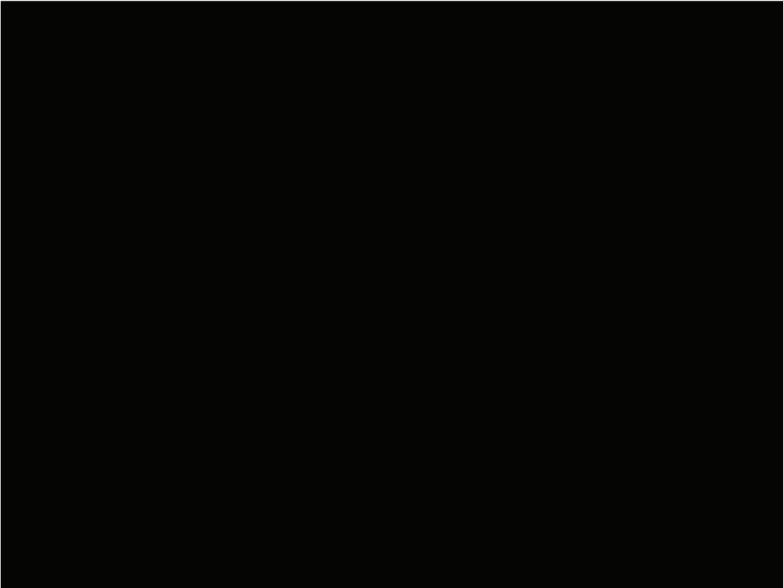
8 minute read
The devil is in the detail
Andreas Hofmann and Willem van Strien, SGS, the Netherlands, discuss new technologies for reservoir characterisation and field and facility health monitoring.
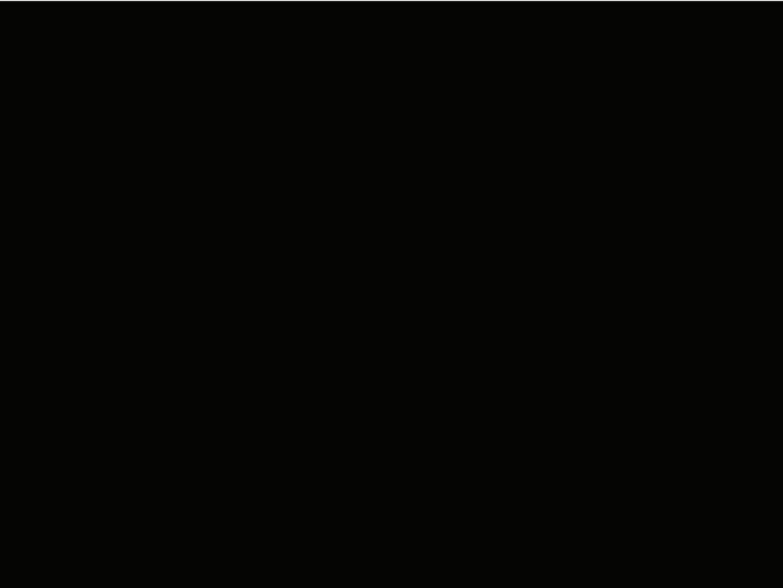
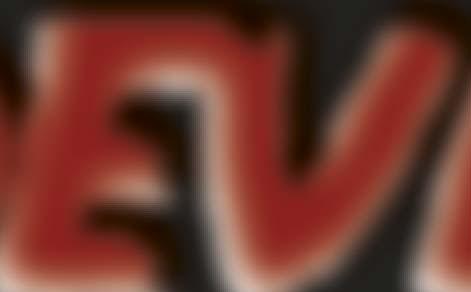

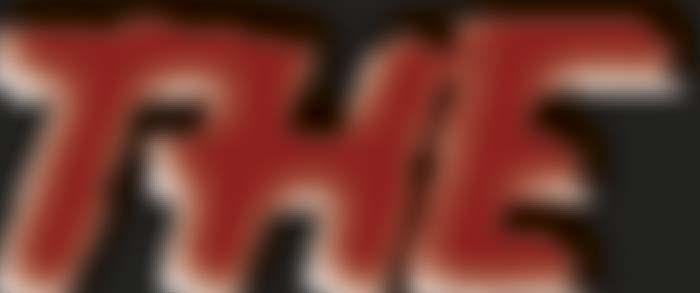
The need for low-cost solutions and enhancing the sustainability of existing facilities and infrastructure in the oil and gas industry has promoted the development of numerous technologies for reservoir characterisation, production optimisation and the monitoring and preservation of well and facility integrity.
In recent years, the development of laboratory analytical techniques has also resulted in an order-of-magnitude increase in resolution and precision. The commercialisation of techniques, which previously were only designed for academic applications, has triggered significant innovation in the oilfield services sector.
High-tech analytical methods now allow for more reliable petrographical, petrophysical, geo-chemical and rock-mechanical analyses of rock fragment sizes smaller than even 0.1 mm.
These developments in turn triggered a significant growth in the use of cuttings, a byproduct of the drilling process rarely used in the past. Apart from solid cores, drill cuttings are oft en the only tangible rock samples coming
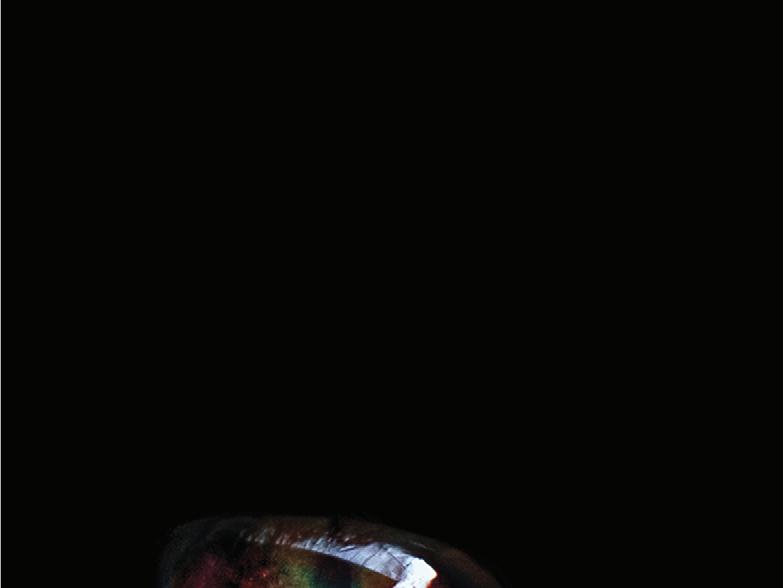
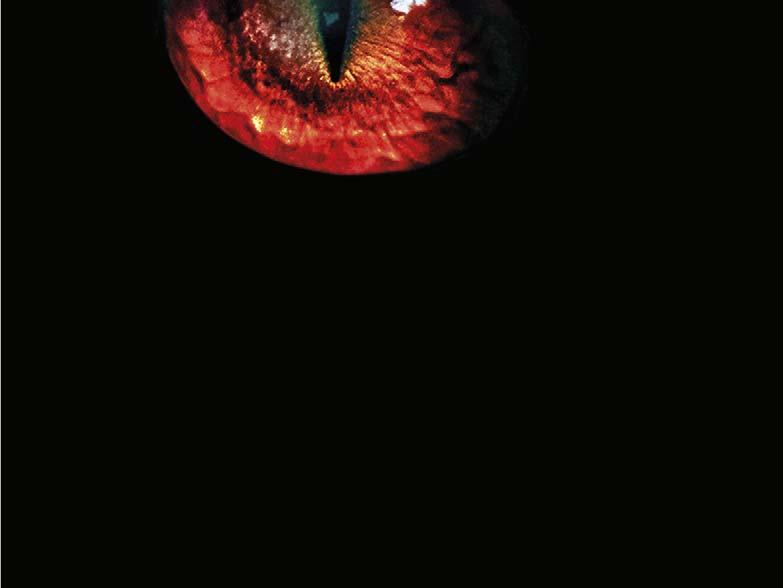
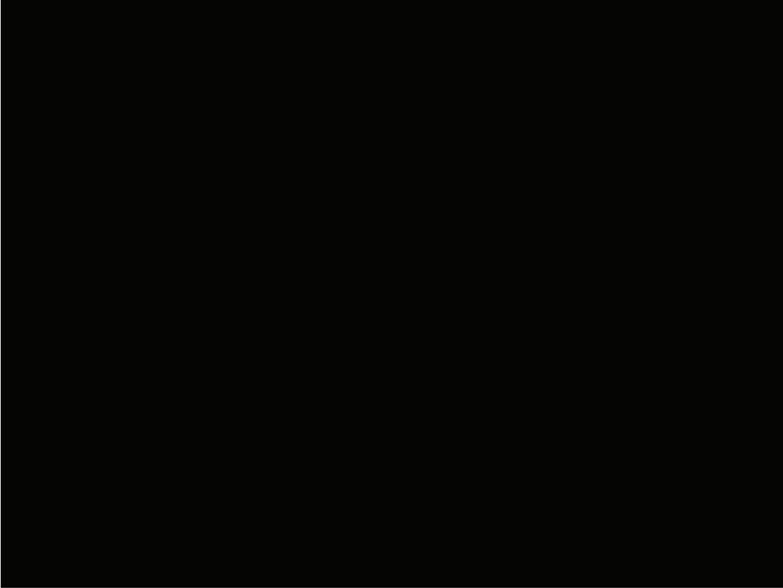
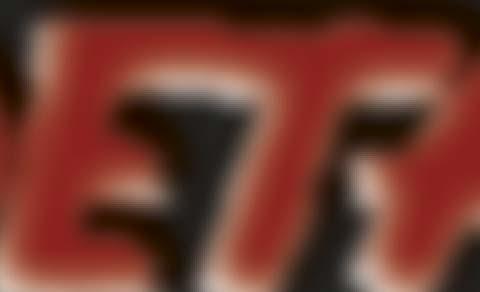
from the subsurface. The routine application of these novel technologies to cutting material is set to lead to a reduction in core acquisition and subsequently have a substantial impact on the cost of drilling.
In combination with wireline and measuring while drilling (MWD) logs, the data acquired from cuttings can be used for reservoir characterisation, geomechanical models and the detection of reservoir heterogeneities.
It is not only geologists and petrophysicists who benefit from detailed mineralogical assessments of solids (e.g. rocks). High-resolution chemical and mineralogical analysis technologies also help production engineers and production chemists to analyse the chemical and mineralogical composition of scales, produced particles (e.g. sand) and the products of corrosion. The monitoring of contamination levels and the changes in the chemistry of the solids and fluids helps to detect potential plugging risks and erosion/corrosion processes at an early stage and to optimise mitigation programmes. Both corrosion and scaling are threats to the safe and economic operation of oil and gas assets.
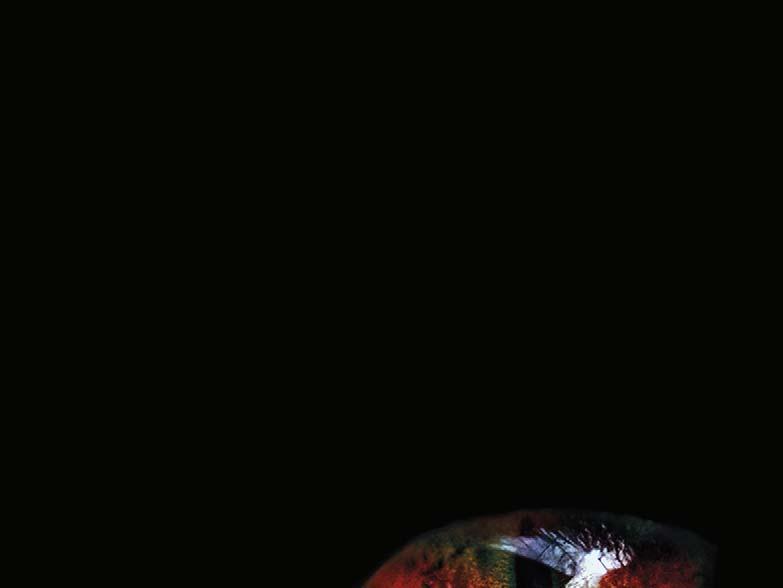
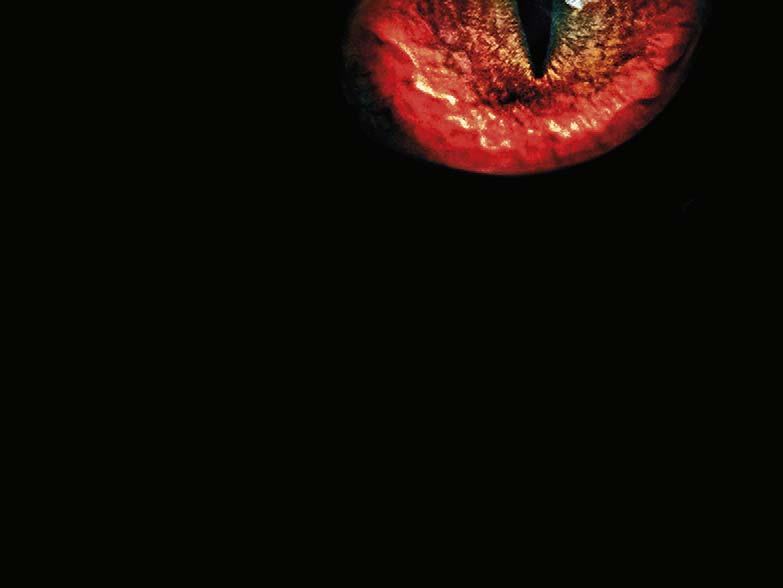
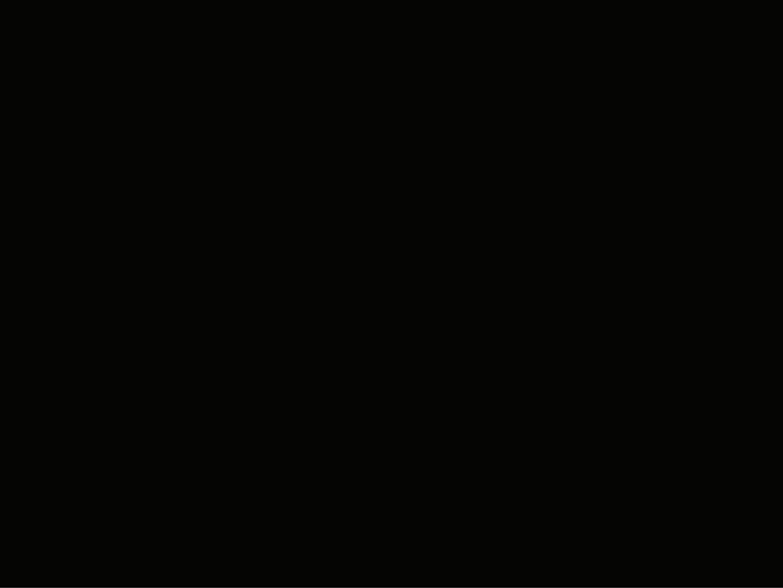
The development of low-cost and fast turn-around microbial DNA analysis technologies in the last decade, such as next generation sequencing (NGS), ushered in a new era for the oil and gas industry.
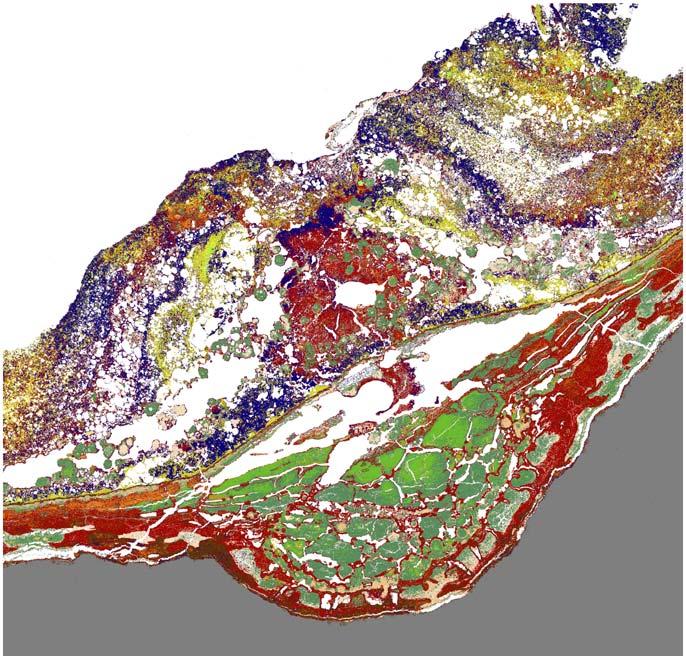
Figure 1. QEMSCAN image of pit caused by microbial attack. Pit depth is approximately 3 mm. Red and green indicate diff erent iron-(hydr)oxide minerals with varying levels of chloride. Dark blue is siderite and yellow is iron sulfide.
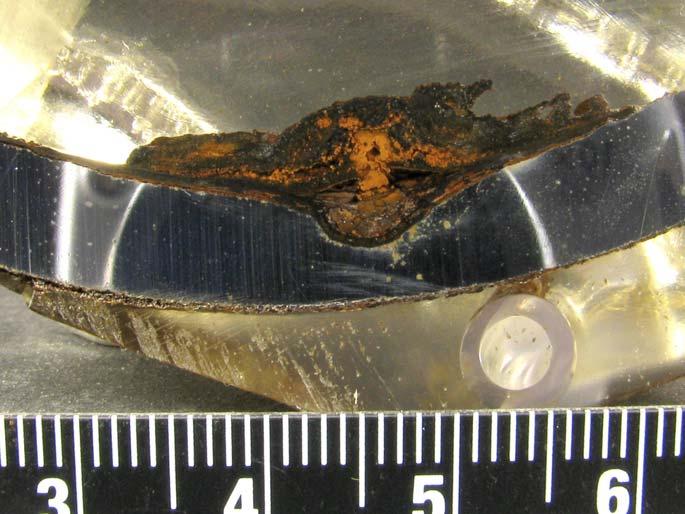
Figure 2. Cross-section showing MIC. This pit developed below a tubercle.
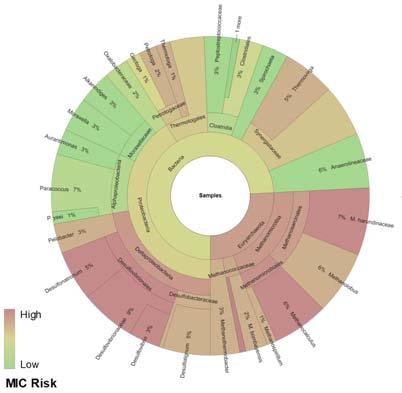
Figure 3. Krona plot showing the microbial assemblage at the corrosion site acquired through NGS indicating MIC risk.
By applying NGS technology on cuttings and reservoir fluids, it has been realised that oil and gas reservoirs and production facilities have diverse microbial ecosystems. The determination of microbial population diversity and metabolic pathways gives insight into reservoir health and the integrity of operation facilities.
The application of microbial DNA technology to the oilfield is still not as common as in other industries (such as food and pharmaceuticals), but it already serves various functions, such as: Detection and diagnosis of microbial driven impacts e.g. microbial influenced corrosion (MIC), reservoir souring and biofouling. Monitoring of the efficacy of biocide chemistry and dosage. Development of microbial production logging tools to identify key producing zones. Monitoring and mitigation of field souring. Development of synthetic DNA tracers. Microbial enhanced oil recovery (mEOR). ‘Micro-seep’ detection for exploration purposes.
Microbial DNA analyses, sampled from diff erent reservoir types and fields, have shown that each hydrocarbon accumulation has a unique and characteristic microbial fingerprint. The microbial population is controlled by variables in the downhole reservoir environment, e.g. the temperature, salinity, pH, nutrients and lithologies. Diff erences in microbial patterns between stacked reservoirs within one field have even been observed, which suggests that, in the future, reservoir zonation in a field could be based on microbial ‘stratigraphy’.
Case study: failure analysis and corrosion forensics
Several water injection wells in an oilfield in the North Sea experienced a deterioration in injection performance and unexpected increased annulus pressure. Classical petroleum engineering methods and logging (such as full-bore electromagnetic wall thickness measurements) were conducted but the cause of the failure remained unidentified. The corroded tubing was pulled and thoroughly analysed, in order to determine the root cause of the failure. 3D laser scanning of the retrieved tubing sections was applied to analyse the metal loss of the individual wells, which showed extensive localised corrosion.
Techniques were applied on the corrosion products sampled in the tubing, which included analysis of the mineralogical and chemical composition of the corrosion products using quantitative evaluation of minerals through QEMSCAN technologies. The mineral composition of the corrosion products located near a corrosion site are the result of chemical reactions between constituents of the injection water, released metals and (in this case) metabolic products from microbial biofilm surface interactions.
Through studying the mineralogy and the texture of the corrosion products the genesis and growth history of the corrosion pits could be reconstructed.
Furthermore, microbial samples were taken directly from the corrosion sites during retrieval. Molecular microbial techniques, such as quantitative polymerase chain reaction (qPCR) and NGS, were deployed to identify the entire microbial population responsible for the corrosion process.
The integration of these detailed analyses allowed the reconstruction of the microbial and electro-chemical processes that took place inside the tubing down to micron scale. It was concluded that MIC, aided by high chloride levels and triggered by the presence of biogenic hydrogen sulfide (H2S), led to aggressive corrosion
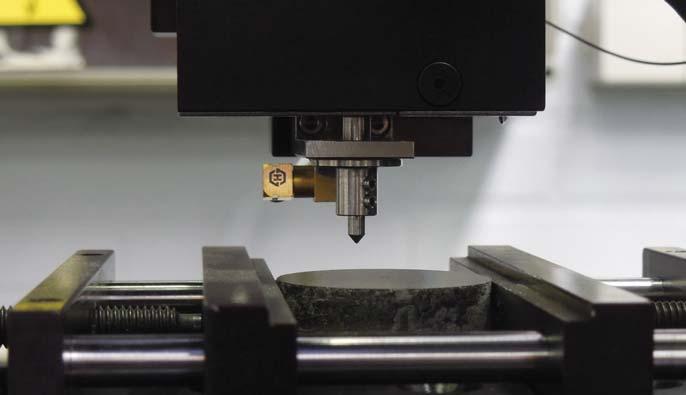
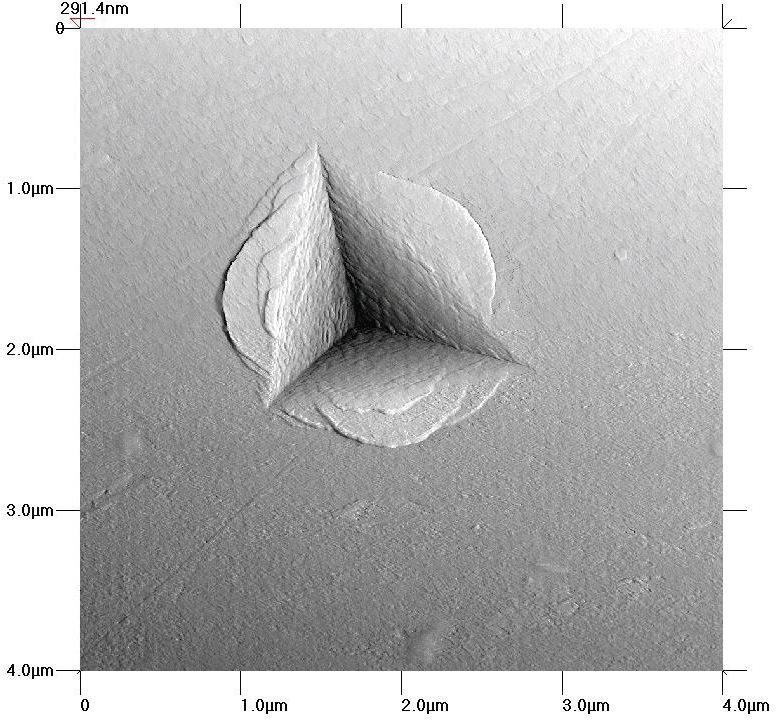
Figure 4. Nano-indenter (top); indentation impact on sample (bottom).
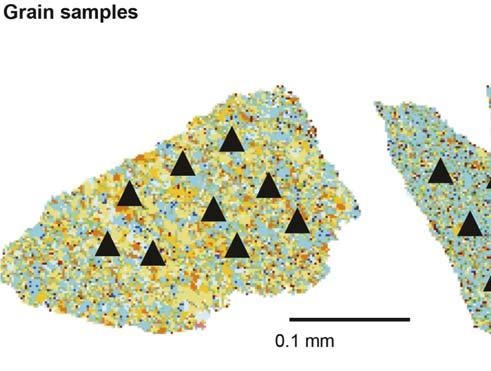
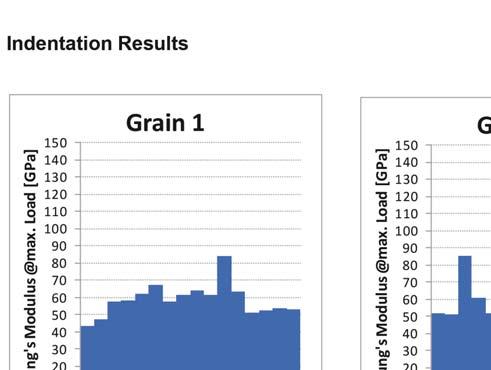

Figure 5. Cutting grain samples with indentation stations (top); Young’s Modulus calculated for each indentation station (bottom).
and subsequent failure of the injection tubing. Released corrosion products floated into the reservoir and caused the deterioration of porosity and permeability, which significantly reduced the performance of the injectors.
Based on the results from the ‘corrosion forensics’, the mitigation strategy was revised and optimised with the objective of minimising future corrosion of the injection strings. Furthermore, an analysis programme of the corrosion products was established for the monitoring of the eff iciency of corrosion mitigation and to detect severe corrosion at an early stage of the process.
Case study: mechanical properties from rock fragments
Unconventional shale plays are very prolific gas reservoirs in North America. The identification of reservoir ‘sweet spots’ and zones for eff icient hydraulic stimulation is challenging primarily due to their mineralogical and mechanical heterogeneities. SGS has developed technologies and workflows that use fragmented core material or drill cuttings, together with wireline logs, to map reservoir heterogeneities and identify the ‘sweet spots’ and reservoir sections with rock-mechanical properties favourable for hydraulic stimulation.
Rock fragments (crushed core and cuttings) from 20 sampling stations of the reservoir section of a shale formation were analysed. The mineralogical composition and rock-mechanical properties of the rock fragments were analysed using QEMSCAN and nanoindentation technologies.
Based on the analysis of the mineralogical composition, representative litho-types for each of the 20 sampling stations were defined and the elastic mechanical properties of the various litho-types were determined by using nanoindentation.
High resolution digital rock models were constructed for each observed rock type by incorporating mineralogical composition, texture, porosity, pore fluid density and the elastic mechanical properties measured from the nanoindentation.
Geomechanical finite element modelling (FEM) was used to calculate the bulk mechanical properties under reservoir pressure conditions for each identified reservoir zone.
The bulk rock-mechanical properties derived from FEM were calibrated at conventional triaxial core tests, which were only available from small sections of the reservoir. The bulk elastic mechanical rock properties modelled for the cuttings – together with Young’s Moduli and Poisson’s Ratios calculated from dipole sonic logs – were used to fill the ‘gaps’ between the sparse triaxial core tests. From the extrapolation and up-scaling of the calibrated bulk rock-mechanical properties a geomechanical profile was established for the entire shale reservoir section that captured the lithological and mechanical heterogeneities.
The resulting geomechanical profile highlighted reservoir sections with rock-mechanical properties conducive to hydraulic stimulation (‘hard rocks’), and identified sections with less favourable rock-mechanical behaviour.
Conclusion
The automated rock properties by indentation (ARPIN) workflow applied in the study clearly highlights the eff ectiveness of the approach of utilising drill cuttings to derive geomechanical properties. Geomechanical data from the well is generally scarce; therefore the workflow adds value in acquiring geomechanical information in any section of interest. Since it is done based on the available drill cuttings, the approach is also cost-eff ective. The workflow could also be applied for hydraulic fracturing, seal and caprock integrity, or reservoir assessments where cores and logs are not available.