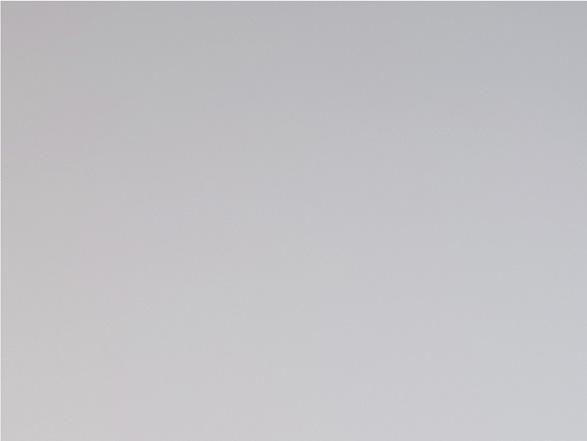
11 minute read
Balance the BOG
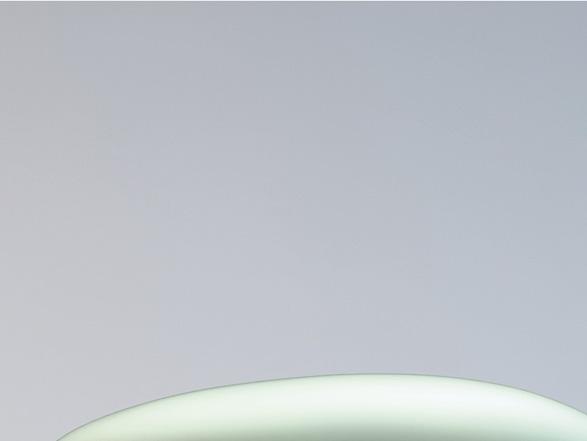

Maksym Kulitsa, Independent FSRU Operations Consultant, Ukraine, and David Wood, DWA Energy Limited, UK, detail the advantages of keeping boil-off gas well balanced.
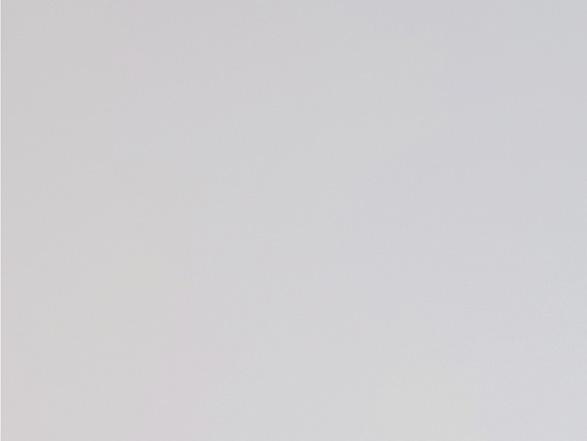
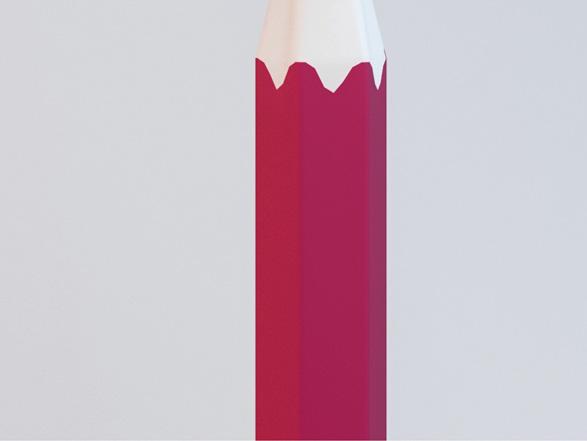
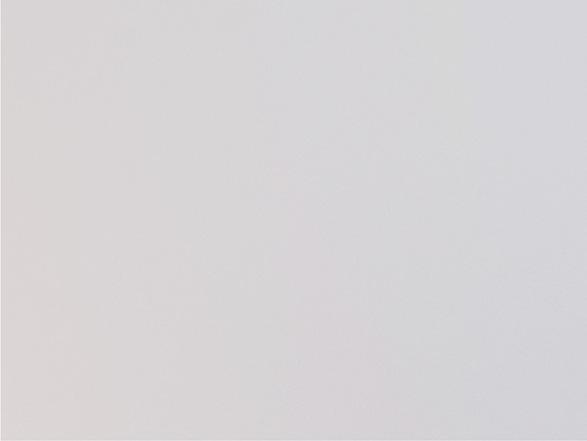
Today’s tendency in LNG marine transport is to minimise fuel spent and to maximise cargo delivered to discharge ports with minimum environmental impact. New technologies have made significant advances in reducing engine fuel consumption. The introduction of dual-fuel diesel electric (DFDE), M-type electronically controlled gas injection (ME-GI), and other fuel-efficient marine engines on LNG carriers, as well as improved LNG cargo tank designs have contributed to this improvement.
Total voyage consumption of LNG is not only dependent on engine efficiency; other voyage operations have an influence. Reducing the LNG heel required for tank cool down prior to arrival at a loading port reduces voyage LNG consumption. During cooling down at sea, excess boil-off gas (BOG) is consumed in the gas combustion unit (GCU) on DFDE or steam dump (SD) on steam vessels. Such consumption is wasteful and leads to atmospheric emissions. Minimising excess BOG therefore has commercial and environmental benefits.
The mandatory Ship Energy Efficiency Management Plan (SEEMP) (MEPC, 2016), EU MRV (EU Monitoring, Reporting and Verification of CO2; mandatory since 1 January 2018) and IMO DCS (IMO Data Collection System on fuel consumption; mandatory since 1 January 2019)1,2 all focus on fuel and emissions reductions. The SEEMP provides incentives to adopt more efficient LNG carrier operational practices in parallel with developing more efficient engine and ship designs.
Traditional procedures applied to cool down LNG carrier tanks prior to arrival at discharge ports are typically not best practice, because less LNG could be consumed for tank cool down. In some situations, liquid marine fuels are consumed to preserve sufficient LNG heel for tank cool down (e.g. during


delays or bad weather). Marine diesel, at approximately US$535/t in March 2021, is costlier than BOG and produces more atmospheric emissions.
More efficient LNG carrier tank cool down prior to arrival at a loading terminal can minimise LNG heel consumption. The proposed balanced-BOG method achieves this with most tank designs and is most effective with LNG carrier membrane tanks.
Cooling down cargo tanks prior to reloading
The typical scheme used to cool down membrane LNG tanks is intermittent spraying – twice a day for three days – prior to arrival at the loading terminal. The LNG quantity consumed in cooling down LNG carrier tanks at sea ranges from 800 m3 to 1600 m3 LNG. That typically involves three warm tanks and one semi-cold, LNG-heel tank. The quantity of LNG consumed in that process influences an LNG carrier’s commercial performance. Excess LNG heel consumption leads to the ship delivering less commercial cargo. The traditional method of tank cool down is convenient but wasteful. Some LNG carriers also consume marine diesel in their engines to save enough LNG heel for tank cool down, thereby increasing operating costs.
Applying a high-spraying regime for short periods increases the tank pressure to approximately 65% - 70% of tank maximum allowable relieve valve setting (MARVS), which is 250 mbarg. At that point, spraying is discontinued to allow time for consumption of the resulting excess BOG generated by the engines, GCU or SD. Such a cooling-down schedule leads to high LNG heel consumption. The BOG extracted between spraying acts to cool the warming tanks and the LNG heel in the tanks (Figure 1), thereby contributing to extra consumption. Repeatedly cooling and warming tanks between spray sessions consumes approximately 300 - 400 m3 of LNG, that is approximately 30 - 50% of the LNG consumed in the traditional cool-down regime.
The minimum LNG required to cool tanks alongside a terminal involves spraying for approximately 10 - 15 hours, depending on the tank type. LNG consumption for cool down at sea is double that quantity. Some operators, for expediency, allow higher cooling rates than cool down tables for the LNG carriers recommend. This causes excessive thermal stress and risks structural damage to the tanks and their pump towers, so is poor practice.
Manufacturers’ cool down tables assist in estimating the LNG heel quantity required for tank cool down during ballast voyages. Adjustments are required for higher heating value (HHV) of the specific LNG cargo composition. Incorrect estimates can result in an LNG carrier arriving at a loading terminal with more LNG heel than necessary (e.g. up to 0.6 - 1.0% of total cargo capacity), reducing the quantity of LNG that can be loaded. On the other hand, insufficient LNG heel available could lead to rejection of the ship at the terminal because its tanks are too warm, and/or the consumption of expensive liquid fuel that is needed to complete the tank cool down. Both outcomes degrade an LNG carrier’s commercial performance. The proposed BOG-balanced method of tank cool down at sea can avoid such situations and substantially reduce LNG consumption.
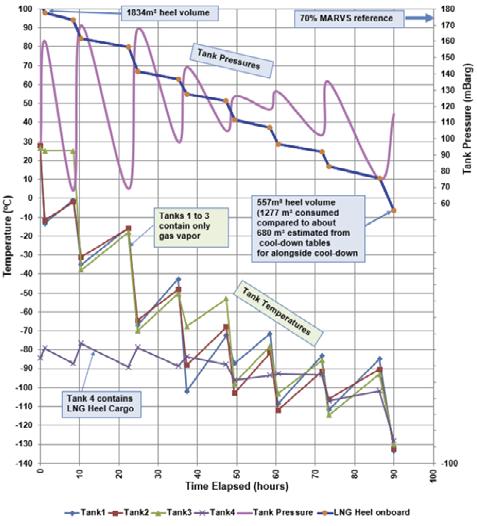
Figure 1. Example of traditional LNG carrier tank cool-down sequence at sea: 92 hours requiring approximately 680 m3 of LNG to evaporate.
Figure 2. Typical performance curve of LNG spray nozzles used in GTT tanks.
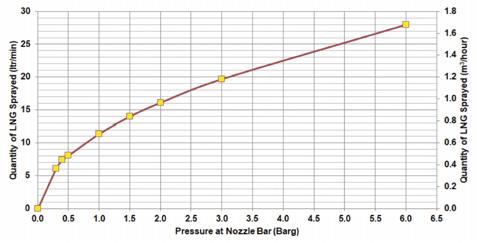
BOG-balanced tank cool down at sea
This method exploits some BOG generated being consumed in the engine room, GCU, or SD with continuous tank spraying at slow rates. Ballast LNG carrier voyages typically follow two patterns: vessel moves at high speed during the cool down regime; or vessel cools tanks down at anchor or at slow speeds. The LNG carrier’s propulsion system (plus GCU or SD capacity) define the BOG quantity/rate an LNG carrier can handle (m3/hr). Continuous, slow-rate tank spraying with LNG enables the engine (plus GCU/SD, if required) to immediately burn the excess BOG, while maintaining constant tank pressure. Moreover, BOG consumption estimates are simplified using manufacturers’ cool down tables. The cooling energy stated in million/Btu units in the cool down tables is divided by HHV (in million/Btu) of the actual LNG heel. This ratio determines the quantity of the specific LNG onboard that needs to be evaporated to cool tanks to ‘ready-to-load’ temperature, i.e. approximately -130˚C for GTT tanks.
Knowing the total LNG required to cool the three warm cargo tanks and the semi-cold heel tank, and knowing the expected total possible gas consumption (by engine/GCU/SD)
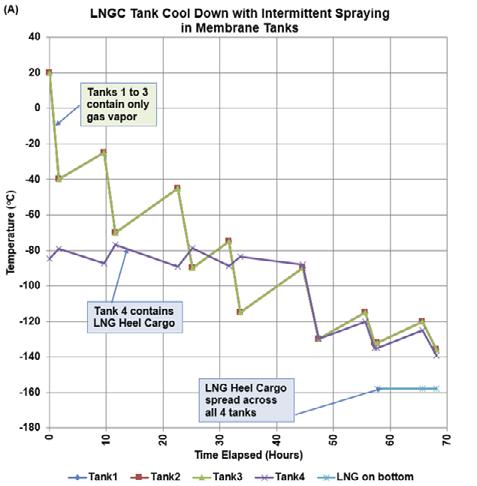
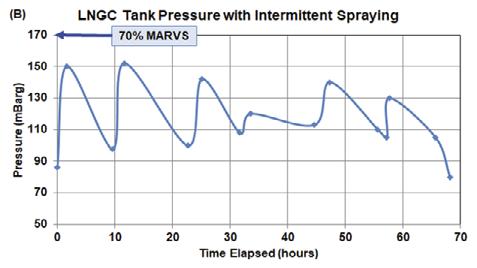
Figure 3. Typical record trends of tank (A) temperature and (B) pressure for the traditional three days of intermittent at sea cool down for membrane tanks.
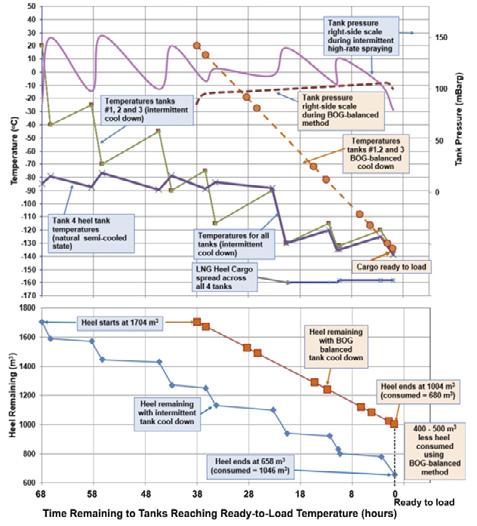
Figure 4. Comparison of traditional (intermittent) three-day tank cool down with BOG-balanced continuous tank cool down at sea. for voyage conditions, the time needed for tank cool down is readily estimated. Specifically, to derive the tank cool down time required – the quantity of LNG consumed to achieve a ready-to-load temperature, less extra accumulated vapour in the tanks, is divided by the available BOG handling capacity rate. This varies depending on voyage conditions. A uniform, slow LNG tank cool down rate for all tanks can then be applied continuously for that time period. That slow rate will be safer (less thermal stress) than faster cool down rates.
To cool an LNG carrier’s tanks down from 30˚C to -130˚C, approximately 680 m3 (approximately 306 t) of LNG is required. Some vapour accumulates in the tanks at the colder state. The total mass of accumulated vapour in the tanks will be approximately 278 m3 (approximately 123 t) for a 160 000 m3 capacity LNG carrier. Thus, only 183 t of BOG needs to be evacuated from the tanks. The time required for balanced-tank cool down at 5 tph BOG rate would be approximately 37 hours, requiring continuous LNG tank spraying at an average total rate of 18.5 m3/hr. Spraying would need to start 37 hours before approaching the terminal. A balance is maintained between the LNG tank spraying and excess BOG extracted from the tanks. Depending on the nozzle spraying pressures, nozzle configurations and spraying regimes, the LNG sprayed in a single tank can vary from <10 m3/hr to >40 m3/hr. The number of LNG spray nozzles and their spraying capacity determines the appropriate spraying pressure in each tank (Figure 2). The cooling progress is easy to monitor and control, cooling the tanks at 4 - 5˚C/hr from 30˚C to -130˚C within 37 hours.
The exact LNG quantity allocated for tank cool down should also take into account some spare capacity as contingency for vessel delays causing the cooling period to lengthen. Heat ingress into the tanks and loading pipework also need to be considered. Some additional time should be allocated for LNG heel to be transferred into each of the cooled tanks after cooling down, if necessary. Typically, a minimum of 6 - 10 cm of LNG on even keel should be maintained in each tank to keep them cool. Adjustments for these factors lead to a more accurate minimum LNG allocation for tank cool down.
The BOG-balanced method plans to achieve ready-forloading tank temperature conditions on the arrival moment at the loading terminal or, ideally, close to the moment that the loading gauge opens. In which case, it is not actually necessary to transfer heel LNG into the cooled tanks. This means that even less LNG and time are consumed for tank cool down purposes.
Figure 3 illustrates the temperature and pressure trends established during a traditional three day intermittent LNG carrier tank cool down at sea, where it consumed approximately 1046 m3 of LNG.
Figure 4 illustrates the BOG-balanced tank cool down method, where only approximately 680 m3 of LNG is consumed, i.e. approximately 65% of that consumed using the intermittent method. Figure 4 also compares intermittent LNG carrier tank cool down (three days cooling in advance of arrival) with BOG-balanced tank cool down. The latter results in a 4 - 5˚C/hr continuous temperature descent with no need for LNG heel transfer. The BOG-balanced method is faster (37 hours vs 68 hours) and consumes approximately half the LNG heel, while providing fine-tuning of tank pressure.
By using approximately 500 m3 less LNG for tank cooling down for each ballast voyage, the approximate commercial
benefit of the BOG-balanced method would amount to US$588 600/yr for an LNG carrier making 10 voyages, assuming a delivered sales gas price of US$5/million Btu and an energy conversion for LNG of 23.54 million Btu/m3 .
Benefits of a BOG-balanced cool down of LNG carrier tanks at sea include: Tank cool down can be optimally and safely controlled with minimum LNG heel consumed, improving commercial performance. Only simple calculations involving LNG quality and voyage schedule, minimising operator error in heel estimation and training requirements. It provides flexibility for adjustments relating to inevitable schedule changes. Spreading LNG heel among tanks can minimise tank warming if loading delays occur, facilitating jetty re-cool down within the charter party laytime allowance. Cool down can be temporarily halted without the risk of venting over-heated vapour while maintaining tank pressure below 70% MARVS. At low or zero vessel speeds, each tank can be sprayed more intensely in frequent bursts, one tank in turn, for short periods. This minimises the total time that each tank is allowed to warm and can be synchronised to prevent tank pressures rising above 65 - 70% MARVS due to vapour expansion. Slower spraying means less nitrogen consumption during tank cool down. Lower spraying pressures at tank temperatures above -140˚C do not cause LNG accumulation in the tanks.
The method reduces the quantity of LNG heel required in vessels fitted with reliquefaction equipment.
Conclusion
Most LNG carrier operators have yet to unleash the full potential of modern vessel designs to improve efficiency and reduce emissions. The BOG-balanced tank cool down method at sea prior to reloading makes such commercially beneficial improvements by ensuring minimum LNG heel consumption. It is sufficiently flexible to cope with changing operating conditions and loading schedules, working particularly well with membrane cargo tanks due to their spray nozzles configuration. The method’s effectiveness could be further improved by modifying one spray coil per tank to have fewer spray nozzles for even more effective and flexible slow-rate spraying.
To learn more about the BOG-balanced tank cool down method, read the remainder of the article by visiting www.lngindustry.com
References
1. DNV-GL. 2019. EU MRV and IMO DCS. 2. ICS-Shipping, 2015, ‘European Union Monitoring, reporting and verification (EU MRV) regulation. International Chamber of Shipping Guidance. 3. MEPC, 2016, ‘Guidelines for the development of a ship energy efficiency management plan (SEEMP).’ Resolution
MEPC.282(70), adopted by Marine Environment Protection
Committee, 28 October 2016.
ADINDEX
Advertiser Page
American Tank & Vessel 37
ACME Cryogenics 45
Canada Gas & LNG 50
Chart 05
Corban Energy Group IFC
CTCI 20
Eilbeck Cranes 41
Elliott Group 15
Gastech IBC
Golden Pass LNG 19
Howden 24
Indra Srl 41 Advertiser Page
Linde Engineering 11
LNG Industry 53
Müller Quadax GmbH 31
NIKKISO 02
REMBE GmbH 42
Temati 27
Technip Energies OBC
TGE Marine Gas Engineering 23
TMEIC Corporation Americas OFC, 49
Uniper SE 13
Zwick Armaturen GmbH 35