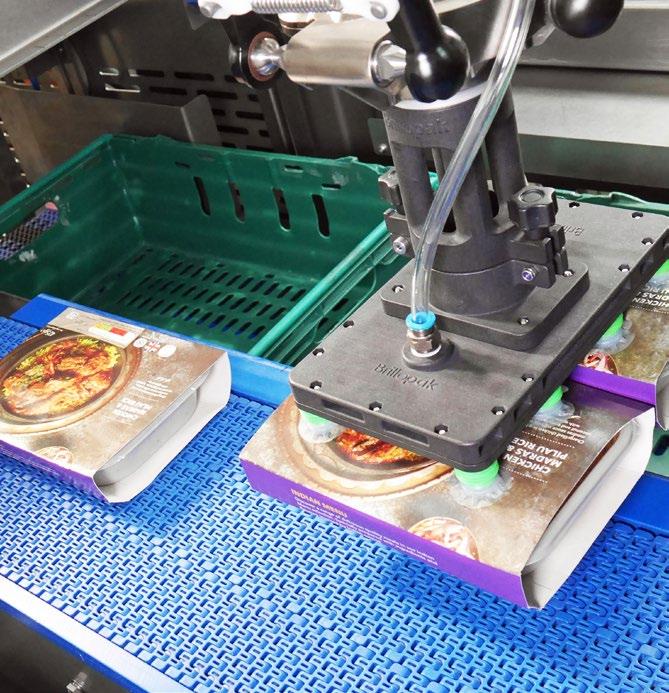
23 minute read
BRILLOPAK
Although air is considered by most to be a free commodity, the reality is when air is being compressed to support manufacturing processes, it can be an inefficient and expensive process.
Automation specialist Brillopak examines the sustainability challenges of compressed air and the steps it has taken to address this issue on its UniPAKer robotic crate packing series.
The sustainability of compressed air as an industrial power source is a bit of an oxymoron. Air itself is clean, safe, convenient and abundantly available. However, the environmental impact of poorly maintained compressed air systems has been long debated.
Reviewing a facility’s compressed air system will undoubtedly reveal many opportunities for reducing energy consumption. All of which can result in considerable savings, improved operating costs, without large capital expenditures.
Used to operate equipment such as pneumatic controls, air tools, pumps, valve actuators, robotics, pistons and larger-scale processes, compressed air typically accounts for up to 40 percent of a manufacturing facility’s total energy bill. Additionally, leak rates can exceed 50% on some compressed air systems.
As well as being a direct source of wasted energy, these leaks can cause major pressure system drops affecting output. This in turn makes the compressor work even harder, shortening the equipment’s lifespan and causing excessive equipment wear and tear.
Taking the lead to reduce automation carbon emissions and meet the UK’s new 2050 Net Zero targets, Brillopak has reengineered its UniPAKer’s compressed air pressure system and end-effector vacuum generators. manufacturer, Brillopak has successfully built the vacuum generators into the endeffector head. Now, rather than sitting external to the end-effector, air is drawn into the centre of the head and fed to each of the five generators, all of which are contained within a special internal casing. Delivering more consistent, targeted and faster airflow.
Tested against early-generation endeffectors, Brillopak reports a 45 percent reduction in air use when picking up and moving products of the same weight into retail crates. Brillopak Director Peter Newman explains. “When we examined the volume and flow rate data on the UniPAKer equipped with these new end effectors, we measured the compressed air system operating at a much lower stable pressure in shorter quicker bursts.”
Creating sustainable value across the entire packing cycle, by adopting this ‘whole system air flow approach’ and improved control and distribution of air, Brillopak reports a 10% reduction in power usage compared to previous models in the series.
Brillopak re-engineers its UniPAKer compressed air pressure system and end-effector vacuum generators, saving at least 10% in power usage.
TARGETING CLIMATE NEUTRAL
Servo drives are proven to be extremely efficient relative to power use in automated cells. By carefully controlling all aspects of the work envelope, the acceleration and deceleration of the robotic arm is better controlled. Striking the optimum balance of fast acceleration and gentle pick and placement, the movement of the UniPAKer’s arm is fluid. “There’s no wasted time. As an electrically-powered robot, energy is only used when the robot is in motion,” explains Peter.
To help manufacturers meet the UK’s new 2050 Net Zero targets, Brillopak has expended a lot of energy re-examining all potential resource-intensive tasks, including the efficiency of every process and component to ensure power is not being wasted. For example, integrating Brillopak cells with electronics up the line helps to pre-empt bottlenecks, address production lags and respond instantly. If no products are coming off the bagging machines down the line, idle conveyors stop.
Sustainability is a never ending cycle of improvements, notes the self-professed eco-engineer. “At Brillopak, every action makes a difference. We have a duty to examine all direct and indirect emissions. Applying the concept of the circular economy that everything has a value, we always use tried and tested energy-efficient components in every build,” says Peter.
Conveyors used in Brillopak cells, for example, are sourced from a company that only include motors, inverters and mechatronic drives with optimised energy efficiency. Likewise, the company optimises the payload/arm weight ratio to maximise efficiency. Automating tasks like case loading and palletising has long been presented as a solution to boost productivity and efficiency and address labour shortages.
The same pressure is on for compressed air systems. As an integral part of the manufacturing process they are unlikely to disappear any time soon. Yet, as Brillopak has uncovered, there are more sustainable options to reduce the psi which in turn reduces energy consumption.
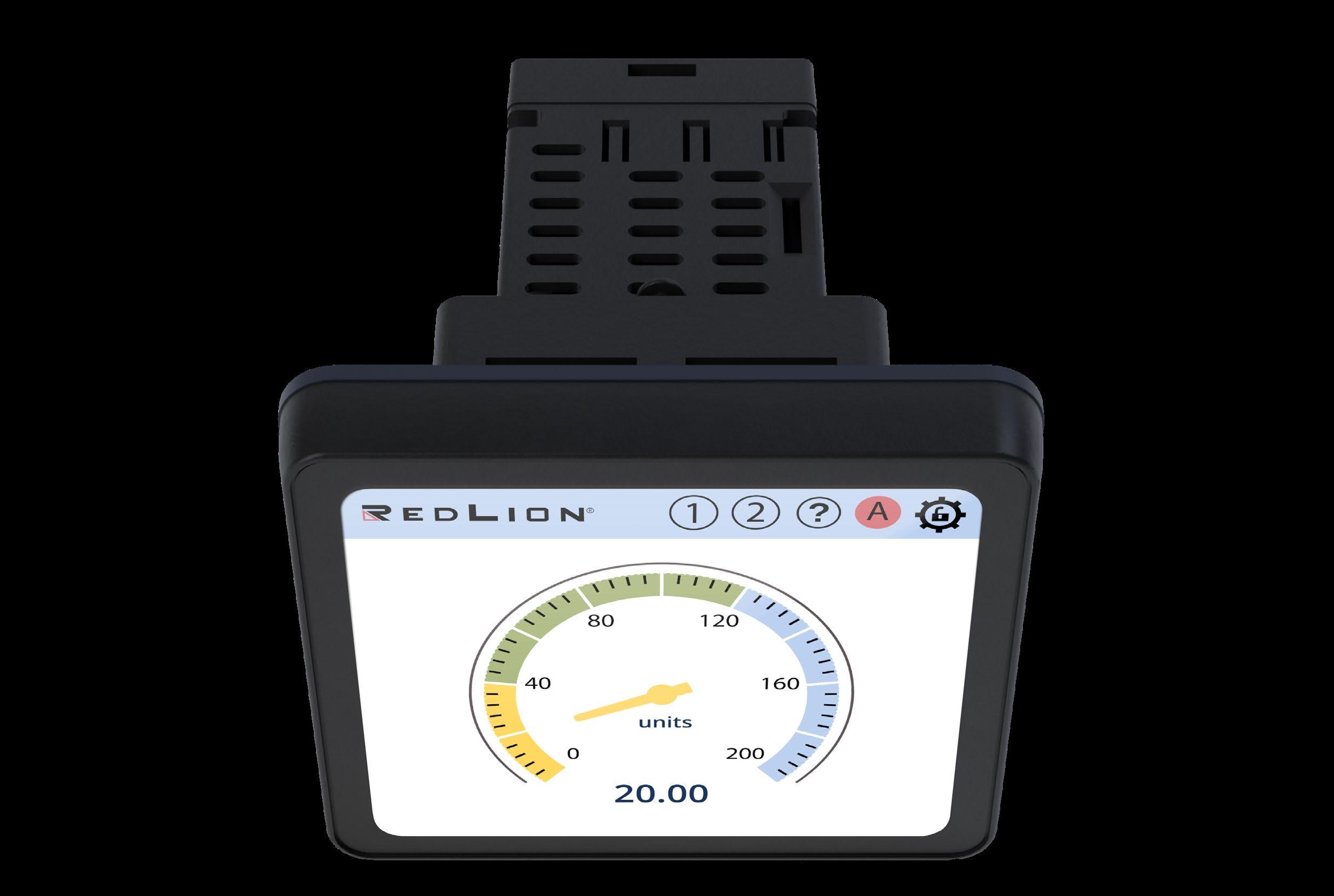
Red Lion’s Graphical Panel Meter PM-50 empowers your customers to monitor their equipment and see their data like never before. This next-generation graphical panel meter not only enhances the appearance of any machine, it connects customers to the information that matters most, where and when they need it most.
Simply change out an old meter to leverage time and money-saving data collection—meaning that creating a smart plant floor has never been easier.
Smart-device connectivity frees critical data from the confines of the plant floor, enabling the remote gathering of workflow and process insights needed to increase production throughout. Instant notifications reduce downtime by keeping your customers on top of @equipment needs. On the panel, a touchscreen interface loaded with vibrant, user-friendly graphics allows for more data with less effort. And a builtin set-up wizard and available mobile programming app means anyone can program the meter. With PM-50, the simplicity of a panel meter meets the power of a connected future. PM-50 is not just a better panel meter. It’s the first device to make the power of Industry 4.0 truly accessible by anyone. Contact Red Lion today to learn more and experience the potential of your own smart factory floor.
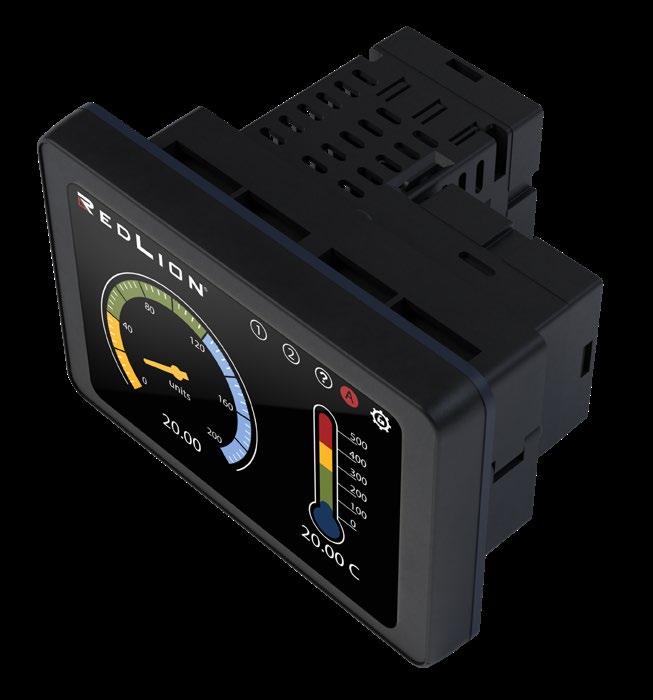

Industrial Reliability & Safety in 3 Steps
By Michael Riccio, CRL, CAT-1 IRT Global Marketing Manager, IRISS Inc.
The critical importance of electrical power to every aspect of our world cannot be exaggerated. It must be generated and distributed effectively to end-users, and any disruption in that process means loss of operations, money, and in extreme cases, life. Therefore, the reliability of electrical power creation and distribution must be continually safeguarded and improved. This does not happen by chance or through reactionary-maintenance tasks, and it must be focused on from the early design stages and continue through the life of the assets tasked with these functions.
Adopting a “Monitor, Inspect, & Manage” approach is a proactive way to avoid the concerns at hand by maximizing the value of workforce time and skill. Scalability is no longer an issue when, instead of going through the time and cost of expanding their workforce, they can apply condition-based reliability technologies to maximize their available workforce skills and availability. These Reliability Technologies can be specified with the specification engineer and Original Equipment Manufacturer at the initial design/build stage or retrofitted into existing equipment through a simple and inexpensive process.
MONITOR
With the use of a monitoring system on transformers and throughout substation electrical equipment, asset conditions can be continually collected, trended, and assessed. Monitors feed data through a gateway to software and apps, allowing the information to be continuously accessed from workstations and mobile devices. When the new equipment arrives from the manufacturer with these monitors built-in, customized parameters can be set for the specific operating and environmental conditions the asset is exposed to that keep it within a “safe zone” to maximize functional reliability. When the asset condition data exceeds the custom parameters, alarms can notify electrical technicians of a possible issue that may require inspection. Keeping human interaction with equipment to only instances where confirmation inspections of potential faults are deemed necessary minimizes workers’ risk and eliminates the humanerror threat to asset functionality.
INSPECT
Once the wireless monitoring system notifies technicians of a possible issue with a transformer or other piece of electrical equipment, the use of pre-
installed inspection windows on the asset allows a safe, efficient method of inspecting and assessing any possible issue during an energized condition. Once solely designed for thermographic inspections using infrared cameras, advancements in manufacturing have led to the inclusion of ports that allow for ultrasound and partial discharge technologies to be incorporated into the inspection. Visual, infrared, and ultrasound inspections can be done simultaneously by a single employee.
Additionally, this design protects inspectors from arc flash/electrocution risk, removes the need for bulky and expensive PPE, and allows the inspection to be accomplished more efficiently. Not only does this represent a significant process improvement driven by original design, but it also falls in line with the most recent NFPA 70E updates and continues to protect critical assets from human interaction/mistakes that may cause failure.
MANAGE
The data collected during inspection can be stored through intelligent asset management tags attached to the pre-installed inspection windows. From the asset location, information can be transmitted into a dashboard system accessible from workstations and mobile devices.
Customizable routes can be established before, and condition reports generated after data analysis to further increase efficiency. These designed aspects allow managers to assess operations and decide how best to increase Mean Time Between Failure (MTBF).
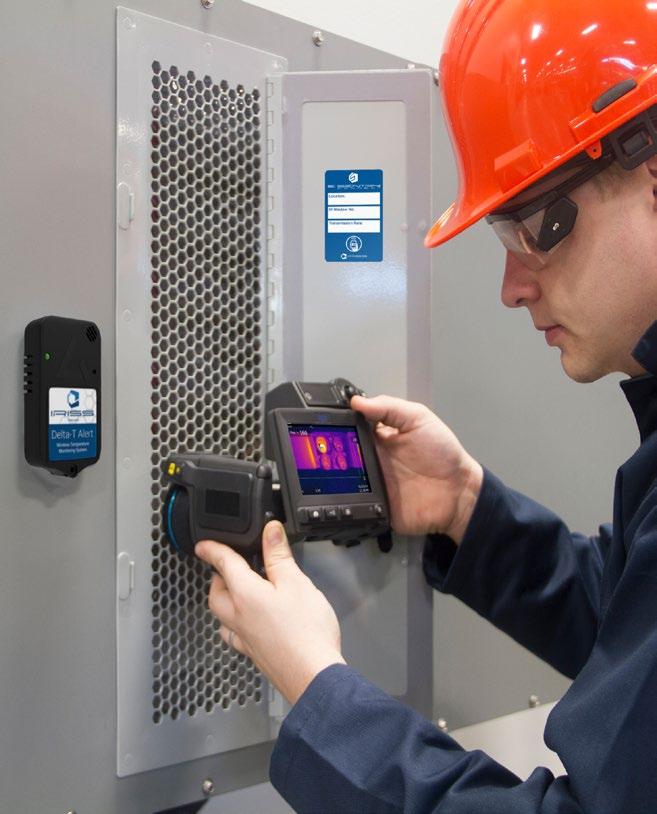
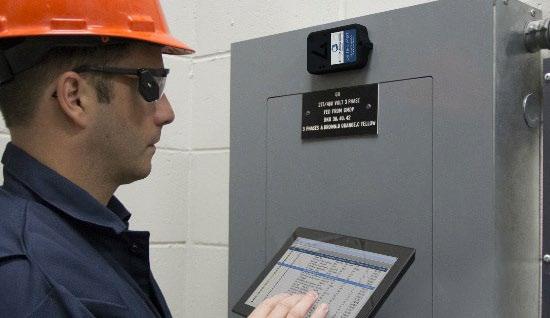
PROPER TRAINING
One major issue facing the industrial world is a coming wave of retirements from the workforce, with fewer new workers entering the industry than the pending need created by this exodus. As the electrical industry expands worldwide, creating the need for a larger workforce, the problem is multiplied. The only way to succeed is to capitalize on reliability technologies designed into the system that allows the industry to do more with less.
While Designing for Safety & Reliability from the equipment-side should drive the overall process toward continuous improvements, the proper tools are only as useful as the hands wielding them. Hardware and software designed/ specified by the engineer and constructed by the OEM are ineffective if the people responsible for their oversight are not adequately trained.
Shifting to an engineered reliability system for the electrical maintenance team means training new and veteran staff alike. With “Monitor, Inspect, Manage,” the use of technology allows single individuals to accomplish inspection tasks with minimal training. Specialized skill sets of electricalfocused staff can be used for actual necessary maintenance/repair activities.
CONCLUSIONS
From the inception of equipment design and manufacture, all possible measures to ensure asset reliability should be specified and implemented. These measures should prove themselves to be learnable, repeatable, and continued throughout any workforce changes to cement the successful practices into the very culture of the role requirements.
Transformers and other critical electrical power assets being monitored remotely cut down on technicians’ routine tasks focused on engineering and electrical operations by providing around-the-clock coverage. When an alarm notification is received, correctly designed and installed inspection windows allow an individual technician to easily do visual, infrared, and ultrasound, and partial discharge assessments of the energized equipment. The data collected on the asset can then be stored, trended, and analyzed through the management software. This process increases the Mean Time Between Failure (MTBF) by allowing for planned shutdown and maintenance only when it is necessary.
www.iriss.com
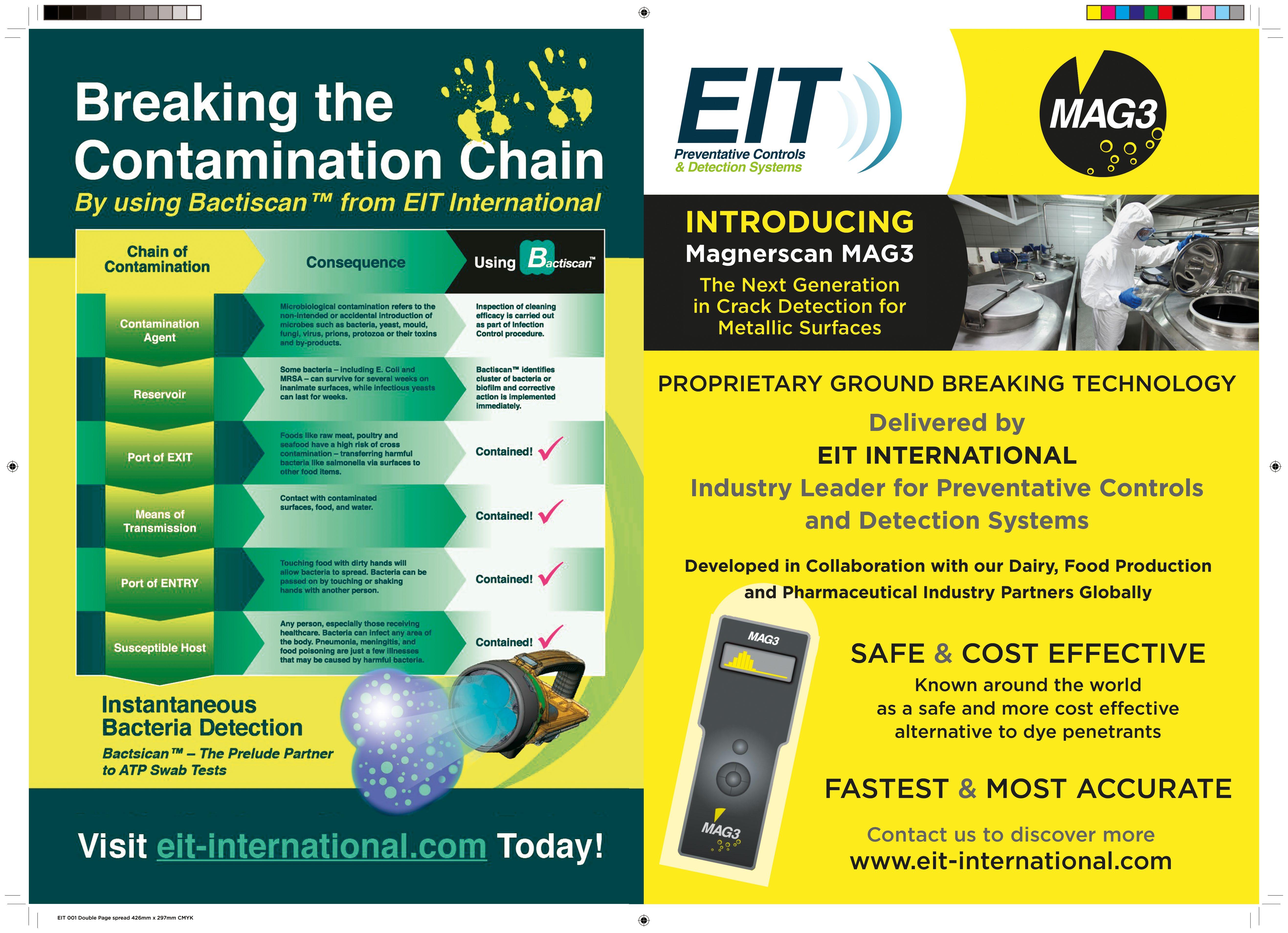
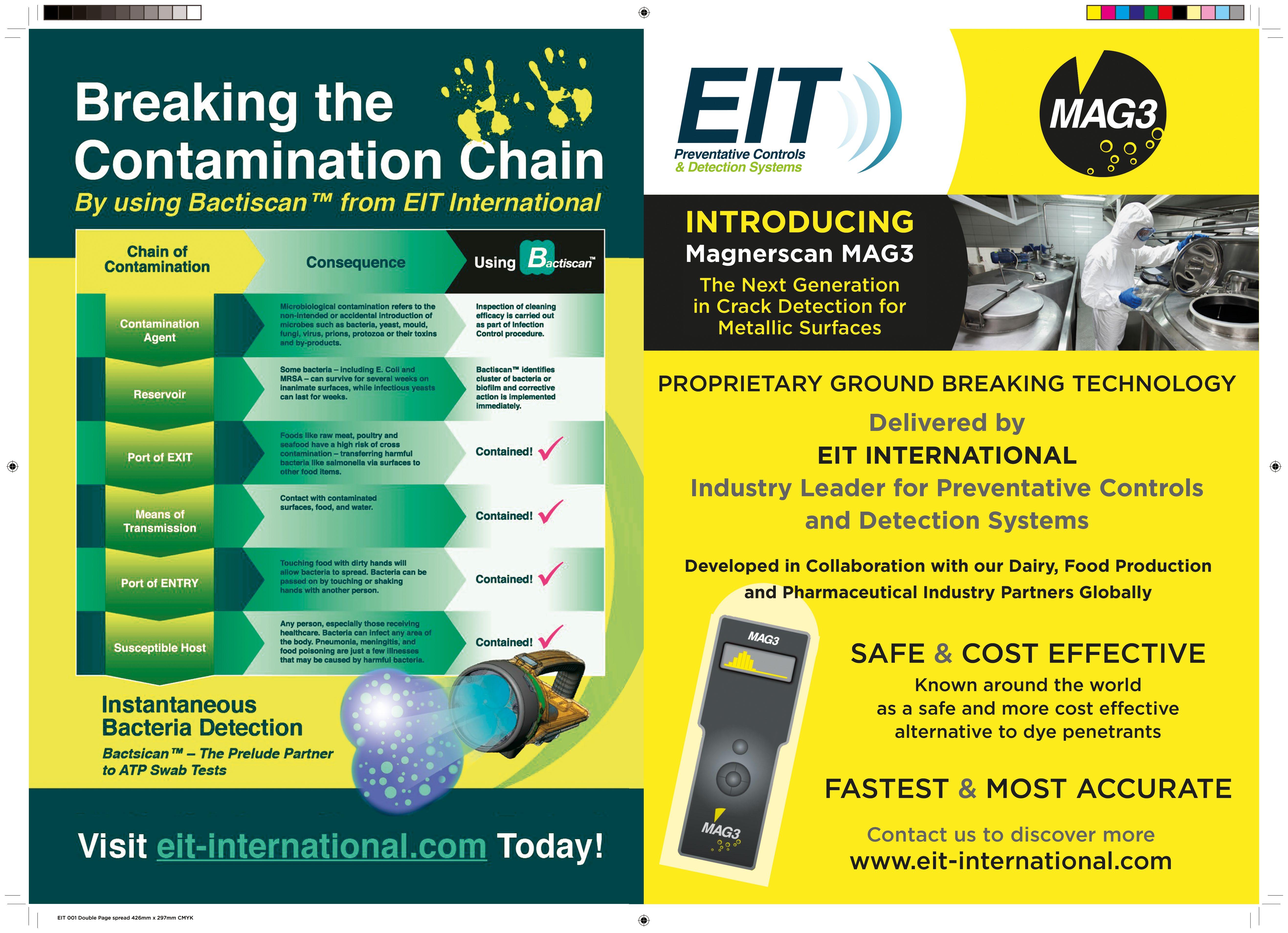
TLV upgrades renowned COSPECT valve to ease installation and minimise process disruption
Through a process of continued development and product enhancements, the renowned three-inone COSPECT pressure reducing valve from steam system specialist TLV Euro Engineering has been upgraded and is now being offered with integrated pressure gauges as standard across the range.
Commenting for TLV Euro Engineering, general manager Michael Povey says: “By upgrading and offering the pressure gauges as standard across the range, we have enhanced the COSPECT to make it even more of a unified steam system solution. The integrated gauges also mean no additional pipework modification is required before or after the PRV, which reduces installation time and minimises process downtime.”.
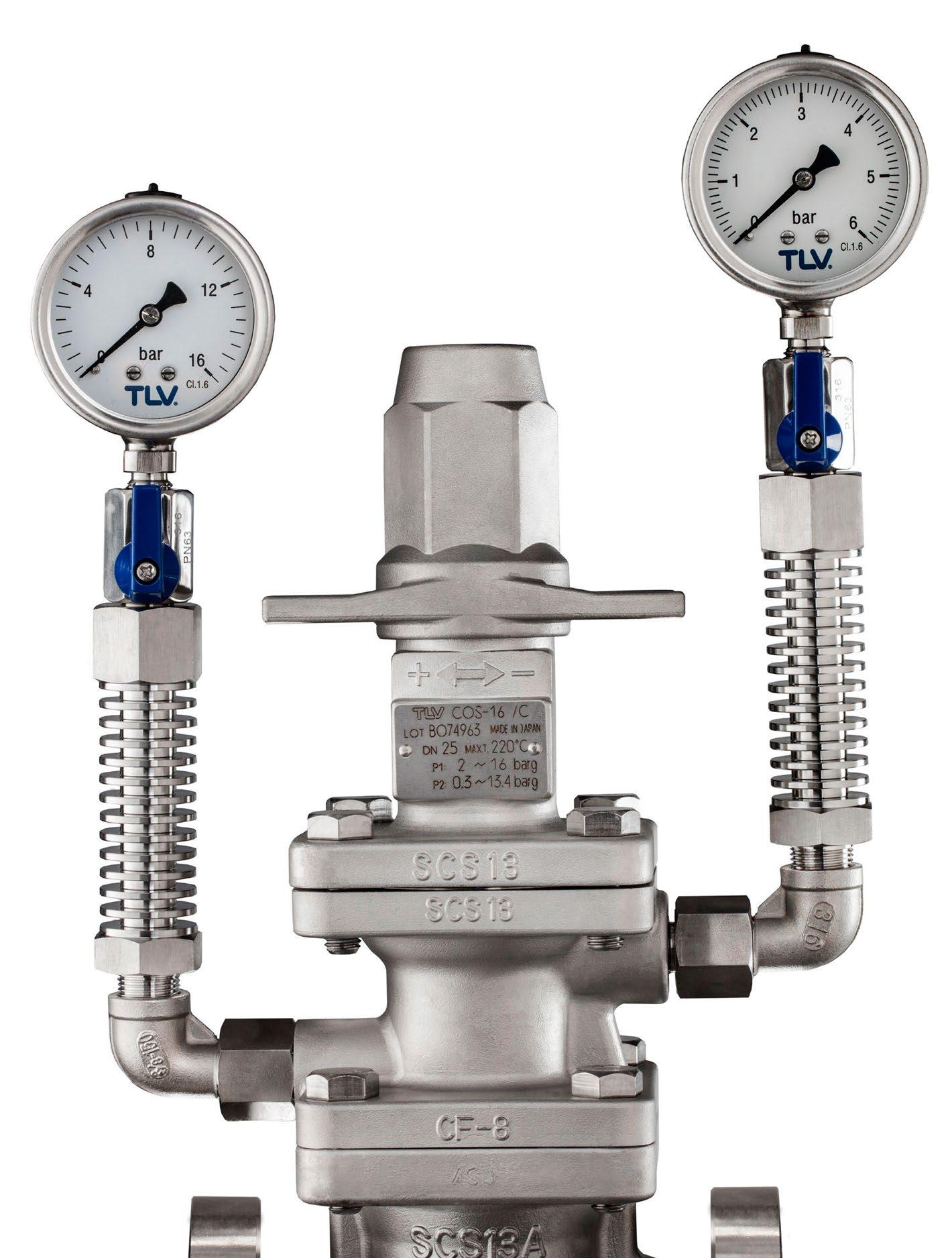
Originally launched over 35 years ago, the COSPECT is a combined pilotoperated pressure reducing valve (PRV), cyclone separator, strainer and steam trap in a single component that overcomes the limitations and inadequacies of conventional PRVs and solves their many associated problems – including fluctuations in primary and secondary pressures and valve hunting and vibration – to provide improvedquality dry steam at a constant pressure and temperature.

By eliminating the conventional arrangement and combining four separate components into a single valve, the COSPECT delivers numerous engineering benefits by incorporating fewer gaskets, spool pieces and fixings, improving moisture separation and providing accurate and stable pressure control. It is also more sensitive to downstream pressure fluctuations, is reliable in operation and its unified, modular construction facilitates easy, in-line maintenance.
In addition to the engineering benefits, the single component design of the five-model COSPECT makes it faster and easier to install, is lighter than the sum of using separate components, reduces the amount of insulation required and reduces the requirement for pipe support brackets, etc.
For further information on the COSPECT and other steam solutions, call TLV Euro Engineering on +44 (0)1242 227223, email sales@tlv.co.uk or visit www.tlv.co.uk.
Smart coupling for fast packaging
Packaging specialist trusts in innovative multiple connectors
Little space, little time, and yet as much flexibility as possible: The requirements packaging machines are expected to meet are manifold. The developed NEO machine puts Meypack in a position to package malleable and flexible bags that are ready for sale. The company from Nottuln in Germany, installed Eisele’s MULTILINE multiple connectors in the prototype, which allowed them to perfectly satisfy the requirements they imposed on space and speed and the necessary level of flexibility.
The packaging specialist Meypack Verpackungssystemtechnik GmbH develops machines for secondary packaging and palletizing. It is imperative - especially in the food industry - to package new products at short notice and in a cost-effective manner - and without compromising on quality.
The greatest possible flexibility “The NEO was designed for the secondary packaging of products”, says Nowak. “While primarily intended for packaging flexible products in trays with inserted lids, it can process small cans and aluminium bowls as well.” Since multiple cylinders have to be supplied with compressed air, the company steered clear of simple compressed air couplings for reasons of space. Meypack decided to pair the machine with the multiple connectors with 8-fold socket body that are included in Eisele’s MULTILINE series. Each connector is fitted with six adaptive inserts with shut-off and double seal, an adaptive insert without shut-off and an A-coded M12-round connector, which is used for the signal transmission to the format parts. The multiple and multi-media connectors of the Eisele MULTILINE ADAPTIVE + E series offer an innovative modular kit system for combining compressed air, vacuum, gases, coolant, liquids, electronics and electrical wiring in one interface.

Reduced installation effort yields savings in time Installation expenses and set-up times can be reduced significantly with the innovative multiple connector. “We only need 25 minutes for the complete format changeover from very small to very large”, confirms Nowak. “This quick change can largely be attributed to the locking lever”. The fully customized multiple connectors make it possible to exchange all functions in one single step and without any tools. Since all connections can be integrated into one connector, the required installation space is minimal as well. Another decisive advantage is that all individual parts are compatible with each other. The base body is composed of plug and socket. The number of connections and the maximum outer diameter can be customized. Thanks to the inserts, it is now possible to combine exactly the media that are needed for each application.
www.eisele.eu/en
WE CREATE CONNECTIONS
www.eisele.eu
MULTILINE „THE INDIVIDUAL“
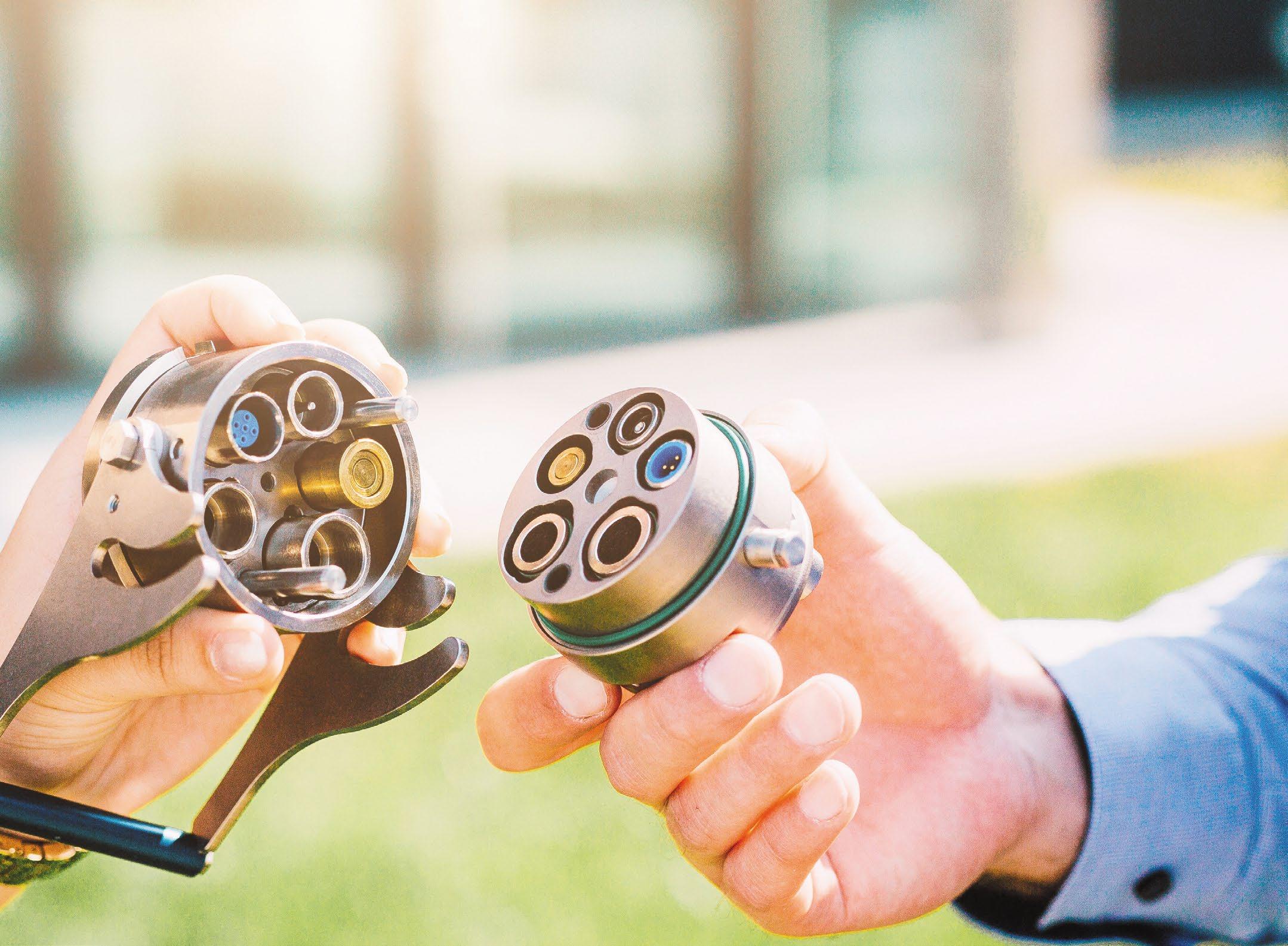
Our innovative connection solutions and components set impressive standards that convince our customers.
Modular connection systems for different operating media such as compressed air, vacuum, gases, liquids and electrical or electronic signals in a single interface.
Assembly / Handling Automotive
Cheese Manufacturer Norseland transform their labelling procedures using the WPL-A from Minebea Intec
Norseland was looking for new ways to automate parts of their manufacturing and reduce the demands on their existing workforce. The WPL-A offered the perfect solution for their labelling processes and has increased the efficiency and accuracy of their labelling.
KEY FACTS

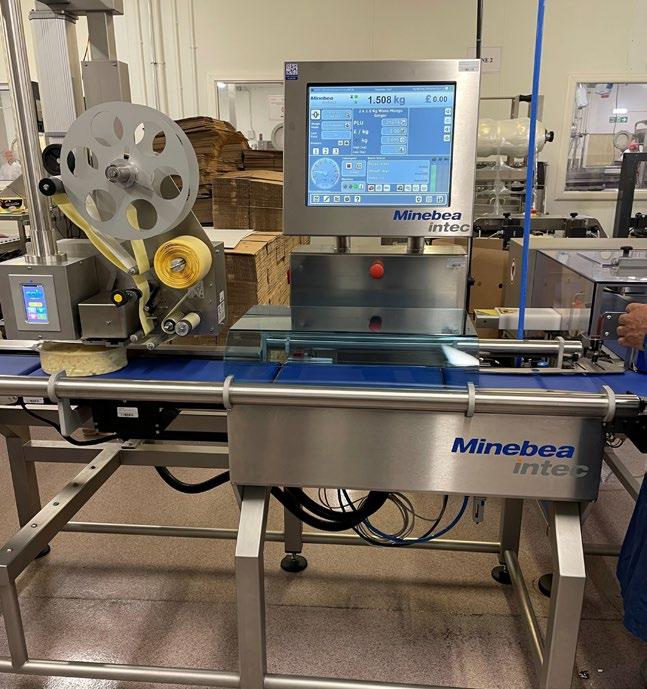
Norseland wanted to automate some of their processes in order to increase efficiency and output. The labelling solutions from Minebea Intec not only fullfilled this task, but also helped to increase workplace safety and prepare for future automation.
APPLICATION
Norseland Ltd have over 30 Minebea Intec products in use within their manufacturing plant; the most recent additions are the WPL-A and WPL-S. Norseland Ltd are using the weigh price labelling machines to accurately label their products and automate parts of their production.
PRODUCTS
1 WPL-A (Weigh Price Labeller – Automatic)
1 WPL-S (Weight Price Labeller – Static)
CUSTOMER BENEFITS
The WPL-A and WPL-S have
• improved the accuracy and efficiency of the labelling processes • helped to reduce overall production costs
• improved workplace safety
CUSTOMER
Specialist cheese supplier Norseland Ltd employs over 150 people and has a turnover approaching £50m. Its primary markets are all the leading UK supermarket retailers, food to go and convenience retail stores, as well as independent retailers.
WPL-A applying a label to the Norseland Applewood Cheese block ready for despatch to a UK supermarket.
Norseland Ltd has its’ manufacturing base in Ilchester, Somerset where they have a diverse and versatile offering. They can provide cheese for every occasion from slices to large blocks and snacking portions. Their No. 1 brands include:
Jarlsberg® UK’s No.1 Deli Cheese with Holes Applewood® UK’s No.1 Smoky Cheese Mexicana® UK’s No.1 Spicy Cheese
PROJECT GOAL AND IMPLEMENTATION
Norseland has a diverse and versatile offering; providing cheese for every occasion from slices to large blocks and snacking portions. The breadth of their product range relies on a varied range of equipment to manufacture and produce products ready for their customers.
Minebea Intec has been supplying Norseland since 2007 during which time the relationship has gone from strength to strength. They currently have almost 30 Minebea Intec products for various applications in their production, the latest additions being the WPL-A and WPL-S for their labelling requirements.
The requirement for new labelling machinery was driven by the need to automate the process, increase the efficiency and accuracy and also due to a lack of labour in the vicinity of their manufacturing plant. Minebea Intec was chosen as their preferred supplier for a number of reasons; the durability of Minebea Intec products, the hygienic standards of the products, the aftersales service and the ability to adapt products to their exact requirements.
In response to these requirements, the WPL-A was manufactured to accommodate the label sizes required by Norseland and the WPL-S was adapted to fit into their existing line. The WPL-A has also proven to drastically reduce the Health and Safety risks of Repetitive Strain Injury (RSI) of operatives who were previously lifting and handling 1.5kg portions of cheese.
This new machinery is in addition to their existing 16 check weighers; Synus and CoSynus used for end of line legal weight checks and metal detection. They also have EWK portion weighers which control the size of the cheese portions and Flexus’ which are used to control the cutting of the smaller portions of cheese and take a smaller footprint within the factory.
They also have 6 Vistus metal detectors, 2 Combics scales used for sampling for legal records and 1 SPC Enterprise software package which provides realtime reporting on the factory processing.
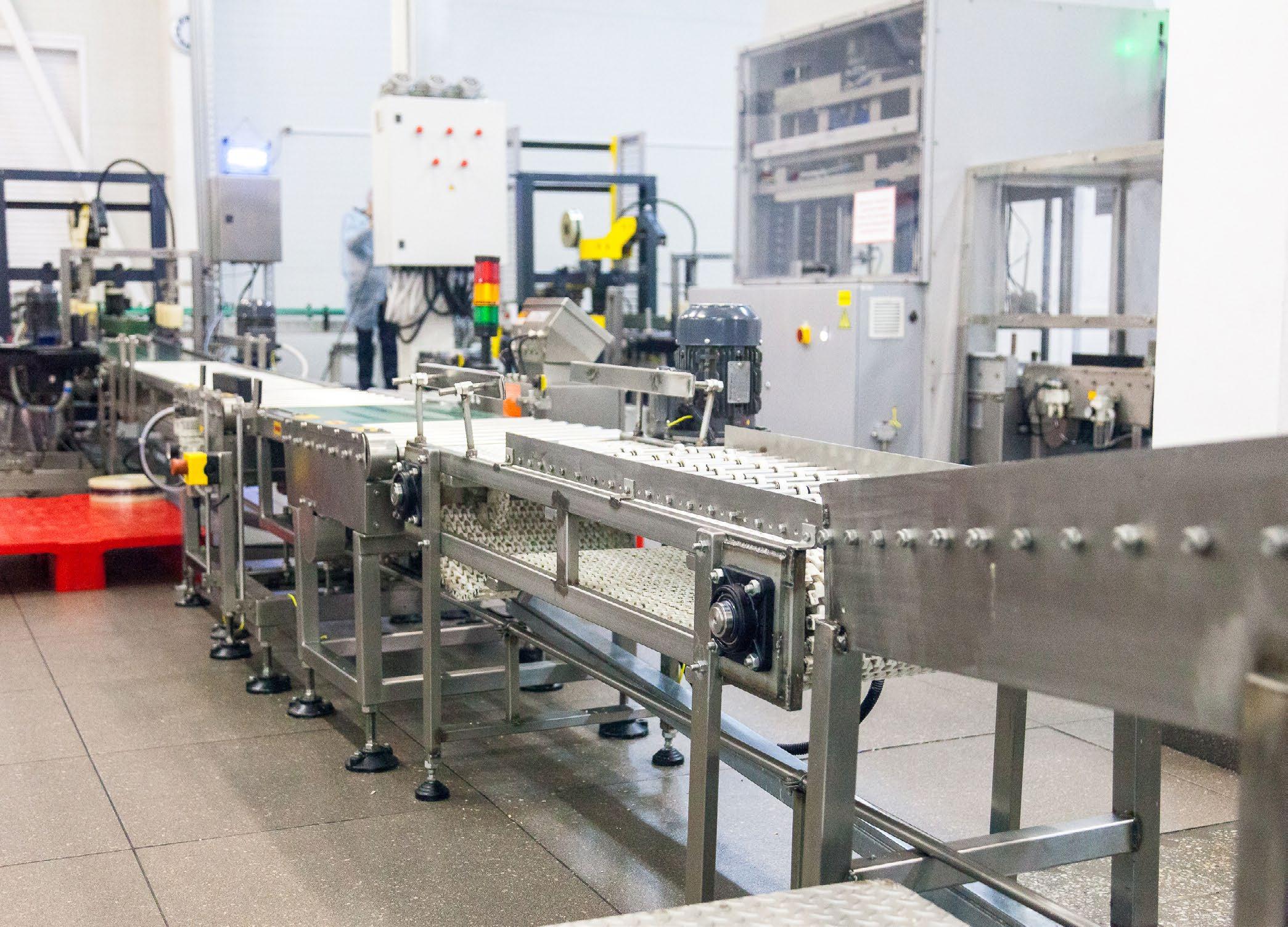
When reliability meets sustainability
Aligning sustainability targets with food safety
Sustainability has become the buzzword of the 21st century and that is set to continue for the foreseeable future. However, it’s not always easy to prioritise sustainability in the midst of increasingly challenging cost, output and food safety targets.
What if you could demonstrate tangible environmental benefits whilst enhancing the reliability and food safety of your plant?
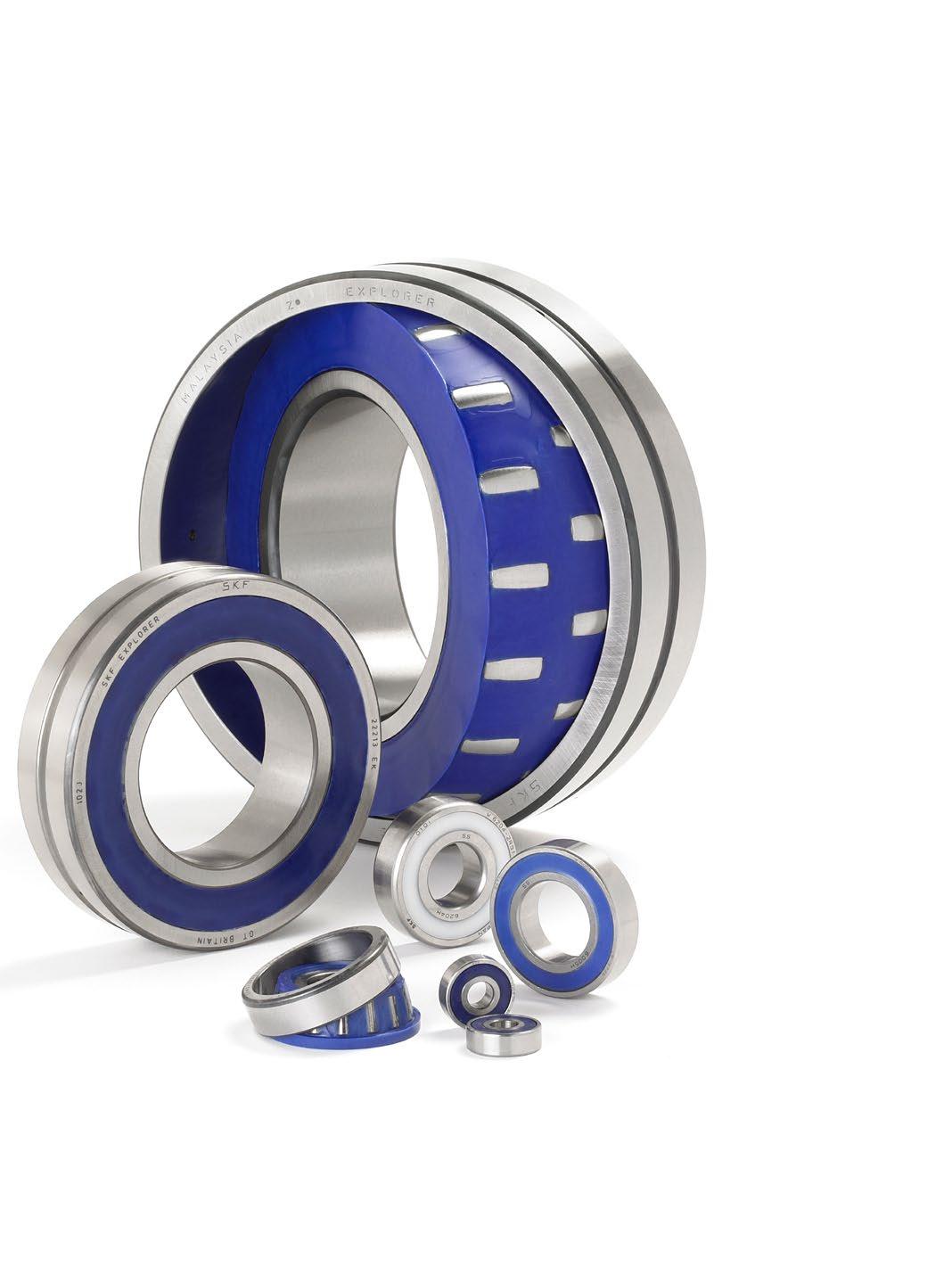
In this article, we’ll explain how you can drive down your downtime, prioritise food safety and deliver incremental environmental benefits, proving that you really can have it all. REDUCE YOUR ENVIRONMENTAL IMPACT WITH RE-LUBRICATION FREE BEARINGS
One of the most effective ways to reduce your environmental impact and optimise your food safety is to upgrade to re-lubrication free bearings. The benefits are far-reaching, from the reduced cost of lubricant and component replacements, to the elimination of wastewater contamination from washed-down bearings grease.
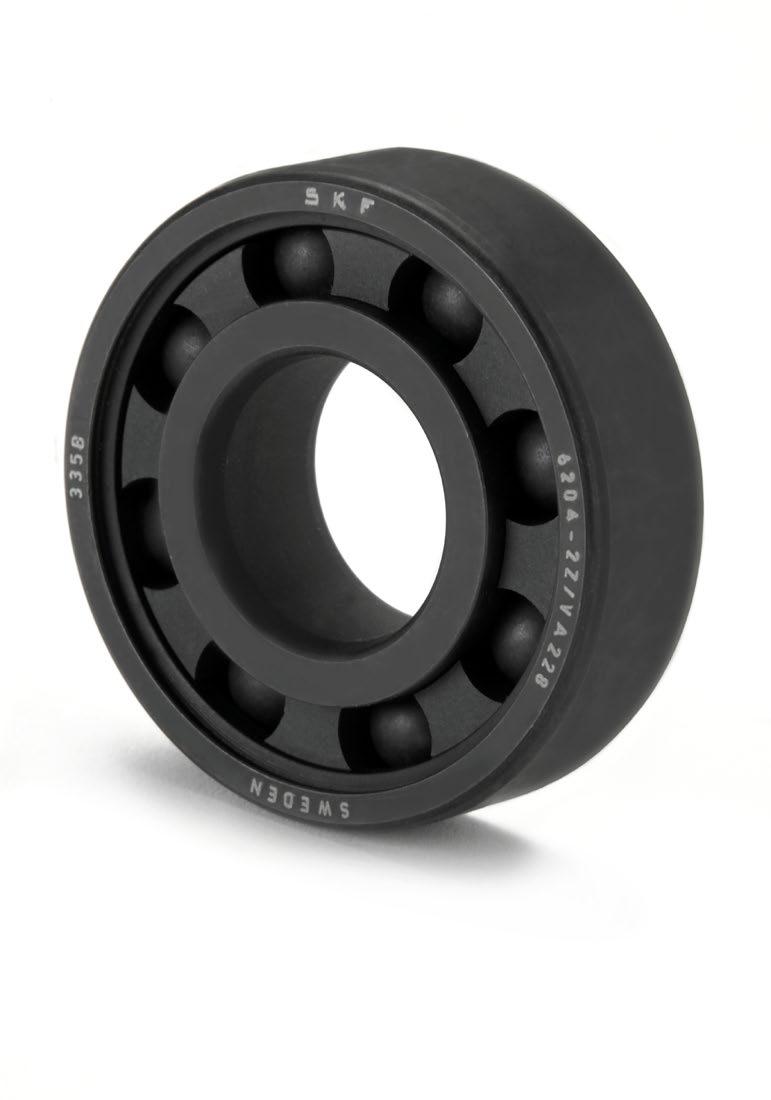
LUBRICATE BEARINGS WITH FRYER OIL
Fryers present a challenge to many plant managers, with bearings often failing prematurely and high levels of maintenance required. What if we told you that you could use the operating conditions to your advantage?
SKF Fryer Bearing Units allow the cooking oil to enter the bearing, acting as an effective lubricant. This enables bearings to run for up to 16,000 hours, eliminating the need to relubricate the bearings after each caustic boil out. You’ll benefit from a significant reduction in maintenance, enhanced uptime and increase reliability, whilst your carbon footprint is reduced.
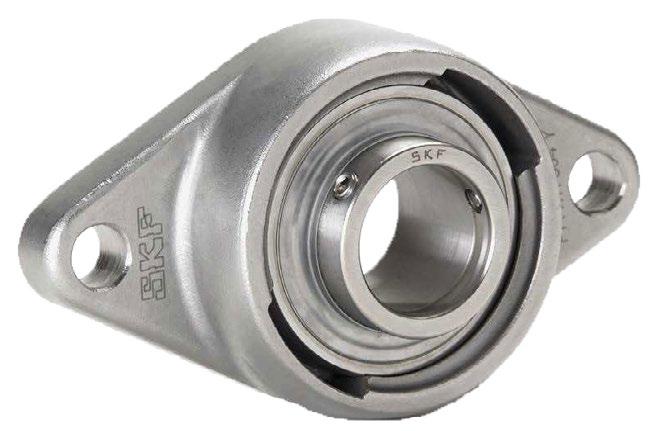
REDUCE THE FOOTPRINT OF HIGH TEMPERATURE GREASED BEARINGS
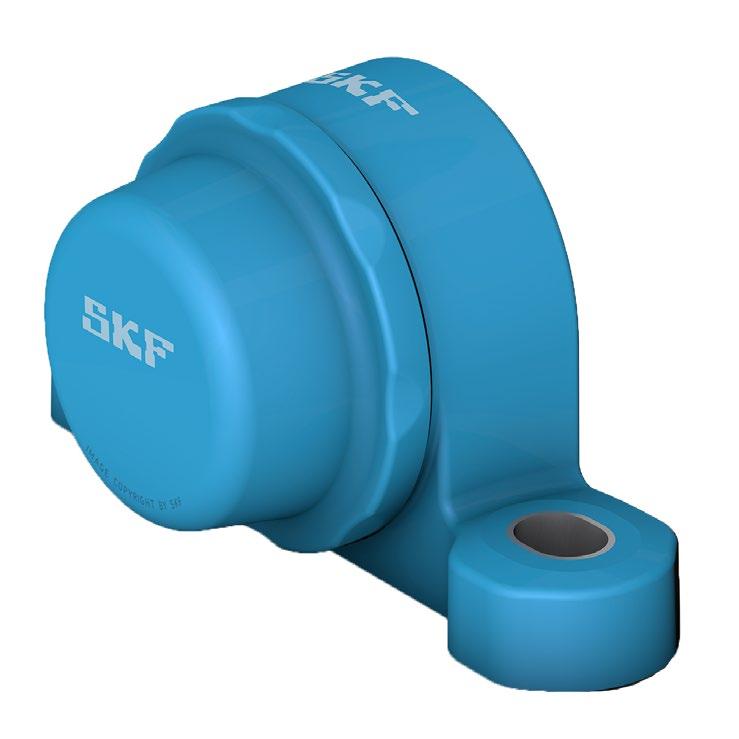
CUT WATER USAGE AND ENVIRONMENTAL WASTE
Every plant manager will know how important it is to have food grade components on your production line. Not only are SKF’s Food Line bearing units food grade, but they can also reduce your water consumption by 33% whilst generating zero landfill.
SKF Food Line ball bearing units are completely sealed, lubricated for life, and designed for optimum performance in even the harshest of processing and cleaning environments. High temperatures can lead to your bearings failing to achieve their expected service life. Not only will this affect the uptime and productivity of your production line, but it also leads to additional waste and an increased carbon footprint.
SKF high temperature bearings eliminate the need to re-lubricate, in even the highest temperature applications. The fully crowned pure graphite cage allows just enough contact between the balls and cage to create a fine powder which coats the rolling elements to eliminate metal-tometal contact. This enables production lines to minimise their environmental impact whilst reducing maintenance expenditure.
PREVENT CORROSION IN CHALLENGING CONDITIONS
When you’re dealing with freezer applications, you’ll be trying to counter the effects of high levels of humidity and rapid temperature changes. This can take its toll on even the highest quality of bearings. SKF bearings with Solid Oil technology are designed to stand up to challenging environments, such as within freezer applications. Available with NSF H1 approved food-grade lubricant, these bearings do not require relubrication throughout their service life. This helps to maximise reliability and reduce costs, whilst ensuring food safety.
CUT YOUR COSTS WHILST PRIORITISING SUSTAINABILITY
Traditional conveyors utilise a huge quantity of water and lubricant every single day during operation. This creates a large amount of wastage, as well as attracting a high cost to the business.
The SKF Dry Lubrication System for Conveyors offers a practical solution which cuts maintenance requirements whilst prioritising sustainability. This fully automated system applies a small amount of SKF Dry Film Lubricant to conveyor chains and guides, keeping the line moving at all times.
Not only does this cut costs and reduce both water and lubricant consumption, but it also helps to improve operator safety, reduce clean-up costs, and optimise productivity.
In today’s modern world, every business needs to prioritise sustainability, ensuring environmentally friendly operation at every stage of the production process.
However, at ACORN®, we understand that it isn’t always easy to balance your sustainability goals with other operational targets, such as cost, uptime and food safety.
ACORN’s product experts can help you to meet your operational goals, without having to compromise on sustainability. Call to arrange a site visit or discuss your pain points, and we’ll find the best solutions that work for your business.
Gentle pumping of critical fluids with Roto’s progressive cavity pumps & AODD pumps
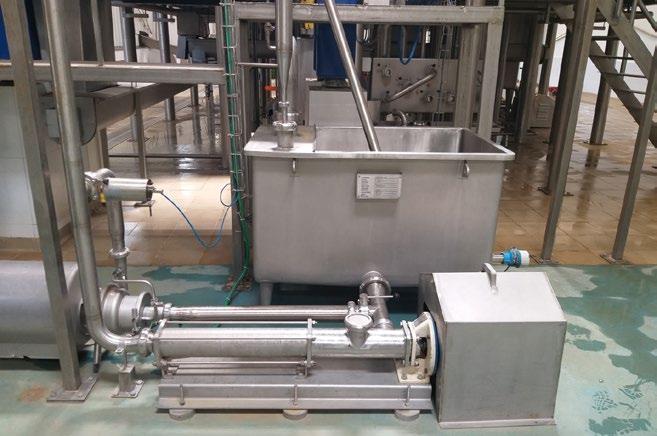
ROTO PROGRESSIVE CAVITY PUMP TRANSFERRING HONEY
Applications in Food, Beverages, Pharma and Cosmetics industries require pumps that can transfer hygenic, shear sensitive, abrasive and highly viscous media with zero contamination. Roto’s food range progressive cavity pumps are made of stainless steel with the smooth surface finish to avoid contamination. These pumps are designed in a way that eliminates all retaining pockets.
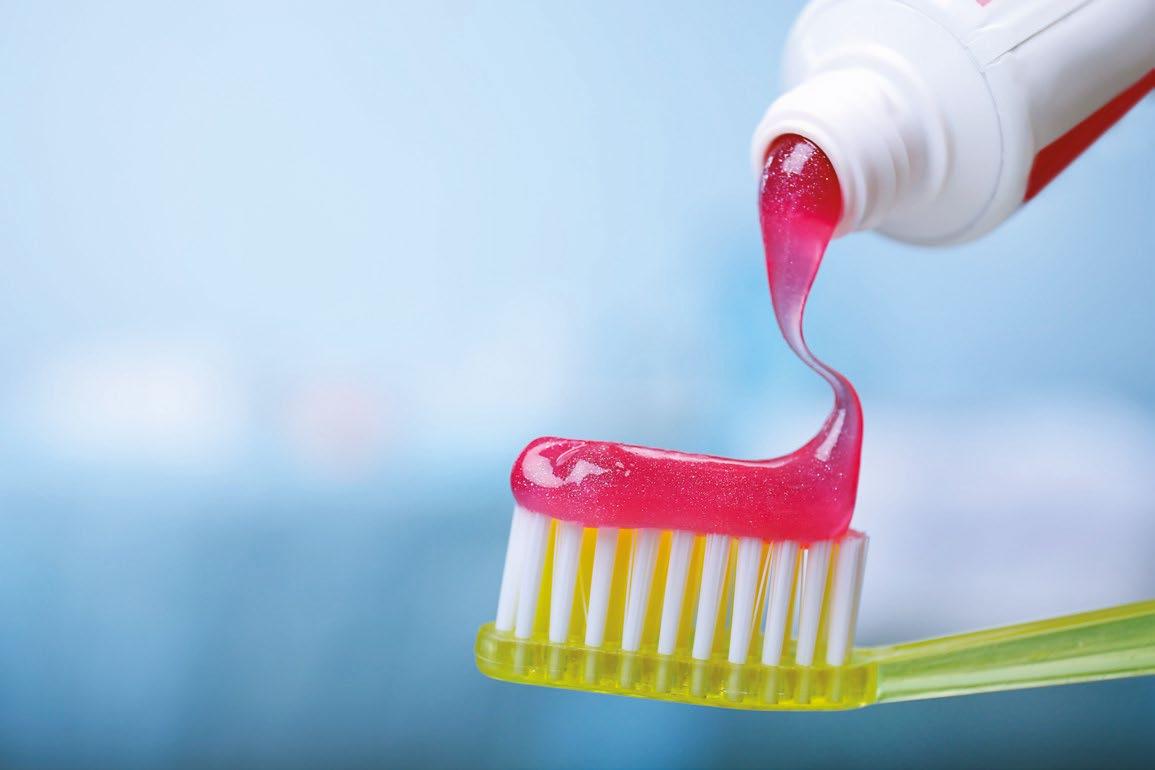
These pumps offer a distinctive edge over other positive displacement pumps as it can be customized in wide throat (standard hopper & oversized hopper) design which helps in transferring nonflowable fluids such as syrups, shampoo, wine must, ketchup, yogurt, dough, meat, vegetables, etc.
PRODUCT RANGE FOR FOOD & BEVERAGE INDUSTRY
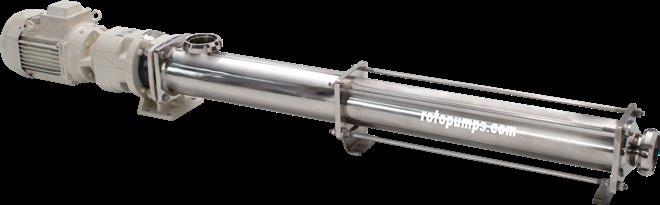
DM Series Progressive Cavity Pump Capacity – Up to 86 m3/hr Pressure – Up to 24 bar
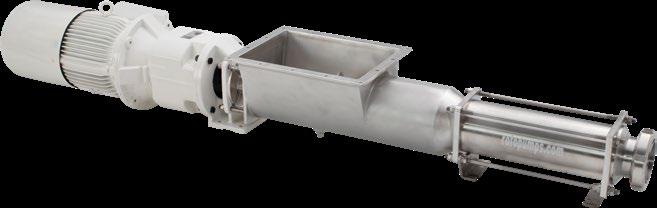
WM Series Progressive Cavity Pump Capacity – Up to 86 m3/hr Pressure – Up to 24 bar 28 FDPP - www.fdpp.co.uk

RAODD Pump in SS 316 MOC Capacity – Up to 60 m3/hr Pressure – Up to 10 bar
CLEANING –IN –PLACE (CIP) TECHNOLOGY
Cleaning is an important aspect while designing food grade pumps. Roto’s CIP feature enable pump operators to clean the pump by running a cleaning agent i.e. caustic, acid or simply water to avoid any contamination with ease. The rotor and stators are designed to be compatible with media as well as cleaning agent. These pumps are equipped with the appropriate drain or bypass system.
ROTO PUMPS UK| 15 YEARS OF DELIVERING POSITIVE DISPLACEMENT PUMPING SOLUTIONS
2004, Roto Pumps Ltd. established a branch in the UK with warehouse and assembly infrastructure to provide positive displacement pump solutions to various industries across Europe. New Market had its own challenges which can slow any new company’s progress. But Roto Pumps Ltd. was not new; it had a rich experience of over four decades with a maximum number of screw pump installations in critical applications across the globe.
To gain a strong foothold in the European Market, Roto Pumps focused on providing customized engineered pump packages, strong service support and ensuring ready availability with optimum stock levels of Pumps & spares. Also, Roto Pumps UK has established an intensive network of distributors and channel partners.
15 years of experience in the European market, Roto Pumps has demonstrated its expertise in application engineering i.e. understanding of complex pumping requirements, handling critical media, optimizing pump life cycle cost.
KEY CAPABILITIES OF ROTO PUMPS UK
• 15 years of strong presence in Europe • Robust supply chain network • Strong sales & service support team in the UK
• Readily available pump & spare parts
Stocks
• Cost-effective & customized engineered packages.
We at Roto Pumps believe in customer delight; we have a team of experienced application & sales engineers in the UK who completely take care of customer’s concern right from receiving inquiry to providing prompt after-sales support.
Dave Bent Roto Pumps Ltd. UK Unit 1, St Elizabeth Park, Grey Street, Denton Manchester UK, M34 3RU Tel: +44 ( 0 ) 161 477 5511 Mobile: + 44 ( 0 ) 7778 637343 E-Mail: davebent@rotopumps.co.uk
www.rotopumps.co.uk
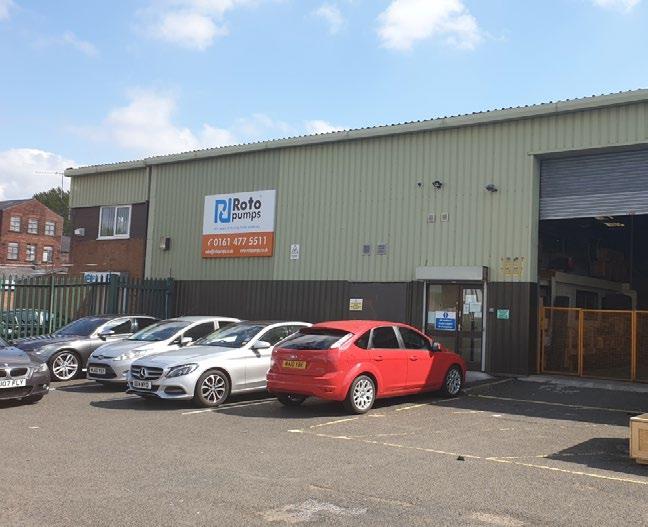