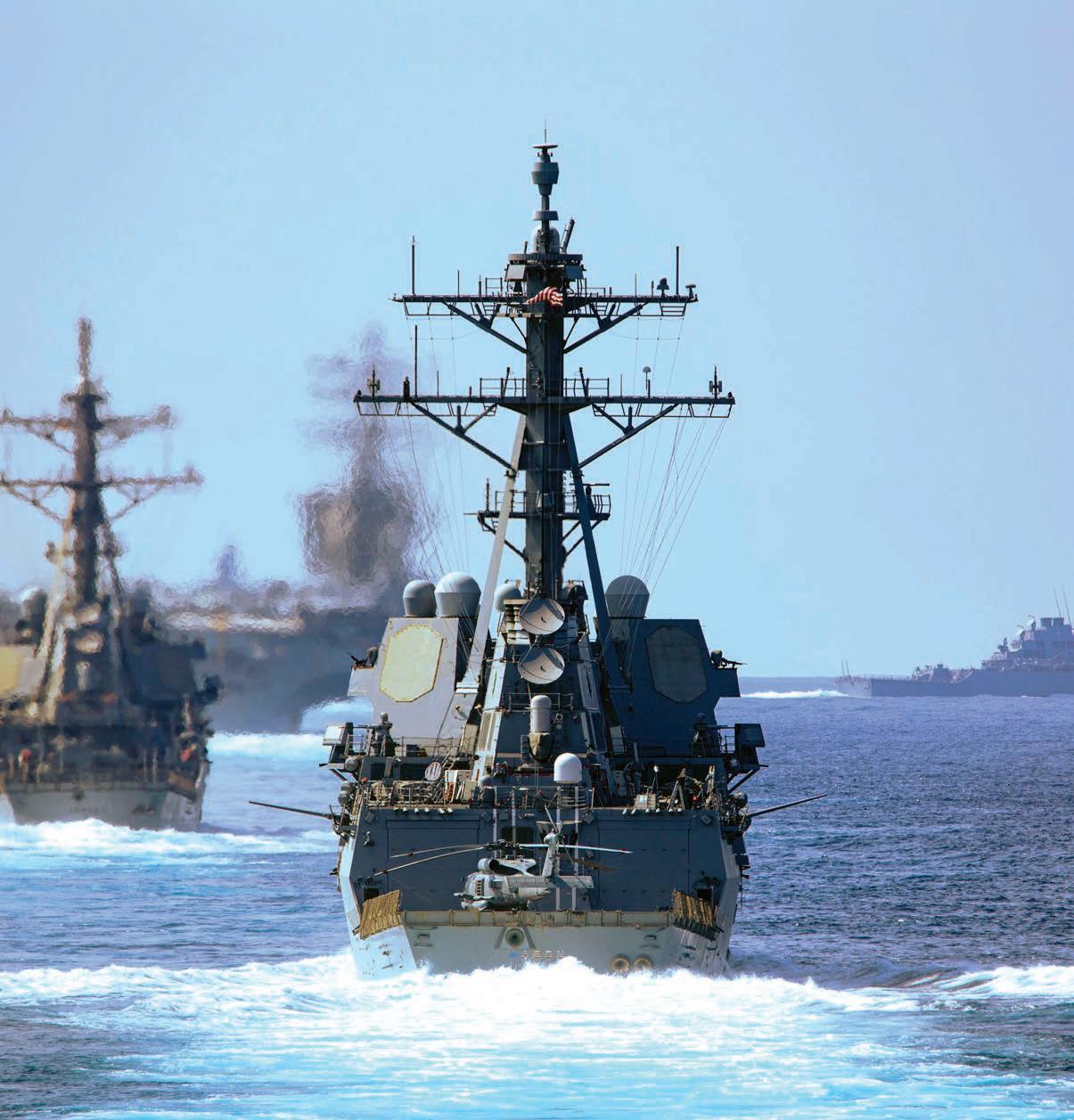
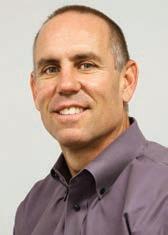
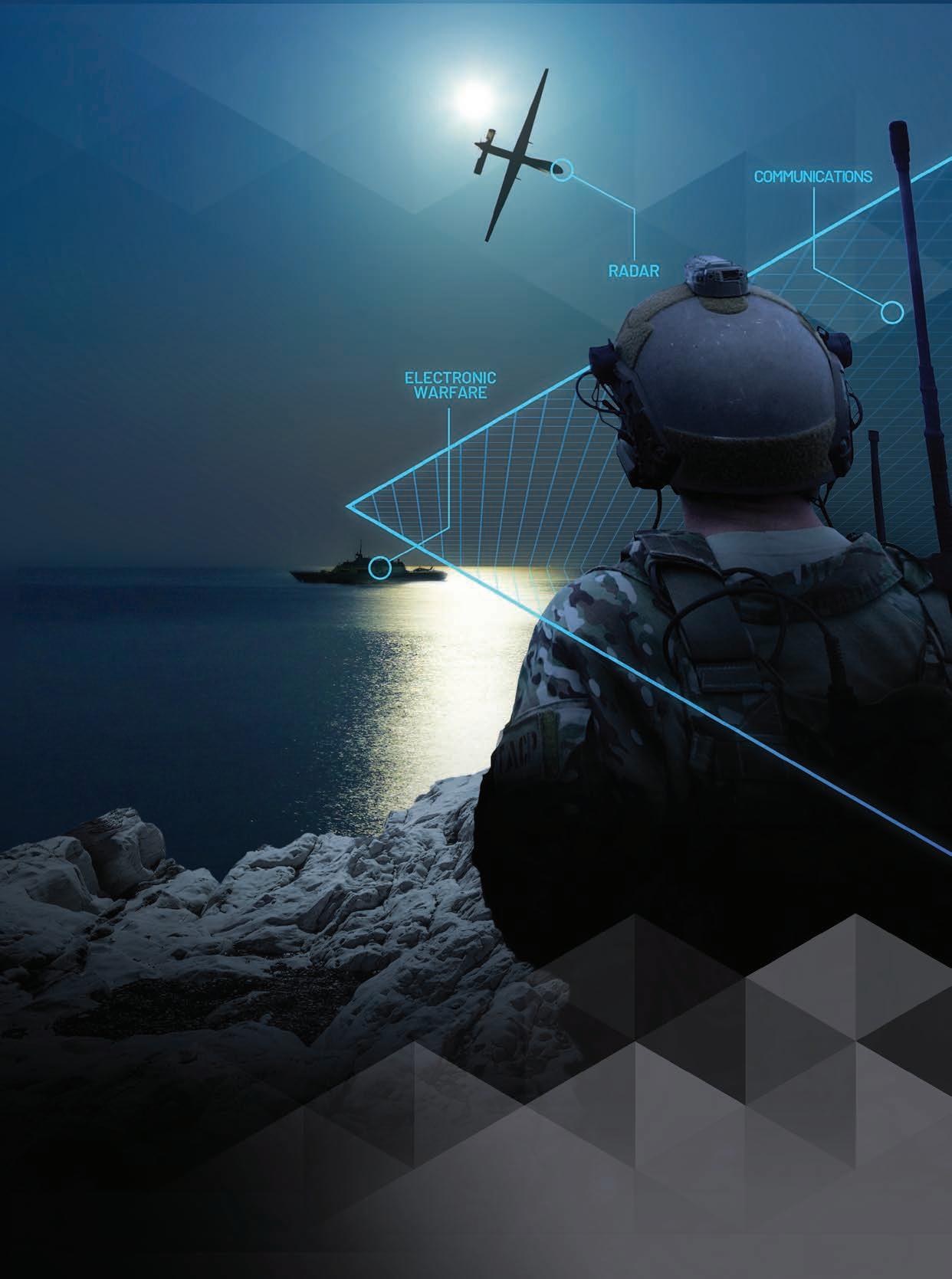
When the mission calls for a 3-phase 3U power supply that can stand up to the most rugged environments, the military chooses VPXtra 704™ from Behlman – the only VPX solution of its kind built to operate seamlessly from MIL-STD-704F power for mission-critical airborne, shipboard, ground and mobile applications.
> 3-phase AC or 270V DC input; high-power DC output
> Available holdup cards store 700W of DC power for up to 80 msec
> Overvoltage, short circuit, over-current and thermal protection
> Provides full output performance during both normal and abnormal transients
EXECUTIVE INTERVIEW
18 MOSA, AI, and unsafe programming languages
By Michael Wilson and Dominic PerezQ&A with Tim Reed, Chief Executive Officer for Lynx Software Technologies
By John McHale, Group Editorial Director
SPECIAL REPORT: Shipboard electronics
24 The evolution of real-time data-sharing in naval warfare
By Dan Taylor, Technology Editor
By Dan Taylor Taylor28 Design challenges for naval equipment enclosures
By Fred Sainclivier, Curtiss-Wright Defense Solutions
32 Shipboard electronics gain tactical edge through ruggedized commercial server technology
By Justin Myers, Mercury
MIL TECH TRENDS: Test & measurement trends
36 Leveraging AI for testing military cognitive systems
By John McHale, Group Editorial Director
INDUSTRY SPOTLIGHT: Managing supply chain, obsolescence, and counterfeit parts
40 Managing today’s military supply chain
By Shan Morgan, Elma Electronic
44 Planning for and minimizing the costs of obsolescence in military and aerospace applications
By Dan Deisz and Ken Greenwood, Rochester Electronics
ON THE COVER:
Naval warfare demands seamless, real-time data sharing across multiple platforms, from aircraft to surface ships to submarines. As conflicts become increasingly complex and fast-paced, the key to winning lies in the ability to communicate critical data in real time. (U.S. Navy photo.) @military_cots
https://www.linkedin.com/groups/1864255/
Whether your mission involves—air, space, ground, marine or subsea—WINSYSTEMS’ rugged highly reliable embedded computer systems are designed to support your critical mission needs. Let WINSYSTEMS assist you in selecting the optimal embedded computing solution that aligns with your application requirements, leaving you more time to focus on system features and delivery.
Tiny Pico-ITX SBC: ITX-P-C444
Low power industrial-rated SBC with NXP ® i.MX 8M series processor, on-board discrete TPM 2.0 hardware security, dual Ethernet, industrial connectors and I/O
COM Express Type 10 Mini and Type 6 Compact Modules
Rugged highly reliable COM modules with Intel® Atom® E3900 and i3, i5, i7 CORE™ processors with on-board discrete TPM 2.0 hardware security
PC/104-Plus SBC: PPM-C407
Low power industrial-rated SBC with Intel® Atom® E3800 series processor, Gigabit Ethernet
49 AirBorn – Introducing TriMate: AirBorn’s next-generation circulars
2 Analog Devices, Inc. –
We have you covered from Alpha to Zulu
35 Atrenne –
When failure is not an option
3 Behlman Electronics, Inc. –3 Phase. 3U. 1 Choice.
47 Dawn VME Products –Dawn powers VPX
45 Elma Electronic –
Leaders in modular open standards enabling the modern warfighter
8 GMS – X9 Spider. The world’s most powerful full-featured wearable AI computer
12 Interface Concept –
Front-end processing boards for edge applications
34 Lansdale – Classic designs are timeless
31 LCR Embedded Systems, Inc. –Develop. Demonstrate. Deploy.
100 Mercury Systems, Inc. –Critical signal processing with unmatched flexibility
42 Milpower Source –
Your design partner for field-proven mil-grade power & networking solutions
51 Phoenix International –Phalanx II: The ultimate NAS
13 PICO Electronics Inc –Transformers & inductors
43 Pixus Technologies –
Ruggedized x410 NI SDRs for maximum performance!
27 Sealevel Systems, Inc. – Get it right.
23 Vector Elect – VME/VXS/cPCI chassis, backplanes & accessories
5 WinSystems – Embed mission success
7 Z Microsystems, Inc. –
Built to perform, for those who serve
AUSA 2023
October 9-11, 2023
Washington, DC
https://meetings.ausa.org/annual/
Aerospace Tech Week Americas
November 14-15, 2023
Atlanta, CA
https://www.aerospacetechweek.com/
Association of Old Crows (AOC) 2023
International Symposium & Convention
December 11-13, 2023
National Harbor, MD
https://www.crows.org/mpage/2023HOME
GROUP EDITORIAL DIRECTOR John McHale john.mchale@opensysmedia.com
ASSISTANT MANAGING EDITOR Lisa Daigle lisa.daigle@opensysmedia.com
TECHNOLOGY EDITOR – WASHINGTON BUREAU Dan Taylor dan.taylor@opensysmedia.com
CREATIVE DIRECTOR Stephanie Sweet stephanie.sweet@opensysmedia.com
WEB DEVELOPER Paul Nelson paul.nelson@opensysmedia.com
EMAIL MARKETING SPECIALIST Drew Kaufman drew.kaufman@opensysmedia.com
WEBCAST MANAGER Marvin Augustyn marvin.augustyn@opensysmedia.com
VITA EDITORIAL DIRECTOR Jerry Gipper jerry.gipper@opensysmedia.com
SALES/MARKETING
DIRECTOR OF SALES Tom Varcie tom.varcie@opensysmedia.com (734) 748-9660
DIRECTOR OF MARKETING Eric Henry eric.henry@opensysmedia.com
OPERATIONS & AUDIENCE DEVELOPMENT (541) 760-5361
STRATEGIC ACCOUNT MANAGER Rebecca Barker rebecca.barker@opensysmedia.com (281) 724-8021
STRATEGIC ACCOUNT MANAGER Bill Barron bill.barron@opensysmedia.com (516) 376-9838
STRATEGIC ACCOUNT MANAGER Kathleen Wackowski kathleen.wackowski@opensysmedia.com (978) 888-7367
SOUTHERN CAL REGIONAL SALES MANAGER Len Pettek len.pettek@opensysmedia.com (805) 231-9582
DIRECTOR OF SALES ENABLEMENT Barbara Quinlan barbara.quinlan@opensysmedia.com AND PRODUCT MARKETING (480) 236-8818
INSIDE SALES Amy Russell amy.russell@opensysmedia.com
STRATEGIC ACCOUNT MANAGER Lesley Harmoning lesley.harmoning@opensysmedia.com
EUROPEAN ACCOUNT MANAGER Jill Thibert jill.thibert@opensysmedia.com
TAIWAN SALES ACCOUNT MANAGER Patty Wu patty.wu@opensysmedia.com
CHINA SALES ACCOUNT MANAGER Judy Wang judywang2000@vip.126.com
WWW.OPENSYSMEDIA.COM
PRESIDENT Patrick Hopper patrick.hopper@opensysmedia.com
EXECUTIVE VICE PRESIDENT John McHale john.mchale@opensysmedia.com
EXECUTIVE VICE PRESIDENT AND ECD BRAND DIRECTOR Rich Nass rich.nass@opensysmedia.com
SENIOR TECHNOLOGY EDITOR Ken Briodagh ken.briodagh@opensysmedia.com
TECHNOLOGY EDITOR Curt Schwaderer curt.schwaderer@opensysmedia.com
ASSOCIATE EDITOR Tiera Oliver tiera.oliver@opensysmedia.com
ASSOCIATE EDITOR Taryn Engmark taryn.engmark@opensysmedia.com
PRODUCTION EDITOR Chad Cox chad.cox@opensysmedia.com
GRAPHIC DESIGNER Kaitlyn Bellerson kaitlyn.bellerson@opensysmedia.com
FINANCIAL ASSISTANT Emily Verhoeks emily.verhoeks@opensysmedia.com
SUBSCRIPTION MANAGER subscriptions@opensysmedia.com
CORPORATE
REPRINTS
CHOOSING THE RIGHT SUPPLIER CAN BE DIFFICULT. ZMicro is here to help you meet your program needs from start to integration. We bring together in-house engineering, on-site manufacturing and the highest degree of quality to deliver rugged computing solutions that you can depend on.
RUGGED SOLUTIONS FOR YOUR PROGRAM NEEDS
No matter what the requirement, we have a solution to help. We’ll customize a product that works best for you.
Our team is focused on delivering quality product from conceptual design to full rate production. Each project team has a dedicated project engineer manager to manage electrical, mechanical,
We’re proud of our well-organized, quality-focused, clean and production facility and see our manufacturing processes in action.
So much of our contributed content – and even our staff-written features – over the past few years have been focused on open architecture initiatives and modular open systems approach (MOSA) initiatives like the Sensor Open Sensor Systems Architecture (SOSA) Technical Standard. We even produce an annual full-sized magazine on SOSA, as well as an issue covering the Future Airborne Capability Environment (FACE). But for the last decade our coverage has often been dominated by the twin topics of obsolescence and supply chain, both of which we cover in this issue.
Fact: MOSA is about leveraging open architectures to bring capability to the warfighter more quickly while enabling lower life cycle costs. Also fact: These systems will help curtail obsolescence by enabling faster upgrades. Even so, all of this still depends on a robust supply chain and, even more importantly, a trusted supply chain.
Starting on page 40, our supply-chain section covers obsolescence management, counterfeit-parts mitigation, trusted sources, and overall supply-chain management.
Shan Morgan of Elma was spot-on in his piece (on page 40) when he described the situation this way: “ … a stable supply chain is critical for both national security and economic strength. And just like a surfer trying to paddle past the break, but who keeps getting rolled back to the shore, managing the complexity of supply-chain solutions needed in today’s defense industry can feel a bit like this same frustrating push-and-pull.”
Military platforms like the B-52 can last decades, while commercial components like semiconductors can have lifetimes as short as six months. We all know the defense industry is at the mercy of commercial component life cycles. This reality is also why the U.S. government is anxious to ensure onshore production of integrated circuits in the U.S so as not to be dependent on Taiwan.
As Dale Lillard, president of Lansdale Semiconductor (Phoenix, Arizona), told me previously, “They don’t make militarized ICs anymore, so the end user is forced to go with COTS [commercial off-the-shelf] technology.”
That shift makes it “more difficult for aftermarket support of commercial parts for military systems today,” he explained. “In the 1980s and 1990s, militarized products were consolidated and the Defense Logistics Agency (DLA) maintained the specifications in a QML [qualified military line], ensuring consistent support from the various manufacturers. The military components were designed into systems and aftermarket suppliers knew they would need to be supported.”
John.McHale@opensysmedia.comLillard said he recommends to his customers with long-life systems using commercial ICs that they should make EOL [endof-life] buys, “as you will never get the parts cheaper and also because you will not get the support that we have provided for military ICs of the 1980s or 1990s.”
The aftermarket business cycle is typically the opposite from the rest of the defense-electronics market, Lillard told me. “When the government doesn’t have money to buy new toys, they make sure they maintain the old ones.”
Regarding authorized suppliers, Lillard still said “there is no other solution except to buy from authorized suppliers.” Doesn’t matter if it’s an automotive part or military ICs, only the original manufacturer knows what they’re doing, he adds.
To demonstrate, he used his favorite analogy: “When I’m working on my 1965 Ford Mustang and looking for replacement parts, I can buy something from China that has on paper all the right information, but when I go to put it in the car I find that the holes don’t match or it’s incompatible in some other way.”
For more on Lansdale Semiconductor, visit www.lansdale.com. For more on aftermarket suppliers, read the article from Rochester Electronics on page 44; the authors, Dan Deisz and Ken Greenwood, also cover the value of authorized suppliers in counterfeit mitigation.
I like talking to the aftermarket suppliers like Dale and Dan and also Ethan Plotkin of GDCA, an aftermarket supplier of singleboard computer designs. It’s a unique business, with not many players. Lansdale, Rochester, and GDCA have been doing this for decades; in fact, many of our key military platforms flying today depend on the IC designs they keep alive. Both companies are still supplying parts from the later 20th century.
Regarding counterfeit mitigation, I always think back to a visit I had with Tom Sharpe of SMT Corp. in Sandy Hook, Connecticut: Sharpe broke out a slide show showing a city in China built only on creating counterfeit ICs. It was eye-opening and depressing. Workers washed counterfeit product in contaminated rivers. Imagine that getting into a consumer product, let alone a military fighter jet. The counterfeiters get better every year, hence the need for multilayer trusted supply chains.
I’ve learned from all these guys. We always talk about artificial intelligence and laser weapons and augmented reality and how exciting those applications are. But many of our mission-critical platforms still rely on parts the grandparents of today’s engineers helped design. That’s a supply chain that has been supported for 50 or 60 years.
FirePoint Innovations – a partnership between Wichita State University (WSU) and the U.S. Army’s Combat Capabilities Development Command, Aviation and Missile Center (DEVCOM, AvMC) – recently cut the ribbon on its Applied Innovation Center (AIC) in Huntsville, Alabama. The AIC is a brand-new collaboration, prototyping, and testbed facility aimed at accelerating technology discovery and adoption for U.S. Army aviation.
The original FirePoint Innovations Center at Wichita State University (WSU) in Kansas is an endeavor launched in 2017 between the university and the U.S. Army’s DEVCOM AvMC. Initially, the WSU program was set up to accelerate joint technology development, transfer, and commercialization between DEVCOM, universities, industries, and government organizations.
Steve Cyrus, executive director of FirePoint Innovations Center at WSU, stated in a 2022 university interview that all concerned with FirePoint regard it as a “force multiplier” for the U.S. Army and its technology development and integration.
Now, the center operates jointly with the Army: “We’re looking at Army technology and pushing it out – but then, also, we’re looking at what’s happening in the startup space and in the commercial sector and seeing what we can press into the aviation and missile center and on their mission to give technology and get technology to the warfighter,” Cyrus said.
Moreover, said Cyrus, the WSU Innovations Center’s effect on work force development within the university community has been profound, noting that WSU spends tens of millions of dollars each year paying wages to students working within its industry and defense programs – which includes FirePoint –ushering along ideas that target the Army’s modernization priorities. The Army’s declared areas of focus and improvement include combat vehicles, air and missile defense, soldier lethality, long-range precision fire, vertical lift, and networking.
The FirePoint Innovations team purposely located the newly christened Huntsville FirePoint AIC near the U.S. Army’s Redstone Arsenal, according to the FirePoint announcement of the launch. Redstone is an Army installation commissioned in 1941 that serves as the host for a variety of U.S. Department of Defense (DoD) tenant commands, the FBI, and NASA’s Marshall Space Flight Center.
The new Huntsville AIC is situated to enable Army aviation leaders to collaborate with emerging technology companies and also offers a way for smaller companies to get involved with the DoD and overcome some of the challenges nontraditional businesses face in the defense market. It is equipped with two
prototyping and testing labs plus proximity to the resources the Army and the private-sector companies need for collaboration and technology development, the announcement noted.
Leading the team as AIC director is military and defense industry executive Matthew Pfrommer, who has experience on several fronts: He has worked in technology companies on design, development, and operational deployment of national asset mission systems, plus he has served as a senior DoD Acquisition Corps Member in multiple roles for U.S. Army acquisition.
In the Huntsville announcement, Pfrommer is quoted as saying that this DoD innovation program is a bit different because the AIC has both the capacity and expertise to actually facilitate the development, integration, and deployment of new technologies and solutions to address capability gaps in Army Aviation.
“This isn’t your typical ‘innovation theater’ program where both sides get together to discuss hypotheticals,” Pfrommer said. “The AIC is where DoD and private-sector engineers can bring their technologies, connect them up, experiment, and iterate to solve problems, rather than broadcasting corporate commitments to the latest buzz on social media or theorizing paper solutions in proposal documents. I’m excited to see the accelerated innovation that comes out of these partnerships.”
This kind of from-the-ground-up collaboration lowers risk for the parties involved: On one hand, Army aviation experts are able to scope out, integrate, and thoroughly test privatesector technologies to ensure compatibility prior to buying them; on the other hand, small businesses are able to shorten the often years-long process and lower the large cost of selling technologies to the Pentagon. Moreover, companies involved from the beginning of the process are better able to engineer specific solutions based on potential users’ ideas, needs, and directions.
The Huntsville Firepoint AIC website lists a number of areas of concentration, including outreach like community relations and industry roundtables; workforce development including training and mentoring; technology transfer including scouting and acceleration; program management including subcontracting and technology alignment; informing requirements, including research alignment with regulatory requirements; and consulting, which could include process assessments and standards development.
According to AIC director Pfrommer, the goal is to eventually establish AICs in other strategic locations around the U.S. to further connect the military, academia, and the defense industry.
Advances in generative artificial intelligence (AI) are enabling adversaries to build new attacks faster and evade signature-based threat detection with ease. The cutting edge of adversarial cybersecurity is becoming more sophisticated, using new technologies to rapidly develop new attacks. Defensive cybersecurity efforts must keep pace with bad actors by using new tools that combine attack signal intelligence with patternmatching capabilities to identify polymorphic threats, or cyberthreats that employ evasive techniques to evade detection from traditional security solutions.
If a breach has occurred or is suspected, the defense cyber team cannot trust any devices on the network and must bring their own equipment to perform the analysis. These “tactical edge hunt kits” are carried by an operator to analyze network threats on location, as many defensive cyber missions occur on segmented, isolated, or otherwise air-gapped networks owned by other organizations or mission allies. A mobile and rapidly deployable hunt kit enables the speedy response essential to remediate threats and protect devices and networks.
Over the last decade, it’s become routine for cyber task forces to visit a site and collect network data for a couple of weeks, after which they return to their lab and run the collected data through an analyzer. By that point, though, the adversary has likely completed its mission, hidden its tracks, and changed its attack. Running replays of data after the fact is no longer enough. What’s needed is to move from snapshot-in-time assessment of threats to a more continuous monitoring model.
Today’s signature-based techniques, while important, are not significant enough on their own to address the advancing threat conditions. They often require knowledge of the attack methods to build the files to perform the pattern
matching. Types of attack are changing too rapidly and bypassing known signatures. Another approach, machine learning (ML)-enhanced anomaly detection, frequently misses critical threats or finds too many false positives. An avalanche of false positives can mask true attacks that might be underway. The efficacy of threat detections is key to the success of cyber hunts to find the “unknown unknown.”
Purpose-built AI makes operators more effective; in part, it prevents the human element from getting overwhelmed by intelligently reducing the noise. Jason Kikta, former Hunt Forward Mission Director, U.S. Cyber Command, stated, “Without the evolution and inclusion of AI in our hunt operations, there’s no way our operators can scale the fire hose of data they need to sift through at the tactical edge.”
The good news is that modernized, compact hunt kits, small enough to fit into an airplane’s overhead luggage compartment, can quickly bring the power of enterpriselevel AI and self-training ML algorithms to the tactical edge, anywhere in the world. An integrated commercial off-the-shelf (COTS)-based, highly transportable system that provides the compute power and AI/ML tools for attack signal intelligence –combined with other tools, such as an aggregated enterprise threat-management system – enables a hunt team to bring the solution rapidly to the battlespace, gaining results in real time versus months after an incident.
Making AI/MI-based cyber hunt capabilities available at the tactical edge enables the hunt operation to see the “unknown unknown” that less powerful approaches would miss. Providing clarity to those unknowns across the systems enables a response to be more quickly orchestrated to act against the threat. Leading-edge organizations are witnessing the effectiveness of AI-driven attack signal intelligence in their cyber hunt operations and choosing to permanently install these tools in their networks for continual real-time defense.
An example of a transportable system that hosts the highest level of kit capabilities and brings AI/ML threat detection to national security cyber tactical-edge communications is a new hunt kit developed in collaboration between Curtiss-Wright Defense Solutions and Vectra AI. The modular and transportable kit leverages AI/ML algorithms proven in national security enterprise environments and makes them mobile for use in the field. Using these algorithms, which can run on CPU- or GPU-based processors, cyber hunt operations that formerly took weeks to conduct now take less than 10 days after being connected to the network (with 36% of detections happening immediately, using fully trained models). Instead of using a single general-purpose algorithm, this hunt kit features 120+ patented AI algorithms and a combination of pretrained and self-learning ML models.
A better way to deal with polymorphic cyberattacks is to fight AI with AI. It’s now possible to detect the “unknown unknown” and cyberthreats around the world that traditional intrusion detection systems (IDS) and signature capabilities would miss. Hunt teams now have the power to effectively detect and deter cyber adversaries.
Walking through the corridors of the Tampa Convention Center at SOF Week, you couldn’t escape the palpable buzz of innovation. This annual gathering serves as a launchpad for technologies that could potentially shape the future of U.S. Special Operations Command (USSOCOM) and other governmental bodies.
From my front-row seat, two presentations in particular caught my attention, each heralding significant advancements in defense technology: Leslie Babich, the director of the SOFWERX innovation lab, and Jim Smith, head of USSOCOM acquisition.
They both took the stage to discuss some mind-bending projects that are currently underway. Here’s my take on what they presented and what it means for the defense industry.
The SOFWERX Phenomenon
I was particularly impressed by Leslie Babich’s insights into SOFWERX, an
2015, SOFWERX has the unique mandate to create and maintain a platform
USSOCOM. Over the years, this lab has contracted $116.1 million through
• 3U & 6U VPX
• Single or dual Xilinx FPGAs - UltraScale™/UltraScale+™ - Zynq™ UltraScale+™ / RFSoCs - Versal® • FMC/FMC+ VITA 57.1/57.4
What makes SOFWERX a success story is its commitment to involving smaller contractors in large-scale projects. This inclusion leads to “lightning-fast” contract awards and brings fresh, innovative solutions to the table.
The numbers presented by Babich speak volumes: 668 knowledge transfers, 54 transitions to programs of record, 101 consignments, and 282 validations. For smaller defense contractors, this is a golden opportunity. SOFWERX serves as a go-between that not only offers a window to showcase products but also handles market research and protects intellectual property.
Essentially, it opens doors for technologies to get from the lab to the battleground faster than ever before.
Their Tech Tuesday initiative caught my eye. Launched in May 2020 in response to the pandemic, this program allows contractors to showcase their technologies virtually. With 835 government personnel and 1,036 technologies already in the ecosystem, this is one virtual event that smaller contractors can’t afford to miss.
The second day of the conference held equal promise. Jim Smith took us on a tour of some extraordinary initiatives. The most ambitious among them? Transforming the MC-130 into a floatplane capable of landing on water. Now, this is no small feat of engineering, but if successful, it could turn the vast expanses of the world’s oceans into potential landing zones, redefining tactical possibilities and presenting substantial strategic challenges to adversaries.
In a world increasingly defined by asymmetric threats, the ability for small units to operate independently is nothing short of game-changing.
The application of such a capability is huge, particularly for operations in the IndoPacific area of responsibility. The goal, as Smith highlighted, is to reduce the military’s dependency on runways.
High-speed, vertical take-off and landing (VTOL) capabilities are also in the works, in collaboration with DARPA, aiming to tackle the “tyranny of distance” that comes with operating over large bodies of water.
Smith also highlighted the concept of “untethered logistics,” allowing small units to be self-sufficient at the edge, generating their own energy, water, and even manufacturing capabilities. In a world increasingly defined by asymmetric threats, the ability for small units to operate independently is nothing short of game-changing.
Another crucial pillar was next-generation intelligence, surveillance, and reconnaissance (ISR). Smith emphasized a three-legged approach combining data from space, cyber, and uncrewed systems. This fusion is designed to provide real-time information at the edge of operations. Given the challenges in contested communications, the need for a balanced approach between broad bandwidth and security is more critical than ever.
As someone who keeps tabs on the developments in the military embedded systems world, I felt like SOF Week was like stepping into a living lab of the future. What we are seeing here is more than mere incremental innovation; it’s a seismic shift in how we think about warfare, logistics, and technology.
For small contractors in the defense industry, the takeaways are clear: The door is wide open for disruptive technologies. Whether it’s in cybersecurity, artificial intelligence, avionics, or any of the myriad fields that underpin modern military operations, opportunities abound.
Don’t just take my word for it; the proof was in the packed halls and impassioned conversations of SOF Week. With initiatives like SOFWERX serving as catalysts, the future isn’t just promising; it’s already arriving.
For more coverage on SOF Week 2023, visit www.militaryembedded.com/sofweek.
Radar module assemblies for U.S. Navy AN/SPY-6 family garners CAES $200 million contract
Mission-critical RF [radio-frequency] technology company CAES reports that it won a $200 million follow-on, full-rate hardware production and sustainment award from Raytheon, an RTX business. Under the terms of the Raytheon contract, CAES will provide fully tested radar module assemblies for the U.S. Navy’s AN/SPY-6 family of radars, which the Navy uses on six classes of ships.
The CAES announcement details the SPY-6’s usefulness in defending against ballistic missiles, cruise missiles, hostile aircraft, and surface ships simultaneously and states that it can realize several advantages over legacy radars, including greater detection range, increased sensitivity, and more accurate discrimination. CAES has already spent multiple years partnering with Raytheon on the SPY-6 program and has begun delivering hardware, according to the announcement.
billion
U.K.-based defense technology company BAE Systems plans to acquire Ball Aerospace (Westminster, Colorado) for $5.5 billion. The BAE Systems announcement cited the prospective acquisition of Ball Aerospace as a “unique opportunity to strengthen BAE Systems’ world class multi-domain portfolio,” as Ball Aerospace is already a leading provider of mission-critical space systems and defense technologies across air, land, and sea domains, with strong growth potential in areas aligned with the U.S. intelligence community and the U.S. Department of Defense’s (DoD’s) priorities. In a statement regarding the planned acquisition, Charles Woodburn, chief executive of BAE Systems, said: “The proposed acquisition of Ball Aerospace is a unique opportunity to add a high-quality, fast-growing technology focused business with significant capabilities to our core business that is performing strongly and well positioned for sustained growth.”
Saab began production of low-radar-signature composite masts for the Finnish navy’s new vessels, with the first of four masts marked by a cutting ceremony at Saab’s facility in Karlskrona, the company announced. In 2019, Saab signed an agreement with the Finnish navy to furnish and incorporate the combat system for the navy’s Pohjanmaa class vessels, which are smaller and faster than frigate-type ships and are used in surface combat. Deliveries for these ships are slated for the 2027-2029 time frame. These masts, produced by Saab for the Finnish navy, are as tall as a five-story building, and the materials used for these masts mirror the composite found in the Swedish Visby-class corvettes. Composite materials have grown in popularity for ship masts because of their potential to reduce ship weight and radar signature.
Uncrewed aerial and ground systems company AeroVironment plans to acquire Tomahawk Robotics (Melbourne, Florida), a company that creates artificial intelligence (AI)-enabled robotic control systems for use on and off the battlefield. The announcement from AeroVironment asserts that its uncrewed systems paired with Tomahawk Robotics’ AI-enabled technology will let warfighters operate various connected robotic solutions on the battlefield and share information between multiple domains with a single platform using a common controller.
AeroVironment CEO and chairman Wahid Nawabi stated that Tomahawk Robotics will become part of the small uncrewed aerial system (SUAS) business unit within AeroVironment’s unmanned systems segment and that AeroVironment intends to retain the Tomahawk Robotics workforce and facilities in Florida. Tomahawk Robotics’ Kinesis control system was integrated into AeroVironment’s SUAS family of systems, including Raven B and Puma 3 AE, in 2022.
The global market for military communications technologies, estimated at $24.2 billion in 2023, will rise to $35.4 billion by 2028, at a combined annual growth rate (CAGR) of 7.9% during the forecast period, according to a new study by MarketsandMarkets, “Military Communications Market by Platform (Land, Naval, Airborne, Unmanned Vehicles), Application, System, Point of Sale (New Installation, Upgrade), and Region (North America, Europe, Asia Pacific, Rest of the World) – Global Forecast to 2028”
According to the study authors, the driving force for growth in the military communications market will largely come from countries responding to rising security concerns, evolving threat landscapes, increased adoption of new technologies, network-centric warfare and hybrid warfare, the need for interoperability, replacement of aging infrastructure, and buy-in from emerging economies that are growing their defense prowess.
The U.K. Ministry of Defence, on behalf of the International Fund for Ukraine (IFU), has signed three contracts to bolster Ukraine’s air defense capabilities with a total value surpassing 90 million pounds ($113.38 million), the Ministry announced. The contracts encompass a $70.55 million agreement with the Norwegian defense firm, Kongsberg, for counter-uncrewed aerial systems (UAS). These vehiclemounted systems are devised to identify, trace, disrupt, or dismantle UAS systems, while Kongsberg’s CORTEX Typhon system is designed for swift deployment and repositioning.
This system can function autonomously or integrate into a broader network, leveraging an intricate array of sensors, cameras, radars, and electronic surveillance tools to impede or destroy drones, according to the statement. Simultaneously, a new batch of aerial reconnaissance drones has been delivered to Ukraine.
The National Oceanic and Atmospheric Administration (NOAA) has ordered two REMUS 620 uncrewed underwater vehicles (UUVs) from HII, the shipbuilding company announced. These medium-class UUVs will be delivered in 2024 and are set to be built by HII’s Mission Technologies division in collaboration with defense-equipment provider W.S. Darley & Co. The REMUS 620, introduced last November, features a battery that lasts up to 110 hours and can travel a distance of 275 nautical miles, the company says.
These UUVs will be customized with a synthetic aperture sonar module, supplemental energy modules, and other equipment. HII notes that NOAA intends to use these vehicles for high-resolution mapping of the Gulf of Mexico, particularly focusing on the restoration of seafloor habitats adversely affected by the 2010 Deepwater Horizon oil spill.
Rheinmetall will send its LUNA NG air-supported shortrange reconnaissance uncrewed aerial system (UAS) to Ukraine, with the expectation of delivery later this year, the company announced. The LUNA NG, which Rheinmetall says translates to “unmanned short-range reconnaissance equipment, next generation,” was designed to detect, classify, and recognize objects, enabling collection of real-time reconnaissance data. The system, according to the announcement of the prospective delivery, includes a ground-control station and multiple autonomous aerial vehicles, as well as launch catapults, optional net equipment for UAS recovery, a truck, and rapid-repair tools. This LUNA NG order for Ukraine is one piece of a broad military aid package from the German government.
Mercury Systems announced that it delivered the processing hardware for the U.S. Army’s first six Lower Tier Air and Missile Defense Sensor (LTAMDS) radars, being built by Raytheon (an RTX business). LTAMDS – the Army’s air and missile defense sensor that is slated to operate on the Army’s integrated air and missile defense network – is a 360-degree, active electronically scanned array (AESA) radar that is capable to performing against a wide range of advanced lower-tier threats, including hypersonic missiles. The company’s announcement notes that Mercury has provided radar-processing systems to Raytheon for Patriot radars since 2009; subsequently, in 2019, the Army selected Raytheon to deliver the first six LTAMDS radars, with Raytheon calling on Mercury to develop an expanded suite of advanced electronic systems that included the radar processing platform, the beamforming platform, and Ethernet switching hardware.
Space Force signs $1.25 million software pact with Integrate
Software-integration startup Integrate won a $1.25 million contract from the U.S. Space Force to improve the Space Force’s program-management software platform. The contract tasks Integrate with providing launch-mission management and coordination software.
John Conafay, CEO and co-founder of Integrate, said that the new contract will enable the Space Force to test the usefulness of Integrate’s mission-management platform as an enabler for the U.S. Department of Defense (DoD) Tactically Responsive Space initiative and as a tool for coordinating the Space Systems Command’s programs.
MOSA requirements for Army aviation procurements to be developed by Parry Labs
Digital-systems integrator Parry Labs has been chosen for two projects under the Aviation and Missile Technology Consortium (AMTC) MOSA [modular open systems approach] agreement, tasks aimed at collaboratively defining the U.S. Army’s MOSA requirements for computing and software operating environments for all future Army aviation procurements.
AMTC – a team of industry leaders and small companies collaborating to rapidly develop and mature guided missile and aviation technologies to enhance national security – has as its mission to develop technology prototypes in response to the rapidly evolving and emerging fields of aviation and guided-weapons systems technology. Under the new agreement, Parry Labs is the industry lead chosen by the U.S. government with other subject matter experts in the defense sector to produce the first modular based systems engineering (MBSE) requirement outlined for all Army aviation platforms.
Figure 6 | LTAMDS radar. Image courtesy Mercury Systems. Figure 5 | Image courtesy U.S. Space Force.NASA CubeSat mission reports successful launch of and contact with autonomous swarm
Blue Canyon Technologies (BCT) – a subsidiary of RTX – announced the successful launch and initial contact with CubeSats for the NASA Starling mission, a technology demonstration aimed at proving the success of cooperative groups of spacecraft operating in a swarm, or an autonomous, synchronous manner.
Under the BCT-NASA collaboration, BCT provided four 6U CubeSats to NASA’s Small Spacecraft Technology program. According to the BCT announcement, the six-month-long NASA Starling mission is aimed at advancing the readiness of various technologies for cooperative groups of spacecraft by demonstrating technologies to enable multipoint science data collection by several small spacecraft flying together. The mission is set to test onboard swarm-maneuver planning and execution, communications networking, relative navigation, and autonomous coordination between the small satellites. The 6U CubeSats will be positioned in a nearly sun-synchronous, low-Earth orbit.
General Atomics Aeronautical Systems, Inc. (GA-ASI) completed multiple takeoffs and landings with its Mojave uncrewed aerial system (UAS) on a dirt strip near El Mirage, California, marking the first short takeoff and landing (STOL) on an unimproved surface for the aircraft, according to a company statement.
The capability to take off and land on unimproved surfaces allows for operation in areas that were previously considered unsuitable for UAS activities, the company says, adding that the design of the craft adheres to modular open system approach (MOSA) principles. The tests included takeoffs in as little as 586 feet and landings in as short as 335 feet. The Mojave UAS is designed for forwardbasing operations without traditional airport runways or infrastructure, the company says, and sports a ruggedized airframe, enlarged wings, and multi-sensor suite.
Network-security developer CodeMettle will execute a contract to provide the software-management and configuration component for all-domain agile command-and-control (C2) systems for National Guard Air Force Special Warfare (AFSPECWAR) forces. The NetOps commercial off-the-shelf (COTS) software – a platform-agnostic solution that provides a single management hardware interface –will be bundled with CodeMettle’s platform-agnostic software that enables users to integrate disparate node components.
According to the company’s announcement, its simplified nodemanagement software controls both enterprise solutions and subsystems, including backhaul, electronic warfare (EW), mounted or dismounted radio frequency (RF), tactical data link (TDL), network, and services/applications. The software is aimed at integrating and orchestrating data and processes from transmission, network, and applications and services into a “single pane of glass” (or unified data-management tool) that requires very little training to use.
Smallsat development facility opened by Lockheed Martin for SDA satellites
Lockheed Martin opened a facility that will house the company’s Space Development Agency (SDA) Tranche 1 Transport Layer satellites; the facility is intended to streamline small satellite (smallsat) development, demonstrations, and processing to enable high-rate delivery.
The 20,000-square-foot facility – at the Lockheed Martin Littleton, Colorado campus – hosts dedicated testing capabilities, including thermal cycle and electromagnetic chambers, scaled to efficiently build and test satellites ranging in size from CubeSats to smallsats. It will also feature six scalable parallel assembly lines and is configurable to host different classifications of missions at the same time and will handle all stages of smallsat development. According to the company’s announcement, Lockheed Martin is currently developing more than 50 satellites for the SDA’s Transport Layer, which when deployed will provide military users with low-latency communication links through a resilient network of integrated capabilities from low-Earth orbit.
Figure 8 | Satellite processing facility. Image courtesy Lockheed Martin. Figure 7 | NASA/Conceptual Image Lab/Ross Walter.Modular open system approach (MOSA) strategies such as the Future Airborne Capability Environment (FACE) Technical Standard are changing how the U.S. Department of Defense (DoD) acquires technology. In my McHale Report podcast with Tim Reed, Chief Executive Officer for Lynx Software Technologies, he and I discussed how MOSA benefits the warfighter and what it means to be certified conformant to the the FACE Technical Standard. Edited excerpts of the podcast are below. To listen to the episode, visit https://militaryembedded.com/avionics/software/mosa-ai-andunsafe-programming-languages.
MILITARY EMBEDDED: Please give a brief description of your responsibility within Lynx as CEO and your history in the defense industry.
REED: I’ve had over 20 years of experience in this [aerospace and defense] sector. I worked on the technology and product side, largely in strategic projects and managing products, product lines in the operating environment areas, especially in areas that needed safety certification. I’ve been working in the hypervisor space for most of my career, and in the defense area in communications, radios, radar, signal processing, security software, munition systems, marine, IoT [Internet of Things] systems.
It was fun early in my career. I got to architect what I think may have been the first application of a hypervisor in a military embedded system for a radio system. And that was before the days when hardware actually supported virtualization. [You have to] kind of get a little clever about how you’re going to host Linux on top of RTOS [real-time operating systems] when you don’t have the hardware to help. It was a fun time.
At Lynx I’m the Chief Executive Officer. I’m focusing on building out my team to drive the initiative that we’re informally calling Lynx 2.0. Lynx was acquired in June of last year (2022) [and] we’re about almost at the one-year mark. We are getting ready to scale [the company] and addressing some new use cases for our market. This Lynx 2.0 vision is really about helping our customers improve the economics of producing robust software
systems. And that can mean the pace of innovation, productivity, the cost of deployments, risk management. The main area where we’re addressing this is embracing open standards and open technologies and making them fit for purpose in the defense market.
MILITARY EMBEDDED: Nearly everybody we speak with in the defense industry is discussing the DoD mandate for a modular open systems approach, also known as MOSA, strategy. Some folks aren’t fond of MOSA, but most folks are embracing it. A MOSA example is the Future Airborne Capability Environment (FACE) Technical Standard, for which Lynx recently achieved certified conformance. Why is FACE so important to the defense industry and the warfighter?
REED: I think the report that Deloitte put out in 2015, that really analyzed the history of government defense programs and their performance, and found that over that prior decade, there was a pretty startling trend, which was a sum total of project overruns was costing an extra half trillion dollars in cost. The average delay for a program is over 21 months. That’s a major problem with the performance of programs. It was a 2015 report, but I can’t say that I’ve seen much improvement in the industry in the intervening eight years. So, we see a major problem here. We have near-peer competition with China. In fact, I saw an article today where some members of Congress are saying maybe we shouldn’t even stop calling it near-peer, just acknowledge that they’re a full-on peer now. Improving the
Tim Reed Chief Executive Officer for Lynx Software Technologiespace of innovation and the scalability of our development in the sector is going to be critical for our national defense.
There’s definitely a need to stop reengineering systems. We do need a common set of tools and platforms to allow this industry to scale. That means we also need some reuse. We see these standards as being a great start. They’re not complete, but the ability to create an architectural standard that facilitates this reuse also facilitates a knowledge base that can be applied from program to program. It’s really important. We do see areas where there can be improved [such as] better contemplation of system behavior. We’re working with industry partners, the U.S. Army, [and] we’ve actually presented a paper on this topic at the Vertical Flight Society … to help extend these open standards even further.
We’re quite aligned with FACE. FACE encompasses lots of things, but obviously POSIX is one element of it. That’s the core of our product line. We are a POSIX native solution and have been for decades. FACE 3.1 really amped up the level of compliance testing required, which definitely suits us quite nicely. As you mentioned, we are certified conformant to FACE 3.1. We have certified on all three major targets in our industry. The breadth of coverage we have, I believe, is the broadest in our segment. And it also is applied to our certified codebase. It’s not a bolt-on that is like an optional little piece of software that may or may not be certified and fit for use in aviation systems. This software that we’ve got [is] certified conformant. And that’s an important differentiator. We think we have a good, shall we say, journey with FACE and there’s more to be done there. We want to contribute to these open standards and how they can address larger system engineering problems to really maximize the reuse potential.
MILITARY EMBEDDED: What does being certified conformant mean as opposed to being compliant or compatible?
REED: Your choice of words is important there. There are ways to use some words that say, hey, we think we’re compatible and we think you can use it and you’ll be happy versus having an outside body actually run the conformance tests and give a third-party attestation that yes, this solution actually meets the intent of what the standard does. For instance, there are firms that are registered as being essentially conformance testing houses for this. In this case, LDRA is one of them. The Open Group provides the standards definition, but I believe they’re also responsible for the test cases themselves. That’s essentially what it is, which is can you prove it to a third party or not? So, we can. We are 3.1 conformant.
MILITARY EMBEDDED: FACE and other open architecture initiatives are changing the way DoD acquires technology. Do you think it’ll also speed up technology acquisition within the DoD?
REED: Yes, it should speed up acquisition and should speed up development and delivery. When you have more commonality in the solution, and you have more people in the industry and
more firms in history familiar with the platform, then you should be able to operate your business much more quickly. As far as how acquisition is changing, it’s pretty clear that MOSA has teeth in a big way. [In spring 2023] the GAO released a report on their findings with the Florida Program Award and what the various factors were for the decision making there. A key factor that drove the decision there was how much the bidders were embracing MOSA and this notion of reuse. That’s really key. I think that opened some eyes in terms of how serious this is. It puts clarity on what the DoD means by modularity and platform transparency. It should be helpful to accelerate the pace of innovation and help performers in this market get a better sense of budget control.
MILITARY EMBEDDED: MOSA is a mandate about how to do open architectures and also leverage commercial technology. In the June issue of Military Embedded Systems Lynx’s Ian Ferguson wrote an article on AI [artificial intelligence] titled “How ChatGPT can help modernize defense and aerospace.” From your view, how is AI impacting defense systems and how are you integrating AI into your solutions?
REED: The potential for impact of AI in this market is much like many other markets where it hard to think of areas where it won’t have an impact. [In our market] software development teams are seeing how AI can be these copilot products can help be an aid for development. Now, of course, this market has some unique challenges. A systems integrator for the defense market can’t just [have] their development exposed to the internet and start submitting code to GitHub for help. That’s just simply not the way the security requirements for this market is going to function or does function.
Then you look at how AI can be used for analysis, how it can aid decision-making and threat awareness in the battlespace –whether physical or cyber – is pretty obvious. There’s no shortage of companies and startups that are out there trying to fill that niche with those kinds of solutions. We think of the systems Lynx is deployed into as essentially mission-critical edge devices. These [are] server-class pieces of hardware that serve a missioncritical purpose. Those hardware units have the CPU and GPU horsepower to run AI workloads. There is no shortage of system integrators and DoD programs imagining ways they can incorporate AI into the operation of those devices. You can think pretty simply about things like drone-attack programs, where you can pair a small squadron of expendable drones that can be paired to, say, an F-35, to fly a mission, and the drone would be
When you have more commonality in the solution, and you have more people in the industry and more firms in history familiar with the platform, then you should be able to operate your business much more quickly.
autonomously flown, and conduct those missions through the use of things like AI. There’s really no shortage of applications where this can be impactful.
MILITARY EMBEDDED: One of the things I see being impactful is with the filtering of data you mentioned. All the ISR [intelligence, surveillance, and reconnaissance] data that’s coming through is more than a human mind can process, so you want to move that filtering up to the sensor level where AI can filter it.
REED: Absolutely. When you look at what the U.S. government is known to be doing to aid the Ukrainian effort, there’s clearly a lot of satellite and signals-intelligence being processed. There have been existing solutions that don’t need AI. But no doubt, you’ll be able to process and adapt to the environment a lot faster if you do use AI in the appropriate way. While what they’re doing is surely still classified, I wouldn’t be surprised if over time we get declassified information about what that technology is [and] that it probably already is incorporating AI to large degree.
MILITARY EMBEDDED: From an AI standpoint, the public gets quite excited about AI, about the possibilities like that solutions like ChatGPT bring. Some embrace it, and some are downright scared of it. What are you hearing from people? Remove the hype. Where is AI tech really at today?
REED: I think it’s now busting through the noise. When I was in school, things like AI and asynchronous VLSI [very-large-scale integration] design were kind of pie-in-the-sky technologies that were always a few decades away. It’s here now. ChatGPT showed the average consumer, the average person on the street, that AI is for real and it’s going to impact their life. It’s going to drive some material changes in the tech sector, and in the broad knowledge economy.
What I’ve seen so far is AI is good at augmenting existing forms of analysis and production in areas that are already wellunderstood. If you have a well-understood domain that you can train an AI on, that’s a great place [where] it can be helpful. But let’s not get too overly ambitious right now. The AI we have right now is frankly terrible at certain things, like conceptualization, or understanding a system and debugging it. It’s not great at innovating.
It can be great at synthesizing code from textbook algorithms, where there’s probably a large body of code out there in the public already. But it’s not that great at innovating brand-new heuristics. You can guide it to craft an algorithm. You can guide it to help you express your original thought, but it’s kind of hard to get to make an original thought. And it’s frankly not even designed for self-criticism and self-awareness, [which] means there’s a large BS factor in the answers you get from AI. So, there’s a lot of room for people to contribute value in the future, where AI is currently not really able to do it, and maybe [that will] change in the future. But I’m generally optimistic, on balance, about what AI will do for the world.
It will [bring] major disruptions. If you look at the printing press, the printed word, that was a major innovation. Society has digested its benefits and its impacts to a point now where we really can’t imagine living without it. But if you were to look at the history of the printed word, some pretty big, impactful, and disruptive things happened. The Reformation and the printed Bible. And from that, you get the wars of religion that lasted over a century. I’m not predicting we’re going to have a century-long war, but our ability to process technology now is much faster than it was half a millennia ago. But there will be disruptions in the economy. Once we get through those disruptions, I think it will be the same way. We will look at this and say how can we ever go back to a world without the internet and AI? It’s going to drive major improvements to our productivity and our general happiness. But there’s going to be a lot of anxiety in the transition as our world is changing around us and people, societies have a difficult time dealing with it.
I’m kind of amused by [recent] Congressional hearings, where there’s chatter about trying to put AI development on pause. Which strikes me is just wildly impractical. I mean, for instance, how would you do it? Who has the authority to do it? How long do you decide when do you decide you stop pausing this innovation? And can you afford the pause when we know full well that China is not going to stop developing this technology?
MILITARY EMBEDDED: Isn’t that a response to their constituents’ fears? They’re trying to win votes.
REED: Yes, and it also might be a response to industry leaders who would like to freeze their place in the market, in amber for all time, [so] they can be part of the regulatory body who can control the innovation and who does the innovation. I can see that there’s some sort of an attempt at regulatory capture here. But in practice, there has already been innovation in the engineering of AI where the amount of resource usage and code needed to actually input these things are getting smaller and smaller. From a practical perspective, how are you going to stop the common person in the open source community from carrying this innovation forward? It’s never going to happen.
MILITARY EMBEDDED: I do appreciate you bringing up the printing press, as an owner and publisher of a print magazine that’s still successful. While it’s not a growth market, print is not dead: it still lives with us. Speaking of growth, what’s the hottest growth area for Lynx? Avionics and safety certification? Cyber? Something else?
REED: Avionics and safety certification is an area of systems that need to compose workloads, typically on upgrading from a single core, deeply embedded design and moving into something that’s more of an edge device, is where we see a lot of interest. The demand for ever-increasingly complex workloads on these systems is driving that change. An example would be the F-35 TR-3 program, with the history of the mission computer, which was a single core system, designed in the late 1990s, early 2000s. Now there are server-class multicore systems, which
are much more complex and [have] rich workloads. Forgive me if I get this number incorrect, I’ve seen multiple numbers published, the TR-3 mission computer platform for the F-35 is roughly 25 to 30 times the compute power of the original system. That increases the complexity of your architecture quite a bit. So, having something like the MOSA.IC [resourcemanagement] architecture that we provide to help control that workload and make it predictable and flight-worthy and secure is very important. We’re seeing a lot of growth in that area.
MILITARY EMBEDDED: Switching gears to cybersecurity: Before this interview, I stalked you on LinkedIn a little bit. I found a post you shared on an article on the Rust Foundation and the nation’s cybersecurity strategy. In your comments, you cautioned that the number of programmers using unsafe programming languages is greater than many believe. Why is that? And how are you dealing with that issue? How big a risk is it?
REED: A little bit about myself. I’m not sure if it came through in your LinkedIn stalking: But I still write my own code. I do keep my fingers in that area. I have been working with Rust for about five years now and absolutely love it. I think it’s just a great innovation in writing code. One of my chief frustrations is having spent most of my career on systems that are implemented with more traditional systems programming languages like C and C++. I’ve never really liked those languages.
[The article on LinkedIn was interesting as it reported] that the government is putting forward good guidance on using programming languages that are memory-safe. But I think that the safety of a language goes beyond just memory safety. It’s very important that it’s the driver of most of the vulnerabilities you see in most commercial code. But the kind of things you care about for making code robust go beyond memory safety. You do want to have, for instance, a small and shareable runtime environment. Right off the bat, that rules out lots of things like Java with its massive virtual machine, Python’s interpreter, etc. These things are very complex [and] challenging to get right.
You also have, in most languages, undefined behavior. You can express a concept and syntax, but depending upon the environment and the compiler you’re going to use, you get different behaviors. C and C++ are famous for this. Rust has as one of its objectives is to ring out all of the undefined behaviors you can get. That’s very meaningful. You can look at how modules get composed. In other languages, you’ll have things like a reference or a pointer, and that will tell you how to handle data, but it doesn’t really tell you who’s responsible for the data, doesn’t tell you who has what the privileges are for using the data.
Rust does a good job solving that problem. When your language solves those problems for you, if you are trying to read code and understand it, or trying to formally verify it with machine checking, or static analysis. When you have these things done by a language it actually means that your ability to comprehend what’s happening is improved. If you look at what
kind of verification conditions are getting generated out of C code, versus Rust, what you’ll find is that it’s like many, many times larger for C, because most of those conditions deal with things like proving that you’re using memory correctly, because the language isn’t helping you do that. And with Rust, the language does it for you. What you’re trying to understand: Is the logic of my code correct? Not: Am I dancing through a minefield correctly and proving that I did it correctly? That’s very helpful for efficiency. I support the use of Rust generally and in our market where robustness matters, and anything that helps us get things done faster. We’ve actually announced support for Rust on our OS and our unikernel. That was delivered for the first time earlier this year. We [also] have more initiatives on our roadmap that we’ll be announcing soon.
MILITARY EMBEDDED: We talked a lot about engineering challenges. But how do you tackle the challenges of recruiting engineers? Because in the defense space that is getting a little trickier. No matter what military show – large or small – I mostly see people who have gray hair like me. It’s not a trend you see at more commercial shows, like the Consumer Electronics Show. Does the military electronics industry have a recruitment challenge on its hands in terms of hiring young engineers? What do you see? And how do you deal with that challenge?
REED: You’re spot on. Talent retention, acquisition, training, is a big challenge. I think you’re right to notice the ageing nature of the workforce. Clearly, there is going to be a need to replenish that workforce and make people more efficient in what they’re doing. There are a number of things that can be done about that.
From a Lynx perspective, what’s nice about where we are in the market is that we’re a commercial-item company. So we sell commercial goods, which gives us the freedom to operate more or less like a normal tech-sector business. We can compete in lots of ways and we’re in the Bay Area, so we do have to compete with firms like Google, Facebook, or you name it. This gives us the freedom to offer more competitive and compelling pay, where we can support remote work; the majority of our workforce is a remote workforce [with the] flexibility of schedule.
A defense integrator has more challenges because of the nature of their security requirements, who they sell to, and the
We need to stop wasting valuable time and resources rebuilding proprietary technology stacks over and over again. We need to drive reuse and collaborative development in the industry.
[laws and regulations] they have to comply with. Thankfully, we don’t have to deal with a lot of those issues. We kind of sit on the border between the normal tech sector and the [defense industry] as far as who we work with, but we do get some of the benefits of being a more normal tech company.
So as far as how do you help the A&D market: Part of that is making sure that we’re developing new technologies that can be rapidly taken up by people coming out of college and are coming out of other parts of the tech sector into A&D. [You don’t want to say to a recruit that] you’re going work on a stovepipe technology that’s 40 years old and entirely proprietary. You can’t really put that on your resume and enhance your job prospects for the future. You want to embrace these technologies that are already in use in other fields and make that about a value that you promote as part of why it’s fun to work in this market. That might be Rust, it might involve containerization, cloud ops, DevOps, a whole host of technologies out there that need to be embraced, to give this market the extra bandwidth it needs to keep up with the pace of innovation.
MILITARY EMBEDDED: As we come to a close, close your eyes and look into the future and tell me what will be a disrupter or a game-changer, from a software perspective, in the defense space five to 10 years from now. Predict the future.
REED: As Yogi Berra said: “Predictions are really hard, especially about the future.” So, with the proviso that I’m nearly 100% likely to be wrong, let’s play this game. I think that when you look at what the Pentagon wants, they’re the primary buyer in our market and they’re going to set some of the rules. They want to start breaking vendor lock on major programs. They want to plan for sustainment and accelerating innovation. What that means is that they’re going to procure their solutions a bit differently. The days of having one integrator own an entire stovepipe technology is less appealing. I think that implies they’re going to have to invest in technology platforms that have a life of their own and avoid this kind of stovepiping of a technology stack. That’s going to require innovation in how procurement’s done.
We need to stop wasting valuable time and resources rebuilding proprietary technology stacks over and over again. We need to drive reuse and collaborative development in the industry. Standardizing on some common platforms and architectures brings this back full circle to MOSA. And FACE is part of that.
But when you look at how procurements are done now, you find yourself asking a question: Which technology and how many units over what schedule are we going to procure? It’s kind of done on that basis, rather than maybe looking at this as defense-as-a-service, which is to say there’s a portfolio of capabilities and opportunities [and] we have to expand a platform. The Defense Department can prioritize what those improvements will be over an agile, incremental development [cycle]. They can evolve the platform with multiple participants
You want to embrace these technologies that are already in use in other fields and make that about a value that you promote as part of why it’s fun to work in this market.
collaborating over time, which is a bit different than how it’s done now. I think that’s going to be more of a trend as we look forward to the next decade. [When] we look at how the market is structured today, it’s hard to see how the pace of innovation would get picked up by an order of magnitude. You’re going to need to structure the way procurement and delivery is done, how collaboration is done, and how reuse is magnified to really pick up the pace of innovation in a material way.
MILITARY EMBEDDED: So that should speed up the defense acquisition process.
REED: If you’re doing business, where you’re expecting maybe once a year or twice a year, to plan the next increment of evolution in your platform, that’s going to involve a procurement cycle. You really can’t afford to have these processes that take place where you spend a good chunk of a year creating an RFP, you’ve got a huge number of months to evaluate, and it’s a quiet period to evaluate the bids. Then there’s the sort of the obligatory protest period to work through. When you’re going to be doing business on a faster turn, and all the participants who are bidding know that the next opportunity to bid is actually closer than the cycle it takes to actually protest, it probably changes the incentives. You spend more time executing, innovating, and being imaginative and less time fighting over what seems like the once-in-a-decade opportunity to succeed. At that point, you really do need to pull out all the stops. I do think there’ll be changes in priorities and incentives in the procurement aspects of these programs. MES
Tim Reed is the Chief Executive Officer for Lynx Software Technologies. Prior to Lynx, he held a variety of positions at Green Hills Software, including in engineering and engineering-management roles for real-time operating system, hypervisor, and compiler tool chain technologies; leading the professional-services organization, and overseeing sales channels and new-product launches. His experience spans automotive, industrial, aerospace, and defense end markets, and he brings expertise in software robustness, formal verification, and the use of new programming languages in safety- and security-critical applications. Tim graduated with a bachelor of science in computer science (engineering and applied science) from the California Institute of Technology (CalTech).
Lynx Software Technologies https://www.lynx.com/
Naval warfare demands seamless, real-time data sharing across multiple platforms, from aircraft to surface ships to submarines. As conflicts become increasingly complex and fast-paced, the key to winning lies in the ability to communicate critical data in real time.
The technical complexities and security implications of data-sharing of sensitive or critical data across multiple military platforms – especially in naval warfare –can make securing this data an unsurmountable task. However, emerging technologies hold great potential to transform the future naval battlefield.
Shipboard electronics encompass a wide range of technologies designed to enhance various operational aspects of naval vessels. These systems can be broadly categorized into a few key areas: communication, navigation, warfare, and sensor systems.
In an era of multidomain operations, the ability to quickly and accurately exchange data in real time across these diverse systems is not just a technical requirement –it’s a tactical imperative. Real-time data exchange enhances several key facets of naval operations:
› Situational awareness: Immediate access to real-time data enables shipboard commanders to have a full understanding of the operational theater. This wide-angle information enables better decision-making and resource allocation and can give a significant edge in both defensive and offensive situations.
› Coordinated action: In a multiplatform environment involving ships, aircraft, and sometimes even satellites, the ability to synchronize actions based on real-time data is crucial for operational success. For example, immediate data exchange between a reconnaissance aircraft and a naval ship could enable the ship to optimize its countermeasures against an incoming threat.
› Asset optimization: Real-time data can be analyzed to adjust the operations of various onboard systems for optimal performance, whether in the area of fuel consumption, weapons readiness, or sensor accuracy.
› Scalability and adaptability: Modern naval operations often involve coalitions with partner nations. Real-time data exchange enables seamless interoperability, enabling a collaborative, flexible, and scalable operational approach that can adapt to evolving threats and scenarios.
Real-time exchange of data is not just a technical feature but a critical enabler that can dramatically influence the outcome of naval operations.
Achieving real-time data exchange is a difficult proposition in naval operations, largely because there’s so much data out there. Subject matter experts say that one of the principal obstacles to seamless communication between aircraft and naval platforms is the sheer volume of data produced by modern sensors.
“Modern high-definition sensors produce large amounts of data, which is very difficult to exchange between various platforms while running real-time applications,” says Emil Kheyfets, director of military and aerospace business development at Aitech (Chatsworth, California). (Figure 1.)
The issue of real-time data-sharing for naval applications is further exacerbated by the “extremely rapid increase in the amount of information produced by manned and unmanned platforms,” says Steven Horsburgh, director of product management in the Tactical Communications Group at Curtiss-Wright (Tewskbury, Massachusetts). These high data volumes demand significant processing power and efficient data pipelines to enable real-time decision-making.
Another critical challenge is the compatibility between various tactical data links (TDLs): “There are a variety of in-
compatible TDL technologies that have been developed in the past 30 years,” Horsburgh says.
Different aircraft and ships may have distinct TDL capabilities depending on when they were deployed or retrofitted. This variety makes real-time data exchange extremely cumbersome as it often necessitates resorting to “the lowest common denominator or alternate means of communications, such as voice,” Horsburgh adds.
Cybersecurity is another – perhaps one of the most important – factors when discussing and designing for data-sharing for naval operations. Both Kheyfets and Horsburgh raise concerns about the cybersecurity implications of real-time data sharing.
“Cybersecurity is also becoming increasingly complex,” states Horsburgh, adding that “multiple security domains (unclassified, NATO secret, U.S. secret, for example) that inhibit sharing of information” make the situation even more challenging.
The stakes are not just technological but also operational, says Hans Weggeman, field application engineer for aerospace and defense at Wind River (Alameda, California).
“Maintaining stable communications [is difficult due to] many types of extreme external conditions,” Weggeman says.
Moreover, the communication protocols, frequencies, and synchronization need to be compatible for seamless data transfer.
Therefore, solving the challenges in real-time data exchange is not merely a technological endeavor but also an operational imperative. Achieving all of this would enable “significantly improved decision-making speed across multiple platforms,” Kheyfets says.
These challenges demonstrate that realtime data exchange is a multifaceted problem that demands a multidisciplinary approach. It is not just about pushing bits faster, but about ensuring those bits are the right bits, reaching the right people, at the right time, in a secure and reliable manner.
The stakes are high, but so too are the rewards: A naval force empowered by seamless, real-time data exchange can adapt more swiftly to ever-changing
conflict dynamics, thereby gaining a crucial edge in modern naval warfare.
One of the most promising solutions is artificial intelligence at the edge (AIAE), which aims to “process most of the data next to the sensors and to path only minimal information between platforms,” Kheyfets says.
Kheyfets’ Aitech is already incorporating advanced processing modules like NVIDIA’s system-on-module (SoM) into small AI-capable solutions.
Meanwhile, Horsburgh is optimistic about modernizing TDLs, such as moving from Link 11 to Link 22 (also known as NATO Improved Link Eleven [NILE]), and using “powerful context-sensitive gateways and intelligent TDL translators” for improved intercommunication. But he points out that while “open standards are making headway on the hardware side
of TDLs, software implementation lags primarily due to the broad and complex scenarios that must be accounted for.”
There are other promising technological solutions like time-sensitive networking (TSN) and precision time protocol (PTP) for high-precision synchronization over Ethernet networks, Weggeman says: “These technologies enable deterministic communication and low-latency data exchange, essential for real-time applications.”
Both Horsburgh and Weggeman tout the modular open systems approach (MOSA) and open standards in technology integration as key to future technological solutions. “MOSA and open standards should definitely be used when designing such platforms,” Horsburgh says, with Weggeman adding that MOSA fosters interoperability, flexibility, upgradability, faster integration, and easier collaboration. (Figure 2.)
During the first quarter of 2023, Northrop Grumman showcased a multiplatform demonstration involving data sharing between airborne and naval systems. The demonstration – performed in collaboration with BAE Systems, Naval Air Systems Command, Office of Naval Research, and Naval Information Warfare Center Pacific –highlighted and leveraged interoperability among various military assets, according to the company. The purpose of the exercise was to improve situational awareness and decision-making in a multidomain environment, Northrop Grumman asserted.
Northrop Grumman used its MQ-4C Triton Flying Test Bed to test an airborne gateway that shared fifth-generation sensor data with ground-based simulators. These simulators emulated various maritime and airborne platforms, including the F-35, E-2D Advanced Hawkeye, and U.S. Navy Aegis class destroyers. (Sidebar Figure 1.)
During the evaluation, the airborne gateway integrated with Triton’s existing
radar systems and used machine learning and artificial intelligence (ML and AI) to facilitate data communication between previously isolated platforms, the company reported, a development that can be capitalized on to enhance the U.S. Navy’s capacity for distributed maritime operations.
“Our gateways provide an open, secure and resilient solution needed to enable
information advantage for our customers,” said Ben Davies, vice president and general manager, network information solutions, Northrop Grumman. “This powerful combination expands the mission sets of maritime platforms to deliver a seamlessly connected fleet – a critical step as the U.S. Navy achieves its naval operational architecture to enable distributed maritime operations.”
“exacerbated by the tendency to focus on new platforms and their capabilities rather than upgrading existing platforms to effectively communicate with the new platforms.”
Designing future platforms to solve this problem is essential. Kheyfets suggests that “Using AI-at-the-edge technology on all platforms will alleviate data exchange issues.” Horsburgh advises that TDL should be “designed in with compatibility, expandability, and upgradability at the beginning of the project.”
New and efficient approaches to cabinet and console design, fabrication, integration, and qualification are enabling prime defense contractors to quickly equip the U.S. Navy with better electronics technology and enclosures while increasing return on investment. As the Navy adds new mission capabilities and refreshes existing ones, the protective cabinets and consoles that house these critical systems are increasingly leveraging innovative design, production, qualification, and integration solutions to deliver more functionality while making them easier to deploy and maintain.
The cabinets and consoles that house shipboard mission electronics, processing, storage, connectivity, and human/machine interfaces (displays and workstations) must be able to protect mission systems from damp heat, saline atmosphere, shock, vibration, and electromagnetic interference (EMI) while maintaining secure and efficient cooling for long-term reliability. Although these enclosures are critical for mission success, their design and manufacture can place unwanted demands on the already limited resources of the companies who could supply both the enclosures and electronic payload.
The result: Design and production of shipboard enclosures is transitioning from the prime contractors over to dedicated enclosure producers that can seamlessly augment the primes’ contractor capabilities with the expertise required to produce quality built-for-purpose enclosures. By taking on the prime contractors’ burden of designing, manufacturing, qualifying, and integrating shipboard electronics enclosures, these vendors create an efficient, low-risk alternative source that enables the prime contractor to instead focus on their primary sources of value creation.
Naval-enclosure vendors, leveraging commercial off-the-shelf (COTS) technology and a modular approach to equipment enclosure construction and payload integration, can enable more vertical-integration capability, design maneuverability, better affordability, and simultaneously lower technology and schedule risk. Affordability and risk reduction are further boosted with proven technology building blocks that enable faster development of purposebuilt solutions for new programs.
This kind of “one-stop-shop” for complete integrated equipment enclosure
solutions – one that addresses the complete technology chain from specification requirements to delivery of fully qualified equipment – drives program value while further reducing risk.
Let’s do an overview of the design considerations required for naval enclosures. (Figure 1.)
Qualification of naval enclosures can be expensive, especially regarding the schedule impact if the equipment under test fails and needs to be re-engineered. High-impact shock qualification (per MIL-DTL-901) using COTS payload equipment is often identified as a program risk. Because of this factor, the assurance of qualification approval is critical. The best way to de-risk shock testing is with a robust engineering phase that assesses system rigidity and reduces equipment shock impact to ensure system survivability. What does this mean? It means that naval-enclosure vendors must have engineering and test teams with deep electromechanical, shock, and vibration expertise across many naval programs.
Depending upon the electronics payload, vendors may use MIL-M-17185 and MIL-PRF-32407 (both addressing resilient mounting) standards for approved isolation mounts to mitigate the risk of shock test failure. In-house modeling capabilities, performed during the design phase of the project, can ensure qualification testing success with no program delays. Those who need such equipment should look for COTS vendors whose testing capabilities include acoustic, shock, vibration, environmental, emissions testing, and qualification.
Payload pre-integration
IPC-A-620 and J-STD-001 (addressing connection and solder) certified operators are required to perform both power distribution and payload wiring. Wire crimping and soldering should be assured by trained assembly technicians. Automated test equipment performs point-to-point electrical verification (continuity, dielectric strength, and insulation resistance per IPC-A-620 or
MIL-STD-202), while fiber-optic cable testing should be performed to MIL-STD-2042 per qualified technicians.
Human-machine interfaces (HMI)
Flat-panel displays (FPD) are the human-machine interface required on a vessel for equipment operation and monitoring. These displays are ruggedized and reliable while offering the highest color fidelity in all conditions over extended periods. Vendors should work with industry-leading embedded display partners to create an FPD specification that meets or exceeds the system’s functional specification requirements for reliability and performance.
If possible, the vendor should procure, validate, and integrate FPDs using in-house produced cabling and interfaces to offer a higher level of turnkey integration. Other qualified suppliers provide keyboards, trackballs, and joysticks that are similarly integrated. The interface between the user and the equipment must be carefully considered to remain mission-focused, following the guidelines of MIL-STD-1472 and ASTM-F1166 (human-engineering design criteria).
Naval enclosures should be built from the ground up, using components and assembly approaches that are intended to meet or exceed the requirements of MIL-DTL-901 (shock) and MIL-STD-167 (vibration) for mission-critical Navy shipboard applications, plus other MIL-STD-810 environmental requirements. Leading enclosure vendors have extensive in-house thermal, structural, environmental, and electromagnetic interference and compatibility engineering expertise gained over hundreds of naval programs, and are able to systematically identify and mitigate the technical risks associated with a new functional specification.
Enclosures need to be designed and built to offer exceptional environmental protection from liquid and other contaminant ingression and EMI and must limit acoustic noise emissions. For example, enclosures and integrated systems should be designed, built, and tested for compliance with MIL-STD-108 and MIL-STD-810 for drip, heat, and humidity environmental protection; MIL-STD-461 for EMI compliance; and MIL-STD-740 and MIL-STD-1474 for acoustic noise generation, among others.
For naval enclosures, the use of common building blocks adds additional functionality while lowering technology risk and cost. The philosophy of this design approach is seen in the use of standard tools for maintenance, use of captive fasteners that can be moved and replaced, removable doors and panels that can hinge left or right, extension slides for full payload equipment access, and easy-to-reroute and quickdisconnect cable and power distribution harnesses. This approach also reduces maintenance complexity, keeping system downtime to a minimum.
Due to their size and weight, U.S. Navy ruggedized enclosures do not easily fit through a ship’s hatch. Cutting and removing portions of a ship’s infrastructure is a common practice required to maneuver and install equipment enclosures above and below decks. Besides significant cost increases and schedule delays, shipboard enclosure installations are one of the leading causes of Navy shipyard injuries during a vessel’s maintenance period. For those reasons, enclosure and system solutions should be purposely built to mitigate these high risks through modularity and hatchability. (Figure 2.)
Designs considering modularity and hatchability also add significant program design and installation maneuverability. Modularity aids rapid solution development and reduces risk by leveraging proven reusable technology blocks with standard interfaces designed for easy disassembly and reassembly. Hatchability – the ability to move enclosures, their payload components, and cooling and power distribution systems through hatches without cutting bulkhead holes and quickly reassemble them where they are required – is a significant cost-saver for contractors.
A key feature of modularity involves the use of cable ladders: This cable-routing approach enables removal of wire-harness assemblies from the enclosure without the complexity of undressing the cables and wiring; the cable ladders can be safely removed from the enclosure with the harness remaining intact and secured. Upon passage through hatches, harnesses are easily reinserted into the cabinet, and are then connected to the payload and enclosure’s connector panels.
This modular construction approach enables system hardware upgrades as necessary and is not dependent on a hull work schedule.
Naval enclosures are designed to protect heat-generating electronics from humidity, ambient heat, saline atmosphere, and other contaminants, requiring them to be sealed. Dissipating electronics’ heat for long, reliable system operation requires careful consideration of the enclosure’s payload, installation environment, and cooling resources available. To address the cooling situation, solutions may be passive (convection and/or conduction), forced-air, liquid (water or refrigerant), or a hybrid of several cooling schemes.
Power delivery, conversion, conditioning, distribution, and electrical isolation of payload equipment are critical functions of all naval equipment enclosures. Power requirements must be customized to specific equipment enclosure configurations. Ideally, the COTS naval enclosure designer should offer an ecosystem of interoperable technology building blocks optimized for efficient enclosure integration of custom power distribution systems, with compliance to MIL-STD-1399/300 (addressing Navy voltage systems), among other considerations.
Enclosures may be equipped with single or redundant power sources and integrated with any power conversion. In addition, an uninterruptable power supply (UPS) may be required by the functional specification. The UPS approach uses power modules
that assure power stability through a transfer switch between two separate sources of supply for continuous power availability and quality; an auctioneering feature selects the most stable of the two sources. For single-source power supplies, battery packs installed in the enclosure or positioned remotely ensure that the payload remains operational throughout power shortages.
While battery technology is evolving quickly, traditional lead-acid banks remain the common choice onboard ship. However, well-established characteristics aside, lead-acid batteries are heavy and space-hungry. As the NAVSEA/NSWCCD [Naval Sea Systems Command/Naval Surface Warfare Center, Carderock Division] assesses lithium iron phosphate (LiFePO4) batteries for naval use, that technology is available to Navy programs, using bestin-class commercial products that offer significant reliability, power density, and extended life benefits to further demonstrate the viability of the new battery chemistry. MES
Curtiss-Wright Defense Solutions https://www.curtisswrightds.com/
Fred Sainclivier is Senior Engineering Manager, 901D, Curtiss-Wright Defense SolutionsInnovators in the area of commercial semiconductors are continuously developing new capabilities in silicon; defense system designers can leverage these advances to build open architecture-based processing solutions. When intelligently packaged for reliable deployment at the edge, the latest commercial data center technologies can advance mission capabilities for the defense and aerospace sector.
U.S. Navy photo by Mass Communication Specialist 3rd Class Nicholas V. HuynhData-intensive applications, such as sensor fusion, artificial intelligence (AI) and high-performance computing (HPC), have been bottlenecked by technologies that do not adequately allow data to flow seamlessly between peripheral devices and the CPU. Add to that ruggedization requirements found in marine/shipboard environments: Finding a viable means to provide high performance data access in a compact footprint becomes even more of a challenge.
Moving data quickly from one component to the next is critical to overall server performance. And at a higher level, servers deployed to move that data must communicate with each other and with displays that form the human interface.
Developments in rugged server technologies are now bringing data centerclass compute performance to aerospace and defense deployments, particularly in space-constrained environments for command-and-control assets. This is enabling AI-based tactical edge computing in critical areas, like signals intelligence (SIGNT), electronic warfare (EW) and C4ISR, for realtime threat assessment and mission-critical decision-making on airborne, surface, and subsurface combatants.
Why use commercial technologies?
Oftentimes, the search for the right rugged server systems starts with identifying the latest commercial technologies available,
then taking the needed steps to ruggedize and package these technologies so they can be utilized in the field, where the system will endure environmental challenges like vibration, shock, saltwater, humidity, etc.
For example, a system designer is looking for a rugged rack server with the latest chipbased acceleration technology to reduce latency and calculate deep learning datasets for inferencing, prediction and real-time decision-making.
System integrators want a rugged rack server that can be deployed using the latest commercial compute capabilities in a SWaP-optimized form factor. For shipboard applications, this includes both surface and subsurface platforms to enable quick sensor processing. These enhanced capabilities are increasingly critical for the end users, who need the most enhanced compute capabilities to make mission-critical decisions in stressful environments.
As a frame of reference, the data center-class 4th Gen Intel Xeon Scalable processors (formerly codenamed “Sapphire Rapids”), low-latency PCIe 5.0 fabrics and the powerhouse NVIDIA H100 GPU are highly sought-after commercial technologies currently driving the design of rugged servers for military and defense applications.
The inclusion of high-speed DDR5 memory and Compute Express Link (CXL) means today’s rugged servers can offer robust, scalable computing ready to handle the challenging workloads in edge computing applications, even those in maritime environments. (Figure 1.)
The speed at which decisions can be reached is increasing in both military and commercial environments. As the defense electronics industry adapts commercial technology to meet its needs, exploiting the continual performance increases driven by enormous market forces, we start to see parallels in how advanced computing enhances data processing, particularly in predictive analytics.
Commercial data centers focus on meeting data-driven, market-specific initiatives. ChatGPT is an example of how data can be rapidly compiled and synthesized, then presented in an insightful manner. This AI-based chatbot is designed to refine data and create a meaningful conversation by predicting the output that best matches the users’ inputs using the latest language processing models.
In shipboard electronics, accurately cataloging data ahead of an object’s identification leads to quicker assessment of friend or foe. Similarly, the ability to define measures to protect a ship at sea or even in port is enhanced by the intuitiveness provided through rapid access to reliable decision-based data. It enables those onboard to build an accurate picture of their environment, and confidently act, reducing decision latency.
As the computing industry’s most common interface standard for connecting highspeed components, PCIe is the primary data path in servers from CPUs to both storage devices and to auxiliary coprocessing components, such as GPUs.
Although PCIe 3.0 was a mainstay in rugged servers for more than a decade, expanding volumes of sensor data mandated more capable protocols, such as PCIe 4.0, which is currently implemented in most newly deployed systems. But even this
leap in data processing seems shortlived with the advent of data-intensive AI-based applications.
The PCIe Gen 5.0 specification was released in 2019, with the first devices launched in early 2022. Commercial electronics, with similar connectivity challenges, are already moving forward in the market with PCIe 5.0’s greater bandwidth, delivering twice the data throughput of Gen 4.0, for an effective bandwidth of 64 GB/sec for a 16-lane link.
The two industry giants among the first to bring Gen 5.0 products to market were Intel and NVIDIA. Intel first supported Gen 5.0 with its 12th-gen core platforms and now includes even higher-performance Gen 5.0 CPUs in the Xeon scalable processor line aimed specifically at server systems. In parallel, NVIDIA is introducing new generations of Gen 5.0 GPUs and DPUs [graphics processing units and data processing units] for both internal and external data paths. Rugged edge servers have certainly benefitted from early adoption of next-gen connectivity.
integrated circuits (ICs) classic designs.
As a global pioneer in IC products life cycle management, Lansdale manufactures over 3,000 classic design ICs in the original package, exactly as they were created and produced by AMD, Farchild, Freescale Semiconductor, Harris, Intel, Motorola, National, Philips (formerly Signetics), and Raytheon.
Our exclusive life cycle management program assures you of a dependable, continuous, cost effective, and high quality source of classic designed ICs today… and tomorrow!
This means Lansdale eliminates the need to go to the time or expense of designing in a replacement part or even doing a complete product redesign –not when we still make ‘em… exactly like they used to.
Log on to our Web site at www.lansdale.com to review our up-to-date product listings and data sheets.
By pushing the boundaries of computeheavy applications, edge-ready servers are packing the processing, storage, and networking power of the latest PCIe Gen5 into integrated systems that minimize latency and maximize bandwidth, while increasing throughput. CPU, GPU, and storage bottlenecks are eliminated to deliver breakthrough data transfer speeds for high-performance workloads.
These dense systems use the latest in low-power, compact computing technologies meaning better thermal load management as well as lightweight, SWaP-optimized architectures. Housing more capability in industry-standard rackmount form factors (1U, 2U, 3U, etc.) eliminates the need for additional servers, saving costs as well.
One implementation of the latest commercial technologies in a rugged edge server is the RES X08, Mercury’s nextgeneration rugged rack server product line that extends the company’s existing
COTS Rugged Edge Server (RES) rackmount family. It optimizes all the latest commercial technologies from Intel and NVIDIA to speed real-time insights and data inferencing directly in the field under extreme environmental conditions. (Figure 2.)
This robust, scalable computing platform can handle challenging edge workloads by delivering higher performance in a smaller or equivalent form factor using data centerclass 4th Gen Intel Xeon Scalable processors, low-latency PCIe 5.0 fabrics, supercomputing NVIDIA H100 GPUs, high-speed DDR5 memory and Compute Express Link (CXL) to infinitely scale system memory.
Ensure maritime mission success
Solving bandwidth challenges at the system interconnect helps ensure mission success, especially in surface and subsurface marine applications, where data must flow from system to system within the confines of an onboard, encapsulated environment. Commercial semiconductor innovators are continuously developing new capabilities
in silicon that defense system designers leverage to build open architecturebased processing solutions. When intelligently packaged for reliable deployment at the edge, the latest commercial data center technologies can advance mission capabilities for the defense and aerospace sector. MES
Justin Myers is principal product manager for Mercury’s Sensor Systems, Edge Division. He has more than six years of combined technical experience in managing, developing, and integrating hardware and software solutions across the aviation and military-spec markets. He received his bachelor of science degree in aerospace engineering from Iowa State University of Science and Technology.
Mercury https://www.mrcy.com/
Designers of test and measurement systems for military applications such as radar and electronic warfare (EW) are stepping up to use artificial intelligence (AI) solutions to enable better testing of cognitive functionality. Meanwhile, modern digital architecture adoption is driving military test requirements.
Artificial intelligence (AI) and machine learning (ML) tools are finding their way into nearly every area of defense systems, from manufacturing, radar system development, and avionics to software development and test and measurement systems.
“Not only is AI impacting the capability of test systems themselves, AI is also having an impact on how we test,” says Jeremy Twaits, Solutions Marketing Manager, Research & Prototyping for Aerospace, Defense & Government, at NI (Austin, Texas). “AI is making systems more adaptable, with behaviors changing based on training data sets. With AI, engineers must know the bounds of the system’s performance and use test methods that meet the most critical and likely scenarios the system may encounter when deployed.
AI tools can also enable cognitive functionality in electronic warfare systems. At Rohde & Schwarz, the company is “helping customers deliver AI/ML-enabled systems by equipping them with tools to deliver high-bandwidth, long-duration RF record and playback systems that are used to train cognitive systems in operationally relevant RF environments,” says Tim Fountain, Global Market Segment Manager, radar and EW [electronic warfare], Aerospace & Defense Market Segment, Rohde & Schwarz (Columbia, Maryland).
“Also, cognitive systems are being use to extract and classify novel emitters in wideband captured data from ELINT [electronics intelligence] receivers,” he continues. “One challenge that our customers repeatedly tell us is that they have no shortage of data from collect activities, but labeling, classifying, sorting, and geolocating those signals is still a manual task that is often overlooked by analysts due to time and budgetary pressures.”
The amount of data being demanded from military users is only increasing, putting more pressure on system designers and those that test those systems.
“With the advancement of high-speed capture technology, the amount of data we’re able to collect is increasing at an exponential rate,” says Greg Patschke, General Manager of Keysight’s Aerospace/Defense and Government Solutions Group (Santa Clara, California). “These large data sets bring the challenge of analyzing the information and formulating results. Currently we are using unsupervised machine learning tools to accelerate the path to insight. We can use intelligent algorithms to identify signals of interest, classify and categorize information, and recognize patterns and anomalies in the data. Utilizing this technology opens the door to a whole new world of data analysis that previously was not feasible.”
Defining scenarios for testing while also enabling adaptability through AI systems will be critical due to the complexity of the systems.
“It is near impossible to test in every possible scenario, but the industry must define critical scenarios and models to test,” Twaits notes. “Due to the dynamic nature and challenge of truly testing and trusting an AI system, a test platform must have adaptability built in to address future test scenarios and requirements. As an example, COTS [commercial offthe-shelf] hardware from NI can link with software tools from MathWorks, such as Deep Learning Toolbox. NI and MathWorks have collaboratively demonstrated how software-defined radios (SDRs) can be utilized for over-the-air testing and assessment of trained neural networks for classifying radar and 5G New Radio signals.”
Contributing to the use of AI in test solutions is having the capability to place test and measurement system functionality in software.
“In the test and measurement industry there is a constant need to improve the
functionality of measurement software,” Patschke says. “The specialized nature of EW testing often requires a level of software innovation and flexibility that we typically don’t see in other industries. For instance, angle of arrival (AOA) testing in relation to radar/EW requires the seamless pairing of both software and hardware to appropriately apply real time kinematics and accurately calculate AOA results.
“A few years ago, this functionality did not exist in [testing] software, but as customer requirements and demands have changed, companies like Keysight have adapted to meet these needs,” he continues. “Customers require systems that possess the flexibility to meet their needs as new challenges surface. The only way to meet these needs at the rate in which they arise is to continue to upgrade our software as much as we possibly can with new capabilities, so that hardware can be continuously repurposed for multiple uses.”
“The most pressing issue that customers tell R&S is that they need a quick, verifiable, and repeatable measurements, often based around a standard,” Fountain says. “Customers often do not have the time or in-house expertise to develop that specific measurement, so may rely on a vendor to have that measurement available as an addon, or in some cases to use de facto industry toolsets such as Matlab and/or Simlink to support quick s/w functionality, especially as FPGAs [field-programmable gate arrays] and GPUs [graphics-processing units] become more prevalent in the measurement data flow.” (Figure 1.)
Defining test systems in software is “exemplified by the trend across the aerospace industry often called model-based system engineering,” says Haydn Nelson, Business Development Manager for Radar/EW, NI. “The push for standardization of systemlevel models and requirements makes software integral to the definition of automated test systems.
“For radar and EW, this is challenging due to the multimission nature of radar and the secretive nature of EW,” Nelson continues. Defining, developing, evaluating, and deploying new methods and techniques is a complex process. As threats evolve, users want new systems faster, and test and evaluation processes cannot stand in the way of this. Software-defined test systems are critical to matching the pace requirements while preserving the sensitivity of system capabilities and performance.
Demand for more laboratory testing is also driving software-defined test systems: “A specific request we see is to be able to test more in the lab in realistic ways, without the challenge of fixed and locked test systems,” Nelson says. “The more one can test before open-air-range testing, the higher the confidence that a new method or technique will be trusted by the end users. Sharing data and proving capabilities is as important as developing the capability itself.”
Complex adversarial threats across multiple domains are driving the performance requirement of radar and EW systems, thus putting more pressure on test-system designers to deliver accurate and efficient solutions.
“In general, the trend is towards ever-higher measurement accuracy and lower phase noise,” Fountain says. “Accuracy and phase noise directly relates to the ability characterize the performance of the radar. On the EW side, we are seeing a move towards higher-fidelity simulation of highly complex electromagnetic scenarios, driven by congested and contested operational environments.”
The digital architecture requirements and modernization efforts of radar and EW systems also demand multifunctionality in test systems.
“At a high level, the requirements for test and evaluation are driven by the adoption of modern digital architectures that require functional, parametric, and system-level test in a single system, as well as ways to segment digital and RF systems for independent test,” says NI’s Twaits. “Additionally, many legacy radar and EW systems are undergoing modernization initiatives for which legacy test platforms are too inflexible to meet the test requirements for new system capabilities. Modernization doesn’t bring infinite budgets for test. New systems and upgrades are constantly balancing the constraints imposed by budget and time-delivery pressures, and being adaptable to changing requirements can, in itself, be a requirement.”
Bandwidth demands also push the limits of testing systems. “Technologically, in the domain of electromagnetic spectrum operations (EMSO), fielded systems are stretching towards wider bandwidths, higher frequencies, greater frequency agility, and more resilience against threats. Accordingly, [test and measurement] equipment must be able to generate and analyze waveforms with appropriate specifications, tune quickly, and create realistic scenarios that stress the unit under test in near-real operating conditions.”
Test systems also reduce long-term life cycle costs by finding flaws early in the design process before a system is deployed.
“A key aspect of delivering on time and on budget is having test strategies that can identify bugs early in the design process,” Twaits says. “Open-air range testing is costly, and not feasible or practical for testing early designs. In radar testing, for example,
customers are looking for hardwarein-the-loop systems that allow realistic targets to be injected into the radar system under test. This allows them to test the system early and often, eliminating issues sooner and assessing the radar against a broad range of scenarios.”
NI offers the radar target generation (RTG) software, which enables customers to operate PXI RF vector signal transceivers (VSTs) as a closed-loop real-time radar target generator. It provides engineers with a single module that can act as a standard radar parametric measurement device and as an RTG that is highly capable and flexible to end-user adaptations. With a fully open list mode, users can define as many as 10 million test targets to sequence at hardware speed, to stimulate radars in ways that would be impossible to accomplish on an openair range.
EW systems are about countering and detecting complex adversarial threats and the test systems about enabling the warfighter to leverage these systems not only efficiently but also safely.
“At its core, EW testing is all about keeping troops safe by ensuring both personnel and equipment are prepared to handle a vast array of electromagnetic threats,” Patschke notes. As the EW testing environment becomes increasingly advanced, customers need to generate the most realistic simulations possible. This can only be achieved by generating high-fidelity, dynamic scenarios that emulate real-world conditions. In the past, this required a large amount of equipment that often lacked any versatility in use. Customers now expect their equipment to not only demonstrate a higher level of capability, such as wider bandwidth and more output ports, but also to offer more flexibility in a more compact size. Keysight has addressed these expectations with a scalable, openarchitecture EW test and evaluation portfolio including the newest M9484C vector signal generator. (Figure 2.)
Fountain notes as a final comment on trends that “there is a desire to move from open-air range test to closed labs,
mainly due to the complexity matrix of open-air tests, the costs and the possibility that RF emissions from tests may be intercepted by unwelcome listeners.”
Open architectures/MOSA initiatives Fountain says he doesn’t see much activity for these initiatives at the test and measurement level. “There are some niche applications for measurement systems at the operational level, where the benefits and added costs of modular architectures such as MOSA [modular open systems approach] and SOSA [Sensor Open Systems Architecture] would be applicable, but in most cases the test and measurement equipment is in a lab, where a controlled environment is desired to provide a high degree of measurement accuracy.”
“In many ways, standard architectures like SOSA are taking a very similar philosophy in embedded design as NI took to test and measurement design with the modular PXI platform: to make systems that are modular, flexible, and interoperable,” Nelson says. “These three goals of modular open architectures are key to the success of future military embedded systems, allowing systems to be designed today and cost effectively upgraded tomorrow. The NI approach to test and measurement mirrors this goal. Having a modular, scalable, flexible, and upgradable embedded system means that test systems must also be modular, scalable, flexible, and upgradable to match changing requirements, capability, and interfaces. We believe that modular test systems that mirror the modular direction of open architecture initiatives will help deliver on the promise of this new embedded system philosophy.”
“Customers who invest in new products want to ensure that their legacy equipment and systems can function in tandem with upgraded platforms,” Keysight’s Patschke says. “This is not only a cost-saving measure but also one that reduces waste by extending the life of older products, while keeping the entire system up to date. Open architecture platforms make sustainability a priority without sacrificing the ability to upgrade down the line. Keysight has placed a premium on open architecture implementation when designing next generation systems.”
Looking forward
AI and software-defined test systems are paving the way for more capability right now and also for tomorrow’s radar and EW test systems for areas such as software-defined radar, spectrum sharing, digital twins, and more.
“One way the future of system testing for DoD [U.S. Department of Defense] customers could potentially evolve is through advancements in digital-twin technology,” Patschke says. “These systems leverage model-based systems engineering (MBSE) methodology to generate digitally realistic testing scenarios that often account for outside variables that prior virtual testing methods could not. The ‘digital-twin’ concept could in theory convert most, if not all, physical system engineering activities into virtual ones. Digital twins have the potential to add extensive value in situations where staging physical tests isn’t practical, and real-world effects are difficult to reproduce. As customers look for more reliable and cost-effective means of testing, the digitaltwin option may become more attractive.”
Fountain says there are four key areas driving test and measurement technology over the next few years:
› Spectrum sharing: Spectrum bands are being redeployed to commercial applications such as CBRS (wireless networks), which leads to a requirement for more complete and precise coexistence testing.
› Software-defined radar: The move from analog pulsed radar to a fully digitally modulated radar, where every pulse can be modulated is already enabling communications between the radar and cooperative assets. But it’s not just radar and comms, but EW, both EP and EA, and [military communications] integrated into a single platform.
› Quantum sensing and quantum radar are still at the very early stage, but if these technologies can be made to work “in the field” they will change the very fabric of how conflicts are conducted.
› Moving from a traditional pulse descriptor word (PDW)-based environment generation to a higher-fidelity in-phase (IQ)-based system, which is driving a demand for higher-bandwidth RF generation capability.
Demand for flexibility and multifunctionality in radar and EW system is also becoming a characteristic of test and measurement requirements.
“We’ve seen many requirements that are demanding test systems to be like a Swiss Army knife: customers want test equipment to do everything in a single system,” Nelson says.
“We often get requests to configure systems that can do parametric test while performing system-level tests such as radar target generation, combined with the ability to conduct RF record and playback. These combined requirements make it hard to do this in a cost-effective manner while maintaining an acceptable size, weight, and power. This is only possible with modular systems that balance closed, specific functionality with the ability to extend capabilities with open software. The trend we are seeing is that modern test systems must be as multifunctional as the systems they are testing.” MES
The pace at which technology is ramping up, including in the military electronics and implements arena, is forcing the defense and aerospace industry to increase its adoption of new tech and parts. Such advances in pace and adoption does expose companies to more risk, but the military supply chain is not alone in this dilemma.
The past several years – both during and after the height of the pandemic –have taught those in industry a lot about how to be flexible in day-to-day work environments, but it has also spotlighted how global businesses operate. If you trace supply-chain disruption down to what happens on the floor of a manufacturing shop, one can easily see how a single breakdown along the line can mean trouble across the continuum, from end-to-end.
Recent disruptions to intricate global supply chains have put significant strain on almost all aspects and resources, not just in the realm of technology. At the same time, defense contractors are looking at multidomain operations and shared technology initiatives, like the Joint All-Domain Command and Control (JADC2) initiative and the modular open systems approach (MOSA) to provide better intelligence and networking capabilities as well as streamlined, cost-efficient system development paths to better enable the military warfighter.
Supply-chain disruption has impacted many facets of the military supply chain and business environment.For those of us in the military and defense industry, a stable supply chain is critical for both national security and economic strength. And just like a surfer trying to paddle past the break, but who keeps getting rolled back to the shore, managing the complexity of supply-chain solutions needed in today’s defense industry can feel a bit like this same frustrating push-and-pull. (Figure 1.)
In order to adequately mitigate critical defense supply-chain risks, there needs to be enhanced resilience to breakdowns within the process. In a February 2022 report on “Securing DefenseCritical Supply Chains,” issued by the U.S. Department of Defense (DoD), four
strategic enablers were identified to help strengthen the global supply chain and avoid similar interruptions in the future. This diverse set of focus areas addresses several factors of the supply chain rather than a single area:
› Workforce: trade skills through doctoral-level engineering skills
› Cyber posture: industrial security, counterintelligence, and cybersecurity
› Manufacturing: current manufacturing practices, as well as advanced technology like additive manufacturing
› Small business: the role of key members of DoD supply chains
Supply-chain resilience and modernization are top of mind for many across all sectors of the defense industry. How does this awareness translate to the actual day-to-day processes the military technology industry need to manage?
One common trend is cost pressures from the DoD being pushed down to the prime contractors, bringing about a new wave of technology, where more is invested in research and development. Advances in high-performance computing and initiatives, like the SOSA [Sensor Open Systems Architecture] Technical Standard, to standardize commercial off-the-shelf (COTS) equipment are all driving the pace of technology, pulling more components in from the commercial market to keep pace with the speeds designers are clamoring for.
Several consequences of this standardization push include:
› Outsourcing by the primes: looking for ways to either minimize volume or technology problems within the supply chain.
› Technology pulled in by system platform providers: examples include putting together chassis, backplanes, and active cards – and possibly operating systems – as well as solving IPMI issues. (IPMI [Intelligent Platform Management Interface] is a standard system-monitoring interface employed by many boardlevel standards.
› Shift in role of traditional suppliers: companies providing “building blocks” –only a backplane, chassis, or power supply, for example – tasked with finding a place to play in the military market.
› Infusion of commercial suppliers: the rapid pace of technology change means more potential entry points of commercial solutions into the marketplace.
The pace at which technology is ramping up is forcing the industry to keep in step, exposing companies to more risk.
In the pre-industrial age, cost versus volume was pretty much linear. To make another widget, you added another person – another widget, another person, and so on.
In the industrial age, fixed costs dominated, so volume increases meant a better cost curve with the goal being to pump out a lot of widgets using the existing infrastructure.
This current “post-industrial” age is not dominated by volume, but rather by complexity, and the major focus is to manage complexity’s impact on costs. Unmanaged cost increases not only hurt an individual company, but can also harm the entire industry in how companies are perceived by their customers.
(Figure 2.)
Although previous production models may have focused on a company spending as little time as possible to get a widget out the door, that’s not today’s business. Success in the military technology industry requires a longer cycle, with a typical project starting about 18 months before a prototype is even
developed, with production starting as much as three or four years after that. With other recent pivots in the global supply chain, such extended development and implementation times become even more impactful to delivery of the final product.
The complexity of this cycle not only relates to technology, but affects all aspects of a business, from sales, program management, and compliance to change
management, customer approvals, and design reviews. No longer is it only the rate of technological change putting tremendous demands on the engineering teams; the recent spate of supply-chain hiccups also then enters the equation as a critical factor.
Some good news: Although delays and disruptions have impacted the supply chain, other factors such as open standards – which help mitigate risks since designs don’t need to start from scratch – are actually helping to form a forward-thinking environment. Many standards groups include key suppliers who commit to support solutions based on the standards themselves. Their membership, awareness, and participation give these companies a different perspective of supply-chain requirements. This situation is creating new opportunities to regionalize manufacturing and inventories, thereby reducing the reliance on single-source suppliers. The availability of key components based on modular open standards that can be used across multiple platforms will encourage further acceleration and adoption of new technologies.
As flow-down continues to occur, manufacturers need to consider a number of factors. When sourcing components, manufacturers must ensure that their vendors are in compliance with the DoD requirements as well. With the strain of constant price increases – sometimes upwards of 20% or 30% for obsoleting technology – affordable traceability is a big challenge. Supply-chain-side operations also must make room for new tooling, new equipment, more personnel, and added training to help ensure that the yield and quality coming out of the manufacturing group stays high and that customers’ delivery expectations are being met.
The key to managing this complex business environment: Companies in the military arena must stay current with the technology as well as the process and must become skilled at balancing resources to increase project risk properly. These moves need to occur across
multiple departments and all partner relationships, so as to deliver quality solutions that meet customer expectations at a fair price point. The ability to balance all of these supply-chain issues affect companies’ ability to grow and the health of the industry as a whole. MES
Shan Morgan is the vice president of sales for Elma. He was previously the senior vice president of sales and marketing for the systems group and also served as general manager of Optima Stantron, the cabinet enclosure unit of Elma. Shan received a bachelor’s degree in aerospace, aeronautical, and astronautical engineering from the University of Arizona.
Elma Electronic • https://www.elma.com/en
Managing supply chain, obsolescence, and counterfeit parts
Military and aerospace supply chains are facing greater challenges than ever before, as systems in these arenas require longer development times and have longer production life cycles than any other industry. The industry must work to overcome such obstacles as component obsolescence in aging systems, prioritization of funding for long-term procurement and maintenance, coordination on the timing of and transition to newer systems, and lengthened budget cycles.
The investment and component life cycle decisions of top semiconductor manufacturers are driven by high volumes, demand for higher performance, lower power requirements, smaller plastic packages, and cheaper costs. Moreover, expected product life cycles can be as short as a single year, or can be as long as five to ten years. Overall, while industry certainly benefits from technological advancements, semiconductor life cycles do not align to the time requirements of most military programs.
When faced with critical-part obsolescence, manufacturers need to find reliable replacements that not only address single-replacement events but also cover the requirements for the full life cycle of a program. Redesigns are an option, but often entail costly development, testing, and requalification. Normal customer/ supplier relationships rarely allow customers to work directly with the semiconductor suppliers to extend technologies, or transfer intellectual property (IP) to prolong component life. Finding replacements in the “gray market” is a hugely risky route, one that raises the prospect of illegal or counterfeit supply.
1. Obsolescence management begins at design and product definition phases. We have all heard stories of products being launched with obsolete components. This is a particularly relevant issue for customers with lengthy development and qualification cycles. Choosing the right component technology and supplier can have dramatic impacts on longterm availability. The lowest-cost sources may not be the best choice for longterm supply. Understanding the risks associated with component selection during the design and product definition phases requires a deep understanding of the timeline for long-term system development and when components are introduced by the semiconductor company. Market misalignment occurs when a long-term system is designed using short-term market products or already-mature products. Architecture misalignment occurs when the choice of processor architecture is clearly close to the end of its life, usually when the
cost of architectural change has postponed an inevitable future. Board design misalignment is what happens when board layouts knowingly specify densely packed, shifting commodity products. Component selection during development often leads to potential premature product redesigns and requalification, as component choices are frequently influenced by the aim of maximizing the potential of older software and hardware solutions.
Market misalignment: There are times when the easy or most efficient component selection is the wrong choice, due to market misalignment. This scenario could be feasible if there is a planned and budgeted last-time purchase within a few years of selecting the components; however, this is seldom the situation. For example, graphics-driver products have a very short lifetime compared with military or commercial avionics displays. Opting for a PC-oriented component in a market where the sole
Get all the latest slot profiles aligned to SOSATM and CMOSS in a single backplane, plus VITA
46.11 chassis
management, air or conduction cooled, integrated payload cards and much more.
With you at every stage!
Leaders in Modular Open Standards enabling the Modern Warfighter
purpose of those components is product development will lead to obsolescence even before the first production units are shipped. When it comes to choosing a graphics driver product up front, it is crucial to consider the long-term system cost and allocate a budget for an early last-time-buy. This move is necessary to safeguard military or commercial avionics displays and avoid obsolescence in a market where PC-oriented components may not meet the requirements of product development.
Architecture misalignment: Commercial avionics has long settled on the PowerPC processor multicore architecture, due to the control for multicore operation and speculative execution across multiple processor cores. The existing multicore PowerPC products have been certified for commercial avionics and software development is proven. It is also true, however, that the end of the PowerPC architecture is on the horizon. It is only a matter of time before the commercial avionics market adopts Arm or RISC-V as its favored architectures. Every single PowerPC-based product being designed today is already on a processor product line that is over a decade old.
Board design misalignment: There is always the temptation to pack DRAM [dynamic random-access memory] as tightly as possible. Many systems have variable amounts of DRAM, whether to enhance the product or to provide tiers within a product family. Packing that DRAM into the smallest possible space could be an advantage. However, the challenge with long-term systems lasting 15-20 years is that DRAM technology will evolve markedly within that time. It is crucial to anticipate this change by strategically designing board layouts up front, thereby minimizing the need for large future modifications.
Market misalignment: Memory products are designed for short-term systems. Fact: The largest memory suppliers no longer stock DDR3, but – coincidentally – DDR3 is the primary memory type supported by the latest PowerPC product. Designing longterm systems without a long-term memory product plan up front is an issue. Memory has been a fast-moving product for decades, as innovations occur at a rapid pace to keep up with data center demands and portable product demands. Long-term systems are a misaligned use for all memory types because all memory types are short-term products.
When addressing obsolescence end users need to consider a number of key questions:
› What is the component’s life cycle status across the application’s lifetime? Not only does the end product’s lifetime need to be considered in component selection, but when the component’s lifetime started, as well as the product’s lifetime start dates and end dates, must be accounted for. Choosing the right components means alignment of product dates with all component dates.
› Are the key components of the design comprehensively documented? Changing software costs about 10 times more than changing hardware. Any component that is directly controlled by software will be the most valuable to keeping a longterm system shipping. These components are typically the highest price items in a BOM [bill of materials] as well. The documentation and archive requirements associated with these types of components must be elevated to alleviate longterm system risk of sustainment.
› Can the true design files (VHDL, Verilog, SPICE models, constraints, source test vectors) be archived at the design phase to offer a chance of rebuild if the unexpected happens? This question pertains to the most intricate, expensive, and software-dependent products: To minimize maintenance risks, it is crucial to create an archive that contains all relevant information about these products. This archive should be independent of any EDA [electronic design automation] tools and operating systems.
› Does the design contain proprietary IP? If so, the ability to “port” such designs when the components are made obsolete may be compromised, or subject to
relicensing and royalties. Embedded IP blocks, particularly within FPGAs [field-programmable gate arrays] and ASICs [application-specific integrated circuits], are commonplace. However, these IP blocks can also make portability and sustainability almost impossible if efforts are not taken to ensure there is a plan for these products. This plan may have to be a fully funded last-time buy or IP licenses up front that allow porting from one technology to another. Simply clicking a button and incorporating IP blocks (presumably because it’s easy to do so) is not a solid long-term system plan. If IP blocks are not incorporated into a long-term plan at the design phase, it may be impossible to come back to them years later for a solution.
Many companies do almost none of this planning for long-term systems in the design phases where the impact would be maximized. From component selection all the way through IP block selection, there are many ways a long-term system company can mitigate risk and schedule for system longevity.
2.
It is important to understand and model the costs and risks associated with obsolescence.
Key questions:
› Does the project plan need to include anticipated product refresh or redesign during its life? If yes, how will it be funded?
› How will the business account for the capital locked down in long-term component sourcing?
› What will the component obsolescence impact be on aftersales service commitments?
› What effect would a shortened product life cycle have on customers and end users?
If the equipment has long qualification, production, or in-service time frames, it will face component obsolescence.
Best-in-class organizations devote skilled multidisciplined workers to handle obsolescence management. Preventative planning can reduce or eliminate cost and risk.
4. Identify important product discontinuation notices (PDNs) that may affect the business and monitor them.
Proactively monitoring component life cycles is crucial to anticipating problems before they occur. Excellent commercial tools are available that can track a component’s life cycle, lead times, and specification changes. Such tools provide alerts that can be triggered when PDNs are issued.
Key questions:
› Will sub-tier suppliers share their BOMs?
› Do sub-tier suppliers have adequate obsolescence-management processes in place?
While many electronics manufacturers offer proactive component life cycle management as a service, others are completely reactive. PDN notifications are typically only aimed at the direct purchasers of the component of the last two years.
5. Last-time buy (LTB) –What to forecast?
Forecasting is not an exact science, and it is likely that forecasts will be inaccurate. It is difficult to anticipate product needs years in advance or possible market disruptions. Underestimating needs has a risk of prematurely terminating a product, while overestimating ties up unnecessary capital in stock and excessive storage costs. If a redesign in the future is planned to limit the cost of the LTB, then the design, requalification, and the opportunity costs of using engineering resources must all be factored in.
6. Purchase from 100% authorized sources
There is a misconception that when a component is discontinued that unauthorized or gray- market sources are the only option. The risk-free option of an authorized after-market supplier should always be the first choice.
The risks of counterfeit and poor-quality components from unauthorized sources represent a significant risk to production yields and mean time between failure rates (MTBR) in the field. Inferior or substandard testing by unauthorized third parties provides a false veneer of confidence that authenticity can be tested. This mimicry of testing may be a visual, an x-ray, or a poor partial copy of the original manufacturer’s test processes. Full tri-temp testing is rarely offered, and the risk of commercial-grade components being remarked as industrial, automotive, or military parts is always possible. (Figure 1.)
Unauthorized component risks include:
› Poor handling, resulting in electrostatic damage and the destruction of the device.
Dawn’s PSC-6238 VITA 62 compliant 3U VPX Power Supply for conduction cooled systems is designed to operate in a military environment over a wide range of temperatures at high power levels. Up to 800 Watts available power.
Dawn is the leader in VITA 62 compliant power supplies for the mission critical market. Wide range of standard features, highly configurable through custom firmware.
(510) 657-4444
dawnvme.com
› Poor storage, whether in excessive heat, cold, or moisture during any part of its storage life. Risks include external lead corrosion, failed solderability, moisture ingress, and/or a catastrophic failure of the device.
› Fake documentation that mimics the original specification or lies about performed tests.
› Recovered, re-marked, or repackaged components masquerading as another product.
There are also documented quality problems related to cleaning chemicals used to recover, wash, and re-mark used components, which can slowly migrate into the products, shorting and corroding bond wires and pads. Superficial testing is not guaranteed to find these faults. Although recovered components may pass these tests and survive for a period in service, their inevitable failures will destroy MTBR figures and result in reduced reliability and damaged reputations.
Original component manufacturers (OCMs) do not provide guarantees for products purchased through unauthorized channels. Providers who are not fully authorized may market themselves as AS6171/4-compliant. While better than no compliance at all, if AS6171/* testing is offered in isolation, this potentially indicates that the parts were not sourced directly from the OCM but have only passed AS6171 testing. This merely minimizes but does not eliminate risk.
Fully authorized distributors are compliant with the SAE Aerospace Standard, AS6496. Simply stated, they are authorized by the OCM to provide traceable and guaranteed products with no quality or reliability testing required because the parts are sourced from the OCM. (Figure 2.)
Bottom line: Expect and plan for the unexpected. The unique qualities of many military and aerospace designs add to the challenge of finding viable solutions to obsolete components. It is more vital than ever before to have partners who can support businesses during unforeseen or unplanned component discontinuations, completely risk-free whenever they occur. MES
Dan Deisz, Rochester Electronics’ vice president, design technology, has more than 35 years of semiconductor design experience. Dan’s group performs all authorized product replications and customer-specific design solutions. Dan is an active member of the Anti-Counterfeiting Task Force (ACTF) for the Semiconductor Industry Association (SIA) and has trained more than 200 CBP/HSI [U.S. Customs and Border Protection/Homeland Security Investigations] agents. Reach him at ddeisz@rocelec.com.
Ken Greenwood has over 30 years of experience in the electronics industry, working in strategic roles at Nortel Worldwide and Matra Comms France before moving into management roles in the connectors and RF/microwave markets. In his current role as Rochester Electronics product & technology solutions manager EMEA, Ken interfaces with Rochester’s supplier partners and the market. Email Ken at kgreenwood@rocelec.com.
Rochester Electronics https://www.rocelec.com/
Threaded
Push/Pull
Break Away
AirBorn builds on its legacy of rugged miniature interconnects by introducing TriMate circular connectors. TriMate’s performance meets or exceeds legacy MIL-DTL-38999 connectors yet they are manufactured in a smaller, lighter, and easier-to-install connector package.
TriMate connectors are offered in three different forms to support different applications: Threaded, Push/Pull, & Break Away . To reduce manufacturing complexity, all three styles mate with the same receptacle. AirBorn offers both the connectors and pre-tested cable assemblies designed to your unique specifications. Let’s go to work!
From the Cold War period (1945-1989) through present-day globalization, the importance of maintaining reliable security coalitions and positive international relationships cannot be overstated. As modern-day warfare relies on technology for achieving military readiness and strength, collaborating on interoperable technological advancements remains an enduring mission for the U.S. and its coalition partners.
To perfect military technology, nations must plan strategically beyond tactical units. This is especially important today, as warfare is no longer focused solely on the physical destruction of enemy forces. By acting as a unified front, coalition partners can integrate more effectively, generate deterrence, and thwart adversarial actions by enhancing the training, deployment, coordination, and real-time situational awareness of allied nations.
For instance, in the Indo-Pacific theater of operations, the U.S. maintains a highly capable cross-section of commandand-control technology that supports situational awareness in today’s battlespace. Going forward, however, near-future warfare requires a new paradigm that provides a comprehensive intelligence picture and detailed situational awareness of joint forces across the theater. This information gathered must be consolidated to inform tactical and operational decisions that prioritize deterrence and the saving of lives.
Commensurate with this future paradigm is the ongoing race to develop and deploy multidomain technology and command-and-control systems, which are helping to shape a new era in modern warfare: developing multidomain capabilities to address “Gray Zone” competition (GZC).
GZC tactics, deployed globally to avoid all-out conflict, are becoming increasingly common. Recent examples include China’s recent statements on Taiwan’s independence and subsequent U.S. responses. Even a recent incident between North Korea and South Korea, during which warning shots were fired over a maritime dispute, demonstrate the persistent need to avoid all-out conflict.
These incidents underscore the urgency to develop and deploy a range of intelligence, surveillance, and reconnaissance (ISR) capabilities across multiple domains, including space and surface. These capabilities can then be digitally applied to command-and-control platforms, which can utilize machine learning/artificial intelligence (ML/AI) software solutions to provide forces with a decision advantage.
Nation-state governments recognize the potential for GZC to bleed into the general population. Social-media platforms like
Twitter and TikTok struggle to maintain credibility amidst the presence of bots and foreign propaganda; while naval, coastal, and aircraft assets are being deployed to physically harass and intimidate opponents. All of these tactics are in use to gain the upper hand in military efforts.
The ongoing Joint All-Domain Command and Control (JADC2) modernization efforts by each service are being driven by all of the multidomain operational imperatives. This is not aspirational; the U.S. is already experimenting and fielding innovative new technologies in both Gray Zone and multidomain operations.
Achieving strength in numbers is crucial for effective deterrence. The moral dimension of war calls for a global effort to ensure democratic nations maintain their leadership role in the global world order. Within a theater strategy, coalition partners possess powerful political-military capabilities that can help maintain a strong global presence. This collaborative approach enhances military command-and-control technology while strengthening support within an integrated coalition.
Creating interoperable systems that enable coalition warfighters to access real-time data and tools across the ground, air, sea, cyber, and space arenas is critical for developing the necessary command-and-control capabilities to compete against military challenges. Seamlessly integrating oncedisparate systems delivers a competitive edge for U.S. joint force and coalition partners. In this way, technology must serve the shared mission, with edge computing and data links two critical systems for achieving interoperability.
Edge computing already forms a foundational part of existing mission partner environments. For example, commercial coalition equipment (CCE) is a core component of a mission partner environment (MPE), facilitating expeditionary coalition or commercial network connectivity. This connectivity enables mission command, network communications (e.g., voice, video, and data), and situational awareness among Army, joint, and coalition forces.
By implementing data links and aerial mesh networks supported by nondetectable video data links, warfighters will be better able to receive fast and reliable internal communications between coalition partners. This technology ensures that synchronized strikes and real-time mission updates can be executed or communicated with clarity, uniformity, and efficiency.
One notable example of video data link technology that continues to improve is the Defense Information Systems Agency
(DISA) Unified Video Dissemination System (UVDS). The UVDS architecture and its related services consistently meet airborne and ISR full-motion video requirements. In both the Gray Zone and multidomain operational environments, its future importance lies in providing persistent, focused, real-time operational information flow to tactical and enterprise end users worldwide.
Despite the view of some scholars, modern warfare is not a stalemate. Rather, it is a fiercely competitive landscape where nation-states strive to achieve independent goals. For instance, China recognizes U.S. multidomain efforts and is now working (according to reports) to develop a competing technology for the JADC2 initiative, known as the multi-domain precision warfare (MDPW) concept.
The U.S. remains highly competitive against China’s MDPW efforts and is deploying new JADC2 technologies. This is a never-ending relay race, where each capability “baton” helps U.S. and allied forces extend their lead in this relentless pursuit of assured communications and decision advantage.
Every effort by industry partners and military service program executive offices is critical in this race.
This is not a drill.
Supports AES-256 and FIPS140-2 encryption
The space tech industry is a collective effort to defy gravity both literally and figuratively, taming physics and driving innovation into soaring new realms. New technologies are emerging rapidly, with new use cases being discovered daily.
This white paper shares the results of a research study on current and future trends in the space and satellite industry, covers a broad overview of industry analysis, and looks at advanced technologies in new designs that deliver vastly reduced cycle times. It also helps identify the drivers of this growth and acceleration, the enabling technology trends, and the pain points new entrants will face.
Read this white paper: https://tinyurl.com/53x7c5yc
James Terry [U.S. Army Lt. Gen. (Retired)] is senior vice president, Cubic Defense.and publish
that educates our readers.
Hybrid artificial intelligence (AI) systems supply the ability to perform accurate prediction and prescription across a wide range of military use cases. In particular, hybrid AI can enable more effective asset management when other methods fail.
Digital transformation is a familiar phrase. But what does it really mean? Some digital transformation is anything using computers to make processes better, easier, or more efficient. Some digital transformation projects using this definition have succeeded.
Nonetheless, how “transformative” are they? Many of them fail, while others would be more accurately described as digital automation. Nothing was transformed; old processes and calculations, which had been manual, were just automated. But new capabilities still needed to be created. While faster and more efficient, these same processes could still be done manually if necessary.
True transformation must go beyond automation. Real digital transformation empowers organizations to do things that were impossible before. This means using data, software, and computers to supply new ways to conduct the mission and supply new capabilities which can’t exist in others. In most cases, moving beyond the visualization of historical data and looking into the future is needed for “real” transformation.
Increasingly, real transformation, doing things we simply could not do before, means the use of artificial intelligence (AI). Amazon and Walmart know (thanks to machine learning [ML]) to suggest selling cat food to customers who buy kitty litter. Even this simple AI makes a great deal of money for retailers.
As digital transformation becomes associated with AI, that in turn is often associated with big data. For military users, it’s essential to understand what big data means.
In retail applications, a bewildering torrent of data is available. It is truly big. Consider barcode scans at a major retailer like Walmart: In a typical week, this retailer generates about 45 billion barcode transactions, all of which are used as part of the big data used to train the company’s AI. It can supply rich business intelligence even without AI. These transactions shape decisions about everything, as the data includes metrics on everything from buying trends, volume, and shipping to labor needs, pricing, and marketing strategies.
Digital transformation in the consumer sector has been most successful when data is cheap, abundant, and readily available. These are not military data attributes, however. Before
embracing civil lessons about big data, AI, and digital transformation, military organizations need to be cautious.
Four common failures are seen when mainstream commercial analysis and AI methods try to address military challenges:
› The populations of people and assets within the military are much smaller: Walmart serves 270 million customers a week, some more than once. That’s roughly 100 times larger than the Department of Defense (DoD) population, including active duty, civilians, guard, and reserve combined. Large retail corporations have tens of thousands of assets, like semi-trailer trucks, which are often similar and have coherent data collection. For example, Amazon probably has around 100,000 trucks. In contrast, the U.S. Air Force has fewer than 6,000 planes that range in make, model, and use, using highly variable data collection systems. Commercial data lakes are fed by massive, coherent data flows; military data swamps feed on modestly sized, chaotic data flows.
› Commercial and civilian data costs are nearly free since much data is collected organically: Your Google search helps train its AI. The company is paid to present advertising. Retail companies must collect all the barcode scans and customer data to complete a transaction. In contrast, military data systems – when they exist – are an added expense, regardless of their potential benefits. In short: Issues such as cryptography and unique defenserelated cybersecurity create a cost differential for defense data if and when it does exist.
› Some civilian enterprises, like Amazon or Google, were born digital and have pervasive data infrastructures: Every product in a large retail system has an SKU, the retailer’s stocking code. Nearly every item has a universal product code (UPC) which is scanned by a radio-frequency identification (RFID) scanner, barcode, or both. These are tracked easily throughout the distribution, stocking, and sales cycle. The U.S. military’s history predates computers: While the DoD has made progress using technology like barcodes and RFID, there exists no central data lake across the DoD supply chain. A complete history of how all parts move through the logistics system does not exist. Even if one did exist, it would pale in comparison to the abundance of data that companies like Walmart or Amazon can gather and track.
› Finally, most mainstream civilian AI takes a long time to train and deploy: Some models, like the retail forecast of Christmas sales, take years to fine-tune. When released to production, civilian data analytics and AI often need massive cloud-computing resources.
These attributes are incompatible with the need for rapid response to unprecedented events. Civilian AI cannot be relied upon when communications are spotty, or when electricity is minimal. Additionally, the large datasets and massive computing power needed by mainstream AI solutions make it virtually impossible to deploy at the edge.
Civilian AI was at the heart of airline ticket pricing when COVID-19 struck. The totally new situation simply destroyed pricing models. In contrast, military operations are supposed to grapple with totally new situations. The war in Ukraine is a good example of how militaries must change and deal with surprises in methods and tactics.
So, civilian big data, digital transformation, and AI approaches are often not compatible with military realities. This raises the question: Is there another possible approach?
Military systems must work quickly, with minimal datasets. They need to accommodate the diversity of DoD assets and personnel.
Industrial firms with some challenges – like offshore oil operations – are turning to hybrid AI. Such hybrid systems, like Lone Star Analysis’ Evolved AI (EAI), are trained in advance through known physics or policy rules, subject-matter experts, and maintenance procedures.
A hybrid AI system like EAI is considered big data-optional, as it is capable of operating with very little historical data.
In other words, we teach the computer things we already know. We only ask it to lear” what we don’t know from data. This approach has the potential to reduce data needs by orders of magnitude. Perhaps more importantly, it can provide predictions for things that have yet to occur in the data.
A few examples of this approach have been seen in the U.S. military already. Several earlier trials run by DARPA [the Defense Advanced Research Projects Agency] showed how retail-style AI simply couldn’t cope with situations where hybrid AI performed very well. Another DARPA program, dubbed AI Forward, is DARPA’s current initiative to explore new directions for AI research that will result in trustworthy systems for national-security missions.
Automating tasks like staff assignments and material requisitions is the norm in the DoD. While some processes stay stubbornly manual, most have been digitized to some degree, but these are mainly automated without being transformed.
Perhaps the richest opportunity in the military for digital transformation is improving readiness. Aviation readiness, for one, is challenging because operating and sustainment issues with aging planes and legacy equipment continue to increase. Unplanned delays in replacement planes and higher-thanprojected use rates have forced life extensions or equipment upgrades for most military legacy planes.
Nowhere do these readiness issues appear more starkly than at the aviation depots. Uncertainty abounds in the depot work flow: When will a plane be available for induction? What will the status be when it’s inspected? How many planned operations will be unnecessary? How much unplanned damage from corrosion or wiring degradation will be found? Which functional shops will be logjammed? How will logjams change the sequence of depot operations?
What’s striking about the depot example is the comparison to the commercial mainstream – small imperfect data versus massive clean data. This approach holds out promise for advanced digital technology during a conflict, as peacetime ways of gathering data will be misleading during hostilities.
Even without a significant confrontation, agile, softwaredefined threat systems are creating change faster than mainstream methods can accommodate. The era of emulating big tech and consumer-facing analytics is waning. Within military organizations, big data lakes are not readily available; even if big data was available, it inhibits the agility warfighters need.
True digital transformation will require moving beyond Silicon Valley’s mainstream. DoD is not selling cat food.
Steve Roemerman is the chairman and CEO of Lone Star Aerospace, Inc. and has served in this role since 2004.
Lone Star Aerospace • https://www.lone-star.com/
For many COTS [commercial off-the-shelf] vendors and VITA members, the Tri-Service Memo issued in January 2019 by the secretaries of the Army, Navy, and Air Force was the highest validation of several decades of their combined efforts.
The memorandum clearly stated that, going forward, modular open systems approach (MOSA)-supporting standards “should be included in all requirements, programming and development activities for future weapon system modifications and new start development programs to the maximum extent possible.”
Examples of MOSA standards include the Sensor Open Systems Architecture (SOSA) and CMOSS, both of which rely on OpenVPX hardware as their foundation.
For those individuals and companies who have worked together over the decades to further the activities of VITA and the VSO, this historic milestone can arguably be viewed as the point at which their collective efforts finally transitioned from evangelism to Department of Defense (DoD) mandate.
After years of working together to champion the performance, reliability, and cost benefits of COTS electronics, and the power of open architectures, that argument has emerged victorious.
What’s more, it’s been codified into law. While the DoD has employed MOSA to varying degrees for nearly two decades,
its use was formally made law and mandated by Congress in the National Defense Authorization Act for Fiscal Year 2017 (Public Law 114 – 328). Section 805 of the Act (“Modular Open System Approach in Development of Major Weapon Systems”) states that approved major defense-acquisition programs “shall be designed and developed, to the maximum extent practicable, with a modular open system approach to enable incremental development and enhance competition, innovation, and interoperability.”
In 1994, then-Secretary of Defense William J. Perry launched the COTS Initiative that enabled military use of commercial electronics.
In his memo, “A New Way of Doing Business,” Secretary Perry wrote: “Moving to greater use of performance and commercial specifications and standards is one of the most important actions that DoD must take to ensure we are able to meet our military, economic, and policy objectives in the future.”
Since then, VITA has led the way, establishing an environment and ecosystem to ensure the success of the COTS Initiative. A case can easily be made that VITA is the most successful consortium effort that industry has yet seen, and provides the best model for bringing together industry, government, customers, and academia in a way that enables business rivals to work together towards the same goals, for the benefit of national security and to establish a healthy technical and economic ecosystem.
The VITA consortium model, which we now see effectively embraced by groups such as the Open Group’s FACE [Future Airborne Capability Environment] and SOSA consortia, has continually provided the best example for bringing together the widest mix of stakeholders to build true community and drive the development of essential open standards.
But this is not a time for resting on laurels. VITA and the standards defined by the VSO are living entities that are built to evolve as technology moves forward and new challenges drive the need for new innovative capabilities.
The consortium approach and the open standards ethos are built for flexibility and to adapt quickly to emerging requirements.
The shift from evangelism to mandate for MOSA is just the beginning and VITA provides a solid foundation on which to continue to architect the future of embedded computing.
Ivan Straznicky is CTO, Curtiss-Wright Defense Solutions.
Curtiss-Wright Defense Solutions • www.curtisswrightds.com
Military Embedded Systems focuses on embedded electronics – hardware and software – for military applications through technical coverage of all parts of the design process. The website, Resource Guide, e-mags, newsletters, podcasts, webcasts, and print editions provide insight on embedded tools and strategies including technology insertion, obsolescence management, standards adoption, and many other military-specific technical subjects.
Coverage areas include the latest innovative products, technology, and market trends driving military embedded applications such as radar, electronic warfare, unmanned systems, cybersecurity, AI and machine learning, avionics, and more. Each issue is full of the information readers need to stay connected to the pulse of embedded technology in the military and aerospace industries.
militaryembedded.com
The X9 AI System is the first rugged system to utilize the NVIDIA® Jetson Orin™ processor family. NVIDIA’s family of systems-on-module are targeted for autonomous applications where live data collection and analysis in real time is essential. This flagship product line from NVIDIA® is being deployed in commercial, industrial and now military applications such as UAV/UAS, autonomous vehicles, and airborne applications. High bandwidth sensor-to-processing gives tremendous advantage to warfighters in at-the-edge battlefield applications.
GMS X9 AI utilizes NVIDIA’s most recent Jetson Orin™ module. The Jetson Orin™ contains 2048 CUDA® engines with an incredible 275 TFLOPS and 64 Tensor cores operating @ 1.3GHz. The Jetson Orin™ has 12 Arm® Cortex® 64bi/cp with 3MB of L2 Cache and 6MB of L3 Cache operating at 2.2 GHz max and 1.6GHz nominal. The Orin supports 64GB memory which is 256-bit wide with a 204.8 GB/s transfer rate.
The Orin is connected to two RMC I/O carrier modules to expand the system I/O to enhance the functionality of the system. The primary expansion card provides quad 10GBase-TX Ethernet ports with PoE+ to power cameras and target sensors. Additionally, it provides quad 3G-SDI ports for video capture via an FPGA. Each camera also supports an RS232/422/485 port for camera control such as PTZ and the other functions on the camera. This module also provides dual 40/100GigE fiber ports and dual M.2 (2280) sites for storage. Additional I/O such as 8K x 60Hz multi-mode 1.4a Display Port, USB-C, and sensors such as Shock, Temp, and Tamper.
The second expansion site is a Rugged Mezzanine Module (RMC-50). Although there are over 30 RMC modules that may be installed in this location, GMS’ standard offering is a Quad CoaXPress® module. CoaXPress® is the most advanced technology in video standards, its digital interface developed for high-speed image transmission in machine vision applications. The CoaXPress® standard supports up to 6.25 Gbps per coaxial cable and soon will support 12.5 Gbps. Unlike other video formats such as CameraLink, CoaXPress® transmission data is in packet form. This allows multiple cameras to utilize the same link, much like cellular data. This unique feature opens up applications where it has not been possible due to size, cost and power.
The X9 family of products redefines embedded computer architectures. The traditional computers in the market (rugged or commercial) require the user to pre-configure their systems up-front making systems over-built and expensive, under-developed for future growth, and inflexible when obsolescence sets in. The X9 Mission Computer’s open Distributed Computer Architecture (DCA) has each specific function available in a sub-system and linked together via Thunderbolt® 4 and a single LightBolt™ cable. Units can be placed up to 50 meters away from each other in any format: Daisy Chain or Star or direct-attach.
This open DCA mitigates obsolescence by upgrading/replacing only those functions required to be upgraded. The 100W power delivery in X9 systems allows each system to be powered on its own or by any of the other systems in the “loop”. There are also options for external power supplies (including MIL-STD-1275) with battery back-up, allowing the system to grow as needed without the limitation of available power. Other X9 modules include: Artificial Intelligence, Storage (fixed or removable), GPU, Workstation, Switch and Display as well as many others.
Ą NVIDIA® Jetson™ Orin™ with 12 Core Arm® 64-bit CPU @ 2.2GHz, 2048 CUDA® Cores, 275 TFOPS
Ą Memory/Storage: 64GB 256-bit LPDDR5; 16TB SSD; 64GB eMMC5
Ą High Speed I/O: 2x 100GigE Fiber; 4x 10GigE w/ PoE+; 4x 3G-SDI or 4x CoaXPress®
Ą Connectivity: Over 30 RMC add-in I/O; M.2 add-in I/O: 5G Cellular; Wi-Fi®/Bluetooth; HD-GPS
Ą GPU: 2x NVIDIA® v2.0 DL accelerator @ 1.6GHz, with vast array of video encoding: H.265, H.264, VP9 and AV1
Ą 8K x 60Hz multimode DisplayPort 1.4a port
Ą USB-C, GigE, USB2 and UART Service port
Ą Voltage, Shock and Temp sensors
Ą Eight tri-color LEDs for status and messaging
Ą Single +20VDC power operation
Ą Dual fan control with tachometer for external cooling
Ą Ultra-small at 6”x4.75”x2” and 2.1lbs.
Ą Temperature: Operates up to extended temp -40°C to +85°C (Optional)
The V1161 100G Ethernet card is a high-performance embedded computing module with the Xilinx® Versal® Adaptive System-on-Chip (ASoC) and NVIDIA® Mellanox® ConnectX®-5 (MC-X5) network interface device. It offers rugged optical and electrical IO options and is ideal for applications needing high-speed interfaces, network offloads, and onboard payload processing. The combination of the MC-X5 device and the Versal ASoC device allows for system designers to leverage the off-the-shelf world-class Ethernet performance of the MC-X5 while deploying unique data processing and security algorithms in the onboard Versal® ASoC device.
The V1161 excels in 10/25/40/50/100Gbs Ethernet applications, featuring hardware offloads for UDP, TCP, RoCE v2, DPDK, GPUDirect, NVMEoF, and other protocols. Combining the MC-X5 and Versal® ASoC maximizes algorithm effectiveness without additional design efforts for Ethernet, PCIe controllers, DMA engines, or software drivers.
The Versal® ASoC's FPGA fabric supports IP cores for Fibre Channel, ARINC-818, sFPDP, Aurora, and more, making it suitable for mixed protocol needs. In XMC or 3U VPX form factors, the V1161 enables a single-slot solution, turning a VPX-based computer into a sensor interface and computing solution with 100G optical interfaces, FPGA fabric, and ARM processor cores.
Ą Up to eight (8) 1G to 25G optical ports via MPO front panel I/O or VITA 66 optical backplane I/O. Electrical I/O via Pn6 also available.
Ą Xilinx® Versal® ASoC (FPGA)
Ą NVIDIA® Mellanox® ConnectX®-5 Network Interface Device
Ą Hardware offloads for UDP, TCP, RoCE v2, DPDK, GPUDirect, NVMEoF, +more
Ą Supports PCIe Gen4 x16, Gen4 x8, Gen3 x16, Gen3 x8
Ą 2 banks of 4GB up to 1866MHz LPDDR4 SDRAM
Ą Onboard embedded PCIe Switch device
https://newwavedv.com/products/fpga-interface-cards/pmc-xmc/v1161-programmable-100g-ethernet-xmc-asoc-card/
www.newwavedv.com
info@newwavedv.com
952-224-9201
www.linkedin.com/company/new-wave-design-and-verification
IC-ARM-VPX3b – 3U VPX LX2080A/LX2160
Arm®-based Single Board Computer
The IC-ARM-VPX3b is a 3U VPX Single Board Computer based on a NXP QorIQ® Layerscape® LX2080A /LX2160A multicore communication processor (8/16 Arm® Cortex®-A72 32/64 bit cores). It is ideal for use in applications requiring high processing and communication performance together with low power. The IC-ARM-VPX3b features up to 32GB of DDR4-ECC and several storage capabilities (M.2 slot, eMMC, F-RAM) which enable system designers to meet large centralized systems’ topology demands and handle heavy traffic scenarios on specific backplane segments. The IC-ARM-VPX3b is partially compliant with VITA 65.0 Slot Profile SLT3PAY-1F4F2U-14.2.14., it provides multiple 10G/40G Ethernet and PCIe Gen2/3 interfaces available on the VPX backplane connectors for high bandwidth connections. This board complies with VITA 46.0 and 65.0 standards. It includes a boot loader firmware for initialization. A Board Support Package is available for Linux or VxWorks Real Time Operating Systems. Optional board accessories include an Engineering kit for debug (JTAG/COP, console) and a 3U Rear Transition Module for development purposes. This rugged board is available in air-cooled and conduction-cooled versions.
Ą 3U VPX
Ą NXP LX2080A/LX2160A Arm® processor
Ą VITA 65 Slot Profile SLT3-PAY1F4F2U-14.2.14 (partial)
Ą Data Plane: 10G or PCIe Gen3 interfaces
Ą Expansion plane PCIe Gen3
Ą up to 32GB of DDR4-ECC
Ą M.2 slot, eMMC, F-RAM
IC-FEP-VPX6e – 6U VPX FPGA board with two FMC+ sites
The IC-FEP-VPX6e is a 6U FPGA processing board based on 2* Kintex® UltraScale™/ Virtex® UltraScale+™ FPGAs and 1*QorIQ LS1046A processor. The IC-FEP-VPX6e is the perfect solution to applications requiring intensive Digital Signal Processing (DSP) in a 6U VPX form factor. The QorIQ® LS1046A processor integrates quad 64-bit Arm® Cortex A72 cores with high-performance Data Path Acceleration Architecture (DPAA) and network peripheral interfaces required by demanding processing applications. The on-board PCIe advanced switch allows versatile coupling between the processor, the FPGAs and the fabric links of P1 VPX connector (Non-transparent configuration possible). The board provides one L2 Gigabit Ethernet switch with 1000BX and 1000G-BASE-T Ethernet ports. Furthermore, the Multiware software package and its simplified API allows to easily integrate the IC-FEP-VPX6e in heterogeneous multi-domains PCIe architectures. Two FMC+ (VITA 57.4) sites are provided to add FMC and FMC+ modules.
Ą 6U VPX
Ą 2 * Kintex® UltraScale™/ Virtex® Ul-traScale+™ FPGAs
Ą QorIQ LS1046A
Ą Gen2/3 PCIe switch
Ą Giga Ethernet L2 switch
Ą 2 * FMC+ sites
The ComEth4682e is a 3U OpenVPX Ethernet switch that is 25/100Gb Ethernet capable. It has been developed for high-computing applications, including radar, sensor, electronic warfare, and network processing. The ComEth4682e integrates a Layer 2 (Ethernet) and Layer 3 switch, as well as a control processor to support Control and Data Planes that are separated by software configuration settings for highly secured 3U VPX systems. The switch features a total of 56 x 25Gbps SerDes: 32 lanes are routed to the rear VPX connectors as 1/10/25Gbs Ethernet ports or can be merged into 4-lane Fat Pipes to obtain 8 lanes as 40/100Gbs Ethernet ports. Likewise for the 24 optical fiber ports, they are routed to the front panel (2*MPO connectors) as 1/10/25Gbs Ethernet ports or can be merged in set of 4 fibers to obtain 3 lanes as 40/100 Gbs Ethernet ports. The ComEth4682e benefits from the proven and expandable switchware network management application. It can be remotely configured by the switchware web interface, SNMP or CLI interfaces. The ComEth4682e complies with the following slot profiles SLT3-SWH2F24U-14.4.3 , SLT3-SWH-4F16U-14.4.13 and SLT3-SWH-8F-14.4.2.
Ą 3U VPX Managed Layer 2+/3 switch
Ą VITA 65.0 SLT3-SWH-2F24U-14.4.3
Ą VITA 65.0 SLT3-SWH-6F1U7U-14.4.14 (option)
Ą Up to 56 ports
Ą 24 optical fibers (front MPO connector)
Ą 1GBASE-KX, 10 & 25GBASE-KR, 40 & 100GBASE-KR4 ports (rear)
ComEth4591a – 3U VPX Dual-Plane 40G Ethernet Switch for hybrid copper-optical backplanes
The ComEth4591a is a ruggedized 3U VPX dual-plane 10/40 Gigabit Ethernet Layer 2/3 Switch developed in alignment with the SOSA™ Technical Standard. It integrates two sets of independent Layer 2 (Ethernet) and Layer 3 Switches & control dual-core ARM processors to support Control and Data Planes that are physically separated. This board architecture is ideal for use in highly secured 3U VPX systems. The ComEth4591a supports the VITA 66.5 style C optical VPX connector through a LightCONEX™ 12-lane optical transceiver module. The ComEth4591a features up to 38 * 1/10/40 Gigabit Ethernet on VITA 46 (copper) & VITA 66.5 (optical) connectors. Ethernet Port allocation is easily configurable through the Switchware and several port combinations are available via the backplane (10GBASE-KR/10GBASE-KX4/40GBASE-KR4).The Switchware allows to remotely control the switch by web interface, SNMP or CLI interfaces. The ComEth4591a is available in conduction-cooled grade.
3U VPX
Managed Layer 2+/ 3 switch
Switching for 2 separate and independent domains
Slot profile SLT3-SWH-4F1U7U1J-14.8.7-n
Up to 38 * 1/10/40 GbE on VITA 46 & 66.5 connectors
Developed in alignment with the SOSA™ Technical Standard
www.interfaceconcept.com
SOM-5993 COM Express® Basic Type7
SOM-5993 is a COM Express Basic Type-7 module (125 x 95 mm) powered by Intel® Xeon® D-1700 Processor (Ice Lake-D LCC) with up to 10-cores for a myriad of high performance applications. This module supports DDR4 memory and PCIe x16 Gen 4. The SOM-5993 is an excellent solution for applications that require powerful computing in a compact design, such as test equipment, edge server, defense and medical equipment.
https://www.advantech.com/en/ products/770fe072-dea9-417c-847521218b711d12/som-5993/mod_4ff392331417-4b53-b9cc-43fa6bfbb428
Advantech USA www.advantech.com
Intel® Xeon® D-1700 Processor (Ice Lake-D LCC)
COM Express R3.0 Basic Module Type 7 pin out
Operating temp.: 0 ~ 60 °C (Standard)/ -40 ~ +85 °C (Extend)
128GB SODIMM DDR4 ECC/Non-ECC support
4~10 core processor, with max. TDP 67W
High speed Ethernet (4 x 10GBASE-KR interfaces, one GbE)
Various expansion (PCIe x16 Gen4, PCIe X8, 4PCIe X1, 4 USB3.0, 2 SATA3)
TREK-60
Advantech’s rugged computing solution is designed for harsh environments with a wide operating temperature range (-30 ~ 70 °C/-22 ~ 158 °F), and is compliant with MIL-STD-810G and 5M3 specifications for vibration/shock resistance. When used in fleet management and surveillance, TREK-60 supports up to eight camera input channels and an integrated AI accelerator for scalable video stream edge inferencing. The RF extension module with an automotive-grade FAKRA connector provides GNSS, WLAN, Bluetooth, and WWAN capabilities for real-time communication, vehicle tracking, and data collection. The embedded dual CAN bus supports diverse vehicle protocols, including raw CAN, J1939, and OBD-II, for vehicle monitoring and diagnostics, while the intelligent vehicle power management system supports ignition on/off/ delay and wake-up event control.
Ą Modular AI Platform for Scalable Surveillance and Fleet Management
Ą Equipped with DeviceOn/iService software for remote device management
Ą Scalable computing performance via CPU boards for specific application requirements
Ą Advanced video surveillance system with AI accelerator for video AI capabilities
Ą Modular design supports the latest RF communication technologies
Ą Rugged platform with automotive-grade shock and vibration tolerance, wide operating temperature and
Ą Easy pairing with second-generation TREK displays via a single-cable connection
https://www.advantech.com/products/1-2jsj5t/trek-60/mod_8e7a0368-4476-4422-a8d4-c8981586dcfc
Apacer TCG SSD SV240 Series is equipped with military-grade encryption that conforms to the FIPS 140-2 Level 2 cryptographic standard and has earned FIPS 140-2 Level 2 certification. The Level 2 validation ensures tamper-evidence through the use of special coatings, seals and labels to prevent security information from being detected. This series can be shipped with many value-adding features, such as wide temperature operation for rugged applications, which Apacer is the first to offer. It’s also available in four form factors: 2.5”, M.2 2280, mSATA and MO297, and is available with optional support for rugged R-SATA connectors. Capacities are available up to 1920 GB. Apacer’s diverse array of extremely secure FIPS validated SSDs take security to the next level for the industrial world.
Ą FIPS 140-2 Level 2 Certified
Ą Interface & form factor: SATA 2.5", M.2 2280, mSATA, MO297
Ą Temperature: Wide Temperature; Standard Temperature
Ą AES 256-bit hardware encryption
Ą TCG Opal 2.0
Ą SMART Read Refresh™
Ą DataDefender™
https://www.apacer.com/en/product/industrial-product/industrialsearch/industrial_ssd/ssd_specialty/fips-tcg-series
APACER MEMORY AMERICA INC.
www.apacer.com
ssdsales@apacerus.com
TCG SSD SV240 Series Embedded HardwareDesigned with the engineering developer in mind, the 524 Series development system incorporates a 9-slot OpenVPX backplane (9 payloads + 2 power slots) with profiles aligned to Sensor Open Systems Architecture (SOSA™) and C4ISR/EW Modular Open Suite of Standards (CMOSS) initiatives. Unobstructed accessibility to cards under test enables probe access with intelligent system monitoring capabilities.
Ą SOSA Aligned
Ą 3U/6U 9 slot payload + 2 power slots SOSA aligned backplane with slot
Ą Open frame for easy card access
Ą Maximum unrestricted airflow and cooling for high-powered cards
Ą Supports 3U x 160mm Modules.
Ą Supports air-cooled modules using IEEE 1101.10 card guides.
Ą Supports conduction-cooled modules using VITA 48.2 aluminum slot guides.
Ą Front mounted LED Array for SOSA Aligned 12V and 3.3 Aux. DC Voltages
Ą DC voltage test jacks for SOSA Aligned 12V and 3.3 Aux. DC Voltages
Ą Front mounted power switch.
Ą Atrenne Chassis Manager System Monitoring Board
The X9 SPIDER Host “Mission Computer” is a breakthrough in technology and contains many industry firsts in hardware, mechanical structures, interconnect and thermal innovation. With over 26 patents pending, its ultra-small, high performance, space-optimized CPU board, I/O bandwidth (455Gbps) and its unique stackable mechanical design, X9 modules can be configured into any system imaginable.
Featuring the world’s first rugged (IP67) 40 Gbps connectors which provide 100W of power up to 50 meters, the X9’s power delivery, management and density is unmatched in today’s market. Its unique design utilizes patented RuggedCool™ technology to provide four-sided cooling and full operation at up to +85°C.
The Mission Computer is a complete system-in-a-box with so much I/O, storage and processing that a single module meets most system needs. The CPU is the Intel® Xeon® W workstation class with 8 cores operating up to 4.7GHz, with up to 128GB of ECC DDR4 DRAM. The graphics engine drives up to four simultaneous displays over four Thunderbolt™ 4 ports. The four Thunderbolt™ 4 ports are capable of daisy chaining to multiple devices, and each provides 100W of DC power up to 50m.
Available I/O for the Mission Computer is impressive: within the Mission Computer are 20 PCIe Gen4 lanes and 20 PCIe Gen3 lanes used to add internal I/O modules such as MIL-STD-1553, serial, CANbus, 100Gb Ethernet and so much more. I/O is available on M.2 or 50W (RMC-50) and 100W (RMC-100) Rugged Mezzanine Carriers.
The available RMC-100 GPU is NVIDIA’s flagship GPU RTX-A4500 MXM, featuring 16GB of 512GB/s GDDR-6, and 5888 CUDA® cores with 17.66 TFLOPS FP-32. With rackmount server-like performance, the CPU is directly connected to the GPU via 8 lanes of PCIe Gen4 for 128GB/sec transfer rate. The Mission Computer provides up to four 100GigE ports via quad optical transceivers and small rugged connectors. 1/10Gb Ethernet is also available via RMC and/or M.2 add-in modules.
The X9 family of products redefines embedded computer architectures. The traditional computers in the market (rugged or commercial) require the user to pre-configure their systems up front making systems overbuilt and expensive, under-developed for future growth, and inflexible when obsolescence sets in. The X9 Mission Computer’s open Distributed Computer Architecture (DCA) has each specific function available in a sub-system and linked together via Thunderbolt® 4 and a single LightBolt™ cable. Units can be placed up to 50 meters away from each other in any format: Daisy Chain or Star or direct-attach. This open DCA mitigates obsolescence by upgrading/replacing only those functions required to be upgraded. The 100W power delivery in X9 systems allows each system to be powered on its own or by any of the other systems in the “loop”. There are also options for external power supplies with battery back-up, allowing the system to grow as needed without the limitation of available power. Other X9 modules include: Storage (fixed or removable), GPU, Workstation, Switch and Display as well as many others.
Ą Intel® Xeon® W CPU 8 Cores @ 4.7GHz (Intel® embedded roadmap); 128GB RAM and up to 16TB SSD
Ą GPU co-processor: NVIDIA® RTX-A4500 with 5888 CUDA® Cores, +384 Tensor Cores @ 18TFLOPS with 16GB GDDR6 RAM
Ą Quad Thunderbolt™ 4 ports w/100W power each; copper or up to 50m fiber
Ą Quad 100GigE Fiber; 1/10 GbE via Rugged Mezzanine Carrier or M.2 add-in I/O
Ą Connectivity options: 3x M.2 sites for 5G Cell / Wi-Fi-6 / BT5 / HD-GPS / Dual MIL-STD-1553 / Much more
Ą Over 30 Rugged Mezzanine Carriers (RMC) for easy system customization and expansion
Ą System I/O port with USB / COM / GPIO / SAM™ I/O
Ą Shock, Temperature and Tamper sensors; 8x Tri-color LEDs for status and messaging
Ą Single +20VDC power operation; can be powered via Thunderbolt® 4 power delivery; optional MIL-STD-1275 w/50ms hold-up
Ą Fully-sealed, submersible and conduction coole
Ą Stackable, modular, interlocking systems use “QuadroLock™” wedgelocks to secure systems together only 6”x4.75”x2” and 2.1lbs
Ą Temperature: Operates up to extended temp -40°C to +85°C (Optional)
The X9 Spider “Server Computer” is a technology breakthrough that contains many industry firsts: 26 patents are pending for mechanical and thermal. Modular and scalable, X9 modules can be configured into any system imaginable. X9 Server Computer has the world’s first rugged (IP67) 40 Gbps connectors that also provide 100W of power up to 50 meters, and patented RuggedCool™ technology provides four-sided cooling and full operation at up to +85°C.
The CPU is Intel’s® 3.1GHz Xeon® D processor featuring 20 cores, with up to 128GB of ECC DDR4 DRAM. The graphics engine and two 40Gbps Thunderbolt™ 4 ports provide up to four 8K video streams, and the ports are capable of daisy chaining and each provide 100W of DC power up to 50m. The X9 Server Computer takes full advantage of this bandwidth via Rugged Mezzanine Carriers (RMC) and high speed I/O devices.
The Xeon® D has two directly piped 100GigE ports providing directto-memory RDMA and RoCE v2, plus there are 24 PCIe Gen4 lanes also under DMA control. With M.2 storage, the X9 Server provides ultra performance RAID via Intel VROC. The CPU is directly connected to the GPU via 8 lanes of 28GB/sec PCIe Gen4.
The available RMC-100 GPU is NVIDIA’s flagship GPU RTX-A4500 MXM, featuring 16GB of 512GB/s GDDR-6, and 5888 CUDA® cores with 17.66 TFLOPS FP-32. With rackmount server-like performance, the CPU is directly connected to the GPU via 8 lanes of PCIe Gen4 for 128GB/sec transfer rate. The Server Computer provides up to two 100GigE ports via quad optical transceivers and small rugged connectors. 1/10Gb Ethernet is also available via RMC and/or M.2 addin modules.
Available I/O for the Mission Computer is impressive: using 20 PCIe Gen4 lanes and 20 PCIe Gen3 lanes, users can choose internal I/O modules such as MIL-STD-1553, serial, CANbus, 100Gb Ethernet and so much more. I/O is available on M.2 or 50W (RMC-50) and 100W (RMC-100) Rugged Mezzanine Carriers.
The X9 family of products redefines embedded computer architectures. The traditional computers in the market (rugged or commercial) require the user to pre-configure their systems up front making systems over-built and expensive, under-developed for future growth, and inflexible when obsolescence sets in. The X9 Mission Computer’s open Distributed Computer Architecture (DCA) has each specific function available in a sub-system and linked together via Thunderbolt® 4 and a single LightBolt™ cable. Units can be placed up to 50 meters away from each other in any format: Daisy Chain or Star or direct-attach.
This open DCA mitigates obsolescence by upgrading/replacing only those functions required to be upgraded. The 100W power delivery in X9 systems allows each system to be powered on its own or by any of the other systems in the “loop”. There are also options for external power supplies with battery back-up, allowing the system to grow as needed without the limitation of available power. Other X9 modules include: Storage (fixed or removable), GPU, Workstation, Switch and Display as well as many others.
Ą Processor: Intel® Xeon® D CPU, 20 Cores @ 3.1GHz; 128GB RAM / 80TB SSD
Ą GPU co-processor: NVIDIA® RTX-A4500 with 5888 CUDA® Cores, +384 Tensor Cores @ 18TFLOPS with 16GB GDDR6 RAM
Ą Dual Thunderbolt™ 4 ports w/100W power each; copper or up to 50m fiber
Ą Dual 100GigE Fiber with RDMA; 1/10 GbE via Rugged Mezzanine Carrier or M.2 add-in I/O
Ą Connectivity options: 3x M.2 sites for 5G Cell / Wi-Fi-6 / BT5 / HD-GPS / Dual MIL-STD-1553 / >30 RMC carriers
Ą Up to 4TB native high-performance SSD
Ą Up to 64TB high-performance SSD w/RAID/RDMA (via RMC-50)
Ą System I/O port with USB/COM/GPIO/SAM™ I/O
Ą Single +20VDC power operation; can be powered via Thunderbolt® 4 power delivery; optional MIL-STD-1275 w/50ms hold-up
Ą Fully-sealed, submersible and conduction cooled
Ą Stackable, modular, interlocking systems use “QuadroLock™” wedgelocks to secure systems together
Ą Ultra-small at 6”x4.75”x2” and 2.1lbs.
Ą Temperature: Operates up to extended temp -40°C to +85°C (Optional)
The X9 and Epic Intelligent Switches provide essential functions in any rugged system. They provide an astounding level of performance and bandwidth that is not even found in rackmount switches, yet fits in the palm of a hand! They are fully sealed, rugged, and battlefieldready with no compromise to performance.
The X9 Intelligent Switch (12 ports) provides an incredible four 100Gb Ethernet ports at a full data rate, as well as eight 10GBase-TX Ethernet ports via rugged mil-circular connectors or RJ-45 jacks for lab or industrial application use. The 36-port Epic Intelligent Switch has four 100Gb Ethernet ports and 32 10Gb Ethernet ports. Both switches open up rugged applications which have never before been possible due to size restrictions, speed or power requirements. X9 Intelligent and Epic Switches may be cascaded for unmatched performance at any size or cost.
The heart of each switch is a Broadcom Ultra Low Latency, high bandwidth enterprise-class switch with up to 880Gbps of core switching bandwidth. This Layer 2/3 deployed switch architecture and Cumulus® Linux control software is well supported via GMS’s quad core Atom processor with 32GB of DRAM and 1TB of SSD. The embedded processor is responsible for configuring the switch and provides a browser-based user interface for control and programming. To facilitate this interface a service port is provided with video, dual USB and a 1Gb Ethernet port for remote access.
All the connectors for power, 100Gb Ethernet, Service and 10Gb Ethernet ports are fully rugged, waterproof (IP67) and have covers to prevent damage when no cables are connected.
The X9 family of products redefines embedded computer architectures. The traditional computers in the market (rugged or commercial) require the user to pre-configure their systems up front making systems over-built and expensive, under-developed for future growth, and inflexible when obsolescence sets in. The X9 Spider family’s open Distributed Computer Architecture (DCA) has each specific function available in a sub-system and linked together via Thunderbolt® 4 and a single LightBolt™ cable. Units can be placed up to 50 meters away from each other in any format: Daisy Chain or Star or direct-attach. This open DCA mitigates obsolescence by upgrading/replacing only those functions required to be upgraded. The 100W power delivery in X9 systems allows each system to be powered on its own or by any of the other systems in the “loop”. There are also options for external power supplies with battery back-up, allowing the system to grow as needed without the limitation of available power. Other X9 modules include: Storage (fixed or removable), GPU, AI, Workstation, Switch and Display as well as many others.
Ą Ultra-fast, low latency, 12 port/36 port intelligent Layer 2/3 switches with onboard 416MHz MIPS CPU
Ą Switching: 4x 100GigE ports; 8x 10GigE ports (X9 Intelligent) or 32x 10GigE ports (X9 Epic)
Ą Up to 880Gbps bandwidth switching via non-blocking, enterpriseclass Broadcom 56760 Switch
Ą Quad core Intel CPU for packet operations and configuration
Ą Configured via Cumulus® Linux for advanced top-of-rack data center IP processing
Ą High-performance stacking; fast failover within 100ms
Ą ContentAware™ engine for scalable, high-density packet classification
Ą DHCP client and server support, plus SNMP
Ą Supports MLPS for short-path routing on WANs
Ą Unicast, multicast and spanning tree capabilities
Ą Advanced SmartHash for load balance across trunk groups
Ą Very low latency, VLAN support, QoS/differentiated services
Ą Only 6” x 4.75” x 2” @ 2lbs. (X9 Intelligent) or 9” x 6” x 4” @ 4lbs. (X9 Epic Intelligent)
Ą Shock, Temperature and Tamper sensors; 8x Tri-color LEDs for status and messaging
Ą Single +20VDC power operation; optional MIL-STD-1275 w/50ms hold-up
Ą Fully-sealed, submersible and conduction cooled
Ą Stackable, modular, interlocking systems use “QuadroLock™” wedgelocks to secure systems together
Ą Temperature: Operates up to extended temp -40°C to +85°C (Optional)
The X9 Storage module provides remote and local removable Mass Storage to the X9 Host computers. The storage canister is removable with over 5000 mating cycles. This makes the storage module ideal for applications where massive amounts of data must be captured at very high data rates and be removed for security or archive needs.
The X9 Storage connects an X9 Host computer (X9 Mission Computer, X9 Server Computer, X9 AI System) via Thunderbolt™ 4 up to 50 meters away without the need for an external power supply (powered by Host) with 40Gb/s transfer rate. Each Storage module supports four U.2 storage devices in a sealed canister. The U.2 may be Quad NVMe, SATA, or up to Eight M.2 (2280) memory sticks. Additionally, NSA approved encryption drives such as FIPS-140-2 or CSfC are available for total security. The locking mechanism of the canister is rugged and tamperproof. It alerts the system as soon as the lever is turned which allows the Host to initiate a Secure Erase cycle if so programmed. A hardware optional RAID controller may be ordered in lieu of the standard software controller.
Storage modules may be cascaded as needed by the system, and each Storage system may be up to 50 meters away from each other.
Thunderbolt™ 4 provides the copper or fiber interconnect, and also transports up to 100W of power delivery over the cable. The X9 Storage capacity and speed have never been achieved in Network Attached Storage (NAS) residing 50 meters away. This removes the distance limitation of Direct attached Storage (DAS) and brings new applications for the battlefield such as ground vehicles, UAV/UAS platforms, command post installations, and shipboard or airborne platforms.
The X9 family of products redefines embedded computer architectures. The traditional computers in the market (rugged or commercial) require the user to pre-configure their systems up front making systems over-built and expensive, under-developed for future growth, and inflexible when obsolescence sets in. The X9 Spider family’s open Distributed Computer Architecture (DCA) has each specific function available in a sub-system and linked together via Thunderbolt® 4 and a single LightBolt™ cable. Units can be placed up to 50 meters away from each other in any format: Daisy Chain or Star or direct-attach. This open DCA mitigates obsolescence by upgrading/replacing only those functions required to be upgraded. The 100W power delivery in X9 systems allows each system to be powered on its own or by any of the other systems in the “loop”. There are also options for external power supplies with battery back-up, allowing the system to grow as needed without the limitation of available power. Other X9 modules include: Storage (fixed or removable), GPU, Workstation, Switch and Display as well as many others.
Ą Storage: Quad U.2 storage canister with high 5K mating cycles
Ą Rugged: fully-sealed, removable canister and mating unit
Ą Connectivity: dual Thunderbolt™ 4 ports with 100W power delivery (each port)
Ą Capacity: Secure, quad U.2 SSD up to 128TB
Ą Supports Quad NVMe™ (x4 PCIe) or SATA or Eight M.2 SSD
Ą Support for NSA approved drive encryption such as FIPS-140-2 or CSfC
Ą Supports RAID 0/1 via software; optional hardware RAID controller
Ą Only 6” x 4.75” x 2” @ 2lbs.
Ą Shock, Temperature and Tamper sensors; 8x Tri-color LEDs for status and messaging
Ą Single +20VDC power operation; optional MIL-STD-1275 w/50ms hold-up
Ą Power surge and spike power conditioners
Ą Fully-sealed, submersible and conduction cooled
Ą Self-retaining dust caps for each I/O connector
Ą Stackable, modular, interlocking systems use “QuadroLock™” wedgelocks to secure systems together
Ą Temperature: Operates up to extended temp -40°C to +85°C (Optional)
The X9 Workstation I/O (“WSIO”) is an integral function of the X9 system architecture, providing user interfaces including displays, networks, input devices, local dedicated secure storage. WSIO allows add-in application-specific I/O and has industry-standard rugged, sealed, dustproof and waterproof connectors to withstand a rugged environment for years of reliable operation.
The X9 WSIO is connected to the Host computer (X9 Mission or X9 Server) via a Thunderbolt™ 4 interface and may be powered directly from an X9 Host up to 50 meters away. Further, multiple X9 WSIOs may be daisy chained to an unlimited number of stations, while Thunderbolt™ 4 provides unlimited expansion to other X9 modules.
Built-in WSIO user interfaces are: one 10GBase-TX via a sealed RJ-45 connector, mini DisplayPort, five 10Gbit/s USB-C (3.2) ports with up to 15W (5V @ 3A) of power delivery to peripherals. All the X9 WSIO connectors are fully sealed and allow a rubber cover when not in use.
The X9 WSIO includes a removable U.2 tray for either a 2.5” NVMe™ or SATA drive, or two M.2 SSD sites. The drives may be NSA encrypted or CSfC type; can be easily removed to archive the data.
The X9 WSIO also provides twelve expansion I/O or sensor sites. There are: six M.2 (3042) for larger I/O modules such as 5G cell modems, dual MIL-STD-1553, or many others from GMS or a third party. Additionally, three M.2 (2242) and three Express Mini sites for I/O such as NTSC video capture, video out, dual 1Gb Ethernet, GPS, Wi-Fi®/Bluetooth and many more. Visit the GMS website for all SAM (Special Application Modules) available from GMS.
The X9 WSIO may be powered by the Host via Thunderbolt™ 4 or powered by external +20VDC power via an IP67 GMS Smart Power™ (patent pending) connector for safe, ultra low EMI.
The X9 family of products redefines embedded computer architectures. The traditional computers in the market (rugged or commercial) require the user to pre-configure their systems up front making systems over-built and expensive, under-developed for future growth, and inflexible when obsolescence sets in. The X9 Spider family’s open Distributed Computer Architecture (DCA) has each specific function available in a sub-system and linked together via Thunderbolt™ 4 and a single LightBolt™ cable. Units can be placed up to 50 meters away from each other in any format: Daisy Chain or Star or direct-attach. This open DCA mitigates obsolescence by upgrading/replacing only those functions required to be upgraded. The 100W power delivery in X9 systems allows each system to be powered on its own or by any of the other systems in the “loop”. There are also options for external power supplies with battery back-up, allowing the system to grow as needed without the limitation of available power. Other X9 modules include: Storage (fixed or removable), GPU, Workstation, Switch and Display as well as many others.
Ą Connection: commercial rugged I/O connectors
Ą Storage: fully-sealed removable storage, 2.5” SSD, 2x M.2, NVMe™ , SATA
Ą Connectivity: dual Thunderbolt™ 4 ports with 100W power delivery (each port)
Ą Expansion: 12 Expansion sites – 9x M.2, 3x Express Mini
Ą 10GBase-TX port with sealed RJ-45 connector (pat. pending)
Ą One sealed DisplayPort with 8K support (patent pending)
Ą Five USB-C ports with power
Ą Connects directly to X9 Host without a power supply; up to 100W downstream power
Ą Only 6” x 4.75” x 2” @ 2lbs.
Ą Shock, Temperature and Tamper sensors; 8x Tri-color LEDs for status and messaging
Ą Single +20VDC power operation; optional MIL-STD-1275 w/50ms hold-up
Ą Power surge and spike power conditioners
Ą Fully-sealed, submersible and conduction cooled
Ą Stackable, modular, interlocking systems use “QuadroLock™” wedgelocks to secure systems together
Ą System I/O, 4x Antennas, 4x Coax video
Ą Self-retaining dust caps for each I/O connector
Ą Temperature: Operates up to extended temp -40°C to +85°C (Optional)
Holt has been supplying MIL-STD-1553 ICs to the military and aerospace industries since 2001 and is a one-stop source for all MIL-STD-1553 components. In addition to Holt’s proprietary products, Holt offers drop-in replacements for existing competitor industry standard solutions, providing customers with a cost effective alternative, reducing lead times and mitigating future product obsolescence issues. Holt is the recipient of numerous supplier awards and coupled with its unparalleled technical support and customer service, Holt stands out as the number one choice for MIL-STD-1553 components.
Holt’s products cover the entire gamut of MIL-STD-1553 functionality, including protocol ICs, IP cores, transceivers and transformers. Holt specializes in mixed signal IC design, integrating both digital protocol and analog transceiver functions on a single IC. Select products also integrate MIL-STD-1553 transformers, transceivers and protocol in a single package, providing customers with the highest level of integration necessary to minimize size, weight, power and cost (SWaP-C).
Ą IP Core Family: HI-6300
Ą Protocol, RAM, dual transceivers and dual transformers in a single 15mm x 15mm package: HI-2130
Ą Protocol ICs with integrated transceivers: HI-6130 and MAMBATM
Ą Error-correcting code (ECC) RAM or RAM parity with BIST
Ą Unparalleled free technical support including plug-and-play reference designs and software
Ą Drop-in replacements for existing competitor industry-standard solutions
Ą DO-254 Design Assurance Level A Compliant options
Rugged Embedded Computers up to 9th Gen. i7 and Xeon Server
The PIP Family, CEC, and MXCS Server are powerful, highly integrated, robust and fanless embedded computer solutions. Selection of the components are purely made on the subject for long-term availability and low power consumption. The systems can be expanded in a very modular way and represent a unique solution for today's demanding and flexible defense requirements. The products are designed to operate under extreme and normal conditions without the need of fans. MPL solutions are engineered and manufactured in Switzerland to meet MIL STD-810 as well as other MIL standards.
The systems include features like wide DC input, reverse polarity and more. Additional GPGPU, GPS, WLAN, CAN, 1553, ARINC, Sound, and UPS modules are available.
Ą Soldered CPU
Ą Ethernet (up to 10Gbit), USB (3.1/2.0), Serial ports…
Ą PCIe, XMC, mPCIe, PCIe/104, MXM, m.2 expansion
Ą Extreme low power consumption
Ą Compliance: e.g. DO-160G, MIL-STD-461, -704, -1275
Ą Availability 10+ years (repair 20+ years)
Ą Optional -40°C to 85°C environment temperature
From LCR Embedded Systems, the SAVE-720 chassis is intended for integrated Command, Control, Computers, Communications, Cyber, Intelligence, Surveillance, and Reconnaissance (C5ISR) systems in Army ground vehicles. The chassis design reflects requirements as stated in the Interface Description Document for C5ISR Systems Integration in Army Ground Vehicles, v1, February 2022. Standardized A-Kit/Vehicle Envelope (SAVE) chassis, conform to size, weight, power, connector requirements and electrical interfaces for C5ISR systems under the SAVE standard.
The SAVE-720 chassis and backplane support 3U VPX SOSA aligned payloads as well as CMFF target payloads common to systems conforming to the standard. It includes the complete connector complement under the standard.
The SAVE standard describes a defined physical boundary for C5ISR systems in ground vehicles which adds long term stability for functional upgrades and provides a standardized integration space for system developers. Leveraging the high data rates of 3U VPX architecture, the SAVE strategy will allow speedy and cost effective technology upgrades enabling battlefield vehicles to maintain operational advantage over competitors in combat.
The SAVE-720 is designed for insertion into the SAVE (Standardized A-kit Envelope), revised with the 2” x 4” top rear keep out area. It allows space within the envelop for cables, shock and vibration and mounting plate. It meets SAVE dimensional requirements: 9.3” (H), 15.9 (W) x 16.1" (D)
The 7 payload and 2 power supply backplane enables use of commonly applied SOSA aligned modules and their associated profiles. It is designed specifically to accommodate payload combinations in SAVE deployment chassis including Ethernet switch, I/O intensive SBC, radial clock and compute intensive full aperture FPGA/RF cards. Five backplane slots include VITA 67.3 full width apertures for extensive RF signal connectivity.
The lightweight aluminum alloy chassis is sealed to provide ingress and EMI protection. Direct connect backplane and I/O panel ensures optimal signal integrity, eliminates most cabling, improves shock and vibration performance and simplifies maintenance procedures.
LCR can support successful project realization from initial concept, custom backplane profile design, I/O testing and environmental testing all the way through to manufacture, module integration and functional test of the final deployed chassis.
For SAVE development activities, LCR offers the DK3-SAVE chassis. The DK3-SAVE is a full featured development chassis intended for use in the test and integration activities leading up to the design of SAVE systems intended for deployment.
LCR Embedded Systems –
Serving critical defense programs for over 35 years
Ą SAVE compliant for Army ground vehicles
Ą Supports SOSA aligned module profiles
Ą I/O complement meets SAVE requirements
Ą 7 payload and 2 power supply 3U VPX backplane
Ą Complies with SAVE SWaP, mounting and I/O requirements
Ą Intended for integrated C5ISR applications including CMFF (CMOSS Mounted Form Factor) payloads
Ą Backplane supports switch, A-PNT, SBC and RF SOSA aligned modules
Ą Rugged bolt together construction
VME and VME64x, CompactPCI, or PXI chassis are available in many configurations from 1U to 12U, 2 to 21 slots, with many power options up to 1,200 watts. Dual hot-swap is available in AC or DC versions. We have in-house design, manufacturing capabilities, and in-process controls. All Vector chassis and backplanes are manufactured in the USA and are available with custom modifications and the shortest lead times in the industry.
Series 2370 chassis offer the lowest profile per slot. Cards are inserted horizontally from the front, and 80mm rear I/O backplane slot configuration is also available. Chassis are available from 1U, 2 slots up to 7U, 12 slots for VME, CompactPCI, or PXI. All chassis are IEEE 1101.10/11 compliant with hot-swap, plug-in AC or DC power options.
Our Series 400 enclosures feature side-filtered air intake and rear exhaust for up to 21 vertical cards. Options include hot-swap, plug-in AC or DC power, and system voltage/temperature monitor. Embedded power supplies are available up to 1,200 watts.
Series 790 is MIL-STD-461D/E compliant and certified, economical, and lighter weight than most enclosures available today. It is available in 3U, 4U, and 5U models up to 7 horizontal slots.
All Vector chassis are available for custom modification in the shortest time frame. Many factory paint colors are available and can be specified with Federal Standard or RAL numbers.
Ą Most rack accessories ship from stock
Ą Modified ‘standards’ and customization are our specialty
Ą Card sizes from 3U x 160mm to 9U x 400mm
Ą System monitoring option (CMM)
Ą AC or DC power input
Ą Power options up to 1,200 watts
For more detailed product information, please visit www.vectorelect.com or call 1-800-423-5659 and discuss your application with a Vector representative.
Purpose-built for extreme, high-bandwidth networking and interface applications, the V1153 XMC card will withstand harsh environments while staying within your SWaP and budget requirements.
Despite the challenges posed to engineering architects to create boards with higher port density, bandwidth, and processing power for radar, signal intelligence, remote sensing, medical imaging, and embedded telecommunications systems, New Wave DV’s V1153 XMC card satisfies these requirements while dramatically increasing bandwidth and providing plenty of FPGA resources to process data and support PCIe host connectivity.
Supporting temperature ranges from -40°C to +85°C and complying with VITA 20 standards, each V1153 XMC card delivers a reliable, long-lasting solution for your rugged embedded needs.
Ą Twelve 1G to 25G optical lanes to MPO front panel I/O or VITA 66 optical I/O
Ą Xilinx® Virtex®/Kintex® UltraScale®+ FPGA
Ą Supports up to PCIe Gen3 x 16
Ą PPS time synchronization with µSec resolution
Ą Thermal sensors for monitoring card temperature
Ą Robust FPGA development framework
Ą Advanced APIs that support multi-core and multi-processor architectures
https://newwavedv.com/products/fpga-interface-cards/pmc-xmc/v1153-12-port-rugged-xmc-fpga-card/
UltraScale FPGA
The XEM8350 FPGA development module with AMD-Xilinx Kintex™ UltraScale FPGA module offers a turnkey dual Super-Speed USB 3.0 host interface using the Opal Kelly FrontPanel® SDK. System integrators can build fully-operational prototype and production designs quickly by integrating this device into their product. Manufacturers of high-speed devices such as JESD-204B data acquisition devices can launch fully-functional evaluation systems without the costly design and maintenance of an evaluation platform.
As an industry first, the XEM8350 features two fully-independent Super-Speed USB 3.0 ports for high-bandwidth applications requiring duplex operation or over 650 MB/s bandwidth. The FrontPanel SDK includes a multi-platform API (Windows, macOS, and Linux) and very low logic utilization on the FPGA. Memory-hungry applications enjoy access to 4 GiB of on-board DDR4 memory with a 64-bit wide data bus and ECC.
Typical applications include:
• LIDAR and RADAR
• Video / Image Capture
• Software-Defined Radio (SDR)
• 5G Systems
• Remote Sensing
• Photonics
• Advanced Metrology
• Data Ingestion Acceleration
Ą Dual SuperSpeed USB 3.0 ports for high-bandwidth data transfer
Ą AMD Kintex UltraScale XCKU060 or XCKU115
Ą 4 GiB DDR4 (72-bit with ECC)
Ą Over 330 I/O pins on three Samtec QTH connectors
Ą 28 multi-gigabit transceivers
Ą Compact form factor (145mm x 85mm)
Ą On-board programmable clock oscillator
The XEM8310-AU25P development module with AMD-Xilinx Artix™ UltraScale+ FPGA offers integrators a turnkey solution with fast (340+ MB/s) USB 3.0 host interface using the Opal Kelly FrontPanel® SDK. Designed for both prototype / proof-of-concept and production deployment, the highly-integrated device includes on-board power supplies, DDR4 memory, and support circuitry in a compact form factor with commercial-off-the-shelf (COTS) availability.
The FrontPanel SDK greatly simplifies hardware / software communication with a comprehensive and easy-to-use API and broad operating system and language support. Opal Kelly SOMs reduce time-to-market, allow teams to focus on their core competencies, and simplify supply chains. Opal Kelly has been ISO 9001:2015 certified since 2019.
Typical applications include:
• ●Data acquisition
• ●Test & measurement, instrumentation, and control
• ●Machine vision / machine learning / AI
• ●Software-defined radio (SDR)
• ●Digital communications and networking
• ●Data security
The Lauterbach TRACE32 Debugger now also operates as a TCF agent. This makes it possible to use the Wind River Workbench or the Eclipse debugger as an IDE and a TRACE32 debugger as a debugging back-end tool.
The Target Communication Framework (TCF) was developed by the Eclipse Foundation as a protocol framework with the goal of defining a uniform debugging communication protocol between an IDE and a target system.
TCF defines a series of standard services. At the same time, the framework is open for the definition of proprietary services.
After the TRACE32 software is started as a TCF agent, it provides its services to the Wind River Workbench or the Eclipse debugger via TCP/IP.
Using its TCF services, the TRACE32 debugger can now provide an open communication interface for debugging with Eclipse or the WindRiver Workbench for all processor architectures and compilers supported by TRACE32.
Ą AMD-Xilinx Artix UltraScale+ XCAU25P-2FFVB676E
Ą SuperSpeed USB 3.0 port for high-bandwidth data transfer
Ą 2 GiB DDR4 (32-bit data interface), 32 MiB QSPI FPGA flash
Ą 149 FPGA fabric I/O and 12 gigabit transceiver lanes (16.375 Gbps)
Ą Compact form factor (100mm x 70mm)
Ą Full FrontPanel SDK and API support
Ą TRACE32 operates as TCF agent
Ą Support for various launch mechanisms
Ą Support for all debug relevant TCF services
Ą Synchronized debugging between TRACE32 and TCF C/C++ Debugger in Wind River Workbenchd
Ą Support for multiple projects (multicore)
Ą Applicable for all processor architectures supported by TRACE32
Ą Based on Target Communication Framework (TCF)
Lauterbach TRACE32 Debugger for Intel x86/x64:
In January of this year, Lauterbach introduced the new CombiProbe Whisker MIPI60-Cv2. The TRACE32 CombiProbe and TRACE32 QuadProbe now offer the same debug features for the Converged Intel® MIPI60 connector:
• Standard JTAG, Intel® debug hooks with Pmode, and I2C bus
• Merged debug ports (two JTAG chains)
• Intel® Survivability features (threshold, slew rate, ...)
However, these debug tools have different areas of application. The TRACE32 QuadProbe, which is expressly designed for server processors, is a dedicated debug tool that enables SMP debugging of hundreds of threads on targets with up to four debug connectors.
The TRACE32 CombiProbe with the MIPI60-Cv2 Whisker, designed for client as well as mobile device processors, can capture and evaluate system trace data in addition to its enhanced debugging features.
Trace capabilities include support of one 4-bit and one 8-bit trace port with nominal bandwidth.
The TRACE32 CombiProbe with the DCI OOB Whisker is specially designed for debugging and tracing of form factor devices without debug connectors. If the chip contains a DCI Manager, the target and the debugger can exchange debug and trace messages directly via the USB3 interface. The DCI protocol used to exchange messages supports standard JTAG and Intel® debug hooks as well as trace messages for recording system trace information.
Ą CombiProbe MIPI60-Cv2 provides debug and system trace capability
Ą Support for standard JTAG, debug HOOKs and I2C bus
Ą Support for merged debug ports (two JTAG chains per debug connector)
Ą Support for survivability features (threshold, slew rate, etc.)
Ą Support for system trace port with up to 8 trace data channels
Ą 128 MByte of trace memory
Ą SMP debugging (including hyperthreading)
Ą AMP debugging with other architectures
Ą BIOS/UEFI debugging with tailor-made GUI for all UEFI phases
Ą Linux- and Windows-aware debugging
Ą Hypervisor debugging
Lauterbach provides support for seamless debugging of hypervisor-based systems. The introduction of the unique Lauterbach Machine ID allows the debugger to identify any virtual machine in the system. This gives the debugger full visibility of the context of all active and inactive virtual machines and provides a supporting framework to load OS specific awarenesses for each virtual machine.
The most important objective of the TRACE32 hypervisor-awareness is a seamless debugging of the overall system. This means that when the system has stopped at a breakpoint, one can check and change the current state of every single process, all VMs, plus the current state of the hypervisor and of the real hardware platform.
The TRACE32 hypervisor-awareness provides the debugger with all of the hypervisor’s information running on the hardware platform. After the OS-awareness is loaded for each guest/VM the debugger can display an overview of the overall system.
TRACE32 assigns each VM a number, the machine ID (mid column). The machine ID is a unique identifier that is used by TRACE32 and appears as an address extension; a concept already familiar to TRACE32 users.
The Global Task List represents the heart of the TRACE32 hypervisor-aware debugging. It lists all tasks/processes/threads of the guest OSes and the hypervisor. TRACE32 can visualize the context of any task in its GUI. Just double-click to on the task name.
The TRACE32 CORE List window displays in detail what is currently running on the individual cores of an SMP system.
The TRACE32 GUI visualizes the context of the current core/task by a double-click on the task name in the TRACE32 Global Task List.
TRACE32 allows the visualisation of any task, even if its VM is currently not active.
Since Lauterbach has systematically extended the well known concepts for OS-aware debugging to hypervisor debugging, it will be easy for TRACE32 users to get started with just a little practice.
Ą Seamless debugging of the total system in stop-mode
Ą Hypervisor-awareness as a loadable debug extension is provided by Lauterbach
Ą Machine ID allows the user to uniquely identify any virtual machine in the system
Ą Machine ID provides full visibility of context of active and inactive virtual machines
Ą OS-awareness can be loaded for each virtual machine
Chassis Manager / System on Module is SOSA™ aligned
The VITA 46.11-aligned WILD™ VPX Chassis Manager / SoM (WABGM0/2) enable critical chassis control, maintenance, and security functions, were developed in alignment with SOSA Technical Standard 1.0, and offer commercial-off-theshelf (COTS) availability.
These are highly-integrated modules. They provide access to plug in card (PIC) JTAG and Maintenance ports, CLK1 usage via on-board Zynq FPGA, network functions, and some optional advanced security functions. For security, the units implement security signal interfaces and a Xilinx UltraScale+ Zynq MPSoC and latest Microsemi PolarFire FPGA, which can be end-user modified with the optional BSP.
Ą Capability: Provides control and access to Plug-In Card JTAG and Maintenance ports, CLK1 usage, network functions & optional advanced security functions
Ą FPGAs: Xilinx UltraScale+™ Zynq (ZU5EG or ZU11EG) & MicroSemi PolarFire
Ą Mounting: Directly on backplane, or via 3U or 6U VPX plug-in carrier card
Ą Power: Only requires 3.3V
Ą Optional BSP: For customizing Zynq PS & PL for security
Ą Standards: VITA 46.11, SOSA 1.0 & MIL-STD-1553
Ą Availability: Commercial off-the-shelf
www.annapmicro.com/product-category/chassis-and-backplane-accessories/ Annapolis Micro Systems, Inc.
marketing@annapmicro.com
410-841-2514
www.annapmicro.com
As an AS6496-compliant distributor and licensed manufacturer, Rochester Electronics offers Military-Grade semiconductor and package solutions, even after the original OCMs have discontinued them.
Rochester stocks millions of military-grade components in our daily inventory, including thousands of distinct part numbers. In addition, Rochester’s in-house high-reliability hermetic assembly line offers a full complement of package styles including Ceramic DIP, Side Brazed DIP, Flat Pack, CQFP, PGA, Ceramic Leadless Chip Carrier, and Metal Can. This variety allows for the continued manufacture of previously obsolete components, all manufactured in partnership with the original OCM to provide a 100% authorized and guaranteed solution.
Rochester can supply a custom flow, built to match the needs of source-controlled drawings based on our commercial and industrial inventory. Our extensive in-house qualification and test facilities ensure complete risk-free sourcing of components in compliance with industry standards. Rochester is a QML manufacturer certified by DLA Land and Maritime to MIL-PRF-38535, offering Class Q and Class V microcircuits for Military and Aerospace applications.
Customers can leverage Rochester’s vast test and design Engineering experience to keep systems running. Rochester can help with suitable alternatives (grades, speeds, finishes, packages) and the creation of additional testing parameters to provide the customer with the evidence needed to qualify these alternate solutions.
We can also support fundamental design changes, such as the replacement of obsolete key components with ASIC solutions. The possibility exists in these cases to transition to an ASIC not only identical in terms of fit-form-function but with no software changes required and no errata. This means that Aerospace DO-254 requalifications, even for safety-critical (DAL-A) applications, can be greatly simplified with minor changes.
Rochester Electronics offers the most comprehensive Stock – Build –Redesign services available for Military and Aerospace customers.
Ą Registered to manufacture ITAR products
Ą QML per MIL-PRF-38535
Ą DLA certified Hermetic Assembly, Electrical Test, Burn-In and Reliability Lab to MIL-STD-883
Ą Class Q (Class B) & Class V (Space) products
Ą ISO9001: 2015 Certification
Ą AS9120B:2016
Ą QSLD DLA Certified
Ą TAPA FSR-A: 2017
Bandwidth or Latency-optimized
Annapolis WILDSTAR™ Versal Premium Boards are the highest performing OpenVPX COTS FPGA Processing Baseboards on the market, with capability for 100Gb Ethernet over copper on the VPX backplane. Blind mate optical and/or RF (VITA 66/67) is also available. All 100GbE boards are VITA 65-compliant and align with SOSA Technical Standard 1.0.
High Performance
These SOSA aligned Plug-In Cards (PIC) integrate the latest Versal Premium FPGAs up to VP2502 with 472 AI Engines. AMD’s new Versal ACAP FPGAs are engineered for processing-intensive applications like Radar, EW, and SIGINT.
High-performance digitization is via Mezzanine Card(s) connected to FMC+ based I/O site(s). Choose between a JESD-based (bandwidth optimized) or LVDS-based (latency optimized) approach.
Rugged
Annapolis rugged FPGA boards are designed from the ground up to perform at the highest levels in the harshest environments. They are designed and tested for reliability, utilizing high performance air, conduction, or air-flow-through cooling for thermal control.
All Annapolis products are engineered and manufactured under one roof in the United States. This co-location of engineering and manufacturing allows for more aggressive design, and better quality control and production flexibility.
Ą General Features
• Up to two AMD Xilinx Versal Premium FPGAs
• Multiple levels of hardware and software security
• A Full Board Support Package for fast and easy Application Development
� BSP options include traditional RTL and new DFX RTL and Vitis™ paths
Ą Mezzanine I/O
• Optimized for VITA 66/67 interfaces
• Based on FMC+
• Available options:
� Jariet Electra-MA: 2TX (64GSps)/2RX (64GSps)
� Xilinx RFSoC: 2TX (5GSps)/8RX (5GSps)
� Xilinx RFSoC: 4TX (5GSps)/4RX (5GSps)
� TI 2TX (3.2 GSps)/2RX (3.2 GSps)
� Others covered under NDA
Ą Mechanical and Environmental
• Air, conduction, or AFT cooled: -55°C to +85°C Operating
• Available in extended temperature grades
• Hot swappable for air-cooled variants
• Only requires +12V and +3.3VAUX from backplane
WILDSTAR Boards
www.annapmicro.com/versal-products/
Direct RF sampling is transformative for Signal Acquisition and Signal Processing. Direct RF data converters operate directly at the antenna frequency, reducing latency and eliminating the need for intermediate frequency stages. Also, Direct RF conversion can instantaneously tune across a very wide frequency span – from 0.1 to 36 GHz. Now you can directly digitize and process wideband signals, simplifying system architecture and enabling new EW, SIGINT, and spectrum processing capabilities.
Annapolis is now offering the lowest latency and highest bandwidth 64 GSps Direct RF solutions on the market:
• WILD FMC+ DME1 (top right) – an OpenVPX Mezz Card
• WILDSTAR 3AE1 (bottom right) – a 3U OpenVPX Baseboard
• WILDSTAR SAF1 (below) – a Small Form Factor Module
Ą WILDSTAR SAF1 Small Form Factor Module
• Use as a single standalone unit or dual-mounted on a 3U VPX Baseboard
• One Intel Agilex Direct RF-Series AGRW014 FPGA
• ADC: 4 Channel, 64 GS/s, 10 bit Resolution
• DAC: 4 Channel, 64 GS/s, 10 bit Resolution
• Mates with modular RF and digital I/O cards
Ą WILD FMC+ DME1 ADC & DAC Mezz (photo above)
• Pair one with a 3U Baseboard or two with a 6U Baseboard
• One Jariet Technologies Electra-MA Transceiver
• ADC: 2 Channel, 40-64 GS/s, 10 bit Resolution
• DAC: 2 Channel, 40-64 GS/s, 10 bit Resolution
• Usable Analog Bandwidth: 36GHz
• Maximum Instantaneous Bandwidth: 6.4GHz
• Run Time Selectable ADC Decimation: 8-1024x
• JESD204B/C interface with 16 lanes up to 30Gbps
• Developed in alignment with SOSA™ 1.0
The 3AE1 provides VITA 67 backplane RF support
Ą WILDSTAR 3AE1 3U OpenVPX FPGA Processor
• SOSA aligned 3U VPX Plug-In Card
• One or two Intel Agilex Direct RF-Series AGRW014 FPGAs
• ADC: 8 Channel, 64 GS/s, 10 bit Resolution
• DAC: 8 Channel, 64 GS/s, 10 bit Resolution
• Supports Analog Interface Cards for front-end personalization
• Air, Conduction, or Air-Flow-Through cooled
• Developed in alignment with SOSA™ 1.0
Contact
Chassis/Switches Support 8x or 4x Gen4 PCIe, Plus Eight LVDS or Dual 100Gb Ethernet
The WILD100™ 13-Slot 3U OpenVPX Chassis (WC31DH) is a COTS 19" rackmount Chassis, Backplane, and Chassis Manager. It includes two HD Switch slots that feature high-density VITA 91 connectors with double the available density, up to 64 lanes of Ethernet or PCIe or 128 LVDS pairs. The two HD switch slots allow the chassis to handle all Data and Control Plane Ethernet via one slot, with the second switch slot dedicated to the expansion plane – Ethernet, PCIe and/or LVDS. This enables deployment for low latency jamming or radar applications.
VITA 91 high-density connectors allow for a completely switched backplane. This enables all the slots to be on the same nonblocking Ethernet switch instead of two switches chained together, and it facilitates a flexible, programmable expansion plane. This supports either 8x or 4x Gen 4 PCIe, plus eight LVDS or dual 100Gb Ethernet.
Optional Switches, FPGA Boards, Storage Cards, VITA blocks and cables are also available. The following Switches include the same high density VITA 91 connectivity:
• WILDSTAR 3E20 3U Ethernet Switch – Up to fourteen 40/100GbE ports
• WILDSTAR 3P20 3U PCIe/LVDS Switch – Up to 128 LVDS or eight 8x PCIe interfaces
• WILDSTAR 3H20 3U Combo Switch – Combines 40/100GbE, Gen4 PCIe and/or LVDS
Ą Chassis & Backplane Features
• Front-loading, air-cooled Chassis with conduction-cooled slots
• Thirteen 3U OpenVPX Slots
� Eight 14.6.11 Primary RF/Compute Intensive profile
� Two HD Switch profiles
� One 14.9.2 Timing profile
� Two 12V-only VITA 62 Power Supply Slots
• Input power is 28VDC per MIL-STD-704F
� 25 Gbps Line Rates on Data and Expansion Planes
� 25/40/100Gb Ethernet
� SDR/DDR/QDR/EDR InfiniBand
� Gen 3/4 PCI Express
� Custom protocols up to 25Gbps per lane
• SOSA™-aligned Backplane profiles
� Payload Profile: SLT3-PAY-1F1U1S1S1U1U2F1H-14.6.11-n
� Timing Profile: SLT3x-TIM-2S1U22S1U2U1H-14.9.2
• VITA 66.5C and VITA 67.3C for payload slots
• Integrated ultra-low skew AUXCLK/REFCLK radial distribution
• Support for CLK1 direct connection between payload slots to Chassis Manager FPGA
• Optional WAB3X0 for two additional 100GbE optical connections
Ą Chassis Manager
• Optimized SOSA aligned and VITA 46.11 compliant WABGM2
• Plugged directly onto backplane, or cabled
• Xilinx UltraScale+ ZU11EG MPSoC running Linux for CHmC
� Processing Subsystem (PS)
� Programmable Logic subsystem (PL)
• Integrated JTAG access/control from chassis manager to each slot
� External JTAG connection with SW selectable multiplexing from each slot
� Xilinx JTAG over ethernet via Chassis Manager
• VPX slot maintenance ports (UARTs) aggregation
• Includes three 10/100/1000 BASE-T external connections which are bridgeable to switch slots
• Supports dual redundant MIL-STD-1553 interfaces
• Optional advanced security features
Ą Application Development
• Standard Chassis Manager support delivered with all systems
• Optional Full Board Support Package for Chassis Manager
� Enables customization if needed of Zynq PS and PL
� Provides fast and robust HDL-based application development environment
www.annapmicro.com/products/wc31dh/
Atrenne, a Celestica company, offers a wide range of high-performance backplanes, with 6U, 3U and hybrid 3U/6U models available. Our Gen-4/5 OpenVPX backplanes are part of an innovative product family that enables end-to-end solutions for 64/100 Gigabit systems.
Designed to the demanding signal integrity requirements of PCIe Gen4 and 100GbE (100GBASE-KR4), these high-performance Gen-4/5 backplanes offer the highest signal integrity in the industry and are typically used in air-cooled or conduction-cooled development chassis. Atrenne can also design application-specific configurations to meet your individual requirements.
Ą High performance 25 Gbaud Gen-4/5 backplanes compatible with 100 GbE (100GBASE-KR4) and PCI Express® (PCIe) Gen-4 (16 Gbaud) on OpenVPX data plane and expansion plane fabrics
Ą Built with MEGTRON 6 – Ultra-low Loss, Highly Heat Resistant Circuit Board Materials
Ą Refined VPX connector with smaller press-fit pins, the VITA 46 Multigig RT-3 is fully compatible and interoperable with the original VPX connectors, providing superior signal integrity performance
Ą VITA 65 OpenVPX™ compliant backplanes
Ą VITA 46/VITA 48 VPX REDI™-compliant with VITA 46.30 compliant RT3 connectors
Ą VITA 46.10 RTM connectors
Ą Provisions for mechanical stops to prevent misinsertion of payload cards
Ą Stiffeners placed every other slot to ensure backplane rigidity
Ą Optional rear transition connectors
Ą Keying and alignment per VITA 65 and VITA 46
Ą Durability: mating and unmating for 200 cycles
NDR374
The NDR374 digital tuner is a 4-channel, superheterodyne downconverter that covers RF signals from 2 MHz to 8 GHz. It is a rugged 3U conduction cooled VPX module, per VITA 46/48/65/67.
The NDR374 digital tuner is designed as a 3U open architecture version of the existing NDR358 tuner to include RF performance, command set and multiple DSP-based modes of operation (the NDR374 enables efficient system integration for existing NDR358 users).
The tuner supports both independent and phase coherent tuning and two units can support 8-Channel coherent operation. Integrated high dynamic range 16-bit Analog-to-Digital converters (ADC’s) are utilized to digitize an 125 MHz wide IF at 368 Msps sample rate.
https:/cyberradiosolutions.com/products/VPX.php
Dawn VPX Cube Enclosures
Rugged, conduction cooled 1 to 6 slot 3U VPX with 6 channel intelligent 400 Watt power supply. Designed to MIL-STD-810E, DO-160E and MIL-STD-461E. For all rugged environments: Air, Land, and Sea.
Small and extremely rugged, cold plate base coupled, conduction cooled enclosure. Full environmental sealing ensures reliable operation in any environment.
Embedded RuSH Technology monitors Power Supply voltage and current on all 6-channels, plus temperature, and (optionally) humidity. Flexible, Dawn patented, “Eye”-tested backplane fabric and I/O mapping supports any application. Backplane is configurable to meet any data plane connection fabric.
Ą 4 channel 3U OpenVPX wideband digital tuner
Ą Aligned with the SOSA and MORA™ Technical Standards
Ą 125 MHz BW per channel
Ą Fast Scan Control Interface
Ą Supports multiple existing NDR358 DSP-based modes of operation (contact for details)
Ą Ideal packaging solution for UAV applications.
Ą 1 to 6 Slots of 3U VPX on 1" pitch (OpenVPX Ready).
Ą Integrated intelligent Power Supply provides up to 400 Watts of 6-channel power.
Ą Embedded RuSH technology actively monitors voltage, current and temperature and talks over system management bus using I2C.
Ą Performance “Eye”-tested and Dawn patented Fabric Mapping Modules allow customization of data plane fabric.
Ą High-bandwidth, differential shielded PCI Express type Rigid I/O panel interface eliminates wiring challenges.
Ą Dawn patented backplane I/O mapping modules enable PMC/XMC to I/O customization.
www.dawnvme.com/product-category/vpx-cube-enclosures/
www.dawnvme.com
Elma’s comprehensive line of backplanes aligned to the Sensor Open Systems Architecture™ (SOSA) Technical Standard enable complex, high speed signal processing in rugged environments. They provide the foundation for high-performance mission-critical systems requiring lower lifecycle costs and rapid technology insertion.
The 3U and 6U backplanes enable complex, high speed signal processing with the latest optical fiber and RF connectivity. They offer support for precision network timing (PNT), and slot profiles for SBCs, switches, radial clock(s) and expansion.
The backplanes support high-speed signals on all data paths and RF and optical connectors. Developers can use the backplanes as configured or work with Elma to identify specific profile configuration needs.
www.elma.com
Ą Field-proven designs in slot configurations from 2 to 14 slots aligned to SOSA
Ą Designs support VITA 66 & 67 optical & RF apertures for connectivity
Ą Support for all slot profile options support critical multimission applications
Ą Support for dual domain Ethernet switch 1/10/40 & 25/100
Ą IPMC chassis management support
Ą PNT timing support
Ą Support the DoD's MOSA initiative as well as CMOSS
V6061 3U VPX Versal® ASoC FPGA + Ethernet Offload Optical I/O Module
The V6061 is a next-generation, high-performance embedded computing 3U VPX module featuring the Xilinx® Versal® Adaptive System-on-Chip (ASoC), NVIDIA® Mellanox® ConnectX®-5 network interface device, rugged optical and electrical I/O, and SOSA™ aligned profile options. This dense combination of devices and technologies maximizes the effectiveness of the deployed applications and algorithms while eliminating design efforts required to establish truly high-bandwidth and low-latency Ethernet, PCIe controllers, PCIe switches, efficient DMA engines, or low overhead software drivers. The V6061 is designed for applications requiring a combination of high-speed data interfaces, network protocol offloads, onboard processing, and data distribution to adjacent processing resources. With its proven performance in 10/25/40/50/100Gbs Ethernet applications, the V6061 benefits sensor interfacing, data processing and distribution, and FPGA co-processing in systems such as radar, signals intelligence, electronic warfare, video, storage, medical imaging, and embedded communication systems. The V6061 includes hardware offloads for UDP, TCP, RoCE v2, DPDK, GPUDirect, NVMEoF, among many other protocol stacks, and excels at high-bandwidth interface applications where data can be processed locally and/or distributed efficiently across the VPX backplane. The V6061 is a standout sensor interface and heterogeneous computing solution whether used standalone or adjacent to other processing elements.
Ą Xilinx® Versal® ASoC (FPGA): VM1502/ VM1802/VC1902
Ą NVIDIA® Mellanox® ConnectX®-5 Network Interface Device Hardware offloads for UDP, TCP, RoCE v2, DPDK, GPUDirect, NVMEoF, + more
Ą Up to eight (8) 1G to 25G optical ports via MPO front panel I/O or VITA 66 optical backplane I/O
Ą 2 banks of 4GB up to 1866MHz LPDDR4
SDRAM
Ą PCIe Gen3/Gen4 support
Ą Onboard embedded PCIe Switch device
Ą Advanced APIs that support multi-core and multi-processor architectures
https://newwavedv.com/products/fpga-interface-cards/vpx-cards/v6061-3u-vpx-versal-asoc-fpga-ethernet-offload-optical-io-module/ New Wave Design and Verification
www.newwavedv.com
info@newwavedv.com
952-224-9201
www.linkedin.com/company/new-wave-design-and-verification
The VPI-250-eSSDC 3U VPX NVMe SSD is designed to align with the Sensor Open Systems Architecture™ (SOSA) Technical Standard. It delivers extremely high performance via a Fat Pipe (PCIe x4). Designed from the ground up to remove legacy layers of hard drive interfaces such as SAS and SATA, it takes full advantage of the speed and parallelism of solid state nonvolatile memory. Streamlined efficient queuing protocol combined with an optimized command set register interface enables low latency and high performance. Data is delivered fast and efficiently with minimal burden on the host CPU.
The VP1-250-eSSDC optionally supports TCG compliant AES-256, CSfC and FIPS 140-2 validated encryption and military grade data elimination as well as hardware and/or software write protect.
The conduction cooled VP1-250-eSSDC is also available in a rugged air-cooled configuration.
Phoenix International is an AS9100D/ISO 9001-2015 certified, NIST SP 800-171 compliant Small Business.
Ą Capacities up to 30TB
Ą Streamlined protocol with efficient queuing mechanism to scale for multi-core CPUs
Ą Supports 12V-only and +3.3 AUX
Ą Optional TCG compliant AES-256, CSfC and FIPS-140-2 Validated Encryption
Ą Military grade data elimination
Ą Operating 100G shock, 16.3G vibration
Ą Operational Temperature from -40° to +85° C
https://www.phenxint.com/portfolio/rugged-open-vpx-nvme-ssd-module/
SOSA™ Aligned Solutions
Pixus offers a full ecosystem of SOSA aligned products from backplanes, chassis platforms, and chassis managers as well as our 3rd party partners for SOSA aligned plug in cards and PSUs. The company has a wide range of SOSA slot profile backplane combinations and enclosure options in various cooling formats. This includes airflow over conduction-cooled fins, Air Flow By, Air Flow Through, and liquid cooling. The company has developed a wide range of backplane at 100GbE and PCIe Gen4 speeds as well as customized designs at higher data rates. The versatile Pixus SOSA aligned mezzanine based chassis manager fits behind a backplane without losing a slot. It features 100% USA based software/ firmware. Contact Pixus today for your SOSA/OpenVPX solution! Contact Pixus to discuss your application today!
Ą SOSA Aligned OpenVPX chassis in ATR, MIL rugged rack-mount, and lab/test formats
Ą Backplane design expertise up to and above 100GbE speeds, RT3 connector
Ą SOSA Aligned SlotSaver mezzanine-based VPX chassis manager, Tier 3+, 100% US based software/firmware
Ą Various advanced cooling options for chassis platforms
Ą Experienced in advanced and creative design requirements
www.pixustechnologies.com Pixus
Enclosures Cases Subracks Backplanes Chassis Integrated Systems Components
Add data storage to your VPX system!
Red Rock Technologies provides a range of 3U VPX SSD products using COTS NVME and SATA SSDs.
Ą Capacities up to 32TB (0 to 70C) and 20TB (-40 to 85C)
Ą NVME transfer rates of 3500MB (0-70C), 1500MB/S (-40 to 85C)
Ą Conduction and air-cooled options
Ą Removable SSD module rated for 100,000 mating cycles
Ą TLC, MLC, pSLC NAND for NVME and TLC, MLC, SLC for SATA
Ą Military erase, FIPS140-2, FIPS197, TCG Opal options
Ą 6U VPX SSD modules also available
Red Rock Technologies www.redrocktech.com
XMC with Removable SSD module
Red Rock Technologies releases new XMC product that provides up to 16TB of removable data storage in a standard XMC slot. It can support one or two COTS
M.2 NVME SSDs; 2260, 2280, or 22110.
Designed for frequent SSD removal with SSD module connectors rated for 100,000 mating cycles.
https://www.redrocktech.com/products/pmcxmc
Red Rock Technologies www.redrocktech.com
https://www.redrocktech.com/products/vpx
contactus@redrocktech.com
www.linkedin.com/company/red-rock-tech/
480-483-3777
Ą Eliminates need for extra VPX slot for data storage
Ą Capacities up to 16TB (0 to 70C) and 8TB (-40 to 85C)
Ą Transfer rates of 3000 MB/s (0-70C) and 1500MB/S (-40 to 85C)
Ą Removable SSD module rated for 100,000 mating cycles
Ą COTS NVME SSDs with TLC, MLC, pSLC NAND
Ą Military erase, FIPS140-2, FIPS197, TCG Opal options
contactus@redrocktech.com
www.linkedin.com/company/red-rock-tech/
480-483-3777
SMPM Female VITA 67.3 to 2.92mm
Male 18" .085 Cable Assembly
Amphenol SV Microwave’s SMPM Female VITA 67.3 to 2.92mm
Male 18" Cable Assembly for .085 Cable is a high-density, highperformance, fixed-length cable assembly that fits into VITA 67.3 blocks and attaches to the chassis I/O connector.
All of SV’s VITA 67 RF cable assemblies provide ease of assembly or disassembly to daughter card and backplane modules.
Floating SMPM coaxial pins ensure excellent RF performance in any mating condition.
VITA 67 RF cable assemblies are ideal for aerospace and defense, ground base station and communication systems, avionics, radar systems, and air transport rack applications.
Ą VITA 67.3 Backplane Cable Assembly
Ą SMPM RF Series
Ą Aligned to the SOSA™ Technical Standard
Ą Phase/delay matched sets optional
Ą Isolation: ≥ 90 dB at 40.0 GHz
Ą Quick Test and Measurement
Ą In Stock Now Through Distribution
https://svmicrowave.com/smpm-female-vita-673-to-292mm-male-18-cable-assembly-for-085-cable
RTD’s LAN24550 is a dual 10 Gbit/s Copper Ethernet Module utilizing Intel’s X550 10 GbE controller. The X550-AT2 Ethernet controller is a second-generation 10GBASE-T controller with integrated MAC and PHY. It provides backward compatibility with existing 1000BASE-T, simplifying the migration to 10 GbE, and provides iSCSI, FCoE, virtualization, and Flexible Port Partitioning (FPP).
10 Gigabit – using stacked switch configurations – can introduce an increased use of redundancy as Active-Active LACP port teaming. Multiple ports grouped into one logical link improves speed and availability.
PCIe/104 and PCI/104-Express stackable bus structures
Intel X550 10 Gigabit Ethernet Controller
2 Independent 10 Gb/s Twisted Pair Ethernet Connections with Integrated MAC and PHY
RJ-45 connectors with integrated magnetics and Link/Activity indicator LEDs
10/1 GbE data rate per port: support for vision systems, network and server virtualization, and LAN and SAN flexibility
-20 to +70°C standard operating temperature
Intel® Xeon High-Performance SBC
The CMX34KB is an advanced PC/104 single board computer with a PCIe/104 stackable bus structure. As a part of RTD’s PCI Express offering, this CPU based on Intel’s 7th generation Xeon processor (formerly codenamed Kaby Lake) is exceptionally suited for intelligent systems requiring high performance in harsh thermal conditions. TPM 2.0 (Trusted Platform Module) included for hardware-based cryptography. The surface-mount Type 2 PCI Express connectors enable users to stack multiple peripheral modules above and below the CPU. The 60GB onboard industrial grade flash drive makes this CPU Windows 10 ready.
Ą PCIe/104 stackable bus structure
Ą Available in modular, rugged enclosures
Ą Intel Xeon E3-1500 Series Processors
Ą 4 Cores, 8 Threads, and up to 4.0 GHz max turbo frequency
Ą 16GB Dual-Channel DDR4 SDAM (surface-mounted)
Ą 60GB standard surface-mounted industrial-grade SATA flash drive
Ą 5 added SATA Ports, 4 PCIe x4 Links, 8 PCIe x1 Links, Dual GigE, 4 Serial Ports, 5 USB 3.0 Ports, 2 USB 2.0 Ports, DisplayPort 1.2 with Audio, Advanced Digital I/O, TPM 2.0 Encryption.
The supercomputing performance of the NVIDIA Jetson Xavier NX meets the modular, stackable versatility of PC104 in this rugged solution. RTD has brought the Jetson Xavier NX to PC104 – the industry-proven, stackable small form factor. With a comprehensive set of on-board I/O and a PCIe/104 expansion bus, users can quickly prototype and deploy complete embedded systems using verified, off-the-shelf modules.
FEATURES
Ą 21 TOPS AI Performance
Ą 384-core NVIDIA Volta™ GPU with 48 Tensor Cores
Ą 6-core NVIDIA Carmel ARM®v8.2 64-bit CPU, 6MB L2 + 4MB L3
Ą Stackable PCIe/104 Type 2 Bus Connector (down-stacking)
Ą I/O connections including DisplayPort, 2 MIPI CSI-2 Video Inputs, One Gigabit Ethernet, 2 USB 3.1 Type A, One Serial Port, One Serial Port or CAN Bus, 14 GPIO, M.2 E-key 3030 Socket (Wi-Fi, BT, NFC, GPS, GNSS, LoRa, NB-IoT), M.2 B-key 3042 Socket (WWAN/SSD), MicroSIM Card Socket, MicroSD Card Socket, Utility Port
Ą Rugged packaging available
20W to 190W low power, high efficiency 28V DC/DC power supply with MIL-STD-704 Hold-up of 50 msec integrated for 135W load.
Dawn PSC-8724 (Standard VPX version) offers following output currents:
• +5V @ 20A
• +3.3V @ 4A (& 3.3V_Aux)
(Note: Total wattage from +5V & +3.3V outputs not to exceed 100W)
• +12V @ 6A
• -12V_Aux @ 3A
• +12V_Aux @ 3A
(Note: Total wattage from +12V & +12V_Aux outputs not to exceed 72W)
Dawn VME Products
www.dawnvme.com
GPS Disciplined Oscillator/Timing-Board
RTD’s SYNC25104HR is a GPS disciplined oscillator (GPSDO) board which provides high accuracy frequency and time reference signals to PC104 systems and external devices. This board utilizes the u-blox LEA-M8F GPS receiver which locks the output signal of a low-noise, high-precision, oven-controlled crystal oscillator (OCXO) to the GNSS satellites. This product enables time synchronization between distributed systems and can be used for a variety of deployments including Time Difference of Arrival (TDOA) applications. Available in PCI/104Express and PCIe/104.
Ą -40 to +85°C operation, passively cooled
Ą GPS/GNSS disciplined precise frequency (10MHz, or any frequency) and low phase noise clock signal generation based on uBlox M8F technology with OCXO
Ą Concurrent reception of GPS/QZSS, GLONASS, BeiDou
Ą Industry leading acquisition sensitivity and single-satellite timing
Ą SBAS (WAAS, EGNOS) can be activated to reach 2.0 m position
accuracy
Ą Available in modular, rugged enclosures
Dawn PSC-8724 (SOSA VPX version) offers following output currents:
• +12V @ 10A (VS3)
• +3.3V @ 4A (& 3.3V_Aux)
(Note: Total wattage from +12V (VS3) & +3.3V outputs not to exceed 120W)
• +12V @ 6A (VS1)
• -12V_Aux @ 3A
• +12V_Aux @ 3A
(Note: Total wattage from +12V & +12V_Aux outputs not to exceed 72W) (Note: Total wattage from -12V_Aux outputs not to exceed 36W)
www.dawnvme.com/shop/power-supplies/psc-8724/
sales@dawnvme.com
800-258-DAWN (3296)
Rantec’s family of 3U VPX power supplies are designed to meet the rigorous demands of modern defense applications for airborne, land, and sea environments. Our family of 3U VPX power supplies offers versatile, reliable, and high-performance solutions for demanding defense applications. With strict adherence to industry standards, certifications, and a commitment to quality, these power supplies are a valuable choice for meeting the stringent requirements of the defense sector.
Our VITA compliant power supplies designed in alignment with the SOSA™ Technical Standard are designed with input voltages of either 28VDC or 270VDC and output power capabilities of up to 1000W. Rantec’s conformance to VITA 62.0, VITA 86.0, and SOSA standards ensure seamless integration into MOSA-aligned defense systems, make these power supplies invaluable assets in mission critical systems.
Manufactured in the USA in an AS9100 and ISO9001 certified facility, Rantec power supplies ensure the highest quality and reliability.
Ą Products designed in alignment with the SOSA™ Technical Standard conform to VITA 62.0 and VITA 86.0 standards
Ą Input voltages of 28VDC or 270VDC
Ą Output power up to 1000W
Ą Designed and tested to meet MIL-STD-461, MIL-STD-704 or MIL-STD-1275, and MIL-STD 810
Ą Designed using NAVSO P-3641A derating guidelines
Ą MTBF: 50,000 hours per MIL-HDBK-217
Ą IPMI Communication Bus per VITA 46.11
Ą Input/Output/Temperature protection
Ą Custom capabilities such as hold-up, nuclear event detection, lightning protection, inrush suppression, and more
The VSC Series is a commercial off-the-shelf DC-DC converter designed for the ‘NewSpace’ market. Performance is guaranteed through the use of radiation lot acceptance tested (RLAT) components. Our proprietary packaging creates a dual-side heatsinking option with very low outgassing.
Radiation tested to 42 MeV/mg/cm2 and guaranteed to 30 MeV/mg/cm2 for SEE and tested to 40 krad(Si) and guaranteed to 30 krad(Si) for TID in accordance with VPT’s in-house radiation hardness assurance (RHA) plan.
The VSC Series are designed for smaller satellites in low Earth orbits (LEO), launch vehicles, and NASA Class D missions where the balance of cost and guaranteed performance is critical.
To learn more about the VSC Series, please review our new app note “VSC Series Space COTS DC-DC Converters and EMI Filters” https://www.vptpower.com/data/application-notes/
Ą 5-30 W output power
Ą Single and dual output options
Ą TID: 30 krad(Si)
Ą SEE: 30 MeV/mg/cm2
Ą -55 °C to +105 °C
Ą Very low outgassing
The NDR664 is a wideband, 4 channel, 3U OpenVPX microwave transceiver that provides frequency coverage from 20 MHz to 18 GHz. The NDR664’s industry leading channel density minimizes system level SWaP. Each of the 4 channels provides a 1 GHz analog IF output with a 500 MHz instantaneous bandwidth.
The 2 tuner channels can tune both independently and phase coherently and the 2 transmit channels can tune both independently and phase coherently and multiple NDR664 units can be synchronized for phase coherent operation. The NDR664 incorporates a super-heterodyne RF conversion architecture to minimize spurious products and yield high dynamic range performance. The fully integrated synthesizers provide fast tuning, low phase noise and the tuning flexibility to choose an alternative IF input/output center frequency (an IF different than 1 GHz) if desired. The NDR664 includes an internal 100 MHz OCXO and accepts a 10 MHz reference input.
Ą 4 channel 3U OpenVPX wideband microwave Transceiver
Ą 20 MHz to 18 GHz frequency coverage
Ą Aligned with the SOSA and MORA™ Technical Standards
Ą Independent and phase coherent tuning
Ą Single slot 3U VPX form factor, 1.5 lbs., 48 W
Ą 1G/10G Ethernet command control
Ą 500 MHz BW (coming soon 2 GHz BW)
https:/cyberradiosolutions.com/products/VPX.php
Apollo MxFE is ADI’s most advanced software-defined, direct RF-sampling 20GSPS wideband mixed signal front end platform.
ADI’s newest MxFE provides a common digitizer platform to direct sample L, S, C, X, and Ku frequency bands to enable innovations in phased array radar, electronic intelligence, test and measurement, and next gen 6G wireless communications.
Developed for application versatility, the Apollo MxFE can direct sample from DC to 18GHz with an instantaneous bandwidth as high as 10GHz per channel. This monolithic 16nm CMOS device utilizes state of the art high dynamic range RF Analog-toDigital Converter (ADC) and RF Digital-to-Analog converter (DAC) cores with the best spurious free dynamic range and noise spectral density available on the market today.
Apollo MxFE eliminates the need for an RF mixing stage for X and C Band, significantly simplifying the front end. Furthermore, FPGA compute can be offloaded to Apollo MxFE’s on-chip digital signal processing (DSP). This saves size, weight, power, and cost. The DSP is all dynamically reconfigurable, enabling narrowband and wideband radar performance in a single device, without requiring recalibration. Apollo MxFE offers a highly flexible platform to enable advanced innovations in aerospace and defense, instrumentation, and communications.
Ą Four 12-bit RF ADCs with a sample rate up to 20GSPS, four 16-bit RF DACs with a sample rate up to 28GSPS, an RF input bandwidth from DC to 18GHz (Ku Band), and an instantaneous bandwidth up to 10GHz.
Ą Best SFDR and NSD to maximize X-Band Radar performance in very congested spectrum
Ą Advanced DSP Features: Real-time FFT Sniffer, a full-rate programmable FIR filter, a 128-tap complex FIR filter, fast-hopping NCOs, DDCs/DUCs, and a fractional sample rate converter.
Ą The DSP is dynamically configurable, allowing for rapid changes between narrowband and wideband profiles without taking down the JESD link.
Ą Apollo MxFE supports JESD 204B/C and a very short reach (VSR) interface.
Ą Operating junction temperature (TJ ): −40°C to +110°C
Ą Total power consumption range dependent on device configuration: 20W to 30W
This CMFF Reference Platform supports application development efforts for systems designed to meet Army hardware requirements of CMOSS (C5ISR/ EW Modular Open Suite of Standards) initiatives. An optional SAVE mounting tray is available.
At the heart of the system is Elma’s 12-slot backplane (12 payload + 2 power slots) with all profiles aligned to the Sensor Open Systems Architecture™ (SOSA) Technical Standard, with high-speed RF and optical I/O support.
The system features an integrated VITA 46.11 Tier 3 Out of Band chassis manager and meets MIL-STD-810G and MIL-STD-461E, MIL-STD-1275E environmental requirements.
Streamline your development efforts and shorten your time to deployment. Payload boards are available as part of the platform. Choose from a growing ecosystem of processor, network, network timing and power supply modules designed to align with CMOSS and aligned to the SOSA™ Technical Standard.
Ą 12-slot SOSA aligned 25/100Gb dual domain backplane (available in 7 slots)
Ą Architecture supports VICTORY and MORA implementations
Ą Rugged 3U chassis to meet CMOSS with optional SAVE tray
Ą Chassis designed to fit Standard A-Kit Vehicle Envelope (SAVE)
Ą Conduction/convection cooling approach
Ą Rugged I/O connectors & EMI filter on removable front panel
Ą Redundant VITA 62 28V DC power supplies
www.elma.com
The RPC16-NAS is a rugged, resilient all SSD storage array designed for high performance, high-capacity tactical edge data capture applications. Its rapidly removable SSD magazines enable a full magazine to be swapped out for a fresh magazine to store and move data from emerging edge environments quickly and without any tools. The RPC16 targets Mobile (Air-Sea-Ground) and fixed Expeditionary environments with its MIL-STD-810G and MIL-STD-461F compliant design.
The RPC16-NAS houses two removable magazines with up to eight SSDs each which can be quickly removed to off load data. The magazines can then be moved to separate locations and plugged into another RPC16 on any other network for further analysis. When used in conjunction with a network switch, the RPC16 can communicate with any other network enabled storage device to store and retrieve data. This eliminates the need for separate direct attached storage devices for each computer or workstation in a network centric environment. Data security is a key component to any edge storage system and the RPC16-NAS addresses this with optional support for AES-256 hardware and file level encryption, FIPS140-2 validation and hardware and/or software triggered Secure Erase and Data Elimination. Phoenix International is an AS9100D/ISO 9001-2015 certified, NIST SP 800-171 compliant Small Business.
Ą Two each 8 drive (16 drives total) Removable Storage Magazines
Ą One each GbE, 2.5GbE and two 10GbE copper network ports standard. Copper and optical interfaces up to 100GbE available
Ą TCG Compliant and FIPS 140-2 Validated Encryption
Ą HW/SW Triggered Secure erase/Data Elimination
Ą MIL-STD-810G and MIL-STD-461F Compliant
Ą
Introducing the Kontron VX307H Computing Node, the ultimate SOSA™ Architecture Booster
This rugged 3U VPX board server takes computing performance to new heights, enhancing your existing HPEC architectures. With innovative features and extensions, it meets the demands of the most challenging mission profiles.
Choose from a range of CPU models, including 12, 16, or 20 cores, with optional 4 or 8 core configurations for specialized applications. Advanced instructions for AI, Signal Processing, and crypto algorithms deliver double the performance of previous micro server SOCs, powering applications like computer vision and media processing.
Connectivity is paramount, with options for Ethernet 100G/40G or 50G/40G interconnects. The VX307H supports open VPX profiles, accommodating I/O intensive and compute intensive applications to meet diverse requirements.
Reliability and robustness are guaranteed, with selected CPU SKUs offering 10-year reliability under 100% active usage. The VX307H is available in air-cooled and rugged conduction-cooled versions, operating in extended temperature ranges and compliant with industry standards.
Powered by the Intel® Xeon® D-2700 Platform, the VX307H delivers exceptional performance with features like Ethernet 100G, PCIe gen4, and on-chip DMA engine. Built-in cyber security measures and compatibility with Kontron SEC-Line elements ensure data protection.
Leverage Intel® Software for optimized performance, including Intel® Media SDK and Intel® OpenVino™ for hardware-accelerated media decoding, AI, and computer vision tasks.
With its superior SWaP-C ratio, the VX307H serves as a reusable building block for rugged high-performance computing. Extensive connectivity options, along with a rich Linux BSP and comprehensive system management features, make it ideal for building powerful and adaptable servers.
Unleash the potential of your engineering projects with the SOSA™ Architecture Booster – Kontron VX307H Computing Node. Elevate computing performance, ensure reliability, and embrace a robust and secure solution tailored for Defense applications.
Ą First 3U product to take up the 100Gb Ethernet challenge
Ą Takes advantage of performance/power improvement to introduce new Air-Flow Through cooling solution
Ą Available in 12-,16-& 20-core versions,enabling computing power to be adapted to SWaP-C applications
Ą Long term availability with 10-years of typical lifecycle
Ą Intel® Xeon® D-2700 HCC processor with 100G Integrated Ethernet
Ą From 12 to 20 cores to enjoy full range of this SWaP-C product
Ą Up to 64GB DDR4 with ECC
Ą Up to 2.97x faster CPU performance compared to prior product generation
Ą 100GbE networking for improved communication times
Ą Up to x16 PCIe Gen4 avoiding bottleneck on expansion plane
Ą Enhanced instructions for Artificial Intelligence and Signal processing (Intel AVX-512, VNNI)
Ą Security enforced by Hardware Root of Trust (Intel Boot Guard, TPM 2.0 Secure element)
Ą Designed in accordance with the Sensor Open Systems Architecture™ (SOSA) Technical Standard
Ą New VITA48.8 AFT (Air-Flow-Through) and VITA47 CC3 (Conduction-Cooled) support
https://www.kontron.com/en/products/vx307h/p171195
RTD’s standard HiDANplus® embedded computer system provides a robust Commercial-Off-the-Shelf (COTS) solution enabling rapid uptime for mission-critical applications. The system includes a rugged single board computer, power supply, mSATA card carrier, and room for an additional peripheral module. Without increasing the enclosure size, functional upgrades can include high-performance data acquisition, versatile networking options, or enhanced capabilities from a variety of special-purpose add-in modules. Additional configuration options include a removable SATA drawer.
The milled aluminum enclosure with advanced heat sinking delivers passively-cooled performance from -40 to +85°C. Integrated tongue-and-groove architecture with EMI gaskets create a watertight solution with excellent environmental isolation. Keyed cylindrical connectors offer easy cable connections while maintaining the integrity of the environmental seal.
Ą -40 to +85°C standard operating temperature
Ą Designed for high ingress protection in harsh environments
Ą Milled aluminum enclosure with integrated heat sinks and heat fins
Ą Rugged Intel and AMD-based Single Board Computers
Ą High-performance, synchronized power supply
Ą mSATA card carrier and optional 2.5" removable drive
Ą Designed to include an additional PCIe/104, PCI/104-Express or PCI-104 peripheral module without increasing overall enclosure size
ArgonFDS offers a range of durable military computing tablets that are lightweight and high-performing, ideal for soldier-wearable, airborne, land-based, and vehicle applications. Its AT70 model has the smallest size and weight on the market, making it perfect for handheld, dash-mount, or bulkhead-mount applications where size, weight, and power matters. The AT70 utilizes low-power processing with superior display performance and can be customized to meet specific program requirements.
ArgonFDS has extensive experience designing and producing compact units for both mounted and dismounted operations. Configurable with different controls and connectors, these units are ideal for interfacing with soldier-level batteries. They support touch screen and high brightness options, use little power in normal operation, and have various mounting solutions for flexible and versatile applications.
Ą Integrated 7.0” Display and Intel® i7 Processor
Ą Extremely Small Mechanical Outline and Bezel Width
Ą High Brightness & Sunlight Readable
Ą Low Weight
Ą Rugged, Analog Resistive Touch Screen
Ą Choice of Windows or Linux OS
Ą Custom User Controls and Connectors
The CALCULEX RAPTOR is a state-of-the-art high-speed fiber optic data recorder designed to meet and exceed modern military platform data acquisition, processing, and recording requirements. With its advanced fiber optic 24-channel input data rates that support 2 Gbps, 10 Gbps, and 25 Gbps per channel, the RAPTOR sets a new standard in high-speed data capture. Its ultra-high density Removable Memory Module (RMM) storage offers 132 TB capacity, which is expandable up to 640 TB. CALCULEX’s RMM proudly boasts the largest data storage capacity of any rugged recording device on the market.
In addition to its ultra-high density capture and storage, the RAPTOR is designed in compliance with the IRIG 106 standard and provides adherence to open architecture time-synchronization practices for precision data recording across multiple data sources. The RAPTOR is platform agnostic/adaptable through Telemetry Attributes Transfer Standard (TMATS) configuration files.
Ą 24 Channels of Ultra-High Speed Fiber Optic I/O
Ą 132 TB Removable Memory Module Expandable to 640 TB
Ą 36 GBps Data Write Speed w/ 72 GBps Roadmapped
Ą Open IRIG 106 Standard Compliant
Ą Flight Qualified Rugged
Ą Long Duration Recording
Ą Ultra-High Density Storage
(850) 266-3656
www.linkedin.com/company/calculex-inc.
XSR & G1 NSA CSfC Approved
Galleon's ultra-rugged XSR & G1 product families are NSA/NIAP-approved for its Dual-Layer Software Full Disk Encryption (SWFDE) & Hardware Full Disk Encryption (HWFDE) for Data at Rest (DAR). The XSR and G1 families include mission computers, NAS systems, data recorders, and file server solutions, all of which are equipped with industry-leading high-capacity removable storage. These removable data modules (RDM's) ensure fast turnaround times for aircraft, ground vehicles, and marine applications.
Industry-standard solid-state drives are leveraged to take advantage of the evolving technology's continuously increasing storage densities and cost reductions. Galleon's products have been engineered to meet the harshest environmental conditions without compromising on performance and functionality. The SWaP-optimized design makes them ideal for a variety of defense applications, ranging from the depths of our oceans through the vacuum of space; and everywhere in between.
FEATURES
Ą Up to Gen 11 Intel Xeon W Processors
Ą Up to 96GB DDR4 ECC Memory
Ą Up to 80 TB MLC removable SSD RDM's (Removable Data Modules)
Ą Conduction Cooling and Natural Convection Cooling
Ą Toolless Removable Data Module (RDM) insertion & extraction
Ą Certified HWFDE using XTS-AES 256bit
Ą Certified SWFDE using XTS-AES 256bit
https://galleonec.com/xsr2-family-ofrugged-computing-products/
R8
Combining the mobility and flexibility of its pocketable form with a business-focused design, the R8 fully rugged tablet offers a unique combination of revolutionary computing power, rugged features and high portability to withstand the most challenging environments. Powered by Intel® 12th Generation processors, it is designed for professional operations close to the edge, where it is needed most. R8 features an 8” LCD display with Durabook’s proprietary DynaVue® technology for an exceptional viewing experience even in direct sunlight.
Weighing in at just 1.9 lbs, the Durabook R8 sports a Coolfinity™ fanless and yet versatile expansion design for ultimate functionality. Its IP66 rating, six-feet drop resistance, MIL-STD 810H and ANSI/UL C1D2 certifications make the R8 more rugged than other comparable devices on the market, making it the most reliable mobile device to support digital and remote operations.
Ą 8” DynaVue® sunlight readable LCD display
Ą Powered by Intel® 12th Generation processors
Ą Sports a Coolfinity™ fanless design
Ą Versatile expansion design for ultimate functionality
Ą IP66 rating
Ą Six-feet drop resistance
Ą MIL-STD 810H and ANSI/UL C1D2 certifications
https://www.durabook.com/us/products/r8-tablet/
Sponsored by Renesas
Applying AI/ML to a system is a journey: It starts with being able to represent system behavior with data, followed by gaining an understanding of what features in the data are important, and then finally building an effective machine learning (ML) model to represent that behavior.
This journey is often not intuitive to embedded systems developers and can be overwhelming without the right tools and services
In this webcast, learn how Reality AI (now part of Renesas) offers a complete auto-machine-learning framework that empowers non-AI experts to start leveraging the power of machine learning in their designs. (This is an archived event.)
Watch this webcast: https://tinyurl.com/2dah6z4x
Viewpoint Systems, founded in 2011, is a leading original equipment manufacturer (OEM) of rugged displays and mission computers. Our reputation as a leading supplier of mission systems equipment has been proven by our products which are fielded globally on wide variety of air, ground, sea, and space platforms, including the International Space Station, Lockheed Martin's X-59 QueSST, and Textron Systems' Cottonmouth Advanced Reconnaissance Vehicle (ARV). Viewpoint’s products, designed to pass MIL-STD-810G and DO-160 test specifications, boast field-proven reliability with over 10 years in harsh operating environments without fail. Our team consists of experts in both mechanical and electrical engineering and design, who work directly with our customers to accommodate their unique requirements. We've distinguished ourselves with our high-quality products, exceptional customer service, competitive pricing, and industry-leading warranty.
Our company's focus on driving innovation in mission system equipment can be seen through the remarkable growth in our product line. Viewpoint Systems has expanded its offerings to include a diverse range of cutting-edge rugged technologies that are tailored to meet the evolving needs of our industry.
Our rugged monitors feature an enhanced LED backlighting system which provides optimal viewability in sunlight environments. We offer a wide range of options including but not limited to touchscreen, NVIS compatibility, QUAD View functionality, and MIL-SPEC I/O connectors. Our proprietary cooling system ensures that our displays do not overheat, thereby extending the life of the product. Viewpoint monitors also feature a host of inputs that can be displayed simultaneously in various PiP and PbP configurations.
Viewpoint's mission computer, the Mantis, delivers lightning-fast, reliable performance enabling you to process data and make critical decisions in real time. The Mantis is powered by the latest, proven processing technology and comes with an internal H.264 or H.265
video encoder for up to 1080p60 video encoding, as well as two mPCIE expansion slots and connector provisioning for customer-specific interfaces such as ARINC-429, MIL-1553, and CANBUS, and was designed for use with all major turrets (Wescam, Trakka, FLIR, etc.). It can also be configured with a secondary PC that is capable of running its own OS and supporting an additional workstation.
Looking for a customizable solution? Our team of industry veterans will work with you to design and build a cost-effective solution within a time frame that satisfies your needs. We follow a disciplined, multi-staged engineering and design process that consistently meets and exceeds our customer's expectations. Connect with a Viewpoint representative today and we'll be happy to help you find a long-lasting solution that meets your needs.
Ą Viewpoint Products are ITAR-Free
Ą All products are proudly made in the USA
Ą ISO9001 Certified Company
Ą Products comply with, or are designed to comply with MIL-STD-810G and DO-160 test specifications
Ą 2 Year Workmanship and Material Factory [Warranty expandable up to 5 Years]
Ą All monitors feature enhanced LED backlighting systems
Ą Standard definition, high definition, and ultra high definition rugged displays
Ą Wide range of Display and Mission Computer options available
Ą Mission computer designed specifically for mission management software applications
Ą Mission computer provides all the hardware required for a multi-mission system in a single LRU
Ą Custom design solutions available upon request
Markets all across the globe are focused on SWaP. In the defense world, designers are searching for newer componentry to usher in newer compact, smarter missile designs capable of protecting today’s modern warfighters. In the space world, the goal is similar: mass reduction! Companies such as NASA continue to focus on this requirement. Today, it is estimated to cost $10,000 to put a single pound of payload in Earth’s orbit. NASA's goal is to reduce the cost of getting to space to hundreds of dollars per pound within 25 years and tens of dollars per pound within 40 years. With this goal in mind, these newer SWaP options must not only be smaller than their incumbent, they too must survive and thrive in one of the harshest environments ever imagined.
Omnetics' Low Profile Micro-D series offers designers a saving of roughly 30% in height, all the while assuring users the same performance and reliability come to expect with previous MIL-DTL-83513 iterations. These connectors are ideal for critical, high-reliability industries, including aerospace, military, and medical. They are built to exceed the specifications of MIL-DTL-83513, while allowing designers the ability to squeeze more and more into less and less. The Low Profile Micro-D connector series offers proven military specification performance and reliability with reduced flange height and weight compared to standard Micro-D connectors.
Low-profile connector types enable designers to utilize boardstacking efforts. This allows for a fast design of each individual section of the instrumentation allowing for more components in a smaller form factor. Applications include hand-launched drones, portable robotic surveillance systems and cube satellites. Omnetics’ Low Profile Micro-D connectors offer the performance and reliability demanded by this industry niche and beyond. They are designed and manufactured using the identical pin to socket system, shell and insulator materials that pass MIL-DTL-83513. Pins are made of ruggedized BeCu copper alloy that insure continuous signal performance through 50 g's of shock and 20 g's of vibration. Their performance has been tested and certified from -55 degrees to +125 degrees centigrade. The low profile connector’s height is significantly reduced by 30% to less than .208” high with some designs.
Ą Durability: > 2000 Mating Cycles min
Ą Temperature: -55ºC to +125 ºC (200 ºC w/HTE)
Ą Current rating: 3 Amps per contact per MIL-DTL-83513
Ą Voltage Rating (DWV): 600 VAC RMS Sea Level
Ą Insulation Resistance: 5,000 Megohms @ 500 VDC
Ą Shock: 50 g’s with no discontinuties > 1 microsecond
Ą Vibration: 20 g’s with no discontinuties > 1 microsecond
Ą Thermal Vacuum Outgassing: 1.0% max TML, 0.1% max CVCM - NASA SP-R-0022
Ą Contact Resistance: 26 milliohms (65 mV) max @ 2.5 Amps per MIL-DTL-83513
Ą Mating/Unmating Force: 3 oz. (.85g) typical per contact
Omnetics’ Nano-D connectors serve mainly in military and aerospace applications. These devices and the modern chip technology that makes them possible impact circuit board designs as well as connector and cable selections. They are fueling the demand for miniaturization at lower voltages and current levels. Our Nano-D connectors serve design engineers well in this new era.
Nano-D connectors are designed to perform at military specification levels for high reliability and to remain working in both portable applications and extreme environments. Most Nano-D connectors evolved rather directly from the older Micro-D connectors and follow similar specifications. As speeds go up, the wavelength of each signal is shorter, and at lower voltages, vibration and circuit noise could confuse the signal. Nano-D connector resistance is kept as low as 12 to 15 milliohms with a capacitance of 2.0pf to 2.4pf, which is ideal for most circuits with low current flow and low voltage.
Portable high-speed digital signal processing devices are expanding the demand for small, lightweight cable and connectors. Nano-D connectors are especially well suited for these ruggedized, environmentally sensitive applications. When specified, cable, signal-speed capability, and formats are designed to match the ultra-small NanoD connectors. Designs include IEEE 1394 fire-wire cable and extend to USB 3.1 formats and CAT 6a wiring. Many of these formats support a wide range of new designs, ranging from circuitry used in small military unmanned vehicles to soldier-worn equipment.
Omnetics’ groundbreaking Flex Pin contact design pre-dates the advent of the MIL-DTL-32139 nano-miniature specification and today all MIL-DTL-32139 sockets mate properly with the Flex Pin. The one-piece unit is stamped from ASTM B194 beryllium copper (BeCu) to deliver high conductivity, low interference, and high resiliency. Its excellent spring properties enable it to withstand shock, vibration, and other rugged conditions and it easily passes military specification requirements. Flex Pin contacts are plated with 50 micro-inches (1.27μm) of gold over 50 micro-inches (1.27μm) of nickel and are rated at 1 amp each. All pins are plated post-forming to verify a no raw edges surface. Our contacts are inspected by our quality assurance experts to guarantee perfection and performance.
Ą Durability: > 2000 Mating Cycles min
Ą Temperature: -55ºC to +125 ºC (200 ºC w/HTE)
Ą Current rating: 1 Amp per contact
Ą Voltage Rating (DWV): 250 VAC RMS Sea Level
Ą Insulation Resistance: 5,000 Megohms @ 100 VDC
Ą Shock: 100 g’s discontinuity < 10 nanoseconds
Ą Vibration: 20 g’s discontinuity < 10 nanoseconds
Ą Thermal Vacuum Outgassing: 1.0% max TML, 0.1% VCM
Ą Contact Resistance: 87 milliohms (87 mV) max @ 1 Amp
Ą Mating/Unmating Force: 2.5 oz. (.71g) typical per contact
Each issue, the editorial staff of Military Embedded Systems will highlight a different organization that benefits the military, veterans, and their families. We are honored to cover the technology that protects those who protect us every day.
This issue we are highlighting the Military Women’s Memorial, a 501(c)(3) nonprofit organization that has as its mission to honor and remember the service of women who have served in the U.S. military – thought to number 3 million since the American Revolution – as it tells their individual stories and collective history to the public in order to inform and empower future generations of service members.
The physical memorial – situated at the Ceremonial Entrance to Arlington National Cemetery in Arlington, Virginia – is a living memorial that houses an exhibit gallery chronicling the history of women’s service, a theater, a Hall of Honor, a conference room, gift shop and an outdoor terrace and Court of Valor. The heart of the Memorial is the Register, an interactive database that includes the names, pictures, service histories, and awards of nearly 245,000 past and present women who have served in the U.S. military services.
The Memorial – which was opened to the public in 1997 – uses as its façade the historic Hemicycle, the large wall dedicated in 1932 that was originally intended as the ceremonial entrance to Arlington National Cemetery. Behind the wall is a gallery chronicling the collective history of military women’s service from the American Revolution to the present and a space that serves as a multipurpose event venue, gift shop, and Hall of Honor where a tribute is paid to servicewomen who were killed in action, died in the line of duty, were held prisoner of war, and received the U.S.’s highest awards for service and bravery. For additional information, visit https://womensmemorial.org/.
Sponsored by Concurrent Technologies and New Wave DV Design and Verification
The VPX standard from VITA is a ruggedized approach to embedded computing that aims to satisfy high-speed processing needs in harsh environments such as flight, ground defense, and other military applications as well as similar processingintensive applications in rail and commercial transportation, imaging, security, and space.
In this webcast, VPX experts from Concurrent Technologies and New Wave DV Design and Verification will detail how the VPX standard and ecosystem enables high-performance computing in harshenvironment, mission-critical applications. (This is an archived event.)
Watch this webcast:
https://tinyurl.com/mr2b6wha
Watch more webcasts: https://militaryembedded.com/webcasts/archive/
Today’s AI [artificial intelligence] computer architectures can handle the demanding requirements of military applications in the field, but program leaders must meet these requirements using open standards that were never initially designed for them. While massive technology innovations promise to make AI faster, more accurate, and more reliable in many real-time decision-making applications (autonomous navigation, threat analysis, natural language processing, countermeasures, etc), lagging interface, cooling, power-supply, and interoperability standards potentially limit these benefits.
Military program leaders deploying transportable AI in existing and new platforms should explore with their systems suppliers how to leverage AI advances in edge applications while preserving a pathway to stillevolving open standards. In this white paper, learn how standardscompliant sensors and sensor interfaces can be partitioned as part of the AI system design. This move can enable program leaders to fully exploit switched-fabric standards with the most advanced GPUs and flash storage, along with advanced system cooling approaches, to maximize AI performance in field applications.
Read this white paper: https://tinyurl.com/yckutxrk
Read more white papers: https://militaryembedded.com/whitepapers
Military Embedded Systems focuses on embedded electronics – hardware and software – for military applications through technical coverage of all parts of the design process. The website, Resource Guide, e-mags, newsletters, podcasts, webcasts, and print editions provide insight on embedded tools and strategies including technology insertion, obsolescence management, standards adoption, and many other military-specific technical subjects.
Coverage areas include the latest innovative products, technology, and market trends driving military embedded applications such as radar, electronic warfare, unmanned systems, cybersecurity, AI and machine learning, avionics, and more. Each issue is full of the information readers need to stay connected to the pulse of embedded technology in the military and aerospace industries.
Shorten development time and reduce design risk with flexible RFSoC FPGA processors, high-speed data converters, and a robust software design suite. Mercury’s proven COTS direct RF broadband processing solutions deliver real-time actionable data for decision superiority. The SWaP-C modular design is ideal for edge applications used in electronic warfare, radar, and 5G communication applications.
FEATURES
2.5" � 4" module, SFF platforms
SOSA aligned 3U OpenVPX, PCIe
8 A/D and D/A channels
Up to 64 GSPS
Coverage to Ku band
mrcy.com/directrf