
8 minute read
Combining data and design
Gilberto Gallo, Drillmec, USA, outlines the importance of technology to rig design and improving drilling performance.

The current market has tightened the space for drilling rig innovation, and rig design is caught in between necessity and limited economic feasibility. Drilling rig advances are therefore shift ing from structurally based to data-driven and process-based ones that seemingly represent a more aff ordable low hanging fruit.
The evolution of the full drilling rig packages now involves a total integration of the diff erent product lines under one system of data management that produces key data for both operations and maintenance. In order to eff ectively exploit this potential, machine learning and AI are gradually being introduced and utilised, opening up to all sorts of data mining to improve drilling performance, equipment durability and maintenance, and reliable and safe operations. However, there still is plenty of room for conventional, operation-based progress, especially by using the newly historical data benchmark exploring new patterns and trends. For example, a recent study on statistics per well in the Permian Basin in Texas, US, showed that 97% (of the 10 terabytes per day per single well) was not being analysed. One of the largest
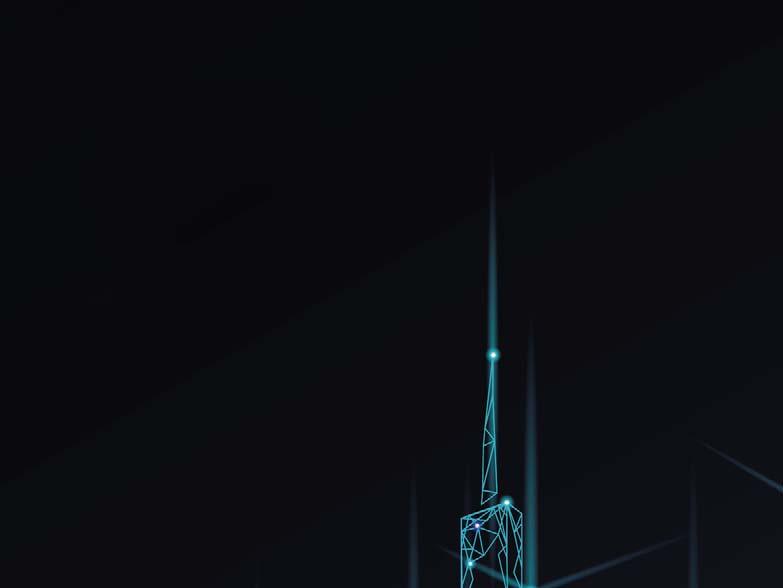
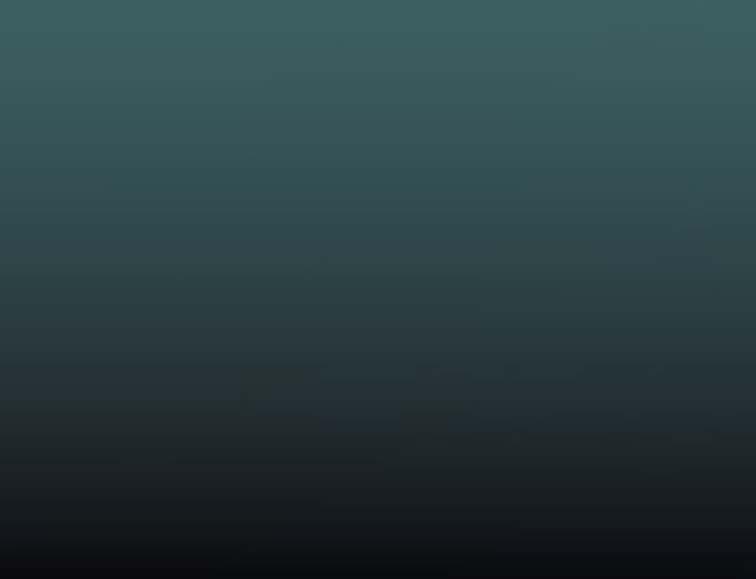


operators contracted a leading service company to analyse 7 years of data on progressive cavity pumps (PCPs), and through machine learning created an application capable of predicting with nearly 90% accuracy the exact day on which the equipment would incur problems, considerably improving predictive maintenance.
The combination of the diff erent advances has dramatically reduced the time for vertical wells drilled and the rig count, where 1000 rigs are able today to cover more ground than 4000 in the 1980s, in the US alone. This achievement went through several cycles of mostly incremental technology improvements, and taking a look at the nature and history of these enables understanding of the importance of innovation in the field, even during a down cycle like the current one.
The historical evolution described in this article emphasises the diff erent types of innovation, both in equipment and automation, developed in the HH-Series hydraulic hoist rigs across a 25-year evolution, culminating in fully automatic operations with the latest accomplishment of automatic casing drilling.


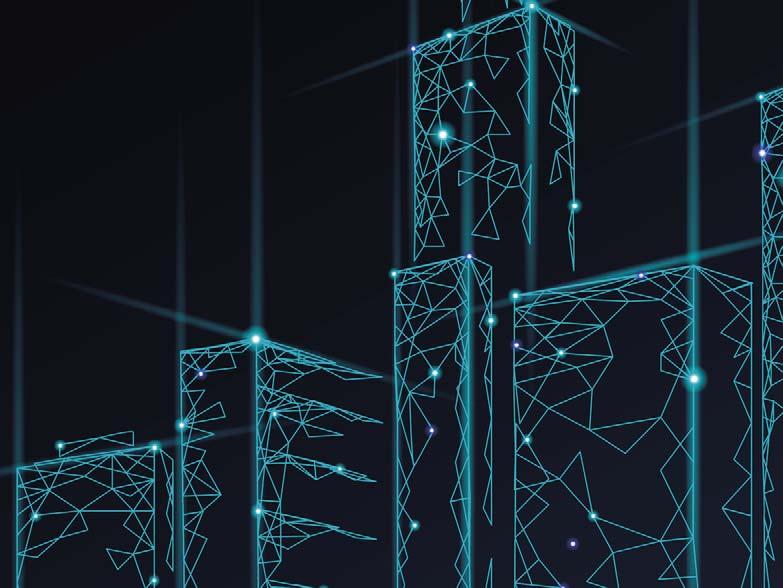

Figure 1. HH-300 mast on trailer.

Figure 2. A low emissions, soundproof HH-300 in town.
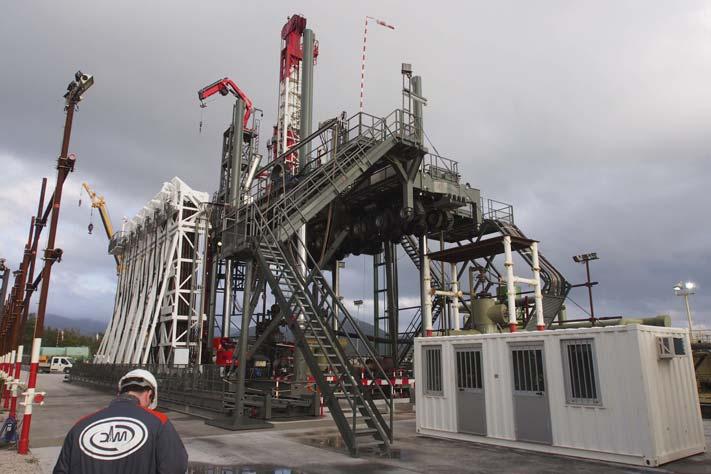
Figure 3. HH-300 automatic drilling rig enabling secure and eff icient operations.
Evolution
The HH-Series began in 1993 with a simple G-75 hydraulic rig for water wells in Italy, currently working in Ukraine. The fast mobilisation and the operations eff iciency of this 75 t (165 000 lb) hookload water well rig laid the groundwork for further development of bigger models of series for oil and gas drilling and workover operations, with a focus on a compact layout and optimisation of rig-up and rig-down operations.
The new design diff ered from conventional land drilling rigs since it did not present a conventional mast structure, or drawworks, long wires or travelling equipment. These were replaced by a powerful hydraulic cylinder, the main hoisting element of the rig, situated on a self-standing telescopic mast with reduced height, permanently mounted on trailers, with other features for faster moving operations (Figure 1). The hoisting system was extremely similar to the current one, based on a telescopic mast fabricated in compliance with API specifications, operating as a hydraulic hoist. It was designed to allow handling of API range 3 (45 ft ) drill pipes, 30 ft drill collars, and API range 3 casings (45 ft ). It was composed of two independent sections, with the bottom one fixed to the trailer frame while the telescopic section ran up and down.
This new, patented design presented a tilting top drive installed on the telescopic mast, in combination with drill pipes stacked in vertical pipe bins.
In the early 2000s, the development of additional hoisting capacity brought the adoption of 272 t hook load rigs (HH-300) in Argentina, Iceland and the US.
The HH-300 used an automatic pipe handling system, which was capable of moving drill pipes from the vertical pipe racks to the mouse hole in complete autonomy.
The old G rigs are now off icially HH-Series. The pipe handler would rotate inside a unique vertical pipe rack surrounding the rig floor. The pipe handler’s arms, installed on a vertical rotating tower, had two clamps grabbing the drill pipes from any pipe of the pipe bins and moving them to the mouse hole or vice versa, depending on an electronic pre-set order. The top drive would then pick a pipe from the mouse hole, lift it and tilt it to the nearby pipe string in the centre hole.
This disruptive innovation further reduced the rig’s footprint, given the vertical stacking of drill pipes instead of horizontally on the ground, and considerably improved the feeding of the pipes.
The unmanned handling of drill pipe presented a crucial safety enhancement: in combination with a hydraulic iron roughneck, making up and breaking the pipe connections, no one was required on the drill floor, thus reducing the drilling crew and resulting in additional eff iciencies and reduced liabilities.
Key to this change was the cooperation and direct feedback of the drilling contractor combined with Drillmec’s ability in flexibly working on finding such a solution.
The HH-Series from now on will have automatic pipe handling systems for models starting from the HH-150 and manual or semi-automatic systems for the smaller and more agile rigs.
With 2006 came the first HH-Series, with a skidding system and self-rising trailerised pipe racks that started operating in Italy.
In 2007, the HH rigs were used on an off shore platform in Congo for a French company, performing workover operations.
Another noteworthy characteristic of the HH-Series rigs is its ability to run operations close and sometimes even in the middle of urban areas from small Swiss towns (Figure 2) to Dallas, Texas, US, while abiding by some of the most stringent noise and emissions parameters.
The carousel structure of the vertical pipe bins helps contain most of the noise and supplementary levels of soundproofing are achieved by solutions aff ecting generator sets, HPU and mud pumps. An anti-spill feature on the rig floor and another floor under the pipe handling system make the HH-Series safe and respectful of the surroundings.
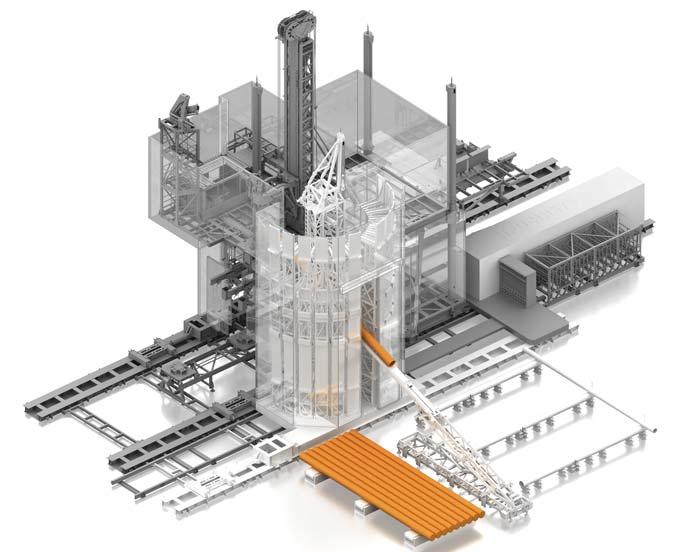
Figure 4. HH automatic casing handling tool.
The first HH-150 was delivered in Siberia, Russia, in 2010, and was able to handle a temperature of -45˚C. The broadness of the portfolio was expanded with the HH-350, with 350 t of hoisting capacity deployed in Colombia and New Zealand in 2011. In the same year, an HH-102 started performing workover operations in Chile while another 25 HH-75 went to China.
In 2012, the first slant HH-75SL started drilling for a major oil company in Australia: it utilised a horizontal pipe handling system at diff erent slanted angles going from 5˚ to 45˚.
The same slant concept was applied the following year to an off shore HH-220 in the UK and in Norway for workover operations.
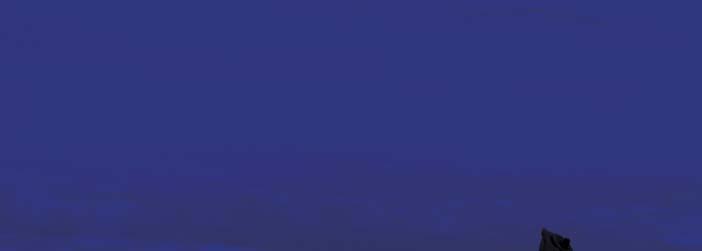

Stay informed
In 2014, several HH-300 rigs with walking systems started drilling in Venezuela.
At this point, the HH rigs are highly automated, safe and eff ective machines that can drill 80% of existing wells, eff iciently performing oil and gas and geothermal drilling and workover operations in six continents.
The advanced automation, combined with key soft ware features, was another fundamental factor that helped the spread of more than 200 units across the globe. The automation of certain routine drilling operations such as tripping and the automatic pipe handling not only reduced the drilling crew, promoting safer and hands-off procedures, but also led to the latest and current version of the HH rigs and arguably the most important development: fully automatic operations.
The first milestone in this regard was reached in 2015: fully automatic tripping operations with an HH-300 (Figure 3) through the new Drillmec Embedded Eff iciency Platform (DEEP) and specifically the Drillmec Automatic Tripping System (DATS) soft ware, once more improving safety and performance. The introduction of a more advanced cyber cabin, with more data points and the application of machine learning and AI, made this step possible.
The last development is being deployed in 2020: automated casing handling. Once the casing is on the rack, it is automatically moved to the catwalk, which carries it through an opening in the middle of the pipe bins carousel directly to the centre hole, where the connection is also completely automatic and unmanned (Figure 4).


Conclusion
The concept of a reliable, small footprint rig package, capable of operating completely automatically through standardised sequences at impressive speed in total safety, has come full circle.
Keep up to date with us to hear the latest in upstream oil and gas news www.oilfi eldtechnology.com
