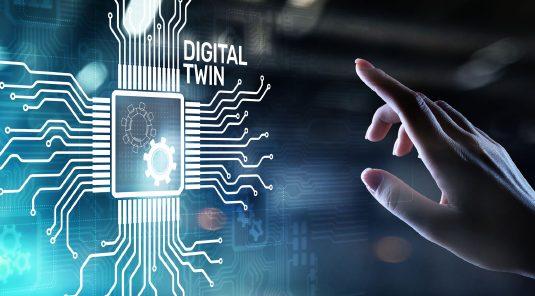
5 minute read
Is industry embracing digital twins?
DIGITAL TWINS
Embracing digital twins
Advertisement
Benedikt Rauscher, manager Global IoT / I4.0 Projects at Pepperl+Fuchs AG, believes that we are definitely on course to meet these figures. He said: “Digital twins are one of the most important and interesting applications for IoT platforms. They are generating added value during the engineering process, during integration and also during operation of plants or machines. Nearly all industrial platforms now also host digital twins or hold the data which is needed for setting up a digital twin.”
Steve Sands, product and marketing manager at Festo UK, pointed out that Digital twins have been available in different forms for several years. For example, Festo has implemented an identifier called a Product Key. Typing A Research and Markets report – Internet of Things (IoT) Digital Twinning: Market Outlook for IoT enabled Physical to Virtual Mapping and Management 2017-2022 – stated that, by 2022, 85% of all IoT platforms will embrace digital twins. Suzanne Gill finds out if industry is still on course to meet these figures. this code into the support portal or simply accessing it through a mobile device by reading a mini QR code the user can gain a detailed understanding of the product. They can draw down from the cloud the product description, images, drawings and connection diagrams, installation procedures and spare parts information. This contains information generic to the part and also individual to its manufacture such as its configuration, manufacture site and date, hardware, firmware versions etc. Industry 4.0 is driving this process further by standardising on a common format called the Administration Shell which enables data such as this to be digitally exchanged and understood in machine-to-machine communications. IIoT platforms will definitely embrace digital twins and this is already in practical use today. Work on the definition and demonstration of the Administration is intensively underway, describing the information content and providing it in UML diagram, XML, JSON and shortly OPC-UA and AutomationML formats.
I went on to ask further questions: Q: What effect are you seeing digital twin technology having on different market sectors (machine builders, systems integrators and end users in manufacturing sector)? Sands: Standardised, digital twins will be essential in making many of today’s tasks faster, easier and more powerful. Machine builders will be able to configure and create powerful simulations of components, subassemblies and machines. Multiple
DIGITAL TWINS
devices will be self-recognising and configuring for faster systems build and programming will be fully supported by a new generation of function blocks. In operation, the digital twin will again be the key to fast, easy set-up of dashboards for condition monitoring and performance optimisation – whether that be quality, productivity or energy consumption. Information in the Administration Shell is intended to be transparent throughout the machine supply chain. Rauscher: Machine builders will offer digital twins to integrators and end users creating new business models and system integrators will use digital twins of machines to simulate a plant before it exists physically to shorten installation times.
For end users, digital twins provide input data for predictive maintenance approaches or enable engineers to optimise the efficiency of their plants and machines.
Q: Do you think the adoption of digital twin technology will affect the role of the manufacturing/process industry control engineer, and how? Sands: Control engineers will be using new software and cloud-based tools to make best use of these digital twin / cyber-physical assets. At the user level these will be more familiar to today’s IT professionals, honing the communication between pieces of plant, machine-tomachine and human-machine interfaces. There is already no shortage of data, the challenge is finding the productivity insights. Filtering, aggregating and effectively communicating information at the right time to the right people. Rauscher: Digital twins are becoming a powerful tool for control engineers and are going to have a big impact on the engineering process and on the operation of a machine or a plant as well.
The digital twin needs data from the physical asset. Additional or already existing sensors have to be connected to the digital twin and the engineers have to set up this connectivity and integrate the additional data into the data platforms and the digital twins. Concepts like P+F Comtrol’s MultiLink implement additional data paths from sensors to digital twins on several data platforms. The data can be used completely independent from the critical communication between sensor and control unit.
Q: How do you think the adoption of digital twin technology will affect the future relationship between machine builders/systems integrators and their end-user customers? Sands: The founders of Industry 4.0 recognised the profound impact on people that the achievement of the vision would have. It has been considered as integral to the journey – starting with the collaboration between service providers, system developers and component manufacturers. This next generation networking needs to continue between machine builders, system developers and end-users. Some collaborative networks will want to fully grasp the vision and potential of Industry 4.0, sharing data, providing new services and sharing in the benefits. However, this is a long leap from many of today’s purchaser / supplier relationships and therefore there is likely to be a whole spectrum of speed and degree of uptake of the new technologies as they become commercially available. Rauscher: Machine builders, integrators and end users have to work together more closely as data has to be provided to the digital twin from all of them. Further, they will all be using digital twins for different purposes.
Providing digital twins offers an opportunity for automation vendors, machine builders and integrators to stay in close to their customers. This is important, as customer data is needed to continue to improve the digital twin. !
SPS 2019 Hall 3A.400
A breath of fresh air in power electronics
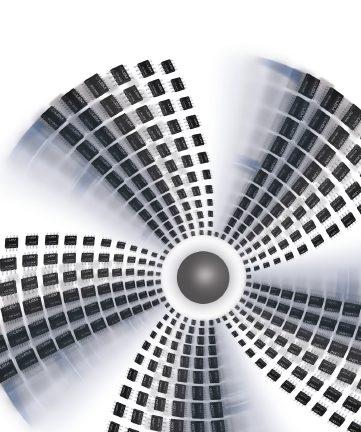
GO series

Cost-effective and accurate, miniature isolated current sensor GO speeds your drives applications. A unique sensor with an integrated primary conductor achieves optimum temperature accuracy, measuring from -40 to +125 °C in a surface mounted SO8 or SO16 package.
• 10-30 A nominal current • Better than 1.3% accuracy @ +25°C • Differential Hall principle measurement: very robust against external fields • 2 μs response time • Up to 3 kV RMS isolation • Double Over-Current Detection outputs for short circuit and over-load protection (SO16 version)
w.lem.com