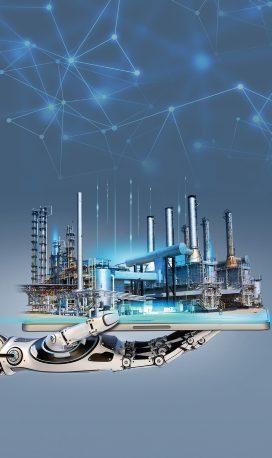
37 minute read
Release your robots to increase productivity
NEW PRODUCTS
Ultrasonic liquid flow meter
Advertisement
The Badge Meter Dynasonics TFX-5000 ultrasonic clamp-on flow and energy meters are now available from Bell Flow Systems.
Designed for non-invasive, ultrasonic transit time flow measurement of liquids, the flow meters are suited to use in water and wastewater treatment, HVAC and oil and gas applications, offering a versatile solution for measuring volumetric flow and heating/ cooling rates in clean liquids as well as those with small amounts of suspended solids or aeration, such as surface water or raw sewage.
The flow meter is available in a variety of configurations and can be selected with features suitable to meet particular application requirements.
Because it clamps onto the outside of pipes the ultrasonic device does not contact the internal liquid which offers the advantage of reduced installation time and cost, no limits on pressure or fluid compatibility.
The meter is available as a flow meter
for water delivery, raw sewage, cooling water, sea water, deionised water, waterglycol mixtures, alcohols, chemicals and many acidic or caustic fluids; or as a heating/cooling energy flow meter for use in conjunction with dual clampon resistance temperature detectors (RTDs) for temperature measurement in hydronic processes and HVAC systems Users can select up to eight parameters to log, including flow rate and total, signal strength, and alarms. A diagnostics tool takes the guesswork out of isolating process or application problems. Users are alerted to out-ofspecification flow conditions and can access a history with the most recent alarm, error and event codes.
Compact analogue transmitters
Delta Mobrey has introduced the D22 pressure transmitter and the D32 differential pressure transmitter, the first new products since starting to trade as Delta Mobrey.
The compact transmitter is said to provide a cost-effective solution for the measurement of pressure, gases, vapours and liquids in a range of applications. It is suited to use in wellhead control panels where space is at a premium. Both products are ATEX and IECEx certified for use in hazardous areas.
The D-Series analogue transmitters offer adjustability. The output signal can be adjusted through an internal zero/span potentiometer, accessible on the electronic board. The transmitters have high levels of standard accuracy, from 0.2%, with even better accuracy available upon request.
Industrial wireless network solution
Emerson is partnering with Cisco to introduce an industrial wireless networking solution that, it says, will fundamentally transform data management to improve plant productivity, reliability and safety.
The Wireless 1410S Gateway, with the Cisco Catalyst IW6300 Heavy Duty Series Access Point, combines the latest in wireless technology with WirelessHART sensor technology to deliver secure data, even in the harsh industrial environments.
The wireless access point provides enhanced wi-fi bandwidth for realtime safety monitoring, including Emerson’s Location Awareness and wireless video. These applications enhance personnel safety practices, improve plant security and help ensure environmental compliance.
Rugged DIN signal isolator
The UL Approved ECT-DIN 2-Wire Isolator from Moore Industries is now available in a narrow 15mm aluminium housing.
The thinner ECT-DIN 2-Wire Isolator with 15mm width retains the same general and hazardous area approvals as the rest of the ECT family of isolators and has the same RFI/ EMI protection and -40°C to +85°C operating temperature range. The ECT-DIN 2-Wire Isolator can be installed in hazardous locations and does not require installation in climate-controlled environments, making it perfect for more extreme locations.
The 15mm ECT DIN 2-Wire isolator and converter with 4-20mA, 1-5V and 0-10V inputs and 4-20mA output, allows more isolators to fit in cabinets and field enclosures where installation space is limited, saving space and money. An
optional externally-mounted flange provides a secure mount, which ensures secure installation in high vibration environments. The ECT is UL approved Class I, Division 2, Groups A, B, C & D T4. A variety of the isolators are available to match the type of AC or DC power available at each location. ECT-DIN 2-wire Output-Loop powered models, ECT 2-wire Input-Loop powered models, or 4-wire (line/mains) powered isolators/ converters and splitters are also available.
thread throughout the project.”
In light of all of this, Leonardo chose Rockwell Automation and its PlantPAx DCS which made it possible to combine all of the control systems in a single platform. Now the central control system for the ships is managed by the Automated Integrated System (AIS), as are the turbines and turbopumps.
Leonardo’s technicians were already familiar with the hardware elements of the PlantPAx solution, meaning that the migration project could be completed without the need for any field rewiring. In collaboration with the Rockwell Automation team, an identical mock-up of the software solution destined for the ships was created on land. This allowed for in-depth functional tests to be undertaken to check that the new system’s functionality was identical to previous levels, making it possible to study possible improvements in the solution and new functionalities
with the help of Rockwell Automation specialists.
The land-based inspection phase made it possible to arrive at the commissioning phase with the onboard software operationally ready and it also overcame the problem of working with two ships located in two different shipyards. For the LNG Portovenere, commissioning took place in January 2016 at the Navantia shipyard in Ferrol, while the commissioning of the software on the LNG Lerici took place in 2018 at the Keppel shipyard in Singapore.
The decision to use the PlantPAx DCS also made it possible to include the emergency shutdown system for safe functioning. A remote service line was installed with a satellite internet connection, to deliver continuous support during navigation. It also gave Leonardo the opportunity to offer continuous assistance during operations, along with support for
PROCESS CONTROL
troubleshooting to maintenance personnel.
“Energy consumption has also been reduced thanks to the new generationcontrol system. Basically, using the PlantPAx DCS, we enjoy double advantages: in addition to progressing from a legacy system to a modern one, today we also have a single system instead of three separate systems, with improved performance and speed,” said Baccelliere.
Having combined all the systems into a single platform also means having a single supervision and control system – in this case based on FactoryTalk – a faster solution in respect of refresh times for the graphic pages and more intuitive for operators.
From an assistance and maintenance standpoint, the ships are now equipped with a remote service system with a satellite internet connection. !
WHILE OTHERS THINK ABOUT THE IIOT
… we are already there.
Networks and computers for a smarter industry.
Powerful computers designed for your needs Secure and reliable networks – anywhere, anytime Vertical intergration from SCADA to field device
Moxa. In the middle.
INDUSTRIAL COMMUNICATIONS
Today ‘smart’ field devices have become the eyes and ears of automation. They provide ever more information and transmit it, via bus systems, to other components in the control network. However, the failure of a device can quickly lead to a malfunction of production equipment.
Traditionally, asset performance monitoring approaches involved monitoring devices for evidence of incorrect operation, pending failure or the need for calibration. This was undertaken with asset management programs or custom-written programs hosted on a desktop or client/server architecture based within a single facility. Today’s IIoT-based asset management solutions typically include condition monitoring, predictive maintenance, asset integrity management and reliability-centered maintenance, and often involve technologies such as asset health data collection, visualisation, and analytics. They improve upon traditional asset management through deeper integration with ERP and computerised maintenance management systems (CMMS) – driving efficient and accurate maintenance work orders.
Accessible from smart mobile devices, IIoT-based solutions provide immediate awareness of performance/health issues. The tools also make documentation and diagnostics immediately available.
The collection of data at a central point in the cloud has key benefits for the transparency and analysis of asset performance information. By establishing a single infrastructure to support multiple facilities, organisations can leverage global expertise, spread ASSET MANAGEMENT MOVES TO THE CLOUD FDT is transitioning into an information exchange platform which will enable cloud-based asset monitoring for field devices. Suriya Selvaraj reports.
costs between different stakeholders, and improve overall system availability. Centralised data access allows users to run various statistics to offer a comparison/benchmarking of individual production lines or plants. This allows an expert at one location to provide more value by being able to consult with other facilities.
In addition, the use of mobile devices for viewing data allows operators to react quickly to unexpected events, changing environments, and continually optimise their bottom-line results. Optimising assets The specialised equipment required for industrial manufacturing has become a focal point for concerns about operational efficiency, preventive maintenance, and costly failures. This explains why cloud-based asset management solutions are becoming an essential tool for operating companies of all sizes. FDT is the industry’s most widely deployed asset management solution, with tens of millions of FDT/DTMenabled devices in use and hundreds of thousands FDT/FRAME-enabled host/ systems installed worldwide. Experience has shown that FDT/DTMs are a universal tool for lifecycle management of any device/network in the process and discrete automation markets. Indeed, they are intended for smart devices providing data-driven business intelligence.
The emerging FDT IIoT Server (FITS) standard – set for release as part of the FDT 3.0 offering – will further empower the intelligent industrial enterprise with native integration of the OPC Unified Architecture (OPC UA), as well as Control and Web Services interfaces for mobile applications. FITS encompasses a robust security solution to safeguard critical automation information and operating data. The standard provides enhanced protection measured via robust multilayered security, and leverages industry standards such as Transport Layer Security (TLS), Web Sockets Secure (WSS) and Hyper Text Transfer Protocol Secure (HTTPS).
Platform independence allows FITS to be utilised in a host of operating within the .NET Core framework. This results in an FDT Server that is deployable on Microsoft, Linux or iOS based operating systems. The solution enables cloud, onFITS Architecture – FDT Server deployed in the cloud with cloud-based FDThub DTM repository access.
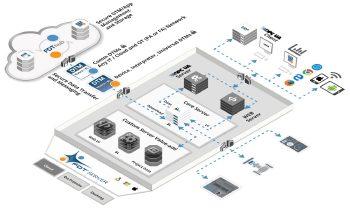
INDUSTRIAL COMMUNICATIONS
premise, edge and desktop deployment methods meeting the needs of the process, hybrid and discrete sectors.
The FDT Server is built around a Core Server, which serves as a center point for range of client/server interactions. It includes an OPC UA Server providing access to DTM data with authenticated OPC UA Clients, and a Web Server enabling the use of web user interfaces on remotely connected, browserbased clients and mobile devices. The solution also supports the use of apps that improve workforce productivity and plant availability. Users can connect an FDT Server in the cloud to one or more plants with a secure virtual private network (VPN).
A key feature of the FITS platform is a cloud-based DTM repository, which enables all certified DTMs (based on FDT 3.0) to be automatically downloaded from the cloud for use in on/ off premise and desktop applications. The repository provides DTM/App storage and device management, as well as secure data transfer and messaging with proactive user alerts when DTM updates are available. The repository eliminates the headache of distributing DTMs.
Operational advantages With the FITS solution, industrial asset management becomes more empowered, thanks to better diagnostics and easier access to device information, reducing downtime improving meantime to repair (MTTR) performance. Users will be able to take advantage of secure and seamless data exchange/ interrogation from sensor to cloud and achieve new levels of information technology (IT) and operational technology (OT) integration.
All DTMs based of FITS comply with the NAMUR NE-107 recommendation, which stipulates that operators need a view of the process including the status of the instrumentation in a simple and uniform way – regardless of source device – to support predictive maintenance strategies.
Its platform-independence means that FITS will benefit companies that operate plants with a diverse array of automation systems and devices. It supports real-time monitoring and predictive maintenance applications requiring uniform access to field devices across platforms.
With FITS, field device data and information can be automatically provided for transport into cloud-based applications. This opens up the way for condition monitoring functions to be realised as cloud-based applications – independent of the automation system. The collected data can also be transferred for further processing in monitoring systems.
Going forward, adoption of the FITS platform will also create opportunities for asset management as a service, with service providers completely managing the cloud environment and implementing a variable cost model based on the number of users and assets to be covered. !
Consistent quality

Mitsubishi Electric’s new automation system helps eliminate picking mistakes in manual assembly processes. Operators are actively led through each assembly step using LED indicators or with automatically opening shutters that require acknowledgement following a successful pick. Based on versatile terminals which can be easily connected to ERP and production systems, the application supports you in achieving your specific manufacturing objectives.
See our Guided Operator Solutions in action: eu3a.mitsubishielectric.com
INDUSTRIAL COMMUNICATIONS
GET SMART BUT STAY SAFE
Find out more about CIP Security – an enhancement to EtherNet/IP technology to address cybersecurity – which allows devices to defend themselves using industry standard, widely adopted technology. D evice level security is a crucial component in industrial digital transformation as Ethernet continues to take over from traditional fieldbus networks.
Indeed, HMS Networks estimates that industrial Ethernet now makes up 59% of new nodes installed on the factory floor today.
Ethernet will become commonplace in process plants as well with the current work being done on the Advanced Physical Layer for Ethernet, also known as Ethernet-APL, which will be capable of installation in all zone and division locations with 1,000m cable lengths.
The benefits of having Ethernet down to the device level and up to the cloud include economies of scale, fewer gateways, streamlined commissioning, and quicker error resolution. Ultimately, ubiquitous Ethernet will drive cost effective operational technology (OT) and information technology (IT) convergence, cloud connectivity, and device analytics.
However, as soon as a formerly isolated industrial network is connected externally, security becomes an imperative because it is not a question of if, but when an attack will come. This is where CIP Security, the security layer for the EtherNet/ IP industrial communication network, comes into play. CIP Security is the last level of defence that is designed to keep workers, assets, and intellectual property safe and secure. strong policies, physical protections, network infrastructure, and equipment security. Multiple layers of defence can slow down a bad actor enough to allow it to be noticed before serious damage is done and such a system can also reduce the desirability of a network as a target. Note that there is no such thing as an impenetrable security system. The goal is to create a system that is hard enough to break into relative to the value of what is being protected to motivate a bad actor to simply move on. CIP security CIP Security – the enhancement to EtherNet/IP technology to address cybersecurity – allows for devices to defend themselves using industry standard, widely adopted technology. CIP Security was designed using Transport Layer Security (TLS), the same secure communication standards used in online banking, and is intended to be applied in industrial automation and control systems. The IEC 62443 family of standards are the leading cybersecurity standards recognised worldwide and contain minimum requirements for building secure automation systems. CIP Security addresses some of the hard-tomeet system-level requirements in those standards, such as: • Identity: Is the sender actually who they say they are? • Integrity: Is the data complete? Has the data been changed? • Authenticity: Did the data originate from the expected sender and in a complete, unchanged format? • Confidentiality: Is an unauthorised party viewing the communication? CIP Security allows a certificate to be embedded into the device to identify itself. The certificate provides a verifiable root of trust. When a network connection between devices is initiated, a ‘TLS handshake’ is used to exchange the certificate. This is similar to how web browsers work. These certificates are used to identify the device and determine if trust should exist between the devices. At the end of the process, the devices share a secret key that can be used for secure communications and
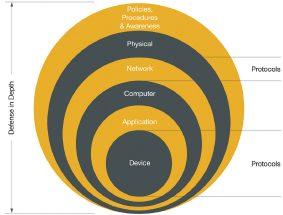
Defense in depth A best in class security strategy focuses on creating multiple hurdles instead of a single fortification that is difficult, but not impossible, for attackers to get past. This defense in depth concept includes
to authenticate that each message has been sent from the correct device and that the data has not been modified. The CIP Security standard uses the Hashed Message Authentication Code (HMAC) which is commonly used with TLS and DTLS communications. If an imposter device tries to send the data, or a man-in-the-middle tries to modify the data, the HMAC will not be valid. Not all automation data on the network needs to be encrypted, so to avoid overhead on the communication process, encryption is optional. If confidential process information or secret recipes are being sent, every packet can be secured with the TLS and DTLS encryption.
CIP Security has recently been enhanced to allow devices to perform certificate enrollment directly for easier initial commissioning of devices. In contrast to the practice of pushing certificates out from a configuration tool, this ‘pulling’ functionality will
INDUSTRIAL COMMUNICATIONS
allow devices to actively request certificates, resulting in improved productivity. The enhancements allow for increased efficiency with timeout responses, increased protection by allowing for a mandatory CIP Security connection for changes, and expanded behaviours for certificate verification. Work is ongoing for the next phase of development of CIP Security, which will add support for user authentication, non-repudiation, and device authorisation. The ultimate roadmap of CIP Security development is to enable EtherNet/IP devices to become autonomous, taking responsibility for their own security and effectively securing themselves from attack.
Conclusion Understanding where to add extra layers of security in a factory is critical. Portions of the industrial network are opened up the cloud to enable predictive maintenance and quality improvement. Other parts contain critical intellectual property. Still others include control of machines that workers interact with regularly and could be hurt if improper signals were sent. Finally, there are areas where incorrect commands could lead to significant product loss or even environmental catastrophe. Some parts of the network are so critical that they are closed off from other areas or are located behind a firewall, but even these areas are still vulnerable to determined attackers. It is clear that the most sensitive areas of a network require the highest level of protection. It I here that CIP Security controllers and devices are a must have to provide a crucial final layer of defence. !
A CIP Security Demonstrator will be on display on the ODVA stand in Hall 5, stand 338 at the SPS event in November.
Make your life easier.

Use the zenon Software Platform to automate your Smart Factory:
` ` ` ` Instant reporting and analytics Ergonomic visualization and control Comprehensive data acquisition and management Quick application engineering and maintenance
www.copadata.com/zenon
INDUSTRIAL COMMUNICATIONS
FOCUSING ON BUS TECHNOLOGY T he network will ultimately determine the entire control architecture – a relatively slow network requires closing of the faster control loops in decentralised devices, while a highperformance network enables engineers to freely decide whether to use centralised or decentralised architectures. A well-accepted network should provide the freedom to select components from a large variety of vendors while a network dominated by a single automation giant will often reduce choice.
So, how do control system integrators or machine builders select their communication network? I do not believe that the majority of users actively select their fieldbus at all – they select the control system vendor and assume that whatever bus system this vendor provides will ‘do the job’.
But how about those users that start their control system evaluation by taking a closer look at the bus technology itself as the key component of their system? Many users that compare technologies in detail find the functional principle of EtherCAT compelling. With EtherCAT, the Ethernet packet is no longer received then interpreted with process data copied at every device. Instead, field devices read the data addressed to them while the frame passes through the node. Similarly, input data is inserted while the datagram passes through. With this ‘processing on-the-fly’ technique the frames are hardly delayed at all. As a result, an EtherCAT frame The communication network is one of the most important technological components of a machine or plant control system. Martin Rostan offers some food for thought about how the fieldbus choice is made.
comprises the data of many devices both in ‘send’ and ‘receive’ direction within one Ethernet frame and the usable data rate increases to over 90%.
Husky, an injection moulding machine manufacturer, reported that by using EtherCAT it was possible to reduce part weight variation which helped reduce the wall thickness of plastic cups produced on the machines. This has resulted in material cost savings of over $180,000 USD per machine, per year for Husky machine users.
It is not just closed-loop controls that benefit from faster communications: in many applications there are so called ‘transitions’, where one has to wait for the part to arrive, the cylinder to reach its end position, or the pressure to reach a certain threshold. With a faster network, waiting times are reduced and the throughput of the machine or plant is increased – increasing efficiency a few percentage points can be easily achieved this way.
EtherCAT is not only fast, it is also precise: thanks to the distributed clock mechanism, measurement values can be sampled and outputs set in a synchronised manner network wide – and with a jitter smaller than one microsecond. This accuracy makes it well suited for use in synchronised motion control applications and for the integration of measurement tasks within the same network.
Increasingly, system integrators and machine builders want to integrate functional safety in their control architecture – and not just to reduce wiring. Conventionally, safety functions have been realised separately from the automation network – either via hardware or using dedicated safety bus systems. Safety over EtherCAT, however, enables safety-related communication and control communication on the same network. Flexible and open EtherCAT also offers flexible topologies that can simplify planning and installation. EtherCAT networks have no practical limitations regarding the topology – line, star, tree, redundant ring and all those combined with a practically unlimited number of nodes per segment. Even wireless technologies can be integrated and the ‘hot connect’ feature which allows users to connect and disconnect nodes or entire network segments during runtime.
To address issues of migration from a legacy bus system a large selection of EtherCAT fieldbus gateways are available to help integrate existing devices with a legacy fieldbus connection into an EtherCAT network and establish interfaces to ‘neighbouring’ or higherlevel systems. ! Martin Rostan is executive director at EtherCAT Technology Group. Process data is inserted and extracted on the fly: the unique functional principle of EtherCAT.
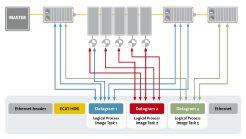
PRO SolCom Process Communications Solutions
Convert your mobile device into a full featured HART communicator.
ProComSol, Ltd is a leader in the design and manufacture of advanced, cost-effective, and reliable HART communication products for the Process Control marketplace. +1.216.221.1550 sales@procomsol.com procomsol.com
Your Global Automation Partner
Local Decision Making ARGEE Field Logic Controller
Multiprotocol block I/O devices that act as simple I/O devices or as stand-alone logic controllers. Field Logic Controllers can be used without a PLC in standalone applications, perform arithmetic, timing and counting functions and share data with a PLC. ARGEE challenges what an I/O device can do by creating a hybrid between simple block I/O and higher level PLCs, keeping intelligence and control local to the machine.
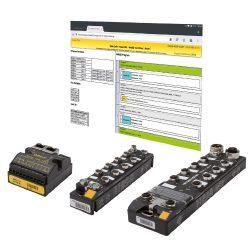
EXHIBITION PREVIEW
Welcome to Smart Production Solutions
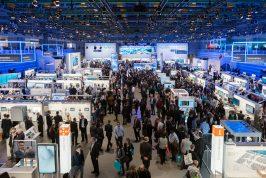
Around 1,650 automation technology providers from all over the world will showcase their latest industrial automation offerings at the SPS - Smart Production Solutions exhibition, which takes place in Nuremberg from 26 – 28 November 2019. T he event will once again focus on the digital transformation of industry, with exhibitors demonstrating a wide variety of products, applications and services.
With the focus moving onto topics such as big data, cloud technology, 5G and artificial intelligence (AI), every year the event attracts more Information Technology (IT) providers. There is also a growing presence at the show of topic-related showcase stands – with automation vendors working together to illustrate digital transformation in the manufacturing industry. Siemens is using the event to present a series of industry-specific applications and future technologies for digital transformation in the manufacturing and process industries. Under the slogan ‘Digital Enterprise – Thinking industry further!’ the stand will feature products, solutions and services from the company’s Digital Enterprise portfolio.
A newly developed system for industrial operation and monitoring will be introduced. The web-based visualisation system comprises Simatic WinCC Unified visualisation software and a new generation of Simatic HMI Unified Comfort Panels. Sinumerik One is said to offer a CNC system for the digital age. By seamlessly combining the virtual and real world, this system makes machine tools more productive, reduces time-to-market and increases machine performance. Siemens will also present new CloudConnect products which enable data to be transferred quickly, easily and securely from plant to cloud. Siemens will also introduce CloudConnect products which enable data from each plant to be transferred quickly, easily, and securely to the cloud. It will also demonstrate PlantSight, a cloudbased portal for all plant information. With this solution, data can be efficiently consolidated, contextualised, validated and above all visualised to create a seamless digital context across a range of information sources and data formats. Plant operators can benefit from the resulting increase in operational availability and reliability of their plants.
Siemens will introduce a newly developed system for industrial operation and monitoring – a webbased visualisation system which initially comprises Simatic WinCC Unified visualisation software and new generation Simatic HMI Unified Comfort Panels. The new system provides the user with a solution for HMI and SCADA applications and in the future also for industrial edge, cloud and augmented reality scenarios.
Softing Industrial Data Intelligence will present its dataFEED OPC Suite with Store And Forward functionality which is able to temporarily store affected data in the event of an interruption of the OPC UA connection.
dataFEED OPC Suite is a modular user interface with intelligent, practiceoriented pre-settings and an intuitive user interface which enables easy and fast configuration of the data exchange.
The new version V5.00 of dataFEED OPC Suite automatically detects any interruption in the connection to an OPC UA Client and ensures the recording of the data can be transmitted for up to one hour. As soon as the OPC UA connection has been re-established, the data is transferred to the OPC UA Client with a correct time stamp.
This new functionality is fully integrated in dataFEED OPC Suite. It can be used with any OPC UA Client and does not require a special OPC UA Historical Access Client for data caching. Using Store And Forward does not affect the security features supported by the OPC UA technology.
Softing will also show smart gateways for multi-protocol process control and a mobile plug & play solution for configuration and maintenance of field devices. > p26
SUPPORT + SUCCESS You optimize your process for maximum safety, reliability and e� ciency, with minimum impact on the environment. We off er process application expertise through our products, solutions and services.
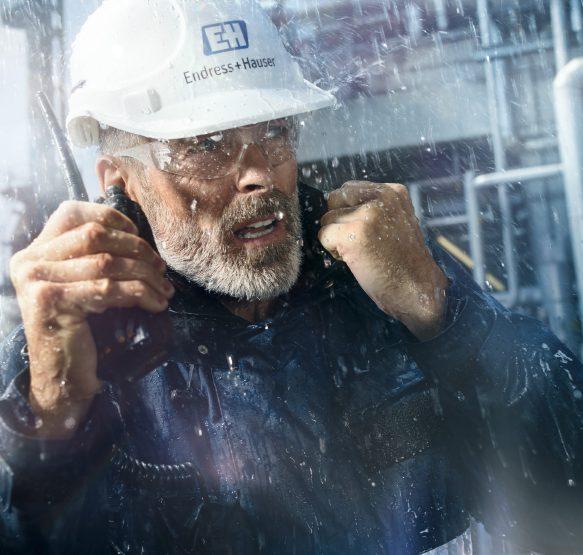
Customers around the world trust us when it comes to process automation. Our shared goal is plant safety, availability and e� ciency. We are with you every day, everywhere.
People for Process Automation
Visit us at SPS 2019 Hall 4A, Stand 135
EXHIBITION PREVIEW
Mitsubishi Electric’s motto for the show will be ‘Your solution partner for smart manufacturing’. On the stand the company will be demonstrating its latest range of automation products and technologies including predictive maintenance, Time-Sensitive Networking (TSN) and collaborative robotics.
Help in handling big data using edge computing will feature prominently on the stand, in addition to the wider application of AI for improved machine and systems intelligence. The realisation and application of these technologies is aided through collaborations with e-F@ctory Alliance partners. There will also be a focus on machine building, with several product developments offering improvements in performance and integration. Distec GmbH will introduce new compact TFT display modules – POS-RP (-PRO), POS-4K-PRO, and POS-IQ-PRO for the Internet of Things (IoT) – designed to meet the needs of applications in harsh environments. The plug-and-play TFT display solutions are installed in a milled aluminum front frame with a stainless-steel chassis and offer front-side IP65 protection against dust and water jets. They can be integrated easily and quickly into various applications, says the company.
The POS-RP series is controlled by the Raspberry Pi based Artista IoT TFT controller with the latest Compute module CM3 or CM3 +. Users can easily program their own applications or use one of the many operating systems supported by Raspberry Pi. WEG will demonstrate a new gateway for industrial-scale condition monitoring and will show its expanded automation portfolio.
The Motor Scan condition monitoring solution was first shown last year as a retrofit option. It enables real-time monitoring of WEG electric motors for predictive maintenance purposes. The collected data can now be transferred to a secure cloud using gateway technology, in addition to the previous option of using a smart device app with Bluetooth. Users can access the data in the cloud through the app or the WEG IoT Platform web portal. This enables detailed analysis of the monitored motors. The gateway complements the existing mobile app and acts as a router that captures all installed sensors within a range of approximately 30m in an industrial environment.
Other stand highlights will include the updated CFW500 and MW500 variable speed drives. The new CFW500 IP66 in frame sizes A and B covers motor power ratings from 250 W to 15 kW. These variable speed drives can operate over a wide voltage range and can be deployed at ambient temperatures from -10°C to +40°C and in demanding environments. The MW500 variable speed drive, which is designed for decentralised deployment, has also been updated. It is now available for lower power levels in the range of 370 W to 2.2 kW and is being launched for 380 to 400 V mains voltage in frame sizes A and B. A sturdy housing design with protection rating IP66 or NEMA 4X allows the variable speed drives to be mounted directly on the motor terminal box or on the wall using an adapter plate. This eliminates the need for a motor feed cable and switch cabinet, reducing complexity and costs for installation and commissioning. A wide range of smart digital automation solutions will be shown by Beckhoff. Innovations will include the XPlanar transport system with freefloating movers for intelligent product transport. These planar movers offer jerk-free motion without contact at up to 4m/sec over planar tiles which can be arranged in an arbitrary layout. Travelling magnetic fields provide for exact and highly dynamic positioning. Also on show will be a machine optimisation solution in the form of TwinCAT 3 Machine Learning, Beckhoff now integrates machine learning (ML) into the overall control system. A trained model can be exported in a standardised format (ONNX) and executed in the TwinCAT runtime. This opens up optimisation potential and new possibilities in predictive maintenance, process control or automated quality control. TwinCAT Analytics One-Click Dashboard will be abother focus on the stand. With just one click this makes it possible to achieve dramatic time savings. Where previously several hundred clicks and work steps were required for HMI design, the new TwinCAT Analytics One-Click Dashboard (OCD) reduces this to a single click. The Analytics configuration automatically generates PLC code for continuous machine monitoring and the dashboard showis the analysis results in an individual design including specific controls and language switching. Drawing on a long heritage of expertise in analogue, mixed-signal and digital semiconductor technology, Analog Devices (ADI) will launch an industry-first portfolio of Industrial Ethernet solutions to address communication challenges within Industry 4.0, Smart Factories, and the digital transformation.
This new portfolio will encompass a range of Industrial Ethernet technologies for building robust, scalable Ethernet connectivity solutions. Designed both today’s industrial networks and for tomorrow’s TSN-based systems, this portfolio is said to offer flexibility, scalability and speeds to support any topology and network architecture in the factory. !

INDUS TRY-LE A DING SCALABLE ETHERNET. TIMED TO PERFECTION.
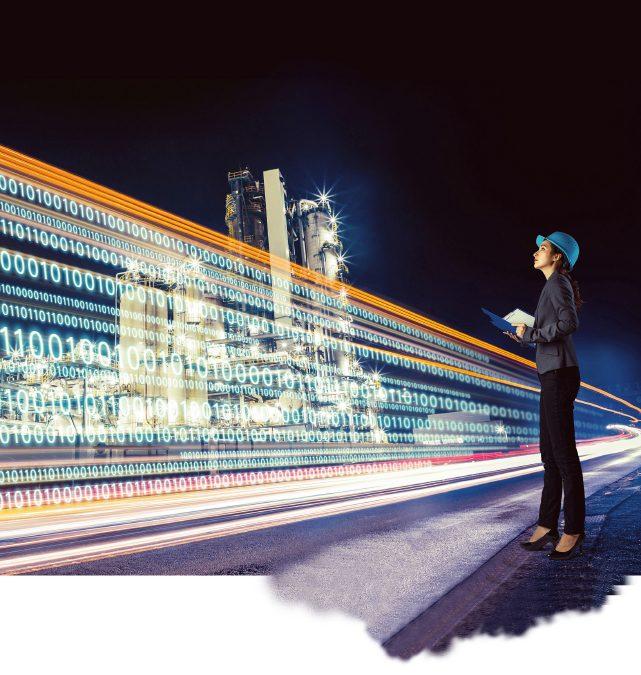
ANALOG.COM/ INDUSTRIAL-ETHERNET We Turn Your Vision of Connected Factories into Reality. Analog Devices´ new family of compatible and interoperable industrial ethernet connectivity products enable best-in-class industrial automation solutions for the connected factory of tomorrow. From complete Time Sensitive Networking solutions for high-performance motion control to innovative 10Base-T1L concepts for robust field instrument connectivity – our market-leading and industry-first ethernet portfolio of software and hardware are scalable and timed to perfection. Designed from ADI’s rich factory expertise and system design knowledge, ADI’s ethernet solutions pave the way for intelligent industrial connectivity to turn your vision of the connected factory into reality.
ROBOTICS
RELEASE YOUR ROBOTS TO INCREASE PRODUCTIVITY
There are thousands of industrial robots used in manufacturing, processing and packaging applications that take-up a great deal of floor space, simply because of outdated safety provisions. Moving to proximity-based safety can release space and improve production efficiency by allowing more freedom of movement on the shop floor, says Oliver Giertz. P hysical cages with safety interlocks and frames with light curtains take-up valuable floor space and obstruct the movement of personnel and equipment around them. While a robot will increase productivity by performing repetitive tasks quickly without stopping, the space around them is holding back potential logistical efficiencies.
Releasing the value in existing manufacturing floor space clearly requires investment. Hence, there is a balance to be struck between the added capacity and logistical efficiency to be gained, and the cost of updating the robot cell. For users of Mitsubishi Electric’s MELFA Series of articulated arm robots it is possible to move away from physical cages without needing to change the robot.
A complete stop of the robot is required for service and maintenance work, it is also required when personnel are working in close proximity to the robot’s reach of movement. Often for loading and unloading tasks or checking individual processes and inspecting work done after a changeover. A full cage is helpful to the operator, because the robot is effectively shut down as the barrier is broken. However, the startup time after the person has left the area can be significant, so time is lost and another opportunity to improve efficiency presents itself.
By using dedicated proximity sensors, it is possible to slow the robot down to a safe speed while personnel work close by, and then bring the robot to a controlled stop quickly if the person enters the same physical workspace as the robot. In this way tasks such as inspection and loading can be carriedout next to the robot, while the robot moves slowly and can stop if necessary. Service and maintenance full stops can be achieved easily from the robot controller, for this reason a cage is not required.
The major advantage – apart from removing the cage and freeing up floorspace – is that using this methodology, the robot can return to full-speed quickly after a period of safer low-speed operation. The transition takes seconds; rather than the minutes required to restart an entire production process if a robot cell has to be stopped by entering a safety interlocked cage or hitting an e-stop button.
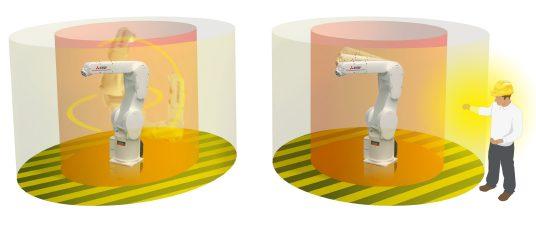
ROBOTICS
Making it possible There are several innovations that make this possible, among them are Mitsubishi Electric’s MELFA SafePlus option, for example, ensures the robot will respond to the new safety regime. With no physical barrier, the safety sensor has to work with additional safety measures to ensure contact is avoided, and if it happens while the movement is slowed down, then the robot stops immediately. Safe Limited Speed (SLS), Safely Limited Position (SLP) and Safe Torque Off (STO) form the basis of achieving the progressive shutdown process. The proximity sensor allows for an adjustable zone system to be created around the robot, this provides feedback that can be used to limit the position, torque and speed of the robot as the human approaches. Safety light curtains and lasers can also be used as secondary feedback options, improving the failsafe modes. The aim is to make a robot cell as small and compact as possible with optimum safety provision. More activity can happen around a robot and the space allows for far more efficient production area logistics. The robot goes from high-speed to slow-speed and back again quickly, allowing both the robot and the human to work quickly and efficiently without stops.
Better robot safety and interaction solutions allow for a continuous work process, maximising the robot’s potential for speed, accuracy and repeatability, while maintaining safe human access and interaction to achieve optimum overall productivity. !
Oliver Giertz is product manager for Servo/Motion and Robotics, Factory Automation EMEA, Mitsubishi Electric Europe B.V.
Ford Dagenham automates operations with robots
Ford Dagenham in the UK has invested in UR10 Universal Robots from RARUK Automation to automate a manual task – applying fasteners to engine blocks. Today the fasteners are applied automatically to engines that arrive on the production line every 30 seconds, across a 24-hour, three-shift operation by seven robots.
Until recently, the task of securing exhaust manifolds to engine blocks using M8 studs and nuts, as well as different types of barrel nut, was performed manually using an electric screwdriver. However, to improve cost efficiency and reduce RSI, the company identified the process as a suitable candidate for automation. As up to six studs and nuts require application on each engine block, the potential savings were notable. A vibratory bowl feeder is deployed to offer up individual fasteners, which are blown through a tube using compressed air to an escapement. From here, a dedicated screwdriver tool bolted the flange of the robot picks up the fastener and runs it down the thread in the engine block to secure the exhaust manifold in position. Development of the process and application was fully supported by RARUK Automation, including training.
The UR10s at Ford Dagenham are currently being deployed as ‘cohabitant’ robots rather than true cobots. This has avoided the need to reorganise and recertify the production line from a safety perspective, saving time and cost.
Hall 7a Booth 330
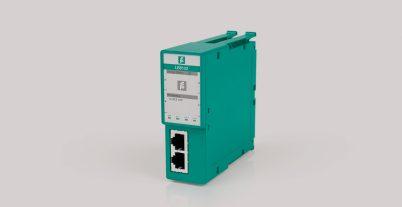
Modernizing plants. Reducing installation space. Improving operational efficiency.
LB PROFINET-Gateway – Opening the Door to IIoT
Cost effcient connection of analogue sensors and actors to modern DCS Seamless integration of device and process data Real-time communication with the control system increases transparency and plant availability Ethernet-based gateway handles large amounts of data at high speeds HART-IP supports asset management
PRODUCT FORUM •
www.controlengeurope.com to read the full story
Alarm systems management Complex industrial systems require complex control systems – but carefully thought out alarms systems
EEMUA is the acknowledged leader in the field, with EEMUA 191, ‘Alarm systems - a guide to design, management and procurement’, being regarded as the benchmark in alarm systems management.
The EEMUA Alarm Systems e-learning module provides an introduction to EEMUA 191 and is positioned at the awareness level. It offers simple and practical guidance to managers, designers, supervisors and operators on how to recognise and deal with typical human-factor problems involving alarm systems. Its scope covers many sectors, including the energy, process and utilities industries.
The e-learning is recommended for both discipline and project-focused engineers from a variety of backgrounds who want to gain an introduction to the fundamental principles for design, management and procurement of alarm systems. The course is also relevant to engineers and managers from operating companies as well as specialist contractors and equipment suppliers.
Visit the EEMUA website for further details.
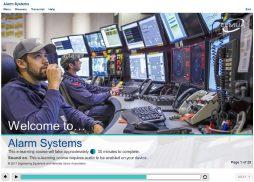
www.eemua.org
Creating a successful control environment
Know what you want, plan what you’ll get, check that you’ve got it!
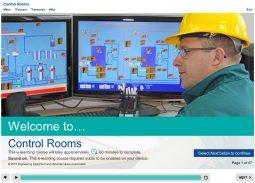
The EEMUA Control Rooms e-learning module provides guidance to engineers and the wider teams involved in the design of control rooms, control desks and consoles. It will help during new-build and modification projects, as well as evaluating existing set ups where people operate industrial processes and activities on facilities such as chemical plants, power stations and oil refineries.
The e-learning will benefit anyone with an interest in process plant control rooms and control desks using Human Machine Interfaces.
It is especially relevant to control engineers, control room console (and HMI) designers and vendors, control room operators, engineering consultants, engineering contractors, engineering managers, facilities managers, graduate engineers, plant operations managers, process safety managers, SCADA engineers and systems support managers. Visit the EEMUA website for further details. The e-learning is positioned at the awareness/introductory level and is an optional precursor to working through EEMUA 201, ‘Control rooms: A guide to their specification, design, commissioning and operation’.
www.eemua.org
PRODUCT FORUM •
www.controlengeurope.com to read the full story
Diamond Processing Industry Goes Digital
• Thanks to a partnership with relayr, Coborn is adding new digital services to their diamond grinding machines which will improve product performance and therefore increase asset utilisation for the customer. • The long-term strategic alliance will also add an innovative pay per use model which will make financing Coborn grinding machines easier for UK and European customers. Romford based Coborn Engineering Company Limited, a global provider of engineered solutions for the diamond industry, and Berlin located relayr, a specialist for industrial solutions in the field of Internet of Things (IoT), have formed a strategic alliance. The purpose of this long-term partnership is to develop Coborn’s diamond grinding machines into smart equipment by installing digital services in their products.
Thanks to anomaly detection through relayr’s AI-based analytics, data collected from Coborn’s machines will allow them to determine and resolve failures in advance. Delivering pre-emptive service to each diamond customer will enable Coborn to offer machines with guaranteed performance and availability targets. Each machine will also
come with an insurance policy to support these guarantees. As an additional feature, Coborn will be offering a pay per use business model for its equipment, also known as an Equipment as a Service (EaaS) model. Partnering with relayr will enable Coborn to deliver business solutions to their customers through a unique blend of technology, finance, and insurance offerings. This unrivaled approach will provide a distinct level of tailored customer support and services whilst guaranteeing the uptime of Coborn’s Intelligent Machines. In turn, Coborn customers will be able to increase their productivity and receive exactly the services they need. www.relayr.io/coborn/
Rotork has increased the versatility of the CK range of modular electric valve actuators with the introduction of the CK Atronik, an intermediate level integral control option, providing a ready-to-operate actuation solution.
The CK Atronik control module houses a reversing contactor starter with mechanical and electrical interlocking, a proven and reliable Rotork design for electric actuation. Connection to a suitable power supply is all that is required for local operation of the actuator.
Digital microprocessor driven functionality delivers motor control for isolating, regulating or modulating valve duties. Configuration is simply achieved with on-board dual inline switches. Integral local control selectors are provided, together with clear LED status indication of valve open, valve closed, valve moving and alarm. Mechanical valve position indication is also provided on the actuator gearcase. Options include analogue control for positioning, analogue feedback, additional relay and network bus connectivity.
All CK modular actuators are environmentally sealed to IP68 (8 metres for 96 hours) as standard for reliability in harsh operating conditions. Plug and socket connections for power, control and between modules assist swift site wiring and maintenance. www.rotork.com/en CK Atronik increases integral control versatility of Rotork modular electric valve actuators
TO BE FEATURED IN THE CEE PRODUCT FORUM
Contact Adam Yates on 01732 359990 07900 936909 or email Adam.Yates@imlgroup.co.uk
Safeguard Your Facility with Layers of Protection

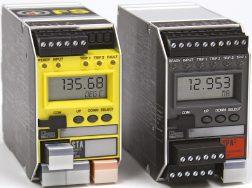
Now Get Moore Industries Alarm Trips with Intrinsically-Safe Field Connections
Moore Industries’ family of rugged and reliable alarm trips now includes the SPA 2 IS for process areas requiring intrinsically-safe methods of protection. The newSPA 2 IS alarm trip lets you directly connect temperature sensors and transmitters in Class I, Div1 or Zone 0,1 hazardous locations without having to use intrinsically-safe barriers, cutting wiring and maintenance expenses.