Bullish on ICEs: Accelleron’s Rofka On boarding CCS: Wärtsilä’s de Gruyter
Nanotech coatings: FuelSave’s EGR advance
MEPC80 preview: CII rules and CCS
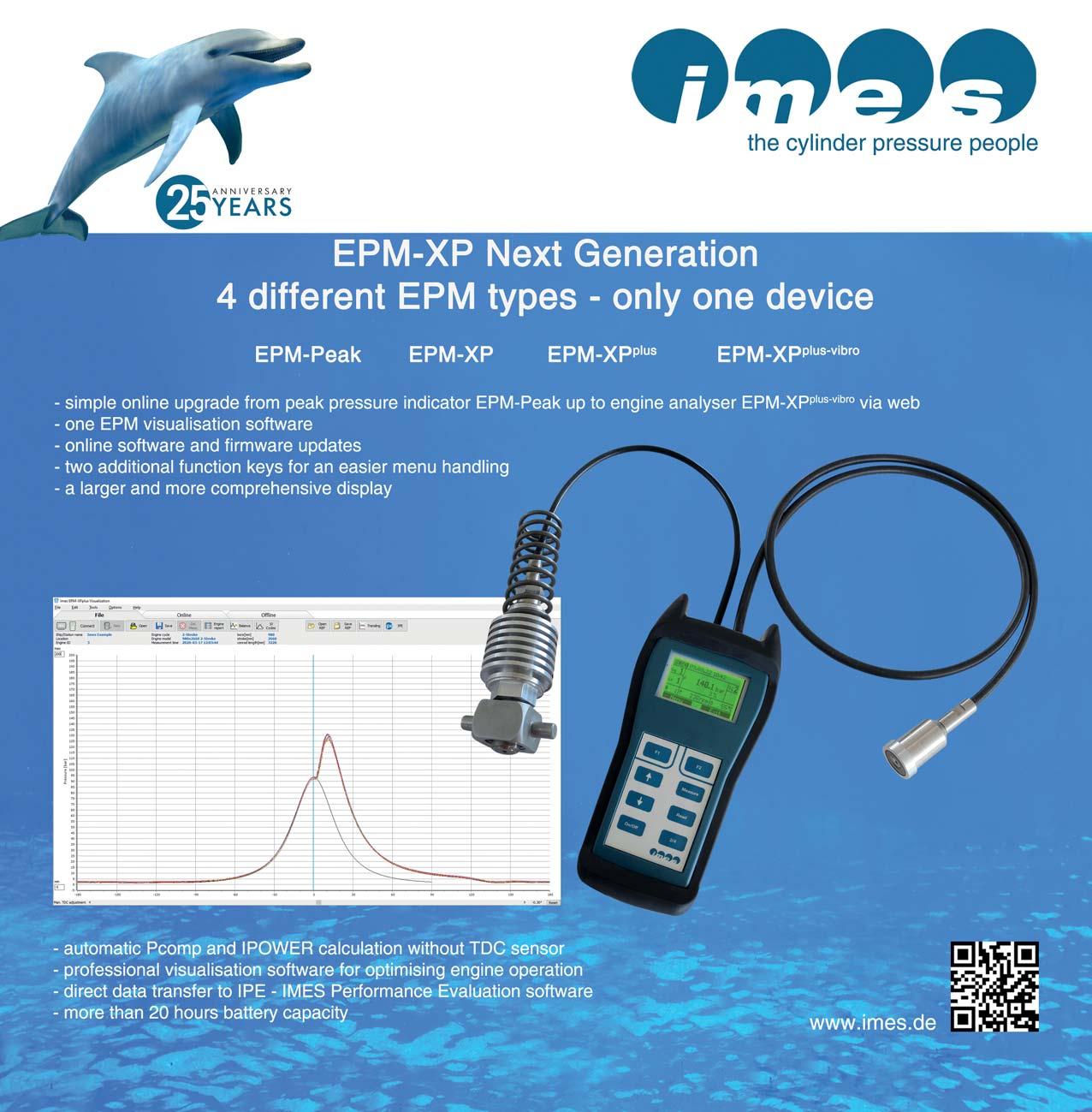
Bullish on ICEs: Accelleron’s Rofka On boarding CCS: Wärtsilä’s de Gruyter
Nanotech coatings: FuelSave’s EGR advance
MEPC80 preview: CII rules and CCS
Combustion Engine Technology for Ship Propulsion | Power Generation | Rail Traction
Technical Programme
Over 200 lectures, interesting panels and keynotes
Exhibition
New technologies and products
New Formats
Pitch Stage, World Café and other new session formats
Technical Tours
Visits to local industry
Networking & Social Events
Welcome Reception and Gala Dinner, over 800 international experts
Intelligent Power Systems
Digitalization & Connectivity, System Integration & Hybridization
Zero Emissions
Alternative fuels of the future, Emissions reduction technologies
Traditional Topics
New engine developments & other new concepts
And many more
Basic research, advanced engineering, Operators/ End-users experience www.cimaccongress.com
Christoph Rofka, Accelleron’s president
14 Pitch perfect
A new propeller design series tailored to the needs of cruise vessels is being developed under a Dutch-led joint industry project (JIP).
17 Wärtsilä
Wärtsilä is increasing the power output from its 31 medium-speed engine to 650 kW, an increase of 6% in power per cylinder.
16 Accelleron launch
Accelleron is on track to unveil a new approach to low-speed turbocharging for the maritime sector at the CIMAC Congress in June in Busan.
10
Leader Briefing Tamara de Gruyter of Wärtsilä discusses the challenges of balancing footprint, solvent and energy requirements when marinising carbon capture and storage (CCS) technology.
12
Will IMO acknowledge carbon capture’s potential in reducing a ship’s carbon intensity when the topic is discussed at MEPC80? Paul Gunton reports.
FuelSave is patenting an innovative new development for EGR solutions that promises to not only reduce NOX emissions but also reduce CO2 emissions in an after treatment process.
Medium & Low Speed products discusses changes that are affecting the wider maritime propulsion market, and Accelleron’s response in an exclusive interview.
New advanced combustion technology designed to reduce methane slip is being developed for Wärtsilä’s large bore engine platform after earlier success with smaller engines.
30
Kongsberg Maritime’s Rune Garen poses some difficult questions of Paul Gunton, and sees opportunities to learn from nature.
MAN Energy Solutions’ Two-Stroke Business has seen the scope of EGR solutions expand since research began in 2004, as it has become a cornerstone in modern engine design and optimisation.
The tanker industry is monitoring the development of regulations produced by the California Air Resources Board (CARB) that will affect the segment from 2025.
The Motorship’s Propulsion and Future Fuels Conference will take place this year in Hamburg, Germany. Stay in touch at propulsionconference.com
The dust has barely settled on the draft agreement of the EU’s FuelEU Maritime legislation, which has seen difficult issues surrounding the admissibility of carbon-based fuels, the range of renewable fuels of non biological origin (RFNBO), certification and the allocation of funding resolved.
The rules themselves are likely to achieve their primary objective of encouraging the early adoption of sustainable alternative marine fuels into the market, which is intended to support the development of the EU’s domestic alternative fuels infrastructure.
The introduction of the multiplier mechanism to drive early adoption demand for alternative fuels represents an elegant solution to the challenge of creating demand, which in turn incentivise the production and hence the availability of e-fuels.
Subsequently, the rules are expected to expect to foster the development of equivalent to 2% of fuel consumption by 2035, at which point the reduction targets for the greenhouse gas intensity of energy used on board by ships will be raised.
The maritime sector is being asked to play a major role in the introduction of alternative fuels into Europe’s supply chain, acting as some of the first stable sources of demand, which will give European fuel suppliers the certainty to develop supply.
The creation of stable reliable demand will then allow alternative fuel suppliers to overcome the myriad technical and economic challenges that introducing alternative fuel supplies will entail – and Say’s Law will then begin to apply as expanding supply begins to create its own demand. Or to put it another way, the chicken and the egg problem is skirted by funding a poultry farm.
For operators in Europe’s short-sea sector who do not have the appetite or means to invest in offtake agreements with green methanol suppliers, the shortage of commercially available methanol for bunkering remains a key constraint to investment decisions, as Pat Wheater hears in this month’s issue.
Wider issues around the emergence of low-cost sources of renewable e-fuel supply in the US incentivised by provisions of President Biden’s blockbusting Inflation Reduction Act mean that European subsidies to operators to expand alternative fuel consumption may end up funding the most competitive renewable fuel plants on the cost curve. In other words, the supply that may be created may be located in Texas or even in Oman and Saudi Arabia. Investments of close to USD30bn into export-oriented green ammonia plants in the latter two have been announced within the last two months.
Nor is the only area where US regulations are likely to have a wider impact on the market. We note that the California Air Resources Board (CARB) proposal has completed consultation on the introduction of OPS requirements for terminals serving the oil tanker segment between 2025 and 2027.
I hope that you find something to interest you in this month’s issue, which also looks ahead to upcoming discussions about the inclusion of carbon capture technology into CII rules, and includes a interesting article on a potential nanotechnology advance that will improve the efficiency of reduction in EGR units.
A new propeller design series tailored to the needs of cruise vessels is being developed under a Dutch-led joint industry project(JIP), writes David Tinsley.
Initiated by research body MARIN, the Wageningen FC research endeavour is the follow-up to the F-Series JIP, which realised a systematic range of 150 fixed-pitch propellers for merchant vessels using the latest technological tools. The R&D work showed that the geometric characteristics of propellers for cruise ships and other vessels such as large motor yachts, which impose especially high demands as to onboard comfort levels, differ from the requirements of the gamut of mercantile traders covered by the F-Series.
The objective of the collaboration partners in the Wageningen FC-series project is thereby to design and test 18 additional, fixed-pitch propellers to suit those applications where passenger comfort is of the highest order, married with exacting energy saving criteria. Only five- and six-bladed screws with a pitch ratio equal to, or higher than, 1.0 are being considered.
The F-series programme, which involved a multiplicity of companies and institutes, had followed successive JIPs realising the Wageningen CD-series open and ducted controllable pitch propellers, and Wageningen TT controllable and
fixed pitch tunnel thruster propellers, including rim-driven units. The latest initiative underscores the fact that propeller design has become a continuous drive for refinement and advance, to achieve the best balance between propulsive efficiency, hull vibration levels, and onboard and radiated underwater noise levels.
The FC project is undertaken through recourse to multiobjective optimisation tools, in combination with both boundary element methods(BEM) and Reynolds-averaged NavierStokes(RANS) CFD techniques at the design stage.
All propeller models will be manufactured on a new, five-axis milling machine, and tested in open water conditions using the quasi-steady measurement technique, which was deployed for the earlier CD-series propellers. The dataset of the FCseries will be included in the software of the F-Series JIP as a subset, so as to enable comparison of results.
At its outset, the budget for the FC programme was estimated at EUR280,000($299,500), and it was envisaged that some EUR 190,000($200,500) would be covered by the study partners.
Wärtsilä is increasing the power output from its highly efficient 31 medium-speed engine, the technology company has announced.
Wärtsilä has increased the power output of its highly efficient Wärtsilä 31 diesel engine to deliver increased power density within the same physical footprint. This upgraded engine will increase its power per cylinder to 650 kW, an increase of 6% in power per cylinder.
The Wärtsilä 31 will have the highest power per cylinder of any engine of its bore size. The upgrade will extend the output range of the 31 to a range of 5.2 to 10.4 MW. The increase in power, compared with the current 31-series engines, means the same power demand can be met with fewer cylinders. This will give significantly lower maintenance costs and will offer space advantages where engine room space is at a premium.
The 31 engine is said to have become increasingly popular for installation on a range of vessel types, including among others, cruise ships, ferries, cable layers, ice breakers and fishing vessels.
“With this power upgrade we are delivering significant added value to our customers,” explained Lars Anderson, Director of Product Management at Wärtsilä. “The Wärtsilä 31 is already the best engine in its class, and this development widens its market advantage even further. By extending its performance, we are making a real contribution to
greater sustainability and supporting our commitment to a decarbonised future.”
The first deliveries of the upgraded engine are taking place during the first half of 2023.
8 The Wärtsilä 31 engine upgrade will increase its power output.
Already, seven higher power output Wärtsilä 31 engines have been contracted.
Ronald Ervik, Managing Director of Herøyhav, a Norwegian fishing company and one of the first recipients of the upgraded engine said: “For our new vessel we opted for the Wärtsilä 31 engine because it is the most modern and most efficient mediumspeed marine diesel engine on the market. Not only will it give us the power we need and with dimensions that fit our engine room design, but it will also lower fuel consumption.”
The conceptual design of a carbon capture system onboard an oil tanker has received approval in principle from ABS. The design forms part of a pilot project to demonstrate end-to-end shipboard carbon capture at scale.
The REMARCCABLE project was initiated in 2022. In addition to Deltamarin, the project’s seven-member consortium includes the Global Centre for Maritime Decarbonization (GCMD) in Singapore, the Oil and Gas Climate Initiative (OGCI), ABS, Stena Bulk, Alfa Laval and the Netherlands Organization for Applied Scientific Research (TNO).
The first phase of the project involved conceptual design and a
front-end engineering design study of the carbon capture system. Following the approval in principle, the consortium’s members will decide whether to advance the project to the next stage.
The second phase would include engineering, procurement, and construction of a prototype shipboard carbon capture system and onshore commissioning.
Phase three would focus on integrating the carbon capture system with the MR tanker and conducting sea trials. Following a full engineering study, the carbon capture system will be built and tested prior to integration onboard a Stena Bulk medium range (MR) tanker for sea trials.
The global shipping industry is
looking at a range of solutions, including low-carbon fuels and onboard carbon capture, to help achieve a target to halve its greenhouse gas emissions by 2050 from a baseline of 2008.
The consortium’s members believe the onboard carbon capture system could help accelerate commercial deployment of shipboard carbon capture technology within the next five years.
The GCMD plans to launch a study on offloading the liquid carbon dioxide (CO2) to resolve potential challenges and inform the third phase of the project.
Hyundai Heavy Industries Engine & Machinery (HHIEMD) marked the renewal of its licensing agreement with Japan Engine Corporation (J-ENG) to build UE low-speed engines with a ceremony in mid March. The scope of the agreement extends from engine development to design, manufacturing, sales, and after-sales service. HHI-EMD is one of the market leaders in the manufacture of low speed 2-stroke main engines.
ClassNK has issued a statement of compliance (SoC) to a second ship recycling facility in Bangladesh, verifying that the facility is in line with the Hong Kong Convention (HKC). Although the convention is yet to be ratified, responsible ship recycling yard operators have begun undertaking voluntary certification so as to ensure rigorous safety standards and support ongoing calls for ESG reporting across maritime.
Samskip has awarded Cochin Shipyard a contract for 2+2 container feeder vessels. The container feeders will be equipped with a dieselelectric propulsion system, but are intended to be primarily powered by H2fuelled fuel cells. The vessels are scheduled for delivery in Q3 2025. The vessels will be equipped with onshore power supply connections. The vessel design was produced by Naval Dynamics AS.
NEOM Green Hydrogen Company has entered into an agreement to develop an export-oriented green ammonia production facility with an annual capacity of 1.2 million tonnes. NEOM aims to start the first green ammonia exports in 2026. Construction of the USD8.5bn export-oriented mega-project is expected to begin after it signed financing agreements with a number of financial institutions on 1 March.
Ports must be able to check the background of all vessels and show bodies such as OFAC that they have the technology to screen ships for suspected sanctionsSource: Wärtsilä Corporation
Although the much-vaunted scheme to realise at least 30 domestically-produced, zero-emission ships by 2030 under the Maritime Master Plan has yet to be endorsed by government, Dutch shipbuilders continue to show resilience and business verve, writes
8 New breed: diesel-electric coasters for Vertom at Thecla Bodewes’ Kampen yard
While Royal IHC is the subject of a further rescue plan due to a dearth of new contracts for larger, complex vessels in its target sectors, orderbooks among many of the industry’s key players have seen some strengthening over the past 12 months. Positive influences are an expansion-minded and innovative domestic shipowning and shipmanagement community, with recourse to an extensive supply chain and network of knowledge centres, underpinned by a Dutch propensity for cost-minded, technologically-pragmatic solutions.
Exemplifying the well-proven practice of many Dutch shipbuilders to assign the bulk of newbuild steel fabrication to yards in lower-cost countries, the Polish-built hull of a roro heavy-load carrier recently arrived at Urk, on the IJsselmeer, for completion by main contractor Hartman Marine. The latest project adheres to the production pattern adopted by the Hartman group for successive stages of its in-house fleet development programme.
The 108m Southern Rock is the third in a series of four vessels of the R3 Carrier-type ordered by Hartman Seatrade. With Partner Shipyard in Szczecin, Poland, having built the bare hull and superstructure, Hartman Marine has put in hand the high added-value phase entailing the fitting of the main engine, generators, compressors, separators, pumps, ballast system, navigation and electronic devices, hatch covers and hatch crane, together with interior outfitting, at its Urk premises.
The 3,500dwt R3 Carrier design is a lengthened version of the R2 Carrier type, a derivation of the M2 Runner multipurpose/project cargo vessel class. Shared key features of the ro-ro and general cargo designs include the proportionally large extent of deck space, provision for sailing in open-top condition, dangerous goods certification, and cost competitiveness. With full-width stern ramp access, the adoption of the ro-ro mode is considered a safer, more cost-
effective and less time consuming cargo working method compared to conventional lo-lo, for the target business involved.
The R3 Carrier is 13m longer than its R2 antecedent, allowing an increase in hold length of some 5m to 74m. Both ro-ro versions can accept rolling loads up to 80t per axle, and the ship’s removable tweendecks can take 5t/m2 up to a total 350t per tweendeck.
The continuity and commonality expressed in the Hartman programme yield important benefits as regards production flow and equipment purchasing. While the seminal M2 Runner series made its debut in 2012 via the 93m Oceanic, the initial ro-ro variant first came into being by way of the R2 Carrier Baltic in 2017, followed in the consecutive years by the Western Rock and Eastern Rock.
The R3 Carrier iteration assumed first form in the December 2021-delivered Celtic, and second-of-class Adriatic was commissioned last October. With outfitting of Southern Rock now in hand at Urk, fabrication of the fourth vessel, Rock Carrier, is under way in Poland before transfer to the Netherlands and scheduled handover to the operator during December 2023.
Inland from the IJsselmeer, on the lower reaches of the River IJssel, the town of Kampen has received a boost to shipbuilding activity through what has become an eight-ship series entrusted to Thecla Bodewes by the Vertom Group.
The 7,000dwt dry cargo carrier generation, designated the LABRAX-type, has been developed in association with Groot Ship Design and features diesel-electric propulsion and CFD(computational fluid dynamics) optimisation of the hull form for efficiency across the power and speed profile. The two holds are completely box-shaped, maximising loading flexibility and cargo intake.
David TinsleyCredit: Vertom
The modular propulsion concept employed is intended to allow the vessel to be readily adapted to future carbon emission-reducing solutions. The system distributes the energy load in efficient manner by using smaller engine prime movers for optimised combustion and fuel usage. The arrangements are also designed to facilitate any future switch to methanol-electric or hydrogen-electric propulsion.
Following sea trials conducted during December 2022, class leader Vertom Patty has been phased into trade, while the second ship in the series, Vertom Cyta, was side-launched at Kampen on February 23 this year with a view to April commissioning. Six more sisters are on order, Thecla Bodewes having been awarded the seventh and eighth units a couple of weeks before Vertom Cyta went down the ways, such that the production programme extends into the latter stages of 2025.
Vertom has also joined forces with Groot Ship Design in a project entailing a series of smaller vessels, of 5,600dwt, based on the same platform as the 7,000dwt type. A construction contract calling for six newbuilds to the 99m, diesel-electric design has been placed with Chowgule & Company in Goa, India.
Each of the 5,600dwt multi-purpose cargo ships has been specified with four main generators of approximately 400kW apiece, feeding two 650kW propulsion motors and a 400kW bow thruster. At ‘economical’ speed settings, achieving around 10 knots at design draught, operation will be on three generators.
The company has gone ahead with further investments in wind-assisted propulsion systems by specifying VentoFoil retrofit installations for two of its existing short-sea cargo vessel fleet, the 2009-built, 118m sisters Progress and Perfect.
VentoFoil is the latest version of the VentiFoil solution, and is a wing-shaped element harnessing innovation in aerodynamics to create a high propelling force relative to its size. Vertom had been studying the wind-assist technology in more detail since signing a contract for two VentiFoil units to be retrofitted to the 2008-built, 90m cargo ship Anna in June last year.
Conoship International’s current work on new designs for the short-sea sector shows a predilection towards dieselelectric main power. Electric motors favour the use of a larger-diameter propeller in combination with an optimised aftship form, as encapsulated by the ConoDuctTail arrangement. This allows for very high propulsive efficiency and comparatively modest power in the electric propulsion motors. The large, fixed-pitch propeller is capable of handling wide torque fluctuations.
Drawing on extensive market research, Conoship has formulated a new CIP series of diesel-electric general cargo vessels suited to operations into small ports and river terminals throughout north and west Europe. Contracts were awarded to Holland Shipyards at the end of December last, spanning a total of five singledeckers. Two 88m cargo vessels will be built for De Bock Maritiem of Alkmaar in accordance with Conoship’s CIP 3600 blueprints, while three examples of the CIP 3800-designated 89.4m version have been ordered by Hartel Shipping & Chartering.
In all cases, the frequency-controlled diesel-electric power train, based on a pair of 374kW electro motors, will regulate the speed of the screw according to variables such as load factor, water level and navigation route. Fuel savings as great as 30-35% are anticipated.
The three diesel generators are to be sited on the upper deck, facilitating access for future adaptation of the prime movers for alternative fuels and the requisite fuel storage. The electric propulsion train would remain unchanged in such a conversion. Moreover, the CIP series has been prepared to facilitate the adoption, either at the newbuild
stage or through subsequent retrofit, of wind-assisted propulsion using Econowind’s VentiFoil sails. Hartel has committed to VentiFoils for the first of its newbuilds, and expects to thereby realise an additional gain in fuel efficiency in the order of 8-12%.
Conoship plans to augment the CIP offering with a 5,800dwt variant, currently under development. Whereas the 3600 and 3800 designs provide for the fitting of twin VentiFoils forward, at the fo’c’sle, the 5800 type is proposed with provision for three such sails along the port side.
A northern research consortium coordinated by Conoship International has examined the feasibility of a shared centre for robotised shipbuilding production. The completed report under the SHARED FACILITY initiative was handed over to the Groningen provincial authority in January 2023, and demonstrated that an automated, micro panel line would be technically, financially and organisationally feasible given sustained cooperation.
Conoship was partnered in the investigative project by the Groninger Maritime Board(GMB) Foundation, technology industry association FME and over 30 companies from the northern Netherlands’ maritime sector, including shipyards and equipment suppliers, plus specialists in automation and digitalisation. Consideration is now being given to a follow-up project, entailing the setting up of a pilot plant or Fieldlab, where companies and knowledge institutions could develop related production techniques for shipbuilding.
The Damen Shipyards Group has implemented a major new phase of business development focused on the offshore energy market. Part-and-parcel of the strategy, the design offering was recently augmented by the FLOW-SV vessel concept, addressing the challenging task of supplying and installing ground tackles for floating wind turbines and prepared for future operation on methanol. Indicative of its resources, Damen is currently undertaking the structural fabrication and outfitting of two high-voltage directcurrent(HVDC) offshore transmission topsides at its Mangalia yard in Romania.
A major investment is taking place at MARIN’s Wageningen establishment, by way of the construction of the new Seven Oceans Simulator centre(SOSc). Expected to be operational by 2024, SOSc will contribute to maritime safety and technology through realistically simulate the behaviour and interaction of ships and crews in challenging conditions and situations at sea.
Besides research into shipping safety, the virtual test facility will enable users to experience and validate the behaviour of newbuilds during the ship design phase, providing insights into the fundamental role of the crew and onboard cooperation. The centre will contribute to the development of innovative vessels offering the highest safety level in adverse sea conditions.
SOSc will feature spherical simulators giving wrap-around, upward and downward projection, with a moving bridge, and a laboratory incorporating VR/AR(virtual/augmented reality) technologies, plus human factor management and observation techniques.
Vertom has also joined forces with Groot Ship Design in a project entailing a series of smaller vessels, of 5,600dwt, based on the same platform as the 7,000dwt type
Tamara de Gruyter of Wärtsilä discusses the challenges of balancing footprint, solvent and energy requirements when marinising carbon capture and storage (CCS) technology for onboard CCS systems, and calls for regulators to bear CCS technology in mind during MEPC80 discussions
Thank you for agreeing to the interview. Looking at the wider regulatory context for carbon capture and storage (CCS), could you discuss the importance of establishing a clear regulatory framework?
If you look at the regulatory context, a lot of things are moving in the right direction. We have had carbon compliance indicators, such as CII, EEXI, and the emissions trading system (ETS) in the EU, as well as fiscal regulation.
These are starting to impact our customers’ operations … driving us all towards a greener world. One element of a greener world for us is also CCS. And I think while the IMO is maybe a bit slower, they acknowledge the potential, but I think then really getting regulations for maritime that are global, that's not really there yet.
But the regulatory environment is important, because it also sends a clear message to the industry, about the kind of technology they should invest in. And carbon capture is definitely one of the many technologies that can help customers.
One of the interesting aspects of CCS that has yet to be defined is how credits for CCS should be structured. Do you think the scheme should ascribe credit if the CO2 is reused?
I think it would be a good thing. When you look a bit more medium or long term, probably it's going to be a licence to operate. It’s going to be part of your operational costs there because that's the only way to incentivise people to bring down the CO2 footprint of the ship by whatever means. I also think, when considering what to do with all this captured CO2, that early movers will have the opportunity to sell the CO2 capture.
Over the medium to long term, we will be capturing way more CO2 compared to other industries. There's likely to be a transition when you're not going to get paid for the CO2 you are able to deliver, but you have to pay to dispose of it. At some point there will be too much and then it will have to be sequestered somewhere. And that probably has a price. I think this will also be a journey for the CO2 industry that will develop after the CO2 is captured.
Which leads into some wider questions about the emergence of supply chains for renewable or green ammonia, green methanol or other e-fuels. Do you think that might also emerge as an end use market for some of the captured CO2 without having to look into underground sequestration?
Of course, green fuels also form part of the potential end-use markets [alongside carbonated drinks and greenhouses]. While we would like to see all the steps in the process ready, I think… you also have to accept that certain things will play out over time.
We are focusing on the onboard carbon capture, but the maritime industry is not the only hard-to-abate industry that is looking at CCS. So, I think we will also benefit in the marine
industry from the infrastructure that will also be built for land based carbon that is [going to be] captured. We are playing a central role in LINCCS (linking carbon capture and storage) for the CCS value chain, which is a collaborative cooperation between many companies.
Since we spoke in Vaasa in 2022, the CCS market has been transformed with a large number of technology developers seeking to develop marinised solutions.
Yes, it does seem to be evolving very quickly. It has definitely become an active space. Within Wärtsilä, we have a saying that “green is not black and white”. Unlike in previous transitions, we think that there will be a multitude of solutions, reflecting local technology and fuel availability.
Looking further ahead, we should recognise that we are likely to be working with fossil fuels for quite a long time. Because, as our experience with LNG has shown, it's not so easy to really transform our whole industry rapidly, and partly because some of the green fuels under consideration, such as methanol or some biofuels, might not be fully carbon neutral unless you combine them with carbon capture.
Before we look at the technology itself, do you think that there could be a role for some sort of certification to ensure the CO2 has been captured and safely disposed of?
I think it's a good question. When I look at it more from a ship perspective, I think it's how are you as a ship owner going to prove that you are capturing the carbon? I think that's the first step, you're capturing it from your fuel. So I think that that is something that probably will be regulated or tested, I can also imagine that you probably have to do a test on board of the vessel to prove that the system is working.
I think that is a separate issue to your wider question, which is how to certify that the whole CO2 sequestration chain has been followed.
A related question is the extent to which you see the introduction of CCS as dependent upon the introduction of a carbon price?
I think that regulation has been one way of forcing the industry to take steps, and the social licence to operate is another strong driver.
We recognise that financial incentives are also required to ensure a common playing field and to reward market participants who have invested in decarbonisation technologies such as this one.
But returning to the first question, do you think that the upcoming meeting of the MEPC committee at the IMO in June needs to add carbon capture into the list of recognised technologies for CII and EEXI purposes?
I would like to see a bit more speed and also recognition of CCS as a technology. I also hope that we realise that
there's not enough carbon or carbon free fuels, that because you will then have to make them maybe with fossil fuels. So, we also have to have enough realism not to rule out certain solutions, because we feel they are maybe not green enough.
Turning to some of the shoreside infrastructure issues, would you like to address any of the concerns about the handling of captured carbon, given the toxicity of pure CO2, as well as moisture constraints.
CCS has been used for many years, so it's not exactly new technology. While I don’t think there has been much incentive to use it in a very wide scale, you could say some land-based projects have definitely proven its technical, but also commercial viability.
At Wärtsilä, we are focusing on onboard carbon capture for maritime, and there is a lot of knowledge in the world by other parties, and at some point would have to buy the shore side infrastructure. There are already some projects, especially in North Europe, ongoing that have started to work on this.
The fact that CCS solutions are actually already in the market, means that the infrastructure to discharge CO2 shouldn’t be a barrier to wider adoption, I guess. Which is a key difference compared with some other breakthrough technologies, like hydrogen.
I think the main challenge that we have is that if you want to marinise this technology, it needs to fit on a ship. And in a lot of cases, it might have to fit on an existing ship where [no] space was [originally allocated] in the first place.
It is very important to show how to make CCS neat and small, but also how to make it durable to be able to use onboard a ship, which is very different from stationary landbased uses. So the challenge is how to use that technology and put it in reliable, sturdy, small footprint, concepts that we can use onboard ships.
And that leads us really neatly on to where you're spending a lot of your time, which is exactly looking at those looking at those challenges.
Yes, exactly. I think the other thing we shouldn't underestimate is that you don’t only have to make it in a size that fits in a weight, but that [you have to manage] the energy consumption. You cannot put a second main engine on the ship just to run the carbon capture plant.
I think that that is an extremely important element. If I can share a story from the market, I remember talking to a ship owner in Asia who was proudly telling me that they had taken part in a carbon capture pilot project. But he also admitted that the vessel couldn't leave the port because the whole engine power was running the carbon capture plant.
He said that as a proof of concept, it worked. But it's not something we can use. The challenge of how to make CCS
There are several regulatory initiatives to promote the use of fuels made with recycled carbon.
These include the EU’s Renewable Energy Directive (RED II), which promotes the use of “recycled carbon fuels” as long as they generate emission savings of at least 70%
possible in reality on board a ship is one we're working on with our R&D team..
And one of the areas of research is around solvent consumption. Is the development of solvents a space that you’re actively looking at, or are looking at mature solvents as a first phase?
Of course, we are testing a lot of different solvents to make sure that we pick the right one. But I think you also need to have [solvent] availability and reusability. I also believe that as this industry grows not only in marine, but also on land, of course, the solvent space will divide.
But I think that solvent selection is definitely one of the key things in order to make CCS a financially viable concept, alongside energy consumption and reusability.
Do you see there being a kind of minimum threshold in terms of energy consumption? Or do you anticipate there may be progressive reductions as the technology matures? Or perhaps both?
I think it's a very good point. Because I think first of all, you need to come with a solution. But solvent selection is a key. It's a key critical factor, because the solvent, of course, also has an impact on the energy needs on board.
Can you give us an update on how things are going with your own developments?
But we are currently doing testing, and testing actually takes quite a long time. We are iterating, we are doing the testing. In addition, we are planning to schedule the next big test within the next 12 months on board a vessel. I'm quite sure that this continue to productise the technology.
within the next 12 months on board a vessel. Im quite at first pilot will also give us a lot more input to e the
And you're looking at developing your onboard CCS solutions for both the 2-stroke and 4-stroke market? Do you think that it will, will be particularly interesting for vessels for operators looking for retro existing assets?
nd finally, you mentioned that ou're your d e and 4-stroke hat it will, will be ting for g retrofit solutions for their g assets?
eah, I think I think it will raise a lot of terest fits because it could er a financial incentive, or how to tions, fits, because for the nt ecially some ybe ithin the that ed to be
Yeah, I think I think it will raise a lot of interest for retro be either a comply with the CII indicator. According to our calculations, I believe that there is a large market for retro merchant segment, it's not so easy to especially with some ships that are maybe a bit older, to still keep them within the eight things that they need to be.
relative to their fossil counterparts.
In the State of California in the United States, a Low Carbon Fuel Standard provides credits for fuels with a lower carbon intensity than petrol, with credits trading at USD 90/ ton of CO2. This measure can be combined with the US 45Q tax credit, which has
recently been increased through the Inflation Reduction Act to USD 60 per ton of CO2 used, providing emission reductions are verified.
The IEA notes that national requirements for low-carbon fuels in aviation fuel have been introduced in France, Norway and Sweden and France.
At first sight, carbon capture and storage (CCS) seems an obvious factor to take into account when calculating a ship’s Carbon Intensity Indicator (CII): it reduces a ship’s carbon emissions and thus its carbon intensity. But it is not currently included in the calculation, although momentum is building for that to be reviewed and IMO’s Marine Environment Protection Committee has it on its agenda..
CII came into effect on 1 January 2023 to provide a measure of a ship’s efficiency in terms of its emitted CO2 per cargocarrying mile, using fuel consumption as the main parameter for calculating how much CO2 is emitted. The notion that there could be a technology that retains some – perhaps most – of those emissions onboard, was not taken into account.
One company that makes such equipment is Wärtsilä and a comment to The Motorship by its director of exhaust treatment, Sigurd Jenssen, gives a clue about its omission. The company looked at CCS a decade ago and “didn’t really think this was doable. But we’ve changed our minds”, he said.
He believes that legislators have been on the same journey as they developed greenhouse gas (GHG) strategies. They began with energy efficiency, voyage optimisation and lowcarbon fuels, but their views have matured to take a more holistic view, he said. “Then, carbon capture easily comes into the picture.”
It is easy to see why CCS might not seem an attractive route towards tackling emissions. The captured CO2 weighs about three times that of the fuel burned, which will have an impact on a ship’s displacement during a voyage; the collection machinery requires a significant amount of fuel (estimates vary, but 10-20% of installed power are typical figures); CAPEX and OPEX will increase; offloading and onshore storage complicate discharge calls; and monitoring and confirming that the CO2 is actually permanently locked away – or transferred to a re-use facility – will add regulatory burdens.
On the other hand, IMO’s Initial GHG strategy includes two related ambitions that share a 2050 goal: to cut annual GHG emissions from international shipping by at least half and to aim to reduce the carbon intensity of international shipping by 70%, both compared to 2008. With carbon capture, “you can essentially reach 2050 targets today”, Mr Jenssen said.
Not only that, but this delivers a much greater total emissions reduction between now and then that could be achieved by the 2-3% per year reduction envisaged by the current CII reduction curve. On that basis, CCS “would enable a much more aggressive reduction in emissions”, he added.
It was the Republic of Korea that first brought CCS to MEPC’s attention, in a paper submitted for MEPC 76 in June 2021, although scheduling pressures led to it being held over for a year, to MEPC 78, for discussion.
Korea’s paper made the same point as Mr Jenssen: “now is a timely stage for introducing measures for onboard CO2 capture so as to promote the adoption of innovative CO2 reduction technologies as well as provide the opportunity to
reduce CO2 emissions … to meet the goals set by the Initial Strategy at the earliest possible moment”, its paper argued. It also noted that EEDI/EEXI calculations should also take account of the impact of CCS.
Discussions at that meeting included views both in support and with concerns about the proposal and the committee asked for “further information and concrete proposals” to be submitted to future sessions.
The result was six submissions on the topic at MEPC 79 in December 2022, including one by Norway. It called on MEPC to set up a dedicated work stream to consider the use of CCS technology, with three terms of reference. First, it should review the status of technological development of onboard carbon capture applications; second it should identify possible options for the accounting, verification and certification of captured CO2; and consider how to incorporate onboard carbon capture into IMO’s regulatory framework.
Lloyd’s Register’s lead decarbonisation consultant, Brijesh Tewari, drew The Motorship’s attention to a particular section of that paper, which suggested that “for the calculation of the CII, the accounting might be easier as the actual mass of CO2 delivered to a certified transport network could be used … [and be] potentially subtracted when calculating the emissions of the ship.” The paper also suggested that “the same approach can be used in a market-based measure such as an emission trading scheme or a levy-based system if developed.”
In that section of the paper, Norway also identified “a need for stand-alone guidelines regarding the verification of systems relating to the performance, the characterisation of the carbon dioxide stream and possibly a recognised certification scheme for environmentally safe permanent storage.” This, it said, could require amendments to MARPOL Annex VI.
Korea also submitted a paper to MEPC 79, in which it noted that CII, EEDI and EEXI calculations are based on tank-to-wake (TtW) methodology, while IMO’s draft Lifecycle Assessment (LCA) guidelines apply a well-to-wake (WtW) approach. It pointed out this inconsistency and said that “onboard CO2
8 We’ve changed our minds” about carbon capture, says Sigurd Jenssen
capture can be included only in IMO GHG regulations based on WtW methodology.”
No decisions were taken on how to incorporate CCS into CII, EEDI or EEXI during MEPC 79, “owing to time constraints”, the meeting’s summary reported. Instead, MEPC agreed “to further consider proposals related to onboard CO2 capture” at MEPC 80, which will take place 3-7 July.
“This means that the documents already submitted are kept alive, which is important”, commented Eirik Nyhus, DNV’s environment director, in conversation with The Motorship. He is also a member of Norway’s IMO delegation and is concerned that there will be little time during that meeting to discuss it in depth, because that meeting will have a busy agenda. It is possible, he said, that the topic could be moved on to the next intersessional meeting or to MEPC 81, which will take place in 2024.
Even if it is discussed during MEPC 80, no firm decisions will be taken on how to apply CCS, Mr Nyhus believes. Not only does it present technical challenges, “but there’s also the issue of what happens with the CO2 once it gets delivered to shore”, he said. “We do not want to see it vented outside the port gates, so environmental integrity is a crucial point.”
Another potential destination for captured carbon could be to use it as a feedstock for making renewable methanol or ammonia, something that would also have to be considered in any WtW calculation and the LCA guidelines, he suggested, since “if you use recycled carbon, there is a potential that would reduce [those fuels’] production footprint.”
It is not only fuel production that would benefit from
captured CO2. A submission by Liberia and the International Chamber of Shipping included a list of industries that can use the gas, such as the fertiliser sector, which they say uses 130Mt per year. Oil and gas processors use 70-80Mt/year for enhanced oil recovery, the paper noted, while other commercial applications include food and beverage production, metal fabrication, cooling, fire suppression and stimulating plant growth in greenhouses.
Asked whether shipowners might gain some form of carbon credit for delivering CO2 for recycling, Mr Nyhus said that this had not been discussed and “it would be really horrendously complicated to make such a system work.” He did not rule out some kind of market-based measure including CCS eventually being developed, but “that is for the post-MEPC 80 era.” A more likely outcome, he suggested, would be that companies would reflect such actions as part of their voluntary Environmental, Social and Governance (ESG) policies.
CII is due to be reviewed in 2025, with adjustments made if necessary to keep the industry on track towards hitting the 2050 target of reducing GHG emissions by 70%. So any changes to its formulation to take account of CCS may not be introduced until then, Mr Nyhus believes. In the meantime, CCS may eventually be addressed through IMO’s LCA guideline. While the first version is expected to be approved at MEPC 80, incorporating CCS may have to wait until a later version he suggested.
That will not be the end of the debate, however. “We still need to have the political discussion at IMO about how, and to what extent, should that guideline be applied to existing and future regulations.” Resolving that could take until 2025, he said. “We are eating the elephant in very thin slices.”
While IMO grapples with the technical and regulatory aspects of adopting onboard carbon capture and storage (CCS), it remains to be seen whether shipowners will embrace the opportunity.
We are planning to, says gas tanker operator Solvang. No, we probably won’t, says car carrier specialist Wallenius Wilhelmsen.
Solvang is one of several shipowners working with Wärtsilä Exhaust Treatment to deploy CCS technology and intends to install a full-scale pilot retrofit on one of its ethylene carriers, the 21,000m3 Clipper Eos. Wärtsilä has already built a land-based 1MW test system at its Norwegian headquarters and plans to fit the ship’s system this year.
When the contract was announced in 2021, Solvang’s CEO Edvin Endresen said that CCS “could be an important key to decarbonise the world’s deep-sea fleet.” The vessel is time-chartered to Japan’s Marubeni Corp, which is “committed to cooperating with Solvang and Wärtsilä … in a mutual effort to drastically reduce the CO2 footprint of the vessel”, the 2021 statement said.
More recently, in November 2022, Wärtsilä secured its first order for CCS-ready 35MW open-loop scrubbers for four 8,200TEU container ships. Their owner and Asian yard have not been disclosed.
Wärtsilä’s head of exhaust treatment, Sigurd Jenssen, told The Motorship that interest in CCS “is massive. Every shipowner is keen to understand how this could be applied to their fleet.” It offers them a way of addressing emissions that is lessdisruptive than alternatives because of the amount of CO2 reductions that can be achieved, despite the cost and operational compromises required, he said.
For example, although additional tanks are required to store the CO2, the added volume is no worse than the additional volume required to store less energy-dense fuels such as LNG and methanol, and certainly better than storing ammonia or hydrogen, he said.
On the Solvang vessel, for example, two deck-mounted tanks will hold about 720m3 of CO2 that will be recovered by Wärtsilä’s carbon capture equipment, which will remove about 66% of the emitted gas. That is sufficient to support a transatlantic crossing and although the extra weight will affect cargo capacity, it is not enough to make the operation uneconomic, Mr Jenssen said.
But for Roger Strevens, vice-president of global sustainability at car carrier Wallenius Wilhelmsen, the 3:1 ratio between the weight of CO2 produced and fuel burned
is a significant concern. Then there is the space needed both for storage and for the capture equipment: “We are volume carriers, constantly squeezing the engine, machinery and fuel into the smallest possible spaces,” he said.
He is also worried about operational impacts. Matching CCS-equipped ships to ports with suitable reception facilities would limit their scheduling flexibility and he foresees practical difficulties in discharging the stored material. “Our preference is to have no obstructions whatsoever on the berth” and offloading “several thousand tonnes of frozen CO2 is going to occupy some space.” In short, as things currently stand, “we don’t see very good prospects for carbon capture onboard our vessels,” he said. But CCS could work for other operators. Those providing short haul services with regular calls at their home port, for example, may find CCS an interesting solution, he said.
An ABB study based on three years of operational ship data mounts the compelling case for integrating battery power onboard modern icebreakers, writes Samuli Hänninen, who specializes in icebreaking vessels at ABB Marine & Ports
The maritime industry is still at the formative stage of realizing the gains available from batteries, but the ability to scale up to megawatt-hour levels is not the only attraction for the zero-emission technology. Evidence newly disclosed by ABB suggests that the improvements made to power efficiency and responsiveness can make a decisive difference for the performance of icebreakers operating in extreme conditions.
Demanding high installed power, icebreakers should also be efficient across a wide variation in power needs, especially given that they operate in areas where emissions face particular scrutiny. However, conventionally the need for high dynamic loads is met by oversizing generators running on fossil fuel – a solution which is highly inefficient when engine loads are low.
Slow load ramping is also a common problem for diesel engines, while new generation LNG engines are even less responsive. At the propulsion controls, icebreaker operators are often ready to respond but left waiting for engines to ramp up. Time lags like this can encourage what some call a conservative approach to operations, and others call out as inefficient: if an engine takes 10 minutes to warm up to 100 percent power, crew operating at loads in the margin between two and three engines will prefer to run continuously on three.
Battery power integration by ferry and cruise ship owners offers strong guidance on the way instantly available stored energy can improve the performance of other ship power sources by assisting peak shaving or spinning reserve, as
well as providing a zero-emission power alternative. Understandably, newbuilds account for the vast majority of battery installations to date, but the number of cruise, ferry and cargo ship retrofit projects is growing.
As one of the leading companies driving sea-going battery power, ABB has evaluated the impact of installing an energy storage system (ESS) onboard icebreaker Polaris. Delivered in 2016 but still one of the most advanced icebreakers in the world, Polaris was the first ship in its class to run on liquefied natural gas (LNG), driving four Low Pressure Dual Fuel (LPDF) engine driven gensets. The vessel is owned and operated by the Finnish state-owned company and has combined electrical power plant output of 22.5 MW.
Like many icebreakers before it, Polaris features an Azipod® propulsion system from ABB – in this case two 6.5 MW stern units and one 6 MW bow unit from the Azipod® VI product family ranging from 6-17 MW, developed and tailored for icebreaking vessels. The high torque induction motors in the propulsors come with a simple and durable construction and can deliver up to 180 percent of over torque, ensuring that the propeller rotates even during the heaviest ice interactions.
Plug-in simulation
Using data drawn from three full winter seasons operating in the Bay of Bothnia, ABB’s Polaris study sets a new precedent in evaluating the impact of ESS technology on a new ship type.
8 ABB’s simulationbased study indicated that installing a battery can play a positive role in the power system of the Polaris
With an overall objective of simulating a battery system that could absorb large load variations, to improve fuel efficiency and ramping capability, ABB uploaded powerplant load profile data from real operations in ice to a MATLAB file. The model evaluated the impact of an ESS Installation on total greenhouse gas emissions, primarily CH₄, in addition to reducing fuel consumption and improving the dynamic performance of the system.
The model worked using a hybrid power system that was simplified in comparison to real operations onboard Polaris, to consist of four main generators (auxiliary generator was excluded), one 4.5MWh and one main system load, with the battery to be charged from the generators. The dual-fuel engines were simulated to operate in gas mode or in diesel mode, with experience-based assumptions made on reduced engine efficiency at lower loads. A linear correlation between load fluctuations, fuel efficiency and CH₄ emissions was also assumed.
Based on a profile that saw Polaris at sea for four consecutive weeks, around 4,000 hours of operations were modelled over a 28-month period.
In the anecdotal example given, a conventionally powered ship working in ice-infested waters and operating at loads at the margins between two and three engines was maintained on three engines, based on the precautionary principle. However, the instant availability of additional power from a 4.5MWh ESS implies room for maneuver. The ESS will provide immediate propulsion power to cover the time it takes for additional main engines to come online, for example.
In the scenario given, safe operations should be possible for more of the time with two engines online supplemented by peak load battery power. From the Polaris simulation, ABB suggests that the immediate availability of power as needed would reduce main engine usage hours by up to a very substantial 46 percent of online time, with consequent fuel and emissions savings, and other knock-on benefits for maintenance and through-life cost.
Together, the operating profile and expectations on environmental footprint make the vessel type the ideal candidate to exploit the peak loading, spinning reserve and
zero-emission power capabilities available through integrating batteries into propulsion. For LNG, ABB’s simulation suggests that including the ESS onboard Polaris would result in a 38 percent CH₄ reduction, 16 percent less fuel consumption (based on 46 percent reduction in engine hours); for diesel, the result is a 10 percent reduction in fuel consumption, 36 percent reduction of engine hours.
By being more responsive to power load needs, the addition of the ESS will also improve the icebreaker’s overall safety margin: an icebreaker engine working to overcome an ice ridge can be exposed to sudden over torque condition, for example; the power ramp with an onboard ESS-equipped vessel is no more than 10-12 seconds.
Despite the limitations of the model, ABB concludes that it is evident from the simulations that installing a battery can play a positive role in the power system of ships like Polaris. As well as reducing the number of engine running hours, the specific example highlights that the use of batteries would also lead to a reduction in the methane slip.
In addition, integrating battery power may be a route to broadening the safety envelope of icebreaking in a way that could allow for reduced installed power/number of main engines. It may be argued that, if most situations requiring full ahead power are relatively short in duration, it would be feasible to increase the capacity of the ESS and do away with one main engine. In some applications, ABB believes this is worthy of further study.
8 The Polaris, the world's first LNG-powered icebreaker, was delivered to the Finnish Transport Agency in 2016. The Polaris features a 6 MW Azipod unit at the bow and two 6.5 MW units at the stern
8 ABB has significant experience delivering electric propulsion systems to icebreakers or ice-going vessels. In 2019, the Azipod-propelled Norwegian coastguard vessel KV Svalbard visited the North Pole as part of an international research project
Christoph Rofka, Accelleron’s president Medium & Low Speed products and VP Communications at CIMAC, discusses changes that are affecting the wider maritime propulsion market, and Accelleron’s response in an exclusive interview with The Motorship
8 Christoph Rofka noted that techno-economic comparisons between CCGTs and ICEs for energy generation reserve capacity were changing as higher levels of renewable energy capacity entered regional and national grids
Before turning to Accelleron’s own activities, Rofka took stock of the intense pace of technological development taking place in the large bore engine market. The technical programme for the upcoming CIMAC congress in Busan in June 2023 revealed the range of areas in which industry participants have been working on solutions.
Rofka also agreed that the depth and breadth of the programme was a testament to the industry’s response to the IMO’s target of reducing greenhouse emissions by 50% by 2050, compared with 2018.
“The decarbonisation targets have transformed research, which [had been] dominated by traditional targets such as higher efficiency, higher power density, and new engine types… before the industry began to take the IMO targets seriously. But we’re seeing a completely different dynamic [and] a different level of spending by engine manufacturers and their partners on R&D.”
Rofka was keen to stress that the current momentum was not restricted to the marine industry, and that a number of promising developments are emerging in the energy market.
Looking ahead, Rofka noted that the International Maritime
Organisation (IMO) was expected to discuss proposals to introduce more ambitious greenhouse gas (GHG) emission reduction targets at the MEPC80 meeting in June.
“Regardless of whether the IMO strengthens its efficiency goals, it is clear that the maritime industry will need to embrace alternative so-called Net Zero Carbon fuels. For ocean going vessels, this will mean that the current propulsion system, with a low-speed main engine directly coupled to the propeller, is here to stay. So the challenge is that this technology has to be ready and available to burn future fuels. And this is where, of course, all the key technology providers, including us at Accelleron, have to play their part.”
Rofka noted that in addition to LNG, the current range of alternative fuels for the marine market include methanol, while the first green ammonia projects are expected to be delivered after 2025.
The emergence of the first large-scale green ammonia export projects, such as the 1.2 million tonnes per year NEOM green ammonia project in Saudi Arabia which was approved a few days before the interview on 1 March, were expected to
be positive in terms of creating demand for carriers, which in turn would create demand for dual fuel engines capable of running on the alternative fuel as fuel.
“It is important for our industry to move forward with confidence, because this is no time for placing bets on something exotic. Given the tight timeframe, you have to get it right from the beginning. And there's not too much time for, let's say, trying out fundamentally different routes that potentially lead to nowhere.”
From the perspective of a technology supplier, Rofka noted that the development of technology solutions for alternative fuels was an interesting challenge. The Motorship notes that this is particularly the case for ammonia, where the first full scale engine tests have yet to be undertaken.
The uptake of dual-fuel ammonia engines is likely to be running ahead of the establishment of ammonia bunkering availability. This early ramp up period was likely to see vessels continue to operate on diesel-like secondary fuels. As a result, the engine concepts are initially expected to remain close to those currently used. From a turbocharging perspective, the difference is that the expected rise in fuel prices is likely to drive a focus on efficiency and specific fuel consumption.
However, if fuel availability ceases to represent a key constraint on specifying alternative fuel engines in the future, we will expect to see an increasing number of pure-ammonia engines. Rofka noted that while hydrogen was not currently expected to play a significant role in deep-sea shipping, it had quite distinct combustion characteristics.
Rofka noted that one unexpected consequence of decarbonisation requirements was that it mightn reveal new opportunities for ICE installations in stationary markets.
The rapid rise in renewable energy generation that is being seen in many parts of the world is creating additional demand for power generation capacity with very high response rates to stabilise the grid. The need for accompanying investments in load balancing capacity becomes increasingly important once the proportion of renewable power generation from solar power or wind powered sources exceeds a certain threshold for a variety of technical reasons, including the possibility of natural
The emergence of monofuel engines operating on ammonia or hydrogen would be likely to see engine specifications change “quite a bit” from today’s requirements. This would pose some challenges as monofuel NH3 or monofuel H2 engines were likely to evolve in completely opposite directions. Engineers would be likely to rely on richer burning strategies to overcome ammonia’s recognised weak flammability and poor ignitability characteristics.
The high flame speed and highly ignitable nature of hydrogen combustion means that engineers would increase air to fuel ratios combustion, which would lead to higher pressure operations on the turbocharger compared to current solutions.
This means that Accelleron is swiftly preparing for the emergence of demand for new turbocharger solutions within highly compressed timeframes. Rofka noted that Accelleron already commenced by simplifying its portfolio and by fundamentally altering its product development model.
Rofka explained in an interview with The Motorship in May 2022 that Accelleron was seeking to introduce a modular design approach towards technology development, in which
fl
uctuations in wind and solar generation, as well as the inertia certain types of power plant provide the grid.
Combined cycle gas turbines have come to replace internal combustion engines for power generation purposes, as their responsiveness and the low cost of natural gas have made them attractive solutions to meet peaks of energy supply alongside base load generation.
However, Rofka noted that the introduction of renewable energy generation at high levels into some local and national grids was creating different loading patterns, with reserve power generation sometimes standing idle for extended periods of time, which was changing the economics of CCGT
comparisons against ICEs.
CCGTs tend to suffer from low cycle fatigue when started up irregularly to a greater extent than ICEs, while ICEs also tend to have a higher efficiency over a wider load range than CCGTs, which are typically ‘tuned’ for an optimal load.
Rofka noted that while batteries can meet short-lived spikes in demand, ICE based capacity might be able to meet longer-term fluctuations in demand.
“We are seeing projects from US, Italy, the UK and in Ireland,” Rofka said.
This opportunity in the power market was quite distinct from existing demand for ICEs for base load power generation in geographically remote areas , islands or an urgent need for capacity build-up.
It's completely different [now]. We are going forward, and we learn as we go forward. And then we have to adapt fast. So that's a completely different philosophy, and then we have to adapt our processes accordingly
component level advances (in the turbine or compressor stages) could be introduced into the turbocharger design platform as advances occur. In parallel, Accelleron was examining the possibility of introducing a design platform specifically designed to allow the core of the unit to be replaced during port stays.
Earlier engagement with industry partners was likely to offer advantages in contributing to the capture of requirements earlier in the product development cycle. This was also a logical response to a fast-evolving market where the future demands for turbocharger solutions and the pathway of development is no longer predictable for the next five years or more.
“It's completely different [now]. We are going forward, and we learn as we go forward. And then we have to adapt fast. So that's a completely different philosophy, and then we have to adapt our processes accordingly.”
“For us it is strategically key that we position ourselves on the most relevant future fuel engine platform developments. So it's not only then to provide hardware for testing, that that feels best and but also to support with engine performance simulation.”
The modular design strategy, collaborative working approach with engine builders, and integrated digital and physical asset approach outlined by Rofka are expected to form part of Accelleron’s upcoming low-speed turbocharging solution launch.
The approach to low-speed turbocharging is still on track to be unveiled at the CIMAC Congress in June in Busan. Accelleron still plans to bring the new concept to market by the end of 2024.
But the concept is expected to go beyond the simple introduction of alternative turbocharger configurations into the low-speed maritime market.
Development tests conducted in 2023 had confirmed that the solution would make a significant improvement in efficiency levels. “Our ambition remains that we want to be the turbocharger maker with the highest efficiency levels and that will not change,” Rofka said firmly.
But Rofka stressed that the modular design was also expected to act as an enabler for quite advanced future service concepts that cannot be implemented today from a design perspective.
The solution was also expected to integrate digital elements into Accelleron’s service offerings. “So the new hardware together with digital and our service capabilities amount to a service offering that is a step change, if not an evolutionary leap.”
While the development of solutions for alternative fuel powered engines is a major focus for Accelleron at present, Rofka did note that the company was studying nascent technologies, like fuel cells, for potential product niches. There were certain prerequisites for such technologies to attract Accelleron’s interest, including a close relationship with the internal combustion engine. In addition, they were expected to include a strong service element to be compatible with its existing product portfolio.
One such opportunity might exist in the application of turbocharger technology to fuel cells, where the technology can be used to increase the output and efficiency of fuel cells. Fuel cell technology still needs to overcome some technical and commercial hurdles and is unlikely to become commercially viable in the short term. Rofka was at pains to
note that despite a flurry of small-scale pilot projects, there was little prospect of fuel cells entering into the marine market before the end of the current decade.
Off-highway expansion plans
Christophe Rofka also noted that as an independent company, Accelleron was free to pursue commercial opportunities in other segments of the market.
The company has begun Intensify its activities in the high speed diesel engine market, and has already launched its first dedicated products.
Rofka noted that the off-highway Market, which is currently below Accelleron’s product coverage in term of engine power and served by turbocharger makers from the automotive industry, provides interesting opportunities.
The automotive market was highly competitive, and faced longer term challenges as electrification and the introduction of hybridisation were likely to reduce the importance of the internal combustion engine in the segment over the medium term. As a result, some suppliers were choosing to exit the market.
However, the challenges facing competitors in the automotive space were likely to create opportunities for established OEMs like Accelleron in the off-highway market. Rofka noted that the off-highway market was unlikely to electrify to a similar extent as on-highway, owing to wellknown challenges with power densities, which would create a demand for solutions capable of handling engines operating on alternative fuel. “But then they won't have the technology supply from the automotive sector. While we believe that that offers a potential entry for us to extend our portfolio towards the [high-speed] end, it's a long journey.”
8 Accelleron is planning to introduce a novel approach to low-speed turbocharging at the CIMAC Congress in June in Busan, South Korea
For us it is strategically key that we position ourselves on the most relevant future fuel engine platform developments. So it's not only then to provide hardware for testing, that that feels best and but also to support with engine performance simulation
Keynote panel topic: The cost of decarbonisation & who is going to pay?
Some of the topics you can expect to discuss with the keynote panel will include carbon levy funding, funding for investment, national incentives, funding for new technology & hypothecation.
Sponsored by:
Book your place now and save 20%
Secure your place at the 44th Propulsion & Future Fuels Conference, the leading technical conference that provides:
A meeting space for the latest innovation in transoceanic zero-carbon shipping Technical solutions for decarbonising the shipping sector of 5,100 ships Multiple networking opportunities.
Supported by:
THE Media partner:
MOTOR
Meet and network with 200 CEOs and technical directors from ship owning, operating and management policy makers, shipbuilding, fuel, equipment and technology suppliers. Visit: motorship.com/PFFBOOK
Media supporters:
Contact: +44 1329 825335
Email: conferences@propulsionconference.com
Swiss-based WinGD is upping its offerings to the market with its latest development for conditionbased maintenance in its WIDE suite that is currently undergoing trails, writes Samantha
8 WinGD expects Enhanced WiDE to simplify engine maintenance for crew and fleet managers
WinGD in partnership with Bernhard Schulte Shipmanagment (BSM) are currently carrying out a pilot project for its latest development in condition-based maintenance module for its WiDE suite that the company says will reduce costs associated with maintenance of engine components. It is expected that with this development it will enable predictive maintenance for two-stroke engines in the long term.
The pilot project will monitor five of the engine components onboard the LNG carrier that are crucial for reliable engine operation, which will include cylinder liners, piston rings, exhaust valves, fuel pumps and fuel injectors. The monitoring will recommend condition-based maintenance intervals by using algorithms to estimate their remaining useful life.
The trial vessel is a BSM-managed LNG gas carrier with two five-cylinder WinGD X72DF engines. The crew on the vessel, using the WiDE engine diagnostic system, will be provided with the possible causes to diagnose faults and prompted to add relevant maintenance tasks. The scheduling of the tasks will be calculated based on the predicted remaining useful life for the components affected.
The WiDE remote support team will validate and improve the system throughout the project, which is expected to last for 14 months.
The pilot project is also being run in collaboration with Propulsion Analytics, the software company that assisted in the development of WiDE, with verification provided by classification society Lloyd’s Register. The lass society has developed a special notification for condition-based monitoring systems, adding emphasis on the importance of this technology for the industry.
Rudolf Holtbecker, Operations Director, WinGD highlights
the need in the industry for condition-based and predictive maintenance that: “many operators are seeking to adopt this maintenance concept to reduce maintenance costs, but they need a robust system approved by class societies.” The shipping industry is being pushed by environmentally regulations to adopt more efficient technologies, requiring continuous learning and increasing monitoring and maintenance demands.
However, one of the advantages that condition-based monitoring will have for the future is that it will help “relieve the crew” of unplanned maintenance, notes Holtbecker. Better planning will also make it easier for crew to ensure that parts are available when needed.
mponents need
e new to the WiDE suite anges upgrade mes with the engine”, comments
Condition-based maintenance will give more insight into the condition of engine components and when they need renewal, moving two-stroke engines a step closer to predictive maintenance. The new upgrade to the WiDE suite will not need any systems changes needed, “just an upgrade of the WIDE software that comes with the engine”, comments Holtbecker.
of its
t is offering ext step in WiDE suite
ntenance, the
Through the pilot project and upgrading of the WiDE suite WinGD is expanding its digitalization services that it is o customers. As part of its next step in development of the WiDE suite condition-based monitoring is expected to take maintenance intervals from fixed time-based maintenance intervals to true condition-based maintenance and further predictive maintenance, the company has explained.
JUNE 2023 Southampton United Kingdom 13 15 TO
For more information visit: seawork.com contact: +44 1329 825 335 or email: info@seawork.com
The 24th edition of Europe’s largest commercial marine and workboat exhibition, is a proven platform to build business networks.
Seawork delivers an international audience of visitors supported by our trusted partners.
Seawork is the meeting place for the commercial marine and workboat sector.
12,000m2 of undercover halls feature 500 and equipment on the quayside and pontoons.
Speed@Seawork on Monday 12 June at the Royal event for fast vessels operating at high speed for security interventions and Search & Rescue.
Speed@Seawork Sea Trials & Conference
The European Commercial Marine Awards (ECMAs) and Innovations Showcase.
experts, helps visitors to keep up to date with the latest challenges and emerging opportunities.
The Careers & Training Day on Thursday 15 June 2023 delivers a programme focused on careers in the commercial marine industry.
New advanced combustion technology designed to reduce methane slip is being developed for Wärtsilä’s large bore engine platform after earlier success with smaller engines
The EU-funded Green Ray project is developing onengine technologies for low-pressure dual-fuel engines – both 2- and 4-stroke – as well as a novel aftertreatment concept. These solutions will be advanced to a high state of technology readiness, including demonstrators installed on two newbuildings and one retrofitted to an existing vessel.
As part of the project, Wärtsilä is developing technology specifically for low pressure 4-stroke dual fuel engines that enables methane slip reduction, increased efficiency and lower operational costs at all engine loads. The project is in line with Wärtsilä’s aim is to demonstrate slip rates of one gram per kWh, a significant reduction compared to existing performance.
“This research will allow us to build on the continuous improvements made in reducing methane slip from gas engines over the past 20 years,” said Sebastiaan Bleuanus, General Manager, Research Coordination & Funding, Wärtsilä Marine Power. “Taking these solutions for newbuilds and retrofits to near commercial readiness will be an important step for the long-term viability of LNG as a marine fuel.”
The technology development for the project targets the largest four-stroke engines on the market as widely used by cruise ships, ferries and gas carriers. It follows and expands on the developments achieved as part of the EU-funded SeaTech project which began in 2019 and included also the development of sophisticated control and combustion systems for Wärtsilä dual-fuel 31 engines. The resulting optimisation could only be achieved by using the advanced engine concepts Wärtsilä already employs.
Another facet of the work undertaken by the Green Ray project will be to measure methane slip on existing modern engines, to update public domain data that can be as much as a decade behind current technology. “This is a key collaboration we are seeing in the Green Ray project,” says Bleuanus. “Industry and academia are pulling together not only to solve the problem of methane slip, but to also make insightful progress on current emission levels.”
Wärtsilä will also develop an on-engine technology for 2-stroke engines around a patented LNG injection system to reduce methane slip from tankers, container ships, etc.
Additionally, Shell has developed a proprietary methane abatement catalyst system that has been lab tested and scaled up to a field demonstration, where it was proven to be effective not only in significantly reducing methane slip (over 90%), but also in handling typical compounds that can degrade the catalyst, via the inclusion of a guard bed. It can be used as a stand-alone solution or combined with either the 2- or 4-stroke engine developments to further reduce methane slip.
The new technologies will be demonstrated at sea in real application during the project in collaboration with the Green Ray partners. Coordinated by VTT Technical Research Centre of Finland, these project partners include Chantiers de l’Atlantique, CMA CGM, DNV GL, Shell, the Finnish Meteorological Institute, MSC Cruises Management and non-
profit organisation Revolve Water. The project will run until 2027, with commercialization of the technologies expected soon after.
The four-stroke combustion developments will be trialled on one of the Wärtsilä large bore engines to be installed on a dual-fuel cruise ship newbuilding currently being built at Chantiers de l’Atlantique for MSC. For Bleuanus, the approach involving collaboration between such partners accelerates the development process. “In collaborative projects where we have customers involved, we can actually achieve the technology demonstration quicker than what was possible, say, a decade ago. We really see that through these collaborative projects the pace of development is increasing.” He cites other projects that Wärtsilä has partnered in as further examples of this collaborative approach, including the Chek coordinated by the University of Vaasa and Wärtsilä’s Partner Campus.
He believes that the inclusion of shipping in the EU ETS is a positive move for the industry, as it will enable the revenue obtained to be fed back into more collaborative projects aimed at large-scale decarbonisation. “It’s not about one or two demo ships. It’s about 60,000 ships involved in international shipping, so we really need to get the scale up happening.”
The Green Ray project has received funding of around €7 million from Horizon Europe. It will run until 2027.
This research will allow us to build on the continuous improvements made in reducing methane slip from gas engines over the past 20 years
As the latest phase in the continual refinement of the company’s direct-drive propulsion offering, MAN Energy Solutions has upgraded its ultra long-stroke, 500mm-bore engine, writes David
TinsleyThe revision of the G50ME-C9.6 as the G50ME-C10.7 has yielded an extended speed and power layout and reduced specific fuel oil consumption(SFOC) values.
As the Mark 9.6, the diesel is widely favoured for installations in medium-range(MR) tankers, Ultramax and Kamsarmax bulk carriers and other vessels. The new iteration ensures broad market applicability with the added benefit of gains in economy. The optimised fuel efficiency is especially advantageous in the context of existing and upcoming regulations, including the stepwise stricter Energy Efficiency Design Index(EEDI).
At its L1 rating, the existing G50ME-C9.6 provides a 1,720kW output running at 100rpm, giving an MCR range of 8,600-15,480kW across in-line configurations from five to nine cylinders. Down the scale, models chosen at the L4 rating deliver 1,020kW on a crankshaft speed of 79rpm.
The G50ME-C10.7 offers the same top-end 1,720kW per cylinder outturn on 100rpm, but is being released in five- to eight cylinder formats, dispensing with a nine-cylinder unit, while providing L3 and L4 ratings at just 75rpm, slower than that of the Mark 9.6 engine. The elongation of the power diagram is most graphic at the L4 point, where output per cylinder is 970kW at 75rpm.
The Mark 10.7 engine is to be released initially only as a fuel oil burning series. It will be available in Tier II mode with either high-load(HL) optimised or low-load bypass(LL-EGB) matching, or as a Tier III engine with either high-pressure selective catalytic reduction(HP SCR) tuning(where the
reactor is fitted upstream of the turbocharger) or with exhaust gas bypass(EGRBP) matching.
Improved SFOC has been achieved for all variants across the load range. For example, in the case of the high-load optimised Tier II engine, the fuel burn at 100% load has been reduced to 164g/kWh from the 167g/kWh of the 9.6 design.
In fact, savings in the order of 3g/kWh are promised throughout. Compared to the 172g/kWh at 100% load of its predecessor, the G50ME-C10.7 in its Tier III version promises 169g/kWh. Similarly, the Tier III HPSCR model of the latest engine is catalogued at 167g/kWh on full load relative to 170g/kWh of the Mark 9.6 type.
Woodward is developing a comprehensive new range of injection systems applicable for new and future fuel powered engines including methanol and ammonia.
Designed to support the global energy transition to low carbon fuels, the comprehensive portfolio of injection systems for P2X fuels in large engines will range from 100 kW/Cylinder to over 1000 kW/Cylinder –to enable all possible combustion concepts.
For applications that require the highest levels of power density and efficiency, Woodward is developing a High-Pressure Dual-Fuel (HPDF) platform for methanol and ammonia injection with full diesel backup capability.
The new range of direct solenoid actuated injection systems is perfectly tailored to meet market requirements for simpler and retrofitted systems, including
methanol injection systems for Port Fuel Injection (PFI) and Direct Injection (DI). The injectors are designed for optimal atomization of the fuel to enable good mixing and minimize wall wetting.
For gas engines that are adapted to run on gaseous P2X fuels such as hydrogen and ammonia, Woodward’s well-known SOGAV gas admission valves are also being optimized to withstand the properties of
these fuels such as poor lubricity, corrosion behaviour and hydrogen embrittlement.
“We are currently collaborating closely with engine OEMs to design and test a range of injector systems that will meet the performance demands of new engines. Current development stages range from full field validation through to SCE and R&D phase with extremely positive results to date,” said Dr. Michael Willmann, Director of EngineeringLarge Engine Systems at Woodward.
“There is a broad variety of combustion concepts for these fuels, and the best choice strongly depends on the target application for the user, whether they are in the marine and shipping sector, power generation or wider industry applications where these engines will be used. We are seeing the creation of a range of solutions to meet specific needs, ” said Willman.
Independent studies have confirmed that Schottel’s dynamic rudder propeller SRP-D offers significant advantages for dynamic positioning operations in service vessels, the company has announced
The SRP-D was launched in 2022. In addition to the embedded electric main drive (LE-Drive) and a propeller shaft with an eight-degree tilt, the SRP-D features a number of improvements, including reduced propeller acceleration/deceleration times and a high-speed azimuth steering system with reinforced gear components, thus achieving double the rotational speed.
A joint study with MARIN and Polish ship designer MMC investigated the effect of thruster response latencies on DP positioning. The study found that the SRP-D rudder propeller demonstrated much-improved position accuracy and enhanced operability of the vessel.
A separate study was conducted with DNV and Norwegian ship designer VARD in which the solution’s performance was simulated to assess the effect of the SRP-D on a service vessel’s operational performance and environmental impact. The study that the DP footprint can be significantly reduced, coupled with expected fuel savings of up to 30 percent depending on the operating point.
Michał Olko, Vice-President and Chief Designer, MMC Ship Design commented that “the results presented in MARIN’s dynamic DP simulations indicated a significant benefit as regards the operability of the vessel. We’re convinced that this fast responsive thruster will be the preferred choice for SOVs, allowing them to meet operational requirements in terms of DP accuracy and overall performance.”
The dynamic properties of the SRP were investigated within a time domain level three analysis commissioned by classification society DNV. The simulation was performed on the numerical model of a real Service Operation Vessel (SOV) equipped with SCHOTTEL propulsion systems. Its positionholding capabilities were examined under extreme weather conditions: high winds, strong currents and effective wave heights of 2.5 metres and 3.2 metres. The results of the extensive simulations at DNV showed a significantly improved positioning accuracy while halving the DP footprint. This permits successful gangway landing operations even in rougher conditions, thus increasing the service life of the vessel throughout the year. Furthermore, every single landing is performed more efficiently, saving time and fuel.
Luca Pivano, Principal Specialist DP Simulations, DNV added “Our simulation results show that with faster thruster response the vessel’s station-keeping performance is greatly improved, resulting in smaller DP footprints compared to traditional thruster response. This benefit is even more obvious in harsh weather conditions.”
Thanks to the lower gearbox that has an additional eight degrees downward tilt, the interaction between propulsion
unit and hull and the propeller flow interaction are reduced. As established in the simulations, these optimizations result in an increased thrust efficiency during DP. Depending on the thruster’s operational direction, simulation also revealed up to 50 percent less thrust loss and fewer forbidden zones.
Karl Randle, Principle Naval Architect, VARD: “The CFD results of the inclined gear box clearly show a significantly reduced thruster hull interaction or Coandă effect for zerospeed station-keeping. This is especially evident for inward flow directions and areas where the flow interacts with or flushes the skeg or other thrusters. The benefits of reduced thrust deduction could be significant for designers and owners in many applications when such considerations are included in detailed analysis procedures.”
Furthermore, the implemented optimisations yield additional savings in fuel consumption. Thanks to the faster response time of the propulsion, the vessel can be quickly held in position with only minor corrections being necessary. This prevents major corrections in position having to be made which would require more power. Depending on the operating point and environmental conditions, this can save up to 30 percent in fuel during DP operation compared to standard rudder propellers.
8 The results of the extensive simulations show a significantly improved positioning accuracy while halving the DP footprint
8 The faster response time of the SRP-D prevents major corrections which would require more power
Hosted by:
Growing Sustainable Supply Chains: Short Sea Shipping & Intermodal Networks Conference Programme
Royal Liver Building, Liverpool, UK
Sponsor: Supporters:
A neutral pan-European network dedicated to the promotion of short sea and feeder shipping and the intermodal transport networks that support the sector.
Chairman: Nick Lambert, Co-Founder & Director, NLA International Ltd
visit: coastlink.co.uk
contact: +44 1329 825335
email: info@coastlink.co.uk
#Coastlink
Media partners: GREENPORT
DAY ONE – Wednesday 3th May 2023
08:30 Coffee & Registration
09:00 Chairman’s Welcome
Nick Lambert, Co-Founder and Director, NLA International Ltd
SESSION 1: MARKET SECTOR OVERVIEW - THE NEW NORMAL IN AN ADAPTING MARKET
Considering Trends, Market Forces, and emerging Opportunities for Short Sea Feeder Services and Logistics
09:10 Port’s Welcome Address
Claudio Veritiero, CEO, Peel Ports Group
09:25 Gold Sponsor’s Address
09:35 Keynote Presentation
Roger Megann, Managing Director, WEC Lines UK Ltd
09:50 Network Development & Appraisal in the Short Sea Sector
Mike Garratt, Chairman, MDS Transmodal
Considers the trend towards longer maritime crossings and the use of non-accompanied modes in short
sea shipping to Great Britain and the case for incorporating the public interest cost benefits of such switching in the appraisal of road, rail and port infrastructure development.
10:05 Building a case for a greener transport alternative for smaller cargo volumes –
Short Sea Shipping and intermodal cargo flow
Michael Rosenkilde Lind, Senior Commercial Manager, Port of Aalborg
A presentation from the Port of Aalborg with the research and findings of the process of trying to establish a new Ro/Ro route with only smaller local stakeholders along with major cargo flows on rail in transit.
10:20 Q&A
10:40 Coffee & Networking
11:15 PANEL DISCUSSION: Post-Brexit & Post-Pandemic: Are we where we need to be?
Panel Moderator: Richard Ballantyne OBE, Chief Executive, British Ports Association
Panellists include:
Doug Bannister, CEO, Port of Dover
Howard, Knott, IEA Logistics Consultant, Irish Exporters Association
Andima Ormaetxe Bengoa, Director - Operations, Commercial, Logistics and Strategy, Port of Bilbao Authority
Sean Potter, Commercial Director, DFDS A/S
12:30 - 14:00 Lunch & Networking
SESSION 2: HOW TO PROMOTE GROWTH AND DELIVER RESILIENT END TO END SUPPLY CHAINS
A look at the changing landscape in end-to-end intermodal networks & the just in time supply chain.
14:00 Opening Address
Michelle Gardner, Deputy Director – Policy, Logistics UK
Logistics UK will highlight the opportunities in the supply chain for innovation and modal shift to benefit the environment and consumers as well as operators throughout the supply chain.
14:15 What mode of transport uses Ports?
Stephen Carr, Group Commercial Director, Peel Ports Group
We explore why the true answer to that question defines why both industry and consumers need to think differently about the role and the functions of modern ports.
14:30 Practical examples of building resilience into a supply chain using intermodal services
Geoff Lippitt, Chief Commercial Officer, PD Ports
How intermodal, short sea shipping, RoRo, LoLo and last mile delivery road haulage can interlink to provide resilience and enhance capacity for ports and operators
14:45 Port of Antwerp-Bruges – providing total intermodal connectivity solutions
Justin Atkin, UK & Ireland Representative, Port of Antwerp-Bruges
With excellent connections to the hinterland by estuary and inland barge, rail, road, and pipeline, discover how the Port of Antwerp-Bruges provides totally integrated transportation solutions, helping shippers ‘green’ their supply chains.
15:00 Q&A
15:20 Coffee & Networking
15:50 PANEL DISCUSSION: Freeports: Driving change for coastal shipping and the supply chain?
A discussion on the impacts and benefits of Freeports. How will supply chains adjust? Xx
Panel Moderator: Richard Ballantyne OBE, Chief Executive, British Ports Association
Panellists include:
Giles Jones, Project Manager, Liverpool City Region Freeport
Ben Harraway, General Manager, Portico Shipping
Nolan Gray, Freeport Director, Tees Valley Combined Authority
Arne Mielken, Managing Director, Customs Manager Ltd
17:15 Conference Day 1 Wrap-Up – Conference Chairman
17:30 Conference Close
17:30 Evening Drinks Reception at the Royal Liver Building
18:45 Conference Dinner at the Royal Liver Building
DAY TWO – Thursday 4th May 2023
08:45 Arrival: Coffee
SESSION 3: SUSTAINABILITY & THE ENERGY TRANSITION – A ROUTE TO SHIPPING FREIGHT SUSTAINABLY
The journey and challenges for ports, shipping & logistics in achieving net zero
09:10 Chairman’s Opening & Summary of Day 1
09:15 Keynote Presentation
David Browne, General Manager, MAERSK
09:30 A Green Port’s Journey to Net Zero
Tanya Ferry, Green Port Consultant, Royal Haskoning DHV
Learn how Royal HaskoningDHV is helping the world’s ports embrace digital innovation, decarbonisation, and new-found resilience. And discover the challenges, savings, and operational benefits to be found on the journey to Net Zero.
09:45 Port of Amsterdam – At the forefront of the transition
Mark Hoolwerf, Deputy Director, Port of Amsterdam International
The port of Amsterdam is a global energy hub, meaning that it stands for a significant decarbonisation challenge. This presentation will focus on how the Port of Amsterdam approaches the energy transition, with a focus on its overall strategy and recent initiatives and developments. This will include subjects such as the role of hydrogen, clean shipping, and the collaboration with different parts of the value chain.
10:00 Lessons learned with shore power
Jacob Bjarkam, Business Development Manager, PowerCon
Shore power is expected to be scaled tremendously. PowerCon will provide key insights and lessons learned on how to best to implement this technology successfully, by sharing hands-on experience from past projects plus the latest news and innovation.
10:15 Q&A
10:35 Coffee & Networking
11:10 PANEL DISCUSSION – Driving Efficiency through Data & Port Collaboration
Improving supply chain efficiency through data, collaboration, and digitalisation
Panel Moderator: Tim Morris, Head of Corporate Communications, Associated British Ports
Panellists include:
Richard Willis, Technical Director - Port Operations & Technology, Royal HaskoningDHV
Eleni Bougioukou, Innovation Manager for Energy & Sustainability, Port of Tyne
Grant Hunter, Director - Standards, Innovation and Research, BIMCO
Ross McKissock, Director of Unitised, Port of Tilbury London Limited
12:20 Conference Wrap up by Conference Chairman
12:30 Lunch & Networking
13:50 Working Group Session ‘What are the blockers governments need to remove to enable the industry to accelerate to Net Zero’
Facilitated by the Chairman Nick Lambert, & Stephen Carr, Group Commercial Director, Peel Ports
15:10 Coffee & Networking
15:30 Technical Visit at Port of Liverpool Hosted by Peel Ports Group, delegates can enjoy a tour of the Port of Liverpool encompassing Liverpool 2.
Conference Fee
Premium Package
£625GBP/ €750euro
Cost per delegate
Standard Package
£590GBP/ €710euro
Cost per delegate
Fee Includes
• Conference attendance including lunch & refreshments
• Electronic documentation
• Technical Visit 4 May 2023
• Conference Dinner 3 May 2023 (Premium Package)
• Presentation download (Premium Package)
Booking Online coastlink.co.uk/buy or complete and fax the booking form below to +44 1329 550192. On receipt of your registration, you will be sent confirmation of your delegate place
For further information on exhibiting, sponsoring, or attending the conference, contact the Events team on: +44 1329 825335 or info@coastlink.co.uk
Venue Royal Liver Building, Pier Head, Liverpool L3 1HU, UK Visit coastlink.co.uk
BOOK ONLINE OR COMPLETE THIS FORM AND FAX TO +44 1329 550192
(Please copy this form for additional delegates)
Please tick all that apply :
Please register me for the Coastlink Conference 2023. I will attend the following:
Conference dinner (3rd May 2023)
Technical Visit (4th May 2023)
Members of supporting associations will receive a discount
I am a member of
HOW TO PAY
*UK registered companies will be charged the standard rate UK VAT
Bank Transfer: Mercator Media Ltd, HSBC Bank plc, GBPaccount, Sort Code: 40-21-03, Account number: 91894919
SWIFT/BIC8: HBUKGB4B BRANCH BIC11: HBUKGB4131C, IBAN: GB61 HBUK 4021 0391 8949 19
Bank Transfer: Mercator Media Ltd, HSBC Bank plc, EURaccount, Sort Code: 40-12-76, Account number: 70235247
SWIFT/BIC8: HBUKGB4B BRANCH BIC11: HBUKGB41CM1 IBAN: GB35HBUK40127670235247
Prepayment is required in full for entry to the conference. Full terms & conditions are available at mercatormedia.com/our-business/terms-and-conditions
Credit/Debit Card: Complete the form with your card details
I have paid by bank transfer
Please fax form. Do not send by email as we cannot guarantee the security of card information.
Please charge my card (delete as appropriate) Mastercard/Visa/Amex
Card Number
Name on Card Expiry Date
Security Code
Credit Card Billing Address
Signature
In many ways, it is a surprise that shipping’s “bigger is better” philosophy did not start to feel the strain sooner. But the pandemic certainly brought forward the schedule, with the few vessels then-deployed on the spot market suddenly raking in cartoonish earnings. In one example, X-Press Mekong, a 2,743 TEU Singaporean feeder built in 2020, fixed a charter of 55 days at $175,000 per day
If one was lucky enough to get in early, a secondhand ship purchase would be earning profit within weeks. But what was impossible to ignore about this handful of vessels was just how old they were. According to Alphaliner data, the average container vessel in the up-to-999 TEU size range is over the hill at 17.4 years old. Unlike X-Press Mekong, most small vessels are not even designed to be feeders, particularly: rather, they are the flagships of yesteryear, from a time when 4,000TEU was still ‘big’.
In an article, the UN council on trade and development (UNCTAD) warned that Europe is facing “a chronic shortage of vessels in short sea shipping.”
“Can we then expect new capacity to come on-line over the next two to three years? Not so soon. Shipping supply can only be increased with a lag: it takes about two years to build a vessel,” the report read.
The maritime industry is already starved for small vessels, then. But other post-pandemic trends are likely to compound the situation. Many manufacturers and retailers are seeking to spread their supply chains across several countries in order to prevent the risk of another covid-like situation bringing their sales to a halt. This will mean that shipping will
have to change, as well – from a situation where China’s onestop-shop enables economies of scale, and produces many of the arguments for 20,000 TEU giants, to a fragmented one where many countries feed into the whole.
The smaller the required vessels become, the worse the economics of the traditional prime-mover and propeller combo become, and the more attractive battery-electric propulsion begins to look. Feeders are bad performers under the IMO’s new CII measure, as they spend a lot of time in port, and sail at higher average speeds. The case is being made by several new small vessel designs including Yara Birkeland, Japan’s Project e5, and an as-yet unnamed DB Schenker feeder ship.
Converging with this is an explosion in another sector, offshore wind, now finally reaching US shores. As well as wind-turbine installation vessels (WTIVs) a generation of new service and operation vessels (SOVs) will be needed to support this segment, not only at the building stage, but also over the course of maintaining the turbines. With their extraordinary requirement for manoeuvrability coupled with the growing possibility of being charged by turbine power at sea, these vessels will create additional demand for electric propulsion.
An ABB installation aboard double-acting ferry P&O Pioneer, and its upcoming sister vessel P&O Liberte, point the way for how this will come about. Making its way from Guangzhou Shipyard, China (passing Greece at time of writing), the vessel is fitted with four ABB Azipod thrusters. These are powered in part by an 8.8MWH battery pack supplied by XALT Energy.
Although the ferry is ultimately fossil-fuelled, using four Wärtsilä diesel engines, the addition of a battery performing load-levelling duties allows the vessel to boast a 40% reduction in fuel consumption compared with a conventional diesel-electric vessel, and “…the most sustainable ferries ever to sail on the English Channel,” on P&O’s social media.
Meanwhile the ABB Azipods add to the vessel’s operational flexibility, enabling it to turn on the spot and approach the dock from any direction.
Electrified propulsion is almost completely efficient, and it is inevitable that vessel electrification will grow as more effort is made to curtail emissions. Podded propulsion therefore, still relatively recent, will likely experience a similar trajectory of improvements and optimisations as the more mature technologies such as four-stroke engines.
Wärtsilä is taking a digital approach, through its OPTI-DP programme. Using advanced computational fluid dynamics (CFD), Wärtsilä made the determination that tilting its thruster’s driveshaft and propeller downward by 8 degrees
Podded propulsion manufacturers have been squaring up to a new challenge recently – ice. Ice-class pods are markedly different in appearance from their openwater brethren, with a bulbous motor housing. The reasons for this are several, but crucially, ice-going ships must generate a massive amount of torque, as it is presumed that they must proceed against continuous resistance from ice. This is not unlike the operating condition of a tug during a towage operation.
For this reason, thruster manufacturers do not want to situate their electric motors inboard of the vessel, which would risk raw power being lost to shaft lines and gearings. Instead, the motors are situated in the water, with as direct a linkage to the propeller as possible. This has the added benefit of reducing noise, because the noisiest parts of the propulsor, the gears, are unnecessary. It also cuts down on the need for lube oils,
nearly eliminates the problem of the ship’s hull geometry interfering with the thruster’s aft-flow, bringing its ‘thrust deduction factor’ down from 0.14 to 0.02.
This has informed Wärtsilä’s thruster design since. “There is minimal friction with the hull and power losses from the thruster,” said Wärtsilä product performance manager for thrusters Petra Stoltenkamp, at a conference in January. “The optimal tilt was 8 with the flow from the thruster not hindered by the vessel hull or other thrusters. We have shown that less power is needed, by optimising propulsion, reducing design costs and lead times.”
There may be many more exciting changes on the way. With electrification of ship propulsion on the rise, podded propulsion, tunnel and bow thrusters, will fit into this new paradigm in a way that the conventional combination of prime mover, driveshaft, propeller and rudder will not. For their manufacturers, there has probably never been a more exciting time to be in the business.
A permanent change
A recent trend in the design of thrusters has been concerned with reducing their footprint. Typically, a good way of
minimising the environmental risks from an emission of oil to sea.
A large motor housing bats away ice chunks before they can reach the propeller; and if the propulsor takes a knock, there are no shafts to bend or be knocked out of alignment.
ABB thrusters are popular in Arctic and Ice applications, with many of the vessels operating in Russia’s Yamal peninsula, including LNG tankers Christophe de Margerie and Yakov Gakkel, fitted with ABB Azipod propulsors. The former made history in 2017, crossing the Northern Sea Route (NSR) in icy conditions without icebreaker assistance, using its ABB Azipods.
More recently, ABB Azipods have been installed on a Van Oord jack-up turbine installation vessel Boreas, under construction at Yantai CIMC Raffles shipyard in China. The installation has an enormous combined power of 16MW, providing extreme power
for transportation of heavy turbine bodies, as well as acute precision when positioning pre-jack-up phase.
“The ease of installing the Azipod system was another key factor in our decision to contract ABB; it is a matter of plugging the ready-made units into the vessel hull, saving considerable time and effort in the construction process,” explained Shiyan Sun, Director, Supply Chain Management Centre, Yantai CIMC Raffles Shipyard.
But it has not all been plain-sailing. After a protracted legal case, ABB paid out more than $150m in compensation after several Norwegian Cruise Line vessels fitted with ABB propulsors experienced failures. In one case, Norwegian Star, an ABB propulsion failure left the vessel stranded at sea, “… imperilling the safety of passengers and crew, and causing substantial harm to NCL’s reputation and business," according to an attorney representing NCL.
Most of the noise in a thruster comes from the blade tip cavitation, there are no blade tips in this design. This thruster was able to get a Silent E notation, because there are no gearings, and we have optimised hydrodynamics with no cavitation
narrowing the profile of a thruster underwater is relocating its motor and hydraulic systems inboard of the vessel, and connecting to its propellers using a driveline. This has had various benefits; it makes the thruster’s systems easier to inspect and repair by the crew. It has also led to marked improvements in thruster hydrodynamics.
Modern thrusters tend to be sleeker and thinner, with fewer bulbous shapes beneath the waterline, and a better swept area for the propeller, allowing smaller propellers to provide the same propulsive power as a larger thruster with a motor situated inside the hub. Locating the motor inside the vessel’s hull also has the benefit of putting a noise barrier between it and the ocean, meaning less noise is emitted underwater – known as ‘underwater radiated noise’ (URN).
However, there are compromises. For one, increasing the inboard footprint of a thrusters means there is less space. It also increases the noise inside the vessel, and for various new vessel types including SOVs, which have large accommodation blocks for turbine engineers, this is unhelpful.
But recently, thruster manufacturers have been able to improve on these principles further, with the application of permanent magnet technologies. This has changed the design of the thruster once again. Kongsberg’s AZ-PM azimuthing propulsors seem at first glance to be fitted with Mewis Ducts, but in fact, they are ‘rim drive’ thrusters, with a stator inside the rim which manipulates a circular magnetic field. A set of permanent magnets inside the rotor causes the propeller to spin.
There are many advantages for this configuration. The thruster is the motor, requiring no motor inside the hull, saving space and reducing noise internally, and having no need for a driveshaft improves the propeller’s efficiency by 10%. This is compounded by the lack of a need for inboard hydraulics and cooling systems.
Another aspect is that by implementing rim drive thrusters, Kongsberg has stumbled upon another benefit – designed this way, the rotors have no tips. This prevents the vortices normally created at the tip of propeller blades, known as cavitation, better optimising the propeller inflow, and eliminating a major source of URN.
Kongsberg is not the only company to have developed a rim-drive thruster; Norway’s Brunvoll and Germany’s Schottel both have their own versions. But the Kongsberg design differs somewhat, featuring a prominent central hub, where the others have none.
Asked whether the hub added hydrodynamic resistance, Kongsberg Technical Product Manager Permanent Magnet Thrusters, Agatha Kalvatn explained that it was “the opposite” – the hub further improves hydrodynamics by preventing cavitation in the centre of the thruster.
In fact, this principle has only just been discovered by the MIT Lincoln Laboratory, in drones, which have recently been fitted with ‘toroidal’ figure-8 propellers with no tips. This redesign has reduced the noise output of drone propellers dramatically.
“Most of the noise in a thruster comes from the blade tip
cavitation, there are no blade tips in this design,” explained Kalvatn, discussing her company’s range of permanent magnet thrusters. “This thruster was able to get a Silent E notation, because there are no gearings, and we have optimised hydrodynamics with no cavitation.”
Kongsberg has also optimised the geometry of propellers in its TT-PM tunnel thrusters, leading to a simplified design. Conventionally, Kongsberg tunnel thrusters were driveshaftdriven with inboard motors, leading to an asymmetrical layout which provided slightly more thrust in one direction than another. But with a rim drive thruster necessitating no driveshaft, Kongsberg has been able to optimise the propeller blades on its tunnel thrusters, to provide equal thrust in both directions.
The PM thrusters’ growing reference list includes Hurtigruten polar cruise vessels Roald Amundsen and Fridtjof Nansen, which each feature two TT-PM thrusters of 2m diameter, which each develop 243kN of thrust. The Havila Kystruten coastal cruiseferry quartet Capella, Castor, Polaris and Pollux are also so equipped, as well as Allseas Oceanic, a subsea vessel.
“By the end of 2024 we will have 60 units installed,” Kalvatn said. “There are rare Earth metals used, as with any permanent magnet design – future designs will consider how to reduce these in construction.”
Kongsberg has shown that it still wants to compete in the non- rim-drive segments however, with a new retractable thruster design, the ULE-PM, in January, featuring a prominent driveshaft and central hub.
By the end of 2024 we will have 60 units installed. There are rare Earth metals used, as with any permanent magnet design – future designs will consider how to reduce these in construction8 Kongsberg’s permanent magnet rim-drive thruster
The all-new 2023 Seawork Conferences will deliver bitesize in-person sessions to help commercial marine and workboat operators face the challenge of reducing operational expenditure at the same time as meeting
Learn how your business can create cost savings in alternative fuels, hybrid propulsion, technology, and design.
Alternative fuels – how operators can make
operator costs
Vessel Design – Optimising
If you are interested in speaking, attending, or sponsoring these sessions please contact the events team on conferences@seawork.com or +44 1329 825335
Book to attend: seawork.com/our-conferences
Media partners:
Rune Garen uses his business development role at Kongsberg to pose some difficult questions
Rune Garen has seen a lot in his nearly four decades in the maritime industry. The naval architect and marine engineer, who is now senior vice-president for business development at Kongsberg Maritime, has a particular focus on hydrodynamics and told The Motorship in an exclusive interview that his job “is to try to connect new things that are coming up and consider how they will impact our industry.”
One of his long-held passions is that we should learn from nature. In our March issue, we quoted him making that point in a retrospective article looking at flapping foils as a means of propulsion. In our recent interview, he cited other intriguing examples.
One of the biggest paradoxes, he said, is the speed achieved by the fastest fish. A bluefin tuna, for example, is typically about 2m long, weighs around 200kg and can reach speeds of about 70km/h. Now imagine a towing-tank experiment with a ship model of those dimensions at such speeds, he said: the power needed would be about 75kW “but when you ask marine biologists if that is possible, they say no.”
In fact, tuna generate as little as 1.1kW, Mr Garen said, so “there must be something that we need to understand to close this gap.”
There is no single explanation, he went on. Its flapping tail clearly acts as a propulsive foil, but “how are they controlling and, most importantly, reducing not only the skin friction, but all the resistance elements they are exposed to?” There could also be effects related to the tuna’s mass-elastic system, in which its backbone stores and releases energy. “We need to dig into this”, he said.
With the release in February of the artificial intelligence (AI) chatbot ChatGPT, some have expressed concerned about AI’s implications. But Mr Garen believes that shipping should embrace AI, saying that it would become “a layer above” existing control technologies. This, he said, “will enhance the way we might optimise vessel operation in the future.”
It might not initially take over ship operations, however. “My hope is that AI can help us in sorting out all the information that we are bombarded with … such that we can make better decisions than before.” But eventually, it “will become a very important part in assisting autonomy in the marine business”, but only when that becomes fully practical. For the foreseeable future, ships will still carry crew so AI will be useful in optimising the man-machine interface, he believes.
Both Kongsberg Maritime and Rolls-Royce Marine – where Mr Garen was director of propulsion research and technology before it was bought by Kongsberg in 2019 – had autonomous ship projects, with Kongsberg Maritime’s most advanced project being Yara Birkeland, designed to carry containerised fertiliser for Norway’s Yara from its factory in Herøya to its export terminal in Brevik.
Kongsberg provided much of its technology, including sensors for remote and autonomous ship operations and its electric drive, battery and propulsion control systems. It went into operation in 2021 as a crewed vessel but during this year
and 2024, it is expected to become fully autonomous and to be approved for un-crewed operation.
Kongsberg has also developed a series of underwater autonomous vehicles (AUVs), of which Hugin Superior is the most advanced. It is used for subsea surveying and can operate at depths down to 6,000m. Vessels such as these will grow in number, size and capability, Mr Garen predicted, and he did not rule out the possibility of cargo-carrying AUVs in the future.
This would avoid wave-making resistance, which can lead to “devastating” energy losses, he said, “so if you can get rid of that troublesome resistance component by operating just under the wave affected zone … that's a very interesting prospect.”
One Kongsberg technology that is already saving energy is its patented rim-drive thruster concept, in which the thruster blades and a connecting yoke are fitted with magnets to form the rotor of an electric motor. The surrounding duct serves as a stator, creating a high-torque motor that is driven by its rim
8 Kongsberg’s patented rimdrive thruster uses thruster blades and a connecting yoke fitted with magnets to form the rotor of an electric motor
rather than its shaft. This gives it a very quick thrust response – from zero to 100% in less than two seconds, he said.
This arrangement has other advantages – not least because there is no space required for an electric motor inboard. It is also quieter than other propeller arrangements, which reduces underwater noise pollution and could make it attractive for applications such as passenger shipping: two recently delivered passenger ships for Norwegian coastal services, Havila Castor and Havila Capella, are fitted with Kongsberg rim-drive bow thrusters.
Late last year, Kongsberg Maritime received its first orders for these drives to be used for commercial propulsion applications, marking a breakthrough into this market, Mr Garen said. They are to be fitted to supply and construction vessels for the offshore wind sector.
But rim drives are not suitable for every application. At low speeds – especially on vessels where bollard pull is important – the nozzle creates valuable thrust from the water flow that the propeller forces past it. But at higher ship speeds the nozzle becomes a drag, ruling the concept out for highspeed applications.
Mr Garen continues to thinking about future technologies, again taking inspiration from nature. Cavitation, for example: it is a perennial problem because of the damage it can cause to propellers, but in nature it has been put to good effect.
He referred to the mantis shrimp, which is a crustacean that typically grows to about 10cm long. It uses cavitation like a hammer to attack mussels to get at their meat: the
cavitation force exceeds what the shrimp could deliver just from its muscle power.
In the same way, he wonders, is there a positive application of cavitation for shipping? It is a question that has intrigued him for several years; “these are complex things and it takes a lot to understand them. But once you have understood them, then you can start to speculate.”
This might seem vague, and he agrees that “there is a long way to go”, but he believes “we should take inspiration from considering how to turn a negative thing into something more positive.”
Nominees for the “Best CO2 Utilisation 2023” innovation award at this year’s Conference on CO2-based Fuels and Chemicals include the company On which has produced the first ever shoe made from a feedstock of carbon emissions. The shoe, and the award, demonstrate the wider innovation picture that shipping is being drawn in to, and it is one being backed by regulators.
In February 2023, the U.S. Department of Energy announced nearly $2.7 million for five R&D projects that will help to accelerate national and international deployment of carbon capture and storage (CCS) technologies for permanent geologic storage or for conversion to other valued uses. And in March 2023, the European Commission launched its Net-Zero Industry Act which in part aims to accelerate the use of CCS. This is expected to have a flow-on effect to shipping as the technology is developed and adapted, particularly to suit hard-to-abate sectors.
A project led by Windship Technology Limited which includes partner Leilac, a subsidiary of Calix focused on the decarbonisation of cement and lime, demonstrates the potential for cross-over from land-based industry. The project combines wind power and a lime-based carbon capture solution for the emissions from conventional diesel engines. It has been awarded £5m by Innovate UK.
Integration of the carbon capture system with the ship’s engines can enable waste heat recovery from the capture reaction, reducing fuel demand. Lime is a highly effective sorbent for the capture of CO2, but for this solution to provide a net reduction or elimination of emissions, the lime used for capture must be produced with low or zero carbon emissions, using shore-based decarbonisation of the lime. Leilac’s patented technology can produce low emissions lime by efficiently capturing the unavoidable process CO2 emissions released from limestone, without additional chemicals or processes.
Leilac’s technology is compatible with clean energy sources, such as hydrogen and electricity, and also alternative fuels, enabling flexible and economical pathways
for the production of zero emissions lime and cement. It is proven at pilot scale, including through its pilot plant, Leilac-1, that has been in operation since 2019 with a capture capacity of 25,000 tonnes of CO2 per year. A demonstration plant, which aims to prove a low-cost module with a capture capacity of 100,000 tonnes of CO2 per year is due to open in 2024, paving the way for commercialisation of the technology at any scale.
This maritime version of the system is compatible with a wide range of ship types, including tankers, container ships and cruise liners. It is retrofittable, fuel agnostic, and can be scaled to meet the decarbonisation ambitions of each ship.
Noting the benefits of research and development already undertaken by the cement and lime industries, Leilac CEO, Daniel Rennie said, “This project marks a significant step in developing a potential route for the efficient and low-cost decarbonisation of the shipping industry. Marine shipping is a particularly hard-to-abate sector, and the very strong synergies that can be made from leveraging the large-scale industrial decarbonisation efforts in the lime and cement industries – combined with the innovative renewable approach by Windship – is an exciting development.”
The project aims to demonstrate the low-cost potential of the proposed decarbonisation solution for shipping and pave the way for zero emissions lime to be used for reducing or eliminating emissions from conventional diesel-powered vessels. The key objective of the project is to design, develop, build and demonstrate a novel drive train system consisting of a single powerful wind propulsion device, working together with a trial carbon capture system to pave the route to zero emission propulsion for bulkers and tankers. This will be installed and trialled on a 15,000dwt bulker.
Carbon capture technology company Ionada recently welcomed DNV to its carbon capture pilot installation at Halliburton Labs in Houston. The visit marked the beginning of a collaboration between Ionada and DNV aimed at supporting maritime CCS projects. Ionada says its unique Hollow Fiber Contactor Membrane technology requires half
the space and 30% of the power of conventional marine solution carbon capture systems. The company completed a pilot system at Halliburton Labs in Texas late last year.
In March 2023, ABS granted approval in principle (AiP) to Value Maritime’s onboard CCS system. The Filtree System – a prefabricated gas cleaning system that filters sulphur and 99% of particulate matter – includes a carbon capture module that captures the CO2 onboard in a battery container. The technology allows vessels to capture up to 40% of CO2 emissions, with the potential of exceeding 90% in the future. The Filtree System has already been installed on over 20 vessels, and is set to be installed on the newbuild container vessels of Nordic that are operated by BG Freight Line and which will additionally feature the modular CO2 capture and storage system.
Also in March 2023, Lloyd’s Register (LR) awarded AiP to Rotoboost, a Nordic hydrogen production company, for its pre-combustion CCS system, Rotobox, which uses a thermocatalytic decomposition process (TCD) where part of the natural gas fuel supply is converted into hydrogen and graphite with a liquid catalyst.
The TCD process significantly reduces CO2 emissions, particulate matter and methane slip by producing hydrogen while capturing carbon in its solid form. The company says Rotobox has the capacity to reduce overall carbon emissions by up to 100%, depending on the heating method used. Converted hydrogen from the CCS can be used for fuel cells or as blend-in fuel for combustion engines or gas-fired boilers.
Kaisa Nikulainen, Rotoboost Chief Executive Officer, says the pyrolytic graphite produced is an excellent batterygrade anode material for electric cars and green steel production. “This circular economy creates a powerful tool to combat global warming and climate change on both land and sea. Our technology also demonstrates great potential in cost-effective production of green methanol and ammonia in land-based facilities, which further provides the shipping industry with other affordable alternative fuel options."
Rotoboost says its solution is easily scalable to meet future emission regulations, with lower electrical power requirements compared to conventional CCS systems and less storage space needed for solid carbon, allowing the system and associated storage to remain compact even for long voyages. The system is well suited to LNG carriers and other LNG-fuelled vessels, offering an additional option for shipowners for decarbonising.
For Andy McKeran, LR’s Chief Commercial Officer, the methane slip reduction potential is also significant: “Solving the methane emissions perception in the industry, through technology and evidence enables LNG to become a future fuel that is readily available today, subject to affordability –which ranks higher than any other alleged lower emissions fuel available today.”
As part of the MerVent 2025 project, GTT has received €4.66 million funding from Bpifrance for the design of an onboard CO2 capture system. The objective of the MerVent 2025 project is to design, build and operate, by 2025, the first commercial container ship with hybrid wind-assisted and synthetic fuel propulsion.
The consortium includes the shipowner Zéphyr & Borée, CWS, designer and manufacturer of the wing sails, the Centrale Nantes University with its research teams specialized in energy optimization, OSE Engineering for the design of intelligent operational performance solutions, and GTT for the design of a CO2 capture system on board. The system will capture at least 30% of the CO2 emissions of the alternative fuels being considered including LNG and methanol.
Wärtsilä has received its first order for a CCS-ready
scrubber systems for four 8,200 TEU container ships. Delivery of the 35MW open loop scrubbers is expected to take place in 2023. Wärtsilä will take measures to ensure adequate space for the future installation of CCS system, incorporate considerations for minimising idle load and optimising utilities, and prepare the control and automation system accordingly. The CCS-Ready scrubbers will also be designed for integration with a particulate matter filter. Wärtsilä is currently testing its CCS system at 70% capture rate and a pilot installation will take place within the next 12 months.
Wärtsilä Exhaust Treatment also has a strong focus on the retrofit market. Team Manager, Integration Engineering Su Len Quach, says that while it is tempting to only think about new vessels, given the finances, timeframes and technologies involved, the existing fleet cannot be left behind. “Not all vessels can be easily retrofitted for future fuels, for example, and low carbon options may only be speculatively available in the medium and long term on the routes they operate. In this challenging and uncertain atmosphere, the industry should turn to solutions that it already understands – and that can create a platform for further development.”
The business case for retrofitting a scrubber today is positive, he says. With the wide and relatively stable spread between high and low sulphur fuels, they continue to offer favourable economics and payback time has been around 18 months. With CCS, they become a futureproofed investment for achieving marine decarbonisation goals. “The technology has also reached a point of maturity and is globally available to a point where exhaust treatment may become as standard as a rudder. All this should give the industry optimism that existing solutions can help support the latest regulations, including CII and EEXI, and prepare for carbon pricing further down the road towards 2030 and 2050.”
8 Wärtsilä has received its first order for a CCS-ready scrubber system for four 8,200 TEU container ships
8 Rotoboost’s pre-combustion CCS system, Rotobox, uses a thermocatalytic decomposition process (TCD)
Last May, MAN Energy Solutions’ Two-Stroke Business announced that it has surpassed 2,000 orders for IMO MARPOL Annex VI NOx Tier III-compliant technologies for its portfolio of MAN B&W two-stroke engines. Today, the company reviews the evolution that has taken place to meet industry demand
NOx Tier III limits were introduced in 2016, and the milestone of 2,000 orders for MAN’s NOx technologies occurred just over a year after the company announced the passing of the 1,000 milestone in January 2021.
Among other statistics, MAN Energy Solutions reported that, determined by bore size, 50- and 60-bore MAN B&W engines account for most NOx solutions (37%). Additionally, exhaust gas recirculation (EGR) accounts for 724 versus 1,292 SCR solutions.
Furthermore, the company reported that some 67 engines were equipped with EcoEGR, representing about 9% of all EGR solutions. EcoEGR is a tuning method that lowers fuel consumption by recirculating a small amount of exhaust gas while operating in Tier II.
EGR prevents the formation of NOx by controlling the combustion process, while selective catalytic reduction (SCR) uses a catalyst and an additive to remove the NOx generated by the combustion process as an after-treatment process.
MAN has long experience with EGR technology and reported its first order in 2011, while its own in-housedeveloped SCR-HP (-High Pressure) won its first order in January 2019. This features a drastically reduced reactorsize, compared to rival systems, to which MAN Energy Solutions has been providing system approval since 2014.
Methanol-fuelled, MAN B&W LGIM engines have a special feature as explained by Kjeld Aabo – Director of New Technologies – MAN Energy Solutions, last year: “Through the use of water emulsion in the methanol, we are able to reach Tier III levels in methanol fuel-mode, completely removing the need for a dedicated NOx-abatement technology. Our introduction of this on our G50-LGIM engine gains us highly valuable service experience – especially in the methanol-carrier segment – while we see a very clear demand for full Tier III-compliance across all fuel types outside this segment by means of EGR.”
Since the first studies into EGR started with MAN Energy Solutions in 2004 and in-service tests were initiated from 2009 both the technology and its use has changed significantly. What at the outset was targeted solely as a measure to comply with IMO NOx emissions requirements, has turned out to become a cornerstone in modern engine design and optimisation, says Lars T. Danielsen, Promotion Manager, Two-Stroke Promotion & Customer Support - MAN Energy Solutions.
First developed purely as a high pressure application for high sulphur HFO, the technology has since then matured and been applied on both high and low sulphur engines, dual fuel engines as high pressure EGR, while R&D efforts and inservice tests have also been conducted as low pressure EGR.
Current versions utilize the high pressure configuration, with its superior response to engine load transients and black smoke prevention, and comes in both the standard
tuning for NOx Tier3 compliance configuration as well as the EcoEGR configuration, which provides fuel and emission reductions in both Tier 2 and Tier 3 operation modes.
“Providing compliance for close to 1,200 engines, and increased efficiency for more than 160 EcoEGR tunings and 250 ME-GA engines, MAN Energy Solutions and its licensees offer a wide range of system suppliers for the water treatment system (WTS),” says Danielsen. “Depending on fuel sulphur content the WTS will be tailored to the specific needs, spreading from a fully high sulphur HFO compatible system to the Otto Cycle methane fuelled ME-GA configuration which offers the latest generation 3 system where all water handling system components are incorporated onto the engine, providing superior hull integration and minimum engine footprint.”
In March 2023, MAN received orders from Hyundai Samho Heavy Industries and HJ Shipbuilding & Construction for MAN B&W G80ME-LGIM dual-fuel engines in connection with the construction of 9 × 9,000 teu container vessels for HMM Co. The engines, which are capable of operation on green methanol and conventional fuel-oil, represent the first order for the G80 bore size and will feature MAN’s EGR systems.
Shipping has come a long way in a short period of time when it comes to the uptake of new fuels. MAN Energy Solutions is proud to have brought three technologies – in the form of EGR, and low- and high-pressure SCR variants –to market so that owners and ship designers can select what best fits their individual project.
The tanker industry is monitoring the development of regulations produced by the California Air Resources Board (CARB) that will affect the segment from 2025
The regulations will extend existing requirements for container ships, reefers and cruise vessels to use shore power or alternative emissions control strategies to the tanker market from 2025.
The rules will begin to apply to tankers docking at the Port of Los Angeles and the Port of Long Beach from the beginning of 2025, while tankers in Northern California have until 2027.
The Motorship notes that the tanker terminals are expected to submit plans to the CARB one year prior to the entry into effect of the regulations. The CARB expects to see compliance plans for tankers calling at the Port of Los Angeles and the port of Long Beach by 1 February 2024, and for the terminals located in northern California by 1 February 2026.
Benjamin Buonviri, ABS Manager of Regulatory Affairs, explained to The Motorship that the CARB received feedback from industry on its air pollution control proposals as part of its interim evaluation. This feedback was duly considered when completing the interim evaluation. After completion of the evaluation, CARB held a workshop in February 2023, which was open to the public, to discuss the outcomes of the interim evaluation.
At the workshop, operators of tanker vessels raised the following concerns:
5 Lack of availability of non-shore power Approved Emission Control System (CAECS)
5 Timeline to adapt existing CAECS for use on tanker vessels
5 Safety concerns
5 Power availability and compatibility (for shore power equipment)
5 Logistical and operational constraints
5 Utility construction delay
CARB has reiterated that it is not aware of any industrywide limitations that prevent implementation of the regulation in California. CARB also indicated that if site specific restrictions are found to prevent implementation then these would be given due consideration. It was further noted that shore power is just one option and that there are other viable CAECS options.
As of the beginning of 2023, all tanker terminals in California have been determined as a regulated terminal or a low activity terminal. These terminal operators now have two years to prepare a CAECS for each or their terminals.
There will likely be implementation issues and CARB is working through these as they are being brought to their attention, however requests for delay need to based on objective evidence.
The CARB noted that many tanker terminal operators have not yet committed to a control strategy and have not yet provided complete terminal plans.
It is to be understood that the responsibility to provide a CAECS lies with the terminal. If through commissioning it is found that a vessel is incompatible with the CAECS, then the
vessel and terminal are responsible for finding another CAECS for the visit. Prior to the next visit the vessel should either modify itself to be compatible with the CAECS provided by the terminal or arrange a separate CAECS.
Euronav, the Antwerp based VLCC and Suezmax owner that has a fleet of 71 ships, would focus on modifying those vessels calling at the west coast USA, which would be between 10% and 15% of the fleet operated by the company, said Brian Gallagher, member of the management board of the company.
There could arise technical issues relating to the installation of shore power connections at the terminals in California – some of the quays are shorter than the vessels, which will force the electricity connections to be located at the bow end, near the pump equipment. There are also issues relating to a lack of common standards – both in the connections (plug standardisation) and in the electricity supply, which works 50Hz in the US, and 60Hz in Europe.
As to tackling these and other potential concerns, Gallagher said finding solutions would be on a case by case or port by port basis with each shipping segment. “As we saw with US Gulf exports competition between the ports tends to drive workable solutions - we would expect the same here,” he told The Motorship
Anne-Louise Dam-Rasmussen, Head of Communications at D/S Norden in Denmark, said that it was too early to comment as the legislation is not due to take effect until the second half of the decade.
8 The CARB is proposing to extend emission reduction rules to tankers calling at terminals in southern California from 2025 and northern California from 2027
Originally, the promise of LNG for the maritime industry had been the same performance for a reduced greenhouse gas contribution of 80%
8 Modern lowpressure and high-pressure dual-fuel lowspeed engines have seen significant reductions in their methane emissions since the first engines entered the market
As well as a specific reduction in CO2 emissions, liquefied methane burned very cleanly, in stark contrast to heavy fuel oil, with vanishingly little particulate matter (PM), and sulphur emissions. Even the more difficult to address nitrogen oxides (NOx), arising not from any particular impurity in the fuel but through incomplete combustion of atmospheric nitrogen, were lower with LNG.
So it came as a shock to those who had not realised -- or had pretended not to realise – when the IMO Fourth GHG Study 2020 revealed that methane engines leaked a whole lot. As a gas with a much higher global warming potential (GWP) than carbon dioxide, a comparatively small amount of leaked methane in ship exhaust, or ‘slip’, could quickly mitigate much of that 20% reduction in CO2 emissions.
SEA-LNG, an interest group whose membership includes at least nine fossil fuel companies, proposes that bio-LNG, captured from biogenic sources of methane such as municipal sewage and compost, may one day take over from fossil methane, and that LNG-fuelled ships are a crucial “pathway” to these circular-economy fuels.
SEA-LNG has criticised what it has called “sensationalist claims” regarding methane slip, as “a transparent attempt to distract the industry from investing in LNG.” The group cited one study which showed a diesel-cycle LNG engine was able
to reduce greenhouse gas emissions – whether CO2 or LNG – by 23%, compared with a diesel VLSFO equivalent. Another interesting finding was that the difference between an LNG dual-fuel diesel engine and an otto-cycle engine was substantial; the latter experienced higher methane slip.
In fact, MAN Energy Solutions (MAN) has suggested that the addition of direct gas injection, as seen in its range of MEGI engines, can amount to a reduction of as much as 90%, with a recorded maximum methane slip of 0.2%.
Despite this finding, manufacturers of LNG-powered engines have been unsatisfied with their level of methane slip, and have sought to devise solutions. Drastic reductions have been achieved by tweaking combustion variables, and a certain amount of progress has also been attributed to exhaust gas recirculation (EGR), which has been a reliable method for finishing off combustion in other cases, such as with NOx in conventional liquid-fuel engines.
This is the preferred method for Winterthur Gas & Diesel (WinGD), using its intelligent control by exhaust recycling (iCER) on its X-DF series of two-stroke engines. Introduced in 2020, the system, which cools and recirculates exhaust gases, allows for a reduction in methane slip of as much as 50%, WinGD has claimed.
Steve Esau, Chief Operating Officer at SEA-LNG, told The
Motorship that methane slip is “effectively solved” in twostroke diesels, “which make up more than half of the LNGfuelled vessels on order today.”
MAN, meanwhile, claims that it has halved methane slip from its engines over the last 15 years. Like SEA-LNG, MAN notes that substantial reductions are available on four-stroke engines by switching from otto to diesel cycle with the addition of direct gas injection. This is because a long period spent around the inlet and exhaust valves in the otto process leaves abundant time for gas fuel to evade combustion.
But it all adds up. What is needed, then, is a strategy to deal with the emissions after they leave the engine, and for this, the engine makers are reviving an old technology, methane oxidation. “Methane oxidation technologies are currently being lab tested by OEM’s where they are showing promising results,” said Esau.
MAN embarked on a project to improve LNG dual-fuel engine emissions with methane oxidation. The premise is to use a catalyst, and heat in excess of 500°C, to displace the hydrogen from methane (CH4), turning it into carbon (CO2) and water (H2O).
Some progress has been made. “The exhaust gas temperatures from MAN’s four-stroke SI and DF engines are in a range that supports the oxidation of methane,” Alexander Knafl, Vice President and Head of R&D Four-Stroke, MAN energy Solutions, told The Motorship
There are a number of precious metals which can be used as catalysts for oxidation: palladium, rhodium, and platinum. The choice of which is best suited to the application is a function of the heat being applied, with palladium offering the best characteristics at low temperature. At 500°C – the temperature being regarded as a minimum by engine manufacturers – theoretical conversion efficiency with a palladium catalyst reaches close to 100%; for platinum, it is closer to 40%.
Because 500°C is the minimum exhaust temperature required, methane oxidation or ‘oxycat’ technology is being touted only for four-stroke engines. “We started developing oxicats as a countermeasure to methane slip in 2017, and we’ve made great progress,” explained Knafl
According to the consensus among engine manufacturers, a methane slip reduction of 70% ought to be possible using methane oxidation technologies. Knafl declared that MAN had managed to meet with this expectation. “In the laboratory we have achieved our 70% methane slip reduction target.”
MAN will put oxicat into operation later this year, Knafl said. “The first pilot installation aboard ship in commercial operation will start in 2023. We anticipate this technology will be available as a commercial solution for methane slip reduction around 2025.”
The future of LNG
A new idea would eliminate methane slip at the source – and a number of other nasties, too. A company called Rotoboost
has developed a similar process to methane oxidation, but designed to be applied to LNG fuel before it reaches the engine, rather than after.
Approved in Principle by classification society ABS in late 2022, and Lloyd’s Register as of March this year, the ‘Rotobox’ process uses a combination of heat and catalyst – in a similar vein to oxycat – to separate liquefied methane into hydrogen gas and solid carbon, rich in graphite. Being solid, the carbon is straightforward to store, requiring between four and six times less volume than CO2 gas. Trivial to offload from a vessel, the graphite can even be sold as a commodity, used to make electrodes and even fuel cells.
Though it would not do anything to stem the demand for fossil methane, the Rotobox would enable existing vessels with LNG fuel tanks and lines to convert to hydrogen operation – and zero emission -- at reasonably low cost, and overcome issues relating to hydrogen’s low volumetric energy density.
The system would, LR Chief Commercial Officer Andy McKeran said, “…solv[e] the methane emissions perception in the industry through technology and evidence,” and would “enable LNG to become a future fuel that is readily available today, subject to affordability – which ranks higher than any other alleged lower emissions fuel available today.”
Despite its problems, SEA-LNG argues that LNG is a frontrunner thanks to the ease with which it can be replaced by biogenically-sourced alternatives. The methane given off by the decomposition of organic matter is practically the same as that which comes out of the seabed in the Gulf of Mexico.
“Bio-LNG is pure methane, so is identical to the highest quality LNG (in terms of methane number),” said Esau. “It can be used in existing LNG-fuelled engines, storage tanks and gas systems without any modification.”
However, if there is to be a bio-LNG revolution, it will suffer from the same issues on a tank-to-wake basis as LNG does now, if not addressed, he explains. “In terms of methane slip bio-LNG will be identical to LNG as methane slip depends on the engine technology and not the form of LNG used -- i.e.
Bio-LNG is pure methane, so is identical to the highest quality LNG (in terms of methane number). It can be used in existing LNG-fuelled engines, storage tanks and gas systems without any modification
used num. is a the gine th a it is ture eing ping and rers, sing atory t.” rcial y will and oost
ggy fossil, bio or synthetic.”Steve Esau
The Mærsk Mc-Kinney Møller Center for Zero Carbon Shipping (MMMCZCS) has published a paper Managing emissions from ammonia-fuelled vessels explaining the need for multiple different treatment technologies to manage emissions
Ammonia slip from fuel handling operations or engine exhaust gas is highly toxic and represents a safety risk for crew and passengers. Other exhaust emissions include NOx formed by incomplete ammonia combustion and N2O, a potent greenhouse gas (1 gram of N2O is equivalent to 265 grams of CO2). Additionally, CO2 emissions will occur if a fossil-based pilot fuel is used.
Different emission management technologies will be needed onboard to treat ammonia boil-off gas (BOG) from fuel tanks, ammonia mixtures from purging and venting operations, and combustion emissions from engines. Some of these technologies are already commercially available for maritime use, including reliquefication and selective catalytic reduction (SCR). Others will need to be adapted for ammonia as a fuel, including gas combustion units/boilers, catalysts, and water catchers.
Ammonia water catchers (chemical absorbers) can treat ammonia emissions from fuel systems resulting from purging operations or shutdowns. While such treatment is not required for LNG, it is usually released to the atmosphere, this is not suitable for ammonia due to safety concerns. Therefore, onboard treatment of ammonia or ammonia mixtures is needed.
A water catcher could consist of a system where the ammonia is vented to a knockout tank before the lines are purged with nitrogen. The liquid ammonia collected in the tank is pushed towards a recovery tank using nitrogen, while the vapours are mixed with fresh water within a water seal until there is sufficient volume for them to be returned to the engine for combustion.
Ammonia slip, N2O, and NOx emissions from engines could be reduced using SCR systems that use ammonia as a reducing agent rather than the more typical choice of urea. “For two-stroke engines, a high-pressure SCR integrated into the engine design can more efficiently reduce the potential increased NOx emission levels relative to conventional fossil fuels, due to higher temperature before the turbocharger,” states the paper.
A wide range of catalysts are used for reducing N2O in industrial processes, some without reducing agents, some using ammonia as a reducing agent. These technologies offer a potentially simple and compact solution where an
ammonia dosing system ensures adequate ammonia for NOx and N2O reduction if ammonia slip levels within the exhaust are insufficient. The challenges for using catalysts to remove N2O include potentially low exhaust temperatures during certain engine operating conditions and the potential for sulphur from the pilot fuel to affect catalyst performance.
Plasma reduction systems are currently being developed for methane slip emission reduction and could also potentially be used to reduce ammonia slip. These systems consist of a catalyst and an absorbent-free after-treatment technology that produces a non-thermal plasma containing a high density of electrons with high energy. This plasma is obtained from a dielectric barrier discharge generated by applying a high voltage between an arrangement of electrodes separated by a dielectric material layer. Exhaust pollutants are converted into harmless molecules via a chain of complex chemical kinetic reactions. This technology is still in the early stages of development, so it is too early to estimate power consumption and reduction rates.
The paper describes three potential configurations for emissions management onboard vessels. A simple option consists of a fully pressurized fuel tank with no BOG, one emission management technology for the fuel handling system and one after-treatment technology for NOx emissions, assuming that ammonia slip and N2O emissions are managed in the engine design.
For a design based on a semi-refrigerated fuel tank (at 6-8 bar) or a fully refrigerated fuel tank (at ambient pressure), BOG treatment will need to be added to the design. The most complex configuration would also add an after-treatment technology to manage engine exhaust emissions where ammonia NH3 slip or N2O emission levels are above acceptable limits. N2O emissions could be treated as part of an SCR in combination with NOx emissions if properly dimensioned.
The paper states that without collaboration, specific parts of the vessel design for handling emissions will be developed in isolation, and interconnected systems and technologies could end up unnecessarily oversized, inefficient, or costly. Additionally, the operational ammonia limits defined in existing class guidelines vary. “Coordinated alignment on thresholds for adequate risk management is required to secure standardisation and industry guidance.”
Any notion of meeting global emissions targets by running ships on alternative marine fuels could be heavily affected by the Biden Administration’s Inflation Reduction Act (IRA), if European policy makers fail to implement fiscal measures to support European shipping’s energy transition, writes
Patrik WheaterWhile the introduction this week of the European Commission’s Net-Zero Industry Act aims to scale up manufacturing of clean technologies to facilitate the bloc’s move to cleaner fuels, the current cost and availability of alternative marine fuels – LNG, green methanol, green ammonia, hydrogen – could make it difficult for shipowners to reach emissions targets without financial aid.
What’s more, since the US$369 billion in subsidies offered under the IRA could see European clean energy producers up sticks for the US, European shipowners may then be faced with the prospect of buying cheaper US fuel shipped to European bunker suppliers.
Many ship operators are privately expressing concern that uncertainty about fuel availability and volumes in five years or so could raise the risks associated with investments in methanol-fuelled engines. Financial risks for alternative fuels in general are exacerbated by the current market uncertainty and current power pricing.
Given the market infancy, buyers need to be confident that alternative fuel suppliers can deliver on their promises and deliver thousands of tonnes a year at a cost that makes economic sense.
Siem Offshore’s ESG Director, Jon August Houge, says soaring energy costs are already pushing liquefied natural gas (LNG) out of the alternative fuel market, and the “business case for green methanol or green ammonia is challenging”.
While the company operates a fleet of 28 specialised offshore vessels and is committed to ordering only zero emission vessels from 2030 and operating a climate neutral fleet from 2050, he said the LNG price is so high that charterers prefer low sulphur diesel.
“We have been looking at future fuels. But right now, it’s a big step to retrofit an existing vessel. When there isn’t a business case, we will need that collaboration with our charterers to make it happen. Ammonia, methanol and hydrogen will definitely be more expensive than diesel. So, in the transition period, I think you need some funding or subsidies to offset the cost,” he said.
For offshore vessel operators, the sustainability race is likely to be dictated by charterers who will have to accept an uplift in rates for chartering ships with the best emissions reduction technology. However, for operators that have to foot the fuel bill themselves, it’s a different story.
According to one European ferry operator, there are hundreds of potential methanol and ammonia suppliers out there looking for off takers, but few are in a position to guarantee long term supply commitments in the quantities and time frames required. The cost and volume of fuel available can be dramatic with tenfold differences depending on the location.
“We see [methanol and ammonia] projects in the US that are 50 times the size of projects in Scandinavia. Of course,
this has to do with the fact that they receive lots of subsidies in the US. So, they are at a competitive advantage and know they will be selling and exporting a lot unless something happens in the EU. No one knows where the supply demand curve is going to cross,” said the operator. “You need to create partnerships where you can invest in the future together.”
Ostensibly, the issue facing European shipowners is that the prices green energy suppliers are quoting is not what the shipping industry is capable of paying.
The impact of inflationary pressures since early 2022 means that prices quoted a year ago have risen to such an extent that it doesn’t make much economic sense to invest in cleaner fuels.
One of the consequences is that the price differential between US clean fuels and European clean fuels have widened so much that imports are equivalent to the cost of sourcing fuels from local European suppliers. “It’s a terrible scenario, it is totally nonsense,” said the ferry owner.
“We are very worried about this because we are actually in a position to really get started and speed up this green transition. But if you're facing a price increase, that is so substantial, then you're in a situation where you can't move forward. It is another roadblock that needs to be resolved. I think it's highly problematic that such a difference between the US and the EU approach to this transition makes it even more complicated.”
8 Other European ferry operators note that uncertainties around alternative fuel supply availability and prices raise financial risks, noting that production cost differentials between North American and European supplies are close to the freight cost at the moment
We see [methanol and ammonia] projects in the US that are 50 times the size of projects in Scandinavia. Of course, this has to do with the fact that they receive lots of subsidies in the USCredit: Stena
FuelSave, the Germany-based technology developer behind the FuelSave+ combustion optimisation product, is in the process of patenting a new development for exhaust gas recirculation (EGR) solutions, breaking new grounds in emission reduction to not only reduce NOX emissions but also reduce CO2 emissions in an after treatment process
8 Sima added that FuelSave was also in the final stages of developing two types of CO2 reduction solutions, which it plans to use to extend the emissions reduction potential of its EGR+ concept
The company has successfully completed trials for a combination of FS MARINE+ with an EGR add-on and demonstrated IMO tier III compliance, installed on a fourstroke test engine at FVTR Gmbh’s large engine test centre in Rostock in Germany. FuelSave’s CEO, Marc Sima, told The Motorship that the week-long full-engine trial had been conducted on a 6M20 over the entire load range.
“The EGR add-on works as an enhanced exhaust gas recirculation (EGR) with a lower recirculation rate due to the already reduced NOx emissions from the water and methanol injections, addressing challenges such as sooting that typically affect an EGR system.”
The test had been conducted by FuelSave as a performance validation, and the technology developer is in the process of patenting further evolutions of the system with a novel innovative injection and aftertreatment solution that uses nanotechnology in the EGR system, which will be put on the testbench as well in the near future.
Interestingly, the next generation EGR advance relies on nanotechnology advances to improve the efficiency of the NOx reduction (see Nanotechnology Solutions). Sima notes that in addition to improving the reduction of the primary fuel being used, the system is also capable of actively reducing the CO2 emissions to break new grounds in decarbonisation.
This advance, which Sima describes as “state of the art for
emissions reduction”, is extremely timely ahead of the extension of the EU’s Emissions Trading System to the maritime sector in 2024, and IMO-level discussions about the potential introduction of a carbon levy. “Our solution is being developed at just the right moment as ship owners and operators are focusing on reducing their CO2 and CO2e emissions.”
The potential of the solution to reduce CO2 emissions had been validated in lab scale tests, which had demonstrated “very sizeable” CO2 emission reductions. Sima noted that the company was developing a version of the solution that is aiming to achieve up to 75% CO2 reduction. Although FuelSave’s FS MARINE+ solution had been approved for use with a number of different 4-stroke manufacturers engines, Sima was keen to note that the EGR add-on will also be applicable to customers in the 2-stroke market, as well as the 4-stroke market.
Sima noted that “an EGR is a passive solution, so you avoid some concerns related to engine test validations and enable a very exciting retrofit pathway” and is keen to collaborate with engine OEMs. “In fact, that is one of the reasons we focused in the FVTR test bench tests to ensure that the test results were incontrovertible.”
Synergies with FS Marine+
Although Sima noted that the EGR development was expected to lead to improvements in its NOx reduction
performance, the solution already validated is creating synergies with Fuelsave’s FS Marine+ technology.
“We achieve synergies with our existing fuel injection solution by improving towards a cleaner combustion, and by controlling the temperature of the combustion to address some of the shortcomings of a typical EGR operation,” Sima said.
Sima added that FuelSave was also in the final stages of developing and validating two new types of CO2 reduction solutions, which it plans to use to extend the emissions reduction potential of its EGR+ concept.
“We are using nano base coatings and elements to improve the catalytic reaction for the reduction of CO2 in the exhaust gas stream of marine engines. We expect to be able to achieve a significant reduction in CO2 emissions, which has obvious advantages for our customers from a CII perspective and in their decarbonisation journey.”
The first trials of the CO2 solution have not yet been completed on the test bench, Sima noted, but the lab results are “extremely promising and exciting” and will provide one of the most exciting value adds to ship owners in the retrofit segment.
Sima noted that CO2 savings from 10-70% are feasible according to the lab results and simulations performed. The variation reflects the recirculation rate, as well as some of the product refinements.
Potential LNG applicability
Fuelsave also anticipated that the initial focus of the research for the EGR+ and CO2 modules had until now been on MDO / MGO and fuel oil (VLFSO/HFO). However, the solutions would be applicable to alternative fuel types.
The low parasitic load of the catalytic module meant it might be an interesting alternative to reducing the methane slip produced by dual-fuel engines operating on LNG.
Sima also noted that methanol was another interesting business case as the solution would lead to a carbon
sion for ings
For example, FS Marine+ creates a NOx buffer which can be used to optimise engine efficiency by traditional means of optimising the cylinder pressures and ignition timing. The increase in NOx due to higher temperatures and pressures inside the cylinder is counteracted by the dynamic liquid injections with proven methods of water and methanol injections. FS Marine+ in combination with an EGR+ add-on further increases this ‘NOx buffer’ – enabling a new emission tier while providing additional optimisation potential for further increasing the overall efficiency and cost savings through lowering the fuel consumption.
ance gine gas al in NOx nge,” is a PEX tical the
The system allows operators to fulfil IMO Tier III compliance standards for reducing NOx emissions even at partial engine loads and DP3 operation.
“We know that there is strong interest from the oil and gas sector and also from the DP3 offshore sector in general in emissions reduction technology that could maintain NOx emissions reduction performance across the load range,” Sima said. The new system operates at low loads, which is a known challenge for SCR systems, together with high OPEX through the catalyst consumables of an SCR and its logistical challenges along with its space requirements. “This is the basis of our value proposition against SCRs,” Sima said.
Marc Sima noted that patents are pending for the nanotechnology that underpins both the EGR+ concept and the upcoming CO2 reduction module. The application of this technology with large bore engines would represent the first such application in the world, Sima noted, as far as he knew, and represented an attractive value proposition for the industry.
Sima noted that FuelSave relies on external collaboration with leading nanotechnology scientists for the nanotechnology for the CO2 reduction technology, for which FuelSave has an exclusive licence in the maritime market. He expects to reveal further details about the technology by May 2023.
negative solution for green methanol, wheras as before it was merely circular. In addition, the catalysed syngases could be reinjected to further reduce primary fuel consumption, which would be a step towards even greater primary fuel savings and CO2 reduction
Marc FuelSa told Th that th has su compl a c M an EGR a 6M2 at FVT e Germa
Marc Sima, FuelSave’s ceo, told The Motorship that the company has successfully completed trials for a combination of FS MARINE+ with an EGR add-on, on a 6M20 test engine at FVTR Gmbh’s large engine test centre in Rostock in Germany
We are using nano base coatings and elements to improve the catalytic reaction for the reduction of CO2 in the exhaust gas stream of marine engines. We expect to be able to achieve a significant reduction in CO2 emissions, which has obvious advantages for our customers from a CII perspective and in their decarbonisation journey
marine engineering equipment •Bilge water monitors & filtration •Seals and bearings •Dry dock services •Underwater repairs •Additives to prevent leakage
•Marine engineering consultancy
•Project management
•Service contracts
Maintaining the highest possible standards for our customers. Service, upgrades and retrofits.
● Governors / Actuators
● Support for all Viking based products and our new simple to install Viking352G upgrade pack (below)
● Spare parts & Service
● OEM quality overhauls and service exchange units
● Propulsion Controls
● Generator Controls
● Power Management
● Turbocharger Condition Monitoring systems
Regulateurs Europa Limited Port Lane, Colchester. CO1 2NX UK Phone +44 (0)1206 799556
Fax +44 (0)1206 792685Email sales@regulateurseuropa.comWeb www.regulateurseuropa.com
Is your damper providing engine protection?
Torsional Vibration Dampers
Maintenance and Repair of Crankshaft Torsional Viscous Vibration Dampers
Tel: +44 (0)1422 395106
Fax: +44 (0)1422 354432 davidwhitaker@metaldyne.com www.metaldyne.co.uk
Formerly Simpson Ind - Holset Dampers
LUBRICANTS
Explore our range of innovative, high performance and Environmentally Acceptable Lubricants,
The international magazine for senior marine engineers
EDITORIAL & CONTENT
Editor: Nick Edstrom editor@mercatormedia.com
Correspondents
Please contact our correspondents at editor@motorship.com
Bill Thomson, David Tinsley, Wendy Laursen
SALES & MARKETING
Brand manager: Sue Stevens sstevens@mercatormedia.com Tel: +44 1329 825335
Even as far back as April 1973 the container shipping industry was looking towards larger and more powerful vessels. However, back then ‘larger’ was equivalent to 3000 TEU, around one-eighth of the capacity of today’s largest.
In today’s fuel-saving environment, the need for such a vessel to travel at 35 knots seems strange. But that was the vision in Japan in 1973. Today’s leviathans make do with a mere 80,000 bhp but then, the power requirement was set at around 240,000 bhp. That such power should be provided by medium-speed four-stroke diesels makes it sound even more incredible. The power unit of choice was to be Mitsui’s 60X engine, rated at 1500 bhp/cylinder at 370 rpm. Around 160 cylinders would thus be needed, and Mitsui planned for these to be arranged in a quadruple-screw configuration, with three engines per propeller. The logic behind this seemingly strange choice would seem to be that a fuel consumption of 980t/day was envisaged. Compared with steam turbines of similar power needing 1200t/day, it sort of makes sense.
Container ships had, by 1973, established themselves in the industry and we were gearing up for another expansion of ship types, thanks to the burgeoning offshore oil and gas fields, which demanded a new type of service and supply vessel. The initial fishing boat conversions were being supplanted by purpose-built ships for platform supply and anchor handling/towing duties. Typical was a recent North Sea contract for six 60m long 1050 dwt vessels of a type which would later become known as AHTS ships. Four were to be built by Appledore, and two by Richards. They would be
equipped with two Allen diesels of 2800 bhp each, driving FP propellers in Kort nozzles, giving a 14.5 knot service speed and bollard pull of 78t. The development of specialised ships continued, with the introduction of the largest-yet all-refrigerated ships, the Queen class bult by Aalborg for Israeli group Maritime Fruit Carriers. With 576,700ft3 (16,330m3) capacity spread across five refrigerated holds, the four Queen ships would join the company’s then 35-strong fleet in worldwide shipping mainly of citrus fruit and bananas. The first Queen ship, Chrysantema, had glass-wool insulated cargo spaces, helping to keep temperatures down to -31 degree C. These were cooled by a Stal ductless system, with four Stal screw-type compressors using Freon 22 refrigerant. The cooling system was designed with a high level of automation, a philosophy which was extended to the ship’s machinery, with a 23,200 bhp B&W 9K84EF main engine and four B&W 8T23HH-powered gensets with total output of 3340 kVA. A final novelty was that Chrysantema, forming the main ship description in the April 1973 issue, merited several colour pictures, the first departure from monochrome printing in our editorial pages.
A special feature was devoted to what -even after coverage of container and offshore vessels - was described as “today’s growth transport industry” – namely the European roll-on/roll-off (ro-ro) sector. Despite the growth in containerisation, the short sea industry was benefiting from the trend to send goods in road trailers, avoiding the need for offloading and transhipment. Avoidance of the problem of returning empty containers was a contributing factor, while Britain and Ireland having recently joined the European Economic Community was giving another extra impetus.
Typical of this breed of vessels was the ‘Free Enterprise’ fleet, operated on the English Channel by Townsend Thoresen. The latest, built by Dutch yard IHC, Free Enterprise VII, powered by three Stork-Werkspoor 4550 bhp engines, was to go on to be ‘jumboised’ and operated under many owners until sunk in 2015.
Production David Blake, Paul Dunnington production@mercatormedia.com
EXECUTIVE
Chief Executive: Andrew Webster awebster@mercatormedia.com
TMS magazine is published monthly by Mercator Media Limited Spinnaker House, Waterside Gardens, Fareham, Hampshire PO16 8SD, UK
t +44 1329 825335
f +44 1329 550192 info@mercatormedia.com www.mercatormedia.com
Subscriptions
Subscriptions@mercatormedia.com Register and subscribe at www.motorship.com
1 year’s digital subscription with online access £222.00
For Memberships and Corporate/multi-user subscriptions: corporatesubs@mercatormedia.com