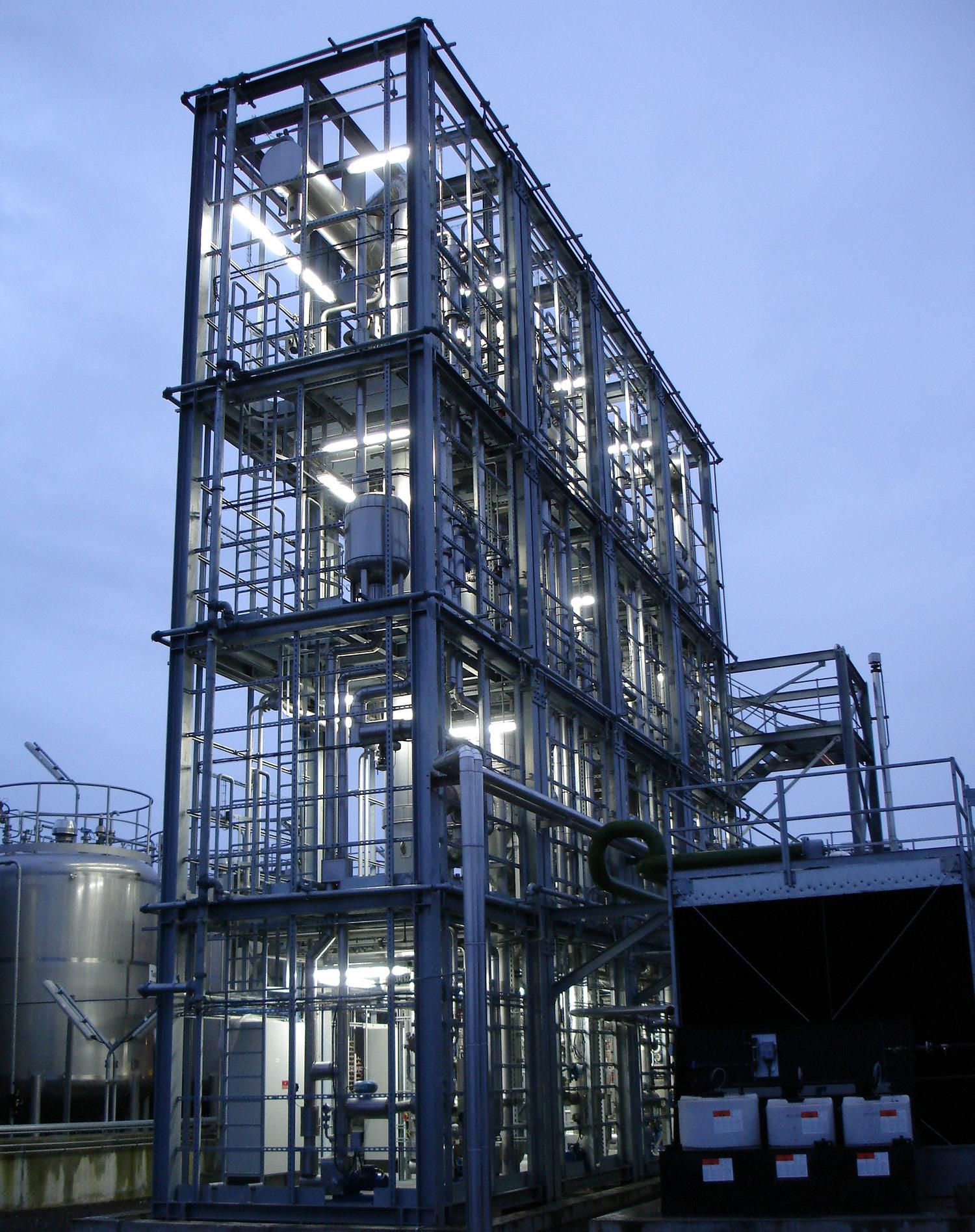
11 minute read
A pillar of progress
feedstock such as ethylene and propylene can also be produced directly by cracking crude oil. Oil refineries are therefore typically large industrial complexes with chemical processing units, such as fractional distillation columns, and use much of the technology as in chemical plants.
Figure 1. A biorefinery is generally defined as a renewable mirror of a petroleum refinery.
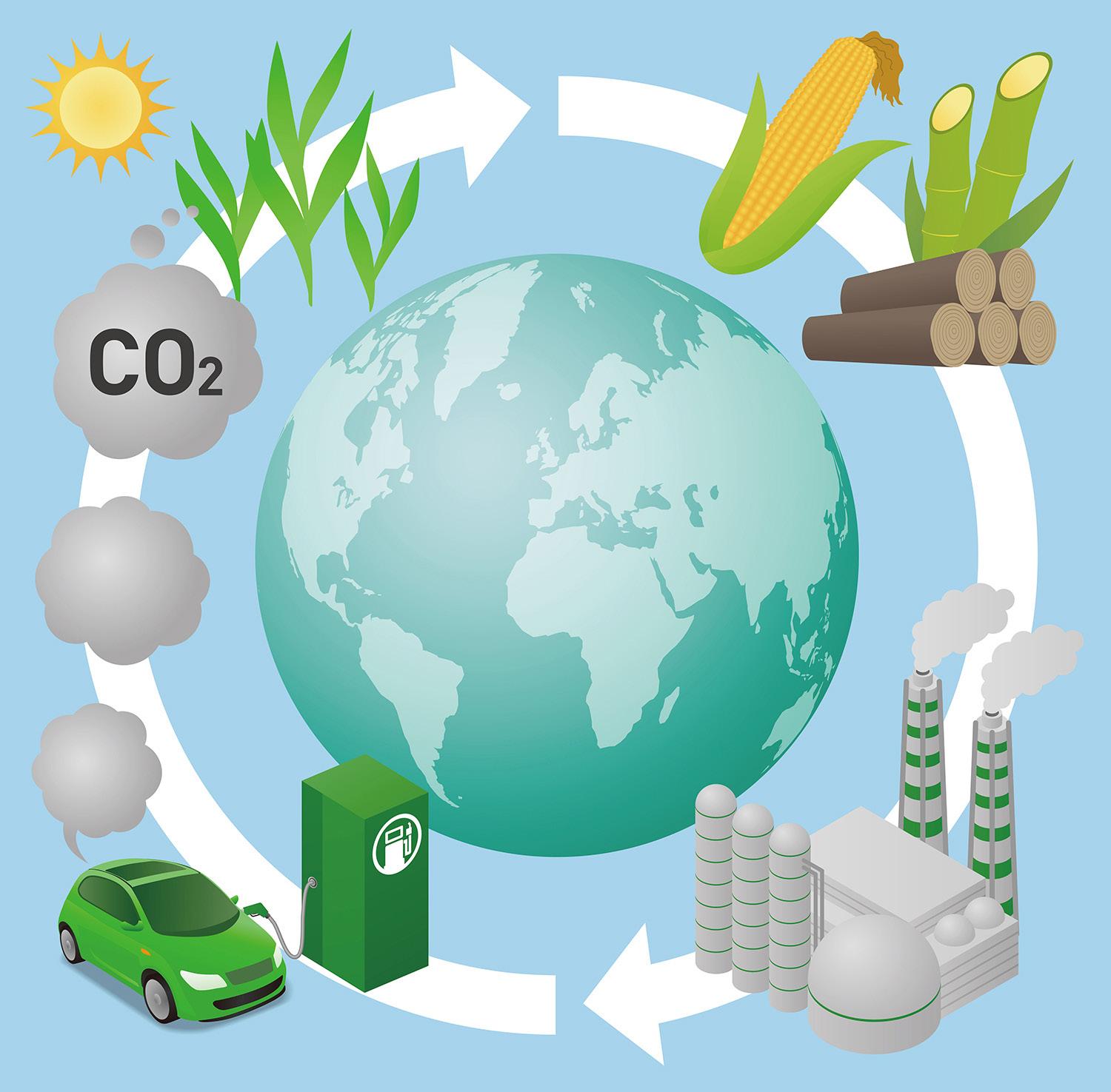
Figure 2. Various plant materials, collectively known as biomass, are a potential feedstock to produce substitutes for petroleum-derived fuels and building blocks for biochemicals.
Replacing fossil fuels with biofuels
Fuels produced from renewable organic material have the potential to reduce dependence on unstable foreign suppliers and lower some of the undesirable aspects of fossil fuel production and use, including greenhouse gas (GHG) emissions, the depletion of non-renewable fossil fuel resources, and geopolitical dependencies. Demand for biofuels could also increase farm income by utilising locally grown renewable feedstocks.
Analogous to petrorefining, the concept of biorefining is emerging. A biorefinery is generally defined as a renewable mirror of a petroleum refinery, where a variety of fuels, chemicals, and power are produced from one source. The characteristics of the modern biorefinery are parallel to the petroleum refinery: an abundant raw material, consisting primarily of renewable biomass, enters the biorefinery and is converted into fuels, biochemicals, and direct energy.
While there are similarities between the biorefinery and the petroleum refinery, there are also important differences. For example, there is more oxygen present in bio-based chemicals, which leads to opportunities for production of certain organic products. Separations are as critical for the biorefinery as they are for the petroleum refinery. Bioprocess separations costs can account for up to 50 - 70% of processing costs.
Various plant materials, collectively known as biomass, are a potential feedstock to produce substitutes for petroleum-derived fuels and building blocks for biochemicals. Biomass is abundant and currently is still low in utilisation. Unlike other renewable energy sources, biomass can be converted directly into liquid fuels, called biofuels, to help meet transportation fuel needs. The two most common types of biofuels in use today are ethanol and biodiesel, both of which represent the first generation of biofuel technology.
Ethanol is a renewable fuel being produced from biomass. Ethanol is used as a blend with gasoline to increase octane, and reduce carbon monoxide and other emissions. The most common blend of ethanol is E10 (10% ethanol, 90% gasoline) and is approved for use in conventional gasoline-powered vehicles. Furthermore, ethanol can be used as an intermediate for the production of green polyethylene and esters. The vast majority of ethanol is currently made from plant starches and sugars; particularly corn starch in the US, but technologies are being developed and enhanced that would allow for the use of cellulose and hemicellulose, the non-edible fibrous material that constitutes the bulk of plant matter.
Biodiesel is a renewable, biodegradable, cleaner burning fuel manufactured from an increasingly diverse mix of feedstocks, such as various vegetable oils, waste animal fats, or recycled cooking oil. Biodiesel is a liquid fuel often referred to as B100 or neat biodiesel in its pure, unblended form. B100 biodiesel can be directly used in existing diesel engines or can be blended with regular diesel, such as B5 and B20, for use in colder climate areas. Biodiesel is made through a chemical process called transesterification whereby the glycerin is separated from the fat or vegetable oil.
Currently, ethanol and biodiesel plants are mostly standalone facilities near their feedstock plantations. The biorefinery is still lacking in competitiveness compared to a
petroleum refinery. The paradigm-shift from the oil-based to the renewable resources-based economy must be supported by not only research and development but also by higher-efficiency separation processes.
The petroleum industry has improved separation efficiencies over the decades by taking advantage of advancements in mass transfer technologies, such as column internals: distributors, trays, and types of packing materials –structured, random packing, and column supports etc. Sulzer Chemtech has pioneered advancements in these internals since the 1960s with the development, design, and production of packings to find the optimum solution for a variety of applications, including a new structured packing for absorbing CO2 more efficiently from flue gas streams of fossil-fuelled power plants.
Distillation is the most commonly applied separation technology. It is critical that the design of these unit operations provides an improved product quality, increased capacity, and lower energy consumption. Design activities are supported by computer simulations, proprietary sizing tools, and pilot plant testing. The simulation models developed from the refining and chemical industries are continuously improved with new empirical data from biofuel and chemical process streams. To improve efficiencies, process intensification techniques, such as extractive distillation, azeotropic distillation, reactive distillation, membranes, and divided wall columns, are being utilised. Similarly, higher energy efficiencies are achieved with heat integration and heat pumps, such as mechanical vapour compression (MVR) technologies.
An attractive solution that addresses both is the integration of bio-feedstock and existing petroleum refineries. Renewable diesel has become the leading alternative as companies invest in a more environmentally conscious energy supply. Completely fungible with petroleum diesel, renewable diesel from biomass-based feeds has lower sulfur and higher cetane than its petroleum-based equivalent and can be used without modification to existing infrastructure. Hydroprocessing units that generate either hydrogenated vegetable oil (HVO) or sustainable aviation fuel (SAF) use bio-based feedstocks from one of three categories – fats, oils, and greases (FOGs). For example, BioFlux® pretreatment technology, developed by Duke® Technologies and licensed by Sulzer Chemtech, is an alternative process designed to economically treat FOGs and enable more efficient hydrotreating operations. Biomass-based FOGs are thermally cracked using conventional refiner equipment and processes.
Conclusions
For biorefineries to compete with petroleum refineries, a number of aspects should be addressed. Process intensification, modularity to reduce plant footprint, higher energy efficiency, reduced water usage, including water reclamation, as well as carbon capture and utilisation are some of the key areas where further developments and continuous process improvements are essentials for the success of the emerging bioproducts industry. Utilising some of the already proven separation technologies with a scale down approach will help to reduce the risk of scaling up from small scale for the new bio-based technologies.
Maria Anez-Lingerfelt, PhD,
Pall Corporation, US, outlines the ways in which biofuels can aid the switch to increased renewable energy production, helping to reduce the world’s reliance on fossil fuels.
The need for sustainable energy is accelerating on several fronts. The war in Ukraine has highlighted the precarious availability of fossil fuels and prompted a rethink by many countries of the places from which they are willing to source vital fuels. Additionally, rising oil and gas prices have seen the cost of living soar to the detriment of consumers and businesses alike. Although biofuels are complex and currently more expensive to produce than traditional petrochemicals, it is important to look at how to make the processing of them scalable and more cost-effective. Making biofuels a key part of a wider renewable energy strategy offers the opportunity to reduce reliance on fossil fuels and move towards a greener future.
Even though many would agree that biofuels are pivotal to the energy transition, there is little consensus on how to make them commercially viable. There is considerable debate around optimal bio-feedstock and the best way in which to process, deliver, and use them. Concerns are also raised over the cost of production and amount of resulting useable energy when compared to fossil fuels.
Technological developments can unlock this conundrum, but more investment is needed in existing solutions, such as filtration, to optimise biofuel processing and to support the scale-up of production to truly industrialised levels.
A complex regulatory landscape
There are differing perspectives on what the current situation is, and how to transition to a better energy future. When launching the latest report from the Intergovernmental Panel on Climate Change (IPCC) in April, the UN’s Secretary General, António Guterres, criticised governments and corporations that have impeded climate change reduction measures and increased fossil fuel production because of vested interests. He said that choices made now will “make or break” the commitment to limiting global warming to 1.5˚C above pre-industrial levels. He also stated that investing in renewables would be vital for the global energy mix, and would offer hope to millions of people adversely affected by climate change.
In the spring, German MEP, Markus Pieper, put forward several draft amendments to the EU’s Renewable Energy Directive (RED II). He proposed increasing the proportion of energy from renewable sources to 45% by 2030 – up from the current target of 40%. He also urged for more biofuels in transport, an introduction in innovation quotas for the development of renewables, and the removal of a ‘cascading’ principle which limits the availability of biomass.
North America has a range of financial stimuli. In the US, there are a raft of federal tax incentives for qualifying renewable energy projects or equipment, including the renewable electricity production tax credit, the investment tax credit, and the residential energy credit. Meanwhile, the Canadian government provides provinces and territories
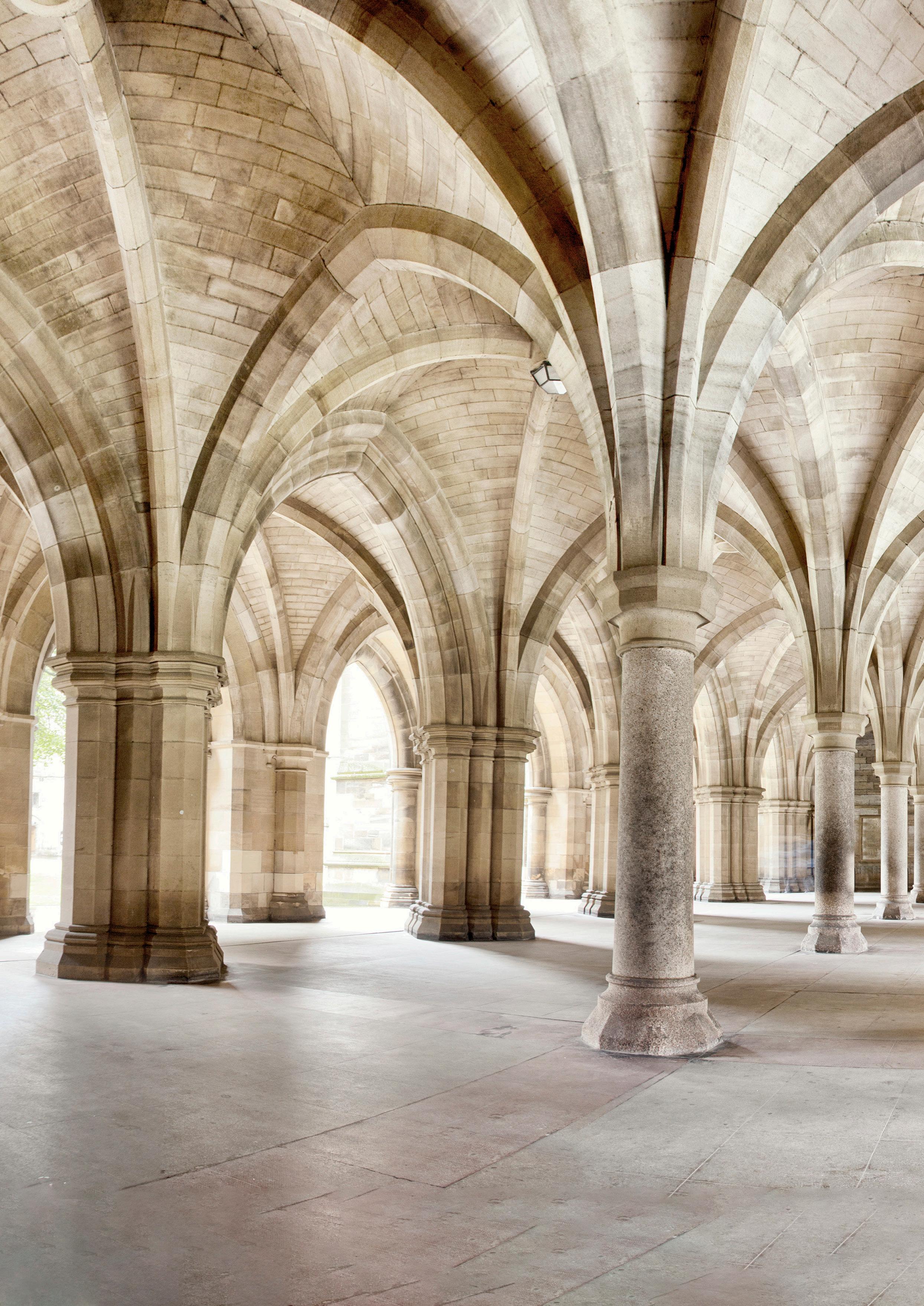
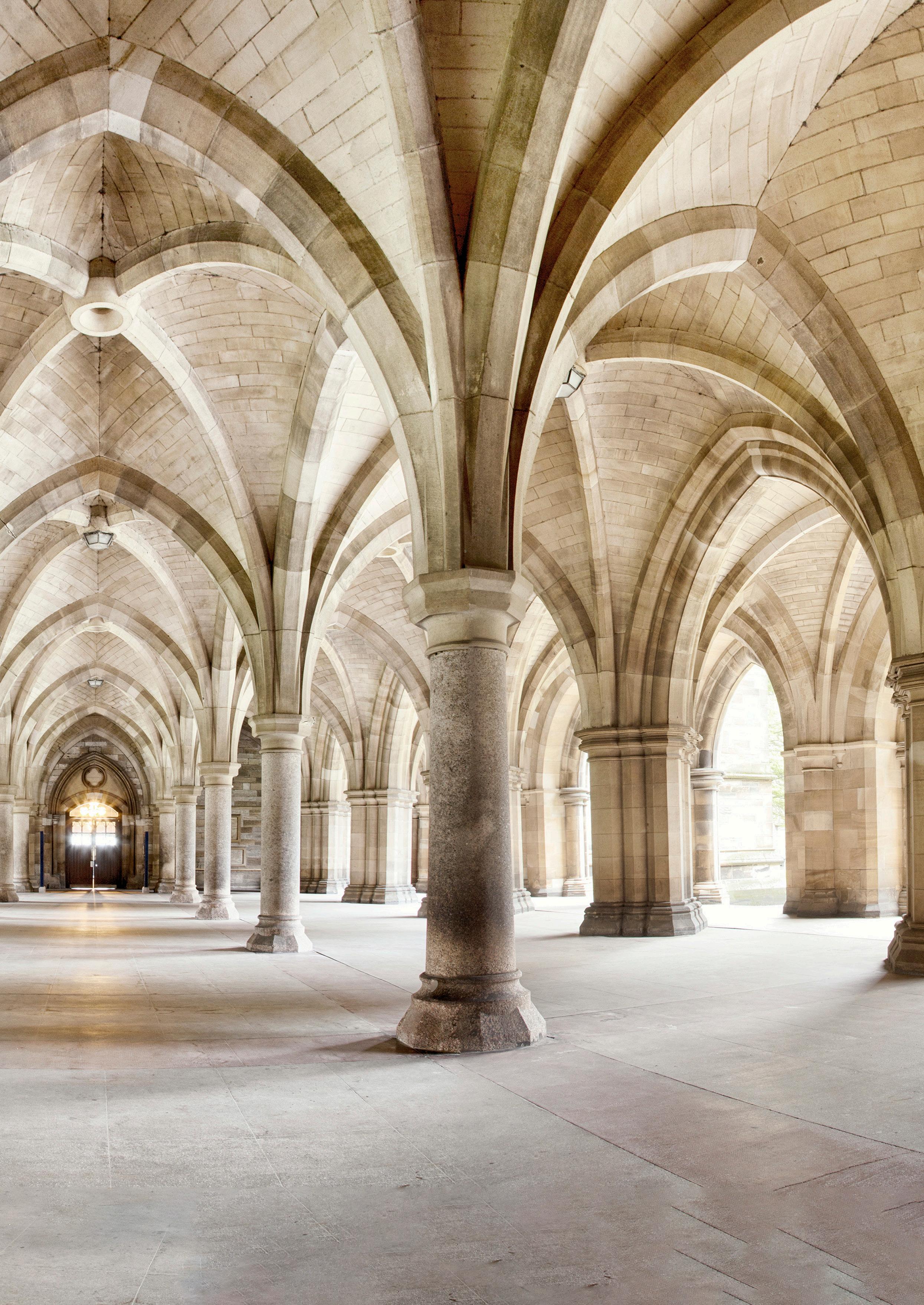
with funding to administer projects via the low-carbon economy fund.
In the UK, the British energy security strategy focuses on increasing offshore wind, reinvesting in nuclear power, and doubling the government’s ambition for low-carbon hydrogen production. Whether by legislative directives or financial impetuses, new measures are being sought in many nations to decarbonise and create a greener future.
Choosing the right biomass
The International Energy Agency (IEA) shows that in 2021, global CO2 emissions were split by sector as power generation by coal (29%), industry (23%), transport (23%), buildings (10%), gas (9%), oil (2%), and other (5%). The IEA also forecasts that demand for biofuels will increase 28% from 2021 levels to 2026. Although discussions on renewable energy often centre on wind, solar, and hydropower, biomass as a source accounts for 97% of global renewable heat production and 11% of global renewable electricity production according to the World Bioenergy Association’s Global Bioenergy Statistics 2021 report (based on 2019 figures).
Production of biofuels from biomass certainly supports changing energy requirements and emissions standards, but there are challenges to consider, both from environmental concerns of the varying source materials to the way in which they are processed. As a feedstock, biomass varies greatly: it encompasses plants such as edible crops, wood, grass, and other non-edible plant material, known as lignocellulosic biomass (LCB). It also includes non-plant material such as animal waste, residential waste such as used cooking oil, commercial/industrial waste, and algae – non-lignocellulosic biomass (NLCB). It is no wonder there are myriad considerations.
If crops such as corn, soy, and sugar cane/beet are grown to be used as a first generation biofuel, their cultivation limits the availability of agricultural land for food production and may be a drain on regional water sources. Additionally, focusing on monoculture or planting genetically modified crops to provide greater yields compromises biodiversity.
As such, the use of non-edible plants or waste materials to produce second generation (advanced) biofuels provides a greater contribution to sustainability.
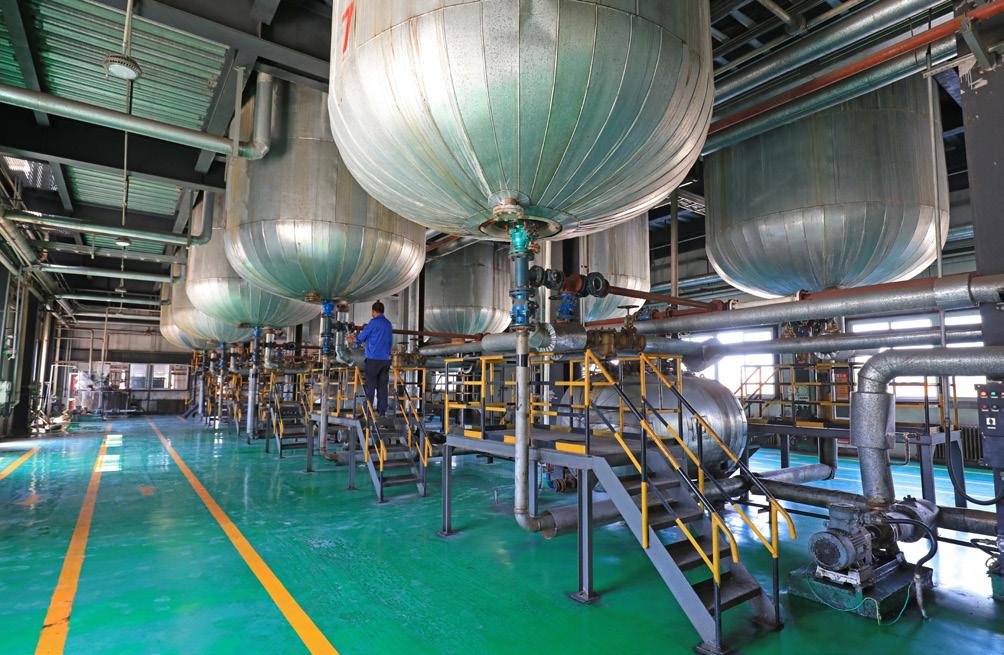
Figure 1. Biodiesel production.
Pre-treatment is the first step
The differing molecular composition of wood, non-edible plants, and waste materials leads to varying levels of solid particulates, water content, gels, and waxes, as well as variable particle size, density, and viscosity. Where these materials are processed together in a refinery, volumes of each within the overall mix may differ, depending on the available supply. Pre-treatment is usually required to structurally alter the biomass into a more consistent form before processing, with minimal degradation to vital components. This can involve physical, chemical, or biological processes, and the method used should be tailored to the biomass source.
Physical pre-treatment may be done by milling or chipping to reduce particle size and increase the overall surface area, thereby enabling greater access to enzymes to break down the cellulose into glucose. However, this is an energy intensive process and does not remove all the lignin content (complex polymers in plant cell walls). Microwave irradiation and steam explosion may also be employed.
Chemical pre-treatment can use alkali or acid additions. Alkali bases increase internal swelling of the biomass to decrease polymerisation and generate lignin breakdown. Acid hydrolysis can improve enzymatic hydrolysis of lignocellulosic material to release fermentable sugars.
Biological pre-treatment involves the use of microbes or enzymes – such as from fungi – to break down the lignin particles and depolymerise the cellulose. This is beneficial in that it produces few toxic substances and does not require much energy, but the process is slow and requires a lot of space.
Technology underpins processing
There are various options to process biomass into liquid biofuels or biogas, with some residual solids that can be used as fertilizer: F Traditional hydrotreating: Involves reacting the lipids with hydrogen in elevated temperatures and pressures in the presence of a catalyst in a refinery. Commercial plants currently use this technology.
F Biological sugar upgrading: This uses a biochemical deconstruction process, similar to that used with cellulosic ethanol, with the addition of organisms that convert sugars to hydrocarbons.
F Catalytic conversion of sugars: Involves a series of catalytic reactions to convert a carbohydrate stream into hydrocarbon fuels.
F Transesterification: A chemical reaction used for the conversion of triglycerides (fats) contained in feedstocks into usable biodiesel. Biodiesel produced by the process of transesterification has a much lower viscosity, making it capable of replacing petroleum diesel in diesel engines.
F Pyrolysis: Involves the chemical decomposition of organic materials at elevated temperatures in the absence of oxygen. The process produces a liquid pyrolysis oil that can be upgraded to hydrocarbon fuels, either in a standalone process or as a feedstock for co-feeding with crude oil