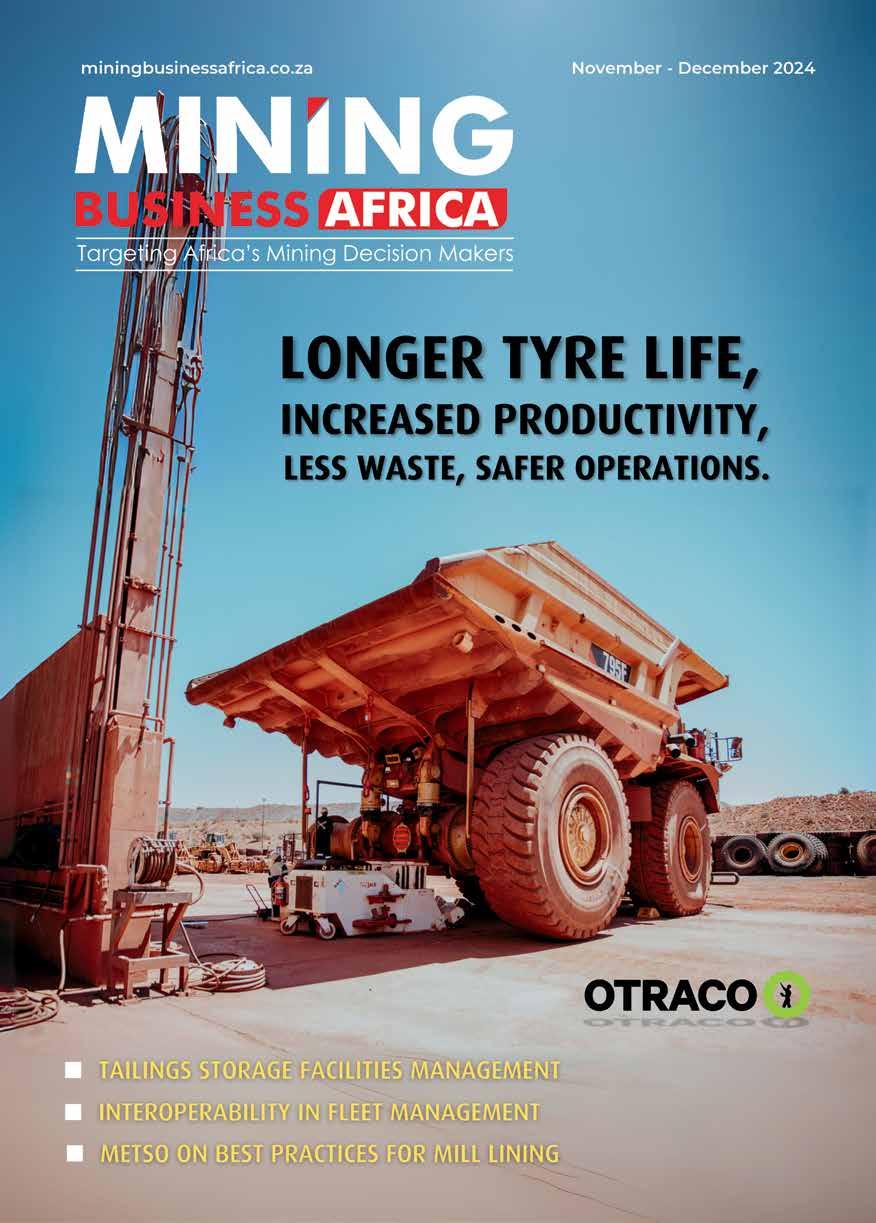
3-6 February 2025
CTICC, Cape Town

Mining Indaba: Creating opportunities for African miners and laying the groundwork for a greener, more inclusive future.

3-6 February 2025
CTICC, Cape Town
Mining Indaba: Creating opportunities for African miners and laying the groundwork for a greener, more inclusive future.
• Implementing innovative technological solutions for enhanced operational efficiency.
• Developing new standards for sustainable and innovative mining practices.
• Increasing resource efficiency and minimise waste.
• Contributing to productivity and health safety while reducing the environmental impact.
Cover Image: Courtesy
Transforming Tyre Management trom a Burden into a Benefit COVER STORY: PG 02
Drawing on over 50 years of know-how and technical expertise, Otraco Africa combines digital solutions and tailored services to reduce costs, enhance fleet uptime, and improve safety across Africa’s mining sector.
Editor
Nick Barnes
editor@miningbusinessafrica.co.za
+27 10 055 3356
Web/Sub-Editors
Jimmy Swira
Jimmy@miningbusinessafrica.co.za
+ 27 10 055 3356
Anita Anyango anyangoanita18@gmail.com
Contributing Writers
Chantelle C.
chantellec@miningbusinessafrica.co.za
+ 27 10 055 3356
Susan M. susanm@miningbusinessafrica.co.za
Sales and Marketing
Winnie Sentabire
winnie@miningbusinessafrica.co.za
+27 83 530 6832 | +27 10 055 3356
Angeline Ntobeng
angien@miningbusinessafrica.co.za
+ 27 078 322 5938
+ 27 010 055 3356
Accounts Precious Chirunga
accounts@miningbusinessafrica.co.za
+ 27 10 055 3356
We are living in interesting times, aren’t we? ‘Google’ the word tariffs, and the first pages about the incoming Donald Trump Administration and its introduction of punitive tariffs on imports pop up instantly. The ‘great man’ has threatened 50% tariffs on Made in China imports and 10% to 20% on goods from other countries.
However, there is a conundrum: American businesses heavily depend on affordable imports from China. While China contributes 35% to global manufacturing, the USA accounts for only 14%.
Whatever the outcome, it is indisputable that a tariff war will harm us in developing countries adversely. We are often at the receiving end of decisions - good or bad - made by developed countries.
Particularly for resource-rich developing countries hoping to capitalise on the demand for critical minerals - key to the green energy transition - a tariff war is a cause for concern. A tariff war would drive up the cost of imports for component manufacturers, prompting them to put projects on hold. This would directly impact mineral revenue for resource-rich countries. Ultimately, there will be no clear winner; it could be worse for us. When elephants in the world economy clash, the grass - us in the developing world - suffers.
Let sanity prevail on the issue of tariffs!
Nick Barnes editor@miningbusinessafrica.com
Art Director/Layout
Augustine Ombwa
Arobia Creative Consultancy austin@arobia.co.ke +254 772 187 334
Circulation/Sales info@miningbusinessafrica.co.za
+ 27 10 055 3356
Published By Media Icon (Pty) Ltd
The benefits of fleet management systems have been highlighted. But what happens when fleet management systems operate in isolation? Mining Business Africa examines.
Every day, there is mobile equipment from several OEMs performing various tasks at a mine site. That’s why disparate software systems designed to enhance different aspects of fleet management are used.
Fleet management desires the systems to work harmoniously. But that’s not how it works in the real world.
Due to interoperability challenges, running many disparate software systems becomes problematic in mines with large fleets. Therefore, mine operators should select interoperable fleet management systems.
Through interoperability, equipment and vehicles from various OEMs are able to communicate and share data, providing a clear picture of the fleet’s performance, location, and condition. Ultimately, they can optimise operations, reduce costs, and enhance the productivity of their fleet.
So, it is inconceivable why a mine operator would get non-interoperable systems.
Based on information various vendors of
fleet management shared with Mining Business Africa, software non-interoperability can be attributed to the following factors:
• Typically, a mining fleet consists of different OEMs, each with unique proprietary technologies and protocols. This poses a challenge when integrating systems from different vendors.
• Fleet management systems are designed exclusively to work with specific equipment. Due to this, data sharing and integration are restricted.
• A common problem is that data
from fleet management systems of machinery varies in format, structure, and quality. The absence of standardised data protocols—an issue often encountered—renders the exercise of integrating information from various sources complex and timeconsuming.
• Due to their conservative attitude, mine operators hold on to older equipment (think—if it is not broken, why fix it?). Unfortunately, outdated equipment may not have connectivity features such as telematics or IoT capabilities. Hence, integrating these legacy systems becomes a challenge. The easy way out is retrofitting or acquiring customised solutions, which becomes an unplanned cost burden.
• While ostensibly well-meant, data sharing across platforms and companies raises issues of privacy and security. However, in an industry where safeguarding data is critical, the concern is: Won’t interoperability compromise data security? The situation becomes complex when systems from multiple vendors are utilised.
As a result of non-interoperability among systems, inevitably, several challenges arise:
• Information is confined within individual systems and not available across platforms. This deprives fleet managers and operators of information on fleet performance, equipment status, and real-time metrics. As a result, this constrains data-driven decision-making, making it harder to optimise fleet operations.
Don’t miss the world’s premier mineral exploration and mining convention
2-5 5
PROSPECTORS & DEVELOPERS ASSOCIATION OF CANADA
Up to 30,0 00 attendees 700+ hours of programming
1,100+ exhibitors Delegates from 130+ countries
Meet investors & senior executives Unrivaled networking pdac.ca/convention | Toronto, Canada
• To manage different equipment, multiple disconnected systems are used. This requires manual data entry or separate dashboards. This is timeconsuming and prone to human error, resulting in delays, inconsistent data, and redundant tasks. The upshot is operational inefficiency.
• When each piece of equipment is managed in isolation, implementing comprehensive predictive maintenance across the fleet is difficult. Consequently, frequent repairs and unexpected breakdowns result in costly reactive maintenance.
• Without real-time monitoring capability of safety metrics and equipment, the risk of accidents and regulatory noncompliance increases.
• It is difficult to add new equipment or upgrade existing systems, as each new component may require additional custom integration work to communicate with legacy systems. This is costly and time-consuming, as new systems require bespoke solutions.
• Additional resources are required to maintain fragmented systems. This could be in the form of middleware solutions, manual workarounds, or dedicated IT staff. This results in higher IT maintenance costs and a need for specialised skills, which lead to additional costs.
• With outdated or incomplete data, managers may make uninformed decisions, which result in poor allocation of resources. As a result, an
operation can incur high operating costs and experience low productivity.
On the contrary, by embracing interoperable fleet management systems, mining companies may benefit in the following ways:
• Allowing all equipment, irrespective of manufacturer, to share data streamlines operations. Thus, through the consolidated view of fleet performance, fleet managers can make more informed and efficient decisions. This can reduce idle time and ensure better allocation of resources.
• By enabling predictive maintenance, an integrated system can significantly reduce costs resulting from unscheduled downtime and frequent repairs.
• Using real-time data, mining operators can track safety metrics and ensure that equipment meets compliance standards, contributing to a safer work environment.
• New equipment or technology can be integrated without the need for an overhaul of the entire fleet management system.
• By enabling diverse systems to communicate, interoperability supports data consolidation. This informs decisions to improve productivity, enhance safety, and support accurate forecasts.
Overall, mine operators have to be prudent in their procurement of fleet management software, emphasising interoperable systems for smooth management of their mobile equipment.
Four years ago, the Global Industry Standard on Tailings Management (GISTM) was introduced to facilitate sound tailings storage facility (TSF) management in mining. However, as expected, mining companies are taking gradual steps towards compliance. Mining Business Africa learns about the challenges they face and practical solutions available from SRK Consulting South Africa’s Lisl Pullinger, Principal Consultant, and Kavandren Moodley, Principal Environmental Scientist.
MBA: Well-intentioned as Principle 15 is, it places a significant burden on mines. What is the scope of information that can be disclosed to the public?
LP: Disclosure has traditionally meant sharing information mainly with shareholders and investors. However, the disclosure envisaged by the GISTM – particularly Principle 15 – is closely linked to the human rights of those most affected by TSFs. They have the right to understand all aspects of how the TSF, and its potential failure, could impact them, as well as the right to contribute to the protective systems and procedures in place.
This includes understanding a TSF’s consequence classification level – low, significant, high, very high, or extreme – based on the potential impacts of its failure. This classification helps gauge the level of risk the facility poses to the environment and nearby communities. Incidents at TSFs must also be disclosed; some companies provide a brief acknowledgment, while others give detailed descriptions and outline subsequent management actions.
For companies working towards GISTM compliance, it’s important to share information on progress and audit results, including
successes and areas still needing improvement. This is particularly crucial for facilities that may not yet meet all compliance standards due to legacy design or financial constraints.
KM: Sharing information on emergency response strategies is essential to ensure that project-affected people are aware of potential hazards and prepared to respond effectively in case of an incident. The GISTM mandates that mines develop comprehensive emergency preparedness and recovery plans, offering stakeholders clear information and opportunities to understand and engage with these plans.
MBA: There are reports of mining companies being selective in what they disclose about their TSFs. From a broader perspective, what could be the potential benefits of full disclosure?
LP: The GISTM is quite prescriptive about the required disclosures, making selective disclosure more difficult. Many companies are not accustomed to divulging such detail, including the TSF’s consequence category. While certain stakeholders may only need an overview, communities may require more detailed information about aspects that directly
affect them.
Full disclosure fosters trust with communities, strengthens corporate reputations, and meets investor expectations. It also promotes more transparent TSF operations, building higher safety levels. For effective impact, however, disclosed information must be easily understood by stakeholders, especially communities. This may involve using plain language and possibly capacity-building efforts to educate communities about tailings, mining practices, TSF risks, and safety protocols, empowering them to interpret the information meaningfully.
KM: Involving project-affected people in emergency preparedness and risk assessment enhances overall risk management. This approach clarifies actions in the event of a TSF failure, reducing the consequences of an emergency and improving safety outcomes.
Establishing strong relationships with project-affected people is essential when discussing TSFs, as this sensitive topic requires a solid foundation of trust for open dialogue. In our experience, building this foundation is a gradual, ongoing process, often needing specialist guidance and local knowledge. With time and consistent transparency, trust can be fostered, making disclosure a key element in
strengthening relationships between mines and affected communities.
MBA: Disclosure of information about tailings facilities often subjects a mine to intense scrutiny from environmental activists. How can mining companies turn this challenge into an opportunity?
KM: The GISTM – and environmental impact assessments in general – encourages a proactive approach to stakeholder engagement. The activist community values increased engagement, which can help mining companies address social and environmental concerns more holistically and collaboratively. This inclusiveness aligns with modern ESG expectations and strengthens a company’s social licence to operate. Disclosing information is part of a process that could transform activist scrutiny into productive dialogue.
LP: TSF disclosure offers mining companies an opportunity to discuss necessary practices with activists. At the same time, they can communicate their efforts to operate within “planetary boundaries,” or sustainable limits. This platform enables companies to clarify misunderstandings, correct misinformation, and present factual data, fostering broader societal support for mining.
MBA: Naturally, a mine can only disclose data when confident that its TSF meets all compliance standards. What range of independent expertise can be sought to enhance compliance?
LP: Meeting the GISTM standard involves a challenging range of tasks, especially given that many TSFs were originally designed for less stringent requirements. Compliance is often a longer-term journey, and disclosure cannot wait until final compliance is achieved.
Instead, disclosures should reflect ongoing progress, showing how mines set and work towards milestones. Once again, transparency and honesty in this process help build trust and
collaboration with stakeholders.
The GISTM calls for the integration of various disciplines, from tailings engineering and water management to human rights, environmental performance, and climate change. Most mines don’t have all this expertise in-house, so they often contract these services from companies like SRK.
KM: Another important aspect of GISTM compliance is ensuring the integrity of the work being done and the recommendations provided by consulting engineers and scientists.
MBA: What should be the main priorities for companies in their pursuit of compliance?
LP: A human-centred approach is fundamental to each GISTM principle, applying equally to affected communities, employees, and investors. The focus is on preserving and protecting human life, requiring early and ongoing community engagement, linked to a detailed and negotiated emergency preparedness and response plan.
KM: The primary focus is on mitigating risks to human life, covering everything from safe TSF design, construction, and maintenance to robust emergency preparedness measures. Environmental protection is also a critical priority outlined by the GISTM, ensuring that tailings management practices safeguard people and the surrounding ecosystem.
MBA: Is there any additional advice you could share with mining companies regarding TSF disclosure?
KM: Disclosure of GISTM compliance efforts should not be seen as an isolated activity but as an extension of stakeholder relationships. As those most affected by potential TSF incidents, project-affected people deserve special attention, and engagement should begin well in advance of any TSF-related disclosures. A strong relationship with communities is essential to ensure disclosures effectively mitigate risk, as intended by the GISTM.
The MyTSF dashboard partnership aims to simplify tailings storage facilities (TSFs) monitoring for African mining operations — typically a tedious and error-prone process when carried out using conventional techniques. Capable of delivering verifiable data in near-real time as and when needed, the MyTSF dashboard facilitates TSF compliance.
By Jimmy Swira
The ratification of the GISTM has brought the management of tailings storage facilities (TSFs) into a huge spotlight globally, and Africa is no exception. While, as expected, there is an intense focus on operational TSFs, the code has left no stone unturned. For instance, Principle 6 states unequivocally: “Plan, build, and operate the tailings facility to manage risk at all phases of the tailings facility lifecycle, including closure and post-closure.”
The MyTSF Dashboard Partnership Thus, measures must be adopted to monitor TSFs throughout their lifecycle. In a perfectly timed development, GeoTerra Image (GTI) has teamed up with AssetAssurance Monitoring (AAM) to provide a viable solution: the MyTSF dashboard partnership.
AAM brings global experience in ground monitoring from space to the table. The company’s lead, John Metzger, has worked on earth monitoring projects in Africa.
In a Teams interview with Mining Business Africa, GTI Director, Mark Thompson, lauds AAM as the right partner GTI needs to deliver the most suitable monitoring solution for clients in mining and related sectors. “It is a marriage of agile capabilities. From the get-go, the synergy between the two entities was perfectly matched, and everything fell into place,” he enthuses, upbeat about the opportunities MyTSF will unlock for organisations needing earth monitoring services.
The MyTSF dashboard partnership supports near-real-time assessments of legacy, abandoned, operational tailings, and mine impoundments. Without a doubt, it addresses the huge demand for reliable land risk reduction monitoring in sub-Saharan Africa.
However, price and availability remain constraints to access on the continent. Responding to this observation, Metzger
explains that MyTSF is precisely what potential clients need.
“Our MyTSF dashboard offers a modern, affordable, and scalable, visually exciting view of this vital global challenge — supporting safe use, and user/community awareness.”
The MyTSF’s strength lies in its convenience for the end-user. It provides unparalleled awareness of abandoned, legacy, and operating TSFs and mine site impoundments. With a modern and accessible dashboard, sharing intra-weekly site details across one or many sites is seamless. Updates are generated every 5-days, based on the Sentinel-2 overpass schedules.
Typically, the data is accessible as GISready or report-ready graphics available from the dashboard results. Other mine site data — whether from in-situ, IoT, or displacement data from local or remote radar systems — are mutually supported. Differential tailings depositions and local precipitation events are reflected in embankment pressures, potential displacements, and asset anomalies.
The MyTSF’s strength lies in its convenience for the end-user. It provides unparalleled awareness of abandoned, legacy, and operating TSFs and mine site impoundments.
This avoids delays associated with red tape at other service providers.
Benefits beyond Risk Reduction
The MyTSF dashboard opens vast opportunities
for end-users — mining companies in particular — extending benefits beyond risk reduction. Three areas are noteworthy:
When organisations have access to reliable data, they may need to hire more personnel to implement data-driven remediation measures, creating employment opportunities.
Reliable data can improve compliance with the GISTM code and regulations in a particular jurisdiction, such as the water use licences in South Africa. This ensures that mines operate on the right side of the law.
Data from MyTSF contributes to and fosters good relations among staff, stakeholders, and the local community. This builds confidence, cementing stakeholder relationships.
The MyTSF dashboard team is eager to serve clients in mining and related sectors. They are committed to providing cost-effective, rapid solutions for land monitoring requirements across Africa. “The MyTSF dashboard is a smarter approach to tailings monitoring that clients have never experienced before and will make a big difference.”
AAM is based in Elko, Nevada and Noblesville, Indian (USA) , while GTI is in Pretoria, South Africa. Yet they are able to work seamlessly, demonstrating the possibilities opened by the power of MyTSF dashboard.
Below are two brief examples in Canada and the USA illustrating the convenience of actionable intelligence:
Stringent environmental regulations govern mining activity. AAM’s TIRI proved instrumental at TSFs under construction in northern Canada, located in an environmentally sensitive area. In-situ instruments were omitted from the original design. Thus, to address this, AAM developed its TIRI product with a focus on providing interactive, visual, and numeric results that were shareable across the mine staff. Guess what happened next? Data addressed all the questions! Operations and Production had a relaible data resource in their suport.
A major user in the USA, a global gold mining leader, manages twenty sites spread over 460 square kilometres through the MyTSF dashboard. Four times a month, refreshed and continuous data are channelled to their desktops through the MyTSF dashboard. This allows one to two staff to assess and better manage two sites spread across 460 square kilometres.
“WearCheck’s highly experienced, well-trained technicians conduct a multitude of visual inspections on a range of components daily.”
Jaco Venter, a senior machinery inspector at WearCheck, conducts ultrasound testing on a winder brake spring nest tension bolt during a non-destructive testing (NDT) routine.
Non-destructive testing (NDT) is one of the advanced field services offered by specialist condition monitoring company, WearCheck.
In addition to traditional oil analysis techniques, the company’s service offering includes other advanced field services (rope testing, technical compliance), asset reliability care (ARC) services, transformer oil analysis, water analysis, and lubricant-enabled reliability (LER) services.
Expert technicians trained within each analysis and monitoring technique perform the tests using highly specialised equipment. Test results are assessed by experienced team members, and feedback is sent to the client.
NDT manager for WearCheck, Adri Ludick, explains NDT. ‘We conduct a variety of testing techniques through which the properties and condition of a component are evaluated without causing any permanent damage to it. This is a useful condition monitoring technique in many sectors, particularly mining, where it helps to enhance asset reliability and availability.
‘Typically, NDT is used in critical mining component assessments, machine condition assessments, and inspection of ancillary
WearCheck offers several non-destructive testing (NDT) services – here, senior machinery inspector Jaco Venter conducts ultrasound testing on a winder brake caliper pin.
equipment such as main vent fans, compressors, mills, pumps and conveyors.
‘In addition to visual inspection, our main tests include eddy-current-, magnetic-particle-, liquid penetrant-, and ultrasonic testing.
‘NDT does not permanently alter the object undergoing inspection, making NDT a convenient asset reliability enhancement tool.
This detects surface defects, (e.g. early-stage cracks), on metallic machine components, and is used across many industries, from aerospace to beer brewing. This NDT technique is applicable to both magnetic and non-magnetic components, including steel, copper, brass and aluminium.
A high-frequency electric current (an eddy current) is induced into the material, and the response is measured, yielding a profile of the component.
Defect-free material has a very specific “fingerprint”, therefore, when the test results are compared to this, the presence of defects is indicated.
With cracks, the earlier they are detected, the less potential damage they cause. Eddy-current testing detects crack initiation at extremely early
stages.
An advanced option is the phased-array eddy-current testing, which creates a 3D picture of the component, giving greater visual insight.
This is a similar application to eddy-current testing, in that both techniques detect surface cracks on magnetic materials. This technique, which is used across a wide range of industries is only used on magnetic material, such as steel.
The process in this test is to magnetise the component and then saturate it with a very fine magnetised ink or a fine powder.
Any anomaly in the surface being tested causes a concentration of the magnetic field around it, therefore drawing the magnetic ink to the crack and making the defect visually detectable. (Eddy-current testing requires the interpretation of a signal on an oscilloscope screen.)
An advantage of magnetic particle testing is that it can be used to test very large surface areas, very quickly.
This is typically performed on non-magnetic
materials (e.g., copper, aluminium), and is essentially a non-magnetic version of magnetic particle testing.
It involves a five-step process. Firstly, the surface is cleaned of all foreign material. Next, it is saturated with a non-harmful penetrating ink. The surface does not have to be horizontal. Thirdly, the penetrant is wiped off the surface of the material. Fourth, a developing chemical is applied over the ink. The developer draws the penetrant from any cracks to form a visible indication. In the fifth step, the component surface is visually examined during and after the development process and results are recorded.
This method is used to test such items as vehicle components and ventilation fan blades.
A “fish finder” on a fishing boat reveals the depth and size of the fish. Similarly, this methodology allows technicians to see sub-surface defects in both metal and non-metal components.
An ultrasonic flaw-detector instrument fires ultrasonic pulses into the material, and simultaneously detects the reflection. By measuring the time difference between the pulse and the reflection and knowing the speed of sound in the test material, the location of the defect is pinpointed.
An advanced option is phased-array ultrasonic testing, where 64 pulses (instead of one) are fired into the component. By fine-tuning the pulse-strength, we can “steer” the beam in different directions. The advanced option yields a 3D picture of the component, instead of merely a pulse on a screen.
WearCheck’s condition monitoring services are used by clients operating in a large and diverse range of industries, including mining, earth-moving, power generation, aviation, maritime, industrial, manufacturing, construction and others.
Just how a “fish finder” on a fishing boat reveals the depth and size of the fish, this uses similar methodology, allowing technicians to see subsurface defects in both metal and non-metal components.
During the process, an ultrasonic flaw detector instrument fires ultrasonic pulses into the material, and simultaneously detects the reflection. By measuring the time difference between the pulse and the reflection and knowing the speed of sound in the test material, you can pinpoint the location of the defect. It is widely used across all industries to detect anomalies.
An advanced option is phased array ultrasonic testing, where, instead of one pulse, 64 pulses are fired into the component. By fine-tuning the pulse-strength, we can “steer” the beam in different directions. The advanced option enables us to get a 3D picture of the component, instead of merely a pulse on a screen.
WearCheck’s highly experienced, well-trained technicians conduct a multitude of visual inspections on a range of components daily. Their eyes are conditioned to recognise earlystage defects which are visible, and to identify potential “hotspots” which require further testing.
Founded in Durban, South Africa in 1976, WearCheck serves as a hub for a significant array of condition monitoring techniques, making its services available to clients across the African content and beyond.
To ensure that clients gain maximum benefit from the different monitoring programmes, and to empower maintenance crews to stay ahead of advancing technology, the company offers a selection of technical training courses, many of which earn the delegates sought-after continuing professional development (CPD) points.
WearCheck, Africa's leading condi�on monitoring company, is commi�ed to serving the mining industry with its range of sophis�cated analy�cal techniques.
Our specialist oil, coolant and fuel tes�ng programmes allow customers to reduce maintenance costs, avoid unexpected mechanical failures and ul�mately reduce unscheduled down�me.
Multidisciplinary laboratory proficiency testing (PT) solutions provider, Qotho Minerals, pronounces its commitment to meeting clients‘ critical and rare earths projects in 2025.
Laboratories in the mining sector need a realistic testing environment that enhances their analytical capabilities. As such, precision and reliability are central to delivering trustworthy results to their clients.
Qotho Minerals (QM) addresses this need by providing customised, pre-planned Proficiency Testing (PT) schemes that mimic real mining materials. The materials are meticulously prepared to ensure they replicate the complexities and variances seen in actual mining operations.
QM is devoted to integrity, quality, accountability, and continuous improvement. The company’s adherence to ISO 17043 (PT Scheme Provider) and ISO 17034 (Certified Reference Material Producer) underscores its reputation for quality and consistency.
“These ISO standards ensure that all our PT programs are designed and implemented with international best practices, giving participants confidence that their results meet global benchmarks. Furthermore, we integrate traceability to Certified Reference Materials (CRMs) into our PT solutions,” says Takudzwa Tsapayi, QM’s Operations Manager, highlighting the effectiveness of Qotho’s approach.
A comprehensive reporting system is a cornerstone of QM’s approach. It provides participants with detailed statistical analyses of their performance.
The generated reports are not just a
summary of results but also diagnostic tools that help laboratories identify strengths and areas for improvement. By equipping laboratories with these insights, QM empowers them to enhance their processes and ultimately deliver accurate and dependable results to the mining industry.
What sets QM apart is its flexibility to explore opportunities across various areas as part of its continuous improvement strategy. For instance, the company has embraced AI and big data to enhance its PT processes, unlocking exciting possibilities on the horizon.
“These technologies streamline processes, enabling more efficient operations and reducing redundancies. For example, AI can help automate the identification of bottlenecks, ensuring that workflows remain agile and responsive to participant needs,” Tsapayi explains.
Another area with significant potential is the application of AI and big data in historical trend analysis. “By examining PT performance data over time, big data tools can provide insights into which analytical methods perform best for specific participants or sample types. This
information helps laboratories adopt practices that maximise accuracy and reliability, fostering continuous improvement across the board,” adds Tsapayi.
QM takes pride in transforming from a smallscale operation to a leader in proficiency testing for the mining industry. A notable milestone was its transition from a suburban two-door garage to a fully operational 1,600m² factory in Broederstroom.
Reflecting on this achievement, Tsapayi notes: “This transformation demonstrates our capacity to meet the expanding needs of clients with state-of-the-art facilities.” Specifically, he highlights two key accomplishments: ISO accreditation and new PT schemes.
A testament to the company’s commitment to quality and reliability is ISO 17034 accreditation, a globally recognised standard for Certified Reference Materials. This demonstrates QM’s dedication to providing clients with reliable tools for achieving accurate results and maintaining international credibility.
In 2024, QM introduced six new PT schemes for Lead (Concentrate), Tin (Ore, Concentrate & Tails), Tantalum (Concentrate & Tails), Lithium (Ore), Aluminium (Bauxite), and Foundry Sands. “These additions highlight Qotho’s growth and ability to cater to diverse and emerging industry needs. For instance, the inclusion of lithium addresses the rising demand for critical minerals
in green energy applications,” Tsapayi explains. Looking ahead to 2024, it will be more of the same for the team at QM. They declare their commitment to supplying PT schemes that help laboratories for mining companies achieve precision in implementing best practices in mineral testing tasks.
Qotho Minerals eagerly adopts innovations that improve the delivery of solutions to clients. It has identified the digital transformation of proficiency testing, particularly online reporting of PT results, as an area it will explore.
In addition to enabling streamlined, real-time reporting, digital platforms open the door to more automated processes. This reduces the manual burden on laboratories, improving the efficiency and transparency of the PT process. As more laboratories embrace these technologies, Qotho is poised to lead the way in offering user-friendly, digital solutions that meet the demands of a contemporary industry.
Strengthened by digitisation, Qotho is firmly positioned for a leading role in niche markets like critical minerals and rare earth elements.
i. Critical minerals
With the global push toward renewable energy and electric vehicle production, demand for critical minerals like recycled black mass and rare earth elements is rising.
“By offering PT schemes for these minerals, Qotho is well-positioned to support laboratories involved in the exploration and analysis of these critical resources, ensuring accuracy in a highstakes market,” says Tsapayi.
ii. Rare earth elements
Qotho also aims to expand its presence in niche markets for rare earth elements. With growing industry regulations and the need for ISO 17025 accreditation, Tsapayi believes Qotho’s PT programs are precisely tailored to assist laboratories in maintaining compliance and ensuring accuracy in these highly specialised areas.
& long term
Specialists in the manufacturing of domestic and industrial pressed steel sectional water tanks
Structa Technology’s Prestanks are hygienically safe, cost effective and a reliable way to store water for commercial sectors, private sectors and even for personalized storage. Temporary or permanent erection at mines, powerstations, building sites, hospitals, water affairs,municipalities, rural communities and agriculture.
Structa Technology is a Level 1 BBBEE Contributor , and is part of the STRUCTA GROUP of Companies
Estimator: Judy van der Walt - watertanks1@structatech.co.za
Director: Rodney Cory - rodney@structatech.co.za C: 082 575 2275 | www.prestank.co.za
“Southern Africa offers fertile ground for industries that intersect with mining. There is a strong case for investment in beneficiation facilities, battery manufacturing, and recycling plants.”
By Bruce Dickinson
As the world accelerates towards green energy and technological advancements, Southern Africa stands at the epicentre with its wealth of critical minerals. The region’s reserves of platinum, chromium, lithium, and rare earth elements position it as a key player in the global supply chain. However, there’s an opportunity here that goes beyond extractionmining in Southern Africa can catalyse economic transformation, bringing sustainable benefits to communities and regional economies long after the mines are closed.
The regional landscape: Abundance and opportunities
Southern Africa’s mineral wealth is wellknown, with the Southern African Development Community (SADC) controlling 90% of the world’s platinum reserves and 80% of its chromium deposits, among other vital resources.
Key regional projects showcase the landscape’s strength and potential including:
• With over USD 1 billion in recent investments, Zimbabwe is quickly becoming a global lithium hub.
• The Zambia-DRC Battery Metals Corridor is a promising initiative enhancing the regional supply chain for battery metals.
• Efforts to revitalise South Africa’s platinum industry are well underway.
Projects like the Lobito Corridor, a vital transportation link, are also strategically enhancing trade and co-investment in infrastructure and related industries. These developments illustrate Southern Africa’s readiness for broader investment across upstream, midstream, and downstream sectors.
Investment opportunities beyond mining
Southern Africa offers fertile ground for industries that intersect with mining. There is a strong case for investment in beneficiation facilities, battery manufacturing, and recycling
plants. Additionally, integrated planning can reveal co-investment opportunities in sectors like infrastructure, agriculture, energy, and manufacturing, establishing a diversified economic base and creating employment in communities impacted by mining.
Mining companies don’t need to shoulder these investment initiatives alone. By inviting investment in shared infrastructure, such as transportation networks, ports, and energy facilities, other industries can piggyback off mining, fostering a sustainable, interlinked economy.
The Impact of the African Continental Free Trade Area (AfCFTA)
AfCFTA, the world’s largest free trade area, promises to reshape intra-African trade by creating a market of over 1.3 billion people. For Southern Africa’s mining sector, this presents a wealth of opportunities. By eliminating trade barriers and harmonising trade policies, AfCFTA will expand market access and attract investors.
With a legacy spanning over a century and a half, we have consistently delivered innovative solutions to our clients’ most complex legal requirements in Sub-Saharan Africa’s mineral-rich countries.
We offer a fully integrated service that is flexible enough to face any challenge, no matter how complex.
Scan the code to learn more.
Additionally, the agreement offers opportunities to develop supply chains within the continent, particularly for emerging sectors like battery and technology. This strategic move will not only boost economic growth but also diversify the region’s economic landscape.
Strengthening policies for a sustainable future Government policies are critical to ensuring that mining and related industries contribute to sustainable development. Southern African countries are progressing in aligning their policies, with efforts in state participation, local content mandates, and environmental protection. There’s room, however, for further enhancement. Streamlining licensing and permitting processes would attract investor confidence and expedite project timelines. Establishing competitive fiscal regimes and striking a balance between royalty rates and incentives would attract investment while ensuring fair compensation for resources. Furthermore, fostering public-private partnerships (PPPs) can mobilise resources for critical infrastructure and energy projects, creating a foundation for long-term economic resilience.
Prioritising ESG and communitycentric approaches
Sustainable mining practices are essential for minimising environmental impact and building positive community relationships. Key areas include:
Southern Africa offers fertile ground for industries that intersect with mining. There is a strong case for investment in beneficiation facilities, battery manufacturing, and recycling plants.
• Environmental stewardship: Mining operations can incorporate renewable energy sources, emissions reduction technologies, and effective waste management systems.
• Community engagement: Transparent benefit-sharing agreements, local employment targets, and skills development programmes can ensure that the benefits of mining extend to local communities.
• Long-term impact: By fostering economic diversification programmes and infrastructure that serves local needs, mining companies can leave a legacy that persists beyond the mine’s operational life.
Looking ahead: A holistic approach to regional growth
With a thoughtful, collaborative approach, mining in Southern Africa can be a powerful lever for regional development. By embracing initiatives like AfCFTA and building out value chains in industries like battery manufacturing, Southern Africa can capture more of the value within the region, creating resilient economies that support communities and industries for generations.
Southern Africa’s critical minerals are not just a resource to be extracted—they are the foundation for sustainable growth, economic resilience, and a prosperous future for the region and its people. Through collective commitment and investment, we can unlock the region’s full potential, ensuring that Southern Africa’s mineral wealth is a catalyst for inclusive, sustainable development across the continent.
Premature liner wear has a significant impact on mill availability. Data tests from regularly monitoring a mill’s operating conditions and liner wear life can be used to determine the design of the next set of mill liners.
By Jimmy Swira
Understandably, African mining companies have their sights set on the bigger picture of increased revenue. However, in this zealous pursuit, their major oversight could be neglecting smaller, yet crucial, details of their operations.
One such detail is mill lining performance. Though seemingly minor when looking at the full processing circuit, liner underperformance can add up over time and significantly hinder the realisation of larger goals. Many sites tend to reorder the same liners that were initially selected when their mill was installed. However, as conditions such as ore characteristics or operating parameters change over time, liners may no longer match well to the application, and problems can surface.
The Importance of a Quick Response
Accordingly, plant engineers need to act promptly once they notice that a reduction in the output of a ball or SAG mill corresponds with the wear of the mill lining. Nonetheless, finding the root cause and the best possible solution can be a challenge.
Mining Business Africa learns from a team of experienced application engineers from Metso how to tackle this challenge. This could have
significant implications for mill throughput if left unattended.
Metso is a global provider of turnkey mill solutions, including equipment, relining machines, liners, and related services to diverse industries. The mill lining team has been consulting on mill lining-related matters for hundreds of projects worldwide, including Africa, for decades.
Drawing from this extensive experience, they share invaluable insights on optimising lining performance and addressing mill lining-related challenges. What is evident from their input is that optimising mill lining and grinding performance involves a sum of many integral parts, all working in sync.
Identifying Root Causes
At the outset, they underline the importance of identifying the root causes of common problems affecting mill production, which guides the approach to lining optimisation.
Håkan Ståhlbröst, Head of Application Support and Value Creation: Mill Lining, asserts that, in most cases, changes in operating parameters and production key performance indicators (KPIs) can affect the wear life of mill linings as
well as the actual liner performance. These KPIs include the charge level in the mill, the speed of the mill, the condition of the media, and the ore feed (percentage blend of feed materials) to the mill. Continuously monitoring these KPIs can provide data that makes it possible to anticipate how the wear will progress, and it is also the base for optimisation of future liner generations.
Based on the data gathered, the following elements should be considered to determine the design of the next set of liners:
1. Materials for Construction
During the design stage, Metso uses known data and optimises the liners according to that, Ståhlbröst explains. “To optimise liner wear life and get balance between different sections of the mill, the liner material can be redistributed so we move excess material from a low-wear area in the mill, making the liner thinner, and instead increase the height/thickness in a high-wear area. It is also possible to change the actual rubber compound or metallic alloy to better meet the wear life targets.”
2.
Lifter profile, height, quantity, and overall volume are the primary lining design variables that impact grinding performance. Consequently, Ståhlbröst advises, “It is desirable to have a wellbalanced lining where different parts wear out concurrently while retaining an efficient profile over the life of the lining.”
3. Fluctuations
Another factor to consider in liner design is that rock and ore are natural materials with variable properties. A lot of control and skill are needed to operate a comminution circuit in a reasonably steady state, meaning that both smaller and larger fluctuations must be anticipated.
Thus, a lining with a long service life that doesn’t infringe on the mill volume and matches the overall liner life with reline intervals is required. On how to create a suitable design, Ståhlbröst suggests, “It is important to monitor every single mill in detail regularly, capture and anticipate these changes, and optimise the
liner design accordingly. Typically, liner design constantly evolves over the life of the asset.”
Asked about determining the best liner material and geometry, Cameron Mather of Technical Sales Support (Consumables) for the African market explains that the starting point is understanding that every mill has unique lining requirements. He highlights customer KPIs, critical mill operating conditions, and actual mill design and drilling patterns as key factors in design configuration.
“The first step in design is aligning with customer KPIs, such as targeted mill throughput, expected liner wear life, mill availability, and scheduled maintenance planning. Additionally, understanding existing bottlenecks and
constraints and connecting these details with short- to medium-term mine planning are essential inputs,” Cameron explains.
Secondly, critical mill operating conditions are factored in. Usually, Metso uses a mill-lining questionnaire and other sources to gather this information from the miner. At this stage, any restrictions on current mill operations are explored, and correct answers to the following questions are sought: Is the mill weight limited or volume limited? Are there mill reline machine capacity limitations to consider? What is the mill ramp-up time following new lining installations?
The design, size, and features of the mill itself and the way it is drilled for liners can sometimes limit or affect the liner design options and to what
extent it can be optimised. Hence, when a new Metso mill is ordered, the team can consider not just the initial liner and the project mill design criteria but also future anticipated changes in process or service that might require a different liner design and layout. Liner interfaces are optimised for Metso mill reline machines to improve safety and relining times. Finally, the design of the equipment considers the best possible mill lining solutions to maximise the machine’s output and enhance operational efficiency.
The actual liner design and choice of liner material depend on several factors:
The type of mill, how it is operated, and the type of ore being processed greatly affect the selection of liners. Ståhlbröst explains, “Some mills require a lot of charge motion, promoting more impact breakage, while others need less charge trajectory as they rely more on attrition. This means that in one case, the liners must be more profiled, and vice versa.”
Chiming in, Nick Green, Vice President of Horizontal Mills, discusses the impact of the pulp discharge system. He notes that, in primary grinding mills, pulp discharge system configuration, wear life, design, and capacity are equally important elements of the grinding mill lining system design. “Where applicable, a pulp discharge system can be accommodated in the lining design for primary grinding mills with high volumetric throughput. In these types of mills, due to pulp discharge system capacity constraints, grinding efficiency may be reduced due to excessive slurry build-up in the grinding chamber, or the wear life of certain pulp discharge system parts may dictate shutdown intervals.” Overall, the manner of mill liner wear, or the design of the pulp discharge system, will influence how well the mill performs.
Similarly, when selecting liner materials, the specific application must be the primary consideration. Some materials are very abrasion-resistant but also brittle and not good at absorbing heavy impact.
Conversely, more impact-resistant materials might be less abrasion-resistant and deform more easily. To counter this, Ståhlbröst stresses that it is imperative to select the best option. “For example, if you are grinding hard gold ore that requires an abrasion-resistant material, but you are using a SAG mill with a lot of impact, we will select a material with high impact resistance to prevent liners from cracking and breaking but also with reasonable wear resistance,” he illustrates.
Sometimes, appropriate abrasion resistance can be achieved by mixing and applying different materials where their properties yield the best possible result. This is demonstrated by Metso’s Poly-Met liners, which consist of wear-resistant metallic inserts and flexible rubber. Another benefit of mixed-material liners is that they tend to retain a more efficient profile throughout the service life of the liner.
Ultimately, the mill’s owner makes the final decision, depending on their respective objectives and preferences.
Selecting and installing the liners, however, is only half the battle. Even more vital is ensuring that the mill’s output fully meets expectations. This involves meticulous steps to optimise wear liner life and better plan maintenance shutdowns.
Post-installation, Mather emphasises the significance of keeping mill operation within the mill lining design specifications to provide maximum grinding efficiency and optimal mill shell protection.
Ståhlbröst adds, “The mill liner and the way it wears, or the design of the discharge system, will influence how well the mill performs. Therefore, it is equally important to track the mill performance and evaluate if the liner can be further optimised to improve grinding efficiency.”
To attain optimal grinding efficiency, maintaining operating conditions is vital. These include charge level percentage, mill speed, feed rate and feed size, and grinding media size.
By and large, continuous performance and wear life monitoring of the installed mill lining should be standard practice to avoid unexpected problems, allow for better maintenance planning, and ensure timely parts sourcing. By measuring or scanning the liners, current and historical wear rates and wear behaviour can be
established.
Subsequently, the information gathered during regular inspections can be used to: better predict the remaining wear life of the liners; develop and optimise the next generation of liners; extend the service life to specific maintenance cycles; optimise liners to last a certain timeframe (to increase mill uptime); minimise weight and cost; and plan reline intervals.
To cap it all, Ståhlbröst underscores two fundamental truths for plant managers regarding design and liner wear life as they pursue liner optimisation.
“As ore properties and the process generally change over time, there is no such thing as the ultimate liner design. Therefore, performance should be continuously monitored to ensure that the liner design is always optimised for the current conditions.”
“We have all the technical prerequisites to monitor critical parameters in a mill. However, the mill conditions and the wear life of mill liners are affected by multiple factors, each of which can influence the outcome in several ways. If something small is changed upstream in production, it will affect several factors downstream, making the process very complex.” The long and short of it is that correct liner selection is a key factor in optimising grinding mill efficiency. However, with conditions always changing – optimisation needs to be viewed as a journey – and one best travelled with a trusted partner who can act as a guide along the way. Working with a partner who truly understands grinding inside and out, from the initial mill selection to the choice of liners, as well as understanding the best selection of Mill Reline Machine (MRM) and related services, can also pay dividends.
The adoption of AI and machine learning in design and optimisation has reshaped the design and optimisation of mill lining. At Metso, this is not exceptional.
Currently, Metso carries out grinding mill performance monitoring through remote service centres. For instance, with SPH-DEM, Metso can run 3D simulations much faster and more costeffectively.
Now, the company is exploring the possibilities of using AI to analyse large data sets and correlate that to liner wear history and performance.
Building on its extensive footprint of equipment, Weir works with customers to transition from reactive to prescriptive maintenance approaches to improve plant availability. Grant Potgieter explains that a focus on maintenance is not just to retain performance levels but to enhance them wherever possible.
Achieving the best return on their plant investment is a primary goal for mines, and partnering with OEMs like Weir is a strategic way to enhance equipment performance while reducing the total cost of ownership. The company is at the forefront of helping mines transition from reactive to prescriptive maintenance approaches, ensuring sustainable and safe operations through the optimisation of technology and equipment.
“We have an extensive footprint of equipment around Africa, and focus on adding further value to these assets through the correct maintenance strategy,” says Grant Potgieter, Strategic Services Manager at Weir. “This means a constant monitoring process, where we can track performance while looking for opportunities to raise our customers’ plant availability for greater productivity.”
Plant monitoring will invariably include a regular wear analysis of components, to monitor whether such wear is in line with expectations, explains Potgieter, as well as to predict future wear and component life. Analysing this wear, however, involves a considerable amount of data from the plant operation itself, such as ore characteristics and throughput.
“Here is it important to remember that each site will have its own variables, so it is
not possible to apply a standard template without understanding the specific plant,” he says. “Operating conditions may also change over time, so the assessment requires close collaboration between our team and the plant personnel on the mine.”
This allows a foundation of data to be established, on which to base the relevant corrective action, whether this is through technology, training or other interventions. Such action may be initially prompted by data that Weir picks up in its procurement process.
“Our years of experience in this market, and our careful documentation of component wear life, including historical and process information, allows us to estimate how long a certain component will last under predefined conditions,” he says. “By generating strategic reports from our procurement system, we can see if a customer is ordering components more frequently than they should be – suggesting that there is wear taking place.”
Technicians from Weir can then visit the site and examine the conditions more closely as part of a root cause analysis. This is most effectively done with a multidisciplinary team including process engineers and mechanical experts, to identify first-hand what the challenge is, and how best to address it.
Potgieter highlights the role of accurate measurement of equipment performance and condition, pointing to the fact that this is not always constant when conducted manually. To provide a platform that would overcome human error, Weir offers its own digital platform to harvest data continuously, accurately and objectively.
“It is significant that we developed our own system to do this, as we understand our equipment solutions better than anyone,” he explains. “Our digital platform allows us not only to gather and process the data from our equipment, but also generates recommendations which identify the actual cause of anomalies.”
As an example, if a sensor transmits a certain vibration signature from an item of equipment, a trained Weir Minerals condition monitoring expert will be able to verify system notifications.
While technology could be one part of the solution, he says, good communication is also crucial. To avoid any lack of communication through people working in silos, Weir arranges monthly quality meetings with customers – to ensure that all stakeholders are on board.
“This has proved to be a valuable way of getting all players involved and committed to the solutions that are agreed,” he says. “In this round table environment, everybody can be allocated a clear role, with tasks and responsibilities agreed in a transparent and accountable manner.”
This format also brings in all the necessary disciplines – from electrical and instrumentation through to mechanical and process – to reflect on the proposed solutions and ensure that the one selected is optimal.
“The key performance indicator that is shared by everyone in these meetings is cost optimisation, so this is really our focus with our discussion and solution,” he says. “We look holistically at safety, value and technology to ensure that whatever is spent on an intervention helps to lower the total cost of ownership.”
This often involves considerable change management, says Potgieter, as long term maintenance strategies may require mine personnel to adjust their procedures. Recognised for its expertise in its aftermarket services, Weir is frequently engaged by its customers to work on strategic shifts in their operating practices to optimise aspects such as equipment turnaround time and costs of refurbishment.
“We collaborate with customers as they adjust their own maintenance strategies,” he says. “To optimise the maintenance of rotables, for instance, we are able to provide service exchange units at regular intervals, as the customer removes a unit from service after a predetermined time.”
This avoids the higher cost of running a unit to failure before repairing, and reduces the risk of any unscheduled maintenance for breakdowns. As the OEM, Weir is then also able to refurbish equipment to their original standard, and offer the appropriate warranty.
SafeGauge technology enables remote monitoring and testing of machinery, reducing the need for workers to be near equipment during hazardous live testing procedures, minimising the risk of injury, including serious fluid injection injuries or crushing and pinching.
The strategic partnership between Booyco Electronics, a leader in proximity detection systems and safety solutions, and SafeGauge offers owners and operators of large mining, construction, forestry, agriculture and earthmoving equipment access to advanced wireless diagnostic tools designed to enhance safety and operational efficiency.
SafeGauge technology is renowned for enabling remote monitoring and testing of critical systems on heavy machinery without exposing workers to the dangerous conditions typically associated with live testing and equipment maintenance. Louis Venter, Area Sales Manager at Booyco Electronics, says that by allowing artisans to conduct tests and gather real-time data remotely, SafeGauge eliminates the need for workers to be in close proximity (line of fire) to large machines during potentially hazardous procedures. This innovation significantly reduces the risk of injury, creating a safer work environment across operations.
The SafeGauge range of equipment includes various specialised tools designed for different measurement needs. The PT (Pressure Transducer) Series is used to measure pressures in hydraulic and pneumatic systems, while the DI (Dial Indicator) Series is designed for measuring clearance, tolerance and wear on machine components. The TM (Tacho Meter) Series measures fan speeds and other rotating components, the LD (Laser Displacement) Series tracks wear on moving parts and the PR (Push Rod) Series is used to measure displacement between two fixed points.
Venter explains that all data collected by these tools can be processed through the Multitool Pro, which allows for real-time generation of reports and graphs. “With its builtin cloud connectivity, the system makes it easy to export or share data instantly, streamlining
operations and improving decision-making efficiency,” he adds.
Venter says that one of the most prominent benefits of SafeGauge equipment is the enhancement of artisan safety. “Heavy-duty machinery in the mining and construction industries can present significant risks during maintenance or diagnostic processes, particularly when it involves hydraulic systems or high-pressure environments,” he continues. “SafeGauge’s wireless system allows these tasks to be performed without workers needing to be near the equipment, mitigating the danger of exposure to moving parts or sudden pressure releases.”
In addition to safety improvements, SafeGauge contributes to increased operational efficiency. By enabling real-time monitoring and remote diagnostics, equipment issues can be identified and addressed faster, reducing unplanned downtime and preventing costly failures. This proactive maintenance approach
not only keeps operations running smoothly but also extends the life of key machinery components, minimising the need for expensive replacements.
“For businesses in mining, construction, forestry, agriculture and earthmoving, where operational continuity is crucial, SafeGauge’s ability to deliver timely diagnostics and maintenance insights is invaluable. It allows maintenance teams to perform their duties more effectively, ensuring equipment remains in optimal condition,” Venter says. “The result is higher productivity and lower maintenance costs, adding value to both day-to-day operations and long-term capital investment.”
“Through Booyco Electronics’ distribution of SafeGauge in Southern Africa, local operations now have access to this world class safety and efficiency solution, helping companies meet stringent safety standards and drive operational excellence in even the most demanding environments,” Venter concludes.
1200+ CONFERENCE DELEGATES
200+ EXHIBITING COMPANIES TH Sub Saharan Africa International Petroleum Exhibition and Conference 9
Join the largest gathering of energy, oil and gas industry professionals in sub-Saharan Africa to explore new opportunities, partnerships, and technologies driving the future of energy.
FEATURING
> Strategic and technical conferences: Delivered by leading voices from the oil, gas, and energy sectors.
50+ PARTICIPATING COUNTRIES
SAIPEC IS NOT JUST AN EVENT BUT A CATALYST FOR TANGIBLE PROGRESS IN THE ENERGY LANDSCAPE ACROSS AFRICA.
Ibrahima Talla Chief Operating Officer Invest in Africa, Senegal
11-13 FEBRUARY 2025
GENERAL ENQUIRIES
Mohamed Ahmed
Event Director, GEP Africa
mohamed@saipec-event.com
+20 10 0179 7986
PETAN MEMBERS
> Networking opportunities: Connect with global professionals and decision-makers.
> International exhibition: Showcasing the latest innovations in oil, gas, and energy.
CONTACT US today to discover more about the 2025 programme, sponsorship and participation options or to book your place on the ninth SAIPEC exhibition floor. Additional special participation rates are available to members of PETAN.
Kevin Nwanze
MNSE Executive Secretary
PETAN
kevin.nwanze@petan.org +234 705 999 222
As South Africa’s energy grid evolves gradually towards using more privately generated power, there are growing opportunities for companies employing steam turbines to boost revenue through electricity sales. Staying ahead of the trend, WEG Africa provides a full service offering to support this move.
Steam turbines represent mission critical equipment for a range of industries from sugar and paper to steel and petrochemicals, but there is now greater opportunity among these sectors to generate more energy to sell into the national grid.
Traditionally, companies using steam turbines have usually consumed all the energy they produce in their processes – with a range of benefits such as supply reliability and cost savings. As the country struggles to keep up with power demand, however, there are more opportunities for the private sector to produce excess electricity for sale into the grid.
According to Alastair Gerrard, Executive Energy Systems at WEG Africa, this trend is already advanced in Brazil – the home of holding company WEG. Many steam turbine users in Brazil have capitalised on these opportunities by increasing their boiler efficiency.
“While it may be common in South Africa’s
sugar industry, for example, to use medium pressure boilers, the Brazilian market uses high pressure boilers up to 140 bar – and gain significant efficiencies with these higher pressures,” says Gerrard. “This allows these sugar producers and other users to upgrade their facilities and considerably augment their revenues through the sale of electricity, while also paying off their capital investments much quicker.”
He points to the government’s strategic direction in establishing the National Transmission Company of South Africa, a key step in transforming the country’s electricity industry. This will open doors for more private companies to ‘export’ excess electricity into the grid, helping to stabilise supply and strengthen the foundation for economic growth.
“This has been successfully achieved in countries like Brazil, and it is exciting to see that we are making progress on this journey in South Africa,” he says. “We believe that WEG Africa has an important role to play in this endeavour –through our long experience in this field and our full service offering for steam turbine users.”
Cobus van Eeden, WEG Turbine Services Manager at WEG Africa, highlights that the company offers customers a turnkey capability. It sizes steam turbine solutions according to the specific operating parameters of the customer’s application, and supplies a bespoke thermal power system. The service also includes installing the machines, commissioning and ongoing after-sales servicing and maintenance.
“As an OEM of steam turbines, gearboxes and generators, we can even help customers to assess their current equipment – whether these
are WEG products or from other OEMs – and provide strategic options and recommendations,” says van Eeden. “In addition to our depth of engineering expertise for repairing such equipment, we can also analyse the potential for enhancing operational efficiency and increasing power output capability of the equipment.”
The company provides long term service level agreements, including contracts for preventative maintenance. WEG Africa also works with customers on their forward planning, which may include considering the transition to electricity exporting.
Gerrard points out that this approach is built on its commitment as an OEM to stand alongside customers throughout the lifecycle
of the equipment supplied. He notes that, while there has in the past been some acceptance of third-party support in this field, WEG Africa favours in-house OEM support for its solutions through service level agreements that give customers confidence in the total lifecycle cost of their purchase.
“Our field service technicians – active in many African countries and offshore – are on site with customers, developing a thorough understanding of their equipment and requirements,” he explains. “We integrate this information within our various functions to deliver the most valuable response and guidance on maintenance scheduling.”
Van Eeden outlines WEG Africa’s extensive engineering capability which includes machine servicing on customers’ sites – from gearboxes and turbines to generators and control systems. Equipment requiring more intensive work can be transported to the company’s 1,200 m2 workshop east of Johannesburg, which prides itself on quick turnarounds.
“Our facility includes full engineering capabilities, including the repair and manufacture of turbine bearings as well as the ability to conduct aftermarket engineering and optimising of numerous components,” he says. “We achieve this through our skilled machinists and technical staff, working with sophisticated scanning and engineering tools.”
In-house access to specialised facilities such as a labyrinth rolling machine for sealing strips, as well as a sandblasting booth for preparing components, further underpins the quality of workmanship and efficiency – thereby minimising downtime for customers.
Hardox ® wear plate exceeds expectations in productivity and service life for both open pit and underground mining.It protects equipment from sliding, impact, erosion, and corrosive wear in all environments, hot or freezing.
50%
Get more uptime and less maintenance by extending service life with 50% or more compared to an AR400 steel or…
…increase the equipment’s capacity by reducing its weight 20% or more with thinner dimensions of harder and stronger Hardox ® wear plate. 20%
100%
Experience more reliable fabrication and less waste in production through guaranteed flatness, thickness, and bending properties, covering all Hardox ® wear plate products.