
8 minute read
Collaboration’s the name of the game
COLLABORATION’S COLLABORATION’S THE NAME OF THE GAME GAME
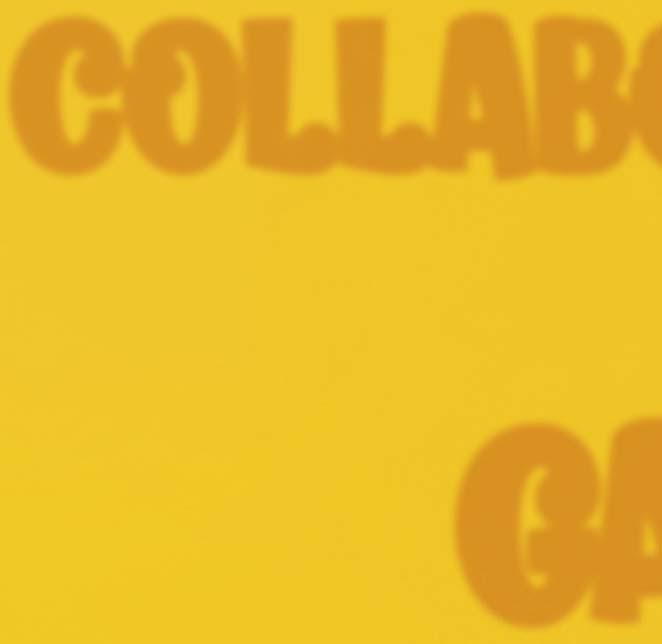

Duncan McAllister, Varel Energy Solutions, USA, and Cody Baranowski, D-Tech Drilling
Tools, USA, explain how supplier-to-supplier collaboration contributed to success in a challenging drilling operation.
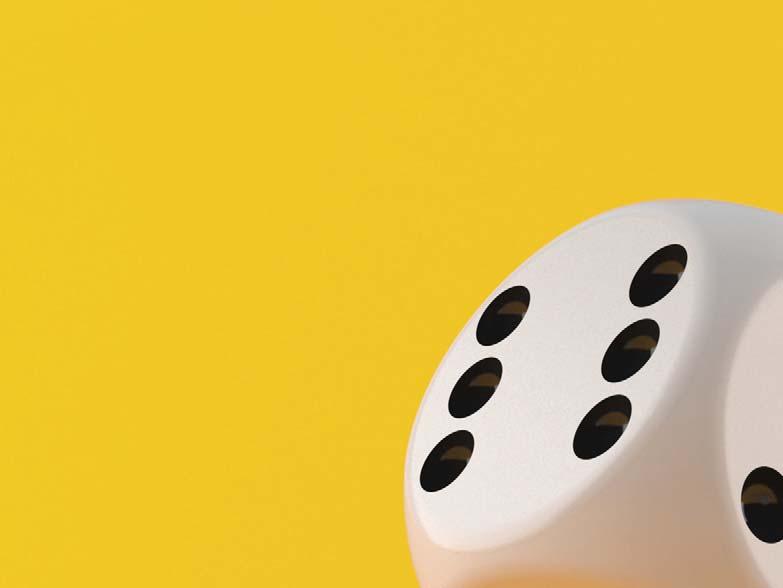

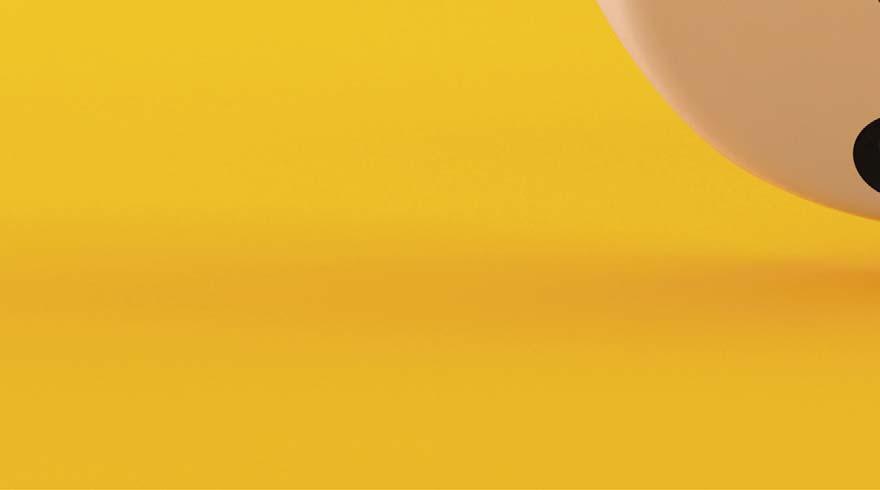
One of the largest challenges within the oil and gas industry has always been communication. Some operators have gone so far as to mandate the use of what is sometimes referred to as the ‘echo effect’, i.e. repeating back the words a person hears from another person they are communicating with, in order to create familiarity. The insatiable drive within all industries, not just the energy sector, to improve communication and collaboration originates from the understanding that the success or failure of goals comes down to communication.
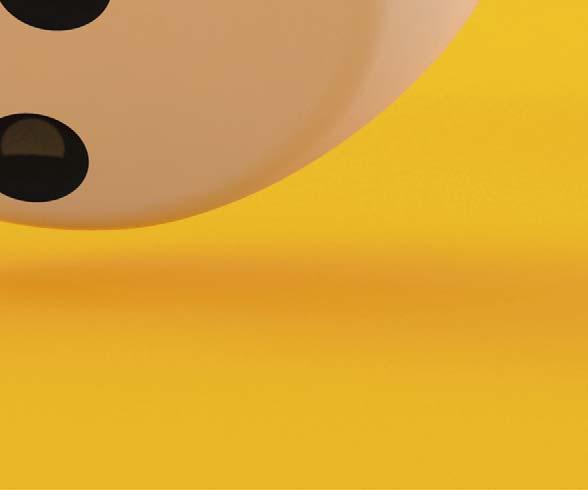

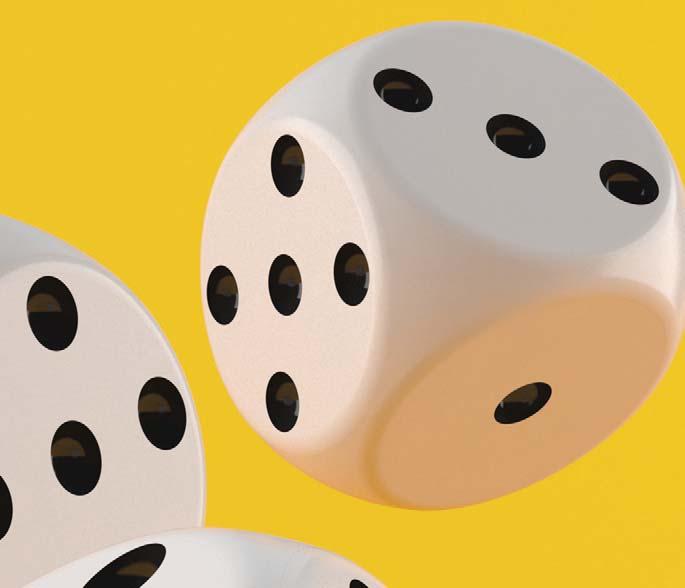
This is not to say that the quality, reliability, and performance of the tools that are selected for a project do not have a major impact on, for example, reducing the number of bits runs per section: what if performance suffers due to the selection of individual tools without prior consideration of the entire drilling system? The best drill bit for a motor assembly does not always work as effectively in a push-the-bit rotary steerable assembly. The challenge of communication in these scenarios lies in an important aspect that is often overlooked: supplier-to-supplier collaboration. When done correctly it can
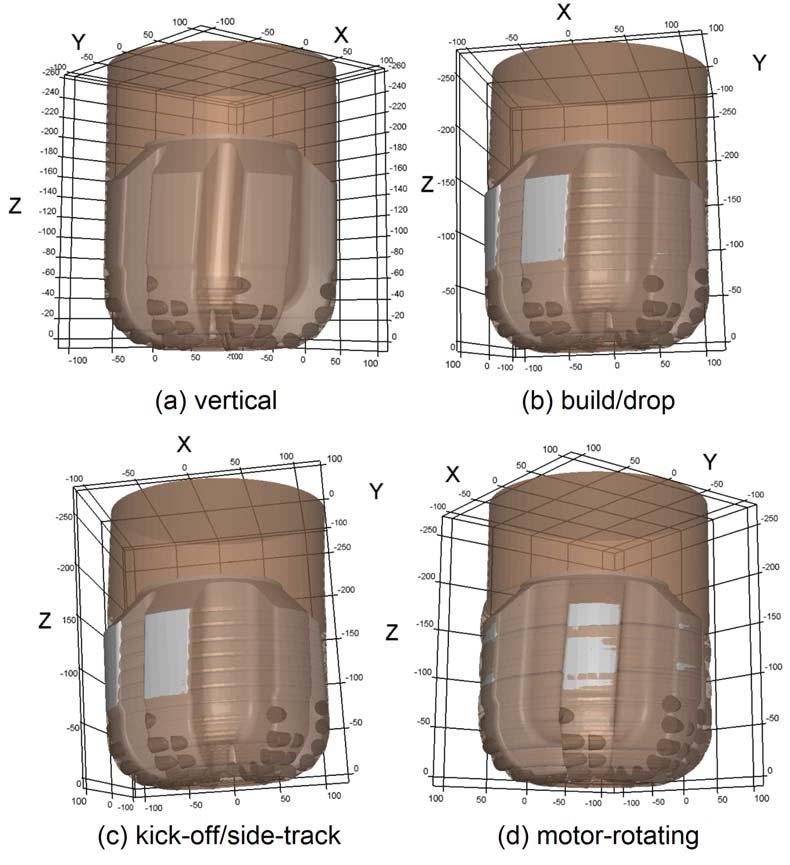
Figure 1. Example of diff erent directional simulation types inside the DigIT-3D soft ware.
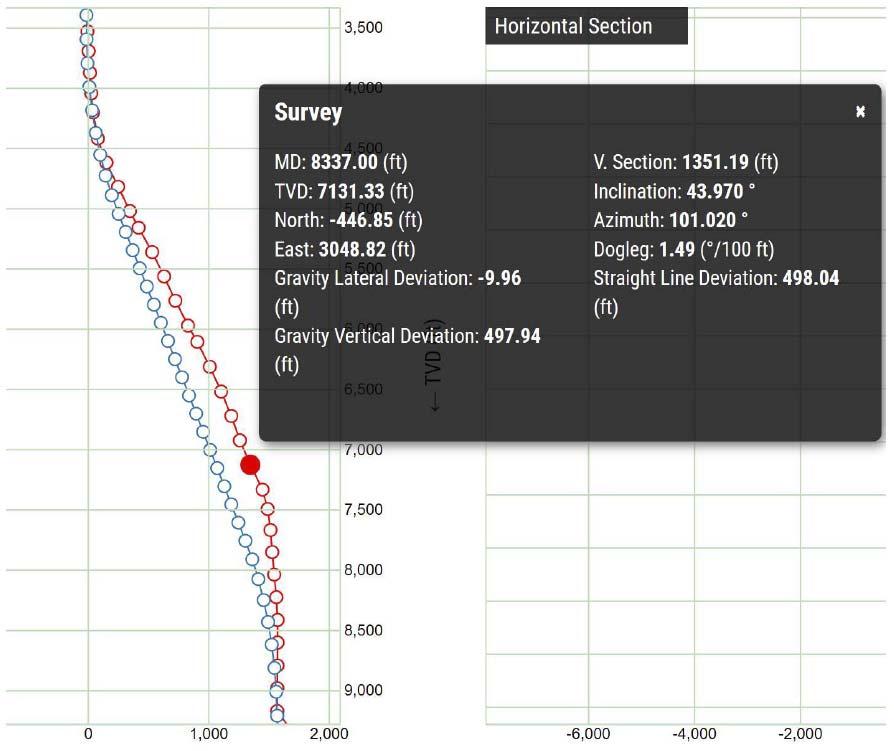
Figure 2. Survey information highlighting the high tangent angles that were achieved and held in this application.
Case study
An operator drilling in Oklahoma, US, faced a challenging 8.75 in. intermediate section with high angle tangents. The operator’s aim was to reduce the number of bit trips without sacrificing overall rate of penetration (ROP). Varel Energy Solutions, in coordination with D-Tech Rotary Steerable, worked to balance the design requirements for the lithology and directional requirements of the rotary steerable system. The companies’ steerable teams coordinated with the operator to create a collaborative approach to selecting the right bit for the application. This approach not only achieved the goal over a long period – completing the interval in one run 21 times over a 30 well period – but was successful on the very first run. Offset wells in the same area averaged 1.9 bits per section.
Developing a solution The target application presented a considerable challenge, not only in terms of decreasing the number of bit runs without sacrificing speed but also achieving directional objectives. The tangent angles on the subject wells ranged from 20˚ to 45˚of inclination. To achieve the directional requirements throughout the interval D-Tech’s engineering team first highlighted the importance of shoulder durability to maintain side cutting capability. By reviewing the rotary steerable tool memory, they were able to identify that the increased cutter size was causing drill string dysfunction. This was visible in the string speed variation in the rotary steerable tool memory. In the case of the smaller cutters, the string speed was more consistent and bottomhole assembly (BHA) rarely entered a state of dysfunction. The 13 mm cutter led to more consistent ROP and a more effective use of energy by the rig and the drill bit. Using the detailed knowledge shared by D-Tech, Varel’s 8.75 in. F613P-F design was selected; most offset designs in the Merge area intermediate sections were 6 blade 16 mm cutters. The use of the 13 mm cutter yielded the added durability that was needed while work was carried out to make sure the aggressiveness would be reduced as little as possible. Although some instantaneous ROP was conceded, it was found that the overall average ROP was able to offset 6 blade 16 mm cutter designs through better shoulder durability and a reduced risk of inducing drilling dysfunctions.
Another important aspect of bit selection that was considered for this application was finding the right balance between side cutting capability and hold tendency. Most bit designs that hold their angle well are designed to resist side forces, such as gravity. This means there is a balance that needs to be reached between side cutting capability and hold tendency. To achieve the desired dog leg severity, the bit would need to respond to the side forces from the push-the-bit rotary steerable system but also have a good hold tendency once the tangent angle was reached. To aid in the investigation of achieving this balance Varel’s engineering team used DigIT-3DTM simulation software to analyse a 8.75 in. F613P-F design on the end of a push-the-bit assembly (Figure 1). The software can simulate different directional drilling scenarios as well as different drive systems. The analysis concluded that the gauge pad configuration would contribute to an added hold tendency
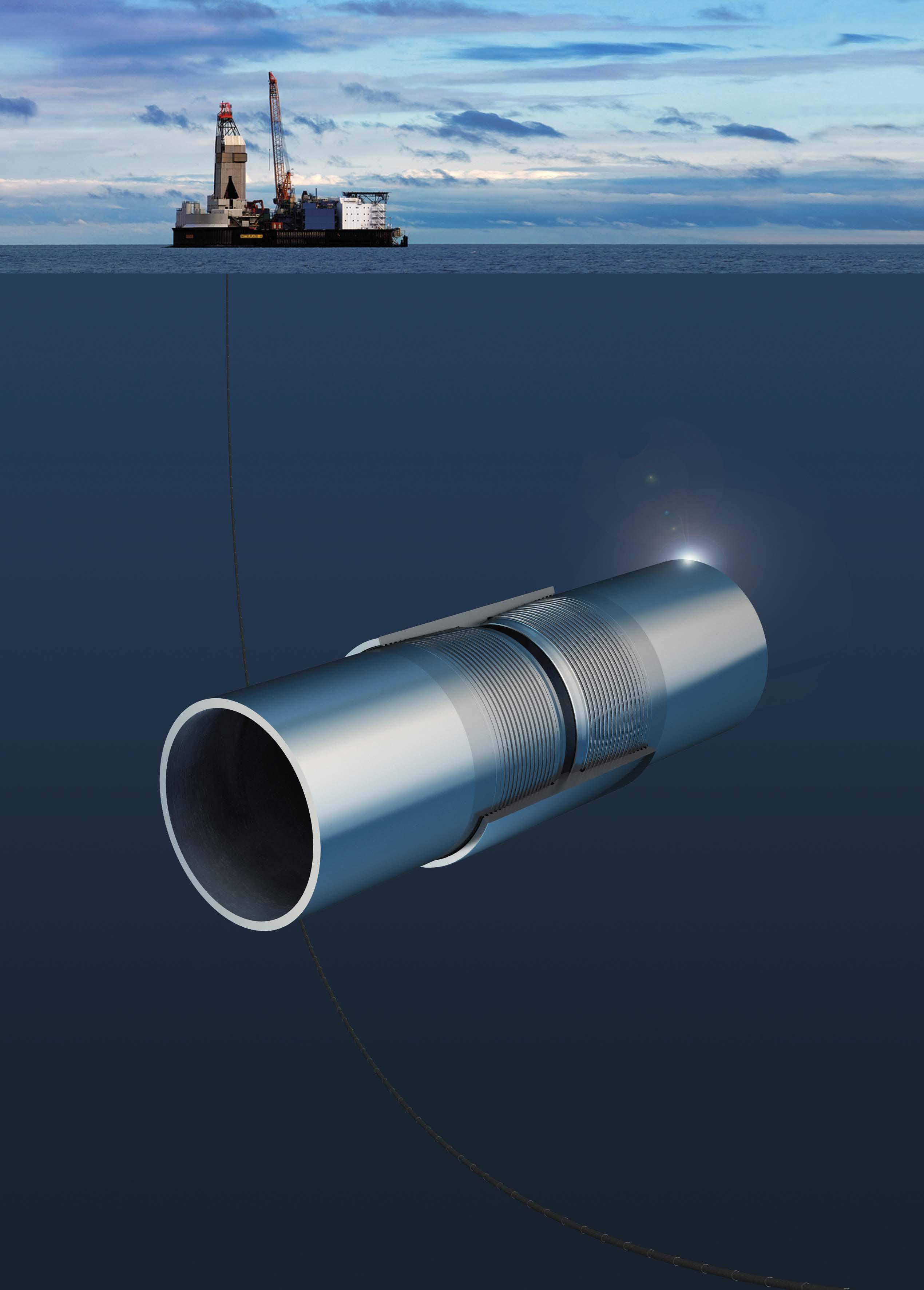
when the bit was not under active steering. Maintaining exposure, as well as the right aggressiveness, to the trimmer and shoulder cutters allowed for side cutting to occur when steer force was applied. The combination of these two features working together led to the balance between side cutting capability and hold tendency that the engineering teams were looking for, as shown in Figure 2.
A third key factor that also needed to be considered, in order to achieve a successful operation, was cutting profile. Steerability of the bit, or the bit’s side cutting capability, is extremely important. When using a push-the-bit rotary steerable tool having an aggressive shoulder cutting structure is critical. If the shoulder becomes dull during the run the bit will not be able to cut laterally when the tool creates a side force. The shape of the bit face and the bit’s ability to be pushed off axis are also important. For the bit to be pushed off its axis, the entire profile, not just the shoulder, needs to be designed with this intent in mind. Varel can create steerable cutting profiles that allow for the creating of low imbalance cutting structure design. It is often the case that primary focus is placed on the shoulder and gauge pad configuration for rotary steerable bit selection, but the cone cutting structure can influence steerability as well. Bit life in all portions of the profile is critical to the steerability of the Figure 3. Drill bit performance dataset from the same 30 wells D-Tech analysed. Figure 4. Recorded downhole string speed from D-Tech run on 16 mm cutter bit.
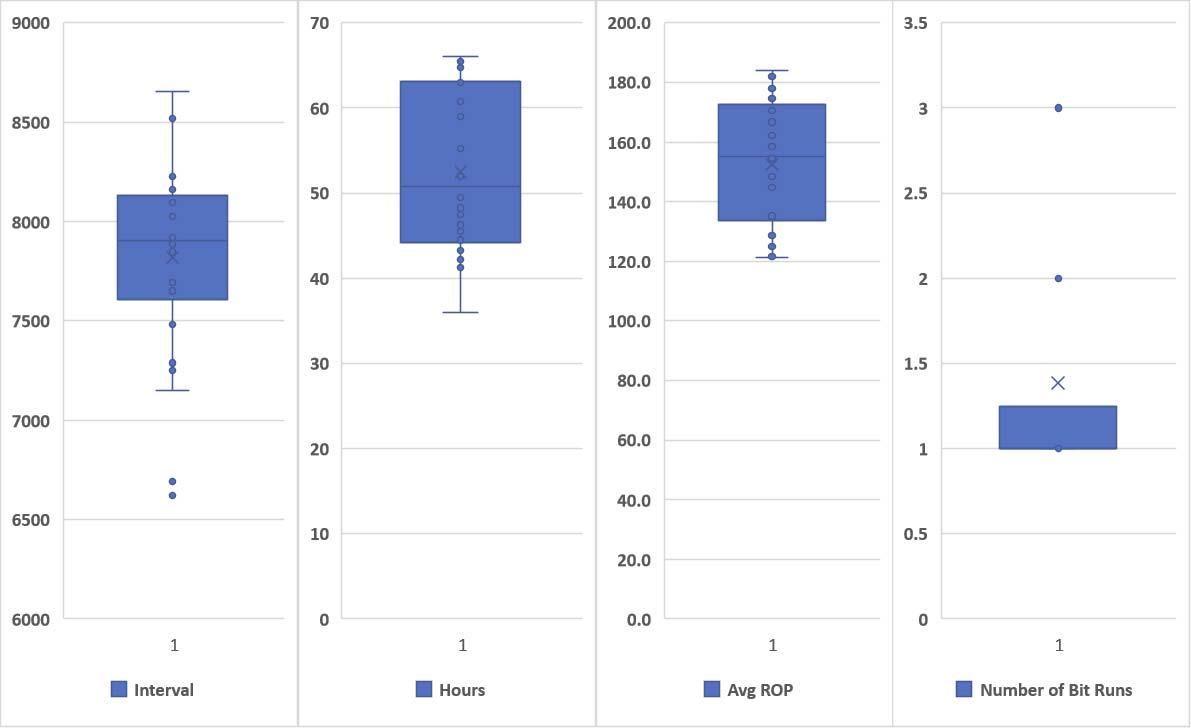
D-Tech tool. It is important that the bit is designed to be durable in the target formation and that its cutting structure can not only withstand the formation but also the additional side force created by the pistons of the rotary steerable in the target application.
Collaboration between the bit and rotary steerable company led to the design of a bit that met the needs of the rotary steerable tool and, ultimately, the operator. The bit provided an aggressive 13 mm cutting structure that balanced the durability needed to maintain side cutting with the desired penetration rate. The bit’s ability to maintain a sharp cutting structure as drilling took place allowed the rotary steerable tool to maintain the target steerability throughout multiple formations that have historically been more difficult to steer in. The exposure of the cutter structure was balanced with the gauge pad length and relief to allow for some side cutting while maintaining a hold tendency. The profile was analysed from the cone to the gauge to achieve steerability and a low imbalance cutting structure.
Results Analysis of the 30 well dataset yielded an average bit run of 1.4, average interval of 7819 ft, average hours of 52.5, and an average ROP of 149 ft/hr (Figures 3 and 4). Each of these major metrics also saw little variation throughout the selected group of wells, verifying the consistent performance that was sought by the operator. Analysis of the steerability revealed that the bit provided the rotary steerable tool with consistent steerability and increased yield. Well plans with up to 5˚/100 ft of build were utilised on intermediates that built up to 40˚or more of inclination (Figure 2). The rotary steerable tool was able to build these tangents without issue, maintain angle in the hold section, and drop the inclination out. This result was achieved due to the durability of the drill bit and its ability to drill through tough formations and maintain a sharp cutting structure. The record setting runs displayed in Table 1 were achieved through lower
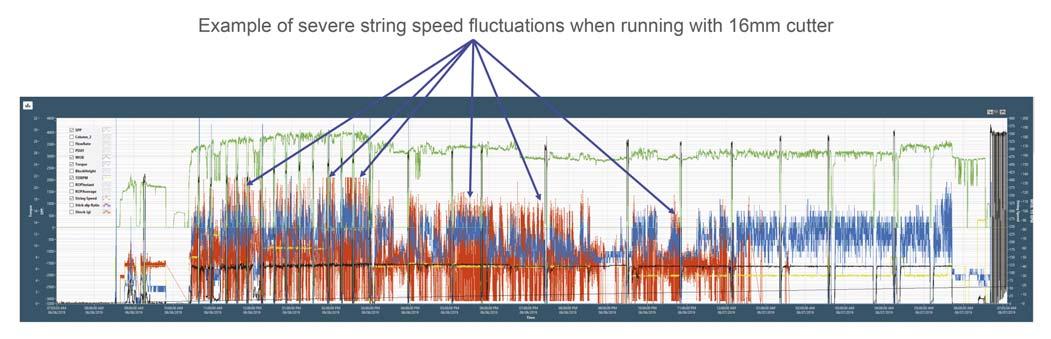
tangent angle.
Table 1. Runs in Mid-Con Merge play, Grady County, Oklahoma, US
Record run Tangent Depth in/depth out Footage drilled Hours ROP Bit
Run 1 20˚ 1211 ft to 8915 ft 7704 ft 37 207 ft/hr 8 3/4 in. F613P-F
Run 2 20˚ 1224 ft to 8876 ft 7652 ft 38 201 ft/hr 8 3/4 in. F613P-F
Conclusion
Though these forms of strategic collaboration occur throughout the industry, there is considerable room to improve the frequency and willingness to dive deeper. As organisations begin to align their core intent towards generating value, there lies a significant opportunity to progress as an industry – finding greater efficiencies, higher performance gains and a more effective use of capital. The system-matched approach to delivering the right drill bit and drive system is one of many ways to build step-change advancements, not only in drilling wellbores, but also for creating a sustainable marketplace for the industry in the future.