
23 minute read
BRILLOPAK
Automation’s brighter for Europe’s largest carrot farmer
Harvesting 4000 acres of root crops a year – the majority carrots – Prestonbased Huntapac Produce is laying the groundwork to boost its automation packing efficiency. Starting with a customised Brillopak vegetable case loading system.
Founded during WWII, family-run carrot farmer, now one of the largest in Europe and supplier to most of the major British supermarkets since 1974 (including Tesco and M&S Food), regards itself as a pioneer. Now, Will Hunter - a robotics advocate since the age of 16 and fourth-generation operations director - is leading a new mission to introduce the best quality control, process and packaging technology to boost productivity, with the fastest ROI.
Having explored numerous robotic pick and place options over the last decade, an innovative mechanical case loading system designed by Brillopak is delivering against Will’s exacting criteria. With an estimated ROI of 2.5-years, Huntapac tasked Brillopak to engineer an affordable, compact bespoke tray packing system to accumulate and present carrot packs into neat layer formations in retailready crates.
Will Hunter explains: “There’s an accepted truth within the farming community that automation can address labour shortages and improve how packs are presented into retail trays. Despite this, it can be hard for many to justify a seven-year ROI on traditional pick and place robots.” An accumulation system based upon Brillopak’s PunnetPAKer design with an innovative retractable overhead push and slide mechanism more than halved the ROI and answered this conundrum. Huntapac’s merging system and bag flippers ensures that each carrot pack is horizontally aligned before being fed into the Brillopak case packing machine.
Having spent several decades working with industry leaders and fresh produce customers to successfully overcome packing automation and quality control issues of this nature, Brillopak was the right firm for the job. The company’s specially-adapted BR2 vegetable packing machine allows Huntapac to run different sized and weighted carrot packs, from 500 grams to 1.5 kilograms, smaller Chantenay carrots, and even parsnips, as well as different packaging materials including new recyclable substrates. All without incurring time delays by switching robot end effectors. FIELD TO YIELD IMPROVEMENTS
Presenting up to 80 carrot packs per minute into retail trays, Huntapac replaced one of its traditional rotary table, manual crate packing lines with the automated system earlier this year. Operating 16 hours a day, five days a week, 1200 tons of carrots are graded, washed, polished, cooled, optically graded by size and quality, packed and checkweighed. Once loaded into the cases, the carrots are then transported to a cold store, ensuring the vegetables stay fresh and maintain their high quality before distribution across the country to fill the supermarket shelves.
Previously reliant on manual labour to maintain a constant case-loading pace, now a disparate, unconnected bagging and checkweighing system has been fully integrated into the BR2 case packing system. “By uniting all the electronics up the line, the machines all communicate with each other via a common control platform installed by Brillopak.

With most carrot crates destined for supermarket shelves, consistent display presentation of the carrots, face up and positioned straight up with the branding and labels clearly visible to consumers is vital
This helps to pre-empt bottlenecks, address production lags and respond instantly if packs get trapped. Should any of these events occur, the upstream packing and checkweighing machines slow or stop automatically until all the processes are in-step with each other again,” explains Will. “The speed is very much governed by the processing speed of our baggers and checkweighers. Although the case loader is capable of going faster, we wouldn’t want it to compromise the quality of our produce,” adds Will.
With most carrot crates destined for supermarket shelves, consistent display presentation of the carrots, face up and positioned straight up with the branding and labels clearly visible to consumers is vital. Huntapac’s existing merging system and bag flippers ensures that each carrot pack is horizontally aligned before being fed into the Brillopak case packing machine.
Four packs are then presented individually onto a collation support plate, nudging each one along until there are four slightly overlapping packs. Director David Jahn describes the sequence: “The concept follows a similar principle to a coin pusher arcade game. As one lands on the previous pack, gravity pushes them over to create crate-ready layer.
As soon as the four packs are in position, a side load slider gently pushes the carrot packs onto a flap opening device located directly above the crate. Simultaneously to the carrot packs lowering into the crate, the slider flap lifts, retracts overhead and drops behind the next set of carrots, pushing next The flexibility of the system assists Huntapac to respond to the seasonal peak demands, including the packing of parsnips – another core part of the grower’s business. The night shift also regularly runs smaller Chantenay carrots on the line.
FERTILE GROUND FOR GROWTH
With Brexit and COVID compounding the resourcing issue, moving from a fast-paced labour intensive crate loading operation to an automated system has been welcomed by the farm. Better staff satisfaction has been observed by Will: “Because we are removing the reliance on agency staff, our productivity per person has significantly increased. Our core Huntapac packhouse team was excited to see the machine go in and felt really connected to the project and the wider benefits of eliminating labour intensive routine activities of this nature. The wellbeing, safety, motivational and upskilling advantages were evident from day one.”
Although crate insertion and removal is currently performed at the end of the cell manually, the carrot farmer hasn’t ruled out automating the crate destacking and palletising phase to complete its packing automation cycle in the future.
As an extremely marginal business, automation has become an imperative in fresh produce packing operations. “In many instances where margins are already compressed, affordable automation can be more effective than implementing traditional lean manufacturing enhancements which tend to only deliver incremental efficiency improvements. Especially when labour input costs are rising higher than fresh produce commodity prices,” notes David Jahn.
Not only does the reduction of manual work streamline packing processes, it also reduces waste and improves worker safety. Flexible machines which can be adapted to seasonal produce and future packing and product applications further increases their viability, with less risk.
Due to the success of this installation, Will is considering automating case loading on all 16 carrot lines, potentially creating a dedicated parsnips line too.
Will concludes: “We have been thrilled by the speed in which Brillopak engineered, installed and integrated all the upstream electronics. Within a couple of hours our carrot case loading machine was up and running and hasn’t stopped performing since. The level of communication throughout the project was exceptional and I don’t recall ever having a machine with this level of complexity run so well from day one.”
www.brillopak.co.uk
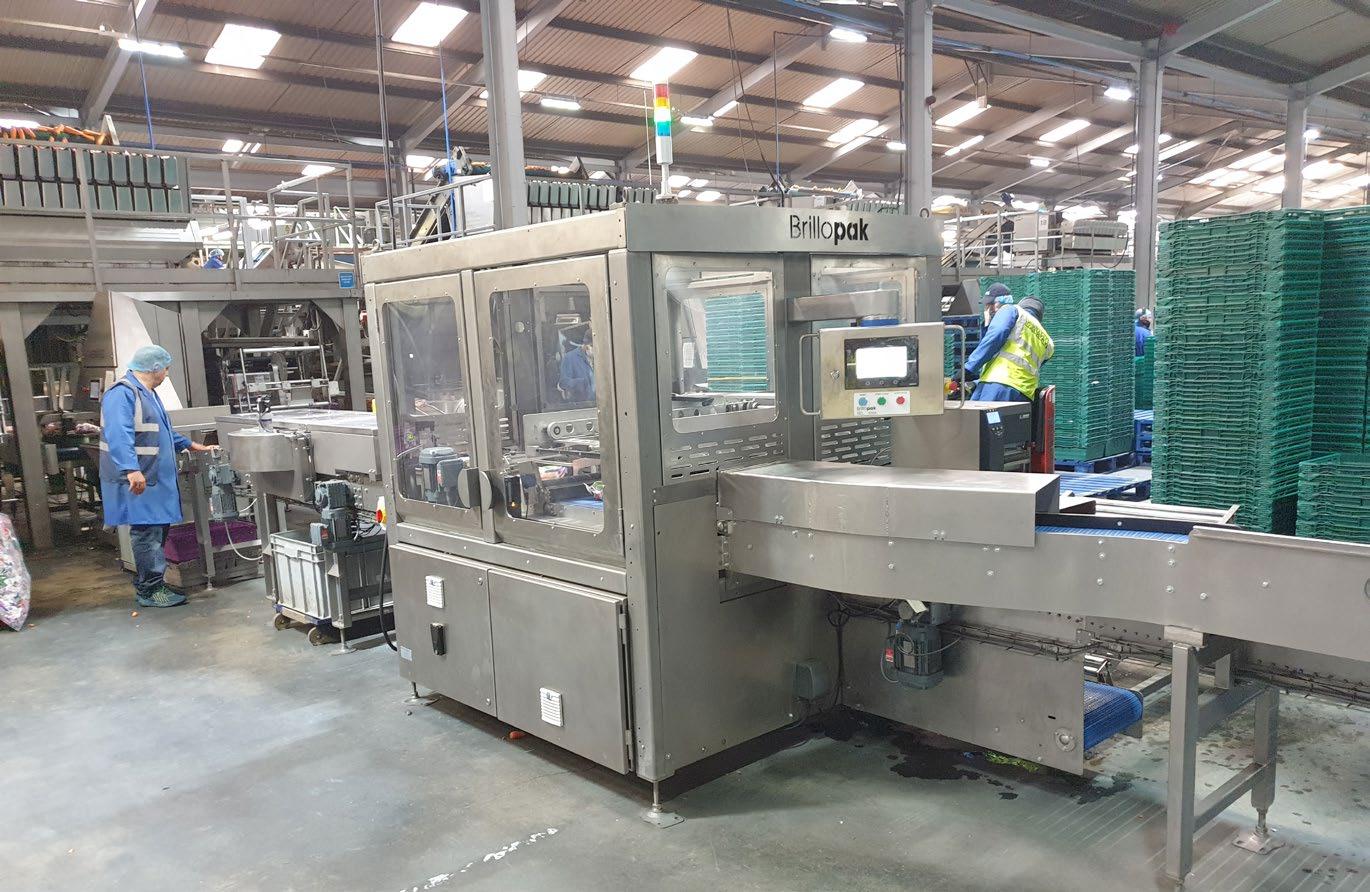
Eliminate Manual Handling, Reduce Risk and Improve Safety with a North Ridge Mobile Pump Kit
Manual handling is one of the most common methods utilised for the transferring of ingredients and waste within wholesale food manufacture. With over 30% of injuries reported to HSE being a direct result of manual handling - when the budget is simply not available to have a fully automated food production system; handling different products in a safe sanitary manner can often prove quite difficult.
Ensuring a production process meets all the current hygienic and food safety regulations is one of the main challenges facing any wholesale food business however one of the most often missed opportunities are investments into automating part of production to improve safety, reduce risk and wastage, increase accuracy or eliminate manual handling. The North Ridge bespoke food grade pump kits are often a solution to this.
CUSTOMER’S REQUIREMENT
When a traditional family run bakery established for over 50 years required a fully hygienic, easy to clean method to transfer Fruit Jams, Toffee Sauce, Fruit curds and Whipped cream they approached us to see if we could help. The variety of products posed a real challenge to ensure components did not wear prematurely, that damage could not be easily performed to the pump and that the customer had a low maintenance solution.
Some of the products were manually dispensed from cooking kettles at high temperatures into their current process at an average temperature of 100 - 110 °C, whilst other fluids which were incredibly viscous, were stored within refrigerators prior to use and needed pumping from cold to maintain hygiene. The customer wanted a bespoke multipurpose solution for their processes, which was sanitary grade, easy to clean, capable of handling all the products in question without manual handling, and suitable for high viscosities and temperatures up to 120 °C.
The unit also had to have a gentle pumping action due to the shear sensitivity of the whipped cream. High temperature liquids can have a negative impact on seals shortening their lifespan, cause issues at pump suction ports and reduce overall pump lifespan if careful consideration is not taken during pump selection.
Their current procedure involved manually transferring sauces via totes and buckets, however the customer wanted to improve their process to automate food transfer, reduce the likelihood of burns or accidents, and eliminate manual lifting and tipping of containers. They needed a custom costeffective unit that operates similar to a semi-automatic liquid filling machine.
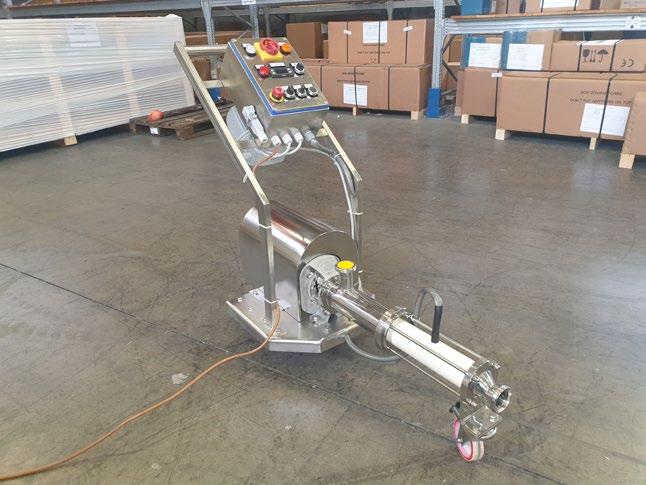
OUR MOBILE AUTOMATED PUMP SOLUTION
We supplied a completely bespoke mobile pump system with an integrated control panel. The pump is 3A sanitary certified, suitable for CIP (cleaningin-place) and SIP (sterilization-inplace) and designed without dead zones where product can build up preventing bacterial growth and cross contamination when handling different liquids. We also ensured the exterior of the unit was easy to clean during spray down by fitting a stainless-steel shroud covering both motor and gearbox. Besides having an integrated inverter for varying flow, the control panel has several other safety and operation features, to enable Start/Stop, reversing of the unit, alarm for motor overload and temperature control sensor to prevent damage from dry running.
The inverter can also be controlled via an App where operators can also view the status of the pump, reduce speed which is essential with some fluids such as Whipped Cream and further avoids the repeated contact of controls by multiple personnel.
PROJECT OUTCOME
Thank to our pump kit the customer improved their production efficiency dramatically, which in the food industry translates as an increase in profitability. The layout enabled users to operate the unit with very little training due to the simplicity of design but also built-in protection ensures the unit cannot be damaged through misuse. Social distancing has been easy to maintain through the use of remote controls, and as processes are automated less personnel are present within confined areas.
If you would like to talk to someone about automating a food transfer application contact us on 01773 302 660, or visit our website at www. northridgepumps.com to see our previous case studies.
We’re pump We’re pump specialists, so you specialists, so you don’t need to be don’t need to be

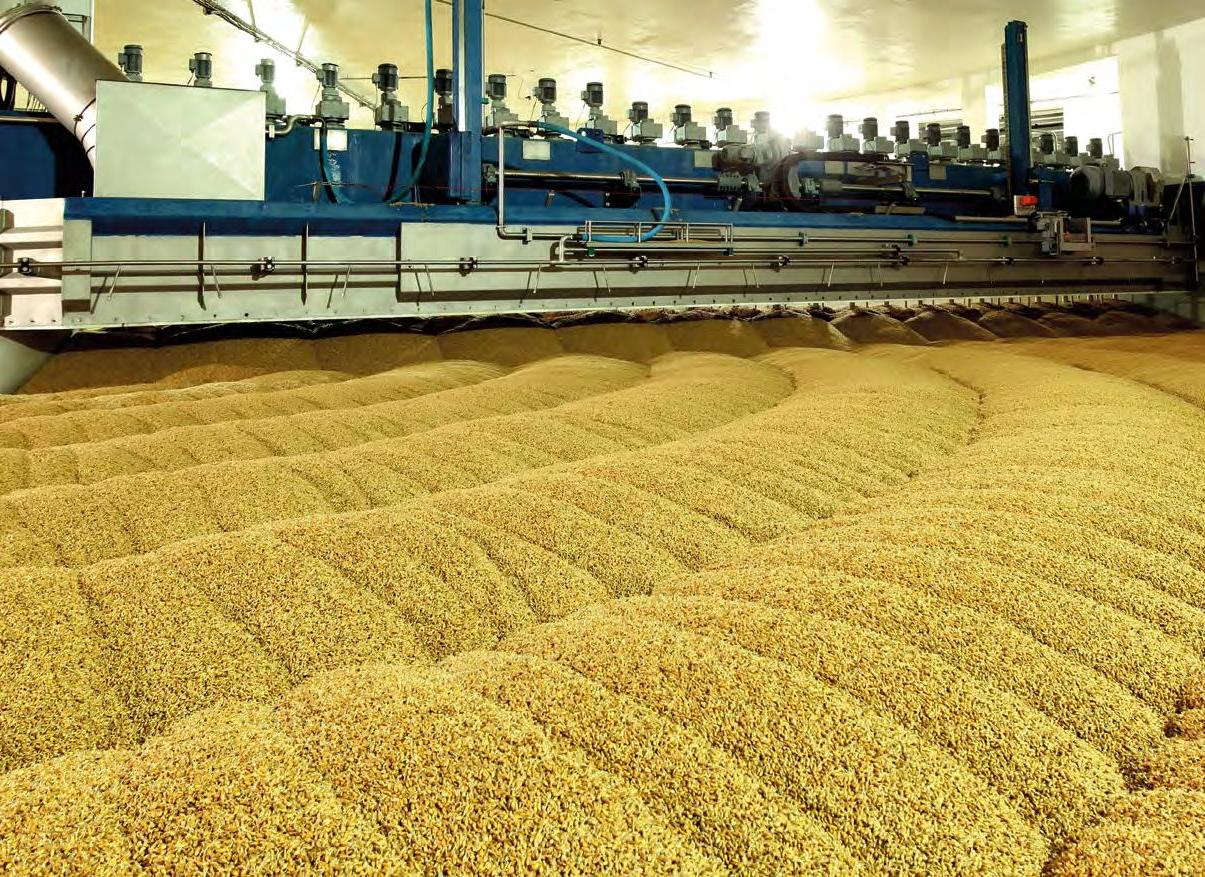


Sanitary Pumps Sanitary Pumps Engineered for Your Process Engineered for Your Process
Optimise performance with specialist support Optimise performance with specialist support
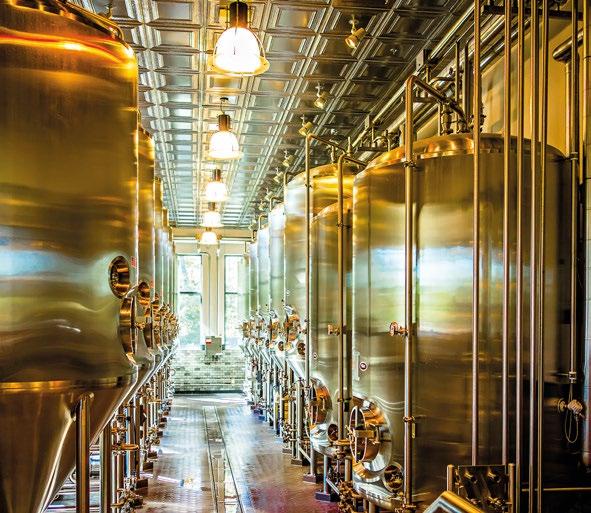


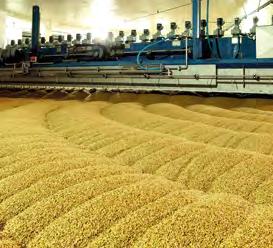

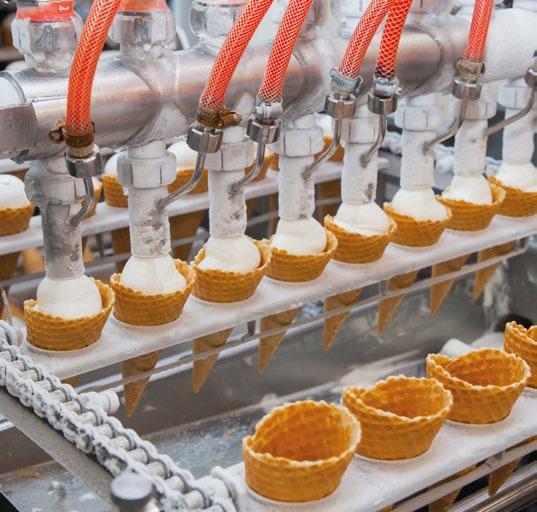
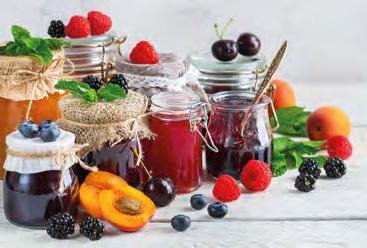

Whether you’re dealing with clogging, separation, downtime, or other issue - Whether you’re dealing with clogging, separation, downtime, or other issue - it’s costly. Time wasted troubleshooting and lower production mean missed it’s costly. Time wasted troubleshooting and lower production mean missed targets and less profit. A sanitary pump is the solution but choosing the right targets and less profit. A sanitary pump is the solution but choosing the right one feels like stepping into a minefield. You know what you need it to do but one feels like stepping into a minefield. You know what you need it to do but with so many options, it’s difficult to know which is best for your process and with so many options, it’s difficult to know which is best for your process and parameters. parameters.
+ Accelerated stator wear+ Accelerated stator wear + Clogging+ Clogging + Changes to fluid consistency+ Changes to fluid consistency + Clean-in-place and sterilise-in-place hygiene issues+ Clean-in-place and sterilise-in-place hygiene issues + Crushing of sensitive products+ Crushing of sensitive products + Inconsistency in finished product + Inaccurate transfer of flavourings or ingredients + Liquid separation + Seal wear or failure + Inconsistency in finished product + Inaccurate transfer of flavourings or ingredients + Liquid separation + Seal wear or failure We’ve been engineering sanitary pumps for sectors such as distilling, brewing, food manufacturing/processing, and more, for 20+ years. We understand industry-specific processes and know what it takes to optimise performance through better-suited pump design - giving you complete peace of mind. We’ve been engineering sanitary pumps for sectors such as distilling, brewing, food manufacturing/processing, and more, for 20+ years. We understand industry-specific processes and know what it takes to optimise performance through better-suited pump design - giving you complete peace of mind. EXPERT GUIDANCE: Our expert engineers understand your process and guide you through the options, so you can confidently select the most suitable sanitary pump. EXPERT GUIDANCE: Our expert engineers understand your process and guide you through the options, so you can confidently select the most suitable sanitary pump.
EXAMPLE PRODUCTS: EXAMPLE PRODUCTS:
+ Abrasive mixtures+ Abrasive mixtures + Creams, milk & ice cream+ Creams, milk & ice cream + Edible oils & fats+ Edible oils & fats + Fish & meat+ Fish & meat + Fruits eg. cooked apples, + Fruits eg. cooked apples, plums, berries, grapes plums, berries, grapes + Grains & seeds+ Grains & seeds + Pastes & purees+ Pastes & purees + Syrups, juices & alcohols+ Syrups, juices & alcohols + Vegetables & peelings+ Vegetables & peelings + Waste eg. trimmings, packaging & offcuts + Waste eg. trimmings, packaging & offcuts + Sheer sensitive liquids + Sheer sensitive liquids + Solid laden or viscous mixtures + Solid laden or viscous mixtures
Hygiene and the Role of Enclosure Design as well as Materials
The need to maintain high standards of hygiene in all food and beverage factories is well understood. Machines, enclosures and systems are all subject to stringent regulations to keep production facilities spotlessly clean.
What is perhaps less well appreciated is a food and beverage factory typically has three different hygiene zones. The three zones are broadly high, medium and low hygiene spaces. Each has specific requirements which must be met by the enclosures that are installed within them.
Here we review the design and build of enclosures, and show how (and why) they keep production lines running, minimise maintenance costs, and also maintain the highest standards of hygiene and safety.
It’s a misconception that IP ratings are fundamentally the most important focus when specifying an enclosure.
In an environment such as food and beverage manufacturing, an IP rating that matches the harsh washdown procedures is a priority. But there are other considerations which are just as important, notably eliminating the potential for bacterial contamination in enclosures which are either connected to the production line or close to it.
It’s also true that not all the machinery or IT systems in food production facilities are located within the “high hygiene” area – data centres, for example, will be either within IT rooms or at the very least in the office.
In fact, there are three “hygiene zones” within a food production plants, defined as high, medium and low hygiene spaces. Because each zone has its own defining characteristics, Rittal has developed two types of enclosure for food and beverage factories: its worldleading, stainless-steel AE enclosure and its specialised Hygiene Design (HD) range.
Each enclosure type has design features and IP ratings that make it more or less suitable for one or more of the zones. This suitability has been proved during rigorous, in-house testing. The results showed, for example, that the HD enclosure comprehensively out-pointing AE enclosures when it came to achieving the highest hygiene standards. This was particularly noticeable in areas such as hinges and the seal where contaminants can linger even after washdown. The tests were conducted over 24 hours using a milk product marked with a fluorescent substance.
Zone 1 is the food zone: it is where food is prepared and it is where the highest standards of hygiene must be adhered to. Rittal’s HD enclosures have been developed with these requirements in mind, which is why they have become the standard housing for electrical controls in this space.
The materials used in the HD enclosure’s construction are corrosion resistant and easy to clean, while all joints are seamlessly welded or glued. This creates a sealed environment for the electrical components inside, preventing water from entering during the wash-down and sanitation process.
Hygienic Design Hygienic Design
Extra cleanliness Extra cleanliness guaranteed guaranteed
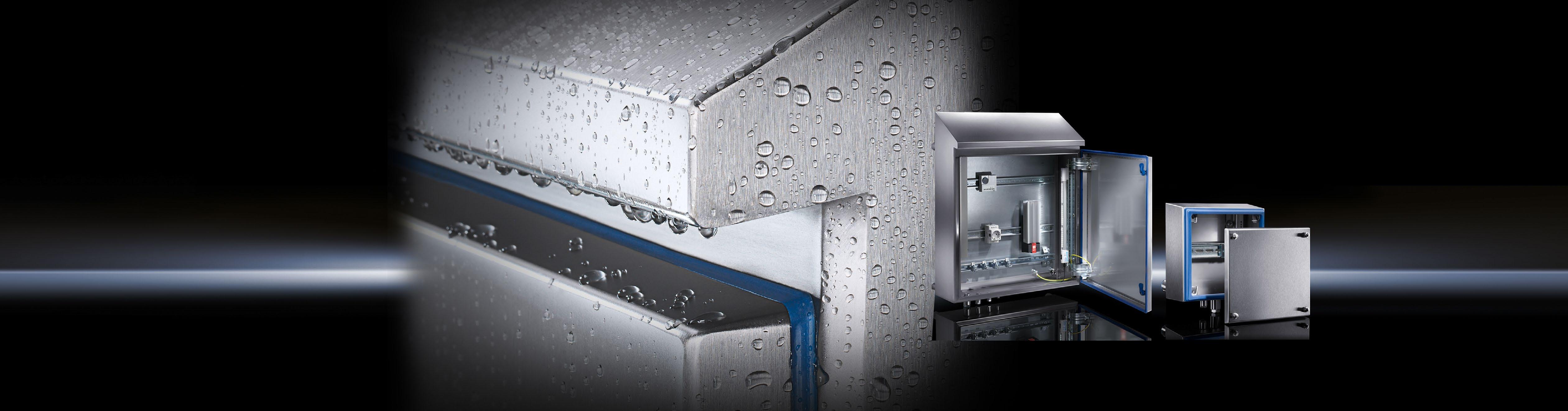
Any water ingress has the potential to seriously damage the machinery, leading to significant maintenance and repair costs, as well as production downtime.
But there are other key design features that have their part to play.
The HD enclosure’s forward-sloping roof stops anyone placing an object on top of it. The slope also means that the top can be easily inspected and allows fluids to quickly drain off.
The enclosure’s hinges are inside the sealing zone to create an easy-clean external surface while, inside, its durable, all-round, external silicone seal effectively stops any gaps appearing. These sealing frames are easily replaced and are dyed blue to clearly distinguish them from foodstuffs.
Unlike AE enclosures, the HD enclosure features no external cavity between enclosure and door, preventing food deposits becoming lodged here.
Finally, the HD enclosure’s lock and lock insert are made of stainless steel. Both the material and their shape allow easy and reliable cleaning.
Even minute amounts of contaminants in a Zone 1 space can build up over time, leading to bacterial growth that will compromises the hygienic standards of the whole facility. Rittal’s tests of the seals, edges and hinges on both enclosures showed no contamination lingered for HD enclosures, while the AE enclosures showed signs of deposits, even after cleaning.
Zone 2 is the spray zone: it is where food is either packaged or undergoing further sterilisation, meaning that products such as milk are enclosed in pipe systems.
The risk of contamination in this zone is therefore considerably lower than in the high hygiene zone but floors are cleaned with cleaning agents so any enclosures in this area have to be resistant to both corrosion and airborne chemical particles from the cleaning products.
Zone 3 is the non-food, low-hygiene zone: here, the risk of contamination of food and beverage products is minimal but there is still a need for specialist enclosures. It typically references spaces such as the IT area or the offices within a factory. While enclosures placed here do not have to comply with specific hygiene rules, they still have an important role protecting critical (and expensive) IT infrastructure. This is becoming increasingly important, with the rising demand for fast data processing to maintain production lines processes and capture performance data. This means factories are now installing edge data centres on the premises as physically close to the source as possible, to reduce latency and deliver close to ‘real-time’ information for management teams.
Rittal’s stainless-steel AE enclosure is ideally suited to both Zone’s 2 and 3. Extensive testing has demonstrated its ability to withstand water vapour, humidity and weak acids, which means it won’t be damaged by repeated exposure to Zone 2 floor cleaners. Added to which, it has a high IP rating which means dust particles from a shop floor won’t foul up the electrical components of a Zone 3 edge data centre.
SUMMARY
Enclosures developed for the food and beverage are perhaps one of the best examples of Rittal’s determination to meet the needs of its customers through tailored, innovative solutions.
Both enclosures have proved their value in testing, and each has been developed through close collaboration with food and beverage processing plants over the last 10 years, inline with guidance issued by the British Standards BS EN 1672-2:2005 +A1:2009.
rittal.co.uk
NEW: Hygienic DesignNEW: Hygienic Design air/water heat exchanger air/water heat exchanger The Rittal hygiene standards for The Rittal hygiene standards for maximum productivity maximum productivity
Significant savings on detergents and disinfectants Significant savings on detergents and disinfectants More productivity, thanks to reduced cleaning times More productivity, thanks to reduced cleaning times Comprehensive system solution, comprised of an Comprehensive system solution, comprised of an
enclosure plus climate control, up to a protection enclosure plus climate control, up to a protection category of IP 54 and IP 69K category of IP 54 and IP 69K
Greater reliability, thanks to DGUV testing Greater reliability, thanks to DGUV testing
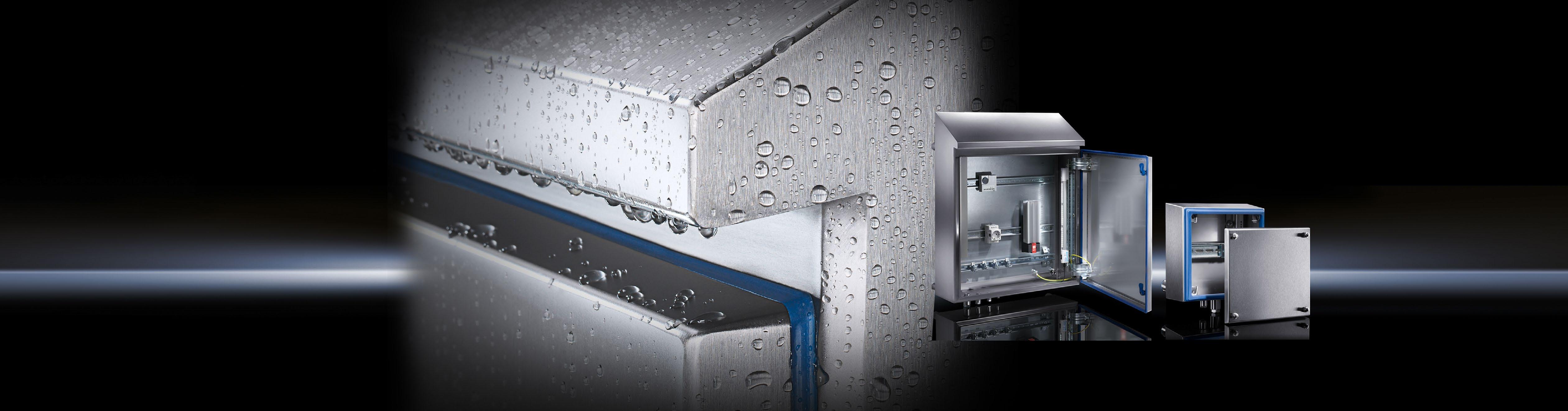
Manufacturing, construction, and engineering are a big part of our economy
But those workers also face a greater likelihood of serious work injuries than other workers.
IN 2019/20 the HSE reported that 111 workers were killed in workplace accidents and 69,206 non-fatal injuries were reported by employers.
Machinery accidents cost employees billions every year and on average employees who are injured usually have to take weeks off work or may never return.
WOULD YOU TAKE THAT CHANCE?
Lockout Tagout is an essential tool in the control of hazardous energy, in a wide range of industry sectors to prevent accidents.
What are hazardous energy sources?
Hazardous energy sources include electrical, mechanical, hydraulic, pneumatic, chemical, thermal, or other sources in machines and equipment.
The unexpected start-up or release of stored energy is immensely dangerous for any employee/operative in close proximity to the machine.
Which form of energy is lock out tag out used to control?
Lock out tag out is a hazardous energy control system used to ensure that machines and equipment are totally isolated from all energy sources. Locks are used to secure switches and valves in the OFF or SAFE position.
Lock out tag out is still the best-known practice for this protection and should be utilized any time the machine or equipment is being cleaned, maintained, and inspected. As well as for company shutdowns, turnarounds, power outages and more.
What is the difference between lock out and tag out?
Lock out means to place a lock on a device that prevents energy release. Tagout means to place a tag on a switch or other shut off device that warns not to start that piece of equipment.
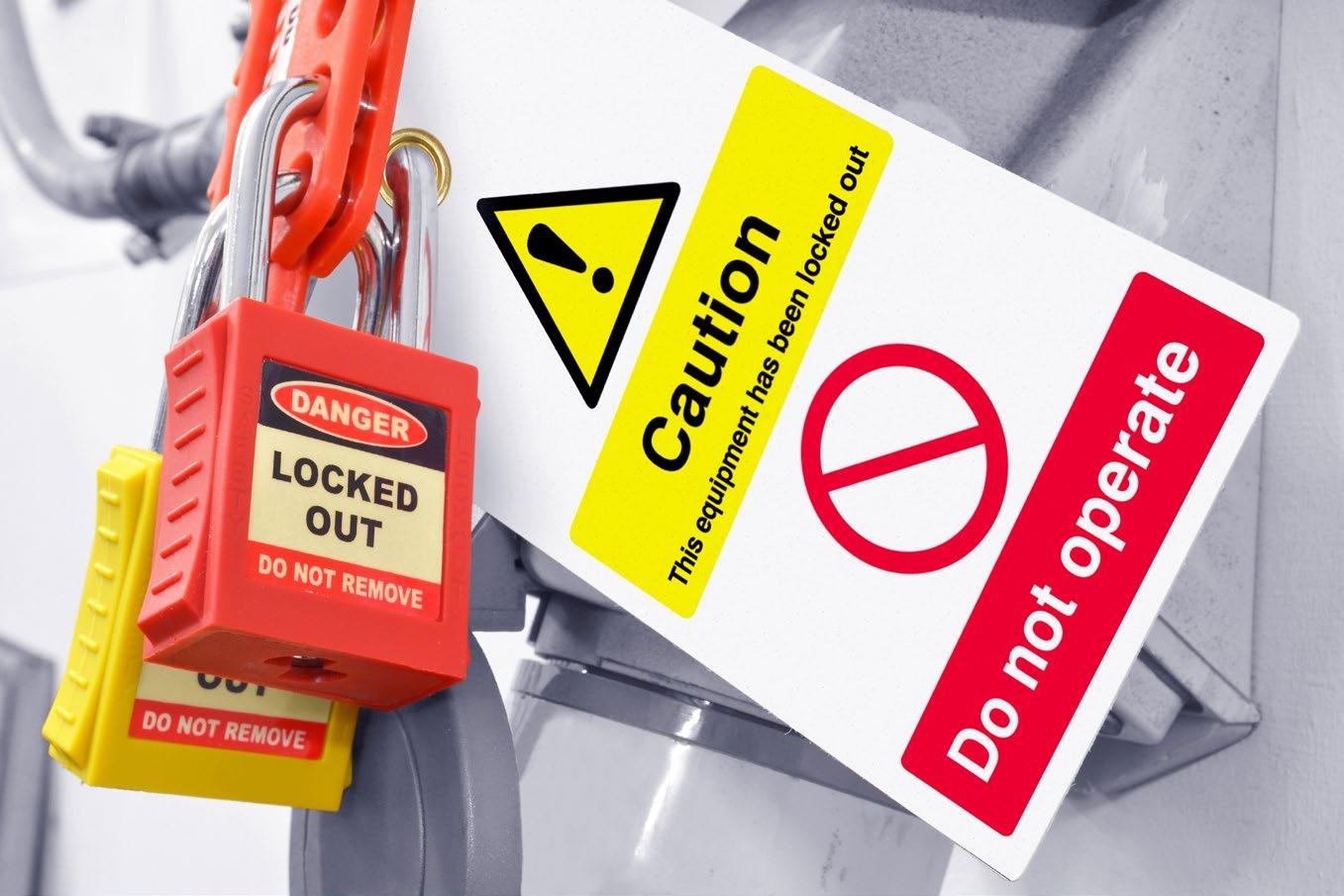
WHAT ARE THE 10 STEPS OF LOCK OUT TAG OUT?
Lock out tag out can easily be implemented by following this simple 10 step process,
1. Prepare 2. Notify 3. Turnoff 4. Isolate 5. Lock/s Application
Recognising the importance of a lock out tag out system is the first step towards implementing an effective safety process. It is not the whole solution, but it can clearly contribute, below are our simple lockout/tagout tips to follow • Clearly identify padlocks and tags either personally or departmentally. • Allow time & apply actions to relieve any stored/residual energies. • Ensure Lockout equipment is suitable for the intended task.
• Develop a written programme, with process & procedures with all details that MUST be followed.
• Any new machines must have a written programme/procedure developed against it. • All new & existing staff are to be trained and made aware of LOTOTO, it’s dangers and how to implement safely. According to the standard operating procedure (ongoing activity). • The only person to remove a lock is the one who applied it. • Implement and review the Lockout
Tagout process and procedures annually. Update and improve where required. • You must Try-Out every time.
Confirming the success of the isolation before proceeding with the task.
STAY ALERT AND DON’T GET HURT!
It goes without saying that industrial equipment can be dangerous, that’s why safety measures, process, products,
and personal protective equipment are used when using them. But machinery can also present hazards when it is not in operation and that’s why lockout/tagout is governed by strict regulations UK wide, such as
• HASAW 1974
• Electricity at work Regs 1989 • PUWER Regs 1998 – Reg 19 for isolation from Sources of Energy • Quarry Regs 1999 • OSHA 1910.147 – Control of
Hazardous Energy - osha.gov
The purpose of these regulations is to prevent injury and fatality. Contact with moving machinery and isolation (including stored energy) is still in the fatal 6, identified high consequence hazards.
Employers must develop, implement, and enforce an energy control program in line with regulations. As well and providing the correct Lockout Tagout equipment to fulfill the procedures in place.
RISK ASSESSMENT
Lockout Tagout is a process designed to reduce/eliminate risk, when performing high risk tasks. A risk assessment should be conducted each time a task occurs with potential risk. The machine/ task specific written energy control procedures will ensure every task has the risk assessed before any action commences. Potentially a one-off task outside of the norm can arise, meaning any works on said task should have a risk assessment conducted by a qualified & authorized representative to control this project. A newly written energy control program should be completed in case of a future re-occurrence.
LOCKOUT TAGOUT SAFETY CHECKS
Audits and visual inspections should be regularly carried out by a competent person, following the specific guidance outlined through regulations and company process/procedures. At least annually, a full audit and site survey should be completed to ensure that all equipment is of high quality, in good working order & in the required volumes to complete tasks. Additionally, the audit should cover and fulfill any newly updated/improved regulations.
It’s also worth noting, any new piece of machinery on site which will require isolation and its energy controlled. Should have a standalone machine specific energy control program written against it (working closely with the manufactures guidelines on its energy sources and moving parts) and trained out to all affected employees. All new employees should be trained to the level of every operative on site with CONCLUSION
Lockout Tagout is not an optional activity! The responsibility to govern this within establishments begins at the top. To instill the culture, behavior, and awareness to a high standard throughout.
Major industries are adopting the LOTOTO process due to the awareness and associated real-life risks. It is now being recognised as best practice for safety management in quarries, oil & gas, heavy manufacturing, food processing plants and more. Sectors such as renewable energy, waste and large retail companies are beginning to apply company-wide procedures utilising LOTOTO to ensure employee and operative safety with a structured and controlled procedural method.
We’ve got a lot of work to do to lockout machines better and control hazardous energy more effectively. Lockout/tagout is not the whole solution it should be combined with effective lockout training.
At Spectrum Industrial we can help by conducting a lockout/tagout survey to help you identify what you need, you can download our eBook to find out what is involved in a lockout/tagout survey.
Or click here to contact us.
Remember, “Short cuts, may cut a lift short!”.

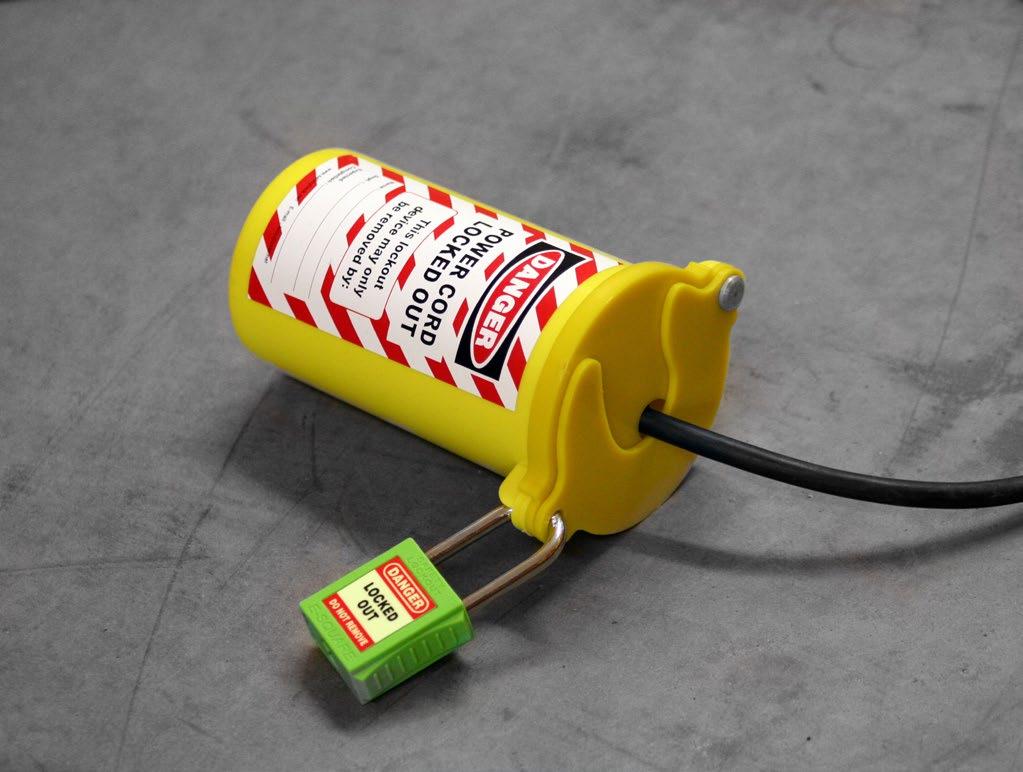