
2 minute read
Australian Laboratory Twin Screw Extruders Lead the Way for Polymer Material Research Applications
Australian Laboratory Twin Screw Extruders Lead the Way for Polymer Material Research Applications Source: Barrell Engineering
Superior mixing and reduced free volume.
When researching new polymers and extruding filaments or fibres or films, there are often some limiting factors that place specific demands on the extruding equipment.
Typically, research is done with small amounts of material, which can take a long time to generate, so ensuring the best use of the available material is very important. One client had a material that took six months to create half a cup, so being able not to waste any was a primary goal.
Traditionally, twin screw extruders have two co-rotating screws which are able to provide high volume outputs, this is preferred in production machines. However, even when scaled down to laboratory sizes, there can still be a considerably large free volume, requiring more material to be able to perform the process. There is also the issue of mixing efficiency. Small screws have a low wingtip speed, which reduces the mixing ability of the screws. Finally, there is the pulsing pressure created, meaning additional devices such as a melt pump are needed to ensure constant pressure and flow, to extrude accurate and consistent filaments or fibres.
Recognising these limitations, Barrell Engineering designed a laboratory extruder that uses counter-rotating screws. The resulting intermeshing screws reduce the free volume significantly and also the amount of material needed to be able to process. The next step was to make the screw sections modular so that different mixing and pressure profiles could be easily created without requiring custom made screws. These features allow for significantly improved mixing profiles and techniques, and improve the capability of adding additional materials to the extruder flow through the additional intake ports. The reduced free space volume, plus the counter-rotating screws, also reduce pressure pulsing, to the point that often an additional melt pump is not required to create accurate extruded filaments.
Despite the different extruder method, scaling up from a counter
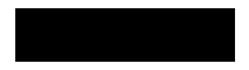
Top: Extruder installation at a materials research laboratory. Below Right: Examples of mixing screw modules.

rotating extruder to co-rotating extruders for production volumes is not an issue, as the resulting mixing profiles are similar.
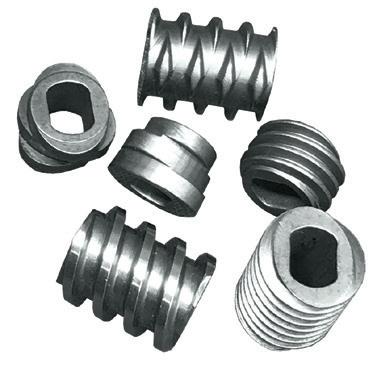
Some of the applications, in which these extruders are being utilised, include the development of new materials for 3D printing, and conductive fibres such as artificial nerve reconstruction.
www.barrell.com.au | sales@barrell.com.au

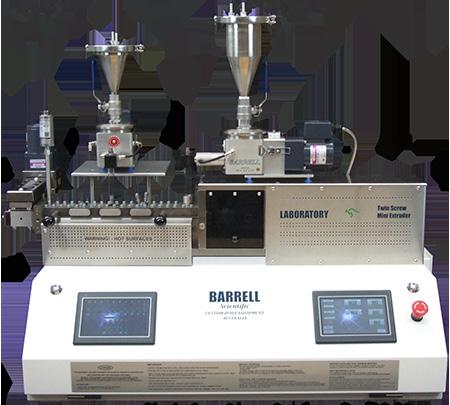