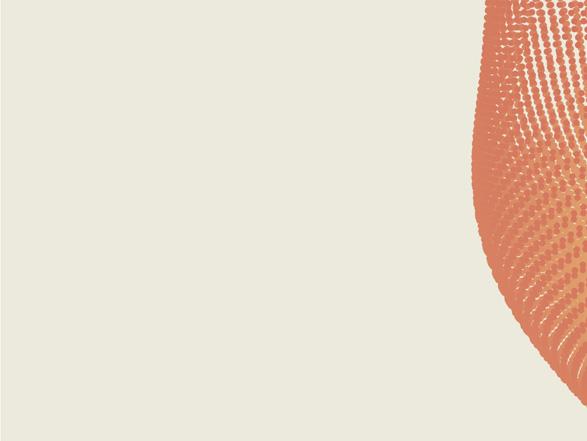
7 minute read
Work the wavelengths
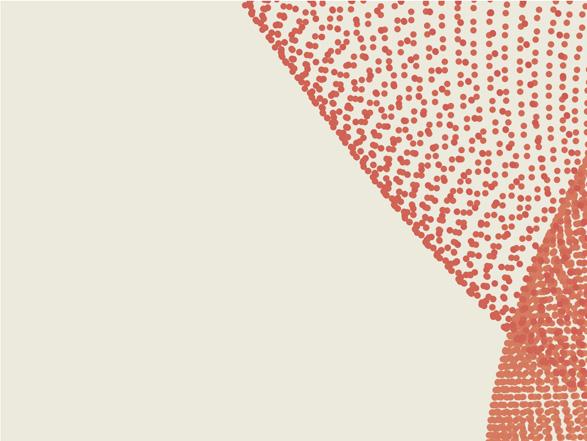
Per Christian Johnsrud, Tunable, Norway, describes multi-gas analyser technologies and how improved gas data could benefit the operation of LNG vessels.
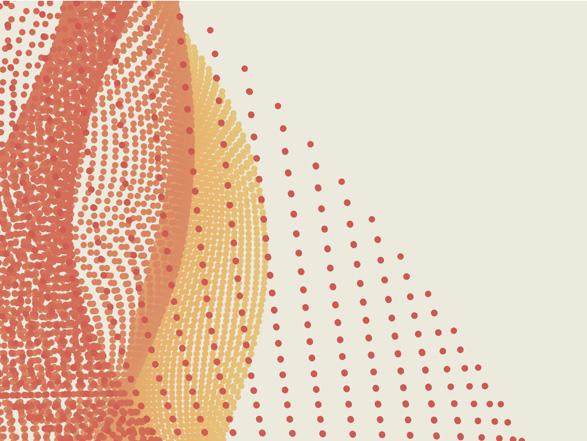
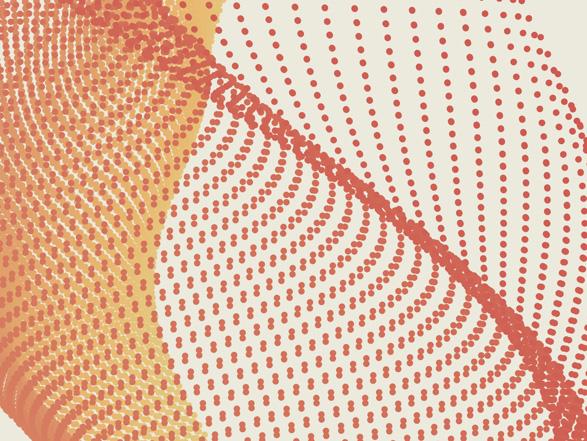
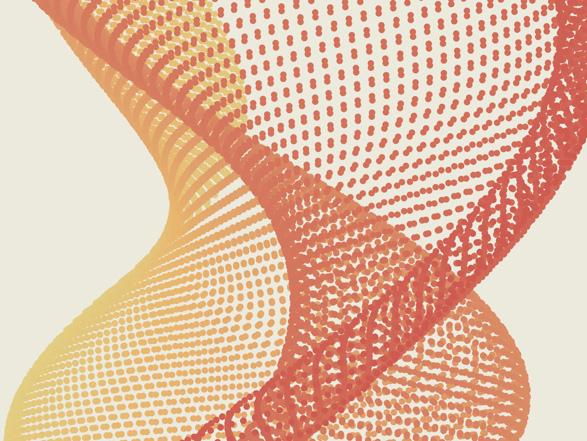
The maritime industry is currently striving to reduce greenhouse gas emissions. Many shipowners are making investments to update their fleets by enabling vessels to run on reduced carbon fuels like LNG. There is a clear drive to improve fuel efficiency and thereby reduce both costs and the environmental footprints of operating vessels. The integration of live data of the fuel quality consumed by the engine will support these initiatives.
By combining multi-gas analyser technologies with a digitalisation algorithm and data analytics, shipowners can obtain valuable information that can improve the operation of their vessels. Going forward with this insight will be of increasing importance.
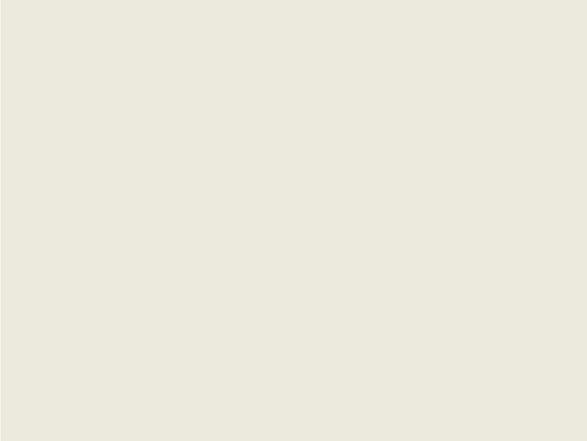
Potential for improved efficiency by access to gas data
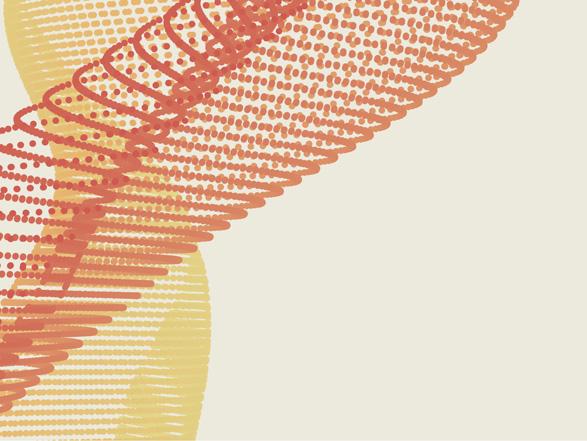
For LNG powered engines, the quality of boil-off gas (BOG) changes over time as a vessel consumes the LNG in the tank. In addition, the combination of forced and natural BOG further adds rapid changes to the gas mixture injected into the engine. This is negative with respect to fuel economy, as the variations in fuel quality forces the crew to run the vessel engines at a worst-case fuel mix scenario to minimise the risk for knocking.
In such a scenario, they could potentially have to operate three engines at a low load instead of only two engines at a higher load per engine. With access to real-time multi-gas data it is possible to tune two engines to run at higher loads which saves fuel. On top of that, operating fewer engines at
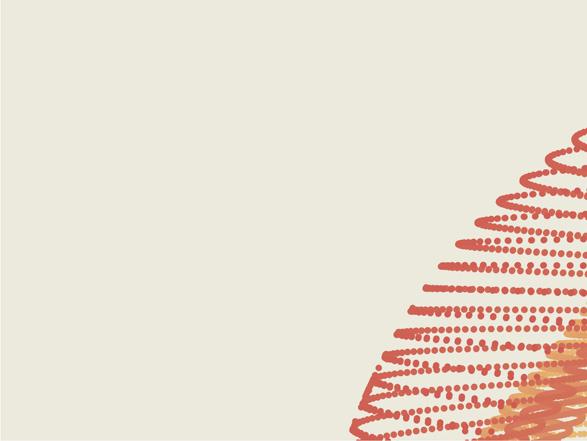

Figure 1. Measurement principle of Tunable’s natural gas analyser technology.
Figure 2. The Tunable micro-electro-mechanical (MEMS) filter is continuously scanning a wide wavelength of the infrared light, to measure gas composition in the fuel gas mixture.
Figure 3. Tunable T1000 natural gas analyser with sampling system. higher loads reduces run hours on the engines, which reduces wear and maintenance costs.
Gas mix information can be combined with other sensor and vessel data to produce valuable performance insight and enable shipowners to better monitor vessel performance. Various data acquisition companies are integrating these data streams to provide comprehensive data analytics. To be able to take full advantage of this data analytics, it is essential to have online gas analysers that provide data updates in real-time.

Improved data knowledge for better understanding of fuel consumption
Some LNG carriers have installed gas analysers for measuring the quality of BOG which is consumed as fuel during sailing. Typically, the shipowner and charterer agree on fixed boil-off rates and fuel consumption as part of a chartering contract. However, actual gas consumption and value is impacted by the gas mix delivered during the voyage and might differ in the end. By having access to online gas analysis of the actual fuel consumed during sailing, the shipowner/charterer will receive improved knowledge which could benefit their commercial agreement.
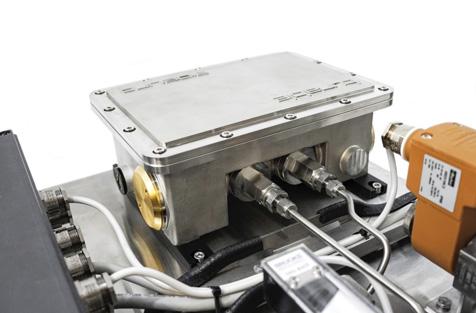
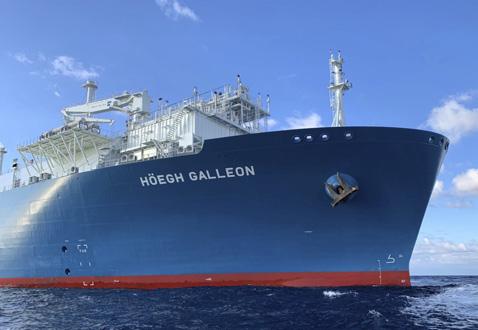
Figure 4. FSRU Höegh Galleon where the analyser system has been in operation since 2019.
Gas analysers are used to measure multiple components
There are various technologies available in the market that measure gas composition, calorific value, and methane number. Historically, gas chromatographs have been used for the measurement of natural gas and LNG. Lately, new analysers based on infrared spectroscopy have entered the market. These technologies are using absorption spectroscopy to measure gas composition. Each gas component has a unique infrared ‘fingerprint’. By illuminating the gas sample with infrared light at various wavelengths, the analyser can determine the presence as well as the concentration of individual gas components. A number of infrared technologies can be used to extract information on the absorption spectra, such as Fourier transform infrared spectroscopy (FTIR) or systems with interference filters that measure a discrete set of wavelengths. Technologies that allow rapid scanning over a broad wavelength range in the far infrared are preferable as they provide faster response time and higher accuracy.
Moreover, for maritime use, it is highly important that the analyser is robust and easy to operate. This excludes systems with delicate optics and fragile mechanics, such as an FTIR. The maintenance requirements of the system should be minimised and they should be able to handle demanding offshore conditions. Furthermore, it is beneficial that the system does not require special gases for recalibration and manual operations while vessels are at sea.
A multi-gas analyser
The Tunable multi-gas analyser measures gas composition by infrared absorption spectroscopy. A small gas stream from the BOG fuel pipe is extracted by a sample probe and fed into the gas analyser. By measuring the transmittance of light through the sample cell at various wavelengths, the analyser determines the gas composition. The measurement principle is illustrated in Figure 1. A key component is a widely tuneable micro-electro-mechanical (MEMS) filter capable of scanning the wavelength of the infrared light continuously
from 7 - 14 μm. Wide scanning allows all gas components of interest to be identified and quantified, and it minimises cross interference. Furthermore, the quick response of the MEMS filter allows dynamic changes of the mixture to be measured, even when sampling relatively small gas volumes. The response time is crucial in dynamic engine optimisation applications. Lastly, the MEMS chip is highly robust, has a long lifetime, and is insensitive to vibrations.
Minimising operational cost
Shipowners are looking for systems that are easy to operate and require minimum need for maintenance and support during operation. With no moving parts, the Tunable multi-gas analyser has been designed to be sufficiently robust for demanding maritime conditions. Traditional systems have been complex and have required regular attendance and consumables such as calibration and carrier gas. By removing the need for these consumables, the shipowner saves cost and space, reduces logistics, and lowers the HSE risk associated with the handling of pressurised gas bottles. The system is ATEX certified for use in Ex Zone 1.
Field test on FSRU Höegh Galleon
Höegh LNG and Tunable have concluded a joint field trial for continuous online monitoring of the composition and calorific value of natural gas. The objective has been to provide a gas analyser that requires less support and reduces Höegh LNG’s annual operation and maintenance cost. As part of the project, Tunable’s natural gas analyser has been in operation on FSRU Höegh Galleon since 2019, where it has continuously monitored the complex composition and calorific value of the BOG. The field demonstration has proven that the gas analyser is successfully measuring mixtures of gases in line with specifications required for LNG carriers.
During operations, remote condition monitoring and service has been successfully tested through a data link, removing the need for onboard service personnel.
The feedback from the operation of the system by the ship operator is that the analyser has enabled them to get in-situ readings without delay and without consumption of calibration gas. This requires less support, implying lower operation and maintenance costs compared to existing technology.
Fast response time an enabler for engine performance
The Tunable system conducts in-line measurements and does not require time for the separation of the gas components, such as in a gas chromatograph (GC). This provides a short response time and allows the identification of rapid changes to the gas composition during operation. By continuous measurement of the gas quality it is possible to operate the engines more efficiently and reduce fuel consumption.
Conclusion
The shipping industry will continue to look for ways to improve fuel efficiency and reduce emissions. This will require better insight of critical fuel parameters. Development of a better data analytics system and performance improvement tools will be important. However, to take full advantage of this system, it is critical to have access to fast and reliable multi-gas data, which the ship operators only acquire through installation of an online gas analyser on the fuel gas system.


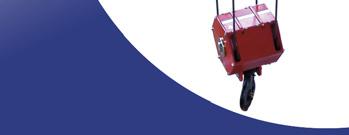




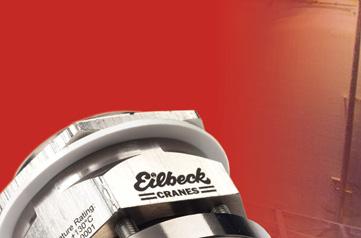
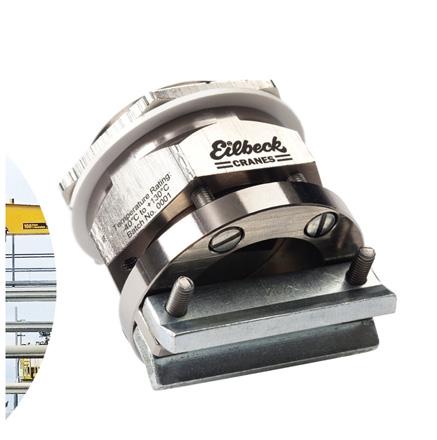
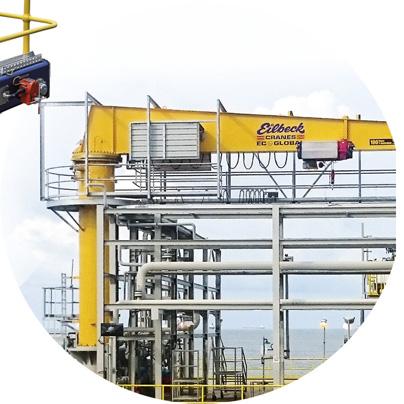