
9 minute read
Paving new paths in Bremen
PAVING NEW PATHS
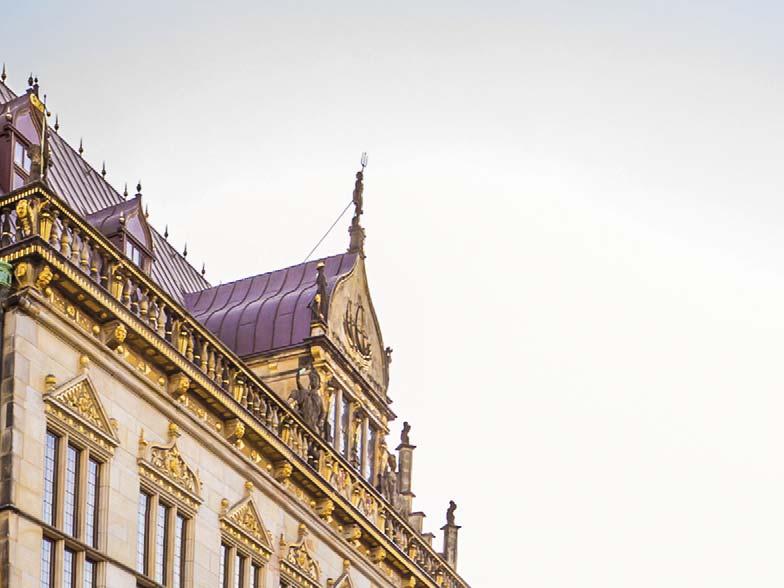
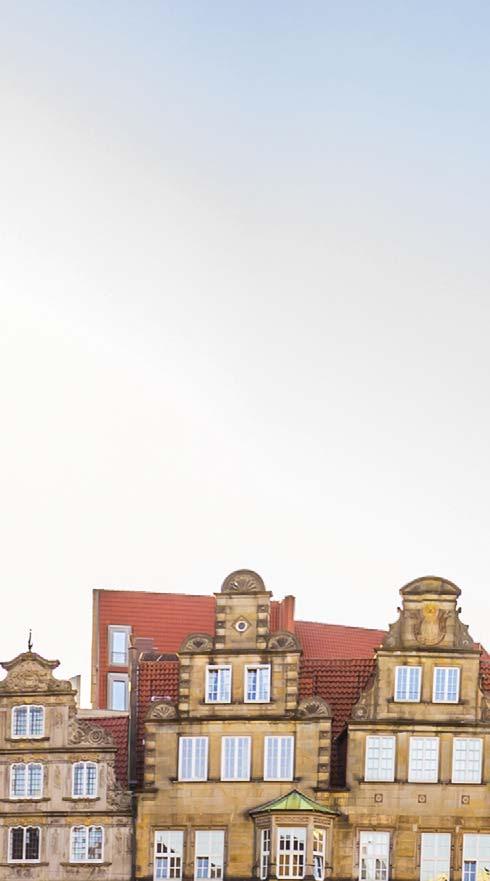

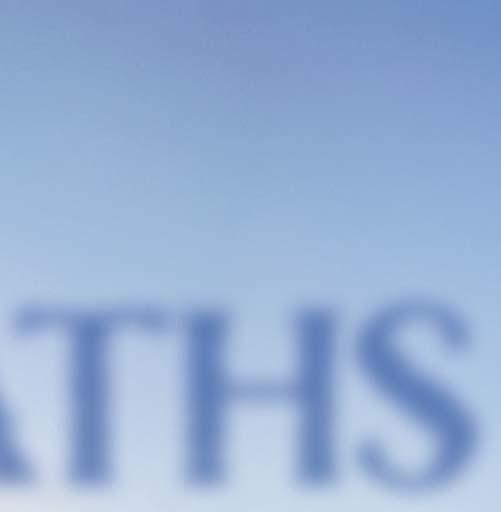
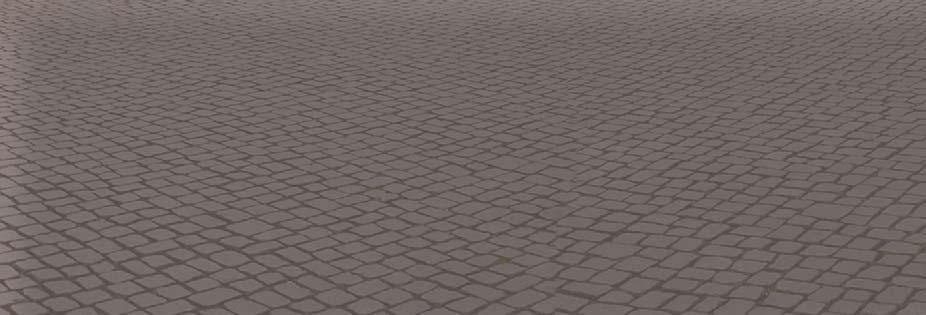


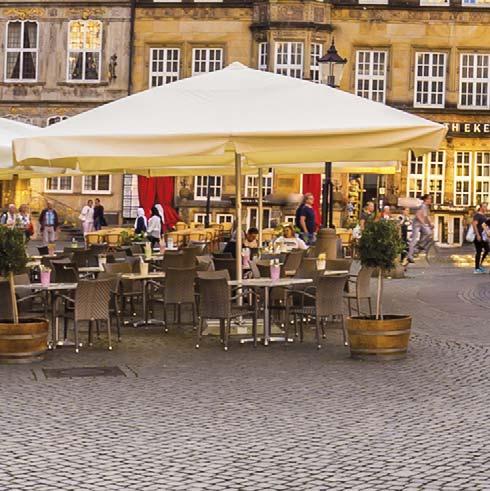

Jörg Eitler, NETZSCH Pumpen & Systeme
GmbH, Germany, highlights a case study in which an electric submersible progressing cavity pump system with a permanent magnet motor was able to convey efficiently and reliably.
IN BREMEN
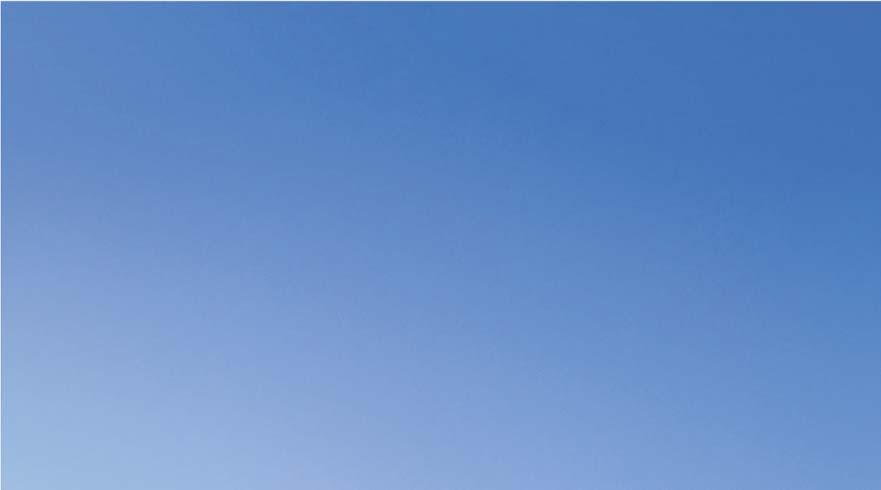
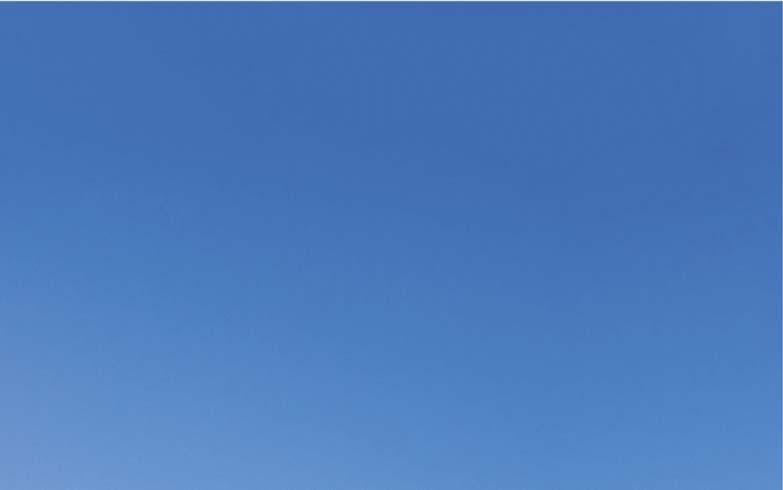

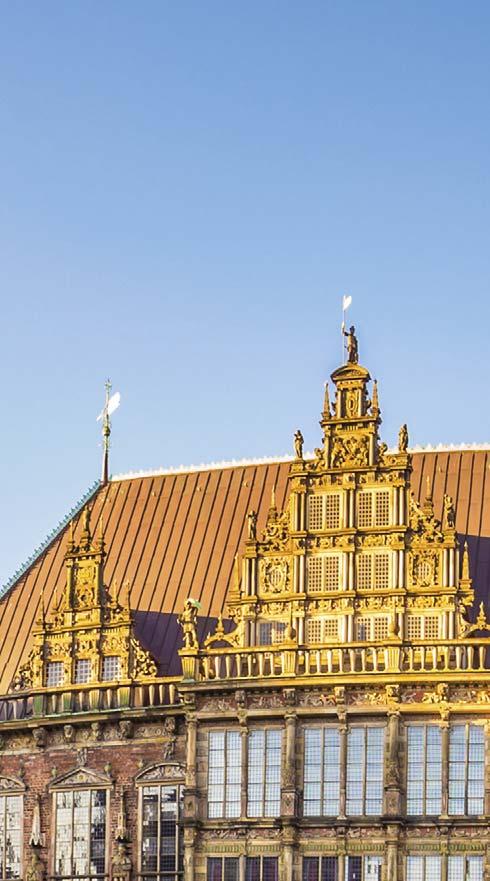

For almost 70 years, a German oil and gas producer has been operating oilfields south of Bremen. For historical reasons, the company uses various types of pumps side by side. The installed centrifugal submersible pumps, pumpjacks, and progressing cavity pumps (PCPs) can handle local conditions, such as partially
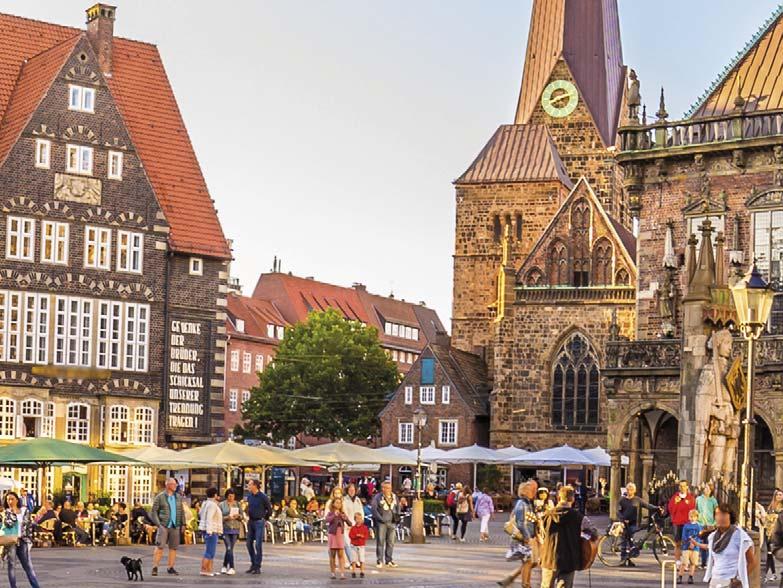


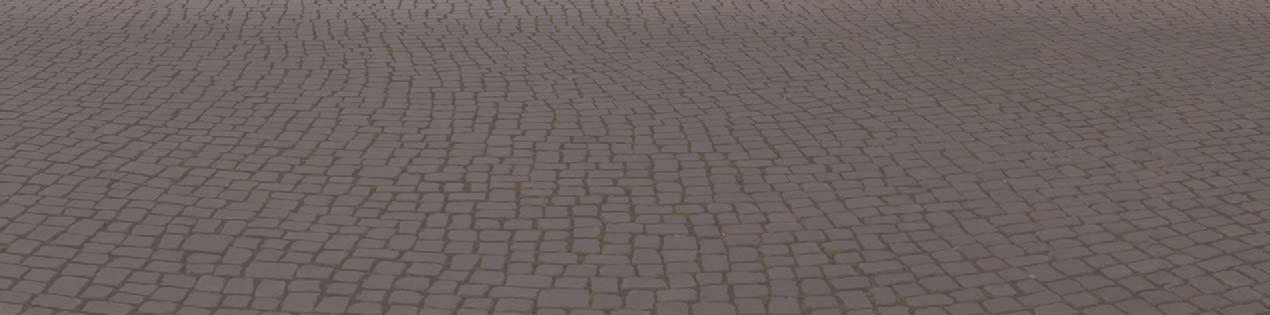

deflected boreholes, paraffin mixtures, and sand mixtures with varying degrees of effectiveness. PCPs, as rotary positive displacement pumps, are particularly suitable for demanding media, such as viscous and abrasive media. However, the pumping rods, which are often up to 3000 m long, may break and the tubing can wear through.

Figure 1. In November 2018, a NETZSCH ESPCP system was installed in the oilfield of a German oil and gas producer. The picture shows the well, which was converted from a decommissioned pumpjack (right) to the rodless PCP (left ).
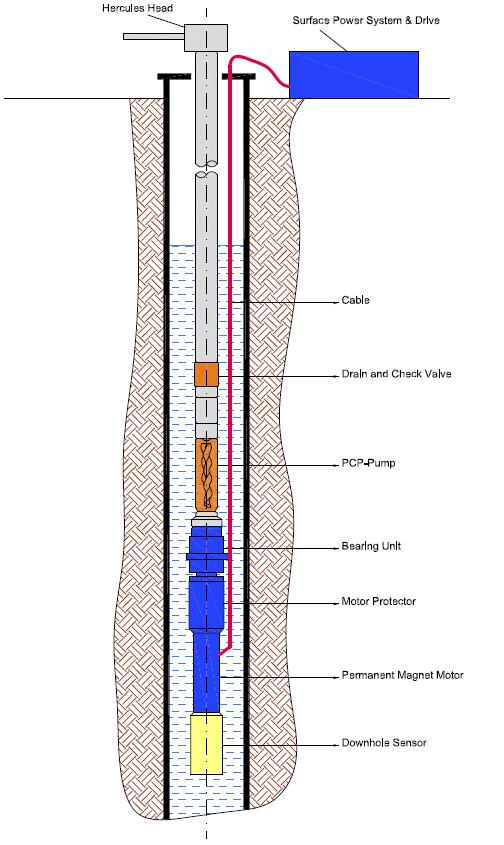
Figure 2. In addition to the PCP, the system consists of a PMM, sensors, a motor protector, a bearing unit, and a FlexShaft . Other components are a check valve, a drain valve, and a cable that is used to power the motor and to transfer data.
By comparison, submersible centrifugal pumps do not use pump rods, but they are not very suitable for fluids that contain sand and/or gas. In an effort to reduce the number of pumping installations, the oilfield operator began to look for an efficient and durable system capable of combining the advantages of both types of pump: a system that combines a submersible motor of a submersible centrifugal pump with a PCP. However, the systems available on the market were out of the question, as they were equipped with a planetary gear system that is highly error-prone. The company finally decided in favour of a solution developed by NETZSCH Pumpen & Systeme GmbH that does not use that vulnerable component. It is a PCP system with underground drive and a permanent magnet motor (PMM). Even with the difficult media, it allowed higher flow rates than the previously used units. It also lowered operating costs due to its lower error rate.
The company uses three different pump types for conveying operations on its crude oilfields south of Bremen. Due to their different design and functions, the different models work with varying degrees of effectiveness in the specific conditions of production wells. Each type of pump has specific advantages and disadvantages; for example, in the case of pumpjacks and PCPs, pump rod fractures occur relatively frequently. Since the rods move constantly during extraction, tubes may become damaged. This is more likely the further the borehole path deviates from the vertical position. As a result, time-consuming work may be required to repair the damage and resume production. In the case of submersible centrifugal pumps, this risk is much lower. They must be very precisely designed and carefully installed to avoid damaging the underground cable during installation, especially if the borehole path is not vertical. However, once the installation is successfully completed, the cables often have a much longer service life than the rods of PCPs and pumpjacks. This is because the cable is not under dynamic load during operation, as is the case with pump rods.
The decision-makers considered a combination of PCP and submersible centrifugal pump, which combines the advantages of both pump types, to be particularly useful and efficient for the applications in the north German oilfields. Moreover, pumps of this kind have already been developed and assembled. These are the rodless PCP or electric submersible progressing cavity pumps (ESPCPs) – PCPs driven by a submersible motor. Based on the advice from oilfield specialists, the company decided on a special model developed by NETZSCH Pumpen & Systeme GmbH, which does not require a transmission ratio between the motor revolutions and the pump, since the motor selected specifically for this application can be operated at very low frequency. In addition to the PCP, the system consists of a PMM, sensors, motor protector, bearing unit, and a flexible rod called FlexShaft. Other components are a check valve, a drain valve, and a cable that is used to power the motor and to transfer data from the sensor.
Conveying of difficult media
The main parts which define the conveying principle of the PCP are a rotating component – the ‘rotor’ – and a fixed component – the ‘stator’, in which the rotor turns. The rotor is designed as a type of round threaded screw with a large pitch, large thread depth and small core diameter. The stator cavity has one extra thread and twice the pitch length of the rotor.
The precise geometrical mating means that conveying chambers are maintained between the stator and the rotor, which rotates inside it and also moves radially. These chambers continuously move from the intake to the outlet side and transport the medium. The volume of these chambers remains constant, and the chambers themselves are self-contained. This not only prevents backflow, but also ensures that the conveyed medium is transported at stable volume and pressure, so that no shear forces and hardly any pulsation occur.
Other pumping systems soon reach their limits if consistencies vary, which results in interruptions, loss of pressure, and material damage. For PCPs, on the other hand, consistency and viscosity of the medium are not relevant to the flow. The multi-phase pumps from NETZSCH can therefore also handle mixtures of oil and water with sand or gas, reaching flow rates of up to 300 – 400 m3/d.

Improved handling
The ESPCP used by the customer was also a model that has a special rotor connection, and was driven from below – from inside the borehole. The special feature of this pump is that the rotation of the rotor is not driven by the aboveground drive head via a very long shaft or rod; rather, the rotor-stator combination and the motor are sunk into the well. The motor and the bearing unit are connected directly to the rotor via a flexible rod. All radial and axial forces of the rotor are absorbed Figure 3. Since there is no pump rod, the pump can be used even for horizontal or heavily by a special underground bearing housing. There deflected boreholes. This means that the DLS is very high. is also a dynamic seal in the well. This movement of all critical components of the pumping unit because the technology of the PCP allows conveying of different belowground has precluded any environmental impact from leaks phases of a fluid. It also conveyed low volumes of 3 to 20 m3/d aboveground. as efficiently as medium volumes of 10 to 100 m3/d. Since there
The motor that has been selected for the system is a PMM. is no pump rod, the pump could be used even for horizontal or It is designed to meet the specific requirements of a PCP. heavily deflected boreholes; that is to say, the allowable borehole With this slow-speed 10-pin synchronous motor, the specified deviation – the dog leg severity (DLS) – was very high. Eliminating speed is the same as the actual speed, removing the need pump rods rules out rod breakage, as well as friction of rods for complex slip calculations and speed measurements. Even against the tubing. This significantly reduced the risk of tubing error-prone, mechanical or magnetically coupled transmission leakage. In addition, it helped achieve higher flow rates in the can be dispensed with. In this application, even a PCP with an tubing and the use of tubes with a smaller diameter. Pressure aboveground drive is not recommended because of the short losses in the tubing were also lower. The rods cannot get twisted, service life of the overall system. However, the PMM facilitates which rules out a dangerous backspin – an abrupt relaxation of underground use. As a result of the PMM, the pumps can the drilling line. be installed deeper. They can also be used if there is a high Other advantages of these rodless PCPs over conventional deflection. A downhole sensor is installed directly underneath PCP models are a smaller axial load, a larger operating window of the PMM. It provides data for the operation of the production well 180 – 500 revolutions, integrated pump and motor protection, and and data on the machine condition. It also helps to troubleshoot the choice of a special, highly xylene-resistant elastomer. Other problems in the well. For example, it measures fluid and motor features include an automatic integrated pump control, which temperature, as well as pressure on the sensor. This component serves to start the pump after a power failure, and the remote also allows adjusting of the speed automatically to the pressure, measurement of real-time pump data for early detection of errors. which prevents the pump from running dry. The system also has a smaller footprint than all systems with aboveground drives. Higher flow rates In November 2018, the NETZSCH ESPCP system was installed The design of the ESPCP system, which is installed in northern and put into operation in the oilfield south of Bremen. It had Germany, was adapted to local conditions. It was therefore able to worked without fault until the first unscheduled shutdown of the convey the highly viscous medium, which contains bitumen and production well, which was caused by exceeding external limits paraffin sediments, sand content of up to 40%, or salt deposits, that were not related to the pump. The system was quickly put with a pressure of up to 300 bar. A gas proportion of up to 40% back into service; therefore, the operator planned to purchase of the pump intake did not pose a problem during extraction, additional systems as a result.