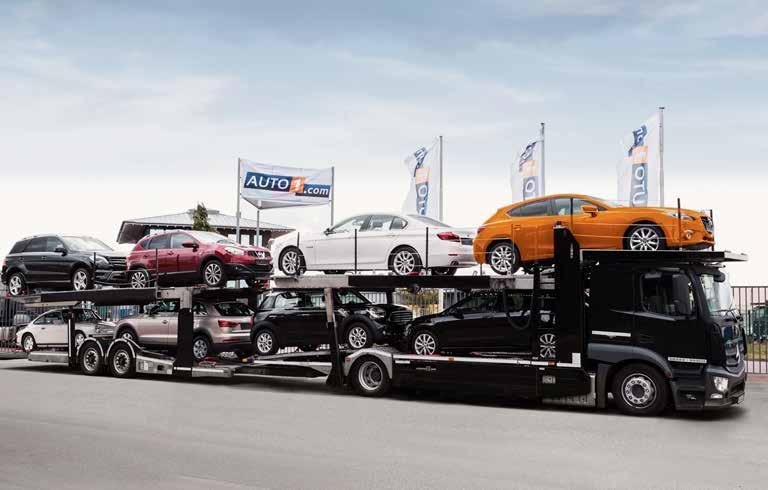
8 minute read
INTERVIEW VP AUTO1 GROUP 16
Petits ou gros, aucune différence
Ces dernières années, le paysage belge des concessionnaires s’est nettement consolidé, avec de grands groupes qui ont fait leur apparition. Est-ce que AUTO1. com vise surtout ce groupe-cible ou le petit garagiste a-t-il lui aussi intérêt à utiliser la plate-forme? Joost Kokke: “Ces gros groupements de concessionnaires ont leur propre réseau et leur propre logistique, ils ont la possibilité de ‘faire glisser’ des voitures au sein de leurs différents réseaux, etc. Nous représentons toutefois une plus-value à leurs yeux également, grâce à notre force de frappe internationale. Mais le petit garagiste local – qu’il soit multi-marques ou concessionnaire officiel d’une marque – y trouve lui aussi son compte! Notre plate-forme est peut-être même plus intéressante pour lui que pour les gros groupements de concessionnaires. Ils ont en effet la possibilité de voir exactement les mêmes voitures sur la plate-forme et de faire une offre. C’est précisément dans ce sens que nous sommes intéressants pour eux”
Advertisement
Un marché en pleine croissance
Le réseau européen de partenaires logistiques AUTO1. com ne cesse de s’étendre. Au deuxième trimestre 2021, le nombre de vendeurs actifs a augmenté de plus de 140% par rapport au même trimestre de l’année précédente. Les partenaires AUTO1.com profitent du réseau d’acheteurs européens maintenu en activité et au sein duquel de nouveaux groupes d’acheteurs ne cessent de se rencontrer. La plate-forme AUTO1.com collabore actuellement avec plus de 300 partenaires logistiques, ce qui donne lieu à une forme d’e-commerce rapide, précis et sans soucis, et ce à des prix compétitifs.
Car-Pass: un argument de ventent
La Belgique est un solide marché d’exportation de voitures d’occasion. C’est dû en partie aux nombreuses voitures de société en fin de contrat. Mais le Car-Pass semble égalemen être un sérieux argument de vente. Joost Kokke: “Grâce au CarPass, les acheteurs savent que le kilométrage du véhicule est correct, souvent aussi que l’entretien a été fait de la bonne manière, et quels sont éventuellement les dommages à la voiture. C’est vital pour la valeur d’une voiture. C’est la raison pour laquelle les voitures belges sont très prisées à l’étranger. Je suis donc bien content que les pouvoirs publics belges aient choisi un tel système.”

Parmi les clients OE, des marques automobiles exclusives telles que Bugatti, Bentley, AMG , Aston Martin
Textar, spécialiste des plaquettes de frein
Textar sort de l’ombre
Si Textar n’est pas un nom très connu, particulièrement en Belgique, cela risque bien de changer, et de changer vite... En effet, Textar tient à se profiler plus nettement. Cette entreprise, allemande à l’origine, est spécialisée dans les plaquettes, tant pour les mâchoires que pour les blocs de freins. Textar est une marque du groupe TMD Friction. Nous avons visité un des centres de production Textar, à Essen, ainsi que le centre d’essai de Leverkusen.
Dans le domaine des garnitures de frein, TMD Friction est un acteur mondial qui emploie plus de 5.000 salariés au total. Chaque année, le groupe fabrique quelque 300 millions de plaquettes, une quantité inimaginable. TMD Friction représente différentes marques de renom, chacune ayant sa propre histoire. Sur les huit marques que TMD Friction possède en portefeuille, les principales ont pour noms Textar ainsi que Mintex et Don (voir l’encadré pour plus de détails).
A gauche: Stephan Giesecke (Global Category Manager PC); à droite: Enrique Wegmann (Senior Manager Process Engineering)
L’union fait la force
Toutes ces marques peuvent se targuer d’une longue tradition.Toutes sont spécialisées dans les pièces de friction et ont joué un rôle crucial comme pionnières à différents moments de l’histoire de l’automobile, en développant des solutions de freinage pour le secteur. Par le biais de fusions, d’accords de coopération et de reprises, ces différentes entreprises et marques ont été réunies au sein d’un dénominateur commun: TMD Friction. Et ce qui est encore plus important: de nombreuses années d’expérience et de savoir-faire ont ainsi été synthétisées, ce qui a fait de TMD Friction un des fabricants de pièces d’origine (mâchoires et blocs de frein) les plus influents et les plus respectés au monde. Parmi les clients, on retrouve les marques automobiles les plus exclusives et les plus populaires – bref, les principaux fabricants d’équipement d’origine. Le développement des plaquettes de frein s’opère en étroite collaboration avec le client OE, qui impose des exigences spécifiques. Le développement d’un nouveau type de plaquette peut prendre jusqu’à trois ans. Les OE représentent plus de 75% de la production, 25% des pièces étant donc destinées au marché de la rechange. A Essen, les pièces d’origine représentent même 90% de l’ensemble. La part prise par le marché de la rechange devrait d’ailleurs encore augmenter. C’est pour cela que TMD Friction ambitionne – en Belgique notamment – une percée encore plus nette sur le marché dit ‘after market’, ce qui se fera sous le nom de marque Textar. Les origines de Textar remontent jusqu’en 1913. Stephan Giesecke (Global Category Manager PC) estime que Textar est en mesure de couvrir jusqu’à 99,46 % du parc de véhicules global. L’offre existe donc bel et bien.
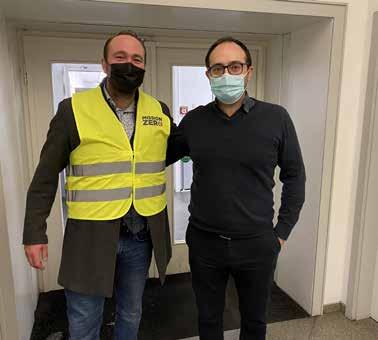
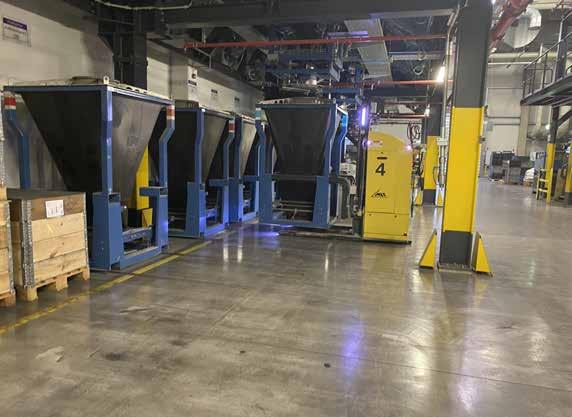
La matériau de friction compte jusqu’à 43 composants. On note généralement entre 4 et 5 composants principaux, qui constituent 80% du mélange. A gauche, un certain nombre de silos de stockage.
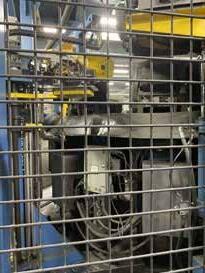
La réalisation et le collage du matériau de friction, un processus thermique. Une grande partie de la production est automatisée. Enrique Wegmann fournit quelques explications quant à la finition. Essen compte 15 chaînes de production finale, chacune d’entre elles délivrant entre 4 et 5 millions de plaquettes de freins par an.
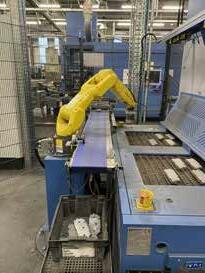
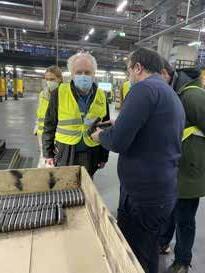
La production à Essen
Textar a démarré la production à Leverkusen en 1934. Aujourd’hui, ce site est responsable du développement et des essais. La production s’opère dans différents sites de par le monde, et notamment à Essen. C’est d’ailleurs là que Enrique Wegmann (Senior Manager Process Engineering) nous a fait visiter les lieux. La première étape de la production consiste à réaliser le mélange de matériaux nécessaire pour les garnitures de frein: le matériau de friction. En fonction du type de plaquette, jusqu’à 43 composants peuvent être utilisés pour ce mélange. En règle générale, 4 à 5 composants principaux représentent 80% du mélange. Un robot les retire des stocks et dépose la quantité voulue dans le mélangeur. Les 20% restants sont qualifiés ‘fine tuning’ par Enrique Wegmann et selon le type de matériau de friction, près de 40 composants soigneusement sélectionnés sont ajoutés – à la main – en quantités extrêmement précises. Enrique Wegmann: “La composition du mélange est soigneusement choisie en fonction du cahier des charges. Ces dernières années; nous avons en outre fait face à plusieurs défis successifs. Notamment à celui qui consistait à ne plus utiliser d’amiante. Aujourd’hui, l’utilisation du cuivre est également interdite. Il faut également compter avec les plaquettes spécifiques pour les systèmes de frein hyper-performants, qui font par exemple usage de disques en céramique. Parallèlement, les exigences sont de plus en plus drastiques en matière de performances pures, de confort acoustique, de baisse de poids et de réduction des particules.”
A Leverkusen, TMD Friction dispose de pas moins de 28 dynamomètres, dont la puissance varie entre 40 kW et 200 kW.
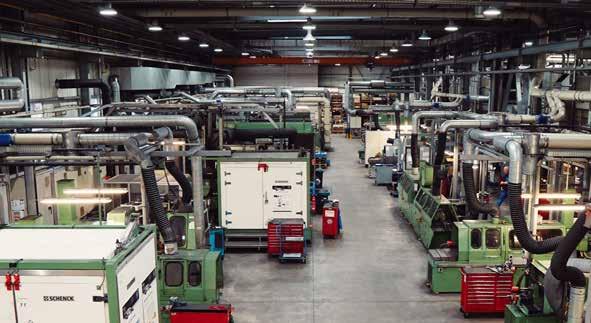

Pierre Kaspar (Senior Manager Testing Services) du département Tests.
Magiques, les adhésifs
Pendant la phase de préparation du mélange, la plaque de support est préparée dans un autre département de production. Cette plaque de support, qui présente évidemment une forme spécifique en fonction de son application, est recouverte d’une couche adhésive. Par-dessus, une autre couche fait office de barrière thermique et prévient les déchirures ou les ruptures du matériau de friction. Le mélange du matériau de friction contient une résine qui réagit à une température variant entre 100 et 200° Celsius, ce qui entraîne la solidification du matériau de friction. Tout cela se fait dans un moule. L’ancrage définitif du matériau de friction à la plaque de support s’opère également par le biais d’un processus thermique. Essen compte 15 chaînes de production finale, chacune étant en mesure de produire entre 4 et 5 millions de plaquettes par an. Les autres étapes importantes du processus de production sont: l’ébarbage et la finition des côtés obliques des garnitures de frein. Sur la plupart des plaquettes de frein récentes, le dos de la plaque de support est équipé dès la phase de production d’un ‘shim’ qui joue un rôle important dans la réduction du bruit.
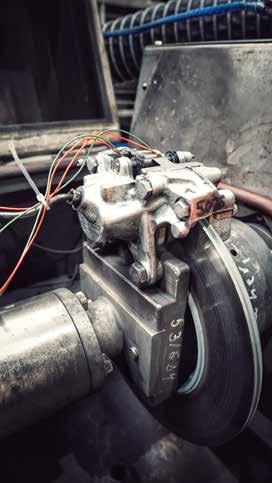
Le disque de frein complet - avec étrier et plaquettes – est monté sur le dynamomètre. Lors du développement de certaines plaquettes spécifiques, ce ne sont pas seulement le disque et l’étrier qui sont montés, mais toute la jambe de force, puisqu’elle a un impact sur les performances.
De très nombreux essais
Les tests jouent un rôle crucial lors du développement des nouvelles plaquettes de freins. Au centre d’essai de Leverkusen, où Pierre Kaspar ( Senior Manager Testing Services) est notre guide, TMD Friction fait usage de 28 dynamomètres dont la puissance varie de 40 kW à 200 kW. Un dynamomètre est actionné électriquement. Le disque de frein complet - avec étrier et plaquettes – est monté d’un côté, tandis que de l’autre, un volant d’inertie permet de simuler le poids d’un véhicule. La vitesse de rotation du disque est actionnée électriquement. La commande du dynamomètre ne s’opère plus depuis une salle de contrôle, puisqu’elle est aujourd’hui électronique. Lors des essais sur voitures particulières, l’accent porte surtout sur les performances, alors que les essais de plaquettes conçues pour les véhicules utilitaires testent surtout la durabilité et la résistance. La notion de ‘performances’ requiert une interprétation fort large. On parle ici aussi bien de performances de freinage pures que de maîtrise thermique et de gestion des NVH (Noise,