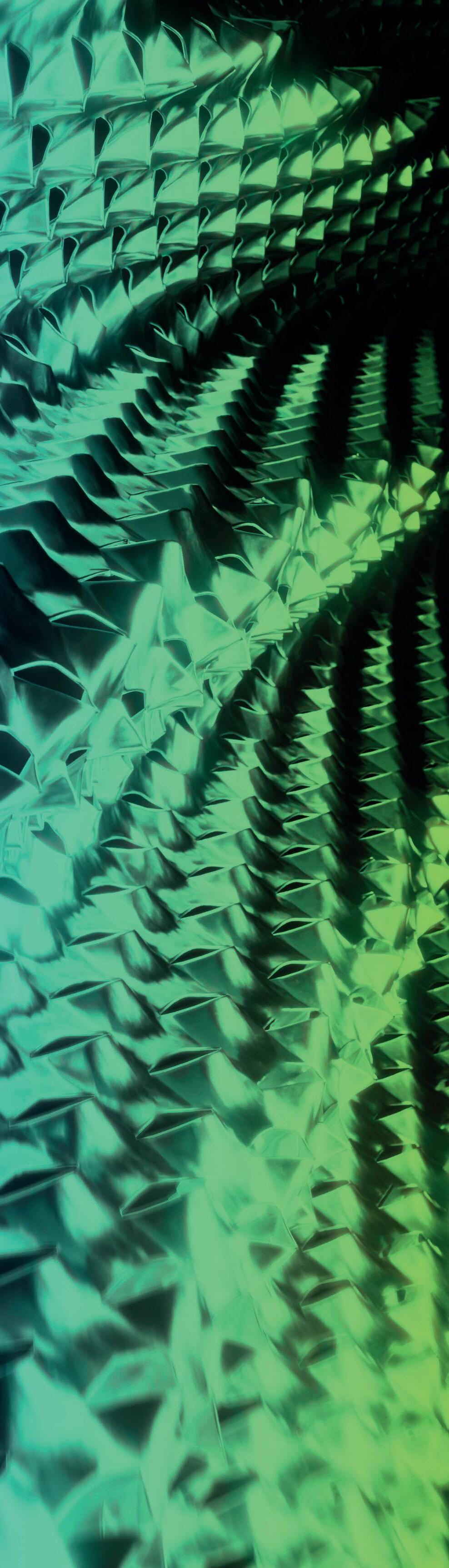
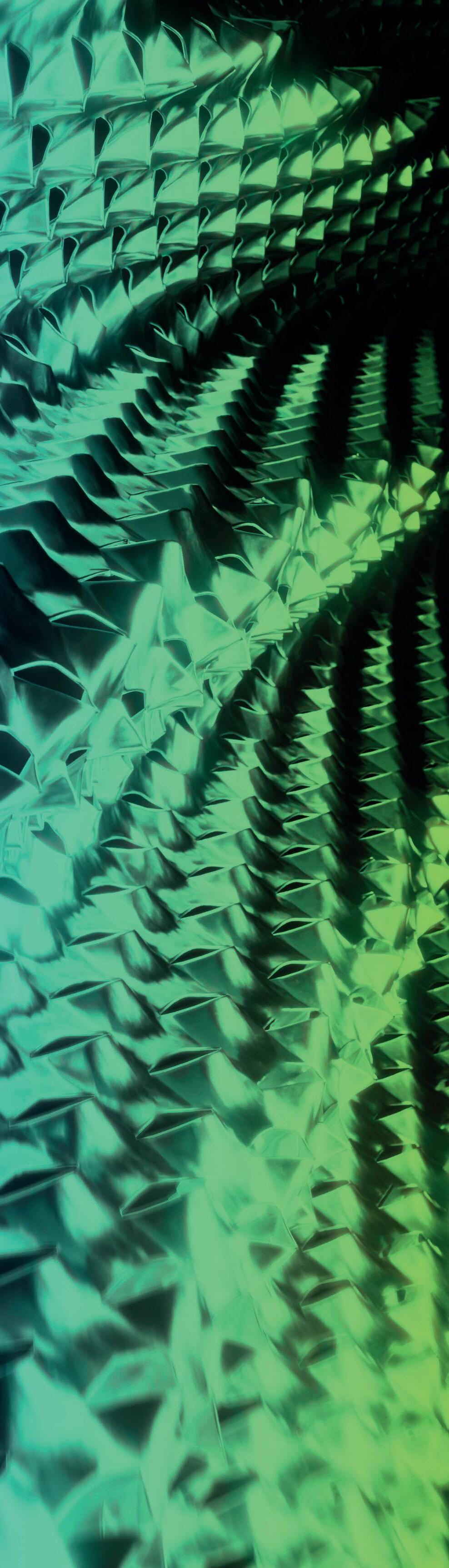
ENERGY GL BAL
Autumn 2024
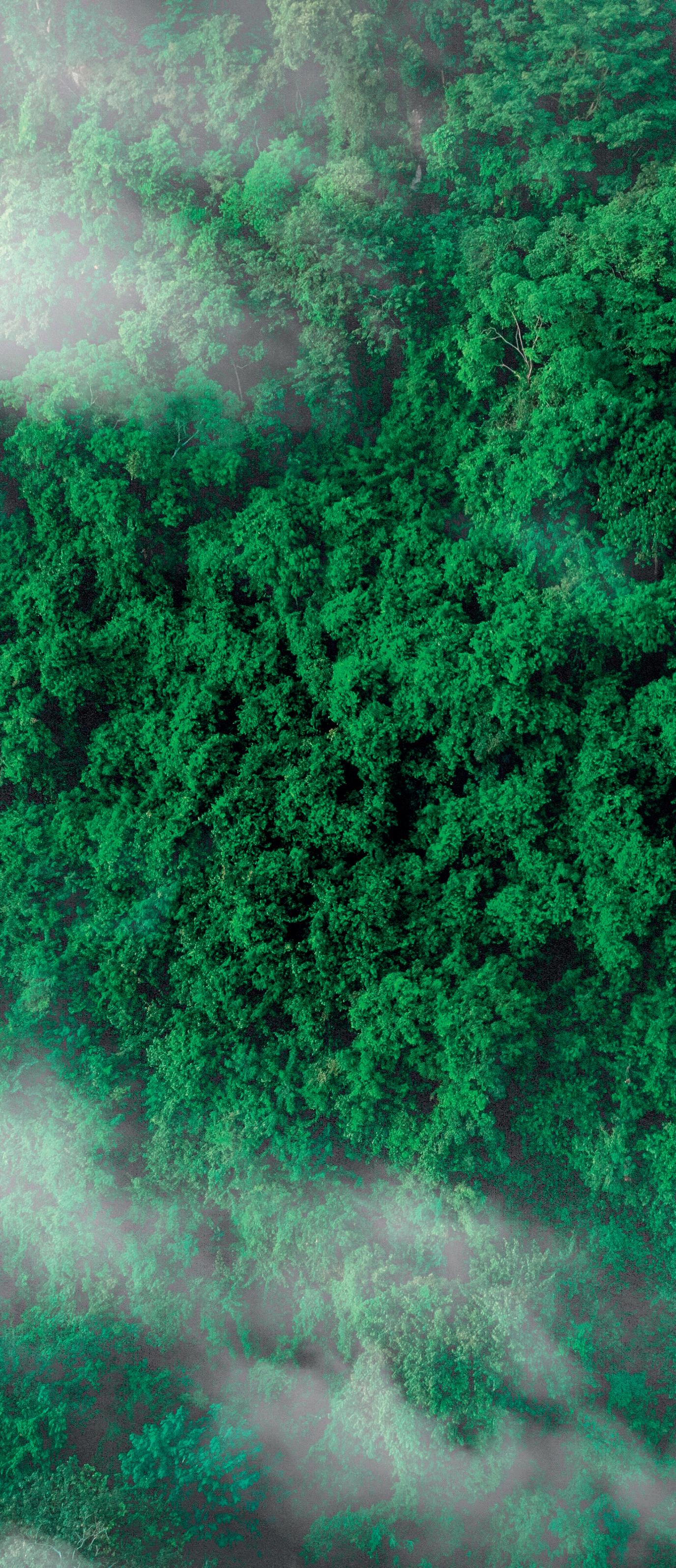
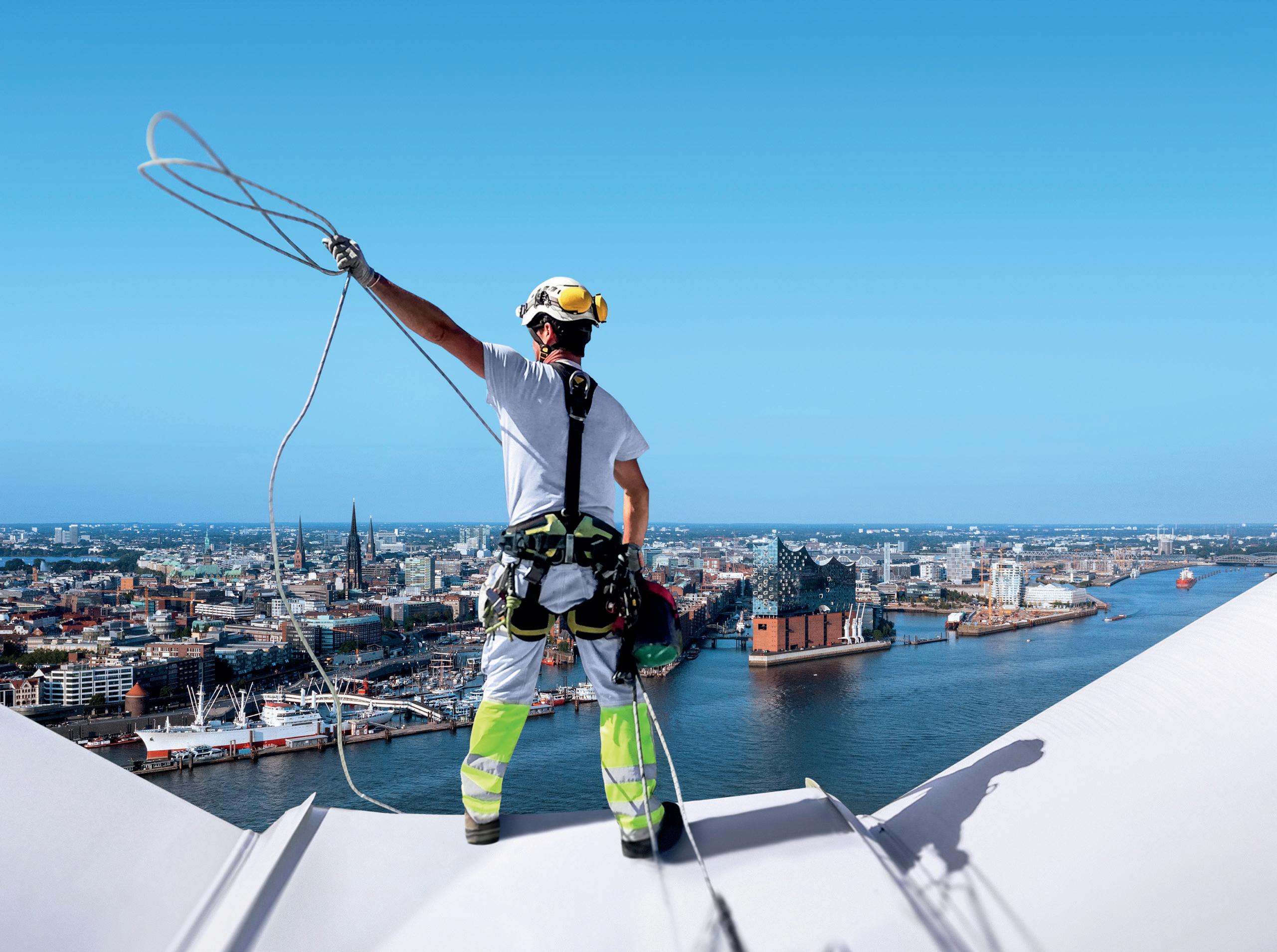
•Meet
•Get
•Visit
•Two
ENERGY GLOBAL
CONTENTS
03.Guest comment
04. The past, present, and future of Australian battery storage
Matthew Chadwick, PhD, Lead Research Analyst at Cornwall Insight, provides an overview of the battery energy storage industry in Australia.
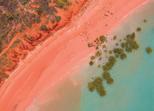
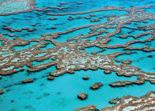

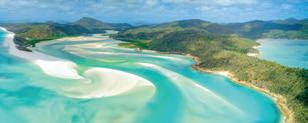
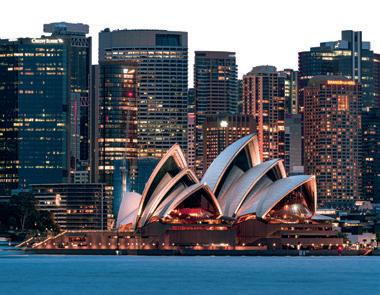
08. Securing subsea cables
David Maloney, Director Subsea Cables, DNV Energy Systems, emphasises that the certification of subsea cables for wind power generation is essential to ensuring safe and reliable deployment of the technology.
14. Enhancing offshore wind operations
Jessica Stump and David Inman, NOV, explain how improvements in modular support vessel design can help to enhance offshore wind operations and maintenance.
20.Creating a digital twin
Xiaobing Hu, Head of Applied Solutions, Manufacturing Intelligence division, Hexagon, considers why digitalisation is crucial in the acceleration of design, development, and operation of larger wind turbines to meet United Nation's Sustainable Development Goals.
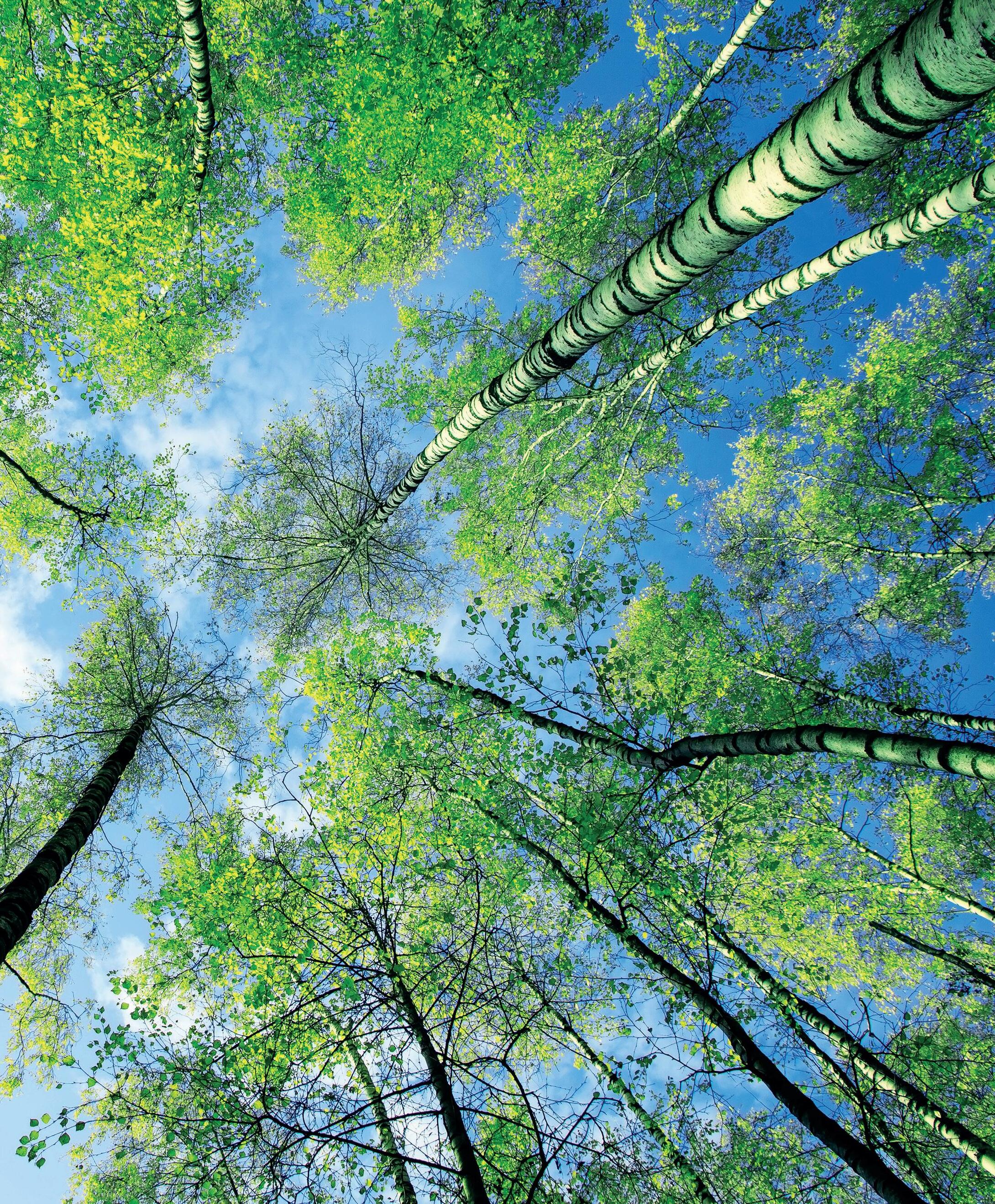
24.On the fast track
Frank Forsberg, Project Manager, ALICE Technologies, USA, discusses how artificial intelligence can be used to optimise and speed up project delivery of offshore energy assets.
28. Harnessing the power of electricity
Leo Hambro, Commercial Director, Tidal Transit, addresses the current state of the offshore wind servicing industry and highlights solutions for sustainably transitioning the sector to net zero.
34.Gathering intelligence early
Brian Bell, Global Director Offshore Wind, Fugro, explores the often-overlooked development stage of offshore wind projects and how geo-data can be used to ensure success.
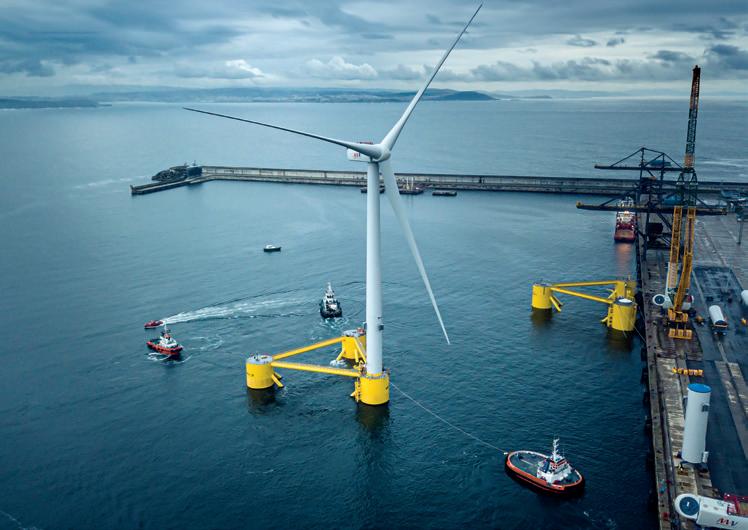
38. An evolution in wind energy
Stefano Santoni, Davi, Italy, examines the need for offshore and onshore wind turbine components to meet increasing demand in the wake of the growth of wind energy.
42.Global news
The new Sulzer MellapakEvo TM structured packing, in combination with advanced MellaTech
column internals, delivers unparalleled performance improvement for columns. Verified at an independent testing facility, this latest mass transfer technology is proven to enhance column performance in both capacity and efficiency.
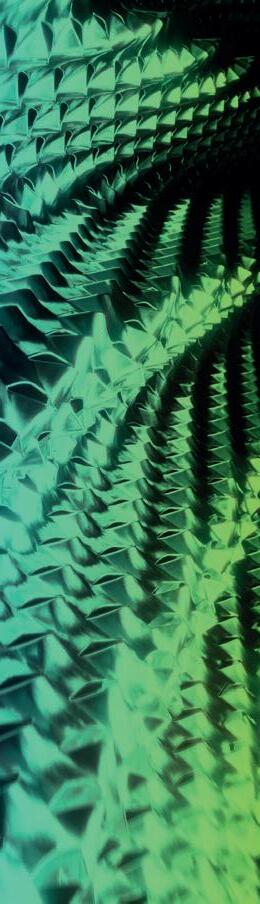
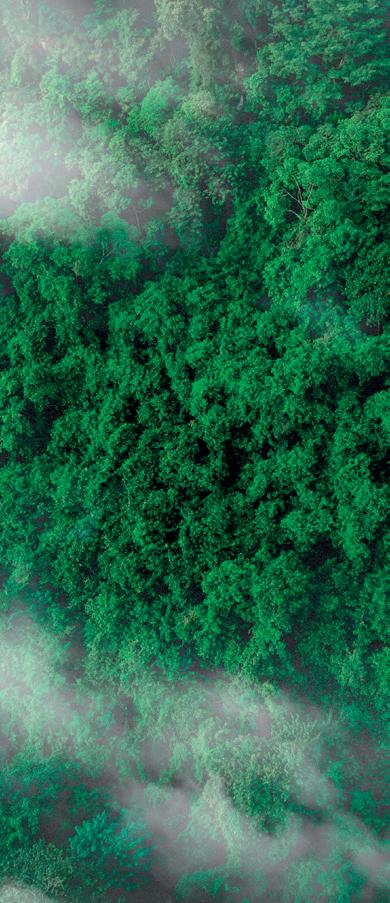
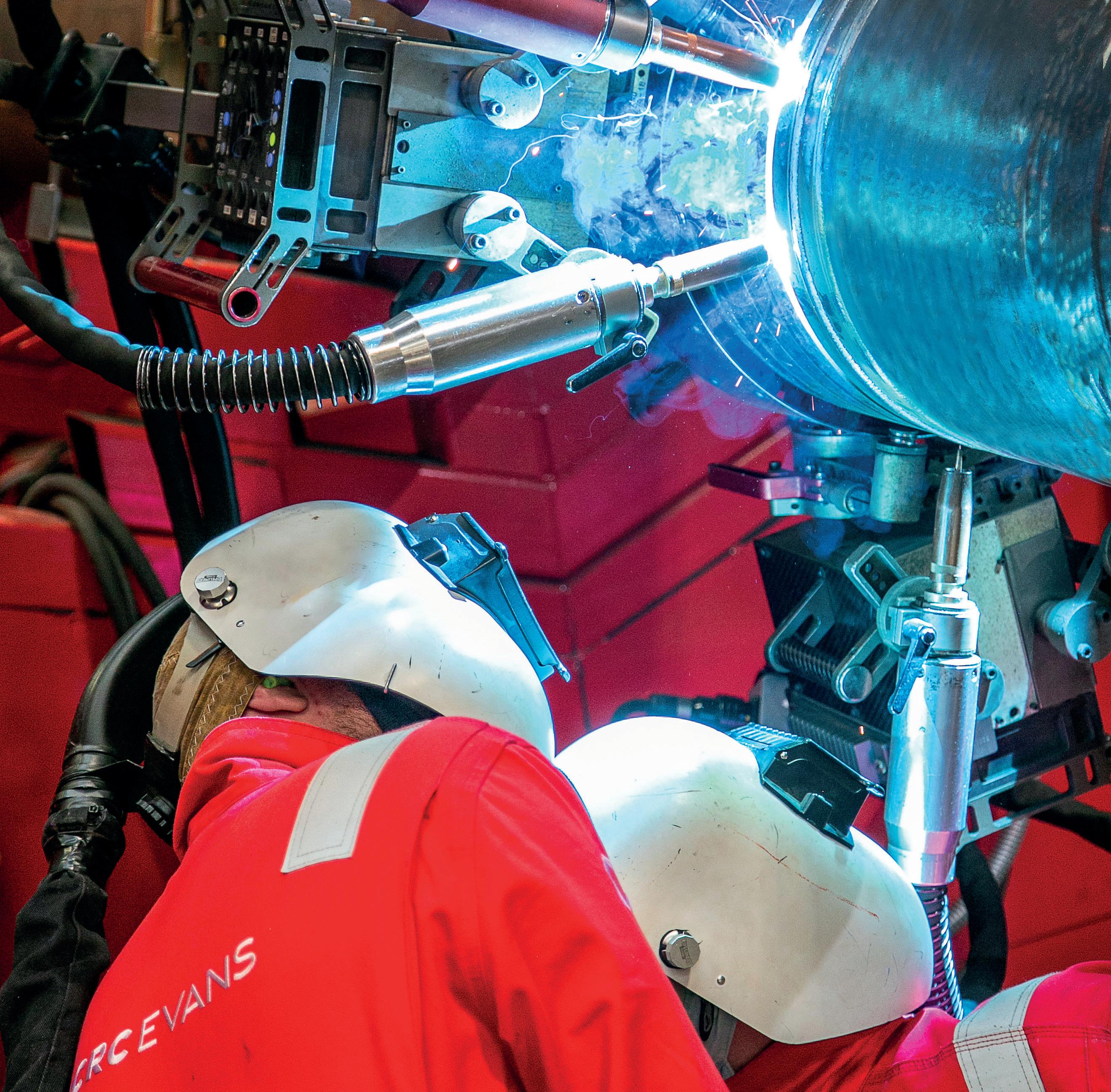
Our priority is the safe on-time delivery of your global energy projects. CRC Evans utilises market-leading welding and coating services, technologies and advanced data solutions, combined with a right first time approach.

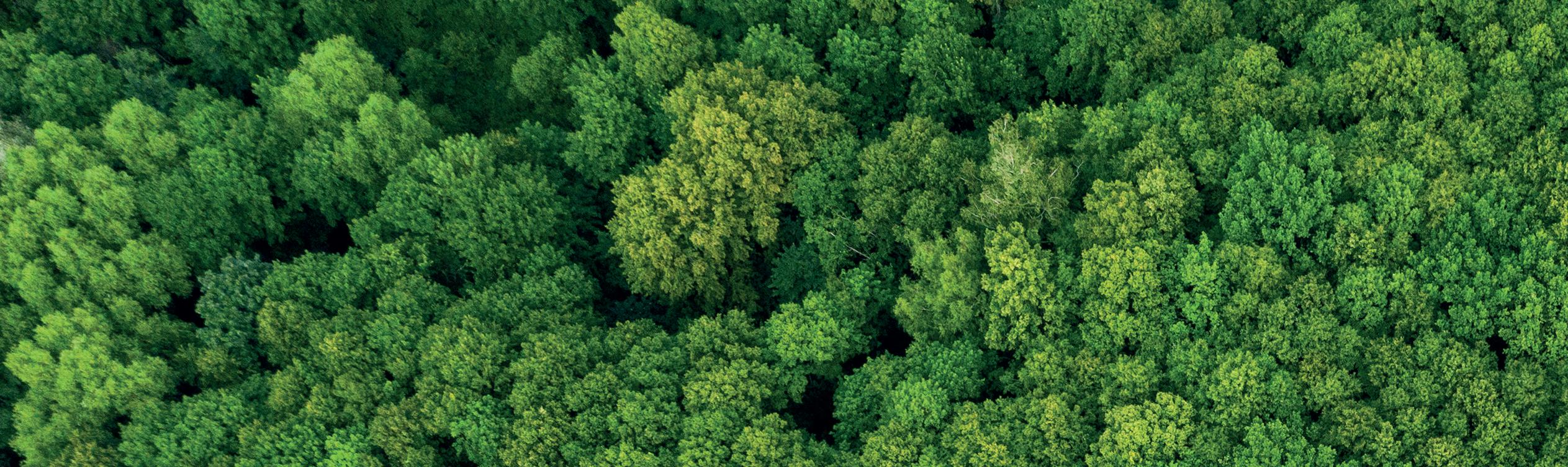
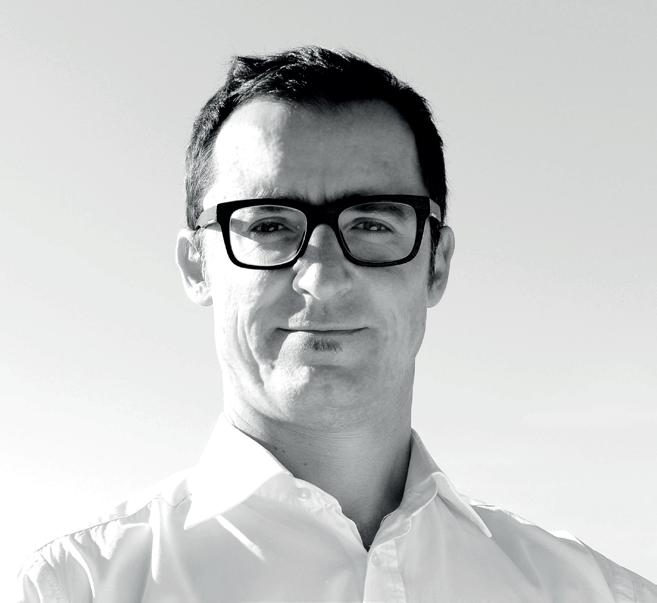
MANAGING EDITOR
James Little james.little@palladianpublications.com
EDITOR
Jessica Casey jessica.casey@palladianpublications.com
EDITORIAL ASSISTANT
Oliver Kleinschmidt oliver.kleinschmidt@palladianpublications.com
SALES DIRECTOR
Rod Hardy rod.hardy@palladianpublications.com
SALES MANAGER
Will Powell will.powell@palladianpublications.com
PRODUC TION DESIGNER
Amy Babington amy.babington@palladianpublications.com
EVENTS MANAGER
Louise Cameron louise.cameron@palladianpublications.com
DIGITAL EVENTS COORDINATOR
Merili Jurivete merili.jurivete@palladianpublications.com
DIGITAL ADMINISTRATOR
Nicole Harman-Smith nicole.harman-smith@palladianpublications.com
DIGITAL CONTENT ASSISTANT
Kristian Ilasko kristian.ilasko@palladianpublications.com
ADMINISTRATION MANAGER
Laura White laura.white@palladianpublications.com
Editorial/Advertisement Offices: Palladian Publications Ltd
15 South Street, Farnham, Surrey, GU9 7QU, UK +44 (0) 1252 718 999 www.energyglobal.com
Cristiano Spillati Managing Director, Limes Renewable Energy COMMENT
As new guidance is introduced to speed up the energy transition, we must learn from successful strategies to involve and empower communities in the process. As Europe works towards its climate goal to cut emissions by 55% and increase the share of renewable energy to as much as 45% by 2030, the European Commission has published guidelines outlining how and where renewables must be deployed in pursuit of these targets. The guidance comes at a critical point –a smart approach is integral to success. The reality of the situation is such that Europe and the wider global community does not possess the luxury of time.
Of course, the success of the transition is contingent on the successful implementation of projects and initiatives. The success of these projects is not determined only by the potential capacity generated or the efficiency of the project, but in the first instance, by the extent of community engagement and acceptance. It is integral that the local community is involved in the decision-making process, during planning and implementation to ensure their active engagement and ongoing support.
This becomes increasingly apparent when considering the number and scale of projects required to meet renewable targets. To allow the necessary projects to progress beyond proposals, and to expedite a process which can fall foul of lengthy delays, it is crucial to move beyond the overly simplistic label of NIMBYism. Developers and policy makers alike must recognise the diverse and legitimate reasons why citizens might oppose renewable energy projects. A real effort is required to understand the opposition posed by local communities and to express the potential benefits of renewable energy in the area. The shift must come toward consistent standards, benefit sharing and for the prioritisation of community engagement as a central component of procedure.
European projects have much to learn from the implementation of successful engagement strategies elsewhere. The wider global community continues to demonstrate the impact of such consistent approaches. Achieving significant, positive, and localised impacts from renewable energy projects requires moving away from a one-size-fits-all strategy. Instead, it necessitates early and active stakeholder involvement and a thorough understanding of the community and its environment. Projects aiming to benefit local areas must prioritise relationship-building and partnerships with the communities they serve, ensuring solutions are tailored to local needs and complexities. Businesses and projects must acknowledge their temporary presence on the land and respect the local residents. Successful development hinges on collaboration with local communities, governments, landowners, developers, and workers. Early and inclusive engagement, particularly with those who may initially oppose the project, is key to successful implementation and fostering community pride and ownership.
Successful renewable energy initiatives share a common theme: their local success hinges on a thoughtful, co-operative, and ongoing approach that integrates local knowledge, expertise, and commitment to achieving positive outcomes for both the community and the area throughout the planning, construction, and operational phases. Strategies must be customised to fit the specific locale and remain flexible. Projects adhering to these principles demonstrate the potential benefits that new renewable energy ventures can offer to residents. Businesses and policymakers must strive to learn from the successes of community-supported projects and collaborate with residents to ensure their effective implementation. Essential sustainable and renewable projects need to be located somewhere, and when developed appropriately, communities can thrive.
OF AUSTRALIAN BATTERY STORAGE
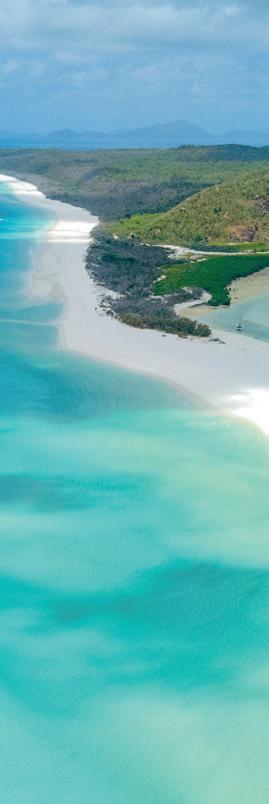
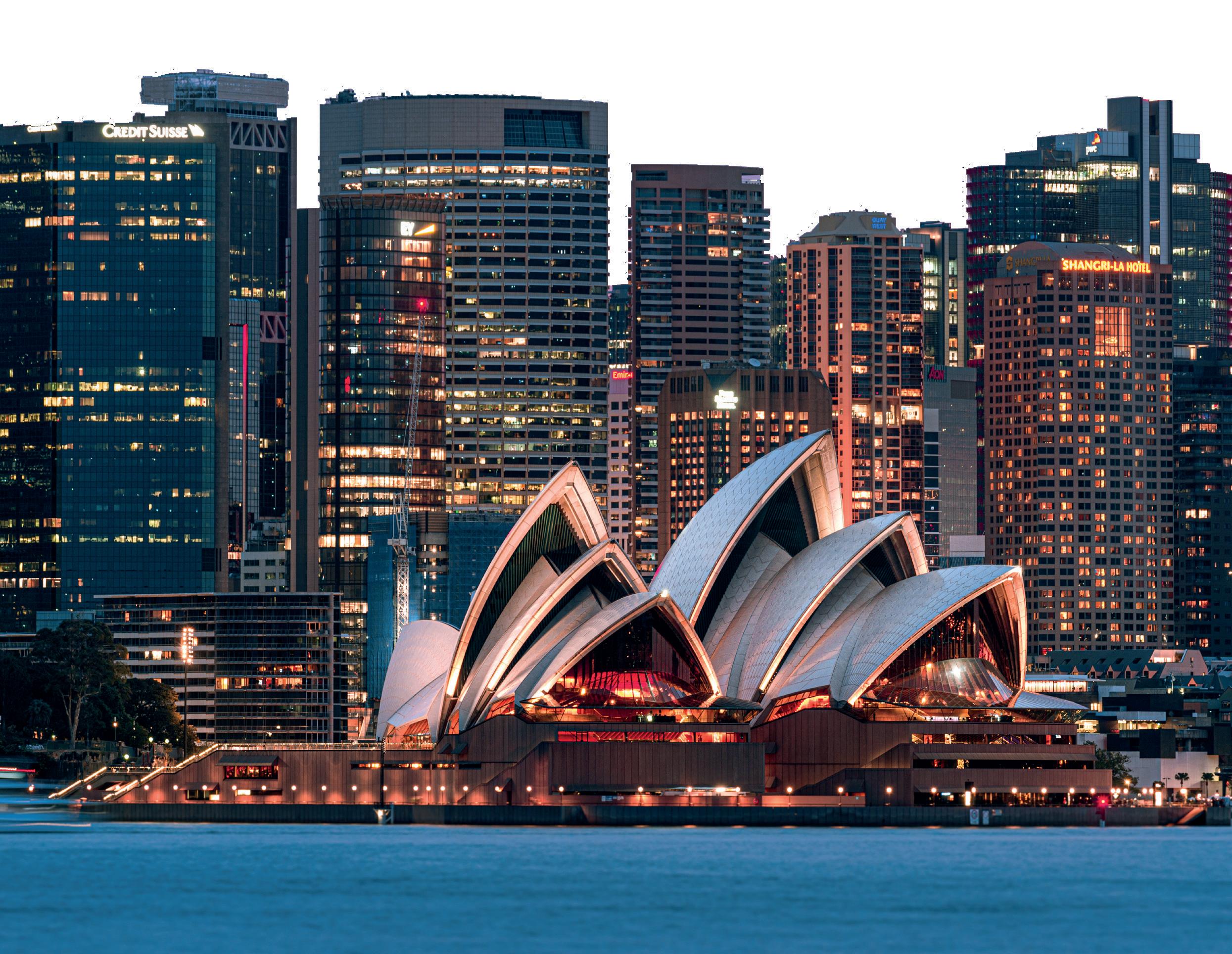
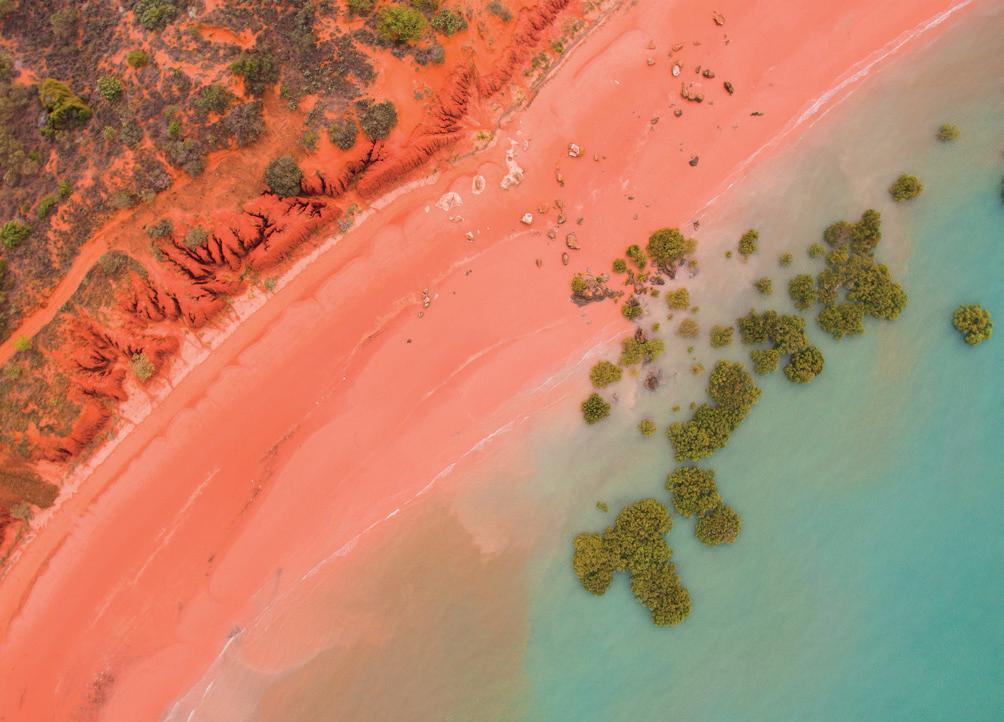
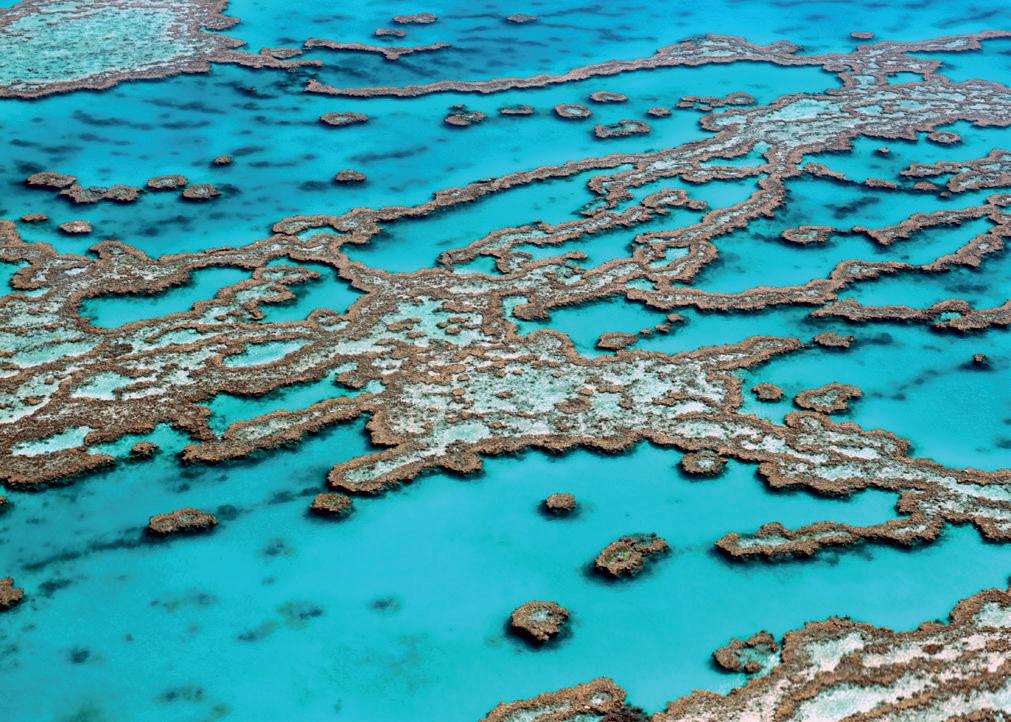
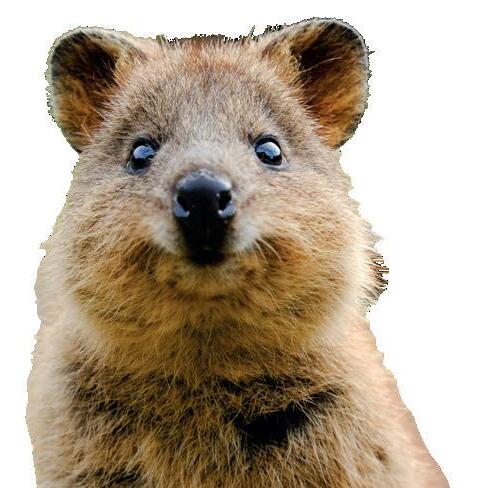
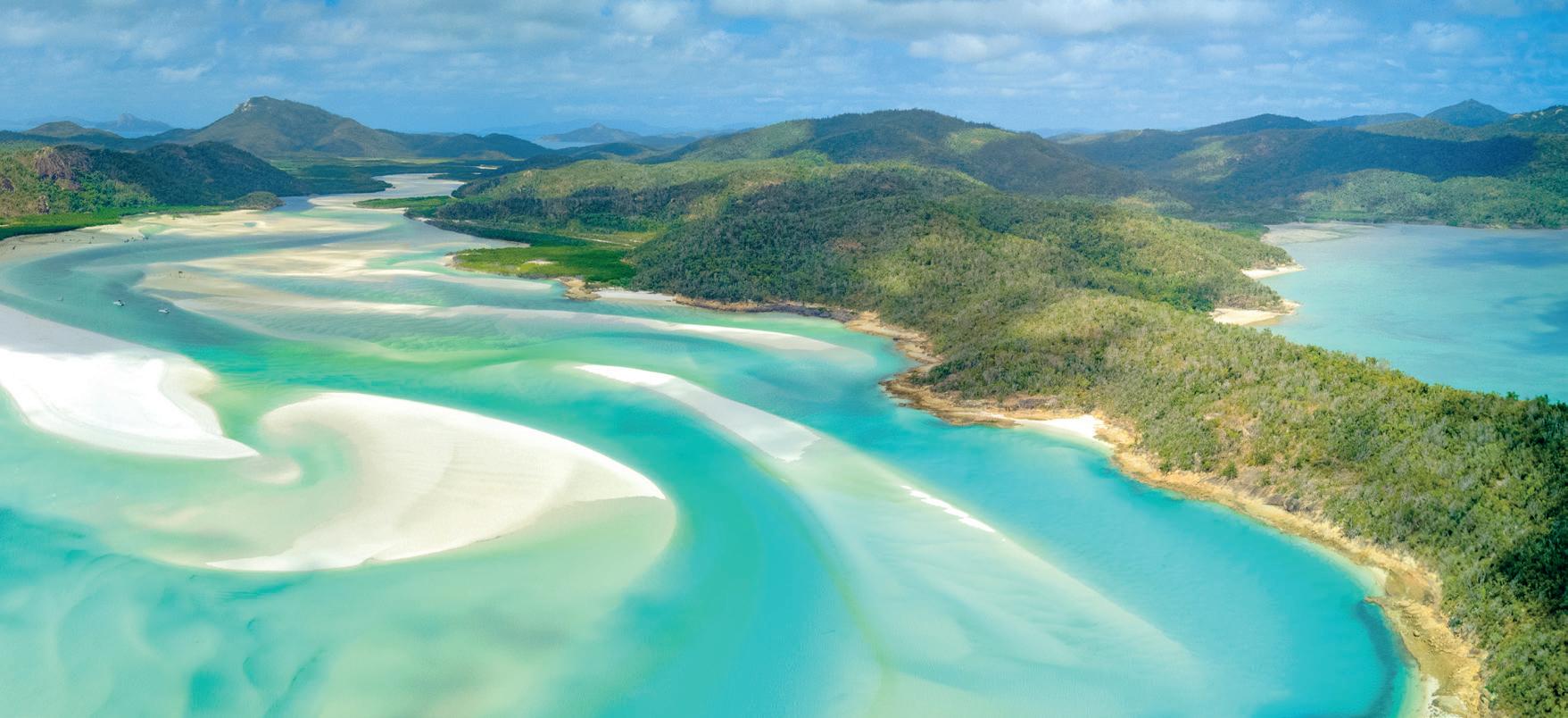
Matthew Chadwick, PhD, Lead Research Analyst at Cornwall Insight, provides an overview of the battery energy storage industry in Australia.
he Australian Government has committed to a 43% reduction in carbon emissions by 2030 (relative to 2005 levels) and net zero by 2050, with the Net Zero Plan – currently being developed for publication later in 2024 – to set out the key policies and measures to meet these targets. These will build on current emissions reduction policies, including the non-legislated target of 82% of electricity generation from renewables by 2030.1 Whilst there is an ongoing debate around Australia’s climate targets and how quickly they can be met, it is clear that renewables will have a key role to play in decarbonising the electricity sector and will account for a growing proportion of Australian electricity generation out towards 2050.
A growing need for batteries
As the penetration of intermittent renewables within the electricity mix increases and the system inertia decreases, this creates a growing need for system flexibility. As an island nation, with no physical interconnection to neighbouring markets, this need for flexibility within the Australian electricity system is further compounded. Cornwall Insight’s latest
National Electricity Market (NEM) Benchmark Power Curve highlights the significant annual growth in electricity storage capacity needed to meet this growing need for flexibility (Figure 1). Although there are a range of different electricity storage technologies that can provide flexibility to the system, the 2024 Integrated System Plan published by the Australian Energy Market Operator (AEMO) indicates that batteries, both distributed and utility scale, are expected to make up the majority of installed electricity storage capacity out towards 2050.2
Compared to other electricity storage technologies, batteries have a relatively low upfront cost and short installation timeline, as well as a greater geographical flexibility on where they can be located. Batteries are also able to respond faster than other electricity storage or flexibility providing technologies and so are better suited to activity in markets such as the Frequency Control Ancillary Services (FCAS), which have provided lucrative revenues in recent years. The combination of these factors has made batteries the most attractive electricity storage technology in the Australian market. However, other longer-duration, electricity storage
technologies are expected to be required as the penetration of renewables continues to grow and the potential for longer periods of low electricity generation, so-called ‘renewable droughts’, increases.
The forecasted growth in battery storage capacity can already be seen in recent investment and development pipeline trends. The Clean Energy Council’s 1Q24 report highlighted that in the last quarter, 760 MW of storage capacity received a financial commitment, with a further 750 MW commencing construction.3 These projects contribute to an electricity storage pipeline of 8.4 GW that have either secured a financial commitment or are currently under construction. The Clean Energy Council report also outlines that this was the fourth consecutive quarter in which electricity storage projects secured financial investment commitments of over AUS$1 billion. These recent trends showcase that alongside the growing system demand for electricity storage there is also a clear appetite amongst developers and investors for these projects.
Recent battery revenues
In recent years, operational battery revenues have been dominated by the returns available under the FCAS,
with >80 – 90% of revenues for many assets coming from these services. In particular, batteries have accounted for a significant volume of the enablement in the quicker response FCAS markets (6 secs., 60 secs., and 5 mins.) where they are better suited than more ‘traditional’ generation (e.g. coal fired power stations) to participate. Whilst FCAS have formed the bulk of revenues for most battery assets, this has particularly been the case for the shorter duration batteries (<1 hour), with longer durations getting a greater proportion of their revenues from wholesale arbitrage.
What does the future look like for batteries?
Battery activity in the FCAS markets has seen lucrative returns in the last few years, supporting the business case for the aforementioned growth in investment and project development. However, Cornwall Insight’s latest NEM FCAS Market Curve highlights that this expected future growth in battery capacity is likely to significantly suppress the revenues available from the FCAS markets. By FY30, Cornwall Insight’s forecast indicates that the average AUS$/MW price across the different FCAS markets will be reduced to 7 – 31% of the prices seen in FY23, with the largest percentage declines seen in the faster response markets.
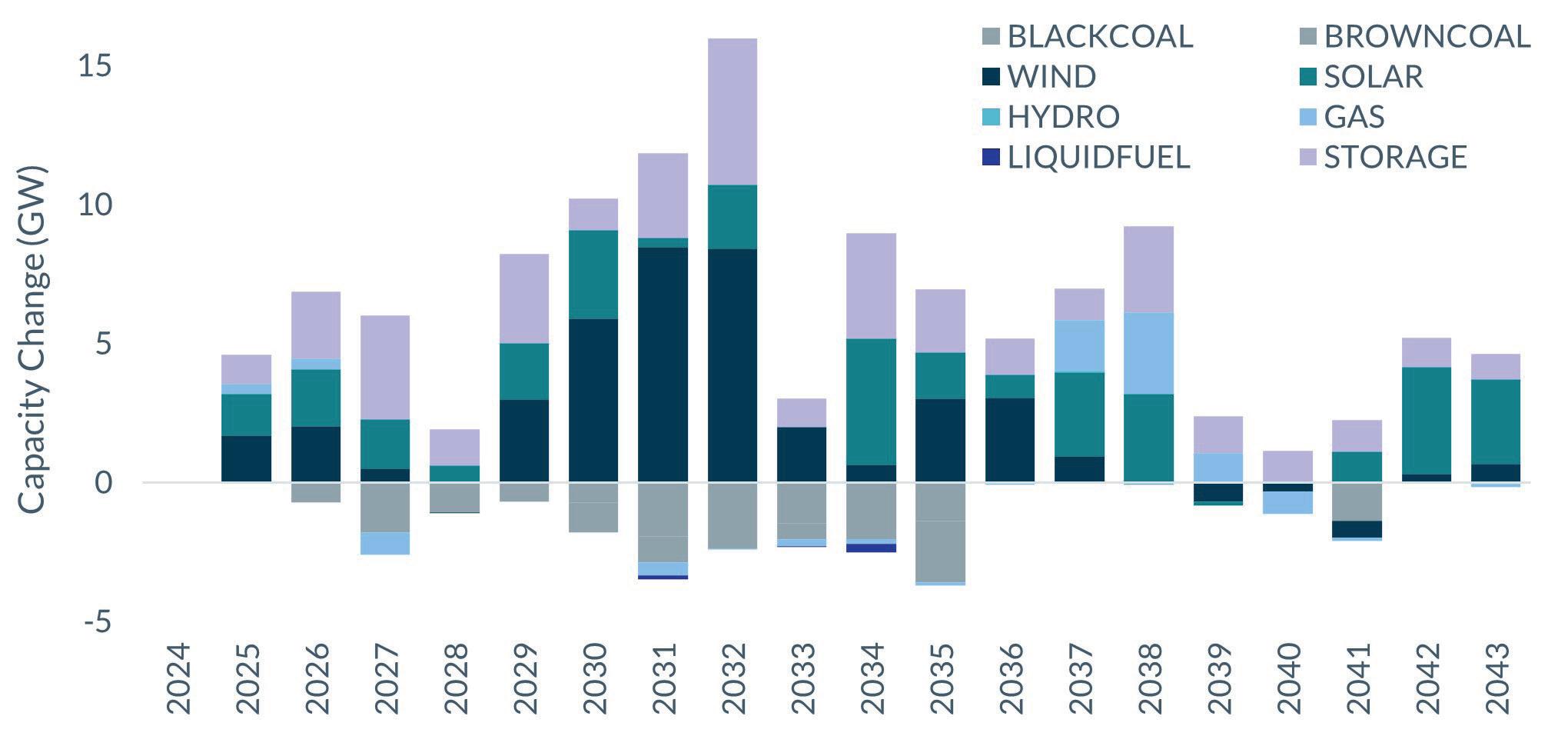
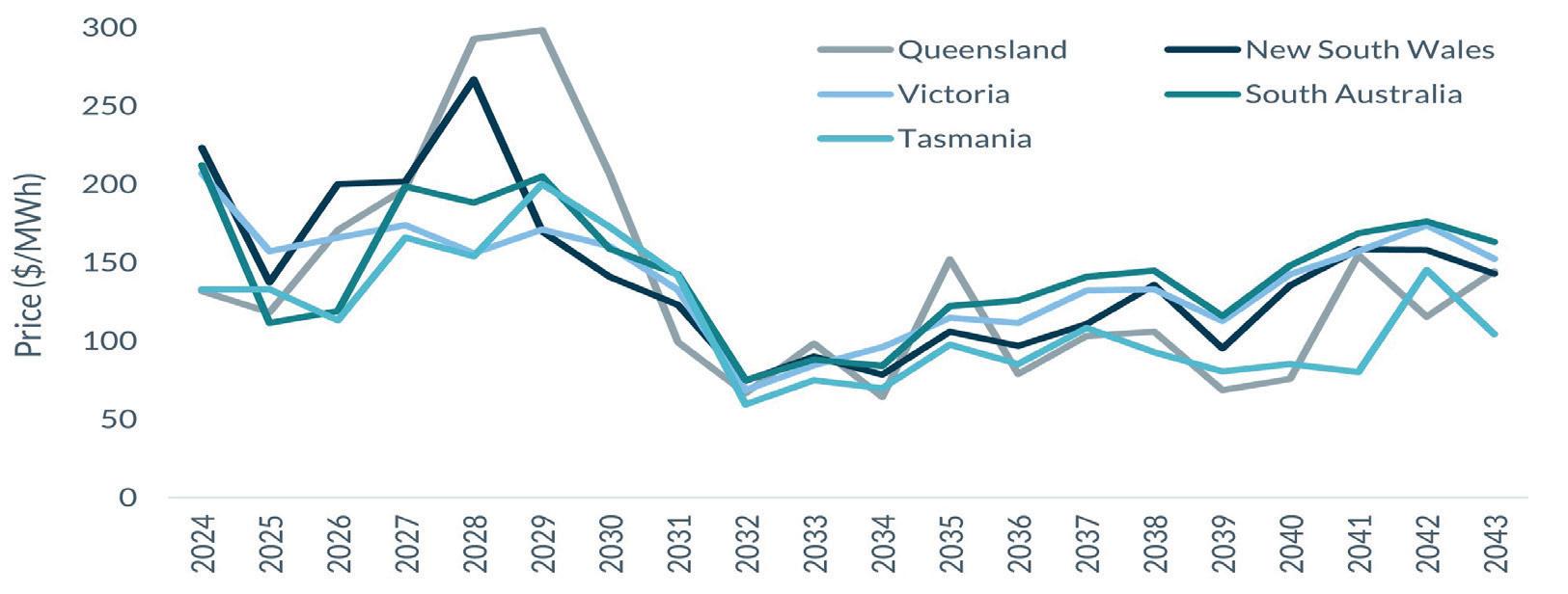
This saturation of the FCAS markets and concurrent reduction in revenues is expected to have an impact on the overall prices that batteries can capture, with a decline across all regions of the NEM post-2030 (Figure 2). However, the saturation of the FCAS markets is also expected to see an evolution in the revenue stack – the combination and optimisation across a series of different revenue streams – for batteries, with a shift towards a greater focus on wholesale arbitrage. The importance of wholesale arbitrage, where a battery charges when electricity is cheap and then discharges when it is expensive to create a price spread and generate revenues, is likely to grow as the volume of renewable energy, and in particular solar, increases. The growth of both utility and residential scale solar installations
Figure 1 Annual capacity mix change (GW), 2024 – 2043.
Figure 2 . Captured price for electricity storage assets (AUS$/MWh) by state, 2024 – 2043.
is creating a surfeit of generation compared to demand during the middle of the day, resulting in increased rates of generation curtailment and lower prices. Across 2022, over 6% of half hourly intervals between 11:30 and 13:30 saw negative prices, up from less than 2% over the same time of day in 2016. Batteries can, therefore, take advantage of these low or negative prices in the middle of the day to charge and then discharge when prices are higher. Alongside generating revenue for battery owners and operators, this wholesale arbitrage also helps to better balance supply and demand on the system.
Although the growth in intermittent renewables is creating a greater opportunity for battery arbitrage, the time of day price profile is also evolving. At present, there is a prominent peak in both demand and prices during the evening (17:00 – 19:00) and discharging during this peak can create the greatest price spreads for batteries. Over the second half of this decade, this evening peak is expected to flatten, with fairly consistent prices expected overnight (17:00 – 06:00) alongside the low prices during the day. This evolution will reduce the price spread achievable for batteries but will open up a greater period of the day during which they can discharge to secure the highest prices, signalling a change in the operating strategy for battery operators.
Conclusion
Overall, the future remains bright for batteries in Australia, with EY’s June 2024 Renewable Energy Country Attractiveness Index (RECAI) ranking Australia as the fourth most attractive
global market for investment in batteries.4 Whilst the increasing capacity connecting to the system and subsequent saturation of the FCAS markets are expected to reduce overall returns, there will be a growing role for batteries in managing supply-demand imbalances through wholesale arbitrage. Battery operators will need to adapt their business strategies to the changing revenue stack, alongside the evolving time of day price profile but are expected to still be able to make generous, if reduced, returns over the next 20 years.
Despite the outlook seeming unfavourable at first glance, batteries will have a crucial role to play in flexibility provision for an increasingly renewable-dominated system. Battery owners and operators cannot afford to sit still and will need to adapt and grow with the changing energy market to remain profitable. But if they can evolve to match the market, then batteries will continue to provide the system flexibility necessary for Australia to achieve a net-zero power system.
References
1. Annual Climate Change Statement 2022: The first Annual Climate Change Statement to Parliament as required by the Climate Change Act 2022’, Australian Government, Department of Climate Change, Energy, the Environment and Water, (2022), www.dcceew.gov.au/sites/default/files/documents/annual-climate-changestatement-2022.pdf
2. ‘2024 Integrated System Plan For the National Electricity Market’, Australian Energy Market Operator, (2024), https://aemo.com.au/-/media/files/major-publications/ isp/2024/2024-integrated-system-plan-isp.pdf?la=en
3. ‘Renewable projects quarterly report Q1 2024’, Clean Energy Council, (2024), https://assets.cleanenergycouncil.org.au/documents/resources/reports/Renewableprojects-quarterly-report_Q1-2024.pdf
4. DE GIOVANNI, A., and WARREN, B., ‘Four factors to guide investment in battery storage’, EY, (14 June 2024), www.ey.com/en_uk/recai/four-factors-to-guide-investmentin-battery-storage
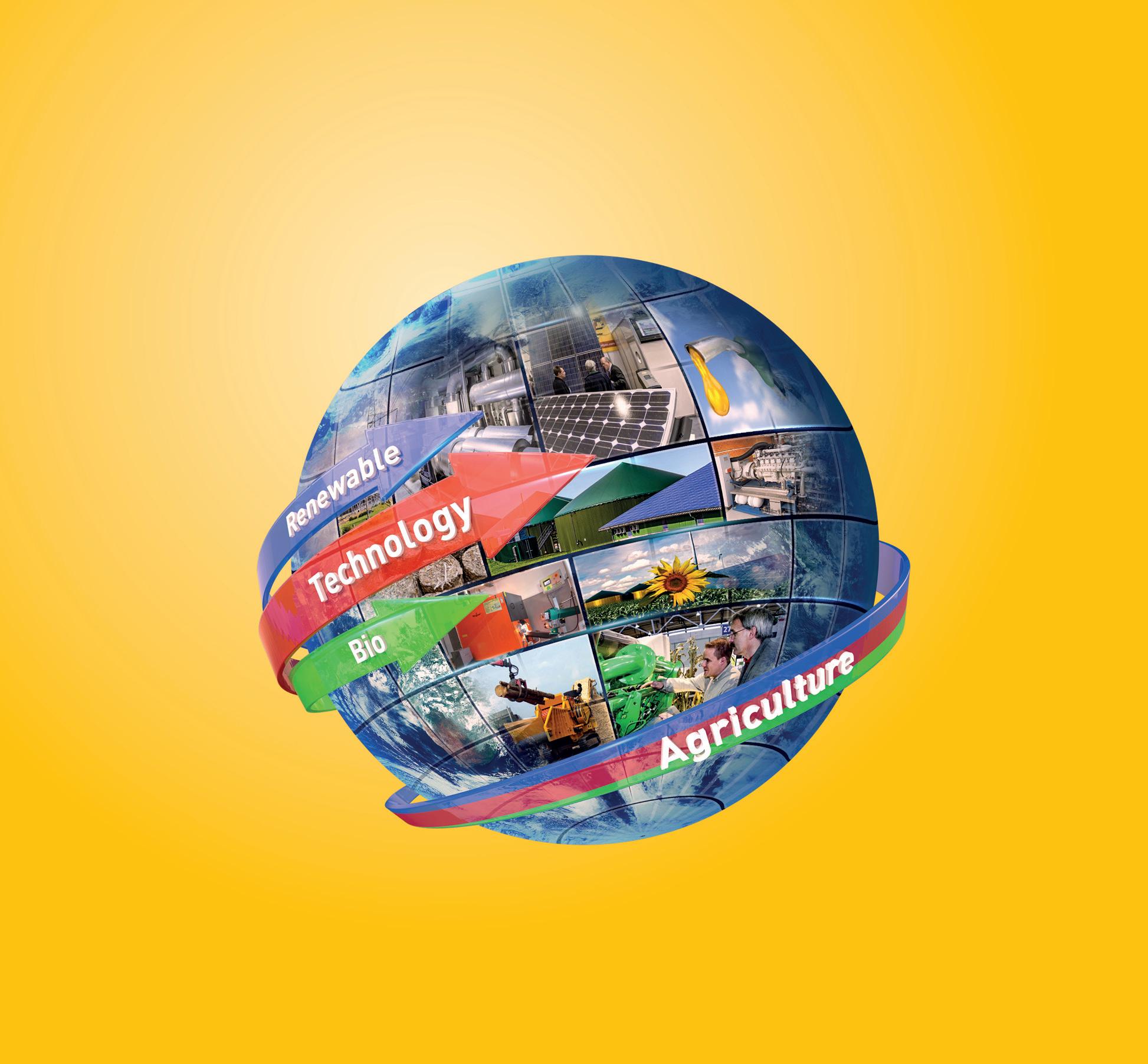
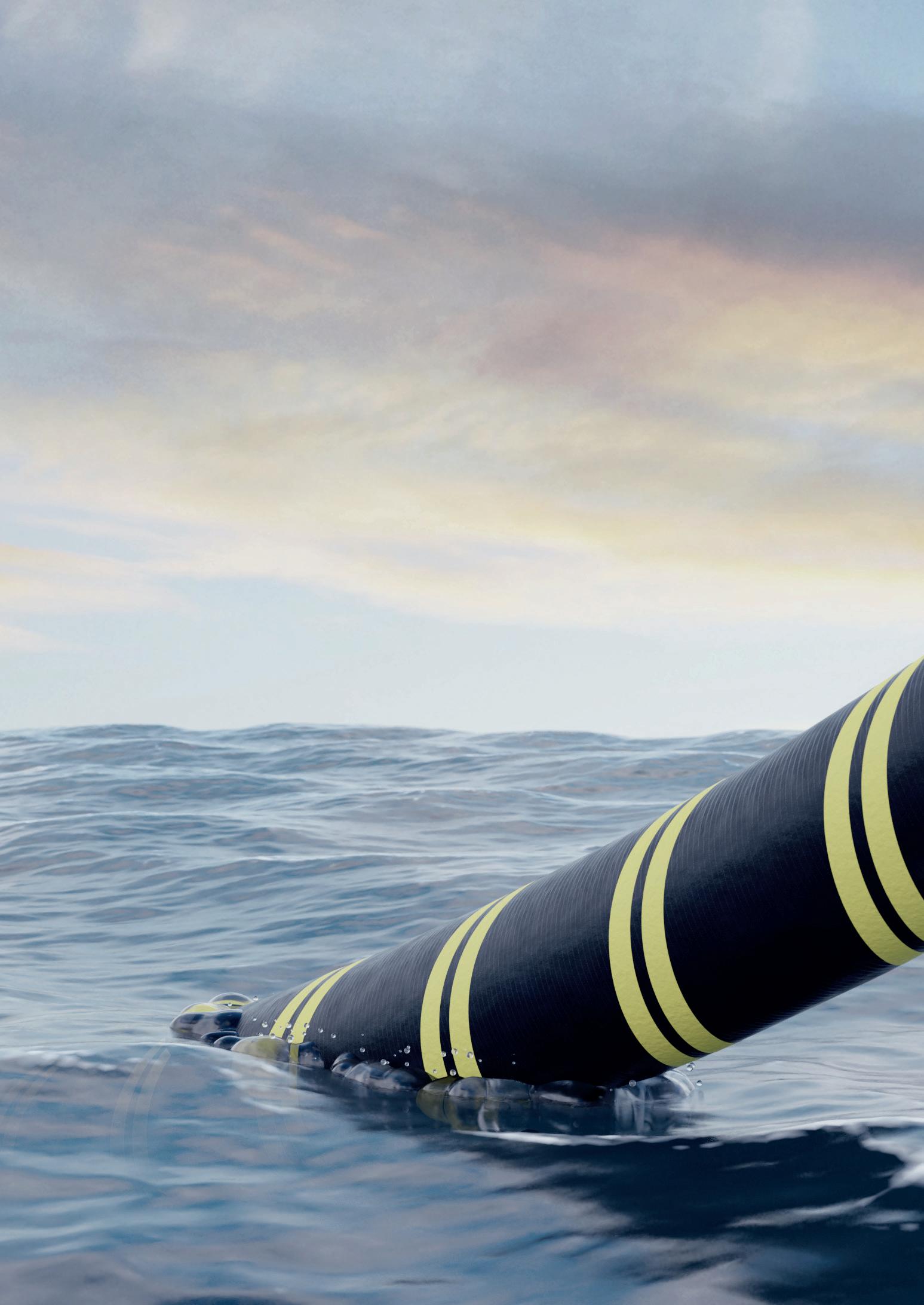
Figure 1 Submarine power cables.
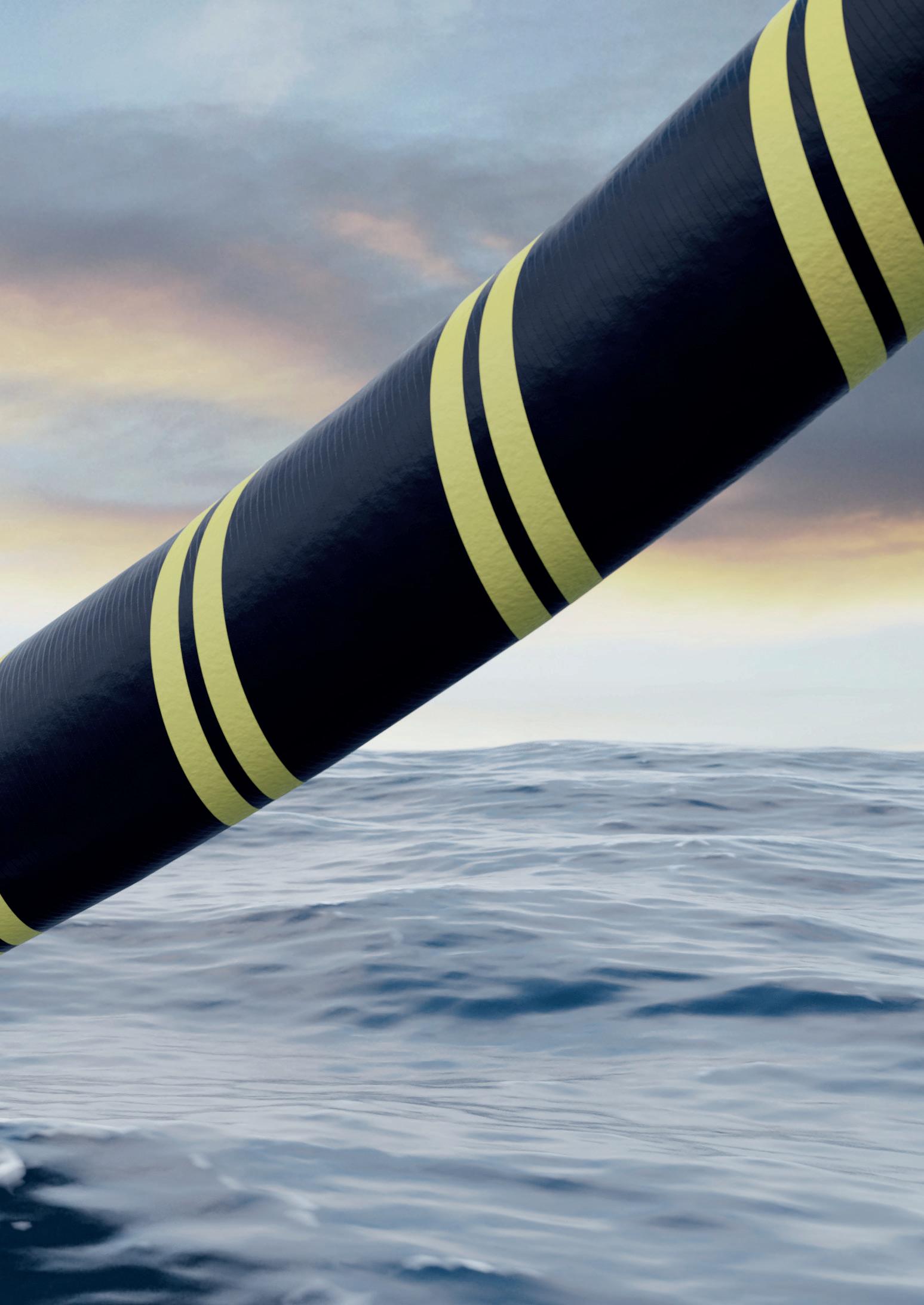
David Maloney,
Director Subsea
Cables, DNV Energy Systems, emphasises that the certification of subsea cables for wind power generation is essential to ensuring safe and reliable deployment of the technology.
fter years spent proving it can be a commercially and technically viable cog in the world’s energy mix, floating offshore wind is set for a crucial role in the energy transition. It is a sector with almost unparalleled potential, allowing developers to place turbines in deeper waters where the winds are stronger and more reliable. To put the size of the prize into perspective, it is estimated that floating turbines will unlock as much as 80% of the world’s offshore wind resource.1
In DNV’s latest Energy Transition Outlook, the company forecast that floating turbines will contribute 5% of total wind generation by 2050, a meteoric rise given its current microscopic market share. As it stands, the levelized cost of energy (LCOE) for floating offshore wind is more than three times that of fixed offshore wind. But despite a recent deceleration in the closure of that gap, DNV remains optimistic – forecasts predict that floating offshore wind will cost only twice the amount of fixed bottom by 2032. By the middle of the 21st Century, economies of scale and improved efficiencies in production mean that disparity will drop to about 30%.
Europe is shaping up to be the global leader in the floating offshore wind market, building on the region’s fixed bottom pedigree to deliver mammoth developments in the North Sea and beyond. But as much as the sector should leverage the successes of fixed bottom wind, floating wind developers must also pay close attention to the challenges that have arisen, many of which they are also likely to encounter.
A familiar technology presenting new problems
One piece of this colossal offshore wind puzzle that is yet to receive the attention it deserves are subsea power cables and the unique challenges they present. Paradoxically, this is something that the industry is well versed in – companies have been laying power cables for decades – but this familiarity means that it has been seen as proven technology. As such, it is often not given the focus it deserves.
The scale of offshore wind connections, the various cable entries at any one foundation, and the interface design also means that previously unknown issues have reared their heads. It is a problem that came to the fore in 2021, when Ørsted revealed it had been hit by a spate of cable issues at several of its offshore wind farms, incurring significant financial costs.
Research from Lloyd Warwick, an international specialist in loss adjustment and claim management, has found that power cable failures are to blame for around 83% of all offshore wind related financial losses and insurance claims. A fact which has remained constant since at least the early 2010s, if not earlier. Moreover, with an average interruption period of between 40 – 60 days for repairs to be carried out, the average combined losses (repair and loss of generation) ranges between US$1.2 million (£941 000) – US$12 million (£9.4 million) for array cables and US$10 million (£7.8 million) – US$30 million (£23.5 million) for export cables.
Gazing into the floating wind crystal ball
Owing to the fact that floating wind is still in its infancy, these statistics relate to fixed bottom projects, but they provide
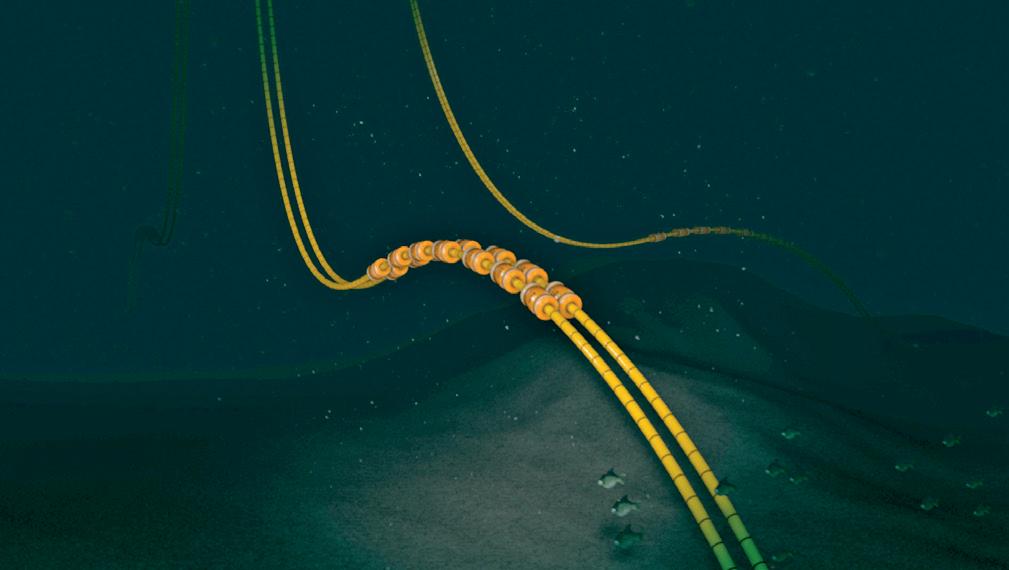
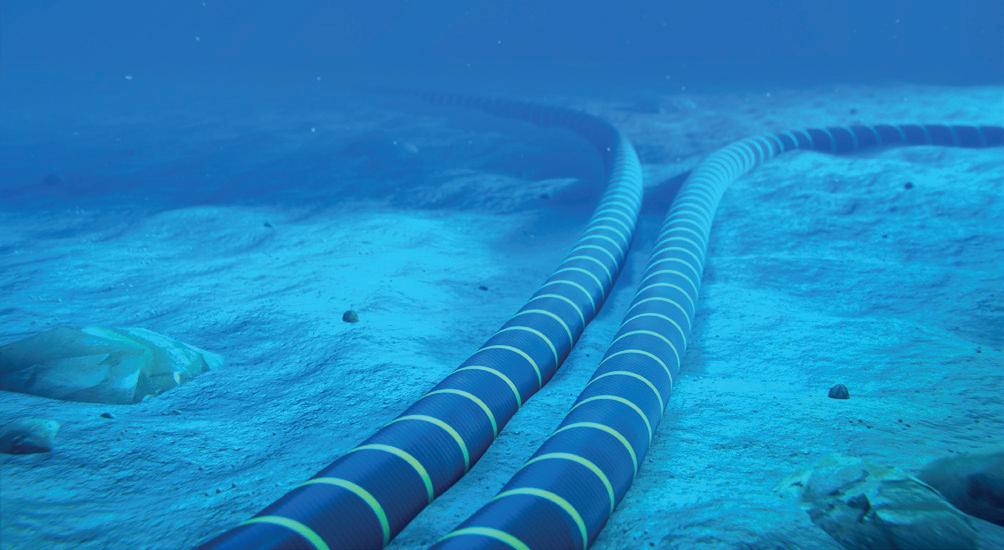
a warning as to what can happen if adequate attention is not given. Projects want to procure cables and they must secure manufacturing timelines, so a lot of work is initiated without going through all the necessary steps. For example, cross-sectional cable designs are selected with very little insight into the specific site conditions, the actual cable route, or the interfaces to the foundation or other third parties.
After the fact, everyone then has to play catch-up to fill in the gaps, and this is where difficulties arise. When it comes to site specific applications for the cable protection systems (CPS), which shield the unburied portion of the cable where it enters the turbine and is exposed to currents and waves, companies often find failure. There is a disconnect between cable original equipment manufacturers (OEMs), installation contractors, CPS suppliers, and the actual projects. They are all working on their own respective areas, but nobody is looking at the full picture and how it all fits together.
Based on DNV’s experience of certifying subsea cables in these markets, it has found that many of the publicly known subsea cable failures in recent years are the result of poor interface design management together with insufficient design for the actual site conditions.
Fortunately for floating wind – where the transition from the seabed to the floater will be significant, reaching hundreds of metres in some cases – this issue is already at the forefront of people’s minds. This might mean stakeholders are pushed to engage earlier and are more aligned on cable integrity, but, with so many interested parties, it is going to be a test.
To date, demonstration and commercial floating wind projects that DNV has been involved in, this challenge has been thrown into sharp focus and companies are having to go above and beyond to prove the safety of their cables. This has typically meant much more rigorous and lengthy design efforts, but it has also required more onerous type and prequalification testing, as well as more onerous O&M strategies.
Regulators and insurers
Markets like the US, Taiwan, and Poland now require third-party certification of their subsea power cables, including CPS solutions. There is growing recognition amongst regulators that the industry has not been documenting this sufficiently, given the recent spate of public failures. Furthermore, these failures are starting to influence existing markets in that regulators are requesting more information regarding subsea cables. Overall, this is a trend which may result in other jurisdictions focusing further on subsea cables.
It is not only the regulators that floating wind developers must convince though. On a regular basis insurance companies are starting to realise just how costly cable failures are and are in turn refusing to grant policies or excluding cables from their cover. New projects are now looking to marine warranty surveyors or third-party certification bodies to verify their assets in the hopes of getting them covered by policies again. It is too big a risk for wind farms to advance without this cover.
Figure 2 . Dynamic cables.
Figure 3 Submarine power cables.
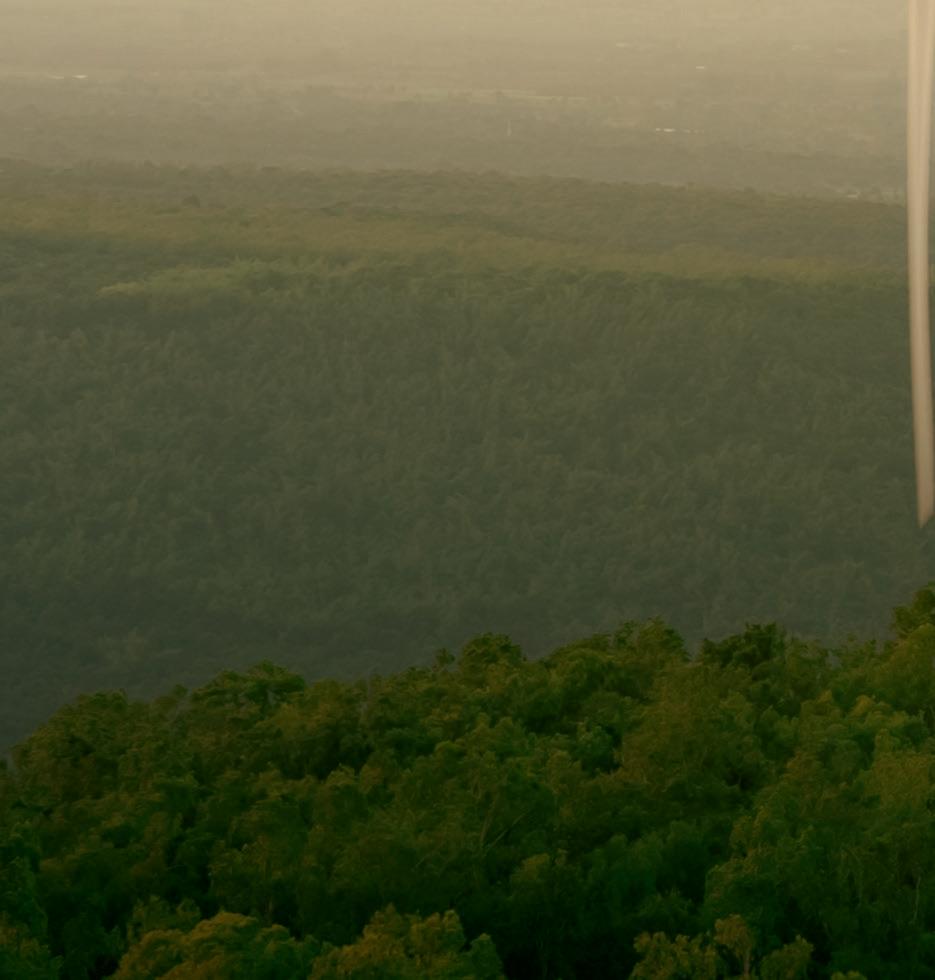
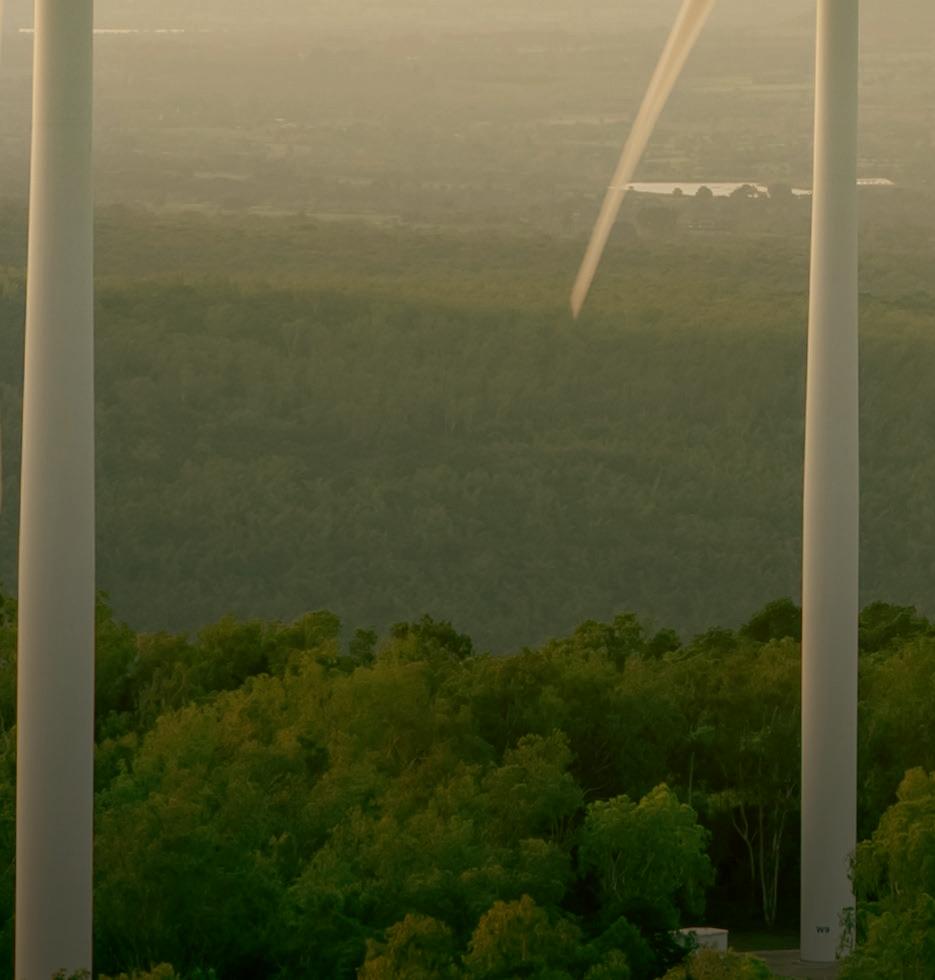
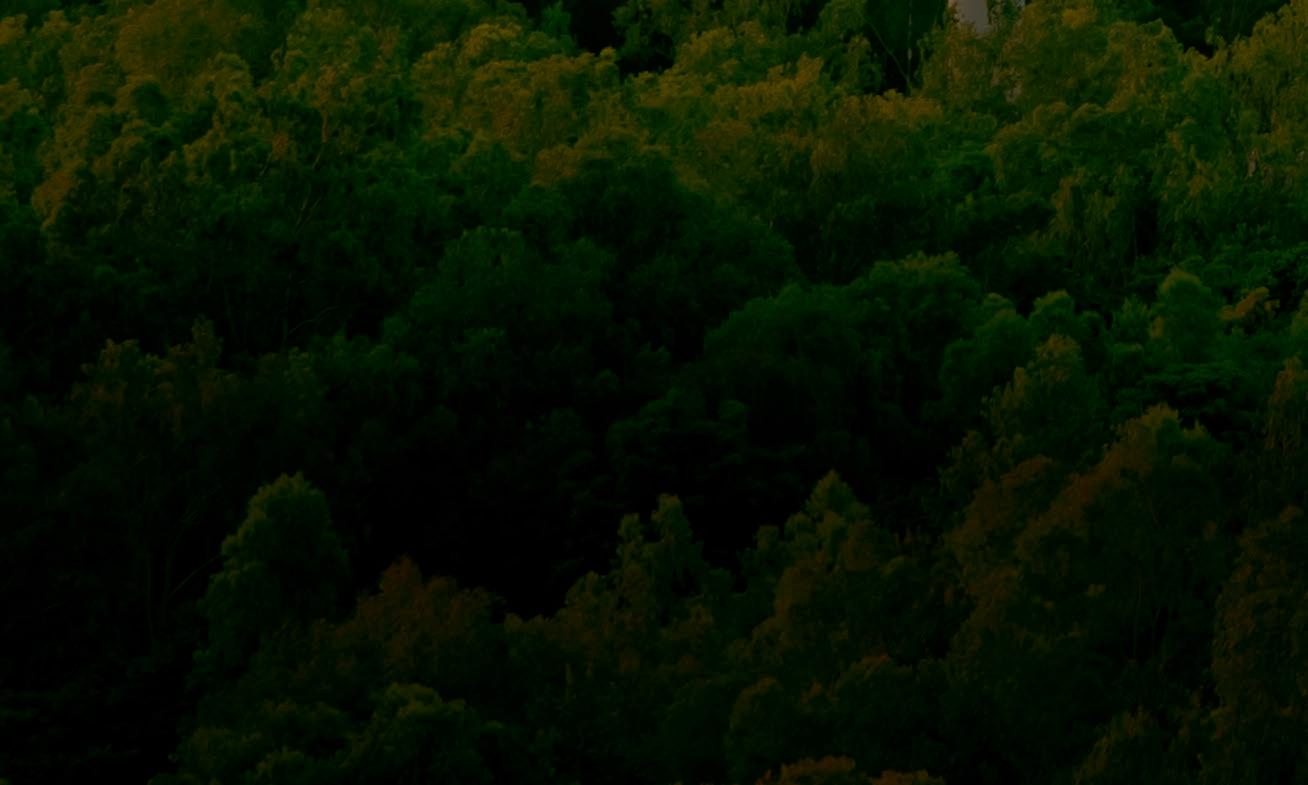
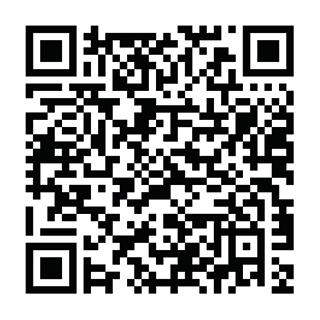
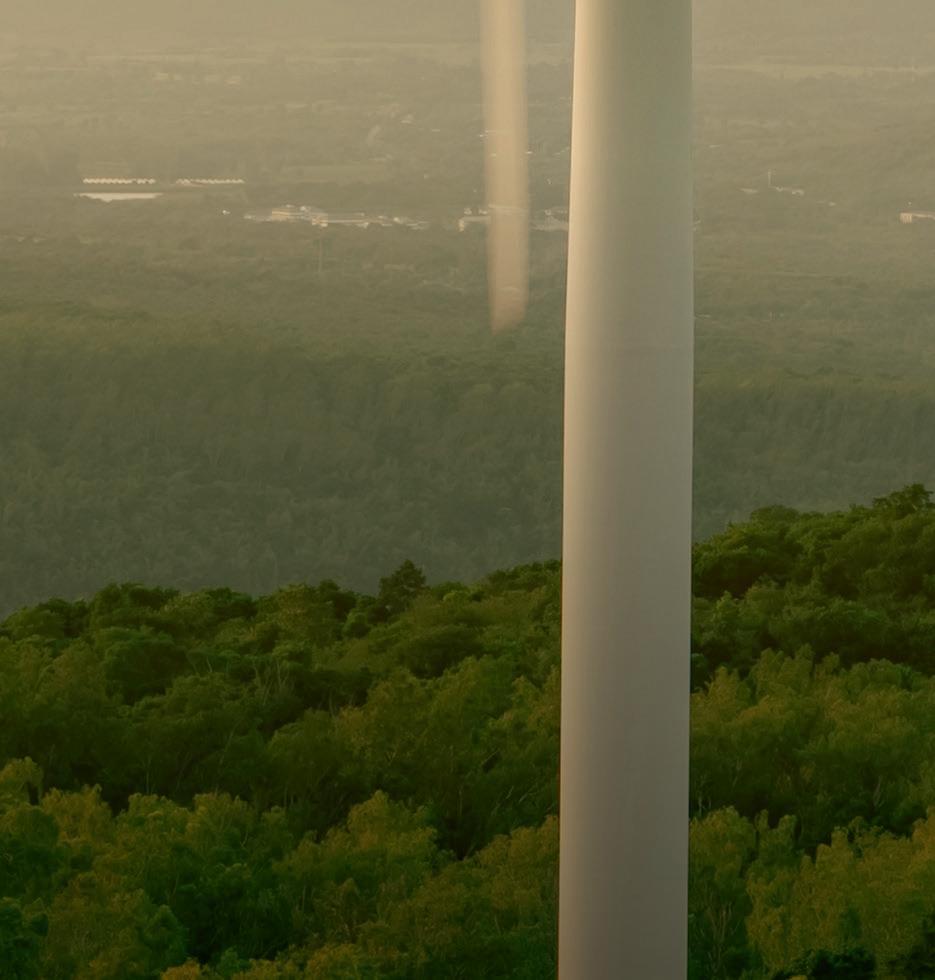
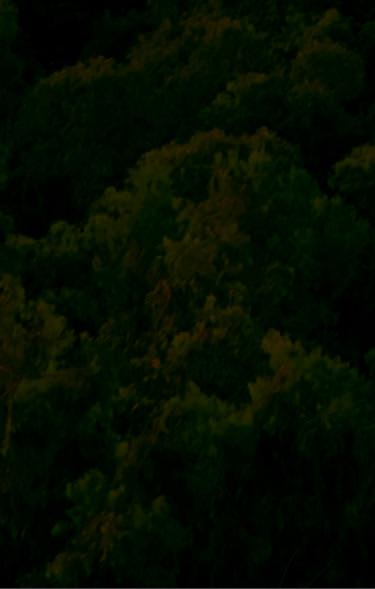
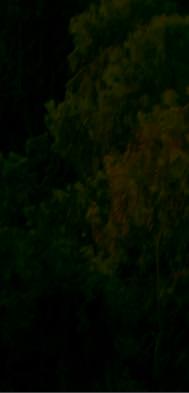
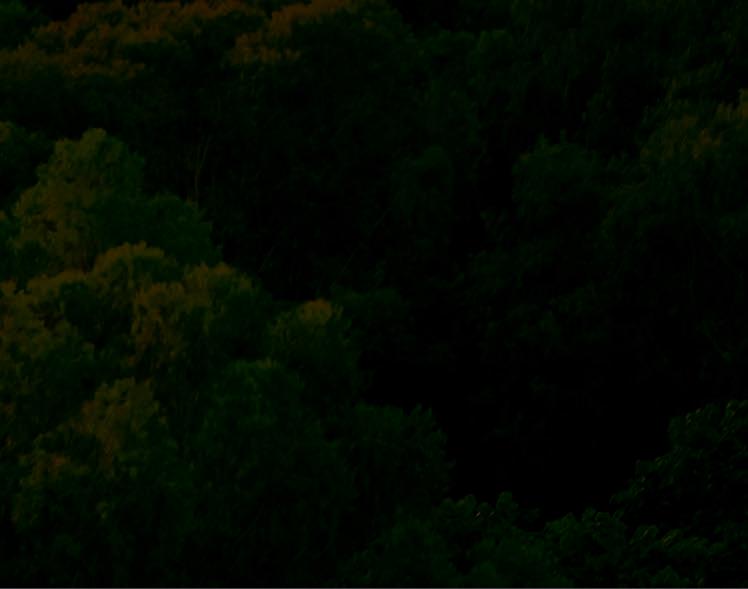
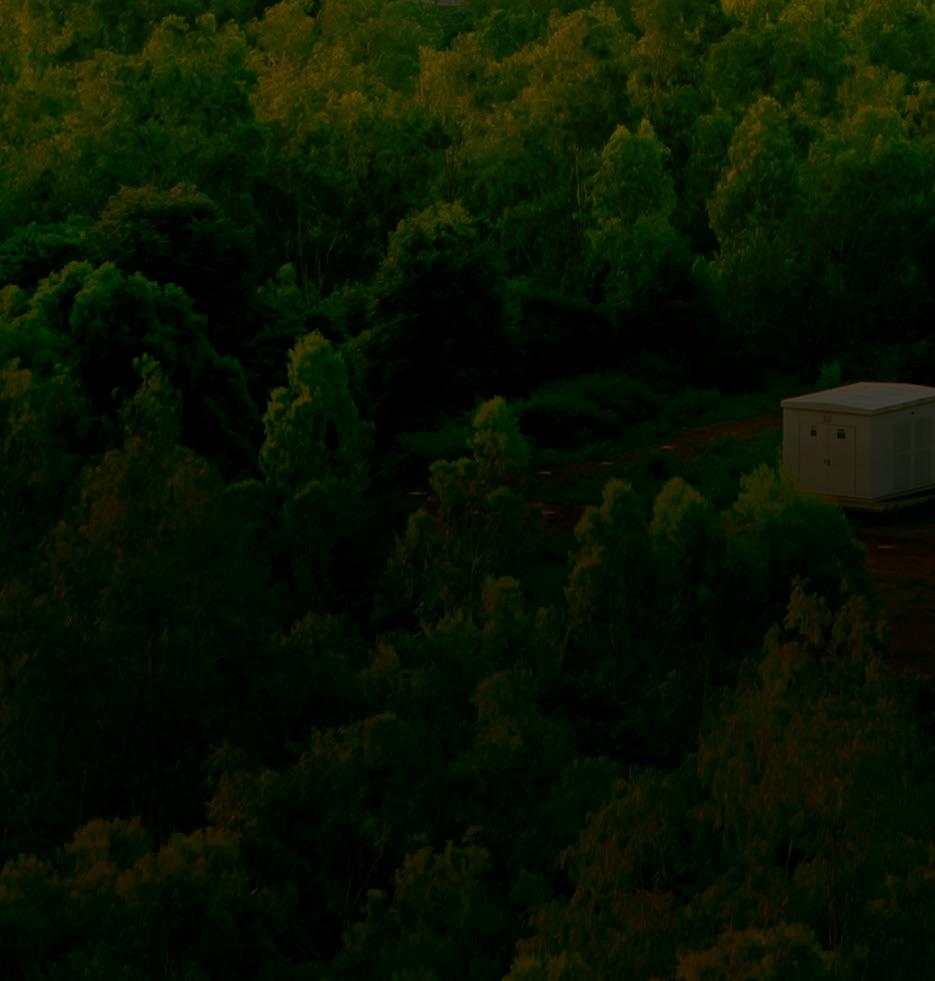
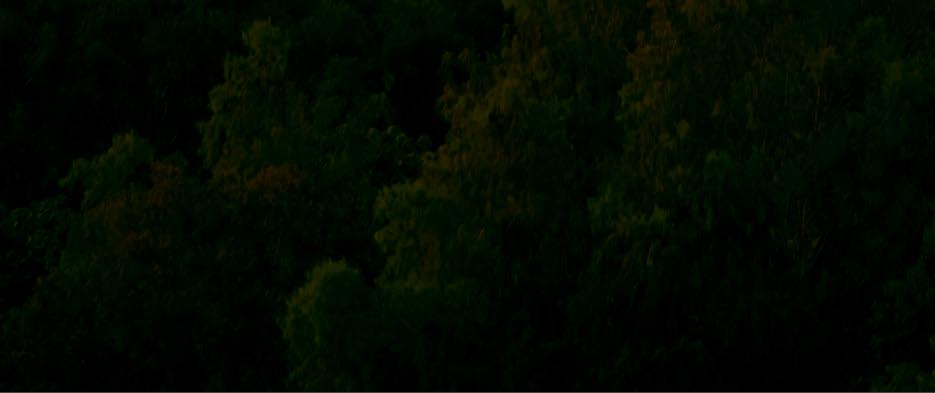
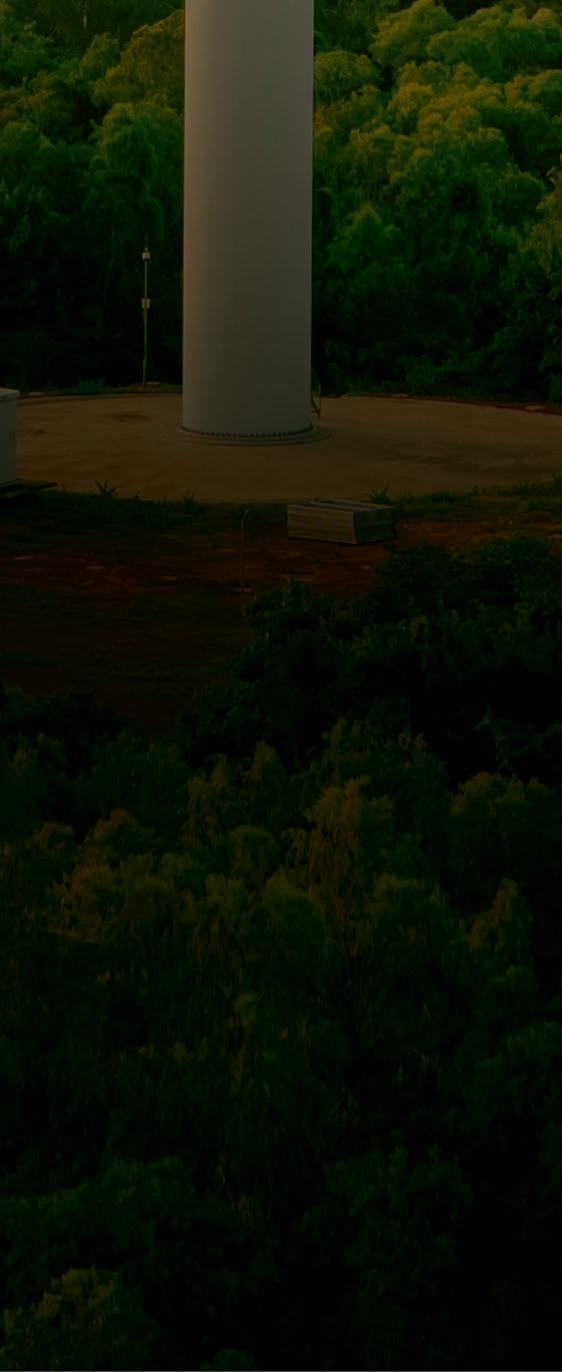
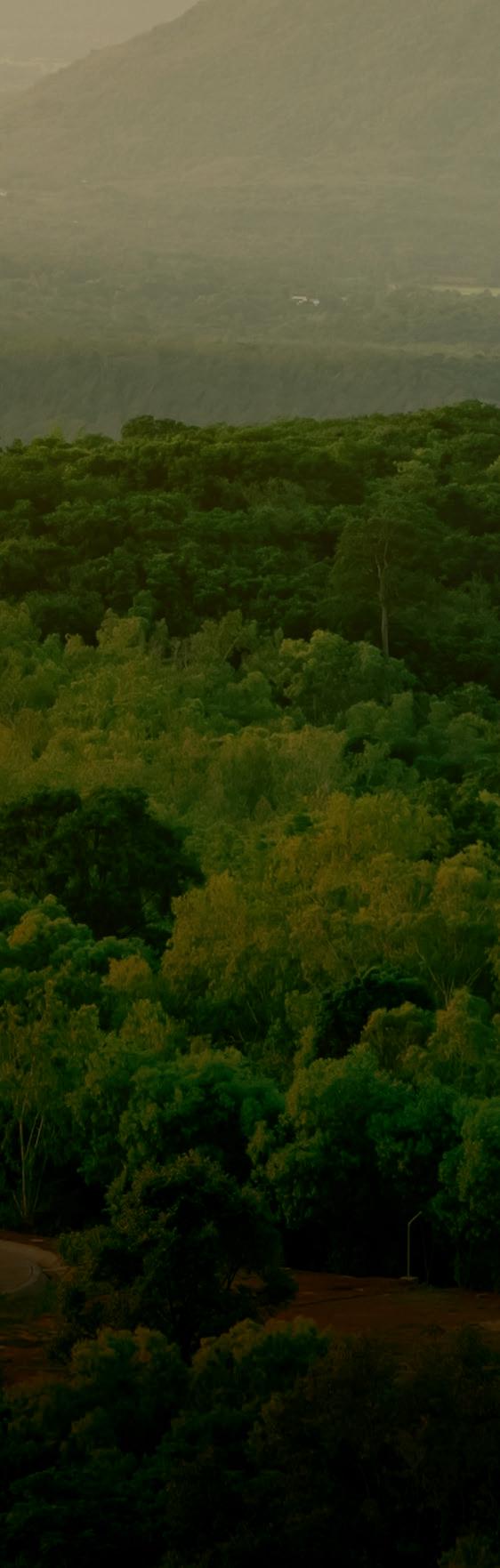
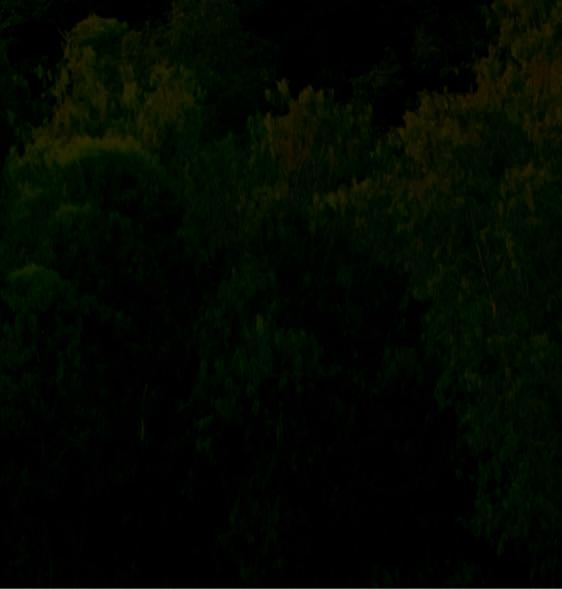
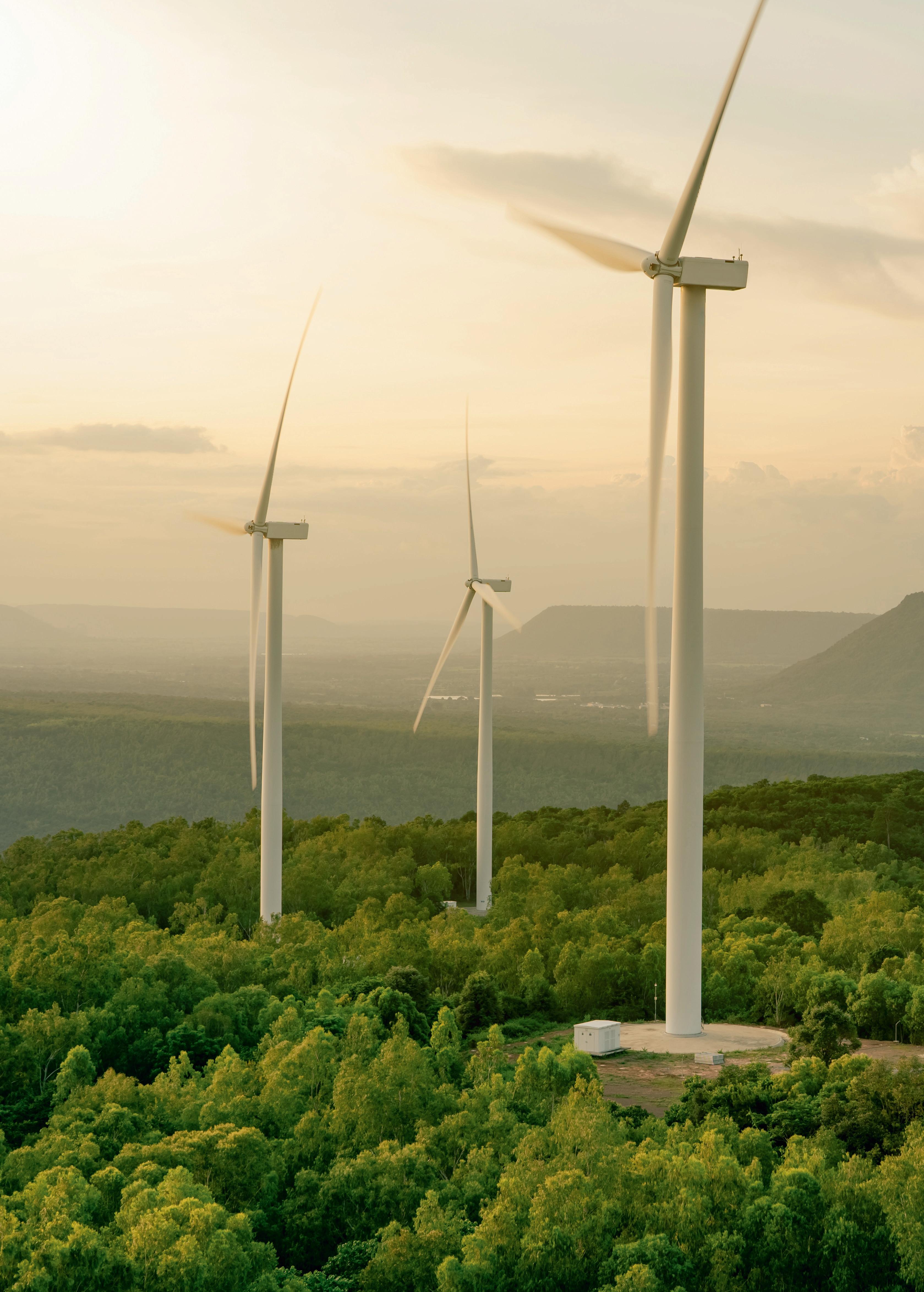
In 2023, it was reported that insurance providers had doubled the price of covering offshore wind projects after a number of years of incurring heavy losses. While this was not entirely due to subsea power cable failures, they still play a significant role in this new reality.
Even developments that have been operational for a number of years are being impacted by this problem; when it comes to policy renewal, they are all of a sudden finding that their project cables are not covered. Insurance brokers and providers have already highlighted the role that independent third-party proof can play in bringing down the cost of insurance and, in some cases, even unlock policies. It is this pressure, more so than regulatory changes, that will incentivise floating and fixed wind developers to put the issue of cables failures at the top of their agendas.
Breaking down the silos
As tends to be the case with problems facing emerging energy technologies, there is already the expertise in the sector required to fix them. Cable OEMs, installation contractors, CPS suppliers, and floating wind developers are packed with people that have the skills and knowhow to get a grip on cable failures.
A lot of good work is already ongoing in this regard, but it is often being done in isolation, from company to company. If the industry is to efficiently and effectively address this problem then it will require the establishment of best practices, and this is where third-party certification can add the most value.
Standards and certification will also help to bring more order and clarity to the subsea cable design process, setting a benchmark for the suitability of the products and technologies. Traditionally the industry standards have focused more on the electrical aspects of cables, as opposed to the full asset design, but there is an opportunity to complement existing standards with new measures. The importance of having a well-integrated standards landscape for turbines and floating foundations is there for all to see, but this way of thinking should be extended to cables. With little effort, it could make a big difference in the performance of subsea cables.
Given there is a large degree of crossover, there is also a chance for floating wind to help itself by borrowing from
oil and gas. Around 30 years ago, the breakthrough in the development of subsea risers, umbilical and flowlines that could stand up to the pressure and fatigue of ultra-deep-water environments helped oil majors to unlock previously inaccessible hydrocarbon reserves. This same tried and tested technology has already provided the bedrock for the development of cables for floating wind and can offer further insights as the sector grows. It is crucial that the wind sector has its own, bespoke standards, but these should be built on the shoulders of offshore oil and gas, and it would be counterproductive to ignore the knowledge gained, particularly regarding the need for qualification testing.
Furthermore, industry collaboration and knowledge sharing via joint industry projects (JIPs) provides significant opportunity in mitigating risks. DNV is currently undertaking two projects in which subsea power cables for offshore wind are included, Floating Wind Reliability JIP and Floating Offshore Wind Substations Phase 2 JIP. Lessons learned and experience from the industry must be collected, evaluated, and translated into requirements documented in globally accepted design standards.
A problem that needs solving now
Indeed, it is ignoring learnings from examples like CPS and flexible riser failures that will consign floating wind to an even more protracted path to maturity. Floating wind will remain an expensive endeavour for years to come and it cannot afford, financially or reputationally, to be plagued by cable failures.
For its part, the skills and ingenuity of the cable industry give cause for real optimism and with more time and space afforded, there is every reason to be hopeful that they can tackle the challenges of floating wind. This can be done by working together in partnership with third-party certification bodies like DNV to ensure quality and safety and provide a transition that delivers, for businesses, consumers, and the environment.
Floating wind should count itself fortunate; there are not many sectors that are able to monitor the mass rollout of a parallel technology, capture the successes, make note of the pitfalls, and feed this back into its own development. Fixed-bottom wind is an invaluable sighting shot that floating developers should make the most of.
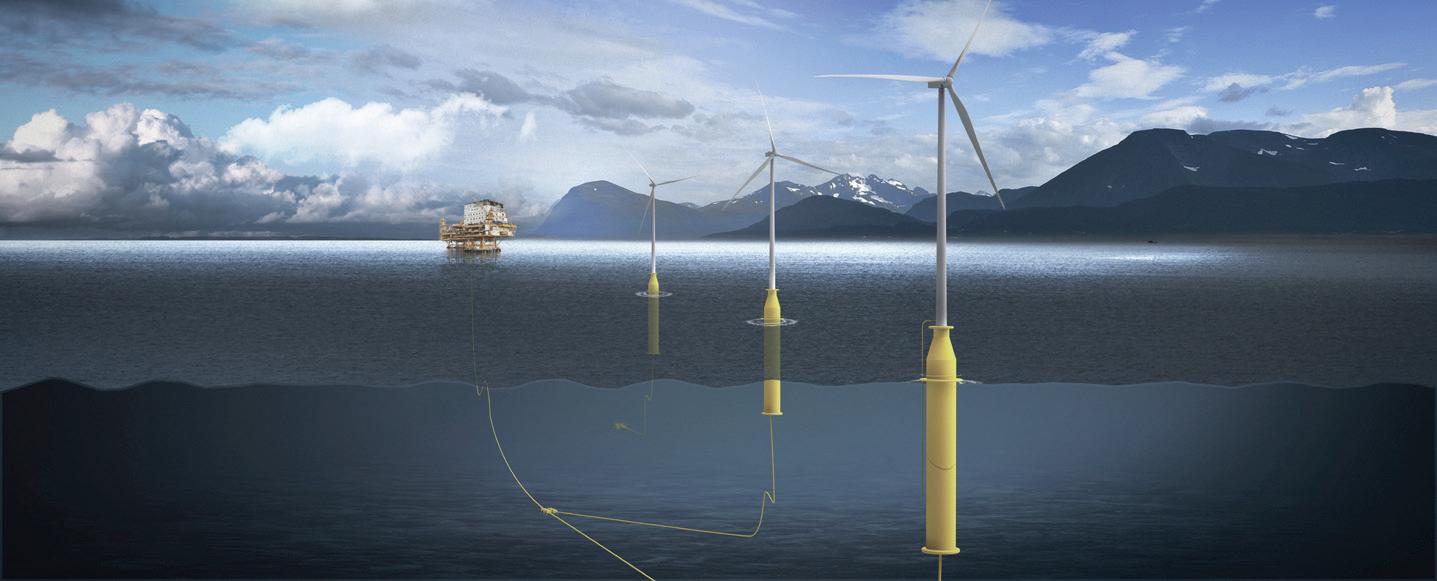
Cable failures are something that the offshore wind industry as a collective need to correct sooner, rather than later. For floating developers, the clock is ticking with many large scale projects aiming for start-up towards the end of the decade, but to be aware of many of the potholes now, rather than encountering them along the way, is a big bonus.
Reference
1. DAVIES, G., ‘Floating wind: Time to turn expertise into action in deeper waters,’ Ørsted, https://orsted. co.uk/insights/expert-take/floating-wind-expertiseinto-action
Figure 4 . A floating offshore wind cable setup.
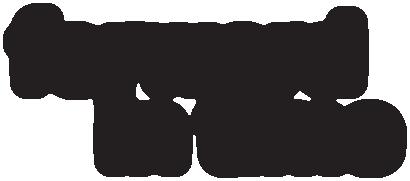
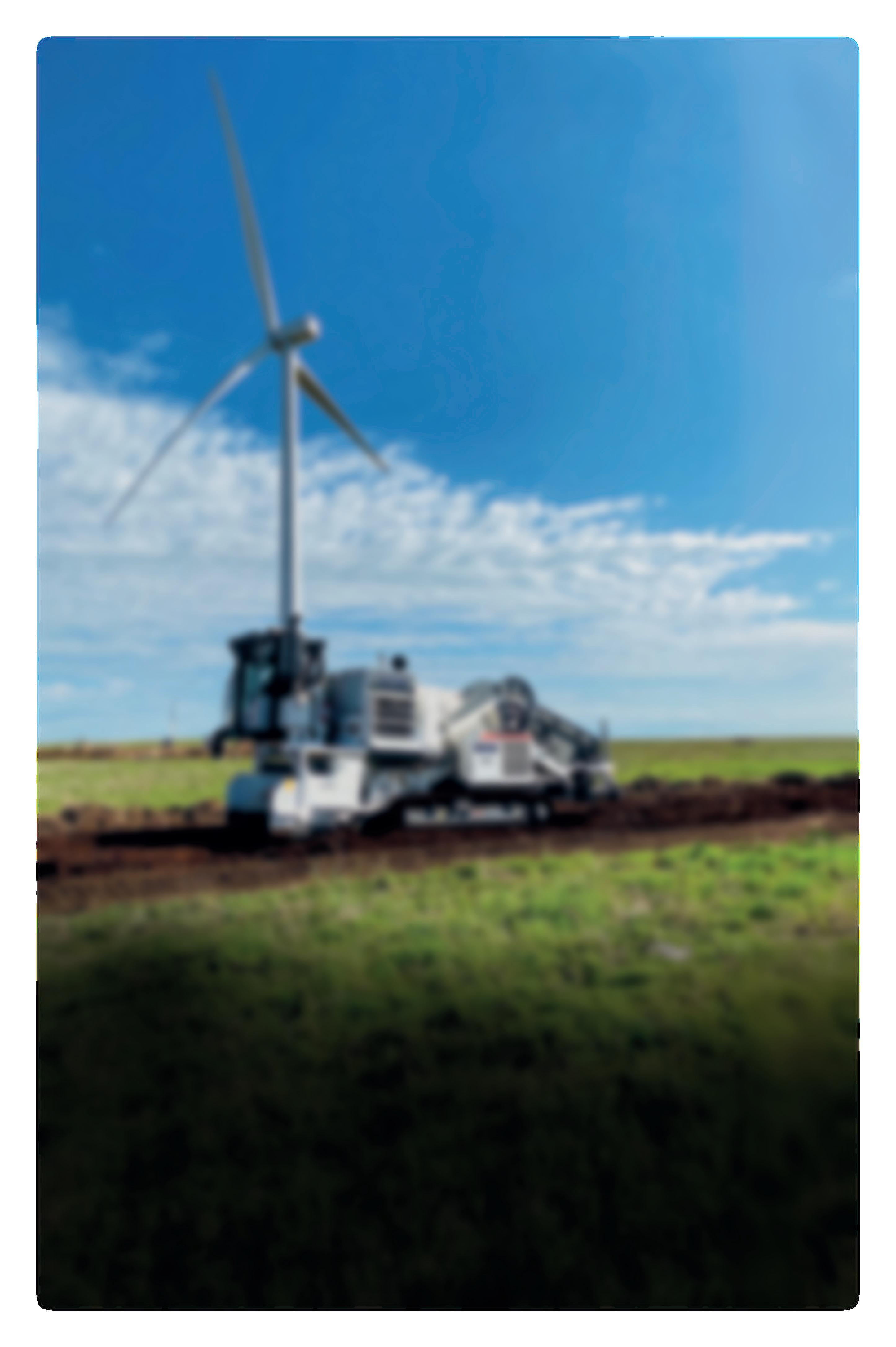
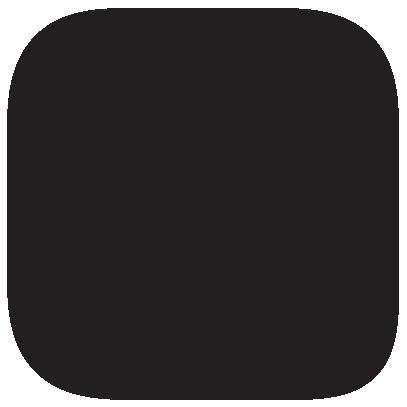
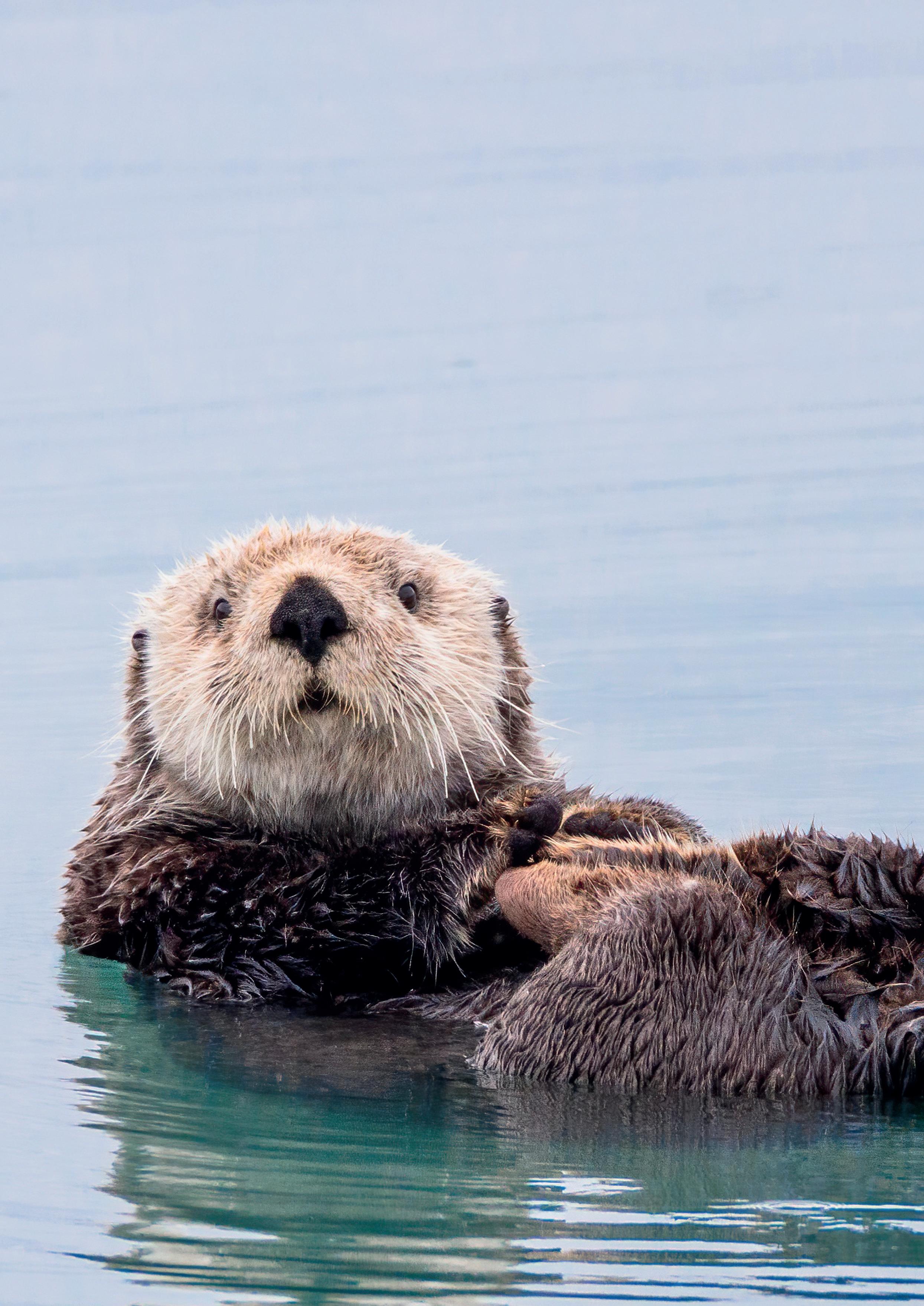
Enhancing offshore wind operations
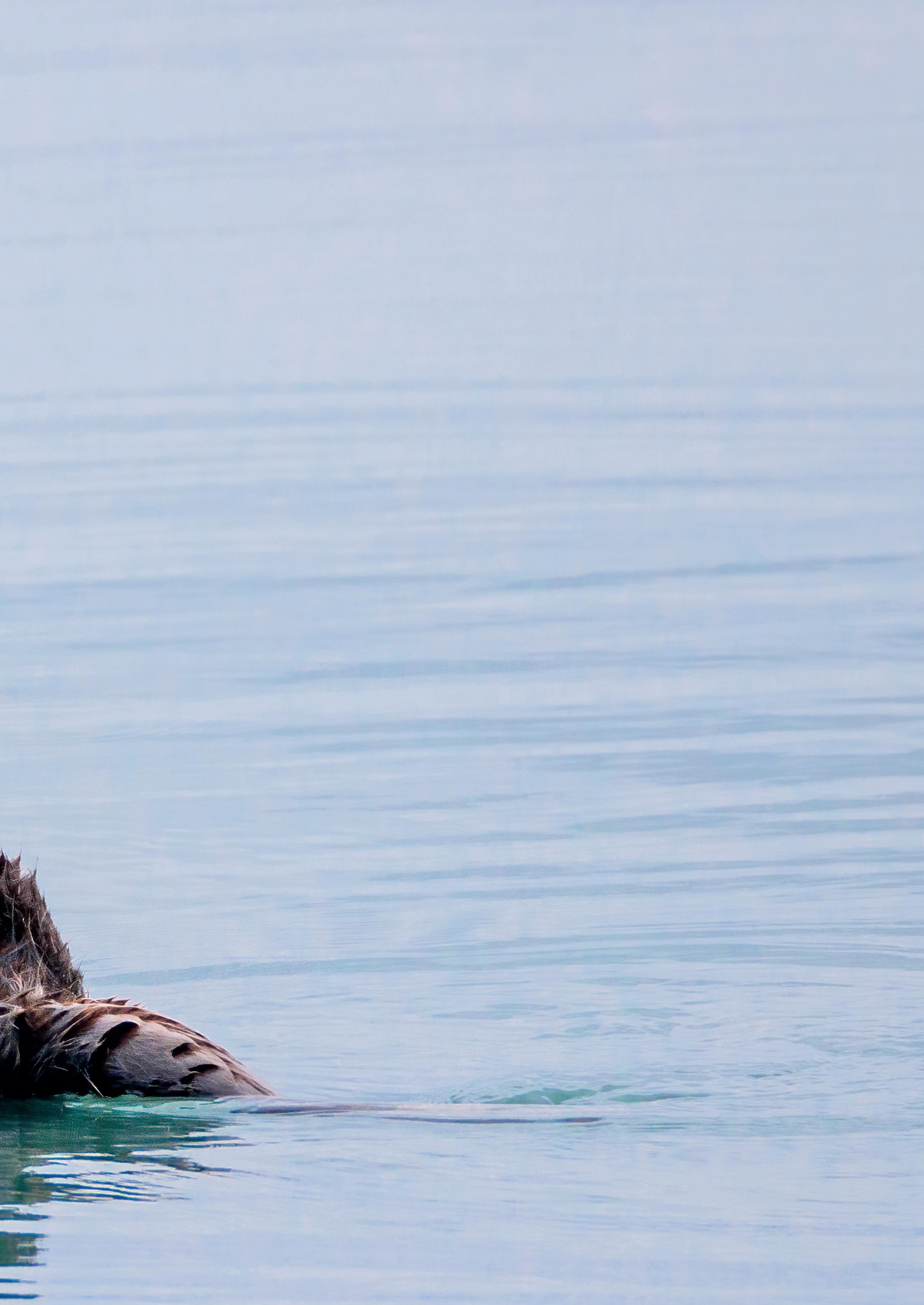
Jessica Stump and David Inman, NOV, explain how improvements in modular support vessel design can help to enhance offshore wind operations and maintenance.
Offshore wind’s rising role in the global energy mix enhances energy security, advances the energy transition, and reduces greenhouse gas (GHG) emissions. Recent economic challenges, such as inflation, higher interest rates, and supply chain constraints, have not deterred this resilient industry from technological advancement and innovation.
As wind farms move farther offshore and into deeper waters, the components become larger, more complex, and of greater scale, necessitating robust operations and maintenance (O&M) strategies. Moreover, O&M is one of the main contributors to the overall costs of any offshore wind farm, accounting for nearly 20% of the total investment required.
Support vessels must be able to operate safely, effectively, and longer in these rigorous environments to support the 20 – 25-year design life of the latest offshore wind farms. Strong winds, high waves, and turbulent seas can drastically affect the ability to conduct O&M activities safely, reliably, and efficiently. Current service operations vessel (SOV) operability is often limited to specific weather windows, leading to costly delays and downtime.
GustoMSC, part of NOV, has developed the Enhydra support vessel series to provide the next step in offshore wind operations. Just as the sea otter (Enhydra Lutris) uses its streamlined body to perform efficient deep dives to the seafloor and adapts its lung capacity to float on the surface, the Enhydra vessel series utilises its extensive deck to facilitate and execute various operations.
The Enhydra modular service and operations vessel (MSOV), the first variant in the series, unlocks capabilities beyond the traditional SOV while serving the entire lifecycle of an offshore wind farm. The concept allows for multiple
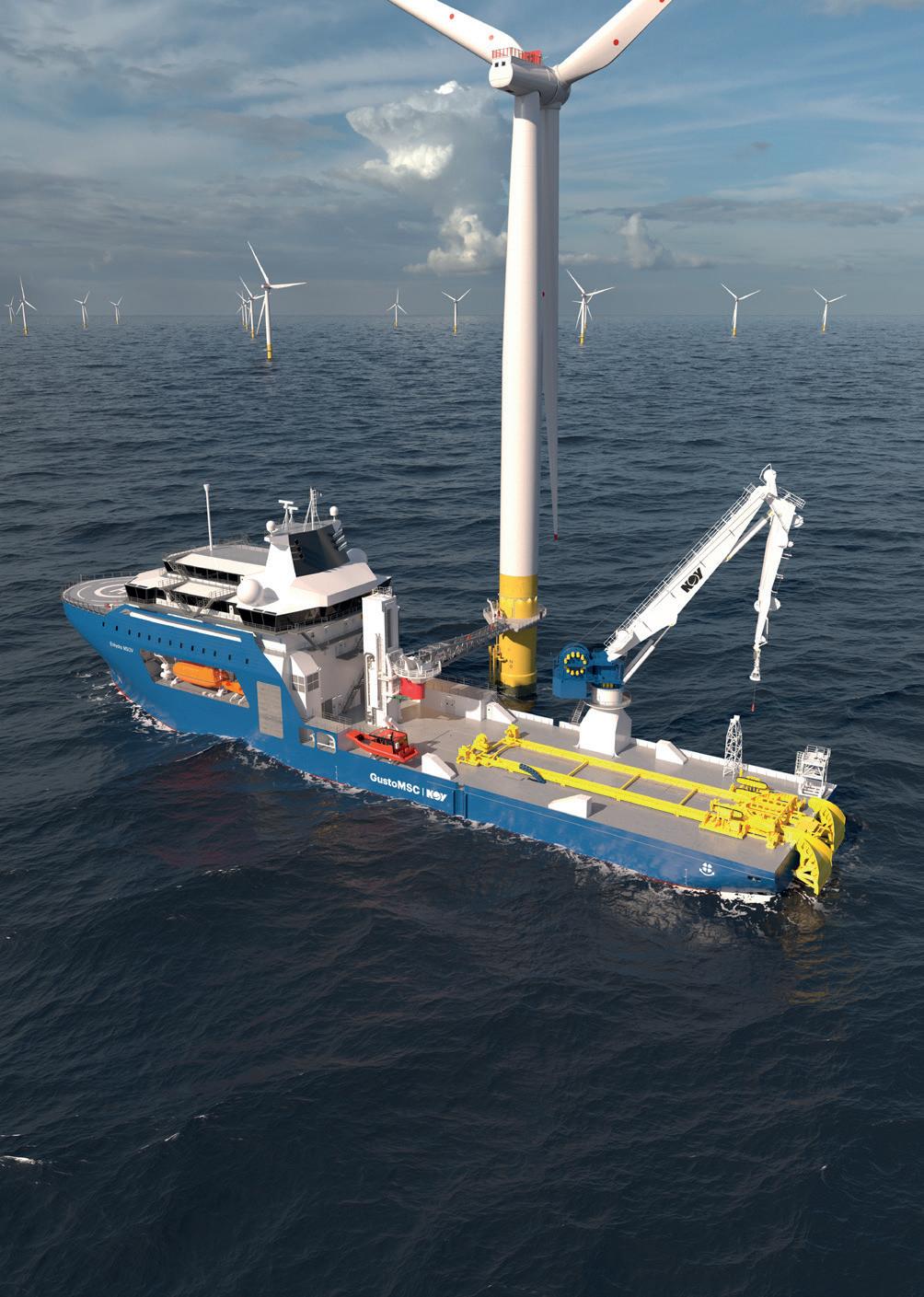
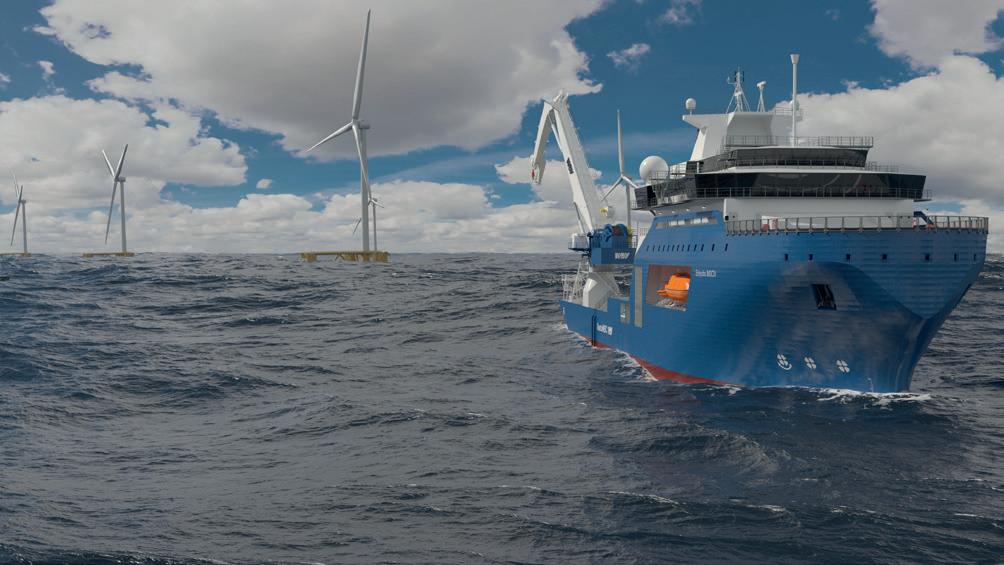
vessel configurations into one design, integrating several NOV technologies. From cable repair and replacement, to subsea inspection and intervention and mooring installation for floating wind projects, this versatility enables developers and service companies to optimise their operational uptime and maximise power generation.
New vessel class
A good vessel design demands an understanding of how it will be used, what equipment it will host, and what operations it will perform. With more than 100 years of experience in designing and engineering mobile offshore units and equipment, GustoMSC understands the importance of the vessel design philosophy.
GustoMSC went back to the drawing board and conducted a detailed study of the current and future operational challenges. Following discussions with industry experts, several O&M-related activities were identified and refined into numerous key work packages, allowing for the development of a vessel design specification.
For additional capabilities, a vessel design requires sufficient size and space, positioning capability, endurance, and personnel capacity. The MSOV concept combines a larger vessel design, modular equipment spreads, and increased comfort, enhancing workability and reliability.
This design provides a more stable platform from which to work. The MSOV has been designed to operate in sea states of up to 4 m (13 ft), opening the operational window for both time and work scope. The vessel design also increases endurance, making it possible for the Enhydra MSOV to stay in the field longer. This major advantage de-risks operations, along with reducing fuel consumption and GHG emissions.
The MSOV will also include standard SOV equipment, such as boat landings, a daughter craft, a motioncompensated gangway, and under-deck storage for spare parts. It will also carry work-class remotely operated vehicles (ROV), drones, autonomous underwater vehicles (AUV), a helideck, and more.
Cable repair
As installed offshore wind power capacity increases, so will the transmission infrastructure. The risk and cost of interarray and export cable damage caused by environmental and human interaction will increase substantially.
Cable repair and replacement operations are time-consuming and expensive endeavours. They require access to specialised equipment and vessel types that will become increasingly scarce. Cable-lay vessels are chartered on long-term projects with substantial backlogs. Meanwhile, there is a shortage of subsea inspection, maintenance, and repair vessels as many are returning to their target oil and gas markets. Limited access to these assets has resulted in up to six-month-long delays in restoring power in some cases.
Connectivity is vital, as the economic viability of these complex and expensive projects requires efficient and effective power generation. Maintaining continuous power flow and managing unplanned events is crucial. The ability to
Figure 1 . With its open deck layout, the Enhydra MSOV facilitates various operations and integrates multiple NOV solutions to optimise operational performance.
Figure 2 A larger vessel design provides a more stable platform, maximising workability and endurance.
Sulzer MellapakEvo™ Packed for Evolution!
The new Sulzer MellapakEvo™ structured packing, in combination with advanced MellaTech™ column internals, delivers unparalleled performance improvement for your columns. Verified at an independent testing facility, this latest mass transfer technology is proven to enhance column performance in both capacity and efficiency.
MellapakEvo has optimized packing geometry as well as an increased effective interfacial area for enhanced liquid spreading and liquid surface renewal. This boosts the vapor-liquid interactions for a superior mass transfer and excellent hydraulic performance.
This innovative design delivers up to 40% better efficiency compared to MellapakPlus 252.Y at a similar capacity. It also offers up to 20% greater capacity than MellapakPlus 452.Y at a similar efficiency, minimizing energy consumption for operators.
Contact Sulzer for a full technical analysis tailored to your needs: chemtech@sulzer.com
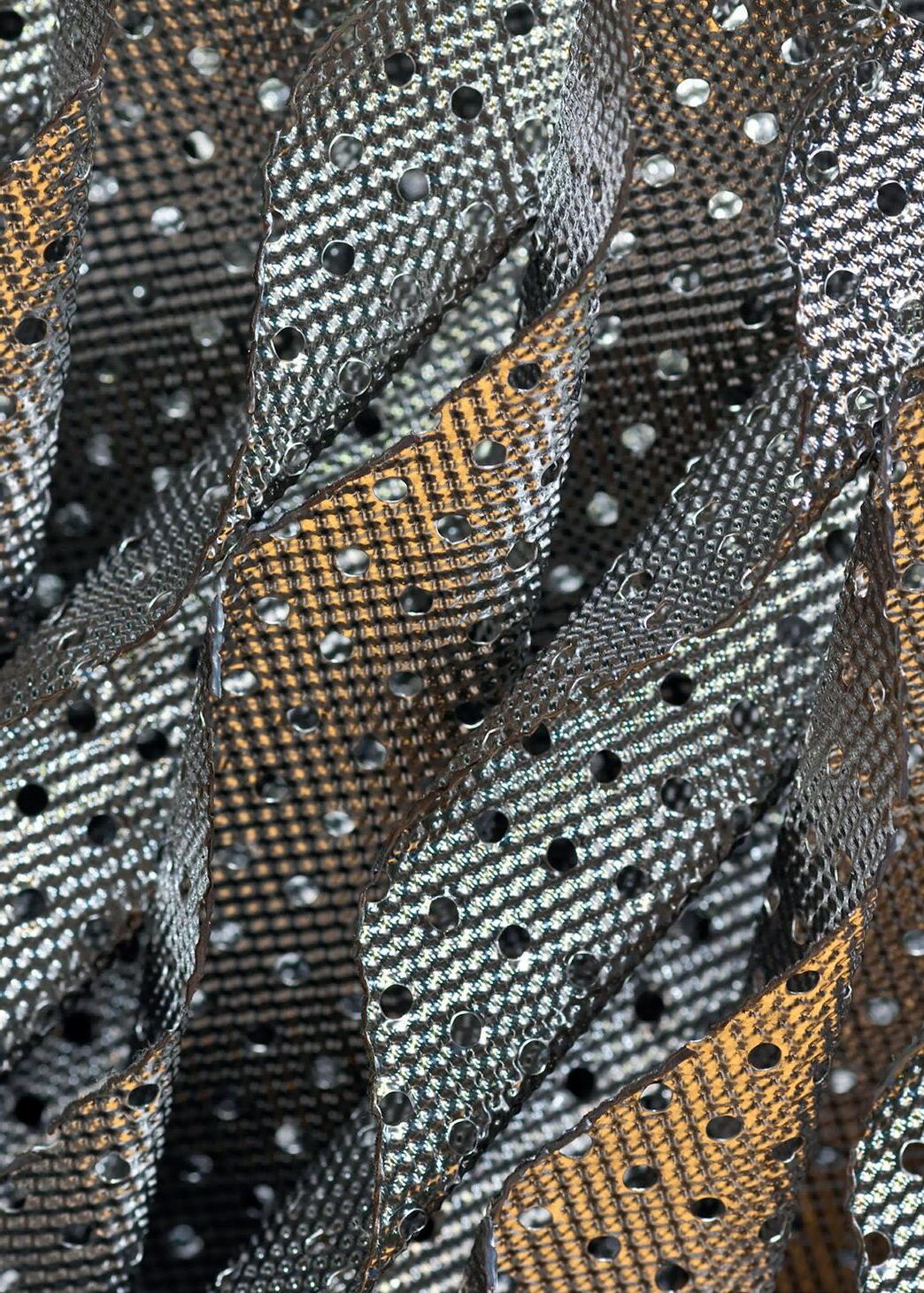
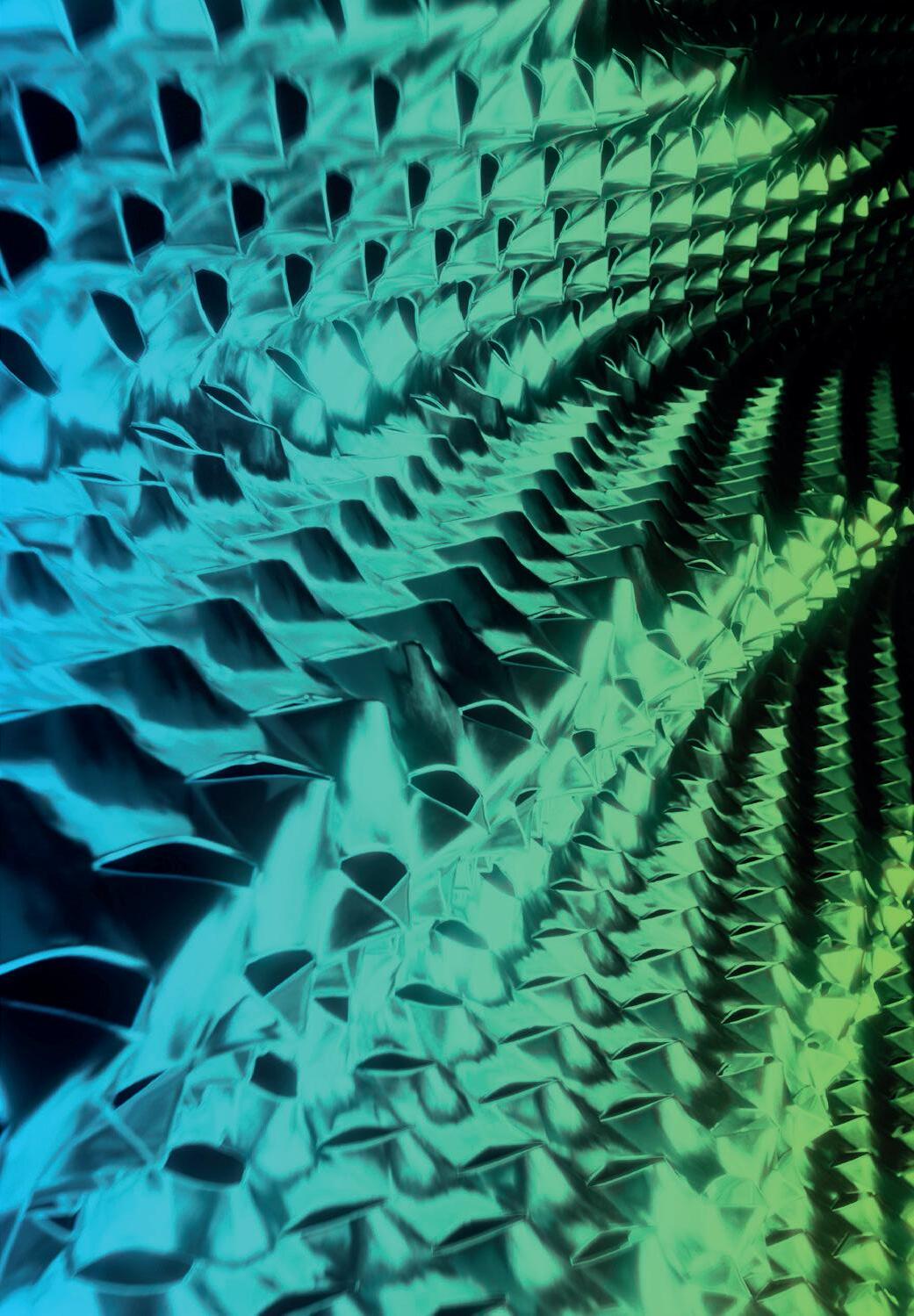
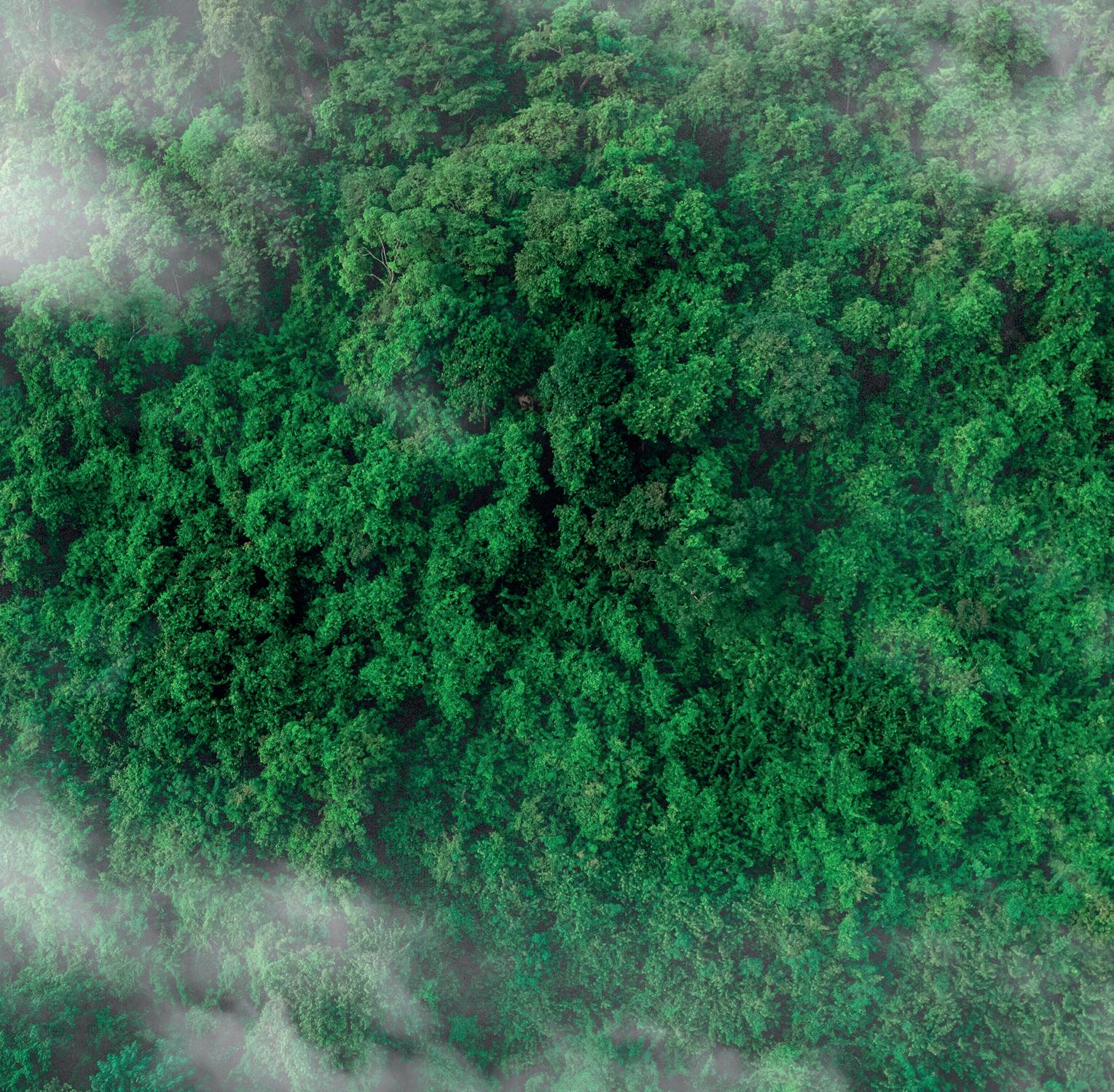
quickly mobilise a repair spread with available assets will help minimise this risk.
The MSOV’s cable-lay and repair spread includes the permanently installed underdeck carousel, the quadrant system, and the necessary winches and tensioners, all from NOV’s Remacut group. This equipment package is modular yet fully integrated into the design for efficient deck and equipment layouts, power supply and regenerations, and controls.
Floating wind
Several demonstrations and small scale floating wind farms are operating, with commercial scale projects anticipated by the end of the decade. Unlocking this vast potential of wind energy in deeper waters requires a holistic approach. One of the major challenges for full scale floating wind farms will be the installation and maintenance phases.
All the components of a floating wind farm are new, large, and complex, and vessels equipped to handle their transport, installation, and maintenance are limited. Mooring line installation for anchor or suction pile tethering and dynamic cable deployment will be new challenges for offshore wind, especially at this scale.
Fixed-bottom offshore wind farms typically rely on monopile or jacket foundations, but floating wind requires platforms to be anchored in deeper waters where seabed and environmental conditions vary. Anchoring floating platforms requires robust mooring systems, as the winds, waves, and currents are more intense and unpredictable. They must also withstand extreme weather events, which can exert tremendous loads on the mooring lines. Additionally, the constant motion of the floating platforms necessitates the use of durable and flexible dynamic cables. These cables must endure continuous mechanical stresses, as well as potential wear and fatigue from constant motion. Installing and maintaining this infrastructure in harsh and challenging environments requires a new class of vessel(s).
Future fuel and energy efficiency measures
Stricter environmental regulations and ambitious GHG emissions-reduction targets have led the offshore energy sector to develop and implement measures that enhance energy efficiency and lower emissions. For instance, vessel owners and designers, including GustoMSC, are exploring the use of alternative fuels, such as methanol, ammonia, and hydrogen, to replace marine gas oil (MGO).¹ All options have advantages and disadvantages; some are more technically challenging, less power-dense, or less economical.
Methanol was chosen for the MSOV because it is available, compatible with little to no modification to the engine or containment setup, and minimises environmental impact, reducing sulfur oxide and nitrogen oxide emissions.
Additional energy-efficient/emission-reduction technologies in the MSOV vessel design can include elements such as the PowerBlade TM , a battery storage and regenerative system that reduces the number of generators online, lowering fuel consumption and maintenance. Depending on the configuration, the system can power operational equipment that is quickly becoming electrified, such as the fully-electric subsea crane from NOV’s Lifting and Handling group. While hydraulic technology remains in use for luffing cylinders, an advanced electric motor system improves control and precision. This approach enhances operational smoothness, reduces downtime, and ensures the crane’s reliability.
Conclusion
Offshore wind operations are inherently dynamic and complex, requiring flexibility and robust strategies to enhance safety, maximise power generation, and minimise environmental impact. A one-size-fits-all vessel approach cannot account for the numerous variables and challenges encountered in these ever-increasingly rigorous environments. As technology advances and turbine design evolves, offshore support vessels must also adapt.
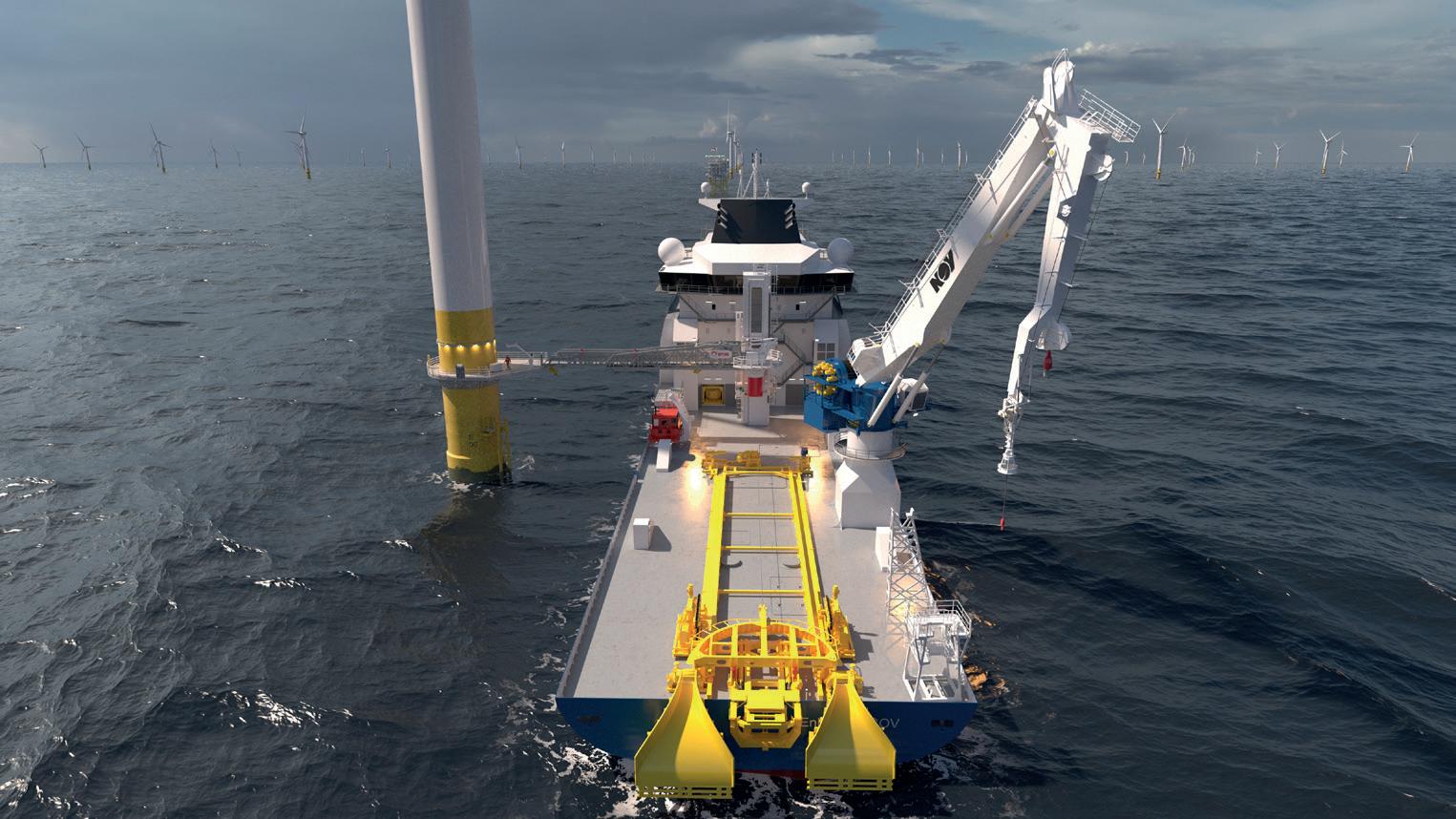
Recognising these challenges, GustoMSC is dedicated to supporting the expansion of the offshore wind industry and advancing the energy transition. By designing and engineering integrated vessel designs tailored to future industry demands, offshore wind farm developers can efficiently maintain their projects to achieve reliable long-term performance and profitability.
Reference
1. ‘Pathway and case study alternative fuels for wind installation vessels,’ GustoMSC, (2024).
Figure 3 . The Enhydra MSOV’s versatility enables offshore wind developers and service companies to boost operational uptime and power generation.
1.200+
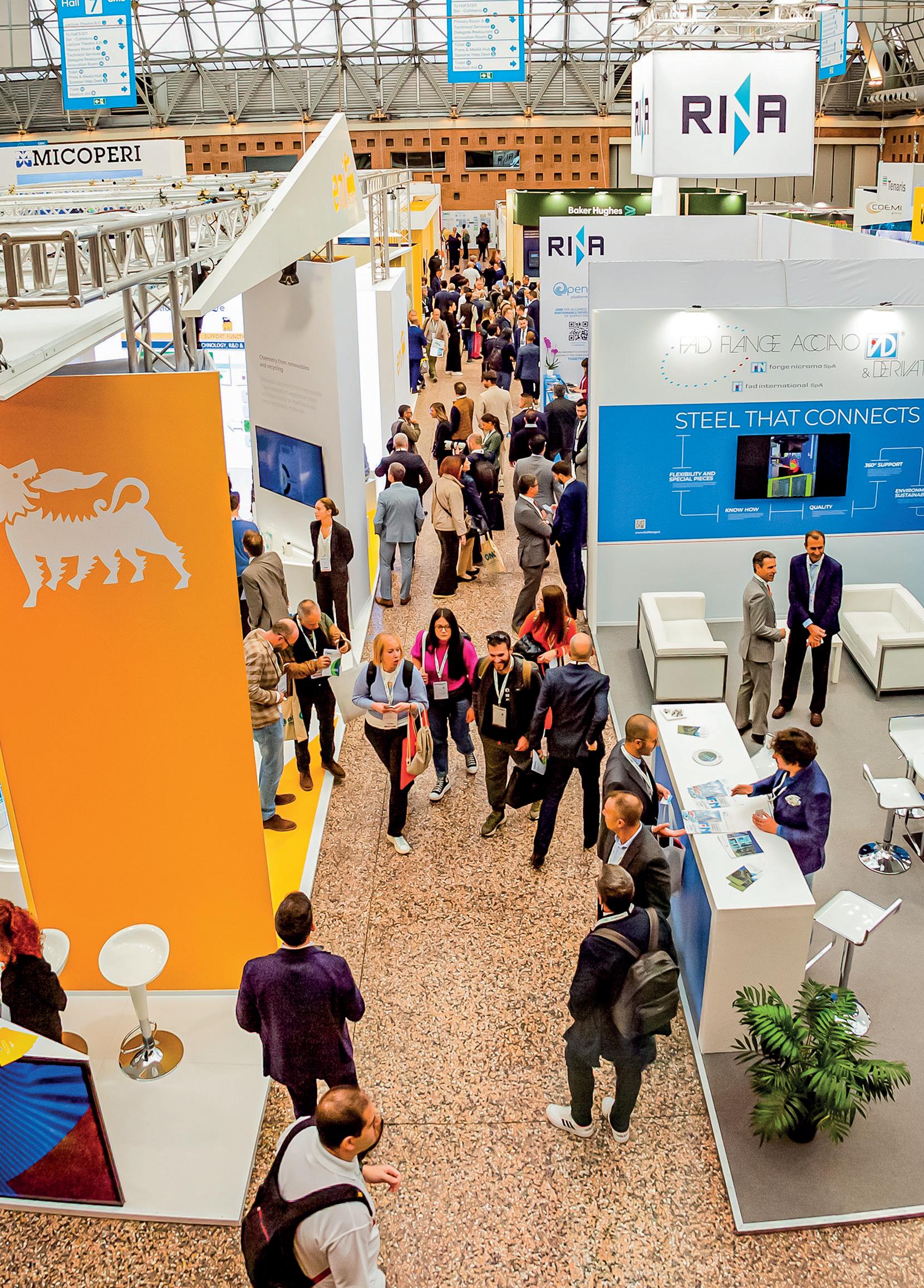
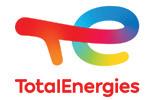
Xiaobing Hu, Head of Applied Solutions, Manufacturing Intelligence division, Hexagon, considers why digitalisation is crucial in the acceleration of design, development, and operation of larger wind turbines to meet United Nation’s Sustainable Development Goals.
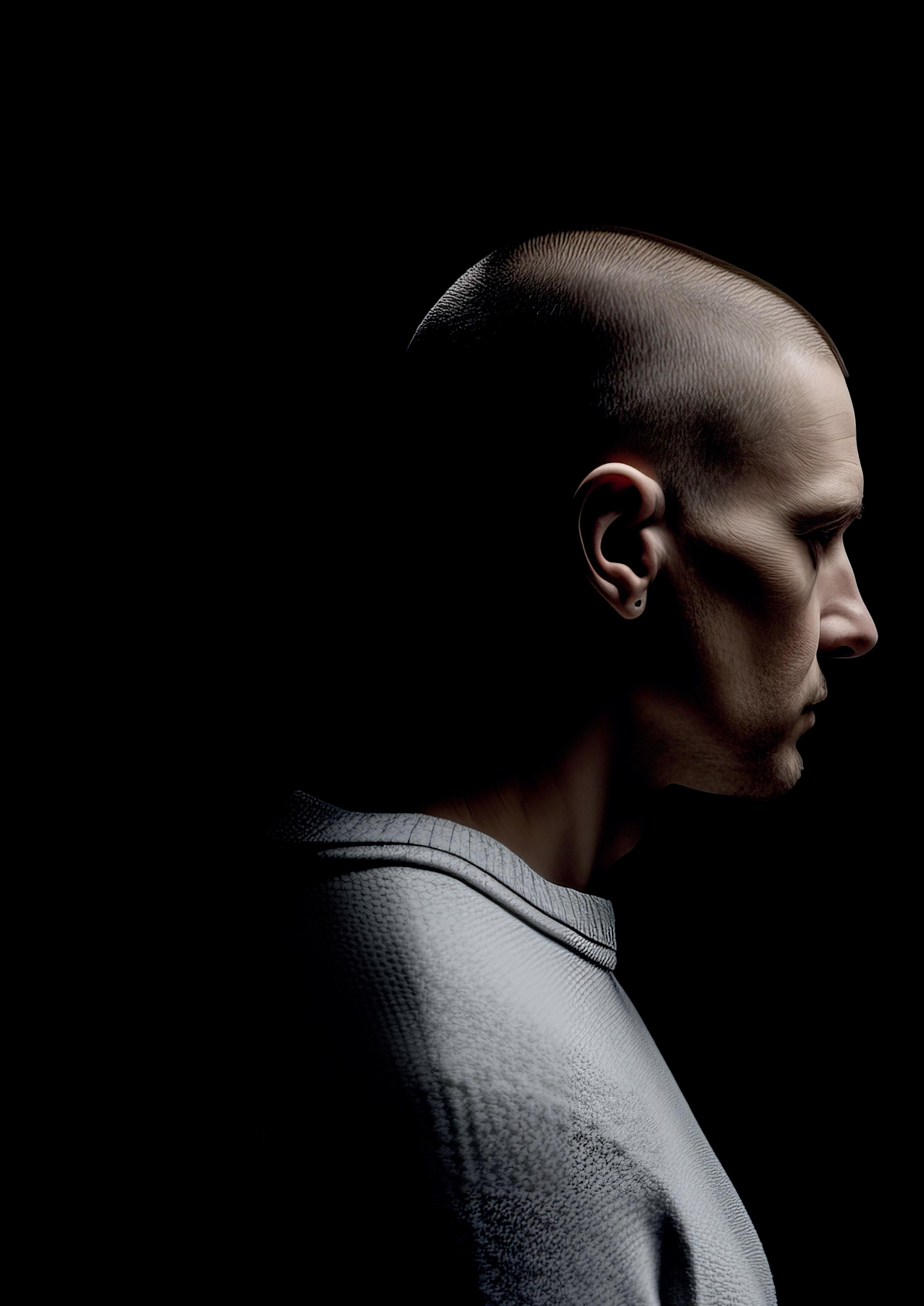
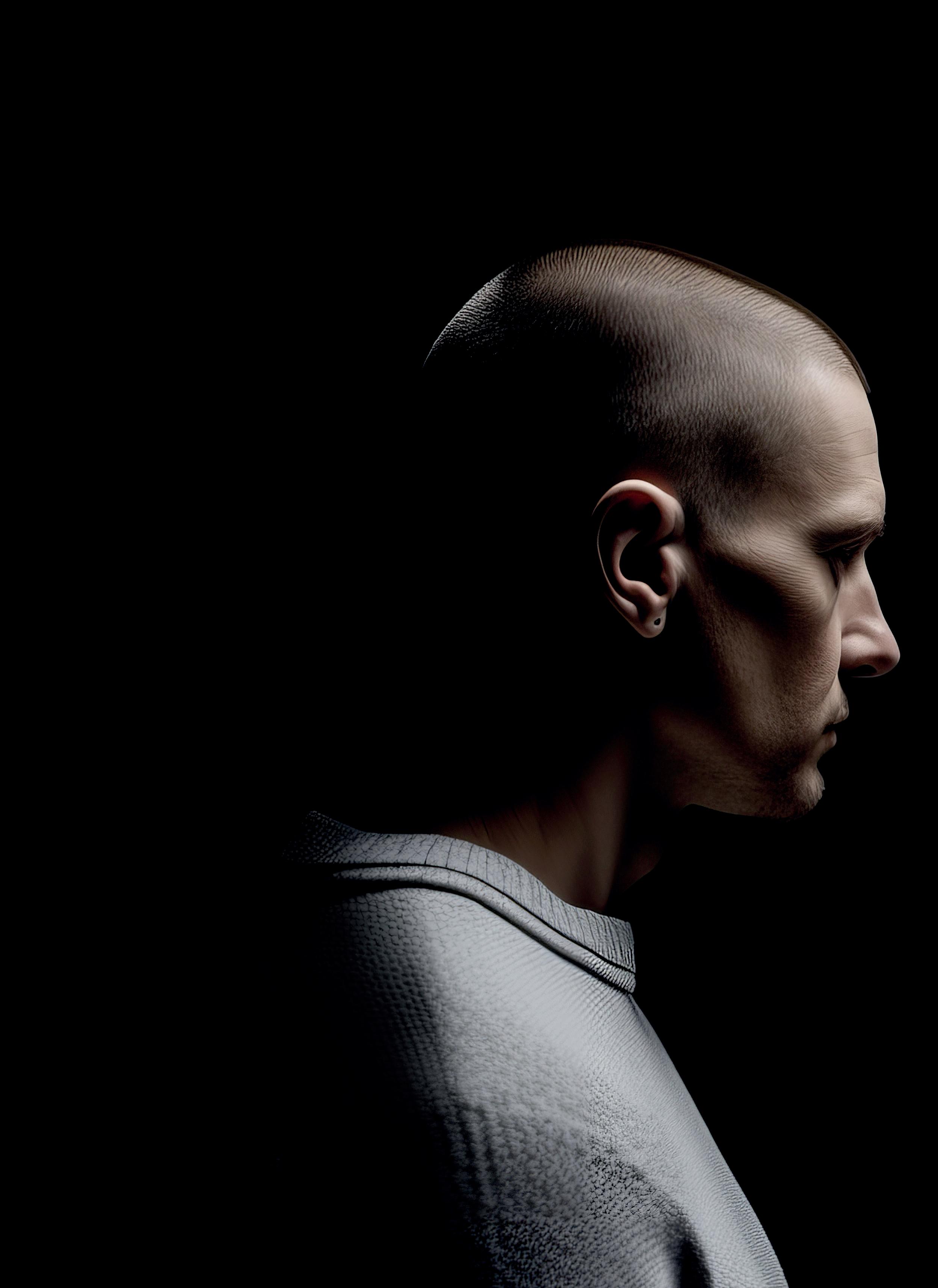
ince the construction of the first wind turbine in the 1980’s, many technological advancements have made the utilisation of offshore wind energy a reality. According to 2023’s Global Offshore Wind Report, 2022 was the second highest year in history for offshore installations, adding 8.8 GW of new offshore capacity to the grid and bringing the total offshore wind power capacity to 64.3 GW, which represents 7.1% of global wind capacity. It has been projected that by 2050, offshore wind will contribute about 34% of total wind energy production.
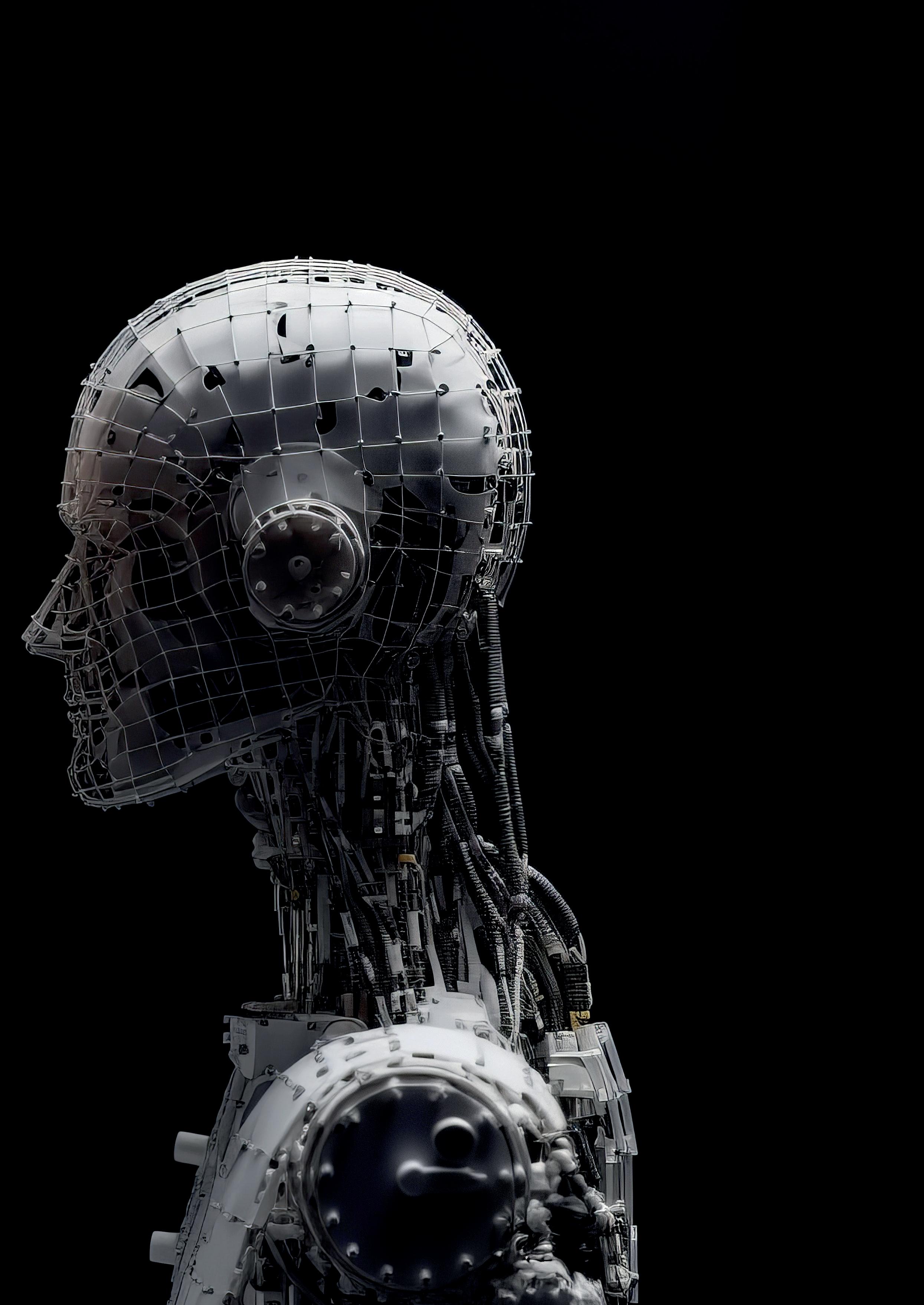
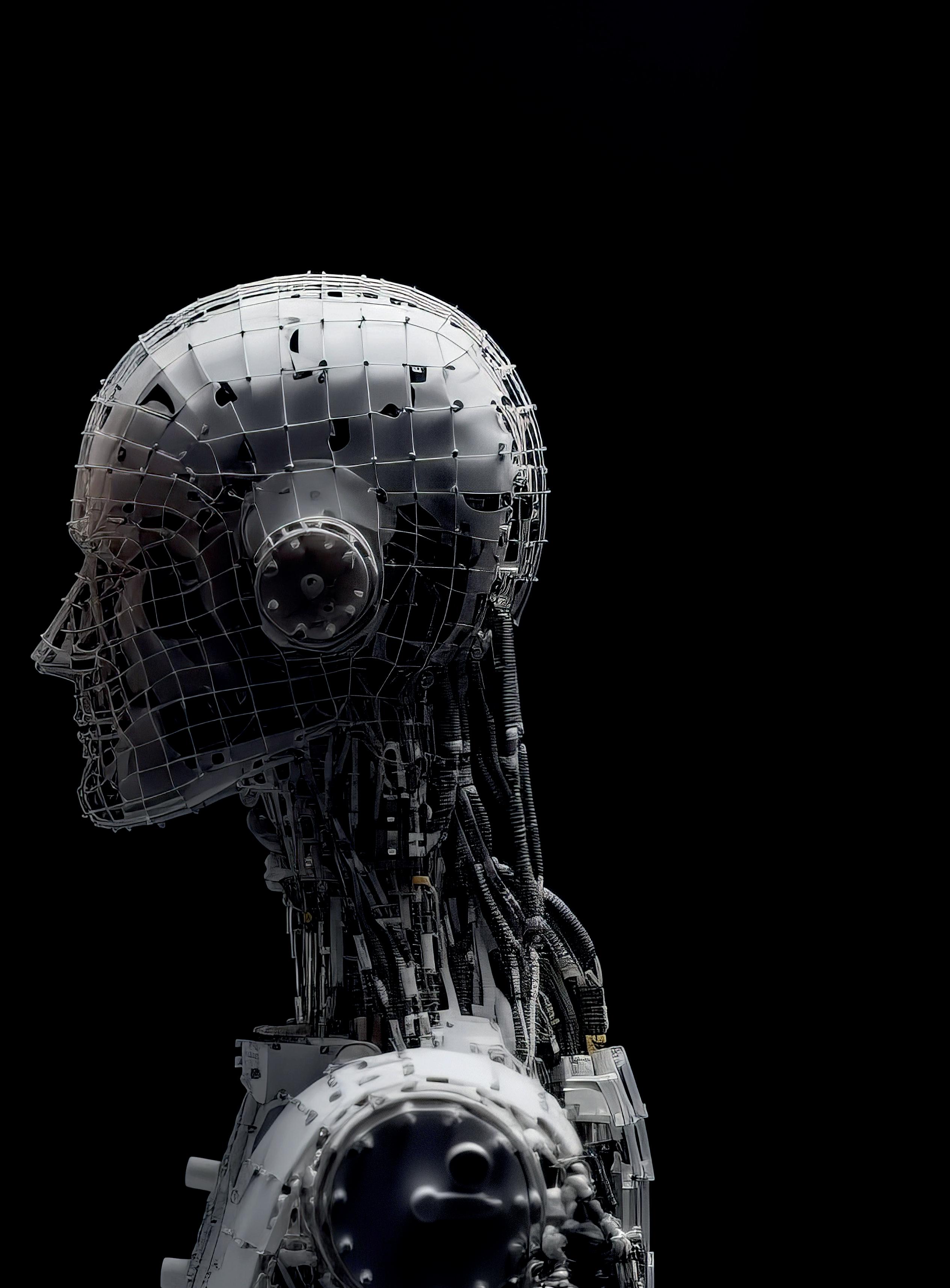
The United Nation’s Sustainable Development Goals (SDGs) include the aim to substantially increase the share of renewable energy in the global energy mix by 2030. Currently, renewable energy sources are estimated to contribute from 28 – 30% of global energy production. To meet the target of a sub 1.5˚C average global temperature rise, it is thought that more than 60% of global energy will need to be produced by a renewable source by 2030, with wind power playing a substantial part in meeting these goals. Wind turbines are a complex piece of equipment comprising physical, mechanical, and electrical systems, with high, upfront capital investment, so insuring they can operate effectively, mostly in remote locations, is paramount.
As dependence on wind energy grows, so does the demand for larger wind turbines; this is because as the diameter of the wind turbines doubles the potential capacity quadruples and vastly increases efficiency. The increase in size has been applied offshore and even floating deployments. For example, the Dogger Bank wind farm has been connected to Britain’s national grid and has started exporting electricity for the first time to British homes and businesses. This is a major milestone in the development of the industry and the transition to a cleaner, more secure energy system.
The 3.6 GW Dogger Bank wind farm is being constructed in UK waters 70 nautical miles (130 km) off the coast of Yorkshire and in the UK’s North Sea in three 1.2 GW phases known as Dogger Bank A, B, and C. The first turbine at Dogger Bank A has started turning and producing electricity. Power from the offshore wind farm is transmitted to the UK’s national grid via Dogger Bank’s high voltage direct current (HVDC) transmission system, marking the first-time use of HVDC technology on a UK wind farm.
Powering up the digital transformation journey
As governments drive energy companies to reduce carbon emissions across their operations to meet net-zero targets, power organisations are looking to fast-track their digital transformation journey to manage new project ventures and remain competitive. Investing in a comprehensive digital transformation strategy will accelerate continuous improvement efforts in an ever-changing economic landscape. It will also promote the long-term resilience of safety performance, workforce and asset productivity, and provide manufacturers of wind turbines with the competitive edge they need to perform at best.
Engaging with a trusted digital transformation partner can help manufacturers create intelligent information from both unstructured, duplicated and disconnected data and documentation, as well as structured digital data sources and databases. This provides manufacturers with the ability to consolidate them to help reduce operational risk, increase efficiency, decrease downtime, remove value leaks, and meet internal and external compliance standards.
Artificial intelligence is pivotal to digital twins
Digital twins are coming of age for these applications –from computer-aided engineering (CAE) companies can benefit from multi-physics simulation software and finite
element analysis simulation. These can be combined with machine learning (ML) software, and other data-driven artificial intelligence (AI) technologies to assist the choice of materials and manufacturing processes to ensure precision and quality standards. By simulating the design, engineering, and production phases, wind turbine manufacturers can drastically reduce design cycles and asset failures thereby saving millions of dollars.
During the wind turbine validation and testing phases, AI and ML approaches can help focus efforts on the most critical tests and fill the gaps by accurately predicting results between data points derived from sensors and metrology. However, this requires high quality data from CAE simulations in the virtual world and the effective use of sensors and metrological data. This results in a reduction in the number of tests necessary, enabling robust wind turbine designs to be certified and deployed sooner.
Ensuring minimal wind turbine downtime by utilising digitalisation
Even once the turbines are commissioned, digital representation through a digital twin is vital to optimise operations for high performance, reliability, and quality. The operation of a wind turbine is deceptively complex. All the disparate mechanical, electrical components, and mechanisms need to operate in tandem to ensure the quality, reliability, and safety of the system. However, components such as the generator, gearbox, blades, and bearings are known to have high failure rates, which are often caused by fatigue stresses, cracks due to strains on the blades, tower, or gearbox components which can be caused by unfavourable weather conditions and even bird strikes. All these failures lead to hazardous situations and costly shutdowns that have a huge impact on the wind farm. Having a digital representation allows for analysis and prediction of when these common failures will occur so they can be pre-emptively dealt with, thereby avoiding hazards and shutdowns.
Using predictive and prescriptive analytics to prevent outages
Predictive and prescriptive analytics are sets of statistics and data modelling techniques, usually based on ML and AI algorithms which use historical data to forecast wind turbine outcome and performance results. With the ongoing shift to AI-based solutions, the energy industry is beginning to take predictive analytics one step further and move towards a proactive approach based on real-time data monitoring and event analysis both to prevent incidents or adjust conditions before a critical moment. This can go further – by feeding this data back into the physics-based representation of the digital twin, new insights can be gleaned that can extend the operation of existing turbines and provide unprecedented risk and cost reduction for subsequent designs.
Conclusion
In conclusion, original equipment manufacturers can reap the benefits of getting to market faster and reducing cost by employing digital platforms and automation. These tools can accelerate innovation and improve engineering design and productivity across the complete value chain right from component suppliers, turbine manufacturers to wind farm operators and owners, and even independent power producers.
CHOOSE THE GLOBAL LEADER IN WIND TURBINES
30 YEARS OF EXPERIENCE AND INNOVATION IN THE WIND ENERGY SECTOR
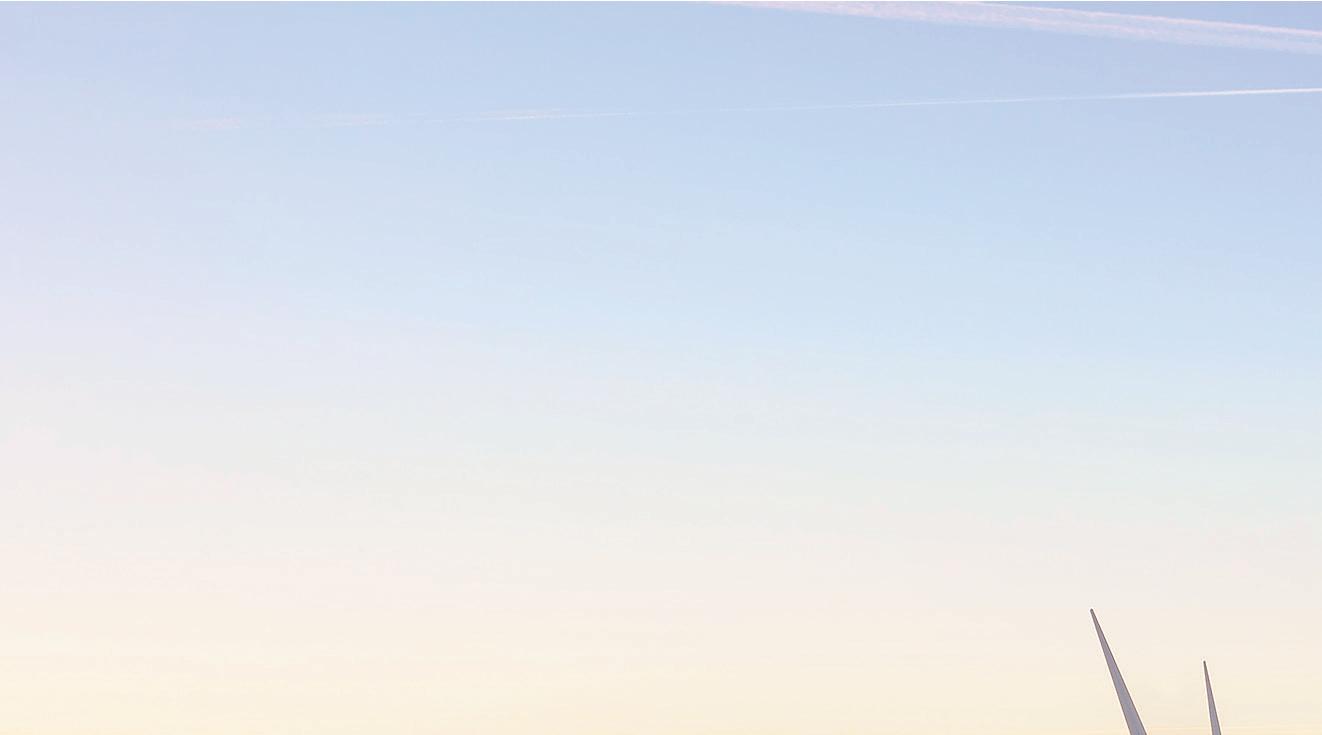
Our products boost wind turbine performance, both offshore and onshore.
Discover our complete solutions for efficient wind energy
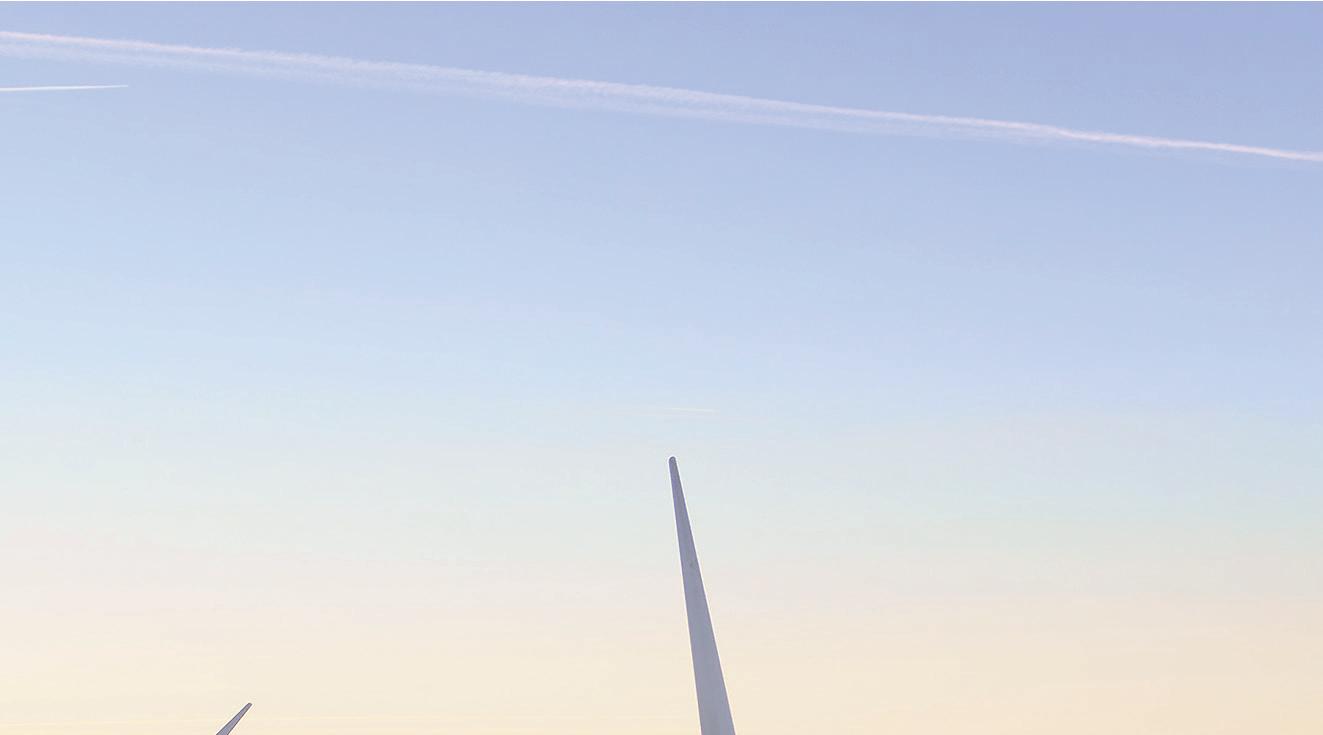
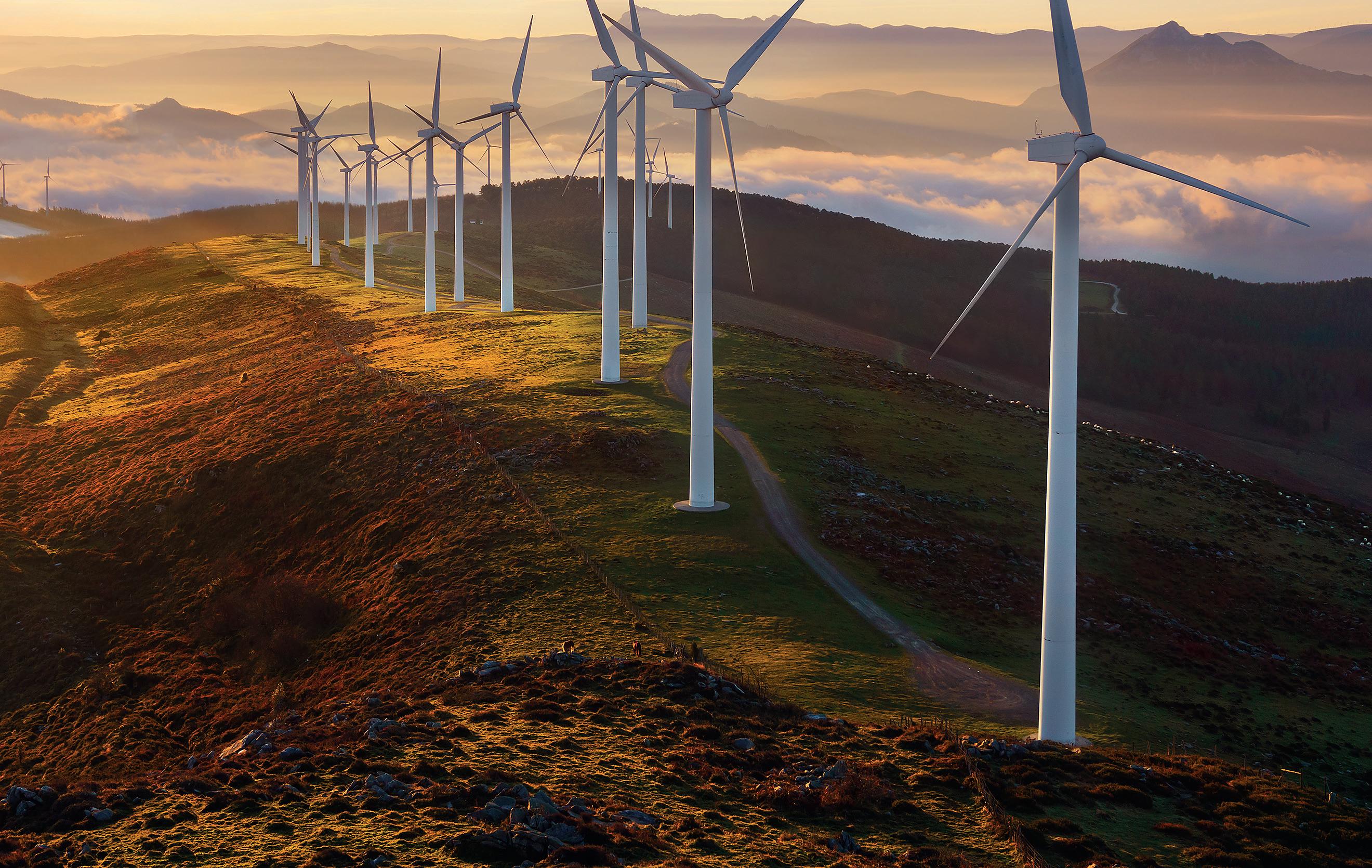
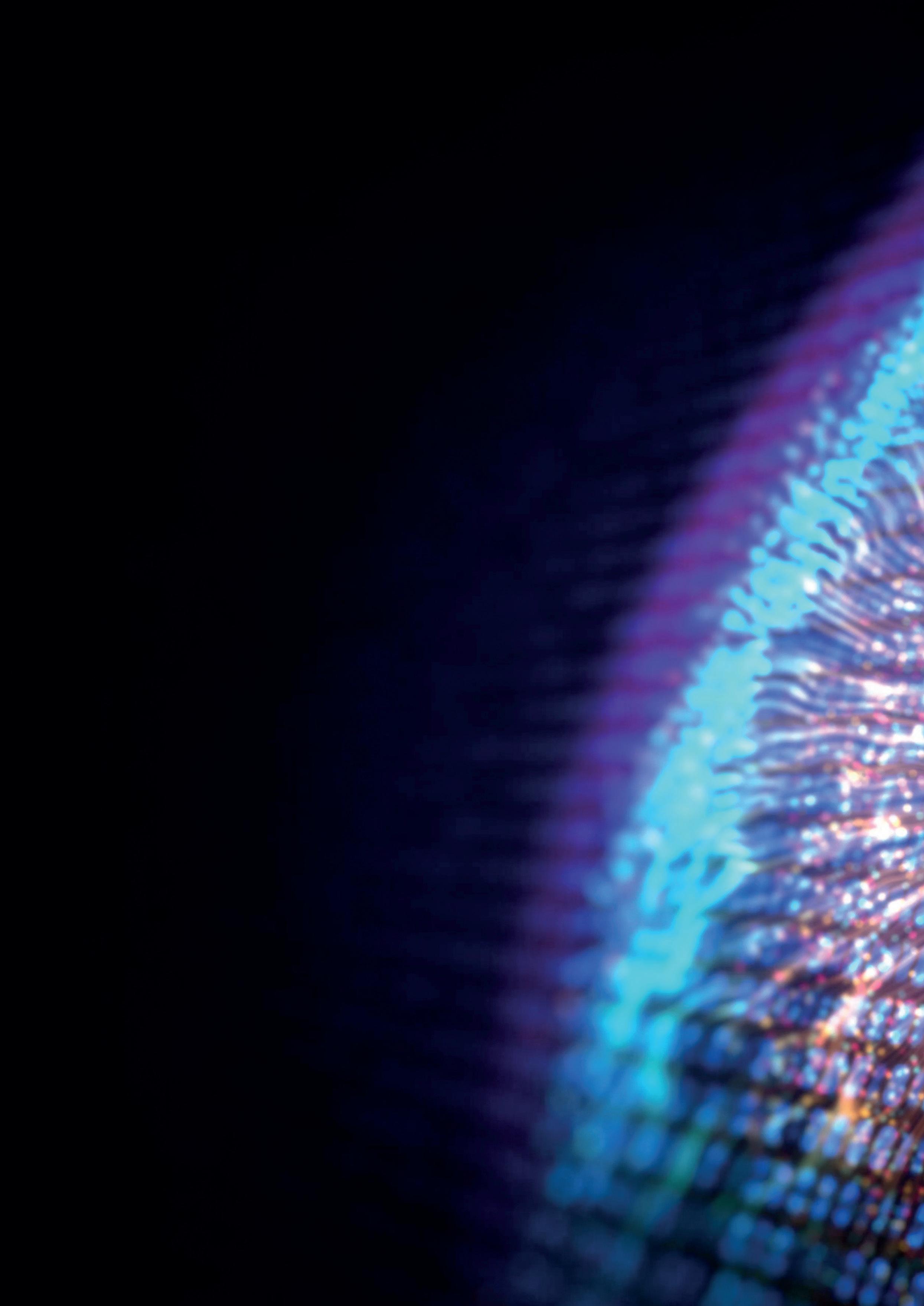
Frank Forsberg, Project Manager, ALICE Technologies, USA, discusses how artificial intelligence can be used to optimise and speed up project delivery of offshore energy assets.
Wind farm construction appears straightforward. A concrete foundation is constructed and wind turbines, made off site, are brought to the location and installed. Wires are placed in channels underground and used to connect the individual turbines together. Once complete, the wind farm starts producing electricity.
Unfortunately, it is not always as simple as it appears.
Weather conditions and supply chain issues are the primary causes of delays in wind farm construction. Both issues can lead to costly downtime and exposure to liquidated damages of tens of thousands of pounds per day.
As the world starts to set more ambitious renewable and net-zero targets, wind farms will only grow in popularity. Efficient construction and the accelerated project delivery of wind farms are key to keeping up with demand.
Labour and supply issues
Ensuring that the wind turbines and electrical equipment are on site when needed can be challenging. Wind turbine suppliers have long lead times of around one year, and delivery dates are commonly a ‘best guess’ at the time of purchase.
This problem also extends to workforce planning. With many project sites in remote and rural locations, including on coastlines and out at sea, it can be hard to find the right people because of the small population living near those areas.
As a result, project managers can struggle to plan, with many moving parts needing to be co-ordinated at one time, each reliant on the other.
Weather woes
Over the last five years, construction project duration was extended by an average of 21% in the UK because of weather, resulting in missed completion dates and significant increases in costs. Met Office data also shows that the UK is 9% wetter now than it was between 1961 – 1990. In July 2022, the UK also had its hottest-ever day of 40.3˚C. These unpredictable weather issues are causing significant
O n the fasttrack
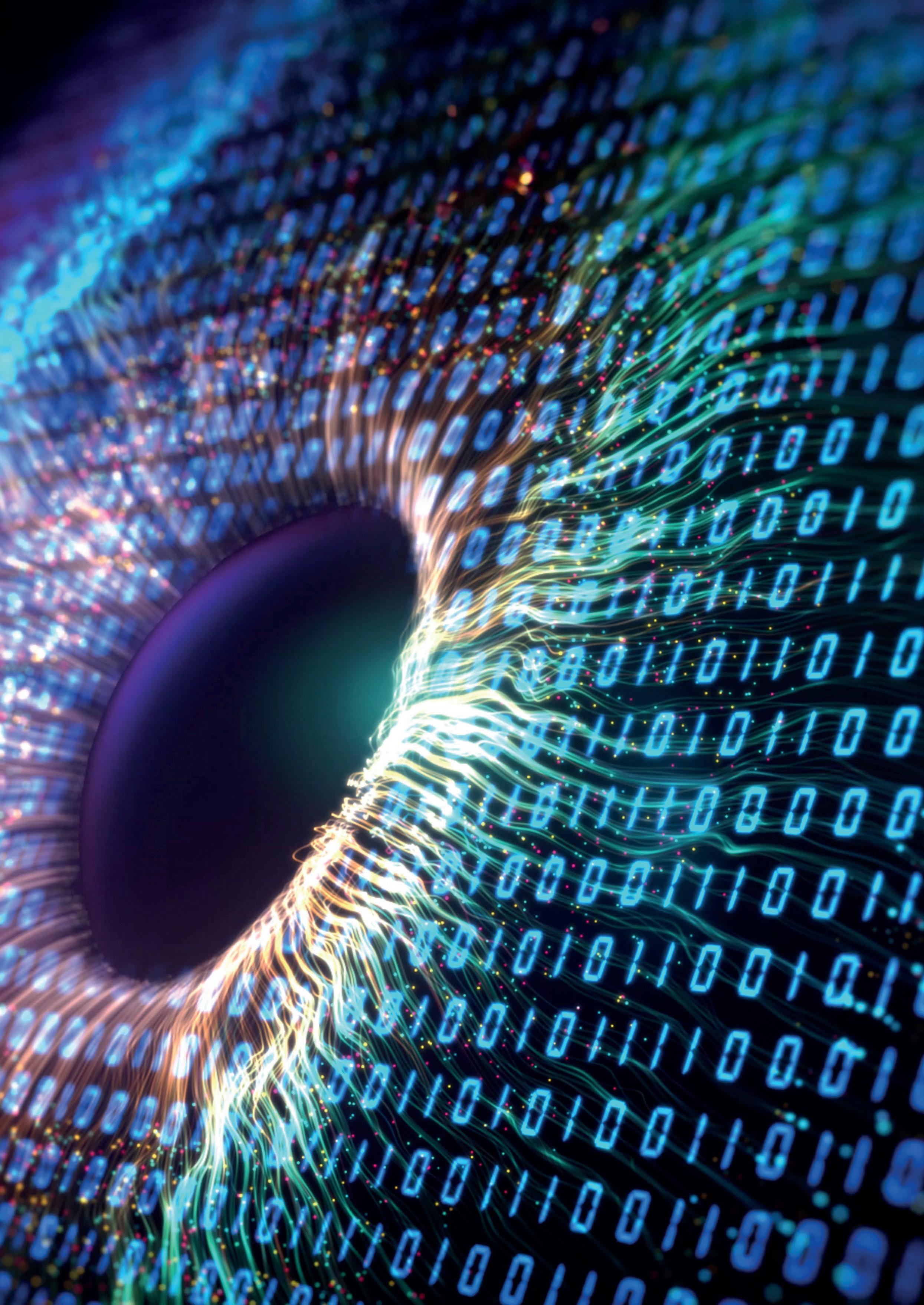
problems with common infrastructure such as manufacturing sites and product transportation.
The remoteness of wind farm sites means that these weather issues can often be exacerbated, causing havoc during the construction phase.
For offshore developments, all components must be pre-made on land before being put on a barge and transported to site. Changing tides and adverse sea conditions can negatively impact both the delivery of the components and the installation.
Onshore, poor weather may delay the concrete pour for the foundations, or even increase the setting times. Wet conditions can make it difficult to move cranes between turbines or run electrical wires in flooded trenches.
Moreover, the number of extremely hot days in the UK are predicted to increase four-fold, with days exceeding 25˚C rising from around 10 days/y to 37 days/y. Hot temperatures can cause health and safety issues for a wind farm construction workforce and increase the risk of more dust and airborne particles being kicked up during construction. This dust can make workers unwell and clog the fans and engines of machinery, reducing efficiency and increasing running and maintenance costs.
These extremes in weather can also damage materials, for example, high temperatures warping metal. Artificial intelligence (AI) can help here, ensuring that programme changes can be made to keep workers, equipment, and materials out of harm’s way while maintaining construction schedules.
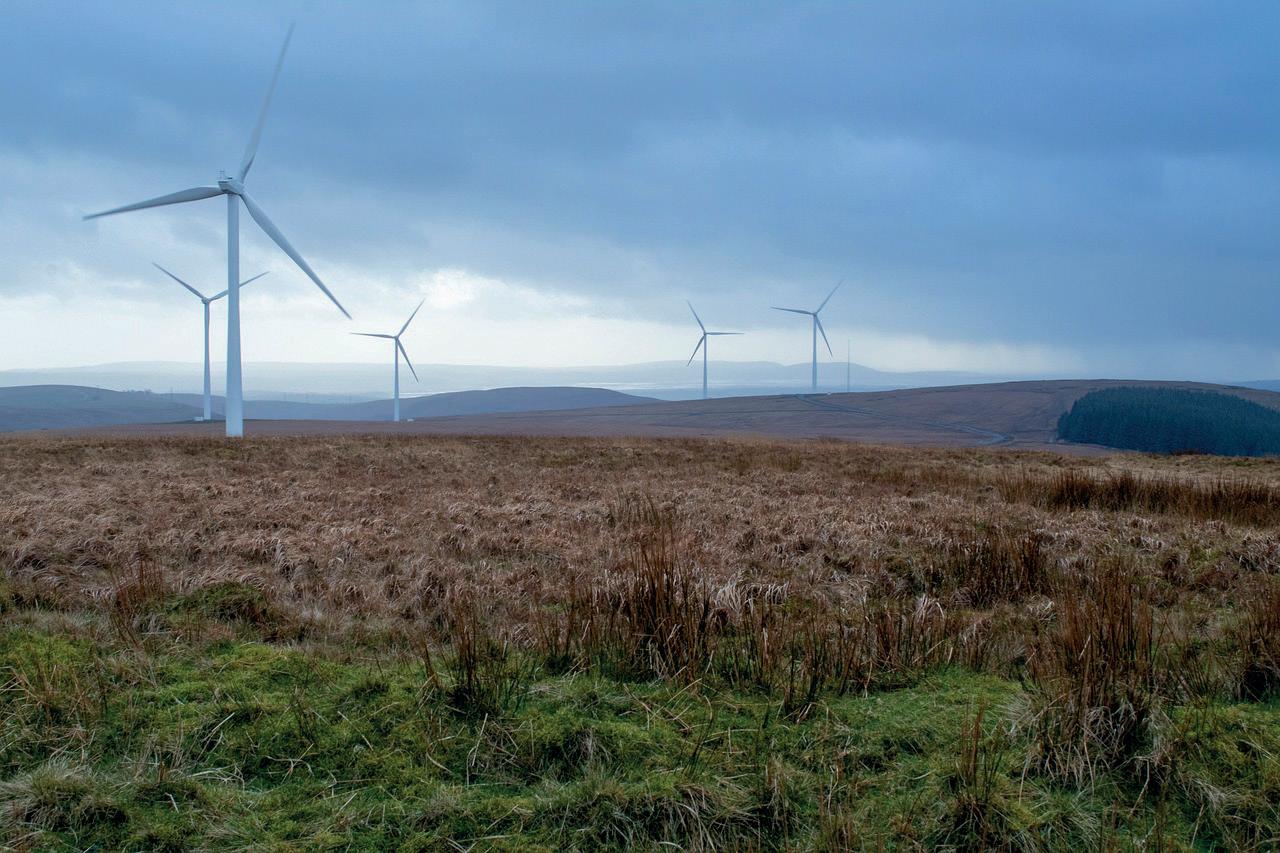
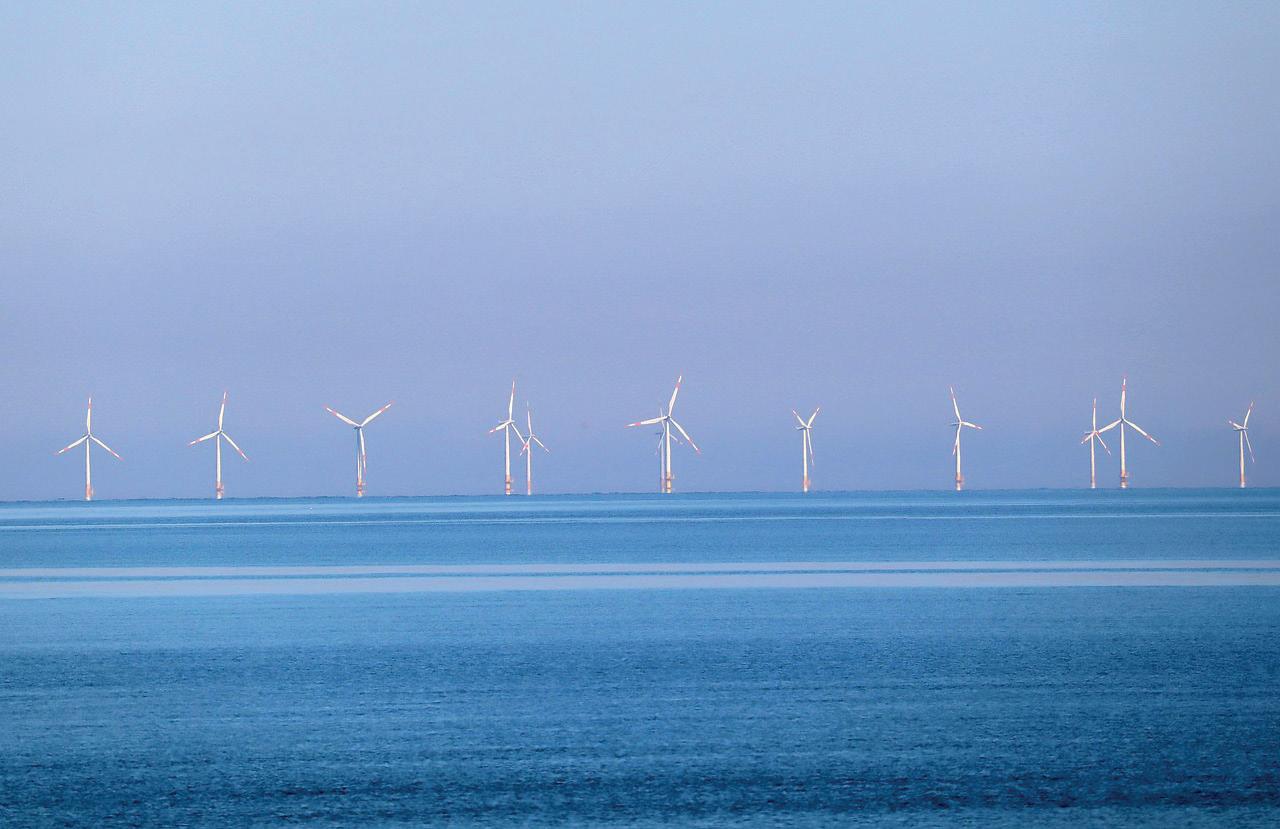
Whatever the specific impact, the weather can significantly complicate and alter project schedules, with one delay having a knock-on effect on everything else. Now, technology has the answer.
AI in practice
By using AI, owners and contractors can rapidly test and prototype different construction schedules to find the most efficient way to use labour, machinery, and materials.
Construction teams can use AI to optimise and explore optimal solutions starting from their baseline programmes created in Primavera P6, Microsoft Project, or TILOS, or they can use AI to create one starting from a 3D model.
AI can also be used to quantify the cost and time impact different scenarios would have on the project, such as the length of build time and the method of transport for the foundations. Any delays can have a significant impact when deciding on an appropriate site, so this optioneering and optimisation process is an important way of understanding and testing the programme.
Case study – using AI in wind farm construction
A floating offshore wind project between NorSea Impact and Implenia Norge provides an example of a wind farm project that is using AI.
The project was focused on finding and developing a production facility to create concrete foundations for floating offshore wind farms. Implenia needed to find a site for the serial production of wind turbine foundations that would yield up to 1 GW/y of energy generation once operational.
It enlisted support from ALICE Technologies, the provider of the world’s first AI-powered construction optioneering software, to optimise serial production to ensure that the most efficient outputs can be achieved. ALICE is helping answer:
> What is the most efficient site layout for constructing and moving the foundations?
> Is one or two launching corridors the optimum solution for increased productivity on site?
> How can on-site resilience be improved?
Driving innovation in energy
Implenia has been exploring several locations for a production facility in order to undertake serial production of concrete foundations for floating offshore wind farms.
AI is being used to assess the feasibility of different sites and identify best practice approaches – even at sites where there is a finite amount of space in which the foundations can be constructed. And since the size of the foundations are large, it limits the number of workstations that can be created and utilised.
To save on transportation emissions and costs and improve productivity, the chosen site would also include steelworks to create the rebar that is needed during the foundation construction process. Both elements have to be planned for.
Creating a foundation
Once each foundation is built, it takes time for that foundation to be transported before a new foundation can be built at that workstation. New constraints specific to each site are also
Figure 1 . Onshore wind farm.
Figure 2 . Offshore wind farm.
being tested – calculating the distance of movement for each foundation and the speed of transportation.
This is a huge benefit when it comes to feasibility as it allows more certainty, a crucial factor in getting major infrastructure projects planned and approved. It removes the need for reactive decision-making that can easily reduce productivity and increase costs.
Seeing the benefits of AI
In the initial testing phase, it was found that most sites could create a baseline level of foundations needed each year. Through the optioneering process, Implenia can test different scenarios to see where productivity gains could be made, adjusting various factors along the way.
During these planning stages, AI is helping to prove the value of having optimised, data-backed schedules. Implenia now has the insight to be able to prove that they can meet the desired production targets in a range of possible locations.
The design can also go a step further by highlighting possible cost and time savings that others may not have considered, such as site configuration, transport method, and timing of the transportation of materials between workstations.
Implenia has experienced a faster planning process with ALICE by 10 times than the traditional methods. Through optimisation with ALICE, Implenia is also able to boost potential foundation production levels considerably.
The program has its own AI algorithm that analyses multiple scenarios based on things like equipment, people, cost, and
then calculates the best way to execute a project that will save money and time.
Using ALICE means Implenia can give the software all the necessary information and create multiple time schedules and scenarios that can be modified in real time, instead of only one or two schedules, like with traditional planning tools.
The future of AI
AI capabilities are only developing as it becomes more mainstream in people’s daily lives and this is extending to the wind farm sector.
AI enables wind farm constructors to proactively analyse numerous different strategies, including labour and equipment usage and construction sequencing.
AI can also provide support during the design planning stages of wind farms. It can be used to optimise designs and yard layouts by analysing different turbine arrangements and cable routes, to make the construction and operation process as streamlined as possible.
It can test the impact of expected or experienced procurement delays. ALICE is parametric, so it will automatically adjust project schedules to help mitigate the impact of delays and give project managers the best chance of finishing their projects on time.
As the wind farm industry is faced with increasing challenges, AI is set to help streamline processes, cut design timelines, and support the industry in finding the most effective locations for wind farm manufacturing sites.
Structural Health Monitoring – SHM
Lasting fitness – turbine monitoring from head to toe
Long-term performance
Minimize the Levelized Cost of Energy (LCOE) and maximize yields – all while extending turbine lifecycles (LTE)
Digital twins
Predict the impact of new functions and improvements without interrupting operations
Investment security
A key building block for strategic decision making and the successful, long-term operation of turbines and wind parks
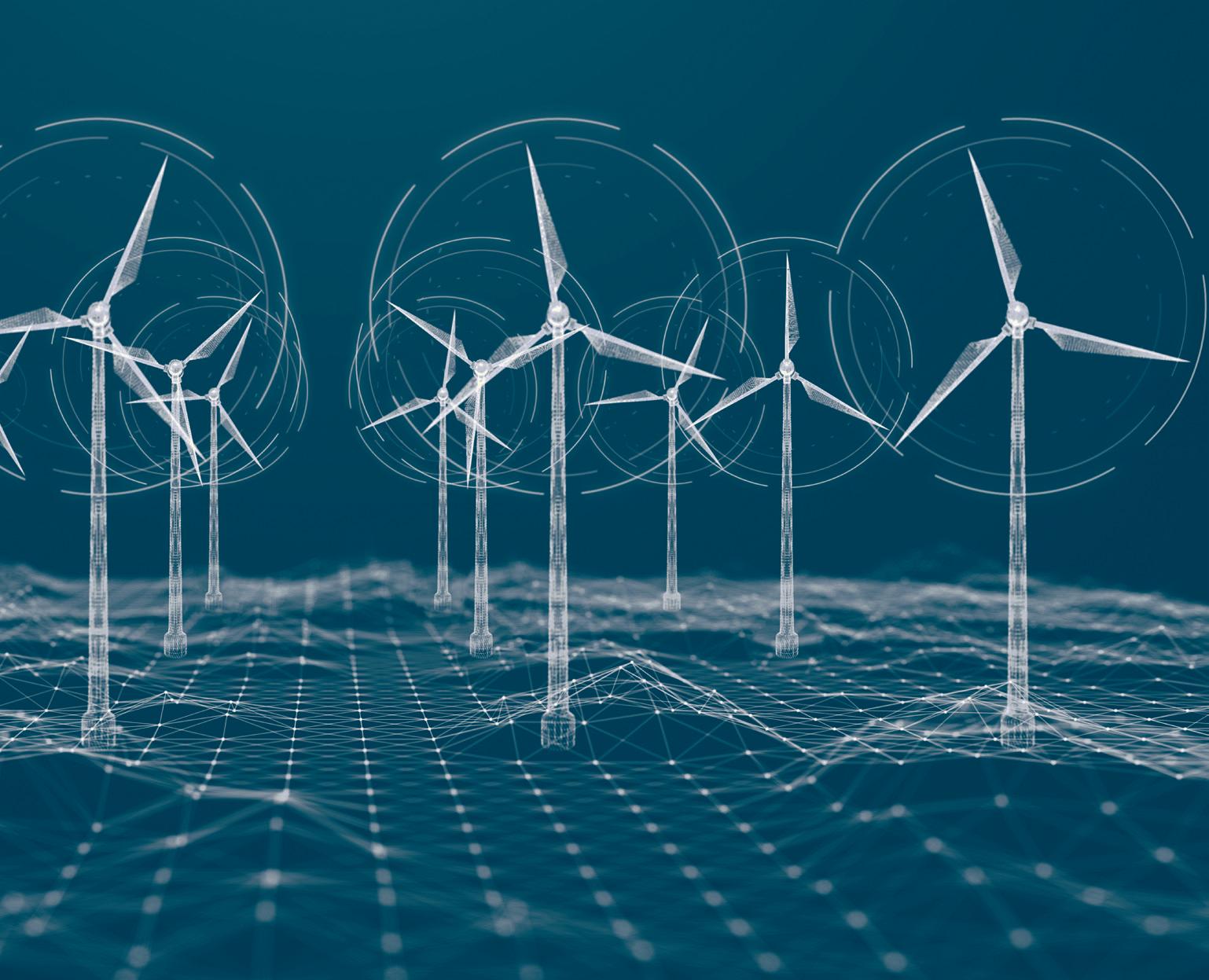
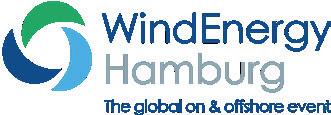
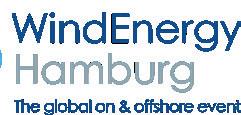
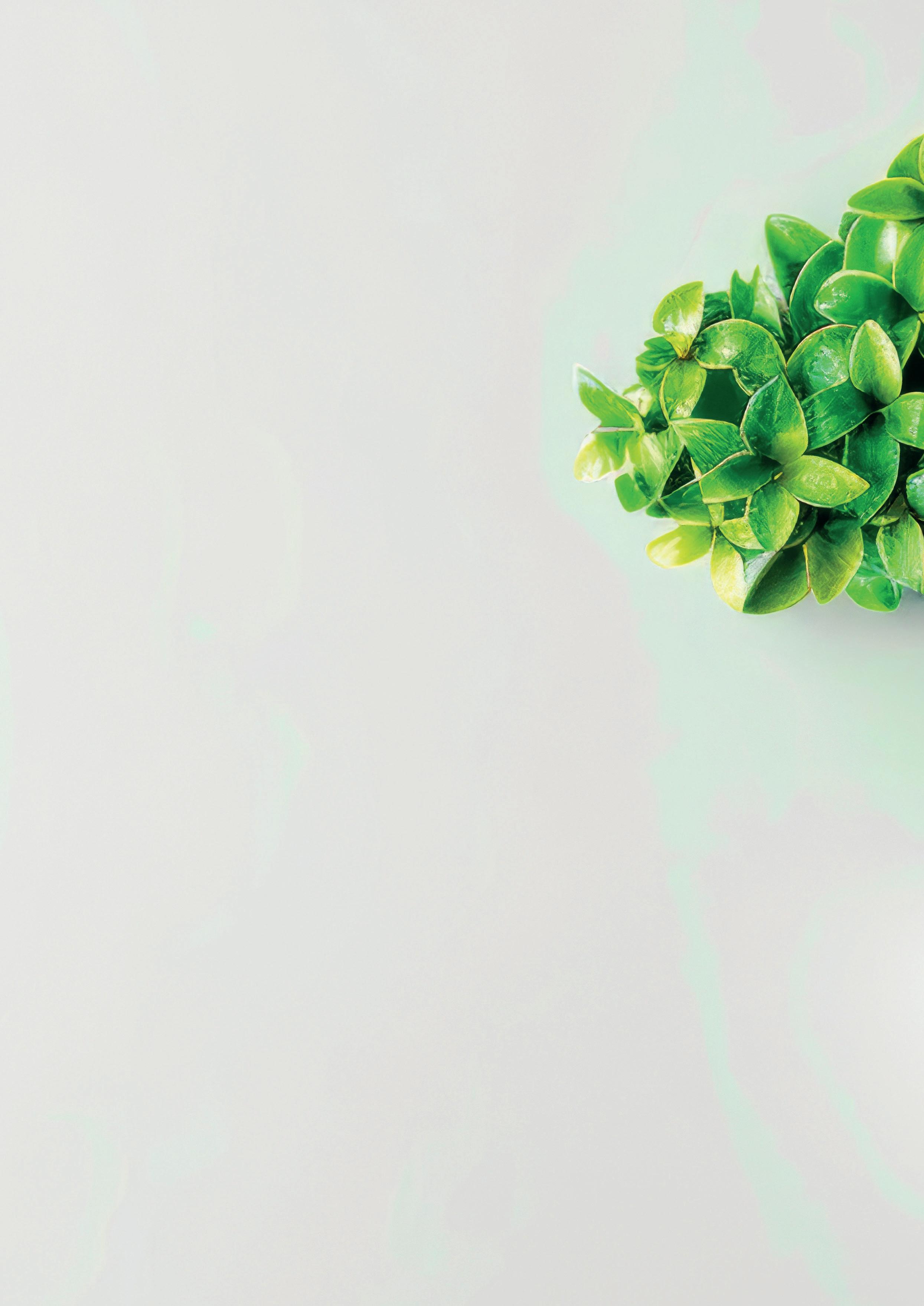
HARNESSING THE POWER OF
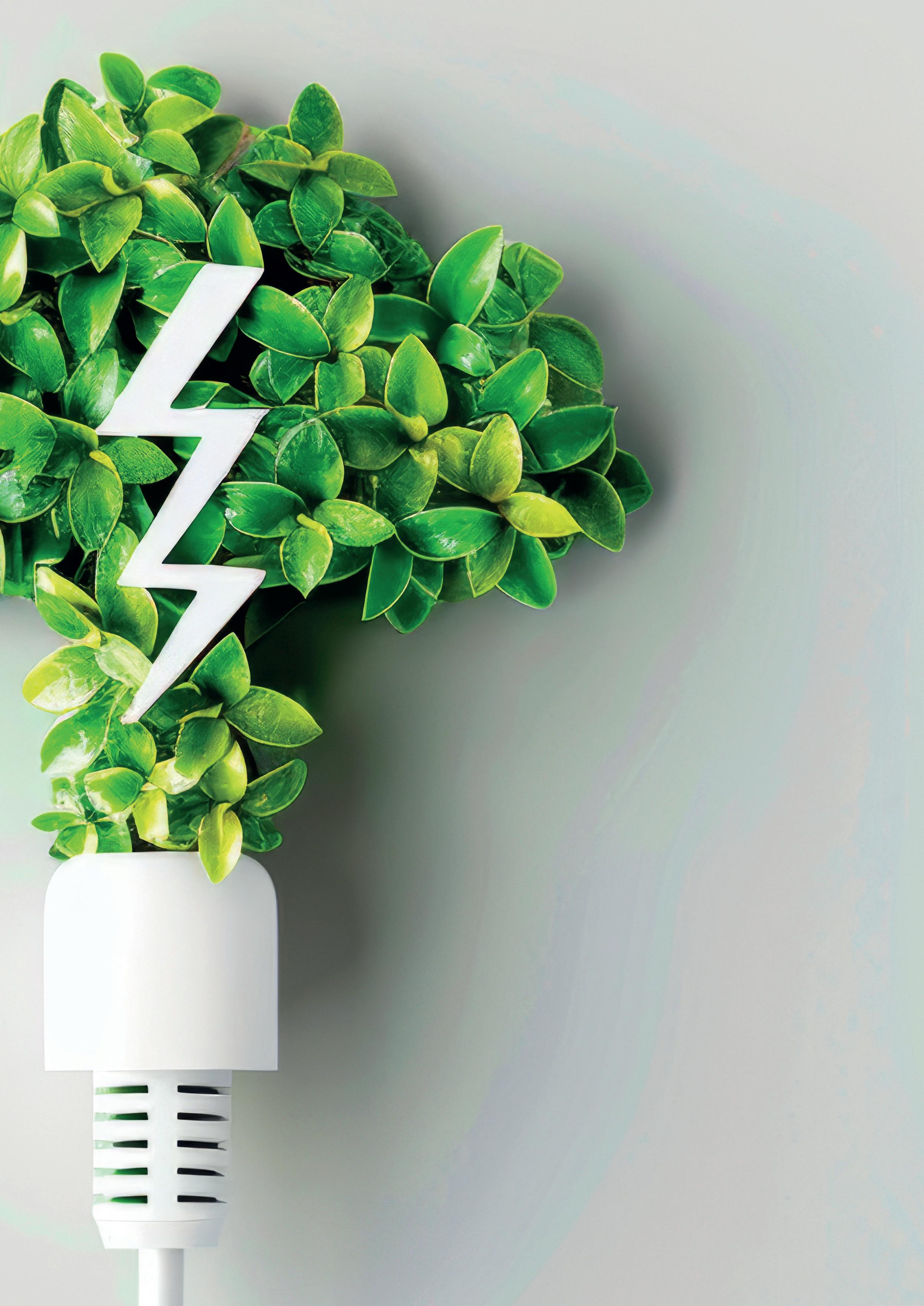
Leo Hambro, Commercial Director, Tidal Transit, addresses the current state of the offshore wind servicing industry and highlights solutions for sustainably transitioning the sector to net zero.
ffshore wind is poised for major expansion in the North Sea and beyond. As part of the UK and EU’s drive towards increased energy security and a low-carbon energy mix, the number of new wind turbines entering operation and supplying electricity to the grid is set to explode; and with this growth comes the ever-growing need for efficient servicing. Like all modes of energy generation, wind turbines require thorough inspections and continuous maintenance to ensure uninterrupted, optimal, and safe operations.
The transfer of engineers and equipment between shore and site is no easy feat – it needs an expert crew of experienced maritime professionals and vessels that are durable and comfortable enough to safely transit in all weather conditions, and there are number of diligent operators working throughout the year to ensure wind farms have the supply of engineers and equipment necessary to maximise yield from the farm.
But herein lies the problem: crew transfer vessels (CTVs) – designed primarily for quick transportation of personnel and light equipment – and service operation vessels (SOVs) –larger vessels that providing a base of operations designed for long-term – burn a significant amount of diesel. CTVs, for example, use around on average 1500+ l/d of fuel in operation. With around 400 vessels currently servicing the UK and Europe,
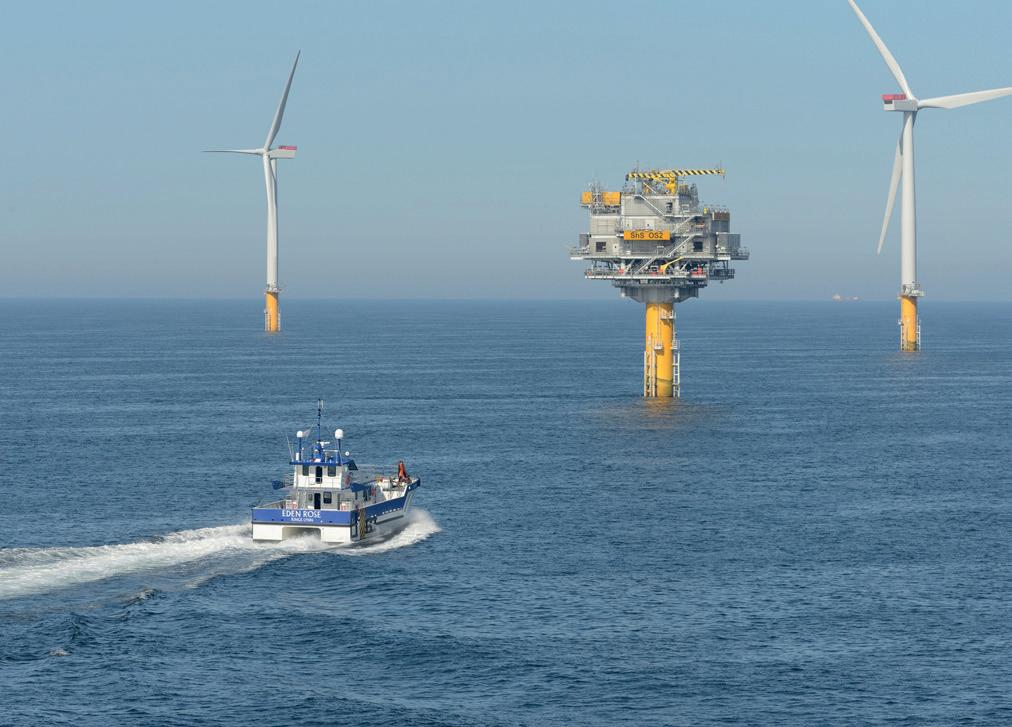
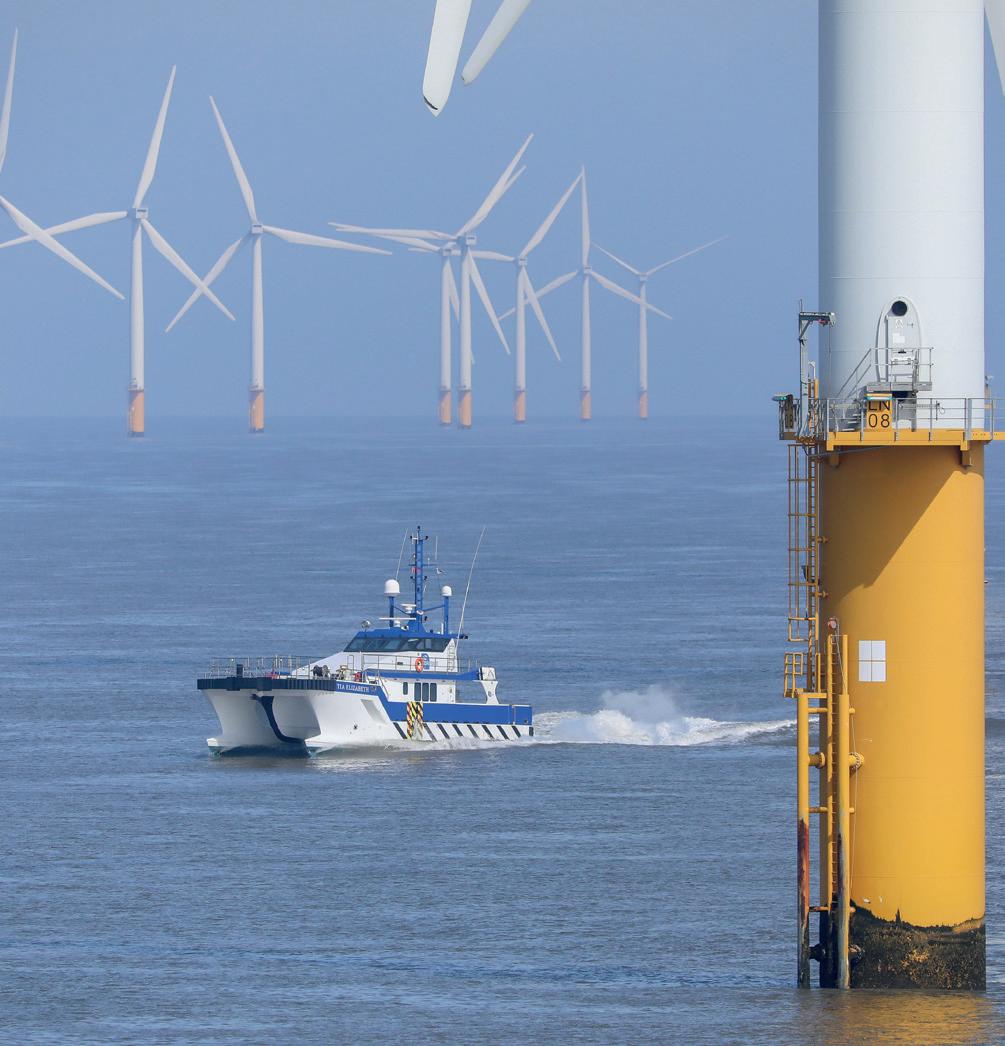
this is a staggering amount of carbon emissions for a service operating at the forefront of renewable energy.
In a sector which generates gigawatts of energy from the forces of nature every year, surely there must be a better option than burning fossil fuels?
What can be done electrically, should be done electrically
The answer, quite clearly, is to electrify the entire system.
Electric crew transfer vessels, or E-CTVs, offer the same safety standards of any diesel-powered boat and can carry an equal load, yet they:
> Benefit from much higher reliability with lower maintenance costs.
> Are more comfortable for crew (without noise and vibrations from a turning engine).
> Benefit from significant noise reduction for people and wildlife above the water and marine life beneath.
> Most importantly, generate zero operational carbon emissions.
Battery density has advanced so rapidly in recent years that the industry is now at a point where it is not only feasible, but makes more economic and environmental sense to use batteries over internal combustion. A huge swathe of wind farm and service operators have 2030 decarbonisation targets, and with the availability of unlimited, cheap energy at source, electrification of CTVs and SOVs is a clear, yet wholly achievable ambition. So where should the industry begin on its journey to electrification?
Careful forward-planning is essential to maximise the positive economic and environmental impacts of transitioning towards decarbonised inspection and maintenance services. For example, if every wind farm operator made the switch to electric, what would happen to CTVs currently in operation? They could easily be exported other countries but, by doing so, the carbon emissions would simply be displaced elsewhere.
The alternative solution is to instead adapt existing diesel-powered CTVs to run on electric, which comes with a number of benefits over building new. Not only does electrically retrofitting vessels reduce the demand for fossil fuels and the significant emissions linked to decommissioning and building vessels, but it also greatly extends the operational lifecycle and keeps them in the value chain for far longer. This circular economy thinking ensures that the drive for sustainability does not counterintuitively contribute to further harmful waste and emissions.
The future of E-CTVs: Building an entire electric ecosystem
There is, of course, the sustainability question around the environmental impact of batteries. Crucially, what happens to the used batteries once they no longer have the capacity to function fully?
Modern batteries are not only significantly cheaper than they were a decade ago, but they degrade remarkably slowly – they only lose about 20% working capacity over a 10-year lifecycle. Even a battery at 80% working capacity still has
Figure 1 . Crew transfer vessel (CTV) carrying crew and equipment to an offshore wind farm.
Figure 2 CTV servicing the offshore wind sector in the North Sea.
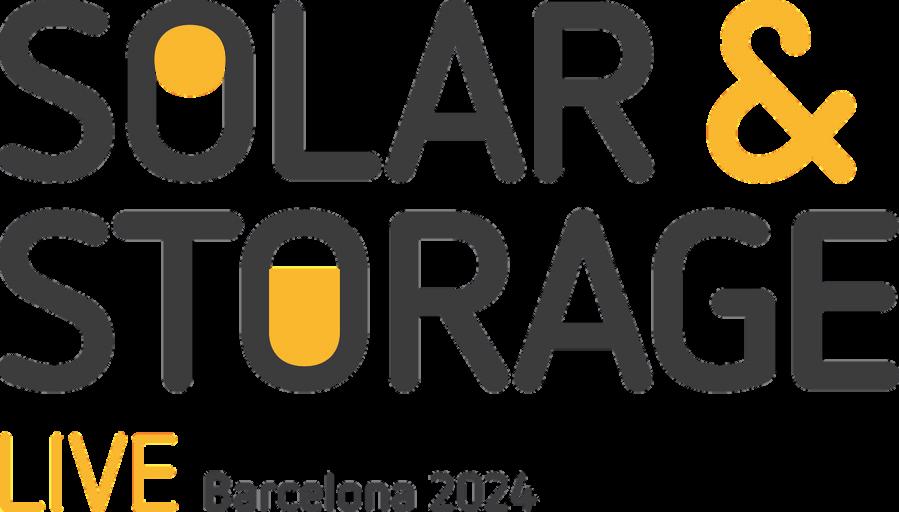
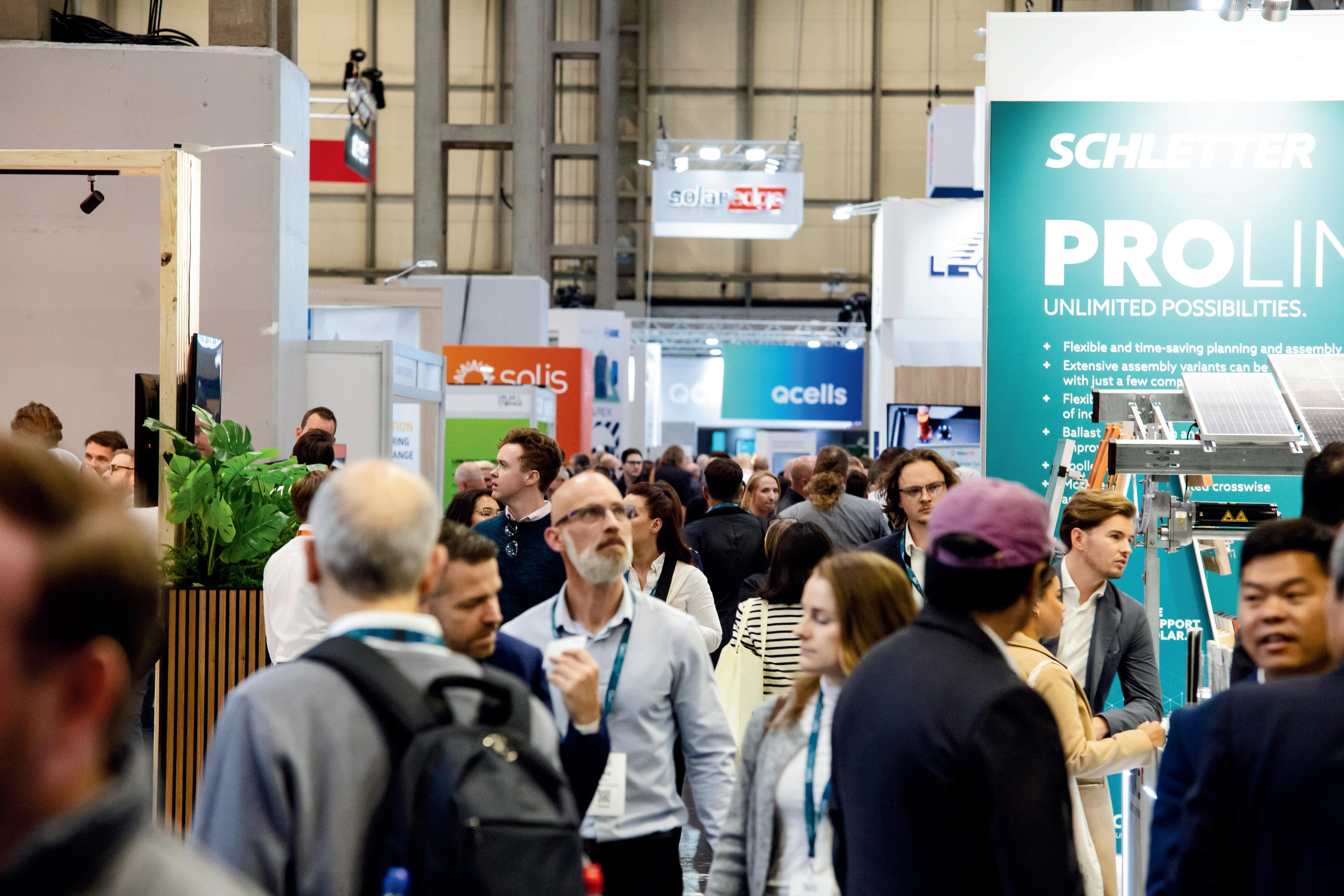
13-14 November, 2024 | Fira Barcelona Montjuic, Barcelona
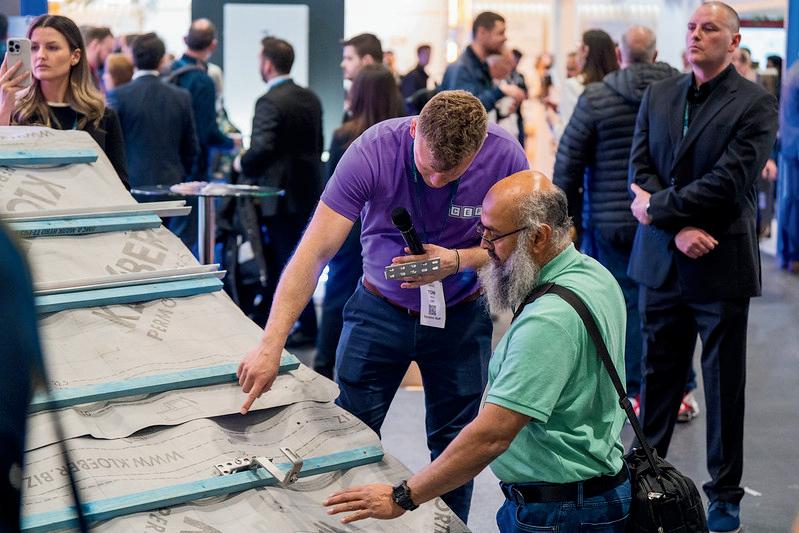
150+ speakers
from across the globe, featuring new ways of thinking and novel partnerships to generate solutions to help power the energy transition.
including manufacturers, installers, property owners and landowners, delivering solar and storage case studies and product demos.
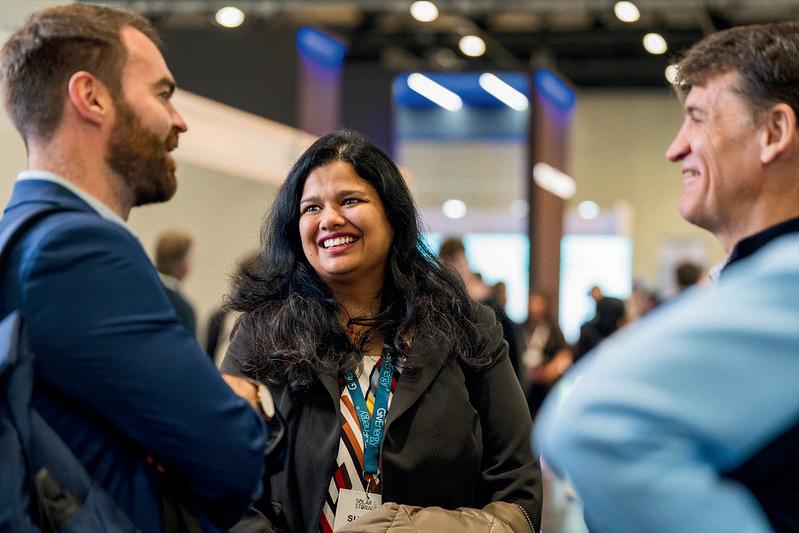
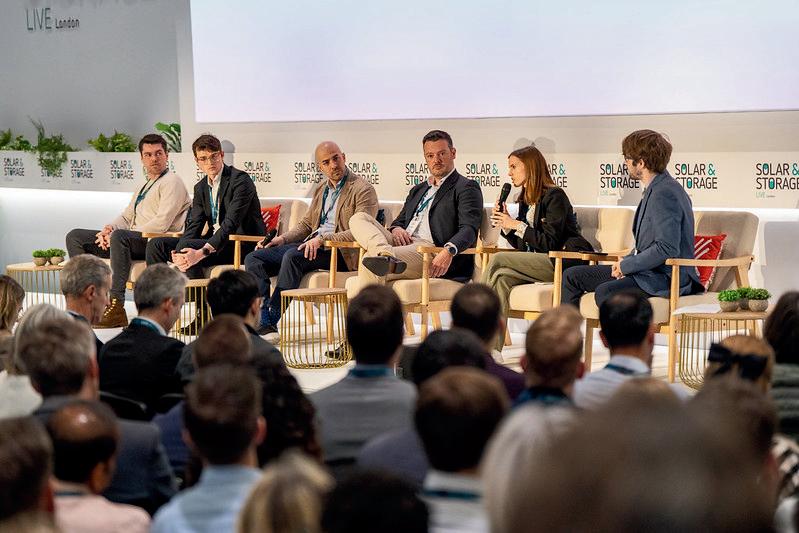
To facilitate networking opportunities, we have a dedicated networking app which goes live a few weeks before the event takes place.
Register for Your Free Ticket Now
https://www.terrapinn.com/sslb/energyglobal
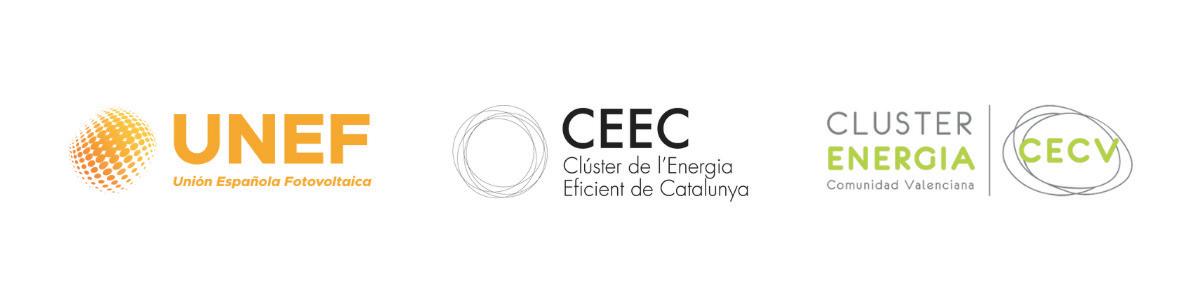
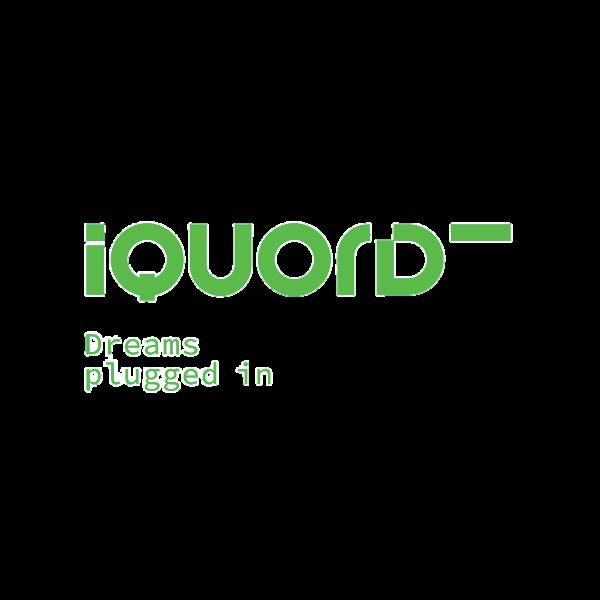
its uses, but at the point when it does need replacing, the next generation of batteries will have much higher working capacities as energy storage technology evolves. When batteries are eventually swapped out, they can be utilised in a number of ways back on shore – the batteries of today will be the quayside batteries of tomorrow, offering a second life for the technology and greatly improving the circular economy of the sector.
Much like conversations around electric vehicles (EVs) on land, there is a certain ‘range anxiety’ attributed to the use of electric-powered vessels. However, the discourse should be shifted away from one of anxiety, and instead to one of proper planning and development of charging infrastructure to ensure efficient, reliable, long-range use of E-CTVs and E-SOVs. Efforts to scale up electric vessels would, after all, be futile without a robust charging infrastructure to support it.
Whether newbuild or retrofit, a new charging system must be developed in tandem with battery-powered propulsion. While onshore charging solutions can provide a convenient and reliable means for electric vessels to replenish their energy reserves at the quayside, it is in offshore charging infrastructure where the sector can truly move the needle. The integration of offshore charging, which allows E-CTVs to plug directly into wind turbines through both fixed and floating solutions, allows vessels to harness the abundantly available renewable energy directly from source and with high efficiency without transmission costs and losses. This greatly extends service vessels’ time on the water and opens up wider areas of the sea that can be serviced by zero-emission vessels.
The ideal long-term future of charging infrastructure is one where all wind farms adapt to serve as offshore charging/fuelling stations for all maritime, not just those servicing the wind sector itself.
The elephant in the room: What about alternative fuels?
Alternative, lower carbon fuels like green hydrogen, ethanol, hydrotreated vegetable oil (HVO), and biofuels are, quite rightly so, gaining popularity and increasingly entering the discussion on decarbonised maritime. While these fuels certainly have their place in a net-zero future, their use-case for offshore wind services are actually rather limited.
Take hydrogen as an example – from a pure energy efficiency perspective, a very large proportion of raw energy is lost in the hydrogen making process. Combined, the energy cost for desalination, purification, and electrolysis comes up to around 50% of the total energy put in, even before the cost of compression, storage, transport, and ultimate conversion back to electricity.
With as little as 30% of the original energy left over at the end of the process, the question has to be: why choose green hydrogen when there is an unlimited, near 100% efficient source of energy at one’s fingertips?
Hydrogen has been lauded the next step to decarbonised maritime but, in reality, it might not be feasible with the costs and timelines required to meet a quickly expanding offshore wind services sector. There is no doubt that green hydrogen
should and will replace brown, blue, and grey hydrogens in energy-intensive sectors such steel and cement, but burning hydrogen to fuel CTVs does not make sense from a cost and efficiency perspective. Instead, the industry should start with electricity and end with electricity.
Other more circular fuels like HVOs have terrific potential to be used in a hybrid capacity, much like plug-in hybrid cars, but there just is not enough fuel available at the scale required to decarbonise the entire system.
In a real-world scenario, a hybrid vessel could sail out from shore with full battery to a site up to 30 – 40 miles offshore, using almost entirely battery power but supported with an additional small amount of diesel for range extension. While servicing a site, hybrid vessels can charge up and use 100% electricity for operations, and then use a small amount of diesel on the way back to shore. This form of operation can reduce diesel consumption by 90+%, which could be replaced with HVO, methanol, or other alternative fuels. This type of system is fuel agnostic, and as long as it leads to an impactful reduction in carbon emissions, it is a much more economical and sustainable alternative to how the system currently operates.
E-CTVs in practice
Tidal Transit is spearheading a world-first design and engineering project to actually retrofit a diesel-powered CTV, Ginny Louise, with over 3 MWh of battery capacity,
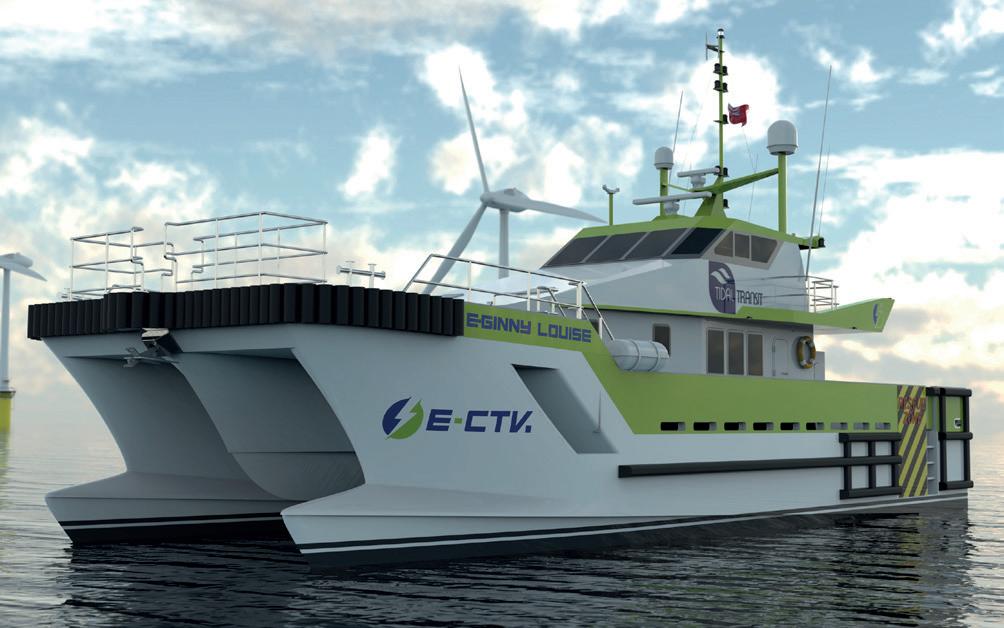
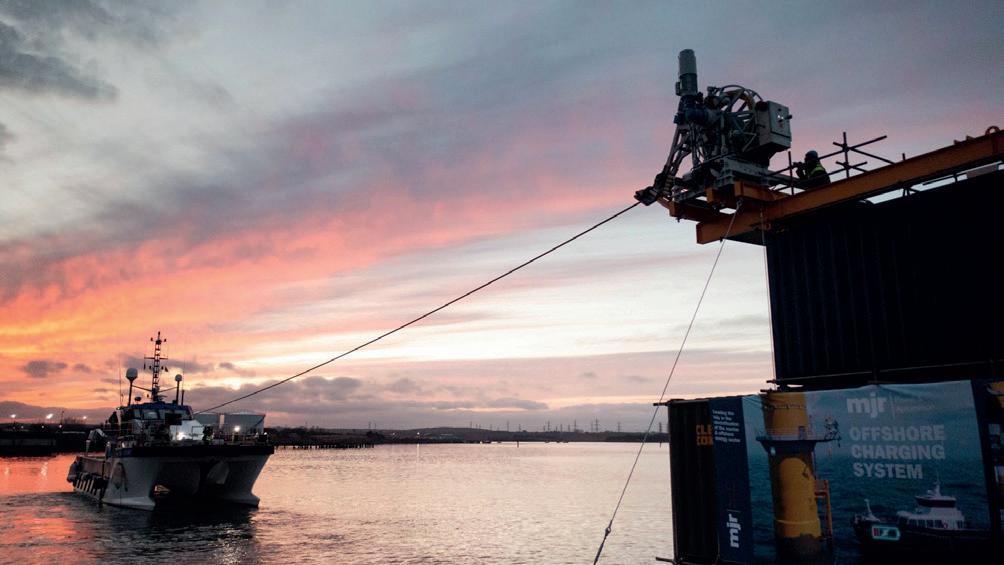
Figure 3 Render of e-Ginny, the world’s first diesel-to-electric retrofit CTV.
Figure 4 . E-CTV utilising an offshore charging system.
electric motors, and propulsion pods. The resulting vessel, e-Ginny, will not only be 100% zero emissions in operation, but also offers increased manoeuvrability, improved safety, and be near-silent for passengers and passers-by.
The initiative benefits from £6.3 million of funding from the Zero Emissions Vessel and Infrastructure (ZEVI) competition, which was set up as part of Innovate UK and the Department of Transport’s strategic plan to develop, deploy, and operate clean maritime solutions. Just 10 flagship UK projects were chosen to split more than £80 million in funding, with the aim of unlocking an industry-led transition to net zero.
As existing shoreside charging capabilities are severely limited, the project will also expand vessel charging infrastructure by installing both an onshore charging station (for overnight charging) and an offshore wind turbine based-charger. These solutions will enable direct E-CTV charging on location, greatly increasing the time and range that electric vessels can stay in operation without returning to port.
A prime example of the type of cross collaboration required to truly make waves in marine electrification, the multi-stakeholder project is being undertaken with partners Goodchild Marine Services, Artemis Technologies, and MJR Power & Automation, with key equipment suppliers such as Volvo Penta, Danfoss, and Corvus Energy.
As it currently stands, E-CTVs like e-Ginny have the capability to facilitate inspection and maintenance of wind farms up to 10 – 15 miles offshore, dependent on hull type, with e-foilers able to reach a distance of up to 25 miles. And that is just the beginning – with enabling technology such as offshore charging and the continued evolution of battery and propulsion systems, such vessels could be operating and servicing wind farms with zero-emissions over 100 miles from shore within 5 – 10 years.
The tide is turning towards electrification
As the offshore wind sector continues to expand and the greater need for inspection and maintenance is realised, closer attention must be paid to offering low carbon alternatives to impactfully drive down the carbon footprint of the industry. Otherwise, the industry risks undoing part of the terrific progress that wind energy is making in the global shift to a net-zero emissions energy system.
It is for this reason that the CTV and SOV industry need a serious rethink. Hydrogen and other green fuels certainly have their place in a low-carbon economy, but efficient electrification which harnesses the incredible power of modern batteries and cutting edge offshore and shoreside charging solutions is truly the future of a decarbonised offshore wind industry.
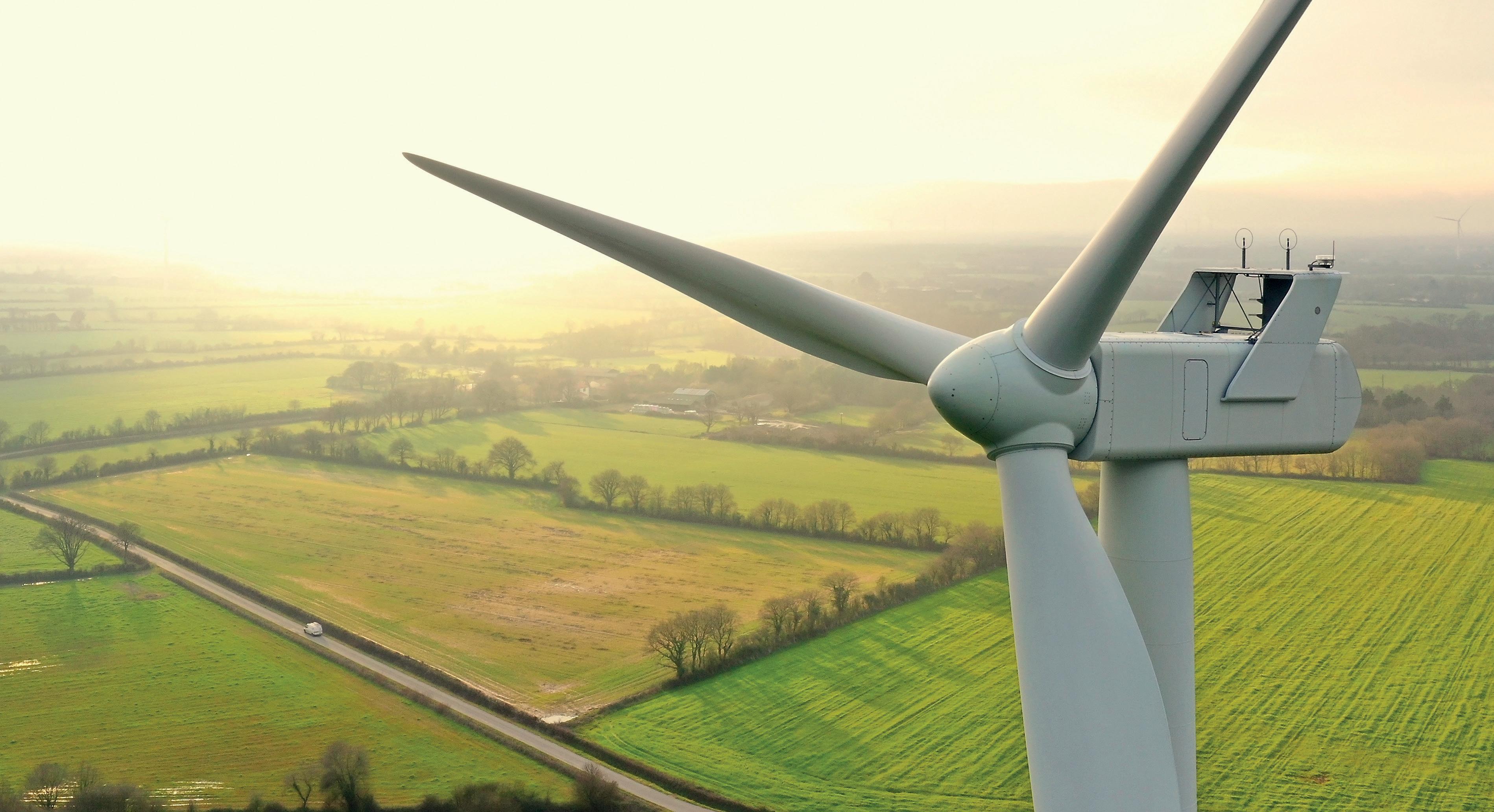
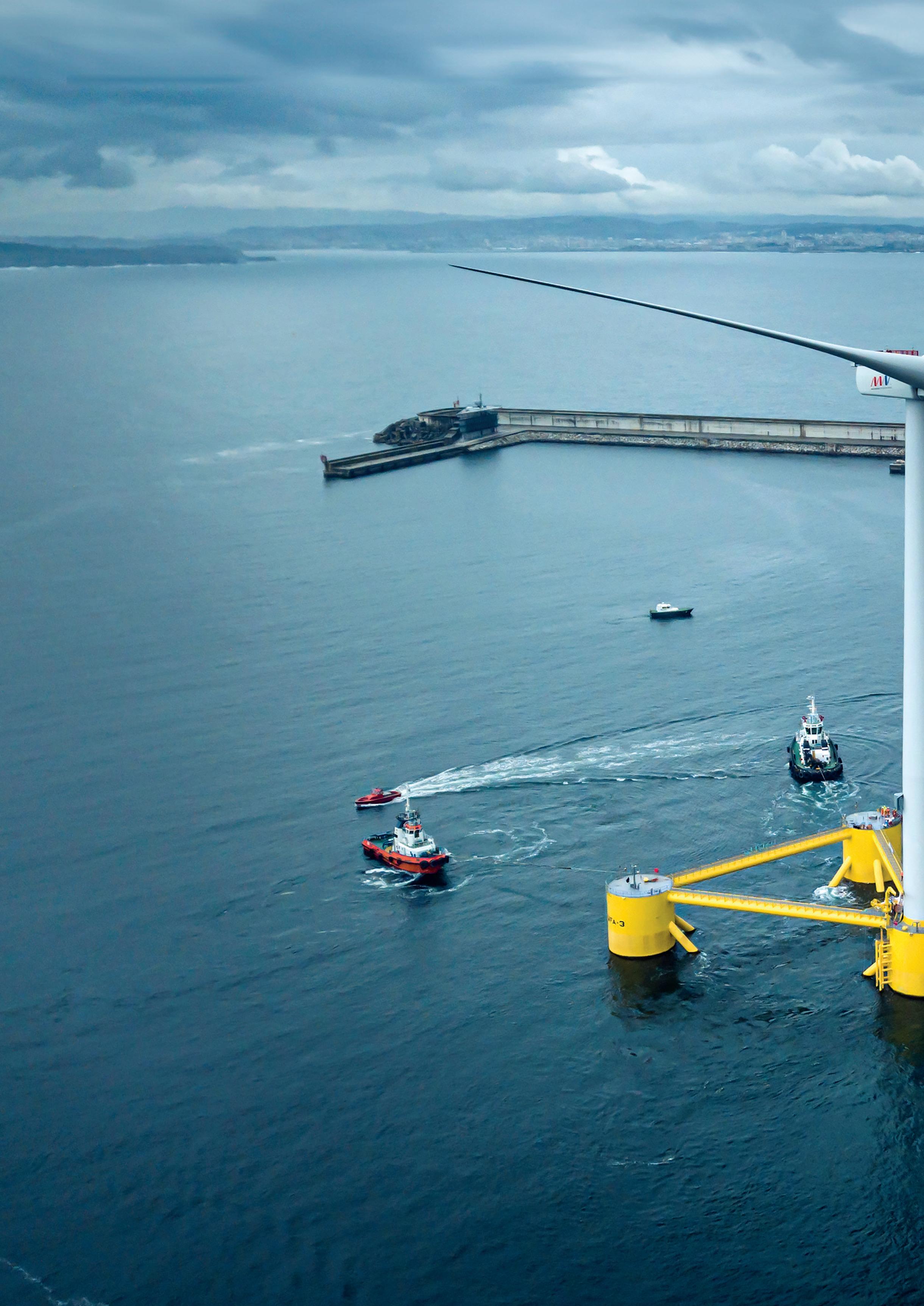
Floating wind energy operation is rapidly becoming a significant part of the offshore wind sector, but with global ambitions to deliver almost 10 GW of floating capacity by 2030, it will require the sector to focus much more on the speed at which it can develop projects and how to collaborate more effectively. Improved intelligence on the natural environment is key to success. A firmer grasp on the geo-data of a given site delivers confidence that a project is viable, but that is only possible if this work is carried out sufficiently early.
Gathering intelligence early
Brian Bell, Global Director Offshore Wind, Fugro, explores the often-overlooked development stage of offshore wind projects and how geo-data can be used to ensure success.
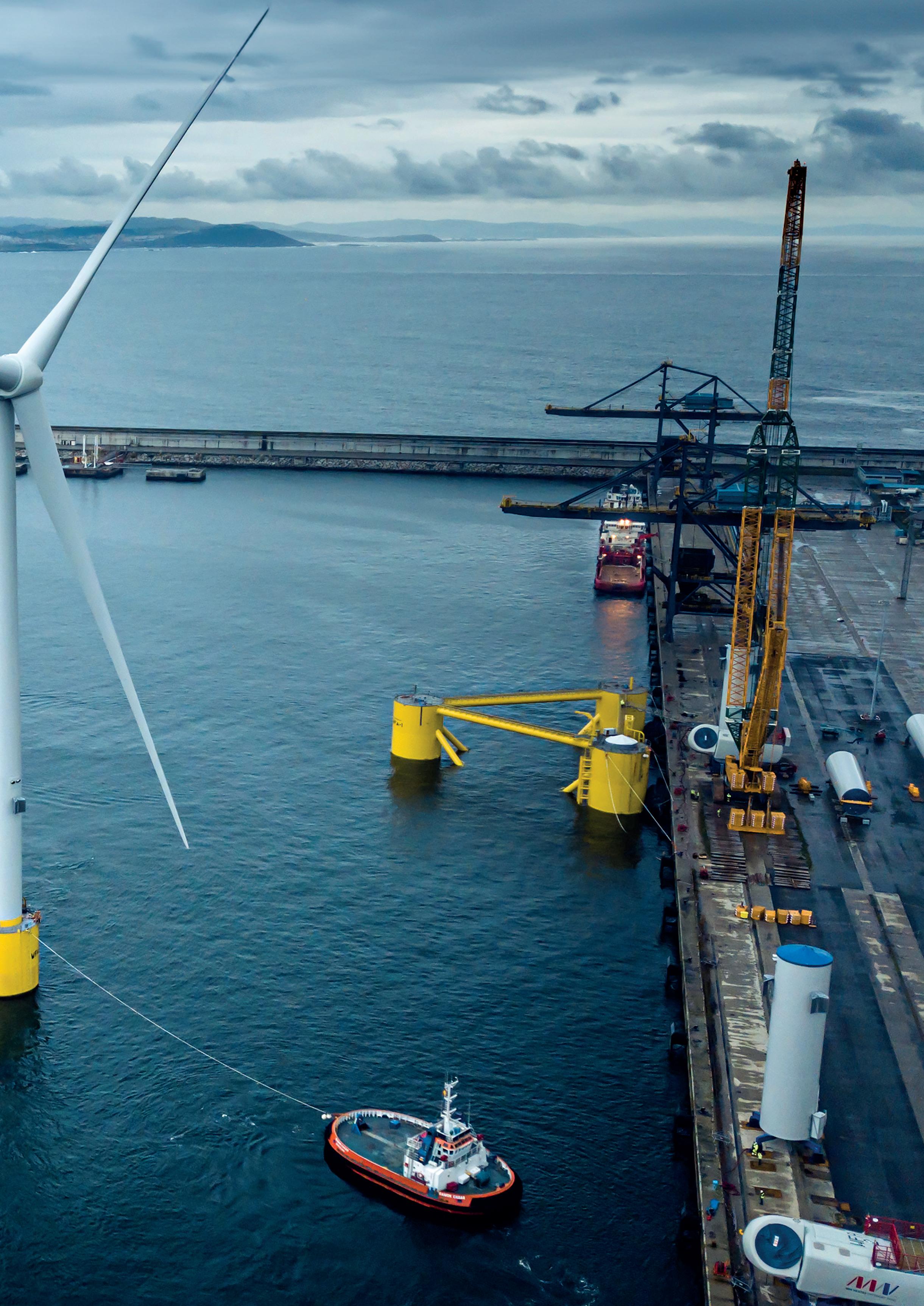
Figure 1 Installation of WindFloat Atlantic in Portugal, Photo courtesy of Principle Power. Artist: DOCK90.
There has never been a more exciting time to be working within the offshore wind industry. It is a sector that is rapidly maturing as more countries explore and embrace the potential of renewable energy whilst establishing regulatory regimes to enable its success.
As with any maturing industry, the passage of time has allowed more efficient and consistent ways of working to develop, accelerating the development timeline and reducing overall cost. Relationships are also changing as stakeholders work together more closely; suppliers have been evolving their capabilities and capacities to support the changing needs of developers and operators. Having supported offshore wind since the 1990s, companies like Fugro have learned a lot about what it takes to optimise delivery.
An added imperative to develop more collaborative approaches stems from global ambitions to deliver almost 10 GW of floating offshore wind capacity by 2030, compared to less than 1 GW today. With the levelized cost of energy (LCOE) for floating wind being double that of bottom fixed (US$200/MWh vs US$80 – US$100/MWh), collaboration will help the sector to standardise and scale engineering solutions for floaters and moorings, accelerate development timelines to reach first power earlier, and develop more cost-effective operations and maintenance regimes.
Understanding the surroundings
To support these efforts, it is essential to have a thorough understanding of the natural environment in which a floating wind farm will be developed. As floating sites move into deeper water further from shore, they increasingly encounter different site conditions to their bottom-fixed counterparts. Having a firm grasp of these conditions allows engineering teams to design robust but cost-effective solutions, which in turn provides
confidence to developers and investors that a project is technically and financially viable. This confidence is only achievable, however, if the work needed to characterise site conditions is performed early enough in the development process.
Site characterisation
Site characterisation typically includes the collection and study of a wide assortment of geo-data types, each one providing valuable insights into the surrounding environment – above, below, and on the seabed. Metocean data helps to understand the effects of wind, waves and currents, geotechnical and geophysical data assesses seabed composition and behaviour, and environmental data describes biodiversity across a wind farm site. These geo-datasets – and more – are combined in increasingly innovative ways to help developers refine a wind farm’s design, optimise a site’s performance, and mitigate its impact.
To keep timeframes and costs manageable, site characterisation is becoming more harmonised and repeatable, with increased cross-industry collaboration to define standard specifications and methodologies that are sufficiently flexible for different environments. There is also an increasing awareness of the need to optimise delivery by combining multiple packages into larger and more efficient workflows, reducing the time and cost of procuring multiple services to reach a certain milestone. This does not mean that smaller suppliers risk losing out or that site characterisation costs are rising; such an approach reduces inefficiencies that could adversely affect project success.
Fixed vs floating wind
The differences between fixed and floating wind farms require slightly different approaches to site characterisation. Floating sites often require geo-data to cover a larger surface area, but their foundation needs may concentrate on shallower soil depths compared to bottom-fixed sites. Floating designers may also have a greater interest in understanding the effects of sea state and currents when considering floater designs and dynamic cable arrays, in contrast to bottom-fixed sites where cables are either laying on or buried beneath the seabed.
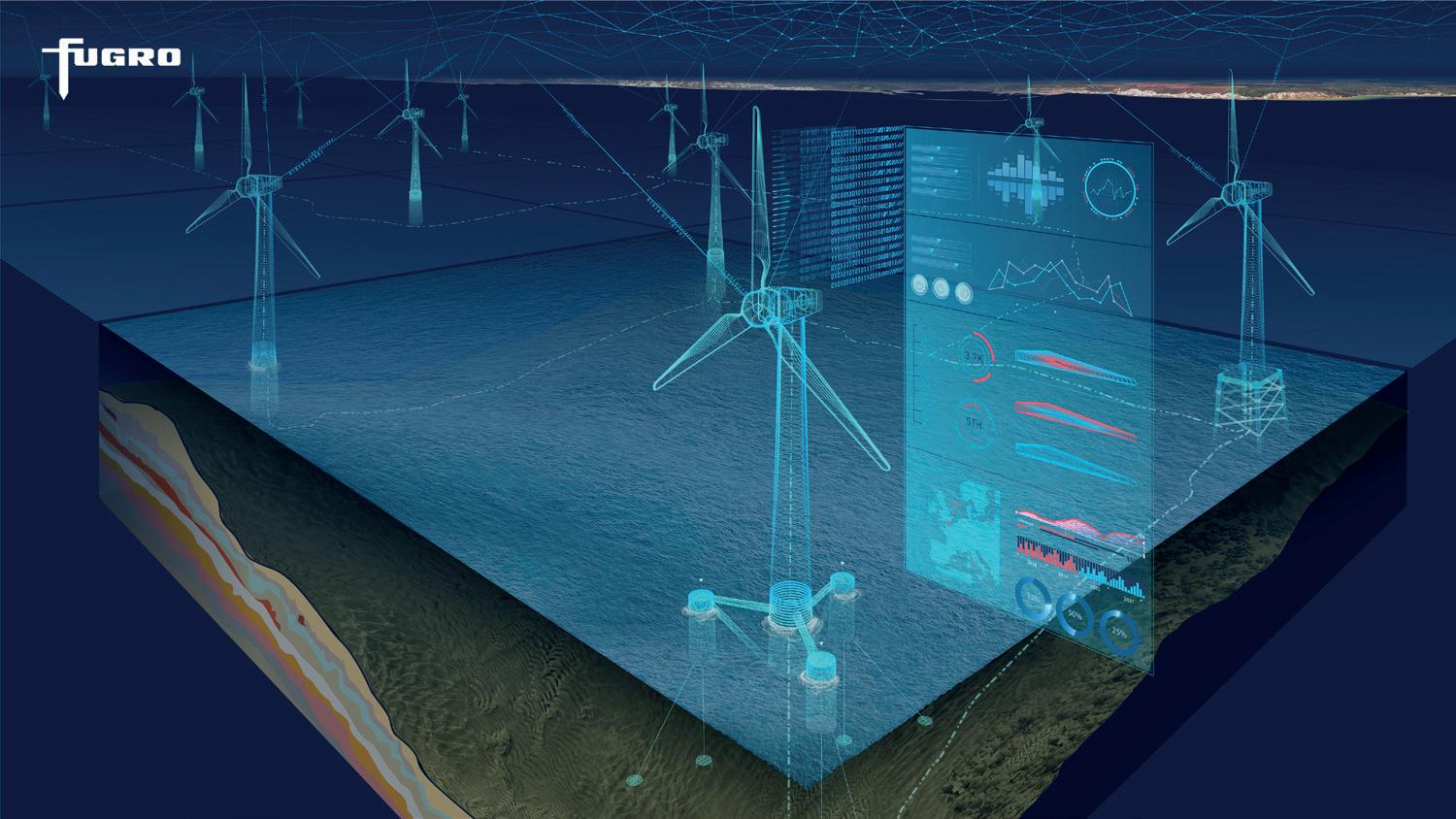
Floating structures must remain sufficiently buoyant to support the turbine infrastructure whilst minimising the amount of motion induced
Figure 2 . Technology advancements allow for the creation of digital twins which can monitor the condition and performance of individual wind farm components in real time.
by wind and waves. There are additional considerations for operations and maintenance as a result – engineers therefore examine the repeated or cyclic effects of motion over time, including how moorings affect the surrounding seabed as a floater moves and whether components undergo accelerated wear due to dynamic forces.
The impact of extreme environmental conditions is also increasingly assessed, such as the level of seismic activity across a site and the prevalence of hurricanes or typhoons. These insights often require additional datasets which need collecting and integrating into engineering models for analysis and component design.
Factors to consider
As floating wind expands to more markets, many of which will be totally new to the technology, there will be additional factors to consider. Electrical grids are needed to connect the growing number of sites and transmit their power back to shore – and these will need to be extended. It is widely recognised by the offshore wind sector that upgrading grid infrastructure is vital to provide the futureproofing that the market needs to mature – the technical, logistical, financial, and ecological impact of doing must be understood to enable success.
Furthermore, the increasing scale and prevalence of offshore wind farms often result in them overlapping with other marine spatial uses such as platforms and pipelines, telecoms cables, transport and shipping routes, ports and harbours, fishing grounds, conservation areas, and military zones. Site characterisation is a valuable means of assessing the potential impact of new wind farms so they can co-exist with these other uses without conflict or concern.
The development process can be accelerated and de-risked by employing the expertise of those who can both acquire and analyse this geo-data, especially as demand grows to deliver faster results. Multi-disciplinary teams of experts can integrate geophysical, geotechnical, and environmental datasets into virtual models or digital twins of a site, which can be used to evaluate layout concepts or mature engineering designs. By helping developers better understand the natural environment in which their wind farms will operate, risk can be assessed and mitigated, decisions can be made sooner, and the development process can be optimised – positively impacting the LCOE and feasibility of floating wind.
Conclusion
The floating wind sector is still very young compared to other markets. To install the hundreds of turbines and thousands of moorings that are needed to achieve widespread 2030 floating ambitions the sector will need scalable and cost-effective engineering solutions, which in turn will need fast and reliable geo-data insights. It will also need collaborative efforts, shared goals, and a collective desire to make floating wind power generation a success.
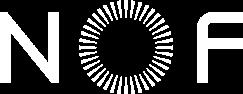
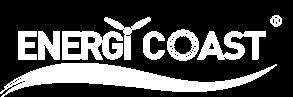

6 th - 7 th November 2024 Beacon
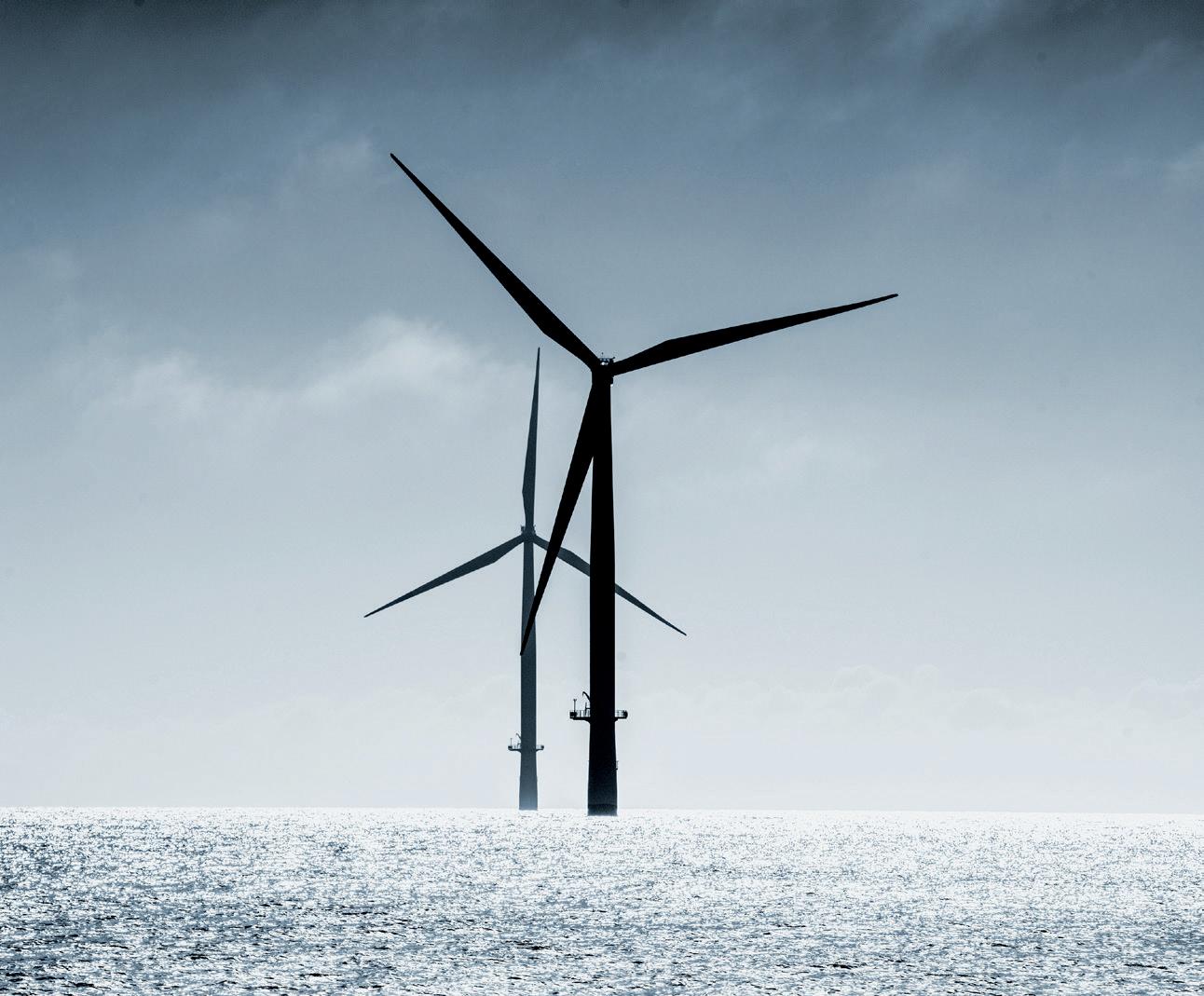
Stefano Santoni, Davi, Italy, examines the need for offshore and onshore wind turbine components to meet increasing demand in the wake of the growth of wind energy.
ind energy, hailed as a cornerstone of the future energy matrix, has been experiencing substantial global growth. By 2030, projections indicate a generation of 2 TW from onshore and offshore wind sources, with offshore wind alone expected to contribute 268 GW. This rapid expansion underscores the critical need for innovative technological solutions that ensure efficiency, reliability, and sustainability in wind energy production. Davi aims to be at the forefront of this transformative era, offering unparalleled solutions tailored for the wind energy sector.
Strategic innovations
Innovation serves as the core pillar of the company’s operations, shaping every product and strategy it deploys. Its presence in over 70% of the plate rolls market within the wind energy sector not only speaks to its expertise, but also to the trust that the industry has placed in its technology. This trust is built on a commitment to rigorous testing and validation by the top players in the wind energy sector, who depend on effective machines to meet their precise manufacturing needs. The flexibility, adaptability, and precision of industry solutions are critically important in producing wind towers and foundations that must meet stringent standards for quality and durability.
Specialisation in this market should be driven by a dedicated R&D team that is committed to pushing the boundaries of plate rolling technology. Companies should focus on continuous innovation, not as a goal, but as a process – a journey of improvement and adaptation to new challenges and opportunities in the wind energy sector. By investing heavily in research and development, companies ensure that they not only keep pace with, but also lead the way in,
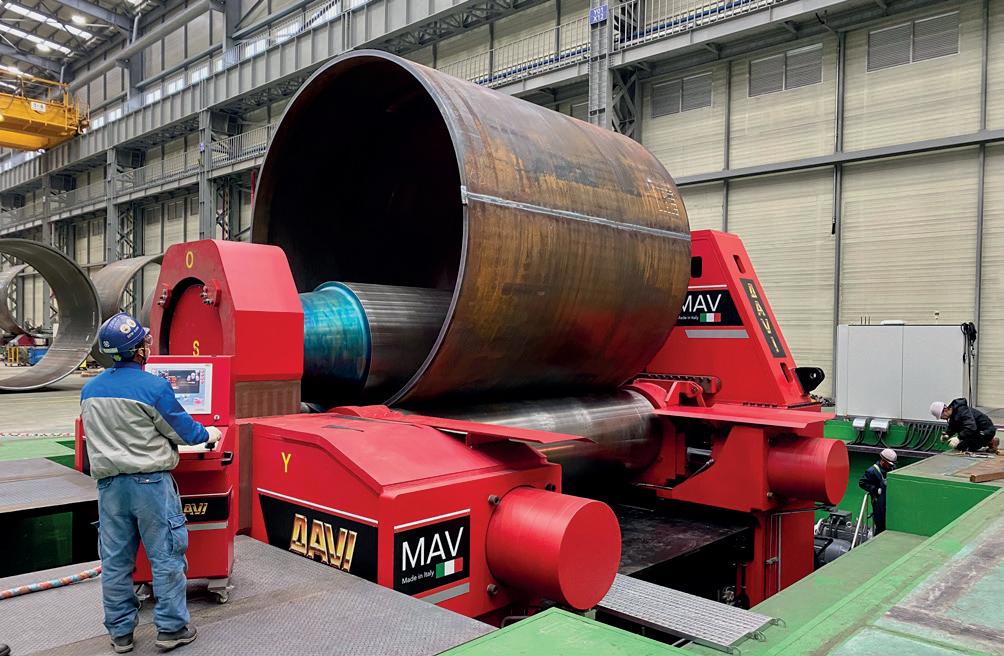
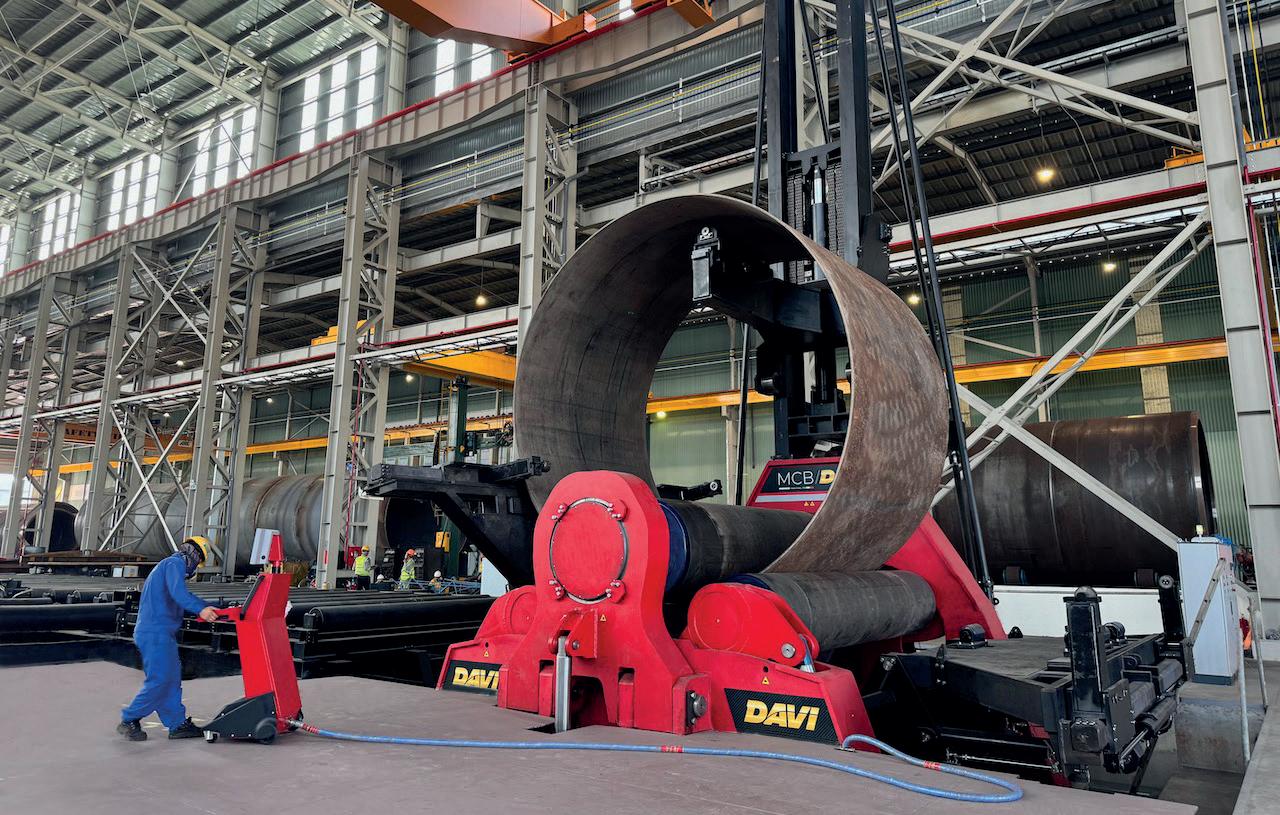
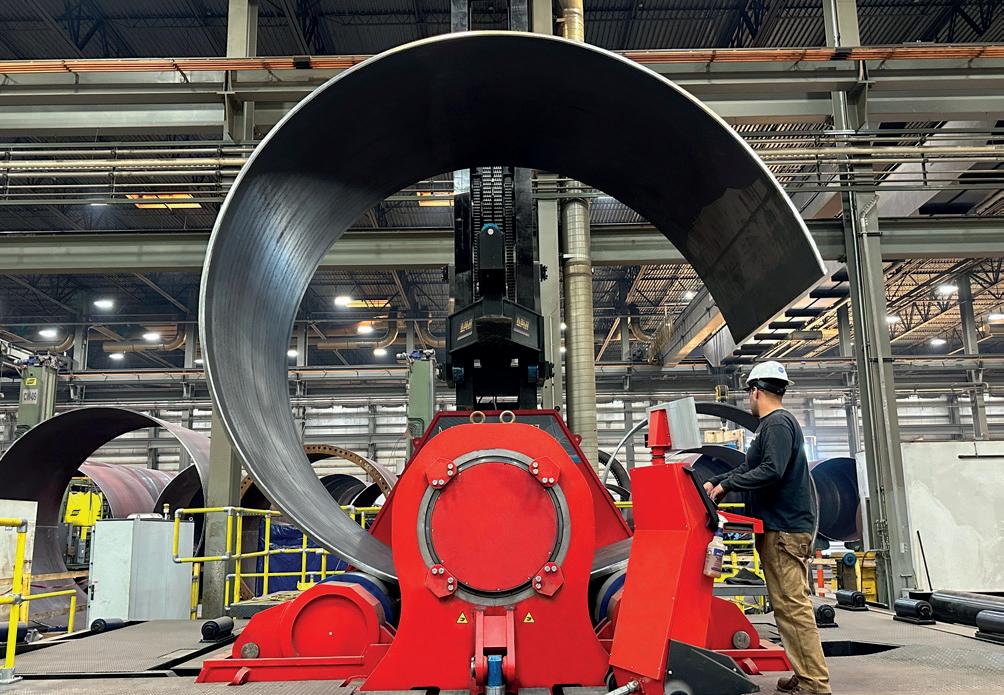
technological advancements. This proactive approach allows companies to develop tailor-made solutions that anticipate and address the evolving needs of the industry.
Each innovation should be the result of collaborative efforts among skilled engineers, who draw on vast knowledge and experience to devise solutions that maximise productivity and efficiency for industry clients. By pursuing these advancements, companies work to be at the forefront of the wind energy industry, consistently delivering products that redefine what is possible in the production of wind towers and foundations. These efforts ensure that as the challenges of wind energy production evolve, so too do the company’s solutions, maintaining its position as a leader in the industry and a trusted partner in the global pursuit of renewable energy.
Offshore and onshore towers production
Davi’s technology plays a pivotal role in both offshore and onshore wind tower production. Implementing advanced machinery and systems streamline manufacturing processes, significantly enhancing production efficiency and product quality. For offshore towers, which can soar up to 120 m and are designed to withstand harsh marine environments, companies should ensure that each machine component meets exacting specifications for durability and stability. Onshore towers, benefiting from the same technology, are optimised for the specific challenges presented by terrestrial environments.
Offshore foundations production
Regarding offshore foundations, there are solutions that are meticulously designed to address the unique challenges posed by marine environments. Technology is critical in the construction of offshore wind foundations, which requires unparalleled precision and robustness due to the harsh conditions of the sea. Davi’s own plate rolling machines ensure that the steel plates used in the construction of these foundations are rolled accurately and efficiently, contributing to the structural integrity and longevity of offshore wind turbines.
In particular, MCB and MAV lines are equipped to handle a variety of plate sizes and thicknesses, which are essential for constructing sturdy bases that can withstand oceanic pressures. These machines are engineered for high performance under demanding conditions, featuring enhanced control systems that allow for precise manipulation of large and thick plates. Such capabilities ensure that each component of the foundation is manufactured to the highest standards, minimising the risk of errors that could compromise the safety and effectiveness of offshore wind installations.
These solutions underscore the company’s commitment to advancing the field of wind energy through technological innovation tailored specifically for the complex requirements of offshore wind foundation production. The company continuously refines technology to meet the specific demands of this challenging environment.
Advancements in floating foundation technologies
Floating foundations represent a rapidly growing segment of the offshore wind industry, particularly important in deep-water
Figure 1 . MAV Plate Roll in action: showcasing the versatility of the three-roll, variable-axis model.
Figure 2 The four-roll model demonstrates its capabilities with essential accessories for the wind energy industry.
Figure 3 . Crafting a cylinder with the MCB Plate Roll.
environments where traditional fixed-bottom foundations are not viable. Davi has been deeply involved in developing solutions for semi-submersible and tension-leg platforms, which are essential for stabilising turbines in deep water. Different innovative approaches in this area not only enhance the feasibility and cost-efficiency of these projects, but also push forward the limits of where wind farms can be realistically developed.
Total cost of ownership and long-term sustainability
A dedication to sustainability must be deeply integrated into a company’s business philosophy, particularly evident in its emphasis on total cost of ownership (TCO). It should be understood that the value of equipment in the wind energy sector extends far beyond the initial purchase price. Hence, a good TCO approach encompasses the entire lifecycle of the machinery, from acquisition and operational costs to maintenance and eventual decommissioning. By evaluating these comprehensive costs, a company can ensure that its solutions not only meet the immediate financial capacities of its clients, but also align with their long-term financial goals.
Moreover, by focusing on the longevity and reliability of the machinery, it can help clients minimise unexpected downtime and costly repairs, which otherwise can significantly inflate the TCO. The use of advanced engineering techniques and quality materials ensure that equipment remains operational over extended periods, thereby spreading the cost of investment over a longer timeframe and enhancing the return on investment for clients.
In addition, a company should actively engage in improving the serviceability of its machines. Its support services should include preventive maintenance schedules and quick-response troubleshooting, which further help reduce the likelihood of operational disruptions and maintain consistent production levels. This proactive support not only extends the life of the equipment but also ensures that it operates within the optimal parameters, thus safeguarding the environmental benefits of using this technology.
Through practices such as these, companies like Davi reinforce the economic pillar of sustainability in wind energy projects. By ensuring that machines are cost-effective over their entire lifespan, a company can support its clients in achieving its sustainability goals. This commitment not only enhances the operational success of its clients but also supports the broader transition towards a more sustainable and resilient energy landscape.
Conclusion
As the wind energy sector continues to evolve, Davi’s persistent goal of shaping its trajectory remains evident. Through continuous innovation, commitment to customer support, and a focus on enhancing the efficiency and sustainability of wind energy production, companies cannot just participate in the energy transition but actively lead it. Solutions, characterised by precision, innovation, and efficiency, ensure that wind energy remains a key player in the global pursuit of renewable energy solutions, promising a cleaner, more sustainable future for all.
Global Hydrogen Review Online
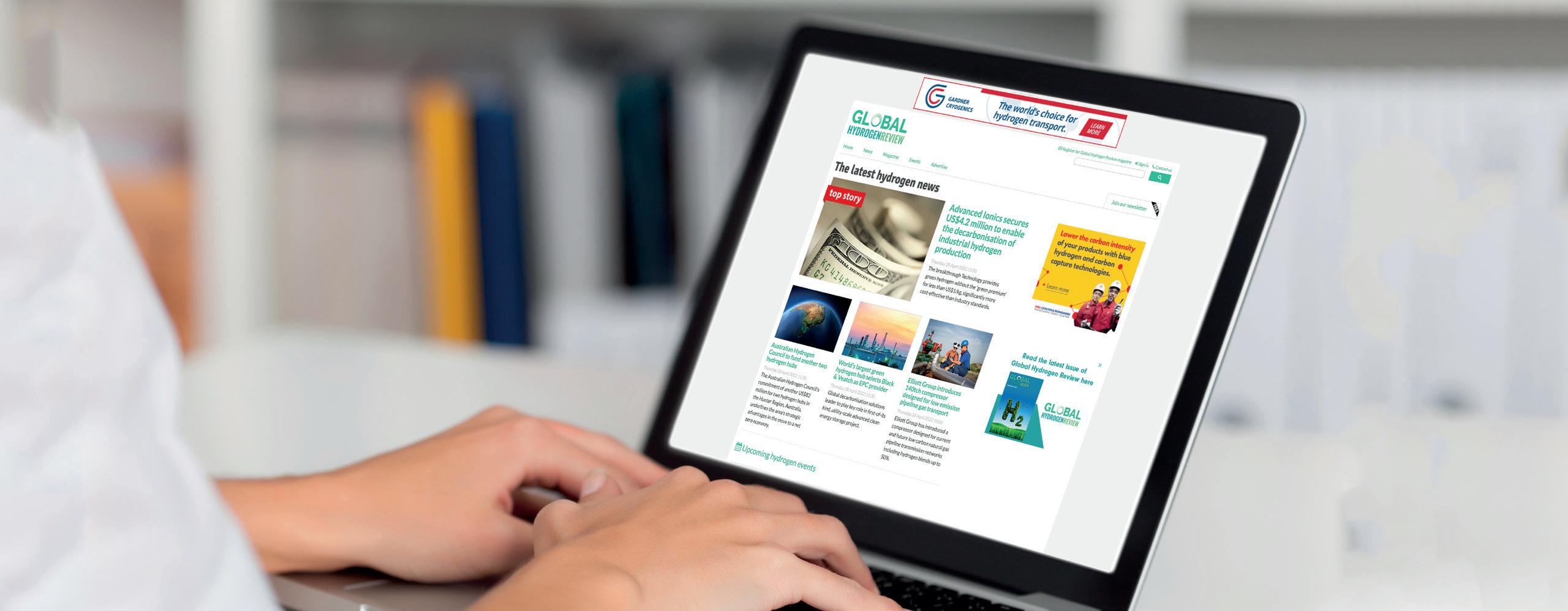
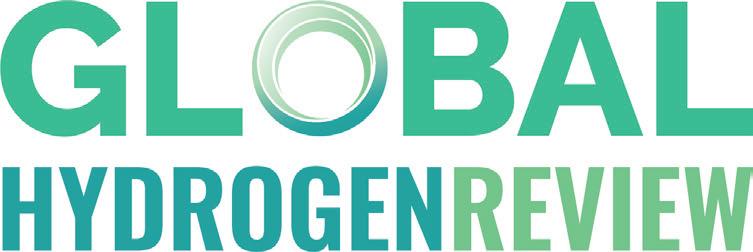
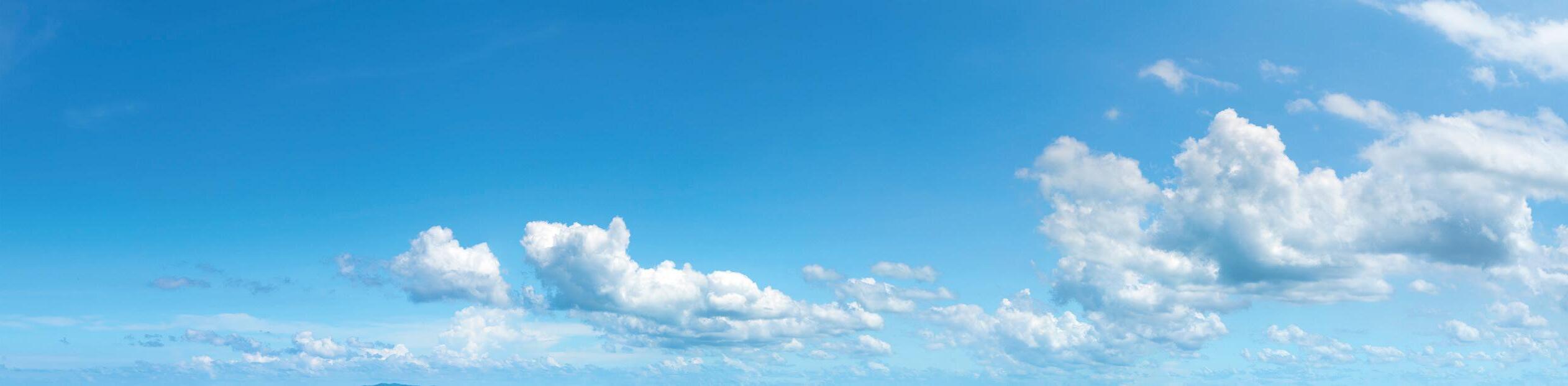
GLOBAL NEWS
Norton Rose Fulbright advises Société Générale on green financing of WTIVs
Norton Rose Fulbright, has advised Société Générale as Mandated Lead Arranger and Agent, along with a syndicate of banks, in relation to two green loan facilities for Cadeler A/S totalling approximately €520 million for the financing of two state-of-the-art newbuild wind turbine installation vessels under construction in South Korea.
The syndicate of banks also included Crédit Agricole CIB, CIC New York, and Korea Development Bank.
The facilities were partly ECA-backed by Export Finance Norway (Eksfin) and the Export and Investment Fund of Denmark (EIFO) and included a direct loan from Korea Eximbank (KEXIM). Both facilities were sustainability-linked and included approximately €100 million of ancillary guarantee facilities to assist Cadeler with the vessels’ operational activities.
This deal represents the third successful green financing for Cadeler that Norton Rose Fulbright has advised on within the last 12 months.
The Norton Rose Fulbright global asset finance team advising on this deal was led by the firm’s Co-Head of Asset Finance, Yianni Cheilas, with support from Senior Associates, Nicholas Papadopoulos and Alexis Remoundos, and Associate, Jennifer Carr. The team was also supported by Finance Partner, Neha Khosla, Counsel, James Tong, and Associate, Jack Zheng, on related finance aspects. New York-based Partner, Brian Devine, advised on Marshall Islands law matters.
Mammoet and Samyang Marine Group announce strategic partnership for South Korea’s offshore wind sector
Mammoet and Samyang Marine Group have entered into a new partnership to establish offshore service port (OSP) facilities to serve projects across sectors in South Korea, with a primary focus on upcoming offshore wind projects. The partnership will integrate full-spectrum terminal management, including handling, staging, marshalling, and stevedoring services, with heavy lifting and installation capabilities. The OSPs, located in the ports of Busan and Masan, will cater to projects in South Korea and the broader Asia-Pacific region.
The initiative arises from the recognition that South Korea’s expanding offshore wind market requires not just infrastructure, but also specialised logistics, handling, construction, and installation services that are critical to the offshore wind sector’s success. Recognising this, the partnership aims to address these needs comprehensively.
The partnership responds to the urgent need for an enhanced offshore wind supply chain and services to meet the ambitious targets outlined in South Korea’s Renewable Energy 3020 implementation plan, which includes 14.3 GW of offshore wind by 2030. Crucial to achieving this target is the readiness of the supply chain, responsible for delivering the components and services vital for the construction of offshore wind farms.
Zhong Neng offshore wind farm inaugurated
Copenhagen Infrastructure Partners (CIP) has celebrated the completion of construction of the Zhong Neng offshore wind farm, a joint venture between CIP through its fund Copenhagen Infrastructure IV (CI IV) and China Steel Corp. (CSC).
Zhong Neng, located off the coast of Changhua County in Taiwan, is the first offshore wind farm in the country to be completed ahead of schedule and meets the highest localisation requirements in the history of Taiwan’s offshore wind power sector.
The project was constructed by a team led by
Copenhagen Offshore Partners, CIP’s exclusive offshore wind development partner, and the local Copenhagen Infrastructure Service Company, the global service provider to CIP.
Zhong Neng received local content plan approval from the Taiwan government in November 2019, and the first turbines were installed in May 2024. Full grid connection is expected by year-end, and, once, fully commercially operational, Zhong Neng will provide clean energy to approximately 300 000 households and present a carbon reduction potential of approximately 550 000 tpy.
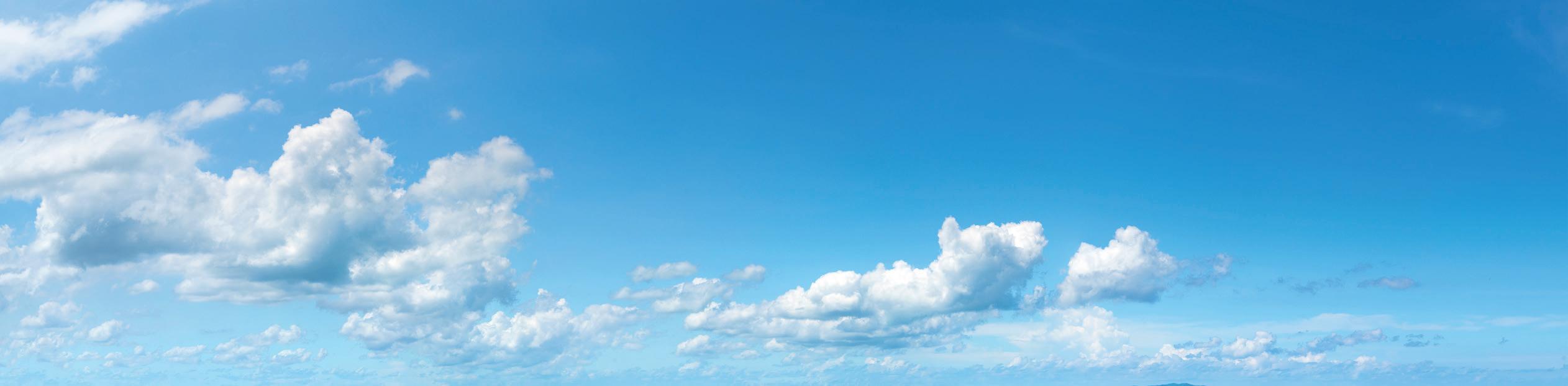
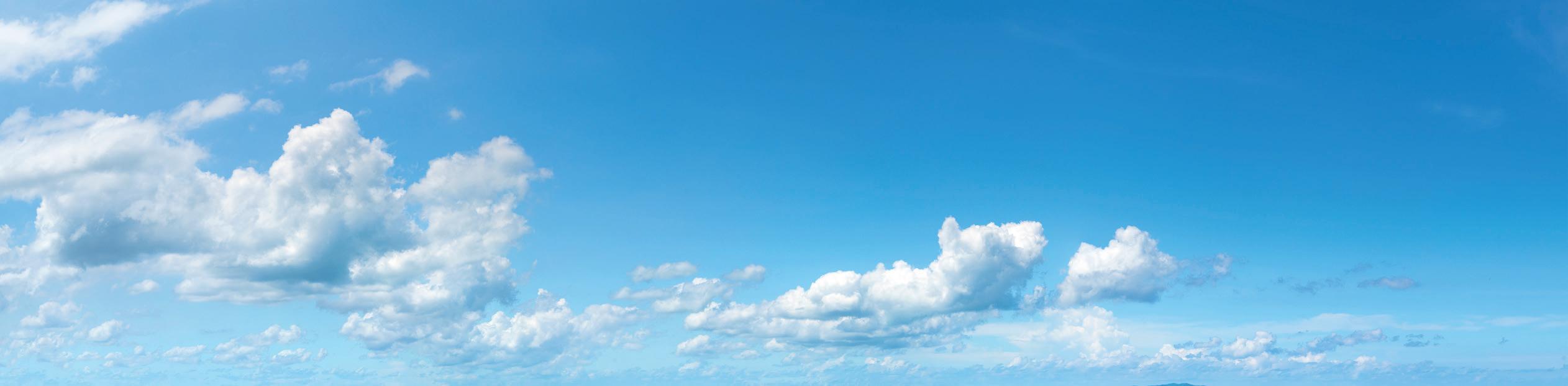
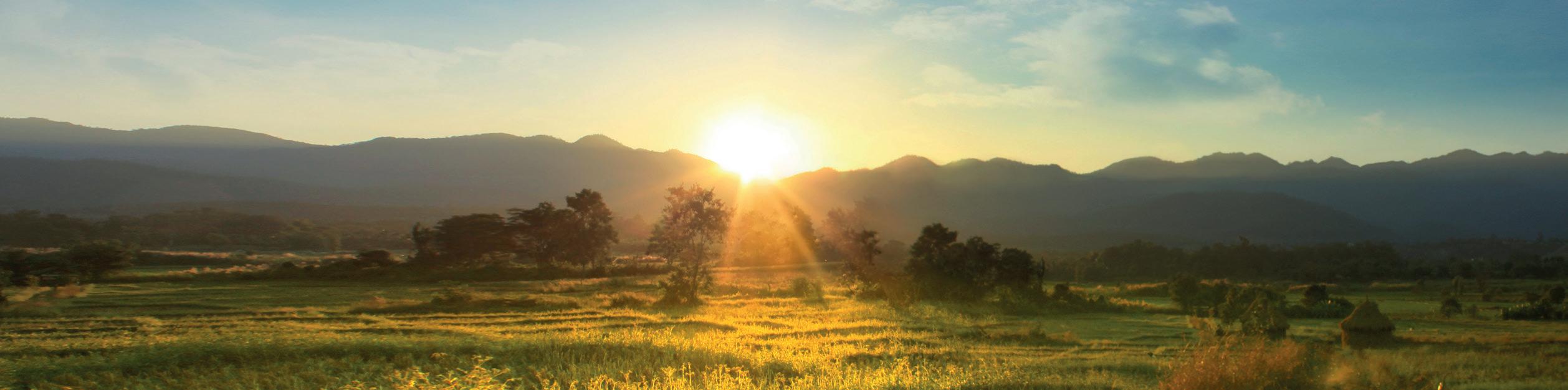
GLOBAL NEWS
Cero Generation’s solar PV project in Greece goes live
Cero Generation has announced that Delfini, its 100 MW solar PV project in Greece, has reached commercial operation. The project will generate 157 GWh of electricity annually, equivalent to powering 58 140 homes and avoiding 65 300 t of CO2e emissions.
The project has been built on mountainous terrain and connects a 2.5 km 33 kV medium voltage (MV) line to a 33/150 kV high voltage (HV) substation (110 MVA step-up transformer). It includes a 10 km network of overhead lines, consisting of 29 overhead line towers connecting the project into the Electricity Transmission System operated by IPTO (ADMIE).
The project, which was financed by lenders Piraeus Bank and Eurobank, also brings more firsts for Cero’s growing operational portfolio, demonstrating its focus on innovation. The project is underpinned by a long-term private power purchase agreement (PPA) with Axpo, making it the first such project in the country not to leverage Greek government subsidies on electricity costs. Delfini is also the first renewable project in Greece to have benefited from the Next Generation EU Recovery and Resilience Facility.
The announcement forms part of the growing solar PV capacity Cero has under development in Greece, supporting the country’s goals to cut carbon emissions by 40% by 2030.
The EPC contractor for the project was Ameresco SUNEL Energy S.A., a joint company established in Greece.
Diary dates
Solar & Storage Live Birmingham 24 – 26 September 2024 Birmingham, UK www.terrapinn.com/exhibition/solar-storage-live
WindEnergy Hamburg 24 – 27 September 2024 Hamburg, Germany www.windenergyhamburg.com
Offshore Wind North East (OWNE) 2024 06 – 07 November 2024 Sunderland, UK www.nof.co.uk/events/ offshore-wind-north-east-owne-2024
Hambach opencast mine steps towards renewable energy
The municipalities at the Hambach opencast mine are joining RWE in setting the course for the energy transition and investing in the expansion of renewables.
Neuland Hambach GmbH, which represents the interests of the surrounding municipalities of Elsdorf, Jülich, Kerpen, Merzenich, Niederzier, and Titz, has combined forces with RWE to establish the project company RWE Neuland Erneuerbare Energien GmbH & Co. KG.
The municipal authorities will hold 49% of the shares in the RWE Neuland solar farms, which went onto the grid at the Hambach opencast mine in recent months. They also have the option to acquire 49% of the shares in all future renewable energy projects at the Hambach opencast mine.
In the Hambach opencast mine, a total of 87 000 modules are currently generating about 50 million kWhr/y of solar electricity in an area the size of about 60 football fields (approximately 45 ha.). Together, the RWE Neuland Solarpark and the RWE Neuland 1 Solarpark plants deliver peak power of 47.2 MW, which represents enough green electricity to supply about 14 500 households per year. A battery storage system with a capacity of 8 MWh has also been installed in order to align the electricity feed-in even better with actual requirements. Just in time for the establishment of the new company, the second extension phase of the RWE Neuland 1 Solarpark was put into operation.
Wood Mackenzie Hydrogen Conference 06 – 07 November 2024
London, UK
www.woodmac.com/events/hydrogen-conference
Solar & Storage Live Barcelona 13 – 14 November 2024
Barcelona, Spain www.terrapinn.com/exhibition/solar-storage-live-barcelona
Global Hydrogen Conference 2024 20 November 2024 Online www.accelevents.com/e/ghc2024
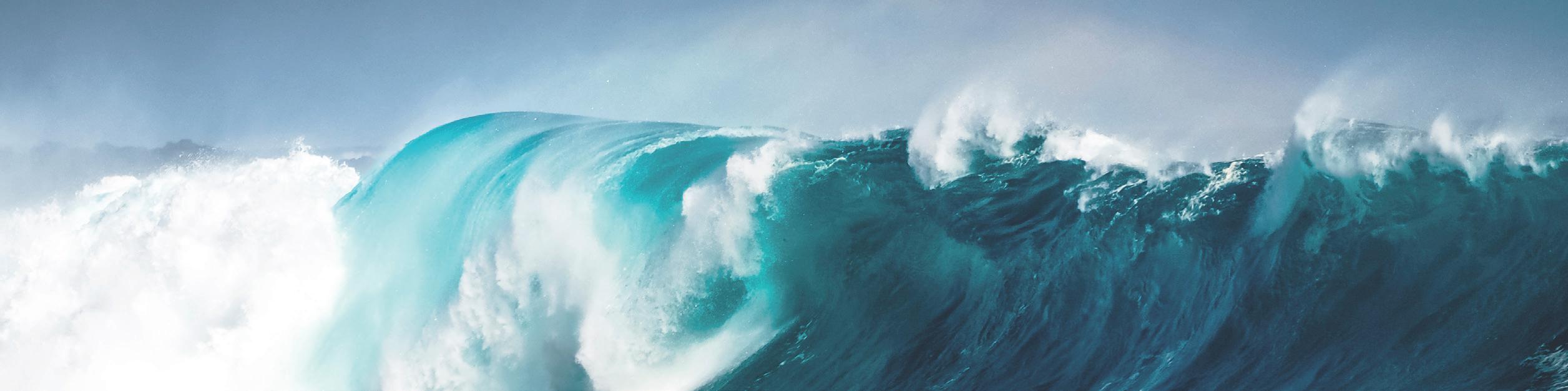
GLOBAL NEWS
SAE secures CfD for MyGen site
SAE has secured a Contract for Difference (CfD) in the latest allocation round (AR) for the MeyGen site. These CfD contracts, which guarantee £172/MWh for 15 years from 31 March 2029, the target commissioning date, will allow SAE to increase the size of the MeyGen 2 development by approximately 9 MW.
On 8 September 2023, SAE secured contracts for 50 MW in AR4 and AR5, and this further success in AR6 will bring the total project under development to 59 MW.
This next phase is in addition to the 6 MW already operational at the site. MeyGen has so far produced 66 GWh of energy, more than all other tidal stream sites in the world combined.
To deliver the 59 MW project, SAE is in advanced discussions with global manufacturing and engineering firms. These non-binding discussions are progressing well, and SAE will provide further updates as and when appropriate.
Wave energy project receives green light from EU
A€19.6 million partnership project, which aims to be the stepping stone towards large scale wave energy commercialisation, has received formal go-ahead from the EU.
WEDUSEA is a collaboration between 14 partners from across the UK, Ireland, France, Germany, and Spain. It is co-ordinated by OceanEnergy and co-funded by the EU Horizon Europe Programme and Innovate UK, the UK’s innovation agency.
The green light has now been received from the EU and the project can proceed to its next stage.
The WEDUSEA project will demonstrate a grid connected 1 MW OE35 floating wave energy converter at the European Marine Energy Centre (EMEC) wave energy test site at Billia Croo in Orkney, Scotland. A rigorous technical and environmental demonstration will happen over a two-year period in Atlantic wave conditions.
Floating on the ocean’s surface, the device incorporates a trapped air volume, with the lower part open to the sea. Wave pressures at the submerged opening cause the water to oscillate and drive the trapped air through a turbine to generate electricity. Electricity generated will be exported to the UK grid via EMEC’s subsea cables.
The wave converter build starts in 2H24 and the demonstration at EMEC is expected to begin in June 2025.
ONDEP project secures €19 million funding to deploy WaveRoller Array
The Ondas de Peniche (ONDEP) project has been awarded €19 million from the EU’s Horizon Europe funding programme to deploy a 2 MW wave energy array featuring four WaveRoller wave energy converters.
The ONDEP project will commence in October 2024 and last for 5.5 years, encompassing the full spectrum of project activities — from design and manufacturing to testing, deployment, and operation. Set in the surfing hub of Peniche, Portugal, the pilot wave farm will be installed and connected to the grid and will continue generating electricity for an additional eight years after the project’s official end.
ONDEP’s mission over the next 5.5 years is to address the technical challenges of future large scale wave farms, ensuring the technology’s reliability and scalability. The project will also establish a comprehensive, end-to-end European supply chain to support the deployment of gigawatt scale wave energy across Europe and beyond.
Co-ordinated by Queen’s University Belfast, the project includes 14 partners from across Europe, including leading companies and research institutions.
THE RENEWABLES REWIND
> Anaergia wins contract for Korean biogas facilit y
> Scotland approves Smeaton BESS
> Fervo receives loan from X-Caliber Rural Capital af filiate for Utah geothermal project
> Q ENERGY raises over €50 million to finance Europe’s biggest floating solar project
Follow our website and social media pages for more updates, industry news, and technical articles. www.energyglobal.com
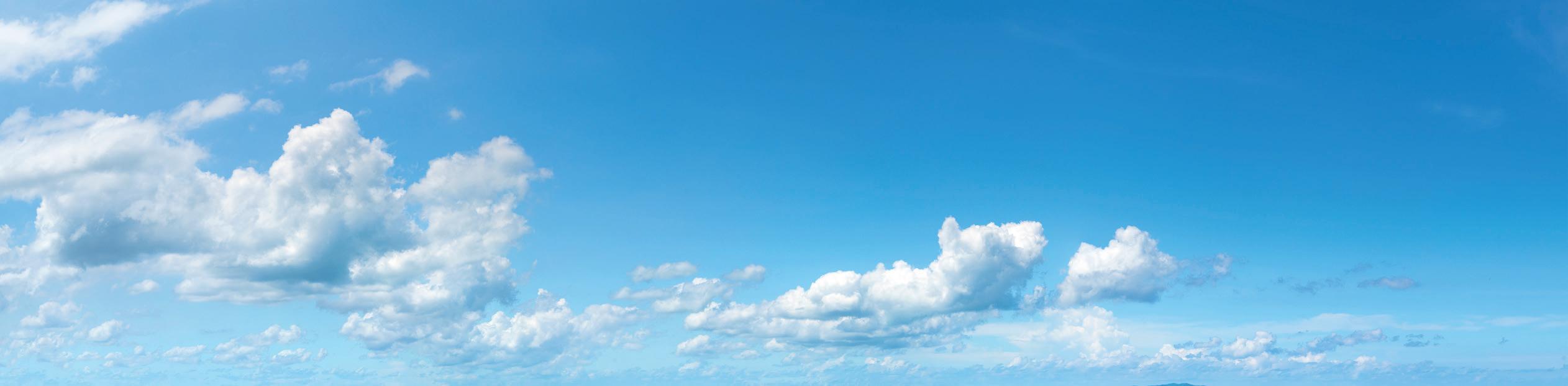
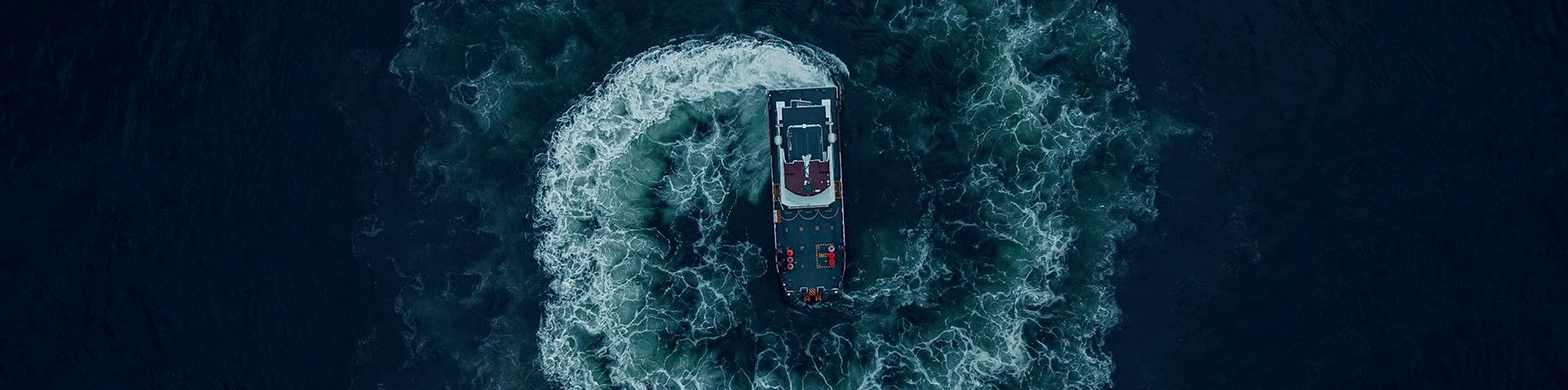
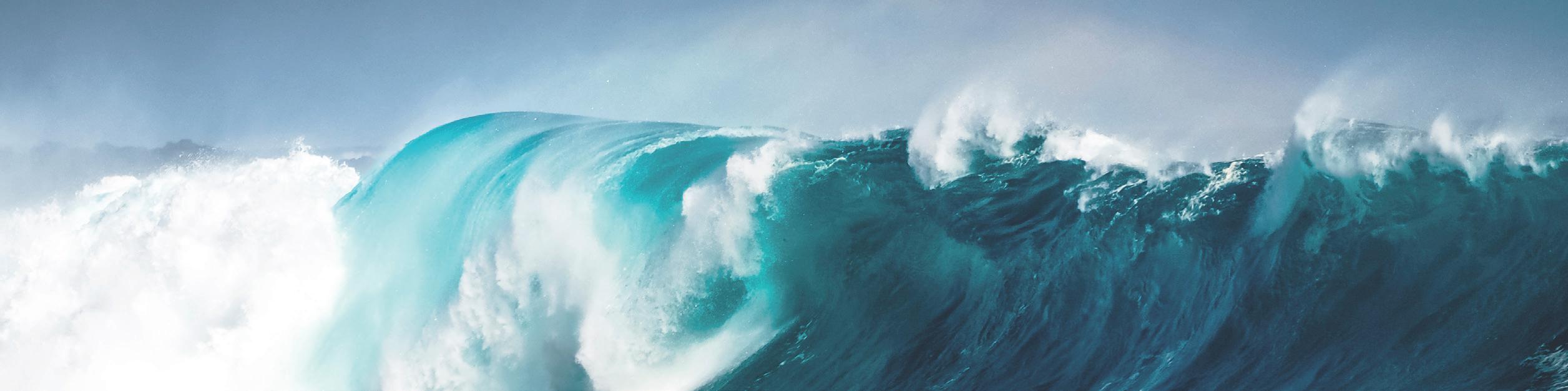
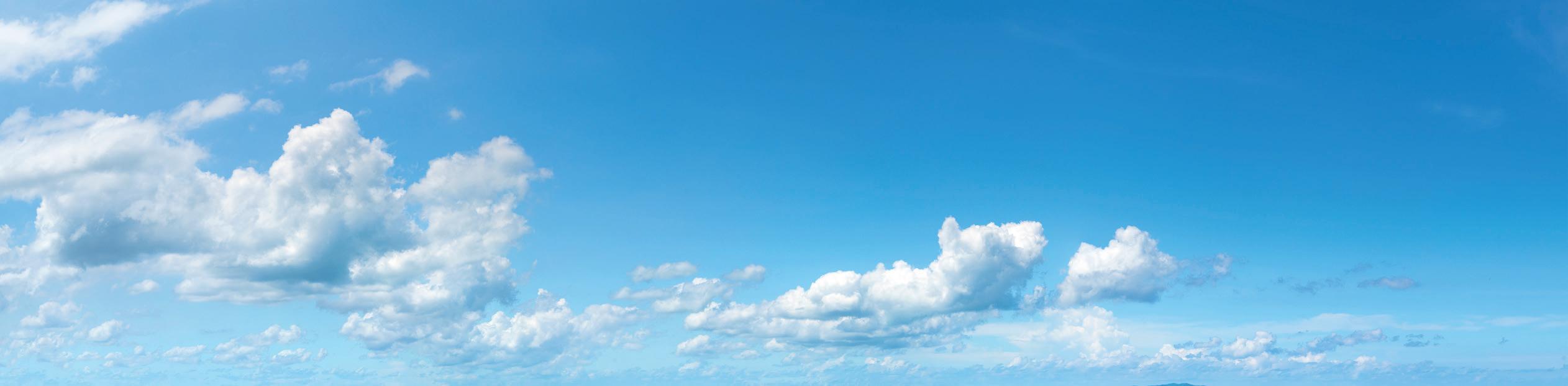
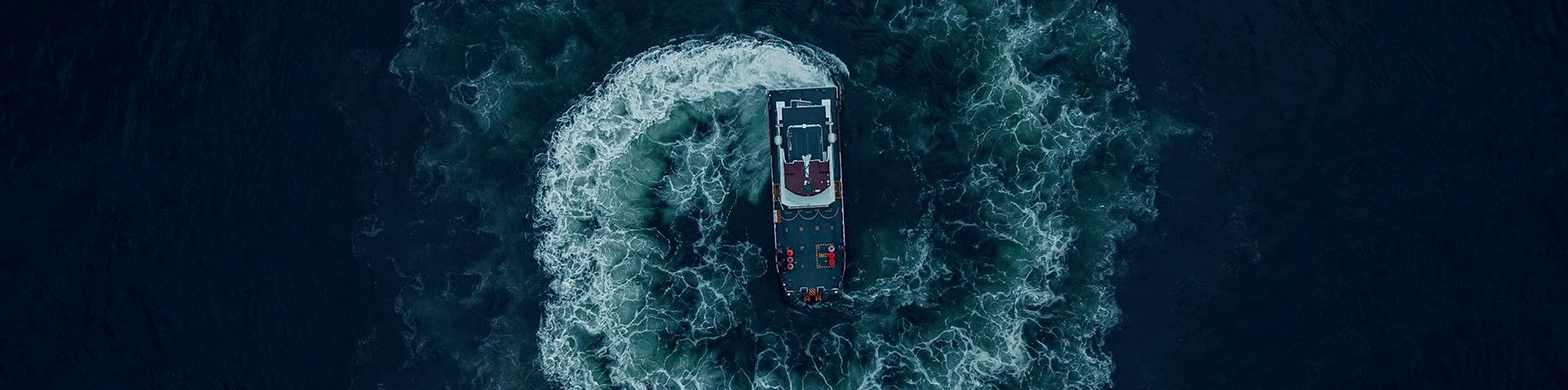
PRODUCT NEWS
Northern Offshore Services announces first commercial application of Volvo Penta’s IPS Professional Platform
Northern Offshore Services has unveiled its new I-Class crew transfer vessel (CTV), named the Impressor, built by Penguin Shipyard in Singapore, which is equipped with the first real-world commercial application of Volvo Penta’s IPS Professional Platform.
The IPS Professional Platform enables flexibility to transform as requirements and the offshore wind industry develops, with propulsion conversions that allow the vessel to adapt to hybrid, fully electric, or renewable/future alternative fuel solutions (such as hydrotreated vegetable oil) without the need to rebuild, futureproofing the vessel.
The Impressor also leverages four engines connected to two drives to meet the specific needs at every stage of operation, and the Eco Mode automatically manages and optimises engine use based on real-time needs during the vessel’s operation.
The I-Class CTV also has battery boxes installed for future use, offering the option to go greener when necessary. Northern Offshore Services have prepared the space for where the necessary equipment will be needed (e.g. converters) to make electric a reality, with batteries from Zero Emissions Marine
and transformers already in place for AC and DC currents for onshore and offshore charging. There was space available for this due to the compact nature of the IPS Professional Platform compared to conventional engines, allowing for the option of adding batteries for future use.
The CTV has a patented five-piece wear and tear high grip fender to reduce the costs and time of repair. The modular design means that only one part will need to replaced, rather than the whole thing each time, and distance boxes enables the vessel to land on all different types of platforms.
The IPS Professional Platform is also a fully-integrated helm-to-propeller system, with the controls, electronics, in-house developed software, propulsion package, and more all designed to work together. The supplier means there is also a single point of contact, making collaboration simpler and allowing the operators and crew to focus on the operation at hand.
The vessel began operating in a UK wind farm on 1 September 2024. A second I-Class vessel equipped with the Volvo Penta IPS Professional Platform will commence operation in early 2025.
ADVERTISERS’ DIRECTORY
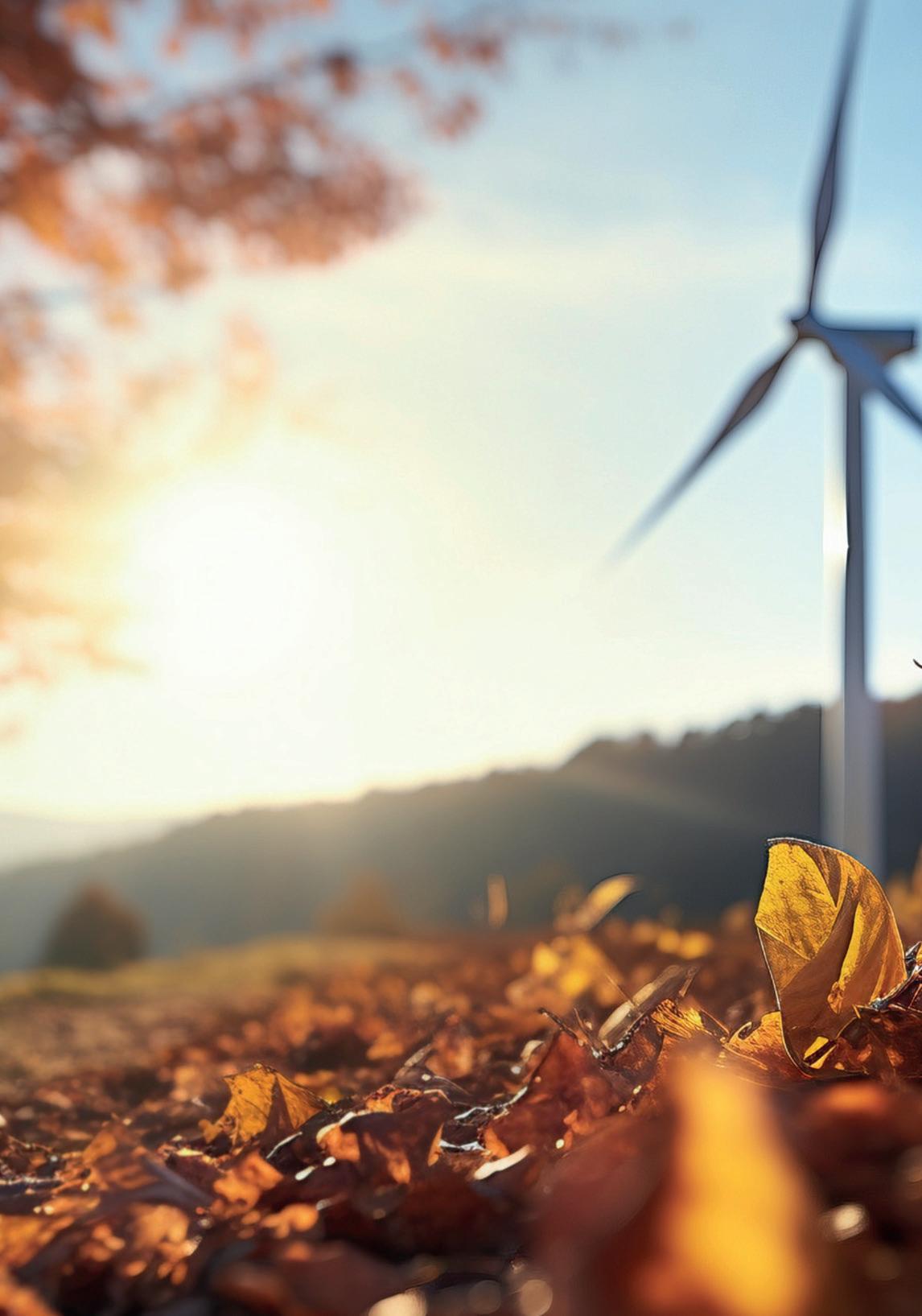
will.powell@energyglobal.com