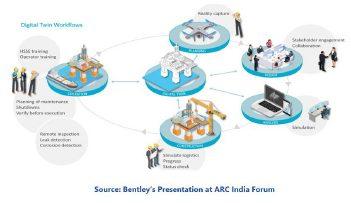
10 minute read
Digital twin collaboration discussed at ARC India Forum
INDUSTRY REPORTS
Digital twin
Advertisement
collaboration
At the ARC India Forum in July, Bentley Systems focused on digital twins, and its collaborative efforts. Tracing the digital journey, speakers from Bentley explained how industry moved from drawing boards to the computer 20 years ago; and then on to servers and now to the Cloud with unlimited computing power. Presentations by Anne-Marie Walters, industry marketing director, Oil and Gas and Manufacturing at Bentley Systems; and Amit Shrivastava, regional sales engagement manager at Bentley Systems, highlighted several areas: • Digital twins have emerged as a key focus area for infrastructure projects and assets. • Integration between information technology (IT), operational technology (OT), and engineering technology (ET) is vital to streamline business processes. • Bentley has developed technology partnerships with companies such as Siemens to help speed industrial growth. Sharada Prahladrao, PR manager at ARC India, reports from the ARC India Forum.
Walters also spoke about digital workflows and the huge benefits realised in terms of health and safety, operator training, planned shut-downs and maintenance after information verification. “Sharing information in a digital, 3D world enables greater collaboration and stakeholder engagement,” explained Walters. “Digital twins help simulate the work environment and perform status checks, predict possibility of failure, plan logistics, check progress and so on.” Shrivastava went on to talk about solutions to combat today’s challenges – the main one being data aggregation. Digital twins require data from information and operational technologies to understand the current state of the project or asset. Combining data from engineering technologies into a digital twin enables simulations so users can try out different scenarios or predict the performance of an asset, he explained.
In this context he spoke about Siemens and Bentley Systems’ jointly developed PlantSight. The two companies created the PlantSight digital twin solution to help customers improve the efficiency of their plant operations, with process plant operations being documented in data. Typically, this information is stored in multiple silos of information in various formats, making it difficult to access and verify. PlantSight brings all this data and information together, then contextualises, validates, and visualises it. It transforms data into one complete digital twin – an ‘evergreen’ digital twin that is continuously updated. It is hoped that PlantSight will help process plant owner-operators realise the benefits of digital twins, up-dated in real time for operations, without disrupting their existing physical or virtual environment.
Shrivastava explained the company’s step-wise approach: • Create a 3D reality mesh from 2D photographs or scans. • Train the software to automatically recognise and classify components. • Visualise classified components. • Aggregate with other information into digital twins.
Reality modelling is already being used to transform photographs into accurate 3D models to zoom in on the trouble spots (such as rusted parts) and fix them. Adding the element of time with continuous surveying,
In previous years Bentley has focused on its going digital strategy and the connected data environment (CDE) at the forum. This year, it was all about digital twins. Walters began her presentation by explaining what a digital twin is and why it is now the company’s focus area. In simple terms, it is the digital representation of a physical asset, process, or system; which is continuously surveyed or synchronised from multiple sources to generate insights for predictability and performance optimisation.
INDUSTRY REPORTS Total set to open a digital factory Total will open a Digital Factory in Paris early in 2020 with the aim of bringing together up to 300 developers, data scientists and other experts to accelerate the Group’s digital transformation.
The goal of the project is to leverage the capabilities of digital tools to create value in all of its businesses. The Digital Factory will be tasked with developing the digital solutions needed by the company to improve its operations, in terms of both availability and cost; offer new services to customers, notably in the area of managing and controlling energy consumption; extend its reach to new distributed energies; and reduce its environmental impact.
Total’s ambition is to generate as much as $1.5 billion in value per year for the company by 2025 through additional revenue and reductions in operating or investment expenses. Commenting on the project, Patrick Pouyanné, chairman and chief executive officer of Total, said: “I am convinced that digital technology is a critical driver for achieving our excellence objectives across all of Total’s business segments. Total’s Digital Factory will serve as an accelerator, allowing the Group to systematically deploy customised digital solutions. Artificial intelligence (AI), the Internet of Things (IoT) and 5G are revolutionising our industrial practices, and we will have the knowhow in Paris to integrate them in our businesses as early as possible. The Digital Factory will also attract the new talent essential to our company’s future.”
The Digital Factory is a new step in Total’s transformation process. It follows the signature of major partnership agreements with Google on artificial intelligence and geosciences and with Tata Consultancy Services on Refinery 4.0.
Innovative Infrared Technology On target. Thereʼs no two ways about it: our cost-effective Xi series IR cameras with their automatic spot fnder func tion and analog/digital outputs are ideal even for OEM applications. Also interested in really fast, rugged, light, accurate, customised and inexpensive infrared thermometers and cameras for non-contact measurements between −50 °C to +3000 °C? Visit www.optris.gobal from 940 € the severity and speed of deterioration can be detected and predicted. A recent example can be found at Shell’s largest onshore construction project, the creation of an ethylene plant in the US. A drone surveying company is continuously creating reality models of the construction site on a bi-weekly basis. The drones take project snapshots and 3D models are created, providing an effective top-down view of how construction is progressing and what needs to be done. Everything on the site is located by an equipment tag; all the databases are connected, with accountability for three million documents and equipment tags. Digital twin benefits Both Bentley speakers highlighted the benefits of employing digital twins which includes: • Efficiency: Improved data quality and security; up-to-date 2D and 3D plant documentation; continuous monitoring and optimising of plant assets. • Cost reductions: Faster operational readiness; direct and easy access to information. • Revenue growth: Faster and collaborative decision making. Digital twins merge the real (physical) and virtual worlds. Both presentations brought into sharp focus the importance of digital twins across industries and substantiated this with examples and case studies. What came across clearly was that when companies collaborate and complement their strengths, end users benefit. !
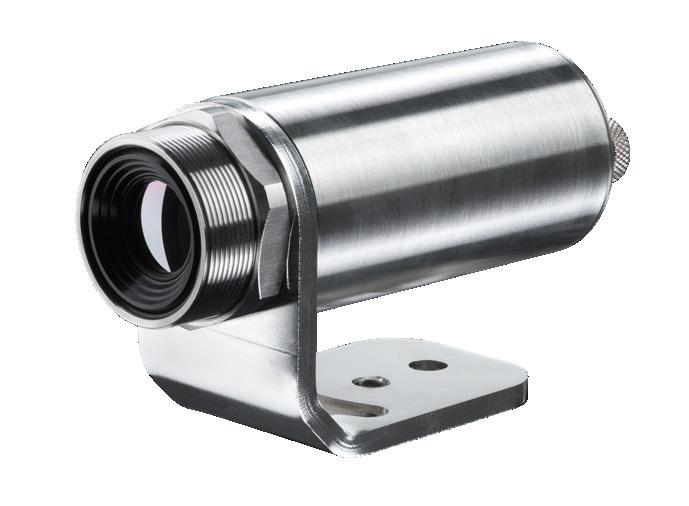
COVER STORY
Plug and work for simple electric movements When simplicity of pneumatics meets advantages of electric actuators
Even if pneumatics is the preferred solution for applications requiring simple movements, the technology is more and more facing a digitalised world. Here, up to date information about actuator status is required to reduce commissioning times, enabling cost-efficient production and deal with shorter product life-cycles.
Moreover, even if pneumatic actuators – regarding investment cost – are the most attractive technology, total cost of ownership must also be considered. Diagnostics and big data require a seamless flow of information from the workpiece to the controller and cloud. Traditional pneumatic systems struggle with this challenge, as the compressed air cannot transmit data. With these factors being considered, it is not surprising that machine builders see electric motion more and more as valid compliment or even alternative to pneumatics. For simple applications and motion tasks, pneumatic actuators are the preferred choice, they combine simplicity in installation and control, and highly attractive investment cost in one. Festo as a leading supplier for both pneumatic and electric automation components, now brought the simplicity of pneumatics to the world of electric automation, with the new electric Simplified Motion Series.
demand for simple electric actuators and solved it in the new Simplified Motion Series. Simplified installation Simplified Motion Series from Festo therefore is not only a new line of electric actuators, it is designed from the bottom up to offer simplicity in installation.
The core component of the Simplified Motion Series, launched in September 2019, is a new integrated motor with a permanently attached drive unit, available pre-mounted to a range of mechanical actuators. This enables rotary and linear movements with a variety of formats for the actuator. This concept not only reduces installation space but also minimizes installation time and cost in production processes. Simplified motion profiles A mechanical installation concept itself does not help close the gap to pneumatics, the deciding feature is Simple movements So, why has the move from pneumatic to electric not happened? Looking at the needs and trends it would be expected that the transformation would be far faster than it is. This might be explained by the evolution in new pneumatic technology, solving new demands with mature technology. However, the more obvious explanation is that most of the complex motion in machines is already solved with electric actuators and simple movements are easily solved with pneumatics.
And in this field, existing electric actuators have some shortcomings: they are still too costly and too complex to commission. A pneumatic system can be put into operation with moderate expertise and a screwdriver, it needs higher training, electric expertise and software know-how to make electric cylinders run between two positions. Festo took this market
COVER STORY
functionality. Therefore, it is important to concentrate on reducing the motion complexity of the Simplified Motion Series actuator to build a real alternative.
A simple movement between two mechanically defined end positions with a pneumatic actuator is done with a hard stop or cushioning and is not always 100% reproduceable in cycle time, Simplified Motion Series implements a fixed acceleration and deceleration ramp with a constant speed to realize a gently cushioned and reproduceable movement.
Pneumatics has the wonderful functionality to switch from a dynamic movement to a pressing mode without additional cost. With electrics this can only be done with programming effort in traditional electric actuators but is solved in a smart way in the new series. Here the speedcontrolled distance can be shortened, transferring it smoothly in a force controlled pressing and movement with zero programming effort.
Basic profile for movement between two end positions: with speed control
Simplified operation and control The concept of the simplicity of pneumatics with the advantages of electric actuators is extended to the control element, combining software free commissioning with state-of-theart control options for simple actuators: Digital I/O and IO-Link.
The motor is equipped with just two standard connectors and is based on the „plug and work“ principle: no software and no need to parameterise.
Providing the same ease of use, all adjustments can be set directly on the motor using 3 buttons and an easy to understand LED menu, the speed level and force level for the two directions can be set. In addition, the buttons are used to set the reference end position and the transfer point from speed to force control. Finally, all movements can be tested by Demo-Mode directly on the device. This enables all axis on a machine to be fully commissioned before the software engineer has even opened their laptop.
At its simplest, the actuators are controlled using two digital inputs, similar to a 5/3-way pneumatic valve, allowing a low-cost installation. Using two digital outputs, it is also possible to detect if the end positions have been reached, like a cylinder switch – but without the additional cost.
The most interesting feature though is IO-Link functionality integrated as standard, bringing the simple electric actuators into the world of Industry 4.0 and digitalisation. With IO-Link, all parameters can be adjusted remotely, copied on multiple drives or used as backup in case of actuator breakdown. Moreover, many process parameters like travelled distance and cycles can be read out easily for predictive maintenance use or sending to the cloud.
Finally, with IO-Link control it is possible to stop a movement at a defined position in the middle of the stroke, avoiding mechanical end stops like with pneumatics. This makes Simplified Motion Series even more flexible.
As all actuators of the series are always containing Digital I/O and IO-Link in one, it´s also possible to use the advantages of both options, like commissioning with IO-Link and control with Digital I/O.
Simple electrical connection via M12 plug design for logic and power supply
Product overview With all these features of software, free commissioning and simple control by Digital I/O and IO-Link bundled in a compact integrated actuator unit, thanks to Simplified Motion Series the simplicity of pneumatics is now combined for the first time with the advantages of electric automation, enabling machine builders to use electric actuators also for very simple tasks, bringing their machines to a new level.
Expanded movement profile for simplified press-fitting and clamping functions: with speed and force control
x x A* B C
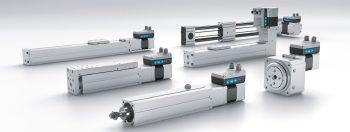