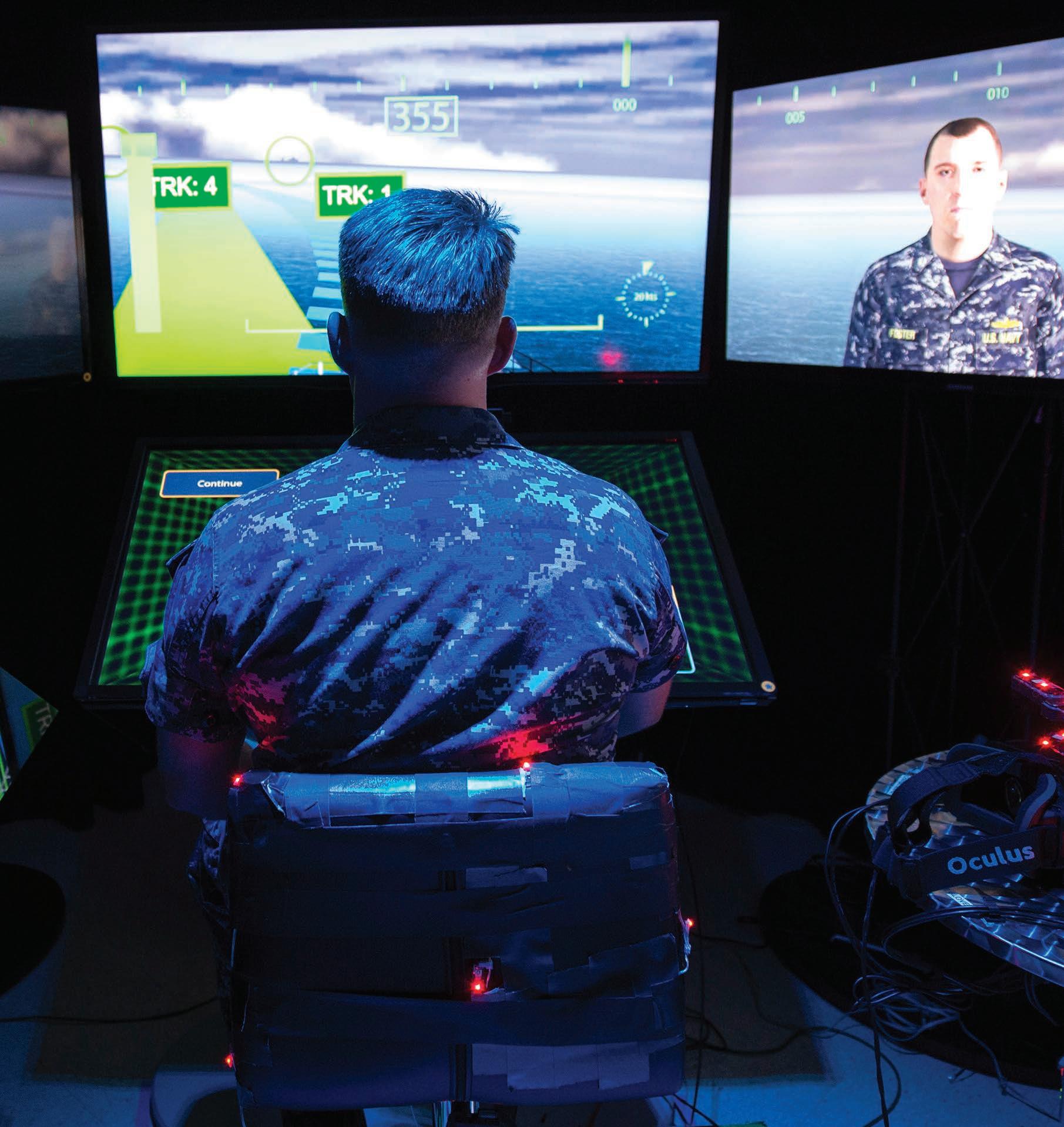
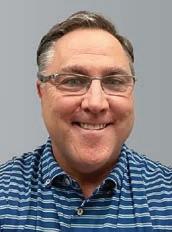
For mission critical applications, Analog Devices delivers proven, beamforming technology with trusted reliability when and where you need it most—from the unknown vastness of space to the unrelenting theater of war.
Optimized Form Factor
Enhance Speed to Market
Low Power, Minimal Heat Dissipation
Find your solution at analog.com/phasedarray
Global
SPECIAL REPORT: Leveraging RF and microwave tech for 5G applications
RF & microwave innovation enables military 5G solutions
By John McHale, Editorial Director
20 Network-centric performance: a key to mission-critical effectiveness
By Kelly Masood, Intilop Corp.
22 Defense industry turns to AR for training, manufacturing, and more
By Dan Taylor, Technology Editor
INDUSTRY SPOTLIGHT: SOSA Technical Standard 1.0: Impact on EW designs
26 MOSA, SOSA, VPX, and power considerations
By Matt Renola, Vicor
30 Multi-INT and SOSA: A consideration of next steps
By Patrick Collier, Aspen Consulting Group and Denis Smetana, Curtiss-Wright Defense Solutions
34 SOSA’s rubber is meeting the road in rapid system development
By Travis Doll, Sciens Innovations and John Orlando, Epiq Solutions
38 VPX and OpenVPX: A guide to military applications, major players, and more
By Dan Taylor, Technology Editor
ON THE COVER:
ADVERTISER/AD
AirBorn
Analog Devices,
Annapolis Micro Systems
ecosystem
Behlman Electronics, Inc.
the pack
Elma Electronic
Designed to
Extreme Engineering Solutions (X-ES)
GMS
LCR Embedded Systems,
Mercury Systems,
Phoenix International
PICO Electronics Inc
Pixus Technologies
chassis with advanced
GROUP EDITORIAL DIRECTOR John McHale john.mchale@opensysmedia.com
ASSISTANT MANAGING EDITOR Lisa Daigle lisa.daigle@opensysmedia.com
TECHNOLOGY EDITOR – WASHINGTON BUREAU Dan Taylor dan.taylor@opensysmedia.com
CREATIVE DIRECTOR Stephanie Sweet stephanie.sweet@opensysmedia.com
WEB DEVELOPER Paul Nelson paul.nelson@opensysmedia.com
EMAIL MARKETING SPECIALIST Drew Kaufman drew.kaufman@opensysmedia.com
WEBCAST MANAGER Ryan Graff ryan.graff@opensysmedia.com
VITA EDITORIAL DIRECTOR Jerry Gipper jerry.gipper@opensysmedia.com
DIRECTOR OF SALES Tom Varcie tom.varcie@opensysmedia.com (734) 748-9660
DIRECTOR OF MARKETING Eric Henry eric.henry@opensysmedia.com OPERATIONS & AUDIENCE DEVELOPMENT (541) 760-5361
STRATEGIC ACCOUNT MANAGER Rebecca Barker rebecca.barker@opensysmedia.com (281) 724-8021
STRATEGIC ACCOUNT MANAGER Bill Barron bill.barron@opensysmedia.com (516) 376-9838
STRATEGIC ACCOUNT MANAGER Kathleen Wackowski kathleen.wackowski@opensysmedia.com (978) 888-7367
Verotec
Commercial and rugged system
Wolf Advanced Technology
aligned video out
Wolf Advanced Technology
HPEC and display
Wolf Advanced Technology
GbE, PCIe Gen4 + HPEC
Wolf Advanced Technology
PCIe Gen4 switch, AV67.3 SDI/RS-170
Wolf Advanced Technology
Display and HPEC
Wolf Advanced Technology
Display and HPEC autonomous SBC
Wolf Advanced Technology
Video I/O with SDI, CVBS
59th Annual AOC International Symposium & Convention
October 25-27, 2022
Washington, DC https://www.crows.org/mpage/2022HOME
Aerospace Tech Week Americas
November 8-9, 2022
Atlanta, GA
Embedded Tech Trends (VITA)
January 23-24, 2023
Chandler, AZ https://www.vita.com/event-4893941
West 2023 (AFCEA)
February 14-16, 2023
San Diego, CA https://www.westconference.org/ West23/Public/enter.aspx
SOUTHERN CAL REGIONAL SALES MANAGER Len Pettek len.pettek@opensysmedia.com (805) 231-9582
DIRECTOR OF SALES ENABLEMENT Barbara Quinlan barbara.quinlan@opensysmedia.com AND PRODUCT MARKETING (480) 236-8818
INSIDE SALES Amy Russell amy.russell@opensysmedia.com
STRATEGIC ACCOUNT MANAGER Lesley Harmoning lesley.harmoning@opensysmedia.com
EUROPEAN ACCOUNT MANAGER Jill Thibert jill.thibert@opensysmedia.com
TAIWAN SALES ACCOUNT MANAGER Patty Wu patty.wu@opensysmedia.com
CHINA SALES ACCOUNT MANAGER Judy Wang judywang2000@vip.126.com
WWW.OPENSYSMEDIA.COM
PRESIDENT Patrick Hopper patrick.hopper@opensysmedia.com
EXECUTIVE VICE PRESIDENT John McHale john.mchale@opensysmedia.com
EXECUTIVE VICE PRESIDENT AND ECD BRAND DIRECTOR Rich Nass rich.nass@opensysmedia.com
ECD EDITOR-IN-CHIEF Brandon Lewis brandon.lewis@opensysmedia.com
TECHNOLOGY EDITOR Curt Schwaderer curt.schwaderer@opensysmedia.com
ASSOCIATE EDITOR Tiera Oliver tiera.oliver@opensysmedia.com
ASSISTANT EDITOR Taryn Engmark taryn.engmark@opensysmedia.com
ASSISTANT EDITOR Chad Cox chad.cox@opensysmedia.com
CREATIVE PROJECTS Chris Rassiccia chris.rassiccia@opensysmedia.com
MARKETING COORDINATOR Katelyn Albani katelyn.albani@opensysmedia.com
FINANCIAL ASSISTANT Emily Verhoeks emily.verhoeks@opensysmedia.com
MANAGER subscriptions@opensysmedia.com
CORPORATE OFFICE
Rd.
WRIGHT’S
Scottsdale, AZ 85257
REPRINTS
COORDINATOR
Tel: (480) 967-5581
“Is it difficult covering standards, is it getting slow?” my dinner companion asked on the eve of the AUSA 2022 Annual Meeting in Washington. He noted how technical standards bodies can be plodding, taking months to deliberate on a specific point without creating much news.
While it’s true standards organizations are not exactly foun tains of breaking news, I told him, the efforts of groups like the Sensor Open Systems Architecture (SOSA) Consortium, the Future Airborne Capability Environment (FACE), and the VITA Standards Organization (VSO) do generate lots of content on the design process of hardware and software solutions for the defense technology community.
In recent times, such efforts – especially since the U.S. Department of Defense (DoD) mandate to leverage modular Open Systems Approach (MOSA) strategies in new platforms and upgrades – are generating tons of technical editorial content for the pages of this journal, as well as for our SOSA Special Edition, FACE Special Edition, and VITA Technologies magazine.
This has been especially true with articles covering the SOSA Technical Standard as it is impacting many DoD applications such as radar, electronic warfare (EW), intelligent systems, and other mission-compute applications. In fact, this issue features SOSA cofounder C. Patrick Collier sharing a byline with Denis Smetana of Curtiss-Wright in an article titled “Multi-INT and SOSA: A consideration of next steps.”
One point from their article: “With MOSA in mind, from the technical and business acquisition perspective, and SOSA as an enabler of MOSA for something like Multi-INT [multi-intel ligence], we see that the SOSA Reference Architecture (RA) is fundamentally well positioned to help realize the potential of Multi-INT applications.”
Also in this issue: Travis Doll of Sciens and John Orlando of Epiq Solutions collaborated on a feature titled “SOSA’s rubber is meeting the road in rapid system development,” highlighting how SOSA affects software-defined radio (SDR) designs.
“Of the many steps to test and validate interoperability in a SOSA aligned system, the point at which system designers start thinking about how they will command and control a device from the outside world makes up a crucial piece of the puzzle,” they write. “This integration requires implementing various MORA [Modular Open Radio Frequency Architecture] and Vehicular Integration for C4ISR/EW Interoperability (VICTORY) interfaces that enable other components to discover the hard ware and ‘talk’ to it for command and control, data ingest and egress, health and status, and then determine its capabilities.”
John.McHale@opensysmedia.comMORA and CMOSS … yes, two more standards; it seems that each standard begets more content on other related standards.
In a way, it’s a content gift that keeps on giving, is how I put it to my friend at dinner. Full disclosure: The standard we were discussing was SOSA, and some may feel SOSA chatter has slowed since the release of the Reference Architecture 1.0 a year ago.
In fact, the SOSA content engine has not slowed, even though the news feed might seem to have stalled, at least until this week at AUSA. At the show, SOSA outreach leaders did make some news around upcoming SOSA document releases.
Valerie Andrew, of Elma Electronic and co-chair of the SOSA Outreach Committee, announced during a public briefing that the SOSA Technical Reference Standard Edition 2.0 Snapshot is expected out in the first quarter of 2023, while the Reference Implementation Guide and the Acquisitions & Contracting Guides are nearly finished and should be published soon.
Perhaps of most interest to all SOSA members: The first rollout of the SOSA Conformance Guide is expected to be published in February of 2023. It will establish equipment requirements and guidelines for Verification Authorities. Andrew added that the consortium is working to ensure the conformance process will not be too overarching and expensive.
During the briefing, FACE Consortium Director Alicia Taylor also spoke and mentioned that FACE is reviewing its own more mature conformance process to see where efficiencies can be added.
That makes me think of yet another reason standards keep delivering content: Regular revisions and updates. Yet perhaps the biggest driver of said content is the enthusiasm for the standard from those involved in the process.
SOSA has that enthusiasm. “While every community within SOSA has its own perspective – whether government, COTS [commercial off-the-shelf] suppliers, system integrators, or academia – the SOSA Consortium model enables all of those perspectives to come together in one room where all the dif ferent communities can listen and interact with each other,” Collier and Smetana note.
As Ilya Lipkin, technical lead for SOSA, has told me, standards processes depend heavily on the enthusiasm and involvement of the volunteers. It’s tough to put a metric on enthusiasm, but all the content we keep publishing and you keep reading is a good place to start.
The U.S. Army is putting considerable resources and time into virtual-reality (VR), augmented-reality (AR), and mixed-reality (MR) equipment and training that is intended to make troops on the ground safer and better equipped.
During late summer 2022, Fort Hood’s Close Combat Tactical Training Center hosted 150 soldiers from Fort Bliss (Texas) and Fort Carson (Colorado) as part of an operational assessment led by the U.S. Army Test and Evaluation Command.
The assessment sought to understand how soldiers interact with the newest software and hardware versions of the Army’s Synthetic Training Environment (STE), a capability that blends virtual, live, and collective training elements to produce an immersive experience that is portable and minimizes use of real firepower and other typically costly, one-time-use training resources.
According to information provided by the Army’s Program Executive Office Simulation, Training and Instrumentation (PEO STRI), the STE intends to interact with and augment live training, which will enable the Army to deliver training service directly where needed. The capability will enable the training audience to be trained on all warfighting functions, across all echelons with joint and Unified Action Partners (UAP). The wide-ranging training will include mission rehearsal capability, interfaces with operational networks, training interfaces with battlefield platforms, interfaces to live training instrumenta tion, and native interoperability with the Common Operating Environment (COE), a defined set of processes used across the military services.
Two pieces of the STE were under test at the Fort Hood assess ment: the Information System (STE-IS) and the Reconfigurable Virtual Collective Trainer (RVCT). The STE-IS is an intelligent suite of training simulation and management software that enables intuitive access and simultaneous training at multiple locations. The STE-IS also uses the “One World Terrain” 3D mapping dataset that integrates actual terrain imagery from around the world.
The RVCT is described on the PEO STRI website as an adapt able hardware system that connects to the STE-IS to activate collective, mixed-reality training scenarios. The RVCT consists of interactive equipment – including heads-up display, high-res olution monitor, and representational controllers – that enables on-the-ground soldiers, squads, platoons, and companies to navigate exercises using actual and computer-generated move ments. The STE-IS-powered family of RVCT systems is intended to replicate key aviation and ground platforms; the Fort Hood assessment focused on RVCT ground systems replicating
Abrams, Bradley, and Stryker fighting vehicles, as well as dis mounted infantry.
A U.S. Army story on the STE testing noted that soldiers who took part in the assessment were asked to offer ideas on how to enhance current systems, such as by varying the volume of sound effects and making simulated movements smoother.
Col. Cory Berg, Project Manager Soldier Training at PEO STRI, explained to the participants that part of the novel nature of the STE lies in its ability to capitalize on “communally avail able equipment and capabilities.” According to information from the PEO STRI, the STE software solution will also leverage commercial off-the-shelf (COTS) and government off-theshelf (GOTS) hardware. Moreover, Col. Nick Kioutas, Project Manager Synthetic Environment at PEO STRI, noted that the Army intends to “exploit the new technologies in gaming” as it advances the STE with the help of industry partners.
Further aiding in the development of the STE, said Col. Mike McCarthy of the STE Cross-Functional Team, is the intentional use of a MOSA [Modular Open Systems Approach], which helps to maximize the ease-of-use, efficiency, and adaptability of the equipment under development.
A deployment timeline for the STE has not yet been set; Brig. Gen. William R. Glaser, Director of the STE Cross-Functional Team, calls the development “an effort in progress.”
The Army is also progressing in its large-scale planned rollout of the in-development Integrated Visual Augmentation System (IVAS). The huge program – reported by the U.S. Department of Defense (DoD) to cost more than $20 billion – plans to bring night vision, thermal vision, tactical edge computing, and enhanced situational awareness to infantry soldiers. The headset, based on the Microsoft HoloLens AR goggles, is aimed at giving individual soldiers superior information and awareness, said to be on the level of fighter pilots.
The IVAS headset, according to a story on the Army’s web site, is intended to give users enhanced rapid target acquisition, navigation, target marking, and more features, including a field of view nearly twice as wide as those offered by current fielded systems.
A press release from the U.S. Army Program Executive Office Soldier reports that it will deliver 5,000 IVAS 1.0 versions and another 5,000 updated versions during 2023. Initial reports had the Army ordering as many as 40,000 of the headsets. The 2023 deliveries are a delay from the previous planned delivery dates in 2021 and 2022.
Digital keys are a core concept in establishing secure networks, one as relevant in a data center application as it is at the edge of the tactical battlefield. While cryptography (crypto) uses both symmetric and asymmetric keys for different functions, for this column we’ll focus on asymmetric cryptography in which different keys are used for locking and unlocking.
The asymmetric cryptography approach has many advantages, such as verifying exactly who sent a particular message. The most common use for asymmetric crypto is in public key infra structure (PKI) applications. In asymmetric crypto, there are both public and private keys. The public key can be freely dis tributed and is used to verify the identity of an entity, such as a person or a server. The private key needs to be kept private to prevent that entity from being impersonated.
Public and private keys are provided by a certificate authority (CA). After the entity creates a certificate-signing request, they pass it to the CA. After verifying the identity of the requestor, the CA will issue the entity its public and private keys as an X.509 certificate.
The CA could be a major internet company, such as Verisign or GoDaddy, or a server managed by an organization. Every operating system has a certificate store where trusted CAs are recorded; Microsoft, Apple, RedHat, and others have vetted the major CAs, but an organization can add or remove CAs from this list. On a typical U.S. Army system, all the internet CAs are removed and replaced with a set of Department of Defense (DoD)-approved CAs.
A hardware security module (HSM) is a device that safeguards cryptokey material and/or accelerates crypto operations. These devices are attached to a CA, either physically via PCIe or USB, or logically over a network. HSMs provide cryptographically secure key generation and secure key storage, as well as crypto services to applications such as certificate authorities or for the encryption of files or databases. These applications are inte grated using industry standard (as well as vendor-specific), libraries and APIs. Using an HSM can ensure, if a server breach happens, key material used to safeguard valuable information will not be compromised, which helps organizations and agen cies lower their operational risks.
The use of an HSM prevents poor crypto key handling by pre venting accidental copying and distribution of crypto keys. It defends against remote attacks and eliminates remote extrac tion of private keys by storing the crypto keys securely on hardware. Where SWaP (size, weight, and power) is critical, traditional HSMs can take up more space than necessary to complete the mission.
Figure 1 | The PacStar Secure Wireless Command Post (SWCP) utilizes the YubiHSM2 for secure private key storage to meet NSA CSfC requirements in the smallest SWaP possible.
The small YubiHSM 2 device enables secure key storage and operations using a proven secure element, extensive crypto capabilities, modern algorithms, and key lengths. It also pro vides role-based access controls for key management and key usage, enabling control over which operations are performed with keys and by whom. The tamper-resistant device, packaged in a low-power nano form factor, is network-shareable.
This USB-based device provides an additional layer of control and key material with M of N wrap key backup and restore, which requires multiple parties to bring their portion of the key together for operations. It can integrate with a variety of applications, including CAs, solutions for VPN, file system and database encryption, interfaces via YubiHSM KSP, PKCS#11, and native libraries. It also gives the user tamper-evident audit logging through operations that leave a verifiable audit trail, all validated by NIST to FIPS140-2 level 3.
With tactical hardware where a high capacity HSM is often not required, the larger HSM can simply be removed and replaced with a YubiHSM2, effectively freeing up two slots in the system. Those slots can then be used to add support for another net work without expanding into a second case.
Some of the first applications of this ultrasmall HSM have been deployed in NSA-approved Commercial Solutions for Classified (CSfC) solutions that use two layers of commercial encryption, such as the PacStar Secure Wireless Command Post (SWCP), a WLAN command post system as registered by the U.S. Army Project Manager Tactical Network (PM TN). (Figure 1.) The system includes both SIPRnet and NIPRnet (Green) networks.
Dominic Perez, CISSP is the CTO at Curtiss-Wright Defense Solutions and a Curtiss-Wright Technical Fellow.
Curtiss-Wright Defense Solutions
Ukraine package, worth $1.1 billion, includes UAS radars, communications systems, and surveillance systems
The U.S. Department of Defense (DoD) has announced a $1.1 billion package in additional security assistance for Ukraine that includes funding for UAS radars, communications and surveillance systems, and more. The funding is provided under the Ukraine Security Assistance Initiative (USAI), which “underscores the U.S. commitment to continuing to support Ukraine over the long term,” according to a DoD statement.
In addition to the High Mobility Artillery Rocket Systems (HIMARS), tactical vehicles, and other military aid, the package includes two radars used with unmanned aerial sys tems (UASs); 20 multimission radars;counter-UAS systems; and tactical secure communications systems, plus optics. DoD spending on Ukraine has sharply increased since the Russian inva sion of Ukraine in February. In May, Congress approved more than $40 billion in additional aid to Ukraine, bringing the total U.S. commitment to $54 billion.
The global missile-defense system market will grow from $23.92 billion in 2022 to $31.32 billion in 2026, with increased use of artificial intelligence (AI) a big factor in the market over that period. The report, from Research and Markets, states that the increasing use of AI is a one of the major factors in the expected growth of the market. The report authors define AI as computer intelligence or intelligence demonstrated by a machine to help perform simple tasks more efficiently or tasks that couldn’t be performed otherwise. North America is the largest region in the missile-defense market, according to the study authors. They also note that a surge in defense spending around the world is likely to fuel growth in the market. The United States makes up 39% of total military spending worldwide.
Unmanned aerial system (UAS) manufacturer Tekever deployed a fixed-wing intelligence UAS during an exercise involving NATO navies off the coast of Portugal, the company announced. The AR5, a fixed-wing remotely piloted aircraft (RPA) system, is intended to provide real-time aerial intelligence, surveillance, and reconnaissance (ISR) data and video.
The REP(MUS) exercise – which involved the United Kingdom and Portuguese navies – brought together 1,500 personnel from NATO and partner coun tries, as well as industry and academia, to test the interoperability of autonomous underwater, surface and air vehicles for maritime operations. The com pany described the exercise as a test of the NATO Alliance’s readiness to use unmanned systems to counter security challenges. The missions during the exercise included submarine warfare, wide-area sur veillance, support of amphibious forces, and searchand-rescue efforts.
Five companies won bids to be an industry partner with the U.S. Air Force on the Advanced Battle Management Systems Digital Infrastructure Consortium, which will support the U.S. Department of Defense’s Joint All-Domain Command and Control (JADC2) effort. L3Harris, Northrop Grumman, Leidos, Raytheon, and SAIC will join the ABMS consortium, which is intended to design, develop, and deploy JADC2 multidomain capabilities. The ultimate vision of JADC2 is to create a com mand-and-control operating construct that will synchronize operations across sea, air, land, space, cyber, and the electro magnetic spectrum.
“The industry consortium will advance the architecture stan dards and digital infrastructure requirements for the Department of the Air Force’s digital backbone to manage, secure, and deliver data across multiple domains in highly contested environments,” according to a Raytheon statement.
Lockheed Martin wins precision-strike missile contract from Army Lockheed Martin won a $158 million contract from the U.S. Army to produce early operational capability (EOC) precision-strike missiles (PrSM), the second production contract received to date for the pro gram, the company announced. The contract, initially announced in September 2021, follows a manufacturing-readiness assessment mile stone visit with the Army, which is an important step toward fielding. The missile is intended to replace the MGM-140 Army Tactical Missile System (ATACMS), a surface-to-surface missile that was also pro duced by Lockheed Martin. The U.S. military announced in 2021 that Australia would be a partner in the program; the United Kingdom mili tary intends to field the missile in the coming years. The missile’s most recent flight was at Vandenberg Space Force Base in California during late 2021, with additional flight tests expected during 2023. A full-rate production decision is expected in 2025.
First radar for U.S. Air Force satellite constellation delivered The Tomorrow Companies (Tomorrow.io) delivered the first radar payload to Astro Digital for satellite integration as part of a $19.3 million contract awarded last year by the U.S. Air Force through its Commercial Weather Data Pilot Program. Tomorrow.io completed assembly and testing of its first precipitation radar, which will support deployment of Astro Digital’s first four Corvus-XL satellites.
In an Air Force statement, John Dreher, materiel leader, Weather Systems Branch, said that global envi ronmental data is essential to effective mission plan ning and execution of air and ground operations. The first planned launch of a satellite is in early 2023, with the full constellation expected to be in orbit by 2025.
A satellite meant to provide situational awareness to tactical warfighters in the U.S. Army is now operational after being launched into orbit this summer, manufacturer Dynetics (a Leidos subsidiary) announced. The Lonestar tactical space support vehicle was launched from Mojave Air and Space Port aboard the Virgin Orbit’s LauncherOne two-stage air-launch vehicle during July 2022, and the vehicle has now been fully checked out in low-Earth orbit. The vehicle was launched on behalf of the U.S. Army Space and Missile Defense Command. Dynetics com pleted on-orbit satellite and payload checkouts with the Army at Redstone Arsenal in Huntsville, meaning the pay load is operational and ready to support the situationalawareness mission for the warfighter, according to the Dynetics statement.
FigureLynx chooses LDRA as FACE verification authority for mission-critical avionics Mission-critical software company LDRA announced that it was chosen as the FACE [Future Airborne Capability Environment] Verification Authority (VA) for Lynx Software Technologies, a company that develops open architecture software solutions for mission-critical embedded systems. Lynx will earn independent validation and verification (IVV) of its software – designed to conform with the latest FACE Technical Standard, edition 3.1 – as it works with LDRA Certification Services (LCS), The IVV is a critical step for FACE conformant prod ucts; in its announcement, LDRA states that the IVV is aimed at ensuring that its joint customers are able to reduce risks, lower costs, and speed time-to-field for their airborne platforms. Vendors deemed compliant to the FACE standard are better able to meet the industry’s need for software reuse, effective interop erability, and rapid upgrades while controlling life cycle costs.
Tomahawk Robotics to provide universal roboticcontrol contract for Marine Corps
Tomahawk Robotics won a con tract to provide a system that would enable U.S. Marines in the field to have universal robotic control of multiple unmanned systems, sensors, and payloads. The contract, which is worth $6.5 million and runs through 2024, is for the Autonomy and Robotics Enhanced Multi-Domain Infantry Squad (ARTEMIS) program through the Marine Corps Warfighting Laboratory.
Under the terms of the ARTEMIS contract, Tomahawk Robotics will integrate six additional unmanned systems – which include both ground and airborne plat forms used by Marine Corps infantry units – as well as ground radios into the Kinesis Ecosystem. The capability is meant to pro vide AI-enabled universal robotic command and control for Marine users, as well as for next-genera tion unmanned systems, sensors, and payloads for dismounted Marine Corps units.
DARPA Blackjack satellite payloads delivered and tested Blue Canyon Technologies (BCT) and SEAKR Engineering (wholly owned subsidiaries of Raytheon Technologies) announced they have delivered one Saturn-class microsatellite bus and completed acceptance testing of the first two of twelve “Pit Boss” battlemanagement systems for the Defense Advanced Research Projects Agency (DARPA) Blackjack satellite program. BCT is tasked with providing a total of ten Saturn-class buses total; the remaining nine buses are expected to ship in late 2022. Each BCT bus includes advanced electric propulsion, a robust power system, command and data handling, radio-frequency com munications, and dedicated payload interfaces that could host several dif ferent U.S. Department of Defense (DoD) payloads.
The Blackjack mission is intended to develop and demonstrate critical elements of a global high-speed network in low-Earth orbit (LEO) that satisfy DoD performance and payload requirements at a much lower cost, with shorter design cycles, and with easier and more frequent technology upgrades.
Figure 5 | A military helicopter in flight. LDRA photo. Figure 6 | Tomahawk Robotics existing Radio Agile Integrated Device (RAID) system. Tomahawk Robotics photo.The X9 modular, scalable, distributed architecture simplifies applications that require rugged high-performance computing, high-definition video, sensor processing, artificial intelligence (AI) battlefield edge processing, storage, display, and I/O in a small, rugged enclosure with amazing performance per dollar per Watt. All X9 products are modular, expandable or scalable, with Thunderbolt™ 4 technology and our patented LightBolt™ 40Gbps connections in copper or fiber, with optional 100W per port power for up-/down-stream sensors and system expansion.
RF and microwave solutions are a critical ingredient in the U.S. military’s plans to adapt fifth-generation wireless technology, or 5G, as the technology will be essential to create more tools for the joint forces.
The U.S. Department of Defense (DoD) –not so much as the driver but rather the consumer of commercial technology –often lags behind the commercial world when it comes to adapting wireless tech nology like 5G and LTE technology. The commercial world is already leveraging 5G solutions en masse: Just look at the screen of any cellphone.
The slower adaption always loses ground, not just to the glacial DoD acquisition pro cess but also to the security requirements for military-communications systems and ensuring the new tech is interoperable with existing warfighter systems.
Defense companies and commercial wireless companies are working together to demonstrate the capabilities of 5G for military programs, including Joint All Domain Command and Control (JADC2). Improved connectivity not only improves communi cations but also speeds the collection of critical data for intelligence, surveillance, and reconnaissance (ISR) missions and electronic warfare (EW) applications.
The DoD began facilitating adoption of 5G technology in 2020,” says Bob Vampola, vice president of the aerospace and defense business unit of Microchip Technology (Chandler, Arizona). “Funding has been provided to demonstrate 5G applications and technologies at various military facilities and for key applications. Funding is intended to promote technology development, mitigate vulnerabilities, influence standards, and engage industry partners.”
The DoD needs 5G for the same reason as commercial users: increased bandwidth and enhanced connectivity.
“What’s going on in [commercial] 5G absolutely is a parallel to what’s going on in the military,” says Bryan Goldstein, vice president, Aerospace and Defense, Analog Devices (Wilmington, Massachusetts) in a podcast titled “Semiconductor supply chain, radar & electronic warfare designs, engineering talent” (readers can listen to this podcast at https://militaryembedded.com/radar-ew/rf-and-microwave/semicon ductor-supply-chain-radar-electronic-warfare-designs-engineering-talent). “The mili tary realized they don’t always need their own systems, but maybe if they could use
the communications protocol and then find ways around encryption and being able to protect data in different way, they could ride onboard with commercial 5G and in parallel LEO [low-Earth-orbit] satellite constellations. [While] we’re just starting to get into this with our [military] customers, they believe this pipeline and this communica tions protocol will work for them in some applications.”
For some applications this means diving “all the way into the architecture of semi conductor transceivers and communications protocol, but [for others] it is as simple as [managing the] encryption methodologies at both ends of their communications chain," he adds.
“5G technology offers fundamental capabilities critical to multidomain operations captured by the military like low latency and wide bandwidth systems, as well as flex ible incorporation of diverse systems to bring different sensors and communications channel together effectively,” just as 5G does in the commercial world with autono mous automobiles and remote healthcare, Goldstein notes.
While commercial 5G systems are becoming abundant, deployment for military 5G systems will be slow as the investment in building blocks for 5G systems has only just begun.
“There is still a long way to go,” says Brian Murphy, business development executive with Benchmark Electronics (Tempe, Arizona). “We are mostly seeing development of the building blocks, like customers looking for custom filters. Filters are really a bell wether that normally comes early in a technology’s development, so that speaks to how early 5G for the battlefield still is. A lot of progress has been made on evaluating vulnerabilities and security and developing solutions to mitigate those challenges. That is an essential step, but still shows that true implementation is several years out.”
Supply-chain issues are also impacting 5G development. “We have been serving commercial 5G customers for some time,” says Hiep Truong, manufacturing design engineer with Benchmark Secure Technology. “While keeping defense designs sim ilar to commercial products has value from a simplicity/replaceability perspective, defense customers have greater supply-chain requirements, particularly for country of origin. While commercial 5G network infrastructure providers are looking to diver sify supply chains away from China, for battlefield 5G this is even more of an impera tive. People are looking for things like filters made in North America without adding so many specifications and requirements that they are no longer close to being commercial products.”
In the same way as commercial users of 5G, military users will need increased band width, more power density, increased coverage, and the like. Enabling these demands starts at the component level.
“ADI [is] starting to get interest from [military] customers talking about our work in about 5G” including RF and microwave solutions such as transceiver solutions, power, and software solutions, Goldstein says. “Military customers are very interested in [5G] work at the hardware and software system level,” he adds.
“We are seeing more and more adoption of higher-power-density GaN [gallium nitride] on SiC [silicon carbide] HEMTs [high electron mobility transistors] and MMICs [monolithic microwave integrated circuits] in the military and aerospace sector in the Ku band, Ka band, L, S, and C bands for radar, electronic warfare, aviation, and satel lite communication applications,” Vampola says. The trend is being driven with the need for higher-output powers for these applications to drive longer distances, as well as new applications such as LEO satellite communication for broadband internet
access. The ICP2840, Microchip’s flagship product for 5G and satellite communication, has output power of 10 W with power-added efficiency (PAE) of 22% and gain of 22 dB, he adds. (Figure 1.)
Battlefield environments, unlike many commercial applications, are often extreme set tings, so the 5G systems and the RF and microwave components deployed to these areas need to be rugged, resistant to extreme temperature changes, and resistant or tolerant to radiation.
“Military systems need to operate flawlessly in harsh environments,” Vampola says. “It will be important that these 5G applications use components that are robust enough to handle these environments. This will require selecting components from the industry that offer better reliability over extreme temperatures, humidity, and even adverse radiation environments. In addition, military systems will require working only with component suppliers who can implement physical/operational security measures, while also offering detailed supply-chain risk-management processes with proven commitment to military applications by supporting longevity of supply.”
These ruggedization and security measures must also be applied in ever-shrinking design footprints as the military continues to issue reduced size, weight, and power (SWaP) requirements in every application.
“We are seeing demand for reduced [SWaP] as well as cost on all RF/microwave components and systems for 5G and other high-frequency communications applica tions,” Benchmark’s Truong says. “One way technology developers are approaching this challenge is by combining RF/microwave/mmWave and digital functions once on separate PCBs [printed circuit boards] or even separate modules into single PCB assemblies or modules using advanced circuit materials. In terms of filters, Benchmark is offering several customizable SWaP-enabling design families, some with responses to 40 GHz, which leverage stripline designs fabricated on low-loss circuit materials for outstanding performance in compact, lightweight packages to fit SWaP needs.”
For such applications Benchmark developed an LPI/LPD [low probability of intercept/ low probability of detection] UWB [ultra wideband] radio module that can be used for secure last-mile communications as part of a broader battlefield network. UWB communications is considered a valuable, complementary technology to 5G that can operate effectively within 5G networks, Truong says. “UWB technology enables secure, reliable wireless connection of soldier-worn sensors and other tactical elec tronics and for last-mile radio connections, such as for wireless robotics controllers, in situations where detection of the signal would put soldiers at risk.” (Figure 2.)
Enabling interoperability within military systems has been a decades-long challenge for defense electronics designers.
“Across the Joint Domain battlespace, there are so many legacy systems using so many protocols and connectivity methods,” Murphy says. “Those are not all going to be replaced overnight. And battlefield 5G represents network communications in place of traditional radio-to-radio communications. For this reason, battlefield 5G is likely to be made up of layers including not just mmWave communications between cellular connectivity points, but also satellite backhaul, LPI/LPD UWB, and other con nectivity options. Since any implementation will need to take place in phases, setting the standards for interoperability will be foundational to the success of the system.”
To solve the interoperability issue over the long term, DoD leaders are also requiring new programs and upgrades to take a modular open systems approach (MOSA). This
Figure 1 | Microchip Technology’s monolithic microwave integrated circuits (MMICs) and discrete devices deliver performance levels required in 5G, satellite communications, and defense applications.
Figure 2 | The LPI/LPD UWB radio module from Benchmark Secure Technology can be used for secure last-mile communications as part of a broader battlefield network.
requirement applies to communications systems as well.
“5G is one of the technologies that will contribute to high-speed, low-latency data transmissions that enable artificial intelligence (AI), battlespace visualization, and other advanced computing applica tions in the defense space,” Truong says. “We’re particularly paying attention to Project Convergence, as one example, where the U. S. Army has announced it will be demonstrating Vertex’s Gateway Mission Router 1000, vehicle-borne hard ware with a MOSA approach to trans late otherwise incompatible formats and securely transmit data. Since replacing every proprietary and otherwise existing standard is not going to happen over night, simple yet powerful MOSA sys tems like this are going to be key.” MES
Viasat is working with the U.S. Department of Defense (DoD) to support development of advanced communications and enable concept of operations (CONOPs) for warfighters. The company won an award from the DoD via the Information Warfare Research Project (IWRP) to conduct research on the use of 5G to support communications for Expeditionary Advanced Base Operations (EABO). The research will focus on network enhancements, command and control (C2), and delivery of advanced processing through the integration of digital-twin and agile software defined network (SDN) capabilities.
“Like the DoD, we see the significant potential for 5G to enhance the warfighter’s ability to produce, consume, and make sense of mission critical data at the point and time of need in contested and congested environments to support JADC2 enablement,” says Craig Miller, president, Viasat Government Systems (Carlsbad, California).
“The ability to swiftly move information and data across the battlespace is essential to the multidomain and joint-force operations needs of the future. The addition of 5G bandwidth and network management capabilities will support C2 for specific missions and greater visibility across highly dispersed forces in EABO and littoral operations in contested environments.”
Achieving secure, resilient communications across multiple transports in expeditionary environments is a challenge due to the necessity to rapidly set up and tear down the network, work across
multiple networks and classifications, and operate in austere and contested cyber and electronic warfare (EW) conditions. Through this government/industry research, Viasat will explore how 5G networking technology and other solutions can integrate to support EABO missions, including needs for Long Range Precision Fires (LRPF); Forward Arming and Re-Fueling Points (FARP); and persistent intelligence, surveillance, and reconnaissance (ISR) capability, according to a ViaSat release.
Using a phased approach, Viasat engineers will address specific application areas of 5G dynamic radio frequency (RF) spectrum and adaptive network planning and management to enable low probability of intercept/low probability of detection (LPI/LPD) through enhanced deployment of 5G nodes for EABO, according to the release. This research will also focus on how to enhance 5G RF and network planning with digital-twin models, use 5G mobile edge compute (MEC) to enable tactical edge compute with artificial intelligence (AI) and machine learning (ML), and how to rapidly deploy and operate a mobile infrastructure in a dynamic and contested environment.
These research experiments, which will be conducted over a period of four years, will leverage the Viasat Expeditionary Lightweight Integrated Tactical Edge (ELITE) Kit solution, Viasat’s 5G and tactical networking System Integration Lab (SIL), and Viasat’s NetAgility product.
Today’s high-demand data environments depend on effective network-centric communications, which can determine mission success and determine the survivability of the warfighter. Conventional approaches have resulted in inefficient systems experiencing bottlenecks and stalled network traffic. A new generation of network acceleration systems is needed to relieve the pain.
Legacy architectures like TCP and UDP [transmission control protocol and user datagram protocol] are pervasive in computer networking. Historically, these protocols have demanded a heavy pro cessing burden on host CPUs and been a key cause of network traffic bottlenecks. As network speeds have increased from 1G to 10G to 40G/100G bps and beyond, host processors continue to be burdened by bottlenecks that throttle critical net work traffic resulting in stalled and inef ficient systems. These bottlenecks can be detrimental to high-demand, contested environment, mission-critical applications. The problem gets even worse in a burst network traffic environment where servers and clients are separated by layers of switches and routers causing significant delay, jitter, and erratic behavior.
Industry attempts have been focused on relieving network congestion and improving throughput by implementing some functions of the TCP/IP protocol suite in com munications controller chips like media access controllers (MACs), integrating CPUs or introducing an ASIC [applications-specific integrated circuit] on the adapter card (NIC) to run the stack. Most of these have been in the form of partial offloads and have resulted in incremental improvements in network utilization from 10% to 30%, which still leaves 60% to 70% unused capacity and efficiency.
Technical advantages in the current landscape Technology has evolved which supports different approaches to tackle network-based challenges including partial offload capability, which improves performance primarily where TCP connections are held open for a considerable period of time. The CPU software still handles connection setup, retries, and exceptions, causing it to stall execution of other application tasks. It also enables the operating system to move all TCP/IP data segment of traffic to specialized hardware on the network adapter while leaving TCP/IP control decisions to the host server.
The two popular methods to reduce the CPU overhead include the TCP/IP checksum offload, a technique that moves the calculation of the TCP and IP checksum packets from the host CPU to the network adapter, resulting in a reduction in CPU utilization;
or the large send offload (LSO), which frees the operating system from segmenting the application’s transmit data into MTU [maximum transmission unit]-sized chunks.
These techniques deliver performance benefits for traffic being sent, although offers little improvement for traffic being received.
In contrast, consider full offload capability, an approach taken to offload all of the components of the TCP communications stack:
› Improves efficiency and data integrity by handling all protocol and data processing-related tasks
› Enables multiple concurrent sessions (from 4 to 1,000 or more), extending network bandwidth and serviceability
› Minimizes network contention and interrupts, enabling emphasis on improved application I/O transaction performance
› Creates network efficiencies by involving the host processor only once for every I/O transfer via memory, substantially reducing the number of requests with no interrupts to the CPU
› Improves system performance by copying data directly from assigned buffers into application memory buffers, removing the three main causes of TCP/IP overhead: interrupt processing, memory copies, and protocol processing
This full offload architecture implements innovative approaches in different technology layers, delivering ultra-fast hardware search engine capability specially designed for efficient search of TCP states in a dynamic array; scalable depth/width of the search engine, enabling a greater number of “state fields” to be searched simultaneously, made possible by ultrawide processing paths of the field-programmable gate arrays (FPGAs); and highly parallel pipelined building blocks automatically scaled up or down, depending upon number of active TCP sessions. These approaches achieve no-jitter processing and data delivery.
As industry experience verifies, CPU-centric silicon technology is unable to deliver sufficient CPU power to meet the most demanding network requirements, although this TCP/UDP acceleration technology implemented in high-performance FPGAs has been solving this problem for the last 13-plus years in commercial, industrial, and military applications.
Below are several defense and military application areas and use case examples. Target areas are the digital battlefield, network-centric warfare, ultra-fast missioncritical and precise communications among military command centers, theatre man agement, satellite base station-to-base station communications, urban warfare, and satellite-to-ground communications.
› Multiple channels receiving large, complex data sets from many sources that need to send/receive real-time, mission-data imagery
› Critical transfer of TCP/UDP communication data between ground stations, by multiple simultaneous channels with low levels of nanosecond latency and zero jitter
› Transfer of TCP/UDP encrypted data between ground stations requiring network security and high-speed data delivery
› Image-transfer applications that require real-time transfer of large images (> G bytes per image) at near 10G or 40G line rates
› Ground stations supporting satellite systems distributing data and images live to an active, complex network
Technology has evolved which supports different approaches to tackle networkbased challenges including partial offload capability, which improves performance primarily where TCP connections are held open for a considerable period of time.
In today’s remote work environment where Zoom (or other remote-commu nication platforms) are used by hun dreds of clients to share live data files, conventional TCP network architectures cause jitter and spikes in presentation. Using TCP offload solutions at the server level handling multiple ranges of client interactions can remove jitter and spikes completely, eliminating the incident of loss of data and misinterpretation. Now consider how critical that kind of network fidelity could be to a military operation.
These customer projects have experi enced network acceleration performance gains of between five to 60 times over conventional approaches, depending on the complexity of the target server/client network.
MES
Kelly Masood, president and CTO, is the founder of Intilop, a company that develops and provides advanced high-complexity network-acceleration and networksecurity solutions. Since 2009, Kelly and his team at Intilop have developed and deployed worldwide 11 generations of full TCP and UDP offload IPs and system solutions from 1 G bps to 100 G bps. His industry experience includes Lockheed Martin and also leading projects with companies including L3, General Dynamics, Lockheed Martin, AMD/ Xilinx, and Intel/Altera. Readers may reach the author at kelly@intilop.com.
Intilop Corporation https://www.intilop.com
The
Augmented reality (AR) is not exactly new technology – the first functional AR systems stretch back to the early 1990s – but the situation in the defense industry has changed dramatically in recent years. Once more of a novelty than practical technology, now military contractors use AR for everything from training to manufacturing to battlefield operations – and that trend is likely to increase.
Lt. Jeff Kee explores the Office of Naval Research (ONR)-sponsored Battlespace Exploitation of Mixed Reality (BEMR) lab located at Space and Naval Warfare Systems Center Pacific, a space to demonstrate cutting-edge mixed-reality, virtual-reality, and augmented-reality technologies and to provide a facility where warfighters, researchers, government, industry and academia can collaborate. (U.S. Navy photo by John F. Williams/Released)The military-electronics industry expects that growing computing power and data processing capabilities will continue to fuel the growth of augmented reality (AR) in defense. Industry insiders say that despite the fact that contractors have already found a wide range of uses for AR, they may have only scratched the surface of what this technology can do.
Augmented training has seen wide implementation in the world of training thanks to its versatility and cost-saving potential.
Mike Blackford, director of business development for simulation solutions and services for Raytheon subsidiary Collins Aerospace (Charlotte, North Carolina), says that the company is currently working on AR technologies in the areas of maintenance training and small-footprint mobile task trainers to support the full-flight and mission simula tors used by the U.S. Air Force. AR augmentations to the trainers include heads-up displays (HUD) and avionics familiarization trainers, he says. (Figure 1.)
The benefits of AR technology for these purposes include a smaller foot print and a lower cost, which results in easier access for point-of-need training and more access for more students, Blackford states.
“For example, difficult events within the full-flight and higher-end mission trainers can be rehearsed prior to the student entering the higher fidelity trainers, thereby increasing the throughput in those devices,” Blackford notes. “We see a reduction in numbers of instructors per student throughput due to the ability of the students to learn on their own.”
Some other benefits include roundthe-clock access to training content for those who want to train on personal time. Moreover, if the training platform is connected to a learning management system, the training can be measured easily. Finally, AR-enabled trainers make it easier to use lower-cost commercial off-the-shelf (COTS) equipment, a move that accelerates the adoption rate of this technology, Blackford says.
Figure 1 | An example of a Collins Aerospace VR-based Mission Trainer housed in the back end of an aircraft. Photo courtesy Collins Aerospace.The question of whether to use virtual reality (VR) or AR comes down to the type of training event: If the event requires a realistic touch, feel, and feedback, officials are more likely to go with an AR solution. But if the event is more about familiarization, VR is the preferred solution.
In the coming years, Blackford says that he expects AR technology to continue to mature to the point that most VR-based applications will evolve into the AR space.
“As key audiences become more comfortable with the technology, we believe it will be leveraged for additional training events,” he says. “You will always have groups who believe this type of training isn’t good enough, but as higher-fidelity full-flight trainers prove to instructors and students that they can learn through this technology, acceptance will increase and it will be used for more training tasks.
“The massive investment being made in the commercial industry toward this technology has already accelerated its adoption rate and we don’t see that slowing down anytime soon,” he adds.
Collins Aerospace is just one defense contractor using AR for training: In September 2022, AR developer Red 6 announced it was collaborating with Boeing on a project that involves “develop[ing] leading edge aerial dogfighting technology and training in advanced tac tical aircraft,” according to a company statement. This project would involve putting Red 6’s Advanced Tactical Augmented Reality System (ATARS) and Augmented Reality Command and Analytics Data Environment (ARCADE) into Boeing-manufactured aircraft, like the T-7 and F-15EX platforms.
“Using the system, pilots will be able to see and interact with augmented reality aircraft, targets, and threats on the ground or in the air while flying and training in their actual aircraft, reducing the cost of and need for multiple plat forms and ‘real world training exer cises,’” the statement reads.
AR for manufacturing AR isn’t just being used in training applications – companies see promise with manufacturing as well, particularly in conjunction with VR. Mike Ambrose, vice president of enterprise business transformation for Lockheed Martin sub sidiary Sikorsky (Stratford, Connecticut), says that the company is using both AR and VR technology for every stage of the product lifecycle, from concept devel opment to manufacturing to the supply chain. (Figure 2.)
“The model-based design data that we create to meet customer requirements ... is incorporated into virtual-reality and augmented-reality tools that accelerate delivery,” he says.
The company uses both VR and AR tech nology to help engineers, factory-floor employees, aircraft maintainers, and the customers themselves “identify and implement efficient, ergonomic work processes,” Ambrose says.
He says that the company accomplishes this task by taking digital data and using it to design a factory that operates more quickly and efficiently.
“Our teams can use the digital model to make our aircraft easier to maintain, and even reduce problems through use of digital tools,” he says. “An example of this is the use of digital torque wrenches calibrated to tighten each bolt to the correct tolerance. When the bolt is tightened to the correct tolerance, the employee using VR glasses and the wrench sees a green signal that lets them know the job has been done correctly.” (Figure 3.)
In the past, when companies only had computer-aided design, they did not have access to digital data on key attributes, specifications, and tolerances.
“In order to have things like virtual reality, you have to have all that data linked,” Ambrose says, who credited VR with reducing gearbox development from three years to a year and a half. “Once that data is in place, you can design the work environment, the work processes, and the aircraft using digital data.”
Asked whether the company placed more emphasis on VR or AR, Ambrose says both were essential.
“Augmented reality supplements virtual reality,” he asserts. “Model-based design and high-powered computing enable both of them.”
As for the future of AR and VR, Ambrose says the rise in computing power is likely to have a big impact.
“As computers become more sophisticated, VR technologies will have access to even more data,” he says. “Also, as more of our suppliers and customers become proficient in the use of these technologies, model-based design will become even more effective.”
AR on the battlefield AR can also be used for battlefield applications. One of the chief potential benefits that the industry has zeroed in on: increasing situational awareness for soldiers.
Northrop Grumman (Falls Church, Virginia) is working with Microsoft’s HoloLens
technology to create an AR headset that provides a graphical overlay on top of a transparent lens that can show additional information to the soldier. The soldier still sees the battlefield as normal, but the lens would provide an interface with detailed intelligence necessary to the mission, according to information on Northrop Grumman’s AR page.
Northrop Grumman’s info says that AR is currently being used by the U.S. Army with the Integrated Visual Augmentation System (IVAS), which includes a ruggedized version of the HoloLens.
Some of the most promising future applications on the battlefield for AR technology include reconnaissance, command, and special operations, but its capabilities could go far beyond that.
On the company’s site, AR team member Wes Harden sums up the AR situation: “Ultimately, we’re developing a user interface that can be applied in a multitude of different ways to many different sectors."
MES
Recent trends in the defense industry show a convergence towards standardizing electronic systems using open standards to increase interoperability, scalability, and reliability; reduce system costs; and minimize the number of custom electronics designs that increase overhead and maintenance.
In 2019, a U.S. Department of Defense (DoD) Tri Services memo was published calling for a MOSA [Modular Open Systems Approach] to be used to the maximum extent possible for future weapons-system modifications and new-start development
programs. The memo, titled “Modular Open Systems Approaches for our Weapon Systems is a Warfighting Imperative,” specifically cites The Open Group’s Sensor Open Systems Architecture (SOSA) Consortium, in addition to the Open Mission Systems/Universal Command and Control Interface (OMS/UCI), Future Airborne Capability Environment (FACE), and Vehicular Integration for C4ISR/EW Interoperability (VICTORY) standards “as vital to our success.”
What does all this alphabet soup really mean? Are MOSA, SOSA, FACE, VICTORY, and others just more attempts by the government to provide the same frame work for oversight within different groups? The answer: The government is trying to provide some guidance with respect to the services (Army, Navy, and Air Force) involved in key weapons development. This MOSA memorandum really announced that there was a need to insure interoperability and commonality across key hardware and software development.
For many years prior, each of the service branches, in cooperation with industry and academia, have undertaken development efforts that have led to many of the working groups including the establishment of OMS/UCI, SOSA, FACE, and VICTORY. These working groups and their efforts have all contributed to the MOSA initiative and driving commonality across future design efforts. Modularity and flexibility from both a manufacturing and design standpoint enables users to address thermal-management considerations and provides adaptability where standards may deviate. Often customers are trying to move the goalposts and push the boundaries of capability and performance; with a modular approach internally,
this flexibility can often be achieved by substitution of one part of another to enable a quick-turn deliverable.
SOSA and VPX power management VPX (VITA 46) and OpenVPX (VITA 65) are two popular standards that are being adopted rapidly, with VITA 62 providing the guidelines for developing a power supply to support both VPX architec ture requirements. The modular powersupply standard includes provisions for redundancy, scalability, and energy storage for systems that may require hold-up. While VITA 62 is intended to support VPX applications, system designers can implement the modular power supply in applications that are non-VPX. (Figure 1.)
The VITA 62 standard provides guide lines for mechanical packaging, electrical and mechanical interfaces, and com munication specifications that a power
supply can contain. Most common offthe-shelf VITA 62-compliant power sup plies are equipped with six outputs:
› a. VS1 +12V
› b. VS2 3.3V
› c. VS3 5V
› d. AUX1 -12V
› e. AUX2 +3.3V
› f. AUX3 +12V
Outputs VS1, VS2, and VS3 are intended to be high-current or high-power out puts, while the auxiliary outputs are for
low power and signal circuitry. VITA 62 power supplies can have different com binations of outputs on VS1, VS2, and VS3 to support VPX applications.
SOSA specifies a power supply with fewer outputs than VITA 62 while heavily referencing VITA 62, VITA 46, VITA 48, VITA 65, and various MIL-STD standards for design guidelines and power and electromagnetic compliance (EMC).
SOSA aligned power supplies only have two outputs, VS1 12V and V(AUX) 3.3V. The VITA 62 standard also defines stan dard control logic, both analog and dig ital, for operating the power supply, which increases interoperability and reduces designers’ burden for implementation.
Both SOSA aligned and VITA 62 power supplies can be equipped with two inde pendent I2C communication channels. An optional communication interface is defined in VITA 46.11 utilizing the intelli gent power-management interface (IPMI 2.0), commonly used in autonomous computer systems that provides manage ment and control of the power supply.
Power supplies designed around VITA 62 and SOSA have multiple input AC and DC input options with a fixed number of outputs; the classes of power supplies to support open architectures are often categorized by their input voltage.
All power supplies defined by the VITA 62 and SOSA standards have at least two alignment key slots based on their input power characteristics. A 3U power supply with a 16V to 50V DC input cannot be inserted into an application that requires 3U single-phase AC power when the system designer implements keying defined by Tables 4.3.2 in VITA 62.0.
Deployment of any new power solution in a defense application requires meeting various environmental and electrical MIL-STD standard specifications before adoption. VITA 62-compliant power sup plies can optionally meet EMC compli ance defined in MIL-STDs 1275, 704, and 461, listed in Section 3.2 of VITA 62.0. Testing power supplies in systems can be a multimonth process requiring iterations
Figure 1 | Shown: 3U and 6U VITA 62 power supplies.to the design of the power supply, EMI filtering, or system backplane to pass required EMC standards. VITA 62 and aligned power supplies stand out in the market by guaranteeing all power-supply models comply with the standards listed in their datasheets and are verified at independent certified test labs.
Figure 2a shows a typical VPX power supply two-stage application where stage 1 is a front-end three-phase AC input module coupled with an energy storage hold-up card to provide 50 ms hold up at full power. The first stage provides a single 28V output and is connected to the second stage, a backend VITA 62 supply where the outputs are loaded at 600 W in aggregate. Calibrated test lab EMI scans in Figure 2b show the entire system passing MILSTD-461G CE102 EMI scans.
Scalability of power solutions is a cornerstone of open systems architecture standards. To this end, VITA 62 and SOSA
standards provide recommendations for power supplies to be paralleled to combine the output capability of their main outputs. Design standards reserve contacts on the connector interface of the power supply to simplify paralleling power supplies and balance their output current sharing.
Paralleling can be taken a step further by unloading the burden of paralleling from the system architect by facilitating current sharing between supplies without the need for reserved contacts that are dedicated for power sharing between supplies. Conventional VPX power supplies require careful system design and special power supply part numbers to enable current sharing between supplies.
Current sharing between power supplies from Vicor have a proven wireless droop sharing algorithm. Figure 3 shows the VS1 +12V output of a 6U power supply operating in paralleling mode. The output voltage varies with load current while still maintaining its voltage within the VITA 62 limits. The power supplies have been tested with as many as four units operating in parallel for current sharing. (Figure 3 and Figure 4.)
If the system designer only requires a single power supply in their application, the power supply can be reconfigured through its I2C communication interface on the fly to disable droop sharing, thus achieving better than 1% output tolerance with under variable load.
I2C communication with SOSA aligned and VITA 62 power supplies are defined by the VITA 46.11 standard. Conventionally, a 3U power supply supports four addresses, which are set by the application by pulling address pins to logic high or logic low. 6U power supplies support five addressing pins and a wider range of possible I2C address assignments. In a single VITA 62 power-supply application, the system designer can
now ignore (No Connect) the I2C pins and communicate with the single power supply on address 0x20.
Another advantage in deploying a modular power supply in an application is the ability to have fast start up times by default or customizable start up times and sequencing. In single-stage back-end power-supply applications, the power supplies are capable of 200 ms startup on all outputs for applications that require it. (Figure 5.)
VITA 62 and SOSA aligned power supplies are designed to be modifiable at the fac tory to vary the output voltage as well have different output voltage combinations that are not part of the standard offering for a variety of applications. (Figure 6.) By using a modular approach internal to the packaging, the user can usually provide changes to output voltages or power levels in short order.
MES
Figure 4 | A stack of four VIT028x6U power supplies can boost system output power capability by 360% compared to a single
5 | In single-stage back-end power-supply applications, default is 200 ms startup on all outputs.
6 | Power supplies can be customsequenced at the factory for a different application.
Matt Renola is Senior Director, Global Business Development –Aerospace, Defense and Satellite Business Unit at Vicor. Matt has been with Vicor for 15 years and has been responsible for managing the Vicor sales teams and global accounts in all of Vicor’s main vertical markets. He has more than 30 years of technical sales and marketing experience and has also worked for major OEMs including Artesyn Technologies, Emerson Network Power, and Vishay Intertechnology. He has an undergraduate degree from Boston College and an MSE from the University of Pennsylvania.
Vicor
SOSA Technical Standard 1.0: Impact on EW designs
Multiple intelligence (Multi-INT), sometimes referred to as multi modality, is a popular term used in recent years to describe C5ISR [command, control, computers, communications, cyber, intelligence, surveillance, and reconnaissance] applications in which data obtained from disparate sensing sources is fused together to derive new information and operational insights. In some cases, this can mean the fusion of SIGINT [signals intelligence] data and radar data, or SIGINT data with EW [electronic warfare] data and EO/IR [electro-optical/infrared] data. In other cases, it may mean combining real-time data with post-mission analysis from previously processed data. Additionally, there are approaches where artificial intelligence (AI) and machine learning (ML) assist via data and information analysis to identify patterns or predict outcomes.
With the U.S. Department of Defense (DoD) push for Modular Open Standards Approach (MOSA)-based architectures, there is strong intent to leverage that proper level of modularity from stan dards like the Sensor Open System Architecture (SOSA) to enable common
building blocks to support multiple mission types, adding an extra dimension to mul tiple intelligence or Multi-INT.
One of the key tenets of Multi-INT or multi modality is that the architecture by its very nature is realizable through the core components of a sensing system which can accommodate more than one mission at the same time. This means when dispa rate mission modalities operate simultaneously (or in series), the system can gather
data from those modalities and process it for actionable intelligence (It is worth noting that the core components of the sensing system could include hard ware level plug-in cards [PIC], software [application software, for example], front-end sensing apertures, and some manner of system management and task management).
SOSA as an enabler of Multi-INT With MOSA in mind, from the technical and business acquisition perspective, and SOSA as an enabler of MOSA for something like Multi-INT, we see that the SOSA Reference Architecture (RA) is fundamentally well positioned to help realize the potential of Multi-INT appli cations. This is evident from some of the SOSA products, such as the logical building blocks (SOSA modules) and the SOSA taxonomy that make up the SOSA RA (as seen in Figure 1 and Figure 2, respectively).
Figure 1 is the core of the SOSA RA. This RA is described, and in so doing, is encompassed, by modules and inter faces; where each module exhibits func tions and behaviors; and interfaces, both logical or physical in nature. The SOSA Consortium was deliberate in its devel opment of these modules and interfaces to ensure independence and low (or loose) coupling. (“Low coupling” means that changes in one of the modules will not impart changes to the others.)
From the SOSA RA technically oriented architecture principle number 13, in section 3.2.2 of the SOSA Technical Standard v1.0, we see the SOSA mod ules exhibit these criteria:
› Severable (can be separated and used elsewhere) – based on business needs, timing requirements, or other drivers
› Has minimal complexity interfaces (minimum interdependencies)
› Can operate as stand-alone or be operated via function/process/ system manager
› Is independently testable
› Does not expose IP
› Facilitates competitive procurement
› Encapsulates rapid change
In Figure 1, we see the potential for how one could envision and subsequently develop any type of sensing system, either for single mission modality or Multi-INT. These logical building blocks, the SOSA modules, enable a variety of implementa tion types.
The importance of this perspective is furthered when we look at the SOSA Taxonomy (Figure 2). That’s because SOSA isn’t solely a set of logical building blocks (i.e., the SOSA modules): it is also a set of infrastructure building blocks. These include items like hardware elements (PICs [peripheral interface controllers], apertures, or connec tors), software runtime environments, or interaction infrastructures, all things used to create capability with SOSA modules. From this we see what SOSA has ultimately accomplished: SOSA has created a sandbox of, to repeat, building blocks (tools) for the developer and end user.
Let’s take a closer look at some of those infrastructure items on the right of the SOSA taxonomy (Figure 2). One example, which is one of the more mature pieces of SOSA, is the hardware element PICs. As we evolve from single INT to Multi INT, we see how current architectures like SOSA and CMOSS [C5ISR/Electronic Warfare Modular Open Suite of Standards] potentially enable single-sensing capabilities on a per PIC basis. Alternatively, they enable the use of multiple types of cards (i.e., FPGA [field-programmable gate array], GPGPU, processor) in a common backplane profile, thereby enabling mission flexibility by swapping out card types.
An example of potential growth from component to system with these SOSA hard ware building blocks is shown in Figure 3. For SOSA, these hardware building blocks
(the PICs) are the proper level of modularity when one contemplates their use in either single INT or Multi-INT systems. These building blocks were developed for both cur rent and future needs.
Another important piece of SOSA infrastructure is software, whether this is application software (from a SOSA module perspective) or software runtime environments (RTEs). Within SOSA there are three RTE options: FACE, virtual machines (VM), or containers. These SOSA RTEs provide an execution environment for SOSA modules (these are the logical entities used in SOSA to develop capabilities), which a system designer can implement as portable software (FACE), containers, or VM.
The way these run time environments are built, based on the SOSA standard’s use of modules, is that capability can be developed that encompasses both software and hardware. It should be possible for contained pieces of software to have correct, welldefined interfaces with which the system designer knows how to interact. That makes it possible to take a piece of software from one place, such as from a card or some other hardware element, and perform the required configuration needed to support Multi-INT operations.
This is the big challenge: to understand how the data from multiple modalities interact. If a system is put into operation with one modality, and we want it to work simultane ously with another modality, it’s essential to know if the same system infrastructure, not just the cards, is able to support that, including all the front-end hardware. This consideration is important, as the front-end hardware includes front-end sensors that may have certain frequency-bandwidth or dynamic-range limitations.
While the DoD’s goal is to have plug-and-play system building blocks, it’s not clear if that model will enable system designers to reuse modules in another application, such as Multi-INT, without making any modifications. To minimize NRE [non-recurring engineering costs], it’s ideal that software is developed so that it’s both adaptable and can be moved from one place to another.
System design has evolved from discrete systems based on individual modalities to where it stands now, with individual modalities supported at the card level – including
software and everything else that goes along with it – in order to deliver a capa bility. In the future, with Multi-INT, it will be possible to integrate more than one modality onto a single card, with all of the associated software based on SOSA modules. Some of the fundamental pieces are now in place, but what really needs to happen to drive Multi-INT system design is an understanding, including all the specifics, of how to interact between modalities.
Where it stands now: The modality focus is at the card level. With that in mind, commercial off-the-shelf [COTS] vendors need to make sure that their PICs have the right interfaces to move the types of data and information in and out of their card and into other cards associated with a particular modality. Another thing for COTS vendors to consider: whether they have the right infrastructure to support two modalities on the same card now. COTS vendors should reach out to their customers to ask if they are thinking about Multi-INT and whether they have any architecture considerations in mind now.
SOSA brings the benefits of open standards to sensor system design. It also enables migration of applications between domains, such as from ground
to airborne platforms. The intent for standards is that they provide building blocks with well-defi ned open interfaces, and the interfaces determine what’s needed to be able to talk and interact with a particular building block. That makes it easier for an end user to build a system using those building blocks, and then to build a completely different system using those same building blocks. In the case of SOSA, while various domains – air, ground or sea – may embrace the SOSA interfaces, there may still be constraints that prevent the migration of an application from one domain to another, such as size and power limitations.
Ideally, it will be possible to take any SOSA card and use it on any platform: for example, an EW card and its application that are used in an Army ground platform could also be used in an Air Force airborne platform. What needs to be considered ultimately: Whether that model will be simple, or if there are other considerations involved when going from one physical type of platform to another, with both platforms operating in different domains but using the same modality. Will one platform have certain constraints that another platform doesn’t? There will be some cases where the physical space is limited, where the space is too small or there are power constraints. There may be situations where it won’t be possible to migrate a card with certain capabilities into another physical domain. The good news is that SOSA is well positioned to consider these variables.
One potential next step in the evolution of SOSA is for the SOSA Consortium to focus on Multi-INT. The industry is moving into a realm where solutions that were previously discrete instances can migrate into complex systems. While every community within SOSA has its own perspective – whether government, COTS suppliers, system integrators or academia – the SOSA Consortium model enables all of those perspectives to come together in one room where all the different communities can listen and interact with each other. By coming together, all the varied communities can work to evolve the standard and define the next building blocks needed to make Multi-INT a reality.
C. Patrick Collier – cofounder of SOSA and chair of its Hardware Working Group – is an open systems architect and systems engineer at Aspen Consulting Group. He was a lead hardware engineer at NAVAIR, where he focused on developing the Hardware Open Systems Technology (HOST) set of standards. Patrick also founded and is currently chair for the VITA 78 (SpaceVPX) and VITA 78.1 (SpaceVPXLite) efforts.
Denis Smetana is a senior product manager for DSP products for Curtiss-Wright Defense Solutions, based out of Ashburn, Virginia. He has more than 30 years of experience with ASIC and FPGA product development and management in both the telecom and defense industry and more than 15 years of experience with COTS ISR products. He has a BS in electrical engineering from Virginia Tech.
Aspen Consulting Group · https://www.aspenconsultinggroup.com/ Curtiss-Wright Defense Solutions · https://www.curtisswrightds.com/
With you at every stage!
Designed to Thrive, Built to Survive.JetSys NetSys ComSys
Using SOSA aligned components, a complete software-defined radio (SDR) solution was created for a TSOA-ID event in a little over two weeks, representing up to a 10-time reduction in cost and schedule compared to solutions developed without the use of well-defined open standards. It’s an open road for the development of improved technologies in military and defense applications.
The Open Group’s Sensor Open Systems Architecture (SOSA) Technical Standard
1.0 was released in September 2021, after almost three years of collabora tion between the U.S. Department of Defense (DoD) and more than 100 man ufacturers of embedded hardware and software. The resulting SOSA Technical Standard promotes portability and reuse of sensor components by defining hard ware, software, and interface standards. For RF and SDR [software-defined radio] payload card vendors, this also means complying with the Modular Open Radio
Frequency Architecture (MORA) specification to ensure their VPX cards can be suc cessfully utilized as envisioned by SOSA.
Of the many steps to test and validate interoperability in a SOSA aligned system, the point at which system designers start thinking about how they will command and control a device from the outside world makes up a crucial piece of the puzzle. This integration requires implementing various MORA and Vehicular Integration for C4ISR/ EW Interoperability (VICTORY) interfaces that enable other components to discover the hardware and “talk” to it for command and control, data ingest and egress, health and status, and then determine its capabilities.
Most hardware vendors focus on the mechanical and electrical requirements defined by the SOSA Technical Standard, whereas software companies tend to focus on the
interface requirements of the card being created. It’s just the natural delineation to play to each side’s core competen cies. Thanks to open standards initiatives like SOSA, more hardware and software companies are collaborating during the development process. The result is that engineers are confident that at the end of the hardware development cycle they will know what is required to fully integrate the card into a SOSA system.
Collaboration among hardware and soft ware developers means ensuring that the time and resources to upkeep the imple mentation of open standards-based interfaces, including MORA, in software and firmware can be shared and allocated appropriately. Such sharing typically enables internal hardware-development teams to focus more on product innova tions and applications.
The common goal of open systems stan dards development is interoperability among platforms, systems, and related components. Validating interoperability
can manifest itself in different ways. There are companies working collaboratively to develop mechanisms utilized in a broader sense across the industry, as well as phys ical demonstrations and testing held at events like the Tri-Service Open Architecture Interoperability Demonstration (TSOA-ID). Such was the case for Sciens Innovations and Epiq Solutions coming together.
Because they were both members of SOSA, Sciens Innovations and Epiq Solutions knew of each other for years through the SOSA community. Sciens’ reputation for imple menting MORA aligned software and firmware within the DoD tied in nicely with Epiq Solutions’ growing line of SOSA aligned SDR hardware.
After discussions, Epiq Solutions and Sciens Innovations decided to create a demo that would show the realization of leveraging Sciens’ MORA software layer on top of Epiq Solutions’ hardware for a live demo at an upcoming in-person TSOA-ID. Creating and demonstrating an SDR product and streaming the results in real time would fully utilize Epiq Solutions’ competencies as an embedded SDR card vendor and Sciens’ abilities as a software and firmware development team, a natural pairing of capabili ties. (Figure 1.)
Sciens used its helux tool kit, developed to fit a specific need in the development of SOSA aligned systems, which would enable the discovery, command, and control of Epiq Solutions’ Sidekiq VPX400. The SOSA aligned Sidekiq VPX400 is a wideband RF card with multireceive and multitransmit capabilities, which would serve as the SDR for the demonstration.
During the TSOA-ID demonstration, this SDR card was able to ingest 800 MHz IBW [instantaneous bandwidth], search for signals of interest, then reconfigure on the fly to find a signal and transmit in that signal range. Without the SOSA standard, this level of integration between hardware and software would typically take several months to bring a demonstration together. By leveraging the MORA specification defined within SOSA, that timeline was reduced to a few weeks.
From zero to 60
From start to finish, the demo was created, tested, and showcased in just two and a half weeks. Along with the hardware-agnostic helux tool kit from Sciens, it included the four main components found in a typical signal-processing system:
› SDR (Epiq Solutions’ Sidekiq VPX400)
› Single-board computer/SBC (connected over 1 GbE and 40 GbE)
› SOSA/CMOSS VPX chassis
› User interface
Prior to MORA and SOSA, each component would have had to have its own docu mented interface specifications defining the architectures a specific interface connects to, capability discovery of each component, and configuration of available resources. For example, in the absence of standard interfaces, the virtual knobs of the SDR would
need to not only be manually searched for, but the definitions of how the knobs could be configured and to what ranges would also be required.
Then comes the arduous task of ensuring the specifications meet the requirements, with the possibility of discovering – many, many hours into development – that the multiple specifications coming together yield a shortage of spectrum range capability, for example. Simply transfer ring RF signal metadata between two components had a high chance of not aligning due to specification incompat ibility, resulting in loss of information and system functionality.
Using Sciens’ helux reference design to provide MORA 2.4 enabled interfaces for Epiq Solutions’ Sidekiq VPX400, the tedious and manual error-ridden pro cesses associated with assembling a standardized SDR card were eliminated, a testament to SOSA’s principles put into practice.
The Sidekiq VPX400 RF transceiver rep resents a single card that can be con figured for many different operating modes. The SOSA primary RF payload slot profile (14.6.11-4) that the VPX400 uses automatically ensures the card’s compatibility with the system into which it is being plugged in. As such, the card becomes immediately functional from an electrical and mechanical standpoint and supports the basic interface require ments of a SOSA RF payload module. (Figure 2.)
Additionally, MORA provides the stan dardized resource discovery, capability profile, management, control, data, and context messaging transported over an Ethernet VICTORY Data Bus (VDB) and Ethernet MORA Low Latency Bus (ML2B). So a MORA board support package (BSP) enables standardized access and control of the RF chain on an SDR payload card such as the VPX400. The Sciens Innovations’ MORA Explorer application running on a separate SBC was used to interface to the VPX400 over VDB and ML2B and provide easy control and observability of this MORA resource.
Figure 3 | The reference design in the helux software and firmware tool kit helps users avoid the manual processes associated with integrating a standardized SDR RF payload card into SOSA aligned systems.
Using a hardware-agnostic, holistic MORA toolkit provided the software and firm ware foundation, the tooling for demonstration, and the support system to keep the project successful and compliant, while facilitating rapid development. The helux tool kit includes software implementations of MORA/VICTORY interfaces, HDL modules for framing, filtering and arbitration of MDM/UDP [Mobile Device Management/User Datagram Protocol] packets, and tools to facilitate end-user interaction and demon stration of SOSA hardware. (Figure 3.)
This approach substantially reduced development time, which will ultimately affect market-entry cost by offloading the risk and financial commitment required for each SOSA hardware vendor to assemble their own MORA software/firmware team. With the common software/firmware integration requirements already handled, hardware vendors can focus on better capabilities for their hardware and the SOSA physical hardware requirements. The result: A far more efficient approach and a more stable solution given that the tool kit supports many cards.
Eliminating integration errors is only one aspect of what the SOSA standard pro vides. For decades, system designers have had to work in the space between being restricted to having one payload slot for each sensor, creating large and cumbersome products, or limiting sensor functionality to get a smaller form factor. Success in bal ancing these demands for increased sensor functionality with smaller sizes has varied.
The versatile specifications defined by SOSA standard slot profiles end the tradeoff between more features/large size and a small form factor. Developers can pack many
SOSAfunctions and features onto a single card, while facilitating data transmission across interfaces for use by other components of the signal-processing system. Leveraging this versatility is one of the benefits out lined in the joint Sciens Innovations and Epiq Solutions demo system.
Putting the SOSA Technical Standard 1.0 into practice is showing real-world benefits, with expedited develop ment cycles through proven interoper ability demonstrations that are helping facilitate the adoption of SOSA and MORA by members of the military embedded community. The open stan dards approach results in greater avail ability of compliant hardware for the DoD to choose from as they try to meet their mission needs.
MES
Travis Doll, Ph.D., the CEO and president of Sciens, is a software engineer specializing in digital signal processing with many years of industry experience in developing and delivering robust collection capabilities to the intelligence community. Dr. Doll earned both his Ph.D. and master’s degree in electrical engineering from Drexel University in Philadelphia. During his graduate years, Dr. Doll was awarded two National Science Foundation Graduate Teaching Fellowships to develop and implement STEM education within the Philadelphia school system. He received his bachelor’s degree in computer science from Dickinson College in Pennsylvania.
John Orlando is CEO and co-founder of Epiq Solutions, an engineering company focused on delivering software-defined radio (SDR) products and turnkey RF sensing solutions. He is an author and presenter on all things SDR, most recently presenting at GRCon 2021 on “Breaking through the 6 GHz Barrier.” He earned a master’s degree in computer science from the Illinois Institute of Technology (Chicago) and a bachelor’s degree in electrical engineering from Rose-Hulman Institute of Technology in Indiana.
to 4 DP/DVI/HDMI independent outputs
supports PCIe Gen4 Integrated PCIe Gen4 Switch
product is one of a family of WOLF products that supports
choice of NVIDIA Ampere
modules, with options for
industrial or mil/
operating temperature
the bandwidth needed to move large data sets, enabling demanding sensor, C5ISR, and other data-heavy tasks.
This guide provides a breakdown of what VPX is, how it is used in military applications, and the major players in the industry.
The military environment is unique when it comes to computing. There are space constraints, as well as concerns about how the harsh environments military sys tems typically operate in affect embedded computer systems. Moreover, data-pro cessing demands on computer systems are increasing contsantly as military customers seek more and more computing power. That’s where the VPX backplane architec ture comes in.
This backplane connector system uses a robust switched-fabric architecture to drive computing power while also making it suitable for embedded military systems. VPX can handle tremendous computing speeds while also giving mili tary customers the flexibility they need, whether it’s in use in the air, at sea, or on the ground.
The VPX standard (also known as VPX VITA 46) is an open architecture computer standard that better facilitates the flow of data in embedded systems. It is dif ferent from commercial computer buses and unique to the military embedded computing market.
VPX goes a step further than past computer buses (like VME) by basing the system on switched fabrics rather than a typical computer bus. In the case of other buses, the signals must wait in line, which results in slower processing speeds. In contrast, fabrics allow the system to have express lanes. So while VPX isn’t necessarily faster than VMEbus, it offers greater scalability and is therefore valuable in military applications.
The VPX form factor uses state-of-the-art fabric architectures such as Ethernet, RapidIO, and InfiniBand to keep current with today’s data transfer rates.
VPX is preferred in the defense industry because of the immense data-speed demands of C4ISR [command, control, communications, computers, intel ligence, surveillance, and reconnaissance], SIGINT [signals intelligence], EW [electronic warfare], and other types of applications. These systems require high-performance computing often in challenging environments, making VPX the preferred choice in this area.
The VPX system was built on VITA stan dards known as VITA 46, the founding architecture for the standards. The OpenVPX standard is built on VITA 65 (which is itself based on VITA 46), and it was developed to create an open architecture that enables compatibility between different products from dif ferent vendors.
The reason for this development was that by the late 2000s, many VPX con nectors and products used a single source for components; VITA 65 was developed to help open up the market and make it easier to build interoper able computing systems. OpenVPX manages the changing profile dynamics of the industry.
Besides VITA 65, other standards are used that were developed off the foun dational VITA 46 standard. There are standards for complementary power (VITA 62), fiber optic (VITA 66), and RF (VITA 67). There is also VITA 78, the Space VPX standard, which defines an open standard for creating backplanes and modules to assemble electronic systems for spacecraft. All of these are evolutions of VITA 46 architecture.
The physical difference between 3U VPX chassis and 6U VPX/OpenVPX chassis panels comes down to size: the 3U VPX dimensions are 132 mm in length, whereas the 6U VPX card dimensions are about twice that at 265 mm. However, this does not mean 6U VPX cards are twice as capable as 3U panels.
3Us have enjoyed a resurgence due to a need for smaller, more compact com ponents and the development of tech nology that allowed developers to pack more processing power into a smaller form factor.
Military benefits of VPX VPX has many applications in the aero space and defense industries in terms of embedded system computing. VPX stan dards are used throughout the supply chain, from components to subsystems.
It has enabled companies to use com mercial off-the-shelf (COTS) products, which gives developers a larger field of suppliers to choose from.
OpenVPX in particular is a living stan dard that is constantly in development as the needs of military systems change. The U.S. Department of Defense (DoD) wants systems that use a modular open system architecture approach, and OpenVPX provides that. It also fits in with the standards of the Open Group Sensor Open Systems Architecture (SOSA), the governing standard that uses other open standards.
Here are some of the specific elements in embedded computing that use VPX:
› SBCs (single-board computers)
› I/O (input/output) boards
› Graphics
› Switches
› Backplanes
› Chassis
› Systems
› Connectors
› Cables
› Power supply
› Disk
› Software
The VPX ecosystem: major players in the VPX industry
There are about 200 companies heavily involved in the VPX industry. The biggest names among these are the principal SOSA members:
› BAE Systems
› Booz Allen Hamilton
› Cubic Global Defense
› Curtiss-Wright
› ELBIT Systems
› FLIR Systems, Inc.
› GE Aviation Systems
› General Dynamics
› HUBER+SUHNER Astrolab
› Intel Corporation
› L3Harris Technologies, Inc.
› Leonardo MW Ltd.
› Mercury Systems, Inc.
› Northrop Grumman
› Raytheon Company
› Sierra Nevada Corporation
› SRC Inc.
› VadaTech Inc.
There are also U.S. government agencies involved in the effort: The Army’s C5ISR Center in Maryland is a VITA member. Two agencies – the Air Force Life Cycle Management Center and the Joint Tac tical Networking Center – are SOSA spon sors. The Navy is also involved through a partnership with the Georgia Tech Research Institute, which is a member of the SOSA and VITA consortia. MES
VITA
https://www.vita.com/ SOSA
https://www.opengroup.org/sosa
The
an example of
The newly enacted CHIPS Act (signed into law August 9, 2022) represents a potential boost in U.S. semiconductor fabrication by providing subsidies to U.S. chip manufacturers and funding for technology and research development. At a high level, the CHIPS Act is set to revitalize domestic manufacturing, lower sourcing costs, and increase job creation, all while strengthening the overall global supply chain.
However, some industries will fare better from the CHIPS Act than others. The defense and aerospace industry, specifi cally, will be left noticeably behind. Why? They suffer from DMSMS – Diminish ing Manufacturing Sources and Material Shortage – where a specific part is designed out, or a supplier’s specific tech nology type is replaced with the next generation. Defense and aerospace sys tems are critically lagging in comparison to other industries because they do not have the resources needed to upgrade their systems to meet current techno logical advancements – advancements that the CHIPS Act prioritizes.
In short, defense and aerospace will not reap the benefits of the CHIPS Act for two main reasons:
1) the Act primarily addresses nextgeneration technology needs and not current or legacy technology needed by those sectors, and
2) the Act focuses on the more competi tive and high-volume, low-mix-related technology sectors, whereas the defense and aerospace sector is more aligned with high mix but lower volumes.
To increase effectiveness and longevity of their technology, the military relies on
systems that are field-proven after many years of deployment. Unfortunately, these legacy-type systems are far and away laggards in terms of technology advancement. That reality makes finding/sourcing/manufacturing these replacement parts difficult. Because of this lag, defense systems run counterintuitive to the current technological market in terms of component life cycles. Commercial industries have a vested interest in shortening component life cycles and regularly upgrading their systems to maintain a competitive advantage and encourage consumers to buy new products regularly. Meanwhile, the defense and aerospace industries seek to extend the life cycle of their components due to the compatibility and testing needs necessary when updating systems to the latest technology.
The CHIPS Act does not specifically address the defense and aerospace arena’s unique manufacturing position; rather, it benefits those with the resources to onshore production and develop their own fabrication plants (fabs). By building their own fabs, manufacturers have full control over the components they produce, which will ideally be built to the latest and more profitable technology. Defense companies could still be left struggling to source the components they need.
The CHIPS Act can also yield tremendous profit potential for those developing their own fabs, another competitive force the defense and aerospace industry is up against. First, fabs are expensive a single fab can cost between $10 billion and $20 billion and take as many as five years to build. With that level of investment in time and money, manufacturers need a strong ROI to make it worth their while. That ROI is most effi ciently found in products with the highest cost and higher volumes, which caters to companies with the best purchasing power (think commercial-sector products like smartphones and smart cars).
The defense and aerospace industry cannot keep up with the buying power of large consumer original equipment manufacturers (OEMs), such as Apple and Tesla, even before the shortage. For decades, defense and aerospace industry buying power lagged after moving to commercial off-the-shelf (COTS) sourcing in the 1980s and 1990s, which put them in competition with bigger players, who quickly dominated market share. During the chip shortage and in the aftermath, the market will continue to favor larger players, leaving scant room for defense and aerospace to make up ground in their production and sourcing strategies.
Between advancements in cutting-edge tech and low purchasing power, companies in the defense and aerospace industry remain in a constant struggle to secure adequate supply, and their long-standing constraints will persist.
Efforts to shore up the high-reliability supply chain that fuels U.S. defense and aero space verticals are more critical than ever before, but the industry must get creative in how it sources components and where they are willing to substitute or compromise, because relief will not be coming from the CHIPS Act.
Frank Cavallaro is CEO of A2 Global Electronics.
Global Electronics
Military Embedded Systems focuses on embedded electronics – hardware and software – for military applications through technical coverage of all parts of the design process. The website, Resource Guide, e-mags, newsletters, podcasts, webcasts, and print editions provide insight on embedded tools and strategies including technology insertion, obsolescence management, standards adoption, and many other military-specific technical subjects.
Coverage areas include the latest innovative products, technology, and market trends driving military embedded applications such as radar, electronic warfare, unmanned systems, cybersecurity, AI and machine learning, avionics, and more. Each issue is full of the information readers need to stay connected to the pulse of embedded technology in the military and aerospace industries.
The 2628AP Real-time Quad Stream PCM Format Simulator series includes fourth-generation low-latency multi-stream telemetry data simulation, advanced TMoIP [telemetry over IP] format data ingest and clock/data output, and optional PCM [pulse code modulation] format validation, record, and test functions. The 2628AP is designed to be light enough to support portable operations while withstanding rigorous shipboard and field mobile applications.
It is compatible with Acroamatics’ TDP product line and has a flexible hardware configuration (from one to four independent simulators). It also supports user-programmed steam rates exceeding 50 Mb/sec and performs in four operating modes: User Defined Stored Format Mode, Stored Format Dynamic User Data Mode (or UDF/User Data FIFO dynamic select data-insertion mode), Sim-Encoded Data recorded file streaming mode, or API user-defined data file mode. It can be delivered with the user’s choice of either Windows 10 or Linux RedHat OS.
Reveal Technology and Teal Drones (a division of Red Cat Holdings) are offering an enhancement of Reveal’s Farsight mapping software by automatically combining imagery from multiple unmanned aerial systems (UASs) to produce high-fidelity 3D maps.
The aim is to enable users to receive Farsight maps and analytics as quickly as possible by increasing the speed of data collection. It was recently demonstrated to U.S. Army Special Operations Command near Fort Bragg (North Carolina).
The software simultaneously gathers data from multiple drones, enabling a single operator to control four drones at once while conducting ongoing 360-degree target surveillance. The software provides line-of-sight analysis, terrain analysis and graphing, “best route” as generated by artificial intelligence (AI), vertical measurements, and a helicopter landing-zone survey. The intent of combining these features is to provide a team with advanced real-time awareness of the situation on the ground in order to increase the success rate of missions.
A man-portable, multidomain sensor package known as the Multi-Mission Explorer (MDX) can employ 3D radar technology combined with sensors to provide surveillance of the battlefield, according to product creator Liteye Systems. The company, which specializes in counter-unmanned aerial systems (C-UAS) technologies, uses 3D radar technology in combination with HD EO/IR [high-definition electro-optical/infrared] and cooled MWIR [midwave infrared] sensors to provide air and ground surveillance, target acquisition, and tracking.
The full MDX system offers RF surveillance and detection, 3D radars, HD EO/IR optical surveillance, target tracking, a laser target designation capability, and omnidirectional and/or directional electronic attack in a small, man-portable, or platform-integrated package that can be remotely operated and controlled by a single operator. The company says the platform is aimed at applications in fly-away security, force protection, expeditionary base defense, port and shoreline security, border security, and various inside and outside-the-wire mission applications..
TDK Corporation has unveiled a new series of ruggedized non-isolated DC-DC [direct current to direct current] converters that the company says can operate in harsh-environment applications like robotics, automated guided vehicles, and communications. The converters are capable of operating from an input voltage of 9 V to 40 V or 9 V to 53 V, and the step-down converter delivers output voltages that can be adjustable from 3.3 V to 15 V, 3.3 V to 24 V, or 3.3 V to 40 V with output currents of up to 20A. In a 1/16th brick form factor, measuring 35.6 by 25.6 by 13 mm, the converters are encapsulated to provide a higher resistance to shock and vibration. The five-sided aluminum case reduces radiated EMI and enables conduction cooling to a cold plate for fanless operation.
TDK says that the converters operate at efficiencies of as much as 98%, which helps to minimize power losses and enables the products to operate in extreme cold or extreme heat. The basic feature models include an output voltage-adjustment pin, negative logic remote on-off, remote sense, input under-voltage, overcurrent notification, and thermal protection. Full-feature models are equipped with a “power good” signal, output voltage sequencing, and the ability to synchronize the operating frequency to minimize system noise.
VPT has unveiled a series of commercial off-the-shelf (COTS) converters for space applications that are designed specifically for smaller satellites in low-Earth orbit (LEO) as well as NASA Class D missions. The VSC Series of COTS products are intended for so-called New Space applications as part of VPT’s space product line, which have been characterized for total ionizing dose (TID) performance including low dose rate (LDR) and single-event effects (SEE).
The VSC Series of DC-DC converters ranges from 5 W to 30 W of output power and includes single and dual outputs of 3.3 V, 5 V, 12 V, and 15 V with a wide input range of 15 V to 50 V with 80 V transient capability. The VSC Series is radiation-tested to 42 MeV/mg/cm2 and guaranteed to 30 MeV/mg/cm2 for SEE and tested to 50 krad(Si) and guaranteed to 30 krad(Si) for TID.
Portsmith offers a durable universal serial bus (USB) to 10/100 Ethernet adapter that is designed to withstand extreme environments on base, in the field, or in the air. The PSA1U1E-EG MIL-STD 810 USB 2.0 to 10/100 Ethernet interface adapter – created together with Portsmith sister company, SGW Designworks – was initially designed as an ultra-rugged part for a U.S. Department of Defense (DoD) client and is now available for wider military and commercial use, according to Portsmith.
The adapter can be used to connect equipment to field computers, tablets, or mobile devices for data transfer, synchronization, programming, or other use cases requiring a reliable and secure wired connection. The adapter is designed to function even after being exposed to blunt force or extreme environmental conditions. The design of the part is intended to appear familiar to personnel and operators on the ground yet remain usable for mission-critical uses. The product was also designed to fit in a user’s hand and be easy to grip even when wet or while the operator is wearing gloves.
Portsmith
VPT | https://www.vptpower.com/
Each issue, the editorial staff of Military Embedded Systems will highlight a different charitable organization that benefits the military, veterans, and their families. We are honored to cover the technology that protects those who protect us every day.
This issue, we are highlighting the Veterans Association of Real Estate Professionals (VAREP), a national nonprofit 501(c)(3) and HUD [U.S. Housing and Urban Development]-approved organization dedicated to increasing sustainable homeownership, financialliteracy education, Veterans’ Administration (VA) loan awareness, and economic opportunity for the active-military and veteran communities. Since its establishment in 2011, VAREP and its members represent and work within all sectors of the real estate, housing, and financial-services industries to improve the lives of servicemembers and veterans through housing and philanthropy. VAREP co-founders Son Nguyen and Dustin Luce realized that while many organizations help veterans with pensions, disability compensation, and critical life needs, no one organization was dedicated to financial literacy, housing, and homeownership. Many of its 7,000-plus members are also veterans, and so are uniquely positioned to understand the various challenges faced by the servicemember and veteran communities.
Among the VAREP programs is a house-flipping program which aims to transform neglected homes into livable houses; a HUD-approved housing education and counseling initiative; and VAREP Cares, which oversees an emergency assistance fund, educational-grant program, and housing assistance fund to help recipients with home purchase costs or repairs. The group also spearheads the “House-a-Vet” initiative in which it receives donated homes, renovates them, and awards them to families around the country in conjunction with national banking partners.
By the end of 2022, VAREP expects that its national footprint will expand to 25 states with more than 45 chapters. The organization works with local real estate, lending, and housing professionals to better serve the needs of military and veteran families in recipients’ communities. For additional information, please visit https://varep.net/.
Sponsored by Annapolis Micro Systems, LCR Embedded Systems, Mercury, and nVent Schroff
It’s been nearly 30 years since the famous memo was sent by then-Secretary of Defense William Perry, stipulating the use of commercial off-the-shelf (COTS) components wherever and whenever possible in military systems. While COTS procurement is now an accepted form of doing business, the main challenges for COTS suppliers remain, namely taking commercial technology and enabling its use for extreme military environments while also managing the short life cycles of commercial solutions. Reduced size, weight, and power (SWaP) requirements have made these issues even harder to navigate. In this webcast, industry experts share methods for ruggedizing COTS systems for extreme military applications and discuss how to manage the obsolescence headaches that come with COTS use. (This is an archived webcast.)
Watch this webcast: https://bit.ly/3fUl3on
Watch more webcasts: https://militaryembedded.com/webcasts/archive/
This white paper details performance measurements compared to predictions of a 16-channel S-band direct sampling receiver design. The design is based on recently released direct sampling analog-to-digital converters (ADCs) clocked at 4 GS/sec and sampling in the second Nyquist zone of the converter. First, the design configuration is described with pointers to online references that provide further description. Next, the receiver is shown for both the RF components and the configuration of the embedded digital signal processing (DSP) that is now integrated into modern data converters. Calculations for single-channel performance predictions are presented and compared against measurements.
A set of measurements combining data from 16 channels evaluates the dynamic range improvements for noise density, spurious signals, and intermodulation products and then a set of observations is presented for the multichannel performance trends that can be used for extrapolation to models of large phased arrays implemented with many distributed receivers.
Read this white paper: https://bit.ly/3V5Kgw6
Read more white papers: https://militaryembedded.com/whitepapers
Military Embedded Systems focuses on embedded electronics – hardware and software – for military applications through technical coverage of all parts of the design process. The website, Resource Guide, e-mags, newsletters, podcasts, webcasts, and print editions provide insight on embedded tools and strategies including technology insertion, obsolescence management, standards adoption, and many other military-specific technical subjects.
Coverage areas include the latest innovative products, technology, and market trends driving military embedded applications such as radar, electronic warfare, unmanned systems, cybersecurity, AI and machine learning, avionics, and more. Each issue is full of the information readers need to stay connected to the pulse of embedded technology in the military and aerospace industries.
The climate of continuous urgency in the geopolitical environment is escalating demand for faster, more powerful and secure aerospace and defense (A&D) systems. From data to decision, silicon to systems, customers entrust their mission-critical challenges to Mercury. Our trusted, secure, end-to-end processing platform leapfrogs incremental gains, bending the curve to power the most critical A&D missions on the planet and beyond. mrcy.com/processing-platform