
12 minute read
Singapore success
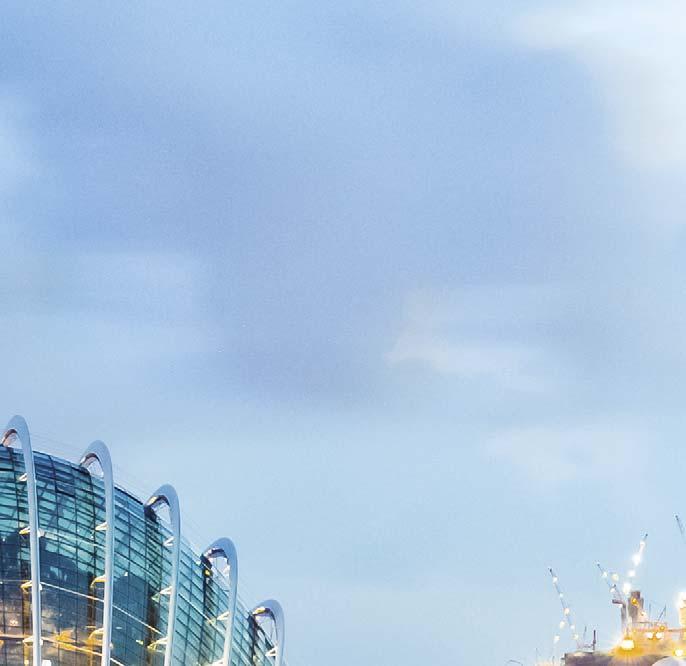
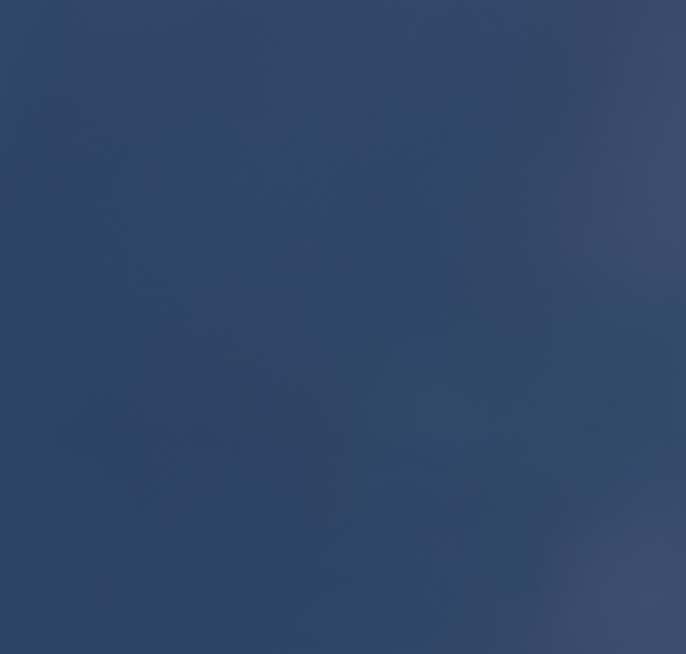
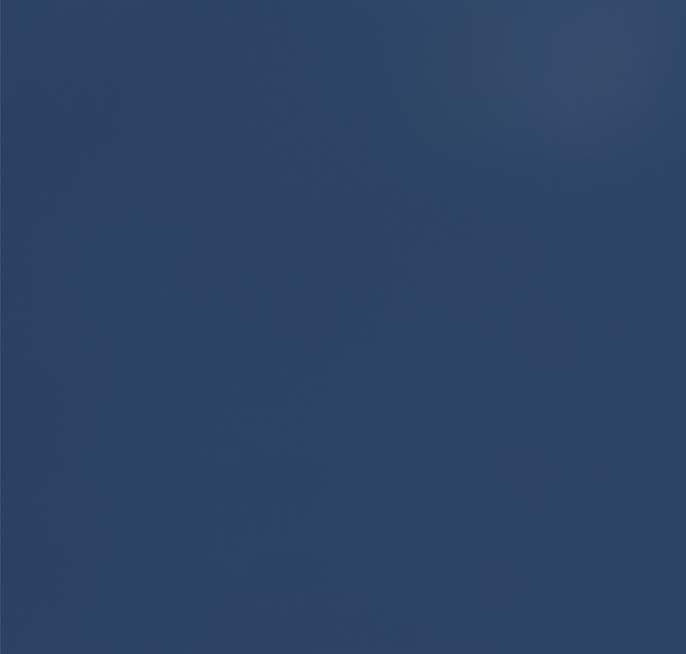
Singapore continued to remain the world’s top bunkering port in 2020. The bunker sales reached 49.8 million t, an increase of 5% year-on-year.1 Introduction of Coriolis mass fl ow meters (MFMs) in the bunker transfer process has acted as a catalyst for this growth. Today there are more than 200 MFMs installed on board the bunker tankers that securely oversee close to US$19 billion worth of very low sulfur fuel oil bunker fuel transactions in Singapore.2 The margin of error here is razor thin; even a 0.5% error would amount to close to US$93 million in losses.
With so much at stake and the bar raised with high standards set using MFM for technology excellence, something special was needed to maintain and safeguard this standard in a sustainable way.
Although the mass fl ow metering system (MFM system) has demonstrated reliable performance over the years, local regulations and custody transfer requirements warranted that MFM be periodically re-calibrated to maintain its capability for bunker fuel transactions. In the absence of a local traceable calibration facility which covers the fl ow/fl uid characteristics for the bunkering application, the MFM must be sent overseas for a re-calibration. This process is expensive and time consuming as it requires a MFM to be removed from the installation site and sent to the suitable calibration laboratory. To avoid fi nancial burdens on the tanker operators and to ensure availability of bunker tankers, the local authority recommended meter verifi cation, a metrologically acceptable pragmatic approach.3 It recommended periodic zero verifi cation (ZV), starting with quarterly ZV in the fi rst year followed by half yearly in the following year. After three years of use, the MFM is required to be calibrated by a recognised and traceable fl ow facility.
Although this approach does not verify the meter’s performance in-situ at actual operating conditions, it ensures that the health of MFM is validated. However, the industry demanded a more holistic approach of validating the meter's performance to ensure continuity of bunker custody transfer operations. Given the challenges the application presented, meter verifi cation using a master meter (MM) was the only viable option.
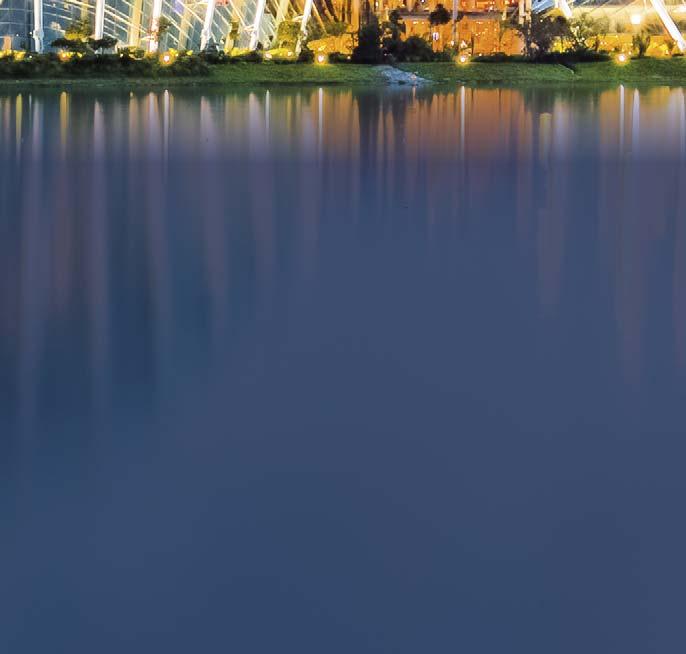
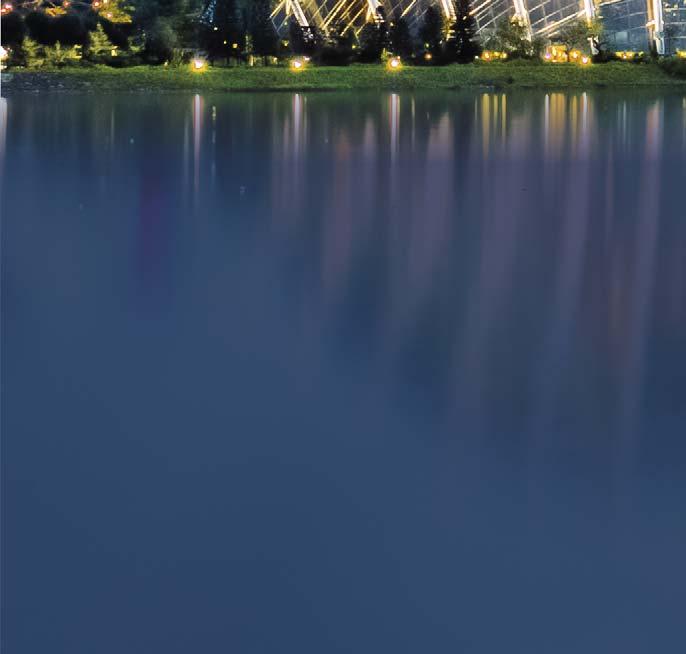
General requirements
Generally, a custody transfer application demands stringent accuracy requirements. The MFM system for bunkering has to fulfi l the overall measurement uncertainty (MU) of 0.5%, in accordance with SS 648.
The MFM from this system must be water calibrated to +/- 0.1% permissible error, and not exceeding 0.2% MU of uncertainty claim for conversion from water to hydrocarbons fuel measurement.
Comparatively for the MM, the requirements prescribed for use as the reference standard were more stringent and complex. These included requirements for bidirectional fl ow, linearity, stability, reproducibility, repeatability error, etc. The MM together with its associated devices are required to be calibrated in an IEC/ISO 17025 accredited calibration laboratory with water and oil of similar properties as bunker fuel. As a rule of thumb, the MM needs to be at least three times better than the MFM under test.

Venkatesh Deshpande, Endress+Hauser, and Darrick Pang,
Metcore International, outline how traceable Coriolis mass flow meter verification will enhance the credibility and reputation of Singapore as a major international port.

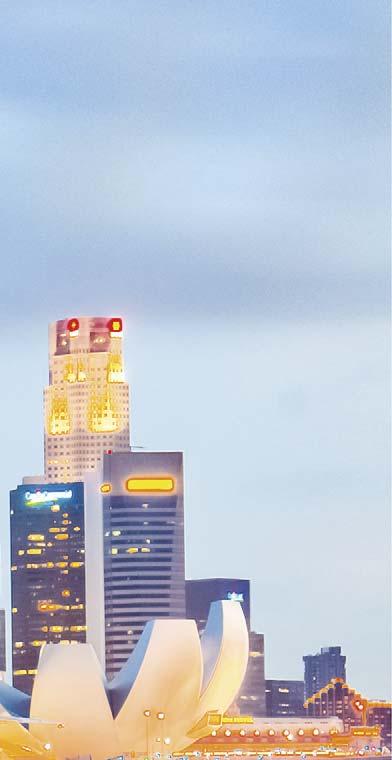
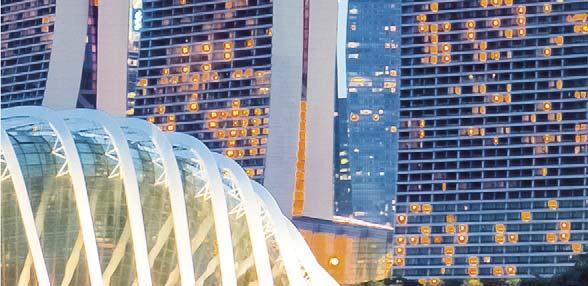
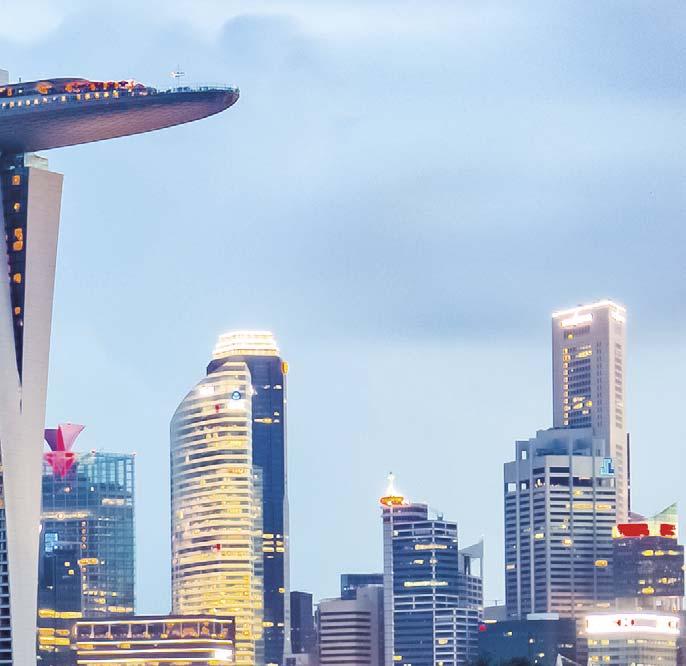

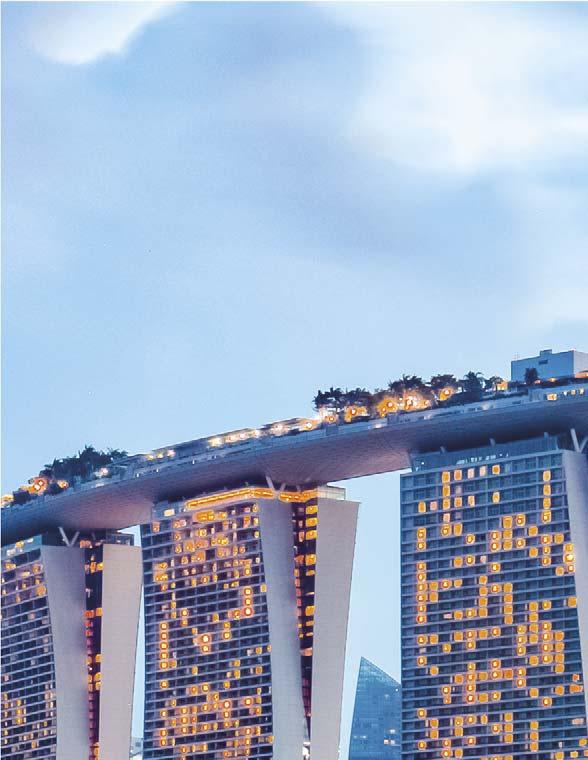
Manufacturing process
Preparation
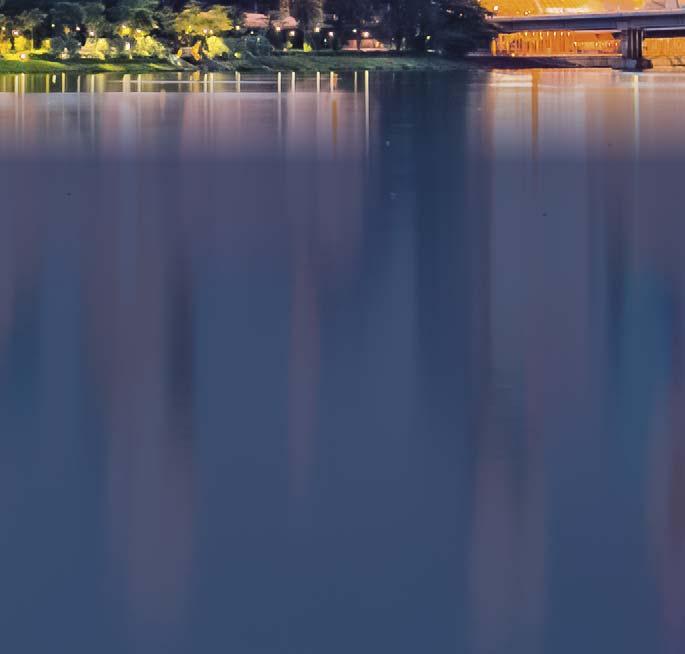
To comply with the requirements set forth by the authority, this MM was manufactured with the most stringent production process with relevant qualifi ed specialists and professional experts monitoring each stage of the process. The utmost professional care was taken in the selection of material and components to ensure the best performance of the meter for the intended application.

Calibration

The MM was subjected to rigorous calibrations, fi rst a bidirectional calibration with water, at Endress+Hauser’s ISO/IEC 17025 accredited calibration laboratory in Reinach, Switzerland, which has a best measurement capability of 0.015%. The results obtained were extremely accurate.
Coriolis MFM measures independent of the fl uid fl ow profi le and has long been recognised to be largely immune to varying process and installation conditions. However, the research has shown that there is a considerable effect on Coriolis measurement accuracy because of fl uid property changes, which can be represented by Reynolds number.
This error is particularly prominent at low fl ow rates in high viscosity fl uids such as bunker fuel. All fl ow metering technologies are affected by this Reynolds number effect.
Following years of research on the Reynolds number effect, Endress+Hauser has developed a patented algorithm that dynamically compensates for the changing Reynolds number. This algorithm has been implemented on all of the company’s Promass Coriolis MFM. Thanks to this algorithm, the meters, with a standard factory water calibration, can measure any fl uid within the prescribed MPE of +/-0.2% per OIML R117-1.4 This has been validated and endorsed by NMi Certin B.V. in the evaluation certifi cate of Promass.5
However, the hydrocarbon industry’s relentless quest for improvements in measurement capability required a fuel oil calibration for this Endress+Hauser MM supplied to Metcore.
It was then calibrated as a fully assembled skid with hydrocarbon products that have similar bunker fuel viscosity range, at an ISO/IEC 17025 accredited independent hydrocarbon fl ow facility in Europe. To maximise the accuracy, Endress+Hauser deployed the enhanced metering accuracy (EMA) procedure during the oil calibration. As part of this procedure, the company’s algorithm provides an output signal that enables the fl ow computer to apply a real time meter factor for every change in the fl uid properties.
EMA calibration covered the entire Reynolds number range that the meter would encounter in the fi eld.
The calibration results with different products were repeatable and accurate within +/-0.05%.
The calibration results and overall measurement uncertainty was computed and reviewed by NMi Certin B.V. and the MFM was endorsed with a declaration enabling it to be used as a MM.
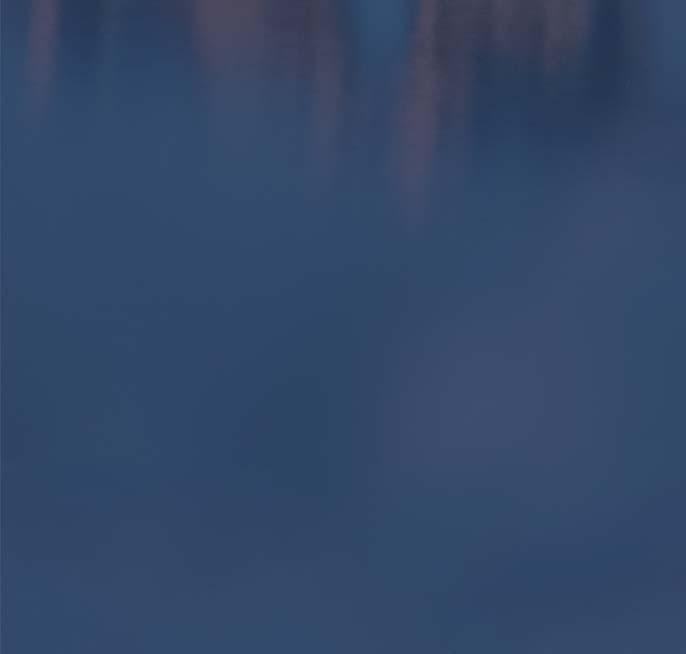
System design
Special considerations were given while designing and selecting the components for the MM system. The system consists of
three major parts: piping section, structural assembly, and electrical and instrumentation (E&I) components.
The piping was designed specifi cally for harsh marine environments and conditions including vibrations, and a proper stress analysis was performed. Piping components were assembled using qualifi ed welders and procedures and tested as per international standards to check for any defects or discontinuity using the most reliable and sophisticated testing technologies.
The skid assembly and structural design was primarily constructed for its mobility and fl exibility, so as to ensure easy interfacing with the bunker tankers’ MFM system.
The E&I components were selected based on their suitability for hazardous area installation and usage. Flow computer and human machine interface (HMI) were designed to be modular, offering fl exibility and easier operation even in hazardous locations.
After assembly, the metering system underwent rigorous tests in the factory, following the stringent Endress+Hauser quality procedures.
Maximising operational effi ciency and easier mechanical and electrical interconnections in the fi eld were the key aspects considered during the skid design.
The verification process
To perform the meter verifi cation using the MM solution, the meter under test (MUT) is connected in series with the MM. The fl ow is circulated in the loop while the process stability is monitored.
Several fl ow parameters are considered for ensuring suitable process conditions are met prior to the start of the meter verifi cation runs. This process stability criteria has been established from years of experience surrounding the operations and maintenance of fl ow measurement systems in bunkering applications. Once the stable process conditions are met at tanker operating fl ow rate, multiple measurement readings are recorded and results on the repeatability and error are tabulated.
As stipulated in TR 80, the MUT is verifi ed to be within 0.12% repeatability and average error of not exceeding +/- 0.3% for the MUT to be deemed suitable for bunker custody transfer application. A verifi cation report is generated which is endorsed by the relevant authorised parties.

Figure 1. Bunker sales volume.1
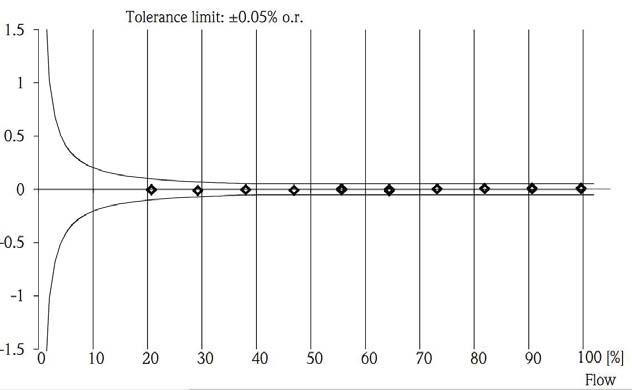
Figure 2. MM water calibration results.
Development of new standards
Following the successful implementation of Coriolis MFM and their resulting benefi ts,6 the industry was looking at harmonisation of measurement methods across the bunker supply chain. This was in addition to the industry need for a traceable, pragmatic, cost-effective and sustainable means of verifying the meters on board the bunker tankers.
The Standards Development Organization/Singapore Chemical Industry Council invited experts from the bunkering industry into the working groups to establish Singapore Standards for meter verifi cation and loading operations of bunker fuel from terminals.
This led to the development of two new Singapore Standards:7 SS 660: 2020: Code of Practice for bunker cargo delivery from oil terminal to bunker tanker using mass flow meter. TR 80: 2020 Code of Practice for meter verification using mass flow meter.
These standards generally addressed the needs of a harmonised measurement method and meter verifi cation of the respective MFMs used across the bunker supply chain.
Operational experience
So far, close to 100 meter verifi cations have been performed using the Endress+Hauser MM solution. These verifi cations include MFMs from a number of suppliers.
One of the key considerations for successful meter verifi cation is achieving process stability. There are many contributing factors that impact this process, including: consistent pumping fl ow rate, pressure, temperature, and aeration during the verifi cation process. Achieving process stability during meter verifi cation is challenging and requires a great deal of expertise in understanding the bunker operation and its process behaviour.
The fl ow computer and its associated HMI was specifi cally programmed to utilise the diagnosed parameters of MFM to determine stability of the process conditions before the start of verifi cation run.
The complete verifi cation operation becomes more effi cient with the MM verifi cation. Overall, the meter verifi cation approach has improved the operational effi ciency for tanker operators as it is more viable and practical as

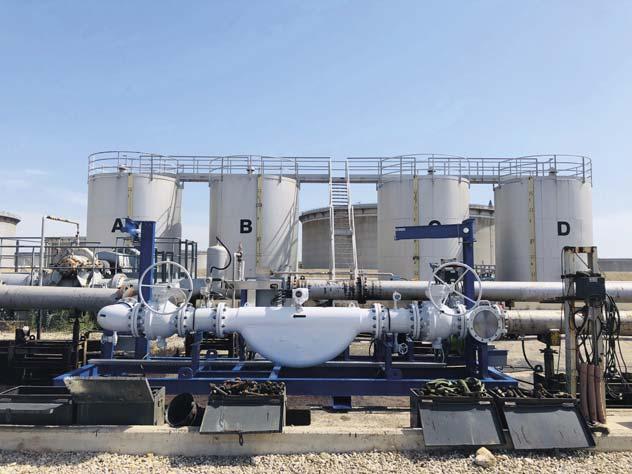
Figure 3. MM assembly undergoing hydrocarbon calibration.
Figure 4. Meter verification in progress using MM.
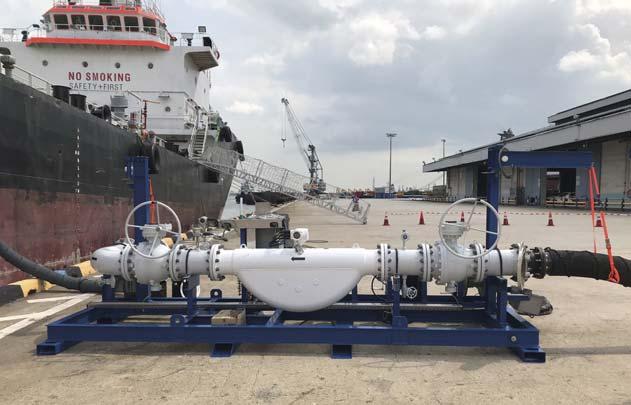
compared to the current system re-validation tests. The downtime needed to evaluate the MFM system performance is minimised substantially, adding to the signifi cant fi nancial savings.
Ultimately, the meter verifi cation methodology enables customers to improve on their bunker tankers’ operating effi ciency management, while optimising their MFM systems for custody transfer purposes.
Further development
The Coriolis MFM’s verifi cation process using the MM solution has been well received by the bunkering industry.
The successful use of a MM as a means of verifying MFMs on board bunker tankers has fuelled interest in not only the global bunkering fraternity, but also from the major oil and gas stakeholders.8,9 There has been an increase in demand for MM solutions by the developing bunkering ports across the globe.
Future development of new ISO standards along the lines of TR 80 and SS 660 will provide the much-needed guidelines for the global oil and gas sector, as well as the marine industry.
In the foreseeable future, the use of the MFM will bring about signifi cant improvements and greater visibility with regards to the digital mass balance of the various stakeholder’s assets. With the improved visibility and good standing, the auditing exercises conducted by fi nancial organisations, such as banks, will become easier.
Many sectors are transitioning to Industry 4.0 by implementing the Industrial Internet of Things (IIoT) in their operations, and this will be a key ingredient in the future roadmap of Endress+Hauser’s MM solution.
Summary
Coriolis MFM have been used in the oil and gas industry for many years as MM to periodically verify the performance of the meter in service in the fi eld. International guidelines such as API and OIML are commonly referenced to perform the meter verifi cation/proving the use of the MM. With the meter verifi cation approach using Coriolis MM, the concerns of the industry stakeholders regarding the re-calibration and performance validation of the custody meter can be holistically addressed. This method enables a reliable and traceable way of ensuring the continuous performance of the MFM on board the bunker tanker without removing the MFM from service, thus eliminating the possibility of downtime in the MFM operations.
MFM are being used in these sectors for reasons such as accuracy, simplicity of operation, low operating costs, stability, availability, proven track record, and compliance to the transparency requirement from regulatory bodies for audit purposes.
By applying the proprietary EMA method utilising optimised Reynolds number linearisation, a new level of MM accuracy can be achieved to address the demands of high precision.
The design of the MM system using a Coriolis MFM is the product of advanced proprietary technological expertise from Endress+Hauser and the extensive experience in the bunkering industry from Metcore International. This collaboration had the support of the Singapore Authorities and the bunkering industry stakeholders, which ensured the success of this project.
Traceable MFM verifi cation will further enhance the credibility and reputation of Singapore as a major international port and is of great value when monetised.
References
1. 'Singapore’s 2020 Maritime Performance Resilient Despite COVID-19
Pandemic', Maritime and Port Authority of Singapore (MPA), (13 January 2021), https://www.mpa.gov.sg/web/portal/home/ media-centre/news-releases/detail/d95e9e96-7df3-4235-80e393dde03dae3e 2. 'Graph: 2020's average bunker price 8% lower than 2019',
Ship & Bunker, (18 December 2020), https://shipandbunker.com/news/ world/240274-graph-2020s-average-bunker-price-8-lower-than-2019 3. SS 648 : 2019: Code of practice for bunker mass flow metering. 4. Organisation Internationale de Metrologie Legale, International
Recommendation R117-1: Dynamic measuring systems for liquid other than water: Metrological & technical requirements. 5. NMi Certin Evaluation Certificate, https://portal.endress.com/ dla/5000910/6098/000/07/TC7149_Pmass300-500_ZE016.pdf 6. 'Factsheet on Case Study on TR48: 2015 on Bunker Mass
Flow Metering', https://www.mpa.gov.sg/web/wcm/connect/ www/8564a1bf-0179-47f7-9a84-0ed5cce14fbf/Annex+A+-+Factshe et+on+Case+Study+on+TR+48+2015+on+Bunker+Mass+Flow+Meter ing.pdf?MOD=AJPERES 7. 'SIBCON 2020: Singapore introduces new MFM bunkering standards
SS 660 and TR 80', Mainfold Times, (7 October 2020), https://www. manifoldtimes.com/news/sibcon-2020-singapore-introduces-newmfm-bunkering-standards-ss-660-and-tr-80/ 8. 'Singapore: Coriolis Master Meter for MFM verification garners international interest', Mainfold Times, (18 February 2020), https:// www.manifoldtimes.com/news/singapore-coriolis-master-meter-formfm-verification-garners-international-interest/ 9. 'Singapore: Milestone achieved as first bunker tanker undergoes MFM verification via Master Meter', Mainfold Times, (22 October 2020), https://www.manifoldtimes.com/news/singapore-milestone-achievedas-first-bunker-tanker-undergoes-mfm-verification-via-master-meter/