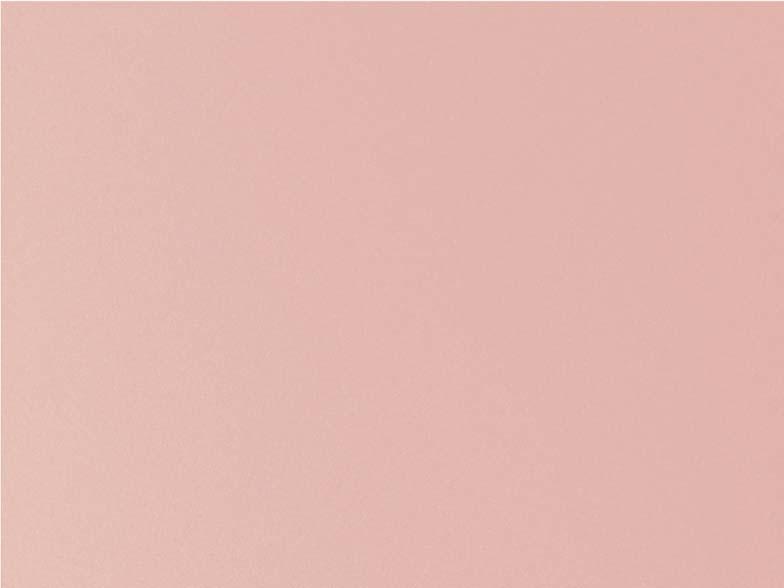
8 minute read
The fi ne margins of success
THE FINETHE FINE THE FINE MARGINS MARGINS MARGINS OF SUCCESS OF SUCCESS OF SUCCESS



Cory Langford, Scientific Drilling International,
USA, discusses how at-bit gamma ray images and continuous inclination measurements enable pro-active geosteering in tight target windows.
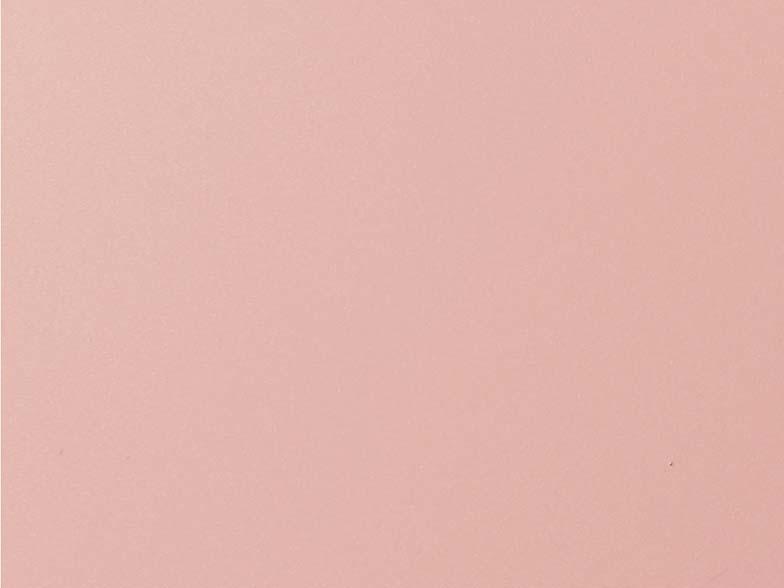

There are a wide variety of downhole logging tools which are used to eff ectively steer horizontal wellbores within a desired target window. The selection of the required real-time downhole measurements to be used in the geosteering process is largely based on the target formation’s expected log response across the drilling window. As the development process of an oilfield progresses, new methods for extracting the hydrocarbons are implemented. One of these methods involves extremely precise borehole positioning within the lateral’s target zone to maximise hydrocarbon recovery. Traditionally, operators who wanted to achieve the goal of staying within a geosteering window of <10 ft would utilise a rotary steerable system (RSS) for a decreased bit-to-sensor distance and better inclination control. With commodity prices for oil remaining in the US$30 – US$40/bbl range, the development of certain mature oilfields might not be economically feasible when the extra cost of running a RSS is required for geosteering purposes.
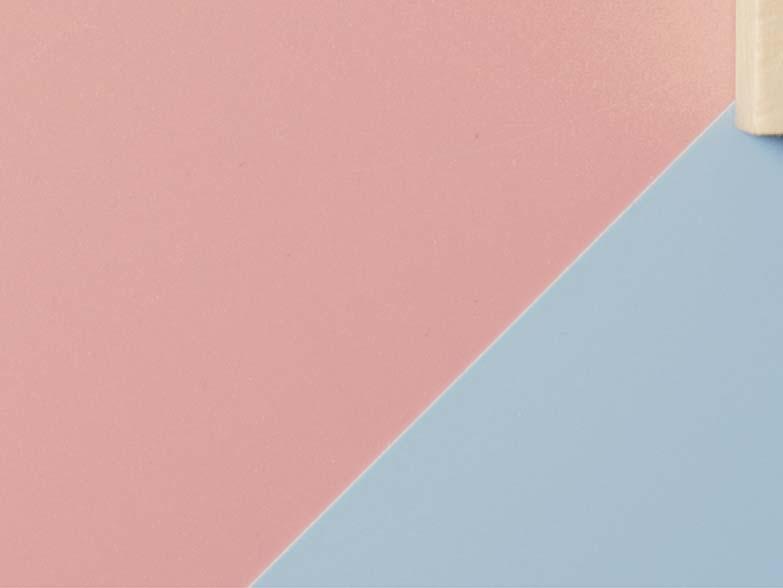
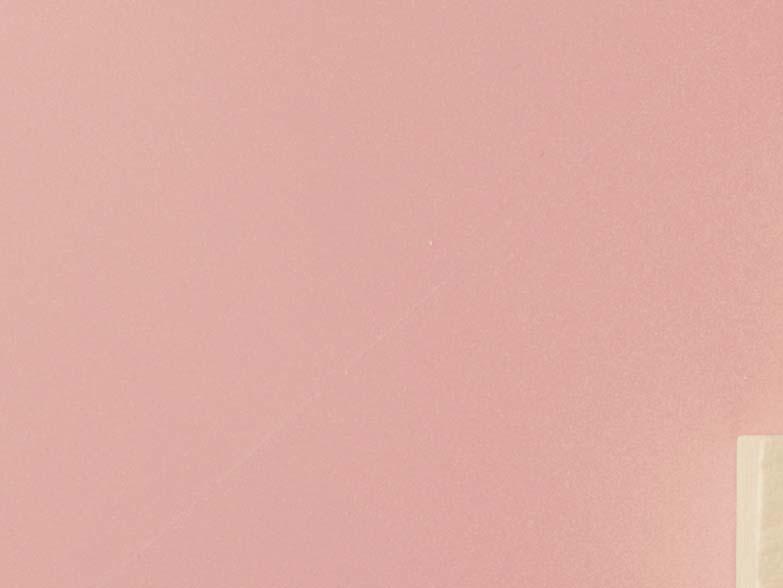
Azimuthal LWD data requirements
While most horizontal wells can be geosteered with a traditional bulk gamma ray logging while drilling (LWD) sensor, there are instances where the target formation does not provide enough gamma ray contrast to adequately determine where the well is positioned by correlation to off set well logs. Azimuthal functionality of downhole LWD sensors provides an accuracy to well placement decisions made in real-time. Determining if an azimuthal gamma ray sensor or azimuthal resistivity tool is needed to stay ‘in-zone’ is usually decided before the well is drilled by looking at off set well data in a pre-well analysis. With a thin geosteering window, target changes in inclination become a critical component to keeping the well within the desired target zone.
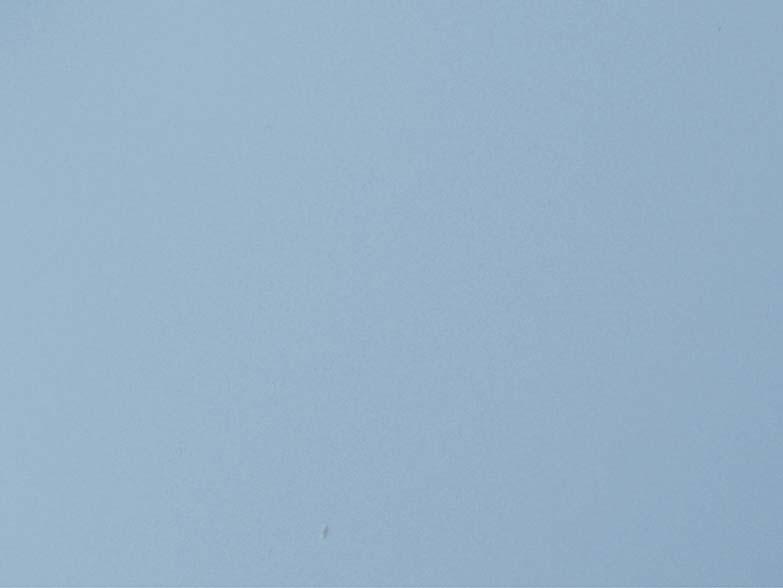
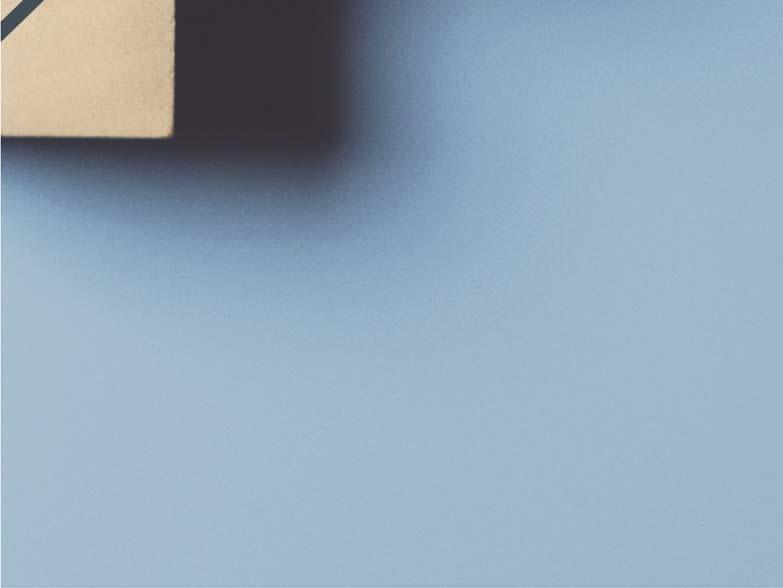
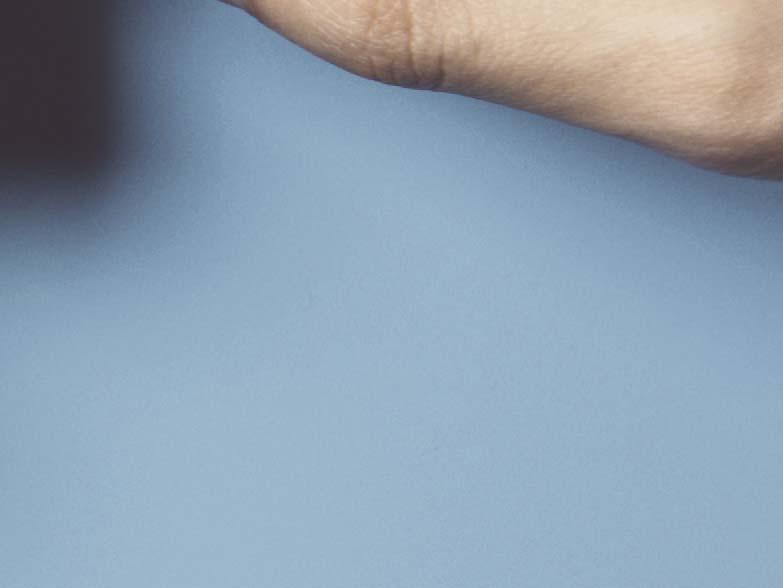
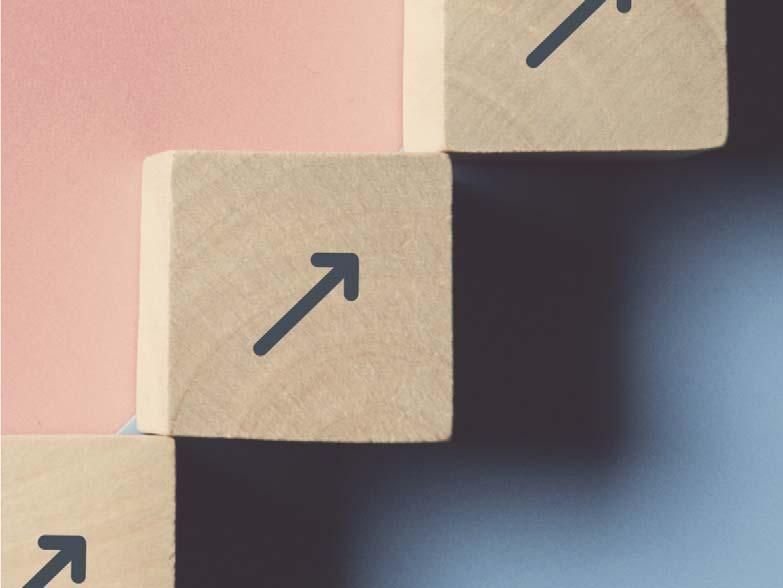
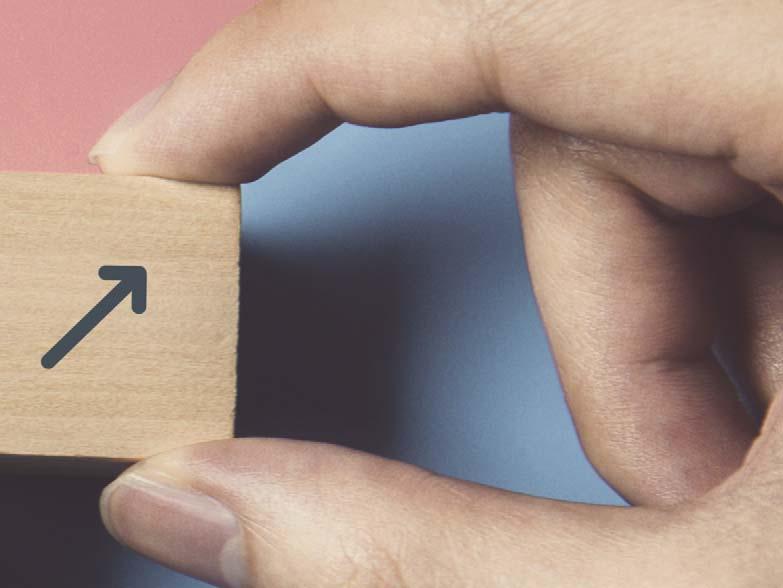



Bit-to-sensor offset effects on geosteering methods
A decreased distance between the bit and LWD sensor can allow for a near proactive geosteering approach. Typical bit-to-sensor distances for gamma ray sensors connected to the measuring while drilling (MWD) probe above a mudmotor fall in the 30 – 45 ft range. This will depend on the length of the bit and motor, as well as the tool design off ered by the directional service provider. RSSs will have a decreased bit-to-sensor distance of 10 – 20 ft , along with the option of a continuous inclination measurement of less than 10 ft from the bit. The shorter bit-to-sensor distance allows for quicker decisions on target changes to limit the amount of the well drilled out-of-zone by reacting quicker to structural dip changes along a lateral section.
Proactive geosteering methods have normally involved running downhole LWD sensors with a deep depth-of-investigation geosteering programmes. Reactive geosteering can sometimes involve making target changes aft er the bit has already exited the target zone, resulting in over-correcting and porpoising the well to try and re-enter the ‘sweet spot’.
With the advent of a geosteering sensor sub which is placed between the mudmotor and drill bit, bit-to-sensor distances can be decreased to less than 2 ft and provide a proactive approach to geosteering. Since the sub is placed below the mudmotor, having a short collar with reliable measurements is the key to success. Scientific Drilling’s BitSub LWD tool is 29 in. long and has azimuthal gamma ray, inclination, and tri-axial vibration measurements 16 in. above the top of the bit (Figure 1). The sub is run in conjunction with a compatible MWD system above the mudmotor and communicates via electromagnetic short hop. This Wi-SciTM technology works in both water-based and oil-based mud systems.

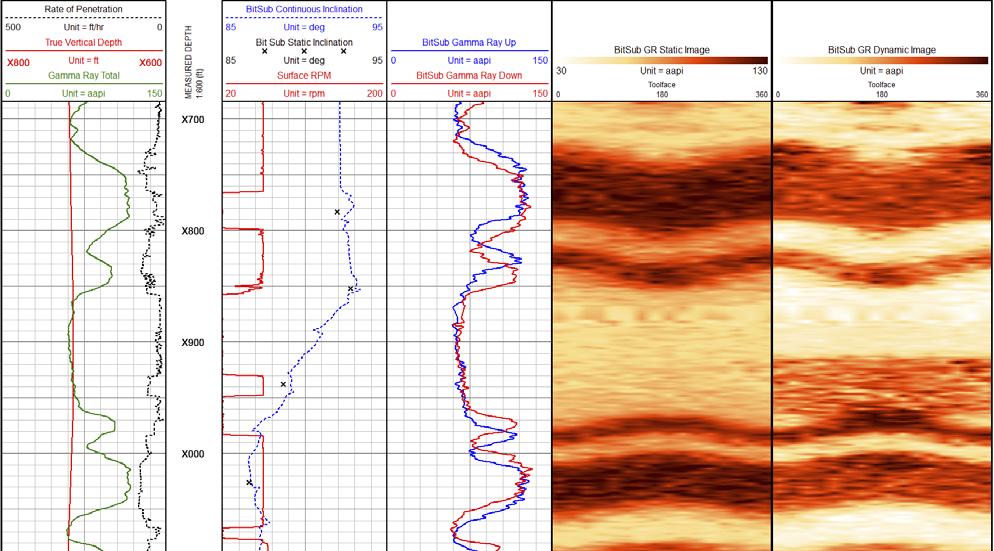
(DOI) for a ‘look-ahead’ approach of adjacent bed boundaries. Since gamma ray sensors provide a relatively shallow DOI with Unconventional shale applications long bit-to-sensor distances, they are generally used for reactive In the past decade, there have been huge improvements in the drilling and completions process of horizontal wells. These changes largely occurred after operators fully entered the development phase of large unconventional resources discovered across multiple basins in North America. Decreasing drilling costs were mainly Figure 1. BitSub schematic showing the length of the collar, as well as the bit-to-sensor distance of 16 in. driven by the increased reliability of downhole mudmotors and MWD systems, novel drill bit designs, drilling mud system enhancements, drilling rig horsepower increases and automation implementation, as well as the ingenuity of an industry that realised the potential of large untapped oil and gas reserves in unconventional shale reservoirs. Along with the step-change of reducing drilling days per well, new completion methods were trialled which resulted in higher extraction rates of hydrocarbons. Staggered well designs, zipper fracs, shorter stage lengths and higher proppant amounts have all
Figure 2. Gamma ray image log from unconventional shale reservoir’s horizontal section.

Figure 3. Gamma ray image log from conventional sandstone lateral section.
contributed to increased production. While drilling costs have decreased dramatically, the cost of completions has remained relatively high due to the aforementioned changes in completion design. In order to ensure the reservoir is being adequately drained after hydraulic fracturing stimulation efforts, the placement of wellbores within target formations is critical. If a well is drilled 100% within a target window, reservoir appraisal studies can be accurately performed to determine estimated hydrocarbons-in-place for a field by examining the production history of wells.
Unconventional shale reservoirs continue to be a large focus for many E&P operators wanting to extract the large amounts of hydrocarbons
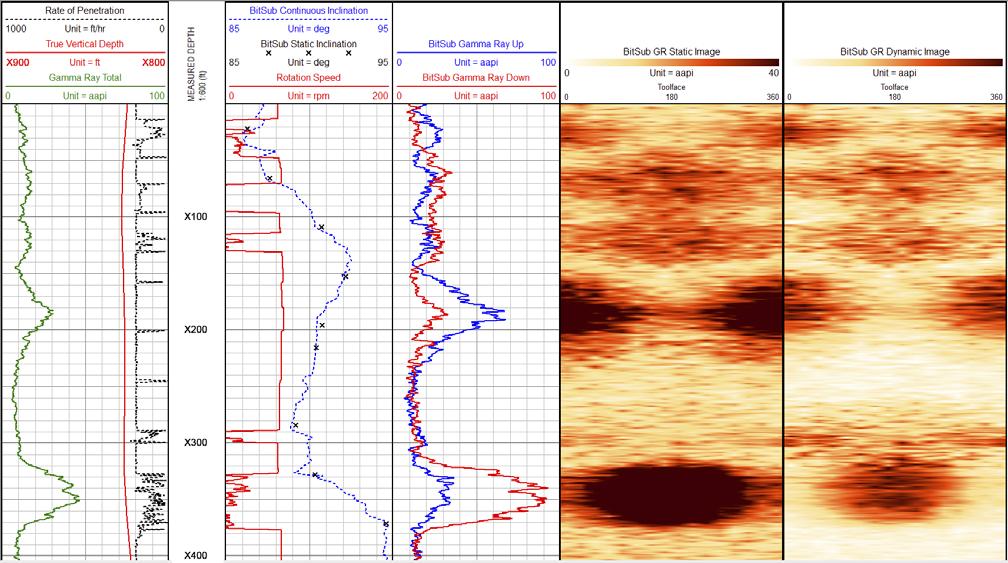
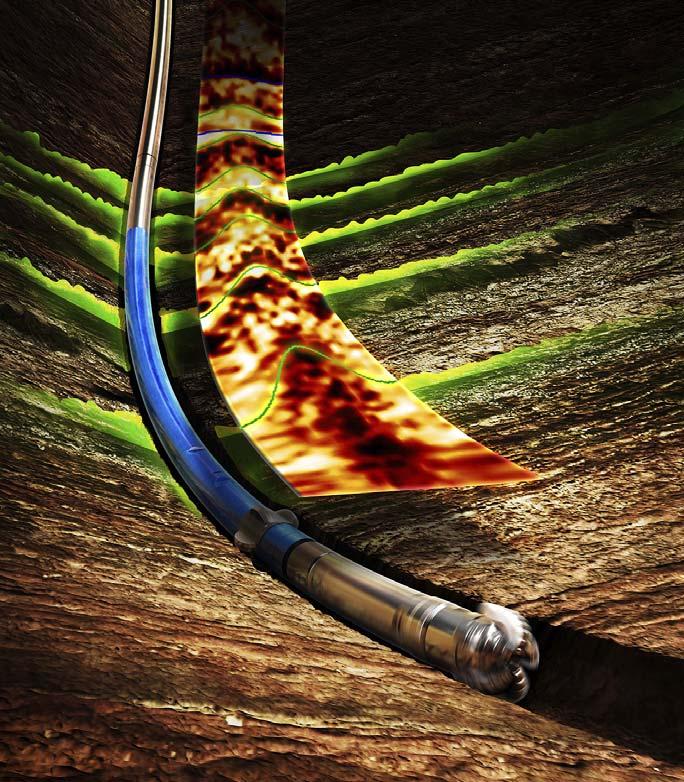
Figure 5. Artistic representation of azimuthal gamma ray acquisition and at-bit interpretation from the BitSub LWD tool.
trapped in the low permeable source rocks. In order to maximise recovery factors, well spacings of laterals have been reduced. With smaller drilling windows, directional survey management and geosteering have become critical inputs into modelling offset fracture interference between adjacently producing parent wells. Multi-well pads and stacked plays have further increased the density of wells in a given area. Directional control and geosteering confidence play a considerable factor in minimising dogleg severity along a lateral section. Figure 2 illustrates how the azimuthal gamma ray identified that the well came out the top of the target zone, and the well trajectory was adjusted using the at-bit inclination measurement. Having at-bit inclination allowed for active monitoring of motor yields while sliding, preventing an over-correction of course adjustment. In addition, drilling dynamics measurements at the bit can be used for constructing optimised drilling parameter roadmaps for the purpose of maintaining high rates of penetration while prolonging the life of downhole drilling bottomhole assembly (BHA) components.
Case study: conventional reservoir
Enhanced oil recovery (EOR) programmes for mature conventional sandstone reservoirs benefit from decreased bit-to-sensor distances due to the necessity of precise wellbore placement in the reservoir. There are instances where the BitSub LWD tool has been utilised to keep a horizontal wellbore at the top of the target formation, in order to extract the trapped hydrocarbons without the additional costs of a carbon dioxide flood. Other case studies for conventional reservoirs include drilling a lateral at the bottom of the target sandstone formation, in order to implement water-flood recovery efforts. Both scenarios have the geosteering programmes incorporate the at-bit azimuthal gamma ray and inclination from the BitSub LWD tool for maximised target zone exposure. Figure 3 shows an example of how the BitSub gamma ray images can provide clear and precise indication of stratigraphic markers, even when the gamma ray is only fluctuating 15 API.
Coal-bed methane horizontal wells
At-bit gamma ray and inclination measurements were primarily developed for coal-bed methane wells, where fractured coal seams, which are stratigraphically bound by shale caps above and below, are targeted with horizontal wellbores to maximise hydrocarbon production. Steering within these coal beds involves multiple target inclination changes, since their thickness can be as little as 5 ft. Having accurate real-time azimuthal gamma ray and inclination ensures that when the bit strikes the shale cap, a confident decision can be made to steer the well back down into the target zone. With a gamma ray sensor at the bit, out-of-zone lateral percentage is minimised due to the proactive geosteering method of identifying whether the bit is cutting up or down the structure. Figure 4 shows a gamma ray image log from the LWD tool showing the well succeeding to stay in-zone by recognising the at-bit inclination starting to build during rotation.
Drilling optimisation from at-bit measurements
LWD tools have a long history of proving their value to geosteering and petrophysical interpretations. The real-time data they provide can influence important decisions about target well trajectories, ultimately affecting the post-well production and completion strategy (Figure 5). Their benefits to the drilling department have been relatively scarce, as they are usually located above the mudmotor and do not provide any insight into motor or bit performance. Through the use of technologies that provide downhole at-bit measurements, such as BitSub, real-time information is created that can steer the well in a tight geosteering target window with minimal gamma ray contrast, and additionally supply the inclination and tri-axial vibration measurements for drilling parameters and mechanical specific energy optimisation.