
12 minute read
David Morgan Product Review
Natural Origins In this issue, David Morgan inspects Orluna’s Fade Adjustable downlight fitted with the new Origin Natural light engine, following its debut at [d]arc room livestream.
David Morgan Associates, a Londonbased international design consultancy specialising in luminaire design and development and is also MD of Radiant Architectural Lighting. Email: david@dmadesign.co.uk Web: www.dmadesign.co.uk A 50-year business trajectory has taken Orluna from its origins in the aeronautical industry into the architectural downlighting market. Started in 1973 by a group of aeronautical engineers, the company was involved in early applications for LED light sources for use in civil and military projects where their efficiency, long life and mechanical resilience were ideally suited. This was long before LEDs were adopted for use in general lighting, so the company had a good headstart in their use. In 2009, Andrew Kilborn took over the company after a career in private equity and venture capital. Under his management, Orluna has become one of the leading suppliers of downlights for highend residential, hospitality and retail applications, working closely with lighting designers and specifiers around the world. His focus for Orluna is to grow the company organically with a long term investment horizon. The company is truly international. It currently has more than 50 employees with overseas offices in Austria, Dubai and Singapore and works with a network of partners in 32 countries. Orluna’s first big success in the architectural lighting market was the Quad 50 range of architectural downlights, which proved to be popular with the international lighting design community and helped to establish the brand. All Orluna products are made in the UK with an above industry average content of UK-made mechanical components. Orluna plans to increase this proportion to even higher levels in the future. Sustainability is an important topic for the company and, by sourcing more mechanical components locally, it will help to reduce the carbon footprint caused by the shipping required to work with overseas supply chains. It will also allow easier re-use and re-assembly of products at the end of the life of the luminaire when light engines and drivers need to be replaced. By focusing on
a limited number of related product types, Orluna is able to create a modular range where common components including heat sinks, light engines and bezels can be used on a variety of different product variants to achieve economies of scale. The latest product introduction from Orluna is the Fade Adjustable downlight fitted with the new Origin Natural light engine. Unusually Orluna luminaires incorporate custom COB light engines made to its own phosphor recipe. The previous generation of Orluna light engines, the Origin, features a CRI of 98 with a very high R9 value of 99. Under the TM30 system the Origin light engine has values of RF of 94 and RG of 101. However, the spectrum of the earlier Origin light engine was not fully continuous and had some dips in the violet and cyan areas. The new Origin Natural light engine improves the RF value to 98 and the RG to 100 so getting even closer to the sunlight spectrum and achieving slightly higher values than a Soraa Vivid 3000k lamp. The spectrum of the new light engine is now noticeably more linear and continuous across all the colours. At the moment, only 2700k and 3000k colour temperatures are available as these are the most used for Orlua projects. A warm, dim light engine is available, which adjusts from 1800k to 3000k with a CRI of 98 and R9 of 98, but at the moment this is not included within the Origin Natural range. The small improvements in the colour fidelity performance of the Origin Natural light engines should be useful to get the attention of the target market of lighting designers. The lit effect from the Fade adjustable downlight sample I tested was impressive with all colours well differentiated, attractive and with a clean, soft-edged beam with no imperfections. I suspect that the wide range of distributions available may be of greater interest to designers, with up to 10 beam angles in most of the Orluna range. Ranging from a very narrow 8° spot up to a 55° wash in the symmetric distributions and with two different elliptical beam angles for asymmetric applications. The Fade adjustable downlight is an 80mm diameter trimless, fully recessed luminaire with a 28° aiming angle. It incorporates both a cone and a baffle for good glare control and visual comfort. With 10 distributions and a wide variety of colour finishes there are many options to fit project requirements. The development of the Origin Natural light engine and the Fade adjustable downlight were understood to have taken around 18 months. Design Director Graham Lunn and Daniel Mahdavi and Chief Technology officer were responsible for these projects. The luminaire is constructed from a conventional combination of aluminium die castings, aluminium extrusions and machined components. The build quality and finish are good and the rotation in both axes is smooth with a positive horizontal rotational stop giving around 350° adjustment. The luminaire snaps positively into a moulded ceiling plate with ball catches that will allow further horizontal rotation if necessary. A somewhat flimsy moulded rubber gaiter fills in the variable gap created as the luminaire is angled back to prevent a direct view into the ceiling void which is a nice design feature. The bezel assembly is easily unscrewed to allow the reflector and diffusing window to be changed on site if necessary. The heat sink on the sample I tested ran quite warm and I noticed that the direct air flow path through the heat sink was somewhat restricted, but I assume that the COB LED running temperature will be within operating limits when used in a ceiling void. Orluna has achieved a very high level of performance with the new Origin Natural light engine, which should differentiate it to some extent from the many other downlight companies. The wide range of optics and variety of luminaire options, including the Fade adjustable that can use this new light engine will definitely give the company a strong story in this market.
www.orluna.com
SIM City Dominic Meyrick, Partner at Hoare Lea, explains how the lighting design studio’s web-based controls app - LightSIM - helped to rejuvenate the lighting for LTS Architects’ new office space.
Back in August 2019, I gave a talk to LTS Architects at their rented offices in Bermondsey. During the conversation that followed, we discussed workplace lighting and I mentioned that I thought their lighting was terrible... fortunately Greg Shannon, director and founder of LTS, took this in good grace, and we went on to examine the existing scheme, with its 600x600 ceiling downlights, together. Recognising that the ‘LG3 throwback’ lighting was awful, Greg had hoped that the task lighting in which LTS had invested would enable everyone to turn off the inherited background fluorescents. However, when they tried this, staff complained that the space was too dark. My CPD seminar had mentioned that this approach doesn’t generally work, and because LTS were moving to a new office at 66 Wentworth Street in Spitalfields, London, I agreed that I would advise on the lighting scheme with a view to trying out new ideas about how an office could be lit to save energy, while creating a comfortable, attractive visual impression. The new office comprises a ground floor containing the main workspaces and a small meeting room, while the basement level is designed around a long meeting table set beneath a timber slatted ceiling, lit by an internal skylight. I had the plans, knew the environment and the work that would be carried out, and so could tailor the lighting accordingly. Obviously, this is the luxury of a Cat B fit-out.
Ground Floor Bang on trend, LTS were thinking of painting the ceiling and services black. Perhaps this aesthetic works in a hip coffee shop, but I didn’t think it would work for an office where visual comfort is paramount and factors, such as age, should be considered. The brain and visual system is designed for daylight. If the ceiling above our heads is dark, our visual system will take us to the time it is naturally dark overhead: nighttime. And so any space will appear dark. Clearly this would be a problem in a workspace. We therefore recommended keeping the galvanised silver elements on the ceiling and painting the concrete slab white. We could then uplight the ceiling and use the interreflection created to bring brightness into the space. Such an approach would mean that the mechanical kit would be lit and, well, why not! If it is there, why not flaunt it à la high-tech architecture. The big idea on the ground floor was to have a continuous linear system, rather than pendants hanging over the desks. The main obstacle to this change was the aesthetic of exposed services, which were set. We knew staff would be largely working in the middle of the floorplate, so the only space available for lighting was around the edge. Supplied by Optelma Lighting, the linear system runs around the space, uplighting the room and creating a background lighting level of 200lux +. The asymmetric system runs right across the windows. This is because at night, windows become ‘light suckers’; putting artificial light on the ceiling above the window opening
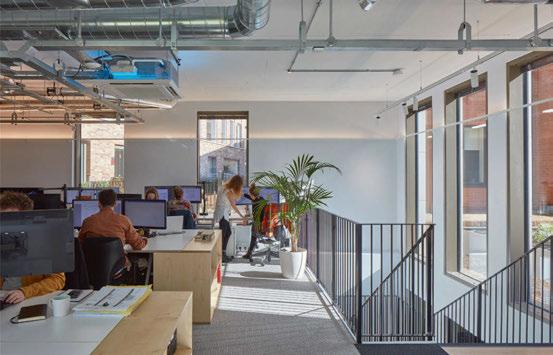




Hoare Lea designed the lighting scheme for LTS Architects’ new office space. In doing so, the lighting designers introduced a continuous linear band of light around the perimeter of the main office space, uplighting the room and creating a pleasant background lighting level. This motif is replicated in the basement area, with a linear lighting strip hidden under the basement’s 15m pin wall. All lighting is controlled via Hoare Lea’s LightSIM Controls app (bottom left), enabling LTS Architects to explore new lighting scenes on screen, before uploading them to the real world environment. (Pics: James Brittain)
reduces the impression of ‘black holes’. Therefore, with the exception of the entrance door, the eight areas of large glazing within the ground floor working area all have the system running across. However, the channel is so small (around 50x10mm) that it appears as a line, which does not upset the aesthetic. We brought 13 Dyson Lightcycle task lights from LTS’s old office. These are the only ‘feature’ light fittings in the interior, and give the task lighting on each desk as required by BS EN 12464-1. Having been a lighting designer for more than 30 years, I am happy to admit that while I love their light, I ‘hate’ light fittings as too often they distract from the architectural character of an interior. However, in this office, the Dyson task light is part of the ‘desk architecture’ and so is a visual enhancement rather than distraction. Away from the main office space, the second big idea was to use concealed lighting. In the corridor between the office area and back meeting room, a floor-mounted, buried light fitting along one side uplights the wall. Opposite, in the alcove area where desks are located, concealed fittings ‘push’ downlighting onto the working area. Finally, rather than trying to hide the ugly fan coil air-conditioning units, we decided to make them a feature, with colour-changing LED lighting putting colour into the space.
Basement The basement comprises a meeting room, break-out space and desking. At present three of the desks are spares, which might in the future be rented out. As there is no task lighting in the basement, it was agreed that pendants would provide direct lighting over these. The main feature is the pin wall, which at 15m long, runs from one end of space to the other. Rather than putting downlighting on this thoroughfare, we specified asymmetric light fittings under the board. This system provides light that washes down onto the corridor that runs from the front to the back of the building. The same asymmetric profile is used in the basement and the ground floor. Interestingly, we changed the lumen package for the LED strip: on the ground floor ceiling it is 3000lm per square metre, whereas under the pin wall in the basement it is 1000lm. Opportunities can be missed if care is not taken when working out the LED strip to be used within a profile. LED tape will only do the job if you consider the lumen package, placement and purpose.
LightSIM Hoare Lea’s web-based LightSIM Controls App enabled LTS to explore lighting scenes, with photometrically accurate imagery on- screen, before they were uploaded to the real-world environment. Once a ‘scene’ is created in the app’s virtual environment, it is sent to a webbased lighting controls system and then imported directly into the enabled light fittings. We specified Mymesh from Chess; this enables each fitting to be ‘spoken to’ without hard wiring a control system. LTS can easily reformat any of the lighting scenes. Whether in the building or working remotely, they can control the light, creating different scenes, while saving energy by making sure light is only on when needed.
Energy The energy use across the lighting, if all on at 100% output, sails close to the maximum requirements of Part L (10.76W/m) for an office space. However, the LightSIM has allowed the ‘trimming’ downwards of the energy use to 6W/m, without losing that all important visual impression; and obviously the task lights are only on as and when required. The key is to remember that the eye, designed for the lit condition of daylight, will not ‘see’ the difference in visual impression of a lit scene when the lighting is at 100%, compared to 70% output. With further ‘tweaking’ the overall energy use was reduced without any detriment to users. Commenting on the success of the solution, Shannon said: “It has been an absolute pleasure to work with Dominic and his team, and watch our humble home come to life. The results have transformed our thinking on lighting, energy use and what’s possible. We have saved significant sums on the build and on our running costs and have gained a beautiful scheme of which we are all very proud.”