
7 minute read
Collaborate or stagnate
the required depth of quay. An idealised fabrication facility, whether in steel or concrete, is likely to require a site of 20 - 30 ha. and a 10 - 15 m draft unless buoyancy devices are used. These requirements are hard to find in one place, and in their absence multiple facilities are needed to fulfil requirements for single large projects, which in itself brings additional logistical considerations.
New facilities will certainly be required, but this is much easier to say than to do. In the UK, a new greenfield port would be considered a nationally significant infrastructure project, and getting it through planning and construction could take up to 10 years. In order to avoid a lack of suitable port infrastructure becoming a bottleneck for the industry, an interim solution is needed.
In the shorter-term, there are opportunities to start generating momentum by splitting activities between existing sites. For example, the Philippines has existing oil and gas, as well as existing LNG infrastructure spread across its thousands of islands that could be repurposed. The downside of this approach is that it will increase costs and risks.
Local supply chain opportunities
Who, exactly, will be doing all this activity? While technology providers have come up with patented solutions for substructures, and turbines are broadly similar to their fixed counterparts – Vestas, Siemens, GE, and others – it is clear that the real challenge – and opportunity – for the supply chain lies in actually building floating wind at a commercially viable scale.
The market’s experience of fixed offshore wind will help, but it can only go so far. For one thing, there are practical differences. Fixed projects have typically geared up for an installation period lasting between 18 months and two years, squeezing it into this tight period because of the expensive equipment required. But floating projects do not require such big, costly installation vessels all the time – meaning the vessel charter profile and cost is different. They require large cranes to install and a lot more tugs to tow them out and install the moorings.
As well as different port facilities, equipment, and services, floating wind is likely to have a different supply chain profile as countries look to develop their domestic industries. For fixed offshore wind projects in the UK, most of the large installation and fabrication contracts to date have been undertaken by overseas companies.
While UK companies have been successful in winning operation and maintenance contracts, most of the manufacturing has been done abroad. Establishing blade factories in the UK and assembling components quayside after shipping them from overseas has been the easiest way for these companies to meet local content requirements.
Figure 3. Floating offshore wind offers the ability to provide renewable energy in challenging geological conditions.
Policy and confidence
The situation will be different for floating wind. As local content requirements become more stringent and the UK government pursues its levelling up agenda, floating substructures will have to be manufactured in the UK. And this requires port infrastructure.
In October 2020, the UK government made £160 million available through its offshore wind manufacturing investment scheme, with half allocated for upgrading port infrastructure – for which Able Marine Energy Park in South Humber received £75 million and Teesworks, the freeport site in the Tees Valley, received £20 million.
With the UK government announcing in last autumn’s white paper that it plans to provide similar backing for floating offshore wind, this is a timely reminder that policy intervention can help create the right conditions for the industry to thrive but that it also takes careful management to maintain momentum.
Confidence will also be crucial to maintaining momentum, and the shortlisting of companies for ScotWind was notable in this regard. As soon as that announcement came, companies rushed to confirm supply chain relationships, including Memoranda of Understanding (MoU) for port space. With the environmental impact assessments, design, contracts, and investment decisions still to come, they want to ensure they meet the deadline of being on the ground and building within five years.
The confidence generated by the early adopters in ScotWind are attracting investment to Scotland. For example, BW Ideol has signed an agreement with Ardersier Port Authority to manufacture concrete substructures for floating wind projects. Here and elsewhere, companies are partnering to make the most of opportunities. In Wales, energy company RWE is partnering with Associated British Ports and the Port of Milford Haven to scale up port facilities for floating wind in the Celtic Sea.
Ultimately, those in the industry know only too well that port infrastructure is the biggest barrier to deploying floating offshore wind rapidly at scale. With limited options for building suitable port infrastructure, the companies who are first out of the blocks may well win the race – not only securing the few available facilities but also building and retaining knowledge that will keep them ahead of their competitors.
Capturing green opportunities
Carbon capture and storage or utilization (CCS/CCU) is a key strategy that businesses can adopt to reduce their CO2 emissions. By selecting the right technologies, pressing climate change mitigation targets can be met while benefitting from new revenue streams. Sulzer Chemtech offers cost-effective solutions for solvent-based CO² absorption, which maximize the amount of CO2 captured and minimize the energy consumption. To successfully overcome technical and economic challenges of this capture application, we specifically developed the structured packing MellapakCC™. This packing is currently applied in several leading CCS/CCU facilities worldwide, delivering considerable process advantages. By partnering with Sulzer Chemtech – a mass transfer specialist with extensive experience in separation technology for carbon capture – businesses can implement tailored solutions that maximize their return on investment (ROI). With highly effective CCS/CCU facilities, decarbonization becomes an undertaking that can enhance sustainability and competitiveness at the same time.
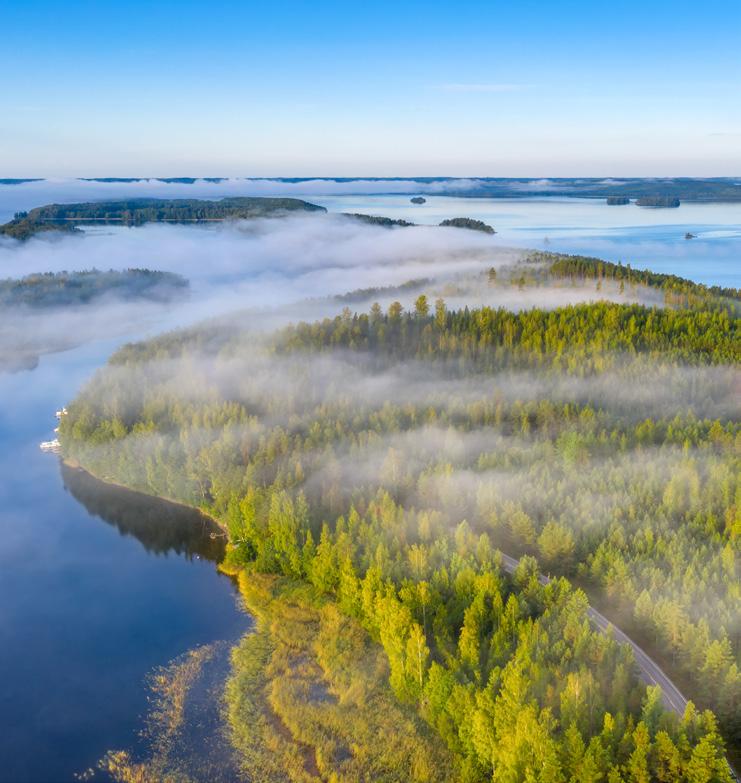
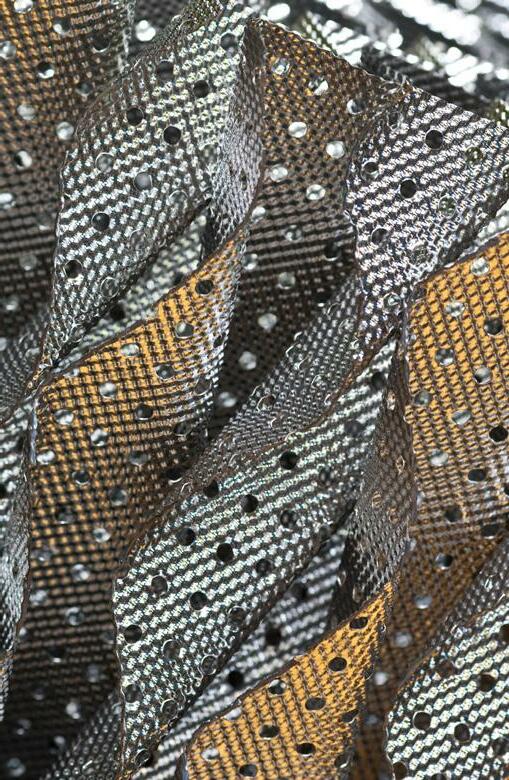
Bahzad Ayoub, Westwood
Global Energy Group, UK, details how the tensions in the offshore wind industry must be addressed in order to accelerate the pace of growth, focusing on turbine OEMs as well as turbine transport and installation companies, suggesting that co-operation is the only way for the industry to succeed.
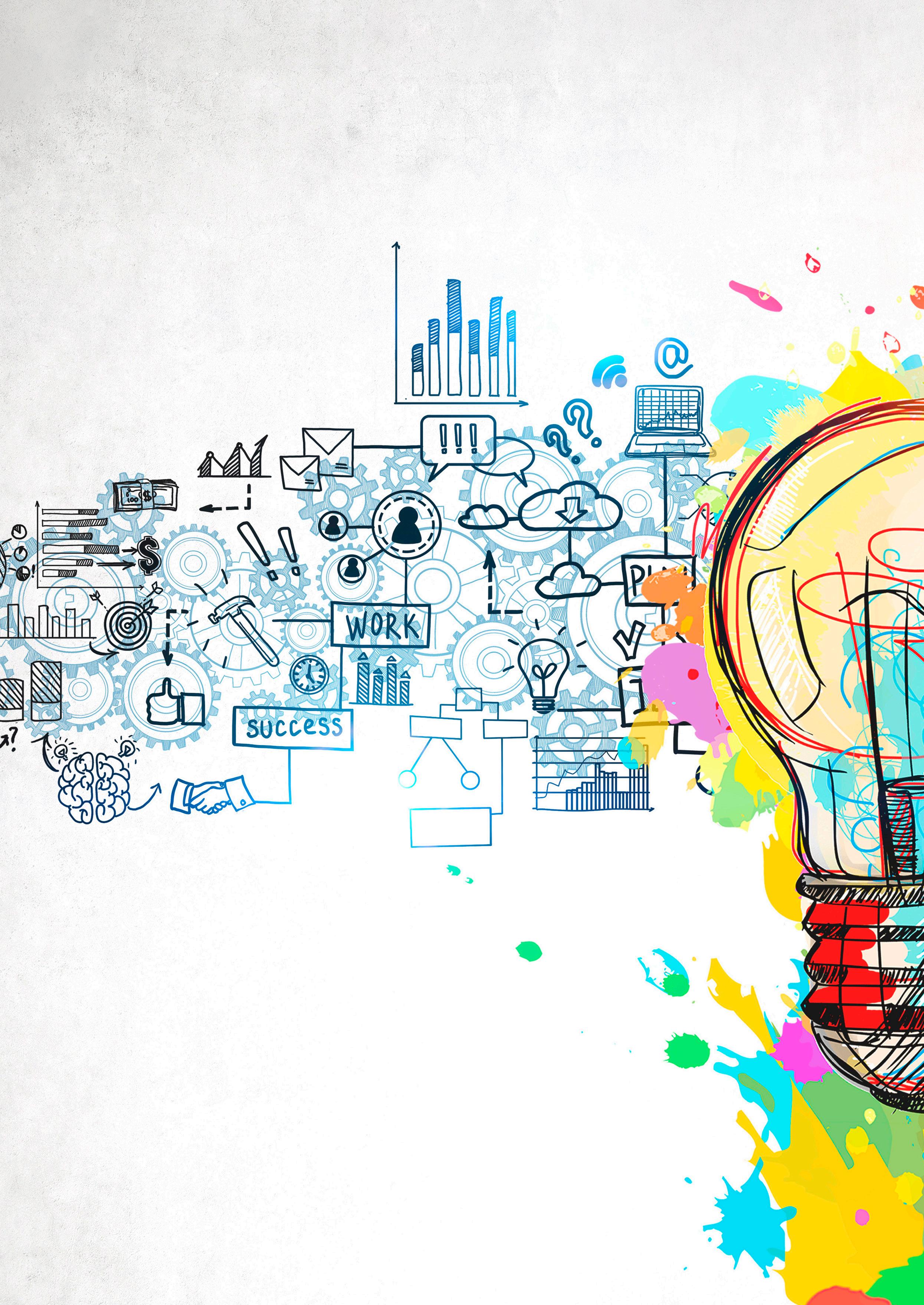
It has been a turbocharged 36 months for the offshore wind sector, with over 30.6 GW of capacity brought online. The rapid growth of the industry, combined with governmental net zero targets and support for the sector, has increased the confidence of offshore wind project developers. As a result of this, over 46 GW of capacity have been sanctioned between 2019 - 2021, representing a 117% increase relative to 2016 - 2018. In addition to this, Westwood projects over 218 GW of capacity to be installed between 2022 - 2030 outside of Mainland China.
Developers taking bigger risks
To get access to this growing market, developers have been willing to make bigger bets. As an example, option fees for the offshore wind Leasing Round 4 in England surpassed initial expectations, with the average option fee at over £108 000/MW.
Aside from paying higher prices for lease areas, (near) zero-subsidy bids to develop projects in countries such as Germany and the Netherlands are starting to become more common. More recently, Denmark selected the winning bidder to develop the Thor wind farm using a lottery draw, as more than one bid came in at a price of DKK0.01/kWh.
These investments are being made even though some developers have recently faced financial headwinds from their offshore wind portfolios. In 1H21, both Orsted and RWE reported that lighter wind speeds had affected their overall offshore wind profits, whilst Equinor reduced its expected offshore wind rate of return from between 6% and 10% to between 4% and 8% (excluding farm downs).
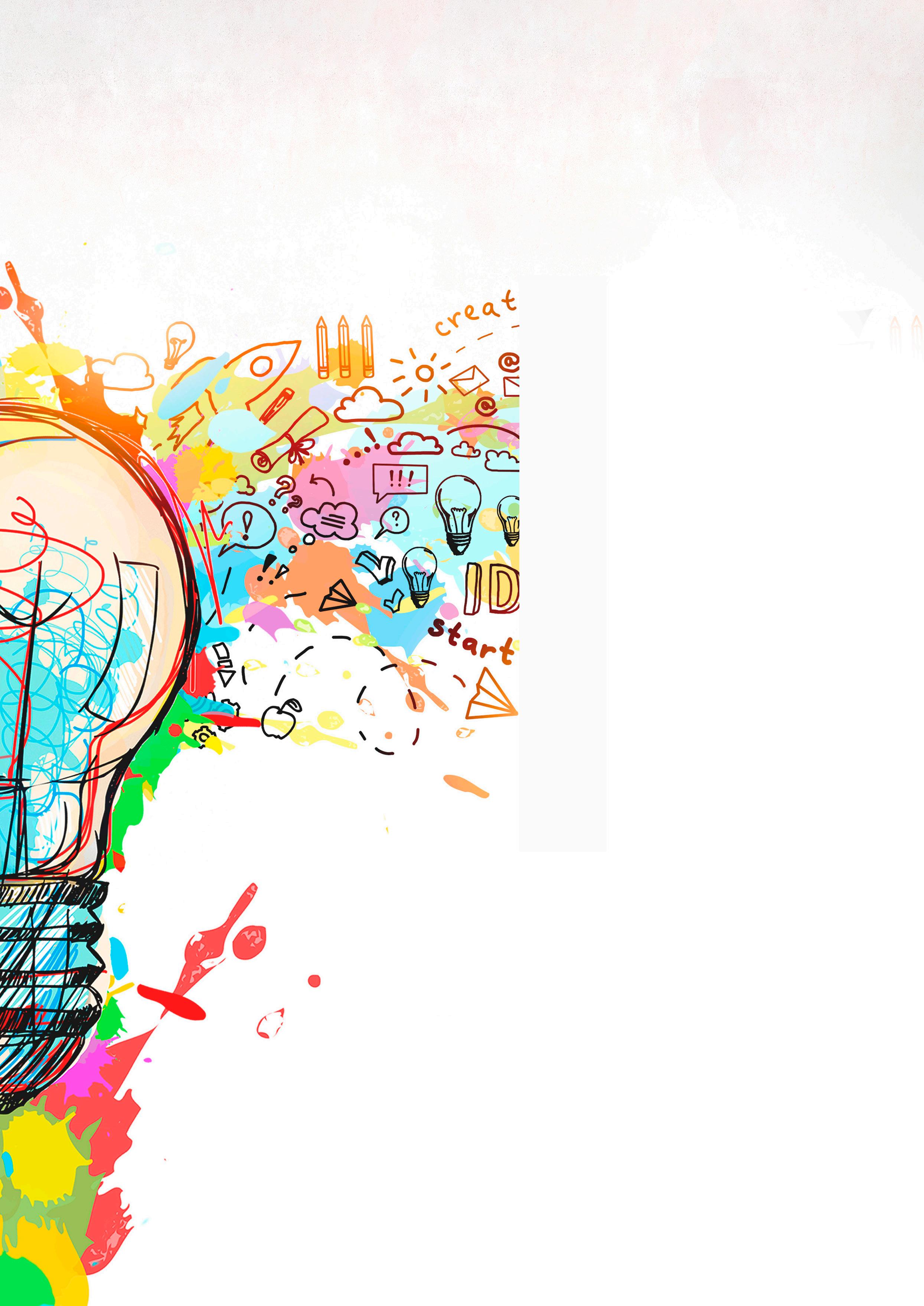
Supporting a cyclical market
An effective supply chain is essential to delivering the growth and return expectations of the wind industry. The cyclical nature of constructing offshore wind farms – typically driven by the timing of leasing rounds – makes this more difficult, as the supply chain must deal with peaks and troughs (when it comes to awarding EPCIC spend).
The inconsistency in the way in which supply chain companies are winning work is resulting in the bottom line of some companies to rise and fall in accordance with the lumpy nature of how projects are being developed.
Increasing competition within the supply chain, cost inflation from raw materials, and rising energy