
20 minute read
Valves Q&A
LNG Industry
asked two companies to discuss some issues regarding LNG valves. VALVES
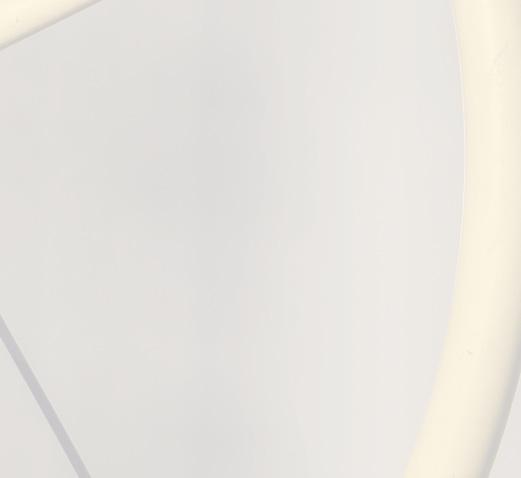
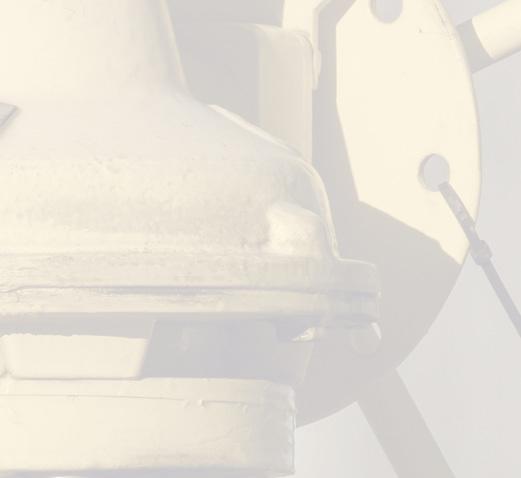
Matt Byers – Director of Product Management Brian Burkhart – Senior Product Manager
Baker Hughes
Matt Byers is the Director of Product Management for Consolidated Pressure Relief Devices, a pioneer in overpressure protection that delivers solutions to the increasingly high standards for safety, efficiency, and emissions reduction faced by the industries Baker Hughes serves. Matt holds a Bachelor of Science degree in Mechanical Engineering from Louisiana Tech University, US.
Brian Burkhart is the Senior Product Manager for Consolidated Pressure Relief Devices. Under his leadership, Consolidated has launched two first-to-market and patented products, representing a true technological step change in the overpressure protection industry: the 2900 Series Gen II Pilot-Operated Pressure Relief Valve and the 1900 DM Series Dual Media (DM) Dual Certified Spring-Operated Pressure Relief Valve. Brian holds a Bachelor of Science degree in Industrial Distribution Texas A&M University, US, and an MBA from the University of Houston at Sugar Land, US.
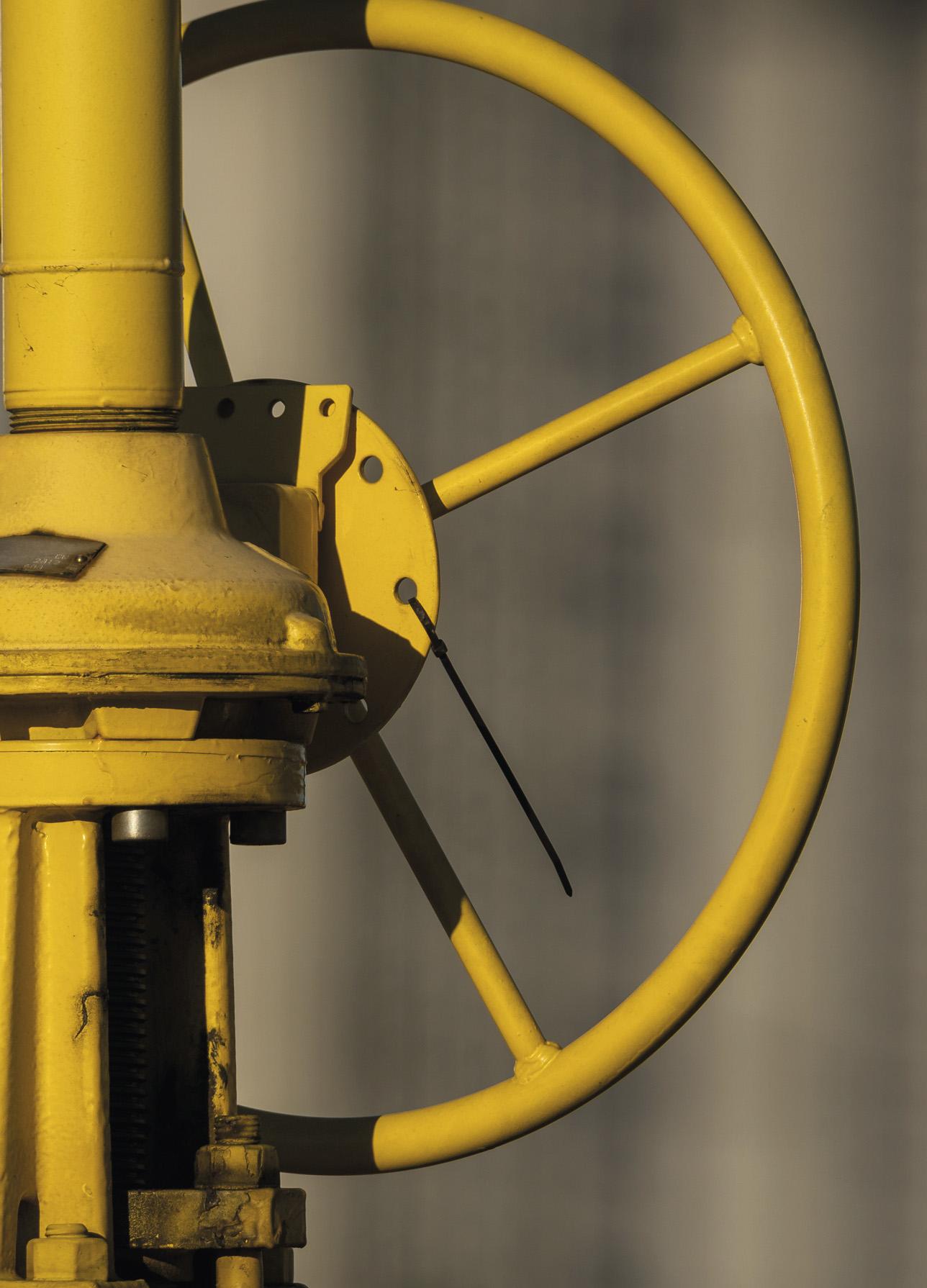
Reid Youngdahl – Valve Technical Specialist
Emerson Automation Solutions
Reid began working for Emerson in 2013 as an Applications Engineer, providing global control valve technical support for various industrial markets such as oil and gas, power generation, and original equipment manufacturers. Reid currently provides technical consultation for severe service control valve applications to optimise customer solutions. Reid is based at Emerson’s office in Marshalltown, Iowa, US.

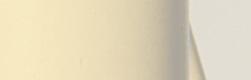


Why are valves considered fundamental devices in LNG operations?
Reid Youngdahl - Emerson Automation Solutions
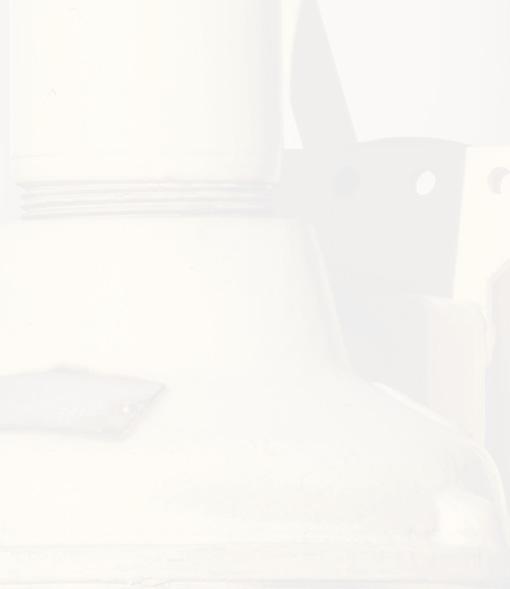
Control valves are critical final control elements within an LNG facility due to their direct impact on key performance indicators as they touch every part of the LNG value chain. Though often overlooked, properly specified control valves enable significant LNG process improvement, such as increased output with decreased energy consumption.
Critical control valve applications within an LNG facility begin with the control of pipeline natural gas into the facility through the inlet feed pressure let-down valves. Next, control valves are fundamental in controlling the process fluids around the absorber column to clean the gas, including the large pressure differential outgassing rich amine let-down control valve located at the bottom of the column.
Compressors located throughout an LNG facility are kept safe and running efficiently with anti-surge valves, which must provide fast and accurate control. Arguably the most critical valves in the facility are the Joule-Thomson (JT) control valves located around the main cryogenic heat exchanger (MCHE) as these have significant impact on LNG production. Finally, finished product LNG is loaded, unloaded, and regassed through control valves.

How is safety kept as a top priority in the design and fitting of valves?
Matt Byers & Brian Burkhart - Baker Hughes
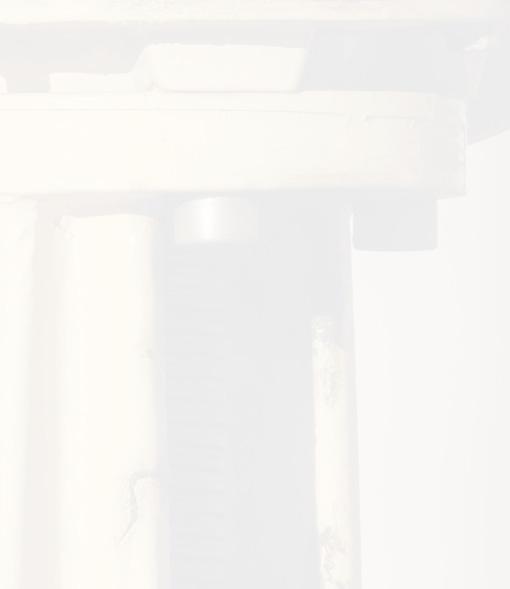

Pressure relief valves (PRVs) are inherently a safety device, so reliability must be unquestioned. Given the extreme temperatures characteristic of cryogenic applications, enhanced sealing features are required to ensure PRVs effectively perform their safety function. As the last line of defence to protect equipment and personnel from an overpressure event, valves must be constructed to minimise leakage and recover effectively from a relief event. Materials of construction, trim designs, and anti-galling measures are all critical considerations for design. Common problems include: Seat leakage: Thermal stress from low temperature causes material deflection. This deflection on a seating surface can result in leakage while the valve is closed, or immediately following a relief event. Galling of bearing/guiding surfaces: Anti-seize grease, commonly used in non-cryogenic applications to prevent galling, quickly deteriorates under cryogenic temperatures. This results in galling-induced wear between the metallic components, which leads to seat leakage, valve simmer, and ‘hang-up’ of guiding surfaces as the valve attempts to reseat following a relief event. Process loss and fugitive emissions: Seat damage as a result of prolonged seat leakage, premature opening as a result of major seat leakage, or the PRV not fully closing after a relief event due to excessive galling can all lead to unwanted and costly release or fugitive emission of process fluid.


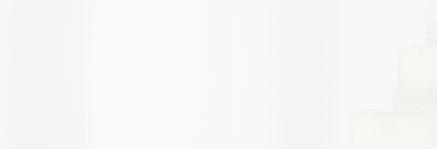
Baker Hughes: Consolidated™ Cyrodisc patented Thermolip technology.
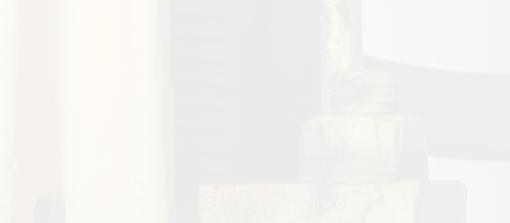
Reid Youngdahl - Emerson Automation Solutions
Emerson continues to focus on the safety and performance of its Fisher control valve and actuator products, including those destined for critical LNG applications. The company’s experts are dedicated to understanding not only normal operating conditions, but also extreme conditions encountered during emergency or transient events, along with the expanding global standards and regulatory landscape, to confirm the safety of our advanced product designs. Emerson has a wide range of materials available for customer selection so valves can safely operate in corrosive ambient environments, and when subjected to process fluid contaminants.
Extensive product design analysis and testing is completed to verify ultra-low fugitive emissions, tight shut-off, noise reduction and other performance characteristics critical to
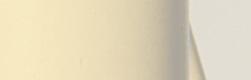


performance in cryogenic and other LNG applications. Consideration of safety is incorporated into every stage of the design and manufacturing process. Emerson’s commitment to safety in the evolving LNG industry protects the environment and reduces the risk of harm to end user personnel and process equipment.
Detail a challenging valve solution that required more ingenuity than normal.
Reid Youngdahl - Emerson Automation Solutions

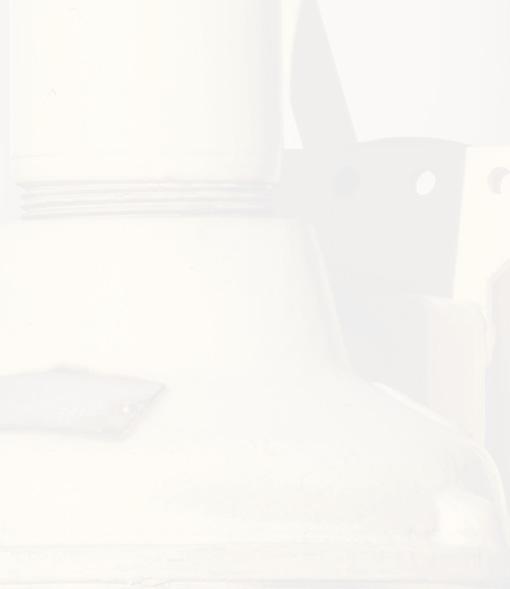
The main cryogenic heat exchanger (MCHE) is considered the heart of the LNG facility, so the JT control valves feeding the MCHE are considered the most critical of control valves. When specified and engineered correctly, licensed process controllers can operate optimally, resulting in increased LNG throughput with less energy use. On the flipside, the implications are great when these high-pressure differential cryogenic assemblies, inherently susceptible to poor throttling performance, are overlooked.
For example, an LNG facility identified that their current JT control valves were a key reason for suboptimal plant performance. Due to an excessive installed deadband, the large cryogenic globe valve assemblies were incapable of controlling to the required small step changes, inhibiting optimised licensed process controller tunings.
Additionally, mechanical assembly reliability issues were observed, such as insufficient extended bonnet lengths creating external ice formation that led to packing leaks and valve positioner stem linkage damage. The facility determined that new high-performance pneumatically operated control valves with strict dynamic performance parameters related to deadband, deadtime, and frequency response were the best path forward.
A complete engineering review was required to meet the necessary throttling performance. The holistic approach included proper severe service trim selection to minimise vibration caused by the high-pressure differential, as well as custom cage characterisation to ensure the installed gain of the assembly was ideal for the given process. Low friction cryogenic valve plug seals were designed to ensure good throttling performance while meeting Class IV seat leakage, as this amount of leakage was acceptable due to the continuous modulation duty in this JT application.
High performance double acting actuators, along with an expertly tuned Fisher FIELDVUE™ DVC6200 linkageless (magnetic feedback array) smart positioner atop a cryogenic extension bonnet, were supplied. To provide best performance, all JT control valve assemblies were dynamically tested while fully submerged in liquid nitrogen at -320˚F. Results exceeded expectations with measured small step change controllability for increments as low as 0.0625%.

Matt Byers & Brian Burkhart - Baker Hughes
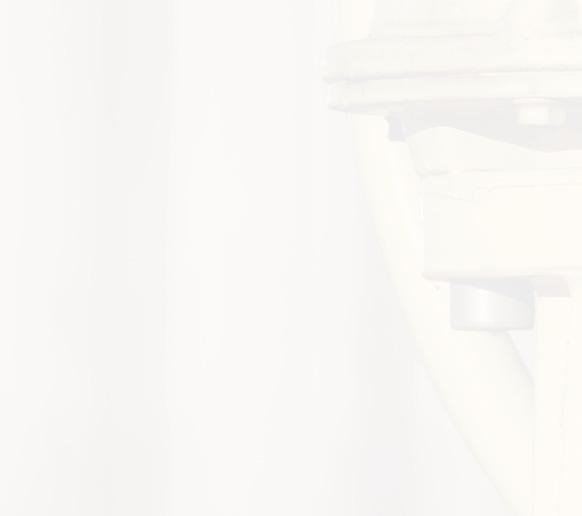
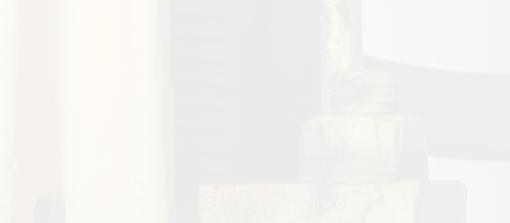
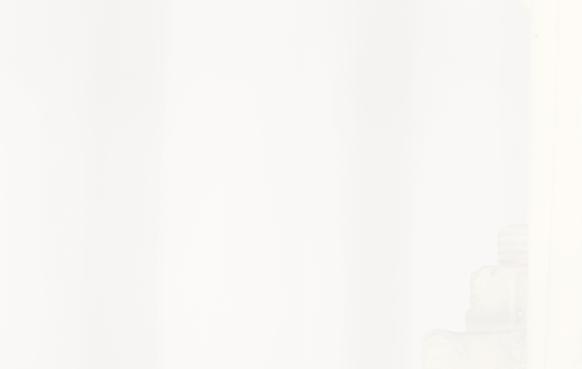
The typical failure mode of a PRV operating with cryogenic media is seat leakage after valve actuation, or when the operating pressure is close to set pressure. The product team at Baker Hughes for consolidated valves looked to high temperature PRV design innovations which have evolved over the last 100 years, mostly on steam applications, from their yoke/side rod constructions to their disc designs. Many of today’s PRVs designed for steam have unique disc designs which leverage thermal expansion principles to provide leak-tight performance at elevated temperatures. These high temperature disc designs have a thermolip feature which uses the temperature differential between the process fluid and ambient temperature in the body bowl to cause a downward deflection, providing more contact stress on the nozzle seat and creating greater seat tightness at elevated temperatures. Applying the same thermal expansion principles that have demonstrated and successfully proven leak-tight performance on high temperature applications, the Consolidated team designed a reversed thermolip Cryodisc. This reversed thermolip produces the same leak tight performance at cryogenic temperature as has been proven with high temperature discs at elevated temperatures. Emerson Automation Solutions: Fisher™ Digital Isolation™ Another common PRV problem in cryogenic applications valve assemblies, like the Fisher TOV solution, come with a that needs to be addressed is galling of bearing/guiding single SIL certification for the final control element assembly rather than SIL certificates for each component. surfaces that can cause seat leakage and potentially cause a PRV to fail to close off after a relief event. Anti-seize grease,
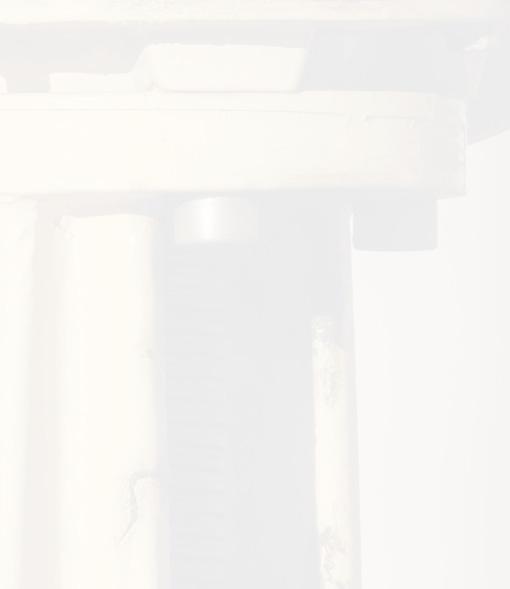

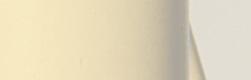


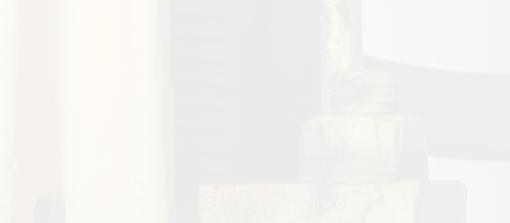
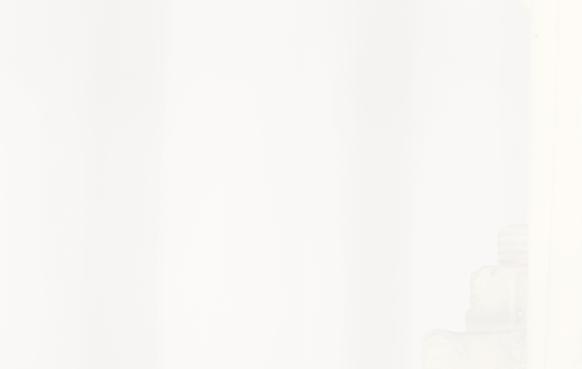
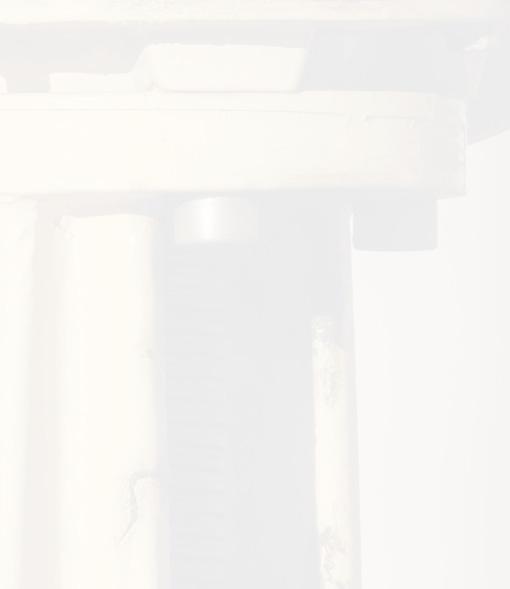
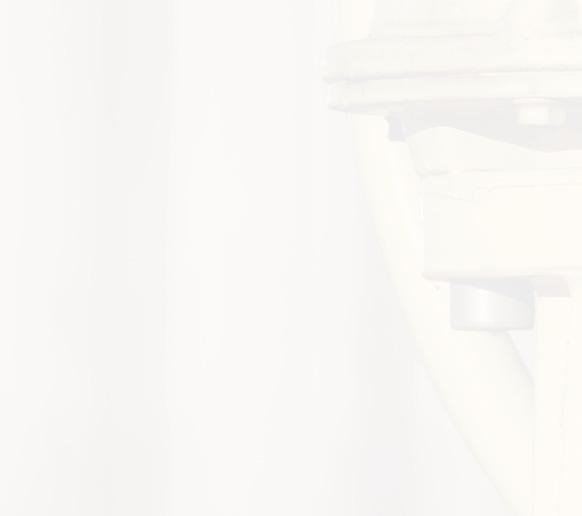
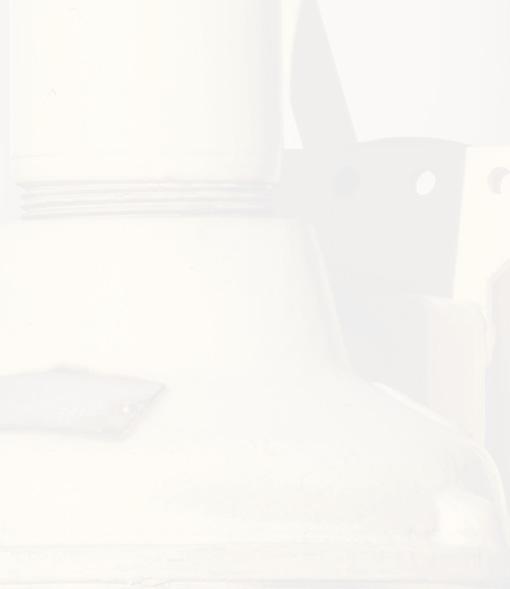


commonly used in non-cryogenic applications to prevent galling and provide lubrication, quickly deteriorates under cryogenic temperatures. This results in galling-induced wear between the metallic components, which leads to seat leakage and hang-up of guiding surfaces as the valve attempts to reseat following a relief event. A solution to address this issue is Titanium nitride (TiN) coating, which is an extremely hard ceramic material, applied to improve a substrate’s surface properties. It is applied as a thin coating, less than 4 μm, and is used to harden and protect metal to metal bearing surfaces and sliding/guiding surfaces. This coating eliminates galling, microwelding, seizing, and adhesive wear on critical PRV components. It has a very low friction, enhances corrosion resistance, and has erosion resistance. Applying TiN coating on critical bearing and guiding PRV components will improve seat tightness after a relief event on LNG and can save users on unplanned downtime, PRV repair costs, process loss, and excessive fugitive emissions.
Describe some recent developments in ensuring zero leakage and guaranteeing endurance.
Reid Youngdahl - Emerson Automation Solutions
Single sourced final control element (FCE) valve assemblies with one complete safety integrity level (SIL) certification to be used within a safety instrumented system (SIS) provide pre-configured online diagnostics to ensure reliable operation, with in-depth factory testing to ensure all devices are working together properly.
A holistic approach is critical when evaluating a valve’s ability to provide zero leakage, while ensuring endurance to high cycles. For example, the valve itself could be properly selected, but if the actuator were sized incorrectly with mounting brackets not designed to handle the maximum torque of SIS valves, issues may be created with maintaining shut-off throughout the life of the SIS assembly.
Single SIL certified and tested assemblies have improved actuator sizing processes and mounting bracketry, and along with factory acceptance testing these ensure the valve shuts off completely for as long as the assembly is in service.
Matt Byers & Brian Burkhart - Baker Hughes
The seat leakage standard for PRVs is defined by API 527 Seat Tightness of Pressure Relief Valves. In this standard, PRV leakage rates for metal-seated, spring-operated PRVs are deemed acceptable at rates as high as 100 bubbles/min. for a valve. This standard is applied and measured in a manufacturing or service setting to a valve that is in its prime condition, but does not address acceptable leakage rates for a valve that is installed and in service. In this condition, it is safe to assume that the valve will experience significantly higher leakage rates due to seat defects from PRV cycling, system debris, or slow erosion over time. By contrast, pilot-operated PRVs are allowed 0 bubbles/min. seat leakage across the main valve seat. This technology ensures zero leakage in the main valve with repeatable performance due to the nature of the valve design and use of a more forgiving seat in the form of soft goods. However, the API 527 standard fails to address the leakage that occurs out of the pilot portion of a modulating pilot valve. This most common design for a modulating pilot valve uses an antiquated modulating technology known as internal modulation, and is the most prone to fugitive emissions through the pilot under normal operating conditions. As this valve approaches set pressure, the pilot will anticipate the need to modulate by releasing a small amount of main valve dome pressure from the main valve and out of the pilot discharge. While this allows for modulation in the overpressure cycle, it has the negative side effect of fugitive emissions even when the valve is supposed to be in a zero leakage state. Consolidated valves offer a unique approach with their true zero leakage bolt-on modulating pilot valve technology. Instead of Emerson Automation Solutions: The Joule-Thomson anticipating an overpressure scenario and prematurely releasing main (JT) control valves are critical to achieve optimal valve dome pressure into the atmosphere, this design waits until set plant perf ormance. It must be capable of precise pressure is reached before releasing any pressure through the pilot throttling control in severe cryogenic temperatures at high pressure diff erentials. discharge, thus completely eliminating fugitive emissions from the PRV under normal operating conditions.
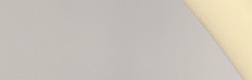

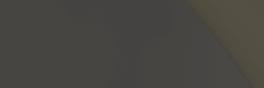
What are the current limitations of valve technology?
Reid Youngdahl - Emerson Automation Solutions

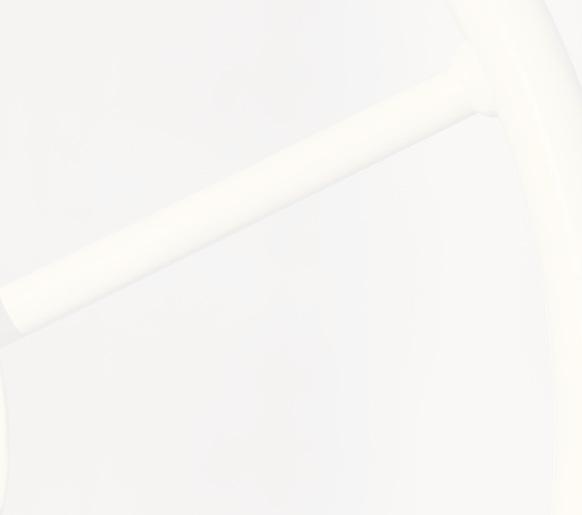
A common practice in the LNG industry is specifying cryogenic control valves to comply with on/off isolation valve seat leakage standards. This is possible, but at the cost of good throttling performance if not accounted for by the control valve vendor.
This situation primarily arises with large, high-pressure balanced cryogenic globe type control valves specified to meet on/off isolation valve seat leakage standards, such as BS6364. Balanced plug seals exist to provide the required seat leakage, but these can add a significant amount of friction to the assembly. If this friction is not properly accounted for, it can greatly inhibit the tight throttling performance of a control valve.
The critical MCHE JT control valves are inherently susceptible to this concern due to applications that often require large, high-pressure balanced cryogenic globe type control valves. The control valves can meet the project specified isolation cryogenic seat leakage requirements via factory acceptance testing, however installed dynamic performance of the valve may not be ideal for optimised licensed process controller tuning. These valves are continuously modulating when the LNG facility is running, thus it is important to ensure valves throughout the facility are being specified correctly.

Baker Hughes: Consolidated 1900 Series Dual Media (DM).
How has valve design developed over the years and where can you see future changes occurring?
Reid Youngdahl - Emerson Automation Solutions
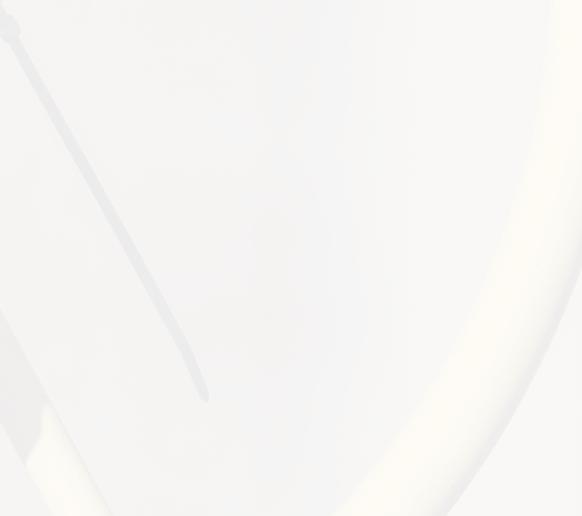
There have been many advancements in control valve designs to meet the severe service application demands of LNG facilities. The ever-increasing liquefaction million tpy export capacity of LNG facilities calls for larger capacity valves, specifically the inlet feed pressure let-down valves.
The inlet feed pressure let-down valves are critical as they begin the LNG process by controlling the pipeline natural gas entering the facility, with poor control valve performance often leading to serious downstream disturbances. The combination of large, highpressure natural gas transmission pipelines; increased required flowrates due to the ever-increasing liquefaction million tpy export capacities; and the requirement for providing good throttling performance has led to the development of tailor-made control valves.
Example facility designs have required multiple NPS 24 CL1500 globe valves with characterised noise attenuation trim to handle both high-pressure differential low flow and low-pressure differential high flow conditions. Further design enhancements to eliminate the high flow induced vibration coupled with non-ideal piping practices in large, high-pressure globe valves include the use of gridded seat rings to provide good flow control and ensure stable operation of the valve and downstream assets.
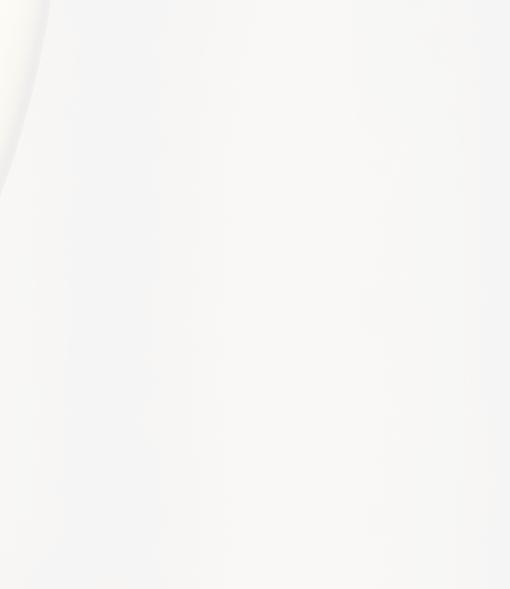
Do you expect there to be an increase in future demand for valves in a particular LNG application or facility?
Reid Youngdahl - Emerson Automation Solutions
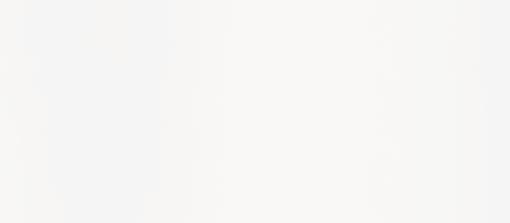
The demand for valve count and applications for a traditional LNG facility remain fairly flat, depending on the licensor and EPC. However, there is a possibility to see an increase in valve count based on sustainable efforts around carbon capture and sequestration. Many operating companies must now support company environment sustainability governance (ESG) efforts.
But the greatest shift in the LNG valve market space is desired support and the services provided by the valve vendor. Start-up and flushing trim can be utilised in the commissioning stage to decrease the time needed to install these valves, especially the critical ones, and to provide a safer plant environment with less crane lifts and man-hours required to get valves installed and operating correctly.
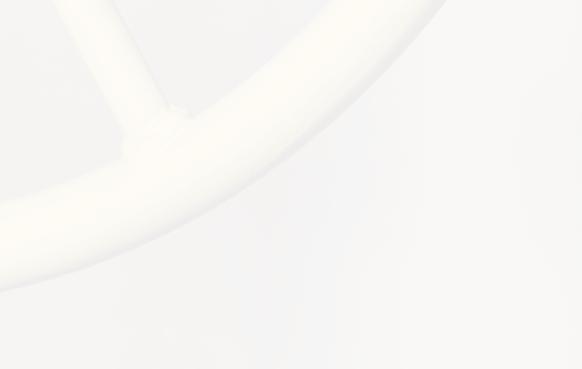
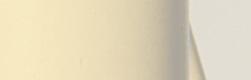


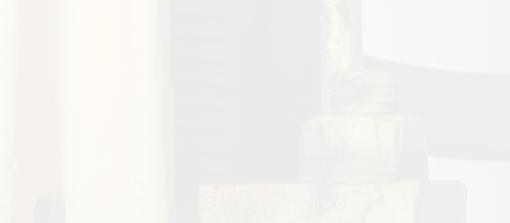
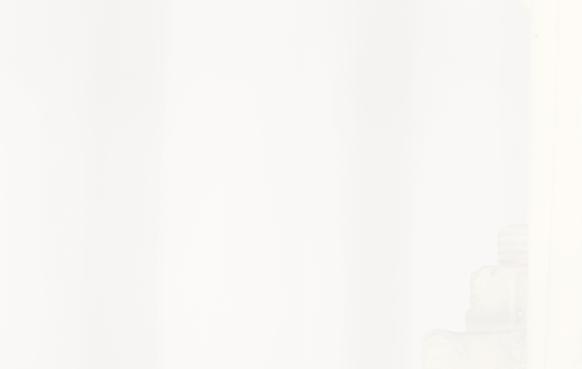
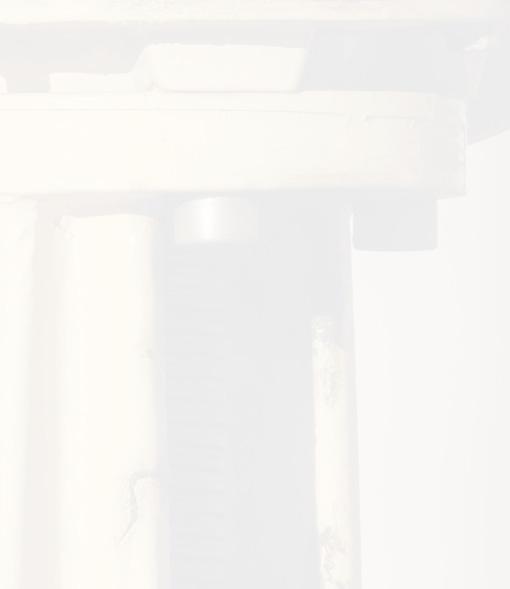
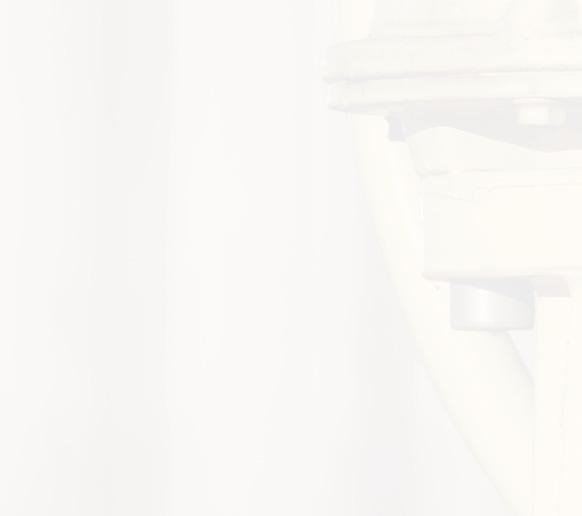
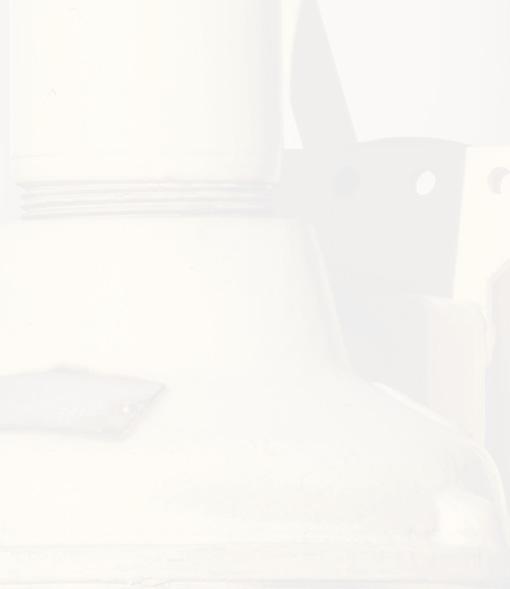


These start-up activities enable cost savings by protecting critical severe service trim sets, and by reducing the need for buying spool pieces and other piping materials to flush the system before operational trim is installed. Compressor anti-surge valve actuator assemblies can be shipped separately to reduce the risk of damaging these high-performance pneumatic accessories when the valves are installed to align the piping.
All these non-traditional needs can be satisfied to enable a successful, safe, and seamless LNG facility start-up.
As the world strives for decarbonisation, is there an opportunity cost between valve cost-effectiveness and applying fugitive emission technology?
Reid Youngdahl - Emerson Automation Solutions
In general, upgrading a valve assembly to a higher tier fugitive emission packing set is a marginal cost adder in relation to the entire valve assembly. However, the higher tier fugitive emission packing designs typically add significant friction to the assembly, which can lead to flow down implications.
Though the cost adder of fugitive emission packing itself is low, the additional friction may require larger actuation and additional accessories that add cost to the overall valve assembly. Another implication is the direct relationship of increased valve assembly friction and deadband. If not accounted for properly, this decrease in throttling performance can result in suboptimal process performance, thus adding additional operating costs to an LNG facility.
These complications make it crucial to select a control valve vendor whose technology expertly navigates the potential trade-off of performance and emissions mitigation techniques.
Matt Byers & Brian Burkhart - Baker Hughes
“Safety First” is the mantra when it comes to overpressure protection. After all, the primary purpose of a PRV is to act as the last line of defence for safety in the event of an unexpected overpressure event. With safety as the top priority, the overpressure protection industry has historically delivered safety solutions at the expense of fugitive emissions, process loss, and eroding profits. That being said, the technology available to the industry over the last century has largely been limited and slow to adapt to the changing needs and demands of the modern economy.
The workhorse valve of choice in the industry has primarily been the API 526 Spring-Operated PRV, and now has millions installed around the world. Based on spring-operated safety valve technology from the 1850s, this valve offers a proven and reliable solution when it comes to safety. However, its metal-to-metal seat design and excessively long blowdown in multi-phase/case relief scenarios make it costly in terms of process loss and unwanted fugitive emissions.
Pilot-operated PRV technology was later introduced in response to calls for increased operating efficiency and fugitive emissions reduction. This new technology was able to both maintain the safety standards of the API 526 Spring-Operated PRV while also allowing operators to run their system at higher pressures without experiencing seat leakage. However, it often came at a cost as upgrading old installed base to this new technology would require high levels of management of change (MOC) activities and piping modifications due to centre-to-face dimensional differences.
In 2020, Consolidated Valves released the new 2900 Series Generation II Pilot-Operated Pressure Relief Valve, an enabler for spring-to-pilot PRV upgrades that reduces emissions due to PRV leakage in an economical manner. This valve is able to retrofit or replace existing API 526 Spring-Operated PRVs to the latest in pilot valve technology while completely maintaining centre-to-face dimensions and almost completely removing MOC activities and their associated costs.
Explain the role of valves in helping to reduce emissions and keep energy consumption low in the LNG process.
Reid Youngdahl - Emerson Automation Solutions
Control valves can play a major role in an LNG facility’s decarbonisation goal to ship carbon-neutral exports. In addition to ensuring fugitive emission compliance within the valve assembly design, properly specified high-performance throttling control valves can reduce the overall carbon footprint of an LNG facility.
Examples include the JT control valves located around the MCHE, which have significant impact on LNG production. When properly specified, these control valves enable LNG process improvements, such as increased LNG output with decreased energy consumption. Fast-stroking, high-performance compressor anti-surge valves enable a compressor to run more efficiently by safely operating closer to the surge line. These increased process efficiencies, coupled with reduced process disturbances, result in less overall gas-to-flare instances, reducing product loss and protecting the environment.