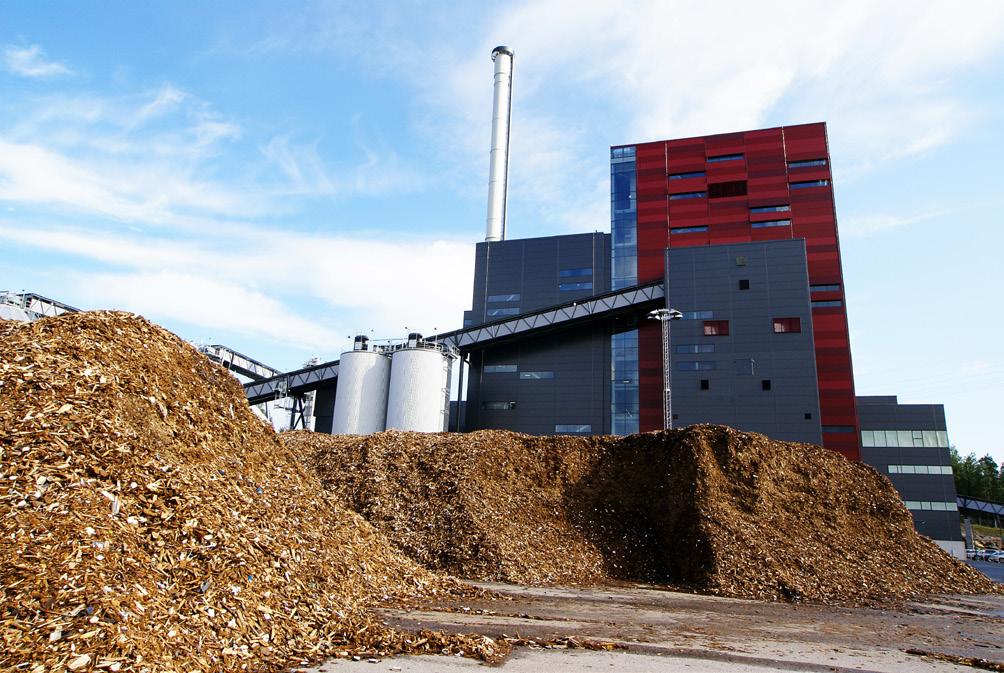
13 minute read
The gear up to green
into a standard petroleum refinery. Syngas may also be produced.
F Hydrothermal processing: Uses high pressure and moderate temperature to initiate chemical decomposition of biomass or wet waste materials to produce an oil that may be catalytically upgraded to hydrocarbon fuels.
F Gasification: During this process, biomass is thermally converted to syngas and catalytically converted to hydrocarbon fuels.
Co-processing optimises the value chain
Where conversion of biomass into biofuels is done in existing refineries, this is termed co-processing. Many refineries operate below their capacity, making co-processing a viable option to meet sustainability goals and maximise production without making expensive investments in refining assets. Most co-processing happens in hydrotreaters, hydrocrackers, or fluid catalytic crackers.
These catalytic processes remove sulfur, oxygen, nitrogen, and metals. It is critical to remove sulfur as this reduces SO X emissions when fuels are combusted; sulfur also poisons downstream noble metal reformer catalysts (<0.5 ppm S is a typical naphtha feed spec). This clean-up also saturates olefins to yield easier-to-process intermediates.
The reaction is carried out in a hydrogen-rich environment over a fixed catalyst bed, and the replacement of sulfur or nitrogen contaminants with hydrogen makes the process a consumer of hydrogen. Protection of the heat exchangers and catalyst beds from fouling is critical to maintaining long-term hydrotreating efficiency. Treated products are then stabilised with heat to remove hydrogen sulfide and light ends. Use of direct steam injection is common.
Figure 2. Biofuels power plant with wood biomass.
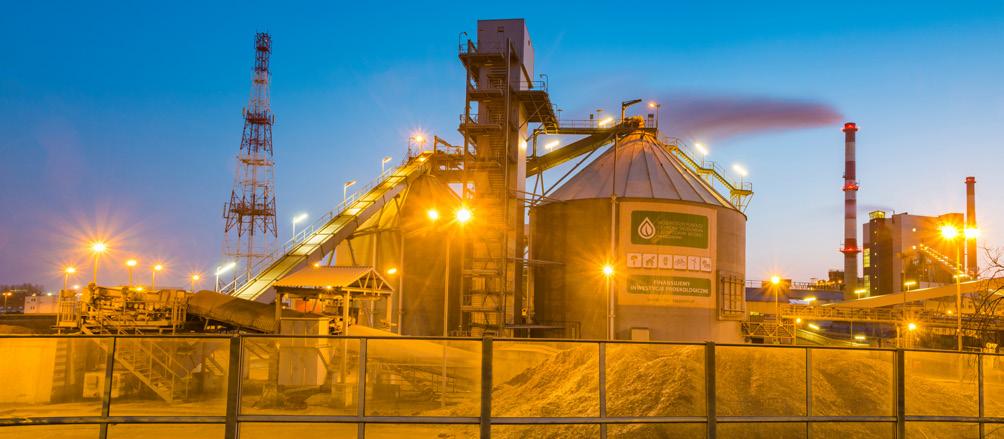
Figure 3. Biomass processing plant.
Why is filtration critical to biofuel production?
Despite pre-treatment, biomass tends to degrade during transportation and storage. These particulate impurities and gels can cause severe damage to downstream equipment if left unfiltered. In addition, biomass typically contains an abundance of oxygen that gets converted into carbon monoxide, carbon dioxide, and water during hydroprocessing. Depending on the type and proportion of the feedstock inserted into the refinery for the production of liquid biofuels, the volume of gaseous products and moisture generated may differ significantly and impact refinery operations.
Some of the challenges include: pressure build-up over the catalyst bed and heat exchanger; additional hydrogen demand; higher gas treatment and removal capacity required; and removal of additional co-produced water. The increased risk of moisture and contamination in catalysts and critical equipment due to biomass processing may lead to frequent downtime to repair or replace these expensive pieces of technology.
In addition to solid particulate removal, separation of water from the final biofuel product is an essential step in the biofuel refinery process. To achieve premium diesel quality, Pall liquid/liquid coalescers can be installed downstream of the hydrotreater to separate and remove water content to an acceptable level.
For example, a major EU producer of biodiesels and sustainable aviation fuels (SAF) uses Pall Aquasep XS liquid/ liquid coalescer filters to polish the refined biodiesel product to an acceptable water content specification of <100 ppm. The coalescer media agglomerates water molecules as the biodiesel flows through it, creating larger water droplets that can be separated from the feed fluid. The dense coalescer media provides optimum separation capacity (typ. ≤15ppm separation level achievable), protected by appropriate particulate pre-filters that can retain the gels and waxes that might otherwise blind and therefore reduce coalescer performance.
The production of biogas happens through anaerobic technology and consists mainly of methane and carbon dioxide. However, it can also contain small amounts of hydrogen sulfide, siloxanes, and moisture, all of which can have a detrimental effect on the production process. To maximise methane output and protect critical equipment such as compressors and membranes, it is important to eliminate as many impurities as possible through particle filtration and liquid/gas coalescence methods. Without efficient filtration and separation technologies, heavily contaminated gases can lead to compressor corrosion, abrasion in moving parts, and degradation of purification units.
In the processing of both liquid biofuels and biogas, investing in an efficient, high-quality filtering system is essential to protect downstream equipment and to ensure installations run smoothly with less downtime. Where poor filtration and
separation choices are made, these may lead to million-dollar adverse consequences.
Increasing filter service life and meeting new biofuel specifications
The Indonesian government introduced a mandate for diesel to contain at least 30% biofuel, to reduce its emissions, and boost its production of palm oil. As a result, one Pall refinery customer found that with the increased biofuel content, its filter service life reduced to one week. Working with the customer, Pall developed a new filtration solution based on its Ultipleat High Flow filter design, which doubled the filter service life and met required cleanliness targets. The filter’s crescent-shaped pleat geometry, combined with its large 152.4 mm (6 in.) dia. and proprietary range of available Pall filter media ratings, allows customers to use significantly fewer filters and smaller housings for high flow-rate applications.
The applications of advanced biofuels
Processing produces liquid biofuels (bioethanol and biodiesel) and biogas, each of which can be used as an alternative to fossil fuels or added as drop-in fuels to mix with the traditional fuel, depending on capabilities and statutory guidelines.
Bioethanol is used in internal combustion engines and can be mixed with petrol to any percentage. It has a 34% lower energy density than petrol, so more needs to be used to achieve the same level of energy; but it has a higher octane rating, meaning that ethanol-driven engines can be designed for higher thermal efficiency with better performance and less energy wastage. Analysis by the US Department of Energy found that on a lifecycle basis, greenhouse gas (GHG) emissions are reduced on average by 40% with corn-based ethanol, and range between 88% - 108% if cellulosic feedstocks are used – depending on feedstock type – compared with petrol and diesel production and use.
Biodiesel can be used in its pure form (B100) or blended with petroleum diesel in the form of B2 (2% biodiesel, 98% petroleum diesel), B5 (5% biodiesel, 95% petroleum diesel), or B20 (20% biodiesel, 80% petroleum diesel). One of the main advantages is that it can be used in existing diesel engines without the need for modifications; additionally, it increases engine life as it is virtually sulfur-free. And experts believe that it can reduce GHGs by up to 78%. However, biodiesel gels in cold weather, making it more difficult to start engines. This also means that it cannot be transported in pipelines, so has to be conveyed by rail, lorry, or barge.
Biogas – often called biomethane – can be used as direct combustion for heating, cooking, and heating water. It can also be used in fuel cells to produce electricity, in internal combustion engines, and, if suitably cleaned from filtration, injected into existing gas pipelines and used for lighting and to make steam via turbines. Additionally, via a catalytic chemical oxidation, methane can be used in the production of methanol and thereby to power cars, buses, trucks, and ships.
Figure 4. High performance filtration technology is key to biofuel production. Syngas – a mix of carbon monoxide and hydrogen – can be applied to many of the same uses as biomethane, in either hot or ambient temperatures. For ambient temperatures, the process of cooling pyrolysis gas and separating condensable and non-condensable phases requires additional energy to reduce stream temperatures. In this respect, syngas under ambient temperatures is easier to transport and offers a wider scope for further treatment, allowing separation of molecules and their additional utilisation.
Selecting the best filter media for hydrotreating
A US refinery was using Pall’s Vector filters in the hydrotreating of melted beef tallow and soybean oil to produce HVO diesel. The customer wanted to increase production and so needed greater filtration capacity. Pall scientists evaluated both process and performance to establish the best filter media solution to arrive at a balance of acceptable filter service life and consistent downstream asset protection (protection of the heat exchanger and extended catalyst life). Pall’s polyester Vector High Flow in an 80 in. length, 1-μm rating, with increased temperature capacity of 100˚C (212˚F) was applied downstream of the original 25 μm-rated filter. This enabled the customer to increase production capacity and maintain predictable, reliable operation.
On the path to greater sustainability
There are examples in many industries of how a willingness to do more is yielding benefits. According to the International Air Transport Association (IATA), the mixing of biofuels with a petroleum-based jet fuel to produce sustainable aviation fuel can reduce emissions by up to 80%, particulates by up to 100%, and sulfur by 90%. This is a great step forwards until electric flight by fully renewable energy sources is commercially viable. Every sector has to do more to enhance decarbonisation and reduce emissions, and the conversion of biomass into biofuels is a key pillar for progress. Challenges on availability of bio-feedstocks remain, along with the volumes of energy required in the production processes. But the use of technology and practical solutions, such as filtration of biomass, must increase to enable the scaling up of biofuel production to help meet climate change goals and enhance global security.
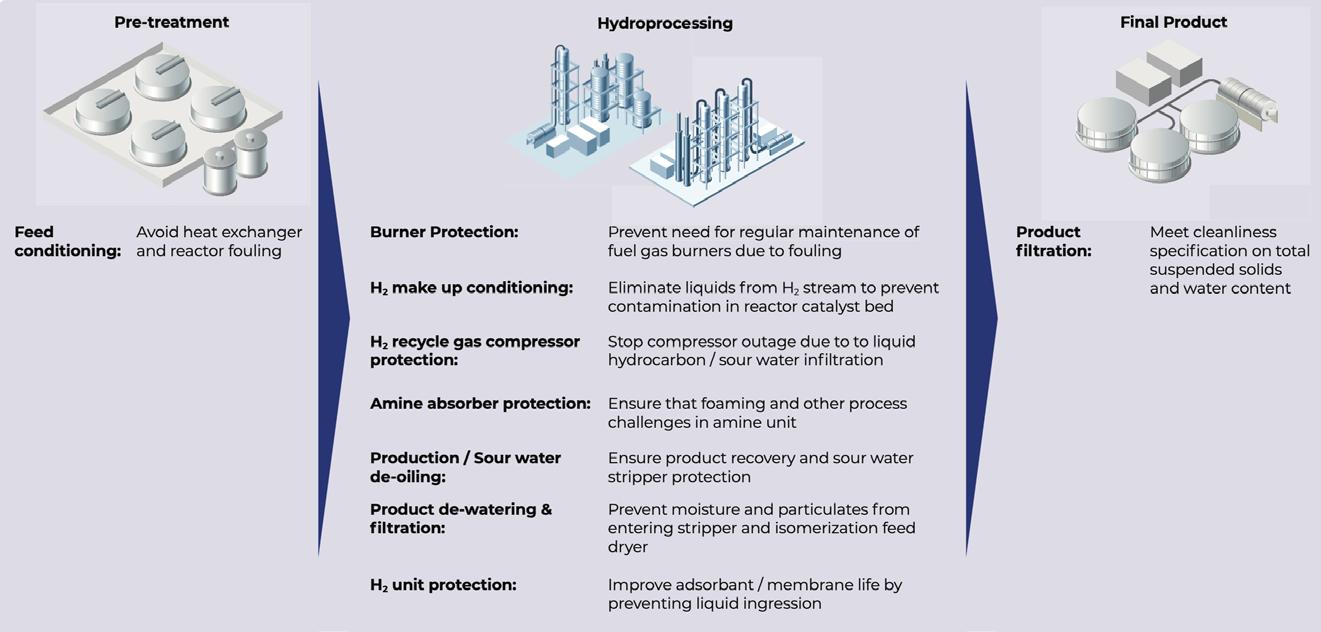
Florian Gruschwitz, MAN Energy Solutions,
Germany, considers the potential of power-to-X and green fuels, and the role they will play in the ramp-up to a green hydrogen economy.
There is no doubt that green hydrogen is a key element on the path to decarbonisation. Nor is there even the least surprise these days that green hydrogen – and power-to-X in general – has gained so much popularity and public attention. For good reason, this will not be a flash in the pan.
Strong drivers, such as the EU’s Fit-for-55 programme, underline the reality that decarbonisation has now become a serious target and many countries have already published ambitious hydrogen strategies. Companies such as MAN Energy Solutions can
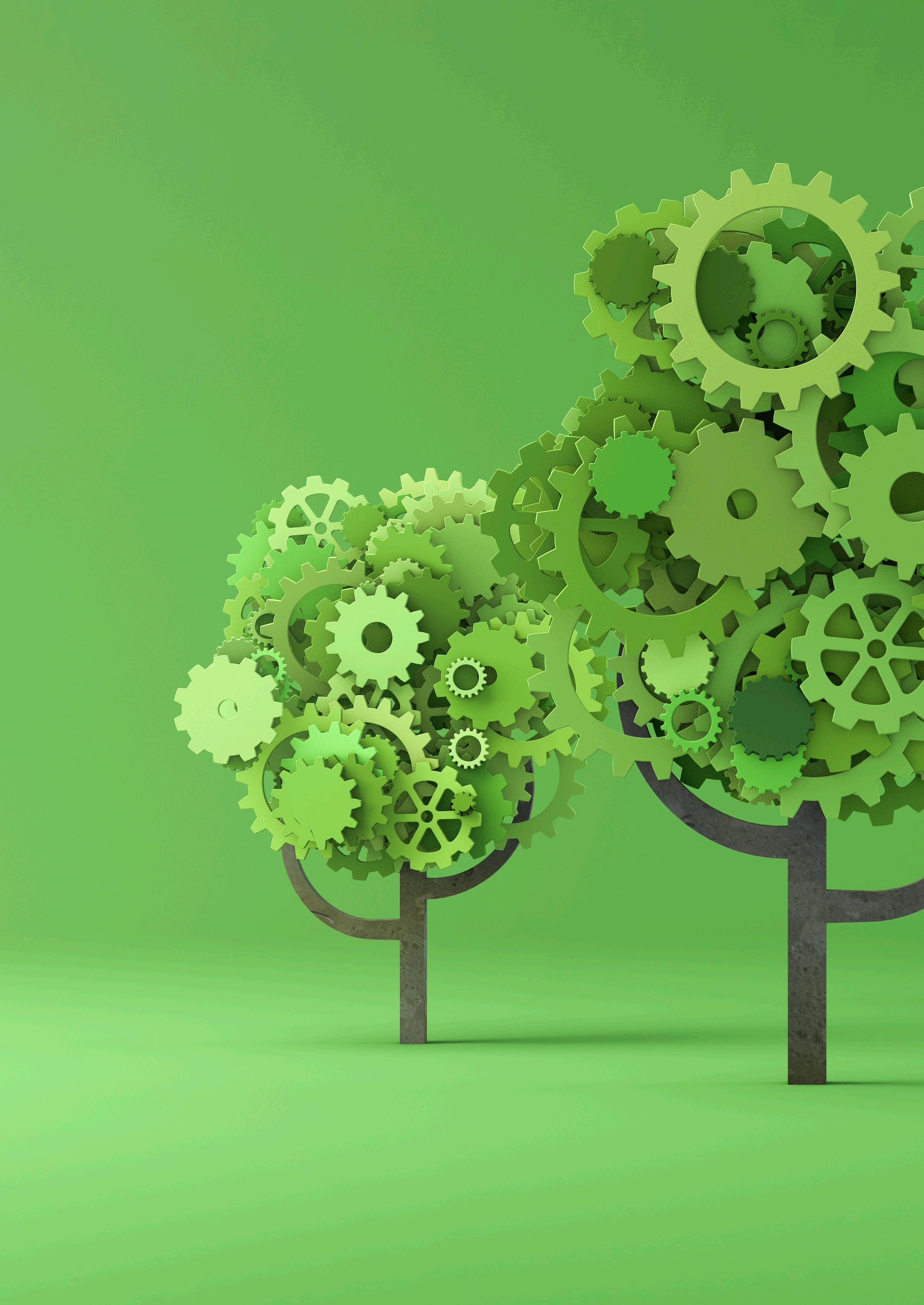
already provide the necessary, key technologies along the power-to-X and green hydrogen value chain and have serious skin in the game through significant investments aimed at further extending the base of necessary technologies.
Mature technologies, for instance for eFuel production, are available that enable the use of existing infrastructure, but much remains to be done in order to create more viable business cases. It can be shown how derivative fuels, or eFuels, can successfully complement green hydrogen in its elemental form and be an important enabler in the ramp-up to a green hydrogen economy.
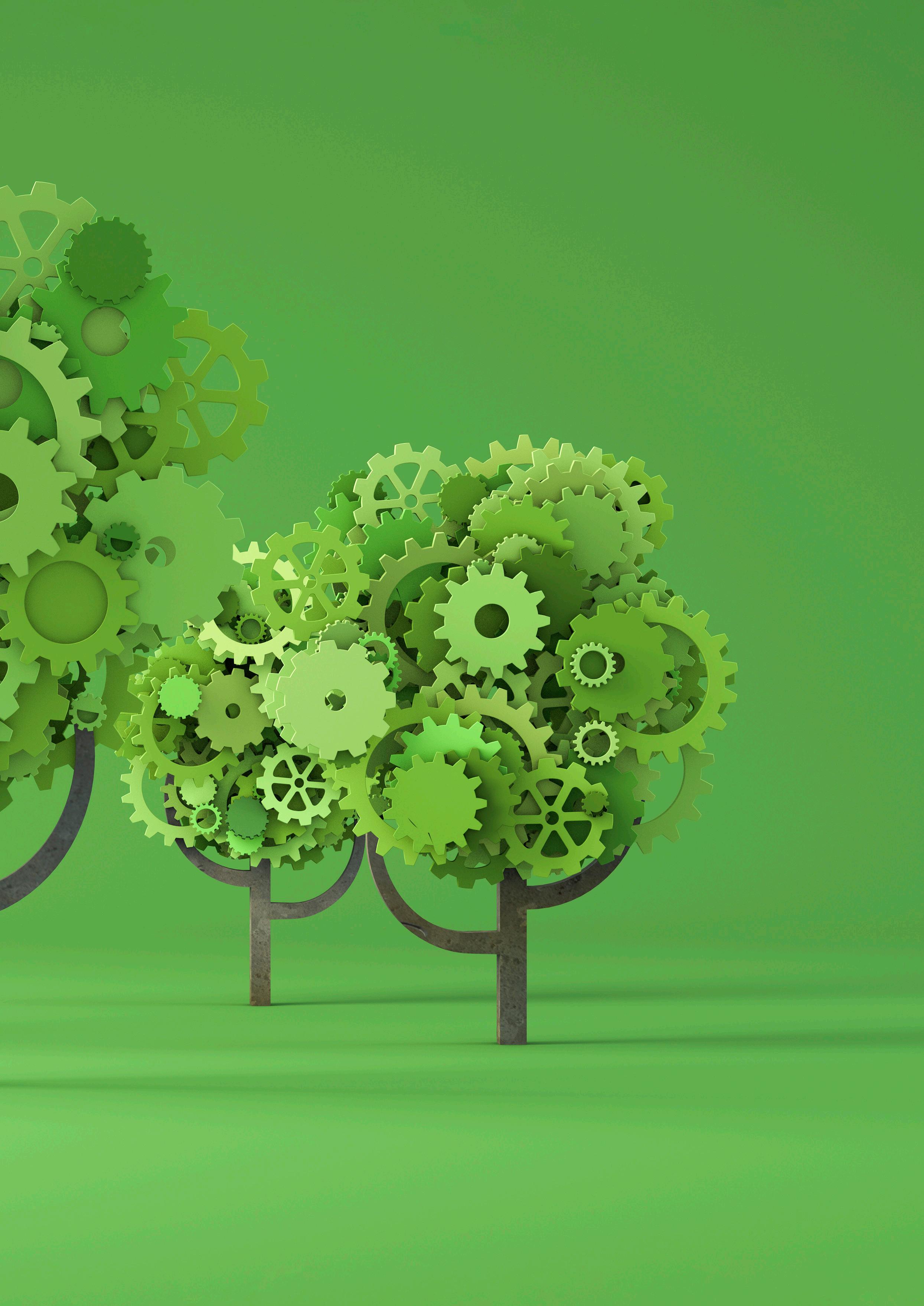
One thing is clear: elemental green hydrogen will not be a one-fits-all solution. Instead, there will be a multi-option scenario where pragmatic approaches will aim at maximum efficiency, whilst at the same time ensuring that a solid base and ramp-up path for long-term transition to green hydrogen is created.
To get the full picture, it is helpful to look at the topic from two perspectives: firstly, viewing power-to-X in the context of how it can play an important role in reaching decarbonisation targets; and, secondly, looking at the main hurdles – but also success criteria – in getting a green hydrogen economy ramped up at a global level.
If it is agreed that decarbonisation is an underlying imperative in order to save the planet, then a policy comprising four elements can be identified, beginning with replacing fossil-fuelled power generation with renewable energy sources. The use of green hydrogen and employing eFuels (based on green hydrogen) are two further elements. And the fourth – for the hard-to-abate carbon sources – is carbon capture and storage technologies, again combined with power-to-X technologies.
These four elements may be viewed as a type of ‘decision tree’ such that, when addressing an application that acts as a considerable carbon source today, all four means of decarbonisation need to be assessed in the order described to find the best fit – i.e., the most effective way to achieve decarbonisation considering all current boundary conditions.
Needless to say, decarbonisation is reliant upon an abundant availability of renewable energy. Accordingly, extending the capacity of renewable energy generation is of paramount importance. The first question in the quest for decarbonisation is then: is direct electrification possible? This means, first of all, replacing all fossil-fuelled power generation with renewable energy. However, natural-gas-fuelled power plants, for example, may be tolerated as back-up or peakers as they facilitate the maximum use of renewable energy in the grid while simultaneously ensuring maximum reliability and grid stability.
Continuing through the decision tree, for applications that cannot be directly electrified as of yet or even in the longer-term, the use of green hydrogen could be a good option, and many examples exist. However, following the Pareto principle, some prominent areas especially suited for decarbonisation can be identified, such as steel production where production with green hydrogen instead of coal would cut carbon emissions considerably.
Another good example of a sector ripe for decarbonisation with green hydrogen is within processes that already require large amounts of hydrogen today. Here, grey hydrogen is currently used and produced by steam reformation with natural gas. One such example is fertilizer production, where ammonia as a main feedstock requires large amounts of hydrogen.
Which leads us to the third stage in the decision tree when neither direct electrification nor the use of green hydrogen as a molecule is possible. In such instances, eFuels may be a solution. Derivative fuels or eFuels in this context are carbon-neutral fuels based on green hydrogen. This includes synthetic methane, methanol, or e-Kerosene – or ammonia produced from green instead of grey hydrogen, which provides a carbon-free option.
As such, derivative fuels could play an extremely important role, acting as a bridge technology and replacing their fossil twin, leading to carbon-neutrality, as a carrier medium for green hydrogen, or even as green feedstock as for the prior-mentioned green ammonia for fertilizer production. One of the great advantages in derivative fuels is their direct applicability today.
A power-to-X solution
Next is a detailed look at the technologies that are available today. MAN has consistently developed power-to-X technology and offers turnkey plants with a capacity of 50 MW and more. The company’s power-to-X solution is a sustainable solution for synthetic fuel production and long-term energy storage. It responds to the fundamental challenges of decarbonisation. The direct use of synthetic fuels allows the decarbonisation of sectors which currently rely on fossil fuels, such as marine, aviation, or certain industrial processes.
Renewable energy is used to run an electrolyser, for example a PEM or an alkaline, which breaks water down into hydrogen and oxygen. The hydrogen is then put into a methanation reactor with carbon dioxide, resulting in synthetic natural gas (SNG). The carbon dioxide can be obtained either by carbon capture from in-house or adjacent industrial processes or power generation using amine scrubbing, pressure swing absorption, or membrane separation. The SNG can be stored, used directly, or injected into the existing gas infrastructure.
Hydrogen production by electrolysis
PEM electrolysis is a process by which electricity is used to split water into hydrogen and oxygen. It consists of a proton-permeable membrane, a cathode, and an anode. When water is added to the electrodes, the external voltage causes a catalytic effect, splitting the water. The hydrogen ions diffuse through the membrane.
To generate 1 kg of hydrogen, approximately 8.9 kg of water is required. In addition, approximately 7.9 kg of oxygen with a purity of 99.95% is produced. This corresponds to the purity required for further use in technical and medical applications. Water of tap water quality is required for electrolysis. The power requirement for 1 kg of green hydrogen is approximately 53 kWh.
H-TEC SYSTEMS is a subsidiary of MAN Energy Solutions and currently offers electrolysers with a nominal electrical output of up to 1 MW. All H-TEC SYSTEMS solutions are integrated, scalable, and containerised. An electrolysis capacity of 1 MW provides enough hydrogen to fill a car tank up to 90 times/d in a 24-hour operation period. These module sizes are particularly suitable for pilot projects and small industrial customers. The electrolyser consists of 110 kW stacks, which can be replaced if necessary, thus extending the service life of the plant. The maximum total electrolysis capacity is currently 10 MW, but will be expanded to 150 MW in the future with the new product Hydrogen Cube Systems (HCS). These are 2 MW modules which make it possible to cater to applications with a high hydrogen demand.
H-TEC SYSTEMS electrolysers have an integrated water treatment and deionisation system. Therefore, only water
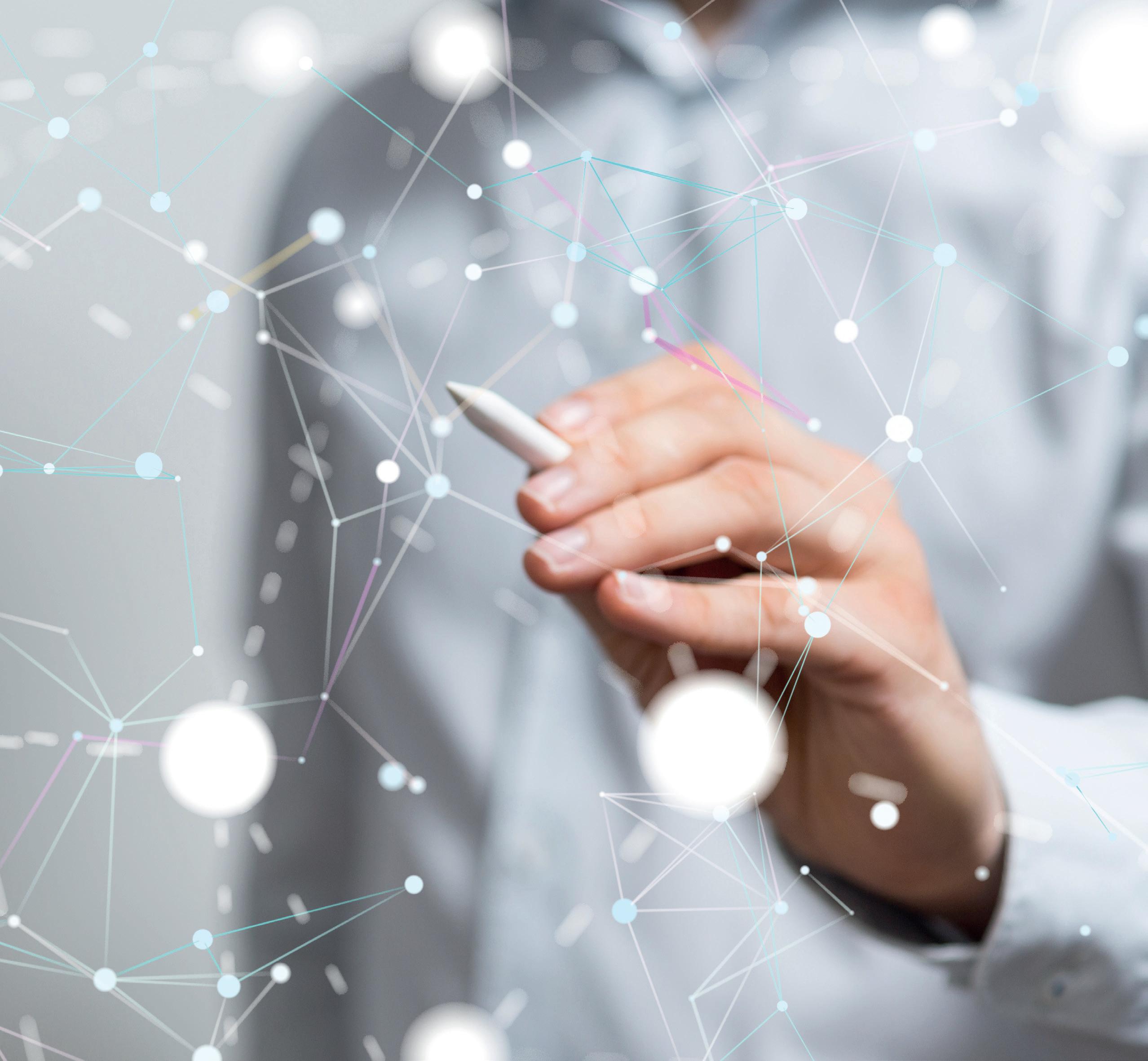