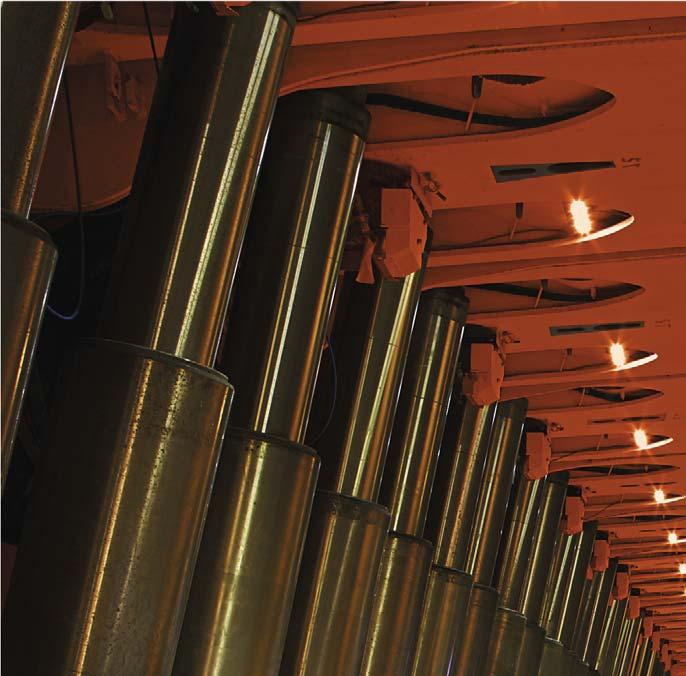
8 minute read
Seal Of The Longwall
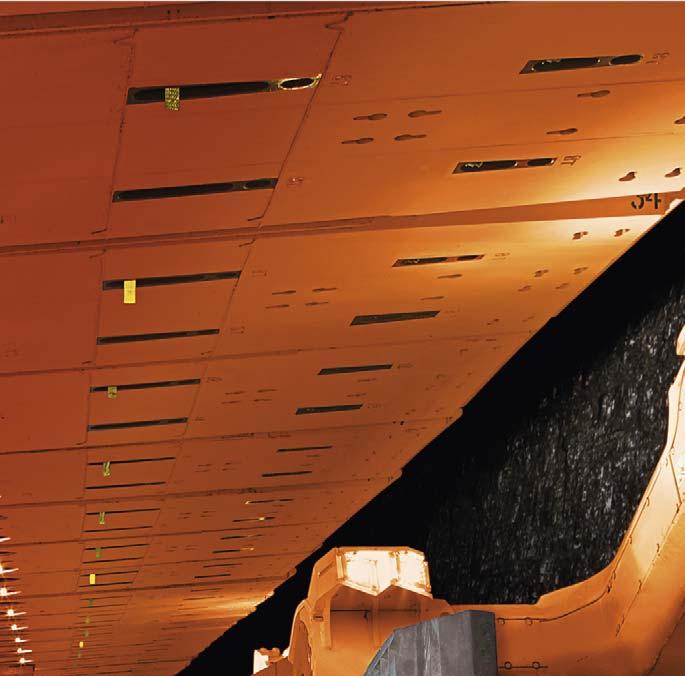

Figure 1. Longwall shearer with seal-powered roof support legs.

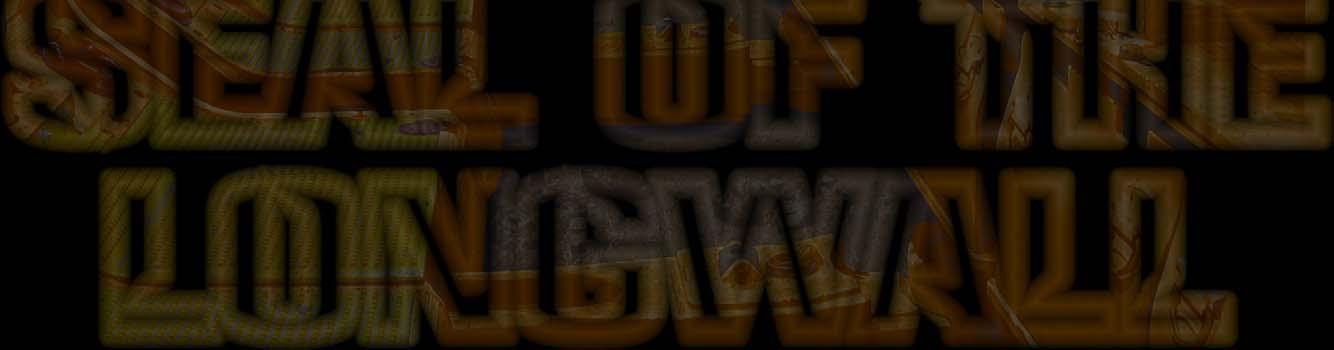
Chris Edge, Hallite Seals International, and Geoff McKenna, Komatsu Mining Corporation, discuss the importance of seals in mining roof supports.

Seals play a critical role in the functioning of the hydraulic cylinders that power mining roof supports. Their use in modern mining equipment means that roof supports can shoulder loads approaching 1800 t. To put this into perspective, imagine the combined weight of more than four jumbo jets stacked on top of each other. Each seal’s profile, design, and choice of materials contribute to mine safety, eff iciency, and productivity. When miners face complex operating requirements, the sealing components in the equipment used to do the work must be equal to the task.
Hallite Seals International and Komatsu Mining Corporation embarked on a collaborative partnership almost 50 years ago that continues to impact the industry today. The partnership started when Hallite provided Komatsu with a uniquely innovative solution for their hydraulic cylinder hardware. Both companies have grown internationally and developed detailed portfolios of solutions for the mining industry throughout the years, and the partnership has remained strong. It is a relationship fuelled by sealing product innovation and a mutual commitment to solid equipment performance and customer satisfaction.
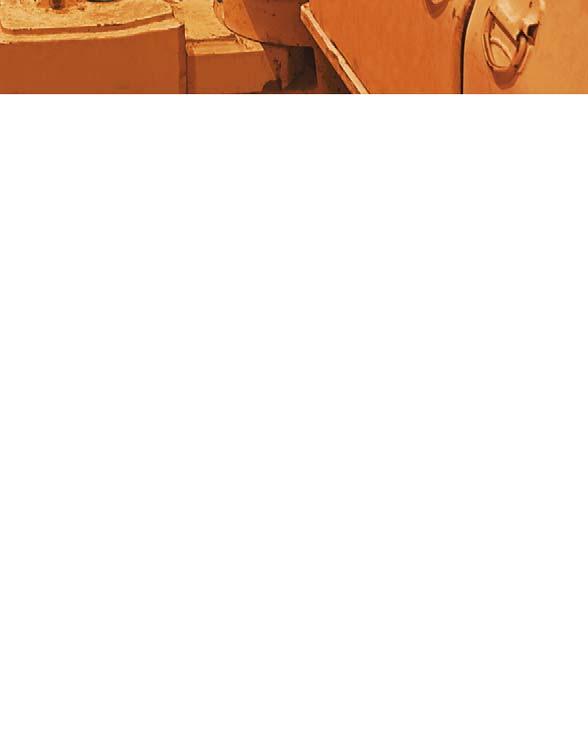
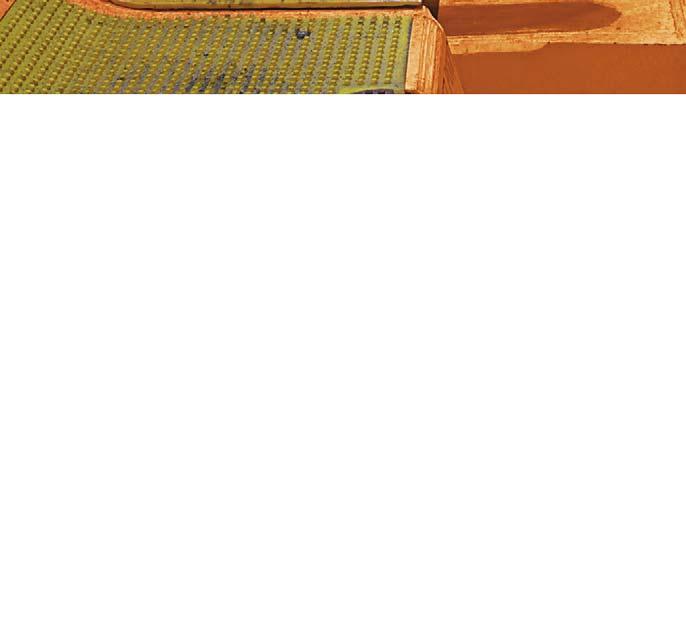
Seal-powered legs
This article will focus on powered longwall mining operations (Figure 1). Specifically, it will discuss the location of critical seals and bearings, their function, and how an industry-leading engineering team is collaborating to continuously improve these products.
Four seal profiles characterise the products and materials
best suited for longwall mining – piston seals, rod seals, static seals, and wipers (Figure 2). The 730 and 740 piston seals represent the inner and outer stage of the hydraulic cylinder leg. Both are assembled with proprietary bearings on each side. A combination of bearing rings of various widths are used depending on the application. The 730 is a double-acting piston seal in a four-part assembly designed for high shock loads and pressures (Figure 3), and the 740 is quite similar, but with a diff erent back up arrangement. The 82 static seal and the 652 rod seal fit in the gland. Static seals function against mating surfaces with no relative motion between each other. Rod seals handle high-pressure, and they are designed with a polyurethane shell, an O-ring energiser, and a polyacetal anti-extrusion ring.
Finally, the 842 wiper is installed at the end of the cylinder and supported by gland bearings. The wiper prevents the ingress of foreign particles and moisture into the cylinder. The 842 wiper is manufactured in Hythane® 371 high-performance polyurethane, and is proven for low compression set characteristics, wear and abrasion resistance, and fluid compatibility. The wiper is also known for a protective flap that directs both dirt and water away from the outside diameter, in order to prevent the water and slurry trap common with conventional wipers.
Continued improvements
Bearing rings
The seal development teams worked together to innovate a solution for the bearing issues, and in 2000, the proprietary TGA material was introduced. Rigorous testing, up to 90 000 cycles, or the equivalent of 10 years of life in a mine, revealed that the bearings possessed yield properties capable of coping with higher pressure and side loads. There have been no reported bearing ring failures since the introduction of the TGA material, and on re-builds, the TGA presents little to no wear.
The aforementioned setup is what characterised a mine in Australia. Over the years, with working pressures and extreme side loads gradually increasing, the maximum diameter for roof support legs adapted to suit these changes. By the late 1990s, three significant seal issues had emerged that required the development of the advanced sealing solutions in use today.
First, operators reported frayed bearing rings following service. Fraying caused metal-to-metal contact, and the fibres fell off the bearings and into the filters, creating valve problems. Second, as cylinders increased in size, extrusion gaps increased, resulting in piston seal damage. Third, wiper seals were ejected on advancing rams. Hydraulic fluid also changed over time from a mineral-based to synthetic solution, consisting of 2% oil to 98 parts water. Water-dominant fluids are much more aggressive than the fluids used previously, accelerating the ageing of the material. The three issues addressed above caused the following changes to come about:
Piston seals

The piston seals featured a profile focused on reducing stress to solve failures. Performance improved from 11 000 – 30 000 cycles – the equivalent of 1 – 3 years of life in a mine. However, the seal development team knew they could do more, so continued to design a 60 000 cycle solution. This achievement required redesigned back-up rings tested up to 60 000 cycles, then up to 90 000, and finally up to 100 000 cycles – where mechanical failure with the seal package outlasted the mechanical parts. The anti-extrusion rings were coloured yellow to help the customer identify the new seals.
Figure 1. Seals and bearing ring types used in roof support leg cylinders. Typical gland and piston sealing configuration.
Figure 2. 730 piston steal with support rings. Wiper seals
Extreme pressures forced the wipers out of the hydraulic cylinder assembly. The development team initially thought that adding more material to the seal would address the issue, but that did not work. They also believed that increasing the fill of the seal would better capture it in the gland wiper seal groove. This increased the surface contact and caused a rocking motion during cycling that forced the seal out of this groove. The team eventually solved the issue by reducing the material in the heel, which decreased the contact on the rod. This solution removed the rocking motion, and a stiff er material provided a sharper stronger lip. The material created more of a scraper with the wiper lip, and the new seal was coloured green for identification.
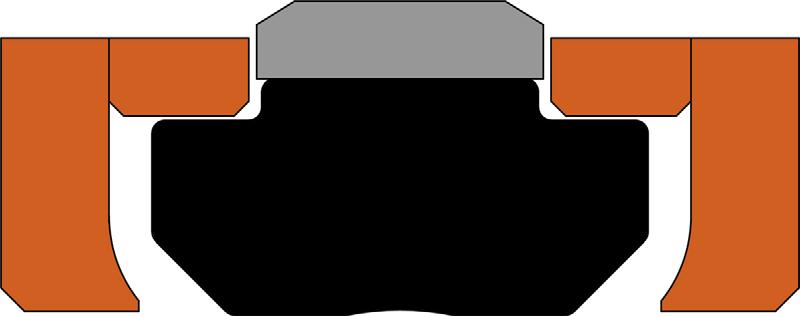
Case study: Australian coal mine
Because of its size and challenging load conditions, a mine in Austrailia required roof supports rated up to 1750 t. When the mining equipment was first delivered in 2007, this load bearing requirement was significantly higher than any other Komatsu-powered roof support in operation. The specification called for a cylinder leg design with a minimum 480 mm bore. At the time, this presented a significant leap in technology for the companies in both the physical size of the leg cylinders and the test life expectancy of a minimum 90 000 cycles. It was the largest longwall mining leg cylinder bore with the longest test life expectancy produced for its time.
Since the team had established best design practices for piston, gland, wiper and bearing ring materials, this historical programme allowed them to demonstrate the products’ performance in an unprecedented field application. The sealing package was successfully installed, the products performed as tested, and they continue to be used on site today.
Forward momentum
The companies are now developing alternative seals for bespoke design hydraulic spool valves used in powered roof support applications. Prototype samples of the initial design will be evaluated and tested at the Komatsu facility in Manchester, UK. As the specialist provider of seals used in Komatsu longwall hydraulic cylinders and various custom-built hydraulic control valves, the team at Hallite are focused on continuous improvements in performance and reliability. Testing rigs at both the seal manufacturer’s facilities and its equipment manufacturing partner’s facilities ensure thorough checks and evaluation of all roof support seal components before they are put into service.
The seals range from less than 10 mm dia. up to large piston seals of 480 mm dia. All are compatible with water-based fluids and a working pressure of 350 bar (5000 psi) up to 1000 bar (15 000 psi). The underground longwall mining environment aggressively impacts all equipment, where unplanned downtime can be detrimental, so product reliability is essential to managing costs.
Conclusion
Improvements in the quality of seals used in hydraulic cylinders and valves, such as those used in armoured face conveyors and shearer ranging arms, are advancing. For example, in order to reduce high shock loads in a shearer ranging arm’s cylinders, Komatsu and Hallite engineers worked together to design a solution. The result was a seal package applied across the range that increased the ranging arm life and reliability.
As Komatsu expands its footprint in China for reliable cylinder and valve designs fitted with reliable seals, the partnership with Hallite will continue to play an essential role in providing established powered roof support equipment suppliers with the solutions they require.
When collaborations, such as the one between Hallite and Komatsu, come together, the findings benefit not only customers of the companies, but promote a better understanding of industry challenges.
SENTINELTM
Endless Possibilities. Endless Savings.
IWT’s wireless solutions provide more than just reliable voice, text and data for real-time tracking, gas monitoring, analytics, and remote sensors. Combining multiple systems into one rapidly deployable network, IWT customer mines experience annual cost savings for life.
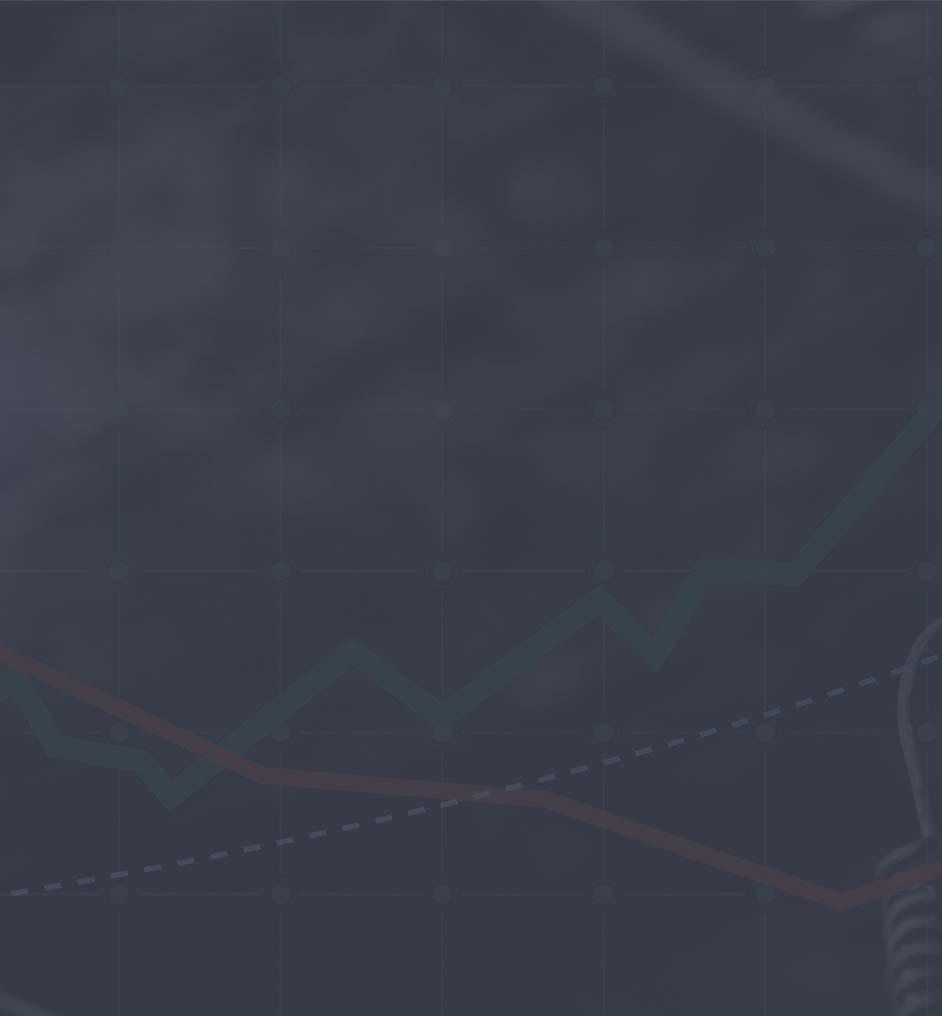

Fewer infrastructure components = Less maintenance No wires between devices = Reduced labor hours 100% recoverable for redeployment in other areas
Always Thinking. Always Solving. Always Innovative.
Profi t
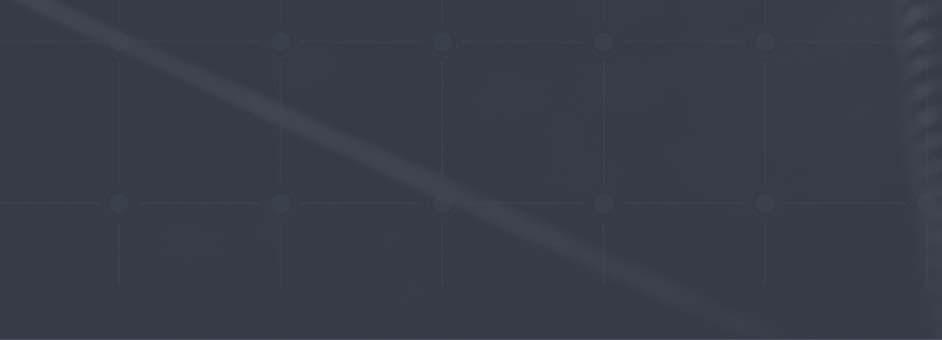