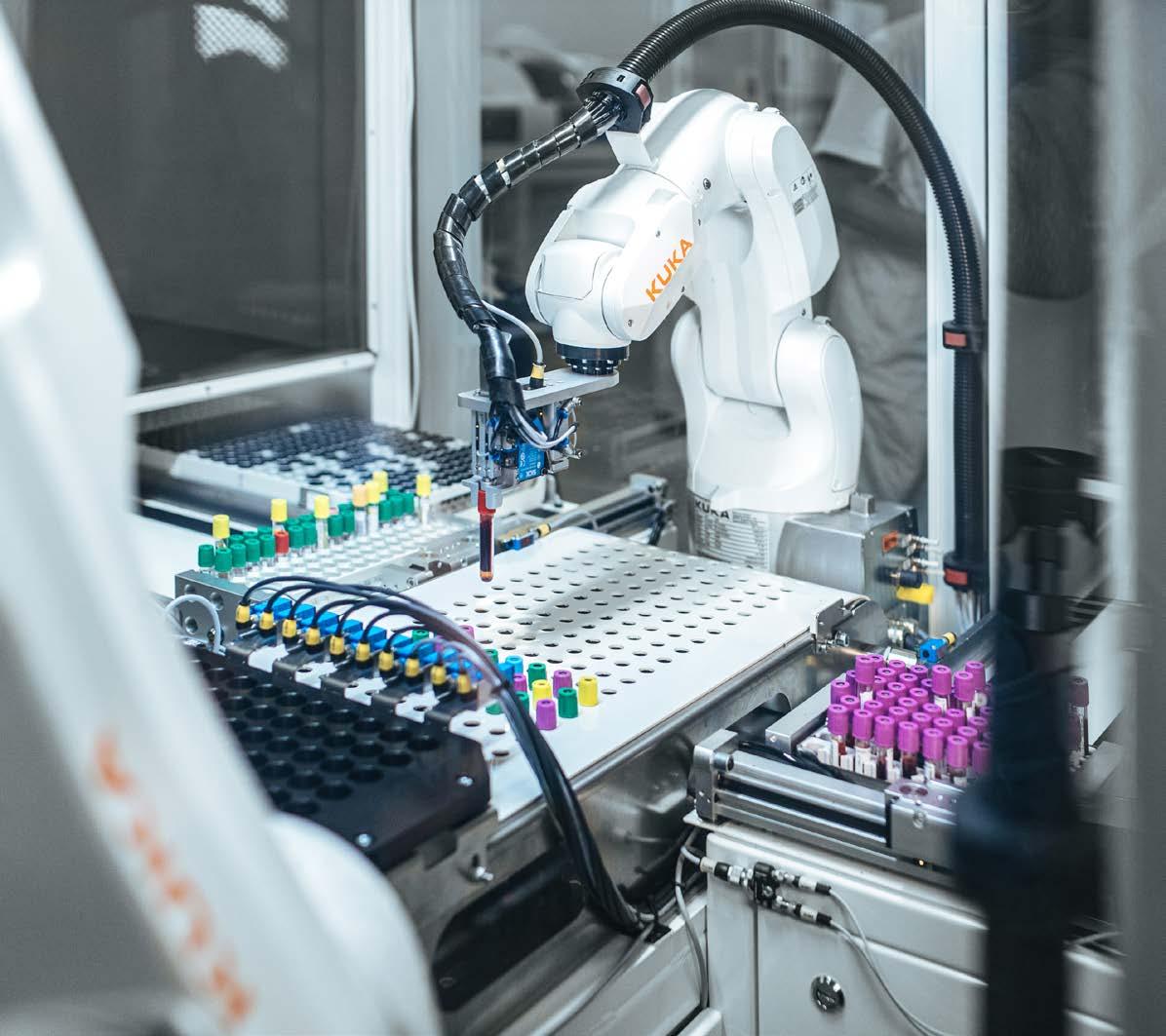

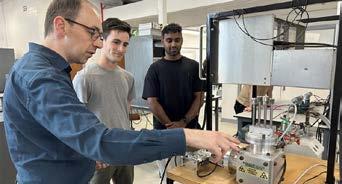
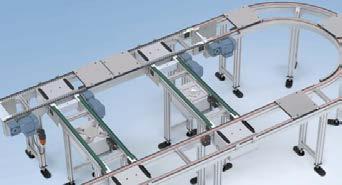

ADVANTECH
Seamless integration for
BURCKHARDT COMPRESSION
Burckhardt Compression offers highspeed compressor solutions that are available for immediate deployment
CP AUTOMATION
CP Automation helps Tata Steel eliminate unplanned outages
MAPAL
MAPAL tool management for DEUTZ in Spain
SIEMENS
Siemens and Spinnova drive innovation and sustainability in textile manufacturing
INTRALOGISTEX
Industry giants set to lead world-class conference programme
Cover photo: kuka.com
FANUC UK
FANUC UK seeks the next young robotics superstars
ABB
GreenIron to deploy ABB technology for greater circularity in metals and mining industries
PRIME VISION
Robots as a service simplifies the automation of sorting operations
BMW
BMW Group scores circular economy win with high-voltage batteries
UNIVERSSAL ROBOTS
Universal Robots and Ultima Forma collaborate to fuel the decarbonisation of aerospace
BECKHOFF
New software addition enables machine learning integration
• High quality materials
• Innovative designs
The leading source for innovators in Technology, Manufacturing and Maintenance within the Engineering & Processing industry worldwide.
Published bimonthly, a subscription to PECM magazine is essential for Process Engineers, Chemical Engineers, Instrumentation Engineers, Mechanical Engineers, Plant Engineers, Precision Engineers, Environmental Engineers & General Engineers, Companies and Organizations in the Food, Dairy, Beverage, Brewing, Semiconductor, Pharmaceutical, Biotechnology, Chemical, Oil & Gas, as well as all UK's major manufacturing units.
Every issue of the magazine contains the latest news, in-depth features, together with product innovations and case studies showing how process engineers are implementing new technologies to reduce costs and impact on the environment.
With over 158,000 readers worldwide the publication is widely read, recognized, and well respected within the Process, Engineering & maintenance industries.
A subscription to PECM magazine is the industry's 'must have' publication.
SUBSCRIBE TO 6 BIMONTHLY ISSUES OF PECM FOR JUST £27
• The magazine gets delivered directly to your door once every issue is published
• The quality of the hard copy enhances the reading experience
To Subscribe please call 01304 806039
SUBSCRIBE TO OUR DIGITAL EDITION COMPLETELY FREE OF CHARGE
Designed for the digital age, the magazine has been created for easy viewing on all electronic devices. All our issues stored in one place: get unlimited access to our previous and future issues.
To Subscribe please visit www.pecm.co.uk/subscribe
EDITOR IN CHIEF
Antony Holter editor@mhmagazine.co.uk
BUSINESS MANAGER
Josh Holmes josh@mhmagazine.co.uk
SALES DIRECTOR
Jake Page jake@pecm.co.uk Tel: 01227 937174
SALES MANAGER
Martin Richardson martin@pecm.co.uk Tel: 01304 086039
DIGITAL MANAGER
Jamie Bullock jamie@mhmagazine.co.uk Tel: 01227 936971
EDITOR
Elizabeth Hutton elizabeth@pecm.co.uk
STUDIO DESIGNER
Richard Bland richard@mhmagazine.co.uk
ACCOUNTS DEPT
Alison Holmes accounts@pecm.co.uk Tel: 01227 936976
PUBLISHING DIRECTOR
Martin Holmes martin@mhmagazine.co.uk Tel: 01304 806039
DIGITAL ASSISTANT
Stacey Goodwood Tel: 01227 936971
MH Media Global Ltd. 18/20 Newington Road, Ramsgate, Kent, CT12 6EE Tel 01304 806039 l Fax: 08721 152240 l www.pecm.co.uk
Advantech, a global leader in the fields of IoT intelligent systems and embedded platforms, announces the launch of the UNO-247 V2, an industrial IoT gateway advancing its successful UNO-200 IoT automation gateway series. Powered by the Intel® N97 processor, the UNO-247 V2 plays a pivotal role in the automation industry and smart manufacturing by enabling remote control, decision-making, and connectivity at the edge of industrial networks. It acts as intermediary between sensors, actuators, and cloud systems, offering robust performance in latency-sensitive environments. By reducing the reliance on centralized data processing, UNO-247 V2 enhances industrial protocol integration, system reliability, optimizes bandwidth usage, and enables advanced capabilities such as predictive maintenance, enhanced cybersecurity, and seamless integration with industrial IoT ecosystems, driving digital transformation and innovation in the industry.
The UNO-247 V2 features comprehensive I/O capabilities, equipped with 4 x Gigabit Ethernet ports, 6 x COM ports (2 x RS232/422/485 and 4 x RS-485), 4 x USB ports, and dual display outputs via HDMI and VGA. This extensive connectivity ensures seamless integration with various industrial devices and systems, making it an ideal solution for complex automation environments.
Powered by the Intel® N97 processor with frequencies up to 3.6 GHz, the
UNO-247 V2 delivers exceptional computing performance for edge applications, offering over a 160% performance improvement over its predecessor. The system supports up to 16GB of DDR5 memory and offers flexible storage options including mSATA and 2.5” SATA drives, enabling efficient data processing and storage at the edge. This enhanced processing power ensures smooth handling of resource-intensive applications while maintaining reliable operation in industrial settings.
The UNO-247 V2’s innovative design prioritizes flexibility and ease of maintenance. Its terminal block provides secure wiring capabilities, while the optimized mechanical design allows for easy RAM access through the bottom plate. The gateway also features a reserved iDoor bracket, enabling future expansion options to accommodate evolving industrial requirements. This adaptable design ensures the UNO-247 V2 meets dynamic industrial needs while
maintaining operational continuity.
The gateway has proven its versatility across various industrial applications, including:
• Temperature control in glass manufacturing, where precise temperature monitoring is critical for product strength and safety. The UNO-247 V2 with multiple RS-485 ports enables PLC connectivity for comprehensive temperature control.
• Real-time kiosk data acquisition in gas stations, enabling the control room to monitor and manage site inventory, transactions, equipment, and safety parameters through cloud/network connectivity.
• Device management systems in factory process automation, streamlining operations through centralized monitoring and control.
• Remote control applications in CNC tooling machines, ensuring secure and responsive machine operation with minimal latency.
For further information, please visit www.advantech.com or contact local Advantech representative.
For valve designs in biogas plants and for upgrading biomethane and CO2, GEMÜ offers technically advanced solutions tailored to each process step.
• Robust valve designs, including globe, butterfly, diaphragm, and ball valves.
• Comprehensive systems, offering complete valves, measurement, and control systems for seamless integration in the gasification process.
• High performance materials, robust testing and specialized polymers for superior sealing.
• Expertise advice to help you select the right valve designs for efficient and safe operation.
The Schmersal Group has expanded its range of optoelectronic protective devices with a series of safety light curtains/grids in Ex design. The new EX-SLC/SLG440 series is designed in the ignition protection types EX d (gas atmospheres), EX t (dust atmospheres) and EX op is (optical radiation) and is thus especially suitable for access protection of potentially explosive areas in industrial production - namely for zones 1 and 21.
There is an elevated risk of explosion in many areas of manufacturing, such as in the chemicals industry, in refineries or paint shops where flammable coatings are being used. In industries that process bulk materials, such as in the animal feed or recycling industries, as well as in sawmills and plants that process cereals and grains, there is a risk of
When one or more of the beams is interrupted, hazardous movements are brought to a halt.
dust explosion and the occasional formation of a potentially explosive dust cloud during normal operation.
Schmersal has developed the SLC/ SLG440 safety light curtain/grids in Ex version precisely for these applications. These devices can be installed in potentially explosive gaseous and dusty atmospheres of zones 1/21 and 2/22, category 2GD and are used to protect hazardous areas and machine access. When one
Suitable for gaseous and dusty atmospheres of zones 1/21 and ignition protection type op is: the new SLC/ SLG440 series of safety light curtains/ barriers in Ex design.
or more of the beams is interrupted, hazardous movements are brought to a halt.
The series is ATEX certified and further certification – IECEx, INMETRO and CCC Ex – are due to follow. The sensor system is accommodated in a protective enclosure made from non-breakable glass.
Ex-SLC440 safety light curtains for finger, hand and body detection are available in versions with a resolution of 14 and 30 mm as well as ranges of between 0.3 and 20 m. Ex-SLG440 safety light curtains are suitable for access control to hazardous areas.
The waterproof and dustproof devices achieve IP66 and IP67 protection class and also have the capability to be used outside.
The new AZM150 electromechanical interlock boasts a slimline design and a holding force of 1,500 N. The AZM150 can be combined with a range of different actuators to suit different mounting situations, including a straight or angled actuator for sliding guards and a flexible actuator for small hinged guards.
A plus point of the interlock is the 360 degree rotating actuator head which is locked by simply putting on the cover. The actuator head with its two insert slits allows for a range of mounting and approach options for highly versatile use. o
SCHMERSAL | Enigma Business Park
Malvern, Worcestershire, WR14 1GL
www.schmersal.co.uk
uksupport@schmersal.com
With rising energy costs and an increasing focus on sustainability, businesses are facing mounting pressure to reduce their carbon footprint while maintaining an optimal working environment. Cooling and ventilating large open spaces such as manufacturing, warehouse & distribution facilities, can be a challenge and sometimes rely on energy intensive air conditioning systems, however, with today’s climate and economic challenges, alternative cooling solutions are more critical than ever.
Evaporative cooling presents a highly efficient and environmentally friendly alternative to traditional air conditioning and can be easily retrofitted to existing ventilated spaces. By leveraging the natural process of water evaporation, evaporative coolers can drastically reduce energy consumption while delivering a continuous supply of fresh, cool, and filtered air.
Among the leading solutions in this space is Breezair, an advanced and recognised direct evaporative cooling system which has been developed to provide reliable, highperformance comfort cooling while significantly reducing operational costs.
Unlike conventional air conditioning, which relies on refrigerant gases, Breezair uses 100% fresh outside air and water to create a natural cooling effect. This process consumes up to 80% less energy, making it one of the most costeffective and sustainable comfort cooling solutions available today.
• Manufacturing facilities, where temperature control and air quality is essential for machinery efficiency and occupant safety.
With a unique design that ensures even airflow distribution, Breezair coolers can effectively replace hot, stagnant air with a continuous flow of fresh, cool air.
For businesses looking to reduce their carbon footprint and operational expenses, Breezair redefines energy-efficient cooling. It has been successfully implemented across various industries, including
• Warehouses and distribution centres, where overheating can lead to employee discomfort, product spoilage, and reduced productivity.
• Other industrial facilities, with intense heat loads where cooling large, open workshops is critical to maintain efficiency and productivity.
With a unique design that ensures even airflow distribution, Breezair coolers can effectively replace hot, stagnant air with a continuous flow of fresh, cool air. This helps improve employee comfort and
well-being, which in turn boosts productivity.
Beyond its energy efficiency, Breezair offers several advantages over traditional cooling systems:
• Lower Running Costs – With up to 80% less energy consumption, businesses benefit from significant cost savings on electricity bills.
• 100% Fresh, Filtered Air – Unlike recirculating air conditioning systems, Breezair continuously brings in fresh outdoor air, improving indoor air quality.
• No Synthetic Refrigerants – By using only water for cooling, Breezair eliminates the need for harmful refrigerants, supporting net-zero and sustainability goals.
• Low Water Usage – Breezair’s advanced evaporative cooling technology is designed to optimise water consumption, ensuring efficient cooling with minimal water usage, making it a sustainable choice for businesses looking to reduce environmental impact.
CPA Engineered Solutions helps businesses achieve their operational and sustainability goals with innovative, energyefficient solutions designed for long term impact.
• Scalability & Retrofit Capability
– Systems can be tailored to small, medium, or large industrial applications and can be retrofitted into existing buildings, providing flexibility in deployment.
To support industry professionals in understanding the benefits, and applications of evaporative cooling, CPA Engineered Solutions is launching CIBSE-accredited CPD training sessions in the coming months.
These expert-led sessions will cover:
• How Direct Evaporative Cooling works and why it is a viable alternative to air conditioning.
• Real-world applications and case studies showcasing energy savings.
• Design considerations to ensure optimal system performance.
• Compliance with energy efficiency standards and sustainability goals.
Whether you are a facilities manager, energy consultant, building services engineer, or sustainability professional, this CPD programme will equip you with practical knowledge to make informed decisions on cooling strategies for industrial and commercial applications.
Attending an accredited CPD session will not only enhance your technical knowledge but also contribute to your professional development, keeping you up to date with the latest innovations in energy-efficient cooling.
CPA Engineered Solutions helps businesses achieve their operational and sustainability goals with innovative, energy-efficient solutions designed for long term impact.
For more information on Breezair direct evaporative cooling or to register your interest in our upcoming CIBSE-accredited CPD training, contact us at:
• sales@cpa-group.com
• Breezair.co.uk
When it comes to the dosing, metering or transfer of aggressive chemicals, flavourings, or abrasive solid laden mixtures there is often only one logical choice – a peristaltic pump.
With innovations in pump technology being few and far between, operators have often been left to create their own control functions, integrate logic and separate custom control panels for pump control.
However, a new locally mounted integrated control function available on the range of peristaltic pumps supplied by North Ridge Pumps is helping to revolutionise pump operation.
Serving users ranging from small scale start-ups who don’t have the time, expertise or resource to set up and configure additional controls, to non-technical operators where the simplicity in design, operation and adjustment means that users are far more likely to use such equipment without causing damage to their pump or interruption of process.
Peristaltic technology is well known for its ease of maintenance which can be readily undertaken by nontechnical personnel with very little or no training
The new control function panel is available fitted and Integrated across the full peristaltic family of pumps, and installed on both new and existing peristaltic pumps.
Specifically, It offers the following functions:
Using
this type of pump means reduced down time due
to its simplicity of design, enabling it to be serviced by users with little expertise in a short amount of time.
Metering Method – Modes can be set to alter how the pump meters from amounts dosed over a set amount of time – (timed metering), to volume proportioning to meet a required concentration based on feedback from an external probe or sensor connected directly to the pump automatically adjusting the volume of chemicals for PH Correction.
Operation – Start and Stop can be controlled remotely via external input such as a float switch on a tank, a control signal from process, or 4-20ma analogue control directly connected to the unit.
Access & Control – Menu functions can have access limited by passcode, or functions hidden, with the unit accessed remotely. It can be controlled by industry leading process control systems such as PROFIBUS®/Profinet /CANbus as well as being IOT Capable.
Eliminating the need for separate Human Interface (HMI), the locally attached display enables full control of the pump via intuitive touchscreen displaying current flow, operating pressure, warnings in case of hose rupture, as well as stopping the pump prior to pump leakage.
Using this type of pump means reduced down time due to its simplicity of design, enabling it to be serviced by users with little expertise in a short amount of time.
Its design eliminates points of failure in processes through the elimination of external accessories as non-return or pressure loading valves are not required, the predictive flow can eliminate the requirement for an external flowmeter and given the user interface it can also remove the necessity of a control panel.
If you have an application requiring the dosing, metering or transfer of chemicals or viscous liquids and want to revolutionise how your process operates - speak to North Ridge Pumps on 01773 302 660 or visit www.northridgepumps.com to see how we can help.
www.northridgepumps.com
In fact, we have a whole range of non-clog metering pumps which will give you incredibly precise measurement of gaseous, viscous and shear-sensitive fluids without any loss of flow.
We’re North Ridge Pumps, the UK’s largest pump supplier with over 25 years’ experience. We’re expert at specifying exactly the right pump for every client – not just an off-the-shelf, one-size-fits-all solution.
That’s probably why we’ve completed over 2,000 successful projects for clients all around the world. You can read case studies at www.northridgepumps.com
MENZEL was asked to manufacture a custom 6600V electric motor to drive a multi stage condensate water pump in a thermal power station. The existing motor needed to be replaced quickly. In just four weeks MENZEL planned, built and delivered a three-phase squirrel cage motor with IC 616 cooling and IP 55 protection.
The requirements: Precision and speed
The customer not only wanted a motor that could be seamlessly integrated into the existing system via plug-and-play, but also one that could be implemented quickly. MENZEL was able to complete the motor in just four weeks.
One of our stock motors in the required size formed the basis. However, the following adjustments still had to be made:
• Precision work on the rotor shaft: conversion to shaft nuts with lefthand thread and laser welding of the keyway.
• Changing the cooling system: Conversion from IC81W to the IC616 system.
• Adaptation of the direction of rotation: including different inner fan wheel Accompanying tests: Extensive tests in the load test field to ensure the highest standards.
• Adapterplate and different mechanical modification: for a plug and play type fixing between the motor an the pump
Thanks to the close cooperation between the customer, our project engineers and our production department, we were able to develop and agree the technical solution quickly.
The implementation: precision meets efficiency
During the planning phase, we went through several changes and special requirements. Thanks to the close cooperation between the customer, our project engineers and our production department, we were able to develop and agree the technical solution quickly.
Our ability to meet technical requirements and commercial details in record time was particularly praised. In addition, the motor was extensively tested in our load test field. Where MENZEL successfully met all customer requirements.
Technical data of the AC-Motor
• Type: MEBKSLF 500-04-011 ACMotor
• Motor application: Condensate water pump in a thermal power station
• Rated power: 970 kW
• Rated voltage: 6600 V
• Rated speed: 1487 min-1
• Type of construction: IM V1
• Protection class: IP 55
• Cooling type: IC 616
• Weight: 7160 kg
The delivery: Precisely to the destination
The finished squirrel cage motor was transported to Japan by plane in order to meet the critical deadline. Installation and commissioning took place at the thermal power plant, where the motor now reliably drives the multi stage condensate water pump.
This project is a prime example of our strengths:
✓ Custom solutions in the shortest possible time
✓ Efficient communication and close coordination
✓ Highest technical precision, made in Germany
ALPMA has mastered the film wrapping of packs of soft cheese, even if the product properties fluctuate and the product types change frequently. The new MultiSAN film wrapping machine packs round and rectangular soft cheese without compromise, as well as cheese in square, cylinder or halfmoon format. Complex conversions or long set-up times are no longer necessary.
Previous packaging machines in widespread use in cheese dairies have been mechanically driven with shafts, cams and gears to synchronise the movement of the individual movements. This solution was fine for packaging one type of product.
The packing many different types of product with folding or wrap-around required a more flexible solution.
Thanks to the LinMot linear motors, the new film wrapping machine from ALPMA can process significantly more different products without any modifications. (Source: ALPMA)
The envelope fold at the bottom of the cheese, which is typical for the wrap-around packaging, is now generated with the help of four horizontally mounted LinMot
The packing many different types of product with folding or wraparound required a more flexible solution.
linear motors, each of which drives a sealing lamella via a linkage. After the cheese has been wrapped in packaging film by the machine and fixed on a round plate by tongs, the lamellas press the protruding film together in quick succession on the underside of the product so that the desired fold is obtained.
“Only the LinMot motors have shown the required performance with the small dimensions we wanted,” reports Helmut Eitermoser, the designer of the MultiSAN.
PS01 – Linear motors.
The MultiSAN uses motors of the type PS01-23x160H-HP-R which can delivery up to 130N with strokes from 20 to 780 mm. A 120 mm, version was chosen for the MultiSAN.
With a cylindrical design of only 23mm., these LinMot motors achieve an extremely high power density.
Always optimal packaging results “We have also used the very sensitive and direct reaction behaviour of the LinMot linear motors to give the operator a tool to react to fluctuations in the product consistency,” adds Helmut Eitermoser.
ALPMA has formed the LinMot motors with the locking mechanism into a module that is used several times in the machine and is designed in such a way that it also acts as a heat sink for the linear motors. (Source: F. Rossmann)
Machine sales doubled
With these features, the new packaging machine from ALPMA has hit the nerve of the market, as the sales figures impressively demonstrate: In the first few months after the machine was launched, they were twice as high as the usual orders in the same period.
For further information, please visit www.linmot.com
Burckhardt Compression, a global leader in reciprocating compression technology, is ready to immediately deploy its High-Speed Compressors (HS-C) and New Build Compressor Packages (HS-C/HS-E) for the midstream and downstream oil and gas industries. Engineered to deliver flexibility, efficiency and reliability, these compressors help operators to enhance performance and minimize downtime.
The HS-C Direct Drop-In Replacements are designed to seamlessly replace a wide range of compressors – including those manufactured by other brands – with minimal modifications, making them a practical choice for operators seeking to upgrade without extensive downtime or redesign costs. The fully balanced frame significantly reduces vibrations, while contributing to smoother operations and longer equipment lifespan.
The field-replaceable cylinder liners offer easy maintenance, allowing for quick replacements and adjustments that minimize
interruptions in production. This feature not only reduces downtime but also provides flexibility, enabling operators to quickly adapt to changing demands or conditions.
In addition to this engineering excellence, the HS-C Direct Drop-In Replacements are compatible with a wide range of standard industry valves. This compatibility ensures that operators can integrate the compressors into existing systems without the need for costly or timeconsuming modifications.
Tailored new build compressor packages
For businesses looking to expand or modernize their operations, the HS-C/HS-E New Build Compressor Packages offer tailored configurations to meet any operator’s specific requirements. Designed and customized at Burckhardt Compression’s facilities in the US and Switzerland, their top-tier quality and performance make them a reliable choice for demanding oil and gas applications.
Standardized packages eliminate the need for special foundations,
The compressors are designed and customized at Burckhardt Compression’s facilities in the US and Switzerland.
reducing upfront capital costs and simplifying the installation process. This standardization also allows for easier maintenance, ensuring that routine services can be completed quickly.
Built with adaptability in mind, these compressors can accommodate a wide range of footprints and cylinder configurations, making them suitable for diverse applications. A streamlined, skid-mounted solution can also reduce interface complexity, enhancing operational efficiency and reducing installation time.
Built with adaptability in mind, the HS-C/HS-E New Build Compressor Packages can accommodate a wide range of footprints and cylinder configurations.
to deliver flexibility, efficiency and reliability, these compressors help operators to enhance performance and minimize downtime.
Burckhardt Compression’s solutions are not only reliable but also economically accessible. With competitive pricing and flexible financing options, it’s easy for businesses of all sizes to benefit from state-of-the-art compression technology.
Importantly, this commitment to affordability does not come at the expense of quality or support. With Burckhardt Compression, operators
can take advantage of best-inclass lead times, ensuring that new compressors are delivered and installed promptly.
On top of this, the company provides extensive support to ensure optimal performance and longevity of its compressors, all the way from initial installation to ongoing maintenance and technical assistance. The strategic US service network, bolstered by global infrastructure, ensures that critical spare parts are readily available. This accessibility reduces delays, keeping operations running smoothly and maximizing uptime.
To complement this inventory, Burckhardt Compression offers extensive technical support to help operators optimize the performance and reliability of their compression systems. Whether through routine maintenance, troubleshooting, or system upgrades, the company’s team of experts provides the support needed to ensure long-term operational success.
For operators looking to improve reliability, efficiency, and availability in their compression systems, Burckhardt Compression’s high-speed compressor solutions represent the ideal choice. With immediate availability, comprehensive support, and a proven track record of performance, these compressors are poised to meet the demands of today’s challenging industrial landscape.
HS-C/HS-E New Build Compressor Packages offer tailored configurations to meet any operator’s specific requirements.
For further information, please visit www.burckhardtcompression.com
Are you handling or transferring a shear sensitive fluid? Does your manufacturing process involve a liquid that alters when heavy force like stirring is applied? This article from Castle Pumps Ltd will give you more of an insight into exactly what a shear sensitive product is and how this impacts pump selection. So, let’s start with a deeper look at the characteristics of a shear sensitive liquid…
What are shear sensitive fluids?
Shear sensitive liquids are those that become altered or even damaged when force is applied. In the most simplistic of terms, they are delicate fluids that change viscosity when “messed with” like shampoo turning into foam, or that contains solids that can be crushed but for the purpose of their use should not be, like fruit pieces in a yoghurt.
In more scientific of explanations, all liquids can be categorised into either Newtonian or nonNewtonian. Newtonian fluids are those that remain at a constant viscosity no matter the amount of shear applied (providing temperature remains the same). These include water, alcohol and mineral oil.
With non-Newtonian fluids, how thick or thin the liquid is can alter depending on the composition of the product and how it reacts to shear being applied. The way the liquid reacts can be identified in four ways - Dilatant (Shear Thickening), Pseudoplastic (Shear Thinning), Rheopectic and Thixotropic.
(application
© 2007-2010 The University of Waikato | www.sciencelearn.org.nz
• Dilant - become much thicker when force is applied - think of a cement mix or pancake batter.
• Pseudoplastic - are the exact opposite, with them become less viscous with increased stress - just like paint or tomato sauce.
• Rheopectric – become more viscous as more stress is applied over time – if you whip cream for long enough, it becomes much thicker.
• Thixotropic – becomes less viscous as more stress is applied over time – if you stir honey over a period of time it becomes much more fluid.
But why does this impact pump selection and what exactly is a shear sensitive pump?
What is a low shear pump?
Whilst certain pumping technologies such as centrifugal pumps apply high shear in
operation, shear sensitive pump designs are able to keep such fluids intact due to their low internal velocity, gentle pumping mechanism and the wider tolerances between their pump casing and internal components. Failing to select a low shear pump when handling a shear sensitive liquid can result in product inconsistencies, damaged solids that need to be intact and costly waste.
Typical low shear pump types are typically positive displacement pumps and include peristaltic pumps, progressive cavity pumps, flexible impeller pumps and AODD pumps.
Does your process involve the handling of a shear sensitive fluid that you cannot risk altering or damaging? Contact the pump experts at Castle Pumps Ltd for help specifying the right pumping solution.
For further information, please visit www.castlepumps.com
Pump smarter, not harder. Use our 15 years’ experience to save excessive wear, process failures, product waste & operator time.
✓ Solid-laden, viscous fluids without clogging/wear
✓ Safe handling of chemicals, fuels & flammables
✓ Highly accurate dosing of chemicals & ingredients
✓ Difficult to pump or delicate, shear sensitive fluids
✓ 99.98% barrel emptying to prevent product waste
✓ FDA & 3A models for food and hygienic applications
Contact our technical sales engineers now!
Huck® fasteners have long been a trusted solution in industries requiring high-strength, vibrationresistant fastening. These fasteners play a crucial role in ensuring structural integrity and safety in a wide range of applications and industries. Given their significance, many engineers and professionals frequently turn to search engines with technical queries about Huck® fasteners. In this article, we address some of the most commonly asked questions about these specialised fasteners.
What are Huck® fasteners?
Huck® fasteners are advanced fastening solutions designed to provide secure, high-strength joints that resist vibration and loosening over time.
What are the different types of Huck® fasteners?
Huck® fasteners come in various types, each designed for specific applications.
HuckBolts®: also known as LockBolts® are a two-piece, highstrength fastening system consisting of a pin and a collar, designed for permanent, vibration-resistant joints. They are installed using a swaging process, which eliminates the need for re-tightening, making it ideal for structural, transportation, and heavy-duty applications requiring superior strength and longterm reliability.
Huck® Blind Fasteners: are highstrength, one-sided (blind-side) fastening solutions used when access to the blindside of a joint is restricted. They provide vibration resistance, high shear strength, and consistent clamping force, making them ideal for aerospace,
automotive, rail, and structural applications where reliability and quick installation are essential.
Which industries use Huck® fasteners?
Huck® fasteners are widely used across multiple industries, including:
Automotive & Heavy-Duty
Trucks: Common in truck chassis, suspensions, and trailers for secure, maintenance-free fastening. They can be used in anything, including defence vehicles and F1 racing cars!
Railroad & Transportation: Applied in railcar construction and track infrastructure to withstand constant vibrations.
Construction & Infrastructure: Utilised in bridges, portable buildings and large metal framed structures for strong, permanent joints.
Solar Energy: Huck® fasteners are used in solar panel mounting systems to secure structures against wind loads and environmental stress.
Wind Turbines: Huck® fasteners are used in tower assembly, nacelles, and rotor components for secure, vibration-resistant connections.
Shipbuilding & Marine: Resistant to corrosion and extreme conditions, making them ideal for naval and commercial ships.
Manufacturing & Industrial Equipment: Used in a multitude of production lines for durable and efficient fastening solutions.
Aerospace: Used in aircraft assembly for their lightweight strength and vibration resistance.
If there’s a fastening requirement, Huck® fasteners have a solution.
How do Huck® fasteners differ from traditional bolts?
Huck® fasteners differ from conventional bolts in several ways:
Vibration Resistance: Unlike bolts and nuts that can loosen over time due to vibrations, Huck® fasteners maintain their hold, making them ideal for high-vibration environments.
Installation Speed: Huck® fasteners are installed using hydraulic, pneumatic and battery tools, making the process faster and more efficient than tightening a bolt and nut.
Structural Integrity: The swaging process of Huck® fasteners creates a permanent joint, eliminating the need for re-torquing or maintenance.
What installation tools are required to install Huck® fasteners?
Installing Huck® fasteners requires specialised tools. These tools include:
Pneumatic: Powered by compressed air, these tools are commonly used in high-volume assembly lines.
Hydraulic: Used for heavy-duty applications, providing more force for larger fasteners.
Battery-Powered: Offering mobility and flexibility for production and field applications.
Are Huck® fasteners reusable?
No, Huck® fasteners are designed to be permanent. Once installed, they cannot be removed without damaging the fastener. If disassembly is required, the fastener must be mechanically removed and replaced.
Reusing nuts and bolts can also compromises structural integrity due to thread deformation, fatigue, and reduced clamping force.
Torque relaxation and material wear increase failure risks, especially in high-load or vibrationprone applications.
For safety and reliability, engineering best practices recommend new fasteners to maintain precise tension and prevent mechanical failure.
How do Huck® fasteners compare to welding?
Many industries choose Huck® fasteners over welding due to the following advantages:
Speed of Installation: Huck® fasteners can be installed in seconds, whereas welding is time-consuming.
Consistent Strength: Welds can be inconsistent due to material variations and operator skill, whereas Huck® fasteners provide uniform strength.
Safety: Welding requires specialised training and safety precautions, whereas Huck® fasteners can be installed quickly with minimal training and risk.
No Heat-Affected Zones: Welding can weaken surrounding materials, whereas Huck® fasteners maintain the integrity of the structure.
How do you select the right Huck® fastener for your application?
Choosing the right Huck® fastener depends on several factors:
Load Requirements: Determine the strength needed for the application.
Material Compatibility: Ensure the fastener material matches or is compatible with the materials being joined.
Environmental Conditions: Consider factors like corrosion resistance, temperature, and exposure to chemicals.
Accessibility: Choose between blind (one-piece) or LockBolts® (twopiece) fasteners based on assembly constraints.
What are the maintenance requirements for Huck® fasteners?
Since Huck® fasteners create a permanent joint, they require little to no maintenance. Unlike traditional fasteners, which need periodic re-tightening, Huck® fasteners maintain their strength and integrity throughout their service life. However, regular inspections of the structure in which they are used are still recommended to ensure overall safety.
Huck® fasteners have revolutionised fastening technology with their strength, durability, and vibrationresistant properties. As industries continue to seek reliable and maintenance-free fastening solutions, the demand for Huck® fasteners remains strong. Whether you’re an engineer, technician, or procurement specialist, understanding the fundamentals of Huck® fasteners can help you make informed decisions about their applications and benefits.
How can Star Fasteners help with Huck® fasteners?
Star Fasteners UK Ltd is a leading distributor and expert in Huck® fasteners, offering comprehensive support to help you make informed decisions about their applications, benefits, and installation. Here’s how we can assist:
Expert Technical Advice: Our team provides specialist guidance
on selecting the right Huck® fasteners based on load requirements, material compatibility, and environmental conditions.
Product Range & Availability: We offer a wide selection of Huck fasteners, including LockBolts®, blind fasteners, and installation tools, ensuring you get the right solution for your needs.
Installation Support:
We supply pneumatic, hydraulic, and batterypowered installation tools and can provide training on proper usage for efficient and secure fastening.
Cost & Performance Optimization:
We can help to identify costeffective fastening solutions while ensuring long-term reliability in high-vibration and structural applications.
After-Sales Service: We provide ongoing support, maintenance advice, and troubleshooting to ensure your fastening solutions perform optimally.
Do Star Fasteners offer a tool repair and hire service?
Tool Repair Service: We provide comprehensive maintenance and repair services for installation tools, ensuring your equipment remains in optimal condition.
Tool Hire Service: Star Fasteners offers short- and long-term tool hire options, ideal for busy periods or specific projects requiring specialised equipment. We also provide service hire tools while your equipment is under repair in our workshop.
By addressing these frequently asked questions, Star Fasteners hopes to provide valuable insights for those considering Huck® fasteners for their projects. Their superior performance and reliability make them a leading choice for industries where strength and durability are paramount.
In today’s manufacturing landscape, water supply limitations, an increase in water charges, and stringent environmental regulations are pressing concerns for industries worldwide. These challenges are driving the adoption of sustainable practices, including exploration into new, more environmentally friendly wastewater treatment solutions.
With water shortage fears growing across the UK, companies are re-examining their production processes with a view to reduce the waste of this valuable global resource.
“Without a rapid, effective treatment option, liquid effluent can become a costly issue to tackle,” says Jamie George, Projects & Business Development Director at Axium Process.
While effluent composition varies with the industry, it is usually composed of microplastics, fats, oils, grease and many other unsavoury particulates. Membrane filtration is able to selectively separate these suspended solids, leaving behind high-quality water that is immediately available for reuse in upstream or downstream processes.
Eliminating the need for damaging chemical flocculants, membrane filtration reduces the risk of damage to our rivers and waterways and could potentially reveal the presence of valuable materials that would otherwise be destroyed using alternative methods.
Jamie George states “Initial pilot trials on the feed material are carried out, either at our Swansea test facility, or at the manufacturer’s premises. These are instrumental in how we identify and adjust process parameters for optimal filtration results.”
Able to provide a reliable, cost-effective solution to reducing discharge volumes with the potential to recovering up to 90% of wastewater, membrane filtration is a tried-and-true solution for water recovery needs. Plants can be constructed in a variety of setups, from containerised units to small, compact systems that can be moved to other areas as needed and can also be designed with future expansion in mind.
Axium’s extensive expertise allows for the design and manufacture of crossflow membrane filtration solutions tailored for diverse applications, all while adhering to international regulations and maintaining the highest of hygienic standards.
For further information, please visit www.axiumproces.com
BYTESNAP
The recent ublox withdrawal from cellular bombshell clearly illustrates how obsolescence poses a significant challenge for manufacturers. Some businesses reportedly face re-development costs of hundreds of thousands of pounds.
A recent industry survey shows 90% of manufacturers face obsolescence issues at least once a year, with 28% experiencing these challenges more than once a quarter. This hampers product development, production efficiency and competitiveness, in a market where agility and innovation are key.
Manufacturers facing complex design and obsolescence challenges need solutions that address immediate problems, and future-proof product designs and operations.
UK-leading electronics engineering consultancy ByteSnap Design has been trusted by companies since 2008 to navigate such scenarios, by redesigning existing PCBs and replacing obsolete components.
ByteSnap’s expertise in embedded systems development and product redesign are highly valued by clients. For example, global bearings manufacturers SKF benefitted from collaborating with ByteSnap on a rugged shaft alignment tools redevelopment project.
DESIGN For further information, please visit www.bytesnap.com
ByteSnap’s expertise in embedded systems development and product redesign are highly valued by clients.
SKF were able to increase productivity and focus internal resources on major projects. Amongst other benefits:
• The newly upgraded products have been SKF’s most successful devices ever with high perceived quality and very low warranty rates
• ByteSnap’s strong technical ability, especially in legacy OS systems, ensured smooth project progression on time, within budget
• Access to ByteSnap’s user interface framework, SnapUI, led to easier and quicker GUI development
ByteSnap’s Redesign service is also a particularly effective match for addressing obsolescence challenges - avoiding costly upgrades or production halts:
“We had a product we couldn’t produce anymore, but with just one meeting a week during development, ByteSnap have redesigned the device and successfully dealt with the technical issues. Very pleased – very little management from our side needed on this.”
–Smart City Infrastructure Manufacturer
Manufacturers should adopt best practice strategies to manage technological obsolescence, including:
1. Regular system audits: Conduct regular audits to identify potential obsolescence risks early. This allows for timely planning and mitigation.
2. Strategic partnerships: Collaborate with technology providers like ByteSnap to leverage their expertise in custom electronics design and IIoT solutions. Such partnerships can help manufacturers stay ahead of the competition by integrating the latest technologies seamlessly into their operations.
3. Check longevity plans: particularly on microcontrollers where the pain is not just in redesigning the PCB but could also be in many months of software porting to a new platform.
By embracing these strategies, manufacturers can keep product development agile and responsive to technological advances, positioning themselves for long-term success in fast-moving markets.
Discover how ByteSnap can help you address design & obsolescence challenges and stay competitive in a rapidly-changing world
Are outdated systems holding you back? Are you struggling to keep up with the latest technologies?
You’re not alone. New research shows 61% of manufacturers believe adopting new tech like Industrial IoT & AI is key to staying competitive, yet many find it difficult to implement these solutions effectively.
By partnering with ByteSnap, you can pre-empt headaches caused by obsolescence and stay on track with production.
Our expertise in custom electronics design and IIoT solutions helps you alleviate supply chain issues, optimise product quality, and stay ahead of the competition.
“ByteSnap is a great development partner for us. We’ve worked with their software and hardware development teams for many years and have always experienced clear communication, innovative problemsolving of technical challenges and projects delivered on time and budget. Their high standards and in-depth technical expertise means we would not hesitate to recommend ByteSnap for embedded design across the board.”
Engineering Manager, SKF
Don’t get left behind. Learn more about how ByteSnap can help. Scan the QR code to get the Futureproofing Manufacturing industry report.
Up to 30:1 turndown
Up to 205 kW per foot
Reduced NO₂/CO Emissions
Air replacement or “Make-Up” High efficiency
technology - modulating gas and air
Ideal for variable plant conditions
Heat input range up to 1,550 kW
Choice of operating fuels
Customised design to suit each install
Proven in a wide range of applications
Choice of burner heat inputs up to 1150 kW
Choice of operating fuels
Ideal for variable plant conditions
Our gas burner systems offer users reliable, high efficiency, process heating solutions.
From design, manufacturing and supply to installation, commissioning and ongoing support, we fulfill process liquid, oven and air heating needs for both new-build and conversion projects.
Larger heat input available on request
APL technology -modulating gas and air
Heat input range up to 1,550 kW
Choice of operating fuels
Packaged burner design
Up to 40:1 turndown
We’ve launched an innovative new line of Board-to-Board Connectors with pitch sizes available in 0.50mm, 0.65m, 0.75mm, 0.8mm & 1.0mm as well as custom sizes, tailored for modern, high-density PCB designs.
Designed for long-life applications and robust handling, these new connectors are manufactured with screwmachined terminations with multi-finger contacts and include a wealth of value-added features and come with either protective pick-and-place covers or heavy duty, shrouded insulators. The options of covers or insulators helps to provide positive polarization and offer
superior durability for the connectors
Key Highlights:
✓ Customizable pitch designs for ultimate flexibility.
✓ Durable gold-plated screwmachined terminals for longlasting performance.
✓ Built-in shrouding and pick-and-place covers for seamless manufacturing.
✓ Superior signal integrity with reduced NeXT/FeXT and stable impedance.
Learn more or request a sample today www.advanced.com 1.401.823.5200
• ‘By Industry, For Industry’, practical guidance for everyday and irregular situations and tasks
• Readily accessible for all in the industry –wherever they are, whatever time they have
• FREE task and procedure checklists
• E-learning for continuing professional development
• Webinars and seminars for knowledge sharing and professional networking
• This selection of specialist publications and many more resources
Analog I/O 16/22 bit & 4-20mA
PT100/1k & TC input
GPS-NTP Server
Expandable I/O ARINC429 Remote fw updates
At Oliver Valvetek, innovation drives our commitment to advancing critical technologies. Over the past few years, we’ve increasingly focused our research and development efforts on creating solutions for Carbon Capture, Utilisation, and Storage (CCUS), a key component in the global drive toward reducing carbon emissions.
We are excited to share that we have developed two 3/8” subsea rotary gate valves, part of a group of prototypes heading to a customer for a pioneering carbon sequestration project in a subsea environment. This milestone showcases our dedication to pushing the boundaries of valve technology through advanced R&D.
Our subsea rotary gate valve is specifically engineered for the demanding conditions of carbon sequestration projects. Its compact size ensures easy placement in constrained spaces, while its cost-effectiveness makes it ideal for scalable solutions in large-scale CCUS applications.
Additionally, it features the same proven metal-onmetal seal technology as our standard gate valves, delivering top performance even in the harshest subsea environments.
This advancement reflects Oliver Valvetek’s ongoing commitment to developing cutting-edge solutions that contribute to a more sustainable future.
www.valves.co.uk
Like many industrial facilities, pipe mills use Nidec Control Techniques Mentor DC drives and ABB ACS580 AC drives (VSDs) to help control the speed and torque of motors. Grid- and site-born transients can have serious effects on critical equipment, which may not be clear until everything comes to a halt. Tata Steel UK had experienced premature failures of its drives, resulting in outages at its Hartlepool site, and enlisted the help of Steve Young of IPMC to investigate and measure the quality of the supply. This resulted in power quality specialist CP Automation being approached for a solution.
Tata Steel’s Hartlepool facility is one of several downstream sites across the UK. It receives the raw materials from the company’s Port Talbot site in South Wales, which the team uses to produce steel pipes. On the site, Tata Steel has a 20” pipe mill with an annual production capacity of 220,000 tonnes of tube products. It can produce these pipes for various markets, including construction, engineering, oil and gas and energy infrastructure.
Elsewhere on site, the company has two separate 42” and 84” pipe mills, which were sold to Liberty Steel in 2017. There is also a pipe coating plant, housed in a couple of buildings owned by Tata Steel. Therefore, there is a mix of companies on site, all relying on the same electrical supply.
Tata Steel is the primary customer of the distribution network operator (DNO) and reimburses the companies sharing the site based on their consumption.
Implementing the SineTamer solution proved highly effective, and I strongly advocate its use as part of a comprehensive approach to mitigating power quality issues.
In 2017, Tata Steel was awarded a significant investment, which involved the introduction of 20+ VSDs — a significant load on top of its existing infrastructure. At the time, the company was unaware of what spare capacity it had on site, so its engineers decided to carry out a power quality study to get a true
indication. The study concentrated on the distribution transformer and downstream supply on which the VSDs would be installed.
Having performed the study, Tata Steel determined that it had ample capacity to support the new drives, which the team subsequently installed. Knowing that VSDs are nonlinear loads that can produce significant harmonics, the team later performed a second study on the same supply to determine the effects of the new drives on the network.
No significant effects were found in the second study, but there was another issue. The site continued to experience unplanned outages, which caused frequent disruptions. Although some of these outages were attributable to onsite issues, most were related to the HV network supplying the facility. Certain areas of the plant were struggling to recover from these outages and the damages were significant in terms of time and cost.
The team struggled to identify the root cause of the outages and invited independent power management consultant Steve Young MIET to the site. Steve suggested looking at all transients manifesting on the LV supply — an area that Tata Steel didn’t focus on previously. Together, they quickly discovered significant transients on the AC waveforms for the supply to drives, which were now being damaged.
Tata Steel decided to perform a twoweek study. The first week involved taking a snapshot of what transients were present and in the second
week the team would install some mitigation devices, before taking further readings.
“During the detailed power quality study, significant transient voltage events were identified at the Hartlepool site,” says Steve Young MIET. “These events posed a substantial risk to connected drives and other critical equipment. Using a thorough data analysis, I determined that these transients were a likely source of recurring equipment issues.”
“The results of the two-week study were quite startling,” explained Denis Jennings, senior project engineer – electrical at Tata Steel Europe. “Within the first twelve hours of fitting the logger, the memory was consumed by transients, which weren’t picked up on previous studies because we’d set the trigger level too high. Therefore, we deliberately lowered the level to get a more accurate picture.”
In the second week of the latest study, Steve introduced SineTamer, a transient voltage surge suppression (TVSS) device that protects AC drives, VSDs, and other sensitive electrical systems. This was temporarily applied as a test, and was immediately successful,
demonstrating significant suppression of transient events.
Unlike other devices, SineTamer uses special frequency attenuation, which is frequency-actuated rather than voltage-actuated. Consequently, the device can actively track and follow the sinewave form — protecting all 360 degrees, not just the extremes. CP Automation had previously introduced the device to Steve, who recommended it to Tata Steel.
“We connected the SineTamer to the same supply and recorded no further transients in that second week,” added Jennings. “It was clear SineTamer would be very beneficial and had already improved the quality of the incoming supply.”
Through CP Automation, Tata Steel purchased seven SineTamer devices. These included one CP18LAY2 voltage disturbance filter, a compact unit that can limit internally generated transients, as well as lightning and utility company-induced surges. They also procured six CP-RM-ST503N4 surge protective devices (SPDs) and fitted the CP18-LAY2 to the main incoming supply, the drive suite previously affected by the outages. Smaller units were also installed downstream on the individual drive supplies.
“Implementing the SineTamer solution proved highly effective, and I strongly advocate its use as part of a comprehensive approach to mitigating power quality issues,” added Young.
Durable, sustained uptime
“Relying on a standard low-cost SPD would have been problematic for Tata Steel,” added John Mitchell, global sales and marketing director at CP Automation. “Once these have blown following a transient, the site is no longer protected. Also, they will only kick in once the voltage hits a certain threshold — by which point, significant letthrough voltage has built up.
“SineTamers can take multiple hits and continue protecting once an incident has occurred, but they also minimise let-through voltage,” added Mitchell. “Tata Steel needed to keep its pipe production online — and there was no doubt SineTamer was the device for the job.”
“Several months on and the difference is night and day,” continued Jennings. “Outages are minimal and, when an issue does occur, devices like the AC, DC and variable speed drives recover far quicker and with minimal disruption. We now have a clean, transient-free supply to the critical drives panels and the impact has been remarkable.
“John from CP Automation has always been very open with us, and we’ve enjoyed working with them,” added Jennings. “I can’t fault the experience we had — and we look forward to working together again in the future.”
For more information about SineTamer and surge protective devices, visit the CP Automation website and download the product datasheets for free.
For further information, please visit www.cpaltd.net
Vision Engineering introduces new ‘HALO’ 4K digital inspection microscope
Vision Engineering, a UK based manufacturer of ergonomic microscopy and digital 3D visualisation technology unveils the EVO Cam HALO, a new 4K digital microscope that redefines the standard for clarity, precision and consistency in inspection and measurement tasks.
Suitable for a wide range of inspection applications, EVO Cam HALO combines stunning 4K image quality with advanced, adaptive illumination, and new intelligent software, empowering users to capture the most challenging details with unparalleled accuracy.
HALO’s key features include 4K resolution which reveals previously obscured details with remarkable clarity, ensuring nothing escapes the user’s view. A Super-Wide Dynamic Range ensures the user captures images with exceptional brightness and contrast, even in challenging lighting conditions. Additionally available with HALO comes a new enhanced Illumination package, including a quadrant light,
panel light, and white/UV light, to optimise illumination for a variety of inspection needs.
New Intelligent Hardware and Software automatically detects lenses and adjusts magnification settings, ensuring seamless workflow and accurate results. Real-time insights are available providing intuitive image capture, measurement, and analysis tools, enabling faster and more informed decision-making. Vision Engineering’s popular 360 Direct/Oblique Viewer also works with HALO, enabling users to inspect details from different angles, revealing hidden features that would otherwise be inaccessible.
HALO is suitable for a wide range of applications, including Medical Devices Manufacture and testing especially in the practices of inspecting translucent tubes, electropolished devices, and other medical components with enhanced clarity and accuracy.
It is also effective at capturing fine details on small, reflective metal parts for precise inspection and quality control – perfect for Micro Mechanics. In the laboratory HALO cam improve the examination of Petri dishes with translucent samples, enhancing contrast and clarity for detailed analysis, and in Industrial Manufacturing, intricate assemblies, solder joints, and other components are inspected with much improved precision and efficiency.
EVO Cam HALO is available for purchase from April 2025, with configurations starting at 6500GBP.
Commenting on the launch, Paul Newbatt, Group Sales and Marketing Director at Vision Engineering says “We are delighted to bring EVO Cam HALO to market, confirming our reputation for innovation, whilst improving the inspection performance available within digital microscopy. 4K image quality plus fully controllable lighting and flexible software available in multiple configurations means that our customers in a wide range of sectors can easily choose the most accurate and consistent digital system for their inspection requirements.”
For more information, please visit https://www.visioneng.com/products/digital-microscopes/evo-cam-halo
Engines were already being built in 1875 at the site in Zafra where DEUTZ today has its main factory for processing engine components. Engine blocks, cylinder blocks, connecting rods and gears are produced here by around 500 employees in modern manufacturing facilities for the Group’s assembly lines in Cologne and Ulm as well as for other customers.
DEUTZ’s new 3.9-litre diesel engine is mostly used in agricultural and construction machines. As an industrial engine, it is designed for long service life and is to be built until at least 2035. Series production is to start in the coming year after the current prototype phase. 50,000
units are to be produced per year. This engine, which will be available in a power range from 55 to 160 kW, represents an important future project for Deutz. As it is the same size as its 3.6-litre predecessor, it can be installed in the same vehicles where it will provide very efficient performance.
“Our engines are typically deployed in off-highway applications like agricultural and construction machines, which are in constant use and move heavy loads. We’ll continue to need internal combustion engine to move those machines. For the time being, it will be in the form that we use today: the diesel engine. Synthetic fuels or hydrogen can considerably
prolong their deployment”, explains Alejandro Castilla De La Hoya, Zafra Plant Manager. He points out that the income from this area finances DEUTZ’s investments in the green segment, which is dedicated to the mobility transformation. The 3.9-litre diesel engine is already set to run on gas or hydrogen in the future. “Based on today’s design, this diesel engine can become a green engine in the long run”, says Manuel Rodríguez López, Industrialization Manager. This is possible thanks to a package of small modifications, particularly to the cylinder head. However, the engine remains mostly the same otherwise. MAPAL is already collaborating on DEUTZ’s first hydrogen engine – a whopper at 7.8 litres.
“Our clients’ development periods for new parts are becoming shorter and shorter”, explains Thomas Spang, Global Head of Tool Management at MAPAL. For tool manufacturers or complete suppliers like MAPAL, this represents a growing challenge. This is above all true if plans change at the last minute, while the deadline for the tool design remains the same. For the engine block of the new 3.9-litre diesel engine, MAPAL only had two weeks after the design freeze to complete a final offer.
An ardent team of experts in Aalen were able to complete this ambitious task on time. Well-tuned workflows proved advantageous for the team as did the many years of experience with the client’s production methods. MAPAL has been conducting tool management for DEUTZ in Spain for 18 years. Several projects have been completed together over the years.
MAPAL already engineered the machining of the engine blocks for the predecessor 3.6-litre diesel engine, which meant they were able to draw on practical experience and didn’t have to start from scratch. For example, the tool experts already knew which machines the engine manufacturer has from previous projects. DEUTZ has equipped its assembly line in Zafra with new five-axis machines over recent years, so they can switch to new products with relative ease.
The digital Tool Management 4.0 doesn’t only handle procurement processes, which are initiated semiautomatically, it also acts as a reporting tool to analyse cost drivers and stocks.
When DEUTZ sent their request, the Tool Management department in collaboration with the Technology Expert Team (TET) in Aalen first gave some thought to the production process. “To be quick here, we don’t concern ourselves with detail at this early stage, but instead pull together reference tools and concepts from previously completed projects”, explains Harald Traub from TET. He is responsible for planning the entire process as Project Engineer. “In this way, we are able to specify an approximate budget and the rough scope of the tool package for the client.”
After this rough planning, the concrete tool design followed in the second week. MAPAL’s offer for the series production of the motor block included almost 100 different tools in the end. Many of
them are custom tools that achieve short machining time and thus high economic efficiency. Aside from these, standard tools are used for milling above all.
To produce prototypes quickly, a few close-to-standard tools were also used. Series production can then begin with the optimal set of tools. As part of their original delivery, MAPAL supplied consumable tools as well as the required tool holders and adapters to DEUTZ. All other consumables will be handled by the tool management on site. From this point on, the client no longer pays per tool but per completed part – i.e., the cost per part is billed.
The unit costs at first correspond to the price determined during engineering. Certain ratios have been agreed upon for the following years. The client receives an increasing percentage of rebate and therefore pays a bit less per unit every year. For this business model to work out, MAPAL has to implement continual improvements to save costs. This is done with new tool technologies and corresponding optimisation. The costs per part are fixed over the term of the contract, after which a reassessment takes place. Such contracts, which run over four to five years, offer the client planning security.
“With our engineering expertise, we support DEUTZ beyond the toolsetting area and cultivate a close partnership”, Spang highlights. After helping to build the prototype, it is the tool management’s turn to shine on-site during series production.
Compared to its predecessor, the HPR400 reamer for fine machining crankshaft bearing journals has three times the tool life and does not require resetting. Sergio Aranda (MAPAL Tool Setter) sees a clear difference. ©MAPAL
During a team meeting, the MAPAL tool manager explains machining with the HPR400 reamer and the differences compared to the previous system. Standing left to right: David Castaño (MAPAL Tool Manager), Manuel Padilla Fernández (DEUTZ Manufacturing Engineering Manager) and Rafael Salinas (DEUTZ Project Manager). ©MAPAL
DEUTZ uses approximately 1,300 different tools in total. Thousands of tools are available from stock and have to be managed in Zafra. To keep inventory at an optimal level (i.e., avoiding bottlenecks while preventing unnecessarily high tool stocks), MAPAL uses its own warehouse management systems and digital solutions with the cloud-based software c-Com for tool management. The digital Tool Management 4.0 doesn’t only handle procurement processes, which are initiated semi-automatically, it also acts as a reporting tool to analyse cost drivers and stocks.
Industrialization Manager Manuel Rodríguez López praises the good collaboration with MAPAL when it comes to tool management: “Over
the course of our cooperation, we have developed extensive technological concepts, which go far beyond mere logistics. Besides achieving cost reductions, tool setting is particularly important for us. The MAPAL employees working on-site have a lot of know-how and ensure that production has exactly the tool they need at the right time.”
MAPAL’s tool manager on site is David Castaño. MAPAL also employs tool setters permanently in Zafra. They make sure that a dozen different parts are produced without a hitch. “It is very beneficial to have David here on-site with us”, emphasises Manuel Padilla Fernández, Manufacturing Engineering Manager at DEUTZ, who works closely with the tool manager. “We can talk about any opportunities for optimisation directly at the machine. We don’t
consider David Castaño to be an external service provider but rather a part of our team. It’s a very strong cooperation.”
If required, new tool solutions can be developed in Aalen via the local MAPAL team. That was the case in Zafra when it became necessary to optimise the tools for machining the bore in the crankshaft and camshaft. In cooperation with DEUTZ, a new machining concept from MAPAL with the HPR400 reamer was implemented. David Castaño is convinced of its advantages: “The tool life of the previous tool was 350 units and resetting was required every 100 units. With the HPR400, we achieve a tool life of 1,000 parts without resetting. The resulting machining quality is exceptionally good.”
For further information, please visit https://mapal.com/en-int/
Developed and verified ‘for industry, by industry’, EEMUA 231 Mechanical Integrity courses are for industrial engineers at every stage – to aid efficient hands-on work with primary containment, including pressure systems, and prevent loss of hazardous substances
Range of courses covering: Legislative Environment; WSE; Equipment Design; Operational Considerations; ALARP; Asset Condition; Test Techniques; Inspection Roles, Process and Reports; Postponement; Responses to Findings and Reporting; Record keeping; Audit; Feedback; User Responsibilities and Competencies; Industry Good Practice; Operating Limits; Decision Making; and more.
• Satisfy industry requirements at each level – Awareness, Basic application, Practitioner, Leader.
• Available to all – free or discounted to EEMUA Members
• Certificated up to 5 years – CPD-approved
• Flexible delivery to suit Learners and companies – Blended, Live online, Classroom, E-learning, or In-house.
• Courses throughout each year, including:
Mechanical Integrity Practitioner Certificate (MIPC®) – blended, live online learning – on-site or on-call – 1:1s and Mentor Support – workbook builds from day-1 for immediate use in on-site application of EEMUA 177, 231 and 232 guidance, and the PSSR ACOP – certificated for 5 years via exam and portfolio assessment – in-depth learning for 27 weeks, flexible 4 hours per week – CPD of 110 hours The MIPC course adapts to the engineering needs of each Learner their company and site/s via a 2-hour induction (made to fit work schedules ahead of the course) – learning on the next course starts 3 March 2025
Asset Integrity Leadership Certificate – blended, live online – for new and experienced Leaders –flexible learning 3 hours per week – 55 hours CPD –certificated – next course starts 31 March 2025
Mechanical Integrity Basics – blended, online course – Basic application competency – flexible 4 hours learning per week for 3 weeks – 12 hours of CPD – certificated via exam – next course starts 29 September 2025
EEMUA 231 Mechanical Integrity e-learning – set at Awareness level – with 1 hour of CPD –immediately available – on-demand.
Siemens, a leading technology company announced an innovative collaboration with Spinnova, a sustainable textile technology company, to help transform the textile industry with sustainable fiber production. This collaboration underscores Siemens’ strategic commitment to driving sustainability and digitalization in manufacturing industries.
Spinnova is known for its groundbreaking technology for producing textile fibers with minimal environmental impact, has teamed up with Siemens to transform the way textiles are manufactured globally. Siemens has helped Spinnova reduce its time to market with its Siemens Xcelerator automation technologies, software, and services.
Scaling sustainability impact with Siemens Xcelerator
Spinnova’s patented technology produces textile fiber using a mechanical process that mimics how spiders weave their webs. This process can be used to produce fiber from a variety of raw materials, from wood to leather, textiles, and agricultural waste. SPINNOVA® fiber can then be processed into yarn and fabrics like any other conventional fiber.
“With their unique technology, based on circularity, Spinnova is setting a new standard for environmental sustainability in the textile industry,” said Eryn Devola, Head of Sustainability at Siemens Digital Industries. “Our Siemens Xcelerator portfolio, our know-how and global network are helping
Spinnova scale, reduce time to market, and increase operational efficiency.”
According to Spinnova, the production of SPINNOVA® fiber emits 74 percent less CO2 and uses 98 percent less water than the global average of conventional cotton, generates zero process waste and requires zero harmful chemicals.
Siemens Xcelerator enables sustainable fiber production at industrial scale
The transformative power of the collaboration to produce sustainable textiles is showcased at the Woodspin factory in Jyväskylä, Finland, a joint venture between Spinnova and pulp producer Suzano. With digital twins to optimize the product and production processes,
IT and OT convergence for enhanced transparency, and robust cybersecurity measures, Siemens is enabling Spinnova to scale up its innovation. This has increased the company’s confidence and expedited time to market, which are crucial factors in today’s fast-paced market environments.
“Working with Siemens has transformed how we approach manufacturing. Their technological expertise has enabled us to ramp up production quickly and brings credibility to our mission,” says Tuomas Oijala, CEO of Spinnova.
“This collaboration isn’t just about advancing technology; it’s also paving the way for a sustainable future in the textile industry.”
The Woodspin factory was simulated and virtually commissioned using a digital twin with Plant Simulation in the Tecnomatix® portfolio, including its operations, material flow, what if-scenarios and identification
Working with Siemens has transformed how we approach manufacturing. Their technological expertise has enabled us to ramp up production quickly and brings credibility to our mission.
of bottlenecks. This saved time, maintained quality and increased the efficiency of operations. A digital twin of the product was used to speed up, optimize and coordinate the research and development of the raw material base using Siemens’ Opcenter™ software, which ensures consistent quality from raw material to finished fiber.
The entire automation architecture is based on Siemens’ Totally Integrated Automation concept, where TIA Portal integrates line control, safety technology, end-to-end diagnostics, drives, and field devices in a unified platform. Siemens Industrial Edge enables Spinnova to collect, process and send operational data to the cloud for analysis in order to track key performance indicators like energy consumption and provide transparency to customers and partners. Spinnova’s cybersecurity concept is based on the Defensein-Depth concept and uses cybersecurity technology from Siemens.
The collaboration with Spinnova is part of Siemens’ broader strategy to encourage sustainable practices using technological innovations. Siemens is dedicated to shaping the future of industries where technology meets sustainability, to create a positive impact on the planet and society.
For further information, please visit www.siemens.com
Industry leaders including Microsoft, Airbus, PepsiCo, Boots, Arla Foods, DPD, and DSV will take centre stage at IntraLogisteX 2025, the UK’s largest logistics and supply chain event. With over 350 exhibitors and co-located with Robotics & Automation and the Sustainable Supply Chain Exhibition, the event at the NEC Birmingham will provide transport and logistics professionals with an unparalleled opportunity to explore cutting-edge solutions in logistics, supply chain, handling, and packaging.
Comprehensive
Bringing together three major exhibitions, IntraLogisteX 2025 offers a unique platform for industry professionals:
• IntraLogisteX focuses on innovations in warehousing and distribution.
• Robotics & Automation highlights the transformative power of automation in manufacturing and logistics.
• Sustainable Supply Chain Exhibition showcases the latest strategies for making logistics operations more eco-friendly.
Attendees will experience live demonstrations, engage with experts, and gain first-hand insight into emerging technologies set to revolutionise the sector. Make sure you register for your free ticket now!
Expert-Led Conference Programme
Across both days, a dynamic conference programme will feature
60+ expert speakers, delivering insights into cutting-edge supply chain and warehousing trends. Attendees will hear directly from professionals driving change through advanced technologies and strategies.
Key speakers include:
• Dean Whitehouse, Head of AI Risk Assessment at the Department for Science, Innovation and Technology, discussing responsible AI deployment in automation.
• Taonga Banda, Data and AI Cloud Solution Architect at Microsoft.
• Homero Gonzalez, Robotics, Integration, and Reliability Specialist at Airbus.
• Daniela Sawyer, Automation Lead at University of Sheffield
• Neha Donald, Senior Director, Global Strategy & Transformation at Pepsico
• Adam Coventry, Former Director of Warehousing at Boots UK.
• Tim Jones, Director of Marketing, Communications, & Sustainability at DPD
These experts will share realworld examples of how they have enhanced operational efficiency and improved customer outcomes through innovative applications.
A full list of 2025 speakers can be found on the IntraLogisteX website.
Exhibitors will present the latest technological advancements across materials handling, packaging, robotics, industrial automation, software, barcoding, labelling, storage, and consultancy. Visitors will witness live demonstrations showcasing cutting-edge solutions from leading brands such as Toyota Material Handling, Locus Robotics, AutoStore, Ocado Intelligent Automation, Bosch Rexroth, Dematic, Zebra Technologies, Mecalux, DSV, SSI SCHAEFER, Exotec, Kaleris, Element Logic, and Swisslog.
Among the exciting debuts at the event:
• AutoStore’s R5 Robot, designed to enhance warehouse picking speed and efficiency.
• Exotec’s latest Skypod system, offering a new generation of intelligent automation.
• Zebra Technologies’ latest suite of solutions, designed to enhancing warehousing and manufacturing operation
With hundreds of exhibitors and live demonstrations, IntraLogisteX 2025 is the ultimate destination to explore future-forward logistics and supply chain solutions. Attendees can condense weeks of research into a single day and make invaluable industry connections.
Secure your place now and stay ahead in the world of logistics.
Register for free today at www.intralogistex.co.uk.
the uk’s largest & leading warehousing & logistics EVENT
11,000+ aTTENDEES
60+ speakers
aFTER THE INCREDIBLE SUCCESS OF the 2024 event, Intralogistex will be back at the nec next year with more visitors & exhibitors expected than even before!
featuring all THE LATEST innovations in MATERIALS HANDLING, PACKAGING, ROBOTICS, STORAGE, WAREHOUSE management, BARCODE & labelling, picking & sortation, Mobile scanning, warehouse automation, transport management, safety solutions, and much more
FREE REGISTRATION IS NOW OPEN VISIT OUR SITE TO GET YOUR TICKET!
Rotaflow are into our fourth decade of designing and manufacturing Swivel Joints. We solve engineering problems where fluids need to be transferred across rotating interfaces, without leakage. Our units are in most engineering sectors: From Brewery, Dairy, Food & Drink, Process & Plant, Drilling & Mining, Oil, Gas and Subsea, Nuclear and Chemical.
Through design and in-house manufacture our swivel joints can allow one or more different flows through a single unit, enabling the pipework to rotate 360 degrees whilst carrying fluids (including hydraulic and pneumatic) of different pressures without cross-contamination or leakage.
There are many different forms of Swivel Joint… from very straight forward designs of our F and FS series, Compact swivels or Heavy Duty to Articulated Pipework configurations, Floating Suction Arms, Jacketed, High Pressure. A Swivel Joint reduces costs by reducing the risk of leakage with its associated downtime.
We are specialists in taking your bespoke requirements and being able to design a solution that can fit your budget, dimensions, materials, FAT/witness testing, hygienic and pressurised environments. We regularly test to Hyperbaric, Seal Life and conduct Temperature/Pressure/ Load Cycle Testing. We are ISO 9001:2015 certified.
With off-the-shelf solutions that are ready to go, or we can redesign and in-house manufacture to enable a quick turn-around with minimal fuss and maximum design experience.
To find out more please visit our website and/or give us a call. Tel: +44(0)1663 735003 | sales@rotaflow.com www.rotaflow.com
Articulated Pipework Torsion In Hoses
Rotating Cylinders
Swivel joints allow pipework to pressure 1/4” to 40” and beyond.
Vacuum to over 20,000psi.
Stock and bespoke production.
Unique bearing/seal design for longer life.
ISO 9001 CE marked where applicable.
Tel: +44(0)1663 735003
E-mail:
In this issue of PECM, we are delighted to showcase Sibor as our New Year Spotlight company.
Sibor has a long history, spanning over thirty years providing leading process control, engineering and project management expertise. Established in 1992, to originally provide process control systems and industrial automation to many industrial applications, such as large blue-chip companies, the company has been focusing on the energy sector more recently, notably the anaerobic digestion renewable energy sector.
Sibor provides turnkey design and build service solutions across manufacturing and automation control, including the following services:
• EIC/mechanical design and installation services
• Process control services
• Process instrumentation services
• Atex design and installation services
• Project management services
• Software development services
• Support services
With a vision for providing automated control systems that provide manufacturing benefits and added assurance throughout, Sibor are trusted professionals throughout the project. From initial requirements analysis, expert software engineers define user-needs from the offset, through to application design and software, component selection and assembly for a successful outcome.
Sibor runs applications as local stand-alone systems or alternatively, as Ethernet/IP networked solutions.
Utilising cutting-edge Supervisory Control and Data Acquisition (SCADA), Sibor ensures streamlined services across all customer applications.
We caught up with Managing Director: Rob Mockridge to find out more,
“We have always enjoyed organic growth and over the last 12 months, the company has gone through a major transition and has now been accredited with ISO 9001 and 14001 and we have also been accredited by safe contractor.
We have gone from strength to strength completing many major
upgrade projects for the MOD and several renewable energy companies, ranging from replacing old for new to major electrical infrastructure and controls installations.
We have seen a 40% increase in business over the last 12 months- an accolade to our strong team.
We are very excited for the year ahead in the anaerobic digestion renewable energy sector and we have just signed two major contracts with renewable energy companies to provide LV power distribution design and installation combined with control and instrumentation design and installation. With a pipeline of projects to follow, allowing us to keep investing in our staff and business activities.
Our growth in control and automation projects is a tribute to our innovative approach to design and comes from our long history in many industrial sectors.”
For further information, please visit T 0844 504 7124 | enquiries@sibor.co.uk | www.sibor.co.uk
FANUC UK is continuing its commitment to inspire the next generation of engineers for the fifth year in succession by supporting WorldSkills UK to find the UK’s best young robotics talent.
Leading industrial automation specialist FANUC UK is continuing its commitment to inspire the next generation of engineers by supporting a search to find the UK’s best young robotics talent. For the fifth year in succession, the company is partnering with WorldSkills UK for the annual Industrial Robotics competition, aimed at giving young people the opportunity to learn how to programme a robot, enhance their engineering prowess, develop
valuable workplace skills such as timekeeping and teamwork – and even earn the chance to represent Squad UK at the international finals in Tokyo.
The competition is open to teams of two young people, who must be within a year of completing a relevant Level 3 Apprenticeship and/or hold qualifications in an engineering-based subject (to a minimum Level 3 or equivalent). The contest has been designed to
accommodate participants with different abilities and is accessible to those with little to no knowledge of robotic systems, as well as those with a robotics background.
The first stage of the competition takes place online from 22-25 April 2025 and will comprise a virtual task using FANUC’s Robot Simulation Software. Successful competitors will then be invited to take part in the live Qualifiers Round, where
Competing with their support enabled me to get a head start in learning about robotics and has boosted my CV.
they will complete a timed robot task at the Smart Factory Expo at the NEC, Birmingham on 4-5 June.
FANUC’s team of robotics experts will provide hands-on training to participants ahead of the National Finals, to be held in Coventry on 11-13 November 2025 at FANUC UK’s Open House event. Eligible competitors will then have the chance to represent Squad UK at the International Finals in Tokyo.
The current UK champions are
Aled Gore and Morgan Leyson, both aged 21 and studying Mechanical Engineering at Bridgend College, in conjunction with Renishaw. When asked about the value of competing in the WorldSkills UK competition, Aled said: “FANUC is the number one company in the automation industry. Competing with their support enabled me to get a head start in learning about robotics and has boosted my CV.”
Morgan added: “I entered in the hope that the contest would help me to grow as a person, and hopefully provide me with opportunities to get into programming in the future.”
For FANUC, the WorldSkills UK competition has become an annual fixture and forms an integral part of the company’s commitment to inspiring the next generation of engineers and plugging the skills gap. “Year-on-year, we’ve seen the quality of participants improve and I’m sure
that 2025 will be no different,” says Paul Coombes, competition organiser and Head of Technical for FANUC UK.
“There are so many benefits to taking part in the WorldSkills UK Industrial Robotics competition –not least the chance to learn from real automation experts how to programme actual robots, hopefully kickstarting a love of robotics that could lead to a future career in the industry. But also, soft skills such as teamwork, record keeping and presenting. And of course, the chance to boost your CV and stand out from the crowd when applying for jobs and apprenticeships in the future. I’d encourage anyone with an interest in engineering to give it a try – you really do have nothing to lose!”
How to apply: Register in teams of two via the WorldSkills UK website from 3-28 March 2025: https://www. worldskillsuk.org/competitions/ industrial-robotics/
www.worldskillsuk.org/competitions/industrial-robotics/
Quirepace are an SME manufacturer and supplier specializing in the niche markets of Pneumatic Tube Systems and Vacuum and Pressure products for Industry and Healthcare applications and are based at their HQ, factory and warehouse in Fareham, Hants.
Portable Industrial Vacuum Cleaners
Under the BVC – British Vacuum Cleaners – brand, Quirepace specialise in manufacturing Industrial Vacuum Cleaners for industry. The BVC brand is best known for the heavy-duty UK manufactured units that deliver the best of traditional, solid, British manufacturing and engineering.
The UK manufactured range of BVC Industrial Vacuum Cleaners consists of machines rated at 1kW to 15kW, with the largest machines being at the limit of what can usefully be called “portable” machines. Fitted with robust wheels and casters, the complete range is capable of being easily manoeuvred to wherever it is needed to be used.
In the industrial workplace, hazards from dusts and spilled product fall into two distinct categories; the first is dusts that are hazardous to health. This category includes obvious products like asbestos and silica dust, but any dust that can be breathed in by the operator or other personnel in the workplace is likely to be hazardous to health to a degree. Industrial Vacuum Cleaners with M-Class and H-Class filtration ensure hazardous dusts are appropriately handled when being recovered.
At the heart of most of the BVC range of Industrial Vacuum Cleaners
is a BVC multi-stage turbine manufactured here in the
UK at Fareham.
The second category is dusts that are hazardous in the environment. The obvious category is dusts that can potentially cause an explosive atmosphere, particularly organic
products like sugar and flour. Some products fall in to both categories such as wood dusts, which are both hazardous to health and potentially explosive. ATEX rated Industrial Vacuum Cleaners must be specified for use in ATEX zones.
The latest innovation in the range of BVC Industrial Vacuum Cleaners is the introduction of a completely cordless vacuum cleaner with 1.5kW of industrial cleaning power. This is achieved by using the new and revolutionary Honda eGX electric engine, which delivers 1/2hr to 1hr cleaning power without the need to “plug in”. With a swappable battery and fast charging combined with a continuously rated motor and turbine the new cordless BVC IV60 eGX delivers a unique solution.
At the heart of most of the BVC range of Industrial Vacuum Cleaners is a BVC multi-stage turbine manufactured here in the UK at Fareham. Quirepace also supply a range of side-channel exhausters
and blowers manufactured in Italy by Esam.
Together, the UK manufactured BVC multistage units plus the Esam side channel machines offer a range of units to satisfy every potential requirement for the supply of both positive and negative pressure air to industrial manufacturers and processors.
The choice of which type is more appropriate for the application depends to some extent whether it
is more important to maintain either a consistent pressure, or a consistent air flow as demand changes; A side channel will tend to vary the pressure against any resistance to maintain a constant flow, whereas a BVC multistage unit will tend to vary the flow to maintain a constant pressure. Quirepace’s expert sales team can guide the user towards the most appropriate solution.
An advantage of multistage exhausters and blowers is their robustness and resilience in harsh environments and an ability to cope with some contamination of the air without destroying the impeller.
BVC Multistage vacuum pumps are ideal for smaller centralised vacuum cleaning installations. Typically these will have 2-3 simultaneous operators and a fixed pipework
network distributed around the facility to serve the various use locations.
Central vacuum cleaning systems may either use a portable BVC vacuum cleaner to provide motive air or may be configured with static plant and collection hoppers, discharging in to FIBC, drums, etc.
Quirepace design and build central vacuum cleaning systems up to around 30kW, with configurations for hazardous dusts and ATEX environments. A wide range of hoses and tools is available to suit all requirements.
Pneumatic tube systems are the best solution for moving small payloads up to around 3kg quickly between multiple locations within a facility. In industry, the principal use for Quirepace pneumatic tube systems is to transport samples for QC testing from the production floor to the on-site laboratory or testing location.
A range of different systems is offered to meet all possible requirements, from the simplest point-to-point “Diana” system, to complex computer-controlled networks. Tube sizes range from 60mm to 200mm, with 75, 110, and 160mm diameters being the most common sizes.
Using a pneumatic tube system for rapid transportation of small payloads, is not only efficient, it also enhances health and safety by removing the requirement for people to walk samples through production areas.
Quirepace Ltd www.quirepace.co.uk
www.bvc.co.uk
sales@quirepace.co.uk 023 9260 3700
For further information, please visit www.quirepace.co.uk
ABB has been selected by GreenIron, an innovative Swedish company working in the mining and metals industries with its patented materials reduction technology, to provide automation and control system solutions for a first commercial facility in Sandviken, Sweden.
GreenIron’s hydrogen-based reduction technology will be industrialized for fossil-free and energy-efficient production of metals, producing fossil-free sponge iron that can then be used in industries such as steelmaking. A single furnace is expected to
reduce carbon emissions by around 56,000 tonnes per year compared to traditional coal-based methods, with the only residual product being water. Scaling up to 300 furnaces would correspond to roughly 35 percent of Sweden’s annual CO2 emissions.
The integration of the ABB Ability™ System 800xA® distributed control system (DCS) will enable the scaling up of GreenIron’s operations. The powerful automation platform will manage the entire industrial process, with the capabilities to integrate control, safety and power management into one system. It
will mean overall plant visibility for optimizations, efficiencies and better decision making based on data and insights.
GreenIron paves the way for circular production processes by producing valuable raw materials from residual products such as landfills and residues as well as virgin ore. The sponge iron products can be used in steel or other metal fabrication processes, including electric arc furnaces, smelting plants and foundries.
“The collaboration with ABB is a crucial part of our scaling up and
future growth as we commence commercial production,” said Ulrika Molander, Chief Operating Officer of GreenIron. “ABB’s system will enable us to make informed decisions, stabilize operations at every stage, and analyze data for our continued journey. It’s an exciting time for us.”
“Together with GreenIron we’re working on fulfilling sustainability objectives that are demanded by the metals industry and wider society,” said Martin Björnmalm, Local Business Line Manager for Metals, ABB Process Industries Sweden. “This is the type of project that underlines our actions in helping industries to outrun leaner and cleaner, and also aligns with an innovative process developed by our customer over many years. With this order, we will work on supporting an impactful industrial solution, bringing our technologies that are entirely scalable for future expansion. Our people are also using their expertise from mining and metals to ensure productivity and efficiency through centralized control rooms, production scheduling, and cost and resource modelling.”
ABB and GreenIron’s technologies are compatible with renewable, intermittent power sources like
solar and wind. The goal is to contribute to the creation of a CO2-free value chain, from the extraction of ore to the production of steel and various metals. Together, these industries account for around eight per cent of global CO2 emissions, according to International Energy Agency (IEA) figures.
As industries undergo increased digital transformation, System 800xA remains key to ensuring safe, efficient and reliable operations,
Together with GreenIron we’re working on fulfilling sustainability objectives that are demanded by the metals industry and wider society
enabling the collection of valuable data and analytics for real-time insights. ABB’s DCS technology has been at the heart of process and energy industry operations for more than 40 years.
ABB is a global technology leader in electrification and automation, enabling a more sustainable and resource-efficient future. By connecting its engineering and digitalization expertise, ABB helps industries run at high performance, while becoming more efficient, productive and sustainable so they outperform. At ABB, we call this ‘Engineered to Outrun’. The company has over 140 years of history and more than 105,000 employees worldwide. ABB’s shares are listed on the SIX Swiss Exchange (ABBN) and Nasdaq Stockholm (ABB).
A customer required a pallet transfer system for the production of gate valves for water pipes, on which the valves could be assembled and buffered. The system needed to transport the valves to the customer’s dipping station where they would be checked for leaks. Three valves are processed on each pallet, making a total weight of up to 250 kg per pallet. The pallets had to have the option to be stopped at the assembly stations. The conveying path needed to be at an ergonomic working height and be secured in accordance with accident prevention regulations (UVV).
The transfer system supplied by mk was constructed out of chain conveyors and accumulating roller chain conveyors. The profile series used was selected to suit the loads being processed. The conveyors form a circuit on which the alignment of the pallets always remains the same, meaning that there was no need for rotating elements. The pallets are stopped for processing at the assembly stations. Here, the pallets are aligned longitudinally to the conveying direction, allowing workers to easily reach every workpiece. Pressing a button releases the pallet again. On the buffering section, the pallets are transported transversely to the conveying direction. This allows a large number of pallets to be buffered one behind the other in a small space. At the transfer to the customer’s dipping station, the pallets are stopped again and transported further as soon as the dipping station becomes free again. The controller and sensors were installed by the customer themselves.
roller chain or a duplex roller chain for higher loads and a larger support surface.
Like all chain conveyors, the system can be equipped with an
optional
tensioning device and continuous lubrication device.
The customer benefitted from the considerable experience of mk in transfer and circulation systems and could rely on them to understand the requirements and execute the best solution.
The KTF-P 2010 chain conveyor is a conveyor system for moderate loads and is ideally suited for transporting workpiece carriers. Its large selection of drives makes it extremely flexible, and it is usually used as the basis for constructing transfer lines. It is available as a single, dual or multiple line system with either a simple
The various chains and wear strip guides allow the workpiece to be optimally placed on the conveyor, while their excellent anti-frictional properties make them extremely low maintenance and sturdy.
Longitudinal slots in the mk 2010 profile beam provide flexible options for connecting struts, guides, sensors and components from the mk profile system.
Like all chain conveyors, the system can be equipped with an optional tensioning device and continuous lubrication device.
The wear and guide strips that support and guide the timing belt are made from ultra-highmolecular weight polyethylene (PE-UHMW), which provides a low friction coefficient with excellent wear characteristics over a wide temperature range (up to 65°C over extended periods).
Ideal as a twin or multiple lane system for transporting pallets or workpiece holders
Load capacity: Up to 500kg
Suitable for dirty and oily environments
Sturdy & low maintenance
Offering products as a service allows users to test new technologies with reduced risks. This is good news for warehouse sorting operations in the parcels, ecommerce and fulfilment sector, where operators can struggle to justify replacing traditional manual processes with robots. To facilitate this changeover, Prime Vision is now offering robotic sorting as a service (RSaaS), allowing its customers to effortlessly implement this highly flexible solution.
Robots have revolutionised repetitive processes, delivering greater efficiency, accuracy and speed in a multitude of applications. This is especially true in sortation operations within e-commerce fulfilment centres and largescale parcel hubs, where workers traditionally sort parcels into roll cages and pallets based on their destination. However, doing this manually is slow, strenuous and error prone. Fortunately, robots are changing this. With advanced navigation systems and advanced software, robots can efficiently move parcels to and from any sorting destination within a predefined area, optimising throughput and reducing reliance on manual labour.
Despite the clear operational benefits of robots – there are barriers to entry. First is attitude. To many, robots are still a solution of the future rather than today, so some operators can be sceptical about replacing a familiar manual process with something they consider experimental.
Next is upfront cost. Buying even a small fleet of robots can involve CAPEX that may not be supported by the budget, giving operators another reason not to automate.
Then there is hassle. To run a fleet of robots, businesses require system design, implementation experts and ongoing maintenance support - all of which can place increased strain on the team and raise operating expenditure (OPEX).
An established technology
Prime Vision is overcoming reservations regarding robotic sorting by providing a proven solution in a flexible service package.
Operating a fleet of over a thousand robots running at the world’s largest postal operators, Prime Vision has standardised this once experimental technology. Standing 1 m high with an 80 x 60 cm loading surface for parcels, each robot can carry small and large packages weighing over 30 kg. Fleets can number from a few robots to over 70, with the ability to move up to 3000 to 4000 parcels per hour. Consequently, Prime Vision robots are suitable for most sorting processes.
This is because robots, equipped with information from the warehouse management system, can drive to any destination within a mapped area, eliminating staged sorting processes and maximising
efficiency. Scalability is built in as operators can easily add or remove sorting destinations, allowing straightforward system optimisation to meet different levels of demand.
LIDAR and an overarching fleet management system ensure safe routing and functionality. With the robots able to detect and avoid obstacles, people can safely enter the area of operation, creating a hybrid space. A shutdown button for the system is also provided.
Considering this install-base, versatility and safety, operators of Prime Vision robots have the assurance of using a proven technology.
Even if attitudes are favourable towards robots, the CAPEX involved in deploying such a solution can be beyond existing budgets. The solution to this is a RSaaS model. Rather than buying hardware, Prime Vision offers its customers a holistic service package that operates on a pay-per-capacity model.
Prime Vision experts will assess the sorting requirements and design a tailored system that integrates with
the existing software and hardware infrastructure of each customer. The team will then implement and deploy the system, carrying out continuous analysis and scaling it up and down as per demand. This model gives operators the chance to try the system and experience the benefits of a right-sized solution without breaking their budget. By paying to capacity, customers only spend on what they are using, ensuring exceptional cost-efficiency.
RSaaS also takes the strain off customer operations teams. The package offered by Prime Vision includes a comprehensive robotic sorting-as-a-service solution, combining cutting-edge technology with seamless integration and ongoing support. From deployment to maintenance, Prime Vision’s service ensures efficient, scalable, and hassle-free automation for sorting operations. This eliminates all the complexities and additional costs associated with ownership. More than that, the continuous management of the system by Prime Vision means total optimisation with no surplus hardware or resource, reducing OPEX.
Prime Vision is overcoming reservations regarding robotic sorting by providing a proven solution in a flexible service package.
This supplier responsibility for the continuous management and optimisation of the robotic sorting system is a benefit in terms of sustainability too. Applying its know-how, Prime Vision can achieve customer aims regarding throughput with the least possible investment of resources. As a service provider, Prime Vision also focuses on maximising the longevity of hardware, carrying out repairs and rejuvenating existing assets when safe to do so. Both contribute to a lower carbon footprint than a traditional ownership model, with the technology expert helping to reduce waste, emissions and resource utilisation.
With the rise of any new technology, there is hesitancy regarding adoption, especially when the transition is from a familiar manual process to a fully automated solution. However, the emergence of RSaaS shows how established robotics has become in complex sorting operations. The fact is that fleets of robots are already streamlining sorting operations within e-commerce fulfilment and parcel sorting centres, reliably moving thousands of items per hour at warehouses around the world.
As attitudes change, it’s about offering cost-efficient options for businesses to trial robotics in their real-world environments.
The highly optimised subscription model of RSaaS from Prime Vision provides exactly this, removing the CAPEX and OPEX of managing a fleet of robots thanks to supplier responsibility for all aspects of the system. Customers only pay for the capacity they need, while accessing a well-supported, highly proficient system that has a big impact on accuracy and productivity. For the parcel and e-commerce fulfilment sectors, robotic sorting is now only one subscription away.
https://primevision.com/robots-as-a-service-simplifies-the-automation-of-sorting-operations/
The L60+ Thermocouple & Fine Wire Welder, manufactured by Labfacility, is a compact, simple-to-use instrument designed for thermocouple and fine wire welding.
It is primarily designed for use by sensor manufacturers to produce commercial grade thermocouple junctions; it is ideal for producing large numbers of exposed junction thermocouples for test and development laboratories. The L60 Thermocouple Welder is ideally suited to transducer and RTD extension lead attachment.
Use of the Thermocouple Welder does not require special skills and most operatives will be capable of producing quality work with little practice. The instrument is supplied with a full range of user accessories including a footswitch.
Suitable for use with wires of up to 1.1mm diameter an argon gas shield facility is included but a satisfactory thermocouple junction is produced without the need for argon. The output energy of the L60 Thermocouple Welder can be varied up to 60 Joules.
• Simple to use Thermocouple Welder
• Designed for the production of commercial grade thermocouple junctions
• Also suitable for other fine wire work
measurement excellence. Here’s to the next 50...
The instrument is supplied with a full range of user accessories including a footswitch.
• Front panel or footswitch operation
• Argon gas shield facility
Supplied complete with the following accessories:
• Wire Holding Pliers & Lead
• Safety Glasses Magnifying Eyeglass
• Argon Hose
• 2 x Carbon Electrodes
• Spare 2A Fuse & Mains Lead
• Footswitch for greater ease of use
• Welder Pen & Plate
• Impact Clip
For more than 50 years we’ve been leading the way in temperature
From small beginnings in 1971, Labfacility has grown and evolved into the UK’s leading ISO 9001-accredited manufacturer and supplier for the complete temperature chain. From Temperature Sensors, Thermocouple Connectors and Cabling to supporting instrumentation and components, we are the GO-TO people for temperature measurement products.
To sustain longevity, you have to evolve...
Our sales team goes above and beyond to provide swift, expert technical advice and support for sensing and instrumentation as and when YOU need it – help is freely available.
Our Sales Team has a mass of experience, plus they are approachable and reliable – just one of the reasons major PLCs and international industry leaders like working with us. Rest assured, you’re in safe hands and not just when it comes to support and advice... For all sales enquiries, please contact us as follows:
Email: sales@labfacility.com
Tel: +44 (0) 1243 871280
With electric mobility continuing to gather pace, recycling highvoltage batteries is increasingly under the spotlight. After successfully launching a closedloop recycling system for the reuse of raw materials from highvoltage batteries thanks to the BMW Brilliance Automotive Joint Venture (BBA) in China in 2022, the BMW Group has now hit another milestone on its journey. On 1 November2024, it launched a panEuropean partnership with SK tes, a leading provider of innovative technology lifecycle solutions. The special recycling process recovers cobalt, nickel and lithium from used
batteries before returning them to the value chain to make new batteries. This closed-loop system is set to expand to the US-MexicoCanada region as early as 2026.
Its long-term partnership with SK tes sees the BMW Group directly involved in the practical recycling processes, allowing it to feed back valuable insights to the development departments. Moving forward, high-voltage batteries from BMW Group development, production and markets in Europethat are no longer fit for use are to be delivered to SK tes in what is the first step towards an
effective and sustainable circular economy for batteries. SK tes then converts the old batteries into high-quality metals that can be reintroduced to battery production. The latter process sees the batteries mechanically shredded, during which the metals are concentrated to leave a material called black mass. The valuable materials, namely nickel, lithium and cobalt, are then recovered in a highly effective chemical process called hydrometallurgy.
Among other things, these secondary raw materials will be used for the new GEN 6 drive train.
“Partnerships like this increase our efficiency in terms of the circular economy. In the closedloop process, all partners mutually benefit from their experiences,” says Jörg Lederbauer, Vice President Circular Economy, Spare Parts SupplyHigh Voltage Battery and Electric Powertrainat BMW AG.
The battery recycling process of SK tes has won numerous sustainability and innovation awards worldwide –from the Business Intelligence Group’s Sustainability Service of the Year to the UN Global Compact’sApex Award.
“The promotion of circular economy is an important strategic topic for the BMW Group. The development of recyclable products, the increase of secondary materials in our components, and the closing of loops play an equally important role,” says Nadine Philipp, Vice President Sustainability Supplier Network at BMW AG. “And by the means of circular economy we are also increasing our resilience in the supply chains.”
The BMW Group follows the principles of Re:Think, Re:Duce,
Its long-term partnership with SK tes sees the BMW Group directly involved in the practical recycling processes, allowing it to feed back valuable insights to the development departments.
Re:Use, and Re:Cycle in the sense of a conservation of resources when it comes to circular economy. From vehicle design and production to recycling and reuse: everything is geared towards ensuring BMW vehicles become a raw materials source for new cars once they reach the end of their useful life.
One such example is the BMW Group’s Recycling and Dismantling Centre. Over a period of 30 years now, the centre has developed processes and put them into practice, making key progress in parts and materials recycling.
Surface testing for curvy and small surfaces / Data memory for 1,245 readings / Measuring geometry 60° / Evaluation also possible without additional software / One-key operation / Calibration standard included
The gloss meter has a measuring surface of Ø 4.5 mm. Thanks to this small measuring surface, the gloss meter enables measurements on particularly small surfaces. With a maximum inaccuracy of 1%, the gloss meter is a high-precision measuring instrument for fast and easy measurements on surfaces. The one-button operation allows quick and easy operation of the surface inspection device.
Another special feature of the gloss meter is the data storage function. This gloss meter automatically stores up to 1,245 measurements. To read the data, the gloss meter must be connected to a computer. No additional drivers or software are required to read the data from the gloss meter. The stored data is saved in the .txt file format on the surface inspection device and can be analysed directly. In addition to the storage of the measured data, a time stamp is created per measurement.
Gloss measurement on curvy and small surfaces
Gloss is one of the criteria that is always taken into consideration when it goes about quality assessment. Correct analysis of the gloss of a certain surface helps to make conclusions about the quality and whether the necessary standards have been met during the production or repair process. Excessive or insufficient gloss may be an indication of the application
of the wrong methods and time of the surface treatment, wear-out, deteriorating condition, and loss of the protective function, since gloss has not only optical effect, but very often, it also performs protective function if coating is applied.
Measurement on the even flat surfaces is an easy-to-perform task, but it often happens that the surface is curvy or the area to be measured is very small. For such challenging tasks a small portable gloss meter has been designed and due to this device even the measurement on the most complicated surfaces has become feasible. Operation of the gloss meter is easy, but the user should remember to be careful to obtain the most accurate results. The sample to be measured or some part of it must be in a stable position as well as the meter and
for each separate part of the curvy surface the upper and lower gloss limits should be determined separately. The convenience and possibility to get the best measuring position is also provided by the design of the measuring instrument. A small measuring window as well as the support area is so small that the device can be applied even on the tiniest parts of the surface. The examples of curvy surfaces may be numerous: parts of the automobiles, bottles, ceramics, window frames, doors, such materials as marble or granite etc. The gloss meter applied on such surfaces carries out the measurement continuously and thus, even the most complicated geometry of the surface, where the character of the surface changes does not prevent the device from getting very accurate data. Application of the other measuring instruments for this purpose does not compare in accuracy with the results provided by the gloss meter.
Gloss – is one of those parameters that has got its own paragraph in ISO requirements, which means that as all the other parameters, it should be treated with attention
and responsibility. Curvy surfaces often have more functionality and a much better optical look, and should not be ignored and left in the background by the producers just because the measurements on them are much more challenging.
ISO 17025:2017 Spectrophotometer Calibration
AMECaL is a Precision Calibration Laboratory accredited with ISO/ IEC 17025:2017. With more than 20 years of experience and thousands of satisfied customers, we have managed to build a stable position on the market. AMECaL is also a brand of its own, selling certified electrical and environmental test equipment to customers all around the world.
All test equipment should be calibrated to ensure that its measurement scale is always accurate and reliable. Due to common wear and tear of an instrument this may not always be the case. Factors like temperature, humidity, pressure and bad user-handling contribute to errors in measurements, which is why calibration services are so important and can save customers a lot of money in the future. Our laboratory is specialised in Spectrophotometer calibration. All measuring equipment naturally drifts with time and require recalibration and adjustment. Spectrophotometer are not an exception to this trend and that is why it is so important to keep them in optimal working order.
AMECaL offers calibration services in accordance to the ISO/IEC
Application of the correct device destroys this type of obstacle and turns the challenging tasks into doable.
- Data memory for later evaluations
- For measurements on small surfaces
- Measuring range up to 1000 GU
- Precise measurements thanks to high accuracy
- Micro USB interface for PC connection
- Simple one-button operation
17025:2017 standard (ISO 17025 spectrophotometer calibration) or National Traceability Standard (traceable spectrophotometer calibration). We understand that every situation requires an individual solution and that is why we are open to custom quotes.
AMECaL is one of the world’s foremost laboratories in the specialised field of optical measurement.
AMECaL has spent many years researching and developing a method of calibration relating to optical gloss measurement. This now allows both instruments and reference standards to be calibrated against measurement standards traceable to international/national measurement standards. ISO/IEC 17025:2017 & ISO 2813:2014
AMECaL also manufacture Reference Standards, to client’s high specifications, distributing them to
an international client base. The innovation of new calibration methods in this highly specialised field is not the only cutting-edge development to the company’s name; AMECaL also excels in complex - and related - areas Our expertise extends to developing new equipment as well; currently in development is our Goniophotometer – which will have some of the best accuracies in the world – some 20 times more accurate than the best available today from NIST USA or NCR Canada
Ongoing technical developments in unique and very specialist areas like these, alongside an ability to deal with an ever-increasing portfolio of products, have put the company at the forefront of calibration know-how.
Universal Robots and Ultima Forma collaborate to fuel the
Ultima Forma, a UK-based technology pioneer, has joined forces with global leader in collaborative robotics (cobots) Universal Robots, to tackle a critical challenge: net-zero aviation. The partnership combines advanced robotics with cutting-edge materials science to help power the next frontier in alternativepropulsion technology from as early as 2035, with the longterm aim of reducing global CO2 emissions by up to 4%.
Liquid hydrogen fuel is one of the most promising technologies to reduce aviation’s climate impact, but it has to be stored in tanks at temperatures below -250°C. This means that the materials used need to be ductile and strong at these very low temperatures while also being lightweight as every
kilogram is critical in an aerospace application.
Ultima Forma has developed a multi-layer solution which combines very thin layers of different metals to tune the properties of the material to remain strong at low temperatures. However, the process needs to be done with great precision each time.
Universal Robots’ UR10e provides Ultima Forma with the means to control the deposition of the metal in each step of the process delivering up to 0.1 millimetres precision – something that is not possible with human workers alone.
“The high level of control that advanced robotics allows us to
have is essential for the quality standards required in aerospace manufacturing,” says Professor Andy Bushby, Chief Technology Officer at Ultima Forma. ”This precision is only achievable with Universal Robots’ cobots as it guarantees the quality and repeatability of those parts, providing our customers with assurance of nanometre-level consistency. Our vision is to use material science, advanced technologies and key partnerships, with companies like Universal Robots, to accelerate the shift toward sustainable energy and help shape the future of aviation.”
With little to no coding or robotics experience required, Ultima Forma was able to get the UR10e unboxed and up and running to a basic level within four hours.
“Our collaboration with Ultima Forma is the perfect example of how advanced robotics can play a critical role in transforming industries and addressing global challenges,” adds Mark Gray, UK & Ireland Country Manager at Universal Robots. “Our cobots are designed to deliver the kind of precision and flexibility needed to tackle complex manufacturing challenges in industries like aerospace. We are proud to be playing a role in Ultima Forma’s mission to decarbonise the aviation
With little to no coding or robotics experience required, Ultima Forma was able to get the UR10e unboxed and up and running to a basic level within four hours.
industry and look forward to seeing this go beyond the R&D phase in future.”
Universal Robots is a global leader in collaborative robotics (cobots), used across a wide range of industries. Our mission is simple: Automation for anyone. Anywhere. With over 90,000 cobots sold worldwide, our user-friendly platform is supported by intuitive PolyScope software, awardwinning training, comprehensive services, and the world’s largest cobot ecosystem, delivering innovation and choice to our customers. Universal Robots is part of Teradyne Robotics, a division of Teradyne (NASDAQ:TER), a leading supplier of automatic test equipment and advanced robotics technology.
About Ultima
Ultima Forma is the UK’s awardwinning pioneer in net-shaped multi-material component production. They specialise in creating components by electrodeposition with meticulously graded material properties, delivering unparalleled performance across diverse sectors including aerospace, automotive, and beyond.
For more information, please visit www.universal-robots.com. | www.ultima-forma.com.
MSc - 1 year full time
time part time Certificate for CPD
MSc - 1 year full time
MSc - 2 or 3 year part time
PG Diploma • PG Certificate
MSc - 2 or 3 year part time
Short Courses for CPD
Designed
Designed
LS Wastewater & Process Consulting Limited offers bespoke consultancy services for Water Process management and monitoring, with a long-term focus on energy and environmental conservation. Together with its sister company, Leachate Solutions: an industryleader in closed landfill engineering and bespoke leachate treatment plants, our consultancy brings over 35 years industrial experience, and an extensive network of engineering professionals working across the water and process industries.
LS Wastewater & Process Consulting Limited has considerable expertise in the following four overarching areas:
• Leachate Monitoring and Treatment: Customised solutions focused on compliant and sustainable discharge and monitoring protocols
• Robust Maintenance & Management Plans: Expert-led closed landfill and leachate management systems.
• Tailored solutions: Meticulous site assessments and surveys are carried out prior to any advice or recommendations being discussed or offered
• Adherence to environmental regulations: All advise is in alignment with current Environmental Agency, or HSE regulations so removing any ambiguity, and avoiding unnecessary issues with stakeholders or regulators.
LS Wastewater & Process Consulting offer informed, expert-led
solutions for water and wastewater management across the entire process industry, agriculture, farming and closed landfill applications.
Using LS Water and Process Consulting, ensures you have all the tools and expertise at your disposal, enabling you to optimise and monitor your business development, while at the same time ensuring you remain compliant with current regulations
Using a consultancy service can bring a multitude of benefits such as pinpointing blockages and optimising process plant efficiency, streamlining process performance without rising costs and methodical action points to upgrade structural processes.
With all UK companies now looking for sustainable best practices, and a route to Net Zero, LS Wastewater & Process Consulting Limited and its sister company, Leachate Solutions pride themselves on providing innovative, futureproofed solutions for the water and process industries, as demonstrated by Leachate Solutions reaching the finals of the Lancashire Business Environment Awards 2023.
To enquire further about our comprehensive consultancy practice, and find out more about the services we offer, see the website and details below:
Tel: Mobile 07764449299 | Email: info@lswpconsulting.com | www.lswastewater.com
Pioneering Consultancy for Landfill and Environmental Management. Your trusted partners in Environmental Consultancy
We’re more than just consultants: we’re your partners in achieving your organisation’s goals.
Our commitment is to provide bespoke solutions for every project, regardless of size. Our team brings over three decades of engineering expertise to the table, delivering long term solutions with a focus on cost efficiency, energy conservation and sustainability.
Closed Landfill Expertise
Management
Monitoring
Treatment
Tailored Solutions
Regulatory Alignment
Water & Wastewater
Management
Monitoring & Control
Cost Control
Quality Monitoring
Rainwater Cost Reduction
Process Performance & Management
Monitoring & Control
Productivitv Enhancements
Systematic Analysis
Cost Effective Solutions
As industries evolve with developments in automation, digital transformation, and sustainability, it is essential to recognise that core mechanical safety systems remain fundamental. Regardless of how sophisticated technology can and will become, robust mechanical solutions are vital to ensure ultimate worker safety and operational security.
Industrial operations continue to transform, but the importance of implementing and maintaining reliable mechanical safety measures cannot be overlooked. Key trends we are seeing shape the industry include:
The rise of Industry 4.0 has established intelligent systems and real-time monitoring into industrial environments – and this is fantastic for the future of industry. However, while digital innovations enhance operational efficiency, they must be supported by fundamental mechanical safeguards to ensure fail-safe protection of the people involved. For example, a data centre, which is an enabler of industry 4.0, requires UPS (uninterruptible power supply) to provide continuous power to critical equipment, ensuring minimal downtime and protecting sensitive data from loss during power interruptions. The UPS needs to be secured with reliable trapped key interlocks to ensure the safety of those who need access to maintain it. Safety therefore cannot rely exclusively on digital systems alone – mechanical trapped key interlocks and other physical safety measures provide a critical and essential layer of security that remains
effective regardless of technological advancements.
As regulatory bodies advocate for more sustainable industrial practices, safety solutions must align with both environmental and workplace safety standards. Durable, longlasting mechanical systems play a crucial role in reducing workplace incidents, minimising downtime, and ensuring compliance with global safety regulations. These foundational solutions contribute to safer and more sustainable industrial operations in the long run.
With the increasing presence of automation in high-risk environments, ensuring robust safety measures at the foundation of operations is more important than ever before. Properly implemented mechanical safety solutions prevent unauthorised access to dangerous areas and help mitigate the risks associated with the maintenance of automated machinery.
According to Deloitte’s 2025 Manufacturing Industry Outlook, manufacturers are prioritising highROI use cases such as customer service and product innovation while leveraging AI for efficiency and cost savings. Investments in data lifecycle management are also a growing focus as companies work to overcome challenges related to data quality and accessibility. However, despite the shift towards digital transformation, maintaining core safety infrastructure remains imperative to ensure operational resilience and the protection of personnel.
For over 100 years, Castell Safety International Ltd, part of the Sentric Safety Group, has provided reliable and high-quality safety solutions across industries in harsh and safety-critical environments. As industries continue to embrace new technologies, Castell remains committed to delivering safety solutions that integrate seamlessly with evolving industrial needs. A longstanding dedication to excellence also means that businesses who partner with Castell can operate with confidence, knowing that foundational safety systems are in place and can be effectively maintained.
Leachate Solutions is an industryleader in closed landfill engineering and leachate treatment plants. With over 35 years’ experience working with Local Authorities (LA’s) on discharge from closed landfill sites, Leachate Solutions was founded in 2015.
The Preston-based company is the UK’s only designer and supplier of the state-of-the-art Airless Methane Stripping Plants for customers around the country, specialising in all closed landfill site services, and solutions for the process and wastewater industries.
The traditional method of using forced air 24/7 to remove methane continues to be widely used but the technology is old, has a high energy usage, significant maintenance costs, and is not environmentally friendly.
The new cutting-edge Fully Automated Airless Methane Stripping Plant System utilises ondemand principals, saving spiralling energy costs and uses stainless steel instead of plastic.
“This technology drastically reduces energy usage and harmful emissions, with a low visual impact and reduced noise pollution. The reduced sludge production and combined low maintenance and operational costs combined makes this the technology of choice for dissolved methane stripping in a wide range of applications from farming to construction across the UK.” explained Jane Rostock: Director.
This technology drastically reduces energy usage and harmful emissions, with a low visual impact and reduced noise pollution.
Leachate Solutions also provide a number of services – for managing water & wastewater, whether it is in the Process industry/ agriculture & farming or closed landfill.
• Control & monitoring services –pump control / management
• Pumping services – supply & Installation / repairs / pump Hire
• Specialise engineering projects
– Treatment & Management of Attenuation Lagoons
From supply & installation of a variety of pumps for most situations
– to – managing & servicing Lagoon projects & pumps
All our pumps and associated equipment are sourced from trusted manufacturers that can support all projects from dewatering to emergencies. Our size ranges from 2” to 12” we have an extensive range of environmentally friendly pumping products to support companies with a variety of pumping options.
“All companies need to apply for and comply with environmental permits from the Environment Agency to discharge liquid effluent or wastewater into surface waters, or into storage lagoons, We offer full consultancy for all closed landfill and process industry work. Our chief Solutions Engineer, Carl has been designing & creating bespoke solutions for many years and can provide onsite assessment for your situation
With many companies looking for sustainable best practices, and a route to Net Zero, our Fully Automated Airless Methane Stripping System has been designed to meet the latest regulations, and we welcome any enquiries from new and existing customers.
Cross+Morse is a Birmingham based manufacturer of Mechanical Power Transmission products and solutions with over 100 years of history, right in the centre of the engineering hub in the West Midlands region in the United Kingdom. We operate in a 5000m2 fully integrated factory with a dedicated and loyal staff who have amassed a depth of technical expertise and engineering experience over our many years of continued service.
and service we are well known for. With our in-house team of application and design engineers at your disposal Cross+Morse are able to provide bespoke technical solutions to your power transmission problems in the most costeffective way.
Cross & Morse are Mechanical Power Transmission solution specialists and at this present time we have £1.5m worth of finished stock on our shelves such as Roller Chain and Sprockets in both stainless and carbon steel, Gears, Racks, Couplings, Torque Limiters, Sprag Clutches, Timing & V belt Pulleys, timing & V Belts, Inverted Tooth Chain, Silent Chain, Sealmaster Bearings, McGill Cam followers, Shaft Clamping Elements, Freewheel & Overload Clutches.
We value innovation highly at Cross+Morse, which is why we constantly invest in new machinery and technology as well as training programmes and apprenticeships to maintain the highest standards of quality
Have a specialised or ambitious requirement? Send us your drawings and application details and we will do our utmost to find the best solution possible, we welcome a challenge! We have been providing solutions for the food and drink, oil & gas, agricultural, pharmaceutical, quarrying, energy and environmental industries, bottling and packaging plants and many more for over 100 years. Our customers come from the widest range of industries and include original equipment manufacturers for packaging, conveying systems and material handling applications. We also export our quality products all over the world, through our network of long standing distributors or directly to the manufacturers and end users of mechanical power transmissions on every continent.
At Cross+Morse we consider customer
support along with in-house design and manufacture an essential element in our service to industry, please browse our website for details and more information on our manufacturing capabilities as well as our stringent quality control. We are certified to ISO 9001:2015 and have been for over 25 years.
Call or email us now to solve your mechanical power transmission problems.
mk have been working intensively to further develop their conveyor technology offering with a range of innovative products and expansions. One of their latest developments, Versamove Electric, is focused on enhancing efficiency, versatility, and environmental sustainability.
Versamove is a modular transfer system for transporting workpiece carriers that can be optimally tailored to the customer’s specific requirements. mk have now added an electric version to the Versamove Standard weight and size class, offering customers a much greener option.
Modular. Versamove’s modular design allows for quick and transparent scheduling and project planning. It has the flexibility to be expanded and is perfect for adapting to conditions on site.
Compatible. While developing the system, mk ensured its compatibility with other systems currently available on the market, for example those from Bosch. As a result, thirdparty workpiece carriers can be used on the Versamove standard. It is therefore possible to extend existing systems effortlessly.
Versatile. Versa stands for versatility. Versamove can be used in virtually all automation and material flow applications.
Transfer lines are constructed from proven mk dual-line conveyors with timing belts, chains or accumulating roller chains, depending on your application. These are then
combined with basic modules such as lift-and-transfer conveyors, positioning units, stoppers and lifts to create a transfer system that is precisely tailored to the customer’s needs.
mk’s Versamove, standard electric has a range of fully electric functional units. For efficient and environmentally friendly process automation, the lift-and-transfer conveyor HQZ, the lift-and-rotate unit HDE, the lift-and-locate unit PE, and the stopper SU/SD are now also available in fully electric variants. This completely eliminates the need for a compressed air supply and can be retrofitted into existing Versamove standard systems with ease.
Versamove standard transports workpiece carriers from 240 x 240 to 400 x 400 mm, with custom
dimensions or dimensions in 80 mm intervals possible. The system can move pallets weighing up to 40 kg. The special feature of this system is its affordable curve modules, which are equipped with a flat top chain or, for compact curves in tight spaces with a round belt.
Other example Versamove accessories include the ZRF-P Timing Belt Conveyor, the SRF-P Accumulating Roller Conveyor, the FPF P 2045 Flat Top Chain Conveyor, as well as a workpiece carrier.
As the sole distributor of mk products in the UK and Ireland, AdaptTech is the only place that this new product can be purchased. Visit their website now to find out more and to download a free brochure.
Email info@adapt-tech.co.uk Call (01949) 823751
No compressed air required
Pre-assembled cabling (Plug & Play)
Quick commissioning
Now
fully electric
High energy efficiency – more environmentally friendly
No hidden cost drivers such as air leaks
Unit 9 Dale Mill, Hallam Road, Nelson, Lancashire, BB9 8AN WIDE RANGE OF STOCK AVAILABLE FOR NEXT DAY DELIVERY
Fibet Rubber Bonding (UK) Ltd
A leading US automotive supplier revolutionised its aluminium machining and cleaning process with HAKUFLUID® 185 and HAKUPUR 439-1, achieving cleaner parts, extended bath life, and improved sustainability.
Switching to HAKUFLUID® 185 a mineral oil-free, watersoluble coolant, eliminated oil contamination in the HAKUPUR 439-1 neutral cleaner bath, preventing re-contamination of aluminium die-cast housings. This ensured consistent cleanliness and longer bath life—extended from one to three weeks—while maintaining productivity.
Trials confirmed foamfree, stable cleaning baths, reducing maintenance and non-conforming parts. The plant further optimised efficiency by lowering bath
temperatures from 60°C to 40°C, cutting energy costs and enhancing biostability.
By embracing oil-free technology, the supplier not only met strict cleanliness standards but also significantly reduced environmental impact— setting a new benchmark for sustainable aluminium machining and cleaning.
INDUS Engineering Services is proud to offer a wide range of custom control panels, automation systems and special purpose machinery. After working on major control and automation projects for several of the south’s leading brands, the company has recently acquired a new premises with the aim of increasing production capacity of bespoke and sub-contract, control panel manufacture. The new premises will also allow us to support the wider range of engineering
INDUS Engineering Services is proud to offer a wide range of custom control panels, automation systems and special purpose machinery. After working on major control and automation projects for several of the south’s leading brands, the company has recently acquired a new premises with the aim of increasing production capacity of bespoke and sub-contract, control panel manufacture. The new premises will also allow us to support the wider range of engineering
activities carried out by the company, such as the design, manufacture, and testing of special purpose machinery. Also, to further our goals to reduce our carbon foot print we will be installing a high efficiency solar PV array in the coming months. For more information on the services that are available please do not hesitate to contact and we will be happy to discuss your project needs and requirements.
activities carried out by the company, such as the design, manufacture, and testing of special purpose machinery. Also, to further our goals to reduce our carbon foot print we will be installing a high efficiency solar PV array in the coming months. For more information on the services that are available please do not hesitate to contact and we will be happy to discuss your project needs and requirements.
www.indusengineering.co.uk
www.indusengineering.co.uk
– OIL-FREE COOLING LUBRICANTS
Precision Performance: Delivers consistent performance & cleanliness in machining with a safer, eco-friendly EHS profile.
info.uk@kluthe.com
+44 (0) 330 175 9970
www.kluthe.com www.kluthe.com
We have been supplying threading tools and gauges since 1987.
Together with supplying plain plug and ring gauges this is all that we do, we therefore consider ourselves to be specialists in this field.
We supply worldwide.
We hold extensive ready stocks that include all of the standard stuff that others offer, but also includes taps, dies, die nuts, die head chasers, thread rolls and gauging for threads not normally available 'off the shelf '.
Our real time stocks can be checked and purchased online at www. threadtools.com Just enter the thread details into the search box on the home page.
You will be directed to the item, if stocked, or to our specials, (custom manufacture), sales team. who will quote to supply at competitive rates, in good time.
As an account holder you can also order online from our listed in stock items, at your normal terms. We realise that you need the right item at the right price and quality, and in a reasonable time frame.
We are geared to provide that.
We can ship stocked items same day.
Our experienced sales staff can assist and advise you on any technical issues.
We welcome enquiries from resellers and can offer terms to suit.
WISEMAN THREADING TOOLS LTD
11 Padgets Lane, South Moons Moat, Redditch B98 0RA UK
+44(0)1527 520 580 sales@threadtools.com www.threadtools.com
HSS DIES & DIE NUTS
HSS DIES & DIE NUTS
THREAD ROLLS FOR ALCO & FETTE HEADS. READY STOCKS CUSTOM MANUFACTURURE
Large shelf stocks for all Standard and many Special Threads. Check our stocks online.
Large shelf stocks for all Standard and many Special Threads. Check our stocks
THREAD GAUGES all types. Large stocks for standard and SPECIAL threads. Any non stocked can be quoted for custom manufacture. CHASERS
THREAD GAUGES all types. Large stocks for standard and SPECIAL threads. Any non stocked can be quoted for custom manufacture. CHASERS FOR COVENTRY
HEADS
stocks for most size heads most standard and some special threads Geometry available for most materials.
Andrew Jones, the Technical Director at Axair Fans talks about their most recent disruptive campaign; We’re Revolting, and specifically how their revolt has led to better results for customers in the industrial fan industry.
I’ve gone into the reasons for our revolting images being scattered around everywhere over the last 9 months, and over that period I’ve spent a considerable amount of time discussing the positive outcomes of the messaging while out on customer visits.
You see, it’s one thing to say something, but getting all those ducks in a row and delivering on them is another, entirely different beast. It takes a companywide collaboration on optimising sales processes, enquiry escalation, technical support hierarchies, and setting achievable service level agreements that every employee commits to.
Firstly, Let’s discuss response times, an inherently unrecognised pain point for most customers in all industries. The meatiest enquiries are replied to and actioned, the small but profitable fish are handled a few days later, while those deemed too small are ignored, discarded with no response to even highlight to the customer that the supplier is unable to give a commercial offer. It’s a bit like applying for a job when you’re 16, if you have 10 years’ experience in coding at 16, you’ll be replied to, but a school leaver with no experience is ghosted, losing motivation and self-esteem with every failed application.
immediately when compared to what they’re used to.
Our proactive response times have been recognised wholeheartedly by our new and existing customers.
When a simple reply to feedback on why they were deemed unsuccessful would go a long way on improving cv quality or actions to take up some volunteering to bolster the experience for example.
Our proactive response times have been recognised wholeheartedly by our new and existing customers; the positive feedback is far greater when the issue is pointed out through visual messaging. It’s made customers recognise the value
Secondly, I’ll touch on one of the most important aspects, technical support. I won’t blow my own trumpet, but I consider myself to be one of the niche fan men that have a unique and natural affinity for physics, and air or fluid movement. Just generally engineering problem solving, it gets me in my flow –meaning it’s where my energies lie best. Not in spreadsheets or analysing sales figures. In a strong man competition, I’m going to liken our pre and after sales technical support to the Stoltman brothers, consistent and likely to lead, you can place your bets and know you’ll probably win backing one of them. Customers recognise this too, they’ve gained a huge amount of trust in our team, that creates barriers to entry for competitors who can only offer price as their leading offer. What use is a product without the reliable backup of presale’s accurate selection, after sales technical and a team committed to service level response times on issues? It’s a difference between saving a few quid on each component, against getting a unit on site, back up and running within a day compared to 6 or more weeks.
I’d call it a result when we’re getting phone calls and emails requesting our “revolting service”, or compliments from brand new enquiries expressing how impressed they are that a simple, yet highly important aspect of response times has been identified and actioned for customer benefit flood in.
Just like AJ in the picture, we’re revolting! We’re changing the rules of the game, breaking the mould. Response times that take some companies days, only take us minutes. Pre-sales and after-sales support is based around your needs not ours, because our job is to empower you. So as they say in Stoke, viva la revolution! Join us now.
Axair. Revolutionary Fan Expertise.
As industries embrace digital transformation, seamless communication between field devices and higher-level systems is critical. IO-Link has emerged as the key enabler of Industry 4.0, offering intelligent, bidirectional data exchange from sensors to cloudbased platforms. Pepperl+Fuchs is at the forefront of this revolution, providing a comprehensive portfolio of IO-Link solutions that bridge the gap between operational technology (OT) and IT.
Pepperl+Fuchs delivers a full suite of IO-Link-enabled sensors, infrastructure components, and interfaces that enhance efficiency, transparency, and predictive maintenance. The Sensorik4.0® portfolio includes:
• IO-Link Masters with OPC UA Interface – A ground breaking innovation that combines IO-Link and OPC UA in a single device, ensuring seamless data flow from the field level to the cloud. This enables real-time analytics, predictive maintenance, and Industry 4.0 applications.
• Advanced Sensors with IO-Link
– From RFID-based Kanban systems to ultrasonic and photoelectric sensors, these intelligent devices provide rich diagnostic data, improving asset utilisation and reducing downtime.
• Plug-and-Play Connectivity
– Standardised three-core cables and automatic device recognition simplify installation,
commissioning, and sensor replacement, lowering costs and operational disruptions.
Unlocking the Power of IO-Link and OPC UA
By integrating IO-Link with OPC UA, Pepperl+Fuchs enables machineto-machine and machine-to-cloud communication, ensuring the accessibility of sensor data beyond traditional control systems. With this approach, businesses can:
• Implement predictive maintenance by detecting issues such as sensor contamination before failures occur.
• Achieve seamless IT/OT convergence, making operational data available for AI-driven
analytics and decision-making.
• Enhance flexibility and scalability, enabling adaptive manufacturing and smart intralogistics solutions.
With the continuous expansion of its IO-Link portfolio, Pepperl+Fuchs is driving digitalisation across industries. Whether for warehouse automation, AGV navigation, or digital inventory management, its IOLink solutions empower businesses to stay ahead in the industry 4.0 era.
Because innovation starts at the sensor level, prepare for the future with Pepperl+Fuchs’ intelligent IOLink solutions.
Get in touch for additional product details or general inquiries.
Tricia Fleming | Pepperl+Fuchs
• +44 161 6336431
• sales@gb.pepperl-fuchs.com
Sensors and Systems with IO-Link
• Complete IO-Link solution from a single source: sensors, masters, and infrastructure
• Ready for Industry 4.0 and IIoT: future-proof with an open, manufacturer-independent standard
• Predictive maintenance: realtime diagnostics simplify troubleshooting and reduce downtime
• Increased system availability and reduced installation costs
www.pepperl-fuchs.com/tr-io-link
In an era where industrial automation is the backbone of manufacturing, JUMO stands as a global leader in sensor and automation solutions. With 75+ years of expertise, JUMO has redefined process control by offering intelligent, adaptable, and high-precision systems designed for critical industries such as food & beverage, pharmaceutical, chemical, water treatment, and energy.
At JUMO, our commitment goes beyond components—we deliver end-to-end solutions that optimize efficiency, increase reliability, and drive digital transformation. From the sensor to the cloud, our technology integrates seamlessly to provide real-time data, ensuring smoother operations and enhanced process reliability.
As a leading system and solution provider of sensor and automation technology we provide you with expert advice from the field to the monitoring level and effectively combine the stages of the automation pyramid that are relevant for the production and process industry. The requirements of the safety zone are also taken into account. What you get from us:
• Comprehensive Process Automation – Our scalable solutions cater to industries requiring precise measurement, control, and automation.
• Digital Integration – JUMO’s connectivity solutions, including IO-Link, PROFINET, and JUMO Cloud, facilitate real-time monitoring and predictive maintenance.
• Industry-Specific Expertise – We tailor automation solutions to meet regulatory and process demands in diverse industrial sectors.
• Sustainability & Hydrogen Technology – With H2-ready sensors and process automation for clean energy, we actively support the transition towards a greener future.
Whether enhancing existing systems or designing new, futureready automation architectures, JUMO provides the technology and expertise to streamline industrial processes.
JUMO meroTRON 104/108/116
Modular one-channel/two-channel controllers with PLC function
104/108/116
• Customizable device menu for user-friendly integration into a wide range of applications
• PLC function with programming via ST code including real-time clock as well as with direct access to operation and display
• Planning security through scalable hardware with Plug and Play
• Communication via USB, PROFINET, Ethernet, and RS485 (Modbus master/slave TCP/RTU)
• Calibration of analog inputs according to CQI-9 and AMS2750
• Large variety as well as large number of analog and digital inputs and outputs
Applications: Industrial furnaces, baking ovens, tempering equipment, and chemical processing
JUMO flowTRANS US W02
Ultrasonic flowmeter
• NEW: now with pressure measurement cell
• Reduced maintenance costs due to low-wear design without moving parts
• High degree of process reliability through precise measurement
• Metal-free design for use in
corrosive media and environments
• Simultaneous measurement of up to 3 measurands (flow, temperature, pressure) at 1 measuring point
• Simple, convenient configuration and operation via Bluetooth using the JUMO smartCONNECT app
• Time and cost savings during configuration as well as the integration in plants and sensor networks through IO-Link
• Connection also possible via analog interfaces and/or pulse output
Applications: Reverse osmosis, desalination of seawater, cooling tower
JUMO DELOS S02
Precision pressure transmitter with switching contacts and display
• Pressure transmitter for liquid and gaseous media
• High degree of process reliability due to maximum accuracy and long-term stability
• Easy configuration via Bluetooth/ smartphone app or IO-Link
• Ethernet-based version available
• Direct cloud connection possible
Applications: Pharmaceutical, food processing, and industrial HVAC systems
www.jumo.co.uk |
JUMO variTRON 500 touch
Touch panel with integrated central processing unit for the automation system
• Touch panel and central processing unit in 1 device
• Application creation with CODESYS V3.5 and with NodeRED
• Creation of clear process and plant visualizations as well as user interfaces
• Full connectivity to systems and components thanks to support for numerous fieldbus systems (such as PROFINET IO-Controller and EtherCAT master) as well as modern communication protocols like OPC UA
• Reliable control technology with independent PID controllers including autotuning function
Applications: Large-scale process plants, batch control, and customized automation
JUMO is more than just a technology provider; we are a strategic partner in automation and process control. With a focus on efficiency, connectivity, and sustainability, our solutions help industries achieve greater productivity, compliance, and long-term operational excellence.
Discover how JUMO can transform your automation strategy.
Visit our website for more information or contact our expert team at the below details for tailored solutions.
Automation and control supplier, Beckhoff, has launched TF38, a new addition to its TwinCAT 3 automation software package. TF38 seamlessly integrates machine learning (ML) capabilities into industrial automation processes, setting a new standard for intelligent manufacturing.
The TF38 function offers a highperformance execution module, or inference engine, designed for the real-time application of trained machine learning models. By supporting established frameworks such as SciKit-Learn, libSVM, and XGBoost, TF38 enables the execution of a wide array of ML algorithms directly within the automation environment. This integration allows for enhanced data analysis, predictive maintenance and optimised production processes.
A key feature of TF38 is its support for the open neural network exchange (ONNX) format, an open standard that facilitates interoperability between various ML frameworks. This ensures that models trained in diverse environments can be seamlessly deployed in TwinCAT 3, providing flexibility and efficiency in developing and implementing ML solutions.
“The introduction of TF38 is a significant milestone in the convergence of machine learning and industrial automation,” explained Beth Ragdale, product manager at Beckhoff UK.
“Embedding advanced analytical functionalities directly into our control systems enables our
The introduction of TF38 is a significant milestone in the convergence of machine learning and industrial automation.
customers to achieve exceptional levels of performance and efficiency.”
The TF38 function is designed to process all inputs, outputs and internal data from the automation controller using machine learning algorithms. This capability not only improves product quality but also supports real-time classification of
machine operational states. By training models with historical data, the system can execute ML models on PC-based controllers, allowing immediate actions to be implemented within the automation system.
Beckhoff’s innovation is further demonstrated by the integration of TF38 into the existing TwinCAT 3 environment. Users can leverage familiar tools and interfaces to develop, train and deploy ML models, reducing the learning curve and accelerating the adoption of advanced analytics in industrial applications.
For more information about TF38 and how it can transform your automation processes, visit the Beckhoff website.
For further information, please visit www.beckhoff.co.uk
Prediction of phase composition and mechanical properties
GS-MR Robotics explore how their patented PRO:Load robotic glass loading system is automating the industry leading IGU manufacturing lines which continue to come with manual loading as standard.
Most of us have IGU double glazing at home but are we aware of the manufacturing techniques employed to make our windows? We can leave the manufacturing details to the experts because glass is a dangerous commodity, right?
Is it a revelation to discover with the level of technology available throughout the manufacturing world, the glass processing machinery manufacturers latest automated high specification IGU production lines still utilise manual loading and unloading as standard? Operators set to load glass panes of all sizes and weights, including patio door sized, throughout their shift for ‘Living Wage’?
Challenges
innovation bringing progress where none was considered possible.
And it’s the same at the end of the ‘automated’ processing line, although unfortunately the IGU is now 2 or 3 times heavier than at the loading end.
A fully automated manufacturing IGU line dependent upon manual labour in two key production areas is indicative of where the glass processing industry is placed regarding meaningful automation.
It should be no surprise then the glass industry has labour issues –loading tonnes of glass every day for the living wage and not much more.
Only long standing IGU machinery manufacturers can explain why they
have failed to produce a proactive automated IG loading system within reach of SMEs budgets. The continuing reliance on a manual handling process which contributes to producing significant amounts of waste is questionable, although having been adopted in excess of 50 years ago, you will struggle to find a video demonstrating the process to any degree.
Manufacturers maintaining their insistence that modern IG processing lines continue to rely on manual loading enables the industry acceptance of that creation of waste, with social media posts proudly showing tonnages of cullet returned for recycling as though cullet glass isn’t waste.
Whilst other industries have accepted automation the glass industry has remained hesitant to acknowledge it could be the necessary avenue securing its future commercial competitiveness.
In 2018 GS-MR Robotics were busy designing automated systems with glass industry issues in mind,
solutions that would challenge the continuing heavy reliance on manual processes, reviewing issues from the recruitment and retention of labour, to increasing costs and stabilisation of production quality.
Feedback from the industry towards robotic automation was anticipated, with a firm reluctance to accept automation could handle glass in its raw state and on its edge, regardless of the already multiple proven automated systems successfully handling other complex commodities throughout global industries - interesting to note the emphasis being placed upon a robot possibly breaking glass when operators had to regularly deal with the impacts of broken glass.
In comparison to other manufacturer’s loading solutions incorporating substantial footprints and major capital investment whilst loading unverified glass, GS-MR Robotics took the proactive and ergonomic route, manufacturing their patented PRO:Load solution loading verified glass automatically via its edge, removing any damage to glass special coatings - the only worldwide solution not to incorporate vacuum cups and operating within a substantially reduced footprint.
Designed and manufactured in house by GS-MR Robotics, the
PRO:Load performs multiple verifications on the glass with capabilities to measure to a 0.2mm variance, only loading the glass if it completes verification. It is GS-MR’s patented process that, for the first time within the global glass industry, keeps problems away from the loading area, eliminating avoidable production stoppages. The GS-MR PRO:Load has the capability to load any manufacturer’s vertical processing IG line with any manufacturer’s software platform - manual loading operators are then upskilled in its operation, significantly reducing rework costs, increasing Health and Safety benefits and employee wellbeing.
Fast forward to 2025, it’s encouraging how the industry has shed its hesitance of robotic automation, not least in terms of looking to achieve improved production quality, reduced materials wastage and reductions in CO2 emissions – essential industry
goals which are met head on by GSMR Robotics automation solutions, with the next two PRO:Load installations set to load the latest LiSEC Flexible Spacer IGU Lines at Press Glass UK’s new high-tech UK site (part of the global Press Glass group).
The global glass industry is changing. With continuing consolidation of the UK market competition is clear. Overheads though, regardless of business size, are overheads and the only smart approach is streamlining processes to eliminate obvious waste.
Challenges spawn innovation bringing progress where none was considered possible. Anyone investing in manufacturing today would lean towards well designed, sustainable and meaningful automation - that would not include an historical manual process which knowingly produced waste.
GS-MR Robotics
Based in Telford, UK. GS-MR Robotics design and build customer driven bespoke and production patented, ‘Industrial Innovation’ Award winning robotic automation solutions for the glass industry.
Hart Door Systems, the original British manufacturer of the highspeed door concept, is confident that there are considerable prospects for another successful year for its Speedor and Typhoon brands.
“Despite global uncertainties on the political front and the ever present debate on climate change I believe our leading Speedor and Typhoon brands will continue to be in demand,” says Doug Hart, Hart’s chairman.
“We have had many successes at home and abroad during 2024 not just through our Speedor range of high-speed doors but through our range of high quality shutters too. Both these leading brands offer industry a choice of solutions for industry and commerce. The fundamentals delivered by Hart are quality throughout manufacture to installation as well as service backup to comply with changing national and international safety standards.
“We are cognisant of Climate Change issues and the need to keep both Hart’s and our clients’ carbon footprints to a minimum by using the latest manufacturing technology to streamline the manufacturing process. Where possible we would use recyclable materials.”
“Looking more closely at the Speedor brand, as Britain’s original manufacturer of the automatic high speed door, Hart has always led the way with developments in commercial door technology by being aware of issues facing industry. The Speedor high speed door is a good example of a robustly
engineered door system for frequent use in high-traffic situations.
“This rapid roll door is robust, requires low maintenance and delivers exceptional wind resistance in exposed areas. While its highspeed opening and closing action improve efficiency, the energysaving potential of this rapid roll door is high, controlling internal temperatures, escaping dirt, odours and noise.
“Special features include; moisturecontrolled electrics, mechanical components shielded from dust and dirt, and a unique guide system offering exceptional wind resistance up to class 5 as defined by DIN EN 12424. There are several options with the Speedor brand namely ECO, Storm, Mini, Conveyor and Cleanroom which together strengthen Hart’s overall high-speed door offer.
“Speedor Storm is our bestselling door, ideal for challenging
applications where reliability is essential. Its increasing success is based on its improved, rugged, design predominately for external use up to 8m x 6m/6m x 8m) often in robust operating conditions with high wind loads.
“We have always had quality as our prime driver and our success with new variants, not just in high-speed doors but shutters such as our new Typhoon range, the fundamentals are quality throughout manufacture to installation and service to comply with changing national and international safety standards.”
“Hart Door Systems is now in its 75th year. It is a global business supplying a range of door and shutter systems to sectors such as automotive, agriculture, communications, consumer foods, energy, environment, exports, food, logistics, manufacturing, power, sport, transport and utilities. To underline our global success Hart’s doors can found in nearly 40 international airports, from Newcastle upon Tyne to the Falklands, from Aruba to Vladivostok. This is a remarkable achievement.”
British design and manufacture, wide range of models covering high security, large doors with high wind resistance (3,000 to 5,000 pascals), fire and high speed automation with systems’ interface.
British design and manufacture, wide range of models covering high security, large doors with high wind resistance (3,000 to 5,000 pascals), fire and high speed automation with systems’ interface.
British design and manufacture, wide range of models covering high security, large doors with high wind resistance (3,000 to 5,000 pascals), fire and high
British design and manufacture, wide range of models covering high security, large doors with high wind resistance (3,000 to 5,000 pascals), fire and high speed automation with systems’ interface.
Hart protects people, products and premises through leading brands.
Hart protects people, products and premises through leading brands. Take control of your business environment.
Globally recognised Hart’s high speed doors and shutters deliver options and solutions for industry wherever you are.
Globally recognised Hart’s high speed doors and shutters deliver options and solutions for industry wherever you are.
Globally recognised Hart’s high speed doors and shutters deliver options and solutions for industry wherever you are.
Take control of your business environment. Call 0191 214 0404 info@hartdoors.com www.hartdoors.com
Call 0191 214 0404 info@hartdoors.com www.hartdoors.com
Hart protects people, products and premises through leading brands. Take control of your business environment. Call 0191 214 0404 info@hartdoors.com www.hartdoors.com
BITO Storage Systems, part of the international BITO group, have a wealth of experience in supplying storage and handling solutions to help companies improve the flow of material in their manufacturing processes. BITO Solution Designers will be on Stand G270 of the Southern Manufacturing & Electronics Show to discuss techniques and products that play a crucial role in assisting manufacturers boost productivity.
Simple, low-cost solutions – such as multi-tier shelving systems, foldable containers and carton live flow racking– can contribute to reduced supply chain costs in manufacturing operations. Shelf bins that perfectly fit the shelving with no wasted space are another example of a product designed to help efficiency and maximise the usage of space in a factory.
Carton live flow racking to organise the movement of components in and around a facility can be used as standalone units to facilitate the implementation of a FIFO approach. Alternatively flow shelves can be retrofitted to pallet racking to create a solution of bulk pallet storage combined with non-palletised smaller unit picking.
Small parts storage - a range of shelving or trolley options complete with small parts picking
containers is available to provide static or mobile small parts storage & picking solutions for factories and workshops. A choice of styles and sizes is available, including SK, RK and CTB, C-item containers. As everything is made by BITO, the containers and shelving are designed to work well together with no wasted space.
The LEO Automated Goods
Vehicles - a family of simple, lowcost driverless transport systems designed to complement BITO’s core shelving and container products. The LEO Carrier at the show is an AGV with 4 shelf levels that can be used as part of an order picking process by moving items between locations within a facility.
Large SL container - also at the show is the 800x600mm half euro pallet plastic container. An excellent alternative to metal pallet boxes that is quieter and lighter but with a 500kg capacity. The fitted feet make it easily movable with a pallet or forklift truck.
Many of the products aimed at helping manufacturers are held in stock in BITO’s Nuneaton warehouse as well as being on display in their Experience Centre, also in Nuneaton.
Come along to stand G270 to discover more about BITO Storage Systems
By Eva Nachtergaele, Regional Product Manager, Hyster Europe.
In industrial manufacturing sites, the efficiency and reliability of material handling equipment are paramount. From the transportation of raw materials to the handling of finished products, forklifts play a key role in maintaining seamless operations. Here, we explore considerations for selecting forklifts for the specific needs of manufacturing, why the importance of customisation should not be overlooked, and how Hyster A Series lift trucks deliver a robust solution.
On busy manufacturing sites with tight production deadlines, the work of a forklift operator can be intensive and physically demanding.
Operators may also be working in harsh environmental conditions, with high noise levels or dusty atmospheres, or where there are corrosive fluids to handle. To keep operators working comfortably and productively, lift trucks need to work extra hard on ergonomics.
Consider operations manufacturing chemical and plastic products. Lift trucks play key roles throughout these applications, from moving raw materials, to feeding production lines, working in both indoor and outdoor storage areas. All while aiming to maintain overall plant productivity.
Raw materials often are handled in large bags, which are stacked on top of one another in a storage
area. High visibility in all directions is therefore a principal factor for operators so the Hyster A Series lift trucks deliver on all round visibility. Manoeuvrability is supported by accurate hydraulics and intuitive operator controls.
Plastic manufacturing operations, for instance, may also produce long or large items. These are wide loads to carry on the lift truck’s forks, so equipment must be selected with a suitably robust mast. Here, specifying truck stability solutions may also help reduce the likelihood of tipovers, especially when turning corners.
Fork positioners may help unlock greater flexibility in a fleet where a wider variety of load sizes need to be handled, including those with unusual sizes or shapes. The ability
to control the forks to accommodate varied loads without exiting the operator cab so often can help enhance the operator experience, making the shift more comfortable.
Lift truck considerations in metal manufacturing
Metal manufacturing can involve tough environments. Lift trucks may require specific solutions to protect the operator and the truck.
Industrial metal manufacturing operations may require a fleet of lift trucks to handle finished metal goods in production areas and warehouses. Here, noise and other distractions are factors that can represent a risk, especially if the truck is working in the vicinity of pedestrians.
These applications should consider selecting lift trucks with features to support driver awareness. For instance, blue and red spotlights, red line awareness lights, and alarms may be available to help indicate to pedestrians where a truck is, and that it is moving or working.
As in any manufacturing operation, there are time pressures, so there can be no compromise on lift truck productivity. Different semifinished or finished products must be handled with high precision and minimal damage, every shift. On these occasions, lift trucks should be selected that cater to the type, shape, size, and weight of the metal loads.
Attachments may play a part, but all-round visibility is the foundation. Operators need the ability to see their surroundings quickly and clearly.
It’s about more than just the operator
Where manufacturing operations are experiencing labour shortages among materials handling operators, improving user experience for operators is often a key consideration. However, operations and service managers have needs too.
As in any manufacturing operation, there are time pressures, so there can be no compromise on lift truck productivity.
Operations and service managers share common goals of maximising uptime and minimising downtime in the face of unrelenting demand. Compressed margins are reducing new equipment budgets, meaning the life of equipment in service is often extended. They must do more with less, and in some cases, operations are running on significant numbers of old and under-maintained equipment, leaving applications vulnerable to interruptions.
Overall truck maintenance and downtime can cause major operational disruptions, and when this is unplanned, it results in unforeseen costs. Hyster A
Series lift trucks offer features to help lighten the load on service managers. For instance, telematics can include systems that routinely flag maintenance requirements and instigate helpful daily operator checks, giving early warning of maintenance issues. Inspections are vital, as infractions can lead to heavy fines. Telematics also enable impacts or other issues to be automatically flagged, so problems can be addressed faster, minimising downtime.
With so many different considerations and factors influencing the right choice of forklift, the ability to customise forklift fleets can be essential. The Hyster A Series lift trucks are designed specifically to address these challenges with A+ Logic, a series of adjustable features to configure the truck to requirements. Through customising the truck at the point it is built, businesses can truly fine-tune their forklifts for their operations, supporting efficiency, uptime, and operator satisfaction.
For further information, please visit www.hyster.com
[ Designed for your profit ]
The UMILL 630 is a potent universal milling center with 5-axis simultaneous power. The low-maintenance torque motor, the direct drive technology, and the powerful motor spindle ensure maximum dynamism. In combination with the symmetrical swivelling range on the B-axis, you can land a really effective punch when it comes to efficiency and productivity. The unanimous decision: more output, more sales, more savings potential. And all for just £189,900. So, what are you waiting for? Strike now.
Pentagon delivers a full turnkey solution for plastic injection moulding from one site of UK Manufacture.
www.pentagonplastics.co.uk websales@pentagonplastics.co.uk
Tel: +44 (0) 1403 264 397
Money-saving champion torque drive
Less wear and maintenance
Up to 50% longer machine service life
Fewer staff tied to the machine
Heavyweight performance from the motor spindle
• Extremely high speed for brilliant surface quality
• High torque to increase the range of components
• Improved competitive ability thanks to shorter cycle times
Totally superior B-axis
• Impressive rotation range of +/- 100°
• Fewer swivel movements
• Larger work area than similar products from other manufacturers
Dynamic direct drive
On all linear axes
• Up to 50% more dynamism
• Rapid motion 50 m/min
energy Save money Integrate the LHS 210/410 series air heaters with Leister’s new CHINOOK blower.
get in touch
Tel: +44 (0)1707 331111 info@welwyntoolgroup.co.uk www.welwyntoolgroup.com
Specifically designed to feed process air at inlet temperatures of up to 350°C
Quiet operating sound level of 58dB(A)
Capable of delivering air flow of 1,640 l/min at 50Hz with a static pressure of 14.6kPa
Monometer foundry furnaces are essential in the metal casting industry, providing hightemperature environments for melting metals and alloys. Different types of furnaces cater to specific needs, efficiency levels, and materials. This article explores four primary types: rotary, crucible, tilting, and reverberatory furnaces, highlighting their features, advantages, and applications.
metal is placed in a crucible inside a heating unit, making them suitable for small batches and specific metals.
• Key Features:
- Fueled by electricity, gas, or oil
- Available in various sizes
- Made from ceramic or refractory materials
• Advantages:
• Applications:
- Used for casting large components like engine blocks, car parts, and industrial items
4. Reverberatory Furnaces
Reverberatory furnaces have an elongated rectangular hearth and reflect heat from the roof onto the metal, enabling bulk melting.
• Key Features:
Rotary furnaces feature a rotating chamber that enables continuous and uniform heating. The rotation promotes efficient mixing and faster melting.
• Key Features:
- Continuous operation for higher productivity
Monometer foundry furnaces play a crucial role in the metal casting industry, providing the high-temperature environments necessary for melting various metals and alloys. Different types of furnaces are designed to cater to specific needs, efficiency, and types of materials processed. In this article, we will explore the four primary types of Monometer foundry furnaces: rotary, crucible, tilting, and reverberatory furnaces, detailing their features, advantages, and applications.
- Handles up to 70 tonnes of iron
1. Rotary Furnaces
- Suitable for ferrous and non-ferrous metals
• Advantages:
- High thermal efficiency and automated operation
Rotary furnaces are designed with a rotating chamber that allows for continuous and uniform heating of materials. The rotation facilitates mixing of the charge, promoting efficient and faster melting than stationary hearth furnaces.
- Reduced labor costs
- Ideal for processing scrap metal
Key Features:
• Applications:
S Continuous operation, which enhances productivity.
- Precise temperature control for high-quality casting
heating unit. This method is effective for small batches or specific metal types.
Key Features:
- Versatile for different metals, including precious ones
S Can be fueled by electricity, gas, or oil.
- Lower initial investment
• Applications:
S Available in various sizes for small or large operations.
S Typically made from ceramic or refractory materials that withstand high temperatures.
the way they absorb heat from the furnace roof. The heat is directed onto the metal via reflected heat from the roof, allowing for large quantities to be melted simultaneously. They are designed with a large vertical loading door on the end of the furnace and a large hearth to deposit the metal to be melted
- Used in die-casting foundries and specialized metal applications
3. Tilting Furnaces
3. Tilting Furnaces
The tilting feature on Monometer furnaces is designed to pour molten metal easily. Tilting can be to various angles, allowing for precise control during the pouring process which minimises spillage and waste.
Tilting furnaces allow controlled pouring of molten metal, reducing spillage and waste.
• Key Features:
Key Features:
- Designed for large-scale melting and holding
- Uses natural gas, oil, or electric rods for heating
• Advantages:
- Ideal for melting large aluminium chunks and copper with oxy-fuel burners
Key Features:
S Designed for bulk melting and holding applications.
- Scalable for different production needs
• Applications:
S Uses either natural gas or oil or electric rods for heating.
- Common in aluminium alloy production and large-scale foundries
S Excellent for melting large chunks of aluminium, Can be used with copper melting with oxy-fuel burners
Conclusion
- Tilting design for improved pouring control
S Enhanced pouring capability due to their tilting design.
- Available in electric, gas, or oil-powered versions
S Available in electric or gas or oil powered versions.
- Suitable for ferrous and non-ferrous materials
S Ability to handle large volumes of metal up to 70 tonnes iron
- Commonly used in metal recycling and alloy production
S Suitable for both ferrous and non-ferrous metals.
S and producing alloys.
Crucible furnaces use a simple design where
2. Crucible Furnaces
Crucible furnaces utilise a simple design where a crucible containing the metal is placed in a
S Suitable for both ferrous and non-ferrous materials.
• Advantages:
S Frequently used in foundries for casting larger components, such as engine blocks, car components , manholes, and industrial parts.
- Enhances safety and efficiency
- Can melt large metal quantities in one cycle
- Quick crucible changes for different metals
4. Reverberatory Furnaces
Reverberatory furnaces are characterised by their elongated rectangular shaped hearth and
Each type of Monometer foundry furnace offers distinct advantages and applications crucial to various metalworking and casting processes. Understanding the capabilities and best uses for rotary, crucible, tilting, and reverberatory furnaces can help foundries and manufacturers choose the right equipment to meet their production goals and enhance their efficiency. By investing in the appropriate furnace technology, businesses can improve their output and maintain high-quality standards in their metal casting operations.
Each Monometer furnace type offers unique advantages for metalworking and casting. Selecting the right furnace improves efficiency, productivity, and quality in foundry operations. Investing in suitable technology helps businesses enhance output and maintain high standards in metal casting.
For more information please contact Christopher Hall c.hall@monometer.com
T +44 (0)1702 472201 www.monometer.co.uk
c.hall@monometer.com
The global need for reliable, clean energy is indisputable and becoming increasingly urgent. However, there is ongoing debate about the most effective processes for producing green energy, and even the precise definition of green energy remains contested. This debate is likely to continue for many years, if not decades. Despite these uncertainties, the demand for clean energy solutions is ever-present. The evidence of global sea temperatures rising and the increased frequency and severity of extreme weather events worldwide underscores the necessity for immediate action.
Green energy projects are gaining traction across the globe. Numerous pilot schemes are being implemented to demonstrate proof of concept, indicating progress in the right direction. However, the question remains whether these efforts are sufficient. Can the planet afford to wait for standard committees to determine the best course of action when the impacts of climate change are already being felt?
Decarburizing the entire energy chain presents a monumental challenge. The transition from longestablished processes, which have been refined over several decades, to green alternatives will not happen overnight. This move involves considerable risk and requires careful planning and execution. The complexity and scale of this task highlights the need for a coordinated and sustained effort to achieve a future with truly sustainable energy.
One aspect of the complex challenge of decarburizing the energy sector is the development of reliable and cost-effective valves. According to the Environmental Protection Agency
(EPA), over 60 percent of fugitive emissions originate from gas valves. This raises the question of how to develop a safe and reliable product in an emerging market when the standards governing such products have yet to be established.
A British company, Oliver Valves, has developed an advanced metal-seated pipeline valve range designed to address these challenges.
Ball valves are known for their simple quarter-turn operation and unrestricted flow path. Features such as non-rising stems and compact geometries make them a common choice for many operators across various processes. The metal-seated variant of the ball valve offers several advantages over the more commonly used soft seat or polymer sealing alternatives, including enhanced resistance to abrasives, increased reliability, and a longer service life. Additionally, the design of metalseated ball valves makes them suitable for applications involving temperatures above 200 degrees Celsius.
The development of metal-seated ball valves represents a step forward in creating reliable, high-performance components essential for the energy sector. This innovation addresses the need for improved valve technology to reduce fugitive emissions and support the transition to greener energy systems.
Creating a metal-to-metal, gas-tight seal is a complex and challenging task that requires a comprehensive understanding of several critical factors. This includes the topography of the components, the stresses involved, and the relative displacements needed to maintain
the necessary contact stress for achieving a gas-tight seal. Achieving this level of precision and reliability is essential, particularly in high-pressure environments where even the smallest leak can lead to significant issues.
Engineers at Oliver Valves have developed substantial expertise in metal-to-metal sealing over more than thirty years, particularly through their work on sub-sea gate valves. These valves are known for their high performance and reliability in demanding conditions, providing valuable insights and experience that inform their current developments.
However, in the context of pipeline ball valves, special considerations must be made regarding the size and geometry of the ball and seat. Both components are inherently complex in shape, and their often-asymmetrical nature complicates the prediction of deflection under pressure. Unlike soft, more compliant seats, a metal seat must deflect at the exact same rate as the ball when subjected to full working pressure to maintain sufficient contact stress and create a reliable seal. These deflections, although microscopic, can contribute to leaks if not managed correctly.
Ensuring that the metal seat and ball deflect in unison requires meticulous design and precise engineering. This challenge underscores the importance of understanding the intricate behaviours of materials under stress and the need for advanced engineering solutions to achieve reliable, gastight seals in metal-seated pipeline valves. The expertise developed by Oliver Valves in this field highlights the critical role of experienced engineering in addressing the complex requirements of modern energy systems.
One potential solution to the challenge of achieving a metal-tometal, gas-tight seal in pipeline ball valves is to greatly increase the size and rigidity of the ball and seat. This approach aims to minimize deflection under pressure. However, this method would significantly raise the associated costs of product assembly. Increasing the ball diameter necessitates a larger cavity size, which subsequently enlarges the pressure boundary between the valve body and its ends. This, in turn, increases the sealing diameter of the end connector, thereby amplifying the blowout force on the end connector. To manage this increased force, either larger fasteners or a greater number of fasteners would be required.
Furthermore, these fasteners must be accessible using conventional tightening equipment, which can add to the overall size and cost of the finished product. To avoid a cascade of increasing sizes and associated costs, it is essential to determine the optimum size of the ball. This ensures the most cost-effective and reliable solution is achieved.
Advanced Finite Element Analysis (FEA) techniques have been employed to derive the optimum size of the ball and the geometry of the seat. These analyses take into account the strengths of materials suitable for hydrogen applications. The derived optimum sizes and geometries have then been tested under inservice conditions to validate the product’s performance across various temperature and pressure combinations. This approach ensures that the valve design is both costeffective and capable of maintaining reliable performance in demanding applications.
At the Oliver R&D facility in Cheshire, a specialized team of engineers focuses on developing cutting-edge valve products. This facility has established a unique hydrogen test standard, which integrates industryrecognized fugitive emissions tests and simulates in-service conditions, including prolonged operational scenarios.
The qualification process developed at the facility is tailored to address the specific needs of pipeline valve applications. This rigorous process includes comprehensive operational and seat leakage tests conducted at both maximum and minimum rated temperatures. During these tests, fugitive emissions are closely monitored to ensure compliance with stringent environmental and safety standards. The objective is to verify the valve’s performance and reliability under the most demanding conditions.
To further demonstrate the robustness and effectiveness of their zero-leakage metal sealing range, the qualification process was extended to include an endurance test of 3,000 operations. This extended testing period is designed to replicate the long-term operational stresses that valves would encounter in real-world applications. After completing the 3,000 operations, the valves were evaluated for their ability to maintain a bubble-tight seal at working pressure and to remain within acceptable fugitive emissions rates. The results confirmed that the valves met and exceeded performance expectations, maintaining their integrity and functionality throughout the testing process.
This thorough and objective testing approach ensures that the valves developed at the Oliver R&D facility adhere to high standards of performance, reliability, and environmental compliance. By subjecting the valves to such rigorous testing, the engineers can confidently validate their designs and ensure that the products are capable of performing reliably in demanding conditions, thereby contributing to the advancement of valve technology in the energy sector.
Nick Howard, Director of Market Development at Oliver Valves, highlights the company’s approach to developing advanced valve technology. By leveraging years of expertise in metal sealing and combining it with a deep understanding of hydrogen applications, Oliver Valves has
developed metal-to-metal sealing ball valves. These valves aim to offer the reliability and prolonged service life typical of metal-seated valves while achieving sealing performance comparable to soft-sealing valves. This development represents a significant advancement in valve technology, particularly for applications involving hydrogen.
Valves are a small yet critical component in the broader context of addressing complex energy challenges. As such, it raises the question of whether additional initiatives should be provided to companies to accelerate the development of innovative products. The transition to green energy and the reduction of fugitive emissions requires not only new ideas but also effective methods to bring these ideas to fruition.
Encouraging further innovation in valve technology could involve offering incentives such as research grants, tax benefits, or collaborative opportunities with academic and research institutions. Such initiatives could expedite the development and implementation of advanced solutions, facilitating more rapid progress towards achieving environmental and energy goals.
Moreover, enhancing the support for research and development in the valve industry could lead to broader advancements in energy systems. Valves, while a small component, play a crucial role in ensuring the efficiency and safety of various processes. Improved valve technology can contribute to reducing emissions, enhancing operational reliability, and optimizing performance across different sectors.
In conclusion, while the development of advanced valves like those by Oliver Valves and others represent a milestone, broader support for innovation is essential. By fostering an environment that encourages research, collaboration, and the practical application of new technologies, the energy industry can more effectively address its complex challenges and move towards a sustainable future.
Introducing the Micronics UX5000 Clampon Flow Meter for use in Hazardous Environments. A high performance ATEX USM, made in the UK with a remarkably low price point.
ABLE, as Micronics’ exclusive UK representatives for the Model UX5000, are delighted to announce the arrival of a truly technically elite and commercially advantageous clamp-on ultrasonic flow meter.
The UX5000 flow meter uses a crosscorrelation transit time algorithm to achieve precise flow measurements. It generates an ultrasonic beam at a specific frequency, transmitting it between transducer crystals in two directions: first from the downstream transducer to the upstream, then reversing from upstream to downstream. As the liquid moves through the pipe, it slightly increases the speed of the ultrasound transmission.
This time difference, calculated as T1−T2, is directly proportional to the liquid’s flow velocity, providing an accurate measurement of flow rate.
Applications for the UX5000 are many-fold. The UX5000 is ideal for harsh, heavy duty industrial measurement of liquid flow in pipes. Being non-invasive and easy to install, it is particularly well suited to the chemical, water and oil industries.
Key Features:
• Non-invasive, efficient, and easy installation, no process downtime
• Cutting edge technology at its most affordable
• Certified for use in hazardous areas (ATEX)
• Reliable measurement accuracy – up to 0.5% with process calibration
• Separate Display (DCSIU) and Remote Measurement
• Unit (RMU) allows flexibility in installation
• Cost effective metering for harsh, heavyduty applications
• Single and Dual Channel Options
• Remote System Setup and Monitoring
Have a live application? Contact our flow specialists to book a demonstration.
Babcock Wanson UK Ltd.
7 Elstree Way, Borehamwood, Hertfordshire WD6 1SA, UK
Tel: 020 8953 7111 | info@babcock-wanson.com www.babcock-wanson.com
“It is not the strongest of the species that survives, nor the most intelligent that survives. It is the one that is most adaptable to change.”
Charles Darwin
In our uncertain environment, energy adaptability is key. When it comes to process heating, Babcock Wanson offers more choice and flexibility to achieve your decarbonisation goals, reduce your fuel bill and allow for energy diversification.
Process Engineering Control & Manufacturing is a lively, engaging, insightful independent publication & directory which offers practical advice & solutions on the technical and management challenges faced by engineers and managers in the process & manufacturing industries.
Subscription enquiries: Call 01304 806039
Email: editor@mhmagazine.co.uk
Advertising enquiries: Jake Page – 0203 907 9166
Email: jake@pecm.co.uk
Editorial submissions or enquiries: Antony Holter – 01304 806039
Email: editor@mhmagazine.co.uk
SQUIRREL CAGE MOTORS | SLIP RING MOTORS | DC MOTORS
Motors up to 25 MW and 13.8 kV
• Low voltage slip-ring and squirrel cage motors up to 3,000 kW
• Medium voltage slip-ring and squirrel cage motors up to 15,000 kW
• Direct current motors up to 2,000 kW
• Frequency converter-proof drives
• In-house load test facility up to 13.800 V, 2.300 kVA, 120 Hz
Customized special designs
• Custom designs for special applications and operating conditions
• Optimized motor design for higher efficiency
• Mechanically and electrically interchangeable motors
• Commissioning worldwide
MENZEL Great Britain Ltd. | UK Branch Office
Martin Rooney | Tel.: +44 1664 500 844
martin.rooney@menzelgb.co.uk
menzel-motors.com