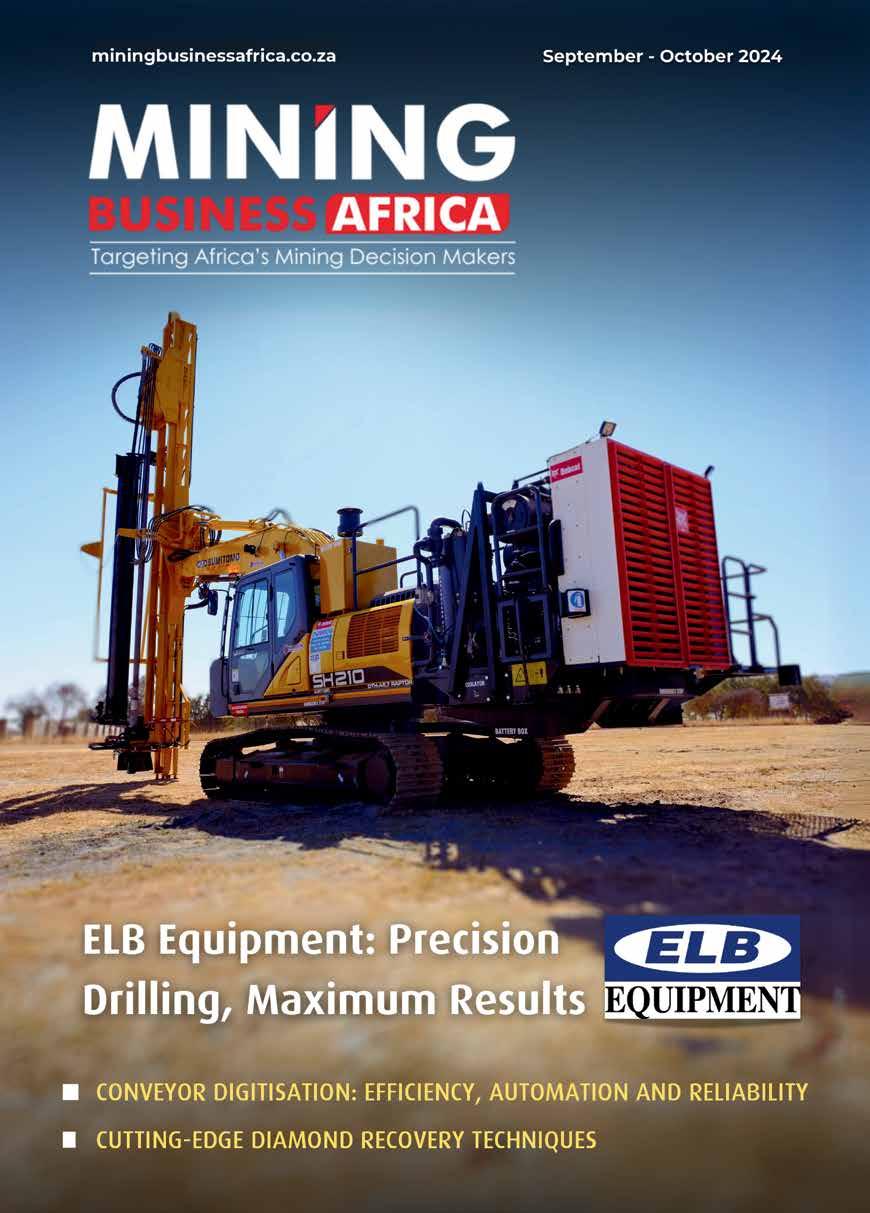
3-6 February 2025
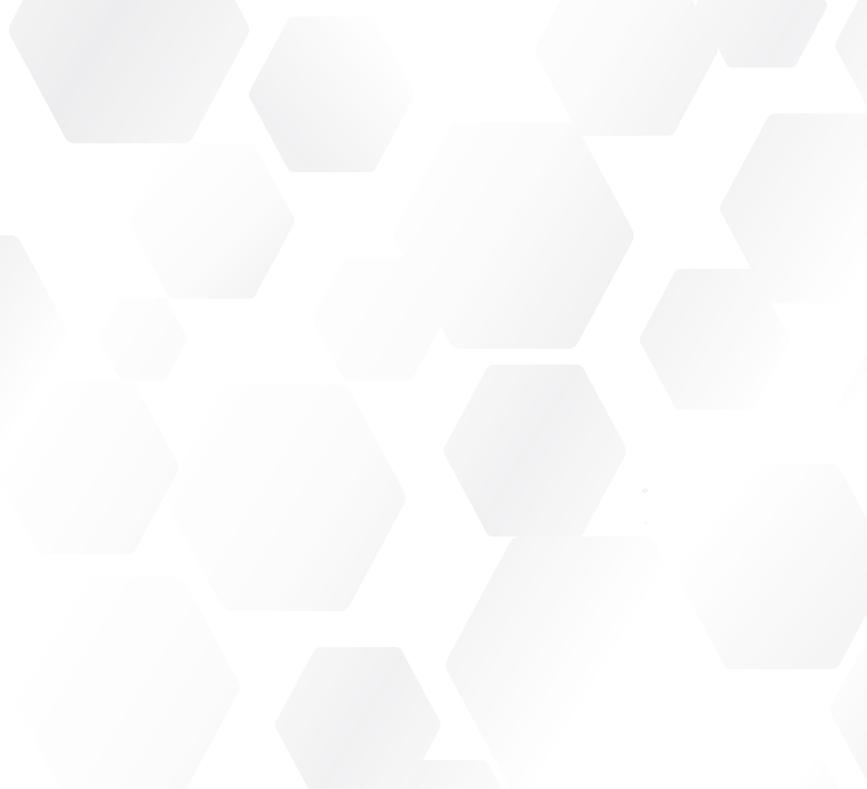
Mining Indaba: Creating opportunities for African miners and laying the groundwork for a greener, more inclusive future.
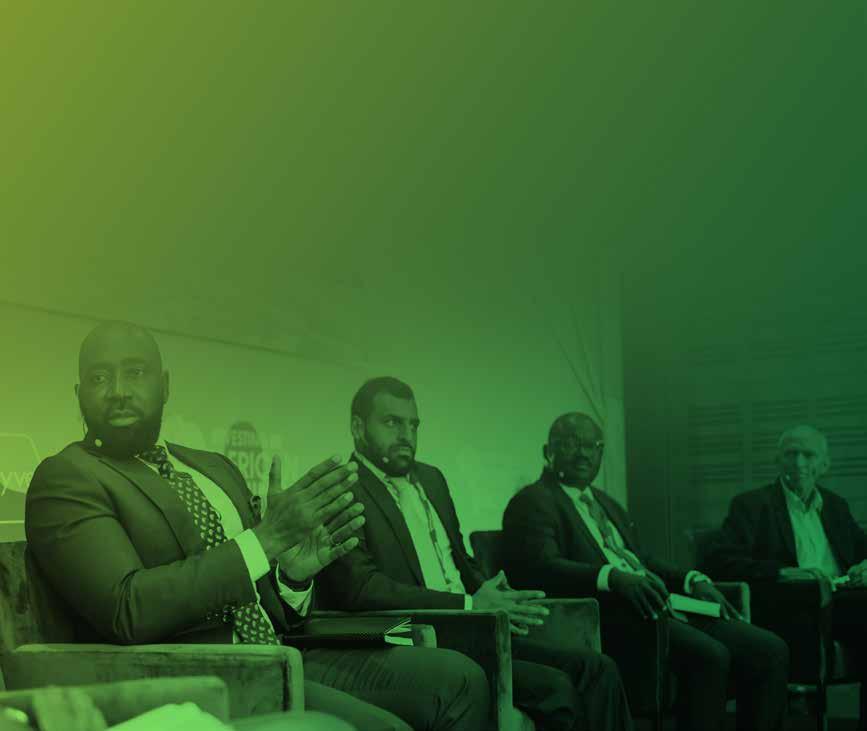
3-6 February 2025
Mining Indaba: Creating opportunities for African miners and laying the groundwork for a greener, more inclusive future.
• Implementing innovative technological solutions for enhanced operational efficiency.
• Developing new standards for sustainable and innovative mining practices.
• Increasing resource efficiency and minimise waste.
• Contributing to productivity and health safety while reducing the environmental impact.
CTICC, Cape Town For more information contact:
Cover Image: Courtesy
COVER STORY: PG 02
Drill Rigs Engineered for Power, Precision, and Durability
Tough and rugged Sumitomo excavators are proving to be the ideal platform for Hyperion Drilling and Manufacturing to convert into drill rigs that are being used across the continent in a wide array of applications. The excavators are available from ELB Equipment.
Editor
Nick Barnes
editor@miningbusinessafrica.co.za
+27 10 055 3356
Web/Sub-Editors
Jimmy Swira
Jimmy@miningbusinessafrica.co.za
+ 27 10 055 3356
Anita Anyango anyangoanita18@gmail.com
Contributing Writers
Chantelle C.
chantellec@miningbusinessafrica.co.za
+ 27 10 055 3356
Susan M.
susanm@miningbusinessafrica.co.za
Sales and Marketing
Winnie Sentabire
winnie@miningbusinessafrica.co.za
+27 83 530 6832 | +27 10 055 3356
Angeline Ntobeng
angien@miningbusinessafrica.co.za
+ 27 078 322 5938
+ 27 010 055 3356
Accounts
Precious Chirunga
accounts@miningbusinessafrica.co.za
+ 27 10 055 3356
In the green movement, the mention of the word ‘coal’ causes some proponents of clean energy (or anything related) to plug their ears as if they had heard a swear word from gangster rap lyrics. Such is their zeal to transition the world toward a green utopia. Well and good.
However, like other idealists who fight for various causes—ostensibly noble—what is often lost on green extremists is the tendency to overlook certain realities. It is no coincidence that many of the militant gatekeepers of these movements reside in Western countries. These nations have achieved unprecedented development and accumulated wealth using filthy coal since the Industrial Revolution in the late nineteenth century. Thus, they are the primary culprits of global warming. Yet, disingenuously, they are imposing punitive conditions on how coal should be used and replacing it with cleaner energy alternatives.
African countries account for just two per cent of global emissions. So, it’s not hard to guess who should be at the forefront of cutting coal consumption.
Moreover, in developing countries, nearly one billion people lack access to clean energy. Currently, the global cost of clean energy is said to be falling and becoming affordable in Western nations. Still, this remains a luxury in African countries, where the majority struggle to make ends meet. Consequently, coal will remain relevant in meeting their energy needs as they diversify their energy sources.
Nick Barnes editor@miningbusinessafrica.com
Art Director/Layout
Augustine Ombwa
Arobia Creative Consultancy
austin@arobia.co.ke
+254 772 187 334
Circulation/Sales info@miningbusinessafrica.co.za
+ 27 10 055 3356
Published By Media Icon (Pty) Ltd
Tough and rugged Sumitomo excavators are proving to be the ideal platform for Hyperion Drilling and Manufacturing to convert into drill rigs that are being used across the continent in a wide array of applications. The excavators are available from ELB Equipment.
Hyperion Drilling and Manufacturing is taking full advantage of the Sumitomo excavators’ power, precision, and durability to produce high quality excavator-based drill rigs for its customers. Thus far, the company has produced 19 Sumitomo-based drill rigs, with firm orders for several more in the pipeline.
Keon Kardolus of ELB Equipment, distributor of Sumitomo equipment in southern Africa, says, in the right application, the excavator-based drill rig is a game-changer, as it is able to slew from centre to left and right rather than in a straight line as is the case with traditional drill rigs. The extendable boom also allows the mast to be positioned closer to the wall or bench, which contributes to improved safety of operators to avoid falling rock or collapsing ground underfoot. Simultaneously, the cost of the excavator-based drill rigs is less expensive while boasting comparable results in certain applications.
Hyperion managing director, Kenny Truter, adds, “Sumitomo excavators are rugged and tough machines. The use of one of the world’s toughest types of excavators is sure to provide tens of thousands of hours of trouble-free drilling. In fact, all of the Sumitomo-based machines that we have produced over the last two decades are either still in use or, in rare instances, up in remote parts of Africa, have been converted back to excavators after the drilling requirement was over.
“That says a lot about the quality of the excavator platform as well as our locally manufactured Raptor series of DTH drills that are designed and mounted to the excavators according to our customers’ requirements and preferences. For example, the down-the-hole type drills can be specified in assorted sizes for holes up to 600 mm and even beyond if required. They can also be specified to incorporate cable, chain, or cylinder mast systems in accordance with companies’ preferences as well as operating procedures and collaborate with the excavator’s own hydraulics.
“They are simple to operate from within or outside the cab through a panel mount and pilot valves outside on the front of the excavator. The standard mast is 6 m high and works with 5 m rods, with options for 7 m masts that carry 6 m rods also available. The drills are technically advanced with control, stabilisation, dust suppression, and enough power to exert 4.5 tons of pushdown at 180 bar and 7 tons of pullback. This is enough to deliver more than 20 000 m drilled per month for some contractors,” says Kenny.
He adds that the rigs are designed to fit a 20–30-ton excavator according to customer preferences. Once the job is done on a site, the rig fits easily onto a standard flatbed truck. The placement of the compressor is at the back of the machine, with cleverly placed diesel and water tanks situated on the deck of the machine to allow thinner dimensions. Along with a fold-flat boom and mast design, the drill rigs can be transported by road without escorts, which simplifies the transport of the machines.
The latest drill rig off Hyperion production line is based on the potent Sumitomo SH210-6 excavator platform and is
destined to go into service with a major drilling contractor. It is expected to deliver unsurpassed power and economy in the Japanese manufacturer’s usual rugged and reliable package.
A number of groundbreaking innovations in Sumitomo’s fuel efficiency technology contribute to fuel savings of over 14% compared to the already efficient previous model. Additionally, handy productivity features that also protect the machine, such as heat circuit cushion valves on the boom, swing relief control, slope travel assist control, and in-cab pressure control, contribute to the ease of use and efficiency of the machine.
The Sumitomo platform retains its easy-to-maintain configurations and easy-to-access maintenance points with reduced grease requirements due to the quality of materials used in the manufacture of the Sumitomo machines.
“Hyperion Drilling and Manufacturing is our top customer. ELB Equipment works closely with Kenny and his team to ensure that the equipment performs optimally at all times. We also ensure that the required tests are performed in accordance with Sumitomo in Japan in order to maintain all relevant under carriage, boom, and operations warranties on each of the Hyperion-built drill rigs,” says ELB Equipment Earthmoving and Construction area sales manager, Devon Harris.
In full agreement, Kenny adds that this kind of cooperation and involvement of OEM manufacturers for every component of the rig, including the excavator platform, compressor, and locally made Raptor rig, sets the company and its custom-manufactured drills apart in an environment that requires the highest assurance of quality, product ability, and safety. “We leave nothing to chance, as a trusted partner, ELB Equipment is with us every step of the way.”
A number of groundbreaking innovations in Sumitomo’s fuel efficiency technology contribute to fuel savings of over 14% compared to the already efficient previous model.
Digitisation has simplified the tedious task of conveyor system management, resulting in tangible benefits. These are primarily in the form of increased efficiency, reduced downtime, and improved safety.
Availability, efficiency, and safety are the most desired aspects of conveyor performance systems in contemporary mining. However, due to exposure to extreme temperatures and other adverse conditions, achieving these goals using conventional techniques can be challenging.
Digitisation
Fortunately, technological advances provide an innovative solution. Increasingly, digitisation is emerging as a tool for optimising conveyor system performance. Results from mining projects, where digitisation is incorporated in conveyor design, show marked improvement. Typically, digitisation involves the integration of automation, robotics, and artificial intelligence.
Digital twin
As part of digitisation, a digital twin, a virtual replica of the conveyor system, is created.
Florian Huthmann of ThyssenKrupp Mining Technologies, who has been involved in conveyor digitisation projects and has done extensive research in the area, has documented his findings (The digitisation of the conveyor).
He offers a more precise description of a digital twin: “The digital twin refers to a complete digital representation of a physical asset. It includes its design specifications and mathematical models, as well as as-built and operational data unique to the specific asset it represents. With the latter, it is ensured that design and reality are in scope.”
Monitoring, analysing, and predicting
Basically, a digital twin can help establish whether the conveyor system operates within design specifications. Through real-time data
and insights from the digital twin, the plant engineer can monitor, analyse, and predict the performance of the belt conveyor in real-time. In this way, ultimately, it can facilitate the following:
Digital twins can help determine whether optimal tonnage can be attained with the existing design or if the system must be modified. Huthmann explains where digital twins would be key: “Conveyors may be over-designed for their intended use, and rather than investing in what is perceived to be a necessary and costly modification, digital twins allow for tests and optimisation.” He cites the example where Thyssenkrupp’s digital twin helped a customer handle 30% more throughput without mechanical modification.
A digital twin allows for early anomaly detection in the conveyor’s performance. With the data gathered from this exercise, a predictive maintenance strategy can be mapped out. “The 24/7 monitoring of a conveyor system can easily pay for itself, detecting faulty parts, incorrect installation of spare parts, or rare black swan events,” Huthmann states, ultimately timeconsuming and costly or catastrophic failures can be avoided.
Besides, where failure has occurred, a digital reconstruction of a conveyor system reconstruction can allow for a thorough rootcause analysis.
A digital twin can highlight operational variables that must be changed to enhance safety.
iv. Reducing OPEX
Energy accounts for one of the highest percentages of conveyor systems’ OPEX. By allowing for an increase in the conveyor system’s efficiency, a digital twin could reduce the power draw. This could contribute to a significant reduction in OPEX. What’s more, there could be a wide scope of other gains.
Revolutionalising conveyor management
By and large, digitisation is revolutionising conveyor systems management in ways previously deemed impossible. With Industry 4.0 becoming part of the machinery DNA, digitisation will open many opportunities and enhance numerous key performance metrics. Indeed, there are enormous dividends from the adoption of digitisation.
Typically, a conveyor digital twin has the following components:
1. Software
The first is software, which accommodates critical parameters such as ambient temperature and topography. For existing conveyors, these are drive power, pulleys, belt length and width, pulleys, etc.
2. Data
The second one is managing data. Data is obtained in two ways: either from a single data dump for once-off health checks or live data from the asset itself from the conveyor. In this context, data includes load from belt scales or power draw.
3. Calibration
The third one is calibration. The digital twin is calibrated to ensure that it is the same model as the physical conveyor. For instance, projected power demand is equal to the physical system.
4. Evaluation
Finally, once good to go, the digital twin can be used to evaluate whether the conveyor system is operating according to expectations.
Don’t miss the world’s premier mineral exploration and mining convention
2-5 5
PROSPECTORS & DEVELOPERS ASSOCIATION OF CANADA
Up to 30,0 00 attendees 700+ hours of programming
1,100+ exhibitors Delegates from 130+ countries
Meet investors & senior executives Unrivaled networking pdac.ca/convention | Toronto, Canada
MBA: We were caught by surprise by the branding of Siemens’ drive technologies business portfolio to Innomotics, when one thought there was no need to fix what’s not broken. What necessitated this move?
Innomotics, an independent company recently spun off from Siemens AG, made a strong impression at the recent 2024 Electra Mining event, where its advanced drive solutions received widespread acclaim. Following the event, Tim Walwyn, CEO of Innomotics South Africa, spoke with MINING BUSINESS AFRICA about the company’s strategy to leverage digitisation and deliver industryleading, customised drive solutions across various sectors.
TW: Innomotics is a way for us to really focus on innovation of our drive technology portfolio on top of the legacy developed by Siemens over the course of more than 150 years. As a standalone company, we have the freedom to be more agile and responsive to customer needs and evolving market trends, allowing us to focus on industries for whom motor and drive systems are key performance drivers, such as mining, utilities, oil and gas, and manufacturing.
MBA: How do you see industries benefiting from Innomotics ‘niche’ drive technologies speciality?
Walwyn emphasized that Innomotics represents a combination of innovation and engineering excellence, built on decades of experience in electric motor and drives. The company is dedicated to bringing cutting-edge technology and reliability to its clients, helping industries enhance operational efficiency through tailored digital solutions.
TW: For our customers, our technology focus means that we bring in-depth process and application know-how to the table. In conjunction with our broad range of products, this means we can partner with customers to develop the best possible solution to every challenge. Our innovations lead to concrete performance advantages such as higher power density, greater availability, reduced emissions, and more optimal control. Increasingly important are the insights gained from smart products complemented by our INSPIRE IQ digital monitoring system, and even end-to-end digitalisation for the mining value chain through our DIGIMINE portfolio.
MBA: What opportunities has Innomotics identified as mining companies and other industries embrace the digitisation of conveyor automation?
TW: As a full-service solution provider to the mining industry, Innomotics delivers electrical, drive-train, automation, and digitalisation solutions for mining plants, which gives us a unique insight into the performance of conveyor systems, and opportunities for their digitalisation. Starting with the equipment, digital technologies enable us to monitor the electrical and mechanical performance of conveyor drive trains. At the next level, our process automation systems incorporate dedicated libraries for efficient operation of conveyor control and safety. We work closely with specialist suppliers of conveyor instrumentation to ensure that all information required for effective automation is available.
Of course, all of the data derived from these systems can be used as a basis for condition monitoring as a basic digital application. From our perspective, what is more interesting is that by building on this robust electrical and automation layer, we are able to derive concrete process optimisations through our DIGIMINE Digital Twin solution.
Digital Twin combines real-time data acquired from the operational conveyor system with advanced modelling of the
physical performance of the machine itself and an understanding of up and downstream processes. Through this holistic view, it is possible to optimise not only the performance of an individual conveyor, but of the complete material flow system.
Examples of possible improvements include reduction of blockages, more consistent material flow into downstream processes, and increased throughput without the need for major mechanical changes.
MBA: Conveyor failure impacts productivity and maintenance costs. How does your IIoT digitisation, Inspire IQ, help address this challenge?
TW: In addition to our DIGIMINE Digital Twin offering for conveyor systems, Innomotics enables detailed IIoT monitoring of key drive system components through INSPIRE IQ, our platform for digital enhancement of motors and drives. The INSPIRE IQ system collates and analyses multiple signals from a drive system in order to detect any change in the operational conditions that may signal a potential failure before it happens. Data acquired includes mechanical and electrical parameters, preventive
maintenance actions, and environmental conditions.
This helps our customer service teams to advise customers of work that can be carried out during planned shutdowns and critical spares that need to be available. In a worst case, we are able to respond rapidly in case of a failure due to the system-generated alerts. This approach has directly prevented downtime incidents at several mining sites around the world.
MBA: Could you take us through the precise steps of what conveyor drive digitisation would entail for a greenfield mining project?
TW: Greenfield projects have the advantage that design alternatives can be explored in order to identify the best option at relatively low cost. Our Digital Twin solution can be used as a simulation tool to assist in the optimisation process. It is important to build in the complete span of technologies that will allow for effective digitalisation from the outset in order to save costs down the line. A major advantage to implementing digitalisation during the engineering phase is that the availability of the Digital Twin system can dramatically improve commissioning performance and reduce ramp-up time, which can have a significant bottom-line impact on projects.
MBA: What about a brownfield project aiming to retrofit its drive systems?
TW: While each brownfield site presents its own challenge, there is still significant scope for digitalisation. We often recommend an incremental approach in these cases. For example, installation of Inspire IQ monitoring technology on the drive train can lead to improved availability with relatively low investment.
As a next step, the Digital Twin system can be applied to particular problematic machines or plant sections in order to improve the performance of obvious bottlenecks.
Finally, the system can be expanded to cover the entire plant scope in order to assist operators to realise continuous performance improvements.
MBA: Ultimately, what would a mine benefit from engaging Innomotics as a conveyor drive digitisation partner?
TW: Innomotics is unique in the scope of our offering, from drive systems, through automation to digitalisation, so we can provide a truly integrated solution.
Our Solutions engineering teams around the world have decades of experience with conveyor systems of all types based on delivered projects as well as close cooperation with major conveyor OEM’s.
Our drive products, combined with INSPIRE IQ, offer the greatest insight into equipment operating status for predictive monitoring.
Our proven DIGIMINE Digital Twin solution goes beyond traditional condition monitoring applications to support operators with concrete recommendations to improve the performance of the entire conveyor line.
MBA: Is there anything you can tell mining companies about the role of Innomotics?
TW: The Innomotics regional office in Midrand supports customers across Sub Saharan Africa in all industries with the complete range of Innomotics motors, geared motors, and Medium Voltage Drives. Our local operations include a brand new geared motor assembly facility in Midrand and a highly experienced engineering team focused on electrification, automation and digitalisation of every part of the mining value chain. We are very excited for the future of our innovative new brand, and equally proud of our long Siemens heritage.
To learn more on Innomotics visit: https://www.innomotics.co.za/
X-ray technology (XRT) offers more than just efficient recovery—it lowers operating costs and leads to the discovery of high-quality, high-value stones.
Increasing OPEX, regulatory compliance bottlenecks, and the increasing shift to underground operations – together with its associated high costs - are common challenges encountered in the contemporary mining environment. The diamond mining sector is not an exception to these trends.
A noticeable challenge unique to diamond mining is reduction of miner product output. Consequently, this has necessitated the urgent need to ‘do more with less’.
For this reason, the objective of contemporary diamond mining is recovering large, high-quality kimberlite diamonds at the highest sorting efficiency with the highest
throughput possible.
And it must be added that the earlier the process is carried in the flow-sheet the better. As highlighted in SAIMM review1: “Earlier recovery of diamonds from the system lessens the exposure of diamond-bearing ore to additional materials handling, pumping, and/or crushing, which has been known to damage or even break diamonds and decrease revenue.”
However, this is challenging to achieve with conventional diamond recovery techniques, inherent with their limitations.
Conventional techniques
There are several conventional methods at the disposal of diamond producers. Commonly
in use are near-infrared (NIR) and X-ray luminescence (XRL), and traditional XRL sorters.
While these techniques serve the purpose, they come with inherent limitations. For instance, NIR and XRL are dependent on visible colour difference or clean, reflective particle surfaces, while traditional XRL sorters have low detection rate for type II diamonds.
In a stark contrast, XRT technology has a significantly higher detection rate. This is the rule of thumb: the success of detection with X-ray transmission (XRT) technology depends on the difference in atomic numbers between the materials being separated.
Unsurprisingly, X-ray transmission has emerged as the preferred recovery technology in diamond flow sheet in applications, specifically in recovery and final product grading across all size ranges. Applications of X-ray transmission (XRT) sorting are found across kimberlite, alluvial, and marine operations.
In comparison to other methods, the advantage of XRT is that it delivers considerably lower percentage yield, comparatively lower running costs with respect to consumables and utilities. What’s more, even at high feed rates, it leaves minimum gangue materials.
Record recoveries that are making headlines attest the effectiveness of XRT. Isn’t it incredible that most of the discoveries are of stones above 1000 carats?
With anticipation, with new breakthroughs from R&D initiatives, enhanced by AI and deep learning, XRT technologies will only get better, unearthing high value diamonds.
1. Pioneering large diamond recovery at Karowe diamond mine – Journal of the Southern African Institute of Mining and Metalurgy Volume 116 – 2016
TOMRA Mining XRT technology recovers exceptional 2,492-carat diamond quickly followed by another record-breaking 1,094-carat from Lucara’s Karowe mine
One of the largest rough diamonds in recorded history, a 2,492-carat stone, was recovered last August by Lucara Diamond Corp. with TOMRA X-Ray Transmission (XRT) technology at the Karowe Mine in Botswana. This extraordinary diamond is the latest of many impressive record-breaking recoveries achieved at the mine’s Mega Diamond Recovery Plant since the installation of the two TOMRA COM XRT 1200 / D 2.0 sorters in 2017, when Lucara Diamond Corp. truly initiated a revolutionary transformation in the diamond mining industry’s recovery process. By integrating XRT early into the flowsheet, post primary crushing, it is possible to recover liberated and free exceptionally large diamonds earlier in the process, thereby extracting revenue from the flowsheet faster and safeguarding diamond value from potential downstream damage or breakage. The 2,492-carat stone is historically the secondlargest diamond ever discovered, following the 3,106.75-carat Cullinan diamond found in 1905. However, it is the largest diamond ever recovered directly from run-of-mine ore. It was followed, just a few weeks later, by a 1,094-carat diamond – the sixth rough diamond weighing more than 1,000 carats to be recovered at the mine, and one of the top 10 largest diamonds in history.
“We at TOMRA Mining are immensely proud to be part of Lucara’s incredible journey,” says Albert du Preez, Head of TOMRA Mining. “Our XRT technology has played a pivotal role in their historic recoveries, including the 1,758-carat Sewelô and the 1,109-carat Lesedi La Rona diamonds. These milestones are a testament to the power of innovation and collaboration in the mining industry. This achievement underscores the exceptional capabilities of our XRT technology and the dedication of our team. We are committed to supporting Lucara, and ensuring they continue to achieve remarkable success.”
“TOMRA’s XRT technology has transformed diamond recovery, achieving unprecedented results and breaking records,” comments Corné de Jager, Diamond Segment Manager TOMRA Mining. “Fifteen of the top 23 largest diamonds, bigger than 400 carats, recovered since TOMRA
Our XRT technology has played a pivotal role in their historic recoveries, including the 1,758-carat Sewelô and the 1,109-carat Lesedi La Rona diamonds.
XRT bulk concentration installations commenced fully in the diamond industry in 2014, were recovered with our technology – thirteen of them at Lucara’s Karowe Mine, which holds recordbreaking finds in various categories. In fact, our TOMRA XRT technology has contributed to the recovery of 7 of the top 10 largest diamonds in history at the Karowe Mine.”
The exceptional find at Lucara’s Karowe mine was swiftly followed by the announcement of another remarkable recovery with TOMRA’s XRT technology in Sierra Leone. The 391.45-carat diamond was unearthed at the Meya Mine in Kono District. In 2017 the famous and historic Type IIa 476.7-carat Meya Prosperity was also recovered with TOMRA’s XRT.
TOMRA’s unique complete diamond recovery solution
TOMRA’s innovative high-capacity XRT technology is a true game-changer in bulk diamond concentration. The extremely precise detection and ejection of exceptionally large and even the smaller particle sizes, and proprietary image processing deliver 100% detection in the specified size range irrespective of luminescence or surface coating, with a guaranteed diamond recovery rate above 98% and remarkably low yields. In addition,
the unique TOMRA COM XRT 300 / FR final recovery sorter featuring TOMRA’s proprietary ultra-high resolution sensor technology and precise ejection has revolutionised final recovery processing to efficiently deliver an ultra-high diamond-by-weight concentrate, thereby contributing to improved & focused downstream security and reduced hand sorting.
Today, TOMRA is the only manufacturer to offer a full recovery service from 2mm to 100mm with a flowsheet covering the entire process –from high-capacity Concentration (+4-100mm) to Final Recovery and Sort House applications (+2-32mm), which includes a detailed analysis of customers’ requirements and the collaborative development of an XRT technology-based flowsheet. With its holistic approach and XRT technology, TOMRA is helping diamond operations in Africa, Canada, Brazil and other countries around the world to maximize recovery while optimizing costs – with the additional benefit of a smaller environmental footprint.
TOMRA’s XRT technology has delivered consistently exceptional performances in a number of key diamond operations. At Gem Diamond’s Letšeng Diamond Mine in Lesotho, shortly after commissioning a TOMRA XRT
sorter in 2018, TOMRA’s XRT technology recovered the biggest stone ever seen at the mine, the 910-carat Lesotho Legend. TOMRA’s
XRT technology delivered an effective solution for coarse fractions in the mining operation’s historical tailings dumps, recovering 15 times the initial investment in 4 years. The Mothae mine in Lesotho, known to produce highvalue diamonds, is also using TOMRA XRT technology combined with the TOMRA Insight digital platform and TOMRA ACT user interface to recover exceptional diamonds from the mine with high sorting efficiency and high throughput, benefiting from lower operating costs. At Mothae, twelve +100-carat diamonds were recovered by TOMRA XRT with an average size of 153-carat/stone.
At Lucapa Diamond Company’s Lulo Alluvial Mine in Angola, also known to produce premium value diamonds, Lulo’s second highest value 227-carat Type IIa diamond was recovered by TOMRA XRT. These are examples of the outstanding results diamond mines are achieving with TOMRA’s cutting-edge sorting technology. These significant recoveries contribute to the development of the diamond industry in the countries where they occur, which in turn can bring positive socio-economic benefits by enabling funding in areas such as education and healthcare.
Key benefits:
• 100% diamond detection in specified size range irrespective of luminescence or surface coating
• High concentration factors
• Low power and operational cost per ton
With our sensor-based sorting systems, we can help you achieve maximum value from your input, and make sure that nothing is lost in the process.
You don’t have to take our word for it, our results speak for themselves: most recently with the recovery of one of the biggest diamonds in history.
Schurco Slurry’s pumps are specially designed to meet the contemporary demands of diamond processing and beneficiation plants globally. They are available in various specifications to suit a wide range of applications in both kimberlite ore and alluvial gravel deposits across Southern Africa.
The diamond mining industry faces challenges such as resource depletion, increasing operational costs, and competition from synthetically made diamonds. And so, in response, heavy-duty centrifugal slurry pump manufacturer Schurco Slurry is expanding its product range to include comprehensive dewatering pump solutions, designed to meet a wide spectrum of applications in the mining sector.
Adaptation key
“The future of diamond mining will depend on how well the industry can adapt to new challenges and opportunities,” says Schurco pump applications and project manager, Marc Young, noting that Schurco Slurry, in particular, is supporting this adaptation through continuous innovation and by providing high-quality products for customers.
He adds that the future of diamond mining in South Africa, and globally, will depend on technological advancements and sustainable practices and that Schurco Slurry is therefore poised to play a crucial role in the evolving landscape, especially from a pump perspective.
“Our goal is to be the best friend of diamond processing and beneficiation, just as diamonds are known to be ‘a girl’s best friend’,” says Young.
As such, he states that Schurco Slurry is “committed to delivering the best solutions to customers and supporting the industry’s journey towards a more sustainable and prosperous future”.
He explains that Schurco Slurry’s experience in the diamond mining industry is evident in the company’s specialised pump offerings.
The company supplies a variety of pumps to diamond processing and beneficiation plants globally, including the S-Series – lined horizontal pumps, U-Series – unlined horizontal pumps, Z-Series – gravel pumps, V-Series – vertical spindle pumps, and D-Series – dual-discharge vertical spindle pumps.
These pumps are engineered to handle the aggressive nature of diamond mining processes, providing reliable and efficient performance across different stages of diamond extraction, explains Young.
“Our pumps are designed with the most rugged materials available. We understand the harsh conditions in diamond mining and have developed solutions that can withstand these environments while ensuring maximum operational efficiency,” he points out.
Young further highlights Schurco Slurry’s commitment to understanding and addressing the specific needs of end-users in the diamond mining sector.
In this regard, the company collaborates closely with process design engineers and mining operators to develop pump ranges and materials customised to the industry’s rigorous demands.
This collaborative approach ensures that Schurco Slurry’s products not only meet but exceed, the performance and reliability expectations of the mining industry, he explains.
“By working directly with end-users, we can design pumps that address their unique challenges,” explains Young, noting that this hands-on approach enables Schurco Slurry to deliver products that are not only reliable
but also perfectly suited to their specific applications.
Schurco Slurry maintains a large inventory of pumps and parts globally, ensuring quick availability and interchangeability with premium slurry pump parts. This global distribution network is supported by comprehensive refurbishing programmes and bearing assembly exchange or repair options, which reduce downtime and increase operational efficiency for mining operations.
In regions like South Africa’s Northern Cape province, Lesotho and Botswana, kimberlite ore – typically found in volcanic pipes – requires specialised processing techniques. Hence, Schurco Slurry’s S-, L- and U-Series pumps are commonly used in kimberlite processing plants, which use crushing processes and dense media separation to extract diamonds.
The Z-Series pumps, with their larger passages and reduced internal velocities, are particularly effective in minimising diamond breakage – a critical consideration given that about 30% of diamond breakage occurs within a pump.
“Our Z-Series pumps are designed to reduce particle velocities, which is crucial in minimising
“Our pumps are designed with the most rugged materials available. We understand the harsh conditions in diamond mining and have developed solutions that can withstand these environments while ensuring maximum operational efficiency.” Marc Young
diamond breakage,” notes Young. This design feature not only protects the valuable diamonds but also extends pump life.
In contrast, some South African West Coast diamond mining operations, which primarily deal with alluvial gravel deposits, rely on Schurco Slurry’s U- and Z-Series pumps, he highlights. These pumps are designed for ease of maintenance and to reduce the risk of diamond loss during routine operations.
The U-Series pumps feature high-efficiency, non-clog impeller designs and Schurco Slurry
expeller seals that ensure zero leakage, making them ideal for the abrasive and corrosive conditions typical of alluvial diamond mining.
“The U-Series pumps are favoured in alluvial plants for their ease of maintenance and reliability. They are built to handle the tough conditions and ensure consistent performance,” says Young.
Further, he adds that Schurco Slurry’s technological innovations are central to enhancing the efficiency and productivity of diamond mining operations.
The Z-Series pumps, for example, enable the passage of large particles at low operating speeds, reducing damage to diamonds and extending pump life. This design not only improves operational efficiency but also reduces costs associated with diamond breakage and pump maintenance.
The company’s commitment to research and development ensures that all pump parts are rigorously engineered and performance-tested to meet the highest equipment manufacturing standards. This dedication to quality control and continuous improvement translates into reliable and cost-effective solutions for the diamond mining industry, he concludes.
Pilot Crushtec International is introducing its new generation TwisterTrac mobile vertical shaft impact (VSI) crusher powered by a Stage V diesel engine. The move to a motor that complies with EU Stage V regulations unlocks new export prospects in highly regulated markets such as Europe and North America.
Designed and manufactured in South Africa by Pilot Crushtec, the TwisterTrac VS350E VSI has over the years gained popularity in export destinations such as Australia and New Zealand. To provide context, since 2013, Pilot Crushtec has sold in excess of 50 units with almost 90% of these deployed into export markets.
To further grow its export sales, the company has become one of the first South African original equipment manufacturers to build a Stage V engine powered machine. Previously driven by a Tier 3 Volvo TAD1651GE engine, the new TwisterTrac VS350E VSI now comes with a Stage V Volvo TAD1382GE motor, allowing Pilot Crushtec to offer the legendary tracked VSI in emissions-regulated markets, in particular Europe and North America, as mentioned above.
“The Stage V project has been in the pipeline for a while as part of our export focus. Our machine development strategy has always placed greater emphasis on offering exportable products and this move allows us to unlock new markets and grow our export sales. We are excited by the prospects of growth in emission-controlled markets such as Europe and North America. In
addition, this project speaks to customers in some of our traditional markets such as Australia, where there is a strong focus on adopting high emissions standards,” explains Sandro Scherf, CEO of Pilot Crushtec.
Jorge Abelho, Director Technical Support at Pilot Crushtec, says the company opted for the 13 litre TAD1382GE from Volvo because it is a powerful, reliable and economical motor built on the dependable in-line six design. The engine incorporates a suite of advanced technologies that work together to not only reduce emissions but also deliver significant improvements in power density, performance and operating efficiency. Designed for easy, fast and most economical installation, the engine’s high-tech injection and charging system with low internal losses contributes to excellent combustion and low fuel consumption.
“Volvo has been our preferred engine partner for a while, largely because of the efficiency of their engine technology. In addition, we find them easy to deal with in terms of information sharing and guidance on the technology. To provide context, we had a technical representative from Volvo at our Jet Park workshop for a week-long factory testing, before deploying the machine for field testing in a tough crushing application with great success,” says Abelho.
For a longer version of this article, visit our website: https:// miningbusinessafrica.co.za/
The collaboration between Bolt Engineering and Distributors (B.E.D.) and Bolt Torque brings premier service, cutting-edge technology, and nationwide support in bolt torqueing and tensioning to companies in different industrial sectors.
When mining companies are planning capex purchases, bolting and tensioning may be viewed as the smallest priority. Yet these pivotal practices have significant implications for productivity and safety. Downtime due to bolting or torqueing failures – including incorrectly calibrated toolscan translate into financial loss, and accidents result in potential breaches of safety regulations and even potential loss of life. As currently production is peaking in African mining, this can prove very costly from a financial and human resources perspective.
Perfectly timed
So, the pre-2024 Electra Mining announcement of the collaboration between Bolting and Engineering Distributors (B.E.D.) and Bolt
Torque could not have been more perfectly timed. The collaboration increases B.E.D.’s capacity to meet the safety and quality requirements from mining companies, reinforcing its position as a leader in the market.
Significantly, the collaboration strengthens B.E.D.’s well-established fastener product portfolio by integrating Bolt Torque’s advanced torque tensioning technology and expertise.
“This collaboration allows us to offer a more robust suite of products and services, including state-of-the-art equipment for precise bolt torqueing and tensioning and the requisite annual tool calibration, which is crucial for demanding mining conditions,” explains Mike Giltrow, CEO of B.E.D., illustrating B.E.D.’s knack of establishing lasting and productive partnerships with reputable suppliers.
While B.E.D. is known for the slogan and ethos of ensuring ‘the perfect fit fast’, it applies a rigorous process in supplier selection. The company thoroughly assesses potential suppliers based on their technological innovation, global and local market reputation, and ability to meet its high standards of product quality and reliability. This ensures that the preferred supplier fits with B.E.D.’s operational ethos and strategic vision.
B.E.D.’s and Bolt Torque’s industry track record
Thus, when looking for a suitable supplier to enable it to offer comprehensive turnkey torqueing and tensioning solutions, B.E.D. selected Bolt Torque: “Bolt Torque’s proven industry track record, sound business ethos, and complementary expertise in bolt torqueing and tensioning solutions align perfectly and synergistically with our operational expertise, organisational ethos and strategy,” enthuses Giltrow.
From Bolt Torque’s perspective, Angus Houston, Bolt Torque’s Global Sales Manager, recounts that, when the opportunity to partner with B.E.D. came up, management did not think twice: “From our perspective as a supplier, B.E.D. is an ideal strategic partner due to its extensive industry and distribution experience, strong local market presence, ethical reputation and unwavering commitment to quality and customer service.”
In particular, Houston cites the following attributes of B.E.D. as the perfect strategic partner:
• Extensive industry experience: With over four decades of experience, B.E.D. has built a strong reputation and a wealth of expertise in supplying high-quality products across diverse industry sectors, including agriculture, mining, materials handling, working at height and welding.
• Commitment to safety and quality: B.E.D. is synonymous with safety and quality, consistently delivering products that meet stringent industry standards.
• Strong supplier and customer relationships: B.E.D. maintains long-standing relationships with an impressive portfolio of both international and local suppliers, built on shared values of trust, integrity, and a commitment to the ‘100/0’ ethos of taking 100% responsibility and accountability, with zero excuses.
• Comprehensive solutions and reliable service: B.E.D. has been a key player in providing tailored solutions for numerous significant projects across various industries. The company ensures reliability in stock, sourcing, and delivery, supported by innovative in-house logistics and management, to meet the needs of its loyal customer base.
Extending B.E.D.’s bolting and torqueing product range and capabilities
The addition of Bolt Torque’s latest technology extends the range of B.E.D.’s product portfolio by including high-precision hydraulic torque wrenches, and advanced wind turbine tensioners for wind farm applications. This addresses some of the most pressing challenges in bolting and tensioning in renewable energy, oil and gas, and mining sectors.
Houston highlights some of the features of the technology and the convenience it brings to the complex task of bolting and tensioning: “The latest Plarad battery-powered torque and tension tools from Germany are engineered to provide precise and consistent results, addressing the issue of variability in bolt torqueing and tensioning, which can lead to equipment failures or safety hazards.”
Of note is the fact that the partnership goes beyond the latest technology. It adds significant value - not only by expanding B.E.D.’s existing fastener range with high-quality bolting and tensioning tools and capabilities, but also by offering a turnkey solution which includes equipment rental, certified and traceable tool calibration and on-site technical support services. In this way, customers not only receive high-quality products - but also the necessary services to maintain and optimise their equipment, thereby improving operational efficiency and reducing downtime.
In particular, Houston sees the rental options as providing the convenience of cost-effective
bolting and tensioning solutions for companies that need high-quality equipment without the upfront investment.
Furthermore, through Bolt Torque`s 20-year association with Top Rope, a leading rope access and on-site contractor, Bolt Torque and B.E.D are able to offer bolting installations on customers’ sites.
What’s more, the new distribution agreement with B.E.D. enhances Bolt Torque’s reach and its service offering to customers: “By leveraging B.E.D.’s 9 branches and established customer base, we can now provide nationwide access to our high-quality bolt torqueing and tensioning tools. Customers can expect not just the best torqueing and tensioning equipment, but also expert guidance regarding its application, ensuring that bolts are tightened correctly and safely,” Houston says, underscoring Bolt Torque’s commitment to maintaining a high standard of service, with rental tools and spare equipment readily available to meet urgent needs. In summary, this dynamic collaboration allows B.E.D. and Bolt Torque to better serve their joint customers; and, together, to tap into new vertical industries and opportunities across South Africa.
Regarding what current and prospective customers in the mining sector should expect, Houston pronounces, “Excellence!” Then, he proceeds to elaborate: “Clients can expect an elevated standard of service and product offerings, marked by speedy delivery, agility and innovation, which will set a new benchmark in the industry.”
Changing climate conditions create a compelling business case for the adoption of effective water recycling and reusing technology, with custom-designed packaged water treatment plants fitting the bill.
VThe rule of thumb is that the desired quality of the treated water is correlates with the effectiveness of the method used in removing contaminants.
arious organisations - prominently the Food and Agriculture Organisation (FAO), Greenpeace, and the World Health Organisation (WHO) - have extensively researched water security. In concurrence, these organisations attribute this phenomenon to climate change, rapid urbanisation, and increasing industrial usage. They contend that these are straining existing water bodies.
As a result, mining companies must constantly seek sustainable and cost-effective ways of managing the increasingly scarce water resources, central to their operations. One of the
tried and tested ways is recycling and re-using wastewater. But first: just how significant is the risk of water scarcity?
The risk of water scarcity
Contrary to the view of climate change sceptics, highlighting the risk that water scarcity poses to mining operations is far from alarmist. In fact, water scarcity has huge implications for human existence and business in general.
The World Health Organization (WHO) predicts that over 200 million people in subSaharan Africa could lack access to water by
2030. Alarmingly, with the region experiencing severe effects of climate change, there are strong indications that this could occur sooner than anticipated and the figure could be higher than initially forecast.
Even more profound is the effect on industries, especially mining. Typically, mineral processing is a water-intensive activity as it requires large water volumes to recover valuable minerals from ore. The improper disposal of wastewater from this activity pollutes the environment.
Given this, water use permits mandate that
mining companies adopt sound water usage and reduce the impact on local water sources. The permits set conditions for water usage and the safe disposal of treated wastewater.
Thus, the current situation is a call to action for mining companies to adopt effective water management techniques to address the challenge of water scarcity.
Wastewater recycling and reuse, using packaged treatment plants, is the route to go. This method helps mines comply with the regulations, as well as manage limited water resources more effectively.
However, packaged treatment plants may not always produce the desired quality. This is because waste streams contain contaminants with carcinogens like uranium, arsenic, and heavy metals like calcium and magnesium. These need thorough treatment. Otherwise, pollution poses significant health risks and environmental hazards.
The good part is that challenges can be turned into opportunities through an effective package water treatment solution. This is achieved by making water suitable for reuse as process water
without compromising process efficiency. Generally, the rule of thumb is that the desired quality of the treated water is correlates with the effectiveness of the method used in removing contaminants. Otherwise, poor treatment can impact the process, while contaminated discharge can cause environmental pollution. On the other hand, effective water treatment can result in high water recovery, reduced reagent use, and reduced power consumption.
To achieve optimal results, mines must be scrupulous in the selection of methods for their packaged treatment plants. Mainly, the following are key treatment options:
• Biological Wastewater Treatment
• Chemical Precipitation and Clarification
• Activated Carbon Adsorption
• Reverse Osmosis Membrane Technology
• All Membrane Brine Concentrator Technology
The right choice goes beyond achieving compliance. It protects water bodies from contamination. In the end, sound water management, through effective packaged solutions, maximises profitability, supports sustainability, and helps meet Environmental, Social, and Governance (ESG) reporting requirements.
The latest addition to WEC Water’s already impressive reference list is a project that really tested the boundaries of what was thought possible in packaged water treatment. WEC Water provided a seamlessly executed turnkey project to fabricate, deliver and commission their biggest ever packaged water treatment plant to a difficult to reach mine in the Democratic Republic of Congo.
The mine needed a water treatment plant that can treat 680m3/hour from the processing plant to reduce the risk of water insecurity on operations and the mine’s overall water use footprint. Adding to the complexity for this plant was the variable quality of the influent water, the remote site location, and the specifications that the mine requested to maintain the highest level of safety on site. As a final consideration, the client wanted to keep the civil requirements to a minimum to reduce on-site installation time.
WEC Water’s team of specialist Process and Mechanical engineers came up with a packaged plant design that ticked all the boxes for the client. They designed a system with two
treatment trains each consisting of a flocculation tank, three clarifiers, four multimedia filters, and intermediate storage tanks. The plant was designed to be modular so that it could be fabricated in South Africa and delivered to site in a remote region of the DRC with relative ease.
This plant represents the biggest packaged water treatment plant that WEC Water has ever designed but that didn’t bother the execution team. They managed the delivery, installation supervision and commissioning with excellence and ensured that the plant was handed over to the client on time and fully operational.
Nigel Birchall, a WEC Water Project Manager, credits the success to meticulous planning and implementation of critical elements to the client’s specific requirements.
“One such consideration was for the plant to use as little liquid chemical as possible” explained Birchall. “It is difficult and expensive to get liquid chemicals to remote sites, and it creates an unnecessary health and safety risk. To address their concern, WEC Water designed the plant to use dry chemical make-up
equipment allowing precise dosing through the automated system without the need for liquid chemical sourcing and handling.”
Logistics creates other challenges in delivering a plant like this. The coordination of the packing, loading, and delivery were critical to ensure that all the parts on all the loads – 18 super-link trucks worth – were delivered to site in good working order. Meticulous planning was done to orchestrate the logistics, and constant management and communication allowed for everything to arrive on site in time. It was a monumental cross-functional effort between the teams on the ground allocating, packing and loading the goods, to the logistics coordinators and transport companies and the teams on the ground in DRC unloading and installing the plant.
This plant is a feather in the cap of the WEC Water team and adds to their already impressive list of references. With successful installations in more than 20 African countries, WEC Water has proven their capability to get their projects completed despite the various challenges associated with working across Africa. In reflecting on this project, Tim Fischer, Process Engineering Manager at WEC Water, said: “This project gave us all some grey hairs and kept us up a few nights, but this is what we come to work to do – Engineer the water of tomorrow. We look forward to the next challenge – the next opportunity to do something extraordinary – so get in touch and let us find a solution to your unique water treatment challenges.
For licensed winders, RCA is generally done every 30 days, not exceeding every 40 days. Site engineers are obliged to adhere to the applicable legislation. WearCheck’s rope inspectors stick to a regular testing schedule of all the ropes in their care.
High productivity, profitability and asset reliability, coupled with minimised maintenance concerns – these are the aspirations of management teams at most mines and other industrial operations.
A sure way to make these goals a reality is to keep a constant finger on the pulse with regards to the condition of all engines, operating equipment and components. In other words, ongoing condition monitoring is essential.
Specialist condition monitoring company, WearCheck, empowers industrial operations with accurate insight into the condition of assets, enabling maintenance crews to optimise the health of a diverse array of machines and their components, using many different testing techniques.
The company serves as a hub for specialised teams that focus on monitoring different aspects across various sectors. In addition to its core service - the scientific analysis of used oil and other fluids – WearCheck also provides advanced field services (AFS) asset
reliability care (ARC), scientific water analysis, transformer oil analysis and lubricant-enabled reliability (LER) services.
To ensure that the required safety standards are met, WearCheck’s AFS team complies meticulously with the strict regulations set out in the South African National Standards (SANS) 10293:1996 Code of Practice for Steel Wire Ropes and various other relevant SANS Codes of Practice, which state that, “Conservatism must prevail where the safety of people or the continuity of production is involved, and great accuracy is not achievable. For the rope condition assessment inspector, the most important issue is reliability of defect detection in terms of the prescribed standard. Sound knowledge and understanding of component behaviour under the given service conditions is indispensable to all parties concerned.”
WEC Water has been in the water and wastewater treatment business for over 20 years and has completed over 400 projects, so when they achieve a major milestone, it is usually worth celebrating.
Through these monitoring techniques, WearCheck’s team of scientists, technicians and diagnosticians can assist customers to ensure that major, unscheduled equipment failure is avoided. This saves both time and money for industrial operations, and boosts productivity and safety.
The AFS team consists of experienced, highly skilled technical operators, who conduct technical compliance, non-destructive testing and rope testing.
This is a discussion around Rope Condition Assessment (RCA), where the integrity of steel wire ropes is tested to the relevant SANS Codes of Practice, and OEM or international standards.
Why test ropes?
Paul Musgrove is WearCheck’s AFS operations manager. He outlines the testing process. ‘We use a standard set of instruments to test a variety of different steel wire ropes. This includes a magnetic rope test instrument, which is affixed to the rope. All WearCheck’s RCA instrumentation is calibrated annually by an independent thirdparty service provider.
‘It magnetises the rope, feeds back information to an on-site computer, and detects anomalies such as corrosion, broken wires, wear, plastic deformation and many other problems that can occur in ropes,’ says Musgrove.
‘We can assess and apply the relevant discard criteria to a rope which has been compromised. The anomalies are calculated, test results analysed, and we advise the rope maintenance team immediately where corrective action is needed.
‘Non-destructive test methods are conducted on site, so that healthy ropes can continue in their normal operation until they have reached the end of life, based on the applicable discard criteria.’
How often should ropes be checked?
For licensed winders, RCA is generally done every 30 days, not exceeding every 40 days.
The RCA, on chairlift ropes and unlicensed winder ropes, is usually done at frequencies as determined by the relevant legally appointed engineer at all the relevant sites. The site engineers are obliged to adhere to the applicable legislation. WearCheck’s rope inspectors stick to a regular testing schedule of all the ropes in their care.
What industries use RCA?
RCA is conducted largely in the mining industry, where double drum winders, chair lifts, elevators and other steel wire rope components are regularly checked.
Also, rope manufacturers rely on RCA as a means of ensuring compliance with quality specs during the quality assessment (QA) process in the production of new ropes.
Who can conduct RCA tests?
The process of qualifying as an RCA inspector is particularly rigorous, to ensure that extreme safety measures are in place. There are currently only about 12 people in South Africa
Paul Musgrove, WearCheck AFS
who are qualified to conduct rope condition analysis, and six of these technicians work at WearCheck.
The highly specialised certification process calls for an artisanal qualification, an N5
Condi�on
certificate, at least 18 months’ supervised work experience in the industry, and two written and practical exams, which must be passed with a minimum of 75%.
WearCheck’s extensive network of laboratories
WearCheck provides condition monitoring services throughout Africa, the Middle East and India – the company’s comprehensive network of 16 laboratories spans the continent and beyond, with a presence in nine countries.
WearCheck serves customers in a range of industries, some of which include mining, automation, manufacturing, wind turbines and power generation, earthmoving, industrial, transport, shipping, aircraft and electrical operations.
The company has established laboratories near industry/mining hubs in several countries, all of which are situated within easy reach for customers. In addition to the labs in South Africa, there are laboratories in Zambia, Zimbabwe, Namibia, Mozambique, DRC, Ghana, Dubai and India.
WearCheck, Africa's leading condi�on monitoring company, is commi�ed to serving the mining industry with its range of sophis�cated analy�cal techniques.
Our specialist oil, coolant and fuel tes�ng programmes allow customers to reduce maintenance costs, avoid unexpected mechanical failures and ul�mately reduce unscheduled down�me.
Using wrong mist eliminator designs for an application can lead to costly damage to equipment (resulting in unplanned repair and replace costs), high energy consumption, and pressure loss. The importance of making the right choice cannot be overstated.
As environmental protection regulations have become stringent, organisations in heavy-polluting industries are more obligated to reduce greenhouse emissions from their operations. In response, there has been a surge in the use of mist eliminators in wet scrubber systems used in process equipment as organisations strive to comply with the requirements. Leading suppliers of mist eliminators Mining Business Africa contacted observe this trend.
The risks
Emissions pose significant risks to operations. Typically, industrial exhaust streams contain contaminants like oil mist, aerosols, sulphuric acid. These are carcinogenic, according to a report from the World Health Organisation. Besides, they can speed up corrosion of equipment components, a costly issue for industries.
Suitable measures
Accordingly, it is vital to adopt effective measures that can minimise equipment damage, reduce greenhouse emissions, and limit worker exposure to heath risks, among others. That’s where mist eliminators come into play.
Mist eliminators
Mist eliminators mechanically remove liquid contaminants from gas streams through
a combination of direct impingement and centrifugal force. That is why they are incorporated in industrial scrubber designs, making wet scrubbers more effective at capturing small droplets containing contaminants or particulate matter.
A wide selection
Advances in Research and Development
present a wide selection of different brands of mist eliminators from OEMs for the industrial end-user’s preference. However, generally, mist eliminators fall under the following categories, according to their applications:
1. Wire mesh mist eliminators
Assembled compressed layers of wire, held
by support grids, wire mesh eliminators are the most common mist eliminators in industry. Placed in either vertical or horizontal airflow, they are efficient at removing smaller droplets. They are placed between the gas stream inlet and the clean air outlet.
Wire mesh eliminators are considered affordable compared to the other types. The wire can be made from materials such as metal, polyester, polypropylene, or glass fibres.
2. Vane (chevron) mist eliminators
As far as the removal of larger droplets from gas streams goes, vanes, also known as chevron mist eliminators, are ideal. With a series of blades strategically positioned in the airflow path, vane mist eliminators are versatile and
Munters mist eliminator profiles are designed to enhance efficiency and reduce environmental impact virtually anywhere liquid droplets and gases need to be separated.
DH droplet separators are designed for horizontal flow, offering high separation efficiency with low pressure drop. These vane-type separators streamline gas and liquid separation, providing robust and efficient mist elimination for demanding environments such as air intakes, cooling coils and scrubber outlets.
DV mist eliminators direct gas flow through specially designed chambers, which are designed to provide maximum gas flow effect. These vane-type separators ensure precise liquid drainage, making them ideal for heavy-duty industrial applications like gas scrubbers, desulphurization units, and chemical plants.
can be used for either horizontal or vertical requirements. Spacing and design specifications depend on the droplet size to be filtered and particular application.The popular material of construction for vane mist eliminators is stainless steel or carbon, though other options are available.
3. Fibre bed mist collection eliminators
Where filtration of sub-micron particles is required in horizontal gas streams, cylindrical fibre bed mist collection eliminators are more appropriate. Some OEMs claim their products have a contaminant removal efficiency of 99.9% from emissions. However, end-users single out pressure drop and inadequate drainage as downsides with fibre bed mist eliminators.
Customisation
In a recent interview with Mining Business Africa recently, Phil Dickinson of Munters
Selecting an eliminator with appropriate specifications can minimise clogging.
Africa stressed the importance of customising eliminator designs to the unique needs of an operation. For instance, where convenient, a vane mist eliminator can be combined with wire mesh to improve the efficiency of wet scrubbers. Gas streams can enter the wire mesh before reaching the vane mist eliminator. Also, multiple layers of wire mesh filters can be used to capture droplets of varying sizes.
Overcoming selection challenges
Dickson also pointed out that selection of a mist eliminator should be done scrupulously.
This ensures there is suitable equipment for an application. Otherwise, significant challenges may arise. One of the common problems is clogging, which is the building of material upon the surface of the mist eliminator. This reduces pressure, resulting in product loss, increased energy consumption, corrosion, unscheduled repair and replacement costs, and low availability.
So, selecting an eliminator with appropriate specifications can minimise clogging. That is why the following factors are key considerations: type of chemical process, particle size, and suitable collection method. And the benefits are: pressure drop, low energy consumption, low maintenance requirements, and decreased damage to downstream equipment.
In the end, informed mist eliminator selection helps organisations to comply with stringent environmental regulations, while reducing operational costs and extending equipment life.
Ongoing maintenance of HVAC systems is just as crucial as selecting the most appropriate system for an application to ensure reliability...
The landscape of HVAC systems for mobile equipment in surface mining and quarrying sectors has evolved significantly over the past decade. The shift has been towards more robust systems capable of withstanding the harsh conditions typical of these operations. Brenton Spies, Managing Director of Booyco Engineering, says that trends in HVAC systems have focused on operator safety and comfort, system reliability and environmental considerations.
“Over recent years, there has been a pronounced focus on operator safety and comfort,” Spies says. “The classification of climate as a Class A hazard underscores the importance of providing operators with comfortable working conditions. Ensuring a safe and comfortable environment is not just about individual wellbeing but also about enhancing productivity.”
“Reliable and effective HVAC systems are crucial in maintaining a safe working environment around the clock, and Booyco HVAC solutions play a vital role in improving working conditions, whether in extreme heat or cold,” he says. By ensuring a comfortable working environment, HVAC systems help maintain cognitive awareness among operators, preventing accidents.
Booyco HVAC systems assists in preventing serious medical conditions that could jeopardise an operator’s health and safety and by combining HVAC systems with air filtration
systems mitigates the risk of respiratory illnesses by removing harmful gases and particles from the operator cab. Booyco HVAC systems are designed to integrate seamlessly with Sy-Klone air filters, enhancing air quality. Booyco Engineering is an authorised distributor of Sy-Klone air filters in southern Africa.
Spies explains that maintaining uptime of equipment on a surface mining site is critical for minimising operational costs, especially given the current pressure on commodity prices. “Good working conditions are integral to this. Operators have the right to stop working if the HVAC system in their cab becomes
dysfunctional, potentially causing significant interruptions to mining operations. This, again, reinforces that reliable HVAC systems are essential to ensure continuous operation.”
Mining environments are inherently extreme, with operations often located in remote areas with severe weather conditions. Dusty operating environments are common, despite dust mitigation efforts. Booyco HVAC systems are engineered to withstand these harsh conditions, with attention to detail ensuring the systems can handle extreme vibrations when traversing rough terrain. Quality components are selected during the design phases to ensure reliable performance under these extreme conditions.
“Ongoing maintenance of HVAC systems is just as crucial as selecting the most appropriate system for an application to ensure reliability, and we offer maintenance contracts and Man on Site (MOS) options that facilitate preventative maintenance and ensure optimal uptime of our HVAC systems, ensuring maximum fleet uptime.”
A notable trend in recent years is the move towards more environmentally friendly refrigerants. Supporting the sector’s commitment to reducing its carbon footprint, Booyco Engineering has developed a fully integrated HVAC anti-idle auxiliary power unit (APU). This innovative solution significantly reduces diesel consumption during operational idle times, leading to a reduction in operating costs.
“The evolution of HVAC systems for mobile equipment in surface mining reflects a comprehensive approach to tackling the industry’s unique challenges, and Booyco Engineering has been at the forefront of these developments with continued emphasis on robust design, operator safety and comfort, reliable performance and environmental responsibility,” Spies says. “By continuously innovating, we ensure that operators work in safe, comfortable environments, enhancing productivity and operational efficiency across the mining sector.”
Mining Business Africa (MBA) is Pan-African bi-monthly publication that focuses on latest developments in mining and allied industries in Africa. The publication covers the scope of critical activities from pit to port – mineral exploration (prospecting), mine planning and development, extraction, mineral processing, storage transportation, as well as beneficiation.
Mining Business Africa provides the desired mileage for companies looking to promote their products and services to a specific niche clientele in the African Mining Sector. Subscribers are located or at least involved in projects in South Africa, Botswana, Zimbabwe, Zambia, Kenya, Democratic Republic of Congo, Kenya, Tanzania, Ghana and Nigeria.
MBA is published by Media Icon, a company manned by personnel with a combined experience of 30 years in the publishing space.
Probably the world’s coolest transformer fluid
With the introduction of NYTRO® BIO 300X, Nynas adds the first product in its new bio-based range, completing its portfolio of high-performance transformer fluids. NYTRO® BIO 300X is the result of years of intensive research. We are now able to offer a 100% renewable hydrocarbon with superior performance according to IEC 60296.A true innovation.For more information visit our website or contact your local Nynas sales office www.nynas.com/transformer-oils
• SF6 free, metal-enclosed, fixed pattern switchgear to IEC 62271-200
• LSC2B-PM (highest level of service continuity)
• 12kV Rated voltage
• 95kV Rated impulse withstand voltage
• Epoxy resin insulated and fully earth screened individual poles and busbars
• Up to 40kA and 3150A (4000A with forced cooling)
• Internal arc classification IAC AFLR 31.5 kA 1 sec
• Type “C” cable interface bushings
• Severe service conditions IEC62271-304-Class 2
• Visual isolation and earthing
• 3-position disconnector with integral earthing
• Width: 500mm (1250A), 700mm (2500A), 1000mm (4000A)