
9 minute read
Keep Things Moving With Mobile Conveyors
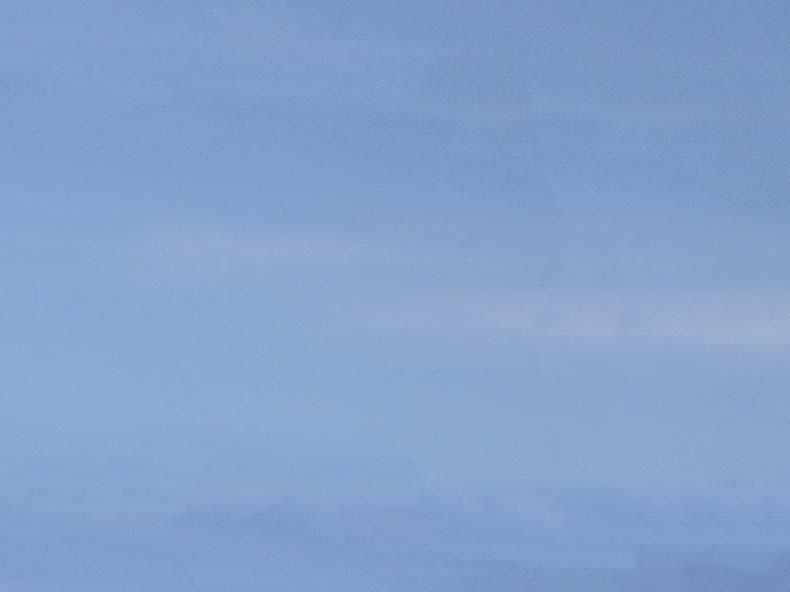
Paul Emerson, Terra Nova Technologies Inc., USA, discusses how fl exibility and versatility can be added to an IPCC system using mobile conveyors.
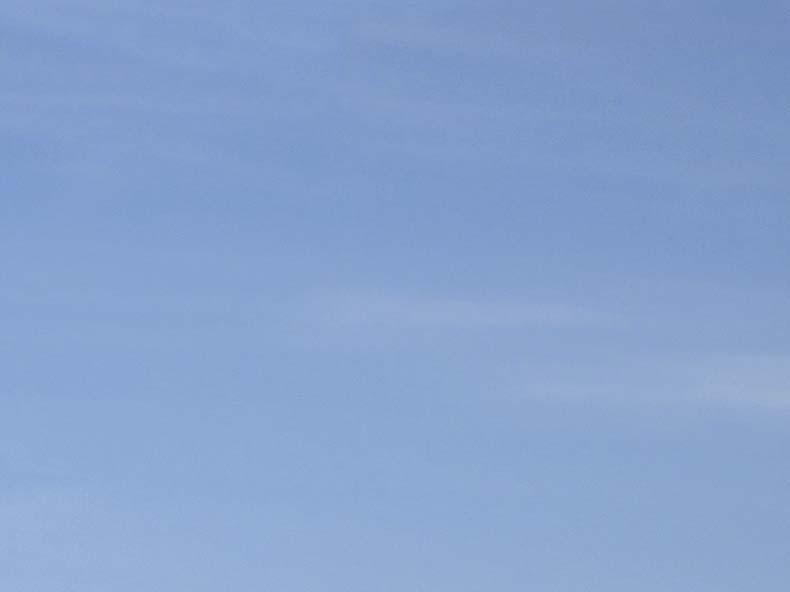
Whilst in-pit crushing and conveying (IPCC) systems have the logical advantages of conveyor haulage when considering the environment, safety, water usage, carbon footprint, dust abatement and the life of mine OPEX, there are also some practical complexities when considering IPCC as an alternative to traditional truck haulage, particularly in deep opencast mines at large capacities. This discussion explores some of the issues, concerns and perceptions related to IPCC systems, as well as the potential to overcome these issues by utilising Super Portable® mobile conveyors, which are integral to the IPCC system.
IPCC challenges
One of the main challenges for the successful deployment of an IPCC system in deep opencast mines is the mobility and flexibility of the system when compared to truck haulage. These mines are dynamic, and mining faces are continuously moving in multiple dimensions, due to advance rate sensitivity, sequencing phase geometry, and selectivity. The flexibility of the trucks provides inherent shovel eff iciency and the ability to adapt to the mine dynamics. Generally, the largest OPEX component in a mine is the truck haulage cost from the pit, which is where an IPCC system can add value through reduced OPEX.
The traditional approach to IPCC in opencast mines has remained relatively unchanged for several decades, relying primarily on truck haulage followed by primary size reduction on ROM material and conveyance.
To add to the diff iculties, most mine plans are designed around traditional approaches at early study stages, before crushing and conveying is properly considered.
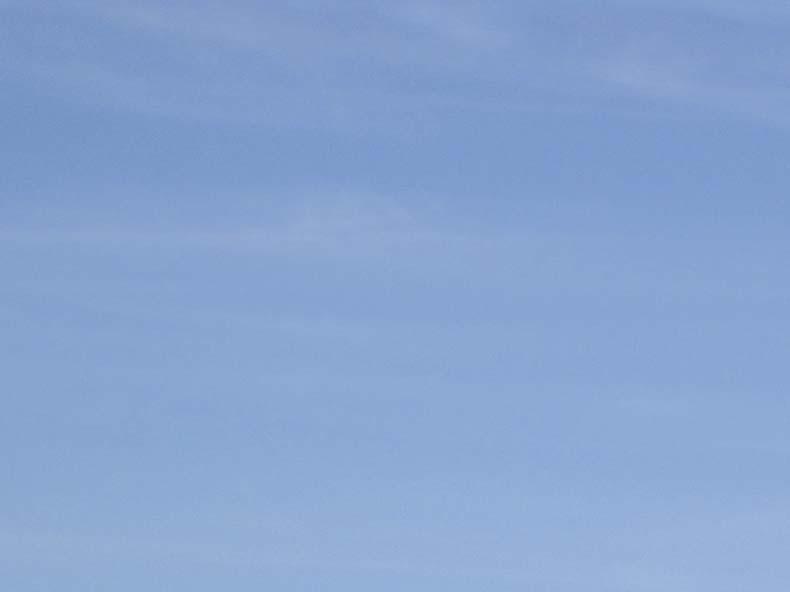

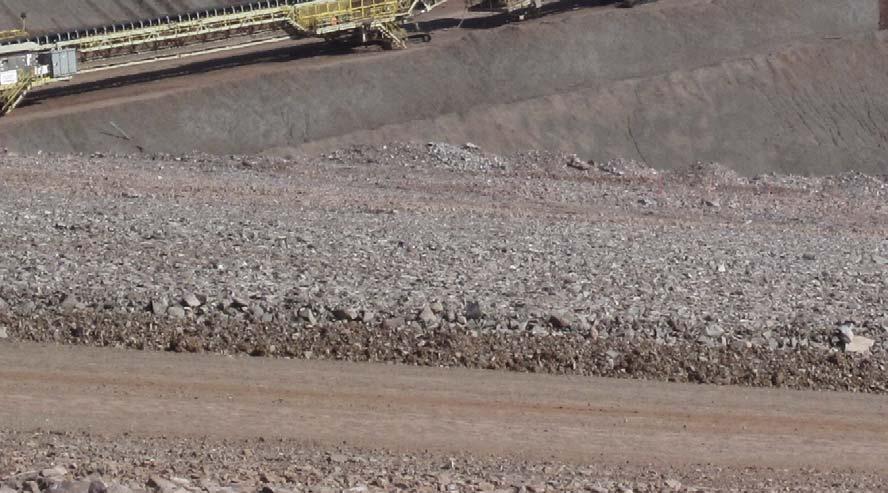
Figure 1. Terra Nova Technologies Super Portable® fully mobile ramp conveyors at a 7000 tph copper operation in the US.


This usually results in the IPCC system being ‘shoehorned’ into a mine plan previously designed for trucks and shovels. The feed to the IPCC system in the pit also presents challenges.
In many mines, the most OPEX eff ective system would usually be to utilise trucks, with a short haul in the pit as a means of interfacing between shovels and primary crushing/sizing, followed by out-of-pit conveyance. This scenario maintains high shovel eff iciency, reduces truck fleet size, and eliminates the costly haul from the pit to the surface plant or waste pile. The issue with this scenario is that there are no practically feasible or proven, truly mobile in-pit truck fed crushing stations available, and for this reason ‘semi-mobile’ stations are limited to really being ‘relocatable’ at best, with a low frequency of moves and high cost of relocation. This does not suit the dynamic progression of most mines.
Mobile direct shovel fed solutions are typically limited to mineral sizers, which usually restricts their use to overburden removal. That said, with mines going deeper and strip ratios increasing, the focus on overburden removal for an IPCC system should probably be the primary focus for most mines, in order to reduce the high OPEX of hauling the overburden/waste materials from the pit. This scenario has the advantage that there are a number of successful shovel-fed sizer stations, which have the ability to maintain some of the shovel eff iciencies associated with loading trucks, and that eliminate double handling. The eff ectiveness of these stations is generally restricted by the mobility of traditional bench conveyors and the high cost and practicality of relocating, extending, reducing, or shift ing these conveyors.
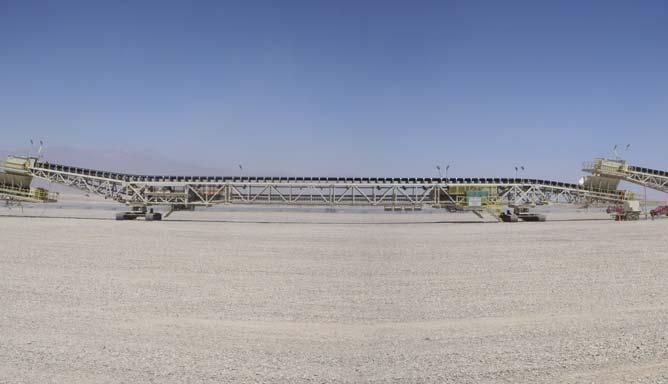
Figure 2. Terra Nova Technologies Super Portable mobile conveyor.
Figure 3. Graphical representation of the mobile conveyors considered in an IPCC system.
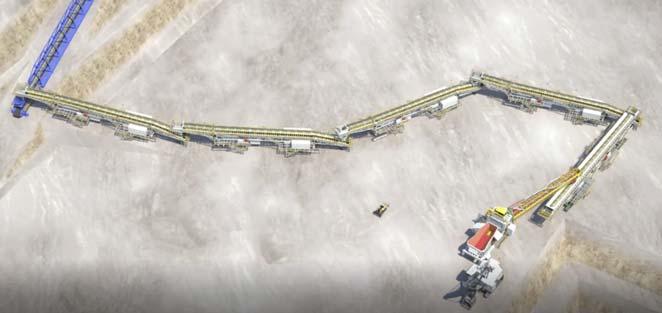
Versatility of mobile conveyors
In 2015, BHP Billiton conducted a study for their Mass Mining Methods (MMM) investigation at Escondida, Chile, where the fully mobile conveyors were eventually selected as the means to practically link fully mobile sizer stations to the out-of-pit conveyors. The highly manoeuvrable and eff icient way in which the self-propelled conveyors, equipped with on-board diesel generators, can be added or removed, in a simple ‘plug-and-play’ manner, allowed for the sizing stations to follow the shovels in an eff ective way, maximising shovel and conveying availabilities and eff iciencies in the pit. In a similar manner, fully mobile conveyors were supplied to a mine in the US to increase its mining eff iciency, by linking the mobile loading/screening unit to a stationary but portable slurry station, in order to maintain the eff iciency of the material handling equipment that feeds the sizing rig.
Inherant system redundancy
One concern of in-pit conveyances, when compared with truck haulage, is the redundancy of the haul trucks. This consideration is oft en debated in IPCC system studies, with regards to the availability of a conveying system compared with trucks. Typically, the argument is that if one conveyor shuts down, then the entire IPCC system is down. On the other hand, if one truck goes down, the system can still operate, albeit at a reduced capacity. This is where Super Portable fully mobile conveyors can overcome this valid concern, in that if any one of the chain of mobile conveyors has an unscheduled breakdown, it is simply removed and replaced in a similar fashion to trucks. Under normal operating conditions, a mobile conveyor is added in for advancing or removed in a retreat mode. Similar 10 000 tph systems, operating in large copper heap leach systems, have proven to have high reliability and usually a few spare machines are also kept on hand to replace operating units in the event of an unexpected breakdown. This type of fully mobile conveyor adds the flexibility and versatility to follow a mobile shovel-fed station and interface with the out-of-pit conveying. Usually, there would be dual mobile sizer stations in a large opencast mine, which provide additional redundancy when combined with a modular mobile conveying system.
Flexibility of mobile conveyors
Another factor to consider when analysing trucks in comparison to conveying for an IPCC system is the flexibility of trucks within the mine pit. Unlike other conveying options, fully mobile conveyors are self-propelled and can be relocated when required. Another benefit of the fully mobile conveyor is that the equipment was originally designed for multi-lift stacking systems, with a variation that is referred to as a ramp conveyor. These ramp conveyors typically operate up 20% grades and have suff icient power for the conveyor and crawlers to account for inclination during operation and relocation.
At the other end of an IPCC overburden/waste rock disposal system, a Super Portable fully mobile stacking system can be deployed. The stacking system comprises a string of fully mobile conveyors, arranged head-to-tail,
feeding a horizontal feed conveyor, arranged at 90˚ to the string. The horizontal feed conveyor feeds a fully skirted horizontal conveyor, which subsequently feeds a telescoping radial stacker/spreader that discharges material to the area being stacked. The fully mobile, self-propelled equipment is capable of retreat or advance stacking and the horizontal conveyor and radial stacker index in advance or retreat modes in unison, without interrupting material feed. Once retreated or advanced by the eff ective length of the horizontal conveyor, the system encounters a brief shut down, in order to add or subtract a fully mobile conveyor, which is then repositioned between stacking areas in rotation, in order to share the workload evenly. When not in use, inspections, scheduled repairs, modifications, cleaning, and preventive maintenance are performed. Each fully mobile conveyor has a complete electrical system – housing its own diesel generator, programmable logic controller (PLC), and drive system – and can be relocated independently.
Availability and reliability
As part of the aforementioned MMM study, BHP benchmarked the performance of a 10 000 tph heap leach stacking system at a large copper mine in Chile, in order to investigate the system’s reliability, availability, and suitability for use in waste rock at high capacities. The conclusion was that there was a very high reliability rate associated with individual fully mobile conveyors – approximately 99.95% net availability with regards to unplanned breakdowns/failures. It was noted that there was high system utilisation with up to 27 multiple units in series at approximately 6800 operating hours/year, and the single system achieved >90% availability. It was further calculated that upward of 95% availability could be achieved with the addition of a spare horizontal conveyor, horizontal feed conveyor, and radial stacker – eff ectively providing a redundant stacking with only three additional pieces of equipment. The stacking system nameplate capacities were achieved/exceeded and conveying waste rock at higher capacities was deemed viable. It was noted that for automatic reconfigurations to take fully mobile conveyors into and out of line, a relatively short time of between 35 and 45 minutes was generally achieved. The system required only a minimal amount of support equipment for the operation, inclusive of spillage and floor preparation, and there was a low annual cost of mobile equipment specific, non-conveyor component spare parts.
Conclusion
A plug-and-play fully mobile approach allows IPCC systems to link mobile sizing stations to out-of-pit conveyors, and negotiate pit ramps, multiple benches, and feed waste stacking systems in advance or retreat. These high capacity, self-propelled, highly mobile, and manoeuvrable conveyors can drive up benches or over stacked material with relatively low ground bearing pressures, requiring minimal dozer support during operation and the ability to negotiate diff icult topography in complex valley fill situations with a high degree of redundancy. Good collaboration between a mine operator and an original equipment manufacturer, as well as using a system engineering approach, increases the likelihood of not only sustaining, but evolving a whole new opencast mining method using this technology. This approach, when combined with the versatility of fully mobile conveyors, can provide further added benefits, such as utilising the same mobile stacking equipment to stack filtered tailings, co-mixed with waste rock and stacking rock containment abutments, in order to overcome geotechnical issues for dry tailings disposal.
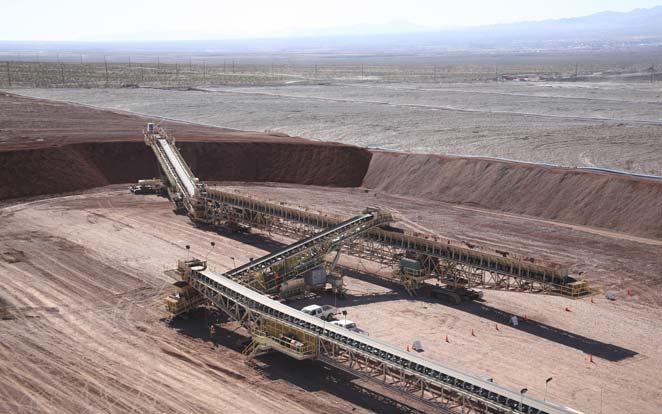
Figure 4. Graphical representation of the mobile stacking system in retreat stack mode.
Figure 5. Mobile stacking system with 27 units in series at 10 000 tph at a copper mine in Chile.
Figure 6. ‘Plug-and-play’ fully mobile conveyors at a 7000 tph copper heap leach operation in the US.

