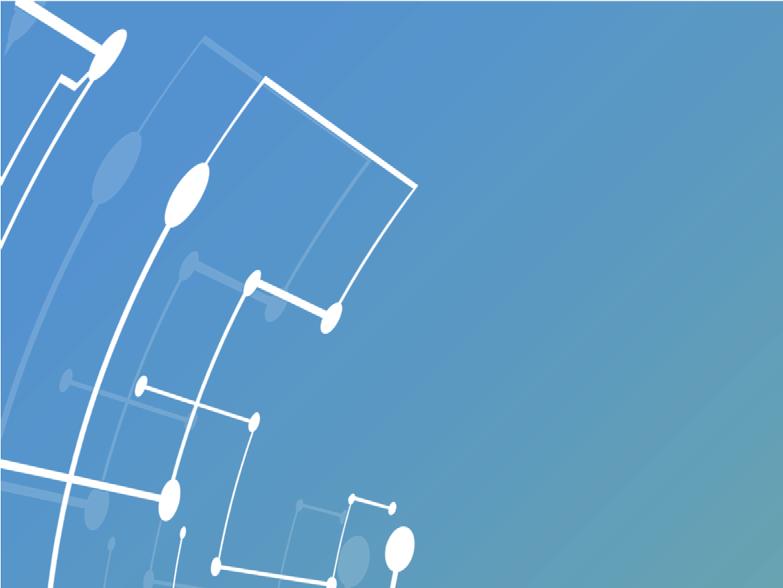
8 minute read
Essential design factors
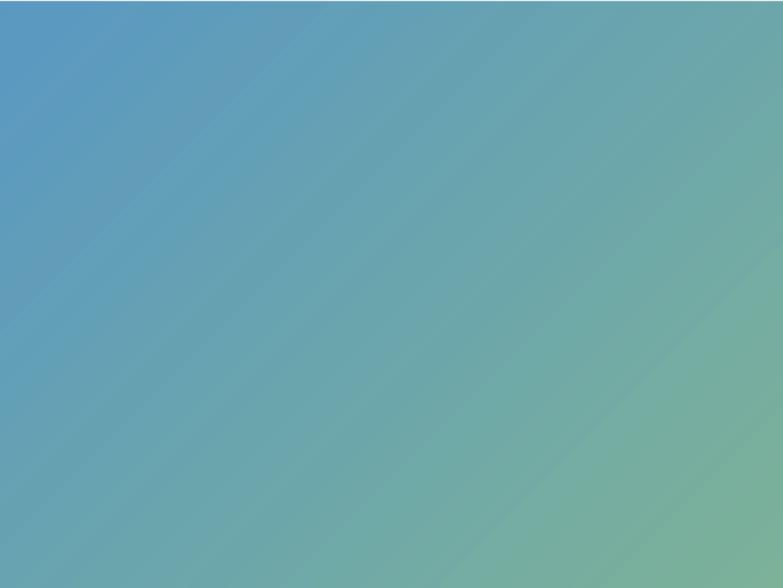
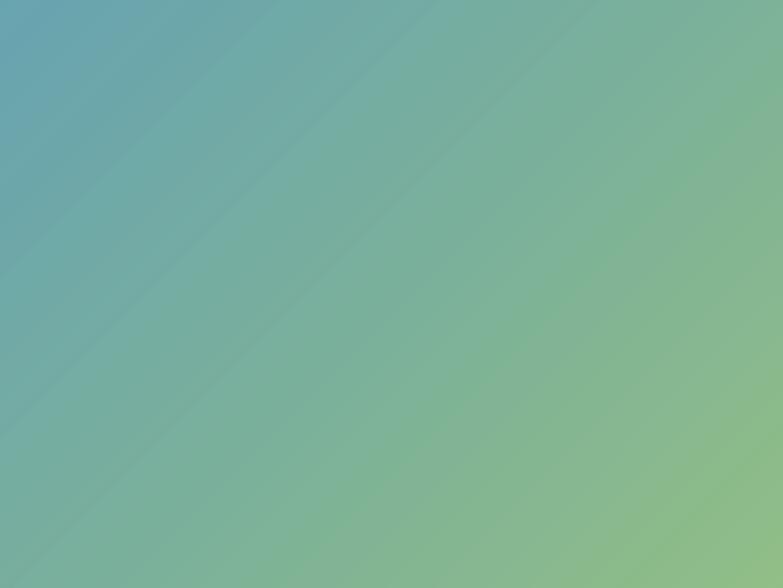
Brandon Stambaugh, Owens Corning, USA, presents three essential design factors to consider when insulating storage tank systems.

Unique in shape and often storing volatile contents, storage tanks are no ordinary structures. They can reach 50 m (164 ft) in height, 90 m (295 ft) in diameter and hold up to 270 000 m3 (9 450 000 ft3). From a thermal perspective, storage tanks house materials demanding a range of temperature environments – from cryogenic (LNG, LOX, LIN) to high temperatures (thermal fl uids, bitumen asphalts, molten salts). Storage tanks present complex challenges for those charged with ensuring an insulation system supports safety, helps preserve contents inside the tanks, and protects long-term operational effi ciencies. Addressing these challenges as part of the design process can support the performance and longevity of the storage tank asset. This article will consider three essential design factors for insulating storage tanks.
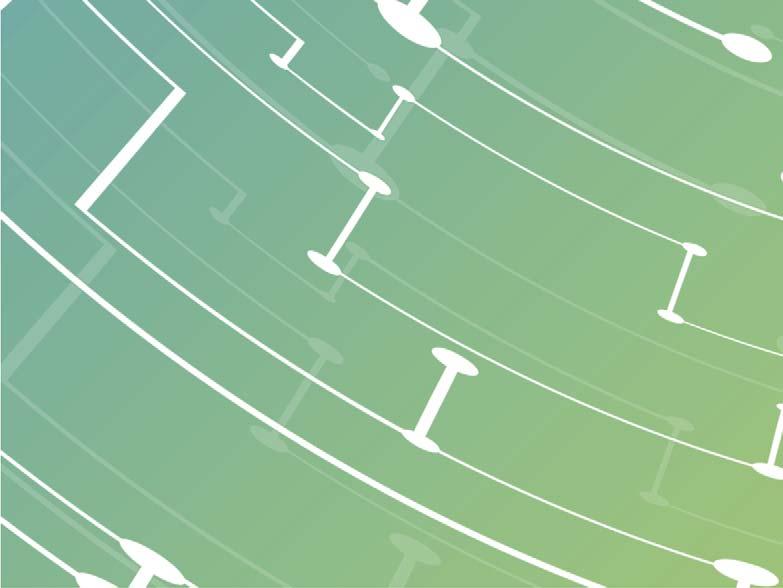

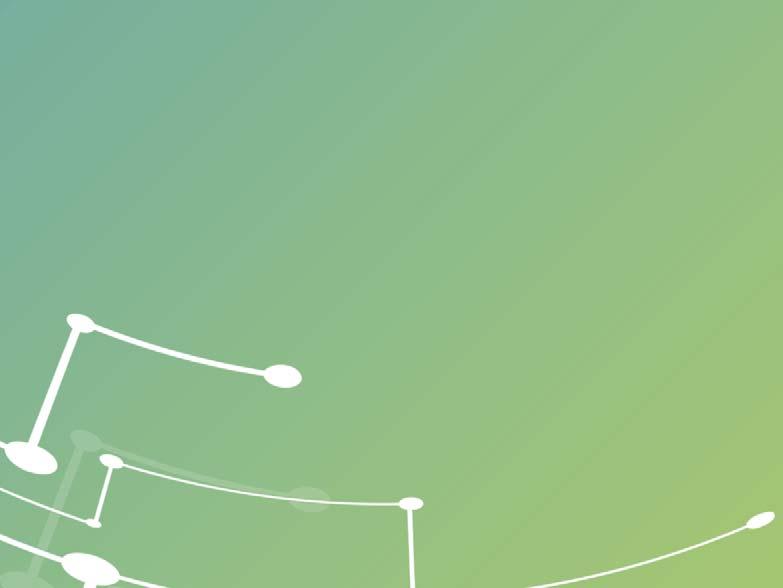
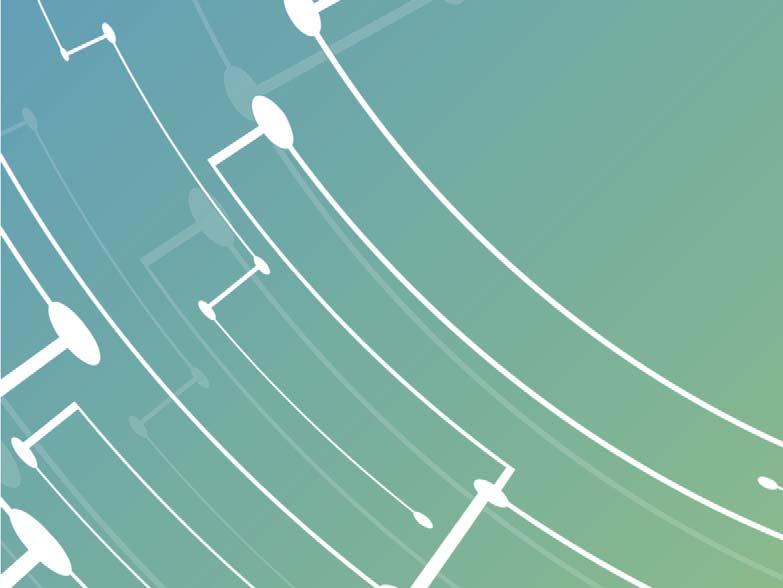
Essential design factor 1: compressive strength, stability, and weight load
When considering insulation materials, compressive strength is often overlooked as a distinguishing feature; however, compressive strength is needed to support loads, such as in tank bases. Compressive failure of insulation can cause deterioration of the insulation system and lead to damage of mechanical systems and equipment.
Tank base insulation must provide the necessary compressive strength to support fi lled containment tanks. Failure to provide adequate support can allow for settlement of the base, which may generate ground heaving, permit foundations to reach unwanted hot or cold temperatures, and reduce thermal insulating capacity. If damage continues, the tank bottom could eventually rupture, allowing contents to leak or resulting in reduced process control and solidifi cation of the contained liquid.
Insulating materials used on tank bases also need to resist long-term creep or compressive creep. This distortion may cause insulation to move or deform and can occur when insulation is under a persistent mechanical load. In addition to providing compressive strength, insulation used on tank bases needs to provide dimensional stability when exposed to extreme temperatures. Organic and open-celled insulation materials, which are generally not suitable for service in this application, may exhibit swelling, warping, distortion and expansion or shrinkage, depending on the temperatures they encounter. Material selection is critical, and choosing an inorganic, closed-cell material, like cellular glass insulation, can provide the necessary stability over time and across the temperature range involved to protect long-term tank function.
Tanks containing cold to cryogenic materials are expected to comply with industry standards such as EN 14620:2006 – ‘Design and manufacture of site built, vertical, cylindrical, fl at-bottomed steel tanks for the storage of refrigerated, liquefi ed gases with operating temperatures between 0°C and -165°C (32 °F and -265 °F)’ – EN 14620-4 and API Standard 625.1 The initial standard dictates elements and application rules for design, while the related EN 14620-4 addresses the use and design of insulation and specifi es the structural requirements involved.2 Tank and support structure insulation should be able to handle the loads involved, providing for considerations related to seismic conditions and capable of withstanding both normal operating conditions and hydrostatic testing pressure.
Similarly, API Standard 625 – ‘Tank systems for refrigerated liquid gas storage’ – addresses components of tanks intended to house liquefi ed gases.3
Additionally, insulation system designers can consider how insulating materials to be used with tanks and tanks bases are examined. Standards such as ASTM C165 – ‘Standard Test Method for Measuring Comprehensive Properties for Thermal Insulations’ – may be used to help determine compression behaviour.4
At above ambient temperatures, if insulation without the necessary compressive strength and dimensional stability is used on storage vessels housing materials, it can put the contents at risk of increasing viscosity and solidifi cation. Foundation settlement under the tank’s weight may also reduce the thermal performance of the vessel. However, use of an inorganic, high weight-bearing insulation, such as cellular glass insulation, can provide the required comprehensive strength and dimensional stability to insulate tanks and protect tank base function. Because cellular glass insulation does not warp or deteriorate, it can also provide consistent thermal performance while managing a heavy weight load.
Essential design factor 2: storage temperature and thermal performance
Tank building standard EN 14620 also outlines thermal requirements for the insulation components used with tanks.1 The installed insulation must maintain internal tank temperature to prevent more boil-off than is permitted while keeping outer tank components above a set temperature. These temperature requirements are in place to help prevent the formation of ice or condensation on the exterior of the tank, along with keeping the ground under the tank from freezing.
The consistency of the thermal performance of an insulation across the temperature range infl uences facility effi ciency and helps to limit heat transfer, achieve minimal thermal expansion or contraction, and supports employee safety.
Another essential practice for reducing energy loss is insulating the tank walls and roof systems. Properly insulating the entire system helps limit energy loss by creating a thermal barrier between the internal process temperature and the external environment. Proper insulation system confi gurations can also help reduce maintenance costs and support employee safety.
Regardless of content temperature, insuffi cient insulation may permit excessive heat transfer. When tanks contain below ambient liquids, insuffi cient insulation may allow the surrounding ground to freeze, adding to the potential for instability or movement. This transfer may mean that the support structure starts to freeze, becomes brittle or develops cracks and mechanical issues. These conditions can damage the tank and could lead to evaporation of tank contents. In addition, when working with cryogenic liquids, the whole tank system should be insulated to help reduce boil-off, which can increase operating costs. When heat enters the cryogenic tank, it gives a cold liquid, such as LNG, the opportunity to evaporate, creating boil-off gas (BOG). Reducing the boil-off helps control pressure within the tank and reduces methane, a prolifi c greenhouse gas, or other products of methane combustion, such as CO2, from venting or fl aring processes from being released into the atmosphere.
At the other end of the temperature spectrum, insulated tank bases are needed to protect materials stored at higher temperatures. In these instances, insulation on the supporting platform can protect the concrete foundations from heat damage and help maintain thermal effi ciency.
Failing to properly insulate tank bases also can increase energy losses – especially when storage tanks holding hot liquids are not completely full. In these cases, the hot liquid is primarily in contact with the base of the tank and, if the base is not insulated, there is little to limit heat transfer, ensure process control or prevent the contained material from increasing in viscosity.
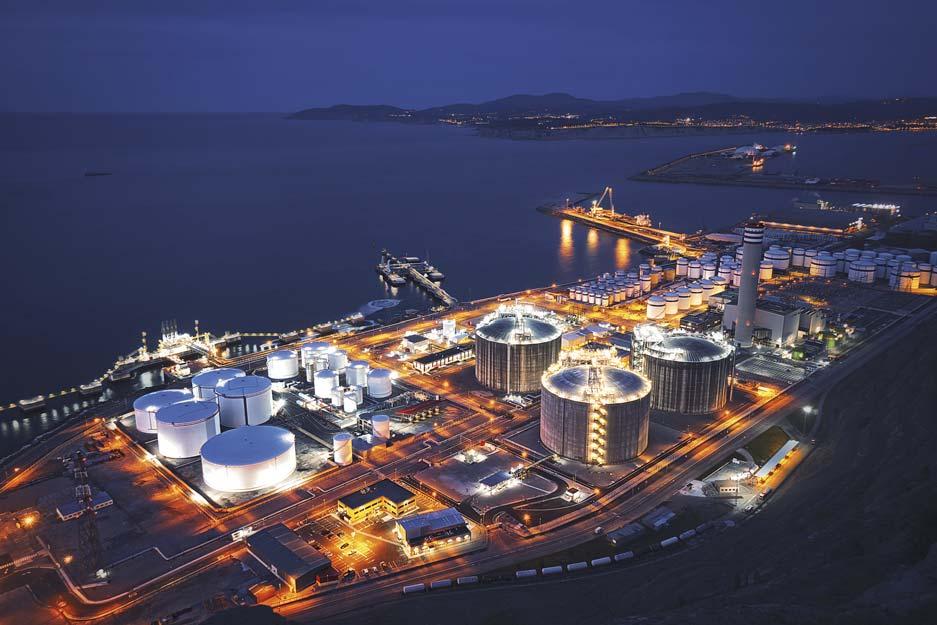
Figure 1. Insulation systems for industrial storage tanks take design and planning.
A specification strategy to mitigate risk

Figure 2. Insulation systems in flat-bottomed storage tank bases and walls help maintain thermal performance.
Essential design factor 3: moisture and corrosion risk
The physics of air and water can also pose a risk as temperature differences between the contents of low-temperature storage vessels and ambient air can prompt condensation to form on the outside edge of storage tanks. Under certain conditions, if permeable or absorptive insulating materials are used, moisture could lead to corrosion under insulation (CUI) and insulation performance could be degraded. Over time, this also may impair the mechanical strength of the tank if corrosion is allowed to progress to a critical state.
Corrosion development under insulation can continue undetected until a leak occurs. A containment breach is a safety concern and may pose a particular hazard for employee safety when the materials contained are high in temperature or pressure, or if the tank holds toxic or fl ammable liquids/gases.
Corrosion concerns can be mitigated by insulating, ambient and high-temperature carbon steel tanks with non-permeable, non-absorptive closed-cell insulation systems – such as those designed to include cellular glass insulation. Using cellular glass insulation, which is impervious to moisture and water vapour, helps protect the system. Installing a non-absorptive insulation also avoids risk of fl ammable liquids or chemicals being retained if a leak should occur.
Despite the range of diffi cult conditions these systems face, 100% closed-cell FOAMGLAS® cellular glass insulation is able to address the challenges and support essential design factors. Used to insulate tank bases for a range of temperatures, FOAMGLAS® High-Load-Bearing (HLB) insulation provides compressive strength to help protect tanks from unwanted settlement and thermal transfer while remaining dimensionally stable. As labour is always an important consideration, this insulation also comes in a range of larger block sizes to help with installation effi ciency.
Properly installed and maintained insulation can also help protect underlying supports from becoming brittle, warping or being otherwise damaged depending on the temperature of stored materials. On all parts of the system, the insulation aids in maintaining internal process/storage temperatures, reducing boil-off and limiting the potential for liquids to have undesirable changes in viscosity. Inorganic cellular glass insulation also remains impermeable to moisture vapour – helping avoid corrosion – and will not absorb water, water vapour or other liquid hydrocarbons.
References
1. 'Design and manufacture of site built, vertical, cylindrical, flat-bottomed steel tanks for the storage of refrigerated, liquefied gases with operating temperatures between 0°C and -165°C', General,
British Standards Institution, (BS EN 14620-1:2006), (2006), retrieved from https://shop.bsigroup.com 2. 'Design and manufacture of site built, vertical, cylindrical, flat-bottomed steel tanks for the storage of refrigerated, liquefied gases with operating temperatures between 0°C and -165°C', Insulation components, British Standards
Institution, (BS EN 14620-4:2006), (2006), retrieved from https://shop.bsigroup.com 3. 'Tank Systems for Refrigerated Liquefied Gas Storage',
American Petroleum Institute, (API STD 625), (2018), retrieved from https://global.ihs.com/ 4. 'Standard Test Method for Measuring Compressive Properties of
Thermal Insulations', ASTM, (ASTM C165-07[2017]), (2017), retrieved from https://www.astm.org/Standards/C165.htm