FOOD & DRINK PROCESSING & PACKAGING
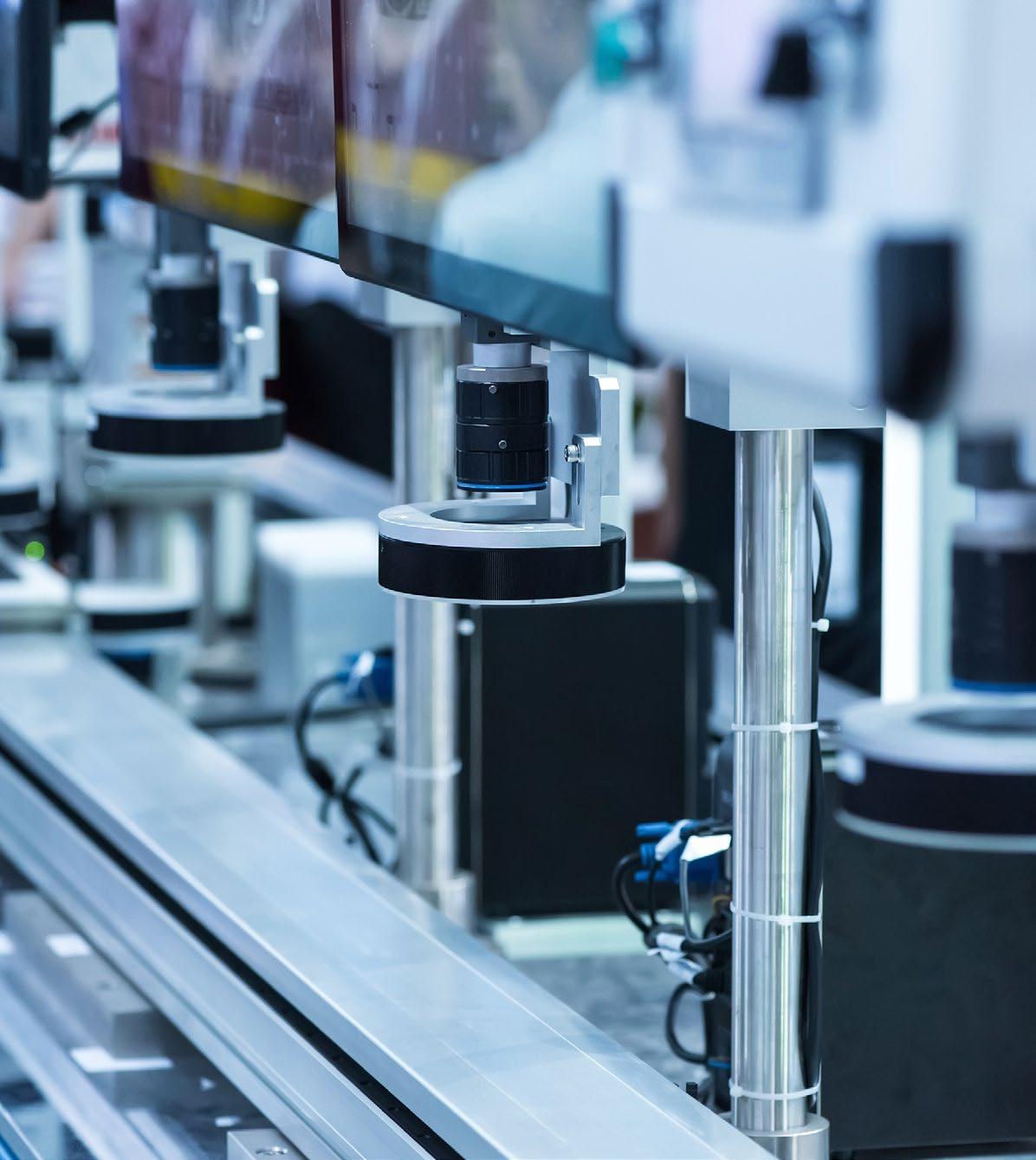
with
with
Product Safety
Process Efficiency
Improved Product Yields
Rapid Fault Finding
Full HACCP Certification
Thru-process temperature monitoring solutions for all your cook applications
PhoenixTM Technology
• Accurate IP67 data logger (Type K or T)
• 10 Measurement Points for full oven mapping
• Thermal barrier options to suit cook regime
• Comprehensive thermocouple range
• Standard miniature thermocouple plugs
• Calibrated thermocouple options
• Food trays and thermocouple jig options
• Full lethality (Fo/Pu) and reporting
• Real Time RF Telemetry options
• Local efficient calibration and service support
Phoenix Temperature Measurement
The 14 time-controlled nozzles of the ZAP-Module from Syntegon apply the sealing medium to no more than three areas: the bottom of the packaging, the top, and the vertical seam. The rest of the material remains untreated so that the packaging still allows moisture exchange and contributes to the flour’s extended shelf life.
Consumers regularly stumble across this situation in the supermarket: when they reach for the flour packaging, fine flour dust finds its way into the shopping bag, the car trunk, and ultimately the kitchen. The only remedy is dusttight packaging. The Roland Mills United milling group has therefore opted for a new line solution from Syntegon that packs flour in highquality, sustainable and, above all, dust-tight packaging.
According to Matthias Karrenbauer, Head of Production and Technology at Roland Mills United, dust-tight flour packaging offers advantages that are worth the investment.
“This packaging offers particularly high quality and is therefore ideally suited for the premium retail sector – a promising market segment for
us.” Roland Mills United is one of the leading grain mills in Europe. Spread across three locations in Germany, the family-owned company processes more than one million tons of flour per year.
When the company decided to replace one of their packaging machines after 40 years of use, the requirements for the new filling machine were high. “Our goal was to find a future-proof line solution that combines sustainable primary and secondary packaging. However, this was no easy task, as the line had to fit a limited space. Out of all competitors, Syntegon provided us with the best technical solution and made us feel comfortable. We opted for their Package Maker PME
4081 BS and Elematic 3001 WAH case packer to package our dusttight flour packs into high-quality cardboard trays.”
Sustainable packaging thanks to innovative sealing technology
With conventional flour packaging, paper is glued, formed into a bag, and then simply folded for closure after filling. Dust-tight flour packaging, which requires significantly less sealing medium, eliminates this challenge. In the PME 4081 BS package maker from Syntegon, a roll feeds uncoated paper into a specialized module. Within the so-called ZAP module, 14 time-controlled nozzles apply the sealing medium to the bottom of the packaging, the top, and the vertical seam. The rest of the material remains untreated so that
With the exception of short interruptions for cleaning and paper changes, the machine runs continuously, achieving an effectiveness of 97 percent.
the packaging still allows moisture exchange and contributes to the flour’s extended shelf life. As the sealing medium is only applied selectively, the packaging material has a fiber content of over 95 percent and can conveniently be recycled as mono-material through the paper waste stream. The PME 4081 BS packages around 80 tons of flour per day in two shifts.
Syntegon’s solution folds the bags using a mandrel wheel before two auger fillers with integrated dust suction stations fill each bag individually in two steps to reduce dusting. Afterwards, the filled flour bags are shaken on the closing chain by means of vibration for about ten seconds to make sure the flour is fully compressed. Finally, thermal sealing jaws seal the bags to create robust, dust-tight, and compact flour packages.
“Our solution reduces downtimes to a minimum,” says Uwe Pfander, Senior Sales Manager at Syntegon.
“With the exception of short interruptions for cleaning and paper changes, the machine runs continuously, achieving an effectiveness of 97 percent. Comparable solutions from our competitors often only reach a maximum of 75 percent.”
Besides the machine’s high availability, the experts at Roland Mills United are also impressed with its packaging flexibility.
“Thanks to extensive test runs, we knew that we could process paper from various suppliers on the machine. This gives us an important competitive advantage,” explains Karrenbauer. For Roland
Mills, it is important not to depend on a single supplier, but to be able to use different packaging materials in the future – one of the benefits delivered by the Package Maker from Syntegon.
The quality commitment of Roland Mills United doesn’t stop at primary packaging. The flour’s secondary packaging needs to live up to high expectations as well. “We want to offer our dust-tight flour bags in premium retail, which is why we invested in a Syntegon case packer that packages them in a sustainable display carton,” Karrenbauer adds. The Elematic 3001 WAH from Syntegon packs 100 flour packs per minute – and is particularly sustainable thanks to minimal use of adhesives. When folding the display cartons, the adhesive is only applied selectively so that the secondary packaging can easily be disposed of in the paper waste. For Roland Mills, this makes the PME 4081 BS package maker and the Elematic 3001 WAH the ideal combination for sustainable as well as dust-tight flour packaging.
www.syntegon.com
Working together in a partnership of equals: Matthias Karrenbauer, Head of Production and Technology at Roland Mills United (left) and Uwe Pfander, Senior Sales Manager at Syntegon (right).We are LAUDA – the world leader in precise temperatures. Our constant temperature equipment and systems are at the heart of important application, contributing to a better future. As a fullservice provider, we guarantee the optimum temperature in research, production, and quality control. We are the trusted partner to electromobility, hydrogen, chemical, pharmaceutical/biotech, semiconductor and medical industries. For almost 70 years we have been inspiring our customers with our competent consulting and innovative solutions.
The right solution for every purpose
We offer a large selection of highquality constant temperature equipment for a wide variety of applications: process circulators, circulation chillers, water baths, custom tailored temperature control systems and industrial systems. You will also find a comprehensive range of reliable aids for your daily work in the laboratory. In addition to water baths, there are also shakers, deepfreeze appliances and stills.
Modular Engineering: Customised temperature control systems according to your specifications
Our extensive portfolio might not always give your exactly what you need for your application. At LAUDA Technology, we can put together custom tailored temperature control solutions such as process cooling units, heat transfer units or secondary circuit units according to your requirements. We produce customised temperature control solutions that we adapt to your needs.
Temperature control systems with state-of-the-art network connection and intuitive operation
At LAUDA Technology, we are constantly driving forward the digitalisation of temperature
If
you are looking for high-quality temperature control solutions for your company, our employees are on hand to provide you with expert advice.
control technology. For example, our Ultracool circulation chillers and the Integral process circulators can already be flexibly networked via integrated web servers. This allows intuitive operation and monitoring via PC or mobile devices – irrespective of location. In addition, LAUDA.LIVE offers new possibilities for device monitoring and parameter evaluation via multilevel access controls from any PC with an internet connection.
If you are looking for high-quality temperature control solutions for your company, our employees are on hand to provide you with expert advice. To prevent problems and costly repairs, our experts will also carry out regular maintenance on your equipment if required.
Service support, every step of the way
Our LAUDA Technology service will support you with; commissioning, system testing, retrofitting/ renovation, maintenance contracts, training, disposal, spare parts logistics and warranty. We support you with our experience as the world market leader for temperature control equipment and systems.
Come and meet us at CHEMUK –Stand L22, Hall1, NEC Birmingham 15th & 16th May.
Or Get in touch today: info@lauda-technology.co.uk www.lauda.de.en +44 (0)1780 243 118
The markets are changing, and thus so are the requirements of the process manufacturing industry. Whether it is fluctuating demand, more customised products or smaller batches, manufacturers need to respond more quickly and flexibly. Here, Bradley McEwan, business development manager at automation and control technology specialist Beckhoff UK, discusses how software and modular hardware enables easy integration of technologies, like robotics and vision, that were once considered ‘standalone’.
Flexible manufacturing is a modern approach that emphasises adaptability, responsiveness and customisation in the production process. Unlike traditional mass production, where the focus is on producing large quantities
of identical products, flexible manufacturing systems can efficiently handle small to medium-sized production runs and easily adapt to changes in product design or customer requirements.
Enabling manufacturers to quickly switch between different products without incurring significant downtime or retooling costs, the move towards flexible manufacturing happened before the destruction of the supply chain, pandemic and global wars. In fact, a major driving force behind the move was because of short run times and manufacturers wanting to test the market with products, owing to end users promoting seasonal events, such as Easter and Christmas.
Typical commercial products, such as shampoo, used to have a life cycle of between three and five years. Therefore, it was financially viable for manufacturers to buy machinery solely for a single product that has a long-life cycle.
Now, we are now seeing a significant decrease in the life cycle of commercial products, which is paving the way for flexible manufacturing. Manufacturers are no longer tied to a product line for the same amount of time, instead they require a production line that consists of at least two or three products.
The advent of Industry 4.0 kickstarted the need for machines
Flexible manufacturing is a modern approach that emphasises adaptability, responsiveness and customisation in the production process.
to become smart integrating into the ‘cloud’ for data analysis to enable seamless reconfiguration. As a result, this changed how manufacturing companies evaluated the capital investment of machines, as the emphasis switched from being on the life cycle of the product, to the life cycle of a machine.
After all, it is not financially viable to buy new machinery every 18 months. Not only it is a significant upfront cost, but it also takes around two years to get the machine sealed and delivered ready for use.
Traditionally, a production line would have a continuous flow of
product, often referred to as a continuous production process or continuous flow manufacturing. This approach is characterised by the steady and uninterrupted movement of products along the production line, with each station performing a specific operation in a sequential manner.
Yet, the introduction of flexible track systems is enabling production lines to have a variable flow of product. Flexible track systems consist of modular units that can be easily connected or rearranged to form different production lines or workstations, ensuring quick reconfiguration to accommodate various product types or changes in production requirements.
These systems, such as Beckhoff’s TwinCAT software platform, combine the advantages of flexible manufacturing with the efficiency of continuous production, achieving greater adaptability and responsiveness to changing demands while maintaining high throughput and efficiency.
Laying down the foundation for modular production, the TwinCAT software-based approach integrates Programmable Logic Controller (PLC), motion control, robotics, vision, Human-Machine Interface (HMI), cloud connectivity and other functionalities into a single software environment. And, as Industrial PCs (IPCs) increase in power, the TwinCAT platform allows for further integration.
By reducing the number of components, such software is designed to allow original equipment manufacturers (OEMs) to enable modular production and start their flexible manufacturing process.
In fact, we believe that PC based automation is a move away from the traditional fixed PLCs, enabling the easy integration of robotics, vision and machine learning applications that were once unimaginable.
For more information about Beckhoff’s TwinCAT and other modular automation software platforms, visit www.beckhoff.com.
Electric drives play an essential role in all processing phases of the packaging industry. NORD therefore offers powerful drives in various performance levels for primary, secondary and end-ofline applications - including both synchronous and asynchronous motors (IE3 or IE5+) with parallel shaft gear units, helical gear units or bevel gear units and centralized or decentralized frequency inverters.
In the primary packaging sector, food, pharmaceuticals and other hygiene-sensitive products are often packaged. Drive systems in these applications must therefore be easy to clean and resistant to chemical detergent and possible contamination. NORD offers FDA-certified drive units up to protection class IP69K as well as modular and flexible worm gear units from the UNIVERSAL SI or SMI series with smooth surfaces. The patented DuoDrive from NORD in a hygiene-friendly design is also predestined for applications in the primary sector. In this geared motor unit, an IE5+ motor is integrated into a spur gear unit. This not only achieves a high level of system efficiency, but also ensures fewer wearing parts and reduced maintenance requirements for further positive cost effects.
In the secondary packaging sector, electric drives have become much more popular than pneumatic drives in recent years. NORD offers efficient drive solutions for the machines used in this area, which are used in conveyor belt and labeling applications, among others. The NORD IE5+ synchronous motor impresses with maximum energy efficiency and exceeds the previously defined efficiency classes. As the permanent magnet synchronous motor achieves its constant torque over a wide speed range, it enables a reduction in the number of drive variants in an overall system. This in turn reduces
NORD’s drive solutions also promise high energy efficiency and low total cost of ownership (TCO) for the end-of-line sector.
management costs and therefore also the TCO.
NORD’s drive solutions also promise high energy efficiency and low total cost of ownership (TCO) for the end-of-line sector. In the packaging of food and beverages, for example, cost advantages of up to 50 % can be realized with NORD asynchronous motors. Centrally controlled servomotors
are usually used here. In contrast, controlled asynchronous motors from NORD represent an efficient and economical alternative. When used with decentralized frequency inverters such as the NORDAC ON, components such as control cabinets are also eliminated, and the costs for cabling and installation are significantly reduced.
The modular product system, the global services with customerspecific support and the wide range of standardized components and customer-specific solutions from NORD are key success factors for economical and efficient drive solutions in packaging technology - which can make a significant contribution to reducing a company’s total cost of ownership (TCO) and energy consumption.
www.nord.com
Decentrally
Decentrally
Low
Low
Compact
Compact
Assembly-
Assembly-
Amidst the rapidly evolving landscape of the box forming machinery sector, the demand for more efficient, sustainable, and robust machinery is escalating. Delta’s innovative automation solutions have played a pivotal role in enhancing the production capabilities of Tecnobox, a box forming machinery company in Spain. This transformation has not only fortified Tecnobox’s position in a competitive market, but it has also set new standards in the industry for technological advancement and environmental responsibility.
Nestled in Levante, a bountiful food-producing region, Tecnobox is renowned for its dedication to quality, innovation, and sustainability. With around 40 employees, this medium-sized company has carved a niche in manufacturing robust, lowmaintenance cardboard box assembly machinery.
Its products are distinguished by the use of standard components to speed up production and a commitment to replacing metal and plastic containers with biodegradable alternatives.
However, the post-pandemic landscape posed unprecedented challenges for the company. A critical component crisis threatened the continuity of Tecnobox’s production, putting its market leadership at risk.
This crisis coincided with a period when Delta was seeking to establish a stronger presence in the market.
Tecnobox’s need was clear.
It required a system that mirrored its current architecture’s reliability, while offering enhanced efficiency. The solution had to be complete and incorporate EtherCAT communication while aligning with its ethos of innovation and sustainability. With its AX3 PLC, MS300, ASDA-B3, DOP100, and LITE Power Supply. Delta emerged as the candidate most suited to meeting Tecnobox’s requirements, not just for the completeness of its offering, but also its ability to deliver it promptly.
Operating two distinct machines within the system, Tecnobox required specialized control architectures tailored to each machine’s unique tasks and performance metrics. The first machine, TB-Pack, utilizes a servo system with the MS300 drive, achieving a production speed of 3000 pieces per hour. Along with the servo system and MS300 drive, it is also equipped with an HMI, PLC, and I/O, making this machine optimally forms boxes of specific types.
The second machine, TBQ-Pack, shares a similar configuration with TB-Pack but substitutes the MS300 with another servo system, allowing it to operate at a faster pace of up to 10000 pieces per hour. These variations in control architecture stem from the distinct production requirements and speed capabilities of each machine.
The journey began with Delta’s proactive approach. Collaborating closely with its regional partner, INDA LEVANTE, Delta offered its comprehensive automation
solutions to Tecnobox. This collaboration was not just about providing hardware; it involved an intricate process of understanding Tecnobox’s needs and tailoring its hardware and software solutions according to Tecnobox’s unique requirements.
Delta’s Project Managers and Field Application Engineers spearheaded the initiative, conducting extensive technical training sessions for Tecnobox
and INDA LEVANTE. Within five months, a prototype machine was manufactured which integrated Delta’s advanced automation systems. As with all implementations, in the early stages there were challenges to overcome, but they served to prove Delta’s confidence in problemsolving and commitment to complete customer satisfaction.
Following the implementation, the results were remarkable. Tecnobox not only overcame the production hurdles, but it did so with a solution that saved approximately 25% in electronic materials costs. Furthermore, the stability and efficiency of Delta’s solutions were not just in line with Tecnobox’s expectations, but also reinforced its market position during a critical period.
Tecnobox not only overcame the production hurdles, but it did so with a solution that saved approximately 25% in electronic materials costs.
This collaboration between Delta, Tecnobox, and INDA LEVANTE transcends a mere business transaction; it exemplifies a synergy where challenges are converted into opportunities. The success story is best encapsulated in the words of Edwin Gomez Rodriguez, Field Application Engineer, Industrial Automation Business Group at Delta EMEA: “This project with Tecnobox not only demonstrates our capabilities in delivering efficient, cost-
effective automation solutions but also reinforces Delta’s commitment to customer satisfaction and innovation. We’re proud to have played a key role in supporting Tecnobox through a challenging period, and this collaboration signifies a major step in our journey towards becoming a recognised name in the automation industry.”
Delta’s unwavering commitment to innovative problem-solving and customer satisfaction, coupled with Tecnobox’s strategic market insights and operational excellence, have created a formidable partnership that stands out as a beacon in the manufacturing and automation industry. The resilience and innovation serve as a compelling model for others navigating the complex landscapes of modern industry.
www.delta-emea.com
Here at Seaways Services we have recently celebrated both 50 years in business and the winning of Lancashire Business View’s Red Rose Family Business Award.
We are a multigenerational family business which has been operational since 1973. The business began supplying hay, straw and agricultural feeds from the docks to feed merchants and farmers along with the haulage of clay pipes. This led to general haulage and delivering milk bottles from there we quickly recognised that not only could we deliver glass bottles but we could also print them. We now print bespoke glassware for all kinds of companies from smaller quantities for companies such as Jeremy Clarkson’s Diddly Squat farm shop to larger companies such as Elite Dairy Vending, Otterbeck Distillery and Riverside Spirits. Since we began we have supplied millions of tonnes of returnable glass, this means that all of our glass packaging is truly reusable or recyclable.
The haulage side of the business has been developed so that we are self reliant, in the last ten years we have taken this a step further by having our own on site workshop which services all of the vehicles we run. We are therefore able to deliver direct to our own customers and also include backloads, goods
Looking to the future, we are hoping to continue to meet our green goals, exceed our charitable objectives and remain true to our business values.
storage along with bulk milk haulage.
Looking to the future, we are hoping to continue to meet our green goals, exceed our charitable objectives and remain true to our business values. We have been green long before it was fashionable and we hope to continue this legacy. This year we are already committed to supporting Pendleside Hospice, Lymes disease, Derian House, AMMF
and the Scottish Milk Championship at the Royal Highland Show.
We had a great year of reflection last year; our 50th year in business evidenced our longevity. We have adapted to survive not only the usual business and family life challenges but also 6 recessions, the joining of the EEC, foot and mouth hitting our dairy customers, a crisis forcing the UK to borrow money from the IMF, record levels of unemployment, Brexit and Covid but we are still not only here but thriving with a smile on our faces!
For more information please visit our website: www.seaways-services.com
In the food and beverage industry, efficient processing and packaging are critical for maintaining product quality, freshness, and safety. Scroll Labs’ innovative vacuum solutions play a central role in revolutionizing these processes, offering precise control, consistent results, and versatile applications across various segments. With unique floating scroll technology, Scroll Labs’ SVF series oil-free scroll vacuum pumps and vacuum pumping systems have the following outstanding characteristics.
• No tip seals or shaft seals
• No maintenance
• Lower power consumption (more efficient)
• Can handle moisture and water vapor without ballast valves.
• Can start with load
• Compact and quiet
Let’s explore how our vacuum technology enhances key processes in the industry:
1. Freeze Drying: Freeze drying preserves food and drink products by removing moisture in a lowpressure environment while maintaining taste, texture, and nutritional content. Scroll Labs’ advanced floating scroll technology streamlines this process, enabling efficient moisture extraction at low temperatures. The SVF series oil-free scroll vacuum pumps are capable of handling water vapor without ballast valves which results in superior product quality and extended shelf life.
2. Freshness Preservation of Flowers, Fruits, and Vegetables: Keeping produce fresh is essential for ensuring high-quality products for consumers. Our vacuum technology removes air and oxygen
SVFA-300 Pumping Systems
from storage environments, preserving the freshness of flowers, fruits, and vegetables. This method extends shelf life and maintains the natural flavors, colors, and nutritional value of the produce. Our customer replaces oil-lubricated rotary vane pumps with SVF-100 (DSVF6) pumps due to higher efficiency, compact size, and maintenance-free.
3. Cannabis Extraction: In cannabis processing, precise extraction techniques are vital for producing high-quality oils and concentrates. By using SVF oil-free scroll
vacuum pumps, our customers’ productivity has increased by 30%. Besides, utilizing SVF pumps enables our customers to remove chillers and simplify filtering in the system.
4. Wine Preservation: Proper wine preservation is crucial for maintaining the integrity and taste of the wine. No oil or contaminates such as debris from tip seals is allowed in this process. Our vacuum technology helps remove oxygen from wine containers, minimizing oxidation and preserving the wine’s flavor,
aroma, and quality over time. Besides its great performance, the SVF-5 pump is compact enough to be installed in the cabinet by our customer.
5. Vacuum Packaging for Medical Purposes: Vacuum packaging ensures the sterility and safety of medical supplies and pharmaceuticals. SVF series pumps create airtight seals, protecting sensitive products from contaminants and extending their shelf life.
6. Vacuum Packaging for Food Storage: In food storage, vacuum packaging plays a key role in prolonging shelf life and maintaining quality. SVF series pumps remove air from packaging, reducing the risk of spoilage and preserving the taste and texture of a wide range of foods.
7. Vacuum Oven Processing of Candy: Candy processing requires precise control of temperature and moisture levels. SVF series pumps can be paired with vacuum ovens to provide the controlled environment needed for candy production, ensuring consistent quality and optimal results.
In addition to our existing scroll vacuum pump, we are proud to introduce our latest innovation: a cutting-edge pumping system designed to revolutionize the food and beverages packaging and processing industry further. This innovative system allows for parallel connection of pumps, enabling seamless switching between multiple pumps to ensure continuous operation. This pumping system ensures that no downtime is required for continuous operation, boosting the efficiency of the client’s operation. With this new product, we reaffirm our commitment to driving efficiency, sustainability,
and reliability in client’s operations, empowering businesses to thrive in an ever-evolving landscape.
In conclusion, Scroll Labs’ SVF series vacuum solutions are instrumental in optimizing food and beverage processing and packaging. By providing precise control and consistent results across a variety of applications, our technology empowers businesses to deliver high-quality products while maximizing efficiency and sustainability. Join us as we transform the industry with advanced vacuum solutions tailored to your needs. www.scrolllabs.com
In the dynamic realm of food production, natural food colours play a pivotal role in enhancing product appeal and preserve their inherent authenticity. Unlike artificial dyes, natural hues are sourced from a rich array of fruits, vegetables, herbs, spices, and minerals, offering a rich palette of colours. From the radiant yellows of turmeric and saffron to the deep reds of beets and annatto seeds.
Plant Lipids UK, a renowned leader in the natural food colours industry, harnesses the inherent power of these sources to craft colours that not only captivate the eye but also tantalize the taste buds.
Introducing Spectra®- Natural Colour Solutions, which harness the vibrancy of nature to naturally colour your products! Our extensive range spans various hues, including Yellow, Orange, Red, Pink, Purple, Brown, Blue, Black, and White. Developed through meticulous research and supported by stateof-the-art technologies, our natural colour solutions are visually striking, safe, pure, and sustainable.
In a world where colour embodies a conscious choice for a brighter future, our natural colours enhance a wide array of product categories.
Plant Lipids UK pioneers innovative alternatives across industries. From our Titanium Dioxide replacer offering a versatile solution applicable beyond conventional uses. To non-caramel brown, introducing new guiltfree indulgence options suitable for a wide range of products. Our commitment to innovation extends across traditional, non-vegan, and plant-based meat alternatives, aligning with dynamic food trends. Explore our tailored colour concepts for various applications, including dairy alternatives, catering to lactose-intolerant individuals, pushing forward the evolution of food.
Plant Lipids UK’s expertise in natural food colours is further exemplified by its advanced extraction technology. Operating from a spacious facility, our Natural Food Colours UK division is equipped with ample
storage and production capacity, ensuring efficiency and reliability at every step. With dedicated personnel offices and cuttingedge laboratories for new product development and quality control, we uphold our unwavering commitment to innovation and quality assurance.
In a world where colour embodies a conscious choice for a brighter future, our natural colours enhance a wide array of product categories. From dairy to bakery, beverages to snacks, and meat to pet foods and nutraceuticals. Our solutions enrich consumer experiences and contribute to a vibrant tomorrow.
Beyond this Plant Lipids UK offers a comprehensive assortment of products that enhance applications with rich aromas and distinctive tastes. Our portfolio includes essential oils derived from botanicals, suitable for various uses. We also provide oleoresins, encapsulating full flavour and colour characteristics, ensuring consistency across applications. Our flavour-plated salts offer a precise burst of taste, and our extensive range of spices and herbs, selected for their unique properties, completes our offerings.
uk.plantlipids.com
Plant Lipids is one of the largest producers of spice oils and extracts in the world.
Based in India, Plant Lipids manufactures and exports essential oils, spice oleoresins, natural food colours, whole and ground sterilized spices to over 85 countries worldwide.
Global food processing automation platform acquires US-based batter, breading and frying equipment manufacturer
Fortifi Food Processing Solutions (“Fortifi”), a global leader in food processing equipment and automation solutions, announced today that it has acquired Nothum Food Processing Systems (“Nothum”). Nothum is a leading designer and manufacturer of batter, tempura, breading and frying lines primarily for protein processing.
“Nothum provides innovative, high-quality equipment backed by strong customer service,” said Massimo Bizzi, Chief Executive Officer of Fortifi. “Thanks to Nothum’s technology leadership, this acquisition expands Fortifi’s advanced processing offerings and allows us to continue serving our customers with excellence.”
Founded in 1971, Nothum is based in Springfield, Mo., and serves the poultry, seafood, vegetables and alternative protein markets. Nothum joins Bettcher Industries, Frontmatec, MHM Automation, REICH Thermoprozesstechnik GmbH
Nothum provides innovative, high-quality equipment backed by strong customer service.
and other leading brands within Fortifi’s portfolio of food processing and automation solutions.
“The Nothum family and team are extremely excited to join Fortifi,” said Robert Nothum, President of Nothum Food Processing Systems. “We are eager to expand our reach and continue to create outstanding food processing equipment as part of the Fortifi family.”
All Nothum employees will join Fortifi’s broad-based ownership program, which provides employees the opportunity to participate in the benefits of equity ownership.
Baird served as the exclusive financial advisor to Fortifi in connection with its acquisition of Nothum. William Blair acted as the exclusive financial advisor to Nothum.
www.FortifiFoodSolutions.com.
Hinojosa Packaging Group continues to expand its international presence with the acquisition of the Italian company MS Packaging. With the addition of the two plants located in the towns of Salerno and Arzano, Hinojosa has entered the Italian market, one of the largest in the paper and cardboard sector in Europe.
MS Packaging is an Italian family enterprise specialised in the manufacture and sale of paper and corrugated cardboard packaging. Comprising a packaging factory and a paper mill and boasting a strong presence in the food and beverage market, the company had a turnover of 60 million euros in 2023. Its entire workforce of about 200 employees will retain their jobs under Hinojosa.
In its desire to offer customers the widest range of products, Hinojosa has integrated MS Packaging as a company that shares the same philosophy, based on innovation, the most advanced technology, sustainability, and proximity to the customer. With the incorporation of MS Packaging, Hinojosa now has a workforce of 2900 employees and 24 production plants located in Spain, Portugal, France and Italy.
Hinojosa now has a workforce of 2900 employees and 24 production plants located in Spain, Portugal, France and Italy.
This operation coincides with the start of Hinojosa’s new 2024-2026 Strategic Plan. After consolidating its growth over the last three years, this will mark a new stage in which the company will be focusing on internationalisation, to continue expanding its supply of sustainable packaging, anticipating the trends of the sector, and thus the demands of its customers.
Hinojosa had a turnover of 739 million euros in 2023, whilst reducing carbon emissions and adding value through innovation
Hinojosa closed last year with a turnover of 739 million euros, 10% lower than the previous year, with the drop in raw material prices being the main factor. Hinojosa was able to transfer this cost reduction on to its customers, in contrast to the previous period when soaring inflation had hiked up raw material and energy prices.
The Group’s international expansion was consolidated in 2023 with the acquisition of 49% of the French company ASV Packaging, which enabled Hinojosa to strengthen its presence in France and improve the service and product it was offering to European customers. The presence of plants in France, along with those in Portugal and Spain, has led to a growth that has also resulted in a 10% increase in the workforce across its network of work centres.
A firm commitment to decarbonisation is another of the company’s main objectives, as part of its ESG commitments to the environment. Last year ended with very positive results in this area: a 22% reduction of emissions and carbon footprint compared to the previous year. And of equal importance for Hinojosa, the company achieved a waste valorisation of 95.2%.
As for the improvements and expansion of its range of products, in 2023 Hinojosa upheld its firm commitment to innovation, the key to identifying the future of the sector and anticipating social changes and customer demands, accompanying them in their growth. This is the case with eating outside the home, a strong trend that reached record numbers in 2023. In this context, last year Hinojosa launched Foodservice, a pioneering range of 100% recyclable and environmentally neutral primary packaging at the end of its life-cycle, intended for beverages and prepared foods. A new product that was developed to meet the current demand of a growing market that seeks to achieve better waste management, helping to slow the progress of climate change.
www.hinojosagroup.com/en
With talk of AI taking over and humans being made redundant what does the future hold for us?
The food and beverage industry is a complex dance of ingredients, processes, and customer satisfaction. Disruptions in this flow can be costly, leading to waste, unhappy customers, and lost profits. But a new sous chef is emerging in the kitchen: Artificial Intelligence (AI).
AI is transforming the food and beverage industry by streamlining operations and creating a smoother flow from farm to fork (or bottle).
Here’s how:
1. Predicting the Perfect Pour (and Inventory):
Imagine a world where you never run out of your favourite drink, and restaurants can optimize their stock to avoid waste. AI-powered demand forecasting analyses past sales data, weather patterns, and even social media trends to predict what and how much customers will buy. This ensures a steady flow of ingredients and finished products, reducing spoilage and stockouts.
2. From Farm to Fork, with Full Transparency:
Food safety is paramount. AI can track ingredients throughout the supply chain, pinpointing potential contamination sources in real-time. This not
AI-powered demand forecasting analyses past sales data, weather patterns, and even social media trends to predict what and how much customers will buy.
only safeguards consumers but also helps with swift recalls if necessary, minimizing disruption.
3. The Art of Personalized Plates:
AI can analyse customer data to create personalized recommendations. Restaurants can use AI-powered chatbots to suggest dishes based on dietary restrictions or past orders. Grocery stores can tailor their offerings to local preferences. This creates a frictionless customer experience, keeping them coming back for more.
4. Maintaining the Flow: The Power of AI-powered Maintenance:
Unexpected equipment breakdowns can grind operations to a halt. AI can analyze sensor data from machinery to predict maintenance needs. This proactive approach prevents downtime and ensures a smooth flow of production.
5. A Recipe for Innovation:
AI can analyse vast amounts of data on flavour profiles, ingredients, and consumer trends. This
paves the way for the creation of innovative new food and beverage products that cater to specific needs and preferences.
As AI continues to evolve, the food and beverage industry can expect even greater levels of efficiency and innovation. From automated harvesting robots to AI-powered recipe development, the future promises a seamless flow of food and drink, from creation to consumption.
However, it’s important to remember that AI is a tool, it will never replace human expertise. For the best results will be from a collaboration between human creativity and the power of AI, the batch control systems available from iCenta Controls, provide the latter. With this approach, the food and beverage industry can ensure a future filled with delicious possibilities and a smooth flow from farm to table.
www.icenta.co.uk
TAILORED SOLUTIONS AND SOLID SUPPORT FOR VARIOUS INDUSTRIES WORLDWIDE
Whatever industry you are in, from plastics to pharmaceuticals and from dairy to aquaculture, you wouldn’t want your production compromised by faltering input of raw materials.
Let DMN-WESTINGHOUSE add reliability to your dry bulk handling processes. Since 1950, we have excelled in designing and manufacturing high-end rotary valves and diverter valves with a stark focus on durability, cleanability and compliance.
Discover your future-proof solution at dmnwestinghouse.com
Product quality, product safety. The guiding mantra in dairy production. That’s why the world’s leading dairy producers rely on the products and solutions developed by DMN-WESTINGHOUSE. Our rotary valves and diverter valves offer the highest level of precision engineering, preventing bridging and possible contamination during conveying processes. At the same time, they guarantee unparalleled cleanability, drastically increasing product safety while reducing downtime for maintenance and repairs.
Through years of experience and valuable partnerships, DMN-WESTINGHOUSE has gained a deep understanding of the global dairy industry and its challenges. We have earned the trust of an industry where hygiene, cleanability, and safety are paramount. In our R&D department, we leverage innovative technology, setting the dairy industry standard. In our factories, we control every step in the manufacturing of heavy-duty rotary valves and diverter valves.
Just like you, we strive for unparalleled quality and consistency. A commitment underscored by our compliance with current certifications, including USDA, EHEDG-ED Class II and ATEX. Whether it’s about infant formula, lactoferrin, (plant-based) milk powders, caseinates or probiotics, at DMNWESTINGHOUSE, we help you maintain the highest quality standards in dairy.
Many producers of dairy products, ranging from baby formula to
lactoferrin, rely on our renowned heavy-duty rotary valves. These valves come in two types and various sizes: the drop-through type (AL/AXL/AML) and the blowthrough type (BL/BXL/BXXL). They comfortably comply with the stringent hygiene standards the dairy industry needs to maintain. All product contact surfaces consist of food-grade material, polished to perfection. They are all radiused and polished to an astonishing 0,8 μm Ra (150 grit), and the rotor vanes have precisely chamfered edges preventing the build-up of conveyed dairy powders.
MZC-series:
Cleaning intervals will vary depending on which dry dairy substances are processed. To
Through years of experience and valuable partnerships, DMN-WESTINGHOUSE has gained a deep understanding of the global dairy industry and its challenges.
reduce cleaning time and resulting downtime, we developed the MZC rotary valves based on our AL— and BL-series. The MZC-I and MZCII are equipped with supporting rails so the rotor and end cover can be removed. The MZC-II opens on two sides for unprecedented easy access and superior cleanability.
These valves facilitate premium process handling, raising the bar in cleanability, hygiene, and safety. The rotor body clearances are set automatically when the rotary valve is closed after cleaning.
Adding innovative solutions can take your dairy production to the next level.
(RID 3.0) is our third generation, detecting unwanted contact between the rotor and body or end covers. This prevents major damage and provides insight into product contamination. RID 3.0 offers 50 times more accurate resistance measurement than its predecessors.
Shaft seal flow control boosts the reliability of our AL and BL heavyduty rotary valve series even more. Precise flow control prevents the build-up of powder residue on the shaft seals, minimising the risks of seal failure, contamination, leakage, damage and downtime.
· Rotary valves equipped with the Sanitary Air Seal (SAS) outboard bearing shaft seal minimise leak risks due to pressure changes inside the valve, thus maintaining the right airflow.
For maintaining hygiene and preventing contamination, cleaning-in-place (CIP) is indispensable. CIP is about cleaning the interior of pipelines, valves, tanks and other equipment without the need for disassembly. In the dairy industries it’s a
necessary, often automated method to maintain the highest levels of hygiene and prevent contamination.
Your perfect Niro replacement
Handling dry dairy solids is about maintaining the strictest standards and requirements 24/7. Are you currently operating Niro rotary valves needing replacement any time soon? Our NR347 rotary valves (NR = Niro replacement) match the outer dimensions of the Niro valves operating within your system, which means they are usually a perfect fit. The NR347 is based on our heavy-duty AL250 model and is made of stainless steel. Meeting all hygiene and safety standards, the NR347 will prove its value day in and day out.
Our diverter valves: boosting efficiency and hygiene
Diverging and converging powders or granulates is a daily routine in dairy production. Safety, efficiency and maximum hygiene are key. That’s why our 2-TDV, 3-TDV, M-TDV, and GPD diverter valves are very much in demand.
Our 2-TDV and 3-TDV diverter valves are designed for quick disassembly and streamlined distribution. The 2-TDV effortlessly
handles two destinations, while the 3-TDV targets three.
The M-TDV efficiently handles the pneumatic transport of powders or pellets, diverging and converging flows to multiple destinations. Available in different sizes, offering up to 14 ports.
Our diverter valves are the perfect choice for systems needing regular, quick cleaning with minimal downtime.
Would you like to know more about DMN-WESTINGHOUSE rotary valves or diverter valves and discover why we are the dairy industry’s choice worldwide?
Please get in touch with DMNWESTINGHOUSE: +44 1249 818 400 or dmn.uk@dmnwestinghouse.com.
Thanks to an adjustable sound cone and small
dead zone, the new Leuze ultrasonic sensors of the 420B and 412B series can be used for many different applications
If you’re looking to reduce the number of different sensors used in your systems, the 420B and 412B series from Leuze are the right choice: The new ultrasonic sensors are available with adjustable sound cone and as switching (HTU) or measuring (DMU) sensors – this allows extremely flexible application. The sound cone can be set via an IO-Link interface to the three ranges “narrow”, “medium” or “wide” and thus adapted to the respective application. As a result, the ultrasonic sensors operate with maximum precision: They are able to detect reliably in situations where optical sensors are pushed to their limits. They also detect glossy, reflective, very dark or transparent surfaces as well as liquids without problem. The 420B series includes ultrasonic sensors in compact cubic plastic housings. It replaces the 420 series. With the new devices, users benefit from smaller dead zones with the same or a higher sensor operating range. The 412B series complements the range of cylindrical sensors in M12 housing with devices featuring IOLink and analog output.
Maximum flexibility in the red housing
Thanks to their adjustable sound cone, IO-Link interface and two switching outputs, the HTU420B ultrasonic sensors in the red housing are suitable for challenging detection tasks. For example, two fill levels can be detected or two positions can be monitored simultaneously. The adjustable sound cone turns the sensors into flexible all-rounders. A narrow sound cone, for example, is suitable for detecting a fill level through small container openings. In its wide setting, the sound cone in turn captures larger areas – ideal in the case of bulk material or diffusely reflective objects with complex surface or structure. Practical: An interruption filter detects brief changes in measurement within a certain interval caused by interfering
The ultrasonic sensors of the 420B series have an adjustable sound cone. A narrow, medium or wide sound cone can be selected depending on the application. This allows, for example, fill levels to be monitored through differently sized container openings
The DMU420B ultrasonic distance sensors continuously deliver an analog output signal (either current or voltage) to the machine control. This allows system operators to monitor e.g. roll diameters to ensure that the rolls are changed in a timely manner. The glossy surface is detected reliably
objects (e.g. an agitator). The sensor suppresses these interfering signals via the IO-Link interface, thereby ensuring a seamless production process.
For the precise measurement of distances
Moreover, to measure distances, system operators can make use of the DMU420B and DMU412B ultrasonic distance sensors. The devices have an analog output (either current or voltage), an IO-Link interface as well as an adjustable sound cone.
Economical solution in the black housing
The Sensor People from Leuze also offer the HTU420B ultrasonic sensors in a standard design with black plastic housing. As an economical solution with one switching output (push-pull), they are suitable for simple detection tasks. Both variants are available in the operating ranges from 10 to 250 millimeters, 15 to 500 millimeters as well as 20 to 1000 millimeters. The HTU412B series has an operating range of 15 to 500 millimeters.
The cubic sensors measuring 20.5 x 41.0 x 15.0 millimeters are extremely compact. The cylindrical sensors of the HTU412B series too are just 50 millimeters long. They are therefore also particularly suitable for applications in constrained spaces. All types can be parameterized quickly: Easy setup and operation is possible using the teach button, via the teach input or via IO-Link.
www.leuze.com
The AM-T100 Time-of-Flight camera (ToF) uses a Sony DepthSense™ sensor to create 3D depth images with millimetre accuracy. The ToF technology enables high-speed 3D imagery of the scene.
With powerful IR illumination and a high image rate of up to 60fps at 640 x 480 pixel image resolution, the AM-T100 achieves a 67° x 51° field of view with a range of up to 6m.
This camera can be used to support, box filling, stacking, volume detection and labelling in logistics and packaging as a means of boosting the efficiency and accuracy of processes.
SCHMERSAL | Enigma Business Park
www.schmersal.co.uk
uksupport@schmersal.com
There are multiple benefits to recycling waste materials, such as reducing waste pollution and primarily, reducing the need for raw material production in the first place.
Balers are hugely cost-effective within waste management, ensuring a safe, clean, and optimised operation, eliminating the need for larger storage areas. On an important sustainability note, balers naturally safeguard against recyclable waste materials ending up in landfill and also helps reduce air and water pollution at large. Lastly, waste balers comply with the latest environmental laws, reduce costs by up to 80% through maximising loads and reducing transport costs, save all-important space and offer concerted effort towards sustainable best practice.
The Kadant PAAL Group is a result of the merger of four European Companies, PAAL, COMDEC, FAES and DICOM, with the recent addition of BALEMASTER USA. The experience within the group ensures that Kadant PAAL are best placed as a provider of proven, tried, and tested baling solutions.
The UK branch of Kadant PAAL Limited, formally known as Dicom Ltd, was established in Great Britain in 1981 and looks after the UK and Irish Markets. They are located on the Meadow Lane industrial estate in Alfreton, Derbyshire.
Kadant PAAL UK manufacture its own DICOM Product range of popular vertical balers and waste compactors, distributing and installing the PAAL range of fully automatic horizontal balers and conveyors manufactured in Germany. With their own Technical and Design Team they can
provide bespoke solutions with fabrication work manufactured at the factory based in Alfreton to suit all requirements. Our mobile engineers are strategically placed across the country in the event of any mechanical difficulties providing a rapid response call out. Furthermore, the Remote Service Support (RSS) system remotely connects technical experts to the machine in question, with the ability to quickly diagnose the cause of faults, alarms or any performance related issues to avoid unnecessary downtime.
Kadant PAAL Limited is a leading powerhouse across the UK waste sector, with industrial recognition for meticulous manufacturing of
premiere compaction equipment. The standard and customised waste compaction systems are manufactured to deal with even the most robust materials, in line with UKCA (UK Conformity Assessed) marking.
Dale Keeling, PAAL Products Technical Sales Manager, Kadant PAAL Limited gives this insight,
“We have an illustrious history, with Kadant PAAL GmbH who date back to 1854 with a printing house that designed balers for paper waste. Our long history gives us credibility and expertise across the design and manufacturing of purposebuilt balers. The entire recycling equipment range is world-class and is precision-engineered for reliability and longevity.
Kadant PAAL Limited UK manufactures smaller, vertical balers, and compactors supplying to household name retail stores throughout the UK. We also provide major retailers such as Aldi and Ikea the full recycling solution for
effective within
management, ensuring a safe, clean, and optimised operation, eliminating the need for larger storage areas.
their Distribution Centres combining the PAAL and Dicom product range, The German manufacturing facility of Kadant PAAL supplies the larger industrial balers, which we supply for these solutions to our UK and Irish customers.”
Kadant PAAL Limited provides a wide range of recycling equipment, suitable for all industries such as agricultural, light metal, MSW, mixed paper, OCC, multi-material, RDF/SRF, Pet and plastic,
“We will be showcasing our leading recycling equipment range once again at the Resource & Waste Management Expo (RWM) 2024 from the 11th- 12th September at the NEC in Birmingham. Presenting an informative and comprehensive stand at the expo we look forward to meeting new and existing customers and networking across the wider waste management sector. Discussing
varying waste management needs and demonstrating our PAAL and Dicom range of products.
For more information, see the websites below: T 01773 520565
www.kadantpaal.com www.dicompaal.co.uk
Around 160 million tonnes of seafood are harvested and processed each year globally, according to the American Chemical Society’s Turning Food Protein Waste into Sustainable Technologies study. Astonishingly, only 20 to 50 per cent of this vast quantity is recovered as edible food. The rest is classified as byproducts or waste — and rich in unused protein. Here, Stephen Harding, managing director at the material handling specialist Gough Engineering, explains how vibratory linear screens support pet food manufacturers in yielding protein’s benefits and harnessing waste sources of protein.
Like many byproducts of the meat industry, seafood waste is incredibly rich in collagen — one of the most abundant proteins in the body. Fish skin, scales, fins and bones are all rich sources of protein, which the American
Like many byproducts of the meat industry, seafood waste is incredibly rich in collagen — one of the most abundant proteins in the body.
Chemical Society’s report describes as, “the most valuable of the macronutrients from both an economic and human diet perspective.”
A leading manufacturer of premium dry pet foods, based in the UK, sought to address how food protein waste was being handled in its production line. They needed a different approach: processing cold press and raw meat into an additive and incorporating this into its kibble. The result was a nutritionally rich pet food containing the right levels of protein content.
To achieve this, the protein would be extracted through specialised processes. The screening of waste — containing residues from the bulk product — would then be recycled back into production in order to ‘close the loop’ on waste. This scheme underlined the manufacturer’s strong dedication to sustainable business practices.
However, the conscientious approach would necessitate quality control screening processes. It would also require feeding/ conveying equipment provided by a material handling specialist.
The food manufacturer approached Gough Engineering. To support the customer with its new production requirements, Gough designed a scheme/system comprising various vibration screening, conveyors and feeding systems. Specifically, Gough’s offerings included linear screens for quality control screening and bucket elevator systems. The bucket elevators would gently handle and feed the product, by gravity from an elevated output, to the final bagging and packing processes.
A comprehensive system was developed, incorporating a vibratory linear screen, a fines removal screw conveyor, gravity fed Z configured Swinglink® bucket elevator and supporting platforms. The equipment, designed for cleanliness, featured a combination of powder coated mild steel and stainless steel. Additional elements included roller stops, pneumatic slide valves and vibration isolation components — all aimed to deliver the desired quality product to the packing lines.
Crucial to the new system was a vibratory linear screen used to separate fine particles. The screen was equipped with twin sidemounted vibratory motors and Rosta Suspension Mounts and sized to the correct product throughput, designed to provide suitable separation.
The screen is designed to offer product screening and feeding in one system, increasing the quality and value of product through the screening of unwanted sizes. The vibratory linear screen would be essential to maintaining the kibble product prior to bagging, keeping it to the highest quality assured particle sizes. Additional options included screening meshes that could be replaced for cleaning and maintenance.
Gough’s design engineers worked closely with the customer to
design the system to suit its unique requirements. Gough Engineering generated and submitted detailed engineering drawings. This was followed by manufacture, assembly and testing at its in-house factory to verify that the system aligned with the customer’s unique requirements.
The final step involved on-site installation and optimisation using SolidWorks and 3D concepts, guaranteeing a seamless fit within the company’s existing infrastructure. This customised approach allowed Gough to adapt its screens, conveyors, and feeding systems to precisely cater to the pet food manufacturer’s unique requirements.
With Gough Engineering’s tailored solutions in place, the customer achieved a notable throughput of around 17 tonnes per hour. The screens, conveyors, and feeding mechanisms integrated into the customer’s modern pet food production line. As the world grapples with the challenges of animal waste and associated environmental impacts, Gough Engineering’s support of the UK pet food manufacturer shows how conscious choices and strategic partnerships can help extract and combine protein’s benefits with dried pet foods.
To learn more about Gough Engineering’ vibratory sieving solutions for manufacturing pet foods, visit its website.
www.goughengineering.com
Step in and save!
Cat® Lift Trucks has introduced wide straddle variants to expand application possibilities and capabilities of its stacker collection. With a wide range of specification choices and specialised options, these trucks offer class-leading adaptability to different applications. This precise matching optimises productivity, ergonomics and safety in your operation
Crucially, wide straddle stackers can lower their forks to the floor, between widely spaced support legs. This is essential when handling closed-base pallets and other load carriers without open fork spaces or pockets. You can stack goods right down to the ground, and with low-profile straddle legs there is minimal wasted space under the bottom racking beam.
An extensive assortment of duplex and triplex masts, in a broad selection of standard and custom lift heights, matches applications perfectly. You can also make full use of your vertical space, with lifts up to 7.0 metres in some cases. Similarly, you may choose standard or customised straddle widths to match pallet and load types, storage patterns and racking configurations.
Cat wide straddle stackers additionally offer alternative chassis sizes and load capacities from 1.6 to 2.0 tonnes. The stackers’ wide straddle support legs are specially designed for increased drive-in and ground clearance, and trouble-free performance on gradients. They have a low profile, with slight downward angling toward their end point, and are equipped with bogie wheels as standard. Meanwhile, the fork tips are slightly pointed and tapered.
Compact and rapidly manoeuvrable, they enable the highest possible stock densities and are ideal in narrow aisles.
This enables easier and faster pallet entry and exit, even when the truck is turning at the same time. ‘Small gains like these, from functional improvements throughout the trucks, add up to significant time savings over repetitive handling cycles.’
And all the advantages of a Cat stacker
The range include a powerful and quiet hydraulic motor, smoothly governed by stepless, speedregulated lifting and lowering control. This provides quick but safe and accurate positioning and movement of forks and attachments.
The platform stackers give a consistent and reassuring sense of balance, control and power. They are steered and controlled via the class-leading, patented, ergonomic emPower tiller head. Compact and rapidly manoeuvrable, they enable the highest possible stock densities and are ideal in narrow aisles. Cat sit-on stackers offer another dynamic and flexible choice. In this case the operator is comfortably seated for the longest, most intense shifts and greatest distances. There are two Cat wide straddle stand-in stacker models, at 1.6 (NSR16N2S) and 2.0 tonnes (NSR20N2S). Similarly, there are two wide straddle sit-on stackers (NSS16N2S and NSS20N2S). Wide straddle is also available on 1.6 tonne platform stackers with folding (NSV16N3S) and fixed platforms (NSF16N3SR rear entry and NSF16N3SS side entry).
www.impact-handling.com
The measurement of low flow is becoming widely used in many industries. However, the smaller the flow, the trickier it is to control and measure, and finding a suitable flow measuring technology at reasonable cost can prove challenging for both users and flow sensor manufacturers.
There is no set definition for ‘low flow’ in terms of measurement limits for fluidics handling. However, low-flow applications encounter amplified flow stability and performance issues not seen in larger flows. The minimal liquid volume being measured in low flows renders them highly sensitive, such that even the slightest disruptions in process or ambient conditions can exert a substantial impact on flow stability.
Within the markets Titan Enterprises operates in, we consider low flow rates as those below 50 ml/min, with many customers seeking flow rates of between 2 and 20 ml/min.
Neil Hannay, Titan’s Senior R&D Engineer observes: “The increase in demand for low flow measurement technologies is being driven by various industries moving towards transporting heavily concentrated liquids, which are then diluted at the point of use.”
Whether cleaning fluid additives, syrups and flavourings for beer or soda, chemical additives for oil and fuel, low flow flowmeters are required to dose these concentrated fluids at the end process, dispensing the precise amount of liquid to the correct dilution.
As mentioned, measuring low flow is a challenging application to satisfy. Here we analyse 5 types of flow meter - Ultrasonic, Turbine, Oval Gear, Thermal and Coriolisand their suitability for low flow measurement.
Ultrasonic flowmeters measure the velocity of flow. Titan’s in-line Atrato© models, using patented time of flight technology, are capable of measuring flows down to 2ml/min. Lower flow rates equate to smaller signals to determine flow rate and as such, this lower signal strength can affect the flowmeter’s capability to produce repeatable measurement results.
Design challenge: Straight-forward engineering vs complex electronics
Advantages: High accuracy; not fluid specific; high signal to noise ratio; no pressure drop requirements; suitable for both turbulent and laminar liquid flow
Disadvantages: Susceptible to process vibrations/pulsations/noise; sensitive to gas entrainment
The energy required to spin the rotor of a turbine flowmeter becomes swamped by the drag from the system at low flow rates. As flow rate reduces and transitions from turbulent to laminar flow, the linearity changes and the measurements become less accurate. Pelton wheel turbines that use low friction, precision bearings can mitigate this effect to some degree and with careful design, are capable of flows down to 1-2ml/min. They are capable of fast response times and operate across wide flow and operating temperature ranges.
Design challenge: Straight-forward electronics vs complex precision engineering
Advantages: Low cost; can be calibrated in-situ; good accuracy and repeatability with rapid response times
Disadvantages: Susceptible to changes in fluid properties; requires sufficient pressure to move liquid through the pipeline at a rate that causes the turbine blades to spin
Positive displacement flow meters, such as oval gear meters, are particularly effective for measuring low flow viscous fluids, although the resolution can be quite low. To obtain good resolution, the oval gear meters need to be small in low flow applications. Installing an oval gear meter in a horizontal position will reduce rotational friction and improve low-flow measurements. The lower the flow, the smaller the gear size, which are manufactured to tight tolerances with small internal clearances to minimise any fluid leakage around the gears
Design challenge: Straight-forward electronics vs complex precision engineering
Advantages: Ideal for viscous liquids, precision chemical dosing; good reliability
Disadvantages: Not suitable for low flow aqueous solutions as the slippage past the moving element is greater than the volume being measured. Trapped air can prevent small gears from rotating – ensure all gas is purged on initial startup. Low resolution
Thermal flow sensors, primarily used for monitoring gas flow, operate on the principle of monitoring thermal transfer using a reference temperature, a heat injection and a detector. The basic approach is that heat is added to the flowing stream and a temperature imbalance being used to obtain a flow rate. They are fluidspecific as the technology relies on the liquid’s thermal properties and are generally calibrated for the specific fluid properties.
Design challenge: Relatively simple engineering vs complex electronics
Advantages: Highly sensitive and able to measure flow rates down to nanolitres per minute; suitable for low pressure drop applications; not so reliant on the dynamics of the fluid to make a measurement
Disadvantages: Fluid-specific. Thermal low-flow liquid flowmeters are non-linear over their temperature range and so require some correction during the process. Not suitable for low boiling point liquids or liquid mixtures with changing composition
The Coriolis is a mass flowmeter, i.e. measures mass flow directly and independently of the liquid’s properties. The Coriolis provides mass flow and density measurements that are both repeatable and highly accurate, even when the composition of the liquid is unknown or changing. Using the principle of accelerating a moving fluid and detecting the reaction on the vibrating tube with sensors, Coriolis meters are very sensitive and flows lower than 0.2 ml/min are possible.
Design challenge: Complex electronics and engineering
Advantages: Extensive material compatibility; can be used for either liquid or gas flow measurement; independent of liquid or process variables
Disadvantages: The primary limitation is the flow must be single-phase and of low viscosity. They are also expensive devices so would not be suitable for low-cost low flow applications
As flowmeters can be the most limiting component of a low flow fluidic system, it is essential to choose the most suitable highprecision flow sensor for your application.
www.flowmeters.co.uk
ViSWIR Hyper APO Features:
• Capable of fully corrected focus shift in visible and SWIR range (400nm - 1700nm)
• Achieves spectral imaging with a single sensor camera by simply syncing the lighting
Floating design adjusts focus for different wavelengths
8mm, 12mm, 16mm, 25mm, 35mm* and 50mm* (*2023)
ViSWIR Lite Features:
High transmittance at whole wavelength of 400nm - 1700nm by adopting hyper wideband AR coat
Outstanding cost-performance for single-wavelength lighting & narrow-band imaging
Compact design
5mm, 8mm, 12mm, 16mm, 25mm, 35mm, 50mm
E/M Coating Services pride themselves on being able to offer customers high quality coating applications and processes for a wide range of industrial sectors. We are uniquely placed to design and manufacture bespoke protective coating solutions in our own highly specialised industrial coating facilities. We have over 40 years of experience in surface technologies and are pioneers in the development and application of solid dry film lubricant coatings.
Our products and services are utilised by high technology markets including the aerospace and oil and gas sectors, ensuring that we are always at the forefront of the latest designs, materials and technologies.
E/M Coating Services, under their brand name Everlube® Products, offers a complete engineered coating development service and our own in house formulation chemists are continually developing new coatings and surface
We have over 40 years of experience in surface technologies and are pioneers in the development and application of solid dry film lubricant coatings.
technologies that are designed to satisfy todays ever increasing engineering requirements.
Our Everlube® range of branded dry film lubricant products have been specifically designed to enhance and improve the performance of critical components and meet a wide variety of industry, defence and customer specifications for critical components.
Our technical services team will work with you to find the product
most suited to your requirements or if you know which product you need please visit our Everlube® Product website directly, we have also produced an Everlube® dry film coatings matrix as a quick reference guide.
Coating removal services are used to ensure that critical components, fabrications or surfaces are completely clean and free from any residual rust or coating residue. By utilising our surface coating removal services you can restore your components or fabrications to near their original condition.
We offer an array of surface, paint and powder coating removal techniques including: burn off, localised high temperature removal, grit blasting, selective blasting, sponge blasting and chemical stripping.
www.emcoatingsuk.co.uk
Protection & life extension of your critical components throughout any crisis!
Protection & life extension of your critical components throughout any crisis!
COATING SERVICES:
COATING SERVICES:
l Thermal Spray & HVOF Coatings
l Thermal Spray & HVOF Coatings
l Dry film lubricants - MoS2, PTFE, Graphite, WS2
l Dry film lubricants - MoS2, PTFE, Graphite, WS2
l Coatings for corrosion, chemical & environmental protection
l Coatings for corrosion, chemical & environmental protection
l Titanium anodising
l Titanium anodising
l Zinc rich coatings for corrosion protection
l Zinc rich coatings for corrosion protection
l Impingment coating processes for ultra thin solid film lubricants
l Impingment coating processes for ultra thin solid film lubricants
l Nonstick/release coatings for low coefficients of friction
l Nonstick/release coatings for low coefficients of friction
l Primers for rubber and plastics for sound absorbing and dampening materials
l Primers for rubber and plastics for sound absorbing and dampening materials
l High temperature resistant coatings
l High temperature resistant coatings
l Rare earth magnet coatings
l Rare earth magnet coatings
l Coatings for EMI/RFI shielding provide highly conductive coatings and platings to control electromagnetic interference
l Coatings for EMI/RFI shielding provide highly conductive coatings and platings to control electromagnetic interference
l Ultra thin conformal parylene coating to reduce friction and protect against contamination
l Ultra thin conformal parylene coating to reduce friction and protect against contamination
l Pre-treatments including Ti Anodising, Phosphate
l Pre-treatments including Ti Anodising, Phosphate
Conversion Coating and Chilled Iron Blasting, Aluminum Oxide Blasting and Vapour Degreasing
Conversion Coating and Chilled Iron Blasting, Aluminum Oxide Blasting and Vapour Degreasing
In our latest project we were involved in the innovative world of aquatic food production where we supplied pumps to assist with automated aquatic mechanical harvesting.
It’s an innovative method of growing crops which could change the way our food, animal food and fertilisers are grown, and have incredibly positive effects on sustainability and decarbonisation in the global environment.
What is aquatic mechanical harvesting?
It’s a way of cultivating floating crops or plants that grow on the surface of a body of water.
Our client - a dynamic agricultural start-up business was looking for a way to automate the harvesting of water-grown crops, and were developing a machine to gently skim the surface and collect the plants growing on the water.
A key part of this operation would be the pumps which would help by automating harvesting at a rate of between 5,000 to 20,000 litres per hour – much quicker than the manual harvesting of crops grown in the ground.
The six aquatic harvesting pumps we were asked to supply would be connected to a weir and would skim the aquatic plants from the water surface, before sending them to large collection hoppers.
Why grow plants in water?
Around the world, farmers are facing big challenges in growing the food we all eat.
The fertiliser, the seed, and the feed ingredients for livestock operations are all becoming increasingly expensive and hard to come by.
These factors are all linked to the problems farmers are having around changing climate conditions, land and water availability and shortages of labour.
In short, it’s becoming more difficult for farmers to run a profitable operation. Aquatic plants could help farmers around the world make more food using less energy, water and land.
These are plants which are grown in engineered ponds and then harvested automatically by robotics in a way that’s quite different to what farmers have done for centuries.
Our client calls them super plants and they are a radically different solution for the global agricultural industry.
In fact, they are unlocking cleaner and more sustainable agriculture that’s both more profitable and has considerably lower carbon emissions.
They’re called super plants because the right varieties can produce large amounts of protein, vitamins, minerals and amino acids.
This means they can be grown to produce feed for animals, potentially for humans too, as a bio-fertiliser to grow other crops and as a soil enhancement to maintain soil health.
What’s more, these are some of the fastest-growing plants on Earth, so they need to be constantly harvested in large quantities.
This is why our client is working with North Ridge Pumps to develop an automated harvesting solution. They’re combining plant science with automation and engineering, to make the operation work profitably at scale, with no need for a huge workforce.
Our specification for this project
Here at North Ridge Pumps, we’re not restricted to a single pump technology.
We use our expertise to offer a tailor-made solution, not something off the shelf. We choose the best pump for any particular client and application - at the lowest lifetime cost.
As these super plants are among the fastest-growing plants on Earth, they need to be constantly harvested in large quantities.
The six aquatic harvesting pumps we specified would be a key component of this automated operation, skimming the plants from the water before sending them to collection hoppers. To do this quickly and reliably, we specified six of our proven flexible impeller pumps.
It’s a pump design based on a circular rubber impeller with a number of flexible rubber vanes contained within a casing.
The casing is actually smaller than the impeller vanes. So the vanes must be bent to get them into the pump head. This then creates a seal and chamber between each vane.
We use our expertise to offer a tailor-made solution, not something off the shelf. We choose the best pump for any particular client and application - at the lowest lifetime cost.
The pump head has several chambers which operate like valves. This makes the pump self-priming, and it works in the same way as a positive displacement pump.
In addition, the impeller is mounted inside the casing so the vanes bend at different angles in relation to the pump inlet and outlet.
Why our flexible impeller pump was perfect for automating harvesting
• Works in any location and in almost any position and still work effectively
• High flow capacity at full motor speed even with low viscosity fluids
• Runs at different speeds to handle different viscosities
• As the pump works by positive displacement, the pressure is constant and the flow rate is proportional to speed
• Gentle pumping action ensures that the fluid consistency is unaffected by shear forces – even milk, cream and thixotropic fluids
• Flow is non-pulsating so the output can be measured accurately with a flowmeter
• Self-primes from dry up to 6m
• Easily handles solids without causing any damage – for example, seeds, grapes and fruit in suspension can be safely handled
• Reversible so tank loading and unloading can be carried out by one pump
• Easy maintenance with only 8 parts in total, only 4 of which will wear
• Cleaning In Place (CIP) friendly so easy to dismantle and clean
Looking to automate one of your manual processes for greater efficiency and profitability?
Speak to North Ridge Pumps on 01773 302 660 or visit www.northridgepumps.com to see how we can help.
Vaplas Ltd established in 1993 is a family run company residing in a 10,000 sq. ft facility in Yorkshire.
Specialising in Plastic machining and fabrication, we house state of the art machinery complete with a full inspection department all certified to ISO9002.
Supplying industries in Food Processing, Pharmaceutical, Beverage and Bottling Plants, Vaplas can supply anything from small components to large machine guards and anything in between.
Milling: Our CNC mills with 5th Axis capabilities can machine intricate, precise one-off parts, or batch quantities of thousands. The strictest quality control standards are operated throughout every stage of manufacture.
Routing: Our investment in CNC routers with full CAD-CAM operation and 5th axis capabilities ensures a routing service which delivers a professional, prompt and precise approach. Vaplas can produce almost any cut shape from an extensive range of industrial plastics achieving an exceptional standard of finish and accuracy every time. Skilled machinists will work with the customer, assisting with problem solving during the design process and recommending cost saving options.
Turning: Plastic turning is one of the key stages of the CNC plastic machining process. It is a form of machining used to produce rotational, asymmetric parts such as holes, threads and grooves. It is also ideal for prototyping several solutions. We have expanded our machine shop to include two brand new DMG Mori CLX 450 Universal Turning Centres which offer multiple options.
Cad Cam: Vaplas uses CAD (Computer Aided Design) CAM (Computer Aided Manufacturing) software to generate toolpaths
Supplying industries in Food Processing, Pharmaceutical, Beverage and Bottling Plants, Vaplas can supply anything from small components to large machine guards and anything in between.
that drive machine tools to turn designs into physical parts. CAD/ CAM software is used to design and manufacture prototypes, finished parts, and production runs.
Fabrication: Whether it’s a machine guard or a plastic tank, our skilled engineers will bend, weld and bond quality stock plastic to perfection. Vaplas can offer and supply quality FDA and other approved materials to withstand extreme temperatures, chemical reactions and impacting to suit all
applications for water, food and drink applications or to reduce friction and display physical and mechanical properties for industrial environments and commercial requirements.
To enable Vaplas to supply this level of service, we have a highly knowledgeable team who speak to customers making recommendations and offering solutions using our extensive knowledge of the industry. We invest in the latest and most cutting-edge equipment and technologies to provide the highest finish of parts, exceeding customer expectations every time.
Why choose anything less?
www.vaplas.co.uk
A manufacturer of cooking sauces making small batches may be transferring the product from one container to another by hand. “We’re only moving small quantities so it’s not worth investing in a pump”. Correct? Perhaps initially, but as production increases there are many reasons to consider more than just the upfront cost of the pump.
Castle Pumps explain five reasons why upgrading to a barrel pump is much more beneficial than continuing to manually handle your product.
1. Increased productivity.
Using a barrel pump is quite simply quicker and more efficient than moving the fluid by hand. Manual transfer is very time consuming for an operator, so if your business begins to upscale production, it becomes less feasible for an operator to keep up. Using an electric barrel pump is less labourintensive, freeing up your workers’ time to spend on more value adding tasks.
2. Safer for operator and workspace
A spill, which is much more likely during the process of manually scooping and pouring fluid, means wasted product and a clean-up. The fluid being stored in a drum or IBC can sometimes also be hazardous e.g. chemicals used for cleaning food processing equipment, and therefore manual handling unnecessarily exposes operators to risk.
3. Accurate measurement
In many processes, a very precise quantity of fluid may need to be dispensed. For example, whilst packaging a final product, or dosing a specific amount of an ingredient into a mixture. Doing this by hand can cause measuring errors and inaccuracies, resulting in an incorrect or inconsistent final product. By using an electric barrel pump with a batch meter, not only is it much quicker for the operator but it ensures product consistency.
4. Product purity
Manually moving a fluid leaves it open to contamination from the air or general environment. Very special care needs to be taken to ensure no external debris gets into the container being used to transfer it – which is absolutely vital in food and cosmetic industries. Using a food grade barrel pump keeps the product safely contained with the hose and pipework and protected from external contaminants.
5. Cheaper in the long run
Whilst manual handling may seem more economical at beginning of production, eventually demand and operator priorities will outgrow this. Using a pump means reduced labour from the operators, giving them more time to focus on other essential tasks, less product waste and less clean up required if a spill occurs. All of this adds up and saves money in the long term!
www.castlepumps.com
In the dynamic landscape of the food industry, maintaining quality, freshness, and safety standards is paramount. Enter Air2GasTech Nitrogen Generators, a game-changer for food producers worldwide. These cutting-edge systems offer a sustainable solution for generating food standard nitrogen on-site, eliminating the need for traditional nitrogen supply methods.
In the realm of food packaging, nitrogen plays a crucial role in preserving freshness and extending shelf life. Air2GasTech Nitrogen Generators ensure a continuous and reliable nitrogen supply, safeguarding products from oxidation, moisture, and microbial growth. Moreover, by producing nitrogen on-demand, they reduce dependence on external suppliers, streamlining operations and cutting costs.
Beyond packaging, Air2GasTech Nitrogen Generators find applications in food processing, purging, and blanketing, enhancing efficiency while maintaining stringent quality control. With customisable solutions tailored to specific industry needs, they empower food producers to meet regulatory requirements and consumer expectations with ease.
In an era where sustainability, safety, and efficiency are paramount, Air2GasTech Nitrogen Generators stand as indispensable allies for the food industry, driving innovation and excellence every step of the way.
www.air2gastech.com
• Replace high pressure nitrogen cylinders and liquid dewars
• Standby mode- only produce N2 when required, saving energy and money
• Continuous & reliable N2 gas supply
• Easy to service & maintain
• Our technology assures long lifetime and excellent ROI
• Installation & Maintenance carried out by our own service engineers
Scan the QR Code to view our product range online.
E: info@air2gastech.com
W: www.air2gastech.com
T: +44 (0) 1360 848130
for your
With the right pump, you’ll avoid:
» Clogging, excessive wear and high maintenance costs
» Crushing of solids or product consistency changes
» Product waste or innaccurate ingredient dosing » Labour intensive pump operation Get the RIGHT pump by speaking to us
Marking a significant food packaging industry milestone, Klöckner Pentaplast (kp) has launched the first food packaging trays comprising 100% recycled PET (rPET) deriving exclusively from trays.
Until now, food packaging trays have been manufactured using ever increasing proportions of recovered PET material; however, the newly launched kp tray is the first to be composed entirely of recycled tray material. This milestone is the direct result of the kp’s Tray2Tray® initiative, which aims to rewrite the PET recycling rules.
“As a bold innovator, we are thrilled to introduce the first-ever 100% rPET tray to the market.” said
Thomas Kure Jakobsen, President, Food Packaging at kp.
“This achievement is a major breakthrough in the packaging industry, and perfectly demonstrates what is possible with the right combination of expertise and technology. Most
rPET in the material loop comes from plastic bottles, of which just 30% goes into food packaging trays, and most of this does not end up being recovered. As a result, countless tonnes of rPET tray material are wasted each year.
“kp Tray2Tray® challenges this by creating a robust closed loop system of PET flake from trays. We work with suppliers to create a separate supply stream of recycled PET from trays, which can be used to create more of the same, rather than being downcycled.”
Thanks to this breakthrough, kp customers can access a fully circular tray solution for food packaging.
We’re not just looking to move the needle on plastic tray sustainability; we’re aiming to begin the next era.
The kp supply chain is RecyClass certified, ensuring the safety, quality and traceability of its PCR packaging solutions. The new 100% kp Tray2Tray® packaging is ideal for businesses looking to control costs pertaining to eco taxes and plastic tax legislation, as well as those looking to advance their ESG strategies.
Thomas Kure Jakobsen added: “We’re not just looking to move the needle on plastic tray sustainability; we’re aiming to begin the next era. One of the biggest advantages of partnering with kp and using kp Tray2Tray® content is that it’s a perfect ‘drop
in’ solution, so switching over is easy, and packaging performance isn’t compromised. Our 100% kp Tray2Tray® packaging is a real, workable tray that offers a glimpse into the future of tray packaging circularity.”
Addressing rising consumer calls for more sustainable packaging solutions, kp remains committed
to pushing the boundaries of sustainability. The launch of a 100% rPET tray underscores the company’s ‘packaging with integrity’ ethos, and its mission to create a more sustainable packaging industry without compromising quality or safety.
To learn more about kp Tray2Tray® click here.
new webinar features expert strategies on enhancing food safety and efficiency in flow wrap
Mettler-Toledo Product Inspection, a global leader in product safety technologies, is pleased to announce its upcoming webinar titled “4 Steps to Maximise Product Quality in Horizontal Flow Wrap Applications.” The webinar is scheduled for Wednesday 8th May with sessions at 9:00 AM and 3:00 PM GMT.
In this impactful session, attendees will hear from industry experts as they explore the challenges confronting food manufacturers packaging products in flow wraps. Against the backdrop of evolving packaging regulations, manufacturers grapple with intricate challenges, including packaging complexities and accelerated production, all of which can diminish crucial manufacturing time and accuracy. This webinar will explore strategies for navigating these constraints to combat rising manufacturing costs and enhance production efficiency.
Experts on the webinar will discuss four key steps to optimise product quality in packaging. These steps include advanced inspection technologies such as metal detection, x-ray, vision technology and checkweighing, specifically tailored to address the unique requirements of horizontal flowwrapped production lines for highspeed applications, such as snacks.
Presenting this insightful webinar is Niall McRory, the Global Key Account Manager at Mettler-Toledo who brings over 24 years’ experience and expertise in food safety. With a focus on creating global standardisation of supply, he has spearheaded initiatives that have led to reduced Total Cost of Ownership (TCO) and provided best-in-class Product Inspection sales and service support.
“We understand the critical importance of maintaining product quality and safety in flow wrap applications, especially in the fast-paced snack industry,” says Niall McRory. “Our webinar aims to provide practical strategies and demonstrations to help manufacturers maximise efficiency and compliance in their production processes.”
The programme’s main focal points include:
Production Principles and Manufacturer Needs:
- Understanding the fundamental principles guiding production processes and the specific needs of manufacturers in the industry.
Product Inspection Application Along the Horizontal Flow Wrap Line:
- Exploring the application of product inspection technologies
throughout the horizontal flow wrap line to facilitate comprehensive quality control.
Inspection of Raw Product:
- Examining the importance of inspecting raw products before they enter the packaging process to detect any contaminants or irregularities and save packaging material costs.
Inspection After Primary Packaging:
- Highlighting the significance of inspecting products after primary packaging to verify packaging integrity and offer highest product quality.
Inspection After Secondary Packaging:
- Discussing the necessity of inspecting products after secondary packaging for bulk goods to address any potential issues introduced during this stage.
Data Management and Service Offering:
- Exploring the role of data management solutions such as PRODXTM in overseeing product inspection processes and the importance of service offerings in ensuring equipment reliability and performance.
Register here to secure your place on the webinar and to better understand how to maximise product quality in flow wrap applications or visit www.mt.com/ pi-flowwrap-webinar-pr
Offer consistent product quality at the point of use for a wide range of applications, guide rails position the IBC and the mixer is raise and lowered into the IBC with a push button operated electrical actuator.
Fixed or mobile mixing stations are supplied complete with a control panel and safety interlocks.
Standard IBC mixing stations can be adapted to integrate with systems on site including pumps, valves, weighing and measuring instrumentation and controls to meet specific site requirements.
Alex Stewart Food Test Lab is a fully UKAS accredited laboratory and is part of Alex Stewart Agriculture. We provide a complete range of food testing and microbiological analysis including food and dairy products, water and beverages, seeds, cereals, oils & fats, raw & refined sugar and other consumable products.
Fats, salt & sugars n Cereals, oils & seeds n Food & dairy products n Water & beverages
Your global network of inspection and analytical services www.foodtestlab.co.uk
21 Sefton Business Park, Olympic Way, Aintree, Liverpool, Merseyside L30 1RD UK T: +44 (0) 151 525 1488 E: laboratory@alexstewartagriculture.com
Virto-Cuccolini’s sieves improve water filtration efficiency in the Produce industry, particularly in the processing of harvested fruits and vegetables, in which water assumes a vital role in rinsing the product, facilitating its handling, peeling, and cutting.
Throughout the process, water progressively accumulates impurities and remnants of the product, such as peels, starches, and pulp fragments, thereby presenting challenges in water management prior to treatment by the purifier and subsequent reintroduction into the production cycle.
The separation of solid parts from the water before treatment simplifies the entire process, rendering it more operationally efficient and cost-effective.
To attain this objective, it is imperative to use a filter capable of capturing very small solid particles (ranging from 0.5 mm to a few microns). This includes starch, which, under certain circumstances, can give rise to foams that pose challenges in disposal.
In this specific context, the Virto-Cuccolini vibrating sieves assume a key role in the solidliquid separation phase within an aqueous environment: they facilitate the efficient extraction of solid particles from the rinse water. This approach not only optimizes the processing workflow but also significantly diminishes the overall expenditures associated with water purification treatment.
Virto-Cuccolini provides a full range of vibrating screens specifically made for managing liquids in the food industry, in Aisi 304 or Aisi 316, both with ATEX and FDA certifications. The great variety of available sizes gives the possibility to both big-scale industrial projects and small pilot
The great variety of available sizes gives the possibility to both big-scale industrial projects and small pilot plants to find the best solution.
plants to find the best solution. Additionally, the Aftermarket Division, offering spare parts, training, and assistance services, provides the necessary support to uphold optimal performance throughout the entire operational lifespan of each vibrating screen.
WBT Services Ltd, based in Gloucestershire, England, is a leading provider of industrial
solutions across the UK & Ireland. As the agent for Cuccolini sieves, WBT Services Ltd delivers bespoke and niche sieving solutions. Cuccolini sieves are efficient for tasks such as policing, grading, and dedusting. Their expertise ensures precise material separation, making them a reliable partner for industrial sieving equipment.
www.virtogroup.com
Delivering the best solutions for solid and liquid classification and separation processes
An effective material handling and classification system is one of the fundamental pillars for many companies operating in the most varied manufacturing sectors. Within many of these processes, the classification of materials through industrial screening is an important step that can determine the quality of the finished product.
For this reason, WBT Services Ltd, a company based in North Gloucestershire that has been offering solutions for dust and fume control systems and for material handling for more than 40 years, selects the best suppliers to serve its customers; and this is how it relies on Virto-Cuccolini, a historic Italian company specialised in the construction of industrial vibrating sieves for the classification and separation of powders and liquids.
This partnership, born in 2019, aims to offer quality and cost-effective solutions to even complex requests and to cover different needs, such as:
- Quickly cleaning the product from unwanted pieces during the first phase of the production line. This is achieved with safety screening, created precisely to prevent undesired particles from entering the production cycle.
- Separating a product by particle size. This is the basis for creating,
A continuous original spare parts supply service is available and can also be arranged on a regular basis.
from a bulk ingredient, multiple products of different fractions that cover different market needs.
- Separating materials from freeflowing liquids or even from dense liquids, such as sludges.
- Recovering waste material to transform and use as a new product or as a new second raw material.
This is a helpful way to start achieving more sustainability in the production process.
Virto-Cuccolini offers a wide range of sieving equipment in Aisi 304 or Aisi 316, both with ATEX and FDA certifications. The great variety of available sizes gives the possibility to both big-scale industrial projects and small pilot plants to find the best solution.
As one of WBT Services’ major focus points are maintaining its customers’ process quality, a continuous original spare parts supply service is available and can also be arranged on a regular basis.
A vibrating sieve can serve hundreds of different applications in the food industry, but also in other sectors in which separation and classification of materials need to be a part of the manufacturing process.
The British-Italian tandem formed by WBT Services and Virto-Cuccolini will make all their expertise available to satisfy customers throughout the UK & Ireland.
www.virtogroup.com
The Chairman of the National Association of Pallet Distributors (NAPD) has called for supply chain businesses to ensure they have a ‘reuse first’ policy in place for pallets.
As new legislation will be introduced in the UK and EU in 2024, environmental reporting will be mandatory for large businesses and is expected for SMEs by 2026. NAPD Chairman Paul Tait said the many companies that supply products such as food, drink, and pharmaceuticals can make the transition more straightforward by reusing their pallets, which will cut the carbon impact of their supply chains.
“Reuse is a central part of a circular economy and enables businesses to make sizeable savings in their emissions and move closer towards their increasing sustainability
Reuse is a central part of a circular economy and enables businesses to make sizeable savings in their emissions and move closer towards their increasing sustainability obligations,
obligations,” said Tait. “Wooden pallets are a naturally sustainable product and companies that reuse them in their supply chains extend the environmental benefits further.”
Used pallets are exempt from packaging waste regulations, so businesses using them also cut down administration and cost.
Saleh Hijazi, press officer for
NAPD, said: “With regulations including the Sustainability Disclosure Standards (SDS) and Extended Producer Responsibility (EPR) in the UK, and CSRD in Europe, coming into force in the months ahead, it’s imperative that everyone involved in goods supply chains works together to mitigate environmental impact and make businesses greener.
“Sustainability-focused strategies for supply chains are no longer a ‘nice-to-have’; they are essential to meeting legislative obligations and the demands of our customers.”
NAPD is the UK association for companies that repair pallets for reuse to a high standard. Its members are bound by a code a conduct and provide additional supply chain services to customers.
www.napd.co.uk
Multiple products?
Different packaging? High capacity?
Multiple products? Different packaging? High capacity?
No problem.
No problem.
● Clever solu�on design based on the latest technologies
● Clever solu�on design based on the latest technologies
● Focus on the opera�ons safety, produc�vity and efficiency
● Focus on the opera�ons safety, produc�vity and efficiency
● Specialist in mul�-line systems with product buffering
● Specialist in mul�-line systems with product buffering
● 50+ years of experience
● 50+ years of experience
● Global supply capability
● Global supply capability
● Maintenance services with 24/7 support
● Maintenance services with 24/7 support
Discuss your next palletising project with Scott.
Discuss your next palletising project with Scott.
scottautomation.co.uk
scottautomation.co.uk
Sco� Automa�on Ltd
Sco� Automa�on Ltd
Tel. +44 (0)1384 210 278
Tel. +44 (0)1384 210 278
info@sco�automa�on.co.uk
info@sco�automa�on.co.uk
Schmersal is set to launch four new electromechanical safety switches with separate actuator: the AZ215/AZ216 and AZ315/AZ316 switches handle safety guard position monitoring of sideways or rotating guard doors. Their stand-out feature is the rotating actuator head made from diecast zinc, which can be easily rotated in 90° increments before installation. This allows the head to be approached from the side from four different directions, as well as from above. With this versatile approach position and possibility of combination with different actuators, the AZ series offers maximum flexibility in installation, as well as a range of universal usage options to the user. The designer can use the AZ switch both for right-hand and
Their stand-out feature is the rotating actuator head made from diecast zinc, which can be easily rotated in 90° increments before installation.
left-hand design on rotating and sliding guard doors.
The plastic or metal switch housing is consistent in design and size with the PS 215/216 and PS 315/316 series position switches, giving the AZ switches an equally compact design and easy integration into the surrounding construction. The small AZ215 and AZ216 switches are consistent with standard EN
50047, while the larger AZ315 and AZ316 switches satisfy standard EN 50041.
In addition to the standard version with M20 cable entry and connection terminals, versions with 4 or 8-pin M12 connector are also available, depending on the number of contacts. With the inbuilt 8-pin connector, AZ switches can be connected to the SFB Safety Fieldbox. Device versions with three contacts in a wide range of combinations can also assume a signalling role in addition to their safety function. The connection terminals on the switch elements, which are rotated by 45°, enable quick and easy wiring.
www.schmersal.co.uk uksupport@schmersal.com
The VeloBlade Flow Runner is an automatic feeding system that is retro ttable onto all VeloBlade Nexus models. This time saving automated production process has a stacking capability of up to 100kg. The Flow Runner removes the need for sta to load the system manually saving you both time and money.
PERFECT FOR PACKAGING
PERFECT FOR PACKAGING
VINYL STICKERS
VINYL STICKERS
POS/POP/FSDU DISPLAYS
POS/POP/FSDU DISPLAYS
OUTDOOR/INDOOR SIGNAGE & MUCH MORE!
PPE/PROTECTIVE SCREENS
OUTDOOR/INDOOR SIGNAGE & MUCH MORE!
PPE/PROTECTIVE SCREENS
The fact that Hart Door Systems has built a reputation for quality and longevity of its wide range of industrial doors, the importance of door maintenance should not be understated says Keith Fisher, Hart’s National Operations Manager.
Servicing industrial doors not only improves their reliability and operational functionality, but servicing is also a requirement under Health, Safety and Welfare Regulations which protect people who come into contact with the doors. Indeed, failure to maintain industrial doors could put the user in breach of Government legislation incurring liability in the case of an incident involving an industrial door which is noncompliant.
As essential support for our clients Hart has comprehensive Service & Maintenance assistance as a specialist department which delivers a range of repair and scheduled maintenance options for its customers to further extend the life of their doors.
Given the very wide variety of industrial classifications we supply doors and shutters to, the emphasis has to be on designing servicing and maintenance packages which are tailored to match the specific needs of our clients’ businesses and the arising usage patterns of the various doors/shutters.
A preventative Servicing and Maintenance Agreement ensures Hart’s servicing is carried out correctly and at the precise frequency thus complying with Regulations. Typically, during a Hart servicing visit all mechanical and electrical elements are checked for missing parts, general wear and tear and Compliance issues.
Mechanical checks include inspecting parts such as drive chain tension, alignment, and lubrication, bearing wear and tear, motor oil levels and fabric tension
and electrical checks include limit settings, cable connections and safety devices.
Hart also has a legal responsibility to ensure doors are left in safe working order after servicing. Again, the issues are wide ranging such as measuring the closing forces of automatic doors where safe contact is the main strategy to prevent hazards.
The closing force of a door ensures correct force limitation under EN 12978 which prevents injury and crushing. Testing should always be carried out with an annually calibrated instrument according to DIN 18650, EN 12453 or EN 12445. On completion of a Hart service visit, a paperless electronic copy of the engineer’s report will be issued
which may include additional recommendations necessary to ensure the doors are safe and compliant to relevant legislation due to changing ‘shop floor’ circumstances.
The sophistication of door systems such as Hart’s Speedor range or its Typhoon shutter range has changed significantly over the years to cater for changing needs by its customers across the globe and indeed by changing climate. To ensure hard working doors in busy industrial environments continue to make a significant daily contribution to efficiency and safety, planned maintenance is essential. www.hartdoors.com
Mettler-Toledo to showcase advanced product inspection technologies to snack manufacturers under the theme ‘Relax, we have got you covered’
– Mettler-Toledo Product Inspection, a global leader in food product safety technologies, is proud to announce its participation in SnackEx, hosted by the European Snack Association. The event will take place at Mässvägen 1, 125 30 Älvsjö, Stockholm, Sweden, on 19-20 June 2024, where MettlerToledo will be both exhibiting and speaking.
At Booth 244, Mettler-Toledo, one of the leading product inspection experts for snacks, will showcase its innovative product inspection technologies tailored specifically for the salty and savory snack industry.
Among the featured product inspection solutions will be:
- Metal Detection:
A unique cut-away throat metal detector will provide visitors with an immersive experience, allowing them to witness firsthand the inner mechanisms of Automatic Test System (ATS). By simply pressing a button, visitors can observe ATS in action as it cycles through test samples, demonstrating the system’s robust metal detection capabilities and reliability. To demonstrate the dramatic difference in detection capability with other real-world metallic contaminants will be the latest Mettler-Toledo throat detector with eDriveTM and ATS. These metal detectors not only showcase the innovative solutions from Mettler-Toledo but also serve as educational tools,
In
addition to showcasing cuttingedge inspection technologies, MettlerToledo will also feature its innovative ProdXTM data management software at the event.
enlightening attendees about the importance of metal detection in product safety and integrity.
- X-ray Inspection System:
The X12 x-ray inspection system showcases cutting-edge technology in product safety and quality assurance. Engineered to deliver exceptional contaminant detection capabilities, the X12 provides unparalleled sensitivity to detect a wide range of foreign materials, including metal, glass, mineral stone and dense plastics.
With its high-resolution imaging and advanced algorithms, the X12 offers superior inspection performance, enabling snack manufacturers to safeguard their products against contaminants and uphold the highest quality standards. Designed as an entrylevel solution, the X12 combines affordability with state-of-theart functionality, making x-ray inspection accessible to all budgets without compromising on performance or reliability.
- Checkweigher and Vision Inspection Combi-Solution:
Representing a groundbreaking advancement in product inspection technology, checkweighing and vision capabilities are combined within a single system, offering enhanced accuracy and efficiency. The Combination Solution provides precise weight measurement and comprehensive label inspection, thereby optimising packaging integrity and compliance with regulatory standards. With its innovative design and advanced features, the Combination Solution is positioned to set a new standard for product inspection solutions in the snack industry.
- Data Management Solution:
In addition to showcasing cutting-edge inspection technologies, Mettler-Toledo will also feature its innovative ProdXTM data management software at the event. ProdXTM offers snack manufacturers
a comprehensive solution for data collection, providing realtime insights into production performance thereby facilitating proactive decision-making and optimising operational efficiency. The information provided by ProdXTM helps manufacturers to comply with regulatory standards and enhance quality control measures throughout the production process. Visitors to the stand can discover firsthand how ProdXTM empowers snack manufacturers to achieve greater transparency, productivity, and compliance in their operations.
During the event, Rob Stevens, Market Manager for Metal Detection at Mettler-Toledo, will deliver a compelling presentation titled “Metal Detection, X-ray Inspection or Both?” scheduled for 19th June at 4.20pm. He will explore the critical importance of foreign body detection in snack
manufacturing processes and will also look at how both metal detection and x-ray inspection technologies play complementary roles in achieving product safety and quality.
Visitors will be able to see firsthand how Mettler-Toledo solutions work in real-life examples. A success story of Mettler-Toledo products in action is PATA S.p.A., one of Italy’s leading producers of savory snacks. Through a longstanding partnership with MettlerToledo, PATA has achieved compliance with industry standards while optimising productivity and reducing costs. PATA’s adoption of the MettlerToledo product inspection solutions, including dynamic checkweighers and advanced metal detection systems, exemplifies the transformative impact of innovative inspection
technologies on snack manufacturing operations.
“We are excited to engage with industry professionals at SnackEx and demonstrate how the Mettler-Toledo cutting-edge product inspection solutions can empower snack manufacturers to enhance product safety, compliance and efficiency,” said Stevens.
Attendees are encouraged to visit Mettler-Toledo at booth 244, to explore the latest advancements in product inspection technology and learn more about the benefits of integrating metal detection and x-ray inspection in their manufacturing processes.
For more information about Mettler-Toledo at SnackEx and its comprehensive range of product inspection solutions, please visit https://www.mt.com/pi-snackex
Over 400 metres of the Unifold® Gutter lining system was installed on London’s iconic venue, The Royal Albert Hall, throughout the summer of 2023.
The Unifold® Gutter Lining System was chosen for its versatility, unfailing ability to replicate existing systems and its long life.
Following a survey by Ampteam personnel, along with Saper Glass Industries Limited, a design solution was provided for the gutters and samples were sent to test fit the Unifold® gutter lining within the gutter cavity, as the throat dimension varied considerably across the profiles.
All runs of the gutter were manufactured to suit the curved nature of the dome which roofs the Hall, and to fit within the minimal throat dimension between the glazing and glazing bars, meaning that bespoke faceted and cranked joint plates were provided so that the new Unifold® lining could follow the profile of the existing gutter.
Full site information was provided including laying sequences, special details and instructions with each delivery of the system.
Ampteam were partnered by Approved Installer, Saper Glass Industries Limited and Faithorn Farrell Timms as contract administrator, and their input and expertise, along with comprehensive discussions throughout, enabled a successful installation of the Unifold® system.
Following installation of the Unifold® every Unifold® gutter run was water tested by flooding the gutter from the top of the run(s) via hose, with additional assistance from the poor weather, and no leaks were detected in any of the installed gutter runs.
Ampteam developed the Unifold® gutter lining system some 20 years ago to provide custom designed solutions to leaking gutter problems.
Unifold® utilises an EPDM membrane at the wet surface for longevity without fear of corrosion, it employs a double sealed joint which can be guaranteed not to leak and the system is engineered to maximise the potential of each and every installation whether it be in conjunction with roof replacement or over sheeting or just to re-line the existing gutter.
It is very often a practical and cost effective solution to consider lining an existing gutter and Unifold® offers exceptional life expectancy and corresponding joint integrity, often far better than the original gutter and following design consideration can often actually increase existing gutter capacity, enlarge outlet orifices and introduce additional outlets with relative ease.
Whenever possible gutters are surveyed by Ampteam personnel. The company actively encourages
contractors to use its survey services and this is available throughout the UK and each Unifold solution is designed to provide the client, the building occupier, with the best possible solution and on occasions this will result in an improvement in performance to the original gutter.
Unifold® is provided with full technical support from advice at the inception of an enquiry through to installation and beyond. Our countywide network of fully trained approved contractors are available to install and provide maintenance inspections and cleaning when required.
Unifold® is installed by approved contractors whose installation teams have been fully trained by Ampteam personnel in house at our training facility and following installation, by an approved contractor, the gutter lining is guaranteed for a period of 30 years.
www.gutterliners.com
The NORD DRIVESYSTEMS’ drive solutions promise high energy efficiency and low Total Cost of Ownership (TCO). NORD asynchronous motors in endof-line packaging can achieve cost benefits of up to 50% when packaging food and beverages. Centrally controlled servo motors are usually used in this context.
In contrast, controlled asynchronous motors from NORD are an efficient and economical alternative. When used with decentralised frequency inverters like the NORDAC ON, components such as control cabinets and the effort for wiring and installation are significantly reduced.
If a control cabinet is required, the NORDAC PRO SK 500P is recommended as its power range of up to 22 kW is ideal for the industry.
NORD asynchronous motors in end-of-line packaging can achieve cost benefits of up to 50% when packaging food and beverages.
NORD also offers suitable solutions for further processing stages of food and beverages. The NORD IE5+ synchronous motor impresses with maximum energy efficiency and exceeds the previously defined efficiency classes. Since the permanent magnet synchronous motor achieves its constant torque over a wide speed range, it enables a reduction of drive variants in a complete system. This reduces the administrative costs and therefore the TCO.
Decentralised asynchronous drives provide decisive advantages in the endofline packaging of food and beverages.
The patented DuoDrive geared motor from NORD is available with powers of up to 3 kW
The DuoDrive was specially optimised for the requirements of the food industry. An IE5+ motor is integrated into a helical gear unit with this patented gear unit/ motor combination. This not only achieves high system efficiency. Fewer wearing parts and reduced maintenance effort also enable further positive cost effects.
NORD DRIVESYSTEMS will present these and more drive solutions from 19 to 22 March 2024 at Anuga FoodTec in Cologne. You will find the company at Stand A010 in Hall 7.1.
www.nord.com
The wheat adhesive experts will share their knowledge on concepts to improve production efficiency in the corrugated industry
At Latam CORR, a fair for corrugated board manufacturers and suppliers in Mexico from 12 to 14 June, visitors can learn how C&D Corrugating & Paper can help optimize production processes. As demand for environmentally friendly adhesives for the packaging industry continues to grow, the adhesive experts can help manufacturers become more resource efficient and cost effective.
As part of the Crespel & Deiters Group, C&D Corrugating & Paper uses the renewable raw material wheat to create adhesive concepts for the packaging industry. Thanks to the recent establishment of a subsidiary in Mexico, the company is able to supply and support customers in Latin America.
Low-cost, high-quality and less waste
Packaging solutions such as the wheat-based adhesives from C&D Corrugating & Paper offer huge benefits for production processes: Optimal composition leads to a reduction in energy costs and adhesive usage.
This not only leads to material savings but also less waste. Moreover, by utilizing a high performance adhesive, corrugated manufacturers can improve efficiency and enhance the quality of corrugated boards.
Adrian Beckett, Head of International Sales C&D Corrugating & Paper, explains: “Our mission is to empower manufacturers to establish a cost-effective and resourceefficient production with adhesive solutions from wheat. We’re looking forward to attending Latam CORR in order to increase our visibility and reach in the Latin American market.”
www.crespeldeitersgroup.com
Optimal composition leads to a reduction in energy costs and adhesive usage.
With the rapid increase of energy costs, businesses are looking at reducing their electricity usage while maintaining comfortable and compliant conditions for products and staff. EcoCooling offers a costeffective cooling solution for food storage and processing facilities. With blanket or spot cooling options available, evaporative cooling offers a flexible approach to process or people cooling that can be easily retrofitted to the majority of buildings.
Evaporative cooling adds humidity to the air, which can be beneficial to some food storage environments such as bakeries, wine and chocolate producers, cereal manufacturers and more, with some of the leading UK brands utilising our equipment for the processing or packing facilities, including Subway, Hotel Chocolate, Premier Foods, Greggs.
The most energy efficient cooling system for large spaces
Even on the hottest days, a standard unit covering a 250m2 area or spot cooling a 15m diameter zone can operate at a cost less than 13p in electricity and 1p in water per hour, based on service costs of £0.12/ kWhr and £1.20/cum respectively (2021 figures). This gives an energy saving of 90% on an equivalent refrigeration-based system with a 35kW cooling load.hhh
Evaporative cooling is extremely beneficial in a bakery environment. The humidity levels keep the bread fresh and don’t dry it out, unlike traditional air conditioning which is extremely dry and can often shorten the lifecycle of fresh produce, so it is highly effective for bakery cooling.
Premier foods were looking for a cost-effective bakery cooling strategy for their Barnsley site. Evaporative cooling can guarantee cool supply air of below 25°C all year round in the UK, making it the perfect solution for those wanting to reduce temperatures in their bakeries. 12 down discharge EcoCoolers were supplied and fitted to 12 existing Air Handling Units (AHU’s) on the roof of Manor Bakeries,
Barnsley to provide cooling for the bakery. The existing refrigeration based cooling system has been decommissioned and the packaging area is now solely cooled using the EcoCooling Evaporative cooling system.
Following commissioning the system was tested and monitored, the following performance figures were recorded for the facility:
EXTERNAL AMBIENT = 23°C (WARM SUNNY CLEAR DAY)
AIR TEMP OFF COOLER = 16.6°C
AIR VOLUME THROUGH COOLER = 4.47M3/S
PRESENT COOLING CAPACITY = 34KW PER COOLER
TOTAL SYSTEM CAPACITY = 12
COOLERS X 34KW = 408 KW
www.ecocolling.co.uk
• Runs at less than 10%
• Runs at less than 10% energy consumption compared to air con
•
• Increase productivity, hygiene and condition compliance
•
• No harmful refrigerants - only 100% fresh air
•
• Avoids air recirculation - improves air quality/reduces smells
• Energy Efficient Natural Cooling - decreases carbon footprint
• New build and retrofit with solutions to fit a range of applications
EcoCooling: the established leaders in evaporative cooling
UK-based with over 3500 installations worldwide; with clients including BT, Marks & Spencer, Herman Miller, Cummins Diesel, Premier Foods, Net-a-Porter and Cambridge University. Case studies online!
Industrial Cooling: Provides 35kW of cooling for only 1.5kW of electricty. 14,000m3/hr of cool air for less than 12p per hour. ROI in under 3 years.
Large UK wide network of installers ready to quote on a solution to fit your needs.
Schubert, an acknowledged innovation leader in the packaging industry, is continuously developing its state-of-the-art top-loading packaging machines. To ensure that customers and employees are always up to date with the latest technology, the company offers regular training courses at its Training Centre, which opened its doors just under a year and a half ago. The demand for these courses is high and Schubert has now invested in a new training machine so that it can continue to meet this demand.
Schubert opened the new Training Centre at its main site in Crailsheim at the end of 2022. And a great deal has been achieved since then. The existing training portfolio was scrutinised and revised in view of responding even better to the specific requirements of customers and employees. In doing so, Schubert developed new formats and content and designed a series of online training courses in addition to the face-to-face courses.
is currently
platform. Personnel capacities have also been increased to enable the far-reaching program to be run continuously. What was lacking, however, was a new training machine. Sarah Busch, Head of Customer Training at Gerhard Schubert, explains:
“Our training concept is based on a well-balanced mix of traditional and digital learning content. Interactive courses and explanatory videos are a great way of understanding and familiarising yourself with certain topics, but some subjects are easier to learn
Our
training concept
is based on a wellbalanced mix of traditional and digital learning content.
when you are standing right at the machine with a trainer and a small team, and you have the opportunity to get hands-on and try things out. As our previous training machines were always fully booked, we decided to invest in a further model.”
From format changeover to troubleshooting – learning on the current model
Typical exercises that are carried out on the new and previous packaging machines include standard activities such as referencing the robots, selecting new programs on the control panel, as well as relevant checks, maintenance, recognising and rectifying error messages and troubleshooting. The training also covers the various system components of the training machine, which is at the cutting edge of technology. From the Transmodul to the F2 and T5
robots to the 3D scanner, the aim is to build up important knowledge. Sarah Busch adds: “The training courses are very popular with both our employees and customers. With our new training machine, we can expand our capacities and offer significantly
more training courses. Our customers and employees benefit from a practical training experience, which ultimately benefits everyone in their day-today work.”
www.schubert.group
Looking forward to meeting the huge demand for training even better in the future with the new training machine: Mario Müller, Training Developer and Thomas
Crafted with precision and infused with cutting-edge technology, Bizerba’s inspection systems are poised to revolutionize how industries monitor and uphold product quality. These systems boast a comprehensive array of features meticulously designed to detect even the most minuscule deviations, ensuring impeccable standards for safeguarding against potential defects and discrepancies. From regulatory compliance to operational efficiency enhancement, Bizerba’s inspection systems deliver a multitude of benefits.
At the core of Bizerba’s latest range lies a fusion of advanced sensors, artificial intelligence, and machine learning algorithms. This powerful synergy enables the systems to conduct thorough inspections with unmatched accuracy and speed, transcending traditional quality control paradigms. Whether it’s identifying irregularities in packaging, detecting contaminants, or assessing product integrity, Bizerba’s solutions provide meticulous scrutiny at every stage of the production process.
Moreover, Bizerba’s inspection systems are renowned for their versatility and adaptability, seamlessly catering to diverse industry requirements with customizable functionalities and seamless integration. Whether deployed in food processing, pharmaceuticals, or manufacturing, these systems embody a universal
Beyond their technical prowess, Bizerba’s inspection systems exemplify a customer-centric ethos, underpinned by responsive support services and intuitive user interfaces.
commitment to elevating quality standards and fostering consumer confidence.
Beyond their technical prowess, Bizerba’s inspection systems exemplify a customer-centric ethos, supported by responsive support services and intuitive user interfaces. Prioritizing user experience and accessibility, Bizerba ensures that its solutions empower operators to harness the full potential of these innovative technologies, thereby maximizing productivity and minimizing downtime.
In an era where regulatory landscapes grow increasingly complex and consumer expectations evolve, robust quality control measures are paramount. Enter Bizerba’s new range of inspection systems, a timely and transformative development
poised to set new benchmarks for excellence in quality assurance.
In essence, Bizerba’s unwavering commitment to innovation, coupled with its dedication to enhancing product quality, epitomizes a vision of progress resonating across industries. With its latest inspection systems, Bizerba reaffirms its position as the trusted partner in the pursuit of uncompromising quality and operational excellence.
Experience the future of quality control with Bizerba!
www.bizerba.com
X-ray inspection systems
Detect various foreign objects and verify the quantity and integrity of your products in food production.
Metal detection systems
Identify contaminants within your products, including steel, stainless steel, and non-ferrous metals such as aluminum.
Bizerba (UK) Ltd
T +44 (0)1908 682740
info@bizerba.co.uk
bizerba.com
Please contact us for more information
Vision inspection systems
Discover comprehensive solutions to assure the quality of your products and their packaging.
Dynamic Checkweighers
Guarantee the quality of your packaged or unpacked goods through precise weighing results.
Systems integrator, Technidrive has partnered with OMB Vibrator Motors, a leading European manufacturer of electric vibrating motors. As OMB’s first and only UK distribution partner, Technidrive provides a new route to market for the Italian equipment manufacturer. The motors become part of Technidrive’s growing roster of industrial equipment for its bespoke drive train packages.
OMB has specialised in designing and manufacturing electric, hydraulic and pneumatic vibrators for industrial motors for 45 years. Manufacturing a range of vibrating motors in electric, hydraulic and pneumatic, specifically designed for integration into industrial machines such as screens, feeders, extractors, separators, hoppers, compactors and more.
Vibrating motors span various industries, playing a predominant role in material handling and screening. In the material handling sector, vibrating motors power screens to separate products based on particle sizes. These applications are prevalent in the food, beverage, pharmaceutical, plastics and chemicals industry.
OMB tailors its motor designs to meet specific requirements of each industry. For instance, the foot-mounted vibrating BM series is manufactured in accordance with IEC 60034-1 and EU Directives including Machinery 2006/42/EC,
Vibrating motors span various industries, playing a predominant role in material handling and screening.
RoHS 2011/65/EU and more. The series also has options suitable for conformance with ATEX directives for operation in explosive atmospheres. The BM-E series also holds UKCA certifications for products to be used in Great Britain.
“Partnering with OMB adds further depth to our solutions as a leading drive systems integrator. The high level of technical support from OMB’s factory, married with our technical expertise in industrial drive systems will positively impact our customers,” explained Andrew Ritchie, technical sales manager at Technidrive. “Technidrive already has an established market presence with many global OEM’s and end user sectors using vibrating technologies. This partnership is a logical next step to bring quality and bespoke integrated solutions to a wider audience”.
The partnership comes during an exciting period of growth for Technidrive. The Northern Irelandbased systems integrator has recently celebrated its 25-year anniversary and was named as a Silver Level Innovator by Innovate NI. This was awarded as recognition for its work creating, testing, developing and validating solutions for industry.
“As a new part of our product line up, OMB Vibrator Motors will support our efforts to strengthen equipment supply for our customers,” continued Ritchie. “Back in 2022, we invested significantly in our space by adding a mezzanine floor, additional warehouse racking and new technology to maximise our storage capacity for equipment from partners old and new.”
Visit Technidrive’s website to discover how OMB vibrating motors can benefit your business.
Global manufacturer of motors and drives, WEG will exhibit at the first edition of Food Manufacturing Live taking place at the National Motorcycle Museum, Birmingham, on May 1, 2024. Among the products displayed at stand 38 is the CFW900 variable speed drive (VSD) and the WG20 geared motor, both specifically tailored to meet the demands of the food and beverage industries.
Food Manufacturing Live is poised to emerge as the UK’s specialist technical event for the food and drink manufacturing industries, where engineers can explore and showcase the latest technological innovations and equipment developments. The exhibition will focus on digital transformation and energy efficiency, providing a unique opportunity for industry to network and stay ahead of the trends that define modern food processing.
WEG is ready to unveil its newest solutions aimed to enhance efficiency in the food processing sector. Among the key demonstrations will be the versatile gearbox, WG20. These helical gear units come in twelve housing sizes for nominal torques from 440 to 159,000 lb-in and are available in both foot and flange designs. Primarily used for packaging machines, bakery equipment and conveyor belts, the WG20 comes in three different models: helical, parallel shaft and helical bevel.
The team will also display the CFW900 VSD. This highperformance VSD has a simplified design, increased power density and ease-of-use that allows the user to access configurations and technical data in a fast and simple way. It comes with an advanced
energy saving function, high operating range, safety functions and features for improving productivity.
“Food Manufacturing Live is great opportunity to showcase our highefficient solutions to a wide range of food sector professionals”, explained Marek Lukaszczyk, marketing manager for Europe and the Middle East at WEG. “In food processing, the adoption of energy-efficient equipment is key to achieve economic and environmental goals.”
WEG will also provide technical information on its new W23 Sync+ hybrid motor, a recently launched line that combines permanent magnet and switch reluctance technologies. The W23 Sync+ has an efficiency rating of IE5 and the W23 Sync+ ULTRA boasts an IE6 rating, with both types having increased power factors.
WEG will also feature other solutions suitable for the food sector, such as the ADVP200SP. This drive converts electrical energy supplied by a PV panel into mechanical energy, which is consequently converted into hydraulic energy by the pump.
Finally, WEG will highlight its remote monitoring system, Motion Fleet Management (MFM), which enables engineers to monitor the performance of industrial assets. The system can be used in food manufacturing networks to provide predictive maintenance and identify faults, avoiding stops in the production line and therefore improving throughput.
“Our products are designed to enhance and improve the efficiency of food and drink production. For instance, the CW900 VSD can adjust the speed of a conveyor system,” explained Lukaszczyk. “Another example is the W23 Sync+ ULTRA, which, compared to conventional induction motors, experiences minimal efficiency loss. It demonstrates a decrease of less than two percent when load and speed are reduced by 25 percent”.
If you need more information on the products mentioned, visit the website. To arrange a meeting with WEG at the Food Manufacturing Live show, please send an email to: info-uk@weg. net.
Food recalls due to allergen mislabelling are still very common in the UK. Food Standard Agency data shows that 314 allergy alerts were issued in the reporting period for 2022/23.
The consequence of food recalls not only leads to tragic loss of life, but also causes serious damage to the brand’s financial health. Pret a Manger set aside £10m to cover legal costs after Natasha EdnanLaperouse died from consuming mislabelled baguettes in 2016 and Celia Marsh suffered from a fatal reaction to a ‘vegan’ wrap in 2017.
Whilst efforts are made to ensure allergens are properly labelled, some food and drink manufacturers are not fully aware of the allergen labelling guidance. Some choose not to invest further and instead opt to ‘hope for the best’. Others have integrated ineffective solutions, such as print rooms.
Print rooms cannot be solely responsible for ensuring that products are accurately labelled (that the right label goes on the right product), as workers may overlook allergens or ingredients. Besides, the print rooms may not have access to all the necessary information.
From raw materials to finished products, it’s the manufacturers’ responsibility to ensure allergen control and provide clear and safe products to retailers and consumers. Allergen control must include, but is not restricted to:
• Supplier verification: Verify that suppliers provide accurate information about allergens present in their ingredients and adhere to appropriate safety standards.
• Allergen testing: Implement regular testing of both ingredients and finished products to verify the absence of allergens and detect any
Whilst efforts are made to ensure allergens are properly labelled, some food and drink manufacturers are not fully aware of the allergen labelling guidance.
contamination. This can include laboratory testing as well as on-site testing methods such as swabbing for the presence of allergens.
• Accurate labelling: Review and improve their labelling and inspection procedures regarding allergen declarations to ensure clear and accurate labelling of all known allergen ingredients.
Harford Autocoding Solutions help manufacturers ensure 100% verification of packaging accuracy, to avoid inaccurate label information and unnecessary wastage. The solutions can be integrated into production lines to send real-time actionable data directly to those who need it. At the start of each production run, the system will ensure that label
printers are set up accurately and in-line barcode scanners are configured to check that the correct packaging materials and labels are used – on each individual product, case or pallet. In some instances, on-line integrated cameras may also be required to ensure that the pre-printed packaging displays the correctly highlighted allergens.
Though this is a huge, essential step towards ensuring compliance, it must also be said that no automated system can ever guarantee total compliance, and full training and operator engagement are also essential to provide world class due diligence.
Harford have enormous experience in helping food and drink manufacturers ensure greater accuracy of labelling for control of allergens, date coding, quality and much more. If you are ready to eliminate risk and improve labelling accuracy using Harford Autocoding, please reach out to us at info@harfordcontrol. com or give us a call on +44 (0)1225 764461.
www.harfordcontrol.com
Features
Accurate Date Coding
Send real-time actionable information directly to those who need it.
Allergen Control
Harford Autocoding Solutions use
accurate date coding setup, label verification and in-line barcode scanner configuration to prevent non-conformances, reduce changeover times, minimise the risk of human errors and decrease the cost of manufacturing.
Ensure allergen information on each package and outer case is accurately labelled.
Batch Control
Efficiently automate coding processes with streamlined batch control capabilities. Auto Lab Triggers
Automatically initiate certain actions based on predefined triggers.
The landscape of food trends is in a constant state of evolution, driven by shifts in consumer attitudes, economic fluctuations, and consequential events both on a national and global scale.
Over the past few months, numerous factors have had an impact on the food and beverage scene including the ongoing costof-living crisis, a continued focus on sustainability, and growing health concerns.
These have caused new trends to develop, existing ‘historical’ trends to fade and others to continue developing, becoming a more integral part of the industry.
Ian Hart, business development director at adi Projects, a division of multi-disciplined UK engineering firm adi Group, discusses the trends developing in the food and drinks industry in 2024 and their impact on the sector.
Picking up from last year, a notable trend in the food and beverage industry in 2024 is the increasing shift towards less processed foods and a greater emphasis on raw ingredients.
Consumers are showing a growing interest in wholesome, minimally processed options, driven by a desire for healthier choices and a deeper understanding of the nutritional value of their food.
This trend aligns with a broader movement towards clean eating and a focus on the origins of ingredients. This shift also reflects a commitment to authenticity and sustainability, and a consumer preference for fresh and unadulterated food experiences. Food and beverage companies are responding by reevaluating their product formulations, opting
As consumers become more health-conscious, there is a growing demand for food options that align with fitness and wellness goals.
for simpler, more transparent ingredient lists.
Consumers are increasingly prioritising ethical and sustainable choices, prompting a shift towards products that demonstrate a commitment to responsible sourcing practices. From ingredients cultivated with environmentally friendly methods to ethically produced goods that support fair labour practices, consumers are seeking transparency in the supply chain.
This trend reflects a heightened awareness of the environmental and social impact of consumption, as individuals actively seek products that align with their values.
As companies embrace sustainability, responsibly sourced offerings are not only meeting consumer expectations but also driving positive change throughout the industry, fostering a more conscientious and sustainable
approach to food and beverage production.
In 2024, we are likely to continue to experience a continued rise of meal kit services such as HelloFresh and Gousto. These ‘recipe boxes’, which supply preportioned ingredients along with chef-curated recipes directly to consumers’ doorsteps, have gained immense popularity.
This trend is indicative of a shift in consumer behaviour towards athome cooking experiences without the hassle of grocery shopping, guaranteeing convenience and variety.
As the industry embraces this model, it not only addresses the demand for time-saving solutions but also reflects a dynamic response to evolving consumer preferences for personalised, chefquality meals in the comfort of one’s home.
Despite the unquestionable popularity of vegetarianism and veganism in the past few years, with nearly one quarter of all food products launched in 2019 being labelled vegan, sales began to stagnate in the past two years.
Sales of meat alternatives were down 13.6% in 2022, with UK supermarkets Tesco, Asda, Sainsbury’s and Morrisons cutting their vegan ranges by 10 per cent, according to The Grocer.
There is likely to be a continued decline in demand for vegetarian and vegan options through 2024, and a primary driver is likely to be concerns over plant-based food being ultra processed, in tandem with a shift towards clean eating and minimally processed options.
As consumers become more costconscious, with 6 in 10 adults in Great Britain spending less on nonessentials due to increases in the cost of living, there is a discernible shift towards seeking affordable alternatives.
However, consumers lean towards alternatives that still align with ethical and health considerations, without compromising on quality. Companies are adapting by introducing a range of valueoriented offerings, recognising the importance of accessibility in providing affordable and satisfying food choices.
The increasing popularity of highprotein and low-sugar products is going to be a prominent part of the 2024 food and beverage landscape.
As consumers become more health-conscious, there is a growing demand for food options that align with fitness and wellness goals. High-protein products cater to those seeking muscle support, weight management, and sustained energy levels, while lowsugar options respond to concerns about excessive sugar intake and its impact on overall health.
This trend reflects a broader shift towards balanced nutrition and a desire for transparent ingredient
lists. Food and beverage companies are responding by innovating and reformulating products to meet these criteria, catering to the consumer quest for healthier choices.
Fuelled by a growing interest in gut health and the proven benefits of probiotics, consumers are increasingly seeking out fermented options. Fermentation is being embraced for its natural preservation methods and its ability to enhance the nutritional profile of foods. From kimchi and sauerkraut to kombucha and kefir, these products not only offer unique and bold flavours but also boast digestive health benefits.
Functional drinks and snacks are designed to offer more than just sustenance, and are gaining popularity for their purported positive effects on the body. From beverages claiming to enhance sports performance to snacks promoting relaxation of the body and mind, consumers are increasingly seeking functional options that align with their specific health and wellness goals.
With an emphasis on ingredients known for their potential benefits, such as adaptogens, nootropics, and performance-enhancing compounds, the industry is
witnessing a shift towards holistic and purpose-driven consumption.
SKU rationalisation
SKU rationalisation is now a leading trend in the industry. Faced with increasing complexities in supply chains, market dynamics, and consumer preferences, businesses are recognising the need to streamline their product portfolios.
By focusing on the most profitable and high-demand items, businesses can enhance operational efficiency, reduce costs, and better meet the evolving needs of consumers. This showcases a proactive approach to adaptability in an ever-changing market, enabling companies to maintain competitiveness and sustainability.
How can manufacturers cater to these fast-growing trends?
To adapt to these emerging trends, devising new strategies and ways of operating is paramount. Catering to health-conscious consumers should be a priority, meaning that looking into creating high-protein, low-sugar ranges as well as functional products is key.
Wherever possible, manufacturers should seek to reformulate their products to feature simpler, transparent ingredient lists, emphasising authenticity and nutritional value.
adi Group can help manufacturers through this journey, assisting in the design and development of specialised production lines and equipment as well as the optimisation of manufacturing processes.
With access to a number of expert divisions, adi Group can help manufacturers leverage new technologies through innovative turnkey solutions to streamline production processes and improve efficiency, enabling them to meet the growing demand for highquality, sustainable food products at scale, enhance traceability and quality control and more.
Following successful feasibility trials at GADDS’ Ramsgate Brewery, SEB Brewing & Packaging is pushing ahead with the installation of a full CO2 recovery system. The technology is designed to capture the CO2 generated by the brewery fermentations, clean, compress and liquify it, rendering it fit for use in carbonating beers and running the filling machines. The results from the feasibility study show the process to be robust, producing liquid CO2 of unparalleled purity, with measured oxygen content of below 15 parts per billion (our wholesale supplied CO2 is around 30 ppb).
The project fits into a wider initiative to hit net zero on site by 2030 and is expected to make double digit reductions in emissions, giving SEB a kick start in their journey. The company’s scope 1 emissions are primarily natural gas (used in the brewery), and CO2 evolved from fermentation, the latter making up around a third of the total. SEB’s target is to recover 75% of this evolved CO2 by the end of the year.
Stage 3 of the project is the installation of CO2 recovery systems in founder breweries, utilising existing transport routes to supply SEB with as much gas as it needs to become fully self-sufficient. In doing so, 65 tonnes a year of direct CO2 emissions will be captured and reused, and 90 tonnes will be removed from the wholesale market.
CO2 capture technology has been used in the brewing industry for over 40 years at breweries producing over 150,000 HL a year. It’s only in the past year that this technology has been scaled down to be fit for use by craft brewers, and SEB (with GADDS’) is the first company in the UK to take the plunge.
Enzymes have the potential to be used multiple times over, at ambient temperatures, and represent no risk to personnel, product, or the environment.
Alongside CO2 capture, SEB is looking at other ways to reduce their environmental impact including a reduction in chemical usage.
Brewery and packaging cleaning cycles traditionally employ caustic based chemicals diluted in very hot water. With enough heat, and enough chemical action, soil (mainly proteins and starches) is loosened and then removed from surfaces, leaving them ready for sanitation. The heat and the chemical use is an expensive drain on resources, and the processes must be carried out with great care to avoid personal injury. The used fluid must then be neutralised prior to discharge.
However, recent innovations in enzyme technology is on the verge of revolutionising cleaning
in the brewing industry, and SEB is positioning itself in the vanguard, helping suppliers trial new products. Enzymes have the potential to be used multiple times over, at ambient temperatures, and represent no risk to personnel, product, or the environment. Trials so far have shown the technology to be very promising and the aim is to replace all caustic on site with enzymes during Q2.
Significant challenges are likely along SEB’s journeys towards net zero, but the company is making early (and serious) headway, building problem solving skills and momentum by backing technological solutions only newly available to the industry. The direction of travel is set for all of us, and SEB is happy to take the lead.
www.sebpackaging.co.uk
Gellert freeze dryers are the perfect solution for manufacturers looking for a reliable and scalable option for regulated food production. With a notable shift towards the freezedried product market, manufacturers and consumers alike are recognizing the benefits of this process. By reducing, or removing, the need for cold chain handling, manufacturers can reduce transportation and storage costs, and as freeze-dried material is much lighter than frozen or refrigerated product, this further lowers costs. Additionally, freeze dried products not only take less energy and cost to store, but they also maintain the biological benefits and flavours of the raw product whilst extending shelf life.
Gellert freeze dryers offer a controlled and repeatable manner for in-situ freeze drying directly on the shelves, ensuring the product maintains its shape, structure, and nutritional value. Gellert has developed a range of freeze dryers with ease of scale-up, user requirements, and operation in mind, making them versatile and popular in the industry.
Some of the beneficial features of Gellert equipment include AutoDry, an intuitive feature that allows users to input their desired temperature differential between the product, sample, and shelves, ensuring the sample can be dried using the AutoDry feedback mechanism,
freeze dried products not only take less energy and cost to store, but they also maintain the biological benefits and flavours of the raw product whilst extending shelf life.
optimizing drying cycles. The chamber, condenser, shelves, and shelf stack can all be constructed from 316L stainless steel for product contact, and a hybrid cooling system is also available on larger equipment, to utilize defrost water by re-heating via the freeze dryer compressors, saving energy and costs.
The most common applications that Gellert’s freeze dryers are used for include: -
• smart foods e.g., supplements and nutraceuticals
• food and beverages
• dairy products
• fruits and vegetables
• pet food and pet treats
All Gellert systems are manufactured in Europe and strictly adhere to compliance regulations such as F-gas.
Biopharma Group is the exclusive distributor of Gellert freeze dryers across the UK, Ireland, and France. Both Biopharma Group and Gellert are well respected and renowned companies, combining years of lyo industry experience. This winning combination allows the Biopharma Group team to help you select the best freeze dryer to meet your specific need and Gellert has accrued a high level of practical experience and in-house expertise, developing an array of different models and configurations to satisfy a broad range of food production purposes.
Contact Biopharma Group’s product specialists to discuss your requirements or request more information.
www.biopharma.co.uk
Fluid Type
Clean and semi clean liquids
Applicable Liquids
Features
Hygienic Tri Clamp & RJT connections
Solid stainless-steel construction 316
Electro-polish optional finish
Low pressure steam clean
Accurate, Long-term Reliability
Easy to Clean & Maintain
Excellent Repeatability
Easy to Install
Durable
Water, Oils, Beer, Foodstuffs Calibration Available