sèche en drainant l’excès de boues. Selon leur nature, les boues sont évacuées contre paiement vers une agriculture, un digesteur, un site de compostage ou un site d’incinération.
La méthode la plus simple est une élimination directe des boues liquides. Celles-ci contiennent en grande partie de l’eau. En augmentant la teneur en matière sèche (par épaississement ou déshydratation), il est possible de réduire le tonnage de boues à éliminer et donc le coût d’évacuation. La flottation des boues biologiques dans une installation DAF (s’il y en a une) permet une épaississement dans une certaine mesure. Mais le coût d’évacuation ne peut être drastiquement réduit que par l’installation d’unité de déshydratation.
Le travail sur mesure nécessite une technologie de qualité. Des moteurs IE3 de Siemens et les terminaux de distributeurs de SMC sont notamment intégrés dans la solution de location de Pantarein.
Principe de la centrifugation
Concept d’une centrifugeuse.
Étape 1 : Le mélange boues-eau entre dans la centrifugeuse par une conduite d’entrée (n° 12 dans la figure) puis est introduit dans un répartiteur (n° 16). Le mélange est ensuite envoyé aux chambres de séparation (n°9) dans le tambour.
Étape 2 : Le tambour (n° 6) tourne en continu à une vitesse élevée (4000-4500 tours par minute). Les rotations génèrent une force centrifuge sur le mélange boues-eau. Les particules plus lourdes sont projetées contre la paroi du tambour.
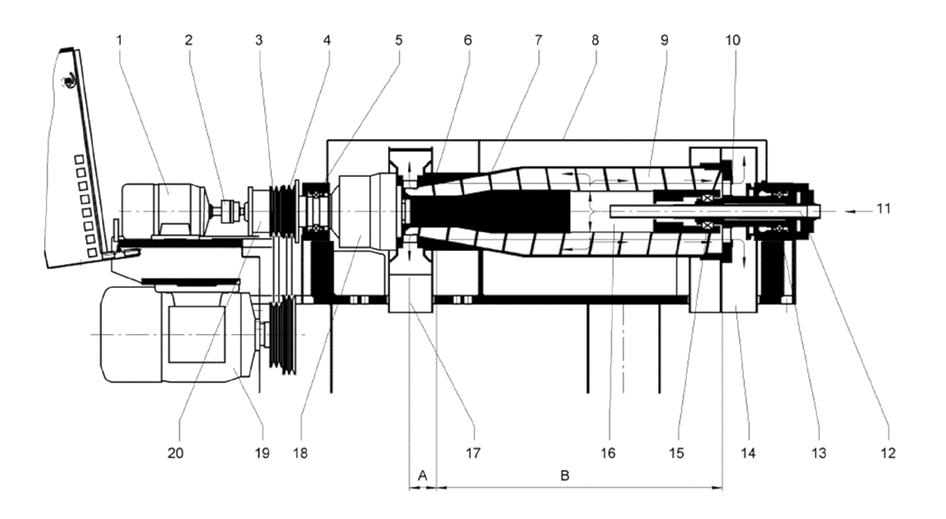
Étape 3 : La vis (n° 7) et le tambour tournent dans le même sens mais à un régime (légèrement) différent. La vis sans fin déplace les particules solides sur la paroi interne du tambour
TOUTES CES ÉTAPES SONT-ELLES NÉCESSAIRES DANS CHAQUE INSTALLATION ?
Wim Mariën (Pantarein): « Non, certainement pas. Cela dépend de plusieurs facteurs : la qualité et la composition de l’eau fournie, la qualité finale souhaitée, l’espace disponible, l’environnement mais aussi l’investissement que l’on souhaite faire. L’élimination des boues coûte cher en évacuation et transport et une centrifugeuse à boues sera rapidement amortie dans certains cas. Il y a peu de travail standard dans notre secteur et c’est la raison pour laquelle nous travaillons avec une équipe de bioingénieurs spécialisés dans le traitement de l’eau et une équipe technique d’ingénieurs en électromécanique. Ce secteur a énormément évolué d’un point de vue technologique. » vers l’élément conique (la zone de déshumidification A) à l’extrémité gauche du tambour. Les boues déshydratées sont récupérées dans un bac via une vis.
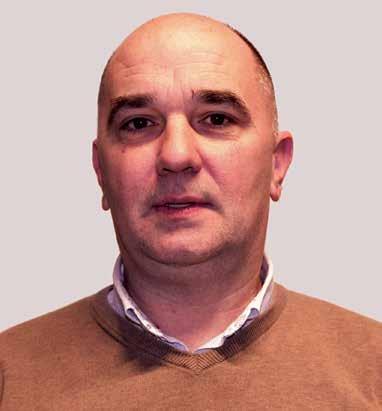
Étape 4 : Le centrat, composé principalement d’eau, est poussé au milieu de l’arbre de la centrifugeuse par la boue (plus lourde). Il quitte la centrifugeuse par les ouvertures du diaphragme à l’extrémité droite de la centrifugeuse. Le disque réglable/diaphragme (n° 10) détermine l’épaisseur de la couche d’eau. Le centrat est recueilli dans un puisard et renvoyé vers la station de traitement à hauteur de l’alimentation de la flottation 1.
Particules en suspension
Les particules en suspension dans les eaux usées sont déterminées par la filtration de l’eau et le séchage du filtre (et le matériau filtré) puis le pesage jusqu’à obtenir un poids constant. Les particules en suspension sont des matières non dissoutes (pas uniquement des matières non décantantes).
La présence élevée de particules en suspension peut être une indication de prétraitement de l’eau (tamisage, prédécantation, …).
DCO
La demande chimique en oxygène est une mesure de la quantité de composés organiques dans les eaux usées et est définie comme la quantité d’oxygène (O2) nécessaire à la transformation (oxydation) des composés organiques en CO2 et en eau. La DCO est exprimée en mg O2/l.
Azote
L’azote est un élément nutritif important pour les microorganismes. Les bactéries ont besoin d’azote pour produire (développer) du nouveau matériel cellulaire. Les microorganismes utilisent l’azote pour leur métabolisme cellulaire dans un rapport de 2-3 % N/COD (ou Nf/CODf après filtration) pour un traitement aérobie. S’il y a peu d’azote dans les eaux usées, il faut alors en ajouter pour ne pas perturber le processus de dégradation biologique. À l’inverse, l’excès d’azote est nuisible à l’environnement. Un effluent riche en azote conduit à un enrichissement des eaux de surface (cours d’eau et rivières) et peut entraîner une eutrophisation (croissance excessive d’algues). Dans un tel cas, il faut adapter le traitement de l’eau pour éliminer biologiquement l’azote des eaux usées.
L’azote peut être présent dans l’eau sous différentes formes : comme azote organique, ammonium, nitrate ou nitrite. L’azote organique peut être transformé en ammonium (minéralisation) par une dégradation microbienne. Dans les eaux usées à forte teneur en N (protéines contenant de l’azote), du NH4+-N est libéré, le pH peut augmenter et il faut être attentif à l’inhibition du NH3
L’azote dans un réacteur aérobie www.aquafin.be www.dewatergroep.be www.esco.be www.farys.be www.pantarein.be www.siemens.be www.smc.be www.swde.be
L’ammonium peut être transformé par les bactéries aérobies en nitrite puis en nitrate (nitrification). Des concentrations d’ammonium supérieures à 10 mg/l peuvent inhiber la nitrification. Enfin, la dénitrification est la conversion microbienne du nitrate en azote gazeux. Nous distinguons les paramètres des eaux usées: l’azote ammoniacal (NH4+-N), l’azote nitrite (NO2--N), l’azote nitrique (NO3--N) et l’azote total Kjeldahl (TKN). L’azote total (TN) est la somme de l’azote nitrique, de l’azote nitrite et de l’azote ammoniacal. L’azote total Kjeldahl (TKN) désigne la somme de l’azote ammoniacal et de l’azote organique.
Phosphore
Outre l’azote, les bactéries ont besoin de phosphore comme élément nutritif. Les micro-organismes utilisent le phosphore pour leur métabolisme cellulaire dans un rapport de 0,5-0,8 % P/COD (ou Pf/CODf après filtration) pour un traitement aérobie. Un excès de phosphore peut également donner lieu à une eutrophisation des eaux de surfaces et doit être évité. Nous distinguons comme paramètres des eaux usées : l’orthophosphate (PO43-) et le phosphore total (TP). Il s’agit de la somme du phosphore organique et de l’orthophosphate. L’excès de phosphate est généralement éliminé par un dosage de fer en biologie. Le dosage de fer à hauteur de l’installation DAF contribue également à la diminution des phosphates. Par conséquent, la concentration de TP après l’installation DAF est plus basse que la concentration de TPf dans les eaux usées.
Conductivité
La conductivité est une mesure de la quantité d’ions présents dans les eaux usées. Plus il y a d’ions, plus d’énergie il faut pour filtrer l’eau dans une installation RO en vue d’une réutilisation.
Valeur du pH
Le pH est une mesure de l’acidité ou de la concentration d’ions H+ dans l’eau. Un nombre important de H+ signifie une acidité plus élevée et un pH plus bas. Le pendant de H+ est l’OH-. Une multitude de OH- signifie une eau basique et donc un pH élevé (un pH de 12 est par exemple très élevé). H+ et OH- forment ensemble du H2O, de l’eau. Autant de H+ que de OH- donne une eau au pH neutre de 7 (pas acide ni basique). Pour les processus biologiques (tant aérobies qu’anaérobies), la plage de pH optimale se situe entre 6,5 et 7,5. Le pH est également important pour les effluents déversés. Les conditions générales de rejet stipulent par exemple que le pH des eaux usées rejetées doit être compris entre 6,5 et 9.
Le concept combine l’expertise des bioingénieurs et des ingénieurs en électromécanique.
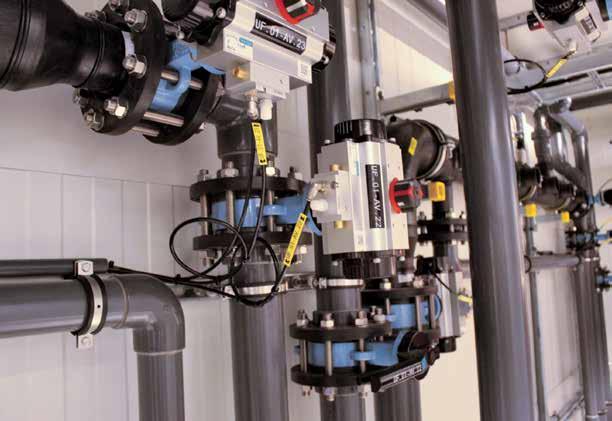