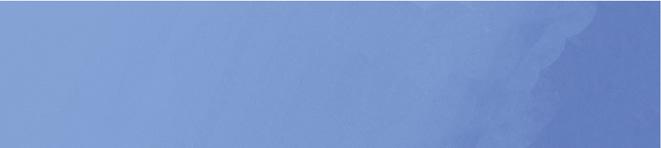
9 minute read
No situation too extreme
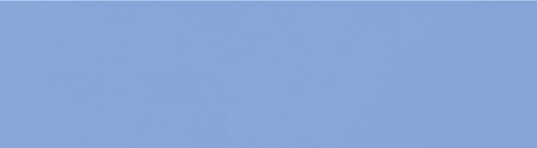
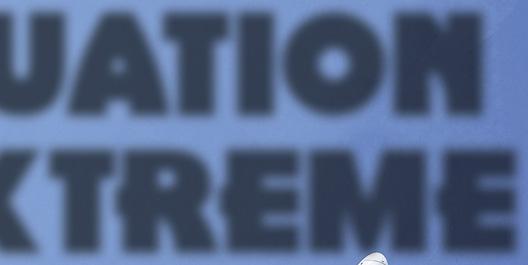
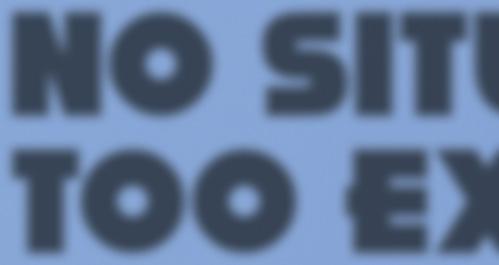
Scott Moreland, QUADAX Valves, USA, outlines the design considerations of valves to be used in applications with extreme temperature requirements.

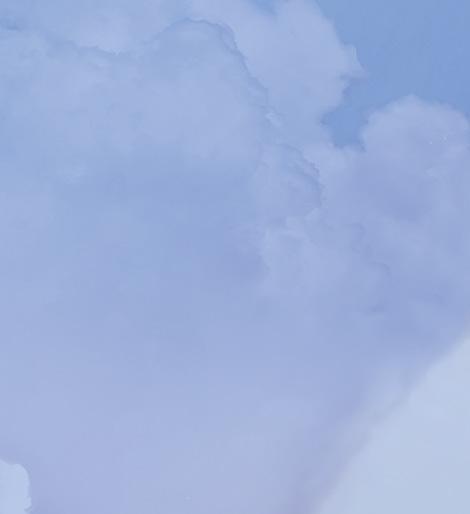
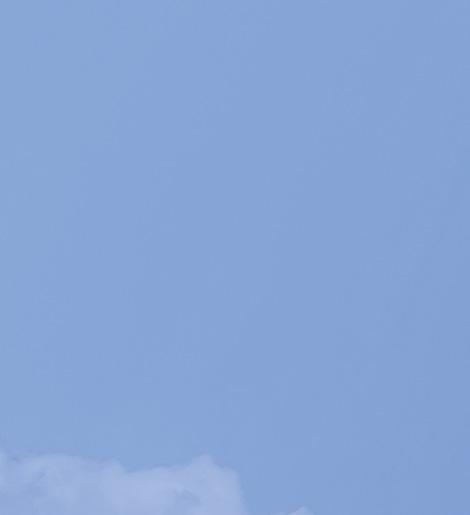
As most piping specialists know, LNG applications can be very difficult to control flow, and it takes a special design with specific materials to work in temperatures ranging down to -454˚F/-270˚C. A design and materials which cannot be utilised in most valve types. While both gate valve and ball valve designs have been utilised, they do not always provide the very best of results – zero leakage in on/off applications. Even most triple offset valves will not allow for zero leakage, due to the elliptical design of the port and sealing areas being most difficult to hold the most stringent sealing. That, coupled with fabricated designs which will be made worse whenever there is any deflection of sealing surfaces caused by pinned disc or inferior stem designs, mean there can be a very small window where a valve can seal perfectly. A four offset design valve allowing for a circular sealing surface, along with very low friction on the seals, will comply with the desired effect of allowing for zero leakage at low temperatures. This is true especially after a high number of cycles at very low temperatures while most other TOV’s have begun a process of increasingly leaking beyond acceptable levels. As a result of a four offset construction and state of the art manufacturing technology, QUADAX® Valves are designed to offer 100% compliance even with the highest tightness and extreme temperature requirements.
Now take those extreme applications and add the requirement to the reliability of functioning time and again sporadically in the unique application of refuelling a rocket with LNG/liquid hydrogen in less-than-ideal weather conditions, i.e. coastal locations. The frequency of the loading at the very low temperatures, the rough handling of the equipment given the surroundings and circumstances of quickly turning on/off the process, along with the outside temperatures and corrosive atmosphere of the coastal locations for launching pads, all give rise to very extreme conditions in which a valve has to operate without failing time and time again – high cycling. The leading aerospace companies in the US have found a strong business partner for their valve requirements and therefore the solution to maintaining zero leakage on/off operation in QUADAX Valves.


Figure 1. US aerospace group launching latest rocket with payload.
Space travel

In order to meet the constantly growing demand for the economic transportation of medium and heavier satellites for civilian purposes, the launching stations for orbital missiles are
continuously expanded. The fuelling systems are upgraded continually and have to be ready for processing at any given time. During the fuelling process, temperature swings are extreme, which must be addressed with a valving solution which requires complete and safe shut-off every time.
When it comes to refuelling that utilises LNG at less than -259˚F, aerospace companies have very well-defined specifications including special testing, special cleaning, and very durable material requirements. To assure zero leakage in these extreme temperatures in the refuelling process, a valve is required which is manufactured with a totally round seat and sealing geometry, along with other features which will provide positive sealing even if the materials are shrinking or expanding given the unique temperature differences throughout the process and from the environment. While other valve designs often fall short, the QUADAX Valve is designed to work in these very low temperatures, as well as in extremely high temperatures (up to 1472˚F).
Besides the negative environmental effect, excessive fugitive emissions could also have an impact on the security and safety of personnel. The operating companies of these launch sites are therefore paying particular attention to this fact and request an individual performance testing for the approval of cryogenic valves which shall be installed in their refuelling systems. QUADAX exceeds at these types of testing and most recently performed a special test combining the cryogenic test according to BS 6364 with an endurance test according to EN 12567. A QUADAX four offset butterfly valve DN 500 mm, ANSI class 150, was tested at the ITIS BV test laboratory in the Netherlands, specifying 10 thermal cycles with a fugitive emission test at 20˚C/68˚F and at -196˚C/-320˚F alternating. In addition, the requirement called for an endurance test, with 500 mechanical movements at -196˚C measuring the internal and external leakage after determined cycles. The benchmark in terms of the seat leakage was less than 3000 ml/min. for a valve of DN 500 mm based on BS 6364 and a maximum allowable fugitive emission of ≤1.0·10-3 mbar·1·s-1 at any time of the cycles. The valve was tested with helium at 19 bar test pressure whereas the seat leakage and fugitive emission was measured after 20/40/80/150/300 and 500 cycles.
As a result of the four offset design and a high precision in manufacturing, QUADAX Valves has provided once more the evidence of a remarkable performance in cryogenic applications.
The test institute, ITIS BV, certified that the seat leakage never exceeded a low value of 590 ml/min., and after 500 cycles zero leakage at all could be detected. Moreover, the fugitive emission at the bonnet and trunnion gaskets of the top entry valve never exceeded a value of ≤1.0·10-5 mbar·1·s-1. The round seat and sealing geometry of QUADAX Valves is a totally friction-free metal to metal design. Due to this round geometry, after several hundred cycles the seat and sealing ring is literally looped-in and can provide the highest tightness even if the material is shrinking and expanding due to extreme temperature differences.

Figure 2. Quadax testing to the latest cryogenic specifications and beyond.
Figure 3. The Quadax technical team works in clean room environments, modifying valves for use in aerospace applications.
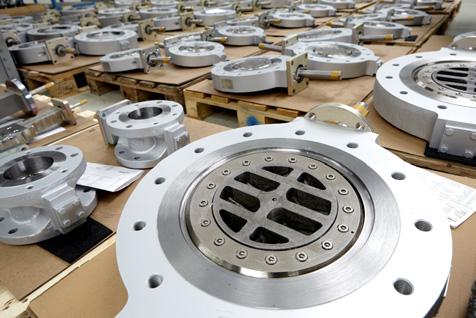
Valve offerings
The successful testing undertaken on the QUADAX brand valves, along with a broad range of size and configurations, provide the user in extreme temperatures with a go-to partner for reliable valves. The five configurations – lugged style, double flanged to ISO 5752, long patterned double flanged to replace gate valve face to face per ANSI 16.10, buttweld end design for welded into lines, and top entry design – allow for complete repairability when a valve is welded into place. These choices, along with piping size ranges from 2 in. (50 mm) to 72 in. (1800 mm) and pressure ranges from ANSI classes 150 - 1500, allow the user to pick the very best fit for their piping systems.
QUADAX’s four offset valves are designed to offer four key principles to the company’s customer base: Extreme temperature ranges. Homogenous materials allowing for same expanding/ shrinkage. Temperatures from -454˚F (-270˚C) to 1472˚F (800˚C). Large temperature swings are easy to handle. Superior tightness. Meet or exceed the most stringent tightness requirements. Bubble-tight even in cryogenic applications. Innovated and patented sealing design. Increased operational safety. Totally friction-free in sealing areas. Reduced risk of failures. No wear in sealing areas. Longer service life.
Reduced operating costs. Higher Cv/Kv values against other TOVs. Lower nominal pipe diameters. Lower torque requirements. Reduced maintenance costs (lower cost of overall ownership).
As a recent LNG customer found by switching to the four offset design, they now have valves in an older facility that are operating better and more efficiently than when the system was new. By switching from a side entry design TOV manufactured by a major valve manufacturer to the QUADAX design top entry, the customer’s people are experiencing less service issues and maintenance on the system; a safer environment with bubble-tight closing and lower fugitive emissions; and lower overall costs to the maintenance budget. This created a success story for QUADAX that has since been replicated at several subsequent user sites and has given a strong referral point for other LNG users to look to whenever they have valving decisions to make for safer, more efficient piping designs.
Designed for beyond Earth
As noted, QUADAX has found such partners in the aerospace industry who, after years of struggling with less effective designs, now specify a four offset valve into their system knowing that they are installing a more reliable and safer option. In the US where the aerospace programmes are now run by private companies in close co-operation with the federal space programme, the need for reliable and safe is at the forefront of all when installing systems for fuelling. Every major aerospace company has moved to using QUADAX in their most critical systems. These companies have found a willing partner that can provide them with peace of mind whenever they design and then install piping systems requiring proven dependability and topmost safe operation for their people and the coastal environments where launch pads are found.
The use of LNG/hydrogen in rocket fuelling systems require increased storage and processing of LNG, which has led to a need to have reliable valves in the piping systems. After years of experimenting and use of inferior products, the aerospace customers now require positive testing sometimes beyond what is referenced in BS 6364 where most triple offset valves can comply, although with much effort and for a short period – primarily during FATs. As provided by the ITIS BV testing, QUADAX more than exceeds the requirements of refuelling systems. Reportedly, the aerospace groups agree that QUADAX valves have been tested beyond the requirements set forth by BS 6364 and provide the best results when utilised in the fuelling systems, with a strong history of performance over years of practical applications.
At a spaceport there is a high technological infrastructure on which spacecrafts are launched. The fuel combination of hydrogen and oxygen, along with LNG temperatures, are mostly used in liquid fuel rockets today. Both in the production and storage of liquid rocket propellants as well as during the refuelling of the rocket, with such cryogenic fuel components having a temperature colder than -364˚F/-220˚C. Reliability and, of course, personnel safety are the top priorities. Even the smallest leakage can have disastrous consequences. That is why the company’s customers appreciate the four offset design, the high quality, and the know-how of QUADAX Valves.
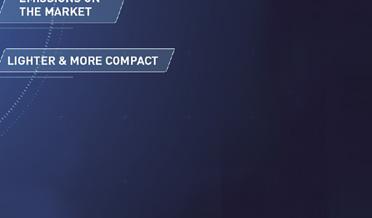

www.quadax.de

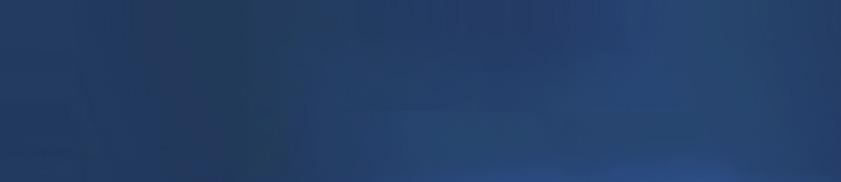