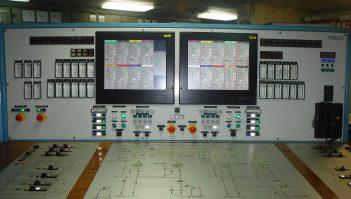
6 minute read
Getting on board with a modern DCS solution
PROCESS CONTROL
Getting on board with a modern DCS solution
Advertisement
In addition to revamping the boilers, pumps and turbines, the project included modernisation of all the control systems – from the central management system to the system used for the turbines and turbopumps. The design and implementation of the new automation system was assigned to the Safety Systems and Information Division of Italian company Leonardo. Dedicated to transporting liquid natural gas, the ships, which have a capacity of 65,000m 3 each, underwent an extensive refit project, in which Leonardo was involved with automation control, sensors and field instrumentation.
At the time of their construction, both the LNG Portovenere and the LNG Lerici were equipped with a Bailey Infi 90 system, which became a legacy system at the end of its lifespan, maintained by the Leonardo service department. The desire to replace the legacy system with a modern, high-performing system was at the heart of the project.
In addition to the central system Leonardo was also tasked with modernising the turbopumps and turbine automation systems, which traditionally had been managed by separate systems. The replacement of all field instrumentation was also necessary, as it had become obsolete. Stoppage time for the ships needed to be as brief as possible. This required good coordination with the other contractors, in order to proceed with installation of the hardware and software in parallel with the revamping of the boilers, turbines, pumps and other equipment – keeping the commissioning phase to a minimum.
All internal inspection activities also needed to be scheduled within the upgrade time window. External certification by certifying bodies also had to be factored in as the ships have dual registry: specifically, RINA – Registro Italiano Navale (the Italian Naval Registry) and ABS – the American Bureau of Shipping.
“In this context, with so many variables and rigid timetables, selecting the best solution and suppliers was a key factor,” said Stefano Baccelliere, homeland security & critical infrastructure LoB / project manager at Leonardo. “On the one hand, our time was very restricted, but on the other we wanted take advantage of the occasion offered by these large-scale works to offer our client a solution that was decisively better than the incumbent solution, to allow for possible future developments.
“We had to lean towards a solution that did not have hidden surprises. We also wanted a system that had high performance levels associated with the management of functional safety, while also being simple to implement, in terms of hardware and software, ultimately delivering fluid migration of the legacy system to the new system. We could not take for granted the importance of finding a supplier that could bring proven experience from three diverse markets – naval, oil & gas processing, and energy – and above all, one with the capacity to make these vertical skills a common Built in 1997, the LNG Portovenere and LNG Lerici are ships designed for the transportation of liquid natural gas. Having reached the middle of their lifespan, the ships needed to undergo a total renovation project including new distributed control systems.
A big challenge The biggest challenge, however, was the short time windows given by the owners to complete the upgrade.
UK INDUSTRY NEWS
GUIDING PRINCIPLES FOR DIGITALISATION
According to Made Smarter, by 2030 the UK will be the global leader in the creation, adoption and export of advanced digital technologies. These new technologies will enable faster, more responsive and more efficient processes to deliver improved productivity and higher quality products at a reduced cost.
To help companies and workforces drive the take up of new technologies in a way that is not disruptive, but which also produces good jobs improved productivity and a clean footprint, Made Smarter has designed six guiding principles which it is asking companies to commit to themselves, as well as extending the relationship to their supply chains.
The six guiding principles for digitalisation are: 1. Partnership at work: A strong partnership is essential to any process of change. Employers will share plans for and address any issues arising from the introduction of digital technology through cooperation, consultation and mutual agreement with the workforce including union representatives where they are present at the workplace. It is a shared ambition that digital technology delivers better jobs, on decent terms and conditions. 2. Health, safety, welfare and environment: Industrial digitalisation presents opportunities to improve safety and environmental impact in the workplace, throughout the supply chain and across society. Companies will assess any potential impacts on health, safety and sustainability arising from the use of digital technology and conduct appropriate training to mitigate any associated risks and to make the most of opportunities for improvement. 3. Developing digital skills for the future: Employers and employees have a shared ownership of skills development. This should be supported through organisational and personal development plans. Companies will ensure that people have access to the training they need. Government and employees (or their union representatives) will be part of the partnership on retraining. Employees and unions, where they are present, will be engaged in developing and agreeing retraining plans. 4. Respect at work: All workers are entitled to high standards of treatment. Job satisfaction, rather than job intensity, will lead to improved productivity. The sharing of data and trust in its use is critical. Companies should consider developing codes of conduct on data use, including within supply chains, drawn up in consultation with the workforce and their representatives. Companies need to demonstrate that employee data is secure and that they are in compliance with regulations. 5. Job security and enhancement: Growth generated by digital technology should be reinvested, where possible, into areas that provide more opportunities and Government, Industry and the Trade Unions have come together to launch a new set of Guiding Principles for Digitalisation to help companies and the workforce make the most of the increasing drive towards a new digital era for manufacturing.
better jobs within the organisation. Individuals should see their roles enhanced as a consequence of digital technology. This will require open and creative ways to generate ideas for new products and/or areas for investment. 6. Equalities, diversity and inclusion: Digitalisation can support inclusivity but issues, including new ways of working and working time, job design, job evaluation, access to training, retraining and progression, can all have equality and diversity implications. Equality impact assessments should be included within any organisations’ plans for digitalisation. Commenting at the launch of the principles, Andrea Leadsom, Secretary of State for Business, Energy & Industrial Strategy said: “Manufacturing plays a vital role in the UK economy and our manufacturers are leading the way in driving innovation, job creation and growth. Through the Made Smarter Commission the Government is working with industry to help manufacturers embrace digital technology and use it to further boost our competitiveness.”
Professor Juergen Maier, chair of the Made Smarter Commission and Siemens UK CEO, said: “We have long said we need a workforce ready for technology disruption and one million existing workers need new digital skills. This partnership between Government, industry and the TUC is the first step in developing a detailed roadmap to deliver this.” !