
12 minute read
Ready To Perform

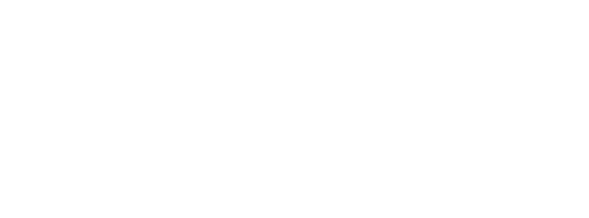
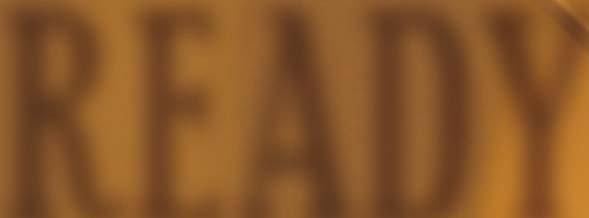

READYTOPERFORM
Marco Mazzamuto Marco Mazzamuto Carlucci, Casale, Carlucci, Casale, Switzerland, Switzerland,
describes the testing describes the testing methodology that was methodology that was used to ensure a new used to ensure a new ammonia synthesis ammonia synthesis catalyst was ready to be catalyst was ready to be successfully introduced successfully introduced to the market. to the market.
Catalytic ammonia synthesis from hydrogen (H2) and nitrogen (N2) atalytic ammonia synthesis from hydrogen (H ) and nitrogen (N represents one of the most important industrial reactions today. The represents one of the most important industrial reactions today. The catalyst used in this reaction is made from iron oxide, with small catalyst used in this reaction is made from iron oxide, with small amounts of other oxides added as promoters to enhance activity and amounts of other oxides added as promoters to enhance activity and stability. Despite the Haber-Bosch process being more than 100 years old, stability. Despite the Haber-Bosch process being more than 100 years old, only incremental improvements have been achieved until recently. However, only incremental improvements have been achieved until recently. However, combined work by Clariant and Casale has led to the development of a new combined work by Clariant and Casale has led to the development of a new ammonia synthesis catalyst: AmoMax-Casale. ammonia synthesis catalyst: AmoMax-Casale.
The new catalyst is based on Clariant’s wustite-based catalyst The new catalyst is based on Clariant’s wustite-based catalyst AmoMax® 10, with more than 100 references worldwide, and is customised AmoMax® 10, with more than 100 references worldwide, and is customised for Casale reactors (patent pending) with notably improved activity for Casale reactors (patent pending) with notably improved activity compared to iron-based catalysts. While retaining the same mechanical compared to iron-based catalysts. While retaining the same mechanical strength and resistance to ageing and poisoning, the new catalyst is strength and resistance to ageing and poisoning, the new catalyst is signifi cantly more active. This feature allows it to reduce the loop recycle signifi cantly more active. This feature allows it to reduce the loop recycle rate and loop pressure and/or to increase the production of ammonia. rate and loop pressure and/or to increase the production of ammonia.
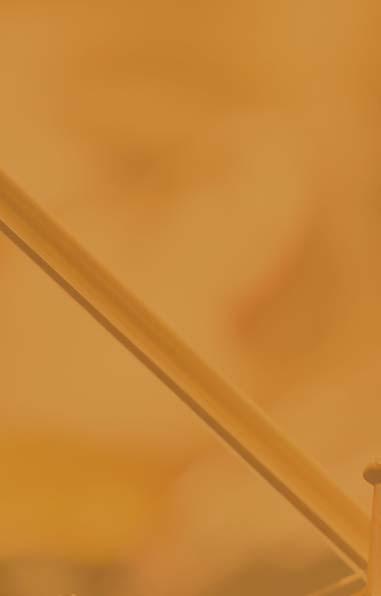

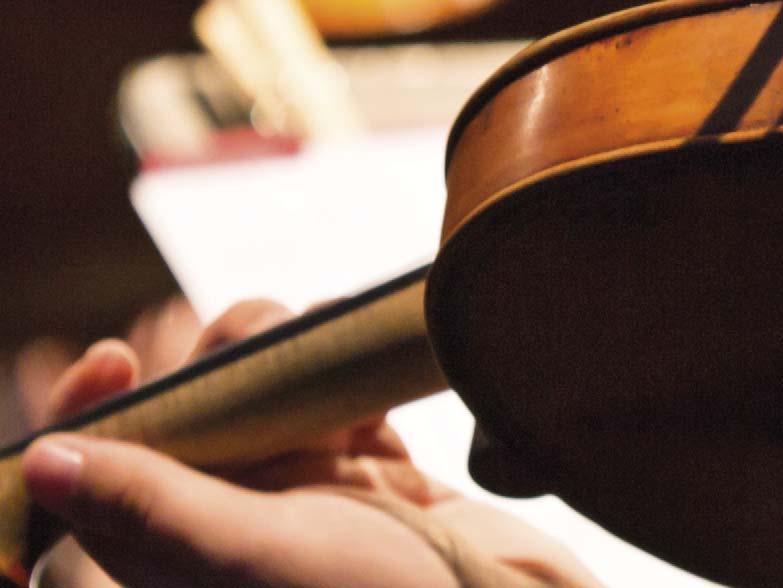

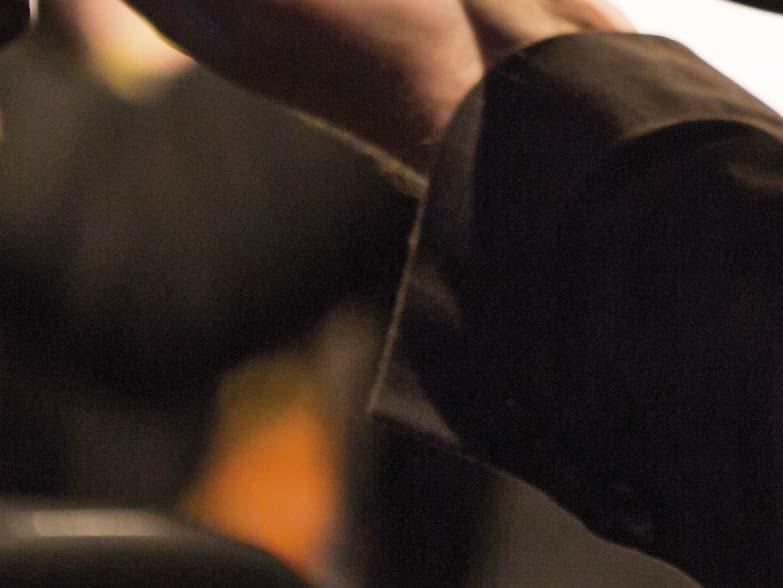
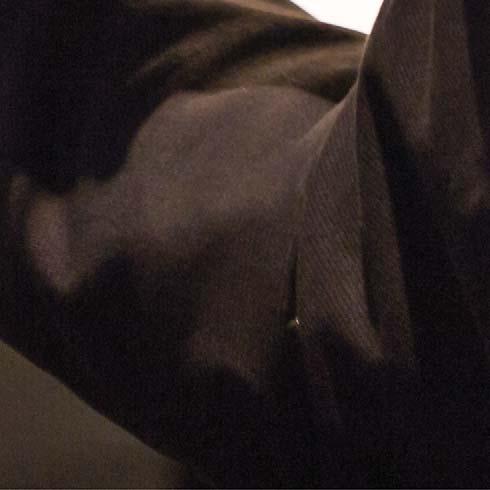
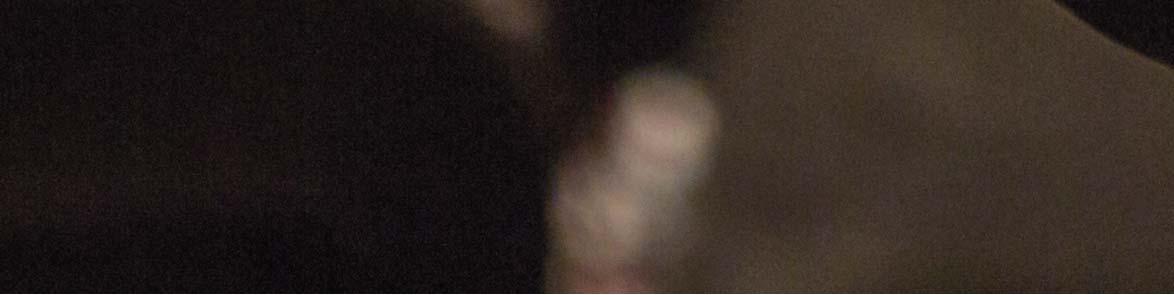
The higher activity of the catalyst contributes to an improvement in overall operating effi ciency, either by saving energy or by increasing plant capacity.
When introducing a new catalyst to the market, performance evaluation is of utmost importance; simple catalytic tests in powder form are not representative enough for industrial applications and are only suitable for screening purposes. A precise and rigorous methodology must therefore be applied.

Figure 1. Comparison between magnetite-based catalyst, wustite-based reference catalyst and AmoMax-Casale.
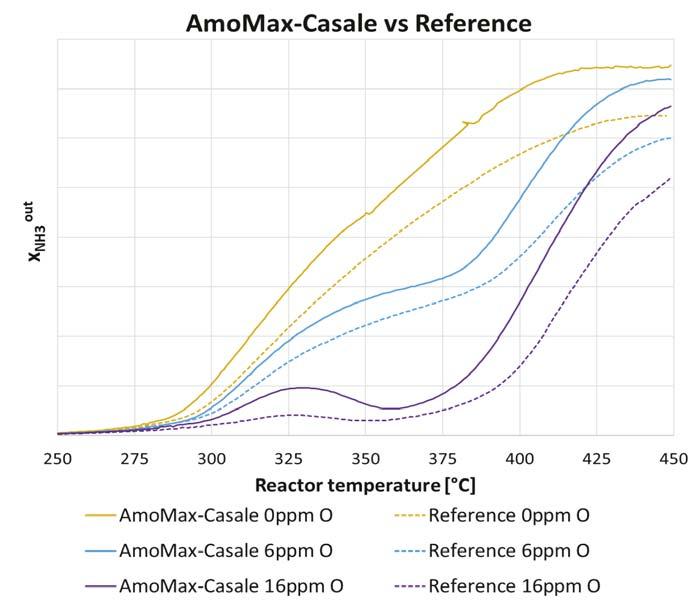
Figure 2. Comparison of poison resistance in different oxygen concentrations.
Table 1. AmoMax-Casale comparison in new converter Reference catalyst AmoMax-Casale
Internals Casale Casale
Production (tpd) 1655 1655 Operating pressure 140 134.5 (kg/cm2g)* Ammonia outlet 17.7 18.4 (% mol) Energy saving - >25 000 (kcal/t) *Outlet converter To reliably validate a new catalyst, laboratory-scale tests should be representative of the industrial catalyst. Catalytic and mechanical tests are therefore performed with the fi nal form and shape of the catalyst. During catalytic tests, the temperature profi le in the catalyst bed is measured and correlated with the heat exchange between the oven and the reactor. Subsequently, a systematic modelling of the obtained data is applied to understand the performance of the catalyst under industrial conditions. The information acquired is used to compare the new catalyst with the best available catalyst technology. In the event of enhanced activity from the new catalyst, as a next step in-depth mechanical stability characterisations are performed to confi rm the robustness of the catalyst. This includes simulations and experiments of friction between the catalyst pellets/granules and the walls of the reactor, crush strength and simulations of start-up/shutdown of industrial reactors. If the catalyst passes all the mechanical tests, proof of concept is achieved and it is considered ready for scale-up. Transferring the catalyst recipe from the laboratory to production scale is a highly complex process, with numerous important parameters that must be considered by the catalyst manufacturer. After a successful scale-up, the catalyst is prepared for shipment. To ensure it maintains its mechanical integrity and activity after transport from the production site to the plant, samples are taken during transportation, sent to different analytical laboratories and precisely analysed. The catalyst is then validated with the same catalytic and mechanical tests applied during the proof of concept phase. If all the parameters are confi rmed, the catalyst is fi nally ready for the market.
Catalyst characterisation
Performance tests
Activity
Laboratory results for the catalytic activity are shown in Figure 1. The test conditions were: Tubular reactor, tests performed on granules. Pressure: 150 bar and H2 : N2 = 3. Temperatures: 300˚C, 330˚C, 360˚C, 380˚C, 400˚C and 420˚C.
The results show how the AmoMax-Casale catalyst outperformed magnetite and wustite-based ammonia synthesis catalysts over the whole relevant temperature range. In particular, the difference from the standard magnetite catalyst is notable.
Based on the test results a kinetic model was created which fi ts very well the experimental data.
Poison resistance
The performance with different oxygen (O2) concentrations in the feed was tested at different temperatures (Figure 2), with the following results: The oxygen poisoning behaviour of the new catalyst is similar to the reference catalyst at all measured O2 concentrations (compare dotted versus full line). The deactivation observed due to oxygen poisoning corresponds to observations in commercial plants.

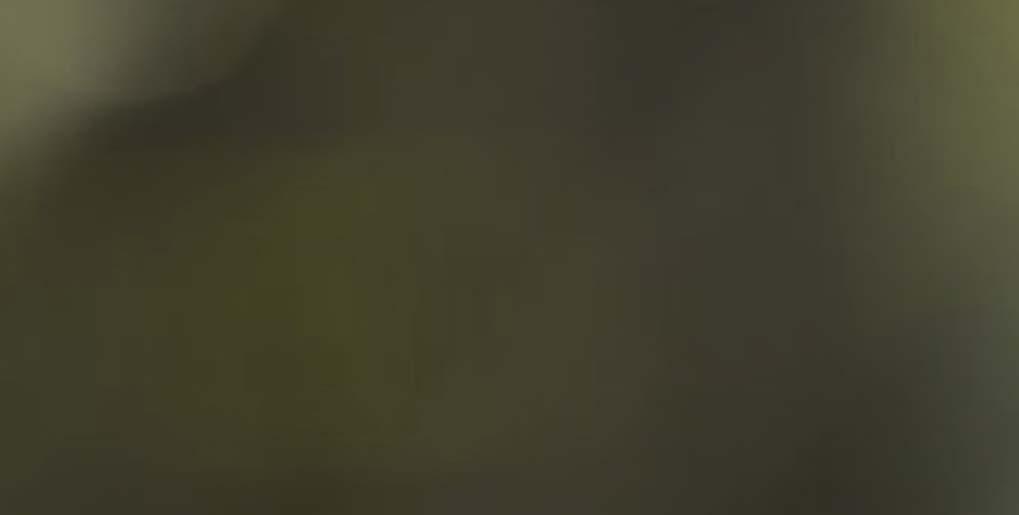
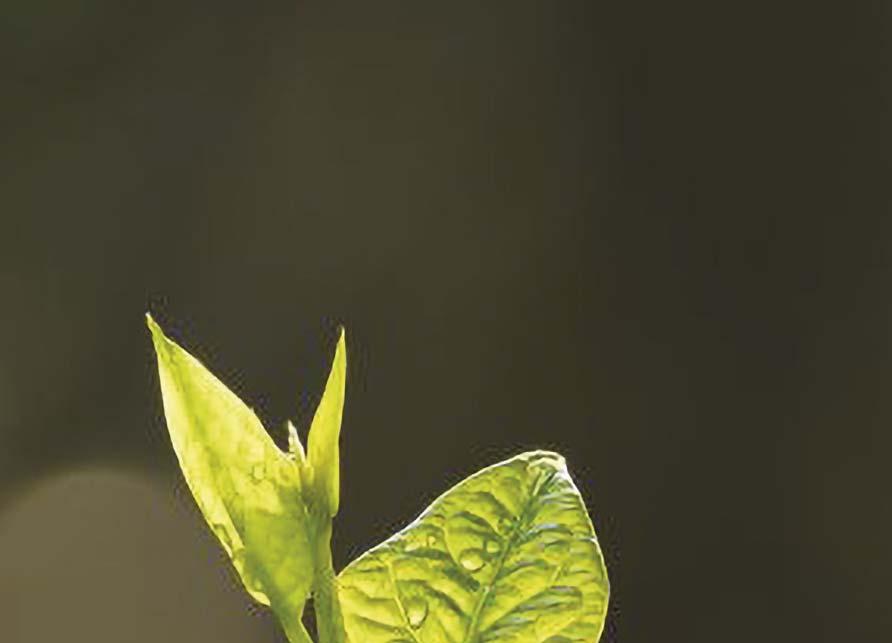
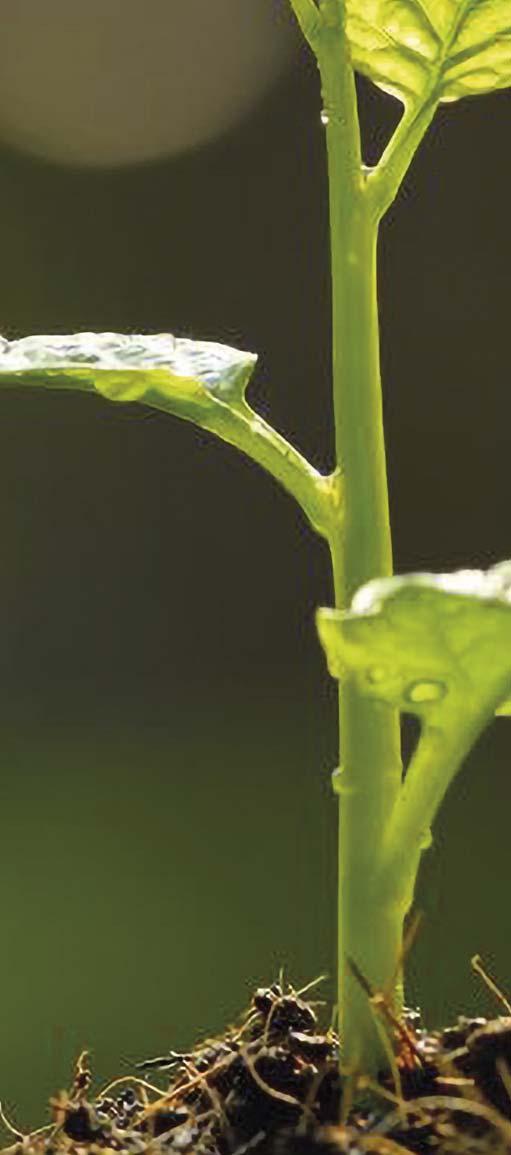

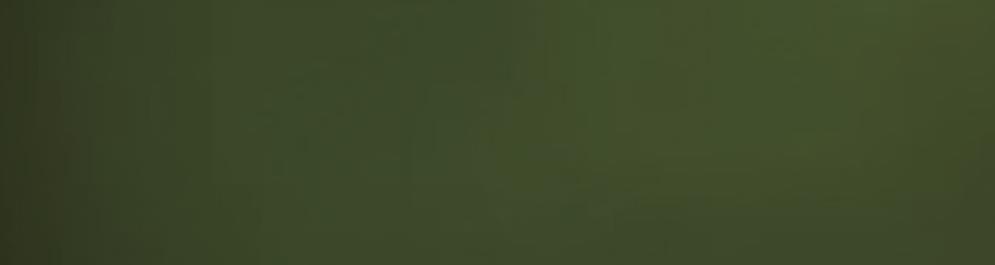
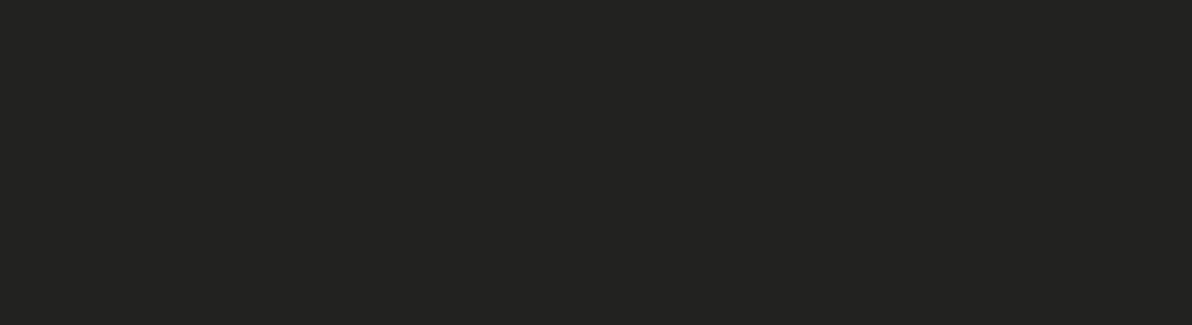
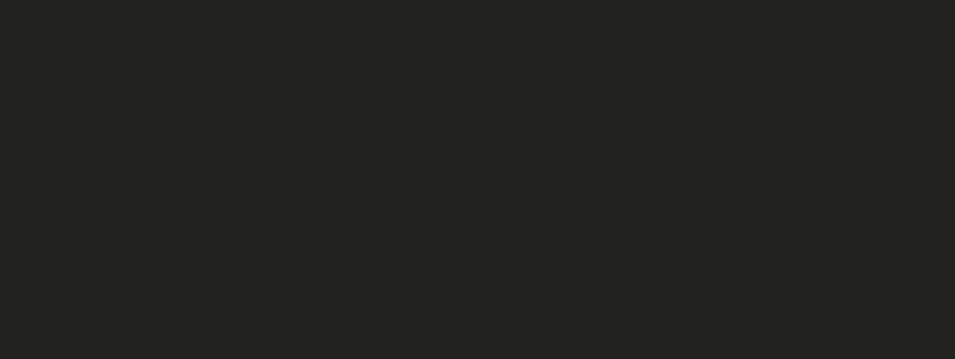
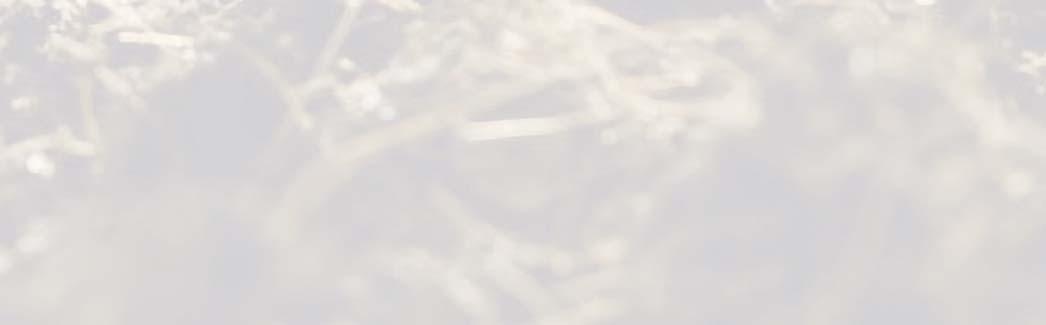

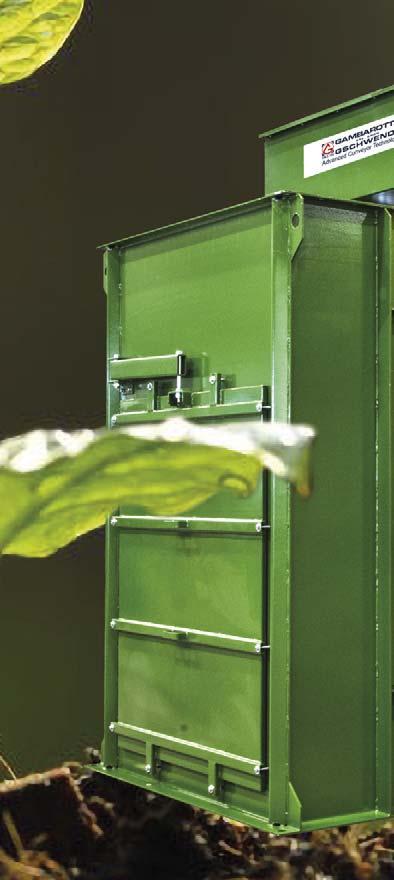


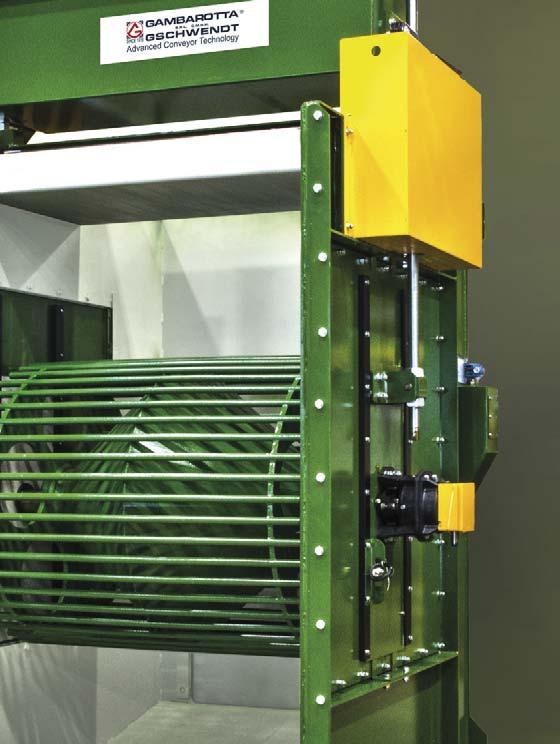

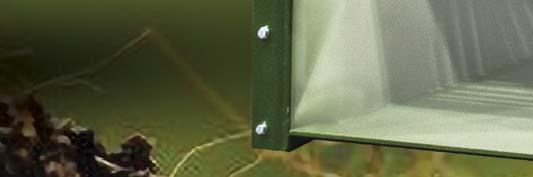
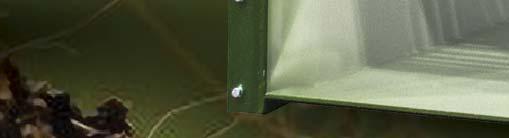

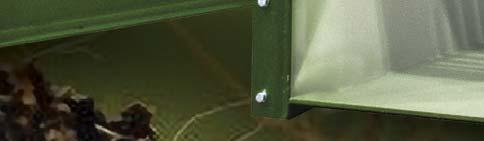

Table 2. AmoMax-Casale comparison in GIAP revamped converter
Despite the higher activity, the catalyst offers greater performance regardless of oxygen concentration.
Pre-revamping Reference catalyst AmoMax-Casale
Internals Other licensor Casale Casale Production (tpd) 1400 1870 1870 Operating 249 231.4 223.7 pressure (kg/cm2g)* Ammonia outlet 14.5 17 18.8 (% mol) Chiller duties 7.2 9.5 8.6 (Gcal/h)** Loop circulation 35 700 38 100 34 100 (kmol/h)** Energy saving - 163 000 >210 000 (kcal/t) *Outlet converter **Inlet ammonia converter Stability
The catalyst shows a notable stability in poisoning conditions. The performance was tested after each poisoning treatment and the activity was measured over time at fi xed testing conditions without oxygen poisoning and after a stabilisation period.
The new catalyst has proven to be very stable in comparison to the wustite-based reference catalyst.
Mechanical tests
Table 3. AmoMax-Casale comparison in Toyo Engineering Corp. revamped converter Reference catalyst AmoMax-Casale
Internals Casale Casale
Production (tpd) 2100 2100 Operating pressure 226.1 217.4 (kg/cm2g)* Ammonia outlet (% mol) 20.7 21.7 Energy saving (kcal/t) - >45 000 *Outlet converter
Beside the pure activities and performances tests, Casale and Clariant also performed tests to assess the mechanical suitability of the catalyst; in particular, the main objectives were to identify the intrinsic properties of the catalyst and how the catalyst could behave inside the Casale internals. The tests performed to mechanically qualify the AmoMax-Casale catalyst have been: Crushing strength properties in Casale internals: the catalyst has been tested with an in-house tool (the ‘Casale wall tester’) to assess the amount of powder produced due to friction of the catalyst with the Casale collectors. The crushing tendency of the catalyst has been compared with a standard wustite and magnetite catalyst without identifying significant differences in the final values. Pressure drop: a test unit was set up to assess the pressure drop generated by the new catalyst and compared with standard catalysts used as references, with the aim of evaluating the pressure drop result inside an axial-radial bed. The result obtained was in line with expectations and with the industrial pressure drop achievable in an industrial converter with a converter based on the standard catalyst. Shear stress test: this test is essentially Table 4. AmoMax-Casale performances in bottle-shaped revamped designed to apply stress to a test sample so converter that it experiences a sliding failure along a Reference (full AmoMax-Casale (full Difference plane that is parallel to the forces applied. front-end load, front-end load, after This test is therefore important for assessing before revamping) revamping) the effect of the catalyst on the Casale Internals Other licensor Casale - internals; after several tests the parallel stresses created on the internal surface are Catalyst life MOR SOR (AmoMax-Casale - comparable to the ones measured with the in third bed) standard catalyst. Production (tpd) 1776 1788 +12 Operating pressure 2206/152.1 2039/140.6 -167/11.5 (psig/barg)* Synloop inerts 11.5 16.7 +5.2 content (% mol) Ammonia at 1.8 1.4 -0.4 converter inlet (% mol) Ammonia at 13.9 13.5 -0.4 converter outlet (% mol) NH3 conversion 12.1 12.1 (% mol) Converter pressure 68/4.7 46/3.1 -22/1.6 drop (psig/barg) *At converter inlet
Catalyst operation in converters
As discussed previously, the new catalyst provides up to 30% higher activity compared with the standard wustite-based catalyst available on the market (the reference catalyst). The combination and synergy of this catalyst with the ammonia converter technology provided by Casale offers high performance, in terms of lower synloop operating pressure and higher ammonia conversion.
These benefi ts can be converted into energy savings and lower natural gas specifi c consumption or higher production if the limitation to a plant load increase is provided by the synthesis loop.
The benefi ts of AmoMax-Casale application can be exploited either with the installation of a new converter or by retrofi tting an existing one.
In case a new converter is designed, AmoMax-Casale can be conveniently applied in all beds, boosting synloop performances. A different layout could foresee a fi rst bed based on the standard catalyst, since it would work with fresh and unreacted gas.
A new converter based on the AmoMax-Casale catalyst and Casale internals to be installed in a new synthesis loop would provide a smaller pressure vessel or, as an alternative, a lower synloop circulation and therefore smaller equipment sizes with reduction of the relevant CAPEX.
When retrofi tting an existing converter, AmoMax-Casale is normally installed in the third bed and also often offered for the second. The application of the catalyst in the fi rst bed is usually not necessary for an ammonia synthesis converter revamping, considering that this basket is working with very fresh gas (low ammonia concentration) and therefore the differences with a standard catalyst are not so signifi cant.
Table 1 compares the performances of a new ammonia synthesis converter pressure vessel designed with Casale internals and operated with the standard wustite-based catalyst available on the market (reference catalyst) or the new catalyst. The comparison is made according to the following boundary conditions: Same catalyst life. Same Casale internals. Same new pressure vessel. AmoMax-Casale loaded in the second and third catalytic beds.
With an optimised ammonia converter internals confi guration and based on the latest Casale technological improvements, the new catalyst is able to enhance the overall synloop performance.
The installation of the catalyst inside a revamped converter can be even more effective considering that an existing converter is frequently working in conditions far removed from the original conditions, and therefore with a design and confi guration that is sometimes no longer optimised for the current operation.
In this regard two different design confi gurations for a GIAP bottle shape converter and for a Toyo Engineering Corp. bottle shape converter are presented, with the following boundary conditions: Same catalyst life. Casale or competitor internals. Existing pressure vessel. AmoMax-Casale loaded in the second and third catalytic beds.
The performance improvements in terms of energy saving and capacity increase are notable (Tables 2 and 3).
Industrial application results
In December 2019 the fi rst load of AmoMax-Casale was installed in a plant located in the Americas.
The original bottle-shaped converter had been already modifi ed by others to a two beds-interchanger confi guration.
Casale revamped the existing internals passing to a three beds-quench-interchanger confi guration and the new catalyst was loaded in the third bed.
A comparison between reactor performances before and after the revamping is shown in Table 4. Performance fi gures after revamping are from November 2020 plant operating data provided by the client.
As can be seen in Table 4, due to the replacement of the internals and the installation of the catalyst in the converter’s third bed it was possible to increase plant production and reduce plant energy consumption at the same time.
In order to maximise ammonia production, the client decided to lower the synloop purge rate; this led to a synloop inert content increase of approximately 45% with respect to plant data prior to revamping.
However, the improved converter confi guration and the catalyst superior activity meant no conversion was lost. Additionally, the syngas compressor operating pressure was reduced by 11.5 bar, providing further energy savings.
It should also be noted that converter pressure drop was reduced by approximately 30% after the installation of the internals.

Conclusion
In a joint multidisciplinary effort involving process engineers, scientists, modelling engineers and fl uid dynamic engineers, a new ammonia synthesis catalyst was created that was ready for the market in less than three years.
The catalyst is now available on the market and has successfully been installed and started up in the fi rst large-scale ammonia plant in the Americas.
ITALIAN TECHNOLOGY
