FOOD & DRINK PROCESSING & PACKAGING
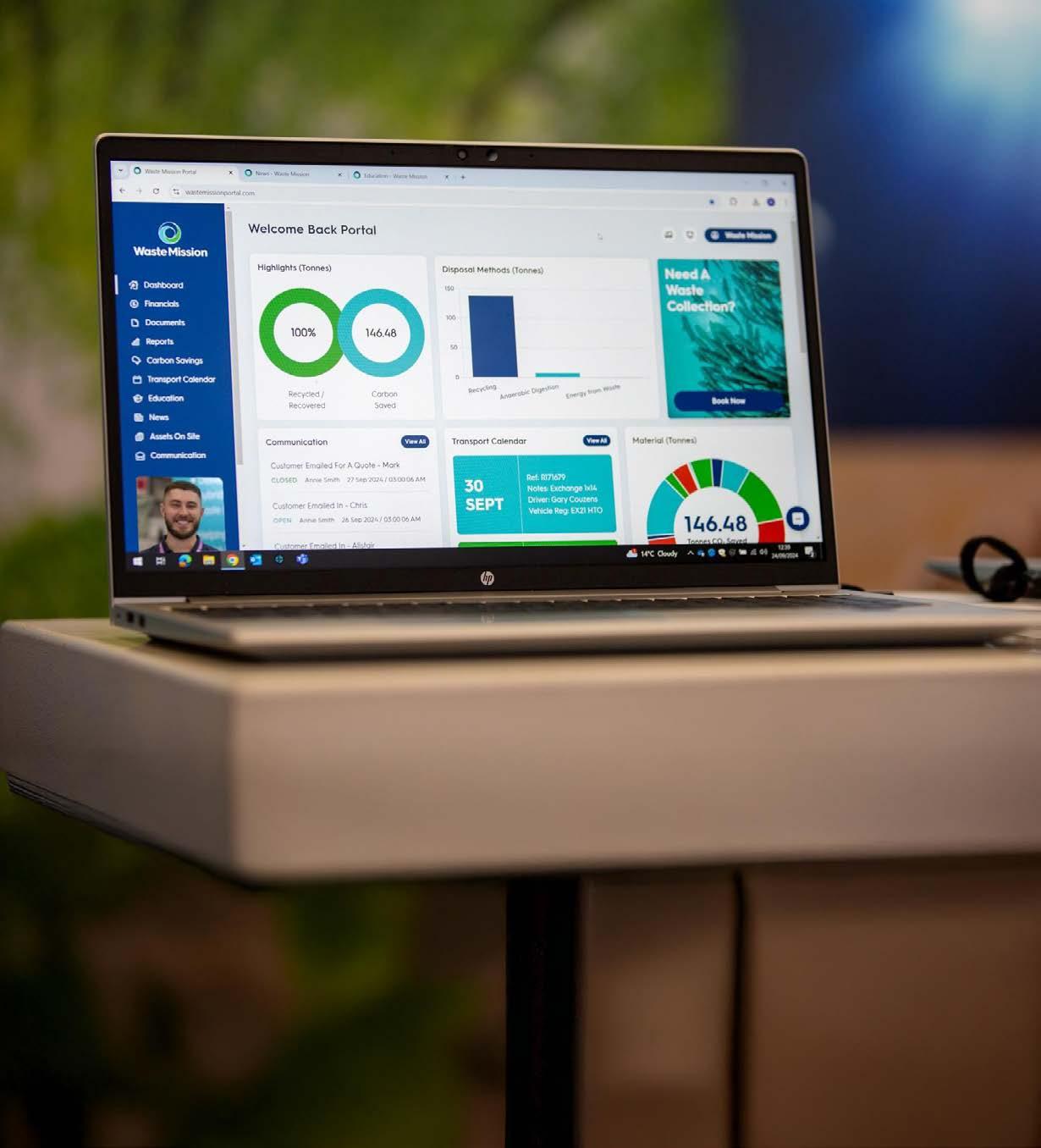
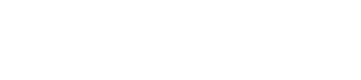
Making sustainability simple ... building a future a few shades greener
Waste Mission Achieves 100% Diversion of Food Waste from Landfill for Inspired Pet Nutrition
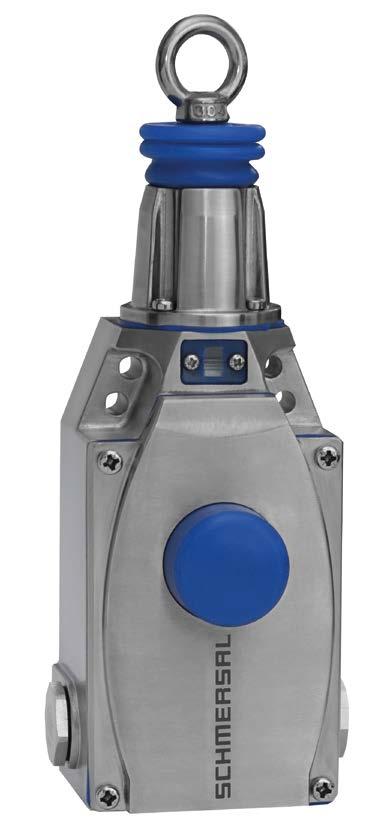
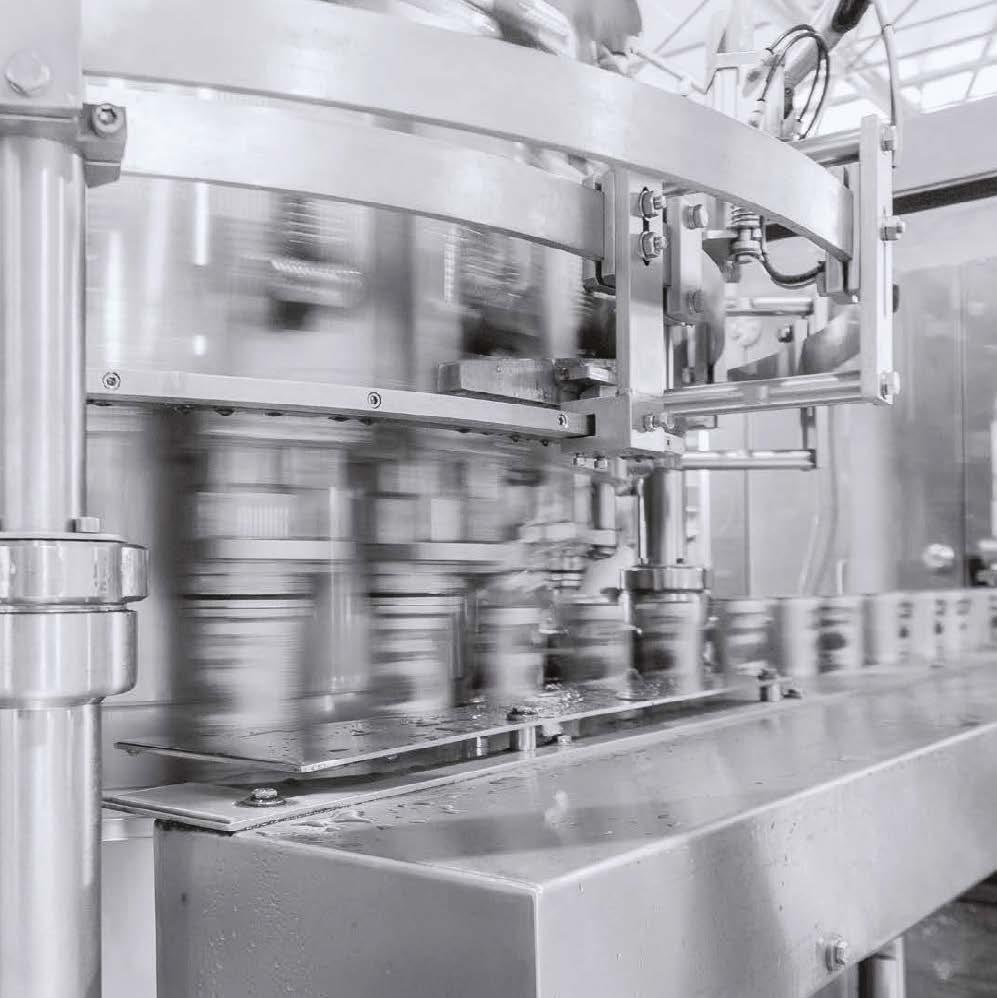
Making sustainability simple ... building a future a few shades greener
Waste Mission Achieves 100% Diversion of Food Waste from Landfill for Inspired Pet Nutrition
The new ZQ901 pull-wire emergency stop switch by Schmersal is characterised by its robust stainless steel enclosure. It offers optimal mechanical and chemical protection in harsh environments and provides the ideal solution for a wide range of applications.
Thanks to the new housing material, the ZQ901 can be used on transport and material handling systems as well as on large system used in the food processing and chemicals industries. The tried-and-tested technology, used in industrial settings, meets the highest availability standards. The ZQ901 offers an emergency-stop function and manual rest, wire break detection and lengths of wire up to 75 metres.
For more information, scan the QR code to download your free brochure.
SCHMERSAL | Enigma Business Park
www.schmersal.co.uk
uksupport@schmersal.com
Editor Amanda Buckingham editor@fdpp.co.uk
Business Manager Josh Holmes josh@mhmagazine.co.uk
Publishing Director Martin Holmes martin@fdpp.co.uk
Digital Sales Manager Jessica Bennett T: 01227 392571
Sales Manager Jamie Bullock jamie@fdpp.co.uk Tel: 01227 392571
Studio Designer Leila Schmitz leila@mhmagazine.co.uk
M H Media Global Ltd. 18/20 Newington Road, Ramsgate Kent, CT12 6EE Tel 01304 806039 www.fdpp.co.uk
All web addresses are interactive, simply click the web address of your choice to view the company website. There is also a
tool bar where you can search for a
Please mention FDPP when responding to items in this
BETHLEHEM, PA—A new TIP-TITE®
Mobile Drum Dumper with integral flexible screw conveyor is designed for use in hazardous locations.
It allows volumetric feeding of bulk material from drums into downstream processes dust free and with minimal operator intervention. The system is mounted on a mobile frame with quick-action floor jacks for stable operation anywhere in the plant.
The hydraulic power unit used to lift, seal and tip the drums is powered pneumatically, eliminating the risk of potential sparks from electrical or other equipment that might otherwise be used to actuate the hydraulics. As an additional safeguard, the controls for the flexible screw conveyor are mounted on extended support brackets, placing them outside of the hazardous zone.
The unit accommodates drums from 30 to 55 gal (115 to 200 liters) and measuring 36 to 48 in. (91 to 122 cm) in height. After the drum is placed in the lifting carriage, the carriage is raised against a rubber gasket mounted inside the discharge cone, creating a dust tight seal. The entire apparatus is then tipped, with a motion-dampening feature stopping the process when the predetermined dump angle is reached.
The material exits the discharge cone and into the charging adapter of the flexible screw conveyor. Fully enclosed inside polymer or steel tubing, the inner screw of the conveyor is the only moving part contacting material, resulting in reduced maintenance and increased reliability. As the screw rotates, it self-centers within the tube, providing ample clearance between the screw and the tube wall to
The hydraulic power unit used to lift, seal and tip the drums is powered pneumatically, eliminating the risk of potential sparks from electrical or other equipment that might otherwise be used to actuate the hydraulics.
eliminate or minimize grinding. The drive motor is located beyond the point at which the material exits the conveyor, preventing contact with bearings or seals.
It can be rolled into storage when not in use, or to a designated area for cleaning during material changeovers. The system is available constructed of carbon steel with durable industrial finishes, with material contact surfaces of stainless steel, or in all-stainless steel finished to food, dairy, or pharmaceutical standards. A broad range of screws with specialized geometries is available to handle free- and nonfree-flowing materials, including products that pack, cake or smear in other types of conveyors.
sales@flexicon.co.uk www.flexicon.com
Dual PEF Pilot to sanitize juices or to extract juices or colours from haard vegetative cells of grass, roots, etc.
The PEF pilot on the left provides a high-in-demand dual capability by 3 sets of processing chambers
• coaxial PEF chamber for liquids with changeable gaps,
• colinear PEF chamber to form volume discharges in juices.
• 12L batch volume with controlled juice heating/cooling,
• flat PEF chamber with 14cm round ground and HV electrodes and a variable gap between both of 0.5-3cm.
and broad fixed & gradually changed pulsing:
• positive rectangular pulses 2,5-50µs at 4Hz to 500Hz;
• el. fields 5-65kV/cm by our 25kV 2kW pulser;
• pulsing time 1s-1h,
• convenient LED lighted control panel.
Please click on its photo to get its pdf brochure.
The brochure of its small table-top version is here
PEF sterilizes juices by 1 of 2 different processes: 1: by electrical stretching bacteria only up to its ruptures or 2: by creating volume el. discharges in a co-liner chamber where free electrons destroy both bacteria and spores. Details:
Select from the list of our versatile pilot and table-top R&D systems to be customized to your objectives from the full list here:
Our PL bench-top systems were used at many R&D labs and cited in various industrial and peer-reviewed publications.
< the automatic & analogue > now are discounted along with its spare UV flash lamps.
The effectiveness of IPL increases with its pulse power & its UV content to the point where bacteria & spores are fully physically disintegrated.
IPL fully sterilises clear liquids in transparent packs as it was proven on our IPL system by the Baxter Corp. (US) with UV resistant spores of B. Pumilos.
We offer to sell all know-how information on our PEF and PUV pilots plus on already sold or just developed UV tunnels.
Please click on images to find more or inquire at https://www.wek-tec.de
This Vortex batch pilot to sanitize powders. Results from this Vortex can be used to construct our already designed flow- through system for photo-chemical processing of up to 100kg/hour powder.
R&D Vortex can effectively modify organic powders by UV Example: D2 vitamin enriching in mushroom powders with its partial sanitation by moving treated powders around a UV (PL) lamp by a Nitrogen enriched air flow to exclude oxidation.
We were first to publish in 1991-2001 on mechanisms of PL sterilization/purification.
Fox Venturi Eductors, for blending powders into liquids – have been used in food and beverage manufacturing for over 35 years. They are an ideal way to continuously produce well blended solutions, brines and beverages. Applications of Fox slurry eductors range from adding few pounds per hour of whey added to a milk stream to blending favour additives into liquids flows of 500 GPM or more.
bags and their accompanying dust and spillage still often surround powder addition to tanks and vessels, which often require staff climbing ladders with bags on their shoulders.
bags and their accompanying dust and spillage still often surround powder addition to tanks and vessels, which often require staff climbing ladders with bags on their shoulders.
Fox Venturi Eductors, for blending powders into liquids – have been used in food and beverage manufacturing for over 35 years. They are an ideal way to continuously produce well blended solutions, brines and beverages. Applications of Fox slurry eductors range from adding few pounds per hour of whey added to a milk stream to blending favour additives into liquids flows of 500 GPM or more.
for
Coco Powder, Whey, and Spice Additives into Milk: Here a dairy manufacturer needed continuously blend pulverized coconut meat, whey, and flavorings into milk on its way to an interim process.
Coco Powder, Whey, and Spice Additives into Milk: Here a dairy manufacturer needed continuously blend pulverized coconut meat, whey, and flavorings into milk on its way to an interim process.
the installation at the largest orange juice producer in the USA. Calcium Citrate is metered into a 2” food-grade Fox slurry eductor at 65 GPM at 70 psig. This venturi has been in service for over fifteen years with zero maintenance.
the installation at the largest orange juice producer in the USA. Calcium Citrate is metered into a 2” food-grade Fox slurry eductor at 65 GPM at 70 psig. This venturi has been in service for over fifteen years with zero maintenance.
From Batch to Continuous liquid/solid blending with Fox Slurry Eductors The addition of powdered products is often left as a manual operation in otherwise highly automated production environments. Scoops, buckets and
From Batch to Continuous liquid/solid blending with Fox Slurry Eductors The addition of powdered products is often left as a manual operation in otherwise highly automated production environments. Scoops, buckets and
As plant production rates increase, processes often evolve from batch to continuous, for which Fox Venturi Slurry Eductors are ideal. Liquid flow is maintained at a constant flow rate by the precision machined nozzle within the venturi. A screw feeder can then dose powder – from a bulk bag, bin, or silo – at a controlled rate. For example, Case Study 9 shows
As plant production rates increase, processes often evolve from batch to continuous, for which Fox Venturi Slurry Eductors are ideal. Liquid flow is maintained at a constant flow rate by the precision machined nozzle within the venturi. A screw feeder can then dose powder – from a bulk bag, bin, or silo – at a controlled rate. For example, Case Study 9 shows
The motive nozzle in the slurry eductor maintains milk at a fixed, constant flow rate, enabling three in-weight feeders to drop additives into the washdown hopper at a constant feed rate, producing the mixture with uniform solids/liquids ratio.
The motive nozzle in the slurry eductor maintains milk at a fixed, constant flow rate, enabling three in-weight feeders to drop additives into the washdown hopper at a constant feed rate, producing the desired mixture with uniform solids/liquids ratio.
Some of the largest global beverage manufacturers now use Fox slurry eductors to blend the ever-increasing variety of flavours that consumers are looking for. And a slurry eductor is not limited to powder feed from just one feeder. Up to six feeders can be arranged to deliver powder in different combinations, or one at a time, to meet continually changing production schedules. Fully hygienic CIP (Clean In Place)
Some of the largest global beverage manufacturers now use Fox slurry eductors to blend the ever-increasing variety of flavours that consumers are looking for. And a slurry eductor is not limited to powder feed from just one feeder. Up to six feeders can be arranged to deliver powder in different combinations, or one at a time, to meet continually changing production schedules. Fully hygienic CIP (Clean In Place)
pellets from palletizers: Fox eductors have been used for twenty years to transport plastic pellets from the end of extruder lines and various types of pelletizers.
Plastic pellets from palletizers: Fox eductors have been used for twenty years to transport plastic pellets from the end of extruder lines and various types of pelletizers.
Additives needed to whey, interim maintains the three losswashdown desired
Coco Powder, Whey, and Spice Additives into Milk:
Here a dairy manufacturer needed to continuously blend pulverized coconut meat, whey, and flavorings into milk on its way to an interim process.
The motive nozzle in the slurry eductor maintains the milk at a fixed, constant flow rate, enabling three lossin-weight feeders to drop additives into the washdown hopper at a constant feed rate, producing the desired mixture with uniform solids/liquids ratio.
Some of the largest global beverage manufacturers now use Fox slurry eductors to blend the everincreasing variety of flavours that consumers are looking for.
eductors, polished and ground in 316 ss, can be rapidly diassembled for quick clean-outs between product runs to eliminate crioss contamination. See attached photo of an electropolished, fully hygienic venturi eductor.
Fox can supply the right properly engineered powder-feed hopper – adjusted per downstream piping geometry. Rather short distances can use a dry hopper. Longer distances , or systems with substantial vertical pipe downstream, need a washdown hopper - to both sweep powders into the eductor, but more importantly, to inhibit air from being sucked in . See attached graphic and photo of a slurry eductor with a washdown hopper.
Plastic pellets from pelletizers been used for twenty years to transport plastic pellets from the end of extruder lines and various types of pelletizers. Mouthwash , Shampoos, Cosmetics
guar, carrageenan and xanthum gum. These are commonly used in sauces, ketchup, etc This application requires what we call coaxial eductors, and eliminates the lumps and clumps common if these powders are just added to a tank.
Most Commonly Asked Questions” in our bulletin on Slurry eductors – which we will be happy to send upon request from our website ( foxvalve.com) A few simple limits : a) Max solids loadfing is about 15 –18% solids by weight, b) Max liquid viscosity about 200 centipoise
An important niche for Fox slurry eductors is the instant hydration of hard-to-wet powders, used as emulsifiers, such as
Of course, there are distinct limits to whether a slurry eductor can work in each application. These are discussed in detail in the “10
USDA-Approved slurry eductors have been used to blend powders into pharmaceutical solutions for consumer products since the 1970ʼs.
Please contact us with details of your application.
www.foxvalve.com
North Ridge Pumps have now released the HTS - a state-of-theart of hygienic twin screw pump designed to achieve the maximum level of sanitation for food and pharmaceutical market.
The HTS is a versatile unit which eliminates the need for a separate CIP pump due to its ability to operate at high and low speeds – low for process duty, and high for effective CIP cleaning and sanitation.
An innovative range of pumps, it is designed to elevate standards and efficiencies where sanitation is required through elimination of dead zones. The pump head is designed to be completely drainable as standard as opposed to other pump designs where the feature is on request.
Typically positive displacement pumps operate at low speed due to the viscosity of liquids, and particles being transferred meaning a reduced speed is required for effective pumping, decrease of wear and to prevent shear of sensitive liquids.
They usually rely on a separate CIP port to bypass slowly rotating parts for effective cleaning, CIP cleaning can be aggressive to internal rubber parts of pumps which are although resistant to the Caustic and acidic nature of high temperature CIP water – they do breakdown over time causing rubber to powderise.
Due to the HTS Twin Screw pump being of full metal design, it keeps internal rubber parts to minimum, which also eliminates the likelihood of rubber parts contaminating liquids overtime ensuring higher quality end product.
This unit is suited for a variety of applications for liquids up to 1,000,000 CP due to its gentle pulsation and axial conveying of liquid, ensuring material integrity is maintained. Its high suction capabilities means that a variety of liquids can be processed at up to 5000L/min and 250M head.
Customisation of flow and pressure generating is obtained from a choice of screw pitches which allows for different flow rates, pressure and solid handling especially when combined with a Variable frequency drive for multispeed operation. It can run dry when fitted with flush seals due to the separation of rotors and pump casing.
Manufactured from Stainless Steel 316 the HTS is resistant to corrosion and oxidisation. The rotor and sealing shaft can be supplied with Duplex or Super
At North Ridge Pumps, we’re not limited to choosing just one pump design.
duplex stainless steel on request, with the screws hardened on request for abrasive applications. Maintenance is easy and efficient thanks to the split casing design for ease of disassembly and inspection port directly above timing gear for set up. A between bearing design with 4 sets of bearings in oil bath ensures extended performance, improved efficiency as well as quiet operation.
It is designed for use in a variety of sanitary industries ranging from dairy, bakery, beverage production, cosmetics, vegetable processing, pharmaceutical, and brewing.
If you have an upcoming requirement and are unsure of the correct solution, speak to North Ridge Pumps to see how we can help.
Optimise performance with specialist support
Whether you’re dealing with clogging, separation, downtime, or other issueit’s costly. Time wasted troubleshooting and lower production mean missed targets and less profit. A sanitary pump is the solution but choosing the right one feels like stepping into a minefield. You know what you need it to do but with so many options, it’s difficult to know which is best for your process and parameters.
+ Accelerated stator wear
+ Clogging
+ Changes to fluid consistency
+ Clean-in-place and sterilise-in-place hygiene issues
+ Crushing of sensitive products
+ Inconsistency in finished product
+ Inaccurate transfer of flavourings or ingredients
+ Liquid separation
+ Seal wear or failure
We’ve been engineering sanitary pumps for sectors such as distilling, brewing, food manufacturing/processing, and more, for 20+ years. We understand industry-specific processes and know what it takes to optimise performance through better-suited pump design - giving you complete peace of mind.
Our expert engineers understand your process and guide you through the options, so you can confidently select the most suitable sanitary pump.
EXAMPLE PRODUCTS:
+ Abrasive mixtures
+ Creams, milk & ice cream
+ Edible oils & fats
+ Fish & meat
+ Fruits eg. cooked apples, plums, berries, grapes
+ Grains & seeds
+ Pastes & purees
+ Syrups, juices & alcohols
+ Vegetables & peelings
+ Waste eg. trimmings, packaging & offcuts
+ Sheer sensitive liquids
+ Solid laden or viscous mixtures
DS Smith, the leading international sustainable fibre-based packaging company have been awarded the Corrugated Post-Print E and F category by FlexoTech International Print & Innovation Awards
2024. The award is for producing ‘outstanding’ flexo printing for Carlsberg 18-pack Pilsner, and the winning packaging was made in DS Smith’s site in Tampere, Finland.
The Flexo Tech International Print & Innovation Awards entries are judged by an international panel of judges on categories including reproduction, degree of difficulty, and to qualify they must be produced in the twelve months prior to the competition.
The winning DS Smith packaging solution for Carlsberg 18-pack Pilsner highlighted how fibrebased corrugated cardboard can be successfully utilised for complex print and graphic design projects with a high-quality finish. The DS
Smith design team demonstrated how the fibres of corrugated cardboard can be reused multiple times and therefore keep materials in use for longer, and in addition, the overall packaging solution was designed to be easy to recycle for the consumer.
Ari Viinikkala, Managing Director, DS Smith’s Packaging, Finland
“FlexoTech is a great and prestigious award. I am proud to represent a company that is successful due to its exceptional expertise in this area. This is validation of the competence and commitment of our team at DS Smith Tampere, with a proven focus on delivering pioneering packaging solutions within the circular economy,”
FlexoTech International Print & Innovation Awards panel of judges: “This is probably the best tonal work on corrugated we have seen. Holding very fine detail in
challenging shades of grey. Superb solid colour.”
Through its purpose of ‘Redefining Packaging for a Changing World’ and its companywide Now and Next sustainability strategy, DS Smith is committed to leading a transition to the circular economy and to delivering innovative sustainable packaging solutions for its customers and society at large.
DS Smith´s site in Tampere, Finland, was also accolated with a FlexoTech International Print & Innovation Award within the same category in 2015 and has been among finalists several times after that.
The Flexo Tech International Print & Innovation Awards ceremony was held in London on Tuesday 17th October 2024.
Viscosity is defined as the “interaction between the different molecules in a fluid – this can be also understood as friction between the molecules in the fluid” and can be measured with various types of viscometers and rheometers using the measurement of centipoise (cP). When creating produce for consumption, manufacturers need to understand the effect created by food and beverage viscosity, which can be affected by the conditions within which it’s used, and are an important consideration when determining manufacturing methods.
Examples of different food and beverage items and their approximate viscosities are noted in the table to the right:
Depending on the viscosity of the product, the pressure and flow rate needed to propel the produce out of its primary container and into its intended location will differ. For example, a thicker, more viscous product will require an increased force versus that of a runnier, more water-like product. The latter is generally easier to transfer because it can be helped by gravity and has less resistance. For many products, however, consumer perception is that the ‘thicker’ a product is, the more superior it is, as it is perceived to have been made with higher quality ingredients. This leads to many products being more viscous than they may actually need to be due to consumer perception driving sales, especially for example, beauty products like creams, hair conditioner or shower gel; and even household products like bleach, washing up liquid or laundry detergent. Working with high viscosities is usually far more challenging for flow-control engineers who need to move fluids through manufacturing lines, ensuring that the liquid is transferred at the correct speed,
Acetate glue
liquid soap
(49°C)
butter (60°C)
Condensed milk (75% solids)
Corn syrup
- 3,000
- 3,000
garnish
detergent
Orange Juice Concentrate - 30 Brix
Orange Juice Concentrate - 60 Brix
Peanut butter
Printers Ink
Resin solution (from 18°C to 24°C)
Salad cream
Tomato ketchup
Toothpaste
Varnish paint
Yoghurt
without damage and without waste. But it’s not just the baseline viscosity of the produce that needs to be taken into consideration,
- 250,000
- 2,200
- 7,140
- 2,600
- 70,000
- 100,000
there are a few scenarios that can impact the viscosity and therefore change the properties of the product:
At Quantex, we understand the importance of viscosity, especially during manufacturing or within a retail or food service environment.
Temperature – a colder temperature significantly increases the viscosity of a product making it more solid and less smooth/runny
Head-height – should a product need to be propelled upwards, it’s working against gravity and will need a higher level of force to move it versus if it was to be released downwards or from above
Molecular levels – gases and liquids hold different levels of viscosity and generally speaking, fluids with larger, more complex molecules or long-chain polymers (e.g proteins, starches, hydrocolloids or gums, etc) will also have higher viscosities
Consistency – fluids with larger, more complex and inconsistentsized ingredients will have higher viscosities e.g soup with ‘chunky’ components versus water
Pressure – the lower the pressure applied to expel a food or beverage item, the slower it will run and the harder it is to drive and maintain the continuous momentum of the product
Freshness/age – if not sealed aseptically, produce can deteriorate
and break down either making the produce ‘runnier’, or it could solidify/ crystallise to cause blockages.
Rheology – some fluids shear thicken or shear thin as their flow velocity increases. Ketchup is a good example of shear thinning where it takes a lot of energy to start the fluid moving and then it becomes thinner. This is why you need to shake the bottle vigorously and then it suddenly pours out. Cornflower slurry is an example of shear thickening – the faster you stir it the stiffer it gets.
The optimal achievement of any pump is a near-vacuum (1 Bar negative pressure) so for a pump to self-prime the fluid must have a sufficiently low viscosity so that it can supply the inlet of the pump. The output of a pump is not constrained and may be several Bar. For extremely viscous liquids the fluid needs to be supplied to the pump using an independent pressure source.Overall, the key to moving viscous fluids is to choose the right pump. There are not many pump designs that can handle highly viscous fluids with precision. Quantex pumps use a positive displacement rotary action, so fixed volumes of fluid (boluses) are carried from inlet to outlet around a rotor – which produces inherently accurate doses and is much less sensitive to variables such as line pressure, fluid viscosity and flow rate. The positive displacement rotary action generates a high inlet vacuum and high pressure on the outlet.
This means that, unlike other pumps, Quantex is able to transfer highly viscous liquids such as ketchup and mayonnaise, sour cream, jam, face cream, hair conditioner and even relish etc whilst being self-priming and with better bag evacuation and less waste. Quantex can even manage very thick fluids such as peanut butter with particulates, but it is necessary to encourage the fluid to the inlet side of the pump as the fluid is too thick to self-prime. The below videos show different solutions at various viscosity levels being expelled with the aid of a Quantex pump:
QX25-SD pump dispensing milk and hot coffee from concertina bottles
QX100-SD dispensing relish condiments
The QX 120-Dl dispensing detergent and various dilutions
Bag-In-Box dispensing ketchup and mayonnaise
Bag-In-Box pump dispensing yoghurt dairy products
Bag-In-Box pump dispensing wine and alcoholic beverages
At Quantex, we understand the importance of viscosity, especially during manufacturing or within a retail or food service environment. And to serve these markets, we’ve developed a range of pumps to suit different flow rate ranges, viscosity levels and dispense applications and the technology holds over 100 global granted patents. Our HighSpeed Eco Pumps use air pressure to activate the diaphragm and seal the pumps instead of a silicone spring, so they are more easily recycled, and can run almost three times as fast as our standard or highpressure pumps.Microdosing Pump
• Low Flow Pump Range
• Bag-In-Box Pump Range
• High Flow Pump Range
If you’d like to learn more or discuss how a Quantex pump could work for you, please email Quantex. GeneralSupport@psgdover.com or call +49 (2065) 89205-0.
www.quantex-arc.com
In the world of food manufacturing, precision is everything. You will know how a consistent taste and texture is vital in meeting your quality standards, reducing waste and protecting your brand with the consumer. Relying on the manual control of ingredient transfer is not only putting the burden on your production team (and we all know that time is money!), but also increasing the chance of recipe inaccuracies due to human error.
And that is why the accurate transfer of additives, flavourings and ingredients combined with the AMP-CONTROL peristaltic pump really is a “batch made in heaven”.
Castle Pumps have recently solved two food manufacturers’ batching requirements with their AMP-CONTROL peristaltic pump. The first was a manufacturer of low calorie sweeteners looking to batch 10 litres of Glycerin at a time during the production process of their products. The second was a commercial bakery wanting to transfer set quantities of olive and avocado oil from an IBC in the storage room into the production room. Both wanted control over the speed at which they could transfer and the ability to accurately determine how much to transfer in each batch. And that’s when Castle Pumps knew the AMP-CONTROL was the ideal solution.
Peristaltic pumps are often used for batching applications thanks to their smooth operation and ability to accurate dose even the smallest volume of fluids at low flow rates. Another huge benefit of the peristaltic design is that with the inner hose being the only wetted part, there is only one component to wear and maintain without risk of seals leaking and valves blocking.
The AMP-CONTROL model in particular however had the intelligence to satisfy the food manufacturers’ requirements of automation and accuracy without the need for the clients purchasing and installing additional control equipment.
As well as its variable speed drive, the beauty of this pump is that it allows batching to be specified either by volume or by intervals, as well as a calendar for operation automation at set date/times. This peristaltic dosing pump also comes with configurable inputs and outputs that can be used for signal relays to determine when the pump should operate for example when fluid in the receiving container has dropped to a set low level. These benefits allow for highly precise dosing of the ingredients whilst also freeing
up operator time to carry out more value adding tasks.
As a fail-safe which is particularly useful in hygienic environments like these clients’, the AMPCONTROL also comes with a hose leakage sensor to shut down the pump and alert the operator, as well as a hose replacement alert for preventive maintenance after a set interval to prevent downtime in production.
Getting the wrong pump for your process can result in inconsistency in the finished product, crushed solids, clogging, excessive wear, loss of productivity, waste of costly product or at worst, contamination. Always trust technical experts to specify the right pump for your application.
www.castlepumps.com
A pump may do the job, but only the right pump will save you excessive wear, process failures, product waste & operator time.
Get the RIGHT pump with our 15 years’ experience in:
✓ FDA & 3A hygienic solutions for food and drink
✓ Highly accurate dosing of ingredients & additives
✓ Delicate fluids sensitive to consistency changes
✓ Solid-laden products without crushing or clogging
✓ 99.98% barrel emptying to prevent product waste
Contact our technical sales engineers now!
Inspired Pet Nutrition (IPN), a leading pet food company (HQ Thirsk, UK), has made a significant breakthrough in its sustainability efforts by achieving 100% diversion of food waste from landfills, thanks to its partnership with sustainable waste management company Waste Mission. This milestone marks a critical step in IPN’s ongoing commitment to environmental responsibility and innovation in waste management.
IPN, known for its popular brands Wagg, Harringtons, Barking Heads, and Meowing Heads, has been a family-run business since 1923. With a vision “to become the nation’s most sustainable, most loved home of pet nutrition brands,” IPN became the first major UK pet food manufacturing business to go carbon-negative in 2020.
Faced with the usual waste management challenges of any food producing company, IPN sought a waste management partner who shared its passion for sustainability and innovation. Waste Mission clearly emerged as the ideal choice, offering not only to divert waste from landfills but also to provide sustainable solutions that minimise environmental impact, conserve natural resources, and even monetise waste streams.
The collaboration between IPN and Waste Mission addresses the growing consumer demand for ethical and sustainable products.
A Deloitte survey revealed that 30% of consumers stopped buying products due to ethical or sustainability-related concerns, while 50% saw the importance of circularity in the product lifecycle.
Circularity refers to a business model in which waste is eliminated, and resources are continuously reused. This approach transforms waste into valuable resources, contributing to environmental sustainability and economic efficiency.
IPN faced various waste management hurdles, including:
1. Meat and fish juice on packaging: These materials were hard to handle.
2. Raw Meat Waste: Inefficient and environmentally unfriendly disposal methods require a modern solution.
3. General Waste Management: Disruptions caused by waste accumulation necessitate an intuitive waste management approach.
“These challenges are not unique to IPN, but we wanted to be show leadership in how we addressed them,” said James Lawson, Director. “Sustainability and waste reduction are crucial for our people, pets and planet approach to ESG. Partnering with Waste Mission reflects our dedication to creating happiness for our pets, their owners and the supply chain.”
Waste Mission implemented a tailored waste management solution for IPN, including:
1. Recycling meat and fish juice –impacted packaging: Specialised processes were introduced to recycle these materials, diverting
them from landfills.
2. Recycling Raw Meat Waste: Innovative recycling methods ensured 100% recycling of raw meat waste.
3. 24-Hour Service Level Agreement (SLA): A 24-hour SLA was established to ensure efficient waste collection and management, prevent operational disruptions, and simplify daily communications.
The collaboration yielded outstanding results:
1. 100% Landfill Diversion: All waste, including complex materials, is now diverted from landfills.
2. 100% Recycling Rate: All waste collected from IPN is recycled, aligning with their sustainability goals.
3. Uninterrupted Operations: The 24-hour SLA has ensured zero disruptions in IPN’s operations due to waste management issues.
IPN continues to prioritise sustainability with Waste Mission’s support, substantially reducing its environmental footprint. “We urge other pet food manufacturers to join us in prioritising sustainability and waste reduction,” said James. “High-quality pet food can be produced while adopting ecofriendly practices and meeting the growing needs of conscious consumers.”
By achieving a 100% recycling rate, IPN has set a benchmark in sustainable waste management. Waste Mission remains committed to continuous improvement and innovation, ensuring IPN’s longterm success in sustainability.
If you’d like to find out more, book a waste review today, or visit the team at Southern Manufacturing or FoodEx 2025.
Kadant PAAL design and manufacture efficient solutions for volume reduction to optimise transportation of recyclable materials, helping to reduce environmental impact and transportation costs.
We are recognised as Europe’s Premier Manufacturer of baling presses including Channel, Twin Ram, Closed End and Metal Balers. Kadant PAAL work globally within the recycling industry whether it is with national waste carriers, independent waste companies, local authority, or FM distribution centres.
The Kadant PAAL Group is a result of the merger of four European Companies, PAAL, COMDEC, FAES and DICOM, with the recent addition of BALEMASTER USA. The experience within the group ensures that Kadant PAAL are best placed as a provider of proven, tried, and tested baling solutions.
Kadant PAAL UK manufacture its own DICOM Product range of popular vertical balers and waste compactors, distributing and installing the PAAL range of fully automatic horizontal balers and conveyors manufactured in Germany. With their own Technical and Design Team they can provide bespoke solutions with fabrication work manufactured at the factory based in Alfreton to suit all requirements. Our mobile engineers are strategically placed across the country in the event of any mechanical difficulties providing a rapid response
call out. Furthermore, the Remote Service Support (RSS) system remotely connects technical experts to the machine in question, with the ability to quickly diagnose the cause of faults, alarms or any performance related issues to avoid unnecessary downtime.
We provide comprehensive bailing solutions. Over the last 150 years we have learnt that each application is unique, each operation having its own particular requirements and needs, processing varied materials.
We understand each project is unique, therefore we have a wide range of options that have been developed to ensure once the customers’ needs have been assessed and identified, we can offer an option that will fulfil the baling requirements, supplying a well-designed, robust and reliable solution. It is inconceivable to produce an individual bespoke baler for each application in the same way that one size does not fit all. With our extensive range of waste management options which are used in applications from MRF’s to retail stores, we are also able to offer bespoke adaptations to provide solutions for your environment.
www.kadantpaal.com | www.dicompaal.co.uk
Liverpool
is a city that’s
Liverpool is a city that’s world famous for many things. Its music for a start (it’s the birthplace of The Beatles, of course, and many other great bands and artists), as well as its world-class football team, Liverpool FC.
world famous for many things. Its music for a start (it’s the birthplace of The Beatles, of course, and many other great bands and artists), as well as its world-class football team, Liverpool FC.
But travel a few miles north of the city to Aintree, not far from the home of the Grand National, which attracts more attention globally than any other horse race, and you’ll find Food Test Lab, a truly world-class Liverpool business.
But travel a few miles north of the city to Aintree, not far from the home of the Grand National, which attracts more attention globally than any other horse race, and you’ll find Food Test Lab, a truly world-class Liverpool business.
“Food Test Lab is an independent, UKASaccredited microbiological testing and chemical analysis laboratory,” explains Laboratory Manager, Cameron Finlay. “Working for a wide range of customers, we provide ISO 17025-accredited microbiological, chemistry and nutritional testing and food analysis of a diverse list of foodstuffs and feeds.”
“Food Test Lab is an independent, UKASaccredited microbiological testing and chemical analysis laboratory,” explains Laboratory Manager, Cameron Finlay. “Working for a wide range of customers, we provide ISO 17025-accredited microbiological, chemistry and nutritional testing and food analysis of a diverse list of foodstuffs and feeds.”
World-class laboratory
World-class laboratory
Food Test Lab’s accredited food testing and food analysis services enable its customers to meet safety regulations, achieve best practice and satisfy consumer needs. Microbiological Manager Jennifer Smith says: “Our highly qualified and experienced team of microbiologists uses the latest technologies and methods to provide accredited microbiological testing of foods, beverages, animal feeds and environmental samples.”
Food Test Lab’s accredited food testing and food analysis services enable its customers to meet safety regulations, achieve best practice and satisfy consumer needs. Microbiological Manager Jennifer Smith says: “Our highly qualified and experienced team of microbiologists uses the latest technologies and methods to provide accredited microbiological testing of foods, beverages, animal feeds and environmental samples.”
Food Test Lab’s purpose-built testing laboratory in Aintree, which opened in 2016, was designed to process a large volume of microbiological samples every day and results are delivered on time according to customer needs, no matter how demanding. “We’ll always try to tailor our services to meet specific customer needs” Cameron smiles.
Food Test Lab’s purpose-built testing laboratory in Aintree, which opened in 2016, was designed to process a large volume of microbiological samples every day and results are delivered on time according to customer needs, no matter how demanding. “We’ll always try to tailor our services to meet specific customer needs” Cameron smiles.
Chemical and nutritional analysis
“In addition to UKAS-accredited microbiological analysis, our food testing laboratories can provide detailed chemical analysis and nutritional analysis for food labelling,” Cameron adds. “Our nutritional analysis and chemical analysis services include moisture, fats and oils, proteins, sugars, sodium, fibre, ash, salt, carbohydrates, fatty acid profile, dietary fibre, energy value and Group I and II nutritional analysis.”
“In addition to UKAS-accredited microbiological analysis, our food testing laboratories can provide detailed chemical analysis and nutritional analysis for food labelling,” Cameron adds. “Our nutritional analysis and chemical analysis services include moisture, fats and oils, proteins, sugars, sodium, fibre, ash, salt, carbohydrates, fatty acid profile, dietary fibre, energy value and Group I and II nutritional analysis.”
Cameron and his colleagues can provide fast turnaround times for groceries, cooked and raw meats, dairy products, processed foods and exports such as meat, fish, honey, milk, coffee, cocoa and beverages. “Our other food lab testing services include heavy
Cameron and his colleagues can provide fast turnaround times for groceries, cooked and raw meats, dairy products, processed foods and exports such as meat, fish, honey, milk, coffee, cocoa and beverages. “Our other food lab testing services include heavy
or Jennifer Smith on +44 (0)151 525 1488 or email laboratory@alexstewartagriculture.com
metals – mercury, lead, cadmium and arsenic – as well as hydroxyproline, peroxide value, pH, Omega 3, 6, 9, trans fatty acids.”
metals – mercury, lead, cadmium and arsenic – as well as hydroxyproline, peroxide value, pH, Omega 3, 6, 9, trans fatty acids.”
International customer base
International customer base
Food Test Lab is the trading name of the UKAS-accredited company Huson and Hardwick, which became part of the Alex Stewart Agriculture Group in 2004. Huson and Hardwick has an enviable reputation as a leading provider of ultra-reliable GAFTA and FOSFA-certified laboratory analysis. Almost 180 years since its formation in Liverpool, Huson and Hardwick continues to innovate and provide exceptional analytical and certification services via Food Test Lab.
Food Test Lab is the trading name of the UKAS-accredited company Huson and Hardwick, which became part of the Alex Stewart Agriculture Group in 2004. Huson and Hardwick has an enviable reputation as a leading provider of ultra-reliable GAFTA and FOSFA-certified laboratory analysis. Almost 180 years since its formation in Liverpool, Huson and Hardwick continues to innovate and provide exceptional analytical and certification services via Food Test Lab.
Expert pet food testing services
Expert pet food testing services
Food Test lab also offers fully accredited test services to makers of pet food. As Jennifer explains: “Makers of dog and cat food are under pressure to ensure increasingly higher quality, so that they meet stringent safety and pet-owner requirements. We’re fully equipped to analyse a wide range of manufactured pet foods and our great technical expertise enables us to choose the right sample preparation method to ensure reliable results.”
Food Test lab also offers fully accredited test services to makers of pet food. As Jennifer explains: “Makers of dog and cat food are under pressure to ensure increasingly higher quality, so that they meet stringent safety and pet-owner requirements. We’re fully equipped to analyse a wide range of manufactured pet foods and our great technical expertise enables us to choose the right sample preparation method to ensure reliable results.”
Offer consistent product quality at the point of use for a wide range of applications, guide rails position the IBC and the mixer is raise and lowered into the IBC with a push button operated electrical actuator.
Fixed or mobile mixing stations are supplied complete with a control panel and safety interlocks.
Standard IBC mixing stations can be adapted to integrate with systems on site including pumps, valves, weighing and measuring instrumentation and controls to meet specific site requirements.
Recently launched by MOONS’ and available in the UK from its UK distribution partner Mclennan, the new AW series ‘Industrial Protective Stepper Motors’ are aimed at harsh environment motion control applications in food and beverage production, medical industries and arduous industrial environments. These new IP65rated microstepping motors feature enhanced surface protection with improved wear resistance and greater impermeability to scratches and abrasions.
With their IP65 rating as standard, the dust- and water-proof motors are available in NEMA frame sizes 17 through 34 and are optionally supplied with brakes and 1000line optical encoders for position feedback with suitable motion controllers. Offering holding torque from 0.31 to 10.3 Nm through the range, the AW series feature MOONS’ high-fill motor windings offering smooth performance across a wide speed range with increased torque over competitive size-forsize motors as well as low inertia rotors for higher acceleration. As standard, the motors are supplied
with M8 or M12 aviation plug connectors that offer further reliability and long-term stability.
Alongside the new AW series motors, Mclennan offers a wide choice of complementary motion controls and drives including the STF series intelligent microstepping drives from Applied Motion Controls Inc. –a subsidiary of MOONS’ and a long-time distribution partner for the motion control specialist. The panel mounted STF series covers three power versions from 3.0 to 10.0 A/phase with a choice of interface options that cover Industrial Ethernet including EtherCAT as well as CANopen and AMP’s proprietary Serial Command Language (SCL) for network communication over Ethernet (UDP or TCP) and RS485. Dual-port communications provide daisy-chain connections for multiple drives, enabling multiaxis synchronisation from hostcontrolled streamed commands. The DC powered drives are also able to take care of local machine control - pre-programmed using AMP’s multi-tasking ‘Q’ language
for motion profiles, math functions, conditional processing, data register manipulation and interaction with on-board I/O. Alternatively standalone motion control is possible for less complex machine applications.
With its own in-house system design and production capability, Mclennan works closely with its distribution partners and customers to bring motion control and automation solutions that, as part of the enabling technology of a machine or process, bring distinct benefits in performance whilst competitively maintaining
high quality and reliability. Mclennan’s engineers can assist with motor sizing, drive technology, and motion controls for MOONS’ complete range of hybrid stepper motors.
For further information please visit www.mclennan.co.uk, email sales@mclennan.co.uk, or call +44 (0) 1252 531444.
“attendees
exhibitors
This has been absolutely fantastic—far beyond our expectations! The turnout has been incredible, with more visitors than we ever anticipated. We’ve attended other shows across Europe in recent months, and this one is by far the largest. The energy has been amazing right from day one, with a constant flow of enthusiastic visitors. We’re thrilled with the outcome!
Agnieszka Radecka Regional sales manager, TME
Meet the power behind UK manufacturing industry and see live demonstrations and new product launches of machine tools & tooling, electronics, factory & process automation, packaging & handling, labelling & marking, 3D print technology, test & measurement, materials, composites & adhesives, rapid prototyping, ICT, drives & controls, plastics & polymers and laboratory equipment.
Free industry seminar programme available online. The exhibition is free to attend, free to park and easy to get to. Doors open at 9.30am on 4th February.
Advanced technology from mechanical engineering and electrical/electronic industries in approximately equal measure awaits visitors to the next Southern Manufacturing & Electronics trade fair, which will take place from 4th to 6th February 2025 at the Farnborough International Exhibition & Conference Centre. The event is on track to be a sell-out, according to the new owner of the show, Easyfairs, with more than 500 stands expected to be booked for the first time. The larger number of exhibitors will create an even more dynamic and informative environment for visitors, allowing people to explore a greater variety of products and services.
The abundance of new engineering technology across such a wide spectrum of technologies makes the venue highly functional for anyone involved in design, manufacture, procurement, training or management looking to source multiple products and services in a time-efficient way. Although the industries represented throughout the hall are multifaceted, there are no barriers between the areas, allowing easy cross-over between the different disciplines. Many of the 9,000+ visitors each year say it is an aspect of the show that is particularly useful, as it encourages a wide-ranging itinerary around the stands, often leading to discovery of firms specialising in technologies
that would otherwise probably not be encountered.
Widely regarded as the largest and most comprehensive annual industrial expo in the UK, as well as being a major global showcase for engineering and manufacturing technology, the event moved to its present location in 2008 and was the first to be held in the new, world-class exhibition centre when it was built a decade later. The show is important enough to attract big-name manufacturers, but is also very accessible to the rich ecosystem of engineering SMEs, as the organisers operate a policy of open access discouraging larger firms from dominating the space to the detriment of smaller
vendors. Easyfairs says that it intends to maintain the intimate look and feel of the exhibition, which is a defining quality that gives it a unique, vibrant atmosphere fostering collaboration, learning and discovery. Testament to its effectiveness as a place to do business is the very high rate of return stand bookings. Many participants are regular returnees and some have supported the show since it started in 1997.
This year’s event will reflect the ongoing growth in digitalisation of production, a prevalence in Industry 4.0 manufacturing systems, an emphasis on reshoring of production, plus new ecological technologies such as green energy generation, power-saving machinery and efficient underfloor heating. On the mechanical engineering side, there will be the latest machine tools, tooling, workholding and other production hardware, plus suppliers of castings, plastic injection and rubber mouldings, fasteners, pressings, wire forms, springs and gaskets. On the electronics side, featured will be PCB design and manufacture, box build services, cables and connectors. Spanning both disciplines will be mechatronics assembly, electro-mechanical components and systems, controls, displays, HMIs and data acquisition systems, sensors, drives and encoders, illustrating just how intertwined the two engineering sectors are.
Robotics and other forms of autonomous handling will feature strongly, driven by a skills shortage in Britain and across Europe. Additive manufacturing continues its progress towards becoming a mainstream production technique and there will be many companies offering equipment, consumables and bureau services. Testing, inspection and measurement serving all industry sectors will be in evidence, as will production planning systems, engineering and business software, materials and consumables. Additional products and services will include oil and coolant, waste recycling, environmental control equipment, packaging and storage, labelling,
hand tools, adhesives, and diverse services from freight forwarding to financial consultancy. The current exhibitor list is available to view at: www.southern-manufacturingelectronics.com/en/exhibitor
Over the three days, visitors will be able to take advantage of an extensive programme of freeto-attend technical seminars covering a wide range of topics to give visitors valuable learning opportunities, with a particular focus on the technical, managerial and environmental issues facing manufacturers today. All sessions will be CPD-approved to ensure they meet specific quality standards. It is an aspect of the exhibition that Easyfairs intends to expand, as promoting education is one of the company’s core beliefs. The Institute for Interconnecting and Packaging Electronic Circuits (IPC) hand soldering competition returns in 2025, as does AutoAero, a specialist thread that runs through the main programme concentrating on matters important to automotive and aerospace engineering. Both sectors directly contribute billions of pounds to the UK’s GDP, while supporting numerous industries and businesses in the supply
chains and providing much needed employment for highly skilled people.
There is free car parking at the Farnborough site, which is well served by road and public transport links, making the venue easy to access. A regular, complimentary bus service runs between the two local railway stations and the showground. Admission to the exhibition is also free. Register today at: https://register.visitcloud.com/
This year’s event will reflect the ongoing growth in digitalisation of production, a prevalence in Industry 4.0 manufacturing systems, an emphasis on reshoring of production, plus new ecological technologies. such as green energy generation, power-saving machinery and efficient under-floor heating.
The food processing industry demands innovation in equipment reliability, hygiene and efficiency. Donghua Limited, the UK subsidiary of the Hangzhou Donghua Chain Group, stands at the forefront with their specialised chain solutions tailored for the Food Processing Industry.
Donghua’s UK portfolio includes high-performance chains such as Roller Chain, Polymer Conveyor Chains, Drytec Stainless Steel Chains, and Universal Attachment Chains. These solutions are designed to maximise durability and hygiene whilst minimising downtime and maintenance costs for food processing companies. In addition, Donghua offers Bespoke Chain solutions which are customised to meet specific customer requirements.
Features like H1 food-grade lubrication and special alloy coatings, highlight Donghua’s
commitment to quality and hygiene, ensuring they supply chains which comply with food safety standards and can withstand aggressive washdown processes.
Donghua’s Food Chains are compatible with the leading food equipment brands including Rademaker, Raque, Meurer, Johnson, Krones, Ishida, Bradman Lane, Baker Perkins, and more.
With a 25,000 sq ft warehouse and a network of regional Approved Product Partners and Stockists who carry Donghua Chain, the company can ensure rapid delivery and local stock availability, helping food processing companies maintain seamless operations.
By integrating innovative design elements such as lube-free chains and corrosion-resistant alloy coatings, as well as in-house
matching of chain to within very close tolerances to eliminate undue stress which causes fatigue failures on attachments, Donghua not only extends the life of its products, but also contributes to customer’s operational sustainability.
Donghua Chain for the Food Industry is manufactured in stateof-the-art facilities with precision tooling, delivering tolerances to within 0.5DIN accuracy.
For more information on how Donghua can enhance your food processing operations, visit: www.donghua.co.uk/food-industry
Measurement Challenge/Difficulty:
Steam being used in breweries had always been overlooked as a source or “reusable” or “capturable” energy. Averaging Pitot tubes typically used were not only inaccurate, but still required costly pipe runs along with very regular and expensive maintenance and replacement. In generating steam, thermal mass meters had been used but presented some of the same problems. Brewers looking to improve their efficiencies needed a new method to obtain and measure a thermal mass balance around the plant for steam generation and usage. Specialty gases such as Carbon Dioxide, Nitrogen, and Chlorine were being used in the utilities and process areas of the brewery. All of these were measured with previously mentioned flowmeter technologies, usually inadequately. The brewers needed a better flowmeter that would reduce the use of expensive purchased gases or be able to monitor use of generated steam and energy demands more accurately.
In beer production, accurate temperature control is critical to any wort boiling kettle since it is a sensitive process and one of the most energy-intensive aspects of beer production. In this case, the kettle is a large vat with tubing coiled around the exterior wall. The tubing carries a mix of steam and water to heat the wort in the kettle. Modulating the proportion of steam vs. water in the tubing enables the brewery to control the thermal transfer profile of the batch process.
The wort boiling process demands a high volume of steam in its initial phase, enough to bring the large batch up to temperature quickly but without burning the wort at points of direct heat transfer. Once the entire contents of the wort kettle reach a boil, a much lower rate of steam feed can then be used to maintain a desirable temperature for the remainder of the heating cycle.
In
beer production, accurate temperature control is critical to any wort boiling kettle since it is a sensitive process and one of the most energy-intensive aspects of beer production.
Steam measurement was made with orifice plates, then averaging pitot tubes. Specialty gases were measured with thermal mass dispersion meters. All of these technologies had similar problems with pipe diameter restriction, maintenance and replacement frequency and costs, and inaccuracies of the devices. Vortex meters especially could not generate accurate readings at low flows in a condensed environment crowded with fittings and tight turns.
V-Cones were installed, reducing operating costs and virtually eliminating replacement expenses. The accuracy of the flowmeters helped the brewery to better calculate their steam/heat balance. V-Cones on specialty gas lines helped reduce usage and more accurately measure produced Carbon Dioxide, resulting in a more economical production. V-Cones measuring Chlorine gas aided in the cleansing cycles thereby reducing gas purchases. V-Cones used in Nitrogen applications measured the gas more accurately, reducing the overall use of gas. Date Installed: 1997.
www.able.co.uk
The symptoms of Climate Change are now very apparent with increases in global temperatures, more frequent storms and flooding where they are not expected and overall changing weather patterns being some of the noticeable warning signs.
Can industry help asks Doug Hart, chairman, Hart Door Systems. Clearly industry, from manufacturing to storage across the globe, can assess the efficiency of the premises they occupy with the ever open door being the most obvious area of wastefulness. In busy and intense warehouse or production facilities, leaving doors open is generally seen as acceptable.
The result is costly heated air escapes, the temperature within the building drops and heating struggles to get back to an acceptable level. More often than not when the door is opened again it is possibly left open because operatives find it much more convenient.
For temperature control and energy management, the automatic door such as Hart’s Speedor is the solution. Speedor’s fast-action is the perfect answer. With quality
We are cognisant of Climate Change issues and the need to keep both Hart’s and our clients’ carbon footprints to a minimum
engineering and durability, Speedor high-speed doors will maintain temperatures within a building while keeping energy costs at an acceptable level.
No matter the industrial classification, Hart can manufacture industrial door systems customised to meet specific needs. As an example the Speedor Storm variant is ready for anything the weather can throw at it. Be it a factory, warehouse, storage facility or any kind of plant operation, where doors must be open frequently for people and traffic the Speedor Storm can withstand wind up to ‘wind class 5’ as defined by DIN EN 12424.
Whether it’s access for deliveries, forklifts or people, there are far too many businesses that leave major entrances open for an
unnecessary amount of time. The knock-on effect is wasted heating, higher costs and a less than optimal working environment.
Speedor Storm is designed specifically to take care of this. It can help with productivity because entering and leaving can be done more rapidly than non-automatic doors. Further it enhances the working environment because the high-speed operation, even on large doors, means there are no unnecessary open stages.
In turn this lowers energy consumption, important at a time when the cost of energy shows little sign of improving and of course reduced energy use has a positive impact on Climate Change.
In conclusion Hart Door Systems’ Speedor range can make a very significant contribution to energy conservation and a carbon footprint. The combination of automation and high speed operation prevents the passage of heated or cooled air escaping from a building only to heat the car park for instance. www.hartdoors.com
MENZEL was asked to manufacture a custom 6600V electric motor to drive a multistage condensate water pump in a thermal power station. The existing motor needed to be replaced quickly. In just four weeks MENZEL planned, built and delivered a three-phase squirrel cage motor with IC 616 cooling and IP 55 protection.
The Requirements: Precision and Speed
The customer not only wanted a motor that could be seamlessly integrated into the existing system via plug-and-play, but also one that could be implemented quickly. MENZEL was able to complete the motor in just four weeks.
One of our stock motors in the required size formed the basis. However, the following adjustments still had to be made:
• Precision work on the rotor shaft: conversion to shaft nuts with lefthand thread and laser welding of the keyway
• Changing the cooling system: Conversion from IC81W to the IC616 system
• Adaptation of the direction of rotation: including different inner fan wheel Accompanying tests: Extensive tests in the load test field to ensure the highest standards
• Adapterplate and different mechanical modification: for a plug and play type fixing between the motor and the pump
The Implementation: Precision meets Efficiency
During the planning phase, we went through several changes and special requirements. Thanks to the close cooperation between the customer, our project engineers and our production department, we were able to develop and agree
the technical solution quickly. Our ability to meet technical requirements and commercial details in record time was particularly praised. In addition, the motor was extensively tested in our load test field. Where MENZEL successfully met all customer requirements.
Technical data of the AC-Motor
• Type: MEBKSLF 500-04-011 AC-Motor
Motor application: Condensate water pump in a thermal power station
• Rated power: 970 kW
• Rated voltage: 6600 V
• Rated speed: 1487 min-1
• Type of construction: IM V1
• Protection class: IP 55
• Cooling type: IC 616
• Weight: 7160 kg
The Delivery: Precisely to the Destination
The finished squirrel cage motor was transported to Japan by plane in order to meet the critical deadline. Installation and commissioning took place at the thermal power plant, where the motor now reliably drives the multistage condensate water pump.
This project is a prime example of our strengths:
• Custom solutions in the shortest possible time
• Efficient communication and close coordination
• Highest technical precision, made in Germany
www.menzel-motors.com
MANUAL & AUTOMATIC BOOT WASHER
Manual boot wash stations, like the ones we supply at Stainless Steel Manufacturing & Equipment, are great for small to mediumsized processing areas and plants.
Manual boot wash stations, like the ones we supply at Stainless Steel Manufacturing & Equipment, are great for small to mediumsized processing areas and plants.
handheld boot brush that enables you to clean the top and sides of your boots and shoes. How to use the Manual Boot Washer:
How to use the Manual Boot Washer:
Our manual boot washer can be used for all types of footwear worn in production areas and is often used on entry and exit to prevent employees from walking debris into changing rooms and corridors.
Our manual boot washer can be used for all types of footwear worn in production areas and is often used on entry and exit to prevent employees from walking debris into changing rooms and corridors.
Manual boot wash stations, like the ones we supply at Stainless Steel Manufacturing & Equipment, are great for small to mediumsized processing areas and plants.
Manual boot wash stations, like the ones we supply at Stainless Steel Manufacturing & Equipment, are great for small to mediumsized processing areas and plants.
Manual boot wash stations, like the ones we supply at Stainless Steel Manufacturing & Equipment, are great for small to mediumsized processing areas and plants.
To activate the manual boot washer, you simply place your foot on the base brushes within the trough, which actuates a valve mounted on the underside of the boot washer. Water the flows through the hose brush and enables you to effectively clean the boot from all angles–ensuring all dirt is removed.
How to use the Manual Boot Washer: To activate the manual boot washer, you simply place your foot on the base brushes within the trough, which actuates a valve mounted on the underside of the boot washer. Water the flows through the hose brush and enables you to effectively clean the boot from all angles– ensuring all dirt is removed.
304/316 stainless steel, providing you with the reassurance that it’s up to standard. What’s more, we aim to accommodate the requirements of all our customers, ensuring that you find a suitable boot cleaning station for your hygienic setting.
To activate the manual boot washer, you simply place your foot on the base brushes within the trough, which actuates a valve mounted on the underside of the boot washer. Water the flows through the hose brush and enables you to effectively clean the boot from all angles– ensuring all dirt is removed.
• Automatic & Semi-Automatic Boot washer.
How to use the Manual Boot Washer:
• Automatic Sensor Operated or Semi-Automatic button operated.
Available in 1-4 stations, the manual boot washer comes with a high-density nylon base brush for scrubbing the soles of shoes and includes a convenient, water-fed, handheld boot brush that enables you to clean the top and sides of your boots and shoes.
Available in 1-4 stations, the manual boot washer comes with a high-density nylon base brush for scrubbing the soles of shoes and includes a convenient, water-fed, handheld boot brush that enables you to clean the top and sides of your boots and shoes.
Our manual boot washer can be used for all types of footwear worn in production areas and is often used on entry and exit to prevent employees from walking debris into changing rooms and corridors.
Our manual boot washer can be used for all types of footwear worn in production areas and is often used on entry and exit to prevent employees from walking debris into changing rooms and corridors.
Investing in a manual boot wash station will ensure your employees perform the necessary washing and disinfecting steps required for hygiene regulations.
Investing in a manual boot wash station will ensure your employees perform the necessary washing and disinfecting steps required for hygiene regulations.
Investing in a manual boot wash station will ensure your employees perform the necessary washing and disinfecting steps required for hygiene regulations.
Manual boot wash stations, like the ones we supply at Stainless Steel Manufacturing & Equipment, are great for small to mediumsized processing areas and plants.
Our manual boot washer can be used for all types of footwear worn in production areas and is often used on
How to use the Manual Boot Washer: To activate the manual boot washer, you simply place your foot on the base brushes within the trough, which actuates a valve mounted on the underside of the boot washer. Water the flows through the hose brush and enables you to effectively clean the boot from all angles– ensuring all dirt is removed.
To activate the manual boot washer, you simply place your foot on the base brushes within the trough, which actuates a valve mounted on the underside of the boot washer. Water the flows through the hose brush and enables you to effectively clean the boot from all angles– ensuring all dirt is removed.
Our manual boot washer can be used for all types of footwear worn in production areas and is often used on entry and exit to prevent employees from walking debris into changing
• Cleaning boots by the action of rotating brushes.
• Automatic dosing of water and detergent.
How to use the Manual Boot Washer:
Investing in a manual boot wash station will ensure your employees perform the necessary washing and disinfecting steps required for hygiene regulations. MANUAL BOOT WASHER
• Removal of the brush is done without the need for tools and makes cleaning the brush and the brush housing simple.
Our automatic stations provide continual performance but are easy to dismantle, requiring no extra tools. In turn, the automatic boot washer is easy to clean, and the rotating tray and brushes can be cleaned individually, allowing you to clean your equipment thoroughly.
Available in 1-4 stations, the manual boot washer comes with a high-density nylon base brush for scrubbing the soles of shoes and includes a convenient, water-fed, handheld boot brush that enables you to clean the top and sides of your boots and shoes.
To activate the manual boot washer, you simply place your foot on the base brushes within the trough, which actuates a valve mounted on the underside of the boot washer. Water the flows through the hose brush and enables you to effectively clean the boot from all angles– ensuring all dirt is removed.
Available in 1-4 stations, the manual boot washer comes with a high-density nylon base brush for scrubbing the soles of shoes and includes a convenient, water-fed, handheld boot brush that enables you to clean the top and sides of your boots and shoes.
The modular belt conveyor offers a reliable versatile solution to many conveying applications.
Investing in a manual boot wash station will ensure your employees perform the necessary washing and disinfecting steps required for hygiene regulations.
Available in 1-4 stations, the manual boot washer comes with a high-density nylon base brush for scrubbing the soles of shoes and includes a convenient, water-fed, handheld boot brush that enables you to clean the top and sides of your boots and shoes.
Investing in a manual boot wash station will ensure your employees perform the necessary washing and disinfecting steps required for hygiene regulations.
The modular belt conveyor introduces a flexible conveying solution that can, due to the nature of the belt itself, convey
Here at Stainless Steel Manufacturing & Equipment Ltd, we can supply a boot washer that is made from Grade
We supply the Lazy Susan Turntable, which is a Stainless Steel Turntable, to meet and exceed the requirements of all industries. We aim to satisfy even the most diverse demands, including those based in the food, drink, pharmaceuticals, packaging and production industry, ensuring that all equipment is manufactured to the highest quality and made to last.
We supply the Lazy Susan Turntable, which is a Stainless Steel Turntable, to meet and exceed the requirements of all industries. We aim to satisfy even the most diverse demands, including those based in the food, drink, pharmaceuticals, packaging and production industry, ensuring that all equipment is manufactured to the highest quality and made to last.
• Supplied with a venture metering system for accurate dosing of the detergent
A turntable that’s made from stainless steel is a cost-efficient investment to make, especially if you’re looking to maximise the efficiency of production.
A turntable that’s made from stainless steel is a cost-efficient investment to make, especially if you’re looking to maximise the efficiency of production.
The Stainless Steel Turntable is just one of the products that we are proud to supply at SSME and is available in various sizes.
The Stainless Steel Turntable is just one of the products that we are proud to supply at SSME and is available in various sizes.
We supply the Lazy Susan Turntable, which is a Stainless Steel Turntable, to meet and exceed the requirements of all industries. We aim to satisfy even the most diverse demands, including those based in the food, drink, pharmaceuticals, packaging and production industry, ensuring that all equipment is manufactured to the highest quality and made to last.
products through inclined as well as horizontal and helical paths.
products through inclined as well as horizontal and helical paths.
We supply the Lazy Susan Turntable, which is a Stainless Steel Turntable, to meet and exceed the requirements of all industries. We aim to satisfy even the most diverse demands, including those based in the food, drink, pharmaceuticals, packaging and production industry, ensuring that all equipment is manufactured to the highest quality and made to last.
We supply the Lazy Susan Turntable, which is a Stainless Steel Turntable, to meet and exceed the requirements of all industries. We aim to satisfy even the most diverse demands, including those based in the food, drink, pharmaceuticals, packaging and production industry, ensuring that all equipment is manufactured to the highest quality and made to last.
We supply the Lazy Susan Turntable, which is a Stainless Steel Turntable, to meet and exceed the requirements of all industries. We aim to satisfy even the most diverse demands, including those based in the food, drink, pharmaceuticals, packaging and production industry, ensuring that all equipment is manufactured to the highest quality and made to last.
We supply the Stainless Steel Turntable in a range of sizes to make it easier for you to find products that will fit perfectly within your industrial setting. When it comes to accumulating products evenly, you cannot go wrong with the Stainless Steel Turntable- it’s specifically designed to bring work closer to the user.
We supply the Stainless Steel Turntable in a range of sizes to make it easier for you to find products that will fit perfectly within your industrial setting. When it comes to accumulating products evenly, you cannot go wrong with the Stainless Steel Turntable- it’s specifically designed to bring work closer to the user.
A turntable that’s made from stainless steel is a cost-efficient investment make, especially if you’re looking to maximise the efficiency of production.
A turntable that’s made from stainless steel is a cost-efficient investment to make, especially if you’re looking to maximise the efficiency of production.
A turntable that’s made from stainless steel is a cost-efficient investment to make, especially if you’re looking to maximise the efficiency of production.
A turntable that’s made from stainless steel is a cost-efficient investment to make, especially if you’re looking to maximise the efficiency of production.
We supply the Stainless Steel Turntable in a range of sizes to
We supply the Stainless Steel Turntable in a range of sizes to make it easier for you to find products that will fit perfectly within your industrial setting. When it
The Stainless Steel Turntable is just one of the products that we are proud to supply at SSME and is available in various sizes.
Space and loads permitting, 90 and 180 degree turns enable products to be conveyed on winding routes through production areas.
The Stainless Steel Turntable is just one of the products that we are proud to supply at SSME and is available in various sizes.
The Stainless Steel Turntable is just one of the products that we are proud to supply at SSME and is available in various sizes.
Space and loads permitting, 90 and 180 degree turns enable products to be conveyed on winding routes through production areas.
We supply the Stainless Steel Turntable in a range of sizes to make it easier for you to find products that will fit perfectly within your industrial setting. When it comes to accumulating products evenly, you cannot go wrong with the Stainless Steel Turntable- it’s specifically designed
The Stainless Steel Turntable is just one of the products that we are proud to supply at SSME and is available in various sizes.
We supply the Stainless Steel Turntable in a range of sizes to make it easier for you to find products that will fit perfectly within your industrial setting. When it comes to accumulating products evenly, you cannot go wrong with the Stainless Steel Turntable- it’s specifically designed
Steel Turntable- it’s specifically designed
The modular belt conveyor offers a reliable versatile solution to many conveying applications.
The modular belt conveyor offers a reliable versatile solution to many conveying applications.
The modular belt conveyor introduces a flexible conveying solution that can, due to the nature of the belt itself, convey
The modular belt conveyor introduces a flexible conveying solution that can, due to the nature of the belt itself, convey
2 FDPP - www.fdpp.co.uk
sizes.
products through inclined as well as horizontal and helical paths.
products through inclined as well as horizontal and helical paths.
Space and loads permitting, 90 and 180 degree turns enable products to be conveyed on winding routes through production areas.
Space and loads permitting, 90 and 180 degree turns enable products to be conveyed on winding routes through production areas.
Stainless steel mixer tumblers are available in three sizes, including 300 Litre, 450 Litre and 600 Litre. They are perfect for mixing dry and wet ingredients.
A mixer tumbler for food can effectively save on labour costs and increase production efficiency. Instead of mixing ingredients in smaller batches by hand, the mixer tumbler will automatically rotate a larger quantity of products at a faster rate.
Features
• 304 stainless steel construction
• Open frame to aid cleaning & maintenance
• Direct shaft drive operation
• Available with stainless steel lid if required
• Variable speed controls
• Mobile or free standing
Description:
• Tip height to customer specification
Our Atomiser Sanitising Conveyors have been designed for the sanitization of the outer surfaces of various products being transferred between low and high care areas.
Operation:
Though stainless steel mixers are designed to boost productivity in the food processing industry, they come with variable speeds – allowing you to choose how quickly the drum rotates. With the addition of a timer control panel you can also program the tumbler to shut off after a specific number of revolutions, saving time and effort.
As well as conveniently marinading ingredients, a stainless steel mixer tumbler enhances the safety of your food processing plant by ensuring no food ends up on the floor.
A huge variety of products can be transported through the Sanitising Conveyor, such as boxed or bagged food ingredients like vegetables, sauces, coatings, blocks of cheese, the list is endless
The drum can also be tilted to make it easier to unload food goods. This not only helps to keep
The solution tank is automatically filled with a pre-dosed mixture of water and sanitiser using a Dosatron water powered dosing pump. When a product is placed on the in-feed roller conveyor a sensor gives a signal to the control panel and the conveyor belt will start. Then using compressed air the mixture is then supplied to five atomiser nozzles which are positioned above and below the conveyor belt. These produce a mist within the tunnel giving total coverage of all surfaces of the products that are
product wastage to an absolute minimum but it makes it easier to clean too.
To prevent cross-contamination, you must give the drum a quick wipe-down inside between uses. Then, at the end of the day, it will need to be thoroughly cleaned, ready for the next day. As a result of being made from grade 304 stainless steel (a material that’s resistant to both corrosion and oxidation), all you need is warm water, a mild soap or detergent, and a soft cloth or sponge to gently wipe the surface clean.
conveyed through the tunnel. The control panel has a built in inverter which allows you to control the speed of the belt and ensures that a wide range of products can be safely passed through the system ensuring that hygiene routines can be carried out quickly and reliably. Atomising sanitization is very efficient as each nozzle only uses .8 litres of solution per hour and with the integral gravity recirculation system the use of solution is kept to a minimum and your products will not come out of the tunnel dripping with water.
At stainless steel Manufacturing & Equipment ltd, design and manufacture a wide range of stainless steel equipment for the food and pharmaceutical industries. Our design team have over 25 years of experience and have worked on projects for many of the major food and pharmaceutical manufacturers. We are based in the West Midlands, just 3 minutes form Junction 10 of the M6. All our products are manufactured in house and we are the UK agent for the SCM boot washer and hygiene station range. We pride ourselves in manufacturing good quality products at competitive prices and as well as our standard range
At stainless steel Manufacturing & Equipment ltd, design and manufacture a wide range of stainless steel equipment for the food and pharmaceutical industries. Our design team have over 25 years of experience and have worked on projects for many of the major food and pharmaceutical manufacturers. We are based in the West Midlands, just 3 minutes form Junction 10 of the M6. All our products are manufactured in house and we are the UK agent for the SCM boot washer and hygiene station range. We pride ourselves in manufacturing good quality products at competitive prices and as well as our standard range
We will manufacture items to meet customer specific requirements.
We will manufacture items to meet customer specific requirements.
For more information or the place an order
Please Call: 0121-661-6346 or Email: sales@ssmeltd.co.uk
For more information or the place an order
Please Call: 0121-661-6346 or Email: sales@ssmeltd.co.uk
MacClancy and Sons Ltd has become Boss Products UK, a proud member of the Boss Industrial Group.
Located in Strathaven, Scotland, they are strategically positioned to serve clients throughout the United Kingdom and the Republic of Ireland.
This exciting new chapter allows the company to forge international partnerships and expand their reach, ensuring that manufacturing facilities in these regions have access to the safest and most innovative fire and explosion solutions available.
Their extended range of offerings now includes the cutting-edge Vigilex Explosion Protection Systems, Boss Process Compression Couplings, VDL Industrial Products and the Raptor Spark Detection and Extinguishing Systems.
With operations commencing on October 1, 2024, Boss Products UK invites you to explore the exciting opportunities this development presents.
Boss Products supports industrial filtration and bulk material handling systems with a full line of integrated Fire and Explosion Mitigation solutions- including Prevention, Isolation, Diversion, and Venting.
The flameless explosion venting device VIGIFLAM Vi is designed in a rectangular shape and consists of three main components: the body, a metal filter composed of several layers to cool flames, and a new innovative explosion panel. This stainless steel membrane is weakened in the middle allowing it to rupture when excessive overpressure occurs inside the enclosure intended to be protected.
The purpose of the VIGIFLAM Vi is to neutralize the flame effects produced during an explosion, which would typically vent through a standard explosion panel. By containing the flames, it helps protect both people and property within a building or room.
The VIGIFLAM Vi is specifically designed for conveyors – bucket, belt, chain, and screw conveyors – due to its compact and efficient design, making it suitable for protecting such equipment in industrial settings.
Boss Products UK has the expertise you need to keep your facilities and personnel safe.
To learn more about how your business can benefit from their fire and explosion protection solutions, contact Boss Products UK today.
Royston, Hertfordshire, UK – 26th November 2024 – Mettler-Toledo Product Inspection, a global leader in product inspection technologies, is excited to announce an informative webinar titled “Superior Inspection of Canned Good with X-ray Inspection.” This highly anticipated event will take place on Wednesday, 22nd January 2025, at 8:00 AM and 2:00 PM UK time.
This must-attend webinar will equip food manufacturers with essential knowledge to overcome the challenges they face in modern canning environments, where high speeds, evolving regulatory standards and the complexities of foreign body detection can make achieving both product quality and efficiency difficult.
The one-hour webinar will look in depth at the following topics:
• Foreign Body Detection & Product Integrity: Manufacturers often face challenges detecting contaminants in cans due to packaging materials or variations in can orientation. The webinar will show how x-ray inspection systems provide precise, automated detection of a wide range of foreign body contaminants regardless of can type (2-piece or 3-piece ring pull). These systems also perform multiple integrity checks in a single pass - verifying fill levels, identifying canning deformities and confirming seal integrity.
• High-Speed Quality Control: Highspeed canning lines can make it difficult to maintain inspection
accuracy and manage product rejects. The webinar will explore how x-ray technology handles these demands with robust line integration, delivering fast, reliable inspections to avoid production stoppages and reduce waste, even at high speeds.
• Real-Time Demonstration: Attendees will see x-ray inspection in action during a live demo on a high-speed test track, showcasing how the systems can be seamlessly integrated into real production environments. The demo will highlight continuous, automated quality checks with minimal disruption to operations.
• Data Management for Enhanced Efficiency: With today’s fastpaced production lines, efficient data management is crucial. The webinar will also explore how x-ray systems can integrate with ProdX™ data management software, allowing real-time monitoring and reporting to streamline audits, reduce human error and provide a comprehensive inspection record for compliance and due diligence purposes.
The webinar will be presented by Adam Green, Market Manager at Mettler-Toledo Safeline X-ray, who has extensive experience in helping global manufacturers overcome the unique challenges of high-speed canning processes. Adam will share his insights on optimising x-ray inspections, achieving compliance and enhancing production efficiency, all without sacrificing speed or quality.
“Canned products are essential across the food and pet food industries, but the demands of high-speed canning can make maintaining quality and safety extremely challenging,” said Adam Green, Market Manager, MettlerToledo Safeline X-ray. “We are excited to present this webinar in order to help canning companies address these challengesproviding manufacturers with the tools they need to improve efficiency and achieve compliance while maintaining high product quality standards.”
Attendees will also have the opportunity to engage in interactive polls throughout the session, gathering insights into industry trends and challenges faced by peers. Additionally, a Q&A session will allow participants to address specific concerns and ask about how the Mettler-Toledo solutions can be applied to their production lines.
Following the webinar, attendees will be able to send in their own cans for validation testing to see how their products perform in realworld production environments.
Register now by clicking here to reserve your spot and gain valuable insights into optimising your canning line for the future or visit: www.mt.com/xray-cans
About METTLER TOLEDO
METTLER TOLEDO is a global precision instruments and trusted solutions provider, across a large range of industries. With a focus on driving efficiency and innovation,
the company aims to deliver value to its customers through solutions that help to boost productivity, combat rising manufacturers’ costs and embrace digitalisation.
The METTLER TOLEDO Product Inspection division designs and manufactures both standard and customised inspection solutions, prioritising product safety, brand protection and quality assurance for food, pharmaceutical and chemical brands. Its solutions help to empower businesses to optimise operations, reduce costs and embrace digital transformation while meeting regulatory compliance. With a focus on safety and precision, the innovative solutions from METTLER TOLEDO help to deliver measurable results, enabling manufacturers to maintain the highest standards of product integrity and consumer trust. By partnering with METTLER TOLEDO, manufacturers will have
the opportunity to navigate the challenges of the modern business landscape and achieve sustainable growth.
With cutting-edge foreign body detection solutions, METTLER TOLEDO provides advanced holistic technologies that automate critical processes and help to mitigate recall risks. Metal detection and x-ray inspection technologies detect and reject contaminated product, plus support product quality and brand protection. Precision checkweighing technologies help manufacturers identify costly over-fills and/or avoid potentially brand damaging under-fills, thus assisting to improve production line efficiency. Vision inspection solutions further enhance the METTLER TOLEDO offering by detecting label defects, reducing the risk of rework and product recalls. To facilitate realtime monitoring and digitalise food safety compliance on a global scale,
METTLER TOLEDO provides the proprietary and innovative data management software, ProdX™.
The range of METTLER TOLEDO product inspection solutions are more than just technological innovations – they’re strategic assets that support business success by helping to enhance productivity, reduce costs and embrace digitalisation. As a trusted partner, the company is focused to delivering value and driving industry excellence for its clients worldwide. METTLER TOLEDO actively supports sustainability goals by providing solutions that help customers minimise food waste, reduce energy consumption and optimise resource utilisation throughout their operations, contributing to a more sustainable future for the industry.
For more information, please visit: www.mt.com/pi-pr
Gellert freeze dryers are the perfect solution for manufacturers looking for a reliable and scalable option for regulated food production. With a notable shift towards the freeze-dried product market, manufacturers and consumers alike are recognizing the benefits of this process. By reducing, or removing, the need for cold chain handling, manufacturers can reduce transportation and storage costs, and as freeze-dried material is much lighter than frozen or refrigerated product, this further lowers costs. Additionally, freeze dried products not only take less energy and cost to store, but they also maintain the biological benefits and flavours of the raw product whilst extending shelf life.
Gellert freeze dryers offer a controlled and repeatable manner for in-situ freeze drying directly on the shelves, ensuring the product maintains its shape, structure, and nutritional value. Gellert has developed a range of freeze dryers with ease of scale-up, user requirements, and operation in mind, making them versatile and popular in the industry.
Some of the beneficial features of Gellert equipment include AutoDry, an intuitive feature that allows users to input their desired temperature differential between the product, sample, and shelves, ensuring the sample can be dried using the AutoDry feedback mechanism, optimizing drying cycles.
The chamber, condenser, shelves, and shelf stack can all be constructed from 316L stainless steel for product contact, and a hybrid cooling system is also available on larger equipment, to utilize defrost water by re-heating via the freeze dryer compressors, saving energy and costs.
The most common applications that Gellert’s freeze dryers are used for include: -
• dairy products • fruits and vegetables
• pet food and pet treats
All Gellert systems are manufactured in Europe and strictly adhere to compliance regulations such as F-gas.
Biopharma Group is the exclusive distributor of Gellert freeze dryers across the UK, Ireland, and France. Both Biopharma Group and Gellert well respected and renowned companies, combining years of lyo industry experience. This winning combination allows the Biopharma group team to help you select the best freeze dryer to meet your specific need and Gellert has accrued a high level of practical experience and in-house expertise, developing an array of different models and configurations to satisfy a broad range of food production purposes.
Contact Biopharma Group’s product specialists to discuss your requirements or request more information.
www.biopharma.co.uk
• Improved efficiency & reduced drying time
• Replicable batches
• Replicable batches
• Improved efficiency & reduced drying time
• Replicable batches
Leading voices from the worlds of aerospace, rail, and energy joined Snap-on Industrial at its Insight 2024 event to discuss the biggest challenges facing industry in the UK and Europe and seek potential solutions.
Gathering at the Red Bull Racing headquarters in Milton Keynes, these captains of industry took part in a Tool Control discussion that highlighted how streamlined tool management systems are solving three of their most persistent problems: reduced productivity, tool loss and damage, and inaccurate reporting.
Challenging economic conditions in the post-pandemic landscape have increased pressure on organisations to optimise their operations, reduce downtime, and save money.
That’s where Snap-on’s suite of all-in-one solutions is meeting a critical need. Powered by L5 Connect software, each tool control system in the Snap-on portfolio allows companies to always have complete visibility of their tool inventory. Not only does this mean they can meet health and safety requirements and CAA guidelines, but it also provides valuable insights that help them save time and money.
Snap-on prides itself on the close relationships it has with its partners, and every new product has been developed in response to customer feedback and urgent industry need.
The discussion panel included representatives from Virgin Atlantic, Lufthansa, and Safran
Virgin Atlantic looked to Snap-on to aid with the transition from a fragmented workforce using individual toolkits to a centralised system with all engineers using automated tool control boxes (ATCs). The airline now has 15 ATCs at its Heathrow site.
While embedding the new system required an initial adjustment period, the ATCs have now become an essential resource for employees at every level. Managers can now benefit from a forensic level of insight, which allows them to evaluate how each box is being used as well as quickly identify breakages. Tracking breakages over time also highlight patterns, which the procurement team can use to anticipate future
breakages, buy new tools, and have them ready for rapid deployment.
The result is a system that works with the existing workforce and optimises performance without any service interruption. As Andy Currey, Tooling & GSE Manager at Virgin Atlantic, said: “Everybody in our workforce was already buying tools from Snap-on so it was a natural fit.”
Aerospace supplier Safran Landing Systems approached Snapon with a similar concern; the company needed to standardise its operations and move engineers away from individual toolboxes to a more efficient shared system.
“Accuracy is exceptionally important for us,” said Neil Bevan, OL Assembly Flow Line Manager at Safran. “While the cameracontrolled system roll-out required an adjustment at first, it’s now universally appreciated and has transformed the level of control we have over our tooling.”
Lufthansa has found that Snapon meets offers three essential benefits: full control, accuracy, and insights. The airline uses Snapon ATCs in its hangers and really put the system through its paces, intentionally trying to manipulate it and force errors (unsuccessfully!) Now, the team know exactly who has each tool, when it was taken from the box, and when it was returned. They also always know the status and availability of the tools monitored by the system. From this data, the team can determine and plan future tool requirements.
Richard Packham, Director UK & Europe for Snap-on Industrial said: “In every industry, our customers are under increasing pressure to operate cost-efficiently and improve productivity without sacrificing quality. We’re proud to help them rise to this challenge by providing intuitive technology and versatile tool systems that offer businesses complete visibility, accurate tracking, and invaluable insights that they can use to optimise their operations.”
To further meet the needs of industry in 2024, Snap-on announced the launch of two new products at the event:
The ATC FlexHub was one of the most sought-after product ideas floated at the previous year’s event in 2023. The Snap-on team took that feedback and ran with it, taking elements of its existing AutoCrib set-up, integrating it with L5 Connect, and enhancing with additional features after deployment in test locations before its official launch, all within 12 months.
Engineered to work at the speed of work, the FlexHub improves tool organisation and visibility. A modular system, the FlexHub is equipped with several different lockers and drawers so that it can hold tools of different shapes and sizes. It’s fully configurable and can grow with you, making it a futureproof purchase. Up to four frames can be configurated currently, but this will soon be extended to 10 or more frames.
Using an attached or wireless scanner, users can unlock tools from multiple lockers at once. When ready to return, users can simply scan the tool and the relevant locker will automatically reopen for easy storage.
The ATC FlexHub also offers an elevated level of control for calibrated items. Users can manually strike tools that require calibration and automatically send an email notification to the relevant team. The locker
containing this tool will then be locked to all other users until the item can be safely removed for calibration.
Powered by L5 Connect, the ATC FlexHub provides businesses with a full audit trail. This is particularly useful when it comes to calibration; administrators can see who flagged the item as requiring calibration, when that decision was made, and how long it took for the tool to be returned to active service.
Let’s talk torque.
Snap-on is the world’s leading torque manufacturer and offers an expansive range of torque screwdrivers, wrenches, and more.
Each torque tool can now be controlled and monitored remotely via ControlTech. This innovative system enables engineers to save time and effort while still ensuring all work is being completed safely and correctly.
ControlTech operates in multiple languages and can store a wealth of data; it can hold up to 1500 readings and 100 pre-sets as well as allowing engineers to choose to measure angle, torque and angle, or torque then angle. All this information can be downloaded and emailed as a CSV file at the click of a button.
Each Bluetooth-enabled tool can connect to the system via app or API and data will automatically synchronise as soon as it is within 100 metre range. While in use, the tool will flash, vibrate, and beep once the target torque is reached.
By continually tracking the tool and taking readings, ControlTech provides an exceptional level of control as well as checking work quality, flagging bolts that may have been over-tightened and when bolts in a sequence may have been missed.
For more information, please visit https://snaponlevel5.com, call 01536 413904, or email ukindustrialmarketing@ snapon.com
United Air Power Ltd (UAP) were established 26 years ago, specialising in Compressed Air, Nitrogen Generation and Process Cooling. Working within a wide range of industries UAP offers bespoke, reliable solutions.
Nitrogen gas plays an important role in the food industry from process to packaging. By replacing the oxygen with nitrogen, food will have a longer shelf life and the ‘just-made’ flavour and appearance can be maintained.
When tasked to provide a reliable source of Food Grade Nitrogen Gas for food production, reliability of supply can create logistical difficulties along with procedures that must be established to monitor and manage the utility. Additionally, safety and handling concerns need to be considered. The cost of addressing these issues can be high and difficult to budget for, while the market price of Nitrogen gas and supplier rates change continually. The environmental impact of truckbased deliveries is another important consideration for carbon footprint reduction.
The ideal solution lies in a range of UAP on-site gas generation systems which UAP can design, supply and install, to meet the customer’s specific needs. This enables users to produce their Food Grade Nitrogen gas on demand on the premises, under their complete control. As a result, companies can generate as much or as little nitrogen as needed, at a fraction of the cost, thereby profitably and sustainably supporting all of the production requirements.
On-site nitrogen generation separates nitrogen from compressed air for use directly at the user’s location. Our on-site nitrogen generation system being modular in design, offers a range of output flows from a few litres per minute to in excess of 130 m3/h from a single module!
The UAP integrated nitrogen generation system pre-treats the air from a standard industrial compressor which is then essentially “sieved” so that oxygen and other trace gases are removed, while nitrogen is allowed to pass through to the application as the product gas. Air separation is not a new idea, but the radical Pressure Swing Adsorption (PSA) design and control systems employed on the Parker NITROSource Plus nitrogen
Nitrogen gas plays an important role in the food industry from process to packaging.
generator range has maximised Nitrogen output and reduced compressed air consumption to achieve even higher levels of efficiency than before.
The sector leading Parker NITROSource nitrogen generation system can reduce costs by up to 90% when compared to traditional methods of supply with a payback period on capital investment typically being achieved within 12- 24 months. Any safety concerns associated with bulk liquid storage or manual handling and changing of heavy high-pressure cylinders are also eliminated.
Using the latest Parker nitrogen generation technology, UAP can design, install and maintain tailor-made solutions to meet the customers nitrogen gas demands. The NITROSource Plus equipment at the heart of our on-site generation systems carry full third-party validation ensuring the generated nitrogen gas not only meets the food grade standards, but in fact exceeds the quality required. These fully scalable systems provide a low cost, safe and efficient continuous source of N2 food grade gas on demand.
For further information and a free no obligation gas survey contact UAP for details.
Packaging Innovations & Empack 2025, the UK’s premier packaging event, is fast approaching.
Scheduled for 12–13 February 2025 at the NEC Birmingham, the event is set to welcome over 430 exhibitors and 7,000 attendees, making it an unmissable opportunity for professionals across the packaging sector to explore cutting-edge innovations and connect with industry leaders.
This event is a unique platform to discover technologies and sustainable solutions that are shaping the future of packaging. Attendees can interact with leading brands such as Waitrose, Diageo, and Kellanova, while gaining insights into trends like smart packaging, sustainable materials, and food service innovations. A must-see feature is DEFRA’s Extended Producer Responsibility (EPR) Clinic, providing clarity on new regulations and their impact on the packaging sector.
Networking remains at the heart of the event, offering invaluable
opportunities to collaborate with decision-makers and innovators. “The event allows businesses to stay ahead of industry shifts while tackling critical challenges like sustainability,” says James Montero MacColl, Senior Marketing Manager at Easyfairs UK.
Each year, Packaging Innovations & Empack evolves to remain at the forefront of the industry. The Smart Packaging Zone, debuting in 2025, will spotlight technologies like NFC chips, RFID tags, and augmented reality that enhance product tracking and customer engagement. Meanwhile, the Innovation Gallery and Packaging Start-Up Awards, sponsored by Ocado Retail, will showcase groundbreaking solutions pushing the boundaries of packaging design.
Over 70 expert speakers will present across the Circular Economy, Supply Chain, and Innovation stages, tackling issues such as sustainable materials, AI in design, and the
growing importance of the circular economy. Highlights include Miguel Arevalo from Google on plastic-free packaging, Tey Bannerman from McKinsey Design on AI’s role in creativity, and Lowelle Bryan from WRAP addressing sustainability challenges.
The Future Trailblazer Awards will celebrate emerging leaders in packaging, offering winners a oneyear membership to the Institute of Materials, Minerals, and Mining (IOM3). This initiative underscores the importance of fostering new talent to drive the industry forward.
Don’t miss this chance to gain actionable insights, connect with top brands, and explore technologies redefining packaging. Register now for your free pass and prepare to shape the future of packaging.
www.packagingbirmingham.com
• Versatile use with high efficiency
• Mobile solution: easy handling thanks to improved chassis
• Optimized design without gaps: simplifies cleaning, reduces maintenance
Essen (Oldenburg), November 26, 2024 – For the first time, Vogelsang GmbH & Co. KG is launching a wine pump that features a VY pump. It stands out with its modified, modern design, pulsation-free operation and the gentle conveying of the grapes and wine without any foam. “Our customers in the wine industry expect a solution that is not only efficient, but also flexible and user-friendly. With the new wine pump with an integrated VY
pump, we offer them exactly that,” says Harald Vogelsang, Managing Director of Vogelsang GmbH & Co. KG. The company presented the new pump for the first time at the SIMEI in Italy.
The wine pump is particularly versatile and capable of conveying liquids of different viscosities. This makes it suitable for handling all the important wine production processes – including decanting the wine from tanks, conveying the pomace after fermentation and maceration, and bottling.
Increased flexibility with simple operation
The wine pump is available in two sizes and five variants. It can be configured differently, depending
on size and flow rate requirements. The solution is also designed for use in confined spaces that are difficult to access. “The new chassis has now a brand new functional design, which makes it much easier to transport the pump,” says Claudio Ragusa, Sales Engineer at Vogelsang Italy. “This is our response to our customers’ desire for greater flexibility and ease of use.” The new design allows users to easily move the pump between different production areas.
The pump’s improved, gap-free design prevents material deposits – which makes cleaning easier and reduces maintenance work. The control technology simplifies daily handling and makes it possible to exchange data on pressures, flow
rates, and work cycles. The pump is also equipped with a user-friendly touchscreen and can be controlled via an easy-to-use app that offers functions tailored to the wine industry.
VY Series: high-performance pump for wine production
The performance of the VY pumps for the wine industry ranges from 10-700 hl/h at a maximum pressure of 10 bar, depending on the application. The pumps consist of a flowoptimized, one-piece housing and therefore offer a high level of efficiency. The soft, elastomercoated rotary pistons ensure a particularly gentle pumping process. The delivery direction of the pumps can be reversed, allowing containers to be filled or emptied as required. The solution is also characterized by its high suction power, reduced noise emissions, and ease of service and maintenance – the latter is also ensured by the integrated QuickService concept.
For more information, visit: vogelsang.info
“The new chassis has now a brand new functional design, which makes it much easier to transport the pump,” says Claudio Ragusa, Sales Engineer at Vogelsang Italy.
Managing resource consumption, such as energy, water, and raw materials—is crucial for improving profitability, sustainability, and operational efficiency. As global pressure to reduce carbon footprints increases, businesses must adopt innovative technologies to monitor critical metrics like energy, electricity, gas, water, temperature, humidity, and air quality. Elcomponent Ltd, an expert in metering and monitoring solutions, provides tools that help optimise energy management, reduce carbon emissions, and streamline production processes.
Energy consumption is a major operational cost. Elcomponent’s monitoring systems offer realtime data on electricity, gas, and heat usage, enabling businesses to identify inefficiencies and optimise consumption. This results in reduced costs and a lower carbon footprint, while
helping companies comply with stringent energy regulations and sustainability goals.
Water is essential but often poorly managed in food production. By using Elcomponent’s advanced water metering, companies can track usage, detect leaks, and optimise water consumption during cleaning, cooling, and processing stages. This helps conserve water, reduce waste, and lower operational costs.
Precise control of temperature and humidity is vital for product quality. Elcomponent’s sensors ensure optimal conditions for both production and storage, while air quality monitoring helps maintain safe working environments and prevent contamination, contributing to product integrity and worker safety.
Continuous monitoring also aids predictive maintenance by detecting potential failures before they happen. This minimises downtime and extends equipment lifespan. Moreover, data on energy use can uncover opportunities for further optimisation, contributing to overall process efficiency.
Elcomponent’s monitoring solutions empower food processors to optimise energy use, conserve resources, and meet sustainability goals. By implementing these systems, businesses can reduce costs, improve operational efficiency, and contribute to a more sustainable future.
Elcomponent Ltd
sales@elcomponent.co.uk www.elcomponent.co.uk
• In-house Design and Installation
• Custom Analytics and Data Services
• Production, Air Quality, Occupancy
• Wired and Wireless Technology
• Web Analysis Platform
• Electricity, Gas, Water, Heat, Steam, PV
Third party outsourcing is playing a critical role in supporting the continuing growth of the UK frozen food industry, according to the BCMPA, the Association for Contract Manufacturing, Packing, Fulfilment & Logistics.
The BCMPA says many of its members are investing in facilities and technologies for manufacturing, storage and distribution to help brand owners maximise opportunities with greater supply chain flexibility and resilience.
“Frozen food is undoubtedly one of the success stories of recent years, and the retail value of the market has increased by 50 per cent over the past decade,” said BCMPA CEO Emma Verkaik.
“With on-going cost of living pressures, frozen foods are popular for their value for money positioning, but for brands to deliver this value effectively, it is essential that all areas of their operation from manufacturing to distribution operate as efficiently as possible. This is where local outsourcing
specialists can help, focusing wholly on day-to-day operational issues to enable businesses to concentrate on brand building and sales.”
One recent investment example is cold storage specialist Magnavale, who is currently completing the construction of a new cold store at its premises in Easton, Lincolnshire. The temperature-controlled facility offers multiple pallet ingress and egress points, and has been engineered to prevent bottlenecks, ensuring seamless operations at all times, including peak periods such as Christmas.
Technological advances, such as IoT integration, GPS tracking, and temperature monitoring systems will also play an important role in driving operational efficiencies. Among the BCMPA’s global logistics members, industry leaders are leveraging innovative technologies to deliver advanced visibility and precise control. These capabilities enable comprehensive tracking across various stages, including inventory management,
order fulfilment, recalls, code tracking, mixing, packaging, and manufacturing support.
In addition to frozen foods’ value for money positioning, consumers are being attracted by the increasing choice of products. This includes the introduction of more vegetarian and plant-based products to meet the growing demand for healthier options. Rapid freezing technology offers an important benefit here, ensuring all key nutrients remain in the product.
“An outsourcing specialist can be the perfect partner to any size of frozen food business, from start-ups to established brands,” said Emma Verkaik. “As consumers increasingly seek quick and convenient meal solutions, the rising demand for frozen food options allows BCMPA members to effectively support brands with reliable and experienced suppliers for their frozen food logistics requirements.”
www.bcmpa.org.uk
The Health and Safety Executive estimates that over two million people in Great Britain are exposed to unacceptable levels of noise at work, with food and drink production being amongst the biggest culprits. Many of the processes that emit the most noise happen during manufacturing, but there are ways that plant managers can reduce it. Here Tom Cash, director at automation parts supplier Foxmere, explains how to lower noise and improve safety on food production lines.
The food and beverage industry is vulnerable to noise-related risks due to the sheer variety of equipment involved.
Filling machines, conveyors, palletisers and refrigeration units all contribute to a constant cacophony. The same goes for the production of products like beet sugar, breakfast cereals and frozen fruits.
According to the Centers for Disease Control and Prevention (CDC), around 46 per cent of manufacturing workers have been exposed to hazardous noise. What’s more, the same report highlighted that close to 14 per cent of manufacturing workers had some degree of hearing loss.
These hazards reflect how important it is for food manufacturers to adhere to legal obligations designed to protect employees and create safer working environments.
In the UK, the Control of Noise at Work Regulations 2005 provides a legal framework for managing noise in the workplace.
These regulations require employers to eliminate noise at its source wherever possible or reduce it to the lowest level reasonably practicable — referred to as “so far as is reasonably practicable” (SFAIRP).
According to the second edition of a guide from the Health and Safety Executive, titled ‘A Recipe for Safety: Health and Safety in Food and Drink Manufacture HSG252’, page 49 defines two critical exposure thresholds.
At 80 decibels (dB), employers are required to inform workers about noise risks and offer hearing protection to those who request it. At 85 dB, stricter measures must be implemented, including controlling noise through quieter machinery or soundproofing.
If these options are not feasible, hearing protection zones must be established, clearly marked and enforced. In addition, health surveillance is also required for workers exposed to hazardous noise levels.
Manufacturing workers are exposed to several noises loud enough to cause noise-induced hearing loss (NIHL) and this Applied Sciences paper cites compressors, pumps, motors, fans, turbines, vents, steam
leaks and control valves as some of the more significant sources of workplace noise.
However, modern automated machinery is often designed to minimise vibrations and reduce mechanical noise, improving both the working conditions for operators and the durability of the equipment.
A prime example is Clippard Spider valves, known for their exceptionally quiet operation with lower noise and vibration levels. These valves are especially effective in packaging lines, where pneumatic actuators perform tasks like bottle capping or product sorting.
Another example is Dematic’s global launch of its noise reduction portfolio. These products are specifically designed to address noise in environments like packaging lines and material handling systems, all of which are sources of high noise levels on food and beverage lines.
The portfolio uses 3D noise mapping to diagnose and visualise noise levels in a facility, much like how a heatmap identifies temperature hazards, providing a clear, data-driven understanding of the acoustic challenges within the space.
Dematic then recommends quieter equipment, such as rollers, slats and belt conveyors, which are designed to reduce noise levels by up to 15 dB.
Despite these advancements, 28 per cent of workers in manufacturing report not wearing hearing protection in noisy
environments — that’s according to the aforementioned CDC report.
This alarming statistic reiterates the importance of integrating quieter machinery and automation systems, which address noise at its source rather than relying solely on personal protective equipment (PPE).
That’s not to say PPE isn’t necessary, because it is. However, automation aligns with best practice for reducing noise exposure, especially when stricter measures are required for machinery louder than 85 dB.
As food and beverage manufacturers must focus on workforce health and safety, integrating quieter automation technologies is crucial not only for meeting regulatory standards but also for enhancing operational efficiency.
Partnering with experts like Foxmere ensures that your production runs smoothly, safely and in compliance.
Contact Foxmere for a noobligation quote on automation equipment ranging from replacement or obsolete parts to complete systems.
In the UK, the Control of Noise at Work Regulations 2005 provides a legal framework for managing noise in the workplace.
New optical sensors feature enhanced detection capabilities and faster commissioning with innovative Power PinPoint LED technology.
The Power PinPoint LED from Leuze emits the maximum light power from a very small surface. The new light source technology can be used to finely position stacker cranes, among other things, using diffuse reflection sensors.
Aligning and commissioning sensors is often very time-consuming. The Power PinPoint LED from Leuze now makes this much quicker and easier. The sensors’ light-emitting diode emits its maximum light power from a very small surface. The Power PinPoint LED generates a light spot that maintains its size, shape and homogeneity over the sensor’s entire working range enabling simple and fast commissioning. This technology also increases process reliability through precise detection. The innovative light source is
available for the first time with Leuze’s new 33C and 35C sensor series as well as the 25C, 3C and 5B diffuse sensor series.
Retro-reflective photoelectric sensors achieve a higher function reserve with Power PinPoint LEDs,
especially with small reflectors. Retro-reflective photoelectric sensors with Power PinPoint LEDs are ideal for object detection in harsh food industry environments.
Small, bright and precise
Sensors with Power PinPoint LEDs generate a small, round light spot with sharply defined contours.
This gives the sensors extremely reliable detection capabilities and enables precise start and end detection
of an object with pinpoint response behaviour during object tracking. Even small objects are optimally
detected by sensors with Power PinPoint LED thanks to their precise detection capability. Another
advantage is that Retro-reflective sensors with Power PinPoint LEDs have higher function reserves forapplications with small reflect ors or large distances. Also, several through-beam photoelectric sensors can be used in parallel with increased detection reliability as their compact light beam minimizes diffused light.
The Power PinPoint LED also
reduces the possibility of unwanted reflection to ensure highly reliable detection.
Throughbeam photoelectric sensors also demonstrate the innovative light source’s strengths. Sensors with the Power PinPoint LED provide extremely reliable detection even in confined spaces – for example battery cells in a filling station.
Power PinPoint LED in stainlesssteel sensors
The Power PinPoint LED is already used in the 33C and 35C sensor series, amongst others. Both series’ ranges include diffuse sensors, retro-reflective sensors and through-beam photoelectric sensors in smooth stainless-steel housings. These are particularly suitable for hygiene-sensitive production and packaging processes. Therefore, they can be used for almost all applications in harsh, wet or hygiene-sensitive environments. The sensors can withstand high mechanical loads and intensive cleaning processes. The 33C and 35C series also include special solutions for packaging processes – including sensors for detection through film, clear glass or PET.
www.leuze.com
Features & Benefits of the MaxiPrime Stainless Steel Pump:
• Handles pastes up to 10,000 poise viscosity ‘COLD’
• Transfer products cleanly, quietly and efficiently
• Eliminates Product Waste
• Simple and Safe Operation
Pastes and high viscosity products pose a challenge as they do not flow easily, preventing the pump from priming properly and causing cavitation, which results in pumping air instead of the product.
The solution is to use a Kecol Maxiprime twin cylinder pressure priming system in conjunction with a Kecol stubby pump, maintaining a positive prime on the pump and thus ensuring that it does not cavitate. As the product level falls, the sides of the drum are wiped clean by the follower plate on the priming system.
• Polished Stainless-Steel pumps or Painted Steel Construction pumps
OPRL has embraced the publication by Defra and the pEPR Scheme Administrator of the Recyclability Assessment Methodology (RAM) for Packaging EPR. Jude Allan, Interim MD at OPRL, described it as valuable clarification both for businesses and for labelling. Allan said: “The arrival of eco-modulation in 2026 will introduce a financial incentive to reduce packaging or to opt for easily recyclable materials. The RAM provides a standard guide on the recyclability
of different packaging materials and formats. The methodology will produce a red, amber or green output, which relates to the ease of recycling at scale. This will help businesses to make effective choices around design, as well as supporting consistent messaging to householders across the UK.“
Clear messaging will be crucial for the success of pEPR – without consumer engagement, lower volumes of waste will be collected, leading to higher costs for producers. To date, OPRL’s labelling metrics have been the only independently assessed system available. Now that the RAM has been published, we will update our Recyclability Assessment Tool to ensure that we fully align with the RAM. Our members will then have access to a truly UK-wide system.”
OPRL research shows that the majority of consumers turn to packaging for instructions
on recycling, so consistent messaging is crucial when it comes to communicating recycling information. Although mandatory labelling is on hold, many brands are still choosing to label packaging products. Allan added: “At such a time of change, brands are looking for help to navigate uncertain waters. Companies know that improving recyclability is a fundamental step towards reducing pEPR costs, but without insight into current and future choices, many are struggling. OPRL’s new Recyclability Assessment Tool is an interactive tool designed to help brands make informed choices around packaging design and reduce financial obligations under pEPR. It analyses a wide range of data, including the size and weight of components, as well as areas like packaging type, materials, and laminations or coatings.”
https://oprl.org.uk
Product Safety
Process Efficiency
Improved Product Yields
Rapid Fault Finding
Full HACCP Certification
Thru-process temperature monitoring solutions for all your cook applications
PhoenixTM Technology
• Accurate IP67 data logger (Type K or T)
• 10 Measurement Points for full oven mapping
• Thermal barrier options to suit cook regime
• Comprehensive thermocouple range
• Standard miniature thermocouple plugs
• Calibrated thermocouple options
• Food trays and thermocouple jig options
• Full lethality (Fo/Pu) and reporting
• Real Time RF Telemetry options
• Local efficient calibration and service support
Phoenix
Michael Stuart, European Sales Director at Anritsu, examines how vision inspection technology is impacting the different stages of dairy production in terms of food safety and quality.
For many years now, the dairy industry has remained within the top three biggest sectors in the food industry across most of Europe. Within the UK alone, a staggering 15 billion litres of milk are produced every year and the industry is worth $5.7 billion at wholesale level.1 With such vast numbers involved, the slightest lapse in food safety could be catastrophic.
Ensuring stringent food safety is of course of the utmost priority across every stage of dairy production. In terms of inspection, equipment such as metal detection is standard on a dairy line. But the variety of dairy products and the various transformational stages they pass through to create a finished product - be it yoghurt, cheese or butter - is enormous. So there are many areas that need to be subjected to careful inspection along the way. Metal detection alone is not sufficient to fully assess the product at each stage.
Whether a dairy business is a small to medium enterprise or a large multinational, the requirement for food safety is the same. However the cost of detection equipment can be prohibitive. Fortunately, the cost of x-ray inspection has come down significantly over the last decade and this is a technology which can be used in a number of different ways and with high accuracy along several stages of a dairy production line. Inspection through the different stages of dairy production In the earlier stages of production,
the risk of physical contamination can be present from the equipment used. Paddles, agitators and conveyors can at times break or begin to disintegrate, allowing fragments to get into the food. As well as this, where there is human intervention, there is the risk of contaminants potentially entering the line. Because most dairy products are still in liquid form at this stage, any foreign bodies quickly sink to the bottom and cannot be easily seen. So X-Ray inspection can be crucial at this stage.
However it’s not always as straightforward as passing the product through an x-ray inspection machine. Irregular or non-homogenous products such as grated cheese, for example, can be challenging to examine. With a traditional single energy Xray system, the “busy” image created cannot always be accurately assessed with std algorithms in order to find any contaminants. In these cases, a dual energy x-ray can be used. A dual energy system creates 2 different x-ray spectra of high and low energy levels. By comparing the absorption ratios of these two spectra it is possible to see what is included in the image in much greater detail and therefore detect if any contaminants might be present.
Moving on to later stages of the production line, it is often the case be that a dairy product has been packaged within a metallised container. Or perhaps a plastic tub with a foil lid, such as a pot of yoghurt. In these cases, inspecting the product using a metal detector is not possible so, again, this is where x-ray technology can be used to see through the packaging.
In terms of the finished product, once everything has been produced, inspected and packaged, there are still ways in which x-ray inspection technology can make a significant impact on a dairy business. Side shooter x-rays for example can be used to measure the fill level in a carton or pot of liquid, to ensure that the correct amount of product is being decanted into each pack. Equipment settings can be optimised accordingly, so customers will get exactly what they pay for each time. Underfilling is legally a big nono, but overfilling even by tiny amounts will quickly add up and amount to significant giveaways over time. All these quality checks can be done simultaneously whilst checking there are no contaminants in the product.
Similarly, producers of irregular products such as cheeses with naturally occurring holes like Emmental and Jarlsberg can benefit from the use of inspection equipment. X-ray technology can be used to ensure the correct weight per slice, taking into account any holes and allowing operators to adjust the machine parameters as needed during production. So as well as detection of contaminants, x-ray inspection has a range of other applications which can actually considerably impact your bottom line by maintaining uniformity and preventing costly giveaways.
Within the UK alone, a staggering 15 billion litres of milk are produced every year.
Machines do of course need to have a very high degree of hygienic design to prevent them posing a contamination risk themselves. High quality machines should be made with antibacterial surfaces. In terms of physical build quality, it’s also advisable to look out for machinery that’s been designed in such a way that if water were to spill onto it, it can’t seep or drip onto the product.
X-ray detection continues to be a growing field in the dairy industry. Beyond food safety and contaminant detection, it is increasingly becoming the primary detection technology for ensuring quality and correct portioning of products. No matter what the product, the complexities of production and the risks to food safety are such that there are many areas along any dairy line that need to be stringently managed.
High quality vision inspection technology can have a huge impact here, preventing risk to consumers, your reputation and your bottom line.
For more information visit https:// www.anritsu.com/en-gb/productinspection
After decades of successful production of baby food and dairy products, Semper AB, a company of the Hero Group, has announced the closure of its plant in Götene. The closure of this facility, which has long been a significant part of Scandinavian food production, marks an important turning point in the company’s history. The building and premises will be taken over by the adjacent Arla Foods plant. Meanwhile, the released factory inventory will be auctioned off in a major online event in mid-February, with complete production lines and selected equipment already available through pre-sale.
The Götene plant has played a vital role for years in manufacturing high-quality baby and specialty foods. It contained some of the most advanced production equipment in the industry, continuously updated through ongoing investments. As a renowned manufacturer and part of the HERO Group, Semper has always placed strong emphasis on modern technology and reliable production processes. As a result, the entire facility’s equipment has been meticulously maintained and regularly serviced. A significant portion of the available machinery, systems, and devices was built or overhauled after 2010, with the most recent systems commissioned as recently as 2019.
To ensure a sustainable approach to the site’s resources, the company has decided to repurpose the existing machinery and systems. Accordingly, an auction will be organized, offering modern equipment – including packaging lines, filling machines, specialized devices, and a wide range of general factory assets. The auction provides companies in the food industry and related sectors the opportunity
to acquire high-performance production tools while promoting the reuse of industrial equipment – an approach that delivers both economic and environmental benefits.
“We are confident that this equipment will continue to contribute to innovation and quality in food production under new ownership,” said Daniel Kröger, Managing Director at Maynards Europe. “Semper’s renowned baby and children’s food was produced and packaged at the Götene plant to the highest standards. Semper was particularly proud of its innovative technology for filling resealable fliptop packaging solutions. The closure of the plant therefore creates lucrative opportunities to acquire top-quality technology in excellent maintenance condition.”
Ahead of the February auction, complete mixing lines, drum dryers, and filling lines for pouches, cans, and flip-top packaging are exclusively available for sale. In addition to systems from manufacturers such as Andritz Gouda, Amixon, and Ruberg, a diverse portfolio of transport and storage equipment is also on offer. This includes ABB palletizing robotics, packaging technology from Cyklop, as well as numerous measuring and cleaning devices.
We are confident that this equipment will continue to contribute to innovation and quality in food production.
Drive electronics from NORD DRIVESYSTEMS is the key to any drive application. With its NORDAC frequency inverters, the system supplier demonstrates its solution expertise also in the fields, where movements must be intelligently controlled. These can be found in various applications, which also have an influence on daily life.
One example is the safe and efficient cutting of food products such as bread, meat or cheese. In every cutting machine used in commerce, crafts and industry, the aim is to precisely control the contact pressure of the relevant food product in the machine. This is made possible by the PLC, integrated in all NORDAC frequency inverters from NORD. It allows to freely programme drive-based control functions. This ensures consistent cutting quality.
Intelligent control functions master industry-specific drive applications
When it comes to bottling liquid food products, speed is an essential factor. NORD frequency inverters ideally meet the great demands on precise speed control. They thus ensure an optimally balanced production process. Furthermore, for example, the NORDAC PRO control cabinet inverter can be integrated via Ethernet. It thereby allows for the remote maintenance of the system. Online tools can thus be used to check components for errors and to evaluate any recorded data of the frequency inverter. This way, NORD ensures high system reliability.
Drive solutions from NORD also take effect when it comes to precise positioning tasks. Here, the company offers its integrated POSICON
module, which, for example, is contained in frequency inverters such as NORDAC PRO. It allows automatic positioning control for different applications such as travelling theatre sceneries for trouble-free theatre performances.
modular range of products meets industry expertise
Solution provider NORD DRIVESYSTEMS develops and manufacturesapplication-specific drive systems from a single source. For that, the company is using its industry expertise with which it supports customers in about 100 industries. The extensive range of modular products consisting of gear units, motors and electronic drive technology forms the basis for the implementation of solutions. The components can be assembled in a modular and optimally matched manner to create customised systems.
The field of drive technology is the newest one of NORD DRIVESYSTEMS, which will celebrate its 60th anniversary next year. Since the beginning of the 1980s, the company has been developing and manufacturing the NORD portfolio for electronic drive control at its site in Northern German Aurich. This comprises the frequency inverters for control cabinet installation, decentralised frequency inverters and motor starters.
www.nord.com/en/home-de.jsp
NORD frequency inverters ideally meet the great demands on precise speed control. They thus ensure an optimally balanced production process.
As a country Spain is well known for its cuisine, with iconic dishes such as paella, patatas bravas, tortilla, Serrano ham and churros, all recognised and enjoyed around the world.
Another famous dish, particularly associated with the southern region of Andalusia, is the cold tomato soup gazpacho. Although less familiar overseas than some of Spain’s other culinary exports, it is hugely popular in its home country.
From humble origins as a summer dish for local farmer and their families, gazpacho has gained popularity with both Spanish families and tourists thanks to its refreshing properties and distinctive fresh taste. As demand has grown, so has commercial production, with large scale modern production beginning in Murcia in the 1990s.
Since then, more and more food and drink producers have added gazpacho to their product range. As well as large suppliers (often supplying heavily pasteurised product in large quantities), recently smaller companies have begun to bring more premium gazpacho and salmorejo products to market.
Salmorejo, which has become particularly popular recently, is similar to gazpacho but thickened with bread, meaning it is eaten from a bowl using a spoon, while gazpacho is usually drunk as a cold soup. Most manufacturers of gazpacho now also produce salmorejo.
These premium gazpacho and salmorejo products are made using good quality fresh vegetables, with a minimum amount of processing, and are often sold as ‘unprocessed’ products, with a short shelf life and higher price, often in smaller plastic bottles which allow consumers to see the product on the shelf. Although 1-litre waxed card and PET bottles remain the most common packaging, larger formats for families, and smaller portions for people living alone or couples without children are also widely available.
HRS Heat Exchangers have been providing pasteurisation solutions for gazpacho for almost 30 years (we supplied out first unit in 1996), as well as heat exchange solutions to help cool vegetables during the
early stages of manufacture, and we have solutions for more viscous salmorejo products.
Because of their thick, viscous nature gazpacho and salmorejo require tubular heat exchangers –rather than plate heat exchangers (PHEs). Depending on the recipe they may contain content such as grains, bread or vegetable fibres (particularly those products designed to be ‘authentic’ or ‘homemade’). Most lines are now used to produce both gazpacho and salmorejo, so equipment needs to be flexible and able to handle the thicker products. In practice this means food grade HRS MI Series multi-tube heat exchanges, designed to maintain product freshness according to the required production capacity.
As a cold soup, keeping the distinctive freshness is a challenge, so any pasteurisation process must be as gentle as possible. That means making it as fast as possible, with the lowest possible temperature lift, followed by immediate cooling. Pressure is typically maintained between 16 and 25 bar, although
higher pressures may be required for salmorejo. This very small temperature gap is required to avoid overcooking the product, and the corrugated tube design of the HRS MI Series allows it to operate within these parameters.
The market for salmorejo and gazpacho continues to grow, and HRS continues to work with key players in the market, including replacing older equipment which is not suitable for salmorejo with more flexible alternatives, supplying new pasteurisers to increase overall production capacity, and providing pasteurising solutions for premium products which maintain the quality of small-batch, top quality brands while ensuring consistency and food safety for the consumer.
To learn more about our pasteurisation solutions for two of Spain’s most iconic culinary creations, please contact us today.
The market for salmorejo and gazpacho continues to grow, and HRS continues to work with key players in the market.
SIG, a leading packaging solutions provider, has announced the sale of 13 filling lines during its participation in Gulfood Manufacturing 2024, held from November 5–7 in Dubai. The deals demonstrate SIG’s commitment to delivering innovative solutions that empower the food and beverage industry.
The sold filling lines cover the company’s entire portfolio of aseptic carton, bag-in-box, and spouted pouch.
Abdelghany Eladib, President & General Manager for India, Middle East & Africa at SIG: “Gulfood Manufacturing 2024 has been an exceptional platform for us to demonstrate our dedication to innovation and sustainability. Securing the sale of 13 filling lines is a testament to the trust our customers place in our solutions. We remain committed to driving the industry forward with pioneering technologies.”
During the event, SIG also showcased innovative F&B products developed at the SIG Customer
Experience Hub, a collaborative space where industry trends are identified, and consumer needs are addressed. The hub enables SIG to support F&B manufacturers and entrepreneurs by creating cuttingedge products and revolutionizing go-to-market strategies.
The event also saw SIG and Almarai launch the campaign “Pioneering Together for 20 Years,” highlighting two decades of collaboration. As the Middle East’s leading dairy and food company, Almarai has recently selected SIG as a strategic partner for its five-year expansion plan, focused on strengthening market leadership and driving sustainable innovation.
On the sidelines of Gulfood Manufacturing 2024, SIG also announced the expansion of its SIG Neo filling machine portfolio, unveiling the SIG Neo Slimline 15 Aseptic, the newest addition to its cutting-edge filling machines for multi-serve aseptic carton packs. Capable of filling up to 15,000 SIG Slimline Bloc carton packs per hour, this machine increases output by 33% compared to SIG’s standard
filling machines for family-sized formats.
Also presented was the world’s first long-life probiotic buttermilk in aseptic carton packs, that MilkyMist, a pioneering dairy innovator from South India, created in partnership with SIG and AnaBio Technologies. This revolutionary innovation represents a transformative leap for the beverage industry, making it possible for probiotics to be seamlessly integrated into shelfstable drinks for the first time, setting a new benchmark in healthfocused packaging technology.
SIG also hosted daily SIG Talks at its booth during Gulfood Manufacturing 2024, featuring global experts who discussed key topics such as packaging material innovations, sustainability, format and channel innovations, machine advancements, digital innovations, and category expansions.
www.sig.biz/en
• Extreme hardness
• Corrosion resistance
• High strain tolerance
• Uniformly applied coatings
• Wear resistance
• Environmentally friendly
• High fatigue performance
• High dielectric resistance (for electrical component applications)
• Plasma resistant coatings
The Peter Schmidt Group presents trends and best practices for food & beverage brands in their PDF “Brands on shelf: how to win in 2025.”
To succeed in the supermarket, food and beverage brands must follow three simple principles: they need to be distinct, clear, and concise. However, when a brand becomes successful, it is quickly copied, diminishing the advantage of uniqueness. The consequence: “Brands are under pressure to constantly reinvent themselves while staying true to their character,” says Inga Wolter, Executive Creative Director at the branding and design agency Peter Schmidt Group. Added to this are the challenges of the overall economic situation and growing consumer uncertainty.
The trend paper “Brands on shelf: how to win in 2025” offers marketeers and brand managers inspiring insights. It focuses on eight trends that brands can leverage in 2025. As Inga Wolter explains: “When cards are reshuffled, every
brand has the chance to be among the winners – if it understands and takes advantage of the changed rules of the game.”
“Analyzing developments in the industry, benchmarking against competitors, and drawing the right conclusions is part of our daily work,” explains Michael Waning, Director Brand Strategy, who supported the evaluation. The agency’s clients include both globally active and wellestablished consumer brands, as well as startups and disruptive players. For all of them, the Peter Schmidt Group is responsible for creating packaging that stands out on the shelf against competitors. “Often, we don’t find the key to surprising new approaches in direct competition but rather in related or even completely different product categories. Our bird’s-eye view of many brands at once helps us with this,” says Waning.
Accordingly, the trends identified
by the agency are quite diverse, and not every trend fits every brand. For classics with decades of presence, it is noticeable that these brands increasingly rely on the power of their iconic design elements: Whether it’s the retro looks of Burger King and Pepsi or the distinctive triangular shape of Toblerone – brands with strong assets use them to build trust and loyalty in a world of endless choices. Of course, these elements are adjusted to the current zeitgeist: through reduction, the characteristic design stands out even more. Other brands, on the other hand, rely on the power of storytelling, use digital extensions, or create new connections to their products through a respectful approach to different cultures and target groups.
The trend paper “Brands on shelf: how to win in 2025” can be ordered as a PDF from the Peter Schmidt Group’s website or downloaded on LinkedIn. http://linkedin.com/ smart-links/AQEzMYDl6prY2Q
(Hall 2.1, Stand A 10). The focus of the company’s presence at the trade fair will be on innovative and sustainable solutions, which optimise the recyclability of packs and minimise the use of plastics – right up to the completely plasticfree pack.
TopSEAL: Attractively packed with less plastic
MULTIVAC offers the widest range of solutions for packing fruit and
vegetable products of all types attractively, efficiently and sustainably – from single machines for smaller cultivation businesses right up to fully automatic lines.
On the MULTIVAC stand will be shown a fully automatic line solution for packing large batches of product, and this line will include the TX 710 traysealer. The machine will be packing fresh berries in environmentally-friendly cellulose trays, which are then sealed with a thin, transparent and compostable film to protect the delicate fruits from being
removed or falling out of the tray. “The traysealer is equipped with sensors and intelligent control technology, which provides constant synchronisation between the infeed of the trays, the sealing process and the transport of the trays within the traysealer,“ explains Franziska Schreiber, Product Manager at MULTIVAC. “This enables the machine to operate continually at the highest level, ensuring that the maximum output and pack quality are assured, while also reducing waste from the process. By using the optional
connection to the dashboards with the MULTIVAC Smart Services, it is also possible to monitor and optimise the production efficiency in real time.” The compact H 130 handling module takes up the filled trays after the packaging process, and it then places these into containers with a high level of speed and accuracy.
The MULTIVAC TopCLOSE™ system or berries enables cardboard trays to be sealed closed in a very simple and environmentally-friendly way, using a labeller to apply self-adhesive labels, without a packaging machine being required. The transparent film label seals the top of the tray closed, while also labelling the pack at the same time. The adhesive is only partially applied to the outer edge of the label, so that it is safe for contact with food. The label is also equipped with consumer-friendly functions such as a tear flap and reclosure feature, and these can be designed for trays of any shape – whether round, square or rectangular. The proportion of plastic in the pack is under 10 percent, and completely plastic-free material combinations are also possible.
The MULTIVAC TopCLOSE™ system uses the L 330 conveyor belt labeller, which enables the labels to be printed with variable data, as well as the print quality to be inspected. The trays are automatically sealed closed “on the run” – at an output of up to 250 packs per minute. This ensures that the delicate food products are processed very quickly, and personnel costs can also be reduced, since the same quantity of product is packed in a shorter time.
The MULTIVAC TopWRAP™ system is suitable for mushrooms and strawberries for example. Here the cardboard trays are filled and then sealed closed over three sides with a transparent film label. The proportion of plastic in the pack is under 10 percent. The label is also available in a cellulose version – so that completely plastic-free packs are possible. The adhesive is only partially applied, so that there is no contact with the product. The L 310 conveyor belt labeller is used for this packaging solution. It automatically seals the packs closed “on the run”, and at an output of up to 150 packs per minute it ensures that the delicate products are processed quickly and efficiently.
Both labellers, the L 310 conveyor belt labeller as well as the L 330, can be converted to different tray shapes and sizes quickly and easily, without any change of tooling being required. In addition to this, a zerodowntime version is available for uninterrupted labelling, as well as various automation options such as denesters, or product infeed and discharge units.
“With our complete solution from one source, which comprises labellers, trays and labels, we want to offer the fruit and vegetable sector completely plastic-free packaging solutions, which are resource-saving and at the same time energyefficient,” explains Ronald Helmel, Business Development Manager at MULTIVAC Marking & Inspection. “This means that today companies in the sector can already meet the requirements of the EU Packaging and Packaging Waste Regulations (PPWR).“
(PresseBox) Muttenz, 27.11.2024
In the near future, bioreactors will have a lasting impact on food production. Especially in the production of cultured meat and plant-based alternatives, these innovative technologies open up completely new perspectives. Just as the introduction of smartphones revolutionised communication, bioreactors could fundamentally transform our view of food production and consumption.
Sustainable innovation through bioreactors
Cultured meat is produced by extracting animal cells and growing them in a culture medium under strictly controlled conditions in the bioreactor. These cells multiply and form muscle tissue, which is then processed into meat products - without the need for animal husbandry or slaughter.
Challenges in organic production
The success of this method depends largely on the precision and stability of the processes in bioreactors. In particular, the control of oxygen content, pH value and CO2 concentration must be precisely adapted to the growth and volume of the cell cultures. A flexible and reliable gas mixing system is crucial here. The mass flow controllers from Vögtlin Instruments offer a solution for these demanding applications, as they can operate with an exceptionally wide dynamic range of 1:1000, e.g. from 0.1 to 100 ln/min.
The solution from Vögtlin Instruments
Vögtlin Instruments supports the food industry with high-precision mass flowmeters specially developed for use in sensitive bioprocesses. The outstanding features include:
Large turndown range: over 1:100 (application dependent) for maximum flexibility.
Versatile programming: up to 10 different gases can be stored in one device.
Robustness: valves that can withstand high inlet pressure and outlet pressure fluctuations.
Reliable protection: IP67 and NEMA 6 protection
Wide choice in materials: elastomers are available in FKM, EPDM or FFKM.
Vögtlin also offers both standalone solutions and OEM systems that can be customised to the requirements of laboratories or production facilities. For maximum user-friendliness, the devices are equipped with a wide range of communication interfaces such as Modbus, Profibus or analogue inputs.
Future-proof technology for a growing industry
With flow ranges up to 1400 ln/ min and a variety of customised solutions, Vögtlin Instruments is a reliable partner for cultured meat producers. Our technologies help to optimise processes in bioreactors
and promote sustainable, animalfriendly and resource-saving food production.
For more information, please visit our website at www.voegtlin.com or contact a Vögtlin flow expert. Telefon +41 61 756 63 314
Retail’s Big Show, taking place from January 12 to 14, 2025, at the Javits Convention Center in New York City. At Booth 3774, Hall 3, Bizerba will showcase its latest innovations in AI technologies, advanced software solutions, and modular hardware designed to enhance operational efficiency and transform the retail experience.
“Our partnerships with industry leaders like Supersmart and Edgify allow us to integrate advanced technologies, ensuring our solutions stay at the forefront of modern retail,” said Andreas W. Kraut, CEO & Shareholder. “By collaborating closely with our partners, we deliver scalable systems that meet today’s needs and prepare retailers for future challenges, helping them remain competitive in an evolving market.”
Bizerba will present advancements in AI technologies, including the
Supersmart Scan & Go System for AI-powered loss prevention, and Edgify, which processes data at the edge to enhance checkout efficiency and the customer experience. These innovations showcase how Bizerba leverages AI to address modern retail challenges.
Additionally, Bizerba will pioneer DeliFresh, innovative software that reduces shrink and ensures food safety compliance in deli environments. By providing realtime monitoring of meats and cheeses, DeliFresh helps retailers maintain freshness while meeting safety standards. Complementing these technologies are Bizerba’s modular, plug-and-play hardware solutions like the K3 Countertop Scale and Q1 800 Commercial Scale, offering flexible, scalable integration for various retail applications.
“NRF 2025 is an ideal platform for
us to show how our technologies drive efficiency while maintaining high standards for IT security and customer satisfaction,” added Ante Todoric, Managing Director Business Unit Retail.
As the industry leader in deli equipment, Bizerba is transforming traditional slicing equipment into intelligent systems. “We are leading the industry in enabling advanced hygiene and safety monitoring across enterprises,” said Joe Hannon, US Business Unit Retail at Bizerba. This allows retailers to meet hygiene standards while improving operational control.
Bizerba invites all NRF 2025 attendees to visit Booth 3774 to learn more about these technologies and explore how they can be integrated into retail operations. Further information about Bizerba can be found at www.bizerba.com
How can you package confectionery and baked goods flexibly in a wide variety of pack formats? With pick & place robots that accurately position each product and systems that effortlessly switch between different packaging materials. Saving precious resources –with virtually no waste. This is our Mission Blue. A true benefit for the climate and the many FMCG manufacturers who have been relying on us since 1966. And for you too. www.schubert.group/en/confectionery-snacks.html
Peltier elements are compact yet incredibly powerful components, adaptable to a wide range of applications. Their unique ability to heat, cool, and transfer thermal energy makes them an appealing choice for both industrial and consumer needs. P&N Europe’s Peltier elements are tailored to meet the customer’s specific requirements. Whether a particular size, shape, or power output is needed, the expert team at P&N Europe is ready to design the ideal solution for any project.
In addition to custom solutions, P&N Europe also offers a variety of ready-to-use Peltier cooling units designed to efficiently heat or cool various applications.
Thanks to their precise temperature control capabilities, Peltier elements are indispensable in numerous industries. In medical technology, they ensure accurate temperature regulation for medical devices and secure sample storage. In the food and beverage industry, they help maintain the
quality of sensitive products by cooling storage and transportation containers. Furthermore, Peltier elements are critical in electronics, providing temperature management for laser diodes, optical sensors, and other sensitive electronic devices.
Experience the precision and flexibility of Peltier technology with P&N Europe.
https://www.pn-europe.com/
Plant Lipids is one of the largest producers of spice oils and extracts in the world.
Based in India, Plant Lipids manufactures and exports essential oils, spice oleoresins, natural food colours, whole and ground sterilized spices to over 85 countries worldwide.
rton Pack S.p.A., a leading Italian company specializing in packaging production for the food industry, has acquired Clifton Packaging Group Limited (‘Clifton’), a UK-based manufacturer of innovative flexible food packaging solutions. Carton Pack is a portfolio company of A&M Capital Europe (‘AMCE’), a Londonbased private equity firm with €650 million of commitments under management.
Founded in 1981 and headquartered in Leicester, UK, Clifton serves a broad range of blue-chip brands, with a particular focus on the wet protein and snacks categories. Clifton has an established reputation for technical innovation in flexible films and pouches, positioning it as a key player in sustainable packaging solutions. Clifton will continue to operate under the leadership of its management team, led by CEO Shane D’Souza.
The acquisition represents a significant milestone in Carton Pack’s strategy to become a leading European food packaging specialist, strengthening its footprint in flexible packaging, expanding into the attractive snacks and protein end-markets and establishing a robust presence in the UK market. The transaction is Carton Pack’s sixth acquisition since 2020 and the third since AMCE acquired a majority stake in the Group alongside the founding Leone family in April 2022.
“We are delighted to welcome Clifton Packaging into the Carton Pack Group,” said Gianni Leone CEO of Carton Pack Group. “The
acquisition represents a vital step in our global strategy to deliver both plastic and paper sustainable packaging solutions on a larger scale to the food industry. This partnership not only expands our product range but also strengthens our capacity to serve clients across Europe and beyond, further reinforcing our commitment to quality, service and innovation.”
Shane D’Souza, Chief Executive Officer of Clifton Packaging, added: “Together, we are poised to redefine the future of packaging by leveraging our combined strengths to deliver unparalleled value to our customers and make a positive impact on the environment. We
will continue to operate under our established brand while benefiting from Carton Pack’s extensive resources and industry expertise, including access to warehousing and distribution in Europe. It’s an exciting time for the Group and we look forward to what the future holds for us.”
Carton Pack was advised by Chiomenti, Weil Gotshal & Manges, Charles Russell Speechlys and Pedersoli Gattai as legal advisers, PWC and EY as accounting and tax advisers, Food Strategy Associates as commercial adviser, Howden as insurance adviser and Ramboll as environmental adviser.
TAILORED SOLUTIONS AND SOLID SUPPORT FOR VARIOUS INDUSTRIES WORLDWIDE
Whatever industry you are in, from plastics to pharmaceuticals and from dairy to aquaculture, you wouldn’t want your production compromised by faltering input of raw materials.
Let DMN-WESTINGHOUSE add reliability to your dry bulk handling processes. Since 1950, we have excelled in designing and manufacturing high-end rotary valves and diverter valves with a stark focus on durability, cleanability and compliance.
Discover your future-proof solution at dmnwestinghouse.com
GREIF-VELOX, the specialist in packaging machinery, proudly presents the VeloFlexLabeler, an innovative and fully automated labeling solution. Developed in collaboration with Moin Robotics, a robotics and automation expert and Bluhm Systeme, a leader in printing and labeling technologies –both based in Germany, the labeler offers precise and flexible labeling for all types of containers, making it particularly suited for full-line systems.
The VeloFlexLabeler enables seamless labeling for a wide variety of containers, regardless of their shape or surface cleanliness. It combines standardized label application with customizable options, such as product details or batch information, and ensures consistent, reliable, and secure labeling.
This compact robotic labeling system is capable of serving multiple production lines simultaneously. Labels are applied independently, with the placement and orientation customizable to specific requirements. Its flexible robotic arm ensures precise labeling of containers in various sizes and shapes, including jerrycans, drums, and IBCs.
With its high degree of automation, the VeloFlexLabeler significantly reduces the manual workload, saves valuable employee resources, increases efficiency, and minimizes errors. Redundancy-enabled printing systems further enhance operational reliability by ensuring no label is missed.
The VeloFlexLabeler is particularly well-suited for the chemical, food, and logistics industries. Its compact design allows seamless integration into existing systems. In addition to standard labelers, the system can also apply tamper-proof seals or static instructions. Its adaptability to various label sizes and positions makes it an extremely versatile solution.
The VeloFlexLabeler by GREIFVELOX offers a state-of-the-art solution that boosts production efficiency, enhances flexibility, and ensures greater safety, all while empowering companies to optimize production costs more effectively and dependably.
Visit the GREIF-VELOX website at www.greif-velox.com
NEW ELECTRIC MOTOR PLANT FROM JANUARY 2024
24,000 m 2
MORE THAN 20.000 MOTORS AVAILABLE FROM STOCK!
Motors up to 25 MW and 13.8 kV
• Low voltage slip-ring and squirrel cage motors up to 3,000 kW
• Medium voltage slip-ring and squirrel cage motors up to 15,000 kW
• Direct current motors up to 2,000 kW
• Frequency converter-proof drives
• In-house load test facility up to 13.800 V, 2.300 kVA, 120 Hz
Customized special designs
• Custom designs for special applications and operating conditions
• Optimized motor design for higher efficiency
• Mechanically and electrically interchangeable motors
• Commissioning worldwide
MENZEL Great Britain Ltd. | UK Branch Office
27 Hunt Drive | Melton Mowbray | Leicestershire LE13 1PB
Martin Rooney | Tel.: +44 1664 500 844 | Mobil: +44 7957 618046
martin.rooney@menzelgb.co.uk
MENZEL Elektromotoren GmbH
German Headquarters
Am Alten Walzwerk 2 | 16761 Hennigsdorf | Germany
menzel-motors.com info@menzel-motors.com