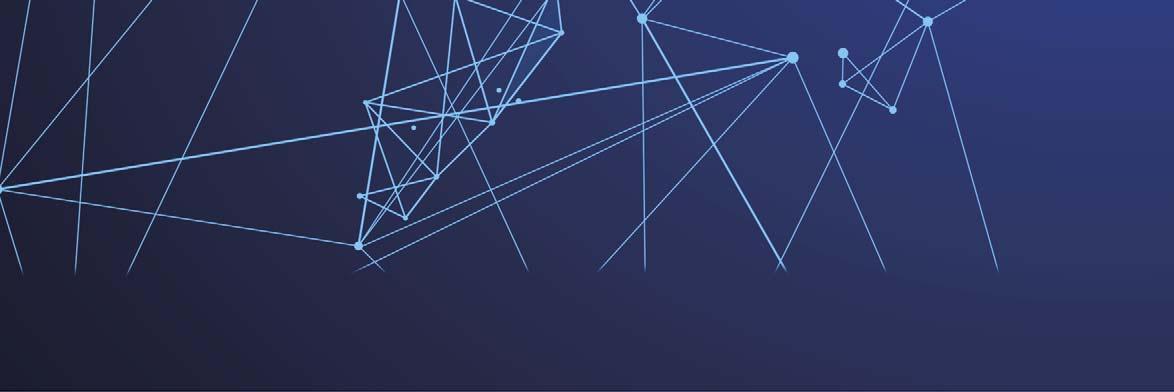
7 minute read
Breaking Through Remotely
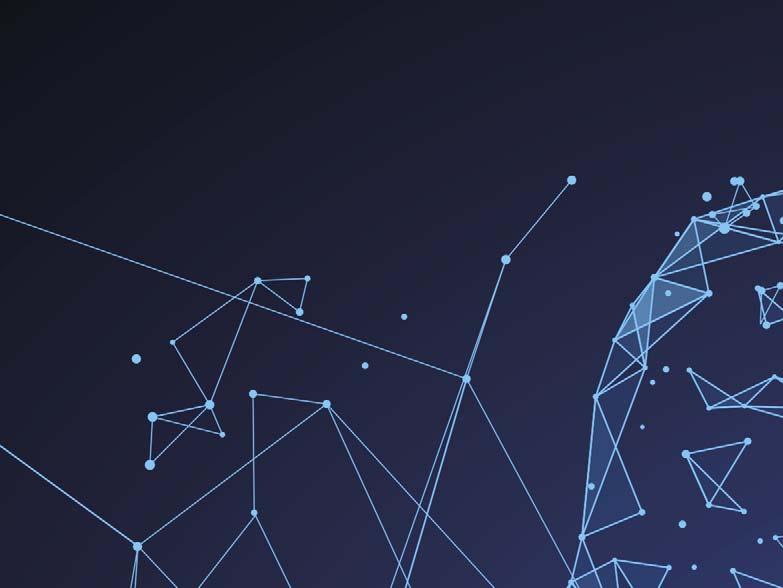
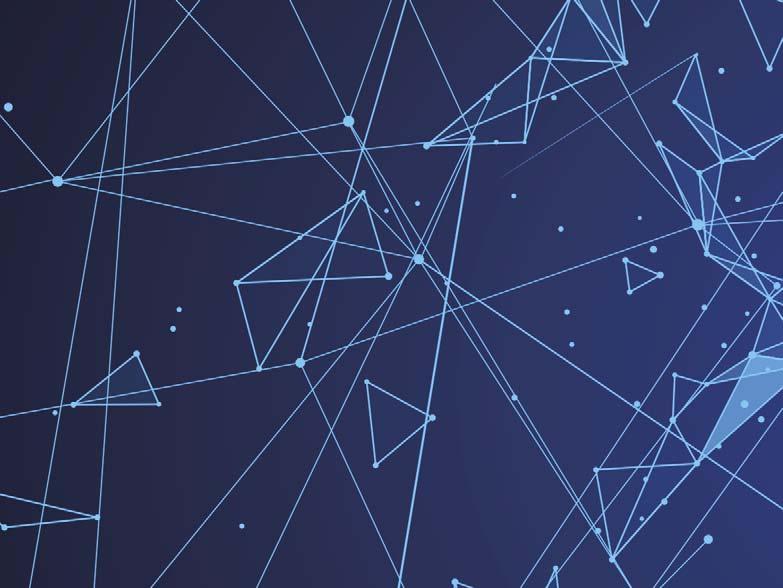
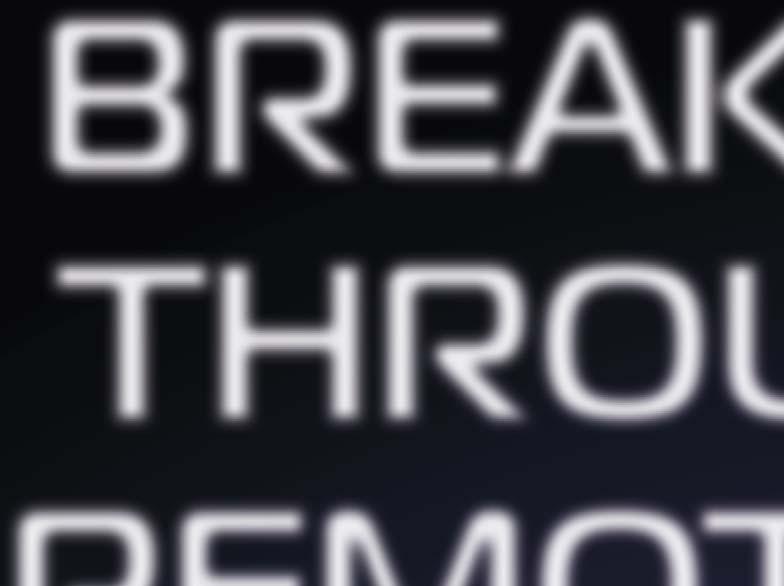


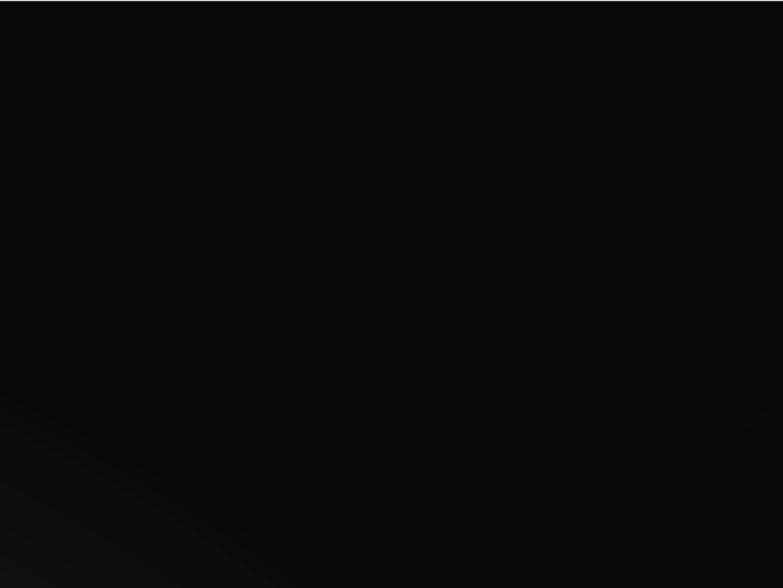
Claude Sharma, HARD-LINE, Canada, considers how automation is helping mines optimise their operations.
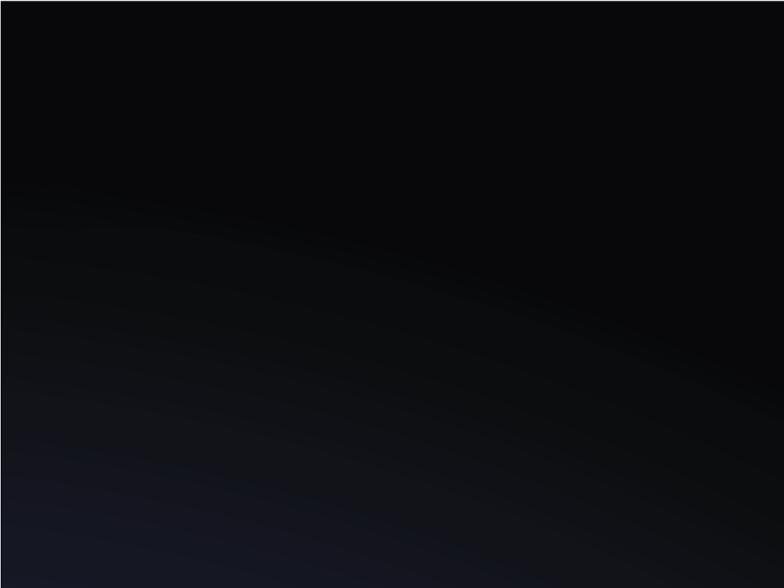
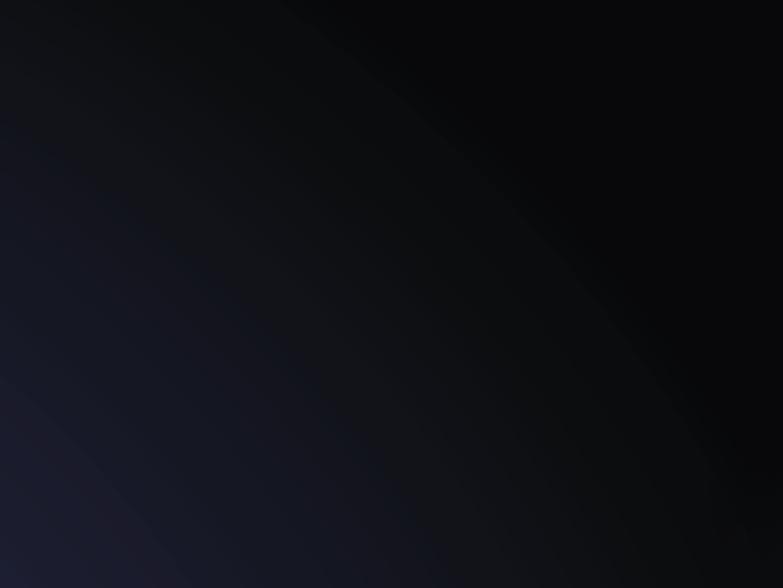
There are more ways now than ever before to extract valuable minerals from surface and underground mining operations, and that trend will rise even further as the digital transformation continues to become more sophisticated. While each producer does not follow the same mold, it is natural that more mines are integrating autonomous and semi-autonomous solutions. The switch to autonomous and/or a gradual incorporation of modern technology could be tricky, trying and expensive, but is nevertheless inevitable. Advancements in this field are meant to meet operational demands at accelerated rates, meaning higher eff iciencies and profits. What must be considered is how many of these new developments promote a much higher standard in safety – protecting workers first, as well as operational assets. HARD-LINE has identified this problem, and its modern and expanding fleet of innovation caters to the changing direction of the autonomous mining ecosystem.
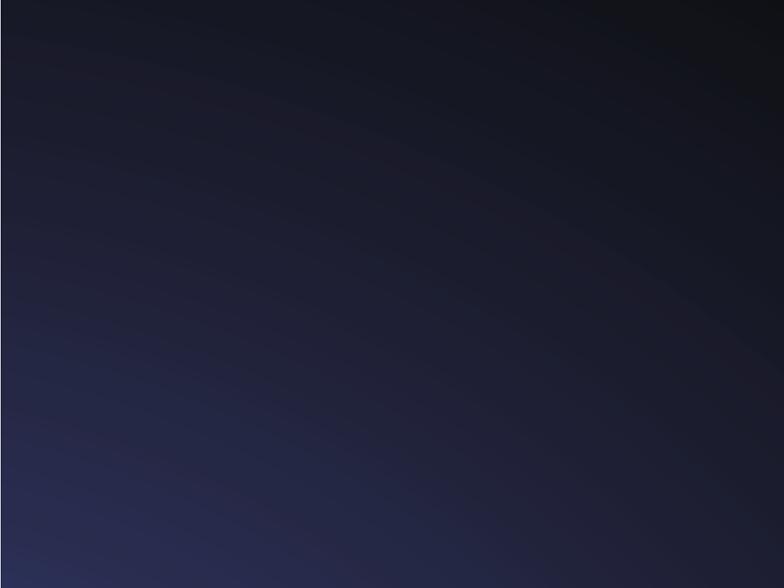
Varying options
A system with automated functions implemented underground at one site could be a perfect fit, depending on the plans of that operation. However, all sites are diff erent and, therefore, so are the needs. Some operations have gone fully (or mostly) autonomous, others are in the blended stages of old and new technology, and then there are those that have yet to adapt; however, an upgrade might not always be necessary. HARD-LINE’s TeleOp packages can match the requirements of any operation, regardless of project type. In the simplest terms, TeleOp allows the tele-remote operation of all types of heavy machinery from a control station in a safe area on the surface or underground, regardless of distance.

Early development: Kirkland Lake Gold, Macassa Mine, Canada
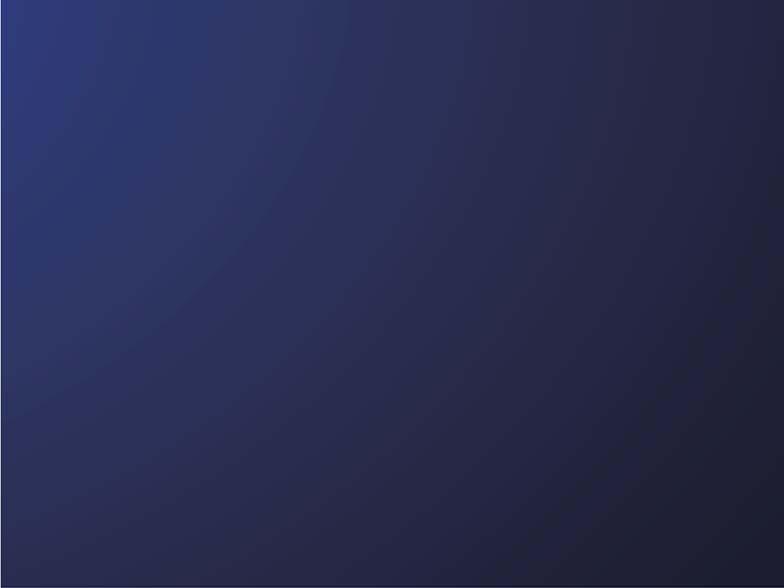
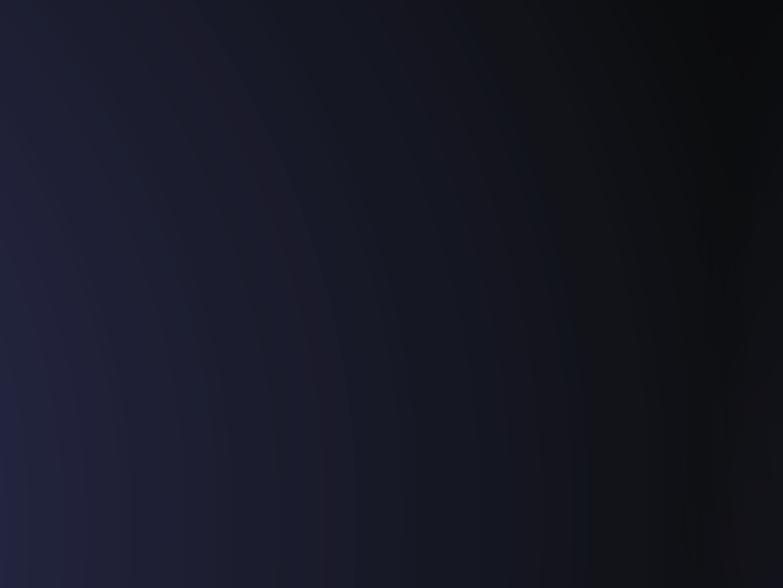
Operating in Canada and Australia, Kirkland Lake Gold Ltd is a senior gold producer with a target production of 1.3 – 1.4 million oz in 2021. This year, the Macassa Mine, located in Kirkland Lake, Ontario, enhanced its TeleOp base system (two control stations above ground) by adding TeleOp Assist, which equips vehicles with 3D LiDAR technology to help keep machines from colliding into walls (Figure 1). The TeleOp system allows for tele-remote operations during shift changes, taking advantage of downtime between blast cycles which increases profitability and production, something that was noted by the mine’s underground general electrical foreman. With TeleOp Assist adding intelligent steering assistance and collision detection modes to the application, vehicles and assets experience less damage while production is maintained or increased. Assist has other time-saving advantages – such as its cruise control feature that allows operators to set a fixed throttle position to help reduce operator fatigue – which aid better prioritisation of time critical operations, such as loading. Another benefit is the takeover command. When it is time for the operator to take full control, it can be done seamlessly as there is no need to stop, or even slow down, when transitioning between modes, whether it is TeleOp Assist or TeleOp Auto.
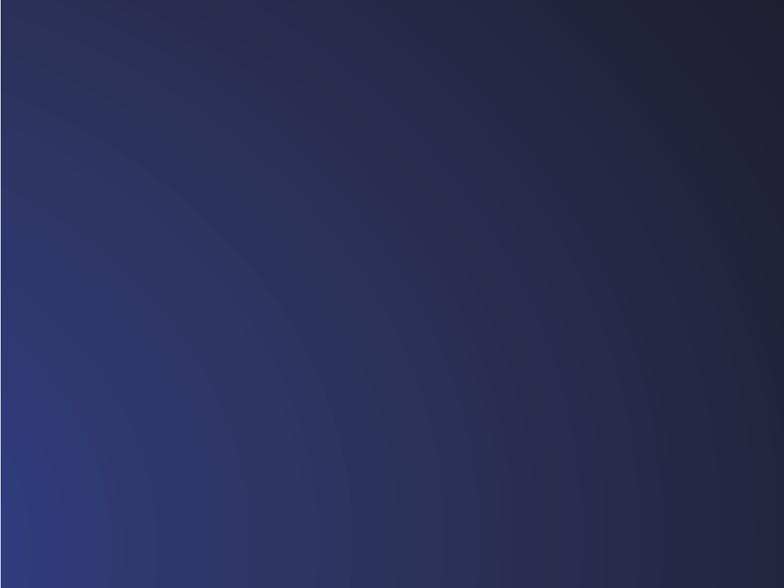
Taking it to the next level: Pucobre Copper mine, Chile
Based in Chile, Pucobre specialises in the exploitation of medium-sized copper deposits. A recent partnership has seen an underground mine in Copiapó use semi-autonomous and assist technology from HARD-LINE for the first time (Figure 2). In this case, TeleOp Auto, a system that allows control of load, haul, dump units (LHDs), as well as trucks in the future, from a control room located outside the mine. TeleOp Assist was also implemented.
A study during the original trial, using semi-autonomous LHD and assist technology, has helped Pucobre make the decision to implement a new design in the mine that will increase productivity. The TeleOp Auto tool facilitates safer operations, while optimising the mining process. This tele-remote application is also intended to be used on heavy machinery for drilling and haulage purposes.
Case study: Underground gold mine, USA
At an underground gold mine in Nevada, US, HARD-LINE’s TeleOp Auto system was trialled on a haul truck. The purpose was to minimise operating costs and maximise eff iciencies by implementing TeleOp Auto on machinery the mine already owns, and to bring additional value to an existing ramp design. The system would allow the truck to manoeuvre on the mine’s 4.5 km ramp during shift changes, while an operator above ground monitors the autonomous operation. A driverless vehicle was operated autonomously 4500 m up the ramp, from an underground area to the mine’s surface portal. The operator took control of the truck once it reached surface parking near the entrance. The application is a step towards an around-the-clock operation that is safe and eff icient. The mine’s underground ramp was the ideal environment to apply this type of autonomous technology. It is the sole access to the underground working area and the primary pathway for transporting material.
Moving material during downtimes proved beneficial as the mine typically losses up to two hours of potential production time each shift during shift changes and blast cycles. This method increased machine utilisation by up to 20% per day when used during downtimes.
Case study: Underground gold mine, Canada
As mine sites explore new avenues of digital transformation, bundling and combining automation packages broadens the optimisation process in any mine.
At a prolific mining district in Red Lake, Ontario, an underground gold mine experienced gains in productivity safely while using TeleOp Multi. The multi system allowed several vehicles and types to be controlled from one TeleOp station. For this project, the mine increased development rates with several operational improvements, including: multiple TeleOp control stations (remotely operated from the surface), six LHDs, a rock-breaker, and locomotive. The underground locomotive transports ore and waste on a dedicated tramming level.
In this case, according to mine management, there were not nearly as many windows of downtime which improved productivity, including mucking rates, material handling rates, and even development and overall stope cycle rates, because the material can move much faster. At the time, approximately 20% of the mine’s muck was being moved using HARD-LINE’s technology. Each TeleOp system is powered by TeleAi, which also allows for the control and monitoring of auxiliary devices and sensors with centralised management, reporting, and diagnostics.

Figure 1. HARD-LINE technician installing 3D LiDAR technology on a load, haul, dump unit (LHD) for TeleOp Assist.
Figure 2. TeleOp Auto increases productivity at Pucobre mine in Chile.
Figure 3. Auto Rockbreaker’s user interface on HARD-LINE’s TeleOp System.
Breaking through autonomously
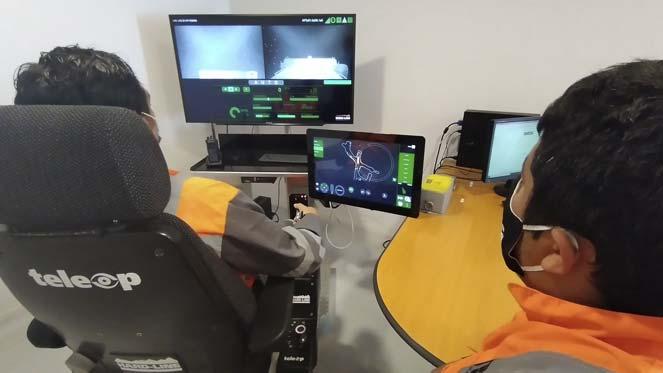
Rock-breakers are integral machines at many mine sites all over the world. While their movements may seem straightforward, the manoeuvrability of rock-breakers can be complex, especially when the autonomous element is involved. Autonomous rock-breakers not only provide the advantages of remote control, such as increasing production, removing operators from dangerous environments, and cutting operating costs; but also producing solutions for limited visibility, poor depth perception, and high latency. Furthermore, it does not require a highly trained operator to manoeuvre a rock-breaker eff iciently and safely.
At MinEXPO 2021 in Las Vegas, Nevada, HARD-LINE unveiled its breakthrough in autonomous rock-breaker technology, known as Auto Rockbreaker, for the first time (Figure 3). A few of its features include: target extraction, obstruction detection, and autonomous manoeuvrability – achieved by utilising state-of-the-art artificial intelligence (AI) and computer vision techniques. The new version of the TeleOp station provides rock-breaker users with a wide array of features, which include touch screen for easy control, buttons for quick deploy and parking, 3D view for better situation awareness using LiDAR and cameras, and easy target selection from candidate targets provided by AI.
Moreover, it off ers easier control features, such as automatic head levelling and a new way to control the rock-breaker called intuitive control. The on-board smart control system provides low latency and safety features that automatically handle failure situations. HARD-LINE’s release of Auto Rockbreaker is a step forward toward improving its fully autonomous suite of mining machinery.
Conclusion
The benefits of optimising a mine with automation are easy to understand. Whether it is a single innovative formula or multiple solutions working in unison, mines are adjusting as technology advances. Automating mines and vehicles not only contributes to much safer working conditions for employees and a better bottom line for businesses, but it shows the industry is moving forward as more companies in all mining fields embrace change.
