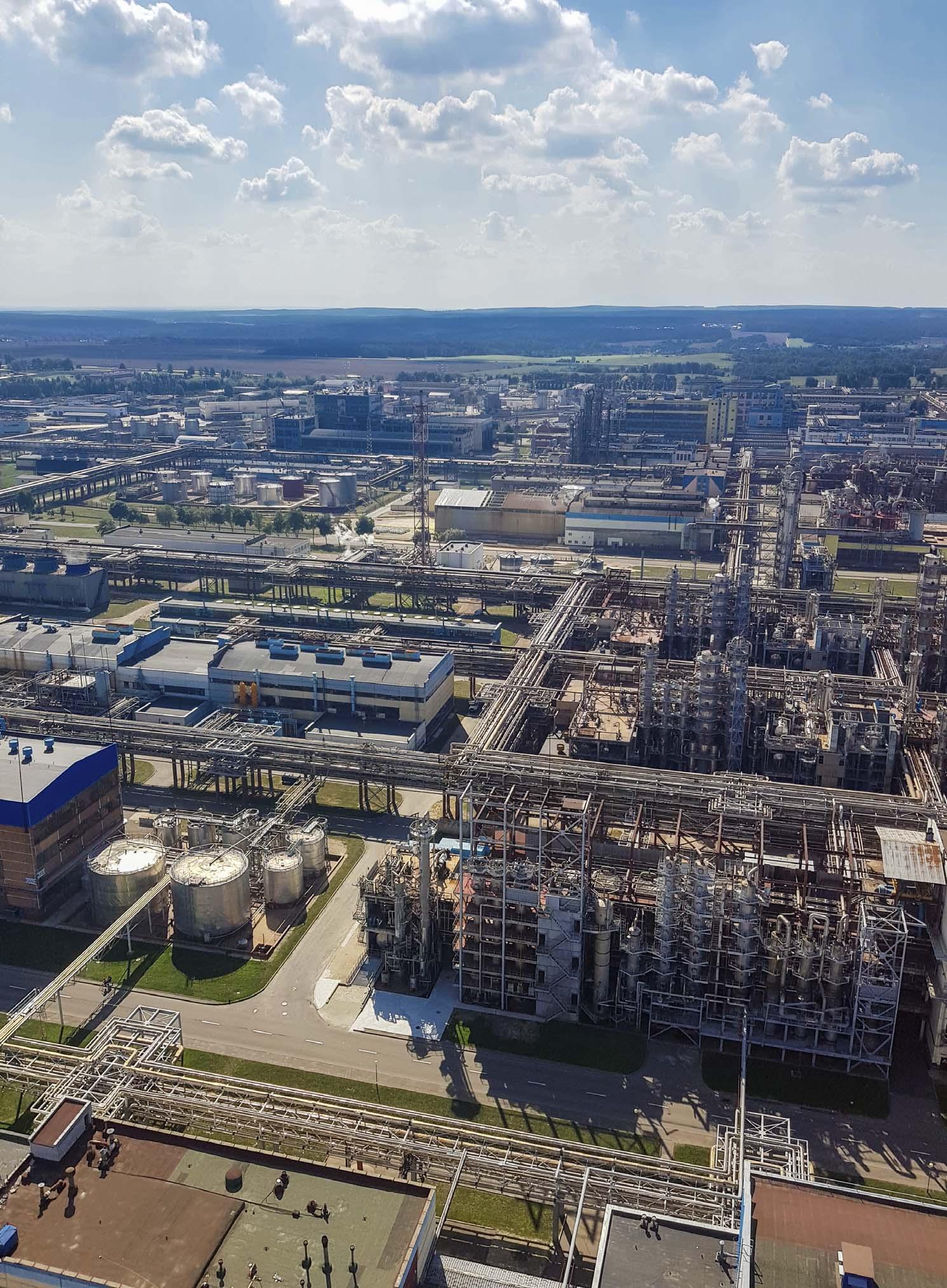
24 minute read
World Review
The World Review covers fertilizer projects either in progress or recently completed and is broken down by region: Africa and the Middle East, Asia Pacific, Europe and CIS and the Americas. Contributions are provided by Bagtech, BERTSCHenergy, Clariant, Haldor Topsoe, OCP Group and Stamicarbon.
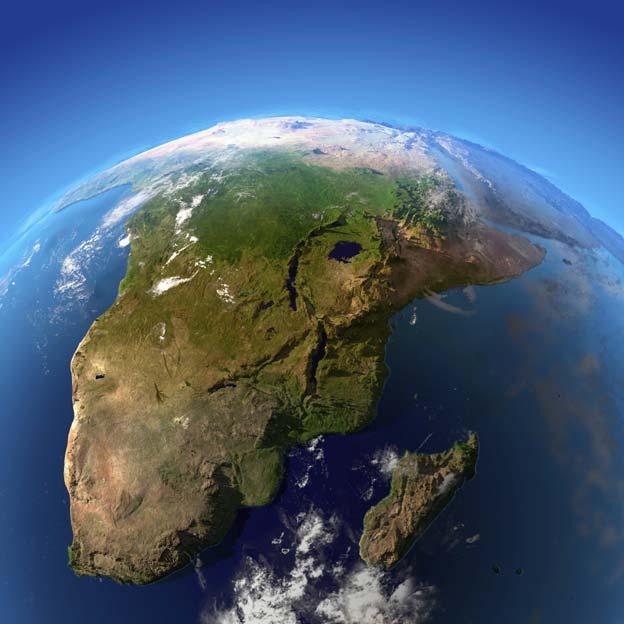
AFRICA AND THE MIDDLE EAST
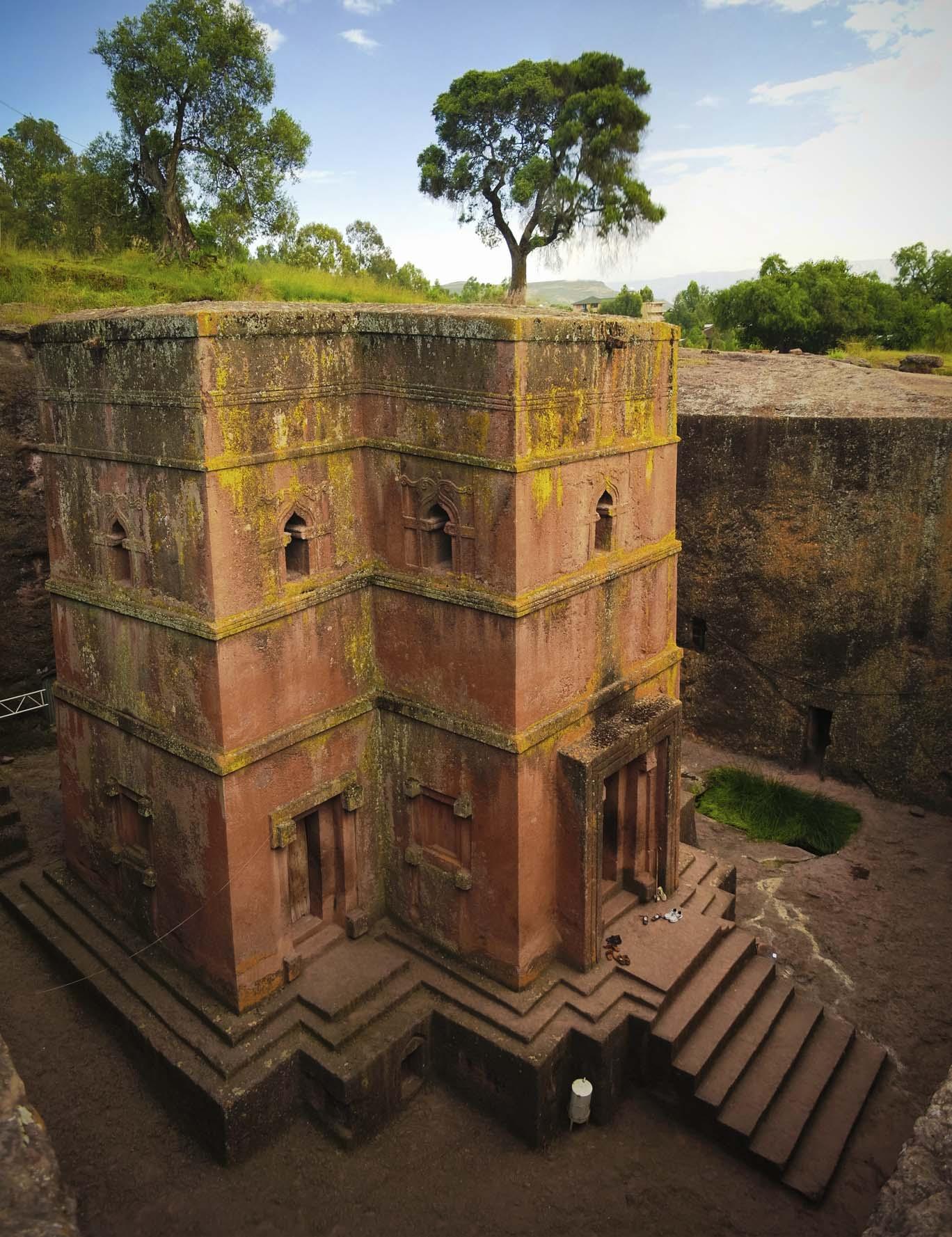
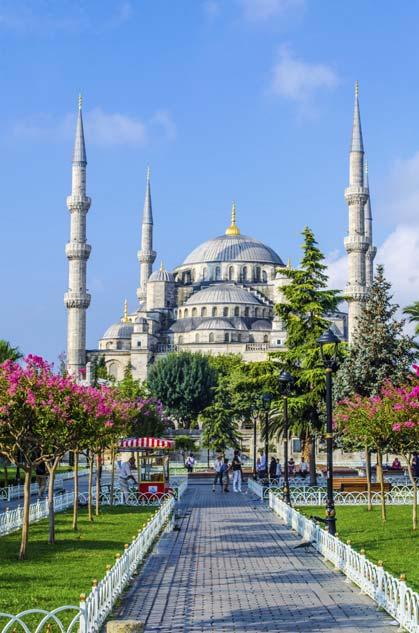
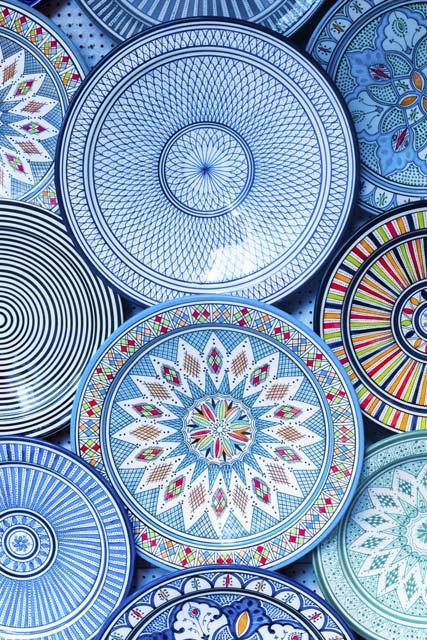

Project round-up
Egypt
KIMA urea plant
Urea melt and urea granulation plant licensed for Egyptian Chemical & Fertilizer Industries (KIMA) by Stamicarbon in Aswan, using its LAUNCH MELTTM Pool Reactor Design and LAUNCH FINISHTM Standard Granulation Design with a capacity of 1575 tpd. The contractor was Maire Tecnimont. The project started in 2011 and was completed in 2020.
NCIC urea plant
Urea melt plant licensed for NCIC El Nasr Co. for Intermediate Chemicals by Stamicarbon in Ain El Sokna, using its LAUNCH MELT Pool Reactor Design with a capacity of 1050 tpd. The contractor is thyssenkrupp Industrial Solutions. The project started in 2019 and is due to be completed in 2022.
Ethiopia
Pan-Africa Fertilizer Complex
The Pan-Africa Fertilizer Complex is a fl agship project between the government of Ethiopia and OCP and it is a symbol of south-south cooperation between Morocco and Ethiopia. It will be located in East Ethiopia in the Dire Dawa City Administration.
The project will use the natural resources of both countries to produce urea and NPS-based fertilizers.
The initial investment for the construction and operation of the fertilizer complex is US$2.4 billion and in phase two it will reach US$3.7 billion. Pre-feasibility and conceptual studies have already been completed.
Once the project is completed, it will satisfy 100% of Ethiopia’s fertilizer demand, creating jobs for more than 1200 people during construction and establishing 500 permanent roles. The project started in 2018 and is due to be completed in 2025.
Ghana
Ghana Fertilizer Complex
A joint venture between OCP Group and the government of Ghana involves the creation of a new fertilizer plant, to be called the Ghana Fertilizer Complex. The fertilizer industrial complex will leverage each country’s natural resources – natural gas from Ghana and phosphate from Morocco – which will be used to produce ammonia and high-quality fertilizers, such as urea and diammonium phosphate, for the local and sub-regional market.
The project is expected to involve the commitment of a signifi cant investment of up to US$1.3 billion, which will benefi t the local economy and communities as well as enhance and expand the agricultural and industrial ecosystem.
The plant will be located in Jomoro in the western region of a future petrochemical hub and will be designed and built using best-in-class technology. The conceptual phase for this project has already been completed.
The project started in 2019 and is due to be completed in 2025.
Israel
Haifa Group ammonia plant
Grassroots 300 tpd ammonia plant in Mishor Rotem for Haifa Group being constructed by Saipem and using Haldor Topsoe technology. Project work began in January 2021.
Morocco
Jorf Lasfar seawater reverse osmosis desalination plant extension
The preservation of water resources remains at the heart of OCP’s strategy. OCP is taking on a capital programme at the existing seawater reverse osmosis (SWRO) desalination plant at Jorf Lasfar,
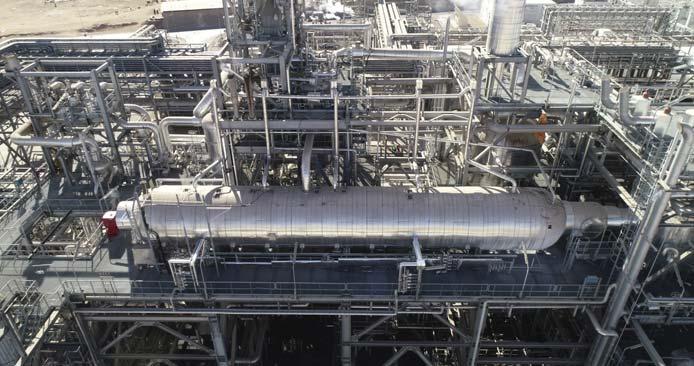
Figure 1. KIMA urea plant in Aswan, Egypt, started up in 2020 using Stamicarbon’s LAUNCH MELT Pool Reactor Design.
Figure 2. Pan-Africa Fertilizer Complex, Ethiopia.
Figure 3. Ghana Fertilizer Complex, Jomoro, Ghana.
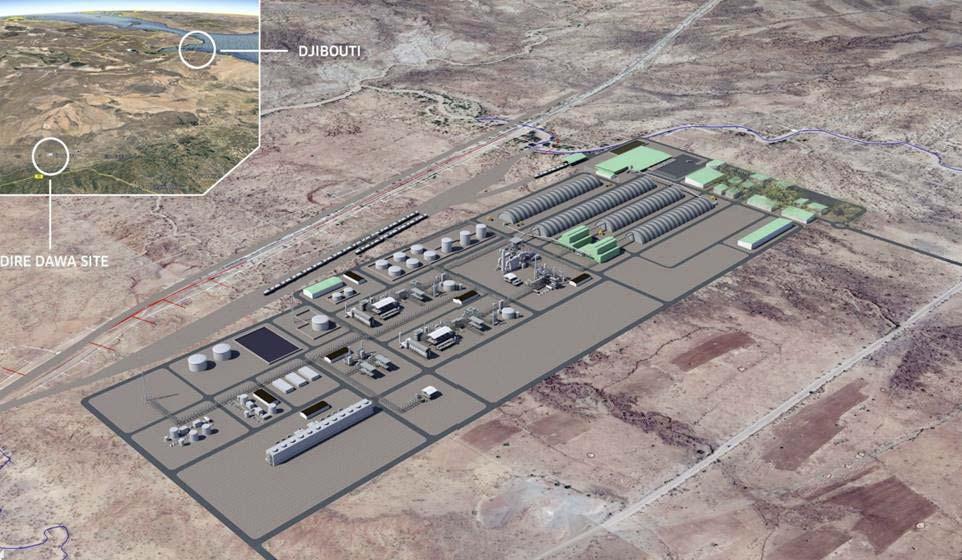
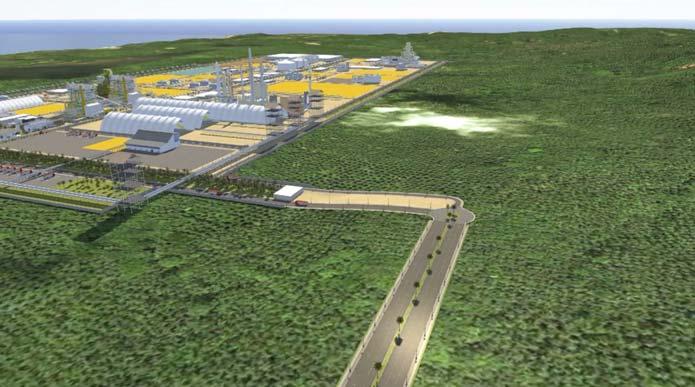
with aims to increase production capacity of processed and demineralised water from 25 million m3/yr to 40 million m3/yr.
This will enable the Jorf Lasfar phosphate hub to respond to the growing demand for processed and demineralised water without consuming water from other natural water resources, such as groundwater and rivers. Considering the constraints of seawater quality variation on the coastal intake, the plant expansion will increase the capacity of the pre-treatment unit based on dissolved air fl otation and ultrafi ltration technology.
Furthermore, the project will use energy recovery device technology to produce the desalinated water with the most effi cient energy consumption possible. The plant will produce two water qualities as per the needs of the industrial complex. The processed water and demineralised water will be stored in four separate water tanks to be distributed to different consumers. In addition to the on-site effl uent treatment, the brine generated by the plant will be diluted into the cooling water system of the Jorf Lasfar hub, and then reused in processing units. The Jorf Lasfar desalination unit runs on surplus clean energy created from the phosphate manufacturing process (the generation of steam in the sulfuric acid production process), which is then transformed into electrical energy. The project started in 2019 and is due to be completed in 2022.
Phosboucraa fertilizer complex desalination plant
As part of the development strategy of the southern provinces of Morocco, OCP has launched an investment programme to transform raw phosphate into fi nal and semi-fi nal products.
The industrial development programme includes the construction of a seawater desalination plant with a capacity of 8 million m3 within the Phosboucraa fertilizer complex (PFC) to feed different units with the required water qualities (processed water, demineralised and potable water).
An offshore intake, positioned at 1.8 km from the shore, will be connected to a pumping station to feed the plant with the required seawater quantities as well as the needed cooling water for the industrial units. The desalination plant will use reverse osmosis technology to produce different water qualities. An ultrafi ltration unit will pre-treat the seawater before it reaches the membrane separation process. The water will pass through the reverse osmosis trains twice to produce processed water as well as the demineralised water.
A post-treatment unit will be installed to alter the processed water quality to fi t with drinking water quality requirements. The plant will run on clean energy produced at the power generation plant that uses steam generated at the sulfuric acid production process, which is then transformed into electrical energy. The brine issued from the plant will be sent to seawater ponds for dilution before it is used by industrial units as cooling water. The project started in 2021 and is due to be completed in 2024.
Safi & Jorf Lasfar Complex
OCP has initiated a signifi cant investment plan to design, in an eco-friendly manner, new production lines and improve the technological performance of existing production lines at the Safi & Jorf Lasfar Complex to meet global standards, including those of the World Bank.
Beyond acquiring technology available on the market, OCP has built strong partnerships to develop new technology. A stand-out example of this is the Sulfacid® process at its Jorf Lasfar and Safi industrial platforms, which reduces sulfur dioxide (SO2) gas emissions by 98%.
OCP’s Sulfacid process combines the expertise of a partner specialised in gas processing and the company’s operational expertise in sulfuric acid production. As a result, the company intends to reduce SO2 gas emissions at fi ve of its sulfuric production lines.
This is a world-fi rst achievement in the sulfuric acid industry. It is an incorporation of an additional gas scrubbing system into the existing contact unit to recover the exhaust gases and convert them to sulfuric acid, which is then reused in the production chain, forming a circular economy.
The Sulfacid process converts SO2 in the fl ue into sulfuric acid of up to 15% by mass of H2SO4, by wet catalysis using activated carbon, oxygen and water. The environmental performance obtained exceeds the most stringent standards in the world. The project started in 2018 and was completed in 2020.
Safi wastewater treatment plant
In order to ensure a supply of processed water at the Safi industrial complex when there are increased demands on water sources in the region, OCP signed an agreement with the local water authority in December 2019 to construct an urban wastewater treatment plant (WWTP) for the city of Safi .
This plant will allow the company to produce 8 million m3/yr of highly treated wastewater that will feed the industrial units, and therefore preserve freshwater resources in the region as well as the environment by avoiding the discharge of urban wastewater into the sea.
The WWTP will use an activated sludge treatment process to create high-quality treated water, followed by a tertiary treatment that consists of a combination of three stages of treatment (microfi ltration, sand fi ltration and disinfection). After the tertiary treatment, water from the plant is sent to the main water tank at Safi ’s industrial units, where it is used as raw water.
The WWTP will also address the sludge issue by providing class A sludge quality at the outlet. This is made possible by the installation of a thermal hydrolysis process (THP) unit. This process solution pressurises the biosolids at a high temperature to improve the digestibility of the biosolids and will eliminate all pathogens before anaerobic digestion, making the sludge suitable for reuse at landscaping.
Furthermore, the plant will recover biogas emitted at the digestor during the wastewater treatment process. This biogas will cover more than 30% of the electrical energy needed to operate the WWTP. The project started in 2020 and is due to be completed in 2023.
Nigeria
Agricultural centres of excellence
Three blending units are currently under construction by OCP Africa Nigeria Ltd. in Kaduna, Ogun and Sokoto and are due
to start production this year. They will have a total production capacity of 500 000 tpy of blended fertilizers.
The facilities will serve as centres of excellence, encompassing storage and blending facilities, quality control laboratories and training centres for both farmers and fertilizer industry players.
By training farmers and market players in agronomical and industry best practices, these centres will promote the production of customised fertilizers that are adapted to the soils and the environment. The project started in 2019 and is due to be completed in 2021.
Dangote ammonia plant
Grassroots 2200 tpd ammonia plant for Dangote Fertilizers Ltd., with engineering and procurement by Saipem and technology from Haldor Topsoe. Construction began in January 2013 and is due to be completed in 2021.
Nigeria multipurpose industrial platform
A multipurpose industrial platform will be built by a joint venture between OCP Africa and the Nigerian Sovereign Investment Authority that will encompass, in its fi rst phase, an ammonia plant and a phosphate-based fertilizer plant. The ammonia plant is expected to have a capacity of 750 000 tpy. The fertilizer plant will be operating at a capacity of 1 million tpy by 2025.
The project falls within the framework of the import-substitution programme being pursued by the Nigerian government since 2016 with the launch of the Presidential Fertilizer Initiative. This initiative aims to domesticate production and promote the supply of high-quality fertilizer.
Using both Nigerian gas and Moroccan phosphate, the US$1.4 billion project seeks to provide Nigerian famers with phosphate-based fertilizers adapted to their soil and crops needs and supply OCP with ammonia. The project started in 2019 and is due to be completed in 2025.
Notore Chemical Industries Ltd. plant
Deployment of ClearView concept – a living digital twin to enhance performance and reliability – by Haldor Topsoe for Notore Chemical Industries Ltd. The project is scheduled to fi nish in June 2021.
Saudi Arabia
Helios project
Grassroots 4GW green ammonia synthesis loop from Haldor Topsoe using single S-300 ammonia converter at the Helios project in the NEOM business region. Contracted by Air Products, the project began in 2020.
Turkey
Gemlik urea plant
Urea melt and granulation plant licensed for Gemlik Gubre Sanayl A.S. by Stamicarbon, using its LAUNCH MELTUltra-Low Energy Design and LAUNCH FINISHOptimised Granulation Design with a capacity of 1640 tpd. The contractor is Maire Tecnimont. Work on the project started in 2020 and is due to be completed in 2023.
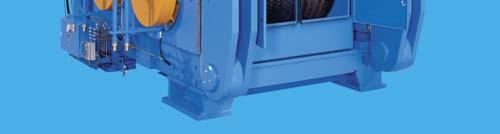
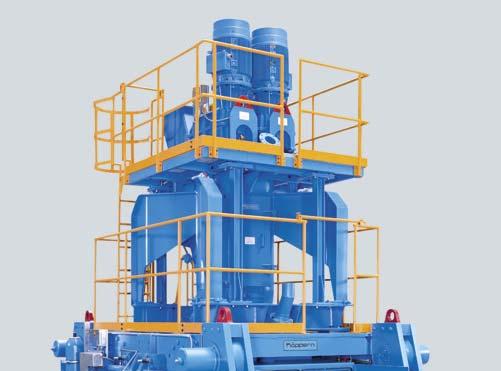

Dry granulation of fertilizers
Our technology has been recognized around the world for dry granulation of MOP / SOP and NPKs. Our services cover pilot plant tests, basic engineering, equipment supply, start-up supervision, and commissioning. Typical fl ake capacities are in the range of 10 –130 t / h or more.
We have received orders for more than 0 fertilizer compactors of latest Köppern technology since the year 2000. The total installed fl ake capacity of these plants is exceeding ,000,000 tpa. Köppern – Quality made in Germany.
• State of the art technology • Process technology know-how • High plant availability • Quick roller replacement
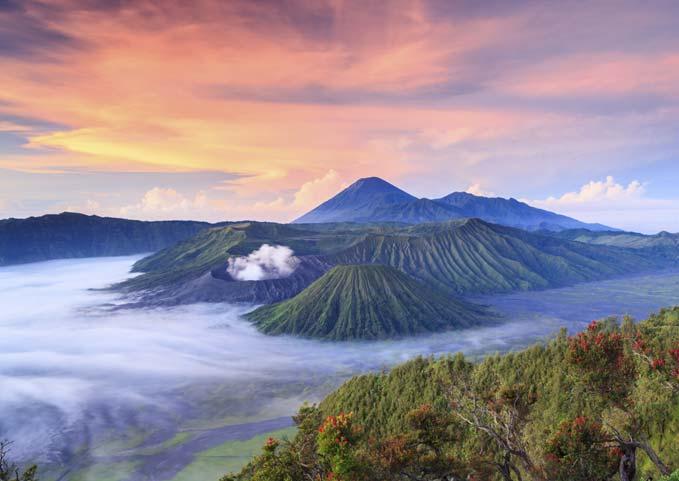
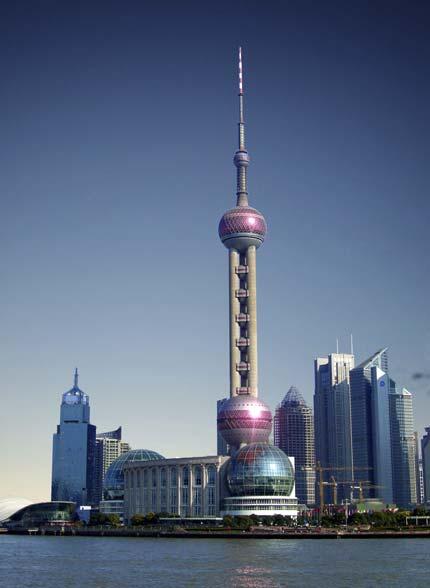
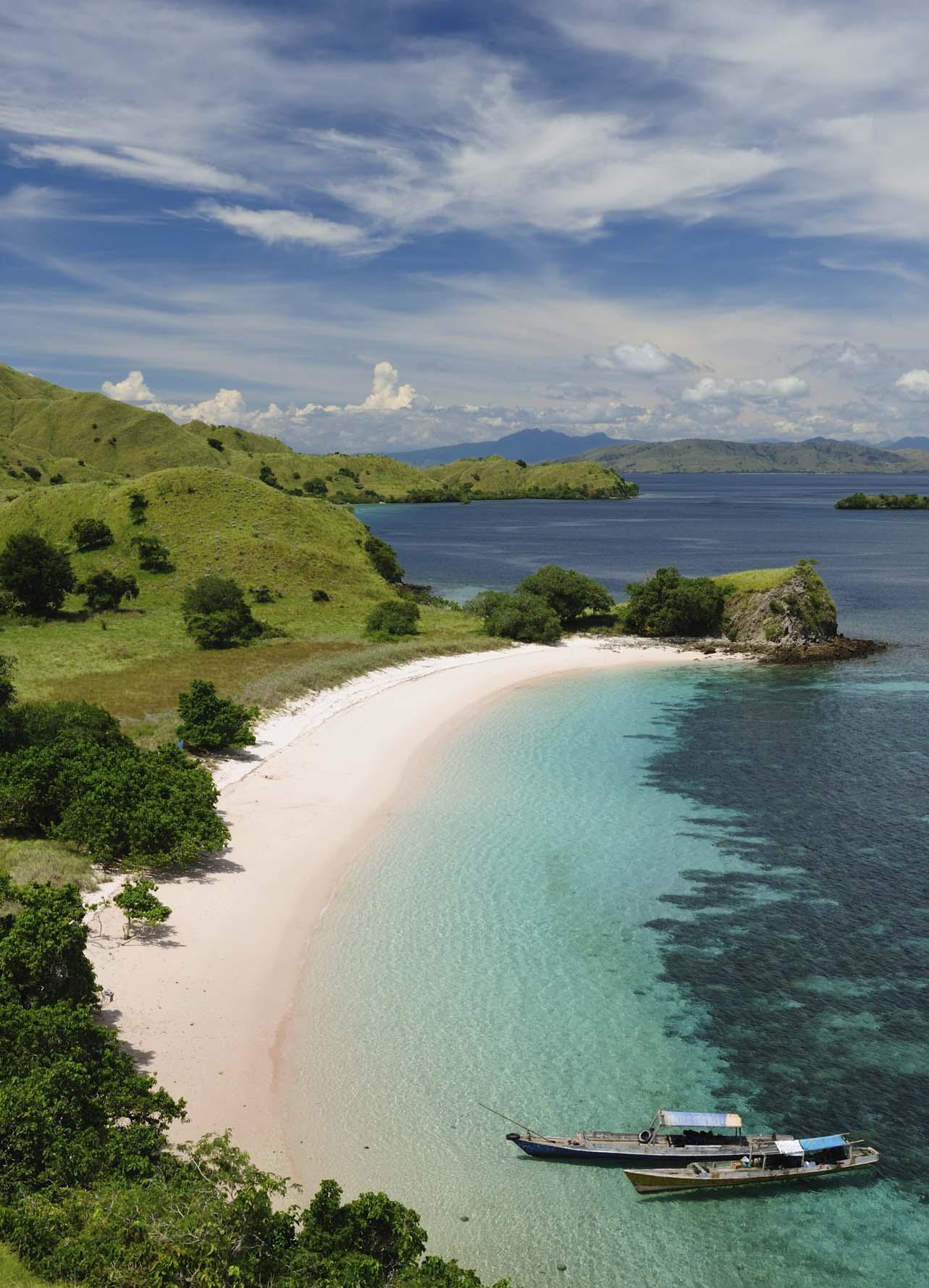
ASIA PACIFIC

Project round-up
Australia
Destiny ammonia plant
Grassroots 3507 tpd ammonia plant for Perdaman Chemicals and Fertilisers in Western Australia. Engineering and procurement by Saipem, using Haldor Topsoe technology. The project began in 2019.
Bangladesh
Ghorasal Polash Urea Fertilizer Project
Grassroots 1600 tpd ammonia plant, constructed by Mitsubishi Heavy Industries for Bangladesh Chemicals Industries Corp., using Haldor Topsoe technology. The project began in September 2018 and is due to be completed in 2022.
Brunei
Sungai Liang urea melt plant
Urea melt plant in Sungai Liang Industrial Park for Brunei Fertilizer Industries Sdn Bhd, licensed by Stamicarbon using its LAUNCH MELT Pool Condenser Design with a capacity of 3900 tpd. The contractor is ThyssenKrupp Industrial Solutions. Project work began in 2018 and is due to be completed in 2021.
China
Henan Xinlianxin Fertilizer XLX-1 urea melt plant
Urea melt plant for Henan Xinlianxin Chemicals Group Co. Ltd. in Jiangxi, Jiujiang, licensed by Stamicarbon using its LAUNCH MELT Ultra-Low Energy Design with a capacity of 2334 tpd. The contractor was Hualu Engineering. Project work began in 2017 and was completed in 2021.
Henan Xinlianxin Fertilizer XLX-2 urea melt plant
Urea melt plant for Henan Xinlianxin Chemicals Group Co., Ltd. in Jiangxi, Jiujiang, licensed by Stamicarbon using its LAUNCH MELT Ultra-Low Energy Design with a capacity of 2334 tpd. Project work began in 2020 and is due to be completed in 2024.
Sanning urea melt plant
Urea melt plant in Hubei for Hubei Sanning Chemical Industrial Co., licensed by Stamicarbon using its LAUNCH MELT Ultra-Low Energy Design with a capacity of 2334 tpd. The contractor is Wuhuan Engineering, China. The project began in 2018 and is due to be completed in 2021.
India
Grassroots 2200 tpd ammonia plant for Hindustan Urvarak & Rasayan Ltd. (HURL) in Barauni, Bihar, constructed by TechnipFMC and using Haldor Topsoe technology. The project began in May 2018 and is due to be completed in 2021.
HURL Sindri plant
Grassroots 2200 tpd ammonia plant for HURL in Sindri, Jharkhand, constructed by TechnipFMC and using Haldor Topsoe technology. The project began in May 2018 and is due to be completed in 2021.
Ramagundam plant
Grassroots 2420 tpd ammonia plant in Ramagundam, Telangana, with Haldor Topsoe HTER, construction by Engineers India Ltd. for Ramagundam Chemicals & Fertilizers Ltd. Construction work began in December 2015 and start-up was achieved in November 2020.
Talcher urea melt plant
Urea melt plant for Talcher Fertilizers Ltd. in Talcher, Odisha, licensed by Stamicarbon using its LAUNCH MELT Pool Condenser Design with a capacity of 3850 tpd. The contractor is Wuhuan Engineering. The project began in 2019 and is due to be completed in 2023.
Indonesia
PT. Kaltim Parna Industri plant
Deployment of ClearView concept – a living digital twin to enhance performance and reliability – by Haldor Topsoe for PT. Kaltim Parna Industri (KPI). The project finished in February 2021.
New Zealand
Ballance Agri-Nutrients Kapuni Ltd. plant
Deployment of ClearView concept for Ballance Agri-Nutrients Kapuni Ltd. by Haldor Topsoe to enhance performance and reliability. The project finished in March 2021.
Pakistan
Fatima Fertilizer Co. Ltd. plant
Deployment of ClearView concept for Fatima Fertilizer Co. Ltd. (FFC) by Haldor Topsoe to enhance performance and reliability. The project finished in November 2020.

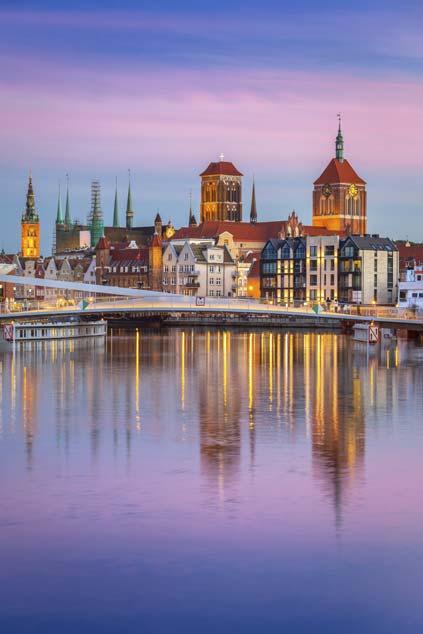
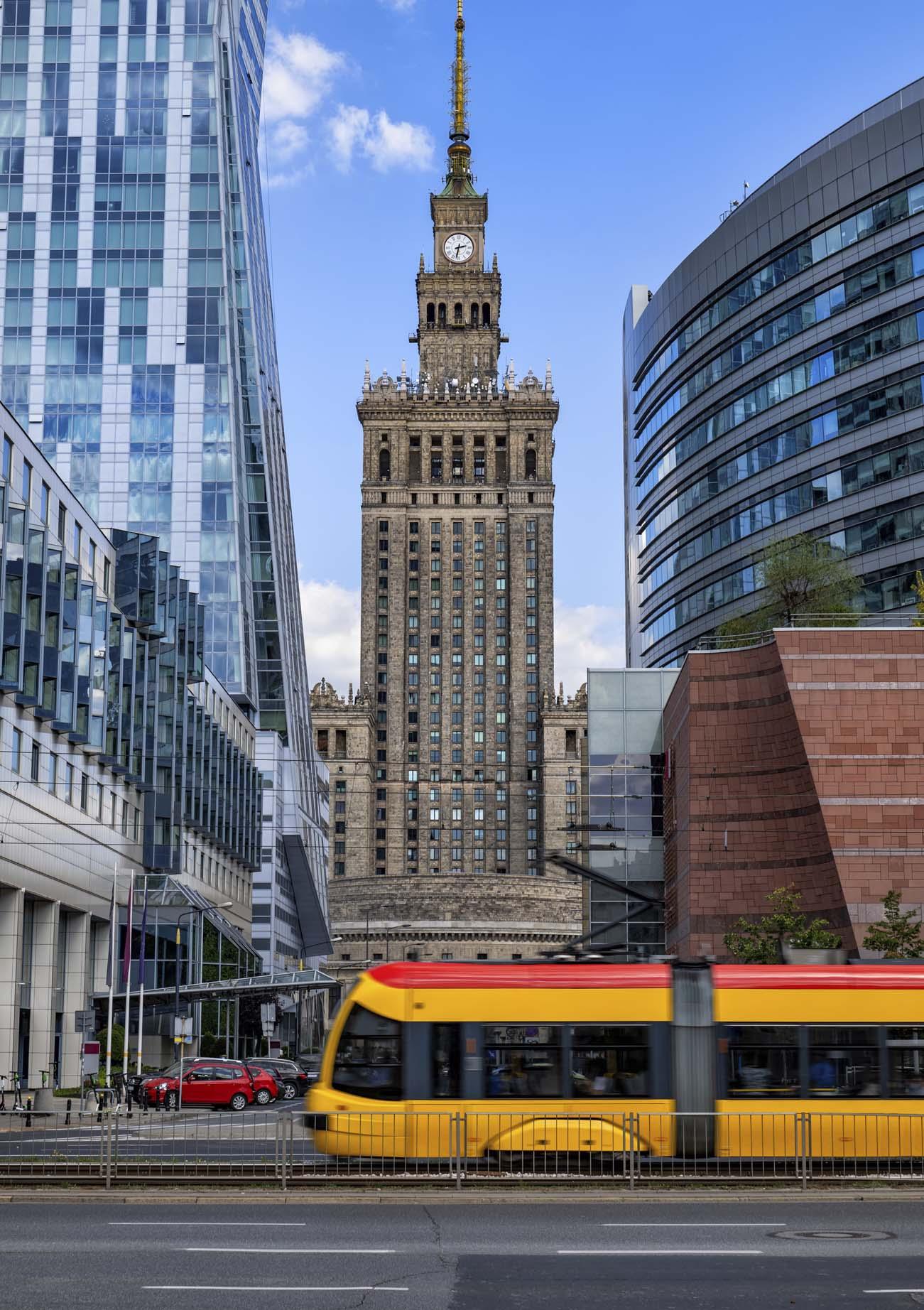
EUROPE AND CIS
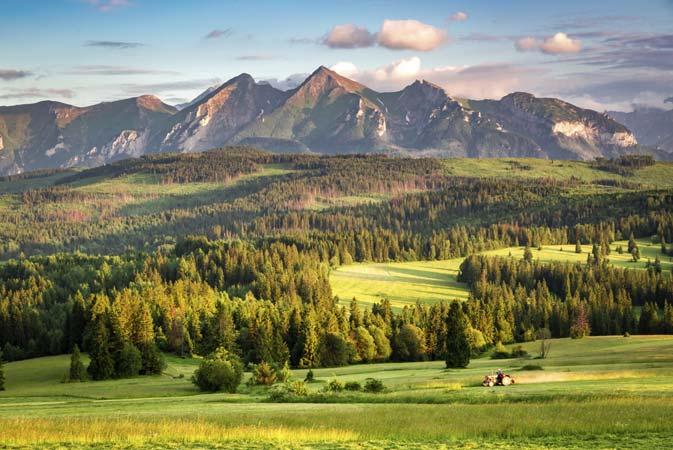
Project round-up
Belarus
Grodno sulfuric acid plant
Engineering, production and supply of a complete process gas cooler system was provided by BERTSCHenergy for the JSC Grodno Azot sulfuric acid production plant, operated by BELNEFTEKHIM.
The scope of supply included fire tube boilers, a water tube superheater, a steam drum, a feed water preheater, a superheater, an economiser and auxiliaries. The process gas cooler system is part of the sulfuric acid plant, with the following parameters: Maximum process gas flow: 224 000 kg/h. Maximum gas inlet temperature: 1200˚C. Maximum gas inlet pressure: 0.35 barg. Maximum heat duty: 28 MW. Maximum steam pressure: 43 barg. Maximum steam production: 36.3 to/h.
The project began in March 2018 and is due to be completed in March 2023.
Grodno urea plant
Plant revamp at JSC Grodno Azot’s urea plant, licensed by Stamicarbon using its EVOLVE PRODUCTTM Diesel Exhaust Fluid (DEF) technology, with a capacity expansion of 90 tpd. The project began in 2018 and is finishing in 2021.
Belgium
Tertre ammonia plant
In November 2018, Yara International ASA selected Clariant ActiSafE to control the speed of their ammonia synthesis catalyst activation at their plants in Tertre.
ActiSafE showed reliable results during synthesis catalyst activation at Yara and was able to optimise and speed up the activation process without stressing the catalyst with too high water vapour formation. The necessary information on water vapour formation was also available during process disturbances at any time of the day, without the requirement of additional laboratory staff or a resultant time delay. In addition, instantaneous water and ammonia concentrations and not averaged values are measured, giving a more realistic picture of the situation than other techniques, such as the Karl Fischer titration method.
A more realistic picture will increase confidence that the operator has full control over the reduction procedure. This is crucial, as ammonia synthesis catalyst reductions are quite rare events for the production site and the majority of the operators will experience them just once in their work lives.
Terte ammonia plant
Yara Tertre faced a pressure drop limitation in the primary reformer, which prevented the plant from increasing its ammonia production. In December 2018, Yara decided to purchase Clariant’s new steam reforming catalyst ReforMax® 330 LDP Plus, which provides high activity but extremely low pressure drop.
Because of a malfunction of the flowmeter during the start-up, the new catalyst suffered a severe coking event during start-up. As a result of close collaboration, Yara and Clariant were able to successfully recover ReforMax 330 LDP Plus.
This case proves that the increased void fraction of the catalyst allowed for extra forgiveness and safer operation under the prevailing harsh conditions and made it easier to achieve a complete recuperation.
Hence, despite this incident, Yara can safely run the plant at full capacity until their next scheduled turnaround. Furthermore, ReforMax 330 LDP Plus operates with a more than 16% lower pressure drop, and is expected to reach the guaranteed lifetime.
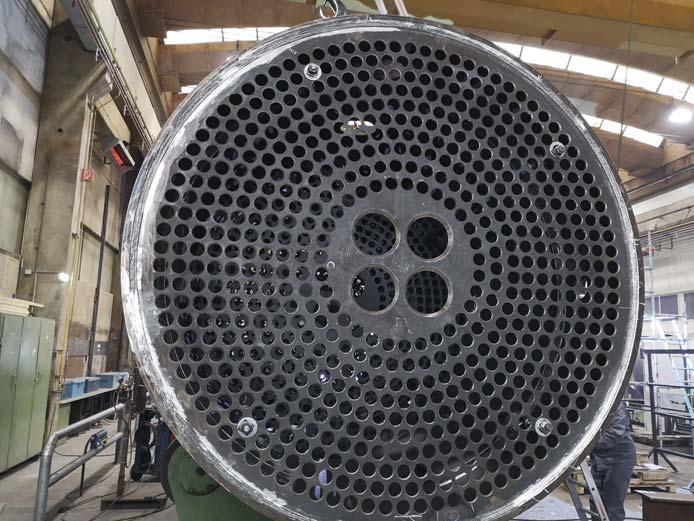
Figure 1. Tubesheet of one of the fire tube evaporators supplied by BERTSCHenergy for the JSC Grodno Azot sulfuric acid production plant.
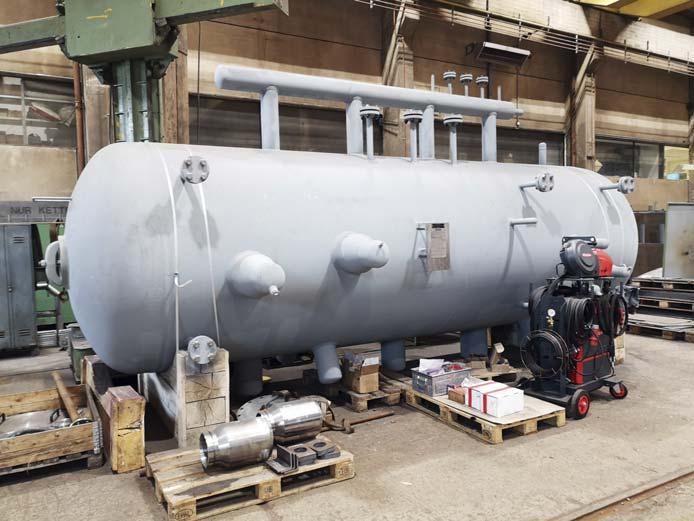
Figure 2. Steam drum supplied by BERTSCHenergy for the JSC Grodno Azot sulfuric acid production plant.
Netherlands
Geelen Plant AFA 2
OCI’s AFA 2 ammonia plant in Geelen is a Bechtel design with a capacity of 1550 tpd and runs a side-fi red Foster Wheeler reformer. Before a turnaround in 2018, pressure drop over the front end was an important production limitation for OCI at AFA 2. The installation of Clariant’s ReforMax 330 LDP Plus catalyst, and optimisation of catalyst volumes in other reactors, has removed this limitation, signifi cantly increasing its energy and production effi ciency.
Since its start-up in June 2018, ReforMax 330 LDP Plus has demonstrated very stable operation and provided a signifi cant reduction in pressure drop across the catalyst bed in the reformer tubes. This improvement will avail the plant of savings of more than €300 000 over the expected catalyst lifetime of eight years, compensating for the catalyst investment.
Poland
Grupa Azoty ammonia plant
Revamp of existing ammonia plant for Grupa Azoty, including upgrading of autothermal reformer internals, refractory upgrade, new Haldor Topsoe CTS burner and lowering S/C ratio. The project commenced in August 2018 and fi nished in July 2020.
Russia
Acron IV ammonia plant
Revamp of existing Topsoe designed ammonia plant for Acron Group, in order to increase capacity to 2500 tpd by introducing Haldor Topsoe HTER. The project at the Acron IV plant commenced in January 2018 and fi nished in July 2020.
Acron urea granulation plant
Urea granulation plant in Novgorod for Acron Group, licensed by Stamicarbon using its LAUNCH FINISHTM Optimised Granulation Design with a capacity of 2000 tpd. The contractor was GAIP Velikiy Novgorod. The project commenced in 2018 and fi nished in 2020.
Kingisepp-2 urea plant
Urea melt and granulation plant at EuroChem Northwest’s Kingisepp-2 site, licensed by Stamicarbon using its LAUNCH MELTTM Pool Condenser Design and LAUNCH FINISH Optimised Granulation Design with a capacity of 4000 tpd. The contractor is Maire Tecnimont. The project began in 2020 and is expected to fi nish in 2023.
Perm Mineral Fertilizers OJSC urea plant
Urea revamp for Uralchem OJSC’s Perm Mineral Fertilizers OJSC urea plant, licensed by Stamicarbon using its EVOLVE CAPACITYTM Design with a capacity expansion of 770 tpd. The project began in 2015 and is due to fi nish in 2022.
ShchekinoAzot urea plant
Urea melt and granulation plant in Pervomayskiy for ShchekinoAzot, licensed by Stamicarbon using its LAUNCH MELT Pool Reactor Design and LAUNCH FINISH Optimised Granulation Design with a capacity of 2000 tpd. The contractor is China National Chemical Engineering. The project began in 2019 and is expected to fi nish in 2022.
ShchekinoAzot ammonia plant
Grassroots 1500 tpd ammonia plant for ShchekinoAzot, constructed by China National Chemical Engineering Co., China, with technology from Haldor Topsoe. The project began in 2020 and is scheduled to fi nish in 2024.
Volgafert urea plant
Urea melt and granulation plant in Togliatti for Volgafert – majority-owned by KuibyshevAzot JSC – licensed by Stamicarbon using its LAUNCH MELT Pool Reactor Design and LAUNCH FINISH Optimised Granulation Design with a capacity of 1500 tpd. The contractor is Maire Tecnimont. The project began in 2017 and is expected to fi nish in 2022.
United Kingdom
Hull ammonia plant
In June 2019, Yara International ASA selected Clariant ActiSafE to control the speed of their ammonia synthesis catalyst activation at their plant in Hull.
ActiSafE showed reliable results during synthesis catalyst activation at Yara and was able to optimise and speed up the activation process without stressing the catalyst with too high water vapour formation. The necessary information on water vapour formation was also available during process disturbances at any time of the day, without the requirement of additional laboratory staff or a resultant time delay. In addition, instantaneous water and ammonia concentrations and not averaged values are measured, giving a more realistic picture of the situation than other techniques, such as the Karl Fischer titration method.
A more realistic picture will increase confi dence that the operator has full control over the reduction procedure. This is crucial, as ammonia synthesis catalyst reductions are quite rare events for the production site and the majority of the operators will experience them just once in their work lives.
Uzbekistan
Uzkimyosanoat ammonia plant
Grassroots 2000 tpd ammonia plant for Uzkimyosanoat Joint Stock Co., constructed by Mitsubishi Heavy Industries using Haldor Topsoe technology. The project began in May 2016 and finished in December 2020.

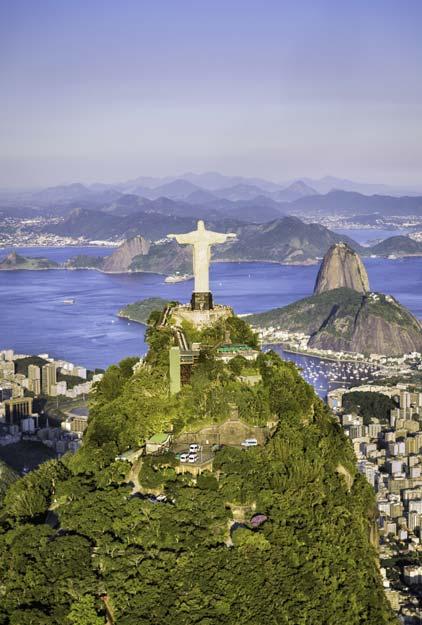
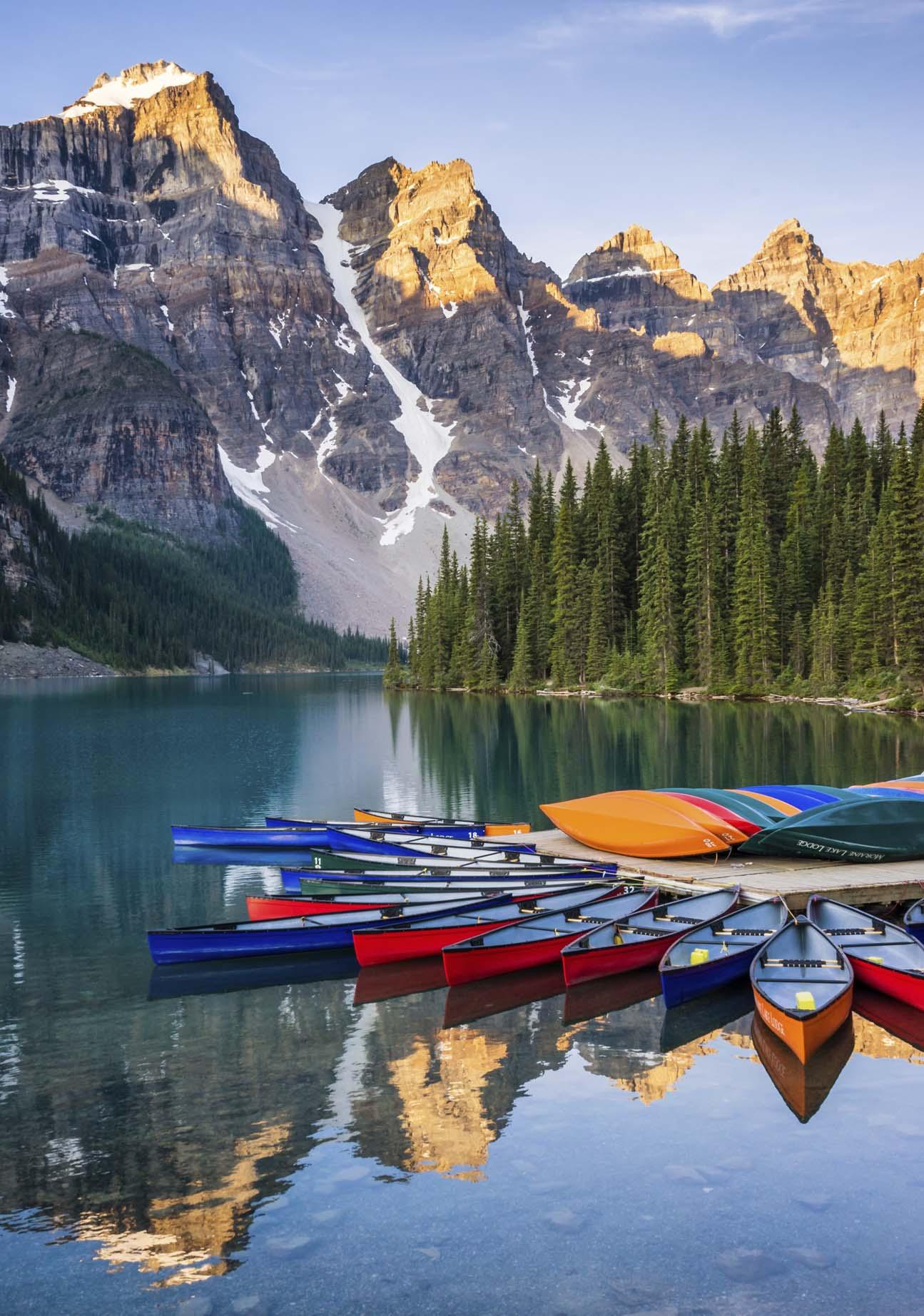
THE AMERICAS
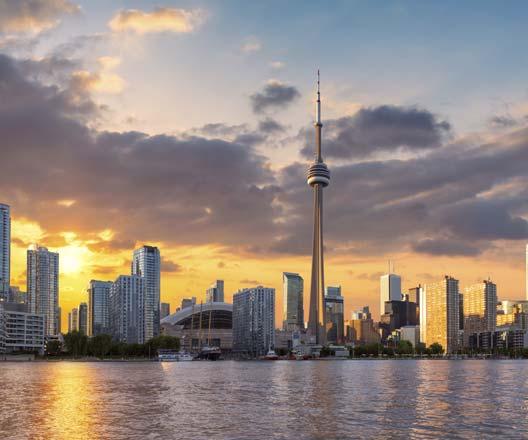
Project round-up
Brazil
NPK blending plant
Bagtech’s fi rst NPK blending plant in Brazil was commissioned by Hinove Agrociência in 2020 in Rio Brilhante, located in the state of Mato Grosso do Sul in the Midwest region. It was a challenging project that aimed to implement a continuous blending plant connected online to the Bagtech Automation System, with a capacity of 60 tph. The project began in February 2020 and fi nished in April 2020.
The main features are: Precision flow control, an advanced control philosophy, low maintenance and elimination of the risk of product damage during operation. Agile processes: process flexibility that allows smaller production batches with greater customisation, improving the product range, mix and scalability. Reduction of operating costs: the high level of control and automation software for Bagtech equipment results in less waste of materials, a more efficient operation and a direct reduction in operating costs. Increased profitability. Communication and decision making: Bagtech’s automation control software allows for quick problem resolution as well as agility in the control of the entire process, making it possible to operate the equipment anywhere in the world.
Canada
Urea plant
Urea plant revamp licensed by Stamicarbon, using its EVOLVE CAPACITY design with a capacity expansion of 300 tpd. The project started in 2019 and is due to be completed in 2022.
United States
El Dorado Chemicals plant
Clariant’s ReforMax LDP Plus catalyst was loaded in the primary reformer of the KBR 1320 tpd ammonia unit at LSB Industries’ El Dorado Chemicals fertilizer plant in Arkansas.
The customer switched to the novel catalyst to achieve a pressure drop reduction and to improve the energy effi ciency of the plant.
ReforMax 210/330 LDP Plus was successfully started up in September 2019.
The customer achieved a noticeable reduction in pressure drop of 4 psi (equivalent to 0.3 bar) measured across the entire reformer, which is approximately 16% lower than for the previous charge. Looking at the catalyst in the tubes
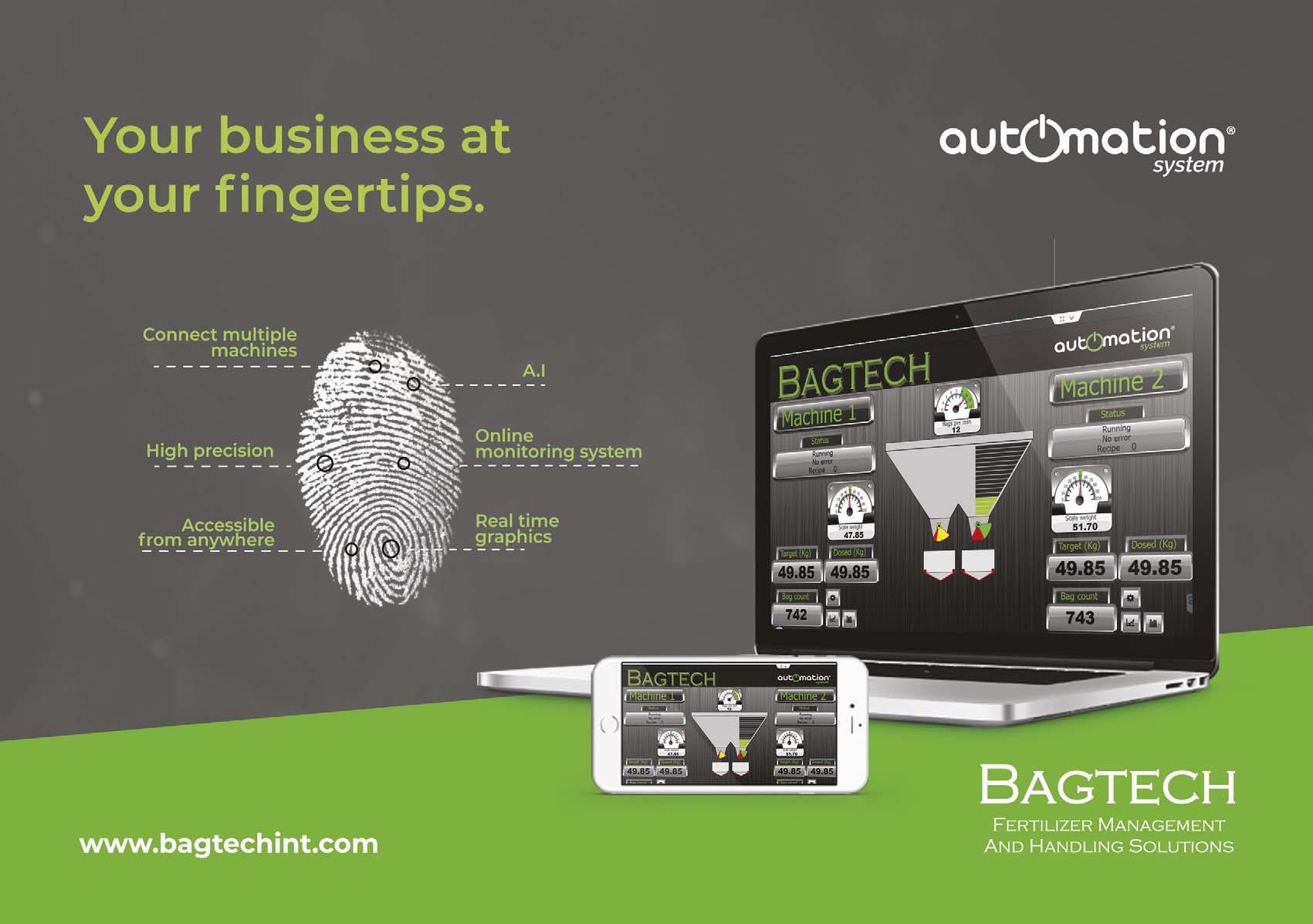
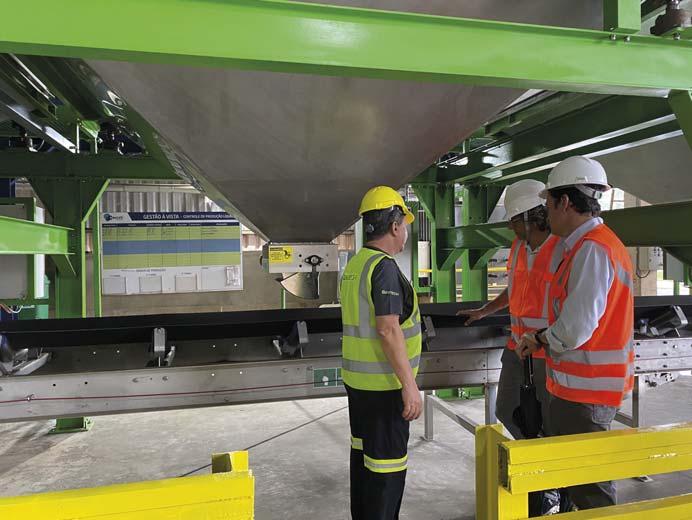
Figure 1. Finishing training with customers at Bagtech’s first NPK blending plant in Brazil.
alone, the expected 20% pressure drop reduction was achieved.
A tube wall temperature survey shows that the catalyst provides excellent heat transfer, as evidenced by a uniform temperature distribution across the tubes with an average tube wall temperature of 1522˚F.
The new catalyst has been very stable so far and is still at the same SOR pressure drop and methane leakage after one and a half years of operation.
Based on the energy savings at the natural gas pricing in North America, the customer achieves an estimated energy cost saving of US$45 000/yr, which is more than US$200 000 over the catalyst’s estimated useful life.



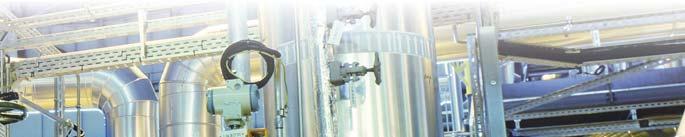

38 | ABC 13 | Argus Media 63 | Bagtech 37 | Bedeschi S.p.A. 04 | Casale 24 | EMT/Doyle Equipment Manufacturing 02 | Eurotecnica 17 | Gambarotta 41 | GEA IBC | GPCA Supply Chain Conference 35 | J&H Equipment Inc. OFC & 27 | Jotun
Gulf Coast Ammonia project
Grassroots 3600 tpd ammonia synthesis loop from Haldor Topsoe using single S-300 ammonia converter for the Gulf Coast Ammonia project in Texas, contracted by Air Products. The project began in September 2018 and is still under construction, with completion expected in 2021.
Urea plant
Urea revamp licensed by Stamicarbon, using its EVOLVE CAPACITY Design with a capacity expansion of 544 tpd. The project started in 2020 and is due to be completed in 2024.
Urea plant
Urea revamp licensed by Stamicarbon, using its EVOLVE CAPACITY Design with a capacity expansion of 660 tpd. The project started in 2019 and is due to be completed in 2022.
Urea plant
Urea revamp licensed by Stamicarbon, using its EVOLVE CAPACITY Design with a capacity expansion of 725 tpd. The project started in 2016 and was completed in 2020.
AD INDEX
07 | Koch-Glitsch 55 | Köppern 49 | Ludman Industries
IFC | Neelam Aqua & Speciality Chem(P) Ltd. 23 | Nel Hydrogen 60 | Palladian Publications OBC | Prayon Technologies 42 | Sackett Waconia 19 | S.I.G. 09 | Stamicarbon 33 | Statec Binder
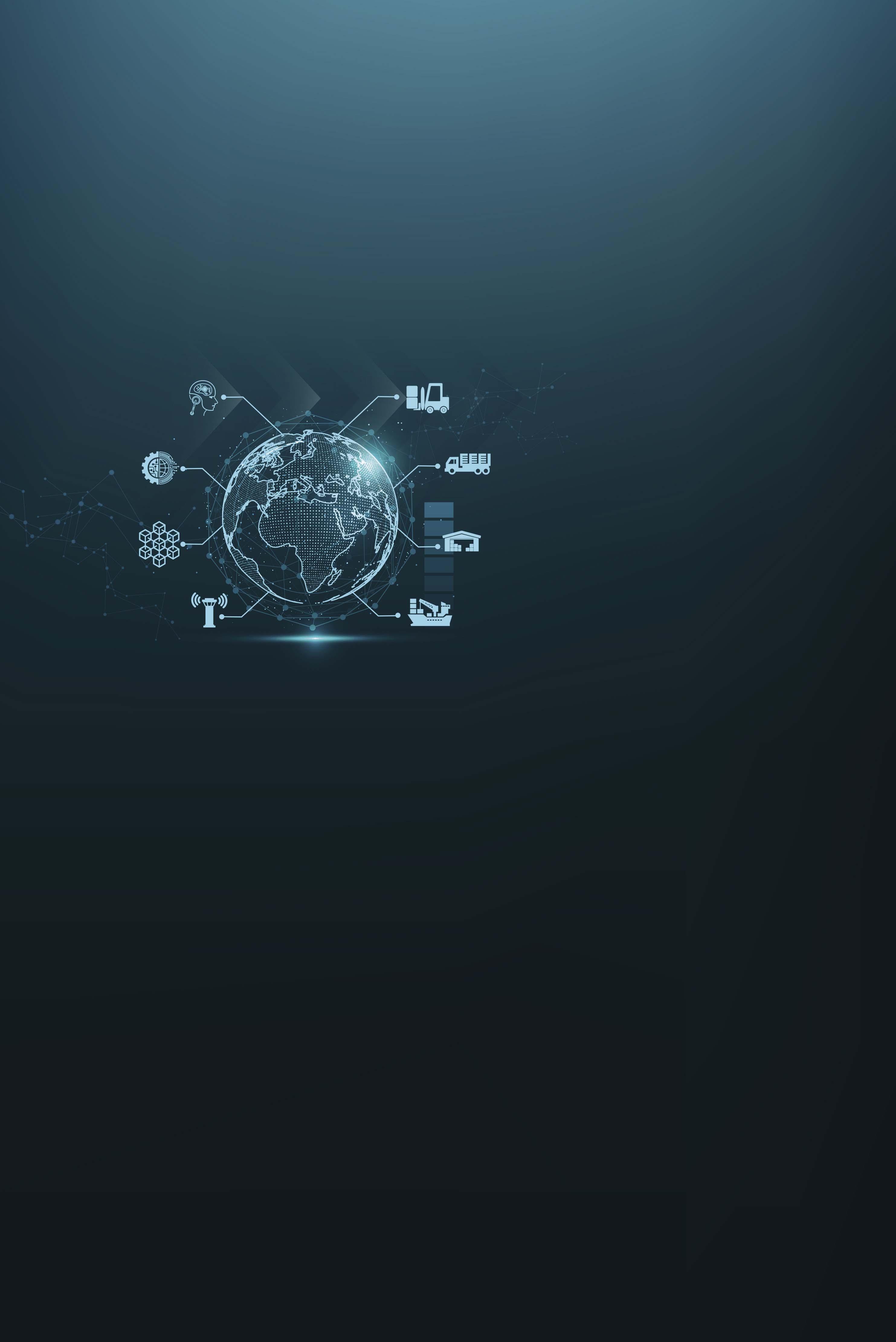