
33 minute read
Feature
Sustainable Materials
Now and Into the Future
Materials are essential for daily life. The global community relies on a broad range of materials to develop critical infrastructure and devices like shelter, communication, education and nourishment. However, traditional materials manufacturing and its practices are growing old. This has prompted scientists, researchers and industry alike to begin shifting to a more sustainable manufacturing and production future, which is led by innovation and a desire to protect the global environment, economy and health.
There are a range of benefits for advancing towards a more sustainable future. Today, the world’s population growth sits at around 1.4 per cent. But in some parts of the world, like Africa, the population growth rate is even higher, at three per cent. A rapid global population increase leads to greater overall production and energy usage. Higher energy consumption – catalysed by inefficient processes – equates to the production of greenhouse gases, which have a damaging impact on the climate and environment. High energy usage during materials production also impacts biodiversity, land-use change and biogeochemical flows, which refers to how chemicals and elements flow between living organisms and the environment. The United Nations have concluded that resource extraction for manufacturing purposes has more than tripled since 1970, including a 45 per cent increase in fossil fuel use. Secondly, the economic impacts of eliminating waste and inefficient processes are an important part of protecting the environment. Improving resource productivity – commonly referred to as a ‘circular economy’ allows materials and products to be recovered from waste and transformed into a new material. This makes waste a ‘raw material’, and value-adds new and improved green materials back into the market. While the notion stems from the concepts of reusing and recycling at a community level, it also extends to manufacturing, which ensures the waste becomes a feedstock for new materials. Materials recycling also creates jobs, with around 12 million people employed in the sector in Brazil, China and the United States. While Australia has a National Waste Policy, introduced in 2018, the nation has room for improvement. Across the 2018-2019 financial year, Australia produced 76 million tonnes of waste, a ten per cent increase on 2016-2017, according to the Australian Bureau of Statistics. The manufacturing (12.8 tonnes) and construction sectors (12.7 tonnes) produced the most amount of waste. Masonry materials, like concrete and bricks; organics; and ash from coal fired power stations were the three highest pieces waste of generated. In all, over half of all waste was sent for recycling, while 27 per cent was sent to landfill. However, history shows that there are always new innovations in technology that drive change towards a more sustainable and better future. Finding new practices that minimise cost, and damage to the environment is a forever changing narrative. Australian research institutions are taking the lead when it comes to building a safer, greener and more sustainable materials market. Together, the vast research expertise, and real-world outcomes are generating materials that address the environmental, economic and health factors for a better world.

ANSTO
The Australian Nuclear Science and Technology Organisation (ANSTO), brings thousands of researchers and scientists together under the same roof to transform leading research to life. Together, ANSTO is crucial to driving Australia’s health, nuclear and environment innovation towards a safer and sustainable future. ANSTO contributed to a large international collaboration on advanced sodium ion batteries led by French researchers, which provides a direction for the design of high-performing sodium ion electrodes. Advanced sodium ion batteries could be used for large scale energy storage. A new type of electrode material with a high energy density that is also moisture stable was synthesised and characterised by the researchers using a range of techniques. The material, O3NaLi1/3Mn 2/3O2, is a sodium-rich layered oxide that did not show voltage fading on cycling. Researchers collected neutron diffraction data using the Echidna high-resolution diffractometer operated at ANSTO’s Australian Centre for Neutron Scattering to elucidate the distribution of metals in the structure. The data, which reveals the position of the metal atoms during cycling, was combined with other experimental and computational techniques. Similarly, researchers at ANSTO conducted an analysis that could extend the service life of welded structure in steels, hence providing durable and sustainable options for the future. This innovation identifies the core material requirements to predict solid-state phase transformation kinetics during the welding of ferritic steels, which are chromium-rich and nickel-free. Researchers found that further tests can be carried out to understand the residual stress profiles predicted in a coupled thermo-mechanical weld model. Then, additional research can be undertaken to understand the risk that welds face in relation to ongoing cracking or damage. This innovation will strengthen the industry’s capacity with long-term solutions, reduce greenhouse gas emissions, and company input costs.
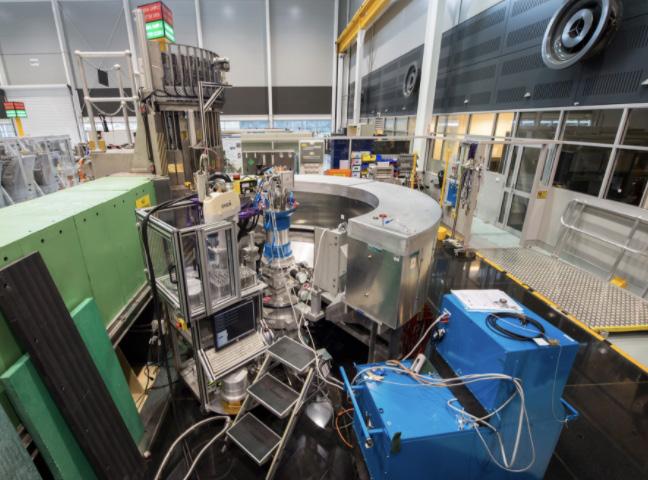
ANSTO’s Echidna high-resolution powder diffractometer. Image credit: ANSTO.
CSIRO

Australia’s national science agency, CSIRO, seeks to imagine, collaborate and innovate towards the greatest challenges in the disciplines of science and technology. CSIRO have created a new material-based solution to help reduce carbon emissions and efficiently store and separate gases. The metal organic frameworks (MOF) are sponge-like materials that have the capacity to capture carbon dioxide and remove harmful contaminants from the living environment. “There’s so much surface that there’s actually a football field worth of surface area in about a teaspoon worth of material. What we do is use all of that surface to soak up a target molecule,” said Associate Professor Matthew Hill, who leads a team of researchers that work on porous materials. The innovation has a vast suite of applications across the energy, manufacturing, water treatment, agriculture and pharmaceutical sectors. CSIRO are already working with the gas industry to understand if the MOFs can be used to replace processing plants with smaller, truck-sized systems. In addition, CSIRO is developing a sustainable coating and surface adhesive technology that can assist the aerospace, construction, energy and mining industries. The specialised coatings and smart polymers protect a variety of surfaces from contaminants like insects, dirt or ice. The surface coatings are also cost-effective in the long-term, as they reduce ongoing maintenance and labour costs, and decrease hazardous and unsustainable waste that meet industry requirements. Researchers have also worked with counterparts at the Beijing MCC Equipment Research & Design Corporation to reduce overall greenhouse gas emissions in steel manufacturing. A dry slag granulation mechanism is retrofitted into blast furnaces, which separates the waste matter into droplets. Air is used to solidify these droplets before a cleaner granulated slag product is extracted, which may be used in products like cement. CSIRO’s Director of Mineral Resources, Jonathan Law said the research was a breakthrough for planet-friendly steel production. “Our collaboration is an exciting step towards the uptake of an innovation with real prospects of transforming the productivity and environmental performance of global iron smelting.
CSIRO Researcher with metal organic frameworks (MOFs). Image credit: CSIRO.
The dry slag granulation rig is fitted to blast furnaces to produce granulated slag and heated air. Image credit: CSIRO.

Deakin University
Deakin University’s Institute for Frontier Materials (IFM) generates more than 30 PhD students each year, and trains around 80 post doctorial researchers at any one time. As such, IFM is well equipped to lead Deakin’s charge in the sustainable materials space through cutting edge research. The centre has six areas of research: • Advanced alloys • Electromaterials • Carbon fibres and composites • Infrastructure materials • Fibres and textiles • Micro/nano materials. In 2019, IFM gained $16.5 million from external research income, through its strong collaborations with other research-intensive institutions. The IFM team have worked with industry partners like Calix Pty Ltd and Boron Molecular to create a new type of battery material that intends to substantially reduce the cost and environmental impacts of other high performance batteries. The research project secured $3 million from the Federal Government’s Cooperative Research Centre program, which links industry with academia to produce results for better technologies, products and services. Professor Maria Forsyth, who leads the IFM team, said the challenge with energy storage was to develop manufacturing capability in Australia. “There is a global search for safe, low cost, high capacity, high performing batteries given the demand for high performance energy storage and electric vehicles,” she said. “The challenge for Australia is to develop a sustainable battery manufacturing industry that has global reach through process innovation.”
In another project, Dr Maryam Naebe developed a new woolbased insulation textile for car interiors. This innovation seeks to address the automotive industry’s need for sustainable alternatives to synthetic and petroleum-based plastics. It is also cost effective, and opens a potential new market for wasted wool.

“Our aim was always to do something that has an impact for industry and for people – we really want to see an improvement in people’s lives and the environment,” said Dr Naebe. The new wool felt is an environmentally-friendly insulating material that is made from a range of available natural resources. It also has increased benefits than the current synthetic textile options, like being flame resistant.
The Institute for Frontier Materials at Deakin University. Image credit: Deakin University.
Dr Maryam Naebe developed a new wool-based insulation textile for car interiors. Image credit: Deakin University.

Deakin University’s Hycel Hydrogen Hub
As one of Australia’s first facilities for safely testing, manufacturing, optimising and training in new hydrogen technologies, Hycel is focused on technologies that use hydrogen rather than processes that produce it. Hycel will be a ‘living laboratory’ that translates lab results into real-world solutions. Hycel’s Establishment phase is supported by $2 million in Commonwealth Government funding. At a global level, the hydrogen market is predicted to reduce carbon emissions by 6 billion tonnes annually, employ up to 30 million people and be worth around $US2.5 trillion by 2050. With a focus on hydrogen usage in transport and gas industries, Hycel’s technological innovations aim to deliver clean, affordable energy solutions that meet Australian and Victorian emissions reduction targets and develop Australia’s hydrogen economy. Hycel leverages Deakin University’s expertise in advanced materials, energy systems, IT and social sciences.

Monash University
Monash University’s metallurgy research is ranked number one in Australia, and in the top ten around the world. The Department of Materials Science and Engineering drives Monash’s high standards and sustainable approaches to steelmaking. Researchers work across six research themes in the materials science and engineering space: • Additive manufacturing • Biomaterials • Functional and energy materials • Metals and alloys • Polymers • Materials theory, modelling and characterisation. Professor Christopher Hutchinson, an expert in materials science, leads the Department, where he specialises in physical and mechanical metallurgy, and 3D metal printing. Professor Hutchinson and his team recently improved the fatigue life of high strength aluminium by 25 times – a new development in the area of sustainable materials. The development is a game changer, as aluminium alloys are the second most popular engineering alloy used in the industry. Professor Hutchinson said when aluminium alloys are used for transport, the design must compensate for the fatigue limitations of aluminium alloys. Hence, more material is used than manufacturers would prefer, leading to heavier structures. “Eighty per cent of all engineering alloy failures are due to fatigue. Fatigue is failure due to an alternating stress and is a big deal in the manufacturing and engineering industry,” he said. Students are also crucial to driving Monash’s sustainability and advance materials agenda, which is evident through program’s like ‘Monash Forge’. This is student-run materials engineering project’s core vision is to inspire a new generation of manufacturers for a sustainable world. Together, the student group develop fundamental, practical and soft skills with an industry focus. The practical opportunities delivered through Monash Forge align research with manufacturing good practice to increase quality, but with minimal environmental impacts. Key areas of research include building a circular product life cycle into all stages of design, and reducing the impact of high-energy needs across industry. A range of companies hire the materials science and engineering graduates from Monash – like Qantas, Telstra, CSIRO, Toyota and BHP Billiton – which is where they put their sustainable materials knowledge to the test.

Monash University researchers recently improved the fatigue life of high strength aluminium by 25 times – a new development in the area of sustainable materials.

University of Queensland
The University of Queensland is committed to generating research outcomes for wider use across industry, and improving the environmental performance of their own campuses and operations. The University’s Sustainable Materials Institute (SMI) – made up of six key research areas and the technology company JKTech – drives sustainable resource development and training for a new generation of materials. SMI develops solutions to global challenges facing the environment, economy, and population towards a path of sustainability. Students are leading the charge at SMI, like the Mine-R initiative, which was developed by Roger Tang and Imam Purwadi at SMI’s Centre for Mined Land Rehabilitation. Tang and Purwadi’s Mine-R product improves satellite imaging technology to readapt and rethink how data on mine rehabilitation is collected and analysed. “Mine-R is really about supporting the mining industry by offering a product that encourages sustainable practices but which is also financially viable. “We are not trying to replace the traditional approach to rehabilitation monitoring – it is more accurate to use drone imaging or, better yet, a team of environmental scientists – but we are focusing on rapid reporting of the bigger picture to make strategic decisions faster,” Tang said. The start-up received $10,000 worth of equity-free funding through the University’s Ventures ilab Accelerator program. In addition, the University’s sustainability office conducts an end-of-year review on campus waste, and examines the campuses waste-to-landfill bins. It found that over 75 per cent of landfill waste on campus for the academic and administrative buildings is made up of organic and recyclable items. But the University’s commitment to zero waste seeks to reduce the items from landfill waste, and find more sustainable alternatives. In 2020 alone, researchers, students and other occupants of the Sir James Foots and McElwain Buildings reduced their landfill but more than half. The Towards Zero Waste program also increased composting from zero to 38 per cent after the program’s implementation.
University of NSW
The University of New South Wales’ (UNSW) Centre for Sustainable Materials Research and Technology, or SMaRT, is a leader in the sustainable materials space. The Centre draws on UNSW’s expansive research capabilities and facilities, and combines them with end-user research for high quality delivery. The Centre was founded in 2008 by Australian Research Council Laureate Fellow, Scientia Professor Veena Sahajwalla. Today, it works with industry, global research partners, not-for-profits, local, state and federal governments to develop innovative environmental solutions for some of the world’s biggest waste challenges. As an internationally recognised centre, it brings enhanced technology to traditional processes like steel manufacturing, recycling and waste management. SMaRT recently collaborated with Spark Furniture in South Australia and the ACT Government’s City Renewal Authority, to turn wasted coffee cups into new rubbish bins in the City of Canberra. The ‘green ceramic tiles’ were engineered during the national COVID-19 lockdown, where single use coffee cups were transformed into tiles that formed the outer layer of Spark Furniture’s newly-designed bin enclosure. Similarly, SMaRT found a new method to sustainably recycle polymer-laminated aluminium packaging materials, like postconsumer food and coffee packaging, into high-quality aluminium, and other high-energy hydrocarbon products. The innovation is based on the microrecylcing science pioneered by Professor Sahajwalla, and builds on other SMaRT innovations like green steel and microfactory technologies. “We developed green steel technology where we extract hydrogen and carbon from old rubber tyres and plastic as an innovative and green pathway in steelmaking, and we now can develop new ‘green aluminium’ with our novel technique called Thermal Disengagement Technology.” “Recycling using new technologies can be a foundation for the manufacturing of high-quality materials from our waste resources, as we seek to develop greater sovereign capability along with economic prosperity,” Professor Sahajwalla said.

Professor Sahajwalla from the University of New South Wales’ (UNSW) Centre for Sustainable Materials Research and Technology, or SMaRT. Image credit: UNSW.
RMIT University
RMIT University incorporates sustainability principles and practices into the learning and teaching of over 84,000 students. Scientists at the School of Engineering recently discovered a method of turning back the emissions clock to transform CO2 back into solid particles of carbon. The process uses liquid metals to make the transformation, which could be a game changer for carbon capture and storage. Dr Dorna Esrafilzadeh, a Vice-Chancellor’s Research Fellow in RMIT’s School of Engineering, led this research. Dr Esrafilzadeh developed the electrochemical technique to capture and convert atmospheric CO2 to storable solid carbon. After designing a liquid metal catalyst with specific surface properties, the carbon dioxide was dissolved in a beaker filled with an electrolyte liquid and a small amount of the liquid metal, which was charged with an electrical current. The CO2 then converts into solid flakes of carbon, which are naturally detached from the liquid metal surface. Dr Esrafilzadeh said the result could be used for a variety of purposes, like electrodes. “A side benefit of the process is that the carbon can hold electrical charge, becoming a supercapacitor, so it could potentially be used as a component in future vehicles. The process also produces synthetic fuel as a by-product, which could also have industrial applications.” Researchers at RMIT have also shown recently how disposable face masks could be recycled to make roads, in a circular economy solution to pandemic-generated waste. Using the recycled face mask material to make just one kilometre of a two-lane road would use up about 3 million masks, preventing 93 tonnes of waste from going to landfill. The new road-making material developed by RMIT University researchers - a mix of shredded single-use face masks and processed building rubble - meets civil engineering safety standards. Analysis shows the face masks help to add stiffness and strength to the final product, designed to be used for base layers of roads and pavements. The use of personal protective equipment (PPE) has increased dramatically during the COVID-19 pandemic, with an estimated 6.8 billion disposable face masks being used across the globe each day. First author Dr Mohammad Saberian said multidisciplinary and collaborative approaches were now needed to tackle the environmental impact of COVID-19, particularly the risks associated with the disposal of used PPE. “This initial study looked at the feasibility of recycling single-use face masks into roads and we were thrilled to find it not only works, but also delivers real engineering benefits,” Dr Saberian said. “We hope this opens the door for further research, to work through ways of managing health and safety risks at scale and investigate whether other types of PPE would also be suitable for recycling.”
Australian Research Council DECRA Fellow Dr Torben Daeneke and Vice-Chancellor’s Research Fellow Dr Dorna Esrafilzadeh. Image credit: RMIT University.
A sample of the recycled road-making material, which blends shredded single-use face masks with processed building rubble. Image credit: RMIT University.

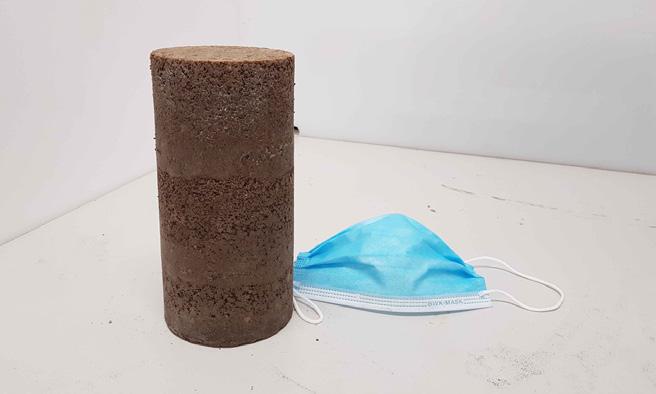

SBRC Director Senior Professor Paul Cooper. Image credit: Paul Jones and University of Wollongong.
University of Wollongong
The Sustainable Buildings Research Centre at the University of Wollongong seeks to address the challenges of modernising buildings and the built environment into clean, sustainable, and resilient structures where people choose to live and work. The Centre’s mission is to assist in the rapid decarbonisation of the built environment. It has a range of facilities that drive this mission and the University’s commitment towards a resilient future. The Building Insights Facility focuses on larger building elements, where it tests capabilities including their thermodynamic, environmental and hygroscopic performance. Similarly, the University’s micro-grid and energy laboratory allows researchers to test electrical loads and generators, and make grid calculations based on their performance. Researchers work together to source renewable energy systems including solar PV, solar thermal, geothermal and wind for a brighter and more sustainable future. Senior Professor Paul Cooper is the Director of the Sustainable Buildings Research Centre, who set a target for his design team to create a building that went beyond the existing benchmarks for sustainable buildings. “Sustainable means effectively you’re not doing any net harm overall – but restorative means you’re doing something that’s addressing some of the environmental damage that has been done in the past,” he said. The Sustainable Buildings Research Centre itself is a net-zero energy building, with access to a working micro-grid and a range of photovoltaic systems. “The building has been carefully designed to generate positive health and wellbeing through a restorative and healthy coexistence with nature, including the use of green walls and native plants, creating a strong connection between the building occupants and the landscape,” Professor Cooper said.
Above: University of Wollongong’s Sustainable Buildings Research Centre. Image credit: University of Wollongong.
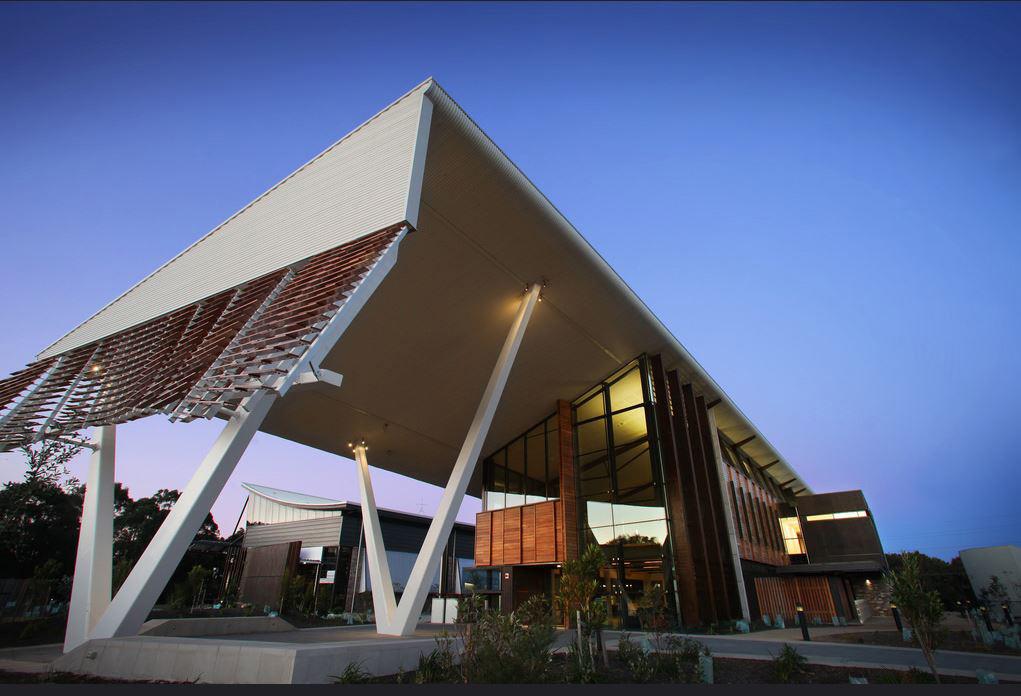
UNSW to Lead New Government Research Hub on Waste
Source: Sally Wood
Professor Veena Sahajwalla at UNSW will spearhead a new national research centre investigating technology for waste reduction and materials processing.
UNSW will take a lead role in research into sustainable communities and waste, as part of the second phase of the Federal Government’s $149 million National Environmental Science Program (NESP). Professor Sahajwalla will lead the Sustainable Communities and Waste Hub, which has previously pioneered microfactories for turning plastic waste into 3D printing material, green-steel technology that recycles tyres and plastics, and transforming textile waste into tiles and benchtops. Professor Sahajwalla is an Australian Research Council Laureate Scientia, a materials scientist, engineer, inventor and the founder and director of UNSW’s Centre for Sustainable Materials Research and Technology. She said she was delighted with the announcement of four mega science hubs, with waste being a key priority. “Waste and recycling have been made a national agenda item by government and through this new Hub we will create actionable knowledge, methods, tools and data for transformation towards circular economies in our cities and regions. “Our capabilities, proposed research activities and transition pathways will deliver the environmental, social and economic outcomes and impacts that are sought by the NESP which funds the Hub,” Professor Sahajwalla said. The Sustainable Communities and Waste Hub consortium is comprised of six research institutions led by UNSW Sydney – working in partnership with CSIRO, Monash University, Swinburne University of Technology, Curtin University and the University of Tasmania. It will coordinate research on reducing the impact of plastics and enhancing sustainable people-environment interactions. It will also develop ways to minimise the impacts of hazardous substances and pollutants, and deliver cutting-edge technical capabilities, particularly in the fields of waste and materials processing. “Australia is world-leading in economic performance, health and liveable cities, but this comes at significant environmental cost with per capita material, carbon and water footprints that are among the highest in the world. “Every Australian generates 2.7 tonnes of waste a year, with only 58 per cent of that recovered from landfill, which is low by international standards,” Professor Sahajwalla explained. Around 87 per cent of plastic ends up in landfill. Experts believe an estimated 99 per cent of all seabird species will have ingested plastic from the marine environment by 2050. These losses equate to lost value in materials from the supply chain, which are replaced with virgin materials, placing additional burden on natural, human and economic resources. Even a 5 per cent improvement in the efficiency of Australia’s material use could benefit the national GDP by up to $24 billion per annum. Professor Sahajwalla said value needs to be placed on the materials in which a product is made, and it needs to be recognised that these materials can be recycled or reformed. “At present, there is a focus on waste management at one end of the supply chain, with an emerging recycling and manufacturing industry at the other. “Protecting the environment and our health from hazardous waste, substances and pollutants is an ongoing challenge and we are all excited to be helping to address this challenge through this new Sustainable Communities and Waste Hub consortium,” she said. NESP has delivered practical environment outcomes through almost 400 successful science projects, and helped to shape the nation’s environmental science agenda over the past six years. Research will be prioritised to meet the most pressing environmental management and policy needs, with an emphasis on climate adaptation, threatened species, protected places and waste impacts. The new hubs are expected to come into effect early this year, with the existing hubs running until mid-2021. This will ensure NSEP continues to deliver valuable research throughout the transition process.

Australian Research Council Laureate Scientia Professor Veena Sahajwalla at UNSW will lead the Sustainable Communities and Waste Hub. Image credit: Anna Kucera.
New Aluminium Recycling Can Drive Manufacturing Prosperity
Source: Sally Wood
A recycling breakthrough at UNSW Sydney will offer new possibilities for the repurposing of polymerlaminated aluminium products, like food and coffee packaging.
Research undertaken at the Sustainable Materials Research and Technology (SMaRT) Centre has found a way that could start a new ‘green aluminium’ manufacturing revolution. It may also aid the Federal Government’s 2020-2021 Budget, and industry efforts to advance Australian manufacturing –increasing sustainability and creating jobs. The new technique to recover aluminium from complex, multilayered packaging is based on the microrecycling science pioneered by the SMaRT Centre under the leadership of its director, Professor Veena Sahajwalla. It builds on the Centre’s waste material innovations including green steel and microfactory technologies. The research shows a new way to sustainably recycle polymer-laminated aluminium packaging materials – like postconsumer food and coffee packaging – into high-quality aluminium, and be a potential source of high-energy hydrocarbon products. Professor Sahajwalla said the technology draws on local innovation. “We developed green steel technology where we extract hydrogen and carbon from old rubber tyres and plastic as an innovative and green pathway in steelmaking, and we now can develop new ‘green aluminium’ with our novel technique called thermal disengagement technology,” she said. The new thermal disengagement technology offers an innovative, efficient and sustainable microrecycling technique to separate the materials in complex polymer-laminated metal packaging waste. It can also transform aluminium into a clean and green metal, which can be extracted to be used as a high-quality material for manufacturing, while minimising residual waste. “Recycling using new technologies can be a foundation for the manufacturing of highquality materials from our waste resources, as we seek to develop greater sovereign capability along with economic prosperity,” Professor Sahajwalla explained. In addition, green steel and green manufacturing are capabilities that have been pioneered for over a decade. “The jobs and sustainability revolution our government wants to create as announced in its 2020 Budget can get a boost from some of these sort of existing innovations where industry and researchers are already successfully partnering,” Professor Sahajwalla said. A shift to renewable sources would also have wide international trade impacts, as Australia’s biggest trading partner, China, bought $10 billion worth of Australia’s metallurgical coal exports in 2019. China still relies on old-fashioned blast furnaces that are heavily dependent on fossil fuels. While most of the world’s current steel production involves heating coal in a blast furnace, green steel technology focuses on phasing this out and replacing it with a new method of liquid steel production. In many countries, waste polymer laminated metal packaging materials, and other municipal solid waste, ends up in landfill or incineration. Some of the materials are recycled in metallic forms from the bottom ash components by industrial separation. In all, waste-reforming technology can create new supply chains and jobs, especially in regional locations, as it does not have to be large scale or expensive. “I see a future where recycling and manufacturing are aligned, where waste and recycling become part of the manufacturing supply chain, and that is important in this new COVID era where we now highly value ‘sovereign capability’,” Professor Sahajwalla said. In one demonstration of how SMaRT is helping to create these new supply chains and aligning these sectors, it has connected an e-waste recycler directly with a steel maker. This enables undervalued metals and plastics which are destined for overseas, landfill or incineration, to be used as feedstock. SMaRT was founded in 2008 by Professor Sahajwalla. Today, the Centre brings researchers in fields of science, engineering, and the built environment together to deliver innovation and technology for rapid implementation. It features 30 personnel, state-of-theart furnaces and laboratories, and sophisticated analytical and processing equipment.

A pallet of compressed coffee pods used in the research by the UNSW Sustainable Materials Research and Technology Centre. Image credit: UNSW Sydney. A researcher works on the rapid transformation process of food packaging waste into value-added aluminium alloy by using a lab-scale Arc furnace at the SMaRT Centre at UNSW Sydney. Image credit: UNSW Sydney.
Common consumer packaging such as coffee pods is a target of the new ‘green aluminium’ breakthrough at UNSW Sydney.


Can We Safely Burn Waste To Make Fuel Like They Do In Denmark? Well, It’s Complicated.
Source: Sally Wood
Waste-to-energy incinerators could help Australia deal with its mounting waste crisis, but experts have warned that burning rubbish may come with risks to public health.
Australia’s two options in relation to the waste crisis typically involve exporting waste or burying it. But to achieve current national targets, policymakers are increasingly asking if waste can be safely burnt as fuel. Proposals for waste incinerators are being considered in the Greater Sydney region, but they have received criticism from the Greens and independent members of the NSW Parliament, who are concerned about the public health impacts. The ACT Government has also recently put a blanket ban on these facilities. But a systematic review of the scientific literature was recently conducted at UNSW, where researchers identified only 19 papers among 269 relevant studies — less than ten per cent — that could help address whether waste-to-energy incinerators could harm the population’s health. The review was conducted by Research Fellow at the Queensland University of Technology, Thomas Cole-Hunter; Knowledge and Translation Broker at the University of Sydney, Ana Porta Cubas; Senior Natural Hazards Risk Scientist at GNS Science, Christina Magill; and Christine Cowie, who is a Senior Research Fellow at the University of Sydney. Together, the research team discovered that there must be a cautious approach to waste-to-energy technology. ‘Waste-to-energy’ incineration is when solid waste is sorted and burned as ‘refuse-derived’ fuel to generate electricity. This can replace fossil fuel such as coal. Australia produces around 500kg of municipal (residential and commercial) waste each year, which is consistent with the average for OECD countries. In comparison, New Zealand is among the worst offenders for producing waste in any OECD country. It produces almost 800kg per person each year. The waste crisis has led to most recyclable or reusable waste in Australia ending up in landfill. This poses a potential risk to both climate and health with the emission of potent greenhouse gases like methane, and the leaching of heavy metals like lead into the groundwater. The research team have encouraged local governments to seek alternative options and turn their attention to global leaders in the space – like Denmark or Japan. These countries heavily rely on wasteto-energy incineration to reduce their dependency on landfills and reach carbon neutrality. Denmark’s waste-to-energy incinerator, Amager Bakke, has even become a tourist attraction, and is celebrated as one of the world’s cleanest waste-to-energy incinerators. Around 300 trucks filled with non-recyclable municipal solid waste are sent to Amager Bakke each day. This fuels a furnace that runs at 1,000 degrees Celsius, and turns water into steam. This steam provides electricity and heat to around 100,000 households. In Australia, a big concern is burning waste that may release chemicals that can harm public health, like nitrogen oxide and dioxin. Exposure to high levels of dioxin can even lead to skin lesions, an impaired immune system and reproductive issues. But Amager Bakke uses control measures, like technologically advanced filters that can bring the amount of dioxin released to near zero.
An additional concern is that implementing waste-to-energy incineration may go against recycling schemes, because of the potential for an increased demand for non-recyclable plastics as fuel. Supply of this plastic may come from the waning fossil fuel industry. This would work against the goal of establishing a circular economy that reuses and recycles where possible. The researcher’s review found a lack of evidence to fully reject well-designed and operated facilities. However, based on the limited number of health studies discovered through the research, the team endorsed a precautionary planning approach to waste-to-energy proposals.
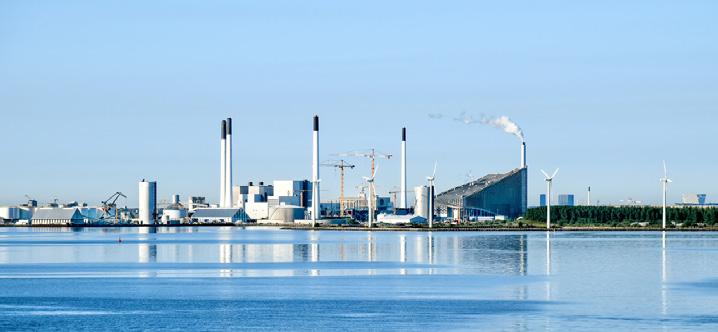
Amager Bakke power plant in Copenhagen, Denmark.
Burning waste may release substances that can harm our health, such as nitrogen oxide and dioxin.

AIBN Nanotechnologist Turning Sugarcane Waste Into Sustainable Packaging
Source: Sally Wood
Sugarcane waste could be a key ingredient in tackling plastic pollution, with a researcher at the University of Queensland’s Australian Institute for Bioengineering and Nanotechnology (AIBN) recently receiving funding to turn the green waste into sustainable packaging.
Dr Nasim Amiralian was awarded $45,000 from the AMP Tomorrow Fund to further her research producing 100 per cent bio-based single-use packaging materials using waste from the sugar production process. Dr Amiralian said there was an urgent need for sustainable packaging to tackle the problem of single-use plastics, which are the most significant contributor to plastic pollution. “Cane-based materials are biodegradable, compostable, thermally stable and grease- and moisture-resistant, making them suitable for packaging hot or cold food and also for use in automotive, aerospace and healthcare industries,” Dr Amiralian said. “However, stronger and lighter materials are needed to make sugarcane packaging an economical alternative to plastic.” “My research has found that adding a small amount of nanofibres to sugarcane pulp leads to a significant improvement to its mechanical properties as well as increasing the shelf-life of food due to the high oxygen and moisture barrier properties.” Dr Amiralian is working on a composite that can be safely disposed of in domestic compost bins and collected as kerbside rubbish, with the AMP Tomorrow Fund grant helping her produce a proof of concept. The grants are designed to help talented Australians take their passion projects to the next level, and Dr Amiralian is one of 40 outstanding individuals who are sharing in $1 million this year. Head of the AMP Foundation, Helen Liondos, said the beauty of the fund is that it is open to any Australian with an unrelenting commitment to what they’re trying to achieve and contribute to the community. “Despite the disruption of this year, so many Australians remain committed to making a positive impact on their communities,” Ms Liondos said. “These individuals, who continue to train hard, create new art, search for scientific or social solutions, are not only inspirations but also confirmation that Australia has a wealth of exceptional individuals to take us into better days.”
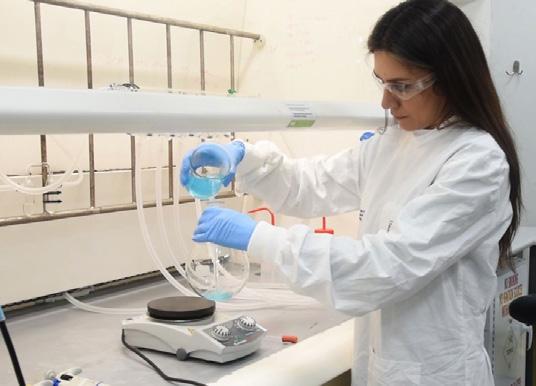
Dr Nasim Amiralian. Image credit: University of Queensland.
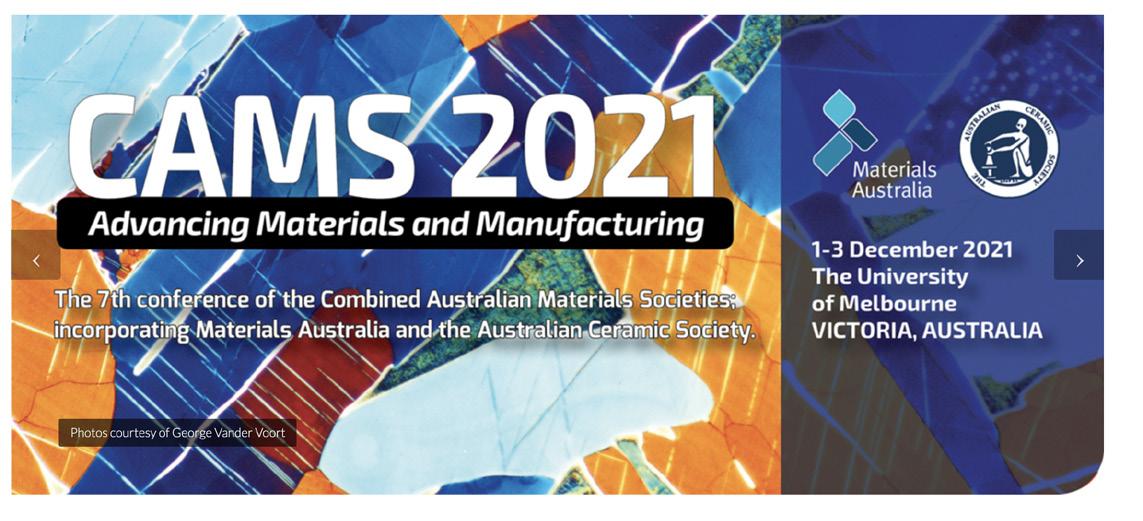
Sticking It To Weeds With A Biodegradable Mat
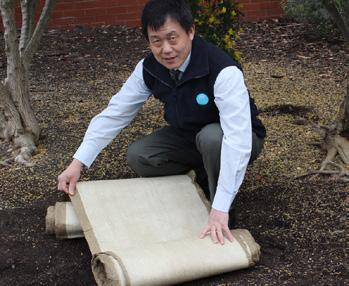
Dr Malcolm Miao demonstrating the linseed matting created from high pressure water jets. Image credit: CSIRO.
Using high pressure water jets, CSIRO developed a new process for making biodegradable weed mats. It stops the need to use binding agents, paving the way for an eco-friendly solution.
The Challenge
Sixty million square metres of polyethylene mats are used in horticulture, gardens and parks, and homes across Australia each year. According to environmental consulting group AgEconPlus, a partner in CSIRO research programs, these mats never fully decompose after their use. Additionally, these mats have other environmental implications. For instance, they prevent rainfall to the soils beneath causing unnecessary runoff and evaporation.
The Response
Using linseed straw and high pressure water jets, CSIRO developed a new type of matting. This unique technique enables linseed fibres to be linked together to form a compact fabric. The materials were developed as part of the Australian Government’s National Weeds and Productivity Research Program, managed by the Rural Industries Research and Development Corporation (RIRDC). The RIRDC invested A$12.4 million in research aimed at improving the knowledge and understanding of weeds, as well as providing land managers with new tools to control weeds and reduce their impact on agriculture and biodiversity. Researchers believe it could also be made using other agricultural waste materials, such as hemp or banana fibre. These materials, unlike their plastic counterparts, are organic and will disintegrate at the end of their lifecycle. Testing indicates the materials retain moisture, encouraging healthy soils beneath and reducing unnecessary runoff and evaporation.
The Results
This technology has the potential to benefit growers involved with organic and biodynamic production across the horticultural sector as well as manufacturers and suppliers of agricultural and garden products. The linseed mat process has exciting implications beyond outdoor matting. For example, the fabrics could be used to create eco shopping bags, minimising the synthetic materials currently being used.
Victoria University Research Turns Recycled Waste Into Valuable Resource
Victoria University engineers are conducting a world-first study that could keep tonnes of plastic, glass and tyres out of landfills.
Dr Ehsan Yaghoubi and Professor Sam Fragomeni are exploring whether blends of recycled materials with self-compacting properties could be an alternative backfill for sewer pipeline trenches. The current practice is to use precious natural aggregates that need to be excavated, crushed and often trucked in from great distances. The project – which includes a geotechnical team from the University of Melbourne, and the geotechnical firm Ground Science, along with City West Water as industry partners – was recently granted funding from Sustainability Victoria’s $37 million Recycling Industry Strategic Plan. Dr Yaghoubi said that while other projects have used backfill mixes with a limited percentage of recycled materials, this project, which uses 100 per cent recycled content for the purpose, is likely a worldfirst. The researchers are trialling blends of recycled tyre, plastic and glass, with glass comprising between 70 per cent and 80 per cent of the final formulation. “Together with our collaborators, we came up with the idea of using a blend of recycled materials because we can control their compaction and density,” Dr Yaghoubi said. Dr Yaghoubi said there is a growing imperative to find new applications for recycled materials since Australia is scheduled to end its glass waste exports from next year, and its plastic, paper and tyres waste by 2024. In addition, China has recently clamped down on accepting Australian waste imports. “Civil engineering projects require more materials than most people realise, whether it is a road, or backfilling kilometres and kilometres of sewer trenches,” Dr Yaghoubi said. “Turning waste into a resource is more important than ever.” City West Water has provided two site locations so the researchers can evaluate the recycled material under real-world conditions. Ground Science will assist with field and laboratory testing and expert advice. While still in its early stages, the researchers have run geotechnical and environmental testing on various recycled blends. They will measure and monitor the performance of two short-listed blends during rain or dry spells over 12 months using a sophisticated fibre-optic sensor to monitor ground movement and settlement.
