Our conveyors? They are running smoothly.
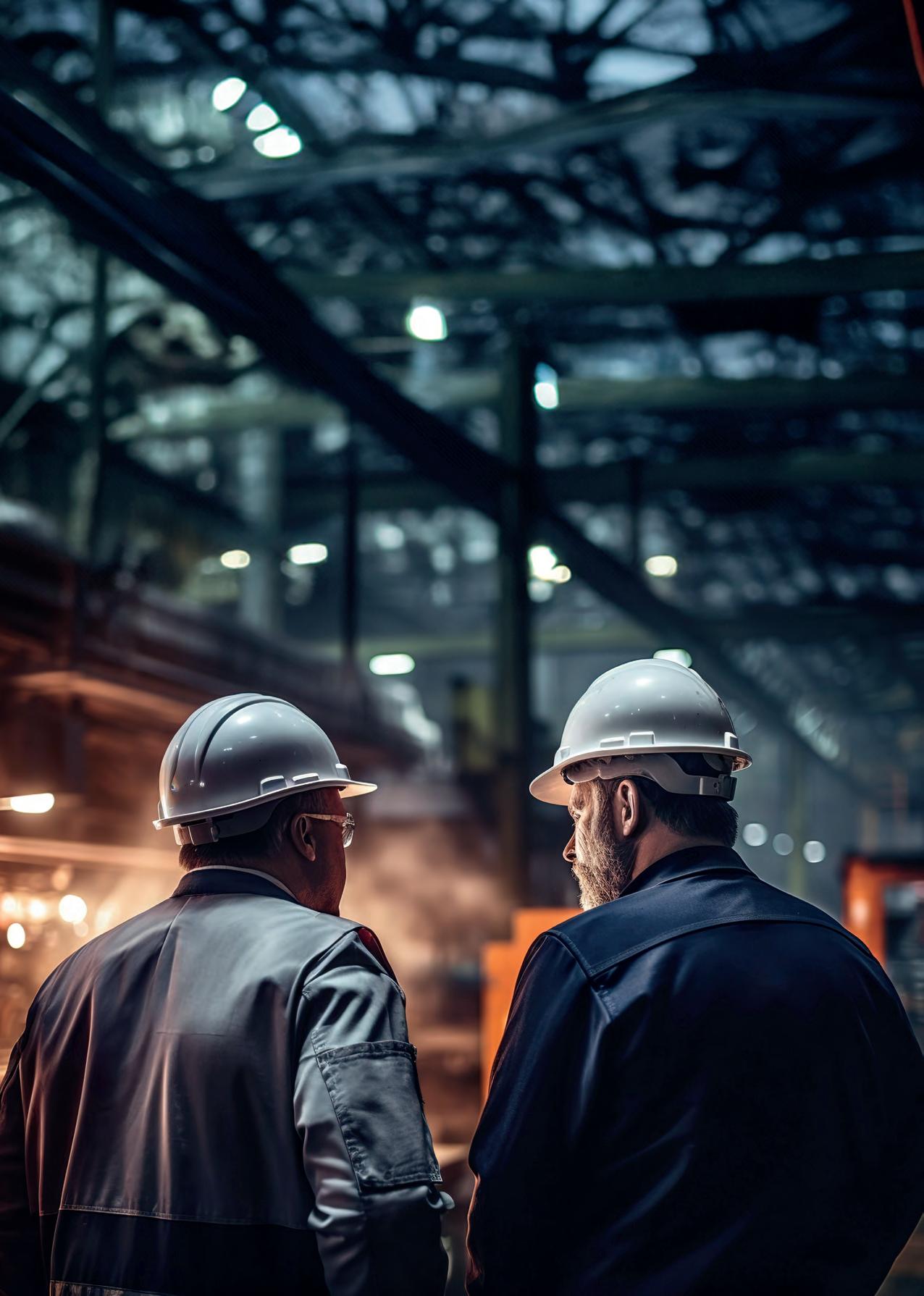
Thousands of chain installations in the industry operate smoothly, convincing operators day by day of their reliability.
We move industries.










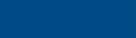











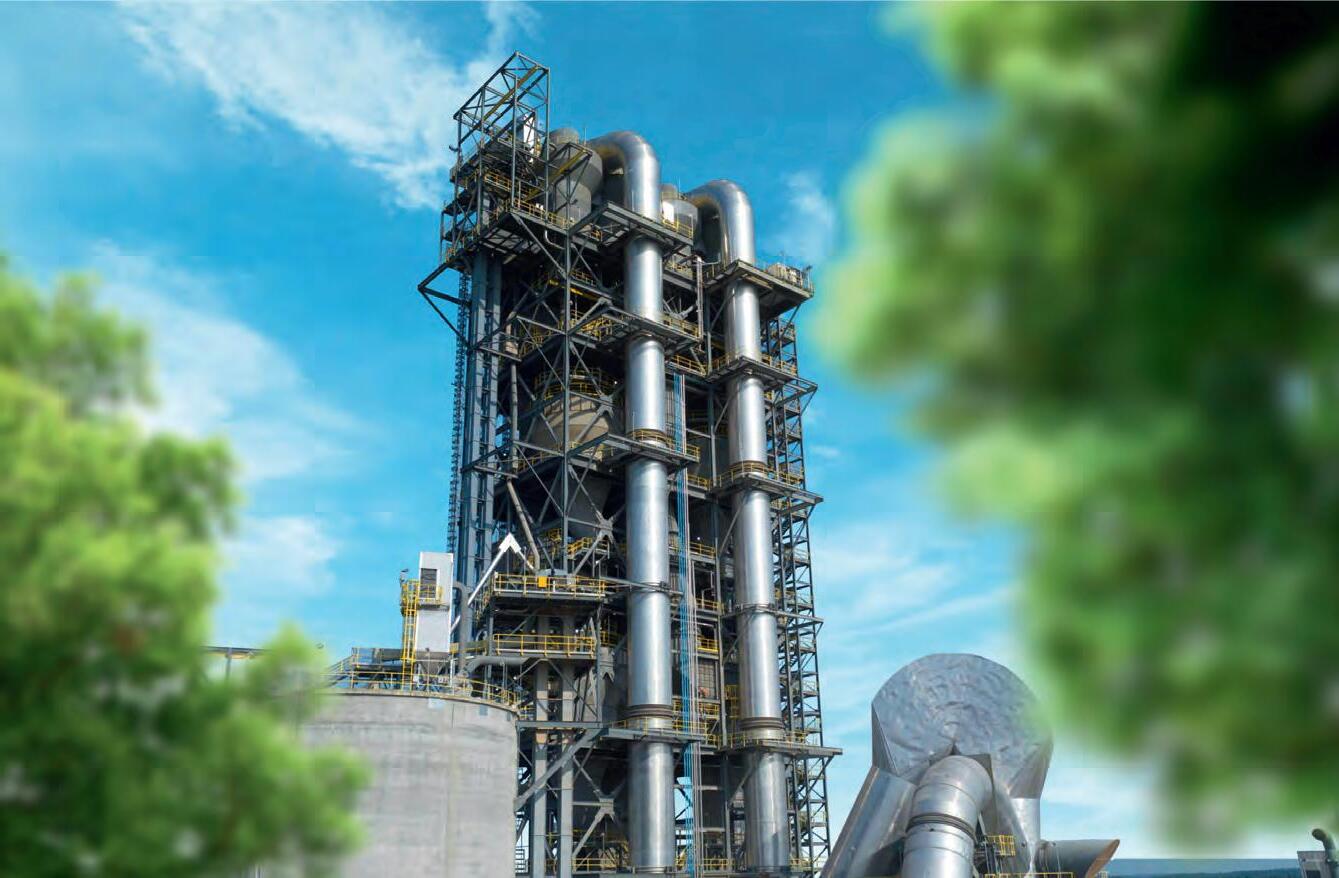
Thousands of chain installations in the industry operate smoothly, convincing operators day by day of their reliability.
We move industries.
Carbon capture is a critical technological pathway for cement decarbonization. That’s a challenge. But there are ways to make it easier. Like converting to oxyfuel combustion. Oxyfuel raises the CO2 concentration in cement plant exhaust gases and makes capturing that CO2 much more cost-efficient.
Here at KHD we’ve been involved in oxyfuel development since 2010. We also come with a long history of excellence in innovation, plant design, and process engineering. So, when it comes to implementing oxyfuel at your cement plant, we are your expert partner.
Discover more on our website or connect with our experts to discuss your specific oxyfuel application needs and let’s deliver Cement beyond Carbon together.
LEARN MORE
Empowering carbon capture with oxyfuel
khd.com/oxyfuel
49 Unlocking Eco-Friendly Energy Solutions
Mirko Ferrari, Turboden, examines the role of ORC waste heat recovery technology as a tool to decarbonise the cement sector.
ROAD TO NET ZERO
10 Cementing A Net-Zero Future
Fabian Apel, Johanna Hoyt, Francisco Marques, Sebastian Reiter and Patrick Schulze, McKinsey, explore potential pathways for the cement industry to accomplish the transition to net zero.
14 Upgrading The US Infrastructure Industry
Mike Ireland, PCA, explains how Portland-limestone cement is just one of many methods being used by cement producers to reduce their environmental impact.
20 Laying The Foundations
McKenzie Smith, Climate Action Reserve, explains how a voluntary carbon market can help fund industries, including cement, to reduce their greenhouse gas emissions.
27 Say Hi To Hydrogen UTIS considers the role of hydrogen technology in not only improving combustion efficiency but also decarbonising cement production.
33 Consolidating Carbon Capture
Jeffrey Tyska, Honeywell UOP, explores key technologies for enabling carbon capture from cement plants.
40 Scaling Up And Cutting Costs
Andrew Baxter, Chart Industries, and Dr Bodil Recke, FLSmidth, discuss a collaboration to identify cost-competitive pathways to reduce CO2 emissions in the cement industry.
43 Zero Waste For Net Zero
Arun Mote, Triveni Turbines, discusses waste heat recovery and waste-to-energy as potential strategies for reaching net zero by 2050.
54 No Waste Heat, A Sustainable Feat
Andrea De Finis and Sara Milanesi, Exergy International srl, explore the benefits of ORC technology over steam Rankine cycle systems and consider the importance of turbine design and configuration.
62 Logistics From Portugal To The World Cachapuz elaborates on the implementation of automation and logistics optimisation systems in the cement industry.
68 Focusing On Air Flow
Ozan Can Ülgen, Araz Cabbarli, Halil İbrahim Karabulut, & Kadir Körükcü, ALFER Engineering, discuss how to optimise fans and ducts, emphasising the importance of inlet line design.
72 Next Generation Construction Materials
Martin Paterson, C2CA, predicts the next best SCMs in the race beyond slag and fly ash.
78 Making White Cement Sustainable
Michele Di Marino, Stefano Zampaletta and Frank Brandt, Cementir Group, explain how to reduce the environmental impact of white cement production, while securing a superior performance.
HEKO Ketten GmbH, Germany, has supplied conveyor chains for the bulk handling industry for more than 100 years. Chains made in Germany are running in thousands of conveyors worldwide. No matter if it is cement, clinker, ash, or fertilizer that needs handling, HEKO’s customers agree that the company’s chains run smoothly. HEKO´s experience solves conveyor problems together with the customers. A wide range of chains and sprockets – even individually manufactured for a specific problem – provide a solution for all demands.
FLSmidth Cement is a technology and service supplier with a passion to help our customers produce cement efficiently. After 140+ years of pioneering new innovations, we are uniquely positioned to be at the forefront of our industry’s green transition.
Find out more at www.flsmidth-cement.com
Production: Iona MacLeod
iona.macleod@palladianpublications.com
Sales Director: Rod Hardy rod.hardy@palladianpublications.com
Sales Manager: Ian Lewis ian.lewis@palladianpublications.com
Sales Executive: Louise Graham louise.graham@palladianpublications.com
Events Manager: Louise Cameron louise.cameron@palladianpublications.com
Digital Events Coordinator: Merili Jurivete merili.jurivete@palladianpublications.com
Digital Administrator: Nicole Harman-Smith nicole.harman-smith@palladianpublications.com
Administration Manager: Laura White laura.white@palladianpublications.com
Reprints reprints@worldcement.com
Hello Dear Reader, and welcome to the March issue of World Cement. Looking at the Contents page this month, you might notice that things are a little ‘greener’ than usual in terms of topics. That’s because the contents of this issue have been specially curated to focus on the challenge of decarbonisation and various aspects of the cement industry’s transition to net zero.
And there’s no doubting the scale of that challenge. By most estimates, the cement industry is responsible for ~8% of all man-made CO2 emissions, making it a major contributor to mankind’s environmental footprint. And demand is only set to grow over the long term as the world builds the vital infrastructure for an increasingly urbanised, energy-hungry, and growing global population. Indeed, the UN predicts that by 2050 – the date that many industries (including cement) and nation states are targeting for net zero – the global population will have risen to 9.7 billion people, 68% of which will live in urban areas.
The cement industry thus finds itself tied to the twin challenges of building the world of the future, whilst playing a pivotal role in limiting the impacts of climate change.
CBP019982
Annual subscription (published monthly): £160 UK including postage/£175 (€245) overseas (postage airmail)/US$280 USA/Canada (postage airmail). Two year subscription (published monthly): £256 UK including postage/£280 (€392) overseas (postage airmail)/US$448 USA/Canada (postage airmail). Claims for non receipt of issues must be made within 4 months of publication of the issue or they will not be honoured without charge.
Applicable only to USA and Canada: WORLD CEMENT (ISSN No: 0263-6050, USPS No: 020-996) is published monthly by Palladian Publications, GBR and is distributed in the USA by Asendia USA, 17B S Middlesex Ave, Monroe NJ 08831.
Periodicals postage paid at Philadelphia, PA and additional mailing offices. POSTMASTER: send address changes to World Cement, 701C Ashland Ave, Folcroft PA 19032
Copyright © Palladian Publications Ltd 2023. All rights reserved. No part of this publication may be reproduced, stored in a retrieval system, or transmitted in any form or by any means, electronic, mechanical, photocopying, recording or otherwise, without the prior permission of the copyright owner. All views expressed in this journal are those of the respective contributors and are not necessarily the opinions of the publisher, neither do the publishers endorse any of the claims made in the articles or the advertisements. Uncaptioned images courtesy of Adobe Stock. Printed in the UK.
Palladian Publications Ltd 15 South Street, Farnham, Surrey GU9 7QU, UK Tel +44 (0)1252 718999
Email: mail@worldcement.com
Website: www.worldcement.com
Thankfully, as even a brief flick through the pages of this issue will reveal, these challenges are far from insurmountable. By acting today, developing the necessary expertise, and taking advantage of new technologies, processes, and ways of thinking about operations, the cement industry can become a leader in the green transition and help build a world we can be proud of.
But of course, the sheer importance of this topic isn’t the only reason I bring it up this month – I have an ulterior motive. And if you’re currently reading this whilst enjoying the surroundings of Hotel Cascais Miragem on Lisbon’s Atlantic coast, then you’ll likely have guessed what that is. I am, of course, referring to EnviroTech – World Cement’s first in-person conference and exhibition, devoted to discussing the cement industry’s decarbonisation journey.
If you are one of those who’ve joined us in Lisbon for EnviroTech, then: Welcome! Or as the locals might say: Bem-vindo a Lisboa!
We have a fantastic presentation agenda lined up for you; featuring industry leaders and technical experts from many of the world’s foremost cement producers and equipment suppliers, covering everything from alternative fuels, to carbon capture, to energy efficiency, digitalisation, SCMs, and more. On top of all that, be sure to take part in the multiple Q&A sessions taking place throughout the agenda, enjoy our evening networking events featuring local cuisine, and attend our closing Panel Discussion on 13 March, showcasing insightful commentary from leading industry stakeholders.
And for those of you reading who were unable to join us for EnviroTech this year, I hope this issue whets your appetite and provides you with a taste of the kind of things we have going on. Perhaps you’ll be able to join us next time? Until then, tchau.
Heidelberg Materials North America has announced a significant milestone in its two-stage competitive procurement process as it works to select the capture technology and contractor for providing the CO2 separation solution for its Edmonton, Alberta, Carbon Capture, Utilisation, and Storage (CCUS) Project. This project will be the first full-scale application of CCUS in the cement sector.
As part of this process, Technip Energies, a world-leading engineering and technology player for the energy transition, has been selected as one of the partners for this effort and has been awarded a front-end engineering and design (FEED) contract for the carbon capture technology for the Edmonton CCUS project. Powered by the Shell CANSOLV® CO2 capture system, the Technip Energies solution which will be the basis of the FEED study, offering cutting-edge performance based on regenerable amine technology.
“We are excited to take this latest step in our journey to produce the world’s first net-zero cement”, said Joerg Nixdorf, Vice President Cement Operations, Northwest Region for Heidelberg Materials North America. “With each milestone we come closer to realising our vision of leading the decarbonisation of the cement industry.”
“We are pleased to have been selected by Heidelberg Materials North America to provide the FEED of this groundbreaking project in Canada”, said Christophe Malaurie, SVP Decarbonisation Solutions for Technip Energies. “Leveraging our carbon capture solution powered by the Shell CANSOLV® CO2 capture system, we are committed to supporting the decarbonisation of the cement industry and Heidelberg towards the production of net-zero cement.”
Heidelberg Materials North America will be commissioning the world’s first net-zero cement plant at its Edmonton location by adding CCUS technology to an already state-of-the-art facility. The plant will eventually capture and store an estimated 1 million t of carbon dioxide each
year, which is the equivalent of taking 300 000 cars off the road annually. Subject to finalisation of federal and provincial funding agreements, the company anticipates carbon capture to begin in late 2026.
Lafarge Canada has announced the completion of another important milestone in the company’s commitment to drive both sustainable and innovative products – the full transition of production from traditional general-use cement to OneCem®, a greener product that results in significantly lower CO2 emissions, at the St-Constant Cement Plant in Quebec.
“We are excited to take another crucial step in our sustainability journey. The transition to OneCem production at our St-Constant plant indicates Lafarge Canada’s nonstop commitment to driving positive change within our construction industry. Our teams have been engaged in reducing our products’ environmental impact by embracing greener practices and materials”, expressed David Redfern, president & CEO of Lafarge Canada (East).
OneCem is a limestone blended cement manufactured using less clinker than traditional Portland cement. By converting the St-Constant Plant’s production to OneCem, Lafarge Canada projects a reduction of about 60 000 t of CO2 emissions in 2024. This equates to CO2 emissions from 16 267 passenger vehicles or 877 972 tree seedlings grown for 10 years.
The St-Constant plant has been at the forefront of driving sustainability and innovation in cement production in Quebec for many years. Building upon its achievements in carbon reduction, the plant has implemented initiatives such as circularity through ECOcycle, as well as collaborating with organisations like CarbiCrete and Patio Drummond to facilitate the production of zero-carbon concrete. This transition to OneCem production at the plant reinforces the company’s decarbonisation strategy, widening the availability of environmentally improved options to customers.
“Our team at St-Constant is proud to be taking actions towards sustainability. With this transition, we are not only reducing our carbon footprint but
also aligning with our organisation’s drive to be a leader for sustainable construction throughout Eastern Canada”, added Andrew Stewart, Vice President of Cement, Lafarge Canada (East). “This is a significant development, and we are eager to contribute to the realisation of a net-zero future.”
CONFERENCE
April 28 – 02 May, 2024
Denver, Colorado
www.cementconference.org
ACHEMA 2024
10 – 14 June, 2024
Frankfurt, Germany
www.achema.de
HILLHEAD 2024
25 – 27 June, 2024
Buxton, UK
www.hillhead.com
FICEM TECHNICAL CONGRESS
02 – 04 September, 2024
Guatamala
www.ficem.org
SOLIDS
09 – 10 October, 2024
Dortmund, Germany
www.solids-dortmund.de
VDZ CONGRESS
06 – 08 November, 2024
Düsseldorf Germany
www.vdz-online.de
By exclusively offering OneCem for general use from its St-Constant cement plant, Lafarge is not only contributing to environmental sustainability but also empowering customers to diminish their own carbon footprint in the built environment.
Cemex and Orcan Energy extend waste heat recovery collaboration to a broad decarbonisation partnership
Cemex and Orcan Energy have announced a large-scale partnership to decarbonise cement production through waste heat recovery (WHR).
Building on the initial WHR collaboration at the cement plant in Rüdersdorf, Germany, the partners will now start to exploit Orcan Energy’s flexible and modular technology for Cemex globally. The goal of this multi-site portfolio approach is to convert large waste heat volumes into clean energy, profitably reducing carbon emissions for Cemex overall.
The global construction materials company Cemex and Orcan Energy AG, a leading cleantech company turning waste heat into clean electricity, will analyse the scale-up of the heat-to-power solutions pioneered by Orcan Energy in parallel at several Cemex plants to capitalise on the benefits resulting from a portfolio of installations. The representative findings will be collected to draw a holistic picture for an upcoming global WHR programme. The portfolio approach with detailed multi-site data collection allows the partners to efficiently and quickly deploy Orcan Energy’s modular applications at scale in the second phase of the collaboration.
Sergio Menéndez, President of Cemex Europe, Middle East, Africa & Asia, said: “We already have an initial collaboration with Orcan. Based on the modularity of their solution, Orcan offers the flexibility of both installation and contracts. Thanks to this crucial flexibility, we can adapt to any upcoming changes in our plants. The approach enables us to reduce carbon emissions right now without limiting ourselves in implementing any future technologies such as carbon capture, utilisation, and storage. This partnership will help us achieve our sustainability targets and contribute to our aim to use all available heat.”
Andreas Sichert, CEO of Orcan Energy, said: “We are looking forward to entering this large-scale decarbonisation partnership with Cemex after our initial cooperation in Germany. This step is a testament to Cemex’s forward-looking strategy and the company’s commitment to achieving net zero. For Orcan Energy, this is another milestone in scaling the business internationally with global enterprises. We are proud to be the partner of choice for the cement industry. Our large footprint across the industry shows the economic capability and the technical excellence of our modular and flexible solution, especially
We understand how it is important to efficiently extract and process precious metals and minerals.
You save valuable resources while keeping your employees and the environment safe.
Improve your processes with our comprehensive portfolio of measuring instruments, solutions and services:
Micropilot FMR67B: 80 GHz radar level measurement even under demanding process conditions for smart safety and increased productivity.
Do you want to learn more? www.endress.com/mining
Cerabar PMC51B: Absolute and gauge pressure transmitter combining measurement accuracy with IIoT functionalities.
Field Xpert SMT70: Tablet PC allows mobile device configuration and plant asset management, even in hazardous areas Ex Zone 2.
in view of uncertain future economic and regulative developments.”
In 2021, Cemex and Orcan Energy started their first joint project in Rüdersdorf, Germany, near Berlin, with the installation of six WHR modules which could produce up to 8000 MW/hr per year, reducing CO2 emissions by more than 3000 t. Following this ongoing cooperation, the companies decided to enter a large-scale decarbonisation partnership, exploring the deployment of WHR solutions in several further sites, multiplying today’s electricity savings and CO2 reductions.
In industrial production, usually 30 – 60% of the energy is lost in the form of heat. Cement production is particularly energy and CO2-intensive. Therefore, the cement industry is actively searching for ways to reduce carbon emissions and utilise its waste heat. Modular WHR technology is a proven and commercially viable energy efficiency solution that can be flexibly installed in several applications. The heat-to-power modules can be placed at the pre-heater as well as the clinker cooler. Both heat sources can either be utilised combined or separately. If the waste heat availability changes over time, the modules can be redeployed at other waste heat sources and sites or even be returned. Thanks to this flexibility, various other heat users can be included in the future – the heat extraction will retain its value in any event.
In response to the demands of a changing market, Aggregate Industries’ cement business has announced the second in a series of planned import operation investments – with expansion into a major new cement storage facility for deep sea shipping lines at the port of Southampton.
As part of a 20-year agreement, Aggregate Industries will be working with port owner Associated British Ports and industry-leading cargo handler Solent Stevedores who will be operating the new substantial cement import facility. This latest investment will help the business maintain a continuous supply of lower carbon cementitious solutions throughout the South and South West of England, and together with the
expansion of storage capacities and enhanced infrastructure, the Port will be able to accommodate larger vessels and improve overall transport efficiencies.
It constitutes an important first step in the cement leader’s ambitious strategy to transition to deep sea terminals, with a number of further import network improvements planned and due to be announced over the coming years.
With each import investment strategically chosen to support the firm’s regional logistics infrastructure, this growth in distribution capability will help Aggregate Industries to offer best in class service to local customers – with minimal lorry miles from terminals to sites – for the ultimate in sustainable, agile, secure supply.
Matt Owen, Head of Supply Chain at Aggregate Industries Cement Division commented: “This is a significant project for us. It constitutes the first stage in a wider programme of planned investments over the short to medium term in deep sea imports designed to enable us to serve growing demand.
“The Southern construction market remains buoyant with lots of major projects in the pipeline this year and beyond. Constituting one of the few deep-sea vessel facilities of its kind in the region, this facility will enable us to remain primed and ready to meet our customers rising demand for lower carbon solutions.”
“Our investment in this Port is indicative of the key role freight is playing in helping us to build resilience and surety of supply for customers, so we can always respond in an agile way to customer demand.”
Clive Thomas, Commercial Director at Solent Stevedores, said: “Welcoming Aggregate Industries to the port with this long-term contract will facilitate a significant upgrade in the facilities and increase the range of products Team Solent handles through the Bulks terminal.”
Harry Eves, ABP Southampton Commercial Manager said: “We are delighted to invest in this development project which will convert an existing building into a state-of-the-art cement terminal enabling Aggregate Industries to import sustainable cement into the UK. The facility and the cargo is a first for Southampton and provides a great addition to bulk operations in the Port.”
Fabian Apel, Johanna Hoyt, Francisco Marques, Sebastian Reiter and Patrick Schulze, McKinsey, explore potential pathways for the cement industry to accomplish the transition to net zero.
The cement and concrete industry has established new targets to lower and even eliminate emissions, such as those set by the Global Cement and Concrete Association (GCCA). These targets aim for a 20% reduction of CO2 per metric ton of cement and a 25% reduction of CO2 per cubic metre of concrete by 2030 compared to 2020 levels. The GCCA calls for complete decarbonisation by 2050.
For the past few decades, cement players have relied on traditional levers to reduce their emissions, such as increasing fuel efficiency, and substituting clinker and traditional fuels with more sustainable options. However, to reach net-zero emissions by 2050, annual capital spending will need to almost double to US$60 billion on average from 2021 to 2050.
McKinsey’s analysis suggests that in the short term, the supply of lower-carbon
cement is unlikely to keep up with increasing demand from end consumers with ambitious CO2 targets, particularly in Europe. This is likely to drive short-term green premiums for cement however, as more low-carbon materials become available to end consumers, especially in Europe, these premiums are expected to decline.
In addition, supportive regulation could help speed decarbonisation. For instance, the 45Q tax credit in the US Inflation Reduction Act offers tax incentives for carbon capture, utilisation and storage technology (CCUS) for projects started before January 2033. Similarly, the EU Innovation Fund supports industry decarbonisation in Europe by funding innovative technologies.
Four pathways show particular promise for effectively targeting the carbon-intensive aspects of cement and reducing its use in concrete. Although some of these solutions require further development to be scalable, each holds significant abatement potential.
Lower-carbon clinker facilitated by CCUS
Clinker, an intermediary used as a binder in cement, is a core component of cement products, but its production process is highly emissive. Lower-carbon clinker uses CCUS technology to capture and manage these carbon emissions before they are released. Other than moving away from clinker entirely, CCUS is the only known technology that addresses the process emissions in clinker production.
Admixtures are substances added to concrete to improve its performance, such as its durability and workability. They can also reduce the amount of cement needed in concrete, which both lowers cement-related costs and reduces concrete’s carbon footprint. However, a few obstacles currently hinder the widespread adoption of admixtures.
Alternative cementitious materials have historically struggled to scale. However, current investment trends and rapid technological advancements have allowed start-ups to disrupt the alternative cementitious space with low-carbon offerings. In particular, supplementary cementitious materials (SCMs) offer promising ways to significantly reduce the carbon footprint of traditional cement and concrete.
Circular economies aim to minimise the environmental impact of concrete by using less
virgin cement – and therefore less clinker – in its production. A few strategies can help cement and concrete players increase circularity, such as reusing concrete waste and incorporating recycled materials in new concrete production.
Although these four pathways are complementary, they will compete for growth and investment among players, and the pace at which they are adopted may differ markedly across markets. Down the value chain, new admixtures and recycling could create great value, although recycling is difficult to scale.
For cement players in the middle, balancing CCUS-driven lower-carbon clinker and innovative cementitious solutions will hold the key to their near- and long-term success as different technologies mature. Their choices will be driven by cost and facilitated by regulators, industry organisations and specifiers building pathways toward decarbonisation.
McKinsey’s analysis has identified nine potential future business models for cementitious producers and solution providers in the pursuit of net-zero cement.
f Low-cost traditional cement players – As lower-carbon options take greater market share, the last remaining producers of traditional cement are expected to be players focused on lowering costs.
f Retrofitted lower-carbon cement producers –Existing cement producers can be retrofitted to manufacture cement with low- to net-zero carbon by leveraging decarbonisation technologies such as CCUS.
f Lower-carbon clinker and cement disruptors – New clinker megaplants and grinding facilities with CCUS capabilities could produce net-zero cement, although cement products using lower-carbon clinker could vary in how emissive they are, depending on the mix of materials they use and their production process. This could be facilitated by offtake agreements and direct collaboration with forward-looking real estate developers and contractors.
f Specialised players monetising CO2 (mineralisation) – Another emerging space is monetising CO2 via mineralisation. Specialised players could use CO2 or carbonated recycled waste in aggregates and SCMs, or directly in the production of concrete during manufacturing and curing processes.
f SCM producers – Players focusing on novel processes and materials could provide SCMs as partial or full replacements for clinker. These may be challengers or existing
suppliers of incumbents. Players in this space also have the opportunity to license their technology.
As cementitious producers navigate the materials transition, other forward-thinking players will be able to find business opportunities supporting them. These solutions providers could offer lower-carbon clinker, fillers, and special cement blends, which will be critical for retrofitted low-carbon cement producers.
As players innovate tailored solutions to meet customer needs, a number of cementitious-solutions providers could emerge:
f Construction material recyclers –These players will own construction and demolition waste, controlling a significant source of raw materials for new construction.
f CCUS as a service provider – Emerging players can offer end-to-end CCUS capabilities, from technology and operation of carbon capture units to CO2 storage and transportation to sinks.
f Providers of construction chemical solutions – New and established players can develop innovative chemicals and additives that allow for a higher share of cementitious materials in cement, less cement in concrete, and higher recyclability of concrete.
f RMC mix optimisation platform players – New platforms could offer data-based software-as-a-service models for RMC mix optimisation, which could reduce the dependency of manufacturers on specific cement types.
To reach net zero, the cement industry will need to engage in active efforts. This will be a real transformation from past ways of operating, and the time to start building this muscle is now. If incumbents and disruptors can invest strategically in innovative technologies and business models, they could be well positioned to lead in the industry landscape to come.
Fabian Apel is an associate partner in McKinsey’s London office, Johanna Hoyt is a consultant in the Toronto office, Francisco Marques is an associate partner in the Lisbon office, Sebastian Reiter is a partner in the Munich office, and Patrick Schulze is a partner in the Berlin office.
SOME THINK THAT WASTE IS WORTHLESS. WE THINK DIFFERENT.
Mike Ireland, PCA, explains how Portland-limestone cement is just one of many methods being used by cement producers to reduce their environmental impact.
From 3D printing changing the face of manufacturing to the untold new levels of productivity promised by artificial intelligence, every industry is incorporating innovation into its products to arrive at new solutions that meet business and sustainability goals.
The cement industry is also experiencing this change, with major investments being made in technology and innovation to meet rising demand while cutting CO2 emissions.
PCA’s Roadmap to Carbon Neutrality, now in its third year, calls for the entire cement-concrete-construction value chain to work together to create new ways to manufacture cement and concrete with an added benefit of being more sustainable. By collaborating, it will be possible to meet consumer and regulatory demands to cut emissions and build for a better future.
This innovation is happening across the industry, from lower-carbon inputs to greener products,
and none has been more widespread than the development of Portland-limestone cement (PLC) and other ternary blends, as well as a new batch of small-scale startups creating new lower-carbon products. Cement has always been a material that is constantly evolving – and producers have always innovated with sustainability in mind.
Going mainstream
PLC is engineered with a higher limestone content, resulting in approximately 10% fewer emissions. Most people consider cement and concrete to be basic building materials that have remained unchanged for decades, but as both PCA and the wider industry know, these materials are anything but mundane – cement and concrete are some of the most versatile, adaptable, and customisable materials in the world. And PLC now allows the industry to, quite literally in some cases, create a new pathway with cement and concrete to reduce the carbon footprint of every project.
With PLC, construction professionals can now conduct repairs with greater sustainability in mind, particularly on projects that have been
historically focused on strength. They can also do this knowing that PLC has been used in virtually every segment of construction, from residential homes and commercial office space to interstate paving and bridges, high-rise construction, parking lots, airport paving, and more.
The demand for lower-carbon cement and concrete is increasing as more consumers understand the need for sustainable concrete, and PLC is one of the most widely available options for cutting emissions in the immediate term and meeting that demand. It performs just like the cement that construction workers are used to working with – having the same specifications and mix design – but with a better carbon profile. PLC can be used anywhere traditional Portland cement is used. All that is needed to ensure the same results is consistent communication among the industry professionals on the job.
The production of PLC in the US has grown significantly in recent years. Currently, there are 34 US states that house cement plants. PLC is produced in at least 24 of them. Based on public announcements, PCA has determined that at least 35% of the domestic cement industry, measured by clinker capacity, has announced the transition from traditional Portland cement production to full PLC production. This translates to roughly 34 million t.
This trend is expected to grow. At least 50 plants are producing or have announced plans to produce PLC in the US. Overall, this accounts for more than 60% of US clinker capacity. And most encouragingly, PLC is starting to become the mainstream option. Statistics from the United States Geological Survey show that by June 2023, the market share for blended cements was 54.5%, and PLC’s share of blended cement was 95%. This marked the first time PLC represented more than 51% of the American cement market.
This growth is remarkable, considering that as recently as mid-2021, the market share for blended cements remained below 5%. All in all, by using PLC and other blended cements, the domestic cement industry managed to avoid more than 2.2 million t of CO2 in 2023 without compromising the strength and reliability of traditional Portland cement.
Continental Cement Company facility, Hannibal, Missouri.People think shipping automation for the cement industry is a complex thing.
And it is. All the processes and the machinery to be controlled takes thought, skill and experience to accomplish.
All of it so that when people use the resulting software and hardware it makes their day go a lot smoother. Less hassle. Fewer errors.
It’s hard to make things so easy, but at PSCL that’s what we do.
Cement Distribution Management Suite
Raw Materials
Receiving
Self-Service Loading Plant Portal
Across the entire cement-concrete-construction value chain, sustainability means very little if it is not backed by performance. Testing new PLC mixes, with test pours and scenarios in a variety of temperatures, wind conditions, and humidities, is crucial.
This innovation is being deployed at scale, with exacting testing to match. In late 2021, The Monarch Cement Company made the strategic decision to test PLC’s efficacy by becoming its own guinea pig. The company used PLC it manufactured in a major capital improvement project: construction of a new raw material storage facility at its Humboldt, Kansas, plant. The plant is a 1.3 million tpy operation that requires well-informed handling and preparation of raw materials before they enter the kiln.
The enormous 97 500 ft2 industrial building, which required 6000 yd3 of cast-in-place concrete, offered Monarch an opportunity to test the new cement’s performance versus its traditional Type I/II product in a demanding application.
The construction comprised above- and below-grade members, as well as vertical and horizontal members, including the foundation, piers and piles, walls, interior floor slab, and surrounding pavement. These members would be put to the test, as operations at the storage facility involve fully loaded tractor-trailers delivering materials inside the building, as well as other heavy equipment, such as front-end loaders and 75 t dump trucks, handling materials within the 300-by-325 ft structure.
Complicating matters is the facility’s Midwest location. Concrete at the Humboldt facility must be highly durable to withstand the numerous freeze-thaw cycles that occur annually to provide a long lifespan.
Acting as both a research and bona fide construction project, the process included testing
of more than 250 concrete samples, with the PLC concrete showing virtually identical performance to the Portland cement concrete. Compressive strengths at seven days were 4400 psi, increasing to 5500 psi by 28 days, and 5800 psi by 56 days.
Despite temperatures ranging from 48 – 94˚F, with winds up to 25 mph at times and relative humidities ranging from quite low (23%) to very high (97%), the result was a successful concrete placement with a more sustainable mix design. More importantly, it was a tangible, large-scale proof of concept of this new product that advances sustainability while maintaining strength and durability.
Carbon capture: cutting emissions at the source PCA members are prioritising the development of carbon capture, utilisation, and storage (CCUS), as this can be a key tool to harness emitted CO2 before it escapes into the atmosphere during the manufacturing process. And beyond capture, the industry is focused on reuse, which brings added value to captured CO2
The technology is nascent, but companies are already making advances toward implementing this solution in their day-to-day operations. To do so, they can leverage significant government assistance, as both the private sector and the government share similar goals of using innovation to stimulate greater efficiencies with lower emissions.
For example, Heidelberg Materials expects the CCUS system on its Brevik plant in Norway – the world’s first industrial-scale carbon capture system on a cement plant – to start operating this year. In 2026, the company plans to begin operating a CCUS system at its Edmonton, Alberta, facility in Canada, which is designed to capture 95% of plant CO2 emissions. Heidelberg has also been selected by the US Department of Energy’s Office of Fossil Energy and Carbon Management to conduct a front-end engineering design (FEED) study on carbon capture.
Greener fuels in, greener cement out Made with everything from tyres to pistachio shells, lower-carbon alternative fuels are becoming more prevalent in cement plants across the United States. As the industry progresses toward carbon neutrality, the
adoption of new fuel sources is taking shape not just at scale, but also at an institutional level.
For example, Continental Cement Company launched Green America Recycling, which provides waste treatment, storage, and disposal facilities at its Hannibal, Missouri, and Davenport, Iowa, cement plants to replace coal with locally available materials to power its manufacturing operations with far fewer emissions. Continental Cement currently has a 42% fuel substitution rate; in 2019, it used more than 130 000 t of discarded materials as fuel throughout its two locations. The company is also working to expand the Green America Recycling facility at its Davenport cement plant to increase the use of non-coal fuels, reducing landfill waste and significantly cutting net emissions.
Continental Cement is also working with the utility companies it relies on to ensure incoming power to the plant comes from renewable energy sources. In 2021, MidAmerican Energy provided 86% of the power for the Davenport plant from renewable electricity sources such as wind and solar. Continental Cement saved more than 150 000 t of CO2 in 2021 alone by using renewable electricity.
These notable activities from PCA member companies are just the beginning. PCA is committed to collaborating with the entire cement-concrete-construction value chain and enhancing overall communication. The industry is stepping on the gas (or the electric vehicle accelerator pedal, if we wish to keep cutting our CO2 emissions) and revving forward in all respects – whether it is optimising cement with PLC or advocating for carbon uptake research so the industry can understand the full use-phase benefits of concrete. Together, the industry is working to meet the demand for a more sustainable future.
Michael Ireland is the president and CEO of the Portland Cement Association (PCA). Previously, Mike was associate executive director of the American Society of Mechanical Engineers (ASME), as well as CEO of two other professional associations. He is a seasoned association executive with expertise in all phases of organisational management, including executive leadership, marketing and communications, workforce development, philanthropy and fundraising, and membership development. Throughout his career, he has been known for fostering a culture of camaraderie and customer focus, thanks to his sense of creativity and ability to help organisations positively navigate strategic change.
Climate change poses a serious threat to society, ecosystems, and the planet. The UN Paris Agreement, signed by nearly every global nation, sets the target of limiting global warming to 1.5˚C above pre-industrial levels. However, the world is already projected to propel right past that target, and it is now critical for the global community to enact rapid and far-reaching transitions across all economic sectors, including land, energy, industry, buildings, and transport to avoid the most catastrophic effects of climate change.
The cement industry is well poised to contribute to the low-carbon transition by significantly reducing its climate impact. Globally, cement production accounts for approximately 8% of all carbon dioxide emissions. Most of these emissions result from the calcination process involved in producing clinker, the primary intermediate component of Portland cement (PC). Replacing PC with supplementary cementitious materials (SCMs) or alternative cementitious materials (ACMs) can eliminate the need for clinker and significantly lower overall emissions from this sector. There are a variety of cementitious materials that can be naturally derived, manufactured, or result as a by-product of other industrial processes.
The current supply of traditional SCMs, primarily fresh ash from coal-fired power plants or traditional slag from steel manufacturing, is shrinking and insufficient to meet growing global demands. Although this is concerning for SCM sourcing, the decline of these emission-intensive by-products signals a positive transition to cleaner energy and industrial operations. To bring new SCMs/ACMs to market and further drive overall, there is a need to incentivise the development and deployment of novel technologies at scale. This is where the voluntary carbon market (VCM) can help. Financial incentives, in the form of carbon credits, can help increase production, availability, and use of new lower-emission SCMs/ACMs. This will ultimately reduce the emissions associated with the cement sector by reducing or removing an emission intensive component (clinker) in the end product.
The Climate Action Reserve’s US Low-Carbon Cement Protocol provides the accounting guidelines for issuing carbon credits to low-carbon cement projects, incentivising industrial-scale availability and use of SCMs/ACMs that can replace PC and reduce associated greenhouse gas (GHG) emissions. The protocol offers a pathway for the voluntary carbon market to help offset costs to competitively bring these SCMs/ACMs to market, which is arguably the most important decarbonisation pathway for the cement industry to meet its environmental goals and significantly reduce emissions.
Under the protocol, the Climate Action Reserve issues carbon credits for emissions reductions achieved from the combination of both:
f The production of SCMs or ACMs that can partially or fully replace PC in ready-mix or concrete products; and
f The use of these products instead of PC to displace associated emissions.
Credits are issued upon reasonable assurance that PC was displaced with verifiable mechanisms.
Emission reduction quantification is calculated as the delta between project emissions, SCM/ACM production, and baseline emissions, PC production.
The US Low-Carbon Cement Protocol sets stringent eligibility and accounting standards to ensure that emissions reductions associated with the production and use of SCMs/ACMs are real, additional, and permanent.
The project developer by default is the SCM/ACM supplier or manufacturer, but can also be low-carbon cement technology suppliers, PC manufacturers, ready-mix concrete facilities, and/or entities that specialise in carbon offset project development. The project developer is expected to provide all necessary parameters to quantify project emissions at a facility-specific level. For baseline emissions, project developers must use site-specific PC parameters if available.
• Multipurpose infeed system for front wheel loader suitable for chipped tyres and other fuel qualities
• Air supported FuelBelt for low friction / wearing and minimum power consumption
• FuelBelt for enclosed transport of RDF to the injection point
• Automatic sampling station to take samples without danger for operator from the RDF
• FLEXIBLE and MODULAR to allow the project to be adjusted to the needs of each step and adapted to the needs of each plant
AUMUND
Foerdertechnik GmbH
alternative-fuels@aumund.de
www.aumund.com
In the absence of this information, a regional and conservative PC emission factor is applied.
The protocol’s performance standard is based on a national and state level assessment of common practice for the production and use of SCMs/ACMs to replace PC. Only the production and use of SCMs/ACMs that exceed common practice are determined to generate additional GHG reductions. Eligible products have a usage rate in concrete at near zero (first-of-its-kind) or less than 5%. Examples of eligible SCMs/ACMs include:
f Beneficiated coal ash (upgraded and/or harvested coal ash), which includes the major co-benefit of targeting coal ash disposed across the country.
f Raw natural pozzolans (i.e. volcanic ash).
f Calcined clays/shale and/or metakaolin.
In 2020, the US concrete industry utilised approximately 11 million t of coal ash and 2.6 million t of traditional slag cement. Based on current market penetration rates of commonly used SCMs in the US for cement and concrete production, the following are ineligible:
f Portland Limestone Cement
f Traditional fresh coal ash
f Traditional slag cement
f Silica fume
Silica fume is a niche product for the cement and concrete industry. Therefore, while it is not commonly used in concrete products in the US, it is readily available making it a ‘business as usual’ case and ineligible for crediting under this protocol.
Legal requirement test
For a project to pass the legal requirement test, the production and use of a SCM/ACM in cement production must be voluntarily undertaken, and not have occurred due to laws, statutes, regulations, court orders, environmental mitigation agreements, permitting conditions, or other legally binding mandates, such as cap-and-trade programmes.
The Reserve did not identify any existing federal regulations that obligate the production or use of SCMs/ACMs. However, some states have legal requirements that would deem a project ineligible:
f CalTrans has a threshold to include a minimum percentage of SCMs in concrete used for state projects. SCMs sold to and used by Caltrans must be above the minimum threshold to be eligible.
f The North Carolina Coal Ash Management Act requires the installation and operation of ash beneficiation projects from three specific sites in North Carolina. Other coal ash harvesting projects not mandated under this act are eligible if they meet all other eligibility requirements.
f Emission reductions from SCM/ACM production facilities that are included under an emissions cap are not eligible. Therefore, SCMs/ACMs being sold to a PC facility under the California Cap-and-Trade regulation are ineligible for crediting.
Project activities must not cause material violations of applicable laws, including air and water quality, labour, and safety. Additionally, the protocol
includes social and environmental safeguards that must be considered in the project design and implemented throughout the lifetime of the project, including mitigation of potential releases of pollutants that may cause degradation of the quality of soil, air, surface and groundwater.
Eligible SCMs/ACMs must meet applicable quality standards to ensure the product is competitive in the market and able to displace PC. ASTM International, a standard setting body, establishes procedures and standards for certifying specific cement and concrete products. For a project to be eligible, the SCM/ACM must meet any applicable ASTM standards and project developers must provide their ASTM standard report when an ASTM standard is available. If the SCM/ACM product does not have a specific ASTM standard, the project developer must provide verifiable evidence (via other standards specifications) that the quality of the product meets end-use requirements and will be used to displace PC.
To achieve the outlined principles in Figure 3, the Reserve employs several measures to ensure the high quality of credits. With multi-stakeholder, local, and public input, the Reserve develops a protocol-specific performance standard threshold to assess project additionality, meaning research is conducted up front to determine common practice and activities above common practice. GHG reduction activities that fall within the business as usual threshold are presumed to be financially viable without access to GHG credits and therefore are not additional. Similarly, all projects are subject to a legal requirement test and all projects undergo independent verification by ISO-accredited verification bodies that have received and passed training both for verifying under the Reserve programme and for verifying under each specific protocol.
Innovations that benefit the climate can be expensive to implement, preventing their widespread adoption. The voluntary carbon market is designed to provide the necessary lift above this financial barrier to make these innovations economically feasible. GHG emission reduction projects are undertaken voluntarily, beyond legal requirements, above business as usual, and in adherence to a rigorous set of eligibility criteria and accounting standards. In accordance with a specific protocol developed by a carbon credit registry, projects can earn carbon credits, with one credit equivalent to
one metric ton of CO2e emissions reduced, sequestered or avoided. Carbon credits have been around for decades (the Reserve’s first offset protocol was adopted in June 2005) and have successfully created an avenue for channelling investments to GHG reduction projects that result in real, additional, permanent, verifiable, and enforceable emissions reductions. Once issued, carbon credits can then be purchased by a company/organisation/individual to mitigate their GHG emissions profile.
Carbon markets have received negative press recently for allowing low-quality credits in the market. As with all sectors of the economy, there are varying degrees of quality when it comes to offsets. The VCM is making strides to address legitimate concerns about ensuring and distinguishing carbon credit quality. One initiative that market participants find very promising is the Integrity Council for the Voluntary Carbon Market (ICVCM), which has developed Core Carbon Principles (CCPs) that provide thresholds for accounting principles, disclosure and transparency, and sustainable development benefits that high-integrity carbon credits should meet. The ICVCM CCP label will distinguish high-quality carbon credits that channel finance towards genuine and additional GHG reductions and removals.
PC makes up only a small portion of the concrete mix by mass (approximately 10%); however, it comprises roughly 80 – 90% of concrete’s total GHG emissions. Thus, one of the most effective strategies to reduce GHG emissions associated with concrete production is to replace some or all of the PC clinker with SCMs/ACMs.
Despite the potential for SCMs/ACMs to significantly reduce concrete’s GHG footprint, they are not ready to be deployed at scale due to significant economic hurdles. The concrete, cement, and SCM/ACM industries require innovative yet costly technological advancements to bring new SCMs/ACMs to market. The voluntary carbon market can provide the financial incentive to increase the supply and use of low-carbon cement, which will result in significant emission reductions.
McKenzie Smith is an Associate Director at the Climate Action Reserve, where she is responsible for advancing the Reserve’s protocol development and update process, leading the implementation, evolution, and expansion of agricultural carbon offset protocols, and applying her technical background and experience to support protocols and projects in the industrial processes and gases sector.
UTIS considers the role of hydrogen technology in not only improving combustion efficiency but also decarbonising cement production.
The Portuguese company, UTIS (Ultimate Technology to Industrial Savings), was established in April 2018 after more than three years in Research & Development (R&D), which included full scale tests with thousands of working hours, specifically in clinker production kilns. The company developed a new and disruptive approach, UC3® technology, using hydrogen (H2) injection in continuous combustion, helping hard-to-abate sectors, such as cement, by improving combustion efficiency (lower fuel consumption), thus allowing an effective and sustainable decarbonisation pathway.
With a multidisciplinary team possessing deep knowledge in different sciences and fields, such as hydrogen, project design/concept/industrialisation, and dozens
The
of years of experience in clinker and cement production, the cement industry was the first industrial sector where the patented UC3 technology was applied (8 years ago).
Since April 2018, more than 140 projects have been implemented in the cement sector, spanning 27 countries, where UC3 technology is widely adapted, including across the world’s major cement producers.
Being a transversal technology capable of optimising all continuous combustion processes (as fuels applied), UTIS is today present in several other sectors, including power plants (e.g., biomass, MSW – Municipal Solid Waste) and steel, with the same purpose and commitment: higher combustion efficiency of the combustion processes to reduce the carbon footprint.
With continuous organic growth, UTIS is today also present, through its subsidiaries, in Brazil and New Zealand, enabling a closer presence with the market, as aftersales.
The UC3 technology, currently at TRL9 (Technology Readiness Level), has been full-scale since 2016, operating for hundreds of thousands of hours, whilst remaining environmentally friendly. The main principles are:
f Hydrogen as an enhancer and never as a fuel (energy basis), maintaining the fossil and/ or alternative fuels (AF) as the source of energy (MW) needed for the clinkerisation process.
f Faster oxidation of the fuel carbon chains (lower CO emissions), enabling a quicker release of its potential energy per unit of time, meaning that more MW are available for the fuel NCV (net calorific value) (more energy (MW) is released from the same mass of fuel).
f Minimised excess of air, for the same burning conditions, providing a lower supply of total energy needed (direct reduction of specific heat consumption (SHC)).
Through a kinetic effect (and not stoichiometric), the addition of H2 promotes a radical mechanism reaction, speeding up the combustion process, allowing higher combustion efficiency of fuels with much worse burn-out (by default, AF and/or fossil fuels are more difficult to burn).
Reaching this new balance, with UC3 technology, specifically in the cement sector, several benefits/ savings can be reached in the very short term. This makes UTIS a great competitor when compared with other BAT (Best Available
•
• Removes 95 to 99% of carbon dioxide emissions
• Easy retrofit
• Suitable for existing and new plants
• Modular solution scales up to all plant capacities
• Less pre-treatment than alternative technologies
•
Technologies), even for kilns retrofits, both from an environmental and economical point of view (with ROI rates, much lower than the usual ones in the industry).
Benefits when applied to clinker production
In this framework, several benefits from this higher combustion efficiency can be translated into:
f Higher productivity
f Lower SHC (less CO2)
f Higher AF rate (less CO2)
f Solid fossil fuel trade-off
f Higher sulfur volatilisation control
f Lower ammonia consumption (less NOx)
f Higher clinker quality (less CO2)
Case studies
1. Higher productivity
An increased oxygen availability for the same draft, allows the kiln to operate with a higher production level, even for ID fans at full capacity.
Considering the absence of external bottlenecks (e.g. feeding systems and/or lack of raw meal), disruptive kiln productivity improvements can be achieved.
2. Lower SHC (less CO2)
Through a more stable kiln operation and increased resilience to process perturbations with lower excess of air, remarkable reductions of SHC can be achieved with direct impact on the decarbonisation pathway.
3. Higher AF rate (less CO2)
With an extended kiln stability limit, through better fuel burn-out, a much higher AF consumption is allowed without compromising the clinker quality. UTIS has a customised solution for total CO2 reduction from fossil fuels usage.
4. Fossil fuel trade-off
The UC3 technology allows the usage of fuels with worse burn-out (by default, with lower specific cost), without losing kiln efficiency. Different types of coals (low to high ashes) and different types of petcokes (low to high sulfur), are the most common requests, fully accomplished.
5. Higher sulfur volatilisation control
The UC3 technology promotes a very high control of sulfur volatilisation (εSO2), even with much higher inputs of sulfur, both from fuels and/or raw/secondary materials.
An industry-leading performance spectrum coupled with exceptionally low energy consumption and other technological advantages ensure that Pfeiffer mills and machines keep your CO2 footprint smaller than that of others. Ask us about it!
Sustainability going forward – Getting it done!
www.gebr-pfeiffer.com
Whenever applied, petcoke additives for sulfur volatilisation control can be avoided.
6. Lower ammonia consumption (less NOx emissions)
The UC3 technology decreases NOx emissions, and reduces up to 100% ammonia/urea
consumption (if used), due to three main drivers: higher kiln stability, lower excess of air and higher TSR (Total Substitution Rate), whenever AFs are in place.
7. Higher clinker quality (less CO2)
The UC3 technology also improves clinker reactivity, both from higher kiln stability, due to the improved fuel burning process. Increased early strength up to 25% can be reached, which opens further opportunities for CO2 reduction in the cement industry.
Continuous research & development
While UTIS continues to develop its UC3 technology for the cement sector, offering a customised solution for 100% CO2 reduction from fossil fuels, UTIS is also investing in the UC3® Systems (ULTIMATE CELL® CONTINUOUS COMBUSTION), which allow the company to deploy its technology, while keeping safety as the highest priority and concern.
The company is proud to announce that no losses have ever been reported across its operations.
The UC3 System is designed for industrial environments, producing both H2 and O2, on demand (without mid storage), complying with local permits and certifications. The system is designed for a plug and play installation, being fully automated, with local command via HMI control and remote control, both from the client’s CCR (centralised control room), as well as UTIS’ own CCR.
Also developed by UTIS is the water pre-treatment system, UCWT – ULTIMATE CELL WATER TREATMENT, which guarantees both higher UC3 system reliability (whenever the root cause is due to lack of water specification fulfilment), and reduced maintenance costs.
Fully committed and capable of bringing industrial savings, UTIS can provide a customised solution for the cement sector to help solve future challenges.
NOx emissions. Case study No. 6. UC3 inputs and outputs (UC3 system with UCWT supply).Jeffrey Tyska, Honeywell UOP, explores key technologies for enabling carbon capture from cement plants.
Decarbonising the industry of cement production is crucial to limiting global warming to 1.5˚C, a target set by the United Nations. According to the GCCA 2050 Cement and Concrete Industry Roadmap, cement producers will have to fully decarbonise by 2050 to meet this goal.1 This decarbonisation process will require major CO2 reductions, as cement currently accounts for nearly 7% of global emissions according to the UN.2 While improved efficiency and savings in cement clinker production will also help reduce emissions, perhaps the most promising method of reducing carbon emissions from cement plants is carbon capture. By 2050, over 1 Gt/y of CO2 will need to be captured by cement producers, which is a more than 400% increase from the 2030 goal of 258 million tpy.3 Honeywell UOP has a portfolio of carbon capture solutions that can help producers achieve these goals while also helping to minimise energy usage and cost of capture. These include solvent, adsorbent, and cryogenic CO2 capture solutions.
Traditional solvents such as MEA (monoethanolamine) have been used for over 80 years to capture acid gases such as
CO2 in natural gas plants, however they face significant challenges in flue gas services due to large regeneration energy requirements, tall absorbers, and high rates of solvent degradation in the presence of oxygen.4 Honeywell UOP’s Advanced Solvent Carbon Capture technology (ASCC) was developed in collaboration with the University of Texas in Austin to help address these challenges and provide a cost-effective solution for carbon capture.
ASCC uses a proprietary solvent in tandem with a high-pressure stripper and a novel heat exchange flow scheme (Figures 1 and 2) to mitigate the effect of these challenges. The solvent enables a high mass transfer rate, leading to shorter and less expensive absorbers. The solvent also has high thermal stability,
enabling high regeneration pressures of 4 – 6 bar (g). The high regeneration pressure significantly reduces the amount of electricity required to compress the captured carbon dioxide to the desired product pressure for sequestration, while also lowering the CAPEX required for CO2 compression. Both the solvent and novel heat exchange scheme enable low regeneration energy requirements, typically ranging from 2.1 – 2.4 GJ/Mt of CO2. While flue gas conditioning is generally required to manage contaminants such as NO2, the ASCC solvent is more resistant to oxidative degradation than many other solvents, leading to reduced makeup requirements and less reclaiming.
While ASCC units often use steam to regenerate the solvent, they can also be configured to run using only electricity. To help lower overall costs, the design involves a unique heat recovery scheme which leverages heat available in the incoming flue gas and overhead compressor discharge.
The ASCC solvent has been tested for over 8500 hours at the National Carbon Capture Centre (NCCC) in Wilsonville, Alabama using flue gas CO2 concentrations of 4 – 12 vol% and a variety of contaminant concentrations, with higher concentration testing performed at the University of Texas. The testing has included a skid specific to the unique heat exchange set up for ASCC, along with the high-pressure stripper setup. The unit has demonstrated low rates of solvent degradation and low energy consumption along with testing metallurgy, effects of contaminants, and emissions. The unit has demonstrated solvent emissions under 1 ppmv and produces CO2 with less than 1 ppmv of SOx and NOx content.5 ASCC has been selected
Figure 2. Front-end engineering design for ASCC.for multiple DOE funded FEED studies, and Korean conglomerate SK has recently selected ASCC to help demonstrate CO2 capture viability at a natural gas power plant.6
Honeywell UOP also offers the UOP CO2 Fractionation Process Unit for carbon capture. This unit combines Honeywell UOP’s pressure swing adsorption (PSA) and CO2 fractionation technologies to provide a low energy and cost-effective solution for CO2 capture. The benefits of the UOP CO2 Fractionation process include low energy usage, an inherently all-electric design, less pre-treatment required than most solvent systems, and a liquid CO2 product. The energy usage per tonne of CO2 product depends on the flue gas composition due to the need for flue gas compression. The energy decreases significantly with increasing CO2 concentration, especially above 15 vol% CO2 on a dry basis. For cement plants with high CO2 concentrations, energy usage can be well below 400 kwh/MT CO2 while maintaining over 95% recovery.7
The significant variation in energy usage with varying inlet CO2 concentration contrasts with chemical solvent systems, which are less sensitive to the inlet CO2 concentration. The lack of solvent also enables reduced flue gas pre-treatment for most cement flue gas, lowering the overall cost of capture. The liquid CO2 product from the cryogenic tower is a key differentiator for customers that need to produce a liquid product,
as liquefying CO2 vapour can be energy intensive. In addition, the amount of power required to produce a dense phase CO2 product is greatly reduced versus solvent systems, as the energy required to pump the CO2 is much less than what is required to compress it. Finally, the UOP CO2 Fractionation Process Unit is all electric, and furthermore, all-electric ASCC is often a great fit for customers with limited steam or fuel gas availability, or those seeking lowest cost of CO2 avoided.
Honeywell UOP has a CO2 Fractionation Process Unit with over 10 years of commercial operating experience on natural gas and has used this experience to help guide the design of the post-combustion CO2 Fractionation Process Unit. The operating UOP CO2 Fractionation Process Unit has demonstrated high recovery (>95%) during operation. Honeywell UOP has also delivered over 1100 PSA systems within the last half century, with user reported operating data confirming onstream reliability claims of up to 99.95%.8
In some areas, the required CO2 purity will be roughly 97% or lower and the required CO2 product pressure will be under 30 bar(g). In these scenarios a PSA unit may be sufficient to concentrate the CO2 up to the product specification. The PSA will operate at a higher pressure than seen in the CO2 fractionation scheme described above, however the simplicity of the unit can sufficiently reduce energy usage to compete with these designs. If there are tight specifications around oxygen, additional purification may be required via hydrogenation or other methods.
Another way to help reduce the energy usage of a cement plant is to utilise an oxyfuel configuration. Air is separated into nitrogen and oxygen, and the oxygen is used for combustion in the cement plant in place of air. This design helps concentrate the CO2 in the flue gas, significantly decreasing the downstream compressor power required and increasing the partial
pressure of CO2 to the CO2 fractionation section. In most cases, an oxyfuel plant will only require cryogenic separation; enrichment via PSA is not needed. CO2 may be recycled back to the kiln if needed. The oxyfuel system typically requires larger expenditures in the cement plant but results in a simpler carbon capture solution with lower utility requirements.
Dehydration
Dehydration is key for carbon capture. For solvent systems, it is typically required on the overhead CO2 product to ensure that the CO2 meets product specifications. For CO2 fractionation systems, a dehydration unit is required to avoid ice formation and to ensure the product meets the desired specifications. Honeywell UOP’s molecular sieve process technology has been used in over 2400 units worldwide, including dehydrating streams with high concentrations of CO2.
Summary
Capturing carbon from cement plants is key to reaching net-zero emissions goals and minimising the extent of global warming. There are multiple approaches to capturing CO2 from cement plants, all of which have unique benefits. Honeywell UOP has a dynamic suite of carbon capture technologies that can be tailored to meet the preferences and requirements of individual cement plants.
Advanced Solvent Carbon Capture (ASCC) is a solvent solution that has low energy requirements due to its unique solvent, high pressure stripping, and a patented heat exchange flow scheme. It has demonstrated very low solvent emissions while also ensuring less than 1 parts per million of SOx and NOx in the product. The unique solvent also allows for shorter absorbers than first generation solvents such as MEA. ASCC can be designed as a steam regenerated system or an all-electric system, depending on customer preference.
Honeywell UOP’s CO2 fractionation system allows for efficient CO2 capture via pressure swing adsorption and cryogenic fractionation. This system lowers the amount of flue gas conditioning needed compared to traditional solvent systems and is a great option for high NOx flue gas. The liquid product is inherent to the design of the unit and can help greatly reduce utilities where a liquid or dense phase CO2 product is required.
When oxyfuel combustion is considered for cement kilns, a more simple and lower energy carbon capture design can be used.
Honeywell UOP’s CO2 fractionation system is a good fit for the high concentrations of CO2 in the flue gas and can minimise energy while producing a liquid product.
Honeywell UOP’s MOLSIV dehydration unit can be used in CO2 Fractionation Units or CO2 product from solvent systems such as ASCC.
This adsorbent can reduce water content of the gas to less than 1 ppmv and performs well even with high CO2 concentrations in the gas.
Honeywell UOP has developed a leading position in separations by providing state of the art technology in gas treating (including CO2 removal), membranes, absorption, cryogenics, distillation, and heat transfer.
Honeywell UOP has demonstrated ASCC technology through over 8500 hours of operating at NCCC, has commercial experience with CO2 fractionation on a natural gas unit, and has commercial experience with MOLSIV dehydration in high CO2 gas feeds. Honeywell UOP’s experience and wide range of technologies helps ensure an efficient solution can be found for cement plants looking to decrease their CO2 emissions.
1. UNECE, ESCWA, ‘Technology brief: Carbon neutral energy intensive industries,’ – https://unece. org/sites/default/files/2022-11/Industry%20brief_ EN_2.pdf
2. UNECE, ‘COP27: UN report shows pathways to carbon-neutrality in “energy intensive” steel, chemicals and cement industries,’ – https://unece. org/media/press/372890
3. IEA, ‘CCUS in the transition to net-zero emissions,’ – https://www.iea.org/reports/ccus-inclean-energy-transitions/ccus-in-the-transition-to-netzero-emissions
4. HERZOG, H., ‘An Introduction to CO2 Separation and Capture Technologies,’ (1999), – https:// sequestration.mit.edu/pdf/introduction_to_capture. pdf
5. Based on internal data from solvent testing at the National Carbon Capture Centre in 2023.
6. ‘Honeywell to collaborate with SK E&S to deploy carbon capture technology across Korea and Southeast Asia,’ – https://www.prnewswire.com/apac/ news-releases/honeywell-to-collaborate-with-sk-es-todeploy-carbon-capture-technology-across-korea-andsoutheast-asia-301941319.html
7. Based on internal study for cement flue gas.
8. Based on reliability data from the 2010 North American User Meeting feedback. 99.95% (1 shutdown/hr) achieved with a preventative maintenance project versus 99.8% (2 – 6 shutdowns/ yr) without a preventive maintenance programme.
Jeffrey Tyska is a Lead R&D Engineer for carbon capture technologies at Honeywell UOP. Since 2011, he has designed various technologies including gas separations.
Jeffrey earned his B.S. in Chemical Engineering at the University of Illinois at Chicago and his M.S. in Chemical Engineering at North Carolina State University.
in September 2021, FLSmidth A/S entered into a MOU with Chart to advance carbon capture technology to significantly reduce CO2 emissions from cement production.
The agreement has seen the initiation of a pilot project at Sugar Creek Cement Plant, for Chart’s end-of-pipe Cryogenic Carbon Capture™ technology (CCC) to capture 30 tpd of CO2 emissions.
The captured CO2 will be liquefied and produced in a state ready for a variety of traditional and emerging utilisation and conversion applications, in addition to geologic sequestration.
The project at Sugar Creek will demonstrate that capture and purification of CO2 at cement plants can be accomplished at a lower cost and with less need for pre-treatment than first-generation carbon capture technologies like monoethanolamine (MEA) solvent.
Chart’s CCC removes CO2 from flue gases by cooling the gas past the condensation point of the CO2 and separating the frozen CO2 from the cleaned oxygen and nitrogen that can be safely released back into the atmosphere.
Once separated, the CO2 and cleaned gas streams are warmed up recovering the energy that went into cooling them down, making this a very energy efficient process. This post-combustion process removes up to 95 – 99% of CO2 emissions without using toxic chemicals or membrane technologies.
Andrew Baxter, Chart Industries, and Dr Bodil Recke, FLSmidth, discuss a collaboration to identify cost-competitive pathways to reduce CO2 emissions in the cement industry.
Because heat recuperation is used, most of the energy required for the process is recovered making it extremely efficient. CCC also offers the added benefit of removing harmful SOx, NOx and mercury pollutants from exhaust gases.
The highlighted features have positioned CCC as one of the most cost effective and efficient processes for carbon capture in difficult to abate industries, including cement, with the added benefit of the captured liquid CO2 available at sufficient quality to be used directly in a multitude of applications.
Recent process innovations have replaced unit operations which represented some scaling risk. Consequently, the process now planned to be built at Sugar Creek will be able to scale to full-industrial scale with no significant process changes.
Minimising the cost of carbon capture Chart and FLSmidth are both determined to make carbon capture more cost-competitive not only for greenfield projects, but also for the existing install base. With approximately 2275 cement plants across the globe accounting for 7% of global CO2 emissions there is a massive environmental incentive for the companies to succeed.
“While end-of-pipe capture technologies like Chart’s CCC can be directly applied without modifications to upstream process, we see opportunities to bring costs down through low-risk modifications and optimisation, with modest investment in the cement plant scope.” says David Leonardus Williamson, Process Engineer and CCUS Specialist at FLSmidth. “It’s encouraging to see that these modifications have already been validated to reduce the cost of capture by 10 – 20% through our collaboration with Chart, and there are still further integration opportunities on the horizon.”
Preparing customers for carbon capture is all part of the process. While a range of technologies is being developed and explored, cement plants are preparing to invest significant sums to meet the demand for a low-CO2 cement process. Knowing where to direct this investment is a concern. FLSmidth helps cement plants understand their options and what is likely to be the best fit for their circumstances.
“The carbon capture unit and the clinker manufacturing process should be integrated, in both design and operation, to yield the best results on a commercial scale”, says David Jayanth, Project Manager –Carbon Capture at FLSmidth. “We also see opportunities for our process automation software to play a key role in optimising both cost and efficiency. Focus for the next years would be on scaling up capture technologies from pilot to commercial systems.”
FLSmidth and Chart are exploring options for scaling-up with optimised capture configurations for site-specific cost reductions and are engaged with several key players in the industry on pre-FEED studies for large scale CO2 emissions reduction. From a capture perspective, Chart offers all the products for a one-stop solution. Refrigerant compressors, multi-stream heat exchangers, and air coolers that make up the bulk of the CCC package are all Chart built, as are the liquid tanks and trailers required for storage and distribution of liquid CO2 to the point of use.
From a cement process perspective, FLSmidth adapts the existing flow sheet & equipment to enhance synergy between the flue gas and capture unit through process audits and simulations, resulting in savings on the total solution for cement producers.
CCC – how it works.Arun Mote, Triveni Turbines, discusses waste heat recovery and waste-to-energy as potential strategies for reaching net zero by 2050.
The cement industry has witnessed tremendous growth in the last two decades. China (51%) and India (9%) together account for 60% of global cement production, according to the US Geological Survey 2023. The global cement industry is expected to grow by 5.4% in value terms from 2023 to 2028. The challenge for the industry, in the near future, is to meet the rising
global demand while reducing its emissions footprint.
In 2023, the Emissions Intensity (EI) of the cement industry was approximately 0.5 CO2/t of cement, according to the International Energy Agency (IEA) or International Renewable Energy Agency (IRENA). When compared to the 2015 data, this accounts for a nearly 10% increase in EI. In order to become net zero by 2050, the
cement industry would need to bring down the EI to below 0.4, a near 20% reduction, by 2030. Clearly, the industry is not on track considering the necessary pace of sustainability actions. Another aspect to take into account is that current investments towards sustainable technology adoption supports the production of only 22 Mt of near-zero emission cement annually, however, this figure needs to be 350 Mt by 2030.
The chemical, steel, and cement industries account for nearly 60% of energy consumption and 70% of CO2 emissions, according to the Energy Efficiency report by the IEA. In contrast to the chemical and steel industries who are ahead in terms of new technology adoption towards sustainable goals, the cement sector is lagging due to intrinsic factors.
Ordinary Portland Cement (OPC) production involves crushing a raw mix of limestone (calcium carbonate), marl (carbonate rich mud consisting of silt and clay) and supplementary
cementitious materials (SCM) – consisting of fly ash, blast furnace slag, and silica fume. The mix is heated to nearly 1500˚C in a rotary kiln, to produce clinker, which is subsequently blended with gypsum (typically <5%), admixtures (for durability and workability), and SCMs. It is then cooled and crushed to be packed as cement in silos. When it is considered that, for every ton of clinker produced, 0.5 t of CO2 emissions are produced, carbon capture, utilisation and storage (CCUS) remains a primary option for emission reduction.
Cement production is energy intensive due to the high amount of heat required to produce calcium oxide (CaO) from limestone (CaCO3) and the milling work involved. If the SCM proportion in cement is increased, the clinker-to-cement ratio can be lowered and consequently CO2 emissions curtailed. To become net zero by 2050, the targeted clinker-to-cement ratio is 0.56, as compared to the present industry average of 0.71, according to the World Energy Outlook and IEA.
One of the roadblocks for fully leveraging SCMs in cement production is the limitation imposed by regional/national standards on SCM content in cement. The limitations of 35% (fly ash in cement) imposed by European standards, and 40% imposed by the US, need to be reviewed and revised to allow the increased use of new SCMs such as calcined clay, recycled concrete, etc.
Presently, cement production involves a thermal energy intensity of 3.6 GJ/t of clinker and an electricity intensity of 100 kWh/t of cement, according to the IEA Cement Outlook. To be net zero by 2050, the thermal and electrical energy intensities have to be brought down to 3.4 GJ/t clinker and 95 kWh/t cement, including a 5 kWh/t electrical energy requirement for CCUS by 2030.
Reliance on fossil fuels for heat and electricity also contributes to the industry’s carbon footprint. While there is an increased adoption of biomass and refuse-derived fuel (RDF)/solid-derived fuel (SDF) for combustion in rotary kilns for clinker production in Europe and the US, in the emerging economies, fossil fuels still dominate the combustion fuel source. As per CAETS Energy Report 2022, reliance on fossil fuels in the cement industry is still above 95% in China and India, two leading global cement producers.
The cement industry has had success in becoming more energy efficient over the years, through the implementation of WHR systems and the migration from a wet to dry
rotary kiln process. Based on the report released by the Institute for Industrial Productivity and International Finance Corporation, the installation of WHR systems in China alone numbered 739, compared to 26 in India and 100 across the rest of the world.
China, the leading producer of cement, has realised the potential of WHR and implemented this technology at a vast number of cement plants. Whereas India and the rest of the emerging economies have abundant unrealised potential in terms of WHR. In India, the current installed capacity of WHR plants is 520 MW, against a total assessed potential of 1100 MW (according to the Best Practice Manual for Waste Heat Recovery in the Cement Sector in India released by PwC India). On a positive note, all major cement producers in India have installed several WHR plants in the last few years, adding around 250 MW WHR capacity. Some of the barriers for a higher WHR adoption in the Indian cement industry include high capital expenditure (Rs. 100 – 120 million/MW) compared to fossil fuel based captive power plant (Rs. 40 – 50 million/MW), policy environment not treating power produced through WHR route as renewable under local Renewable Purchase Obligation (RPO) for power purchase by industry, and relatively lower awareness among smaller cement players and operators of brownfield cement installations.
Typical WHR systems rely on waste heat from a new suspension preheater and air quenching clinker cooler (AQC), which are installed upstream and downstream of the rotary kiln respectively. The latest cement plants use a multi-stage cyclone preheater to pre-heat the raw material mix before it reaches the kiln. As the number of stages of preheating increases, the waste heat potential of the plant also decreases. Typical pre-heater exhaust temperatures range between 280 – 450˚C and typical AQC exhaust temperatures range from 250 – 330˚C. To put this into perspective, a cement plant with a 10 000 tpd capacity with typical plant parameters, can produce around 15 MW of power from waste heat.
Power generation, typically, can range from 25 – 45kWh/t of clinker, for WHR applications.
Triveni Turbines has a strong reference list for injection condensing steam turbine generators (STGs) demanded by the cement industry. These turbines are custom-designed to suit low inlet parameters and high flows, corresponding to flue gas conditions from the pre-heater exhaust and allow the admission of low pressure injection steam from AQC boilers. Low pressure
InterSep enables you to separate a wide variety of raw materials in a highly energy-efficient manner, while remaining flexible and compact. With the upgrade of the new high-performance separator of the latest generation, InterCem has the right product for every specific application. A low bypass rate ensures the highest possible separation efficiency. Whether as a single component or in a complete plant.
Contact us: InterCem professionals will also find the right solution for your requirement.
intercem.de
condensing modules are suited to handle variability in the operation, while yielding best-in-class steam path efficiencies.
Triveni has installed multiple turbines in WHR applications for the cement industry, replacing an earlier installed turbine module with higher capacity. These turbines offer benchmark heat rates and contribute towards increased captive power capacity and energy efficiency.
The in-house installation and commissioning teams have expertise in providing a plug and play experience to customer’s plant operators. This experience is complemented by a strong after-market team.
Triveni’s turbines are operating in cement plants worldwide, generating power from waste heat. Whether in brownfield or greenfield plants,
Triveni has the expertise to propose steam turbine solutions to drive customer success.
Case study: India
The turbine, operating reliably since Aug 2020, has allowed a major cement player operating a 7 million tpy cement plant at full capacity, to reduce dependence on the grid for power, and also improve plant returns and efficiency.
Project highlights
The cement plant based in Madhya Pradesh wanted to increase WHR power generation due to an increase in cement capacity. The existing 3000 RPM turbine, supplied by an overseas technology company, was operating with low efficiency. After studying the on-site conditions, Triveni Turbines replaced the existing 14 MWe STG set with a high efficiency, higher rpm 22 MW injection condensing turbine set with 10.50 ata, 295˚C high pressure steam and 2 ata, 190˚C medium pressure injection steam.
Challenges
The STG set was placed on the same foundations and within the same housing as the existing STG. It uses the same hardware, such as the lubrication oil system, control oil system, MCC panel, various other electrical panels, distributed control system (DCS), cables (including the existing civil foundation), gearbox and alternator. The complete installation and commissioning (along with the dismantling and removal of the existing STG set) scope was carried out by the qualified in-house team of engineers.
Solution
The customer was satisfied with the 7 MW increase in WHR power generation. The load on the producer’s captive power plant (CPP) has been reduced by 7MW, there has been a reduction in power generation costs and coal requirements, as well as lowering the carbon footprint operations. The modification was carried out with minimal CAPEX investment and will benefit the OPEX costs while generating power. This indirectly helps reduce cement manufacturing input costs.
Case study: Turkey
Project highlights
The cement customer based in Turkey wanted to install a STG in order to optimise the WHR boiler operation due to the low generated pressure and temperature. After studying the scope requirements, the team at Triveni Turbines recommended installing injection condensing steam turbines.
The STG set was designed, assembled, tested and dispatched from the manufacturing facility located in Bangalore, India, to operate at low pressure and temperature levels. Triveni Turbines undertook the complete installation and commissioning scope which was carried out by the qualified in-house team of engineers.
The turbine internals such as blades and rotors have been designed to meet the set pressure and temperature requirements and efficiency levels. The usage of waste heat generated from production processes will reduce the power generation costs and the coal requirements, as well as lowering the carbon footprint of operations.
Triveni Turbines is commercialising its sCO2 technology and can provide cement plant owners with sCO2 turbine solutions meeting specific plant conditions.
The next frontier in efficient and compact turbine technology is the adoption of sCO2 for closed loop Brayton cycle – sCO2 turbines. These turbines derive their compactness, for the same MW, from the density of the fluid (super critical CO2) adopted and its thermo-physical properties at moderate temperature and pressure. A significant reduction on the scale and size of the turbine, improved efficiency, and faster start-up capability are advantages.
Research programmes aimed at reducing emissions in the cement industry, whether in raw material innovations, adoption of more pre-heaters for flue gas heat absorption, novel carbon capture techniques, or electrification have the scope to reduce WHR potential at plant level, in the future. The current scale of WHR installations extends to 20 – 25 MW, based on a cement plant’s production capacity and equipment (pre-heaters and coolers) employed. However, if the scale of WHR installations is in the sub-10 MW range, as may be the case for cement manufacturers with smaller capacities, sCO2 turbine installations are deemed practical, as the technology itself is currently in the commercial demonstration phase.
As China and India are the leading global producers, financing the cement industry transition to sustainability is inherently tied to the economic conditions of the emerging markets and the liquidity of the global financial system.
To keep the carbon footprint to a minimum, municipal solid waste (MSW), SRF or RDF, sewage sludge, plastic waste and biomass are
available as AF, for combustion in the rotary kiln. Test results have shown that adoption of SDF/RDF as AF has no adverse impact on emissions and complies with Kyoto Protocol measures. Sewage sludge, after treatment of wastewater streams, has moderate quantities of silica and sand, and therefore, can be used in cement production by blending its incinerated ash with OPC or by generating co-combustion before addition to OPC. Plastic waste, available as a municipal and industrial waste, has a high calorific value of 30 – 40 MJ/Kg, however, chlorine content management has to be attended to while adopting plastic waste as AF.
Collectively, it is estimated that aforementioned AF have a CO2 reduction potential to the tune of 12% and recommended proportion of AF, for combustion in kiln, is under 25%.
Among the EU28 nations, the proportion of AF adopted is around 37% for plastics, 18% for mixed industrial waste, 15% for tyres and 13% for biomass.
Adoption of AF in the cement industry and substitution of raw materials for cement production requires close cooperation between cement plants, municipalities (for MSW/RDF/SDF/biomass), steel plants (for slag as raw material), sugar plants (for bagasse), fertilizer plants (for carbonate slurry as raw material), power plants (for fly ash), marble plants (for marble slurry), and industrial sources (for waste oil) that are within the logistical limits of a cement plant.
AF can also be supplemented as a fuel source for a waste heat boiler in addition to being combusted in the rotary kiln. The higher the enthalpy of the inlet steam to the steam turbine, the more power can be derived from the turbine equipment and the plant’s dependency on the grid can be minimised.
Among the new technologies focussing on raw materials to minimise emissions in cement production is Brimstone, which relies on calcium silicate rocks for cement production instead of calcium carbonate (limestone). As a result, the calcination of carbonate is avoided and CO2 emissions minimised. This technology is at a TRL (Technology Readiness Level) of 5, having completed pilot scale testing of cement produced.
A pilot plant for commercial production is in the planning stage. If successful in progressing to TRL 9, this technology will eliminate the need for deployment of expensive CCUS technology. Based on the Breakthrough Agenda Report, 2023 released by IEA/IRENA, low emission
cement is at a 75% premium compared to conventional cement production.
Calcined Clay (a pozzolan-siliceous and aluminium material which when powdered and combined with moisture reacts with Calcium Hydroxide (CaoH) to form compounds with cementitious properties) as a SCM has good potential. This material is abundantly available and its adoption to the tune of 50% is possible, with potential to reduce CO2 emissions by 30%, according to CAETS Energy Report 2022. This emission reduction potential has attracted the interest of 40 cement companies across the globe.
A couple of technologies are focusing on the enhanced capture of CO2 from calcination. This includes LEILAC 2, with a new calciner concept at a TRL of 5 and Indirect Olivine Carbonation, also with a TRL of 5.
There are other research programmes that are exploring electrochemical calcination of carbonate, with an aim to entirely avoid kiln combustion. However, these are at a TRL of 3, which is too low to make a commercial impact in the immediate future.
Electrification of the kiln is yet another technology promising a lowered carbon footprint. The technology is from Coolbrook and involves a RotoDynamic Heater (RDH) capable of heating air, nitrogen and process gases to 1700˚C without the need to burn fossil fuels.
Most of the research should analyse exploring the optimal raw materials mix, novel carbon capture techniques through funding from national governments and incentivising carbon reduction. Considering that cement production is dominated by China and India, technological solutions suiting local needs have to be evolved and adopted. Additionally, policy interventions should support the transition away from carbon intensive methods.
Mr Arun Mote has over 45 years of varied experience in the engineering industry including working as a Business Head/CEO of a company. Before joining the Triveni Group, he worked with Larsen & Toubro Limited (Caterpillar division), SKF Bearings India Limited, GMMCO Limited (Caterpillar affiliate), Blue Star Limited and Magneti Marelli India Limited. Mr Mote has been associated with Triveni Group since November 1999 and has been on the Board of Triveni Turbine Limited (TTL) as Executive Director since November 2012. In addition to being on the Board of TTL, he is also on the Board of Triveni Energy Solutions Limited, a wholly-owned subsidiary of TTL.
Mirko Ferrari, Turboden, examines the role of ORC waste heat recovery technology as a tool to decarbonise the cement sector.
The global cement industry is facing one its hardest challenges when it comes to dealing with sustainability. On the one hand, it has to continue meeting global cement demand that is constantly rising year by year, and on the other hand, it has to reduce CO2 emissions caused by the production process.
As of the beginning of 2024, around 145 countries worldwide have announced or are considering net-zero targets. For European countries, this challenge is to reach net zero by 2050.
However, according to the International Energy Agency (IEA), the direct CO2 intensity of cement production (measured in tons of CO2 per ton of cement produced) has been largely flat in the last five years, in contrast to the necessary annual decline of 4% by 2030, to get on track with the NZE by 2050 scenario.
Taking this into account, enhancing the energy efficiency of the cement production plant is one of the quickest and most effective ways to reduce global fuel consumption and thus the related CO2 emissions (Scope 2 – indirect emissions).
It logically ensues that employing waste heat recovery (WHR) methods stands as the most straightforward way to enhance the energy efficiency of the clinker production process, since it can generate up to 30% of the electricity consumed by the cement plant. This is achieved by harnessing the thermal energy present in the hot gaseous streams. Otherwise, not only would this energy be wasted, but it would also entail the use of valuable resources, like water or electricity, for the processing and cooling of these streams.
Over the last 15 years, the cement industry has witnessed the emergence of Organic Rankine Cycle (ORC) technology as a viable and secure alternative to the traditional Steam Rankine Cycle. The continuous improvement in technical solutions, the enhanced economic competitiveness, and the growing global focus on a greener and more sustainable environment made heat recovery through ORC more and more attractive. Governments around the world have also played a significant role in driving this shift towards sustainable practices.
Over the course of 2022 – 2023, Turboden, a Mitsubishi Heavy Industry Group company and a leading provider of ORC plants for medium/high temperature applications in energy-intensive industries, secured six new projects in the cement industry alone. This achievement underscores the increasing appeal for cement plants to use ORC technology.
While various strategies can be implemented to reduce carbon emissions from cement plants, such as transitioning to lower-carbon fuels, promoting material efficiency, and carbon capture technologies, WHR from the production process stands out as one of the most effective
14 MW turbine assembling at Turboden workshop. Turboden 5 MW ORC unit in CRH cement factory in Slovakia.and efficient ways to immediately make cement plants more sustainable and financially rewarding. Combining WHR with other technologies will be crucial for cement plants in the future.
By capturing and utilising waste heat to generate electricity (or both electricity and thermal power in the form of hot water up to 110˚C), cement plants can enjoy several benefits, including:
f Cost savings. Installing an ORC system can result in cost savings for cement plants by reducing the energy they have to buy from the national grid for production plant operation, thus lowering energy bills. Additionally, cement plants that install an ORC unit can ideally lock in electricity prices for the entire lifespan of the system, mitigating risks associated with energy market fluctuations. WHR Levelised Cost Of Energy (LCOE) is typically lower compared to other renewable energy sources like solar or wind which are not constant and depend on external conditions. By using an ORC unit, cement plants can also cool down the gas produced while generating electric power, eliminating the need for electricity-consuming air-to-air heat exchangers or water in conditioning towers. This last point is particularly relevant in countries where water scarcity is a real problem.
f Improving efficiency. Implementing an ORC solution enables cement plants to enhance their overall energy efficiency by harnessing the thermal power generated during the production process that would otherwise be dissipated into the environment.
f Enhancing competitiveness. With the increasing focus on sustainability and energy efficiency, cement plants that demonstrate their commitment to reducing their carbon footprint will be better positioned in the market.
f Environmental benefits. The cement industry is responsible for approximately 7% of global CO2 emissions, according to the IEA. By reducing energy consumption and carbon emissions through ORC technology, cement plants can contribute to global efforts to mitigate climate change and minimise their impact on the environment.
f Reducing fossil fuel consumption in cement plants with power plants. The electricity produced by the ORC unit is used to power internal loads, thereby reducing the need for energy generated through less environmentally friendly means. This leads to lower energy bills and decreases global carbon emissions.
Cement plants typically have two sources of recoverable thermal power that can be utilised
through an ORC unit: exhaust gas from the preheater towers and hot air from the clinker cooler. Turboden has installed numerous ORC units in cement plants, recovering energy from either or both sources. The electrical power output of these units ranges from 1 – 11 MWe, depending on the exploitable thermal source conditions. However, Turboden can offer units with mechanical power ranging from 600 kWe up to 20 MWe from a single turbine; the company has successfully implemented more than 400 ORCs worldwide across different sectors.
The exhaust gas or hot air from the process enters a heat recovery exchanger, which transfers the thermal power in the gas stream to a thermal vector, typically thermal oil. The heat exchanger is designed to effectively handle the gas stream’s specific conditions, managing pollutants and dust commonly present in the gas. The thermal vector then transfers the thermal power to the ORC working fluid, often cyclopentane for cement plant applications (being the working fluid that best fits with the thermal source characteristics in terms of temperature). The cyclopentane is evaporated and
enters the turbine, the core product of Turboden, generating the required mechanical power, which is converted into electric power by a connected generator.
The expanded vapour then passes through an internal heat exchanger called a regenerator, where it releases heat to its liquid phase coming from the opposite side. After the regenerator, the vapour enters the condenser, where it further cools down and returns to a liquid phase. This condensation can occur through a cooling water circuit or by utilising ambient air directly. In the latter case, there is no water consumption for ORC plant operation, a significant advantage in water-scarce regions. The ORC working fluid is continuously pumped back through the regenerator to the evaporator, completing its cycle.
Compared to other heat recovery solutions like the traditional Steam Rankine Cycle, ORC technology possesses several advantages. It exhibits flexibility during operation, as it can handle thermal power inputs ranging from 20 – 110% of the design inlet, while maintaining high efficiency close to the design level.
Due to this adaptability, ORC turbines remain a viable option for cement plants considering the integration of Carbon Capture technologies like oxyfuel, or other exothermic processes, and post-combustion capture. These turbines can operate at high efficiency both before and after the modification of the kiln line.
In the case of other CCS technologies, such as the well-known post-combustion capture with amines, Turboden has conceptualised its large heat pump. This solution produces high-temperature steam to support the carbon capture process, steam that would otherwise be generated by burning traditional fossil fuels.
In addition to supplying the LHP for any amine-based CCS technology, Turboden, as part of the Mitsubishi Heavy Industry Group, which is a prominent player with its own proprietary amine, can
support the customer with the complete CCS solution.
Turboden systems also operate automatically, eliminating the need for constant personnel presence at the plant, allowing cement plant operators to focus on their core business.
The WHR system is installed in bypass to the existing gas treatment line, ensuring uninterrupted clinker production even if the WHR unit experiences downtime. Furthermore, when compared to other green energy technologies like solar photovoltaic, WHR has higher economic efficiency due to higher utilisation rates (it can ideally operate throughout the cement plant’s operating time, resulting in higher kWh production annually) and requires much less space.
Over recent years, the volatility of energy costs has demonstrated its ability to impact businesses, even in growing markets. WHR with ORC has evolved into a mature and proven technology that can secure a fixed electricity price for the plant’s entire lifespan. This protects at least partially cement plants, as observed in previous years with existing Turboden ORC installations, from sudden and unpredictable peaks and fluctuations in energy prices.
With electricity and gas prices on the rise in many countries, the imposition of increasing carbon taxes on CO2 emissions (already implemented in many countries), and the availability of incentives aimed at industrial decarbonisation, the historical cost barrier that hindered investments in energy efficiency intervention in cement plants is becoming increasingly fragile. The pursuit of a more sustainable world will ultimately break down this barrier, compelling more cement plants to invest in intelligent and effective solutions to enhance their efficiency. Drawing upon more than a decade of industry expertise and offering the flexibility to generate either electricity or high-temperature heat based on project requirements, Turboden is poised to embrace this challenge and spearhead the sector toward a more sustainable future.
Mirko Ferrari is Sales Engineer for Industrial Heat Recovery at Turboden, focusing on projects in hard-to-abate industries. He supports potential customers to find optimised solutions for each project, tailored specifically to their case. He holds a Master’s degree in Energy Engineering.
Andrea De Finis and Sara Milanesi, Exergy International srl, explore the benefits of ORC technology over steam Rankine cycle systems and consider the importance of turbine design and configuration.
When it comes to reducing carbon emissions and increasing sustainability in industry, cement falls in the hard-to-abate sector. This is due to the challenge the cement industry faces to simultaneously curb CO2 emissions while meeting an increasing global demand. Even though cement production dropped drastically in 2022 (down 5% to 4158 million t) this will not always be the case, as developing countries experiencing economic growth will need new infrastructure, consequently, there will be a higher demand for cement production.
Given that the CO2 intensity of cement manufacturing slightly increased by 1% in 2022 and the same happened for electricity intensity, (reaching around 100 kWh/t cement in 2022) reducing energy demand by means of energy efficiency improvements is one of the crucial and most effective measures to both decrease the cement sector’s energy intensity and tackle CO2 emissions. The target set in the IEA NZE Scenario requires that the carbon intensity should fall by 4% by 2030.
This explains why waste heat recovery (WHR) technology is gaining prominence in the cement sector and is expected to grow at a CAGR of 12% by 2032 (Global Market Insight).
This shift toward deployment of heat recovery technologies is further driven by the growing adoption of Organic Rankine Cycle (ORC) based systems, which can recover a significant amount of heat from low-temperature sources.
WHR systems employed in the cement industry to convert the thermal energy contained in waste gases and exhaust air from the preheater and clinker cooler into electricity fall into two categories: steam Rankine cycle and ORC. Compared to 55
Rankine cycle technology, ORC has the advantage of recovering heat even from low-temperature resources, hence adding profitability to resources that were previously unexploitable. In addition, ORC features higher flexibility of application, eliminating the use of water and the consequent associated costs for water treatment and make-up. Other benefits of ORC for WHR over steam Rankine cycle systems include:
f Compact and automated systems which do not require dedicated personnel onsite.
f Higher performance in off-design conditions.
f Design adaptability which gives the option to use the most efficient working fluid to extract the maximum power from the resource.
f Simple and reliable product maintenance adding longevity to a power plant life.
A WHR solution based on an ORC system for cement applications involves the WHR unit transfering the heat from the exhaust gases to
the intermediate fluid and the ORC cycle, which receives the heat from the WHR intermediate loop and converts it into electricity by means of a turbine. The intermediate fluid usually used in the WHR unit is thermal oil or water. A typical ORC cycle consists of several key components:
f The turbine: the key component of the plant, producing mechanical energy to be converted into electricity by a generator directly coupled with the turbine shaft.
f The heat exchangers: they extract the heat from the intermediate thermal fluid. Shell and tube heat exchangers are usually applied but the geometry and configuration can vary depending on the energy source and the total thermal input.
f The oil circuit and feed pumps: this brings the organic fluid from the condensation pressure to the maximum pressure of the cycle.
f The condenser: with the direct air to fluid heat exchanger, the organic fluid is cooled and liquefied before entering the pump. The use of an air condenser has several advantages as it eliminates the need for water, reduces the condensing pressure of the cycle, leading to higher power production, and reduces the equipment to install, thus minimising plant costs.
When required, a water-cooled condenser can also be used.
The turbine is the core of the ORC technology. The most common choice of turbine configuration for ORC systems employed by ORC suppliers are axial or radial inflow turbines. Exergy International, one of the main ORC suppliers with more than 500 MWe in its portfolio, studied and introduced the use of the Radial Outflow Turbine (ROT) applied to the ORC cycle in 2010. This technology is still unique today to Exergy’s ORC systems.
Employing the ROT technology in an ORC system for WHR applications is a simpler, more efficient, and economically viable solution:
f It has a higher efficiency over axial turbines by up to 6%. This higher performance relates to the nine stages on a single disk, reducing the size and length of the turbine compared to axial turbine, less tip leakage and disk friction losses, and a minimal 3D effect due to the low blade height and low blade height variation.
An Exergy Radial Outflow Turbine in the workshop.HEKO offers the whole range of chains, rollers, sprockets and scrapers for reclaimers. HEKO products are proven in thousands of bucket elevators and conveyors, worldwide.
f No gearbox is needed due to to the low rotational speed (1500 – 3000 rpm) that allows a direct coupling with a generator with two or four poles and more reliability for the overall system.
f There is less limitation on cycle pressure and on blade manufacturing leading to a superior flexibility extending the range of application.
f Simpler construction technology, which is more compact and easier to transport and install.
f Maintenance is easy and of a low cost. The mechanical group of the turbine containing the bearings, oil lubrication system and seals can be easily removed without the need to drain the organic fluid away from the cycle, thus, reducing the downtime of the plant to one day compared to approximately one week or more when using other turbine technologies.
Plant capacity: 5000 tpd
Type of process:
Dry
Fuel used: Coal
Application:
Waste heat recovery in cement production.
Model used:
EPSd 730
Flue gas outlet temperature (1,2): 170˚C
Flow of kiln exhaust gas: 330 000 Nm3/h
Temperature of kiln exhaust gas (1): 335˚C
Flow of clinker cooler air (2):
300 000 Nm3/h
Temperature of clinker cooler air (2): 300˚C
Cooling agent: Air cooled condenser
Electrical generation: 7000 KWe
The typical cycle efficiency of a WHR ORC system at full load is around 25%. With a ROT, even in conditions of 60% of nominal load, 90% of relative efficiency is still achieved (22.5%).
As mentioned before, exhaust streams from the clinker cooler and the kiln preheater contain exploitable thermal energy that can be converted into power. In dry process cement plants, nearly 40% of the total heat input is available as a residual resource. Clinker coolers release large amounts of hot air ranging in temperature from 250 – 380˚C, corresponding to a range of heat from 330 – 540 MJ/t of clinker. Kiln preheaters release flue gases in a temperature range of 300 – 450˚C, corresponding to a range of heat of 750 – 1050 MJ/t of clinker. Once the portion required for drying purposes is deducted, typically by raw and coal mills, the residual heat can be then transferred to the ORC and converted into power, with no impact on the normal operation and production capability of the cement plant.
The exhaust gas or hot air from the process enters a WHR unit where in the heat recovery exchanger, the thermal power is transferred to a thermal vector, typically thermal oil. The thermal oil vehicle delivers the load to the organic fluid of the ORC cycle. The organic fluid circulates in a closed circuit where, when in liquid phase, is increased in pressure by a pump, heated up and evaporated respectively in the preheater and in the evaporator, receiving heat from the thermal oil vehicle, and finally expanded in a turbine. Then the exhaust vapour condensates in the regenerator and cools down in the air cooler before restarting the working cycle.
The use of the working fluid in the ORC cycle is important to obtain higher efficiency or to respond to specific cement manufacturing needs. More than 12 different type of fluids have been tested already by Exergy and ORC suppliers, and a big focus from R&D is currently dedicated to the hot gas filtration with ceramic candles for by-pass applications, potentially providing exploitable heat at higher temperatures.
Waste heat potential referred to plant capacity. (Plant capacity (tpd): 5000; kCal/kg clinker: 800; kg raw material/kg clinker: 1.6).
In cement applications, the selected organic fluid is usually cyclopentane because it is well matched to the thermodynamics of the process, thus improving the cycle’s performance. But in some cases, due to safety or environmental regulations in place in several countries or regions, such as the Seveso III directive (2012/18/EU) in Europe, the use of refrigerants or a non-flammable fluid can be a solution. Exergy has already designed and successfully applied an ORC solution
Table 1. Cement plant case study.that utilises a refrigerant as a working fluid for an application in a cement plant in Italy with a capacity of 2600 tpd and an installed power of 3.6 MW.
An ORC system represents a very effective and viable solution to:
f Decrease the energy demand of the cement manufacturing process producing clean power onsite that can be employed to feed the cement manufacturing process needs. It is estimated that up to 30% of the internal process’ needs could be covered by self-production from an ORC-WHR system. Electrical consumption can also be reduced through the cooling fans on the air/air heat exchangers on the clinker cooler side, because with WHR installation, the cooling is performed by the boiler.
f Decrease the operating costs connected to the reduction of the energy bills for the demand of electricity from the grid.
f Increase the sustainability of the manufacturing process by reducing indirect CO2 emissions associated with the demand for conventional electricity from the grid. Another environmental indirect benefit derived from the use of ORC relates to the saving of water in the Gas Conditioning Tower (GCT). The GCT normally uses water to cool down the gases, yet, with ORC, such waste of water can be avoided.
f Increase competitiveness and attractiveness on the market by deploying measures that increase the energy efficiency and respond to the call for the reduction of carbon footprints.
f Facilitate access to electricity with independent microgrids for remote or isolated sites.
Exergy has designed and studied many WHR systems for the industrial sectors employing the ROT and has 11 WHR power plants from industrial
applications in its portfolio. Exergy’s ORC systems can be applied to cement plants of any size, from small modular units up to tailored power plants for a total power installed of 50 MWe.
One example of an ORC WHR system for cement application that EXERGY has studied for a possible customer is a 7 MWe ORC unit which recovers the exhaust gases from the kiln and clinker cooler of a cement plant with a capacity of 5000 tpd.
From kiln exhaust gases at the temperature of 335˚C with a flow rate of 330 000 Nm3/h and exhaust clinker cooler air at 300˚C and a flow rate at 300 000 Nm3/h, it is possible to generate 7 MWe (Table 1). This solution is designed with an Air-Cooled Condensing system and based on Exergy’s ROT technology.
An ORC WHR system installation for a cement plant has a typical payback time of 4 – 6 years depending on the electrical output of the ORC required, the cement plant configuration, the price of electricity and local government incentives such as carbon credits, green certificates, and any additional premium for saved CO2 emissions that can sensitively contribute to reducing this time-frame.
With the increasingly pressing climate crisis, it is becoming more urgent for the cement sector to reduce its carbon emissions and energy consumption. Several countries are already moving to adopt policies and roadmaps to accelerate the decarbonisation of this sector, but more cooperation between advanced and developing economies is needed to accelerate this process. As the IEA reports, “cement emissions remain stubbornly high and the development and deployment of new technologies is essential to get on track with the NZE scenario.”
In this context, WHR represents a valuable opportunity and a key technology for the cement sector to give an immediate answer to the challenges of carbon and energy intensity reduction, whilst supporting the transition to other technologies currently under development.
Andrea De Finis has a degree in Engineering from Politecnico di Milano. He has gained throughout his career an extensive experience in sales activities of industrial plants with a focus on cement.
Sara Milanesi is a communications professional with 15 years of experience working for the energy sector. She is skilled in communications and in B2B marketing strategies to support sales growth.
Quality analysis is essential to your products, productivity and profitability. We offer solutions that fit. Determine quartz in raw meal, free lime and clinker phases, clinker content in cement with a Thermo Scientific XRF/XRD system in the lab. Minimize raw mix variability, satisfy multiple quality control targets with a Thermo Scientific online elemental analyzer. Link both instrument results with AccuLINK software. Your most demanding requirements in process and quality control will be met.
Cachapuz elaborates on the implementation of automation and logistics optimisation systems in the cement industry.
Last year marked the thirtieth anniversary of SLV Cement, a journey that began in Portugal in collaboration with Cimpor and Secil. This partnership has launched Cachapuz to become a global reference in the implementation of automation and logistic optimisation systems in the cement industry. The company now collaborates with the main players in the sector and has a presence in all geographical regions.
The 1990s marked a period of significant economic and social development in Portugal, driven by its accession to the European Economic Community (EEC) in 1986. The application of structural funds aimed to modernise key sectors and improve infrastructure, leading to a substantial
increase in demand for construction materials, particularly cement.
In the early 1990s, Cachapuz faced the challenge of automating bulk cement dispatch, enabling the conditions necessary for truck drivers to perform load operations autonomously, safely, and optimally. This solution was designed to be integrated with existing information and automation systems, providing dematerialised and controlled procedures.
The challenge was accepted, and the developed solution eliminated the need for a loading operator, reduced average loading time, and optimised the loaded quantity, preventing trucks from being overloaded or having to return to the silo loading lane to complete the load.
The impact of the solution was immediate, enabling shorter turnaround time and resulting in increased service capacity and an extended dispatch window, with potential for 24/7 operation, while reducing operational costs.
By the end of that decade, all Cimpor and Secil cement plants in Portugal’s mainland and
islands had automated bulk cement dispatch with self-service operations.
The success of automating bulk cement dispatch strengthened the partnership with Cimpor and Secil, leading to new challenges, particularly the evolution of the solution to cover other material flows and operational procedures.
Thus, a comprehensive solution emerged, focused on addressing logistic challenges in optimising raw material reception and cement dispatch. This solution was fully integrated with ERP and plant automation systems. It is designed to address the needs of a dynamic and ever-evolving industry, particularly those using alternative fuels in order to reduce emissions in the cement industry.
In the next decade, SLV Cement’s internationalisation process was initiated, propelled by the established partnership with Cimpor and Secil. This collaboration enabled the solution’s expansion to other plants and countries where these companies operate.
The international implementations at the Cimpor and Secil plants heightened the external visibility of Cachapuz and its solution. This, in turn, fuelled growth in the countries of operation and drove entry into new geographical regions.
From Egypt and Tunisia, to Brazil and Argentina, and more recently in Spain, Côte d’Ivoire, and Cameroon, this range highlights the company’s collaborative growth and commitment to service quality improvement. These commitments, grounded in emerging trends and technologies, have translated into tangible outcomes.
The international expansion of SLV Cement and the adaptation of the solution to diverse cultural and operational realities have led to its quick adoption by other major players in the sector operating across various countries. This strategic positioning has enabled Cachapuz to actively participate in many of the cement industry’s corporate, regional, or local digital transformation initiatives with the aim to develop and implement more intelligent, sustainable, and stakeholder-focused systems.
Secil-Outão Plant (Portugal).Ensure each step with…precision
Paths to Decarbonisation
Alternative Fuels and H2
Process Optimisation
Change of Fuel-mix
Easy permitting
Lower Costs
Over
In the last few years, Cachapuz has focused on the technological development of SLV Cement, leveraging advancements driven by the Industry and Logistics 4.0. paradigms. The vision involves creating an integrated, intelligent, and collaborative ecosystem centred around individuals participating in the cement supply chain, all while prioritising environmental sustainability. This vision aligns with the emerging paradigm of Industry 5.0.
This emphasis has been consistently pursued in collaboration, particularly with entities within
the National Scientific and Technological System. A noteworthy partnership has been established with the University of Minho and its research and innovation institutions, where knowledge is transformed into value through a continuously updated, distinctive offering aligned with sustainable digital transformation initiatives in the cement industry.
It is worth highlighting that Cachapuz is a founding member of the Digital Transformation CoLab (DTx), where it presides over the Strategic and Supervision Committee. In collaboration with DTx, projects are undertaken in the physical, digital, and cyber domains, namely in the areas of advanced materials (intelligent and sustainable), hardware and sensors (micro, nanoelectronics, and flexible electronics), and software and information systems (artificial intelligence, internet of things, communications, and cybersecurity). These projects ensure the technological roadmap of SLV Cement and position it in the next generation of advanced cyber-physical systems.
SECIL
“The SECIL and Cachapuz partnership represents a ground-breaking and visionary alliance, marked by commitment to dedication, innovation, and excellence. This strategic collaboration serves as a guiding light for progress, demonstrating a continual pursuit of advanced and adaptable solutions. Together, SECIL and Cachapuz have consistently redefined the standards of quality and efficiency, always attentive to the emerging needs of their customers.”
João Maria Forjó, Information System DirectorCIMPOR
“Since the beginning of our journey, SLV has been a transformative solution that has significantly enhanced Cimpor´s dispatch processes, bringing improvements in operational efficiency and control. Before, Cimpor´s dispatch processes had room for improvement in its accuracy, compliance, and real-time monitoring.
This level of control has had a direct positive impact on our overall performance and, consequently, on the level of service we provide to our customers. In conclusion, SLV has proven to be more than just a tool. It’s a strategic asset that has redefined how we approach dispatch processes.
We extend our sincere appreciation to the Cachapuz team for their innovative solution and ongoing support during this long partnership. SLV has become an integral part of our success story, and we look forward to continued collaboration and mutual growth.”
Tiago Soares, Cimpor´s Information Technology Director
DTX Colab, Portugal
“Since the beginning of the collaborative innovation partnership between DTx and Cachapuz, our main focus has been to support the creation and the development of ground-breaking technological solutions that seamlessly integrate physical and digital components, revolutionising Cachapuz’s core area of activity, positioning it as a leader in the next generation of evolved cyber-physical systems in the weighing sector. Looking ahead, DTx CoLAB expects to embrace new challenges, co-creating and developing projects that not only deliver value to Cachapuz but also have a tangible impact on our associate’s innovation ecosystem and business partnerships.”
André Matos, Chief Executive Officer of DTX ColabThe growth through partnership and collaboration has been a decisive factor, positioning SLV Cement as a solution sought after by the cement industry for the automation and optimisation of logistic processes, service improvement, and increased transport efficiency. Moreover, it contributes significantly to the reduction of its environmental impact. As demonstrated by the enduring relationship of over three decades with Cimpor, Secil, and some scientific entities, collaborative work and partnerships are the cornerstone of valued co-creation, supported by a vision of continuous improvement and that is focused on customers and service quality.
• Updated user interface simplifies training and operations
• Quality on-screen instrumentation graphing
• Supports multiple cameras/displays
• User configurable
• Captures/stores images
• Supports legacy D/I output, modbus or Internet temperatures
• Compatible with Windows 10 network/security requirements
Cabbarli, Halil İbrahim Karabulut, & Kadir Körükcü, ALFER Engineering, discuss how to optimise fans and ducts, emphasising the importance of inlet line design.
The primary step in radial fan design is the correct determination of the system resistance. Since the fans are turbomachines whose flow rate changes depending on the system resistance of the line in which they operate, the design point should be determined according to the ducting losses. It is also necessary to consider the physical properties of the gas which is transferred in the system and the dimensional spatial constraints. The power that the fan will consume is related to the density of the gas passing through it. Therefore, correct determination of the density value is an important point in fan design. If the fan is operated in a place with higher or lower system resistance than the design point, there is a risk of inefficient operation. The inlet ducting of the fan is also important. The relevant AMCA 201-02-R2007 system effect standard should be examined.
Through CFD analysis, ALFER Engineering verifies the fans it has designed with unique fan design correlations. The company also identifies the problems that may occur and offers solutions. The final filter fan design values from the Heidelberg Materials Togo Project are indicated in Table 1.
According to initial studies with the prospective new impeller, the expected casing loss (including inlet box loss) is approximately 700 Pa at 1 200 000 m3/h actual inlet flow with 0.749 kg/m3 inlet gas density. Therefore, the design total pressure rise target is set at 4230 Pa between the rotor inlet and rotor outlet boundaries to give a total pressure rise of 3669 Pa between the casing inlet and casing outlet.
When the final filter fan was designed in the Alfer design infrastructure, the first issue considered in the meridional geometry prior to analysis
was blade positioning. In the expected positioning for radial fans, the low speed shroud flows in the radial direction (vectors), meaning that the ideal blade angle has the same value in the lower shroud and in the upper shroud. It is believed that this is more accurate in terms of the ideal blade angle.
As the rotor is exposed to high temperatures during operation, rotor mechanics must be considered in the design. To increase volumetric efficiency, the inlet cone design has been adapted to prevent the air drawn from the inlet pocket from circulating inside and narrowing the passage area.
After designing the final filter fan meeting the desired flow and pressure values, steady and transient CFD analyses were validated.
Transient analysis results are shown in Figure 1. The most important parameters are the flow turning from the inlet box to the fan rotor and the distribution of velocity
leaving the rotor blade. By analysing Figure 1, it is clear that there are no vortices created at the transition from the inlet bell mouth to the rotor. However, due to the cylindrical shaft, there is a relocating vortex behind the shaft. As the flow leaves the rotor, it gradually diffuses through the volute and leads the flow to the outlet properly. It then stagnates at the cut off. The stagnation point is another parameter showing the design match and correct cut off position.
In addition to the velocity, the total pressure of the filter fan is also visualised. Figure 2 shows the total pressure distribution inside the filter fan. By analysing Figure 2, it can be seen that the total pressure is distributed uniformly at the exit of the rotor which is the indication of proper distribution of the flow at the rotor inlet and outlet passages. The same can be said for the diffusion process starting from the volute cut-off region to the outlet. Through analysis of the filter fan outlet, it
can be seen whether the total pressure requirements are met.
As a result, the fan requirements are accurately determined and the correct design is made. The design is then verified by CFD analysis, and a final filter fan design has thus been realised, meeting the requirements and operating at 86% efficiency.
In this example, an aerodynamically efficient final filter fan was designed and the inlet duct optimised. The revised duct design was verified by the CFD analyses after the design.
Final filter fans play a crucial role in the cement industry as they regulate and filter the air flow. While they ensure the proper pressure and flow rate in the system, the process remains environmentally friendly by meeting the standard dust emissions. Essentially, the final filter fan plays an essential role in maintaining the efficiency, safety, and environmental sustainability of the cement manufacturing process.
In order for the final filter fan to work efficiently, proper flow must be ensured at the fan suction. If the inlet duct of a final filter fan is not properly designed, it can lead to uneven airflow distribution, improper pressure conditions, and inefficient material conveyance. Ultimately, a poorly designed inlet duct for a final filter fan can undermine the overall efficiency, performance, and safety of the cement manufacturing process.
Since the inlet condition affects the whole flow field inside the filter fan, the inlet flow should be separate and uniform. Accordingly, the inlet duct was analysed.
Solution
Bag
Heavy
ESP
Fan
Martin Paterson, C2CA, predicts the next best SCMs in the race beyond slag and fly ash.
With an expected increase in cement production from 4.2 to 5.0 Gt/year by 2050, driven by population growth and urbanisation, there is an urgent need to reduce clinker content and increase supplementary cementitious material (SCM) usage to lower concrete’s carbon footprint.
Reducing clinker content aligns with the available clinker production capacity, currently at a 70% utilisation rate, and the trend towards lower clinker and higher SCM use in cement. Laboratory tests have shown that cement blends with only 25% clinker can match the quality of existing solutions. However, accommodating these new blends requires evolving from prescriptive cement standards to performance-based specifications, as exemplified by the EU standards [EN197] specifying 34 unique cement types, many utilising SCMs.
The availability of traditional SCMs such as fly ash and slag is increasingly becoming a concern due to their scarcity in many regions. The main reasons for this are the increased demand for sustainable construction materials, shifts in energy production, regulatory changes, economic factors, and geographical constraints. This scarcity poses a challenge for sustainable construction practices, as these materials are essential for reducing the environmental impact of concrete and cement production. In light of this scarcity, the need for alternative SCMs has become paramount.
Beside calcined clays, slags other than GGBFS and various mine tailings, waste concrete emerges as a viable and abundant solution to this challenge. Unlike most of the other mentioned alternatives, waste concrete is widely available and often found in proximity to construction sites where it is needed the most. This readily available source not only addresses the scarcity issue but also minimises transportation-related environmental impacts, making it a pragmatic and sustainable choice for SCMs in concrete and cement production. By harnessing the potential of waste concrete as an SCM, not only are the demands of the construction industry met but a contribution to the circular economy also takes place via the
repurposing of materials that would otherwise end up as waste in landfills.
The global concrete recycling landscape is characterised by both environmental challenges and significant economic potential. Each year at least 3 billion t of new concrete waste is generated worldwide, underscoring the magnitude of the issue and this does not even take into account the huge amount of waste that has been landfilled over the decade. However, this challenge is also an opportunity, as it paves the way for innovative and sustainable solutions. Size estimates for the major global concrete waste markets are shown in Figure 1.
While most of the currently available solutions focus either on landfilling or downcycling the waste to a road base aggregate, C2CA being a Dutch tech startup, has developed an innovative process (Figure 2) to transform this concrete waste into a highly reactive SCM, to either replace clinker in cement or cement in concrete.
“The process is unique and combines a series of technologies to ensure a clear separation between the different fractions, a smooth liberation and the highest possible yield of fines and an activation step which transforms the fines into a reactive binder”, states Thomas
Considering the potential to harvest 15 – 30% of SCM from the concrete waste, the processing and upcycling could replace 450 – 900 million tpy of cement, which is equivalent to 25% of the global annual production and accordingly would allow for a reduction of 2% of global CO2 emissions.
“To unleash the full potential of our technology
it will need several thousand decentralised plants operating with the C2CA process but in the long term, we believe we will find enough global partners to create a significant impact on the reduction of greenhouse gas emissions”, states Martin Paterson, CCO and Head of Products.
Martin further highlights that the processing of concrete waste not only has enormous environmental potential but also is very interesting from a commercial perspective:
“While traditional downcycling – this is mainly crushing down the concrete waste to road-based aggregates – can be sold to the market at a price of max. €2 – 5/t, the upcycling and selling of the gravel, sand and fines as an SCM can result in a total value of €30/t of upcycled concrete waste.”
The C2CA process, along with its associated machinery and resulting products, has undergone an extensive development in various industrial-scale projects involving collaborations with both industrial and academic partners over the past four years.
Priya Perumal, C2CA Chief Science Officer explains: “In 2023, we successfully processed 1000 t of waste concrete, allowing us to fine-tune our process for enhanced reliability and quality. Our various output products went through rigorous testing for concrete mixes, encompassing evaluations of compressive and splitting strength, frost/thaw resistance, and shrinkage. Additionally, our involvement in six distinct sustainability projects within the Dutch government showcased the exceptional density and strength development of our materials. Importantly, these characteristics were identical to the reference structures produced with virgin raw materials.”
The next milestone of the C2CA global rollout strategy, is the construction and operation of its first fully commercially scaled plant in the Netherlands. This flagship facility is set to commence production in Q2 2025, with the capacity to process approximately 150 000 tpy of waste concrete.
The project will be executed and operated through a joint venture with a local construction and recycling company. Their Circular Manager explains: “The Dutch construction sector is ready for upcycled construction materials and there
The C2CA process allows for adjustments to maintain a certain high-level uniformity. Advanced screening methods increase the input material quality, the crushing and separation steps can be adjusted to control the chemical composition of the fines and if required, local side stream materials can be added. The variations in chemical properties are shown in Figure 3.
The main fractions, being CaO and SiO2 which are expected to take part in the hydration reactions, are responsible for the binding properties of the RCF. However, SiO2 is either crystalline quartz or exists as hydrated products of the parent material and CaO exists as CaCO3 or in hydrated products. These main elements of RCF can be activated to enhance the reactivity with additional mechanical, carbonation and thermal treatment, which is taken care of by the C2CA process.
SCMs are expected to be lower in calcium compared to traditional Portland Cement (PC) and high in pozzolanic reactivity. From the ternary diagram of the existing SCMs (Figure 4), slag with relatively high calcium content goes close to PC. Silicafume (SF) lies close to the SiO2 rich zone and metakaolin (MK) mid-way between SiO2 and Al2O3 with great pozzolanic properties. RCF can be placed in a region between hydraulic and pozzolanic materials with the presence of both CaO and SiO2 With enhanced treatment, the potential of this material can be tapped at higher replacement levels with PC.
is a strong push from the government and private sector to replace up to 50% of virgin raw materials by 2030. We have been searching for technology that is efficient, mobile, capable of operating in all weather conditions, and versatile in handling variable input quality and found everything in the C2CA process. The aim of committing to sustainability and keeping customer needs at the forefront, while guaranteeing high-quality output materials and robust economics made us believe in this long-term collaboration.”
Answering the initial question on who will win the race of replacing slag and fly ash as traditional SCMs are not straightforward and will require a set of global and local solutions.
“There is no silver bullet and even though the CO2 emissions for our recycled concrete fines (validated by a third-party Life Cycle Assessment), confirm a low carbon footprint of less than 20 kg CO2/t of produced SCM, the industry needs to consider other solutions in addition. In many locations, calcined clays, geopolymers or activated mine tailings might be the right solution but the big advantage of concrete waste is that it is globally widely available and close to the construction areas”, states Martin.
Thomas adds: “To make a significant short term reduction in the CO2 emissions from our sector, all solutions must be explored. Our focus is to produce a SCM from locally available raw materials, upcycled locally and delivered to local concrete producers. Joining forces is key to
Figure 4. RCF in the Ternary Phase Diagram.achieving this vision: by working together, sharing ideas, exploiting synergies, we can build a low carbon future with a much more diverse cement and concrete composition.”
While collaborative efforts are key, a pivotal aspect involves advocating for legislative and standards changes to accommodate new, sustainable construction materials.
By fostering an environment that encourages and aligns with green practices, the way for a future is paved where industry growth and environmental responsibility go hand in hand.
With over two decades of experience in Project Management, International Sales, and Business Development, Martin Paterson is recognised as a leader in sustainable technology for the cement, concrete, and mining industry. His impressive career is anchored by an M.Sc. in Civil & Environmental Engineering. Martin’s entrepreneurial spirit
is evident in his ability to identify opportunities, lead bids, negotiate contracts, and cultivate customer relationships.
His leadership is not only marked by strategic vision but also by the ability to efficiently lead teams and navigate the intricacies of company operations. Martin’s strategic versatility was showcased in various key roles at Christian Pfeiffer, FLSmidth A/S, and IBAU HAMBURG.
Michele Di Marino, Stefano Zampaletta and Frank Brandt, Cementir Group, explain how to reduce the environmental impact of white cement production, while securing superior performance.
Over the past few years, Cementir Group has undertaken a resolute commitment to address the pressing challenges posed by environmental issues and climate change. This commitment is reflected in its multifaceted approach, targeting the reduction of CO 2 emissions and water consumption, preservation of natural habitats, and the promotion of technical solutions to minimise environmental risks. The group’s dedication to a low-carbon economy has earned accolades from CDP, an independent organisation, and a benchmark for environmental reporting.
In December 2022, the group achieved an ‘A’ rating for the second consecutive year in the Climate Change category, surpassing sector averages (B) and European averages (B). Simultaneously, its leadership position in CDP Water Security, with an ‘A’ score, has been confirmed. For the first year, Cementir has also been recognised Supplier Engagement Leader by CDP, positioning itself among the top 8% overall companies globally assessed for Supplier Engagement on climate change.
The recognition as a Supplier Engagement Leader underlines, once again, its commitment to environmental stewardship. Even in 2023, Cementir submitted the CDP Questionnaires (Climate Change and Water Security) and as of January 2024 it is still under evaluation, awaiting the official 2023 rating.
In July 2021, the group’s CO2 emission reduction targets were validated by the Science-Based Targets initiative (SBTi), aligning them with the ambitious ‘well below 2˚C’ objective outlined in the 2015 Paris Climate Agreement.
In 2023, following the formalisation of the guidelines for the cement sector by SBTi, Cementir updated its transition plan and filed a commitment to be aligned to 1.5˚C SBTi scenario. As of January 2024, the validation process from SBTi is still in progress.
The efforts to diminish environmental impact cover the entire value chain, from procurement and manufacturing to logistics and distribution. Cementir Group actively collaborates with local communities, suppliers, customers, non-governmental organisations, and various stakeholders. Through a comprehensive 10-year roadmap, Cementir Group aims to implement more disruptive measures to combat climate change, emphasising the maximisation of existing technologies and the groundwork for breakthrough innovations leading to the production of ‘net-zero emissions’ cement.
From 2022, the group has intensified its focus on innovation, a fundamental driver for sustainable progress. Ongoing studies and the development of low-carbon cement were completed and the installation of a pilot carbon capture and storage (CCS) unit at
Aalborg Portland has started with additional feasibility studies of CCS technologies at selected plants. Consequently, the 2030 Roadmap underwent updates to include the deployment of carbon capture technologies at the Aalborg plant, in addition to actions already planned for all its operations. The CCS test facility is part of the ConsenCUS project, consisting of several leading research institutions and companies, and funded by the European Union’s Horizon 2020 research and innovation programme.
Cementir’s commitment to sustainability extends to its white cement production, where unique challenges arise. As the world’s leading producer and exporter of white cement with approximately 25% share of worldwide trade and a production capacity of over 3 million t, Cementir Group, through its renowned global brand Aalborg White®, has played a pivotal role in iconic structures worldwide, from the Kennedy Centre for the Performing Arts in Washington to the Naturalis Biodiversity Centre in Leiden, and from Azabudai Hills in Tokyo to the Mei Xi Hu International Culture and Art Centre in Changsha.
The distinct features of white cement, characterised by its colour and high performance, are achieved through the meticulous selection of highly pure and carefully chosen raw materials, complex production processes, and an exceptionally rigorous quality control process.
Transitioning towards more sustainable production in the white cement segment involves a distinct set of challenges compared to grey cement, due to major differences in the production process and the high-quality standards required. Common actions to reduce carbon footprint, such as the use of alternative fuels (AF) and supplementary cementitious materials (SCM), face heightened challenges, particularly concerning the colour impact.
From a process perspective, the limited usage of AF due to their negative impact on colorimetric performances creates a main challenge. Cementir Group has
partially mitigated this limitation through the recovery of waste heat from the cement kilns in Aalborg, DK. The Aalborg plant recovers excess heat from cement production, providing district heating to approximately 30 000 local households.
In 2022 alone, the Aalborg plant delivered approximately 1.3 million GJ of energy, equivalent to an estimated 150 000 t of CO2 not emitted from a local coal-fired power station.
On the product front, the SCMs currently used to lower the clinker ratio in cement while preserving performance, pose a challenge for white cement. Almost none of these materials can effectively replace white clinker without negatively impacting whiteness – the distinctive value proposition in comparison to grey cement. Therefore, the selection, availability, and quality consistency of materials become crucial in reducing the carbon footprint in white cement production.
To address these challenges, Cementir introduced D-Carb, representing a continuous and consistent decarbonisation effort for the Aalborg White range. As a leader in white cement, Cementir has embraced the challenge of lowering cement’s carbon footprint within the constraints linked to colour and performance requirements.
Leveraging long-term expertise in research and development and industrial production, a comprehensive investigation was carried out, starting from customer needs, and going upstream to the entire value chain, encompassing clinker and cement composition, production, and raw materials selection.
To provide customers with more than just a product, technical collaborations have been established with leading companies in the admixtures sector as well as with loyal customers to deep dive into several end-applications.
In order to meet the tight timing for more sustainable solutions, fast-prototyping techniques were deployed, involving extensive experimentation at lab and full-scale trial levels. This has allowed to turn a proven concept into an industrial reality: D-Carb family.
D-Carb is a new umbrella brand for white low-carbon cements, supporting industry-wide decarbonisation efforts. D-Carb will be rolled-out in Europe initially, and then in all other regions.
The first product of its kind, a CEM II/A-LL 52.5R will be produced in Aalborg and set to be launched in April 2024 in bulk and bags, further expanding the product offerings in Europe.
D-Carb matches a lower carbon footprint (-15% of emissions documented with Environmental Product Declaration by third party in this first product) with outstanding performances at early ages comparable to CEM I. Moreover, it
offers improved rheology and whiteness in certain applications. The interaction between well-known Aalborg White® clinker and limestone has been optimised, leveraging in-house extended expertise in white cement.
This high-quality standard enables the group’s customers to consider replacing CEM I in their manufacturing processes after a specific testing programme. No incompatibility with admixtures has been experienced during the extensive experimental phase. Cementir Group will keep up its customer-centric approach with its technical experts equipped to guide customers in adopting this new product and integrating it into their production processes.
As part of Cementir Group’s overarching roadmap, ongoing evaluations are underway to strengthen the D-Carb offering within the low-carbon cement spectrum. Cementir Group is committed to leading the way in sustainable cement production, contributing to a greener future for the construction industry. Through innovation, collaboration, and a steadfast commitment to environmental stewardship, the company strives to redefine the possibilities of cement production, sounding the bell for an era of sustainability and resilience for generations to come.
Michele Di Marino joined Cementir Holding in 2010, working in Copenhagen, Denmark. As the Commercial and Business Development Director, consolidating the leadership position White Cement in Europe and working on several growth and strategic projects. In 2017 he relocated to Rome and took on the role of Group Chief Sales, Marketing & Commercial Development Officer, leading global commercial strategy. He is pursuing the Sustainability & Innovation agenda.
Stefano Zampaletta is in charge of defining and coordinating the Group sustainability roadmap for a lower carbon product range and its roll-out at Group and
local level to support the Group’s CO2 emission reduction targets. Within this, the project in his focus that is he co-leading, is FUTURECEM®: a sustainable solution for cement and concrete technology. He also coordinates innovation activity on cement-based solution and products within InWhite Solutions®. During his 20 years’ of experience in the cement and concrete industry, he has covered different positions in technical assistance, quality control and R&D.
Frank Brandt is the Export Sales Director for Aalborg Portland A/S Denmark. In his position, Frank takes responsibility of all Aalborg Portland’s subsidiaries and sales activities on the European market for white cement. Frank has a Diploma in Business economics and has more than 15 years’ experience in International Sales in different industry sectors and regions.
ABB www.global.abb
ALFER
KC8
KHD
KIMA-Automatisierung
Minerva Engineering www.minervamuhendislik.com.tr
Mirion
PSCL www.pscl.com
Quantum
Endress
ES
SOMA
Thermo
UTIS www.utis.pt
VDZ Congress