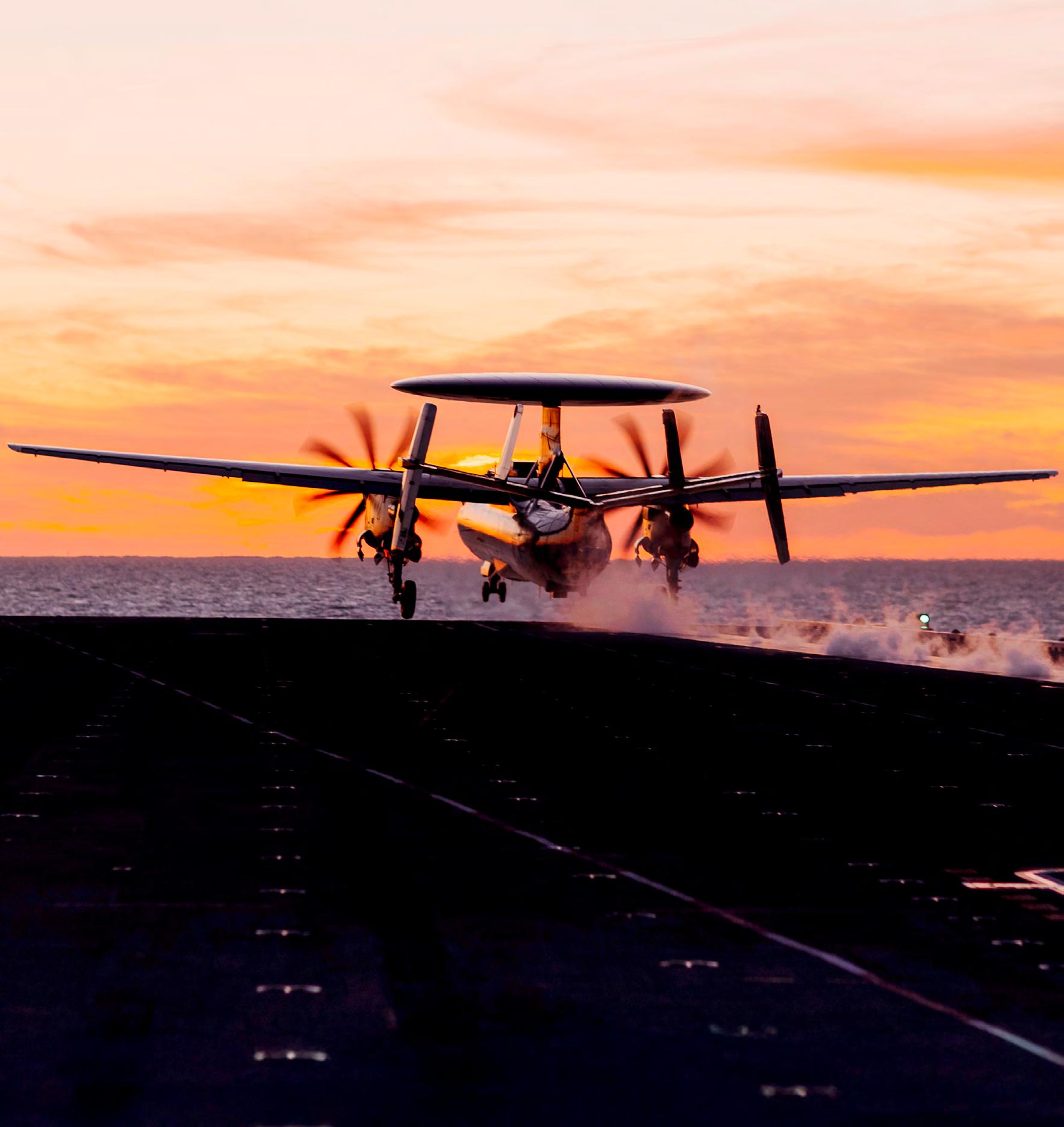
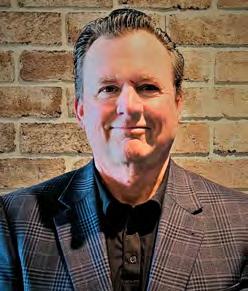
Across radar, EW bands, and beyond, Analog Devices provides broad and narrow-band GaN power amplifier MMICs for your next-gen phased array and communication systems.
analog.com/gan
Editor’s Perspective
5 MOSA reaffirmed, empowering small business By John M. McHale III
Mil Tech Insider
7 New hybrid FPGA devices a game-changer for radar and signal processing By Mike Southworth
Guest Blogs
38 Modernization without disruption: The deadline to enhance DoD communications By Lou Rojas and Steve Axt, Tyto Athene
40 The U.S. Army’s new SBOM requirement By Nick Mistry, CISO and SVP, Lineaje
42 Securing military embedded systems: three challenges By Shane Fry, RunSafe Systems
Defense Tech Wire
8 By Dan Taylor
Editor’s Choice Products
44 By Military Embedded Systems Staff
Connecting with Military Embedded
46 By Lisa Daigle
12 When OEMs and LEMs come together: A defense case study By Ethan Plotkin, GDCA
SPECIAL REPORT: Air & missile defense radar
14 Managing the data deluge: How military radar systems are getting smarter By Dan Taylor, Technology Editor
18 The evolving battlefield: How radar technology is advancing in the age of advanced electronic warfare and C-UAS By Nate Knight, Anduril Industries
MIL TECH TRENDS: Leveraging the Sensor Open Systems Architecture (SOSA) for radar applications
20 Q&A with Travis Slocumb, CEO of Pacific Defense By John M. McHale III, Editorial Director
INDUSTRY SPOTLIGHT: RF and microwave designs for electronic warfare
26 Benefits of a single-chip device architecture for meeting increasing demands of EMSO By Jason Timpe, AMD
30 Qualified components in military and aerospace design: terminating and attenuating microwaves in space By Tibor Urbanek, Cinch Connectivity Solutions
Improving RF adaptability for RF system-in-packages By Brian Kimball, Mercury Systems
©
An E-2D Hawkeye attached to Airborne Command and Control Squadron (VAW120) takes off on Nimitz-class aircraft carrier USS George Washington (CVN 73). The E-2D carries AN/APY-9 radar, radio suite, mission computer, integrated satellite communications, and updated flight management system. The APY-9 radar features active electronically scanned array (AESA) radar, which employs electronic scanning to the mechanical rotation of the radar in its radome. U.S. Navy photo by Mass Communication Specialist 3rd Class August Clawson. To unsubscribe,
https://www.linkedin.com/groups/1864255/
By John M. McHale III
Fans of the U.S. Department of Defense’s (DoD’s) modular open systems approach (MOSA) mandate got a nice surprise before the December holiday season: a new Tri-Service memo emphasizing continued support for MOSA, well-timed with new DoD leadership coming in focused on reforming acquisition.
The first MOSA Tri-Service memo, published in 2019, mandated that all new programs and tech refreshes must leverage MOSA. The latest memo – signed by the Secretaries of the Army, Navy, and Air Force on December 17, 2024 – states that “MOSA shall be implemented and promulgated among the military services to facilitate rapid transition and sharing of advanced warfighting capability to keep pace with the dynamic warfighting threat.”
Simply put, they see MOSA a way to get technology more quickly into the hands of the warfighter, as a tool for speeding up acquisition. Successful MOSA examples were called out in the memo: the Sensor Open Systems Architecture, or SOSA, Technical Standard; Weapons Open Systems Architecture (WOSA); and others.
The memo also lists the three new MOSA sections added by Congress to Title 10 of the United States Code (USC):
› “Section 4401 requires MOSA in major defense acquisition programs [MDAPs],
› Section 4402 requires the implementation of MOSA in program capability development and acquisition weapon system design, to include verification of MOSA requirements, and
› Section 4403 relates to ensuring the availability of major system interface standards and support for MOSA in defense acquisition.”
The service leaders went on to direct that all DoD acquisition officers commit to “all five MOSA pillars: (1) employing a modular design, (2) designating modular interfaces, (3) leveraging consensus-based open standards, (4) establishing enabling environments, and (5) certifying conformance.” To read the memo, visit https://tinyurl.com/y3cced9y.
MOSA initiatives are having an impact as seen by increased requirements for items like SOSA aligned products. However, enthusiasm and mandates cannot change the laws of bureaucratic physics – governments move slow, not fast. MOSA strategies are long-term plays, but faster procurement and acquisition reforms are being called for by the new Trump administration and its supporters.
“Procurement is a mess, and given that the Pentagon purchases more goods, services, and software than all other federal
John.McHale@opensysmedia.com
agencies combined, this is a huge crisis,” write Joe Lonsdale, co-founder of Palantir, and his colleague John Noonan in a blog titled “America Needs Better Defense Acquisition.” Read it here: https://blog.joelonsdale.com/p/america-needsbetter-defense-acquisition.
They say the new administration “can seize the moment, learn from what worked and didn’t work in [Trump’s] first administration, and make generational changes to our defense bureaucracy.”
Lonsdale and Noonan write that trimming down the “Federal Acquisition Regulation (FAR), first issued on April 1, 1984,” is a good place for the new administration to start. “The [FAR] has almost doubled in length, and with it the complexity of the overall federal procurement processes – not just the Defense Department,” they state. “The FAR was written to level the playing for all companies, big and small, who sought government contracts. But as with many federal regulations, the cure was worse than the symptoms, and it favored the biggest companies with the highest proportion of lawyers.”
The authors also call Foreign Military Sales (FMS) approval a “suffocating” process that favors the big defense companies, blocking out new innovative companies.
Innovation is needed, as are more organizations like the Defense Innovation Unit (DIU), which we’ve covered in this space before, around their work integrating commercial uncrewed tech into the defense space and Lonsdale and Noonan tout as an effective acquisition solution.
They also discuss the aforementioned Title 10, saying it has “become swollen with obsolete and choking legal requirements. This creates fertile grounds for long and contentious lawfare when bids don’t go a company’s way, dragging out deployment of new weapons by years. And because it is so difficult for little companies and startups to bring on the lawyers and lobbyists and staff to contend with this dizzying array of red tape, the government must set aside billions in small business contracts just to give them a shot. Small business is the backbone of our country, but welfare does not get the taxpayer the best value for his money.”
They’re absolutely right. However, the participation of smallbusiness electronics suppliers in MOSA initiatives like the SOSA Consortium hint that the new MOSA additions to Title 10 may actually empower small business. We’ll see.
For more on acquisition reform and technology Lonsdale is worth reading and listening to – he’s often a guest on CNBC’s SquawkBox – and is a good follow on Twitter (@JTLonsdale).
ADVERTISER/AD TITLE
23 Acces I/O Products, Inc. –M.2 – The new, more flexible alternative to PCIe mini cards 36 AirBorn –TriMate next-generation circulars
2 Analog Devices, Inc. –Amplify your spectral dominance with the GaN edge
3 Annapolis Micro Systems –64 GS/s Direct RF is at hand!
33 Behlman Electronics, Inc. –The race to open systems –Behlman leads the pack again!
17 Elma Electronic –Leaders in modular open standards enabling the modern warfighter
48 GMS –
X9 Spider. The world's smallest ultra-rugged battlefield A.I.
25 Haivision –Make informed decisions faster
37 PICO Electronics Inc. –Size does matter!
29 State of the Art, Inc. –Reliability … the only option
EVENTS
Satellite 2025
March 10-13, 2025 Washington, DC https://www.satshow.com/
embedded world 2025
March 11-15, 2025 Nuremburg, Germany https://www.embedded-world.de/en
Sea-Air-Space 2025
April 6-9, 2025
National Harbor, MD https://seaairspace.org/
AUVSI Xponential 2025
May 19-22, 2025 Houston, TX
https://www.auvsi.org/events/xponential/ xponential-2025
GROUP EDITORIAL DIRECTOR John McHale john.mchale@opensysmedia.com
ASSISTANT MANAGING EDITOR Lisa Daigle lisa.daigle@opensysmedia.com
TECHNOLOGY EDITOR – WASHINGTON BUREAU Dan Taylor dan.taylor@opensysmedia.com
CREATIVE DIRECTOR Stephanie Sweet stephanie.sweet@opensysmedia.com
WEB DEVELOPER Paul Nelson paul.nelson@opensysmedia.com
EMAIL MARKETING SPECIALIST Drew Kaufman drew.kaufman@opensysmedia.com
WEBCAST MANAGER Marvin Augustyn marvin.augustyn@opensysmedia.com
VITA EDITORIAL DIRECTOR Jerry Gipper jerry.gipper@opensysmedia.com
DIRECTOR OF SALES Tom Varcie tom.varcie@opensysmedia.com (734) 748-9660
STRATEGIC ACCOUNT MANAGER Rebecca Barker rebecca.barker@opensysmedia.com (281) 724-8021
STRATEGIC ACCOUNT MANAGER Bill Barron bill.barron@opensysmedia.com (516) 376-9838
EAST COAST SALES MANAGER Bill Baumann bill.baumann@opensysmedia.com (609) 610-5400
SOUTHERN CAL REGIONAL SALES MANAGER Len Pettek len.pettek@opensysmedia.com (805) 231-9582
DIRECTOR OF SALES ENABLEMENT Barbara Quinlan barbara.quinlan@opensysmedia.com AND PRODUCT MARKETING (480) 236-8818
INSIDE SALES Amy Russell amy.russell@opensysmedia.com
STRATEGIC ACCOUNT MANAGER Lesley Harmoning lesley.harmoning@opensysmedia.com
EUROPEAN ACCOUNT MANAGER Jill Thibert jill.thibert@opensysmedia.com
TAIWAN SALES ACCOUNT MANAGER Patty Wu patty.wu@opensysmedia.com
CHINA SALES ACCOUNT MANAGER Judy Wang judywang2000@vip.126.com
PRESIDENT Patrick Hopper patrick.hopper@opensysmedia.com
EXECUTIVE VICE PRESIDENT John McHale john.mchale@opensysmedia.com
EXECUTIVE VICE PRESIDENT AND ECD BRAND DIRECTOR Rich Nass rich.nass@opensysmedia.com
DIRECTOR OF OPERATIONS AND CUSTOMER SUCCESS Gina Peter gina.peter@opensysmedia.com
GRAPHIC DESIGNER Kaitlyn Bellerson kaitlyn.bellerson@opensysmedia.com
ASSISTANT Emily Verhoeks emily.verhoeks@opensysmedia.com
By Mike Southworth
The three traditional compute architectures used for high-performance embedded computing (HPEC) and radar processing are CPUs [central processing units], GPUs [graphics processing units], and FPGAs [field-programmable gate arrays]. In many cases, a combination of these technologies is employed within a single subsystem, with software applications and workload optimizations influencing hardware selection. While GPUs have received much attention in recent years and are the dominant architecture of choice in the data center market for artificial intelligence (AI) applications, they also have constraints such as very high-power consumption, short product life cycles, and compatibility requirements for specific software development frameworks and architectures. For some applications, depending on how the software is written, FPGA devices may provide a compelling alternative to GPU processing. For example, algorithms developed for radar processing tend to be optimized for digital signal processing and FPGA environments.
Military and aerospace defense integrators, especially in the signal-processing application space, have typically turned to low-latency FPGA devices as coprocessors for signal-processing CPUs, forming the technical pillar for ingesting and processing massive amounts of time-critical radar and sensor data. More recently, FPGA vendors have begun to evolve discrete devices into hybrid, multifunction system-on-chip (SoC) solutions that bring much greater flexibility and capabilities to signal processing applications. For example, AMD (formerly Xilinx) offers a family of adaptive compute acceleration platform (ACAP) devices with a heterogeneous architecture that combines traditional programmable FPGA logic with powerful CPUs, a variety of DSP and math engine accelerators, and high-speed network fabrics. Moreover, ACAP devices such the AMD Versal Premium VP2502 ASoC (adaptive system-on-chip) now include AI accelerators. This top-of-the-line Versal device provides 472 adaptive intelligence engines, with 157 TOPS [trillions of operations per second] performance, which can be used to support AI, machine learning (ML), and 5G signal processing.
Foundational to these ACAP devices is the software programmable logic, which includes 3.7 million logic cells in the VP2502. ACAPs then add power-efficient hard IP blocks for high-speed DRAM memory and Ethernet and PCIe interfaces, together with additional embedded compute engines, including 7,392-slice digital signal processor (DSP) engines; a multicore Arm Cortex A72 CPU; a dual-core Arm Cortex R5F real-time processor; a platform-management controller; and a built-in programmable, low-latency network-on-chip (NoC) fabric. The NoC functions like an extremely highspeed Ethernet switch internal to the device to connect everything within the Versal to everything outside the device.
This mix of heterogeneous accelerator types combined with programmable logic delivers flexibility to match the unique needs of signal-processing applications. In some cases, from a power consumption standpoint, one type of accelerator engine might be more optimized for a specific type of match function. Users can evaluate application workloads and then use whichever ACAP engine is best matched to that compute problem. Because these devices are extremely customizable, the amount of performance and power consumption can be varied and fine-tuned as required.
The Versal family features built-in Arm processors that run the PetaLinux operating system, which enables the possibility of making a single-slot, system-on-a-card VPX module – aligned with the Sensor Open Systems Architecture, or SOSA, Technical Standard – capable of standalone operation and delivering significant size, weight,
Figure 1 | Rear view of Curtiss-Wright’s VPX3536 FPGA engine with VITA 66 fiber optics.
and power (SWaP) advantages. Such modules can also serve as highly performant, reconfigurable software-defined processing engines sitting in a slot next to a traditional x86 payload or I/O intensive plug-in card (PIC) processors.
Another game-changer for the use of FPGAs in radar and signal processing applications is the on-chip presence of AI inference engines. System integrators can now use the image-recognition capabilities of AI and ML algorithms and frameworks. Overall performance can be further enhanced by splitting signalprocessing workloads between the board's DSP and AI engines.
An example of an HPEC COTS [commercial off-the-shelf] processing module that leverages the new class of ACAP hybrid architecture FPGAs is Curtiss-Wright’s VPX3-536 Adaptable Processor, a highperformance SOSA aligned 3U VPX FPGA PIC module (Figure 1). The card is designed for use in demanding sensorprocessing applications, including latency-sensitive radar, EW [electronic warfare], and signals-intelligence DSP.
The hybrid devices can help meet demand for SWaP-optimized, SOSA aligned HPEC radar and signal-processing parts while leveraging the potential of AI/ML to improve image recognition.
Mike Southworth is Senior Product Line Manager, C5ISR, for Curtiss-Wright Defense Systems.
Curtiss-Wright Defense Systems https://www.curtisswrightds.com/
By Dan Taylor, Technology Editor
V-BAT selected as Japan Maritime Self-Defense Force’s first maritime ISR platform
Shield AI’s V-BAT uncrewed aerial system (UAS) has been chosen by the Japan Maritime Self-Defense Force (JMSDF) as its first maritime-based intelligence, surveillance, and reconnaissance (ISR) platform, the company announced. The JMSDF will acquire multiple V-BAT units under the agreement, with plans for additional orders in the coming years. These systems will enhance the surveillance and intelligence capabilities of JMSDF surface vessels.
The V-BAT, a single-engine, ducted-fan, vertical takeoff and landing (VTOL) UAS, is operationally deployed across multiple global regions, the company says. It features a compact design that enables launch and recovery in confined spaces, making it suited for shipborne operations. The UAS is also capable of operating in GPS- and communications-denied environments, according to the statement. In addition to ISR, the V-BAT supports strategic targeting, searchand-rescue, and maritime interdiction.
Red Cat Holdings, Inc. won $518,000 in new orders for its Edge 130 drone from the Army National Guard and another U.S. government agency, the company announced. The combined orders include 12 units of the Edge 130, a military-grade uncrewed aerial system (UAS) designed for mapping, inspection, surveillance, and reconnaissance.
The Edge 130 is a portable system that features a lightweight design of 1,200 grams, over 60 minutes of flight time, and rapid deployment capabilities that allow for hand-launching within one minute, the company says. The Edge 130 was integrated into Red Cat’s product lineup following its acquisition of FlightWave last September. The drone’s size, weight, and vertical takeoff capabilities make it suited for maritime and littoral operations.
Schiebel won a multiyear service contract with the European Maritime Safety Agency (EMSA) for its CAMCOPTER S-100 uncrewed aerial system (UAS), the company announced. The contract, which includes two fixed years with an option for an additional two, will support EU member states with remotely piloted aircraft services (RPAS) for emission monitoring and maritime surveillance, announcement notes.
To date, the S-100 has operated in more than 1,780 deployment days across Europe, including missions in countries such as Croatia, France, Spain, and Germany. The UAS has been utilized for day and night maritime surveillance, search and rescue, oil-spill detection, and monitoring ship emissions for compliance with International Maritime Organization (IMO) regulations, the company says.
Lockheed Martin will integrate infrared threat-detection system on
Lockheed Martin won a $270 million contract from the U.S. Air Force to integrate advanced infrared threat-detection sensors onto the F-22 Raptor, the company announced. The system, called the Infrared Defensive System (IRDS), consists of distributed, embedded TacIRST sensors designed to improve the aircraft’s survivability and lethality, according to the statement. Lockheed Martin will handle the integration of IRDS.
The company says the IRDS is intended to enhance the Raptor’s ability to detect and respond to threats in current and future operational environments. This effort is part of ongoing modernization programs to ensure the F-22 remains a capable air-dominance platform. The integration project will include development, testing, and evaluation to ensure seamless operation of the IRDS within the F-22.
Deployable rotorcraft support system completes testing in Germany
Hensoldt finalized testing of its modernized “Einsatzunterstützungsanlage Neue Technologien” (EUA NT) system at four Bundeswehr helicopter bases, the company announced in a statement. Commissioned by the Federal Office of Bundeswehr Equipment, Information Technology, and In-Service Support (BAAINBw) in May 2022, the EUA NT upgrade extends the system’s operational lifespan by 15 years, the company says, with the deployable system supporting Bundeswehr rotorcraft, such as the NH90 and Tiger helicopters, during all mission phases.
The EUA NT consists of two container types: The system container provides a secure IT base, supporting network connections classified up to ”secret,” modernized software, and communication systems for data and radio connectivity. It functions as a relocatable command cell with two IT workstations. The personnel container complements this setup with additional ergonomic workstations for as many as six operators.
Leidos won a $120 million contract from the Naval Information Warfare Center Pacific to provide key management architecture, engineering, and cybersecurity support services for the U.S. Department of Defense (DoD), intelligence community, and civilian agencies.
According to the terms of the contract, the company will be obligated for a one-year base period and four one-year optional extensions, with a scope that involves designing, developing, testing, integrating, and maintaining technologies to support cryptographic key management systems. Leidos will build on its existing work in cryptographic key management by delivering secure electronic key material solutions for U.S. and allied national security customers, the company says. The effort aims to enhance operational efficiency and modernize key management processes across various defense and intelligence platforms.
[
Patria, Babcock to partner on 6x6 vehicle for U.K. armed forces
Patria and Babcock International Group signed a Memorandum of Understanding to partner on the Patria 6x6 vehicle platform for the U.K. armed forces, the companies announced in a joint statement. Patria will lead the design and development of a tailored version of the 6x6 platform.
The Patria 6x6, currently part of the multinational Common Armoured Vehicle System (CAVS) program, is a modular vehicle platform designed for diverse missions. The program – led by Finland and joined by Latvia, Sweden, and Germany –has delivered more than 200 of the more than 800 vehicles ordered, with ongoing production, according to the companies.
German electronic warfare center gets software, hardware upgrades
Airbus Defence and Space, in collaboration with Hensoldt, is supplying software and hardware updates for Germany’s Airborne Weapon Systems Electronic Warfare Center, the companies announced. The upgrades are designed to improve the generation and management of mission-specific electronic warfare (EW) data for German armed forces aircraft, including the A400M, according to the statement. The effort aims to enhance system automation, reduce response times, and ensure compatibility with advanced weapon systems.
Under the cooperative project, Hensoldt is providing IT services and deployable hardware, such as servers and workstation computers, to support mobile operations. Airbus is delivering updated operating systems to streamline mission planning and execution. The agreement is intended to strengthen Germany’s defense capabilities by increasing mission effectiveness and ensuring readiness against evolving threats, the statement adds.
Netherlands Patriot air defense system to be replenished
Raytheon won a $529 million contract to supply the Netherlands with a Patriot air and missile defense system fire unit and associated equipment, the company announced. The contract, issued through direct commercial sales, includes a fire unit equipped with radar, launchers, command-andcontrol stations, and additional support systems. This effort will replace a fire unit the Netherlands donated to Ukraine. The Patriot system – a ground-based air and missile defense capability designed to counter threats such as long-range cruise missiles, tactical ballistic missiles, and various airbreathing systems – is currently used by 19 countries and is designed to defend against complex and large-scale aerial threats.
Uncrewed ground vehicle market to rise to $5.05 billion globally by 2030, study predicts The global market for uncrewed ground vehicles (UGVs), valued at $3.21 billion in 2024, is expected to reach $5.05 billion by 2030, according to a new market study by TechSci Research, “Unmanned Ground Vehicles Market-Global Industry Size, Share, Trends, Competition Forecast & Opportunities, 2030.” The UGV market, say the study authors, will be driven during the research period by breakthroughs in robotics and autonomous technology which will lead to increased use of the vehicles in such areas as defense, agriculture, and logistics, where they can perform tasks independently in difficult environments.
The researchers note that as improvements in artificial intelligence/machine learning (AI/ML) and sensors continue to accrue, UGVs are becoming more efficient and reliable, making them valuable for operations like surveillance, reconnaissance, and material handling.
UAS detect-and-defeat capability of T7 robot gets trial in Army exercise
L3Harris Technologies reports that it demonstrated a new drone detect-and-defeat capability for its T7 robot system during the U.S. Army’s Vanguard 24 capstone experiment. During the exercise, L3Harris integrated a counter-small UAS onto a T7 robot to demonstrate remote UAS detection and defeat; the test also was a trial of the ability to remotely sense, monitor, and decode other signals of interest using the L3Harris Individual CORVUS Node.
“This demonstration proves it is possible to expand the future roadmap of the multimission T7 platform,” said Ed Zoiss, President, Space and Airborne Systems, L3Harris. “Using readily available technologies through the T7 network is a powerful example of our commitment to help customers dominate future mission scenarios, from counter-small UAS to spectrum sensing and beyond.”
AI-enabled GPS tech firm wins Space Force contract
Slingshot Aerospace won a contract worth $1.9 million from the U.S. Space Force’s Space Systems Command (SSC) to further develop its already operational GPS-jamming detection technology by incorporating enhanced geolocation and artificial intelligence (AI) to detect threats around the globe in near-real-time and help anticipate future threats to international security.
The Slingshot Aerospace announcement notes that the new SSC program, PNT-SENTINEL (Positioning, Navigation, and Timing – Secure Electronic Navigation Threat Intelligence and Location), provides Slingshot with new funding to enhance its already operational technology by incorporating AI and predictive analytics to more rapidly disseminate insights to the warfighter and support faster, more informed decision-making.
USAF authorizes full-rate production on EW for EPAWSS BAE Systems reports that the U.S. Air Force (USAF) cleared its new F-15 electronic warfare (EW) system for full-rate production as part of the $615.8 million (USAF) contract with Boeing to install the Eagle Passive Active Warning Survivability System (EPAWSS). EPAWSS comprises two kits manufactured by BAE Systems, which the company describes as integrated radar warning, geolocation, situational awareness, and self-protection solutions – standard equipment on the new F-15EX Eagle II. It is also reported to be part of the upgrades on the Air Force’s fleet of nearly 100 F-15E Strike Eagles. The announcement states that the Air Force says EPAWSS can enable equipped jets to “deny, degrade, deceive, disrupt, and defeat radio frequency (RF) and electro-optical/infrared threat systems within contested and highly contested environments.”
Capability development follow-on contract for
Collins Aerospace (an RTX company) announced that it won a follow-on contract worth up to $904 million over five years to continue development of the U.S. Navy's Cooperative Engagement Capability (CEC). According to the company’s statement, CEC is a network that integrates sensors across surface, land, and air platforms to enhance integrated fire control.
Under the terms of the contract, Collins Aerospace will advance the CEC system’s capabilities by improving interoperability, expanding weapon and sensor coordination, and integrating additional data sources. Collins Aerospace has been the sole provider of CEC since 1985 and has deployed the system on more than 174 platforms across the U.S. Navy, U.S. Marine Corps, and international forces. The most recent contract, following a previous five-year Design Agent contract, allows for the company and the Navy to engage in future task orders to support engineering activities related to the system’s ongoing development.
Thales won a contract from the French defense procurement agency (Direction générale de l'armement or DGA) to supply several hundred SonoFlash sonobuoys for the French navy. Manufactured in France in partnership with local small and medium-sized enterprises, the SonoFlash sonobuoy is designed to enhance the country’s antisubmarine warfare capabilities, according to the Thales announcement. The company asserts that the sonobuoy can be deployed from maritime patrol aircraft, such as the ATL2, and helicopters, including the NH90, to detect submarines. It operates in both active and passive modes, featuring a low-frequency emitter and a high-directivity receiver. According to the company, when combined with the FLASH dipping sonar, the SonoFlash sonobuoys enable wide-area submarine detection and responsiveness to evasive maneuvers. The system’s communication capabilities allow data sharing across surface ships, aircraft, and acoustic support centers equipped with sonobuoy processing systems.
By Ethan Plotkin
What happens when defense programs can no longer get support for obsolete electronics circuit cards, like computer boards, graphics cards, power supply controllers and many more specialized electronics assemblies that make defense systems “smart”? These circuit card assemblies (CCAs) are often commercial products that have been discontinued by their OEMs.
Commercial off-the-shelf (COTS) circuit card assemblies (CCAs) are great value for companies who make smart defense systems, because they’re ready to order and save all the time, cost, and risk of developing a similar design in-house. However, like all commercially produced items, they eventually become obsolete – meaning they get discontinued.
Legacy equipment manufacturers (LEMs) can offer answers to all players in the defense supply chain who experience these challenges by developing newsources-of-supply (NSOS) for obsolete
electronics. Military service (Army, Navy, Air Force) teams and their primes can take control of diminishing manufacturing sources and material shortages (DMSMS) and rebuild broken supply chains.
For example, over the past six years, we’ve worked extensively with the U.S. Navy and its OEM suppliers to provide obsolete legacy CCAs in support of the RIM-7 Sea Sparrow anti-missile defense system. The Sea Sparrow is used by NATO vessels and domestic U.S. Navy ships to defend against low-flying/high-speed incoming missiles. It’s a ship-saver and a lifesaver.
Obsolete CCAs proved to be a tough challenge after the Navy transitioned support for Sea Sparrow from its prime contractor to “organic” Navy depot support.
Within four years, the responsible Navy program office and their internal suppliers managed to restart the production lines for five DMSMS CCAs, from four
different embedded electronics OEMs. Theoretically, these successes saved more than $10 million in taxpayer dollars. Pragmatically, they’ve enabled the program office to maintain readiness in the face of not being able to reliably get upgrade funding.
To enable this success, the Navy teams contracted GDCA to work with electronics OEMs so GDCA could resume production for DMSMS CCAs.
As with many U.S. Navy surface systems, the NATO Sea Sparrow Missile System is supported by a complex supply chain that has evolved throughout the system’s life.
From the acquisition phase through to full-rate production and deployment, the Navy engaged its prime contractor for design, manufacturing, and repair. Internally, the Navy program office, inservice engineering agent, logisticians and depots, and NAVSUP [Naval Supply Systems Command] all coordinated efforts to support the prime supplier.
At the time the Navy decided to take over primary operation and sustainment for the system (around 2018), there was a lot of electronics obsolescence, including many COTS CCAs. This situation meant that the Navy could not get the spares or repairs it needed to complete its sustainment mission.
Moreover, it was often impractical for the Navy to do technology refreshes of the system configuration, because of the extensive cost of hardware replacement and resulting certification. Some of the boards had been discontinued as early as 2006. By the time it assumed support responsibility, the Navy still needed reliable CCAs until the 2030s at least.
Initially, the Navy attempted to take on the remanufacture of these obsolete cards itself. However, after reverseengineering the first DMSMS CCA, the service determined it didn’t have the resources to sustainably manage multiple and simultaneous reverse-engineering projects.
This is where LEMs come in, as they’re in business to help those customers who cannot upgrade. They also help embedded OEMs resolve a common dilemma: do they end-of-life less profitable products and leave customers in the lurch, or do they continue sustaining low-volume/non-strategic products to keep customers happy?
OEMs grow and maintain market share by introducing newer and better products; LEMs have a more service-oriented business model and partner with OEMs to sustain older “legacy” products. From manufacturing and engineering to sales and supply chain management, LEMs are set up to provide embedded boards that require life cycles beyond what makes economic sense for the OEM.
LEMs offer the added benefit of being OEM-authorized. This means that OEMs have qualified LEMs to take over their legacy designs: producing new, authentic boards and systems that are form, fit, and functionally the same as the products as originally manufactured by the OEM.
Since 2007, we (GDCA) have been providing the U.S. Navy with an obsolete CCA, originally manufactured by Motorola Embedded Computing Group (now Penguin Computing). With support from Penguin, GDCA was able to restart the CCA’s production line and had already provided nearly 500 newly manufactured units and more than 60 repairs over the years. The primary customer at that time was NAVSUP and there was no visibility into the end-users’ system.
We also went on to help the Navy with supplying end-of-life boards from Abaco Systems, Acromag, and Mercury Systems.
The success of these efforts delivered several benefits: First, the Navy was able to secure the boards it needed for as long as they will be required. This allowed the Navy to succeed in its mission to support the warfighter with timely parts and support. Secondly, OEMs could enable support for legacy products without having to spend valuable resources, which enabled allowed them to maintain customer satisfaction while simultaneously focusing on newer strategic products – essential to everyone’s success.
Often, the scope of work required to support legacy designs is so far outside of normal manufacturing processes the risks of project overrun and ultimate failure create a downward spiral of issues and resolution that can last years, with no end in sight. Working with an LEM is not only more productive, but also can save a lot of time, money, and headaches. The LEM acts as a shock absorber between OEMs who must move on to stay competitive and program offices who must stay put to sustain legacy systems. MES
Ethan Plotkin is the CEO of GDCA, Inc. (“Great Designs Continued Always”), who used his experience in supplychain risk management (SCRM) to lead the company from its early days as a small OEM into becoming a trusted legacy equipment manufacturing (LEM) partner for defense and related OEMs across the country. Ethan has also worked extensively with the National Defense Industry Association (NDIA) and currently leads the Supply Chain Network Committee, which facilitates collaboration between government, industry, and other NDIA divisions to strengthen national security through industrial supply chains. Ethan Plotkin obtained a bachelor of science degree in industrial engineering from California Polytechnic State University-San Luis Obispo.
GDCA https://www.gdca.com
By Dan Taylor
Every second, military radar systems collect terabytes of data about potential threats in the skies above. But having data isn’t the same as having intelligence. In an age of information overflow, the U.S. Department of Defense faces a new kind of challenge: turning this tsunami of radar data into actionable battlefield insights.
The military stakes couldn’t be higher: Air and missile defense systems must detect, track, and respond to threats in real time. With hypersonic missiles, drone swarms, and other sophisticated threats becoming increasingly common, radar operators need to process and analyze massive amounts of data faster than ever before. A delay of even a few seconds in converting raw radar data
into actionable intelligence could mean the difference between a successful intercept and a catastrophic failure.
Data deluge
Today’s military radar systems collect enormous amounts of data. Sorting through this mountain of information quickly enough to be useful in combat is the big problem facing industry.
The first hurdle is simply moving all this information around. “With direct digitization and wide bandwidth sensors, radar front-ends are producing more data that needs
to be communicated to the back-end processor,” says Matt Alexander, chief engineer for sensor systems at Mercury Systems (Andover, Massachusetts). “This is driving the need for high-speed fabrics such as 100/400 Gbit Ethernet over fiber.”
Traditional processing power just isn’t enough anymore. “Even traditional radar processing becomes more computationally complex due to the increase in data,” he continues. “This is driving the need for the highest-performing processors.”
Carl Nardell, principal engineering fellow at Raytheon (Tucson, Arizona), says that while radar systems generate massive amounts of data, “most of this data is not very useful.” The solution? Process it immediately, he says. “The more we can process data at the point of collection, the more tractable the problem becomes.” (Figure 1.)
Industry is racing to develop smarter ways to handle this information. Dr. Justin Pearson, senior director of architecture and business growth in aerospace and defense at Wind River (Alameda, California), says that the most promising technology includes edge computing, high-performance data compression, and cloud integration for managing massive real-time data flows.
The role of artificial intelligence
Artificial intelligence (AI) is quickly becoming a useful tool for turning all this radar data into useful battlefield information. By processing information faster than humans and spotting patterns that might otherwise be missed, AI is changing how military forces collect and analyze radar data.
One of the big ways AI can help is that it is capable of spotting things that traditional processing methods might miss, Alexander says.
“AI has the ability to improve sensor effectiveness by leveraging the increase in data and by exploiting features in data not exploitable by conventional processing techniques,” he says.
He points out that AI could help with several key tasks: better filtering out
enemy jamming, identifying the difference between real threats and false alarms, identifying what kind of object it’s seeing, and keeping track of targets in confusing situations and cluttered environments.
The crucial advantage of AI systems is speed. Nardell notes that “a single graphics processing unit (GPU) can perform millions of times more analysis operations than a human.” This amped processing power means faster decision-making in critical situations.
“By using AI, we can automate intelligence analysis to provide useful insights in seconds rather than hours, days or weeks,” he adds. “AI has the ability to massively scale up human operations. AI can help process reams of data into actionable intelligence and accurate targeting information at speed and scale in high-risk environments.”
However, there are limits to how AI can be used in military systems. Pearson notes that it’s still early days for AI, and it can’t be used yet in safety-certified elements. However, AI can still be helpful by helping radar systems work in difficult conditions, he says.
“[AI can] recognize and classify targets using image recognition and radar signal processing, with deep learning models identifying objects like vehicles, aircraft, or drones even in degraded environments such as heavy jamming or low visibility,” Pearson explains.
AI is also proving valuable in countering enemy actions. “AI will be able to more effectively make use of multifunction apertures,” Alexander says. “Dynamic scheduling of sub-apertures is a complex problem that AI will be able to optimize.”
While AI currently gets most of the attention, defense industry engineers are looking at other new ways to handle the massive amounts of radar data produced every day. One promising approach involves using light instead of electricity to process data.
“While digital signal processing remains a foundational component to radars, novel photonic and analog processors are being developed to process – on operationally relevant timescales – large quantities of data,” Alexander says. “We are seeing an increasing interest in photonic interconnects and inclusion of photonic processors.”
Combining data from multiple sources is another strategy. “Data fusion, particularly across multiple platforms and multiple sensor types, assists in reducing false alarms and discriminating decoys,” he explains. (Figure 2.)
The challenge is similar to those faced in other technological areas, Nardell says. “Electronic warfare and sensor data analysis are fundamentally becoming big data problems,” he says. “The data is simply too large and complex to manage or process using traditional methods.”
Nardell believes traditional computer science offers some solutions to the data glut, pointing to relational databases, parallel compute techniques, and edge processing as tools that could help with the data-processing challenge.
High-performance computing is another important tool, Pearson says, as it can perform large-scale data processing through parallel computing, accelerating simulations, real-time decisions, and predictive modeling (such as in combat scenario planning).
Figure 2 | The Mercury Systems HDS6605 is a 6U OpenVPX server blade featuring Intel's 2nd-generation Xeon scalable processor for edge-processing applications. (Image courtesy Mercury Systems)
Delivering intelligence to the battlefield
Edge computing is particularly promising. Processing data near the battlefield slashes latency and bandwidth needs, allowing for real-time analytics even in remote environments, Pearson says, noting that radar systems are able to analyze data locally “to trigger alarms without waiting for centralized systems.”
Raytheon is working to deploy GPUs at the point of intelligence collection to enable important, useful data to be refined and routed to the warfighter quickly, Nardell says.
“We now have the ability to process data at the point of collection with compute power that had only been available in a datacenter, mainframe, or server,” he says.
The goal is to reduce large amounts of data into useful information that can be easily shared, which “allows a very small amount of transferred data to impact the OODA [observe, orient, decide, and act] loop of an adjacent platform or even commander,” Alexander says.
The capability to process military radar data is one thing – protecting it is quite another. A security breach could have major consequences for military operations, so the defense industry is building protection into systems from the ground up rather than adding it later.
“Security must be built in, not bolted on as an afterthought,” says Matt Alexander, chief engineer for sensor systems at Mercury Systems (Andover, Massachusetts), noting that Mercury Systems uses various methods to protect sensitive information, including FPGA [field-programmable gate array]-based cryptography, root of security, secure boot, sensors, fingerprinting, and physical protections against system infiltration.
While the amount of data has increased dramatically, the fundamental security challenge remains familiar. Carl Nardell, principal engineering fellow at Raytheon (Tucson, Arizona), does not believe the industry will have trouble solving it.
“Data security is not a new problem, and [it’s] one that simply is compounded by the increased flow of data between sensors and consumers of data,” Nardell says. “While data security requires a certain amount of overhead, both in terms of data volume and processing, this does not represent a new or limiting challenge.”
When it comes to radar data, Dr. Justin Pearson, senior director of architecture and business growth in aerospace and defense at Wind River (Alameda, California), says good security practices include using “end-to-end encryption protocols like AES-256, TLS, and VPNs; applying zero-trust security models with continuous verification; and implementing strong key management systems.”
Physical protection is just as important as digital security. Alexander points out that advanced protection technologies “can mitigate reverse engineering” and “safeguard confidential data and IP against adversarial threats even when a system has been compromised.”
Regular testing and training are also essential parts of data protection. Pearson emphasizes the importance of conducting regular security audits and training personnel on cybersecurity best practices.
The military can test these systems during training to ensure they work in combat. “Agreeing on what data and insights must be shared can be proven out in training exercises and thus ensure a robust networked effect during a future conflict,” Alexander adds.
Local storage systems are also important when communications are cut off. Pearson points to promising new tech like distributed storage systems with local caching that enable offline access during disruptions, as well as ruggedized tablets and augmented-reality goggles that can provide real-time mission insights. (Figure 3.)
The role of open standards
Open standards like the Sensor Open Systems Architecture, or SOSA, Technical Standard are changing how the defense industry approaches radar system development and procurement, making it easier to integrate new technologies and work with multiple vendors.
“Open standards widen the pool of candidate technology and capability providers,” Alexander says. “For instance, some open standards allow for the insertion of 3rd-party radar modes. This type of model enables dozens of organizations to develop and integrate radar mode IP in addition to the radar OEM [original equipment manufacturer], making the radar a best-of-breed system.”
Software containers have been particularly helpful in implementing these standards.
“Containerized software has been the biggest enabler for drawing upon the best AI capabilities from any source,” Nardell says. “The standardization of hardware has commoditized compute capability such as GPUs, enabling the latest and best hardware to be applied to this area without updating algorithmic software.”
At the end of the day, using SOSA aligned parts just makes it easier for systems to work together, Pearson says.
“The SOSA [approach] provides welldefined, standardized interfaces that enable seamless integration of hardware and software components from
different vendors, ensuring that radar, sensor, and computing systems can exchange data securely and operate collaboratively, reducing proprietary lock-ins,” he says.
The modular nature of parts aligned with the SOSA Technical Standard also makes it easier to upgrade systems. “SOSA encourages modular components that are easily upgraded or replaced, allowing new capabilities like advanced data encryption modules, AI accelerators, or storage systems to be integrated without redesigning the entire system,” Pearson continues.
Adherence to open standards also helps the industry in another major way – saving money.
“Open standards lower development costs and extend system lifespan by allowing easy replacement or upgrading of components without requiring overhauls,” Pearson says. “A radar system with SOSA compliant components can receive upgrades to processors or storage modules without major redesigns.” MES
Go from development to deployment with the same backplane and integrated plug-in card payload set aligned to SOSATM and CMOSS. Includes chassis management, power and rugged enclosure for EO/IR, EW, SIGINT and C5ISR applications.
With you at every
By Nate Knight
The contemporary military landscape is undergoing a profound transformation, driven by rapid advancements in electronic warfare (EW) capabilities and the proliferation of uncrewed aerial systems (UASs). This evolution is posing serious challenges to conventional radar systems, as traditional radar solutions struggle to keep pace with emerging threats and tactical requirements. No longer can military forces rely solely on large, centralized radar installations: The battlefield of tomorrow demands a paradigm shift in both radar technology and deployment strategies.
To ensure that warfighters have the necessary tools to maintain superiority in the ever-evolving electronic battlefield, substantial innovation in radar technology is imperative. Now facing the industry: The questions of how radar technology is advancing to meet new demands, and what the implications are for future development and research in this critical field of defense technology.
The rapid progress of electronic warfare (EW) capabilities and evolving threats from uncrewed aerial systems (UASs) mean a fundamentally altered nature of modern conflict. The electronic battlefield is becoming increasingly complex as adversaries develop sophisticated methods to disrupt radar systems. Modern jammers now generate highly targeted and adaptive interference, while advanced spoofing techniques create false radar returns. The integration of radar systems into broader networks has also opened new avenues for cyber-based attacks. Additionally, artificial intelligence (AI)-driven EW systems enable realtime adaptation to counter specific radar configurations, necessitating a new generation of robust, networked, and resilient radar systems.
Simultaneously, the proliferation of small UASs has introduced a new dimension to modern warfare. These widely available and increasingly sophisticated platforms serve multiple purposes, from reconnaissance to weapon delivery systems or even as sacrificial or expendable
jammers. Their small size and exceptional maneuverability make them elusive targets for traditional radar systems. Further, the ability to deploy large numbers of small UAS in coordinated swarms overwhelms traditional tracking and engagement systems. This threat landscape demands radar systems capable of detecting, tracking, and classifying multiple small, agile targets in complex environments while maintaining the ability to manage traditional threats.
As the battlefield continues to evolve, future radar technologies must become adaptable, resilient, and capable of addressing these threats simultaneously.
The vulnerabilities of centralized radar installations against these emerging threats have created the need for a shift toward distributed, low-size, weight, and power (SWaP) radar networks. These smaller, more cost-effective radar systems are capable of operating within a larger, decentralized network, offering enhanced resilience against attacks or failures, as the loss of individual nodes doesn’t compromise the entire network. Additionally, a distributed architecture provides more comprehensive coverage, particularly in complex terrain or urban environments, making them better suited to address modern warfare challenges.
For maneuver formations, the prevalence of small UASs and other asymmetric threats has necessitated the development
of defensive capabilities at the individual vehicle level. Equipping vehicles within a formation with their own radar systems enhances operational flexibility and vastly improves the survivability in contested environments. By adopting this distributed model, military forces can better adapt to the evolving nature of electronic warfare and maintain operational effectiveness in the face of emerging threats.
Technological advancements in radar
These advancements in radar technology are fundamental to developing radar systems capable of meeting the challenges posed by modern EW and small UAS threats.
High-data-rate samplers enable radar systems to capture and process vast amounts of information with unprecedented speed and precision. High-speed sampling enables much finer resolution in both range and Doppler domains, crucial for detecting and tracking small, fast-moving targets. It also supports wider bandwidth operations, which means that radars can gather more information about targets and their environments and leverage more sophisticated signal processing techniques, which enhance a radar’s ability to distinguish targets from clutter and interference. These advancements are particularly valuable in complex environments such as cluttered urban battlefields and multithreat scenarios, where it is critical to distinguish small UAS from background noise or from each other.
COTS beamforming capabilities
The availability of commercial off-theshelf (COTS) beamforming capabilities is accelerating innovation in defense, enabling the development of more agile and adaptable radar systems. Leveraging commercial technology for military applications not only reduces time to deployment but also decreases development costs and fuels continuous improvements. Modern commercial beamforming technologies enhance radar performance by offering improved spatial resolution, interference rejection, and multitarget tracking capabilities. In addition, commercial beamforming solutions often offer scalable architectures and flexible system designs to meet various operational requirements.
3. Software-defined radar
As radar hardware becomes more digital, more functionality is moving from hardware to software, creating systems that are more flexible and can be quickly updated. Software-defined radars can be rapidly reconfigured or updated to address new threats or operational requirements without hardware changes. Additionally, a single software-defined radar can perform multiple functions (e.g., search, track) by switching between different software-defined operational modes. (Figure 1.)
4. AI and ML integration
The integration of AI and ML into radar systems is enhancing the ability of these systems to distinguish between threats and non-threats, and to adapt to new electronic warfare tactics in real time. AI algorithms can automate the classification and identification of targets, considerably reducing the cognitive load on human operators. Moreover, ML techniques enable radars to dynamically optimize their waveforms based on the current electromagnetic environment and mission requirements. Further, AI-driven radar systems can identify and mitigate various forms of interference and jamming in real time, enhancing sensing performance in contested environments.
5. Smaller and more cost-effective
Advancements in component technology are enabling the development of compact radar systems, while new materials and manufacturing techniques
are facilitating the production of smaller, lighter antenna arrays and other radar components. Moreover, the use of highly integrated, multifunction RF and digital circuits is reducing the size, weight, and power (SWaP) consumption of radar systems. Developing smaller, more power-efficient radar systems without sacrificing performance is crucial for widespread deployment across military vehicles and platforms.
Outlook: The new generation of radar systems
The ongoing evolution of radar technology is a critical component in maintaining military superiority in the increasingly complex electronic battlefield of the future. The move toward decentralized, networked radar systems – coupled with advancements in high-data-rate sampling, software-defined architectures, and AI integration – will usher in a new generation of radar. These advanced platforms will see enhanced resolution and target detection, heightened adaptability, and rapid reconfiguration. AI/ML will enable automated target classification, dynamic optimization of waveforms, and real-time adaptation to EW tactics.
The result: A new generation of radar systems that are smaller, cheaper, and much more quickly developed than ever before – enabling the widespread deployment of decentralized sensing capabilities across military vehicles and platforms. This agility in development and deployment will be crucial to staying ahead of the evolving threat landscape. These distributed, networked systems will be deployed across multiple platforms, including individual vehicles, thereby enhancing operational flexibility and survivability in contested environments.
Ultimately, the radar of the future will be a highly adaptable, resilient, and intelligent system capable of ensuring that military forces can adapt quickly to emerging threats.
The importance of continued innovation in defense capabilities cannot be overstated. As adversaries continue to develop new methods of EW and deploy increasingly sophisticated unmanned
systems, the ability to detect, track, and engage these threats will be crucial. The future of radar lies not just in powerful hardware, but in intelligent, adaptive systems that can outsmart and outmaneuver advanced tactics and elusive UAS threats. By embracing these advances and continuing to push the boundaries of what is possible in radar technology, the industry can ensure that warfighters have the tools they need to operate effectively in the complex, contested battlefield environment. MES
Nate Knight is Head of Air and Missile Defense at Anduril Industries. Prior to joining Anduril, Nate served as vice president of Air and Missile Defense at Numerica Corporation. At Numerica, Nate led the company’s air defense division as well as several internal technology initiatives. His team provided innovative software technology to major U.S. Department of Defense (DoD) programs including U.S. Army Integrated Battle Command System (IBCS) and U.S. Air Force Cloud-Based Command and Control (CBC2) Fusion. Nate has a doctorate in computer science from Colorado State University, having completed research in the area of robust reinforcement learning for non-linear control systems.
Anduril Industries https://www.anduril.com/
By John M. McHale III, Editorial Director
Leveraging open architecture designs for EW [electronic warfare], PNT [position, navigation, and timing], and other applications, Pacific Defense is pushing innovation and adding to the momentum of the U.S. Defense Department’s (DoD’s) MOSA [modular open systems approach] mandate. In this Q&A with Travis Slocumb, co-founder and CEO of Pacific Defense, he elaborates on the benefits of MOSA and how 2025 will be a pivotal year for MOSA. Slocumb also covers the impact MOSA initiatives like CMOSS [C5ISR Modular Open Suite of Standards] and CMMF [CMOSS Mounted Form Factor] will have on military technology shares while also sharing Pacific Defense’s origin story. We also discuss how to speed up the DoD’s acquisition process and recruit engineering talent to the U.S. defense industry.
MCHALE: Please provide a brief description of your responsibility within Pacific Defense and your experience in the defense industry.
SLOCUMB: My responsibility is to create and lead a company strategy that meets, preferably exceeds, the needs of our customers and their ongoing missions in a dynamic geopolitical environment
today, and for decades to come. The critical element is building a team and a culture that is aligned to these missions in a real sense, where every engineer in the company understands the “why” associated with the requirements we design and build to, and is empowered to seek faster and better with the process discipline required to successfully field new products and capabilities. We have spent about five years building what I believe to be “best-in-class” teams in engineering, manufacturing, program management, finance, etc., and now we are able to double down on our MOSA [modular open systems approach] technology base and drive much harder and faster than any traditional [U.S.] DoD [Department of Defense] program I have ever worked on. All of that said, my primary daily responsibility is to make decisions
with the speed that our team needs and deserves without getting in their way, and to know and care about our people who are committed to our shared success and work very hard.
I have been fortunate over the past 40 years in the industry to get to know many very accomplished professionals and learned all I know from watching and listening to how they solved problems. In the early days it was technology development with the original radar innovators, like Fred Nathanson, Lamont Blake, etc. In the 1990s I worked as a contractor on a series of DARPA programs that were focused on a very real and problematic emerging global threat. Under the right circumstances – including PEO [Program Executive Office] and program engagement, focused FFRDC [Federally Funded Research and Development Center] performance, industry playing to their strengths and collaborating – this can be a very rewarding experience for an earlyto mid-career engineer. A lot of learning across multiple disciplines. Finally, Raytheon was a step up to a C-level role in what was, at the time, Space and Airborne Systems based in El Segundo. I somehow landed in the middle of a great team with a strong technology base that was on the precipice of having to compete on several new, large programs. That was serious fun, and we won a few of them, culminating in the Next Generation Jammer Mid-band program. I had the unique experience of being the BD [business development] executive for the segment through the competitive process, then converting to the product line VP post-award on point for negotiating the EMD [engineering and manufacturing development] contract with a great Navy team, then saw it through CDR [critical design review] before moving on. Lots of exposure to lots of great people, like Bill Swanson, over the years, and for that I am grateful.
MCHALE: How has your Raytheon experience helped you now lead a supplier to companies such as Raytheon?
SLOCUMB: With the exception of a couple of programs, we aren’t really selling much to the large traditional primes
currently. Most of our product sales volume is from smaller nontraditional direct suppliers, and most of our anticipated growth will likely derive from other sources over the next few years. We sell modular products to everyone, so it is certainly possible that these relationships could grow in the future. We put a high premium on technical support, getting our products to perform to customer expectations in their environment. We seek and generally get balanced terms on our contracts and purchase orders. At any larger company, you learn to hire the smartest, most experienced, and respectfully communicative contracts professionals you can find, and I believe at Pacific Defense we have done exactly that.
MCHALE: Please describe how Pacific Defense came to be; how Spectranetix, Spear Research, Perceptronics fit together; and the company’s mission within defense electronics.
SLOCUMB: The creation of Pacific Defense was inspired by lessons learned throughout my career, and particularly from the experience of running a sizable EW [electronic warfare] business at a first-tier supplier/integrator. This afforded a comprehensive view of the future threat environment and, as a supplier to both domestic and international 4th-gen fighters, provided lessons learned in rapidly evolving global operations, where legacy kit was steadily falling behind. There was, in 2019, a growing base of MOSAbased software-defined radio (SDR) and utility card technologies that, with additional investment and engineering leadership, could form the basis of a new generation of EW capability better suited to what has become a software-based fight. Spectranetix stood out as a clear leader in the field, and I was very fortunate to convince Rick Lu and team to jump on the bandwagon. To their credit, the Spectranetix engineers were thought leaders who had already spent several years working with Army C5ISR [command, control, computers, communications, cyber, intelligence, surveillance, and reconnaissance] to bring high performance CMOSS [C5ISR Modular Open Suite of Standards] technologies to the EW portfolio.
Spear Research is our EW system center of excellence. We have had a lot of success integrating third-party applications like SCEPTRE and various government-owned frameworks, but [we] still see a need to design, rapidly implement, and verify organically created algorithms/techniques. We have a long-term capability roadmap maintained by the team in Nashua (New Hampshire) and El Segundo (California), and provide quarterly software drops to all of our customers who want them.
Perceptronics, our partner, is an innovative, pure-play AI/ML [artificial intelligence/ machine learning] research company with capabilities ranging from embedded applications like signal classification and RF signal anomaly detection to novel data fusion algorithms and advanced mission planning and support frameworks enabling trusted autonomous operations. We realized early on that bringing our EW subject-matter experts and our data scientists together on one integrated team focused on system level performance on a sustained basis was the only way to credibly bring AI to the EW fight. For example, Perceptronics has delivered AI-based radio type recognition software that allows our EW systems to identify enemy and friendly radios quickly and accurately, a key requirement for modern spectrum warfare. In addition, we have integrated AI/ML techniques that include machine learning classifiers and Bayesian algorithms to improve detection performance, minimize false alarms, and reduce operator workload in our EW systems.
Though EW was a primary motivator to start the company, we rapidly realized that integrated communications and networking, A-PNT [assured position, navigation, and timing], cyber, and a variety of mission command applications were easily integrated and synergistic with the EW mission. Now we spend a lot of time bringing these capabilities together in a single chassis to support a variety of use cases, like networked EW in a dense UAS [uncrewed aerial system] threat environment. Our company motto is
“if it does not work in the field, it does not really work.” We participated in well over 100 live exercises over the past couple of years, and always bring back lessons learned that end up in our MOSA baseline.
Lastly, I cannot say enough about how powerful MOSA is once you fully embrace it with rigorous adherence to CMOSS, FACE [Future Airborne Capability Environment], and SOSA [Sensor Open Systems Architecture] standards, and stick to it as an engineering discipline and a business model. I view it as a significant departure from the world I grew up in, and a game-changer for national security, especially winning the nonkinetic fight. People often ask me, “what if the department backs away and does not require it?” My answer is that we still have, as a company, all of the benefits that matter in any competitive procurement … speed, maturity, affordability … and will never turn back.
MCHALE: Pacific Defense is particularly focused on producing technologies based on MOSA strategies such as SOSA, CMOSS, and CMFF [CMOSS Mounted Form Factor]. Why does MOSA have so much momentum in the defense community right now and how does it benefit the warfighter?
SLOCUMB: I see increased momentum in senior leadership in the services, especially over the last year. Budgets are very tight, and we are spending a fortune to maintain an installed base that is aging out and is frankly not very capable. Our adversaries are putting technologies in place rapidly that are impactful globally, and our leadership knows that we have to radically change the way we do business. The open model is very intuitive – a dollar spent to mature the base benefits all customers. Once the base reaches an adequate level of technical maturity in industry, the ability to rapidly pivot to field new capability is unlimited, if we can collectively get out of our own way.
I am proud to have started a company that absolutely has proven, in a relatively short amount of time, that the model is viable and needs to be the way of the future, starting now. Frankly, I think some customers struggle to believe what we show them, but we will keep going to every live event we can and keep pounding the drum.
I think 2025 will be a pivotal year for MOSA. (Figure 1.)
Our warfighters are amazingly resilient and adaptive, but they still spend a lot of time planning, configuring, fixing, fatfingering, and dealing with uncertainty about the environments they work in. The model of having multiwaveformresilient comms, APNT, EW, signals intelligence, cyber, and robust mission planning all living on cards in one box, on a single backplane, enabled by some level of autonomous decision aids, is a game-changer. The ability to focus on planning and managing the fight across many nodes on a battlefield with speed, certainty, and precision is the goal. There is still a lot of software to be written to meet this goal, but with a MOSA base [what is learned from] each use case, or deployment, are relatively easily feed forward into the next drop. We do this routinely, and work with industry partners to establish the tools and discipline to make the model supportable, for example, continuous ATO [authorization to operate].
MCHALE: Some DoD leaders have called for more metrics on MOSA success to combat naysayers. How would one describe or measure the success of a MOSA initiative?
SLOCUMB: Well, you really can’t beat the “tried-and-true” schedule and cost to field a new capability, as well as mission-related performance metrics. Many of the traditional “off-the shelf” proprietary products out there are not architected to support change or rapid third-party capability integration, and typically are not attached to a software factory. Stick with fixed price development, make schedule and cost your primary [evaluation] criteria, and you will likely get a MOSA-based approach. I like the “try before you buy model” where system level capability is evaluated by a government-sponsored third party, and the ability to [leverage] plug-and-play capability, hardware or software, is rigorously assessed. The only naysayers we see are those with long-standing equities that are threatened by the model, no need to elaborate here.
Success equals a satisfied user, and a system that gives our warfighters a sustainable advantage at a very reasonable cost. This is doable.
MCHALE: Aside from MOSA, what are the types of design requirements are you seeing from your customers?
SLOCUMB: The usual performancebased specifications: environmental, SWAP [size, weight, and power], legacy interfaces, etc., most of which do not relate to MOSA. There are several positive trends that are synergistic with MOSA, including a renewed interest in model-based system engineering and new UX/UI [user experience/user interface] technologies that address intuitive system management and real-time optimization. The ability to give a young operator a new system that is intuitive to use, requiring a minimal amount of training to get up and running is highly valued. Our industry segment has traditionally struggled with putting sufficient emphasis on UX development and refinement. Rightly so – we put a lot of energy into system engineering and system-level validation. I am constantly pushing my team to put that level of energy into UX refinement as well. Candidly, we are not there yet, but this is a priority going into 2025.
MCHALE: MOSA initiatives enable more commercial technology to get into military systems; that said, does the DoD acquisition process need to speed up to truly take advantage of commercial innovation? If yes, how so?
SLOCUMB: From a legal perspective, the DoD opened the door to speed several years ago with OTA [Other Transaction Authority] and MTA [Middle-Tier Acquisition] contracting. We view disciplined adoption of MOSA by DoD and industry as an excellent complement to the legal remedy to get to the commercial timelines desired. We are involved in a current competition where vendor solutions are undergoing environmental qualification prior to selection for contract award. This is unprecedented in the legacy model, and a great example of a government team that has absolutely found the recipe and done the disciplined work over the past year to succeed in breaking new ground.
In addition to our growing modular product portfolio, we are planning to launch several system-level products for commercial sale next year, where the customer can cut a purchase order for the product and solicit ongoing engineering support to evolve the product to user needs, including integration of emerging third-party capabilities to counter rapid changes in the threat environment. Additionally, this installed base will have access to quarterly capability drops already on our roadmap. A bit further out, but under consideration internally, is a service-based model for EW, comms, A-PNT, etc. More to come on the service-based model over the next year.
MCHALE: Pacific Defense recently announced the team for the CMFF program, which includes Thales Defense & Security Inc., BAE Systems, as well as Regal Technology Partners, Palantir, and STC. What makes this team ideal for CMFF and how is Pacific Defense leading it?
SLOCUMB: Teaming, partnering, collaborating with industry and government partners is the heart and soul of our company. Between plug-in cards and software applications we have integrated with well over 30 partner companies, mostly in public settings. We are already working closely with our CMFF partners on related development efforts and have great relationships at the working level; this team is already fully functioning. Our partners are very good at what they do and are well-established, and they clearly see the transformational potential of a MOSA-based approach to rapidly deploying new capabilities like CMFF. I don’t really need to explain why this group is ideal … their reputations speak for themselves.
How do we lead it? We put a thoughtful, compliant, affordable plan on the table, solicit feedback, and manage to the plan. Fun fact: We have a very experienced program-management team in the company, perform quarterly EACs [estimates at completion] on all programs, and generally hold across the portfolio, quarter after quarter. We are fair, communicative, and respectful … which goes a long way.
MCHALE: What other disruptive technology or innovation do you see being a game-changer in the defense electronics arena? Predict the future.
SLOCUMB: Once programs like CMFF, HMIF [human-machine integrated formation], and CCA [collaborative combat aircraft] are fully configured and in the hands of our soldiers we will likely see very powerful ways to leverage the network that we can currently only imagine. These architectures will enable automated decision support across domains and give our team the speed needed to stay way ahead of our adversaries. Clearly the addition of large numbers of low-cost unmanned network nodes will change the game. We will always see a trend toward lower-SWaP-plus-cost systems, especially on platforms that attrit at some rate.
We also observe that successful use of AI in the commercial market relies on powerful, centralized processing to train and update models. Defense missions, however, must adapt quickly in environments without access to such computational power. Working with Carnegie Mellon University, we are developing innovative approaches to use AI directly at the edge of conflict.
MCHALE: The defense industry is embracing new technologies and methods, but some corners wonder if the same is being done with new engineering talent. There seems to be a lot more gray hair at military shows like AUSA and Sea Air Space than at non-defense trade shows. Does the military-electronics industry have a talent recruitment challenge on its hands? If so, how can it be solved? How does Pacific Defense recruit engineering talent?
SLOCUMB: Maybe, but we certainly do not see this trend. We seek energy, passion, and commitment, and we see this at all ages from our interns to our octogenarians
who frankly are still kicking it. Our team runs fast and hard, and we have had had to “grow up” very rapidly, which creates a fair amount of natural attrition, but we see no age trends relating to this. I’m guessing we are a young team compared to peer companies … our lead engineer is in his early 40s, and we have key engineering leadership roles filled by very talented individuals in their 20s and 30s.
I am the “recruiter-in-chief,” probably the most important aspect of the role. It’s all about the network. I have worked with some people in this company for decades. We also have seven locations across the country, each with a fully functioning networked Software Integration Lab [SIL], and we seek the top talent in each area. We have a robust summer intern program (my favorite by far). These “kids” are amazing, and we hire many of them. We had one intern that we could not place, but he kept coming to work at intern wages, learning and doing a great job. You cannot beat that kind of commitment, and, yes, we ultimately hired him. MES
Travis Slocumb is CEO of Pacific Defense and worked with Emerald Lake Capital to found the company in 2020. At Pacific Defense, Travis leads a proven team of highly skilled engineering talent that solves complex customer challenges with integrated electromagnetic hardware and software solutions. He has experience as a product line general manager, strategist, business development leader, and chief technology officer. Prior to his role as CEO of Pacific Defense, Travis launched and led the Electronic Warfare Systems (EWS) business unit at Raytheon Technologies, including programs like Next Generation Jammer, ALR-69A, ALR-67-V3, towed decoys, EWPMT, and several strategic classified efforts. He also served as VP of Business Development and Strategy for Raytheon’s Space and Airborne Systems segment. Travis earned a bachelor’s degree in mathematics from the College of William and Mary in Virginia.
Pacific Defense
https://www.pacific-defense.com/
RF
By Jason Timpe
The future of electromagnetic spectrum operations (EMSO) used in the military requires a new approach to how these systems are architected. Given today’s technologies, a single-chip architecture offers the best approach by integrating radio-frequency analog front end, traditional field-programmable gate array logic, dedicated DSP [digital signal processing] hard IP blocks, and vector processing cores to provide a truly flexible and power efficient single-chip computing solution that is well-equipped to be the cornerstone of any future EMSO system.
Today’s contested and congested electromagnetic spectrum requires new solutions to meet increasingly demanding electromagnetic spectrum operations (EMSO) mission requirements. Wider bandwidth and frequency agility are increasingly necessary for these systems, placing new demands on both the radio-frequency (RF) analog front end (AFE) and the digital signal processing (DSP) portions of the system.
Traditionally, these two portions of the system have been conceived, designed, and implemented separately because the engineering skill sets are different and usually organized in distinct and separate groups. The connection between
the AFE and DSP processing is usually accomplished through a JESD204 SERDES [standardized serializer/deserializer] interface. Even though the segregated design approach provides more freedom for each, it is becoming necessary to consider the analog and digital portions in a unified way.
Field-programmable gate arrays (FPGAs) provide a very efficient way to implement custom, reconfigurable, low-latency DSP algorithms; however, increasing demands of EMSO systems require massive amounts of DSP compute resources in a size, weight, and power (SWaP)friendly form factor that is not possible with the traditional FPGA and discrete AFE approach.
Current and future EMSO systems need increased analog performance and more
efficient DSP in a SWaP-optimized design, while maintaining the customization and low latency of a traditional FPGA-based solution. Industry trends show that a singlechip device architecture, which integrates a variety of compute devices into a single silicon device, is the best way to address both the demanding analog and signal processing requirements of modern EMSO systems with today’s technology.
Analog system requirements: bandwidth, latency, SWaP
Traditional EMSO system designs separate the RF AFE from the DSP system and use a JESD204 interface to move the data between the two. While this approach works for older systems, the extremely high sample rates and low latency required by modern EMSO systems break the traditional architecture. (Figure 1.)
Moving such a large amount of data requires a very fast serial bus with many lanes, all of which consume significant amounts of power and add latency to the system in the serialization and deserialization of the data. Even when two devices are integrated within the same package in a multi-chip module (MCM), there could be limitations to how many pins can be allocated to the bus, placing limitations on the bandwidth of the data.
Another solution is to use downconverters and other signal processing within the AFE to limit the amount of data sent to the downstream DSP device. Because this signal processing is built into hardware, it can be more efficient than a software or FPGA-based solution doing the same function. However, the designer is forced to make choices when developing the AFE that might not be appropriate for a given application. This approach also leaves little room to modify the behavior of this signal-processing chain. Additionally, the bandwidth limitation between the two devices means that while the overall system might have wideband performance, this is limited only to the portion of the signal-processing chain contained in the data converter.
One approach that removes these constraints is to fully integrate the RF AFE within the DSP device, creating a single-chip AFE and DSP solution that eliminates any serialization or deserialization. This move results in the lowest possible latency between the RF and the DSP system. Furthermore, there is no question of pin or bus limitations between the devices because they are integrated into the same device.
Digital system requirements: throughput, flexibility, SWaP
Like the RF analog portion, the DSP requirements for EMSO are also evolving and creating new challenges for system designers, such as the need to process a much wider instantaneous bandwidth (IBW). This actually increases the overall signal-processing
requirements more than the linear increase in IBW, leading to the need to use larger FPGAs or multiple FPGA-based solutions to meet the DSP requirements.
One solution is to implement the signal processing in an application-specific integrated circuit (ASIC). This option would be a much more DC-power-efficient implementation than an FPGA; the downside is that ASIC development is expensive, time-consuming, and inflexible. It is also possible that during development, or even after deployment, new threats or requirements emerge. If the signal processing is based on an ASIC, the functionality is fixed, making modifications both challenging and costly.
This reality is why FPGAs are so useful to EMSO systems and are in fact widely deployed in the defense and aerospace arenas. While they don’t provide ASIC-level performance, FPGAs far exceed the performance of software solutions and are flexible enough to adapt to changing requirements, shifting workloads, and mission profiles. Caveat: While traditional FPGAs provide low latency and configurable DSP compute power, they suffer from net compute efficiency with regards to DC power. Solving the DSP demands of current and future EMSO requires very large FPGAs, or even multiples, thereby exceeding the SWaP constraints of systems.
To address the massive DSP demands and SWaP requirements of EMSO systems, key DSP IP blocks can be implemented in ASIC-like hard IP blocks to reduce total power consumption and increase DSP compute. These hard IP blocks can then be integrated with an FPGA fabric to provide more DSP compute at a lower dynamic
By applying the same strategy, but targeting DSP functions used for EMSO, a lower-power solution can be realized.
power consumption. Figure 2 shows the increase in dynamic power compute efficiency for two common DSP building blocks: FFT [fast Fourier transform] and channelizers.
Hard IP blocks are included in programmable logic for common functions like memory controllers, protocol IP, and others to reduce power and improve overall customer solution for years. By applying the same strategy, but targeting DSP functions used for EMSO, a lower-power solution can be realized. Of course, if the solution only contained hard IP blocks, similar flexibility constraints of an ASIC-like solution would exist.
The best approach is integrating multiple compute types in a single-chip solution with the RF AFE to provide a balanced solution that can meet RF analog, DSP compute and SWaP requirements. (Figure 3.)
Single-chip device optimized for EMSO AMD Versal RF Series devices take a single-chip architecture approach that integrates RF AFE along with four different types of compute within a single device.
First: the traditional FPGA programmable logic of DSP slices and lookup-tables (LUTs). These provide the flexibility needed to adapt to changing requirements and mission profiles. Second is the hard IP blocks to handle the increased DSP throughput requirements. Select DSP functions implemented in dedicated hard IP blocks includes 4 GS/sec FFT/iFFT, the channelizer, polyphase arbitrary resampler, and the LDPC [low-density parity check, a class of error-correction codes] decoder. Implementing these key DSP functions in dedicated IP blocks delivers notably
better power and area savings compared to soft-logic implementations and enables more compute power in the same physical area to meet constrained form-factor requirements.
Third are the AI engines for DSP, which are an array of SIMD [single instruction, multiple data] vector processors that can perform several signal-processing functions – including filters and beamforming – and can also handle neural networks. Because they include a floating-point path, they could also be used downstream of the other signalprocessing blocks, adding dynamic range for these later stages. The total DSP compute power provided by the top of stack Versal RF Series devices would require multiple FPGAs for an equivalent computing solution. The amount of programmable logic required to meet processing requirements is also minimized, further reducing size and weight.
Finally, the devices include an Arm subsystem – both standard application cores as well as real-time cores – that turns them into true software-defined, adaptive system-on-chips, providing drivers for programming the integrated high-resolution RF data converters, as well as a means of controlling the rest of the digital signal processing fabric.
Bringing it all together
The future of EMSO requires a new approach to designing systems: A singlechip architecture integrating RF AFE, traditional FPGA programmable logic, dedicated DSP hard IP blocks, and vector processing cores can provide a flexible and power efficient single-chip computing solution that can serve as the backbone of a future EMSO system. MES
Notes
1 Based on an AMD internal analysis to calculate the theoretical DSP compute (including hard IP, AIEs, and DSPs) offered by the Versal RF VR16xx devices, and on AMD engineering projections in November 2024, using the hard IP functions in Versal RF Series devices to measure dynamic power versus the total power calculation of an AMD soft logic implementation, as measured with AMD Power Design Manager (2023.2.2), based on AMD Vivado 2023.2.2 IP catalog.
Jason Timpe has been the Radar/EW System Architect for AMD for the last four years. In this role, he creates aerospace and defense requirements for the RF product line, develops radar signal processing reference designs, and drives solutions for real-time signal processing. Before he joined AMD, Jason worked for BAE Systems doing FPGA, mixed-signal, and digital design on IR and EW systems. He also worked for Sun Microsystems and Northrop Grumman; he served as a sector-wide Xilinx and Vivado software expert within Northrop Grumman. Jason has a master’s degree in electrical engineering and bachelor’s degrees in electrical engineering and literature from the Massachusetts Institute of Technology.
AMD • https://www.amd.com/en.html
NASA first selected our chip resistors for a mission to Jupiter and Saturn that launched in 19 7 7 and is still operating in interstellar space. Our chip resistors continue to be selected for high reliabilit y applications on Ear th and in space On Ear th, our resistors are selected for mission critical applications in militar y weapon and defense systems In space, our chips are found in weather and communications satellites and on missions to Mars, Jupiter, and Pluto
Mission Critical? Choose State of the Ar t resistors.
St a te o f the A r t, Inc.
R E SIS TI V E P RODUC T S
Made he USA .
RF and microwave designs for electronic warfare
By Tibor Urbanek
Using qualified components is vital to mission success in military- and aerospace-employed design and deployment, particularly for microwave technology in space termination applications. The parts-qualification process tests that components provide reliable performance for the lifespan of the mission, improving performance and safety. By adhering to industry standards – such as MIL-DTL-39030, which covers the qualification and general requirements for coaxial and stripline electrical loads for testing – and leveraging advanced testing and evaluation methods, designers and engineers can develop reliable and effective space hardware that can withstand the harsh conditions of space.
When designing for space applications, the reliance on qualified components must be balanced. At any given moment, lives may depend on the speed and accuracy of communications. The demanding environment of space missions, characterized by extreme temperatures, high radiation levels, and the
absence of atmosphere, necessitates using components that are efficient and thoroughly vetted for reliability and performance.
Qualified parts for space (QPS) components, specifically those for microwave technology in space termination and attenuation applications, must undergo a meticulous part qualification process for the success and safety of space missions.
Build with the goal in mind These components are essential building blocks in aerospace design, serving as
the foundation for the reliability and functionality of spacecraft. Integral to space missions is microwave technology, especially for applications involving communication, radar, and telemetry, due to its ability to transmit data over long distances with minimal signal loss.
SubMiniature version A (SMA) terminations are used to maintain the performance of microwave circuits by terminating unused ports. SMA terminations absorb microwave energy, preventing signal interference and reflection. The use of QPS terminations in these applications ensures the integrity of microwave systems and affirms that these components can withstand harsh space conditions and perform reliably throughout the mission. (Figure 1.)
QPS attenuators and terminations undergo intense qualification and screening guided by MIL-DTL-39030 and MIL-DTL-3933, which specify the performance and reliability criteria for military and aerospace applications. This testing is conducted under simulated space conditions, including thermal cycling, vibration, and radiation exposure. These tests are designed to identify any potential weaknesses and confirm that the components can withstand the stresses of space travel. Parts are engineered and tested to meet or exceed 1% total mass loss (TML), and 0.1% collected volatile condensable materials (CVCM).
The qualification of QPS attenuators and terminations involves comprehensive testing guided by military standards. For QPS attenuators, the qualification process is guided by MIL-DTL-3933 level T, focusing on the rigorous demands of space applications. Note: While our qualification was based on MIL-DTL-3933 level T, attenuators meet the requirements of MIL-DTL-3933/14, /16, and /25 for parts ending with N and S. The T-level is associated with space parts requirements. (Table 1.)
For QPS Terminations, the qualification is guided by MIL-DTL-39030, particularly /3 and /6. Since no standard exists for space-qualified terminations under MIL-DTL-39030, we developed our own qualification process. This process is partly based on MIL-DTL-39030 and partly on MIL-DTL-3933 level T, ensuring that these terminations can perform reliably in space conditions.
MIL-DTL-3933 and MIL-DTL-39030 offer two screening levels: N (non-screened) and S (screened). For space applications, our company created three distinct screening levels for space attenuators and terminations: A, B, and C. These levels correspond to different degrees of testing rigor, with Level C being the most stringent and recommended for all spaceflight applications. Each screening level is tailored to ensure that the components meet the specific requirements of their intended application.
› Level A is recommended for nonflight applications, such as preflight system evaluation.
› Level B is the absolute minimum testing recommended for spaceflight applications, such as low orbit satellites, which may need cost-effective space terminations.
› Level C is the highest level of screening, recommended for all spaceflight applications and deep space missions.
in space missions
QPS attenuators and terminators have been integral to several high-profile space missions, including the Emirates Mars Mission, Parker Solar Probe, and Europa Clipper. These components have demonstrated their reliability and performance in the harsh conditions of space; their ability to maintain signal integrity and manage power levels has proven critical in these challenging environments.
examination of part qualification
The part-qualification process is a comprehensive procedure to test that components meet the strict controls of aerospace applications. Design must account for factors like radiation resistance, thermal stability, and mechanical robustness. For microwave components used in space-termination applications, the standards for qualifying components include minimal signal loss and reflection, ability to maintain function under extreme temperatures and radiation levels, and durability against mechanical stresses such as vibration and shock.
Using qualified components directly affects the performance and safety of space missions, as microwave components must perform reliably to guarantee effective communication and data transmission. The challenges associated with microwave frequencies in space include signal attenuation, interference, and thermal management. Qualified components help mitigate these challenges, ensuring that microwave systems operate optimally.
Space-qualified SMA terminations are used in satellite communication and telemetry systems to reliably terminate signals and prevent reflection. Reliable microwave components are crucial for long-distance communication with Earth in deep-space missions. SMA terminations are also used in thermo-vacuum chambers to simulate space conditions when testing the performance of microwave systems.
Signal attenuation – the loss of signal strength over distance – can be considerable and detrimental in space. Qualified components are designed to minimize attenuation, ensuring strong and clear signals. Because electromagnetic interference can disrupt microwave signals, space-qualified components are shielded and designed to minimize such interference. Moreover, microwave components generate heat, which must be managed in the vacuum of space. Qualified components are tested for thermal performance to operate within extreme temperature ranges. (Figure 2.)
Successfully navigating the challenges of space exploration requires a meticulous approach to component selection, testing, and integration. Ensuring that all components can withstand the harsh conditions of space is paramount for aerospace engineers. This reality involves several key strategies:
1. Thoroughly test and evaluate: All components must undergo comprehensive testing to simulate the extreme conditions of space. This move verifies that each part can perform reliably throughout the mission’s duration.
2. Adhere to standards: It is essential to understand and follow industry standards for component qualification. Standards such as MIL-DTL-39030 provide detailed guidelines for ensuring components meet the necessary performance and durability requirements.
3. Collaborate with trusted vendors: Partner with reputable vendors to source reliable, space-qualified components. These partnerships provide access to highquality parts that have been tested and certified.
4. Continuous monitoring and updates: Regularly reviewing and updating components is necessary to keep pace with technological advancements and evolving
standards. This proactive approach helps maintain the reliability and effectiveness of space systems.
By implementing these strategies, engineers designing for space applications can effectively navigate the complexities of part selection, integration, and compliance. This consistency will drive the success and safety of their space missions, particularly in the critical area of microwave frequency operations.
From the earth to the sky –and beyond
Qualified components, meticulously vetted and certified for their intended applications, play an indispensable role in ensuring the safe completion of space missions. Through rigorous part qualification and adherence to industry standards, QPS terminations and attenuators are designed to meet the stringent requirements of space and militaryindustrial applications. MES
Tibor Urbanek, Product Manager at Cinch Connectivity Solutions, has nearly 30 years in RF and microwave design and leads three product lines at Cinch Connectivity: Midwest Microwave, Semflex, and ModICE. He holds a Bachelor of Science degree in networking and telecommunications and an MBA from the University of Phoenix. Readers may reach the author at Tibor.Urbanek@ cinch.com.
Cinch Connectivity Solutions https://www.cinch.com/
Behlman introduces the first test-proven VPX power supplies developed in alignment with the SOSA Technical Standard. Like all Behlman VPXtra® power supplies, these 3U and 6U COTS DC-to-DC high-power dual output units feature Xtra-reliable design and Xtra-rugged construction to stand up to the rigors of all mission-critical airborne, shipboard, ground and mobile applications.
> 6U power module developed in alignment with the SOSA Technical Standard
> Delivers 1050W DC power via two outputs
> VITA 46.11 IPMC for integration with system management
> 3U power module developed in alignment with the SOSA Technical Standard
> Delivers 800W DC power via two outputs
> VITA 46.11 IPMC for integration with system management
By Brian Kimball
Mixed-signal devices have seen an increase in popularity as design techniques and process technologies continue to advance. However, end users still find themselves forced to make difficult trade-offs between bandwidth, dynamic range, and power and then must be committed to their decisions for the lifetime of the device. Next-generation modular RFSiP designs will introduce a new degree of freedom to address diverse signal-processing applications.
Mixed-signal and FPGA (field-programmable gate array] technologies are the two most foundational elements to any RFSiP [radio-frequency system-in-package). Although FPGAs are renowned for their use across a wide variety of applications and situations, the application absoluteness of mixed-signal offerings is far more
challenging. Mixed-signal designers, bounded within the laws of physics, are forced into making consequential compromises between bandwidth and RF
noise. To alleviate this inherent shortcoming, a malleable mixed-signal architecture is necessary to facilitate improved adaptability for RFSiPs.
Mixed-signal devices, responsible for analog-to-digital conversion and digital-to-analog conversion (ADC/DAC), have enjoyed major advancements in recent years. Despite the rapid breakthroughs and evolution, however, mixed-signal end users are still forced into making difficult tradeoffs amongst bandwidth, dynamic range, and power. Prioritizing bandwidth to collect more data leads to escalating susceptibility to noise and decreased signal quality. Conversely, shifting concentration to
improved dynamic range leads to a narrower bandwidth, thereby restricting the amount of data. Further compounding matters, low power is averse to both bandwidth and dynamic range. This back-and-forth contention is depicted in Figure 1 as a three-way duel involving bandwidth, dynamic range, and power.
To date, the status quo for RFSiP devices has been to commit to a particular mixedsignal die and then be saddled with that decision over the course of its lifetime. That mixed-signal die selection could either: (1) excel in bandwidth at the expense of dynamic range, (2) excel in dynamic range at the expense of bandwidth, or (3) make comprises between bandwidth, dynamic range, and power. Although the FPGA fabric itself is wide-ranging and ubiquitous, the rigidity and immobility in mixedsignal die choice stymies RFSiPs from being the all-embracing, application agnostic signal processing platform they’re capable of becoming. Concordantly, mixed-signal die innovation is happening on faster timescales than its companion FPGA technologies. These speedily progressing mixed-signal entrants come in singularly unique footprints while their FPGA counterparts tender highly flexible, scalable die with ascendancy across a common footprint schema. In aggregate, these circumstances only intensify the likelihood of post-decision dissonance in mixed-signal die choice for next generation RFSiPs.
Altering attention to the application space, many mixed-signal die offerings are deliberately contrived with aerospace and defense operations in mind. These assorted applications are out of rhythm with one another regarding bandwidth, dynamic range, power, and channel mix. Cases in point, EW [electronic warfare] denies an opponent’s use of the electromagnetic spectrum by jamming enemy communications, disrupting radar systems, and protecting friendly forces from electronic attacks. Consequentially, EW applications crave mixed-signal technologies dedicated to expansive spectral ranges, ultrawide bandwidths, and brisk response times.
Contrastingly, ISR [intelligence, surveillance, and reconnaissance] concentrates more on information gathering to gain a clearer understanding of the adversary’s capabilities. ISR missions commonly gravitate to collection of target-quality data via penetrating and persistent monitoring. Predictably then, to strike a balance between seeing as far and as wide as possible, RF ISR yearns for mixed-signal technologies equally hierarchizing dynamic range and bandwidth attributes.
Dynamic range addresses the “far” aspect by increasing the range of signal strengths that can be effectively processed, while bandwidth addresses the “wide” aspect by increasing the difference between the upper and lower frequencies in a continuous
band. Increasing in divergence from EW, communications operations focus on enabling the flow of information. This information-sharing deprioritizes broad searching proficiencies for ameliorated dynamic range. Accordingly, mixed-signal technologies devoted to higher SNRs [signal-to-noise ratios] will excel here because enhanced SNR makes signals clearer and easier to interpret as opposed to signals being corrupted or obscured by noise.
Further aggravating the application-space dilemma, all three of the previously listed cases are subjugated to inordinately dissimilar SWaP [size, weight, and power] envelopes based upon the numerous potential platforms in which they’re performing. This volatility sensibly ripples its way down to the RFSiP. As a result, the ideal RFSiP needs to be capable of acclimating and responsively yielding to its habitat, even within the same application space.
The tile approach for flexible mixed-signal solutions
TriMate’s performance meets or exceeds legacy MIL-DTL-38999 connectors yet they are manufactured in a smaller, lighter, and easier-to-install connector package.
TriMate is offered in three different forms to support different applications: Threaded, Push/Pull, & Break Away — all three plug styles mate with the same receptacles.
The way forward for mixed-signal die flexibility is to introduce modularity within the RFSiP itself. By generating this new degree of freedom for mixed-signal die selections, next-generation RFSiPs can more nimbly wield the power of adaptation to address a broader range of signal processing applications across a greater diversity of onerous platforms. The strategy for attaining intra-RFSiP modularity for mixed-signal die involves a so-called tile concept as depicted in Figure 2.
The decisive key to modularizing an RFSiP is the calculated dissection of its smaller constituents, in this case mixedsignal tiles, into well-defined and stable interfaces. Stable interfaces can only be achieved with the proper foresight of the desired product variants over an extended product life cycle.
In a survey of the emerging mixedsignal die market over a three-year time horizon (2024 to 2027) in close coordination with best-of-breed mixed-signal providers, it was found that the mixedsignal die candidates all had strong similarities to one another. This correspondence helped assuage inclusivity pressures across an eclectic variety of ensuing mixed-signal die offerings. The amalgamated data across mixed-signal vendors helped steer Mercury Systems toward the adoption of a 19.5 mm by 23.5 mm tile architecture. Importantly, every tile forthcoming adheres to this singular, common electromechanical footprint to achieve modularity.
Creating a new RF system-in-package
These inaugural tiles leverage the same organic substrate material as the base. This is possible because the chosen bump pitches and associated high-speed serial interfaces don’t need to use any of the more exotic materials, techniques, or methodologies. This materials symmetry favorably reduces cost, risk, complexity, and timeline, while widening the aperture for capable tile vendors as well.
At the outset these tile interfaces will adhere to JESD204B/C [the Joint Electron
Device Engineering Council’s current serial standard], since that’s what the market currently dictates. In the years ahead, it’s anticipated that UCIe [Universal Chiplet Interconnect Express] will transition into the serial interface of choice for SoCs [systemon-chip]. Murkiness remains, however, around the specific version of UCIe that will be more universally accepted.
There are very prominent differences between the two vying UCIe alternatives: UCIe Standard is cost-effective and flexible, while UCIe Advanced is power-efficient and adept at higher bandwidth densities. UCIe Standard packages use organic substrates with metal traces, support channel lengths up to 25 µm and have a minimum bump pitch of ~110 u (or μm, shorthand for micrometers). UCIe Advanced packages use silicon interposers or bridges, support channel lengths up to 2 µm, and have a minimum bump pitch of ~45 u. Given the physical constraints imposed by UCIe Advanced, the use of UCIe Standard will be the likely choice that sophisticated multichip packaging suppliers will pursue. This probable choice will undoubtedly result in chiplet suppliers ensuring their product offerings include wide support for UCIe Standard.
The novelty in the tile approach is the concerted effort toward achieving mixed-signal modularity. Any cloudiness surrounding comprehension of a modular RFSiP will wane over the course of this maiden program, retiring risk until opacity subsides. Once the risk wanes, it may ostensibly be prudent to consider driving intra-RFSiP modularity as an open standard. Modular RFSiPs can unlock adaptability, reusability, and ease of upgrades. All these things are welcomed, urgently required, and important for today’s modern aerospace and defense applications.
Brian Kimball is a Systems Architect within the Advanced Concepts Group of Mercury Systems. Kimball has over 25 years of experience in RF, mixed-signal, and digital processing design for defense and aerospace applications. Key domain proficiencies center on end-to-end EW, ISR, comms, and radar architectures for various platforms spanning airborne, ground, surface, subsurface, and space.
Systems https://www.mrcy.com/
By Lou Rojas and Steve Axt, Tyto Athene
Ushering in a new generation of Internet Protocol (IP)-based communications has been a primary goal for the U.S. Department of Defense (DoD). Since the end of 2021, the DoD has been working toward network and voice modernization that relies on IP-based services instead of time division multiplexing (TDM) circuits. The department also set a policy that eliminates the use of TDM and requires the migration of all component mission requirements for transport to IP-based services by March 2025.
The director of the Defense Information Systems Agency (DISA) referenced this transition in his vision for a more unified network, noting that replacing outdated TDM circuits with IP-based infrastructure is a key action. For decades, TDM circuits and services have been central to the DoD’s communications infrastructure. While it has served its purpose well, these legacy systems are costly to maintain and inadequate for today’s communications needs.
Clear communication between teams and personnel will make or break the success of the mission at hand and support warfighters in-theater. Using a holistic approach to properly transitioning to IP-based circuits for communications transmission offers the DoD substantial operational benefits including enhancing command, control, communications, computers, intelligence, surveillance, and reconnaissance (C4ISR) capabilities; strengthening cybersecurity posture; and preparing the department for future technological advancements.
Voice modernization: crucial to the mission
Implementing IP-based circuit modernization requires a shift in technology, training, culture, operations, and maintenance – understanding the true impacts and benefits of IP-based communication and its further effects are important. IP-based circuits and transmission provide a flexible, scalable, and secure communication environment that enhances mission readiness and supports real-time command and control.
TDM technology replacement has been a long time coming across the industry and many carriers are participating in the dismantling of all TDM-related products and services – as asymmetrical warfare becomes more data-intensive and reliant on realtime communication, the need to replace outdated systems has become essential.
Modernizing DoD’s voice architecture fills the need for users to collaborate from anywhere, at any time, and from any device. In moving to IP-based connections, warfighters
can be mobile and connected through the internet with the ability to communicate anywhere. IP-based telecommunications systems enable the warfighter to keep the same phone number, even when moving to a different command, post, station, or base through the use of VoIP endpoints and soft clients.
There is a security benefit to voice modernization as well. Moving to networked systems creates interoperability, enhanced visibility, and added security for communication operations. As cyberattacks grow in complexity, modernizing communication systems is crucial for protecting classified information and ensuring resilient and secure communication. The IP-based DoDIN [Department of Defense Information Network] also enables monitoring, patching, and consistent updating as part of a cybermaintenance routine.
IP-based networks create a higher capability set for users as well, with more advanced and always-connected technologies. Such networking-based use supports operations across new geographic locations and accommodates additional users, which is not possible through TDM due to cabling issues, connection types, or bandwidth limitations.
The robustness and flexibility of IPbased telecommunications networks
enable mission support across globally dispersed enterprise environments. As voice modernization across the DoD is transitioning to IP-based approaches, it is essential to have a roadmap in place that enables defense teams to easily and effectively shift use to meet specific mission requirements without disrupting the mission.
Establishing a transition roadmap
The TDM decommissioning process is more than just the standard telephone private branch exchange (PBX) switch. Teams must consider telephone management and accounting systems, voicemail, conference bridge, required ancillary equipment (SYSLOG, backups, network time protocol, domain name systems), 911, and land mobile radio.
The biggest pain point in the whole TDM-to-IP modernization is the fact that defense groups can’t just move the telephone PBX – everything else that interacts with the telephone system has to be migrated onto the same IP-based network. This reality creates an enormous amount of work, followed by a necessity of having all DoD entities interconnecting properly, between different agencies, battalions, program offices, and more.
The physical effort of upgrading to a new system is not difficult, but the process of getting everyone on the same page –clear lines of responsibility for navigating and sifting through hundreds of lines of cybersecurity scans, STIGs [Security Technical Implementation Guides], and additional requirements – is a challenge.
The DoD and its branches must fully understand, operate, and sustain legacy technology, while at the same time using modern technologies to transition with the least amount of risk. The ability to effectively translate the programs and processes from old systems to new, and test them, is key for the continuation of mission operations.
To meet the DoD’s goals on modernization and the migration onto IP-based services by March 2025, defense agencies must use a clear-cut roadmap:
› Assessment and planning: Establish a customized plan by conducting a
detailed audit of existing TDM systems, aligning stakeholders and performing a business-impact analysis.
› Proof of concept and pilot: Validate the selected IP-based solution in a controlled environment with minimal risk and deploy it in a limited pilot.
› Incremental rollout and transition: Deploy the IP-based systems across the organization, prioritizing low-risk areas and maintaining service continuity.
› Full transition and optimization: Complete the migration of all services and optimize network performance to enhance scalability, speed, and resource efficiency.
› Continuous improvement and innovation: Ensure the network evolves with the business, enabling future technologies like 5G and AI [artificial intelligence] to be integrated smoothly.
The modernization process to IP-based systems is not static; transitioning from legacy TDM systems to modern IP-based networks requires a comprehensive and risk-aware approach to ensure operational continuity, minimize disruptions, and remain efficient all while modernizing for the future. TDM systems operate on outdated infrastructure, offer limited scalability, increase cybersecurity risks, and require high maintenance that carries high costs.
DoD leadership has recognized the benefits of transitioning to IP-based communications as a critical step to modernizing communications infrastructure, supporting better decision-making in the defense theater and combat.
Lou Rojas is Senior Director, Marine Corps Business Group at Tyto Athene. Steve Axt is Unified Capabilities Architect at Tyto Athene.
Tyto Athene https://gotyto.com/
The McHale Report, by mil-embedded.com
Editorial Director John McHale, covers technology and procurement trends in the defense electronics community.
By Nick Mistry, CISO and SVP, Lineaje
It’s in the U.S. Army’s nature to act with precision and synchrony when executing complex tasks such as multi-domain operations, training, and logistics, so why would we expect anything less from the software that powers it?
To uplevel the integrity of software used by the Army, the Army’s Assistant Secretary for Acquisitions, Logistics, and Technology issued a memo in August 2024 mandating software vendors provide a software bill of materials (SBOM) for all new software contacts, including commercial off-the-shelf (COTS) materials, by February 2025. The policy aligns with the Biden administration’s Executive Order (E.O.) 14028, which requires that vendors working with federal organizations to attest to the security for all software meet the newly defined NIST Secure Software Development Framework (SSDF) requirements and help move the industry toward improving
federal supply-chain security. However, we have a long way to go – a full 91% of organizations experienced a software supply-chain attack in 2023 alone, according to a recent study from cybersecurity firm Data Theorem.
As part of E.O. 14028, organizations that worked with federal agencies were mandated to fill out the U.S. Cybersecurity & Infrastructure Agency’s (CISA) Secure Software Development Attestation Form. The form reinforced the four “secure by design” principles:
› Ensuring security controls are in place to protect software development environments.
› Taking steps to actively assess the trustworthiness of third-party components in software.
› Maintaining provenance data for all components, including third-party and open source.
› Establishing a robust vulnerability-management capability.
Despite ample time to complete the form and adhere to this particular requirement of E.O. 14028, research conducted by Lineaje at RSA Conference 2024 revealed that 80% of impacted organizations were unprepared to meet the initial deadline of June 11, 2024. Even worse, the survey found that 65% of security professionals hadn’t even heard of E.O. 14028. Budget limitations and a lack of staffing resources markedly slowed software supply-chain security and maintenance measures.
If software vendors fail to comply with the SBOM mandate for the Army dictated in the memo, the country’s national security is at stake. With faulty software, threat actors can easily penetrate the U.S. Army’s network of partners, or worse, the Army itself.
At the heart of the software compliance mandates is the SBOM. The SBOM provides a holistic, transparent view of an organization’s software supply chain by detailing all of its software applications’ components, libraries, and dependencies. With an SBOM, security teams can see the level of risk in each part of their software, thereby making it easier to detect vulnerabilities early and prevent attacks. Furthermore, SBOMs are critical to identifying or detecting sources of compromise in the supply chain by ensuring the SBOMs provide accurate source or provenance information and a requisite component level to enable independently verifiable supply-chain integrity in the software. This is especially important for the U.S. Department of Defense (DoD) due to the nature of its systems and the data it stores. If a threat actor penetrates the Army’s networks, our national security is at stake.
The new SBOM mandate from the Army memo also prioritizes SBOMs over attestations. Army leadership views SBOMs as the most efficient method for ensuring supply chain security. As we get closer to February 2025, software providers looking to earn coveted contracts with the Army must work on generating, managing, and sharing accurate SBOMs.
Ahead of the February 2025 deadline, software providers need to take the following steps:
› Use a solution that has comprehensive SBOM generation. SBOMs must be automated in line with the National Telecommunications and Information Administration (NTIA) standards. Having a solution that has comprehensive SBOM generation ensures all opensource, third-party, and customdeveloped software components are accounted for and meet the guidelines.
› Have visibility into contracts and subcontractors’ software supply chains. Subcontractors are included in the new policy, so software providers must be able to track, share, and manage SBOMs across multiple vendors and partners to solidify compliance across the entire ecosystem.
› Be proactive with vulnerabilities. Organizations need to not only identify vulnerabilities but must also take action to fix them
quickly – even for open-source code that has no available patches. Software providers must have the tools in place that provide solutions.
› Create a secure channel to share SBOMs. Software providers should have tools that provide secure channels to share SBOMs and security attestations with the Army and other federal agencies and that maintain confidentiality and software integrity – all while meeting obligations.
› Have an SBOM repository. Software vendors need to have a central repository for all SBOMs, so that the information shared with customers is controlled, and security teams can better manage access privileges.
The new SBOM mandate from the Army has the potential to create safety and security for U.S. armed forces, ensuring they are better protected against the increase in cyberthreats. According to the U.S. Cyber Command, 20% to 30% of global cyberattacks from advanced persistent threat (APT) groups have targeted defense or military institutions. With the software supply chain being one of the top three cybersecurity concerns, according to information from the Enterprise Strategy Group, it will be critical for the Army to keep the supply chain top of mind over the coming years. By having the tools in place to streamline visibility into the components of the software, create efficient SBOM creation, and manage vulnerabilities, software vendors can ensure compliance with the ever-evolving DoD requirements and stay ahead of the curve.
Nick Mistry is a Senior Vice President and CISO at Lineaje.
Lineaje https://www.lineaje.com/
Sponsored by Micross
During this webcast, industry experts in high-reliability RF electronics design, packaging, testing, and qualification of hybrid multi-chip modules (MCM) provide the latest options and best practices for realizing the optimal RF/mW for space and high-reliability applications. Also covered: the considerations and deliverables required to deploy RF MCMs in hi-rel space applications plus insight into challenges and solutions faced by designers and engineers. (This is an archived event.)
Watch this webcast: https://tinyurl.com/yc542eay
By Shane Fry, RunSafe Systems
Embedded systems form the backbone of modern defense capabilities, controlling everything from weapons systems and communications to flight controls and mission-critical sensors. As adversaries become increasingly sophisticated with regard to cyberwarfare, securing the software within these embedded systems is necessary to maintain military advantage and operational resilience.
As modernization continues, there are three unique challenges to securing embedded systems that will need to be addressed to enable military systems to not only perform their intended functions, but also resist cyberattacks that could compromise their integrity or availability.
1) The trillion-dollar code problem
A pressing challenge for the security of military embedded devices is the amount of existing memory-unsafe code that needs protection. Because many embedded military applications are written in C/C++, they are susceptible to memory-based vulnerabilities, which represent up to 70% of exploitable vulnerabilities in embedded software.
Over the last several years, CISA [the U.S. Cybersecurity and Infrastructure Security Agency] has emphasized the need to rewrite code into memory-safe languages to defend critical infrastructure from attack, particularly by nationstate actors. However, for the vast majority of weapons systems, rewriting code is not something that can be easily accomplished. The cost to rewrite the code base for military weapons systems would run into the billions, if not trillions, of dollars. Beyond the astronomical cost, such rewrites would require extensive testing and developer and engineering resources, potentially disrupting critical defense capabilities and preventing innovation in the capabilities brought to the field.
There are two main options to tackle this obstacle: First, work on selective rewriting by identifying and rewriting critical components in memory-safe languages like Rust. Second, apply runtime protections to protect software in the field from the exploit of memory-based vulnerabilities.
2) Safety-certified systems and security
Safety certification serves as a rigorous validation process for aviation systems. Certifications like DO-178 and DO-330 are designed to ensure the reliability of aircraft components during flight operations. However, it is crucial to note that while safetycertified code is essential, it does not inherently guarantee secure code.
With the risk of exploitation of embedded devices growing, safety and security need to be addressed concurrently. In safety-certified environments, this is easier said than done, as each line of code must be meticulously accounted for and its impact on the system thoroughly documented. Adding a new security feature to secure an aircraft engine controller, for example, would require an extensive, time-consuming certification process first.
The solution lies in developing cybersecurity solutions that can achieve safety certification. Such an advancement would be transformative for securing weapons systems, enabling the protection of critical military assets without compromising safety requirements. Until such solutions are available, development teams must deal with the complex responsibility of balancing safety and security considerations – a situation that becomes increasingly difficult as cyber risks evolve and codebases grow.
3) Securing legacy systems
A third hurdle involves securing legacy systems that remain actively deployed. Legacy systems rely on outdated software that may not be designed to withstand modern cyberthreats, leaving them vulnerable to attack due to lack of updates and compatibility issues with newer security technologies. Additionally, many of these systems are in the sustainment phase of their life cycle, during which major architectural changes are impractical or impossible. Take, for example, the A-10 – the nearly-50-year-old aircraft commonly known as the Warthog – which must implement modern security measures within severe budget constraints.
Essential steps for protecting critical assets and addressing these questions include enforcing cybersecurity requirements for systems in development, conducting thorough vulnerability assessments throughout the operational life cycle, and deploying runtime protections at the device level.
Improving the cybersecurity of embedded systems in military assets will require a shift in perspective. No system is completely immune to attack, and many deployed systems have known security issues that need attention. Organizations can get ahead of these issues now by looking for proactive security measures to protect devices and systems at runtime and by following CISA’s Secure by Design and DevSecOps best practices. Doing so will provide a path forward to significantly enhance the resilience of military embedded systems while preserving their essential operational capabilities.
Shane
Fry is CTO of RunSafe Security.
TECHNOLOGY, TRENDS, AND
Military Embedded Systems focuses on embedded electronics – hardware and software – for military applications through technical coverage of all parts of the design process. The website, Resource Guide, e-mags, newsletters, podcasts, webcasts, and print editions provide insight on embedded tools and strategies including technology insertion, obsolescence management, standards adoption, and many other military-specific technical subjects.
Coverage areas include the latest innovative products, technology, and market trends driving military embedded applications such as radar, electronic warfare, unmanned systems, cybersecurity, AI and machine learning, avionics, and more. Each issue is full of the information readers need to stay connected to the pulse of embedded technology in the military and aerospace industries.
The ANELLO Maritime INS from ANELLO Photonics is an inertial navigation system (INS) designed for maritime applications, leveraging the company's proprietary silicon photonic optical gyroscope (SiPhOG) technology. This system is intended to provide precision and reliability for autonomous surface vessels (ASVs) and autonomous underwater vessels (AUVs) in environments where GPS signals are compromised or unavailable. The INS integrates SiPhOG with an advanced artificial intelligence (AI)-driven sensor fusion engine which gives the tool the performance of high-precision optical gyroscopes with the efficiency of silicon photonics. Its compact form factor and low power consumption (<6W) make it a fit for maritime environments.
Key features include reference-grade position, velocity, and attitude at 100 Hz; high-precision three-axis gyroscopes with unaided heading drift under 0.5º/hour; and dual triple-frequency GNSS [Global Navigation Satellite System] receivers capable of static heading. The system offers advanced GNSS spoofing detection; a robust dead-reckoning ability; and an IP68-rated enclosure resistant to water, corrosion, and salt spray. Additionally, it is engineered to perform under heavy shock and vibration across land, air, or sea, enhancing reliability in challenging conditions.
The Nordic Thingy:91 X is a globally certified, multisensor prototyping platform designed for cellular IoT and Wi-Fi locationing applications. The battery-operated device supports LTE-M, NB-IoT, GNSS, DECT NR+, and Wi-Fi SSID locationing, enabling streamlined development of IoT solutions. At its core is the nRF9151 system-in-package (SiP), which occupies a 20% smaller footprint than its predecessors and supports global operation without U.S. tariffs. Preloaded SIM cards from Onomondo and Wireless Logic enable immediate cellular IoT connectivity, while integration with Nordic’s nRF Cloud platform enables precise device location through its web interface.
The platform is equipped with environmental sensors, motion-tracking capabilities, user-programmable buttons, and multiple antennas. Its 1350 mAh rechargeable Li-Po [lithium-ion polymer] battery, managed by Nordic’s nPM1300 power-management IC, ensures long battery life with accurate fuel gauging. The device also leverages the nRF7002 Wi-Fi companion IC, enabling developers to balance location accuracy and power consumption across cellular (single-cell and multicell), Wi-Fi, and GNSS technologies. This flexibility makes the platform a good fit for asset tracking and other location-dependent IoT applications. The Thingy:91 X is supported by Nordic’s unified nRF Connect Software Development Kit, which offers scalable software tools and developer-centric resources, including training through the Nordic Developer Academy.
Holt Integrated Circuits | www.holtic.com
The SafeAir Raptor from ParaZero Technologies is an autonomous parachute-safety system designed for Anzu Robotics’ Raptor and Raptor T drone models. Intended for use in both defense and commercial applications, the SafeAir Raptor’s sensors are engineered to autonomously monitor key flight parameters, detect failures in real time, and deploy safety measures to minimize risks during uncrewed aerial system (UAS) operations. The system is specifically designed to ensure safe flight over populated areas and protect payloads, making it a tool suited for advanced drone missions in urban and defense scenarios.
It complies with international voluntary ASTM F3322-22 standards, ensuring FAA eligibility for operations over people, and features mechanical flight termination to stop rotors and prevent parachute entanglement during emergency deployments. Weighing just 185 grams (less than half a pound), the SafeAir Raptor is lightweight and integrates with the Raptor series in under ten minutes via plug-and-play installation. Its autonomous capabilities include low-altitude emergency response, with a minimum safe deployment altitude of 40.96 meters (135 feet) and an average descent rate of 4.11 m/sec (13.5 feet/sec). The system is equipped with a black box to store flight data for post-deployment analysis, enhancing operational transparency and diagnostics. Additional features include reusable components, industrial-grade materials, and the ability to reduce operational insurance costs.
The TDM-P240WH5TAGF-RND2, a 24-inch military P-cap [projected capacitive] touchscreen monitor from industrial monitor company Elgens, is a high-performance display solution tailored for extreme environments. Certified under MIL-STD-461G and MIL-STD-810H, the monitor is built to withstand harsh conditions, including shock, vibration, and extreme temperatures ranging from -40 °C to +70 °C. Its robust aluminum bezel and metal case construction, paired with a front-side IP65 rating, protect against dust, water, and other environmental hazards, which aim it at extreme outdoor and industrial use. The monitor also features a 1920 x1080 full-HD LCD display with a brightness of 1500 nits, ensuring excellent visibility even in direct sunlight.
This military-grade monitor includes an antiglare coating with antireflective Mosmite film to reduce reflections and improve clarity. It is equipped with secure, durable connections via metal circular connectors for HDMI, USB, and 24 VDC power input, with accompanying cables for seamless setup. The monitor supports multiple mounting options, including rackmount and panel configurations, enabling flexibility for diverse applications including defense, aerospace, and industrial. It integrates a P-cap touchscreen for enhanced user interaction, and its 90 W power adapter ensures consistent performance across a variety of power systems.
The rugged ATMOS full-stack server is a high-performance, modular computing solution designed for military and industrial environments. Featuring five independent nodes, each powered by the latest Intel Xeon scalable CPUs, the system delivers up to 160 cores and 10 TB of RAM when fully configured. Each node supports 2 TB of RAM, dual 15.36 TB SSDs [solidstate drives], and an optional NVIDIA GPU for intensive computational tasks. With its stackable ATMOS chassis rail system, the server is expandable from one to five or more nodes. Onboard uninterruptible power supply (UPS) battery backups in each node ensure uninterrupted command-and-control (C2) operations on the move, even in power-compromised scenarios.
The system’s ruggedized design operates efficiently at temperatures between -15 °C and +55 °C and can withstand shock, vibration, and high-altitude conditions. Certified to MIL-STD-810F and MIL-STD-810G standards, the server is also compliant with MIL-STD-461F emissions requirements when paired with the optional 461 filter. Its half-rack-width configuration measures 17.50 inches by 12.00 inches by 15.00 inches and weighs under 70 pounds, enabling deployment in compact spaces. Connectivity is robust, with 10 G NIC [network interface card] ports and optional external stackable NAS [network attached storage] for up to 246 TB. Security is ensured by FIPS 140-2 module compliance, ensuring data integrity and protection in sensitive operations.
The Rohde & Schwarz R&S SMW200A vector signal generator and its midrange counterpart, the R&S SMM100A, feature high-performance error vector magnitude (EVM) measurement, addressing the challenges posed by complex modulation schemes in 5G NR FR2 [new radio, frequency range 2] research and RF component testing. The tools are aimed at use in high-demand applications such as power-amplifier testing, 5G research, and wireless-connectivity development.
The R&S SMW200A features an updated user interface, enhanced microwave hardware for higher output power above 20 GHz, and an optional RF linearization software (R&S SMW-K575) that uses digital predistortion technology to optimize EVM at high output power levels, ensuring stability and accuracy across the frequency spectrum. The R&S SMM100A vector signal generator has a low phase noise option (R&S SMM B709), enabling EVM performance better than –53 dB for IEEE802.11be signals with 320 MHz bandwidth. Both models support retrofit options, thereby enabling users with earlier versions to upgrade to the latest specifications through a service and calibration process.
Rohde & Schwarz | www.rohde-schwarz.com
Each issue, the editorial staff of Military Embedded Systems will highlight a different organization that benefits the military, veterans, and their families. We are honored to cover the technology that protects those who protect us every day.
By Editorial Staff
This issue we are highlighting Heroes on the Water (HOW), a 501(c)3 non-profit organization that provides recreational wellness experiences by way of kayaking and fishing to veterans and their families and (as of 2018) civilian first responders. The on-water programs, according to the charity’s website, integrate structured boating and fishing activities in a pressure-free environment, creating opportunities for community building and personal healing.
Veterans and their families often face difficult transitions from active duty to civilian life, often characterized by feelings of isolation and emotional distress. The HOW outdoor programs aim to address these issues, creating a supportive environment where participants can engage with peers who understand their experiences. The peaceful rhythm of the kayak, the bond with nature, and the focus required in fishing bring a calming balance, reducing stress and promoting cognitive healing, according to information from HOW. The outings and outdoor experiences are ways to empower the veterans, promoting resilience, self-confidence, and social connection.
The organization leads two different types of programs: One program type is run by 60 volunteer-led chapters in local communities across the U.S., which provides free outdoor programs and services to veterans, first responders, and their families. The other is by way of the HOW Therapeutic Program, in which the organization consults with the U.S. Department of Defense and Veterans Administration to collaborate with recreational therapists to tailor individual therapies to meet users’ therapeutic needs. Since its founding in 2007 by retired Air Force officer Jim Dolan, Heroes on the Water reports that it has (as of the end of 2024) served 66,297 veterans, service members, and first responders; logged 4,448 days on the water; and organized 50,085 volunteers across the U.S.
For additional information, visit https://heroesonthewater.org/.
De-risking military avionics and ground-based systems with open architectures
Sponsored by RTI and BlackBerry
Modern military systems increasingly rely on high-performance computing platforms to meet the growing demands for software and software reuse. In response, the U.S. Department of Defense (DoD) mandated in 2019 that all new platforms and upgrades adopt a modular open systems approach (MOSA) to accelerate deployment, minimize downtime, and reduce long-term life cycle costs by easing integration and fostering re-use. For avionics platforms, the Future Airborne Capability Environment, or FACE, Technical Standard has been instrumental in enabling MOSA across multiple platforms and is already integrated into deployed systems.
In this webcast, industry experts explore the impact of the FACE approach and examine the technological and bureaucratic challenges that must be overcome to unify standards across the ground-vehicle and airborne domains. (This is an archived event.)
Watch this webcast: https://tinyurl.com/38rw9rpe
Watch more webcasts: https://militaryembedded.com/webcasts/
Embedded
with VITA
By TEWS Technologies
The VITA 93 – QMC mezzanine card standard is set to revolutionize embedded computing systems by bringing higher bandwidth plus high levels of modularity, flexibility, and scalability, leading to enhanced system performance and adaptability.
In this white paper, learn how the new VITA 93 – QMC standard intends to address the inherent challenges in current mezzanine card standards through its innovative QMC architecture, enabling unprecedented flexibility and scalability while maintaining backward compatibility and rugged reliability. In addition, the white paper covers how VITA 93 –QMC builds on lessons learned from previous standards, blending their best features with new capabilities for the future.
Read the white paper: https://tinyurl.com/bdewfmfu
Get more white papers and e-Books: https://militaryembedded.com/whitepapers
Military Embedded Systems focuses on embedded electronics – hardware and software – for military applications through technical coverage of all parts of the design process. The website, e-mags, newsletters, podcasts, virtual events, annual Resource Guide, and print editions cover topics including radar and electronic warfare, artificial intelligence/machine learning, uncrewed systems, C5ISR, avionics, and cybersecurity. Don’t miss any of it!
Military Embedded Systems is also the largest source for coverage of the Sensor Open Systems Architecture, or SOSA, Technical Standard and the Future Airborne Capability Environment, or FACE, Technical Standard. We exclusively produce the once-yearly SOSA Special Edition and FACE Special Edition. militaryembedded.com