
9 minute read
Digitising the field
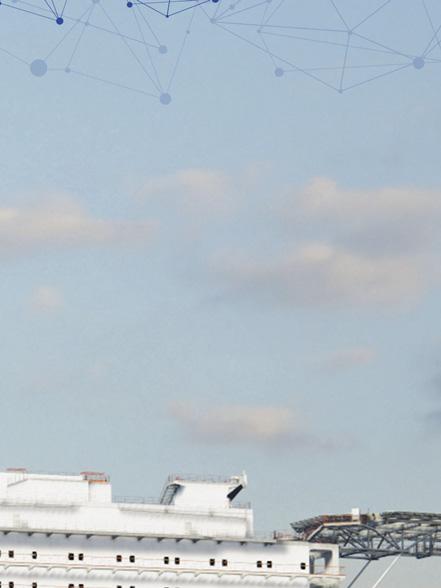
Figure 1. View of the high fidelity VR model of the FLNG in CETO® .
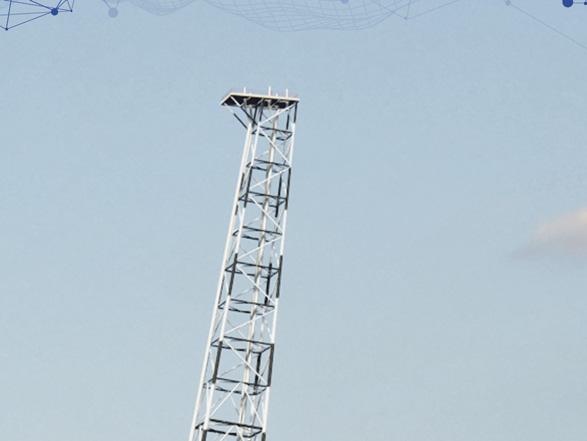
Ludwig Gross, Fabrice Rey, and Julien Métayer, Technip Energies, France, outline the available advanced solutions for collaborative operator training.
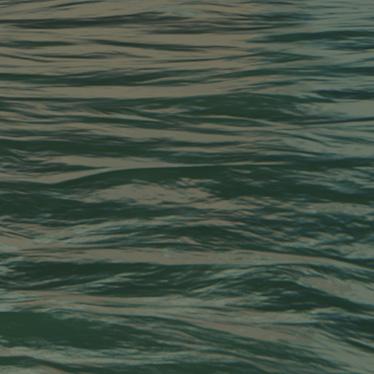
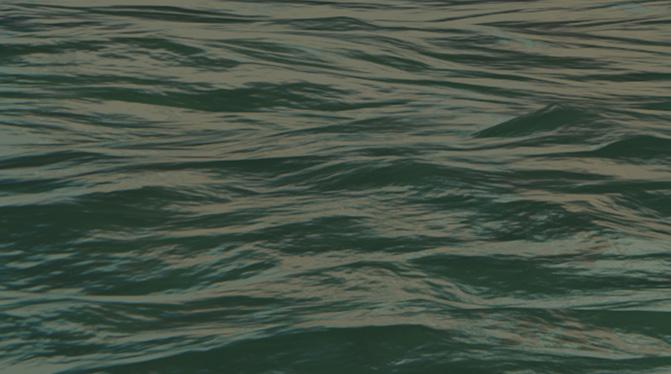

When it comes to plant safety and productivity, plant operators are key personnel. This is a fact well known to process industries such as LNG production. Plant operators are in charge of conducting operations efficiently and managing day-to-day production and upsets to avoid major incidents. Their skilled responses are essential for safe and profitable production management. With more complex plants in remote locations, operating companies face the challenge of finding new ways to train operators that are less costly and more efficient. Offering a digital induction to field operations or the acquisition of new skills without leaving the office is a personal development opportunity much appreciated by plant operators, particularly millennials. These smart and innovative training solutions assist plant management in mitigating the loss of knowledge and competencies following the retirement of the more experienced workforce.
For more than a decade companies have been using operator training simulators (OTS) on a routine basis. However, an OTS is dedicated to the console operator. Field operators must rely on on-the-job training (OJT). A major limitation of physical OJT is the increased risk from junior operators handling critical situations. In such events, the senior operator will have to take over control, limiting learning opportunities for the less experienced junior. To enhance field operator training, companies have been turning to immersive training simulators (ITS) in addition to OJT. Standard ITS is a valuable tool for maintenance planning and for

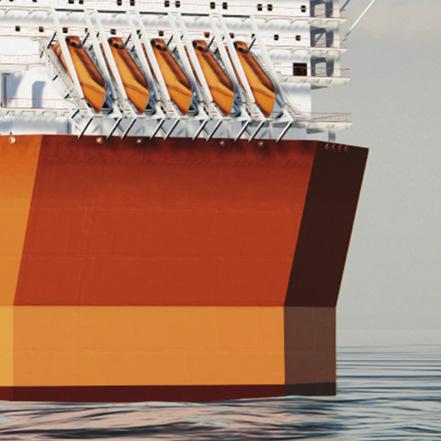
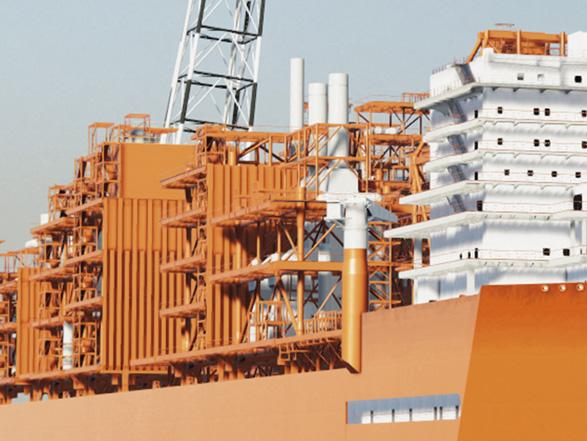
familiarising operators with plant topology. It will also cover the training on routine procedures and emergency response plans. However, it is currently limited to basic feedback from the plant. As such, the trainee will not be able to evaluate the consequences of his actions on the plant process.
A digital simulator training tool
A Plant Operator Digital Simulator (PODS) is a digital asset where actions performed in the virtual field or control room and their interactions are reflected accurately. It relies on the connection of the expertise gained in OTS projects and ITS project development and mitigates some drawbacks of each individual solution.
This training tool integrates two training interfaces, one dedicated to console operators and the other to field operators. Both interfaces access the same virtual environment in realtime. Trainees can practice collaborative scenarios between the field and control room. Most emblematic scenarios would be related to unsafe process conditions and critical operations, such as start-up activities. These activities require major field operation under control room supervision.
For the interactive simulation solution, Technip Energies stands on its proprietary interactive simulation platform. CETO® is built to provide the company’s project teams and clients an in-house solution to visualise 3D environments and interact with them in the most natural possible way. This involves a state-of-the-art physics engine that replicates the behaviour of the real world inside the simulation. It also requires a strong expertise in computer science to deliver user-friendly solutions based on technologies such as virtual and augmented reality. Last but not least of the cornerstones inside CETO is its capability to deploy massive 3D models in the scale of a whole plant, and optimise the workflow to achieve this. CETO has a strong track record in offshore operations including heavy lifts and ROV operations. Based on this experience and to widen its service market, Technip Energies has developed a complete in-house ITS product offering. As with most ITSs, it is capable of providing scripted reactions of the plant to the user actions. However, such scripted actions cannot provide a process realism at the scale of a plant or even at functional unit level. This is within the capabilities of the process simulation.
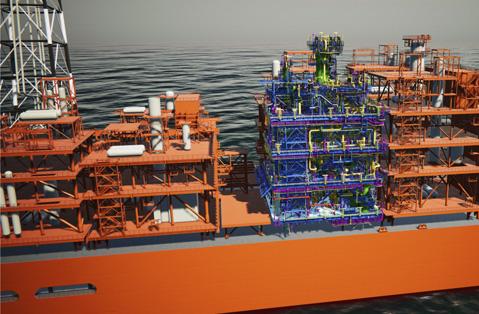
Figure 2. A VR model automated import from engineering 3D model.
Figure 3. Two simulators and two interfaces immersing operators as a single goal.
Relying on specialist teams
For the process dynamic simulation, Technip Energies stands on its specialists. The team has been developed with skilled personnel to offer a valuable in-house solution during project execution and operation phases. This involves dedicated specialists with a strong knowledge of the different tools available on the market and their preferred use cases. It also requires a detailed knowledge in process control and operations to deliver added value to project and operations. Additionally, the team provides increased flexibility during the engineering phase.
The team has a strong track record in engineering transient analysis in close collaboration with process engineers. Based also on its experience, Technip Energies has developed a complete in-house dynamic simulation lifecycle solution. Based on the engineering transient analysis, the specialist team delivers models for integration to the integrated control and safety system (ICSS). Technip Energies plays an active part in the virtual commissioning of the ICSS and the OTS delivery.
As Technip Energies hosts both CETO and dynamic simulation specialist teams, it has been natural to connect CETO to the process model to provide a fully realistic reaction of the plant response to the field operator actions. The field operator and the mechanical dynamics world are now connected with the console operator and its fluid dynamics world.
Beyond the interactive simulation solution and dynamic simulation team, Technip Energies leverages all the competencies of an engineering company. PODS has been the opportunity to develop internal add-ins to transform an engineering 3D model into a virtual reality model or to develop an in-house monitoring interface. In turn these developments open the way to new applications. Following PODS development and through internal synergies, it is now possible to remotely share a virtual reality during 3D model review, accompanying the increased importance of the human factor engineering for operating companies. Similarly, process simulation has developed light interfaces that are also used as plant production dashboards accompanying the digital transformation of the company’s clients.
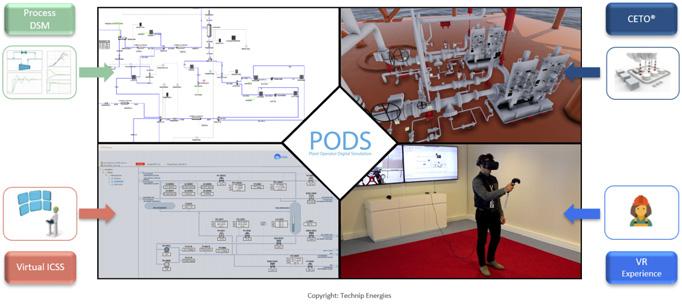
Technip Energies has designed innovative workflows to provide training modules for collaboration between field and console operators in a cost-effective way, multiplying the value for its LNG clients. In the course of the demonstrator development, it became clear that PODS is an ideal tool for other project activities. The activities identified so far cover the writing of start-up procedures, the development of augmented reality applications for field personnel, and the deployment of robots in unmanned facilities.
The writing of the operating procedures prior to start-up is a complex and time-consuming activity for all LNG projects. It requires senior operators to fully understand the design intent of the plant. They have to thoroughly go through all the project documentation issued by process and instrumentation and acquire an in-depth knowledge of the plant. This can lead to misalignments and misinterpretations. Within PODS, the operator is immersed in the final plant and confronts the simulated facility with his/her initial interpretation of the control and safety system, assumptions on the process response, and sparse understanding of the plant layout. This simulated facility confirms the behaviour of the automation, provides the proper feedback of the fluid dynamics, and exposes the operator to the reality of the physical environment. In this secure environment, the operator will perform the start-up operations with his/her initial grasp. PODS will record all actions and parameters. By reviewing the outcomes of the operations, the operator gains specific experience. The operator now can run an optimised sequence seeking the best efficiency and safety. Once the operator has stabilised the best sequence, PODS will generate a draft of the procedure, including all steps with explicit KPIs and validation criteria. During the peer review, PODS is available to the reviewer to run and stress test the procedure. By having a more robust procedure with PODS, the facility start-up is executed more efficiently, avoiding on-site trial and error and failure of critical equipment, and reducing start-up time to achieve earlier production.
In addition to the expected gains on traditional activities, PODS is also a tool that will assist in the deployment of other digital services. Among those services, PODS can address augmented reality and unmanned facilities and robotics.
ATEX grade augmented reality devices are reaching the market. Soon field operators in LNG plants will be equipped, but use cases are difficult to validate in the field, hindering any wide deployment. Much caution remains among operators who do not appreciate the operational gain of augmented reality as field tests are not performed. On the other hand, management is concerned about heavy deployment. It is apparent that return on investment (ROI) of such novel technology will require significant change management. The proof-of-concept strategy in this domain has reached its limits.
To target multiple sites, various facilities would require large IT infrastructures on each site. PODS proposes a solution to this problem: the augmented reality product will be simulated in PODS. All real-time data useful to the operator is computed in the PODS environment. The augmented reality application will deliver this data to the operator, multiple data configurations will be proposed, and any new sets of data could be tested easily. Moreover, the look and feel of the future augmented reality application will be tested. Operations and management will then validate the information selection and ergonomics of the application. This will feed the specifications of the augmented reality deployment to the site.
PODS infrastructure is extremely light. Deployment of PODS on multiple sites to evaluate the augmented reality solution on multiple teams can be performed in a very short time with limited costs. The two targets achieved are a strong evaluation of the ROI and an easier adoption.
For unmanned facilities, PODS also supports developments in robotics, serving as a training ground for robots. It will be possible to test procedures and record automated features. PODS can undertake all this in a cost-effective way long before the plant is completed. Once the plant starts operations the virtual environment is still available as a digital twin of the robot deployed in the field. PODS emulates robot behaviour to provide data to the supervisor software, such as Cyxpro. It will also assist in determining when human site intervention is required. These operations are conducted in co-operation with Cybernetix, Technip Energies’ robotics affiliate.

Summary
From the start, PODS was designed as a full digital twin for operators. It delivers high-fidelity computation of field, control room, and process conditions interacting in real-time. For major contractors, such developments in operator training can be a game changer. A contractor’s focus on industrial ROI instead of software profitability ensures maximised benefits for end users. As such, PODS is playing a key role in Technip Energies’ participation to the LNG industry’s digital transformation.
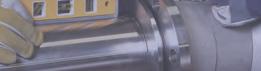


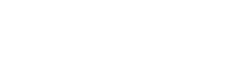
• Reduce Number of Expansion Loops • Longer Piping Runs with Fewer Joints • Increased Support Spacing IncreasedSupportSpacing • Reduce Boil-Off Gases • Lower Maintenance Costs • Double-Wall Vacuum Insulated DoubleWallVacuumInsulated la
Piping
MOST COST EFFECTIVE WAY TO TRANSFER CRYOGENIC LIQIQUIDS WE OFFER TECHNICAL ASSISTANCE FOR YOUR PIPE SYSTEM DESIGN EM DESIGN
INNOVATION. QUALITY. SUPPORT. EXCELLENCNCE